印度煤基直接还原铁生产建设近况
直接还原铁技术现状

冶金管理2006年第8期直接还原铁是铁矿在固态条件下直接还原为铁,可以用来作为冶炼优质钢、特殊钢的纯净原料,也可作为铸造、铁合金、粉末冶金等工艺的含铁原料。
这种工艺不用焦炭炼铁,原料也是使用冷压球团不用烧结矿,所以是一种优质、低耗、低污染的炼铁新工艺,也是全世界钢铁冶金的前沿技术之一。
直接还原炼铁工艺有气基法和煤基法两种,按主体设备可分为竖炉法、回转窑法、转底炉法、反应罐法、罐式炉法和流化床法等。
目前,世界上90%以上的直接还原铁是用气基法生产出来的。
但是天然气资源有限、价高,使生产量增长不快。
用煤作还原剂在技术上也已过关,可以用块矿、球团矿或粉矿作铁原料(如竖炉、流化床、转底炉和回转窑等)。
但是,因为要求原燃料条件高(矿石含铁品位要大于66%,含SiO2+Al2O3杂质要小于3%,煤中灰分要低等),规模小,设备寿命低,生产成本高和某些技术问题等原因,致使直接还原铁生产在全世界没有得到迅速发展。
因此,高炉炼铁生产工艺在较长时间内仍将占有主导地位。
一、直接还原铁的质量要求直接还原铁是电炉冶炼优质钢种的好原料,所以要求的质量高(包括化学成分和物理性能),且希望其产品质量均匀、稳定。
1.化学成分。
直接还原铁的含铁量应>90%,金属化率要>90%。
含SiO2每升高1%,要多加2%的石灰,渣量增加30kg/t,电炉多耗电18.5kWh。
所以,要求直接还原铁所用原料含铁品位要高:赤铁矿应>66.5%,磁铁矿>67.5%,脉石(SiO2+Al2O3)量<3%~5%。
直接还原铁的金属化率每提高1%,可以节约能耗8~10度电/t。
直接还原铁含C<0.3%,P<0.03%,S<0.03%,Pb、Sn、As、Sb、Bi等有害元素是微量。
2.物理性能。
回转窑、竖炉、旋转床等工艺生产的直接还原铁是以球团矿为原料,要求粒度在5~30mm。
隧道窑工艺生产的还原铁大多数是瓦片状或棒状,长度为250~380mm,堆密度在1.7~2.0t/m3。
直接还原铁生产工艺的分析

直接还原铁生产工艺的分析世界上直接还原铁生产技术已经成熟, 技术发展极为迅速, 根据Midrex 公司预测, 2010年全世界直接还原铁产量将超过7300万t。
于高炉流程存在着生产成本过高和环境污染的两大难题, 炼铁工艺由高炉流程逐步向直接还原铁短流程过渡已成为定局。
当今的钢铁企业对这一革命性技术工艺越早开发越能占据主动; 不敢承担风险, 迟疑不前, 必将处于被动和落后的局面。
因此, 直接还原铁的开发不是“有所为”和“有所不为”的问题, 而是生产工艺的选择问题。
1 世界直接还原铁生产技术现状1.1 生产工艺发展态势由于某些国家天然气资源丰富, 直接还原铁生产技术在南美洲、南非和东南亚诸国的发展极为迅速,而印度则后来居上; 特别是委内瑞拉、墨西哥等国, 生产历史已超过20余年, 生产规模不断扩大, 直接还原铁产量已占本国钢铁产量的绝对份额; 而奥钢联、韩国合作开发的直接还原与熔融还原技术与日俱进; 浦项钢铁公司的直接还原铁生产大有代替高炉炼铁之势。
对这样的发展态势, 作为世界钢铁生产大国的中国, 我们绝不可掉以轻心。
1.2 世界直接还原铁主要生产工艺??? 世界直接还原铁生产工艺大致可分为两大类: 一种是气基竖炉生产工艺; 一种是煤基回转窑生产工艺。
前者生产量约占总产量的92%, 而后者约占总产量的8%。
在这两种生产技术的基础上, 又发展了熔融还原生产技术。
近年来, 将直接还原与熔融还原技术加以组合, 形成了COREX-Midrex联合流程, 颇受人们的关注。
直接还原铁主要生产工艺见表1。
??? 应该指出, 世界上Midrex法和HYL法应用的比较普遍, 各项技术经济指标亦趋稳定, 生产工艺成熟可靠。
特别是墨西哥的HYL法, 生产技术不断创新, 由于开发了“自重整”技术, 使建设费用减少了26% , 电炉的耗电降低了5%~6%。
印度由于缺乏天然气, 但精煤的资源丰富, 因此多采用煤基回转窑的生产方法。
直接还原的现状与发展
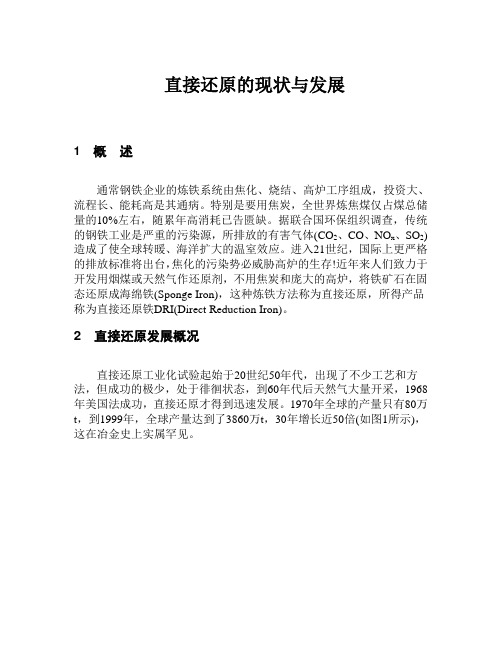
直接还原的现状与发展1概述通常钢铁企业的炼铁系统由焦化、烧结、高炉工序组成,投资大、流程长、能耗高是其通病。
特别是要用焦炭,全世界炼焦煤仅占煤总储量的10%左右,随累年高消耗已告匮缺。
据联合国环保组织调查,传统的钢铁工业是严重的污染源,所排放的有害气体(CO2、CO、NO x、SO2)造成了使全球转暖、海洋扩大的温室效应。
进入21世纪,国际上更严格的排放标准将出台,焦化的污染势必威胁高炉的生存!近年来人们致力于开发用烟煤或天然气作还原剂,不用焦炭和庞大的高炉,将铁矿石在固态还原成海绵铁(Sponge Iron),这种炼铁方法称为直接还原,所得产品称为直接还原铁DRI(Direct Reduction Iron)。
2直接还原发展概况直接还原工业化试验起始于20世纪50年代,出现了不少工艺和方法,但成功的极少,处于徘徊状态,到60年代后天然气大量开采,1968年美国法成功,直接还原才得到迅速发展。
1970年全球的产量只有80万t,到1999年,全球产量达到了3860万t,30年增长近50倍(如图1所示),这在冶金史上实属罕见。
直接还原生产海绵铁发展的客观原因有:(1)世界多数国家严重缺乏焦煤,其中不少国家有优质丰富的铁矿以及天然气和烟煤资源,它们因地制宜地借助本国资源发展直接还原工厂,如委内瑞拉、印度尼西亚、墨西哥等国有丰富天然气及优质铁矿,主要发展气基竖炉,以1995年统计为准产量达2829万tp/a,占直接还原铁总产量的92%。
而南非印度新西兰有丰富的烟煤及优质铁矿石,直接还原以煤基回转窑法为主,虽然产量仅为246万tp/a,但从近年发展趋势看,大规模的煤基回转窑法生产的直接还原厂正在纷纷建立,印度Goldstar公司建立了生产能力为22万tp/a的直接还原厂,采用Corex法:南非Iscor公司建立了生产能力为723万tp/a的直接还原厂,采用SLPRN 法;新西兰厂建立了生产能力为90万tp/a的直接还原厂,采用SLPRN法。
直接还原技术现状及其在中国的发展展望
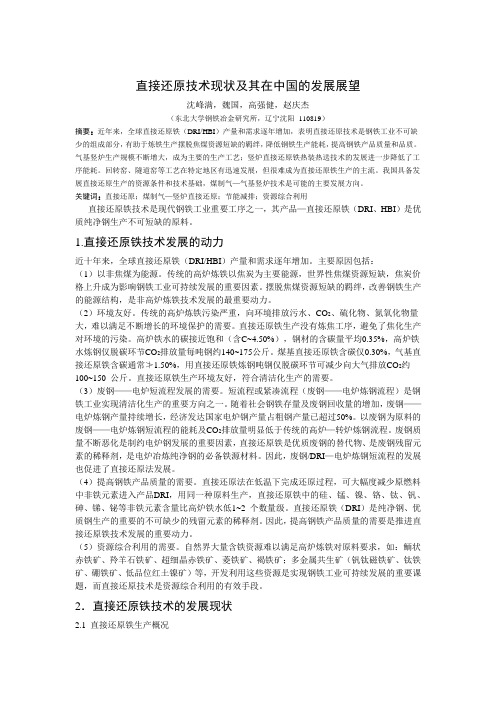
直接还原技术现状及其在中国的发展展望沈峰满,魏国,高强健,赵庆杰(东北大学钢铁冶金研究所,辽宁沈阳110819)摘要:近年来,全球直接还原铁(DRI/HBI)产量和需求逐年增加,表明直接还原技术是钢铁工业不可缺少的组成部分,有助于炼铁生产摆脱焦煤资源短缺的羁绊,降低钢铁生产能耗,提高钢铁产品质量和品质。
气基竖炉生产规模不断增大,成为主要的生产工艺;竖炉直接还原铁热装热送技术的发展进一步降低了工序能耗。
回转窑、隧道窑等工艺在特定地区有迅速发展,但很难成为直接还原铁生产的主流。
我国具备发展直接还原生产的资源条件和技术基础,煤制气—气基竖炉技术是可能的主要发展方向。
关键词:直接还原;煤制气—竖炉直接还原;节能减排;资源综合利用直接还原铁技术是现代钢铁工业重要工序之一,其产品—直接还原铁(DRI、HBI)是优质纯净钢生产不可短缺的原料。
1.直接还原铁技术发展的动力近十年来,全球直接还原铁(DRI/HBI)产量和需求逐年增加。
主要原因包括:(1)以非焦煤为能源。
传统的高炉炼铁以焦炭为主要能源,世界性焦煤资源短缺,焦炭价格上升成为影响钢铁工业可持续发展的重要因素。
摆脱焦煤资源短缺的羁绊,改善钢铁生产的能源结构,是非高炉炼铁技术发展的最重要动力。
(2)环境友好。
传统的高炉炼铁污染严重,向环境排放污水、CO2、硫化物、氮氧化物量大,难以满足不断增长的环境保护的需要。
直接还原铁生产没有炼焦工序,避免了焦化生产对环境的污染。
高炉铁水的碳接近饱和(含C~4.50%),钢材的含碳量平均0.35%,高炉铁水炼钢仅脱碳环节CO2排放量每吨钢约140~175公斤。
煤基直接还原铁含碳仅0.30%,气基直接还原铁含碳通常≯1.50%,用直接还原铁炼钢吨钢仅脱碳环节可减少向大气排放CO2约100~150 公斤。
直接还原铁生产环境友好,符合清洁化生产的需要。
(3)废钢——电炉短流程发展的需要。
短流程或紧凑流程(废钢——电炉炼钢流程)是钢铁工业实现清洁化生产的重要方向之一。
直接还原炼铁的现状及发展趋势

气基还原 , 产 厂主要集 中在南 美、 东 、 生 中 东 南 亚 等地 区 , 委 内瑞 拉 、 如 墨西 哥 、 非 、 南 印度
维普资讯
攀 钢 技 术 似烧 结 的环冷 机 , 近 年才 开 发 的还 原设 备 。 是
2 12 燃 料 . .
・5 ・
Arx是 M irx 的 一 种 改 进 形 式 , 取 e de 它
目前 使 用 最 广 泛 的 是 天 然 气 , 用 天 然 使
消 了天 然 气 的 重 整 炉 , 天 然 气 部 分 氧 化 后 将 入炉 , 炉 内 热 海 绵 铁 催 化 裂 解 【 。HYL一 靠 3 J Ⅲ也 在 尝试 采 取 这 种 工 艺 , 消 重 整 炉 【J 取 4。
之一 。
生产 工 艺 主 要 集 中 在 竖 炉 气 基 还 原 的
Mirx HYLⅢ 、 de 、 HYLI三 种 工 艺 , 原 块 状 还
矿 石 , 图 2所 示 ; 如 回转 窑 S / R 工 艺 占有 L N
一
1 世 界 直 接 还 原 铁 生 产 简 况
定 比例 ; 外 , oe 另 C rx工 艺 近 年发 展 迅 速 。
世 界 直接 还 原 铁 产 量 增 长 迅 速 , 2 0 到 05 年 , 接 还 原 铁 产 量 将 达 到 70 0万 t1 】如 直 0 _l , 2
图 1所 示 。
。
年 份
’
0 o
o 0
图 2 直 接 还 原 炼 铁 工 艺 的种 类
一 。
图 1 世 界 直 接 还 原 铁 年 产 量
典 型 的 竖炉 还 原 工 艺 有 米 德 雷 克 斯 直 接 还 原公 司 ( 户 钢铁 公 司 子公 司 ) Mir ( 神—I ( 4 、 e l 图 ) Arx l
铁矿石直接还原现状及提高质量的对策

甘 肃 冶 金GANSU METALLURGY第 43 卷第 1 期2021 年 2 月Vol.43 No.1Feb.,2021文章编号:1672-4461( 2021) 01-0030-05铁矿石直接还原现状及提高质量的对策权芳民,王明华(酒泉钢铁(集团)有限责任公司钢研院,甘肃 嘉峪关735100)摘要:通过对国内外煤基直接还原铁生产现状研究及存在问题的分析,依据传统经典铁矿石还原理论,在铁矿石碳气化直接还原技术的基础上,提出了铁矿石碳循环增氧还原技术,并通过隧道窑和回转窑两种还原设备进行试 验验证。
铁矿石煤基还原试验结果表明,该技术不仅可缩短铁矿石的还原时间,而且可提高还原产品的金属化率、降低生产能耗和碳的排放,对促进我国直接还原铁技术的发展具有重要意义。
关键词:钢铁;直接还原;技术现状;提高质量中图分类号:TF55 文献标识码:AThe Status and the Improving Quality Countermeasures ofFe Ore Direct Reduction TechnologyQUAN Fang-min , WANG Ming-hua(Steel Research Institute of Jiuquan Iron & Steel ( Group ) Co.Ltd., Jiayuguan 735100, China )Abstract : Based on the analysis of the present situation and existing problems of coal-based direct reduction iron production at home and abroad , and the traditional classical iron ore reduction theory , and the iron ore direct reduction technology ofcarbon gasification , the paper puts forward the technology of carbon cycling oxygen-increasing reduction of iron ore. The test verification is carried out by two kinds of reduction equipment , tunnel kiln and rotary kiln. The test results of coal-based re duction show that the technology can not only shorten the reduction time of iron ore , but also improve the metallization rateof reduction products , reduce production energy consumption and carbon emissions. It is of great significance to promote the development of direct reduction iron technology in China.Key Words : iron and steel ; direct reduction ; technology status ; improving quality1引言钢铁企业高炉炼铁工艺经历近200年的发展, 其技术完善程度几乎达到极致。
直接还原铁生产技术及现状

直接还原铁生产技术及现状铁生产技术的发展历史可以追溯到公元前2000年左右,最初的铁制品是通过在炭火中烧烤铁矿石来获得的。
这种烧烤技术被称为古老的冶金学,也被认为是人类历史上最早的冶金技术之一古代的铁生产技术在公元前1000年左右经历了重大的革新,这是由于铁矿石的高温还原反应被发现。
这种高温反应是通过将铁矿石与木炭或石炭混合,并在高温环境下加热来进行的。
这项技术的发现使得铁成为了当时最重要的金属之一,但其生产量仍然相对较小。
在一些古代文明中,如中国、印度等,铁的制造和使用逐渐扩大,为社会的农业、战争和工艺生产做出了重要贡献。
到了公元前300年左右,铁生产技术再次得到了改进。
在罗马时代,一种称为“减氧法”的技术被发明,这个技术将铁矿石与木炭放入特殊的炉子中,并且通过控制加热和供氧来获取较高纯度的铁。
这项技术极大地提高了铁的生产效率,使得罗马帝国在铁材料的生产和使用方面取得了巨大的进展。
这种技术的使用也标志着对铁生产的进一步工业化,奠定了现代铁产业的基础。
到了中世纪,铁生产技术进一步发展,很大程度上得益于对炼铁炉的改进。
这些改进包括提高炉子的结构、使用更多供氧装置以及改进燃烧气体的预热系统等。
这些改进使得炼铁过程更为高效,并且提高了产量和纯度。
到了18世纪,随着燃烧技术和冶金科学的进展,铁生产技术又迈上了一个新的台阶。
在这个时候,由于煤炭的大量使用,炼铁工艺发生了革命性的变化。
在这种现代炼铁法中,矿石和煤炭被放入高炉中,在高温环境下进行化学反应。
通过这个工艺,大量的铁矿石可以得到还原,得到高质量的生铁。
这种先进的炼铁法被广泛应用于欧洲的工业革命中,推动了工业化的进程。
随着时间的推移,各种现代技术和创新被应用于铁的生产过程中,这些技术包括用电解法提纯铁、高炉法等。
现代大规模铁生产以高炉和电炉为主,这些炉子能够生成高品质的铁,用于制造各种铁制品。
此外,利用再生铁和废钢再生技术也成为现代铁产业的重要组成部分,以提高资源利用效率和减少环境影响。
煤基直接还原铁生产技术的发展

一、工艺流程
Fastmelt 工艺是 Fastmet 工艺和炼铁电炉的综合。来自回 转窑的直接还原铁在炼铁电炉中熔化生产铁水。
ITmk3 工艺是在回转窑中生产粒状铁。团块在回转炉中 加热到 1450℃, 在还原和熔化之后, 炉渣在回转窑中分离。铁 水和炉渣被冷却并从回转窑中排出。
0.00 GJ
2.47 GJ
4.10 GJ
燃气
( 0 kg- CO2 ) ( 141 kg- CO2 ) ( 234 kg- CO2 )
1.54 GJ
2.95 GJ
0.00 GJ
电能
( 103 kg- CO2 ) ( 198 kg- CO2 ) ( 0 kg- CO2 )
0.00 GJ
0.07 GJ
表 8 研究 A 研究结果概括
高炉( 50 万吨 / Fastmelt 工艺( 50 ITmk3 工艺( 50
年铁水) 万吨 / 年铁水) 万吨 / 年粒状铁)
消耗
31.47GJ
14.26 GJ
14.09 GJ
煤
( 2936kg- CO2 ) ( 1330kg- CO2) ( 1314kg- CO2)
技术与装备纵横
煤基直接还原铁生产
技术的发展
□袁 文
目前, 世界炼铁生产的主流是高炉工艺, 但该工艺需要 一些原料准备设备, 如焦炉、烧结设备等, 而其会给环境带来 很大影响。气基直接还原铁如 MIDREX 工艺是高炉炼铁工艺 的替代方法之一, 然而, 该工艺受到以经济方式获得天然气 的限制。在这一背景下, 对可以使用更广泛的原料和燃料, 且 对环境更加友好的新炼铁工艺的需求日益增加。为了满足这 种 需 求 , 人 们 开 发 出 3 种 煤 基 直 接 还 原 铁 生 产 工 艺— —— Fastmet 工艺、Fastmelt 工艺和 ITmk3 工艺。采用这些工艺可以 通过粉矿和煤生产出高质量的铁, 如直接还 原 铁 、铁 水 和 粒 状铁。而且, 这 3 种工艺在能耗和环保方面可以与高炉竞争。
近几年印度钢铁行业发展的特点及影响
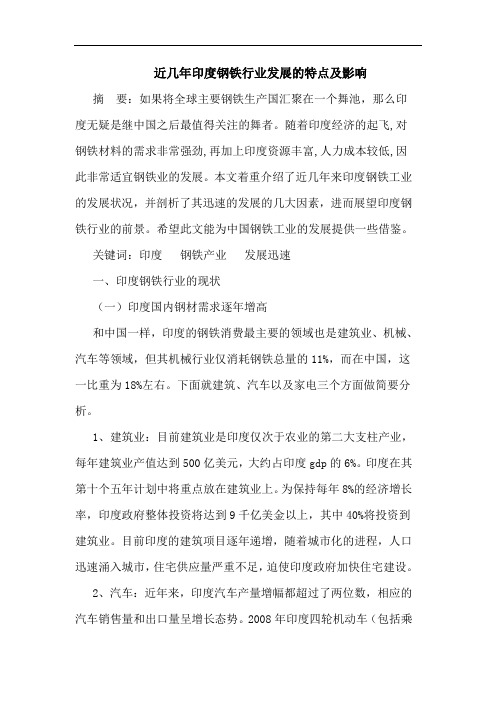
近几年印度钢铁行业发展的特点及影响摘要:如果将全球主要钢铁生产国汇聚在一个舞池,那么印度无疑是继中国之后最值得关注的舞者。
随着印度经济的起飞,对钢铁材料的需求非常强劲,再加上印度资源丰富,人力成本较低,因此非常适宜钢铁业的发展。
本文着重介绍了近几年来印度钢铁工业的发展状况,并剖析了其迅速的发展的几大因素,进而展望印度钢铁行业的前景。
希望此文能为中国钢铁工业的发展提供一些借鉴。
关键词:印度钢铁产业发展迅速一、印度钢铁行业的现状(一)印度国内钢材需求逐年增高和中国一样,印度的钢铁消费最主要的领域也是建筑业、机械、汽车等领域,但其机械行业仅消耗钢铁总量的11%,而在中国,这一比重为18%左右。
下面就建筑、汽车以及家电三个方面做简要分析。
1、建筑业:目前建筑业是印度仅次于农业的第二大支柱产业,每年建筑业产值达到500亿美元,大约占印度gdp的6%。
印度在其第十个五年计划中将重点放在建筑业上。
为保持每年8%的经济增长率,印度政府整体投资将达到9千亿美金以上,其中40%将投资到建筑业。
目前印度的建筑项目逐年递增,随着城市化的进程,人口迅速涌入城市,住宅供应量严重不足,迫使印度政府加快住宅建设。
2、汽车:近年来,印度汽车产量增幅都超过了两位数,相应的汽车销售量和出口量呈增长态势。
2008年印度四轮机动车(包括乘用车和商用车)生产量为232万辆,成为世界第八大汽车生产国。
从目前的发展趋势来看,如果印度保持现有的鼓励政策,未来10年中汽车行业每年的增长幅度将达到16%,并且将成为全球汽车的主要生产和组装基地。
3、家电:关于家电的市场需求,据印度全国应用经济研究理事会的调查显示:随着印度中产阶级数量的增长,一个大的消费品市场正在形成。
根据印度人口普查显示,城市人口占25.75%,农村人口占74.3%。
]随着城市工业化的发展,农村人口呈递减趋势,城市人口将达到30%。
并且人们已越来越注重产品的品牌、质量、外观和方便程度。
国内外转底炉的发展趋势及我国发展转底炉技术的建议
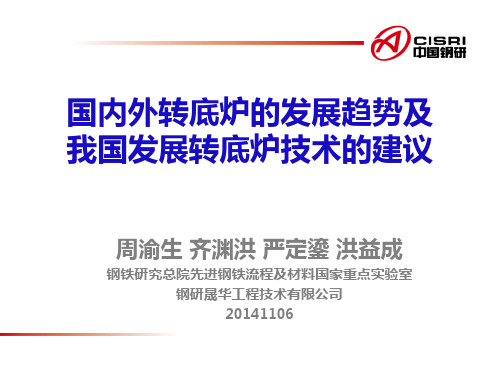
HBI水冷后使用。Fastmet煤气热值必须大于2000kcal/m3。炉内辐射传热
的火焰温度1200-1400℃,设备作业率为92%左右,Fastmet生产每t DRI 需消耗天然气2.24GJ(约63m3)、80度电及320kg煤粉,转底炉的设计
一、国内外转底炉技术的发展过程简介
FASTMET和小高炉间的燃料消耗、总能耗比较
项 目 单位 FASTMET 700m3小高炉
耗煤量
耗外供气体燃料量 耗电量 总能耗
GJ/thm
GJ/thm GJ/thm GJ/thm
11.2
4.6 2.2 18.0
22.8
1.4 24.2
一、国内外转底炉技术的发展过程简介
Kakogawa Commercial Plant Material Flow 加古川示范工厂的物料平衡
Waste to be treated (14,000ton/y ) BF Filter Cake BOF Flue Dust EAF Dust Other Waste : 5,000ton/y : 6,000ton/y : 2,000ton/y : 1,000ton/y
一、国内外转底炉技术的发展过程简介
1、转底炉直接还原工艺简介 钢铁厂每年产生大量含锌、铅高的废弃含铁粉尘,高炉不宜使用,环保限制其排 放输出(美国的委托处理费是~250$/t ,欧洲200欧元/t ,日本是2000日元/t ), 如何对其经济地回收利用是困扰冶金行业的一个难题。因此,转底炉煤基直接还原 技术应运而生。 冷固结含碳球团炉料从装料区装入转底炉炉内仅1-2层,炉料随着炉底一起转动, 不会受到挤压。先在预热区内被加热到1000℃以上,然后进入1200 ℃ -1400℃的还 原区加热10-20min。在还原区,炉料中的Fe和K、Na、Pb、Zn等氧化物陆续被含碳 球团中的碳自还原,K、Na、Pb、Zn等元素以气体的形式随烟气逸除。还原后的金 属化球团经过冷却区后被排出炉外冷却,部分再氧化金属化率降低一些。煤气燃烧 及反应生成的烟气沿着与炉料转动相反的方向流动,最后流入废气净化处理及余热 回收系统。
2023年全球粗钢、生铁、直接还原铁产量汇总与分析

2023年全球粗钢、生铁、直接还原铁产量汇总与分析粗钢产量合计18.882亿吨,同比持平根据世界钢铁协会的统计数据,2023年全球粗钢产量合计18.882亿吨,同比基本持平。
全球71个纳入该机构统计的国家和地区粗钢产量合计为18.497亿吨,同比微降0.1%。
分地区来看,欧洲、北美和南美粗钢产量同比下降,其他地区产量同比增加;分国家来看,全球前十大产钢国中,日本、德国、土耳其、巴西粗钢产量同比下降,其他国家同比增加,尤其是印度产量增幅达到11.8%。
2023年,亚洲和大洋洲合计粗钢产量为13.672亿吨,同比增长0.7%。
其中,中国粗钢产量为10.19亿吨,同比基本持平,占全球粗钢产量的份额从2022年54.2%微降至54.0%。
印度粗钢产量为1.402亿吨,同比增长11.8%,是前十大产钢国中产量增幅最大的国家。
日本粗钢产量为8700万吨,同比减少2.5%,主要由于国内钢厂熔炼设备的关闭。
JFE钢铁公司按计划于2023年9月16日关闭了位于京滨地区容积为5000立方米的2号高炉以及1号电弧炉。
日本经济产业省(METI)预计2024年一季度该国将生产2198万吨粗钢,同比增长约1.7%,这主要得益于国内汽车行业的强劲需求。
然而,日本经产省预计该国一季度钢材总需求将下降0.5%至1992万吨,建筑业和制造业(不包括汽车业)的疲软预计将拖累整体需求。
随着日本劳动法的变化,日本建筑业的疲软预计将持续到二季度。
自2024年4月1日起,日本将对建筑业工人实行每年360小时的加班时间上限,自然灾害情况下的恢复性建设工作除外。
新劳动法预计将延长施工时间,减少项目数量,从而影响钢材需求。
2023年韩国粗钢产量为6670万吨,同比增长1.3%。
东南亚国家中,越南粗钢产量同比下降5.0%至1900万吨;印度尼西亚粗钢产量估计同比增长2.8%至1600万吨;马来西亚粗钢产量估计同比增长4.1%至750万吨;泰国粗钢产量估计同比下降6.7%至496万吨。
直接还原的现状与发展
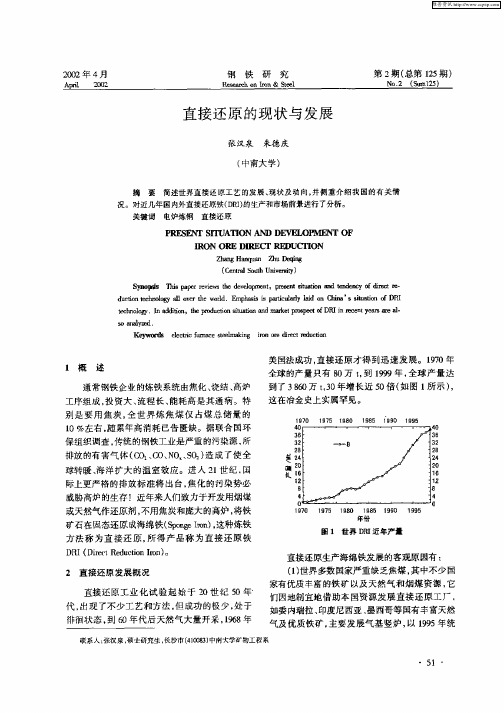
・
维普资讯
计为准产量达 22 万 a 占直接还原铁总产量的 89 , 9 2%。而南非印度新西兰有 丰富 的烟煤及优质 铁矿石 , 直接还原以煤基回转窑法为主, 虽然产量 仅为 2 4 6万 a但从近年发展趋势看 , , 大规 模的 煤基回转窑法生产 的直接还 原厂正在纷纷建立, 印度 gl t 公司建立 了生产能力为 2 万 t o sr da 2 , a的 直接还原厂 , 采用 Cr 法 : o x 南非 I o公司建立 了 e sr e 生产能力为 73 2 万 a 的直接还原厂 , 采用 S t UI N
通常钢铁企 业的炼铁系统 由焦化、 烧结、 高炉 工序组成 , 资大 、 投 流程长 、 能耗高是其通病。特 别是 要用焦炭 , 全世界炼焦 煤仅 占煤总 储量的 l O%左右 . 随累年高消耗已告匮缺 。据联合国环 保 组织 调查 , 统 的钢铁工业 是严 重 的污染 源 , 传 所 排放 的有害气体 ( O 、O N s 2造 成了使全 C 2C … O 0 )
d e o e r lg l 0 h ol E h s s prc lr ad 0lC ia’ i ao fDRI u ' nt , oy a rtew r d & o l d mpai i at ual ll l hn ss ut n o s i y t i tcr lg .h d io h rd c o tm o n ehto y o ads n.tepo u tn su lna dmak t r6 e f R nrvn e r -a- i l re o p t D Ii . t asme l p a o ee y s r 0aml
( 中南大 学 )
摘 要 简述世界直 接还 原工 艺的发 展 、 现状 及动 向 , 并侧重 介 绍我 国的有 关情 电炉炼钢
全球直接还原铁生产现状及发展趋势
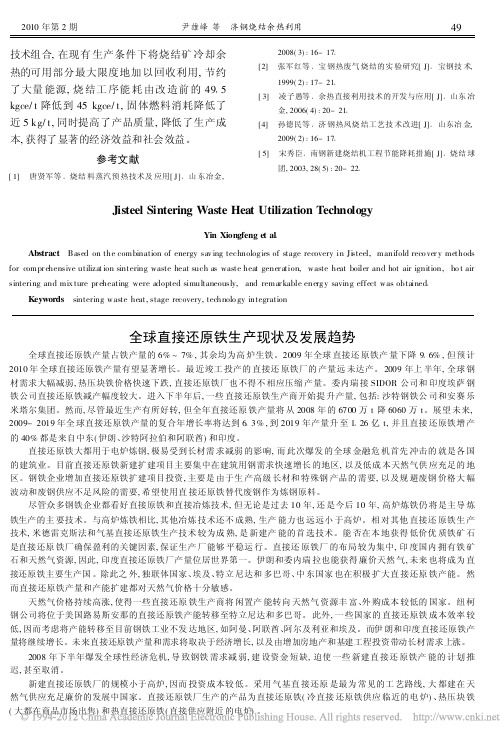
技术组合,在现有生产条件下将烧结矿冷却余热的可用部分最大限度地加以回收利用,节约了大量能源,烧结工序能耗由改造前的4915kgce/t 降低到45kgce/t,固体燃料消耗降低了近5kg/t,同时提高了产品质量,降低了生产成本,获得了显著的经济效益和社会效益。
参考文献[1] 唐贤军等1烧结料蒸汽预热技术及应用[J ]1山东冶金,2008(3):16-171[2] 张军红等1宝钢热废气烧结的实验研究[J]1宝钢技术,1999(2):17-211[3] 凌子愚等1余热直接利用技术的开发与应用[J]1山东冶金,2006(4):20-211[4] 孙德民等1济钢热风烧结工艺技术改进[J]1山东冶金,2009(2):16-171[5] 宋秀臣1南钢新建烧结机工程节能降耗措施[J]1烧结球团,2003,28(5):20-221Jisteel Sintering Waste Heat Utilization TechnologyYin Xiongfeng et al 1Abstract Based on the combination of energy sav ing technolog ies of stage recovery in Ji steel,manifold reco ver y methods for compr ehensive utilizat ion sintering waste heat such as waste heat gener ation,waste heat boiler and hot air ignition,ho t air sintering and mix ture pr eheating were adopted simultaneously,and remar kable energ y saving effect was obtained 1Keywords sintering waste heat,stage recovery,technolo gy integration全球直接还原铁生产现状及发展趋势全球直接还原铁产量占铁产量的6%~7%,其余均为高炉生铁。
煤基直接还原炼铁法的能耗与环境负荷

煤基直接还原炼铁法的能耗与环境负荷(表)据中国钢铁新闻网2007年2月13日报道:近年,世界粗钢产量随着亚洲的经济成长而持续增加。
现代炼铁法的主流是高炉法,但高炉法为了提高其效率而必须大型化,并且需要环境负荷大的烧结设备和炼焦炉。
作为替代高炉法的炼铁法,有MIDREX法所代表的气基还原铁冶炼法,但气基还原铁冶炼法需要大量的天然气,所以地区选定受到限制。
在上述背景下,对于今后的炼铁法而言,如下的期待正在日益高涨:1)降低能耗与环境负荷;2)减少投资费用与运行成本;3)适应宽泛的原料与能源。
为了回应这样的期待,神户制钢与Midrex技术公司共同开发了3种煤基直接还原炼铁法——FASTMET、FASTMELT和ITmk3。
这些方法可以用世界各地富存的铁矿粉和煤炭生产高质量的铁源,例如DRI(直接还原铁)、铁水和粒铁。
它们的能耗与环境负荷与当今普遍使用的大容量高炉法不相上下。
煤基还原冶炼法1 煤基还原铁冶炼法的定位作为煤基还原铁冶炼法的FASTMET、FASTMELT、ITmk3是使用世界上较为大量存在的粉矿石和煤炭的方法。
2 工艺流程铁矿石和作为还原剂的煤炭预先混合,并被成型为球团或压块状的团块化混合物。
这种团块化混合物供给RHF(转底炉),在RHF内被还原。
团块化混合物在RHF的炉床上铺一层或两层予以加热。
在FASTMET、FASTMELT法中,炉内加热到1250~1350℃,以直接还原铁的形式排至炉外,而在ITmk3法中则加热到1450℃,在炉内还原、熔融而以粒珠的形式排至炉外。
对FASTMET法来讲,可以做成高温还原铁和经冷却做成低温还原铁,或者以HBI(热压团块铁)的形式来利用制品还原铁。
FASTMELT法是将还原铁熔炼炉组合到FASTMET法中的方法,把RHF排出的高温的铁装入还原铁熔炼炉,边利用其显热边冶炼生产生铁。
ITmk3法则在RHF内生产与炉渣分离的粒铁,与炉渣一起排出的粒铁,用磁选机等分选机选出粒铁。
直接还原铁方式比较
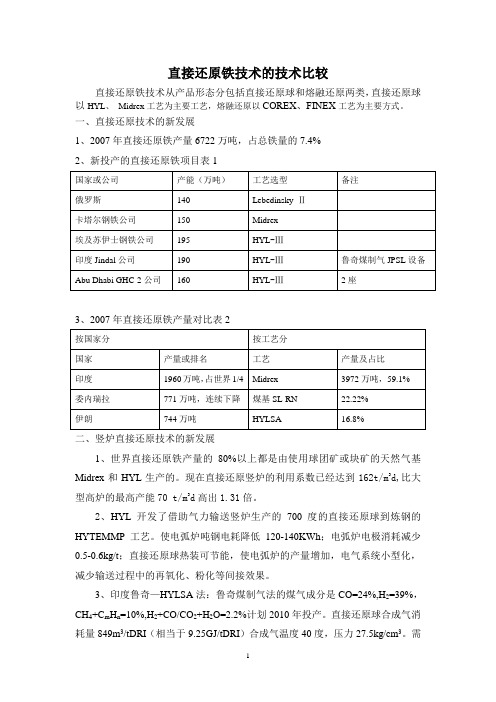
直接还原铁技术的技术比较直接还原铁技术从产品形态分包括直接还原球和熔融还原两类,直接还原球以HYL、Midrex工艺为主要工艺,熔融还原以COREX、FINEX工艺为主要方式。
一、直接还原技术的新发展1、2007年直接还原铁产量6722万吨,占总铁量的7.4%2、新投产的直接还原铁项目表13、2007年直接还原铁产量对比表2二、竖炉直接还原技术的新发展1、世界直接还原铁产量的80%以上都是由使用球团矿或块矿的天然气基Midrex和HYL生产的。
现在直接还原竖炉的利用系数已经达到162t/m3d,比大型高炉的最高产能70 t/m3d高出1.31倍。
2、HYL开发了借助气力输送竖炉生产的700度的直接还原球到炼钢的HYTEMMP工艺。
使电弧炉吨钢电耗降低120-140KWh;电弧炉电极消耗减少0.5-0.6kg/t;直接还原球热装可节能,使电弧炉的产量增加,电气系统小型化,减少输送过程中的再氧化、粉化等间接效果。
3、印度鲁奇—HYLSA法:鲁奇煤制气法的煤气成分是CO=24%,H2=39%,CH4+C m H n=10%,H2+CO/CO2+H2O=2.2%计划2010年投产。
直接还原球合成气消耗量849m3/tDRI(相当于9.25GJ/tDRI)合成气温度40度,压力27.5kg/cm3。
需要使用块煤或型煤。
鲁奇炉现在已发展到Mar kⅤ型,炉径5.0米,每台产气量10万m3/h,,可满足90万吨竖炉生产。
三、熔融还原炼铁工艺的发展1、现有主要炼铁方法的生产率指标比较表3:2、高炉、COREX、FINEX等技术的生铁质量对比表4:3、COREX技术的缺点:a、直接使用粉煤、粉矿的比例不能高于15%,必须使用块矿原料为主。
b、对块矿的理化性能有很高的要求,提高了原料成本,使铁水成本上升。
c、在炉体中部的高温区使用了很多排料布料的活动部件,使设备的维修成本及热损失增加,设备利用率降低。
d、要依赖稳定的焦床来保护炉缸,冶金焦比例高于13%。
气基竖炉直接还原炼铁简介

气基竖炉直接还原炼铁简介XX热能技术有限公司(公章)二零零七年八月八日一、总论1.1 项目背景及项目概况项目起源于焦煤冶金的固有缺陷、优质钢市场需求强劲、废钢严重短缺以及我国天然气资源不足的现实。
自从1735年英国人亚·德尔比发明了煤炭炼焦的方法,采用焦炭的冶炼方法(如高炉)已经取得巨大进步,达到了空前完善的程度,提供的金属材料品种齐全、质量优良、数量巨大,为人类物质文明和社会进步做出了巨大贡献。
然而,随着全球环境和资源压力的日益增大,传统工艺的弊端日益突出,体现在:严重依赖于焦煤;冶金反应重复进行;优质钢生产严重受限;对复杂的多金属矿处理显得无能为力;工厂生产规模大、工艺环节多、需要巨额投资;焦化、烧结、高炉等铁前系统产生的大量烟气、粉尘及水污染;焦化、烧结、高炉等铁前系统的流程长、工艺复杂,导致热效率低,能源浪费严重等。
近年来,随着我国钢铁产量逐年攀升,每年焦煤开采量至少为47425万吨。
按煤炭详查资源总量估计,2070年以后我国的焦煤资源将面临枯竭,传统的焦煤冶金工艺将无法进行正常生产。
与此相反,大量的非焦煤资源在冶炼工艺中却无法得到充分利用,因此开发和采用非焦煤炼铁工艺已迫在眉睫。
非焦煤炼铁工艺是指不使用焦炭进行炼铁生产的各种工艺方法。
按工艺特征、产品类型及用途,可分为直接还原法和熔融还原法两大类别。
直接还原法(Direct Reduction)是指“以气体燃料、液体燃料或非焦煤为能源和还原剂,在天然矿石(粉)或人造团快呈固态的软化温度以下进行还原获得金属的方法”。
熔融还原(Smelting Reduction)则“以非焦煤为能源和还原剂,在高温熔融状态下进行金属氧化物的还原,得到含碳的液态金属”。
与直接还原的不同之处是,熔融还原的发展目标只是探索和推广用煤炭代替焦炭的冶炼方法,其产品还是与传统冶炼工艺一样的液态产品,如铁水。
目前,全世界工业规模的直接还原法已有十几种,而大多数熔融还原工艺还处于研发阶段,已商业化的只有COREX。
直接还原炼铁技术的最新进展doc

直接还原炼铁技术的最新进展作者: 胡俊鸽,吴美庆,毛艳丽, 钢铁研究摘要撰写人 TsingHua出版日期: 2006年4月30日直接还原铁能够作为电炉、高炉和转炉的炉料。
DRI代替优质废钢更适合于生产对氮和有害元素有严格要求的钢种,如用于石油套管、钢丝绳、电缆线等的钢种。
最近几年,由于钢铁市场升温,废钢资源呈现世界性紧缺。
2003年,我国钢铁企业生产回收的废钢铁和非生产回收废钢铁合计为1502万t;而全年炼钢消耗废钢与辅助炼钢消耗废钢之和为4 750万t。
显然,国内的废钢缺口专门大。
以后几年,随着国际市场废钢资源的欠缺,世界对废钢的需求量将不断增加。
现今,在废钢资源全世界性紧缺、国际市场价钱几回上扬的情形下,关于我国来说,寻觅废钢替代品已迫在眉捷。
直接还原铁和热压块铁是最好的废钢替代品。
1直接还原炼铁技术进展状况2003年世界直接还原铁总量为4900万t。
比2002年增加了10%,不同工艺所生产直接还原铁所占份额如下:Midrex 为%,HyLⅢ为%,HyL Ⅰ为%,Finmet为%,其他气基为%,煤基为%。
直接还原工艺依照还原剂不同可分为气基和煤基。
气基直接还原工艺中,竖炉Midrex、Arex(Midrex改良型)和HyL Ⅲ工艺、反映罐法Hy LⅠ、流化床法Fior和Finmet工艺,都已取得了工业应用,流化床法Fior、Cir cored和碳化铁法在工业上应用不久就停产了。
煤基直接还原法中,取得工业应用的有回转窑法和转底炉法(Inmet-co、Fastmet、Sidcomet、DRylron),新开发的多层转底炉Primus工艺已于2003年2月投产。
气基直接还原工艺气基还原工艺可分为利用球团矿或块矿的工艺和利用铁矿粉的工艺。
各类气基直接还原铁工艺进展状况如表1所示。
表1各类气基直接还原铁工艺进展状况工艺装备工艺特点所用原料目前状况研究进展F ior(委内瑞拉)4个流化床反映器生产能耗高于竖炉Midrex和HyLⅢ铁矿粉Side tur厂于1976年投产,1985年开始,年产量达到35万t~41万t。
- 1、下载文档前请自行甄别文档内容的完整性,平台不提供额外的编辑、内容补充、找答案等附加服务。
- 2、"仅部分预览"的文档,不可在线预览部分如存在完整性等问题,可反馈申请退款(可完整预览的文档不适用该条件!)。
- 3、如文档侵犯您的权益,请联系客服反馈,我们会尽快为您处理(人工客服工作时间:9:00-18:30)。
印度煤基直接还原铁生产建设近况
1.概述
1980年以来,印度是世界上建设煤基直接还原铁生产装置最多的国家,据不完全统计,已建有生产直接还原铁用回转窑25座,年产能力约192万t,已建设施一般都已正常稳定生产。
采用的工艺有SL/RN(德)、ACCAR(美)、KRUPP-CODIR(德)、SIIL(印)、TDR(印)、OSIL(印)和JINDAL(印)七种,详见表1,但均采用回转窑。
印度第一台煤基直接还原铁装置是在联合国工发组织资助下建成的,于1980年投产。
已建回转窑最大直径为5.0m,最长为80m,最大年产能力为15万t。
在印度第一个采用煤基直接还原铁-电炉(DRI-EAF)流程联合企业是SUNFLAG钢铁公司,该公司除直接还原铁设备外还建有50t电炉、三流方坯连铸机和棒材连轧机,年产值直接还原铁(以下简称DRI)15万t,钢20万t。
表1印度煤基直接还原铁装置生产建设情况表 (大小33,792k)
印度发展煤基直接还原法有三个原因:
(1)印度拥有丰富的富铁矿和非炼焦煤资源,焦煤很少,目前已探明的天然气资源也不多。
(2)印度由于年产钢总量和社会钢积累总量小,国内废钢资源短缺,需要DRI作为电炉原料。
(3)以印度条件为依据,对比高炉-转炉流程和直接还原-电炉流程,在吨钢建设投资和吨钢生产成本方面,后者均略占优势。
与气基直接还原法相比,煤基直接还原法(回转窑型)存在着生产规模小、劳动生产率低、产品质量较差等缺点,为此在90年代中期以后,印度也重点发展气基直接还原法。
在不长时期内,气基直接还原铁年生产能力(用天然气和COREX炉气)达到400万t,远超过煤基法生产能力总和。
2. 生产工艺
印度直接还原铁公司采用工艺形式最多的是德国鲁奇公司开发的SL/ RN法,SIIL公司(即印度海绵铁公司)在引进SL/ RN生产线实践的基础上开发出的工艺方法,与SL/ RN法接近,这两种工艺合计数为16座。
采用德国KRUPP-CODIR法建设的直接还原铁设备共有三台,另塔塔公司开发的TDR工艺和该法接近,这两种工艺合计数为5座。
采用美国ACCAR法建设的有一座。
ACCAR法的特点是部分使用煤(一次燃料),另从炉头喷入天然气或轻柴油(二次燃料),优点是单位生产能力增加,并提高产品质量、金属化率和控制DRI的含碳量;缺点是部分用较贵的燃料(天然气或油),印度奥里萨(ORISSA)公司在自己生产实践的基础上开发了OSIL法,用此法新建了一座直接还原铁装置。
印度JINDAL公司自己建设了中试工厂开发了JINDAL工艺,于1991年在本公司投产了一座年产能力为10万t的DRI装置。
1993年为MONNET伊斯帕特公司提供了一座JINDAL法DRI装置,年产能力亦为10万t。
3. 印度煤基直接还原铁生产经验
(1)印度各煤基直接还原铁厂一般均采用印度富铁矿为原料,不用球团矿。
入炉铁矿粒度为6~20mm(炉料中小于6mm占5%以下),要求煤的灰分熔点1200℃以上,反应性大于100Co/克碳/分,由于用国产原燃料,因而成本较低。
加之印度在引进国外工艺设备基础上很快开发了印度自己的工艺并由国内提供设备,因而大幅度降低建设投资以及吨铁财务生产成本。
(2)无论采用何种工艺,煤基直接还原法在采用不同原燃料时,其操作参数也要相应变更,所以在决定采用某种原燃料后,必须对该种原燃料作必要的试验室试验,以获得该种原燃料所需采用的操作参数。
在印度海绵铁公司内,即使在年产3万t能力时,也在联合国工发组织资助下建有原燃料试验的各种设备,包括原燃料化学成分分析、高温性能、铁矿石还原性能、高温碎裂情况、煤灰分的熔点、煤的反应性能等。
印度设计DRI厂的著名设计咨询公司——Dastur公司也专门设有试验室为各用户提供原燃料试验数据。
我们认为这一点很重要。
印度煤基直接还原铁生产所以稳定,每炉炉役达130~140天,是他们充分掌握原燃料性能并据此正确确定操作参数的结果。
(3)窑炉温度的精确测量和控制,对避免结瘤和保持高质量海绵铁的连续生产至关重要。
如奥里萨海绵铁公司把窑炉按不同温度分成12个温度控制段,分段进行温度测量、控制,效果甚好。
(4)注意综合利用回转窑烟气余热,已在五个煤基直接还原铁公司中,利用余热建有7500kW发电机组3台,12000kW发电机组2台,15000kW发电机组1台。
(王定武)。