直接还原铁生产工艺
新一代Midrex钢铁生产工艺
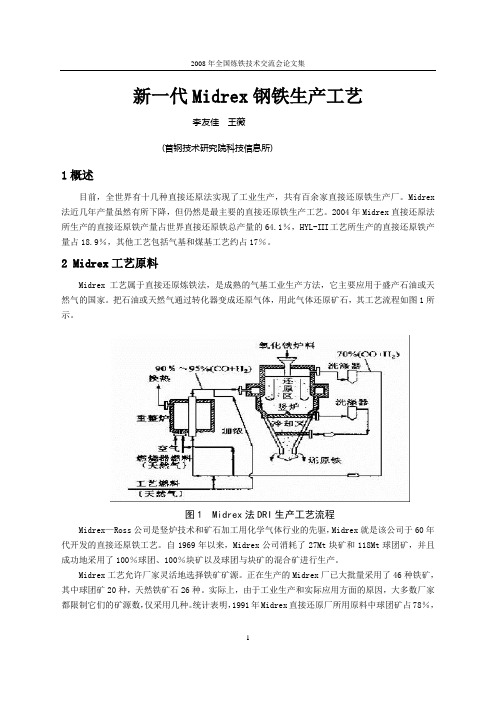
新一代Midrex钢铁生产工艺李友佳王薇(首钢技术研究院科技信息所)1概述目前,全世界有十几种直接还原法实现了工业生产,共有百余家直接还原铁生产厂。
Midrex 法近几年产量虽然有所下降,但仍然是最主要的直接还原铁生产工艺。
2004年Midrex直接还原法所生产的直接还原铁产量占世界直接还原铁总产量的64.1%,HYL-III工艺所生产的直接还原铁产量占18.9%,其他工艺包括气基和煤基工艺约占17%。
2 Midrex工艺原料Midrex工艺属于直接还原炼铁法,是成熟的气基工业生产方法,它主要应用于盛产石油或天然气的国家。
把石油或天然气通过转化器变成还原气体,用此气体还原矿石,其工艺流程如图1所示。
图1 Midrex法DRI生产工艺流程Midrex—Ross公司是竖炉技术和矿石加工用化学气体行业的先驱,Midrex就是该公司于60年代开发的直接还原铁工艺。
自1969年以来,Midrex公司消耗了27Mt块矿和118Mt球团矿,并且成功地采用了100%球团、100%块矿以及球团与块矿的混合矿进行生产。
Midrex工艺允许厂家灵活地选择铁矿矿源。
正在生产的Midrex厂已大批量采用了46种铁矿,其中球团矿20种,天然铁矿石26种。
实际上,由于工业生产和实际应用方面的原因,大多数厂家都限制它们的矿源数,仅采用几种。
统计表明,1991年Midrex直接还原厂所用原料中球团矿占78%,而块矿只占20%。
另外,对适合于Midrex直接还原工艺及其炼钢的铁氧化物原料的选择还应从化学和物理特性以及还原特性几方面加以考虑。
铁氧化物原料化学成分的重要性通常取决于最终使用者而非直接还原工艺。
随着三十多年来直接还原技术的进步,铁氧化物原料的化学成分对Midrex工艺来说已变得不太重要了。
然而化学成分对其后的DRI炼钢工艺却非常重要。
在直接还原工艺中,就原料而论,唯一的主要化学变化是从铁氧化物中脱氧,没有熔炼或精炼发生,基本上氧化铁原料中的所有杂质和脉石都存留在还原产品中。
神户制钢煤基直接还原铁生产工艺(下).
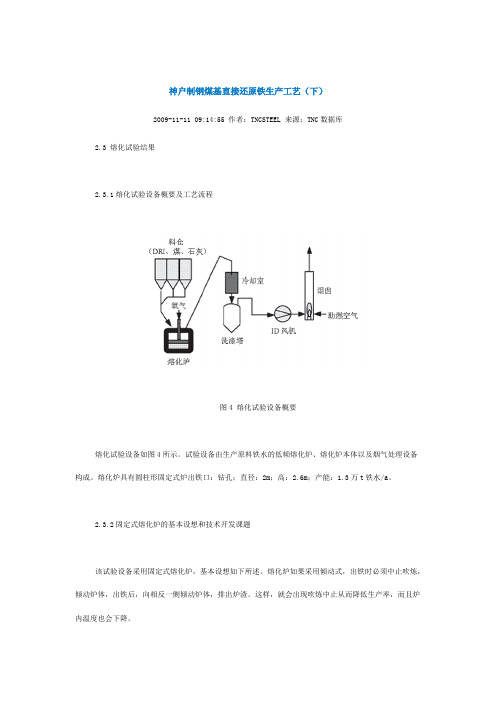
神户制钢煤基直接还原铁生产工艺(下)2009-11-11 09:14:55 作者:TNCSTEEL 来源:TNC数据库2.3 熔化试验结果2.3.1熔化试验设备概要及工艺流程图4 熔化试验设备概要熔化试验设备如图4所示。
试验设备由生产原料铁水的低频熔化炉、熔化炉本体以及烟气处理设备构成。
熔化炉具有圆柱形固定式炉出铁口:钻孔;直径:2m;高:2.6m;产能:1.3万t铁水/a。
2.3.2固定式熔化炉的基本设想和技术开发课题该试验设备采用固定式熔化炉,基本设想如下所述。
熔化炉如果采用倾动式,出铁时必须中止吹炼,倾动炉体,出铁后,向相反一侧倾动炉体,排出炉渣。
这样,就会出现吹炼中止从而降低生产率,而且炉内温度也会下降。
而采用固定式炉,出铁时不需倾动炉体,继续吹氧和熔化直接还原铁,可定时排出铁水和熔渣,出铁渣时只是带出铁渣显热,炉内温度没有下降,而且生产率也基本没有降低,可以连续作业。
如将RHF生产的还原铁高温状态装入炉内,则可进一步提高生产率。
2.3.3熔化试验条件及操作参数熔化试验为一周几次的间歇运转,将低频炉约1450℃的原料铁水(6t)装入熔化炉后,开始第一次吹炼。
吹氧使铁水中碳燃烧,充分运用炉内二次燃烧升温,铁水温度达到规定值后,从中间出铁口排出约2t 的铁水和熔渣。
然后,在残留铁水(约4t)和少量渣的状态,反复多次进行还原铁(DRI)熔化和出铁渣操作,试验结束时从残铁排出口排出铁渣。
本试验所用的原料铁水成分和DRI成分分别示于表4和表5。
装入熔化炉的碳材使用钢铁厂产生的小粒焦粉(固定[C]=85%)。
表4 原料铁水主要成分 %表5 直接还原铁(DRI)主要化学成分%2.3.4熔化试验结果(1)吹炼中铁水温度、[C]的变化将原料铁水装入炉内时,铁水温度大约降到1350℃,但第一次吹炼升温到1500℃左右出铁。
第二次吹炼后,铁水温度基本保持不变,反复进行直接还原铁的熔化和出铁渣作业。
吹炼中控制炉渣的形成,[C]含量基本保持在饱和状态。
无烟煤生产还原铁的工艺流程

无烟煤生产还原铁的工艺流程下载温馨提示:该文档是我店铺精心编制而成,希望大家下载以后,能够帮助大家解决实际的问题。
文档下载后可定制随意修改,请根据实际需要进行相应的调整和使用,谢谢!并且,本店铺为大家提供各种各样类型的实用资料,如教育随笔、日记赏析、句子摘抄、古诗大全、经典美文、话题作文、工作总结、词语解析、文案摘录、其他资料等等,如想了解不同资料格式和写法,敬请关注!Download tips: This document is carefully compiled by theeditor. I hope that after you download them,they can help yousolve practical problems. The document can be customized andmodified after downloading,please adjust and use it according toactual needs, thank you!In addition, our shop provides you with various types ofpractical materials,such as educational essays, diaryappreciation,sentence excerpts,ancient poems,classicarticles,topic composition,work summary,word parsing,copy excerpts,other materials and so on,want to know different data formats andwriting methods,please pay attention!无烟煤生产还原铁的工艺流程主要包括煤气化、煤气净化、还原铁生产等环节。
直接还原炼铁

直接还原炼铁在低于矿石熔化温度下,通过固态还原,把铁矿石炼制成铁的工艺过程。
这种铁保留了失氧时形成的大量微气孔,在显微镜下观察形似海绵,所以也称为海绵铁;用球团矿制成的海绵铁也称为金属化球团。
直接还原铁的特点是碳、硅含量低,成分类似钢,实际上也代替废钢使用于炼钢。
习惯上把铁矿石在高炉中先还原冶炼成含碳高的生铁。
而后在炼钢炉内氧化,降低含碳量并精炼成钢,这项传统工艺,称作间接炼钢方法;而把炼制海绵铁的工艺称作直接还原法,或称直接炼铁(钢)法。
直接还原原理与早期的炼铁法(见块炼铁)基本相同。
高炉法取代原始炼铁法后,生产效率大幅度提高,是钢铁冶金技术的重大进步。
但随着钢铁工业大规模发展,适合高炉使用的冶金焦的供应日趋紧张。
为了摆脱冶金焦的羁绊,18世纪末提出了直接还原法的设想。
20世纪60年代,直接还原法得到发展,其原因是:①50~70年代,石油及天然气大量开发,为发展直接还原法提供了方便的能源。
②电炉炼钢迅速发展,海绵铁能代替供应紧缺的优质废钢,用作电炉原料,开辟了海绵铁的广阔市场。
③选矿技术提高,能提供高品位精矿,使脉石含量可以降得很低,简化了直接还原工艺。
1980年全世界直接还原炼铁生产量为713万吨,占全世界生铁产量的1.4%。
最大的直接还原工厂规模达到年产百万吨,在钢铁工业中已占有一定的位置。
海绵铁中能氧化发热的元素如硅、碳、锰的含量很少,不能用于转炉炼钢,但适用于电弧炉炼钢。
这样就形成一个直接还原炉-电炉的钢铁生产新流程。
经过电炉内的简单熔化过程,从海绵铁中分离出少量脉石,就炼成了钢,免除了氧化、精炼及脱氧操作,使新流程具有作业程序少和能耗低的优点。
其缺点是:①成熟的直接还原法需用天然气作能源,而用煤炭作能源的直接还原法尚不完善,70年代后期,石油供应不足,天然气短缺,都限制了直接还原法的发展。
②直接还原炉-电炉炼钢流程,生产一吨钢的电耗不少于600千瓦·时,不适于电力短缺地区使用。
直接还原铁生产工艺

直接还原铁生产工艺铁生产工艺是指将铁矿石加工成熔融的铁的工艺过程。
这个过程涉及到多个步骤,包括矿石的破碎、研磨、还原和熔炼。
在本文中,我们将详细介绍铁的生产工艺及其各个步骤。
首先是矿石的破碎和研磨。
铁矿石通常是硬质的岩石,包含铁和一些非铁物质。
为了将铁从矿石中分离出来,首先需要将矿石破碎成较小的颗粒。
这通常通过使用破碎机完成,破碎后的矿石通常有不同大小的块状或颗粒状。
接下来是还原步骤。
还原是将氧化铁还原为金属铁的过程。
铁的主要矿石是赤铁矿,其中主要包含氧化铁。
为了将氧化铁还原为金属铁,需要将矿石暴露在高温和还原性气氛中。
常用的还原剂包括焦炭和煤炭。
在高温下,焦炭中的碳会与氧化铁反应,生成一氧化碳和金属铁。
这个反应通常在高炉中进行。
高炉是一个巨大的建筑,具有特定的构造和设计,以便在高温和高压下进行还原反应。
还原反应会生成熔融的铁和一些其他非铁杂质,如硅、锰、磷等。
这个熔融的铁被称为铁水。
铁水通常含有3-4%的碳,这是因为焦炭中的碳在还原过程中溶解到铁中。
然而,为了生产不同类型的铁和钢,通常需要调整铁水中的碳含量。
这可以通过转炉等其他工艺来完成。
最后是熔炼步骤。
熔炼是将铁水转化为不同类型的铁和钢的过程。
熔炼通常包括炉外和炉内两个阶段。
在炉外阶段,铁水被倒入钢包中,并添加一些合金元素和其他调整剂,以调整铁水的化学成分。
在这个阶段,还会进行一些化学分析和实验室测试,以确保铁水达到所需的质量标准。
在炉内阶段,钢包被转移到炉内,并加热到高温。
在这个温度下,铁水会进一步净化和冶炼,以去除残留的杂质。
这通常通过吹氧的过程来完成,即将氧气从底部吹入钢包中。
氧气与铁中的碳和其他杂质反应,生成气体,从而进一步提高铁的纯度。
最后,经过一系列的处理和冷却过程,铁水被铸造成不同形状的铁和钢产品,例如铸铁管、钢板、钢筋等。
总的来说,铁的生产工艺涉及多个步骤,包括矿石的破碎和研磨、还原和熔炼。
这些步骤需要高温、特定的还原剂和合金元素等条件。
复杂难选铁矿中直接还原技术简介

书山有路勤为径,学海无涯苦作舟复杂难选铁矿中直接还原技术简介2.1 直接还原技术简介直接还原是指铁矿石或含铁氧化物在低于熔化温度之下还原成固态金属产品的炼铁过程,其所得产品称为直接还原铁(DRI)。
直接还原铁具有成分稳定、有害杂质低、粒度均匀等多种优点,是最好的废钢替代品,也是冶炼优质钢和特种钢的必备原材料。
目前,世界上已应用和正在试验研究的直接还原工艺有40 多种,而应用于大规模生产的有20 多种。
直接还原工艺按其主体能源的不同,可分为气基直接还原和煤基直接还原。
国外直接还原铁生产主要以气基的竖炉直接还原工艺为主,而我国天然气资源相对缺乏,且优先用于石油化工和民用,使气基直接还原铁工艺受到限制但我国煤炭资源(尤其是非焦煤)却很丰富,这种能源结构决定了发展煤基直接还原铁工艺是我国的首选工艺。
煤基直接还原铁的工艺主要有回转窑、转底炉等技术。
回转窑曾是发展直接还原铁的主导工艺,但因其存在生产效率低、能耗髙、容易出现结圈结瘤等缺陷,严重制约了自身的发展。
转底炉(RHF)直接还原技术,是由轧钢用的环形加热炉演变而来的炼铁新工艺,最早是用来处理钢铁工业产生的含铁、含锌粉尘及废弃物,近10 余年移椬为冶炼设备,进而演变成为生产海绵铁(DRI)的设备。
转底炉的代表工艺有Fastmet, ITmk3、COMET 等。
其中mnk3 工艺被称为第三代炼铁法,该工艺是由日本神户制钢公司与美国米德兰公司联合开发出的煤基直接还原技术。
ITmk3 工艺流程为:直接将球团矿或者粉矿均匀地铺在炉底上,随着炉底的旋转,炉料依次经过预热段、还原段、控制还原段,通过控制转底炉使DRI 还原时轻度熔化,生成粒铁,同时脉石也熔化,形成渣铁初步分离,反应完毕后卸人砌有耐火材料的热运输罐内或快速冷却,整个过程需要10 ~50mino 如图1 所示。
电炉dri生产工艺

电炉dri生产工艺
电炉DRI(直接还原铁)生产工艺是一种利用天然气或其他气体作为还原剂,将铁矿石直接还原成铁的工艺。
这种工艺通常包括以下几个主要步骤:
1. 铁矿石预处理,首先,铁矿石需要经过破碎和磨矿等预处理工序,以便使其颗粒大小适合于电炉内的还原反应。
2. 还原反应,在电炉中,将经过预处理的铁矿石与天然气或其他气体一起注入,通过高温还原反应,将铁矿石中的氧化铁还原成金属铁。
这一步骤需要严格控制温度、气氛和还原剂的流量,以确保还原反应能够高效进行。
3. 熔炼和收集,在还原反应完成后,得到的金属铁与其他杂质和残余物质一起熔化,并通过特定的工艺进行分离和收集,得到高纯度的直接还原铁产品。
4. 尾气处理,在电炉DRI生产工艺中,还需要对产生的尾气进行处理,以减少对环境的影响。
尾气处理通常包括除尘、脱硫和脱氮等步骤,以确保排放符合环保标准。
总的来说,电炉DRI生产工艺是一项复杂的工程系统,涉及材料科学、化学工程、热力学等多个领域的知识,需要严格控制各个环节,以确保生产出高质量的直接还原铁产品。
同时,随着环保意识的提高,工艺中的尾气处理也变得越来越重要。
希望这些信息能够对你有所帮助。
直接还原铁

直接还原铁直按还原铁和熔融还原铁的生产直接还原铁和熔融还原铁的冶炼统称为非高炉法炼铁。
(一)直接还原法生产生铁直接还原法是指在低于熔化温度之下将铁矿石还原成海绵铁的炼铁生产过程,其产品为直接还原铁(即DRI),也称海绵铁。
该产品未经熔化,仍保持矿石外形,由于还原失氧形成大量气孔,在显微镜下观察团形似海绵而得名。
海绵铁的特点是含碳低(<1%),并保存了矿石中的脉石。
这些特性使其不宜大规模用于转炉炼钢,只适于代替废钢作为电炉炼钢的原料。
直接还原法分气基法和煤基法两大类。
前者是用天然气经裂化产出H2和CO气体,作为还原剂,在竖炉、罐式炉或流化床内将铁矿石中的氧化铁还原成海绵铁。
主要有Midrex法、HYL Ⅲ法、FIOR法等。
后者是用煤作还原剂,在回转窑、隧道窑等设备内将铁矿石中的氧化铁还原。
主要有FASMET法等。
直接还原法的优点有:(1)流程短,直接还原铁加电炉炼钢;(2)不用焦炭,不受炼焦煤短缺的影响;(3)污染少,取消了焦炉、烧结等工序;(4)海绵铁中硫、磷等有害杂质与有色金属含量低,有利于电炉冶炼优质钢种。
直接还原法的缺点有:(1)对原料要求较高:气基要有天然气;煤基要用灰熔点高、反应性好的煤;(2)海绵铁的价格一般比废钢要高。
直接还原法已有上百年的发展历史,但直到20世纪60年代才获得较大突破。
进入20世纪90年代,其生产工艺日臻成熟并获得长足发展。
其主要原因是:(1)天然气的大量开发利用,特别是高效率天然气转化法的采用,提供了适用的还原煤气,使直接还原法获得了来源丰富、价格相对便宜的新能源。
(2)电炉炼钢迅速发展以及冶炼多种优质钢的需要,大大扩展了对海绵铁的需求。
(3)选矿技术提高,可提供大量高品位精矿,矿石中的脉石量降低到还原冶炼过程中不需加以脱除的程度,从而简化了直接还原技术。
当前世界上直接还原铁量的90%以上是采用气基法生产的。
我国天然气主要供应化工和民用,不可能大量用于钢铁工业。
隧道窑装法生产直接还原铁工艺介绍

隧道窑装法生产直接还原铁工艺介绍隧道窑罐装法生产直接还原铁(海绵铁)是瑞典人在1911年首先用于工业生产直接还原铁(海绵铁)的方法,经过多年的技术发展,已经是一种有效的生产直接还原铁(海绵铁)的方法。
一九九二年河北东瀛有限责任公司在此基础上进行了大量的技术改进和创新,研制开发了新型的隧道窑直接还原铁(海绵铁)生产法。
开创了在我国使用隧道窑生产海绵铁的新纪元,在此后经过不断的改进和完善,形成了无论从投资规模的大与小、无论自动化程度的高与低的系列海绵铁生产工艺,它能满足各种环境、各个区域、各种投资人群的要求,河北东瀛有限责任公司所研制开发的各种工艺无论从投资比例还是投资效益、无论从产品成本还是对原料要求、无论从产品质量还是工艺的成熟性、设备运行的可靠性、稳定性,无论从节能还是环保在我国都是唯一可信赖的、也是遥遥领先的。
它是将精矿粉、煤粉、石灰石粉,按照一定的比例和装料方法,分别装入还原罐中,然后把罐放在罐车上,推入条形隧道窑中或把罐直接放到环形轮窑中,料罐经预热1150℃加热焙烧和冷却之后,使精矿粉还原,得到直接还原铁(海绵铁)的方法。
使用隧道窑直接还原铁(海绵铁)生产工艺已有几十条生产线建成投产。
当精矿粉含铁67%以上时,此法生产的直接还原铁(海绵铁)实物分析结果是:C≥0.04%, S<0.01%, P<0.02%, SiO2<3%, MFe≥86%, TFe≥92% M≥94%。
1.隧道窑生产工艺的特点:(1)原料、还原剂、燃料容易解决此方法所用的原料是精矿粉或品位≥60%的赤铁矿或褐铁矿,这远比富铁块矿好解决,同时,生产中不需要把精矿粉先变成氧化球团,生产费用也低,而且生产中不添加任何粘结剂,这样避免了原料的污染;还原剂是普通无烟煤粉或焦碳末,煤中灰分熔点也不要求很高;供热的燃料是普通动力煤或煤粉,有多余高炉煤气、焦炉煤气、转炉煤气、混和煤气、石油气的地方也可用这些气体做热源,还可使用发生炉煤气或重油作为热源,使用范围十分广阔。
钢厂各个车间生产工艺(图片)
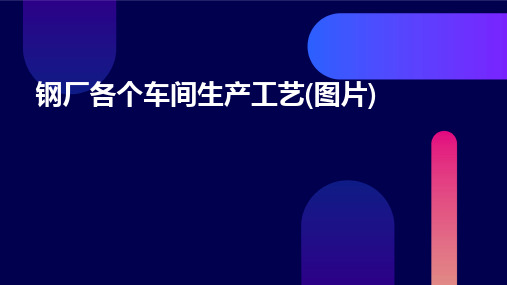
转炉炼钢工艺
总结词
环保、高效、低成本
详细描述
转炉炼钢工艺是一种利用氧气和铁水反应来生产钢的工艺。它具有环保、高效和低成本等优点,是目 前应用最广泛的炼钢工艺之一。转炉炼钢工艺流程包括铁水预处理、转炉炼钢和精炼等环节,最终得 到不同品质和规格的钢材。
电弧炉炼钢工艺
总结词
灵活性、小规模、高合金钢
详细描述
直接还原铁工艺
总结词
直接还原铁工艺是一种将铁矿石直接还原成海绵铁的工艺,通常在较低温度下 进行,以避免产生铁水。
详细描述
直接还原铁工艺通常使用天然气或煤作为还原剂,将铁矿石在较低温度下进行 还原,得到海绵铁。该工艺具有能耗低、污染小等优点,但同时也存在生产效 率较低、成本较高等问题。
熔融还原铁工艺
THANK YOU
球团车间生产工艺
总结词
球团是将细磨物料通过造球机制成球形团块,再经过 高温焙烧,使物料发生固结的工艺过程。
详细描述
球团车间的主要设备包括造球机、焙烧设备、冷却设 备等。造球机用于将细磨物料制成一定粒度和形状的 球形团块,焙烧设备用于提供高温环境,使球团内部 的矿物发生固结。冷却设备用于将焙烧后的球团快速 冷却,以避免其内部的晶体结构发生改变。
炭,以便后续的运输和使用。
烧结车间生产工艺
总结词
烧结是通过加热粉状物料,使其发生物理和化学变化, 最终形成致密块状物料的工艺过程。
详细描述
烧结车间的主要设备包括烧结机、燃烧器、除尘设施等 。烧结机是烧结过程中的核心设备,铁矿粉、溶剂、燃 料等原料在烧结机上经过点火、烧结、冷却等工序,最 终得到烧结矿。燃烧器用于提供烧结所需的热量,除尘 设施用于收集烧结过程中产生的烟尘,以减少对环境的 污染。
直接还原铁技术

直接还原铁技术直接还原铁是铁矿在固态条件下直接还原为铁,可以用来作为冶炼优质钢、特殊钢的纯净原料,也可作为铸造、铁合金、粉末冶金等工艺的含铁原料。
这种工艺是不用焦碳炼铁,原料也是使用冷压球团不用烧结矿,所以是一种优质、低耗、低污染的炼铁新工艺,也是全世界钢铁冶金的前沿技术之一。
直接还原炼铁工艺有气基法和煤基法两种,按主体设备可分为竖炉法、回转窑法、转底炉法、反应罐法、罐式炉法和流化床法等。
目前,世界上90%以上的直接还原铁产量是用气基法生产出来的。
但是天然气资源有限、价高,使生产量增长不快。
用煤作还原剂在技术上也已过关,可以用块矿,球团矿或粉矿作铁原料(如竖炉、流化床、转底炉和回转窑等)。
但是,因为要求原燃料条件高(矿石品位要大于66%,含SiO2+Al2O3杂质要小于3%,煤中灰分要低等),规模小,设备寿命低,生产成本高和某些技术问题等原因,致使直接还原铁生产在全世界没有得到迅速发展。
因此,高炉炼铁生产工艺将在较长时间内仍将占有主导地位。
1.直接还原铁的质量要求直接还原铁是电炉冶炼优质钢种的好原料,所以要求的质量要高(包括化学成份和物理性能),且希望其产品质量要均匀、稳定。
1.1 化学成份直接还原铁的含铁量应大于90%,金属化率要>90%。
含SiO2每升高1%,要多加2%的石灰,渣量增加30Kg/t,电炉多耗电18.5kwh。
所以,要求直接还原铁所用原料含铁品位要高:赤铁矿应>66.5%,磁铁矿>67.5%,脉石(SiO2+Al2O3)量<3%~5%。
直接还原铁的金属化率每提高1%,可以节约能耗8~10度电/t。
直接还原铁含C<0.3%,P<0. 03%,S<0.03%,Pb、Sn、As、Sb、Bi等有害元素是微量。
1.2 物理性能回转窑、竖炉、旋转床等工艺生产的直接还原铁是以球团矿为原料,要求粒度在5~30mm。
隧道窑工艺生产的还原铁大多数是瓦片状或棒状,长度为250~380mm,堆密度在1.7~2. 0t/m³。
直接还原炼铁演示课件

2.2 HYL-III(Energiron)法工艺
C4 H H 2 O 催 化 3剂 2H CO
炉内压力:600KPa 天然气能耗:
10~11.3t/GJ 炉料在整个炉内停留
时间:大于10h 还原区温度:
900~960℃ 金属化率:>91%
H 2 C> O 2
14
2.3 HYL-ZR法工艺
直接还原炼铁
1
一 直接还原炼铁简介
1 、定义 直接还原炼铁(Direct Reduction Iron)是一种采用
天然气、煤气、非焦煤粉作燃料和还原剂, 使用球团矿、 块矿、粉矿在在软化温度以下直接还原生产固体直接还原 铁( DRI /HBI) 的炼铁工艺技术。
2 、优点 ① 使用非焦煤,取消了炼焦和烧结等高能耗高污染工序 ② DRI/HBI 中P、S和和有色杂质(Cu、Ni、Cr、Mo、Sn等)
4
一 直接还原炼铁简介
7、世界直接还原铁生产概况 2012年,全球直接还原铁产量达到7402万吨,其中
印度位居第一,2005万吨。伊朗第二,1158万吨。
全球主要直接还原铁生产大国/MT
5
一 直接还原炼铁简介
6
二 直接还原炼铁的方法
➢ 目前世界上有十几种直接还原法实现了工业生产,包MIDREX、 HYL、转底炉、回转窑等。根据还原设备的形状和所用的还原介 质进行分类的直接还原工艺如下表(2007年的数据)所示。
➢煤基转底炉法工艺造块困难、产品含铁品位低且含硫高, 质量稳定性差,而且设备运转部件大,生产控制和运行维 护难度大。
➢流化床法,还原气体一次通过的利用率极低(约10%), 气体循环消耗的能耗高,产品还原程度不均匀,粘结失流 导致生产稳定性差等问题。
DRI ( 直接还原铁)和HBI (热压铁块)的贸易和运输

DRI ( 直接还原铁)和HBI (热压铁块)的贸易和运输DRI ( Direct Reduced Iron) “直接还原铁”是一种高品质冶金产品(97%的纯铁含量)通过矿粉,球团或矿块同天然气或煤加热化学的还原反应中得到,反应温度比铁的溶点低。
相对高品位的铁矿作为填料。
矿粉可以直接应用,不需要烧结过程。
生产1吨的DRI,大概需要1.5吨的铁矿。
(一)直接还原法生产生铁直接还原法是指在低于熔化温度之下将铁矿石还原成海绵铁的炼铁生产过程,其产品为直接还原铁(即DRI),也称海绵铁。
该产品未经熔化,仍保持矿石外形,由于还原失氧形成大量气孔,在显微镜下观察团形似海绵而得名。
海绵铁的特点是含碳低(<1%),并保存了矿石中的脉石。
这些特性使其不宜大规模用于转炉炼钢,只适于代替废钢作为电炉炼钢的原料。
直接还原法分气基法和煤基法两大类。
前者是用天然气经裂化产出H2和CO气体,作为还原剂,在竖炉、罐式炉或流化床内将铁矿石中的氧化铁还原成海绵铁。
主要有Midrex法、HYL Ⅲ法、FIOR法等。
后者是用煤作还原剂,在回转窑、隧道窑等设备内将铁矿石中的氧化铁还原。
主要有FASMET法等。
直接还原法的优点有:(1)流程短,直接还原铁加电炉炼钢;(2)不用焦炭,不受炼焦煤短缺的影响;(3)污染少,取消了焦炉、烧结等工序;(4)海绵铁中硫、磷等有害杂质与有色金属含量低,有利于电炉冶炼优质钢种。
直接还原法的缺点有:(1)对原料要求较高:气基要有天然气;煤基要用灰熔点高、反应性好的煤;(2)海绵铁的价格一般比废钢要高。
直接还原法已有上百年的发展历史,但直到20世纪60年代才获得较大突破。
进入20世纪90年代,其生产工艺日臻成熟并获得长足发展。
其主要原因是:(1)天然气的大量开发利用,特别是高效率天然气转化法的采用,提供了适用的还原煤气,使直接还原法获得了来源丰富、价格相对便宜的新能源。
(2)电炉炼钢迅速发展以及冶炼多种优质钢的需要,大大扩展了对海绵铁的需求。
直接还原法

5、世界煤基直接还原铁生产概况 ★据统计 ,1980 年全球直接还原铁(海绵铁)的产 量仅为728 万 t ,2006 年约为 5980 万 t。平均 年增长率在 8 % 以上。印度连续四年为最大 的直接还原铁生产国 ,2006 年产量接近1500 万t , t ,同比增长35 % , 35 ,占世界总产量的 25 % , ,委 内瑞拉以产量 860 万 t 位居第二 ,伊朗以产量 690 万 t 位居第三 ,墨西哥以产量620 万 t 位 居第四。 2008 年底还有一些新增产能将投
1、Fastmet法 ★Fastmet 法是采用环形回转炉生产直接还原铁的一种 方法。该方法用煤粉和铁矿粉作原料 ,制成的冷固结含 炭球团矿在炉中不依靠焦炭和天然气而实现高温还原。 ★特点: (1)用转底炉运载炉料 ,并在高温敞焰下加热实现快速还 原。 (2)还原过程时间很短 ,仅仅 6~12 min ,设备的起动与 停止、 产量的调整都可比较简单地进行。
2、直接还原法的优点 ①不用焦炭,取消了焦炉、烧结等工序 ②DRI中硫、磷、有色金属杂质含量低,利于炼优 质钢 3、直接还原法的缺点 ①对原料要求高,要优质的高品家地区严重缺乏焦煤, 不能发展高炉— —转炉工艺, 但他们有丰富的天然气和普通烟 煤, 有价廉质优的铁矿石。 ②科学技术进步,对钢材质量和品种提出了更 高的要求。 ③废钢-电炉-连铸连轧钢铁生产短流程的兴起。
1、Midrex和 Hy L - Ⅲ 气基竖炉技术 目前 ,全世界共有百余家直接还原铁生产厂。 Midrex和 Hy L - Ⅲ 气基竖炉法是最主要的直接还 原铁生产工艺 , 2006年这两种方法所生产的直接 还原铁产量占世界直接还原铁总产量的 78 . 1% ( Midrex 法 占 59 . 7 %, Hy L - Ⅲ法 占18 . 4 % )。 近年 ,这两种工艺技术得到不断发展。
直接还原铁生产工艺

直接还原铁回转窑铁磷还原法生产工艺一、直接还原铁是精铁粉或氧化铁在炉内经低温还原形成的低碳多孔状物质,其化学成分稳定,杂质含量少,主要用作电炉炼钢的原料,也可作为转炉炼钢的冷却剂,如果经二次还原还可供粉末冶金用。
二、直接还原铁生产工艺概述1、什么是直接还原炼铁法?直接还原炼铁法是在低于矿石熔化温度下,通过固态还原,把铁矿石炼制成铁的工艺过程。
2、常用的直接还原炼铁法有哪些?在工业上应用较多的有铁磷还原法,铁精矿粉还原法等,即将轧钢氧化铁磷或精矿粉经还原铁压块机压制成块后,装入焙烧管进窑焙烧,生产出了优质还原铁。
直接还原铁经粗破(将直接还原铁锭破成块状)中破(将块状直接还原铁破碎成0~15mm的颗粒状)后,再经过磁选,去除SiO2、、CaS和游离碳等杂质。
用户可再次使用还原铁压块机压制直接还原铁颗粒,使直接还原铁颗粒成型并达到一定的堆比重g/cm3要求。
直接还原铁破碎颗粒直接影响压块物理特性(压缩性、成型性、堆比重g/cm3)对特钢生产起到至关重要的作用。
三、铁磷还原法概述1、什么是铁磷?铁鳞又称氧化铁皮、氧化皮。
在钢材加热和轧制过程中,由于表面受到氧化而形成氧化铁层,剥落下来的鱼鳞状物。
铁鳞可用作氧化剂和制铁粉的原料。
轧钢氧化铁磷是钢材在加热炉中加热后在轧制过程中,其表面氧化层自行脱落而产生的。
2、为什么用氧化铁磷?有什么注意事项?还原海绵铁可采用热轧沸腾钢氧化铁磷作原料,因为沸腾钢氧化铁磷中的TFe、C、S、P化学成分含量,能满足还原海绵铁生产的技术要求。
在还原海绵铁中最好不要以高碳钢或合金钢氧化铁磷为原料。
3、什么是铁磷还原法?有哪些类型?铁鳞还原法就是以铁鳞为原料的直接还原法生产工艺。
铁鳞还原法生产过程可分为粗还原与精还原。
在粗还原过程中,铁氧化物被还原,铁粉颗粒烧结与渗碳。
增高还原温度或延长保温时间皆有利于铁氧化物还原、铁粉颗粒烧结,但会生产部分渗碳。
鉴于在精还原过程中脱碳困难,在粗还原过程中,控制铁氧化物还原到未渗碳的程度是必要的。
- 1、下载文档前请自行甄别文档内容的完整性,平台不提供额外的编辑、内容补充、找答案等附加服务。
- 2、"仅部分预览"的文档,不可在线预览部分如存在完整性等问题,可反馈申请退款(可完整预览的文档不适用该条件!)。
- 3、如文档侵犯您的权益,请联系客服反馈,我们会尽快为您处理(人工客服工作时间:9:00-18:30)。
直接还原铁回转窑铁磷还原法生产工艺一、直接还原铁是精铁粉或氧化铁在炉内经低温还原形成的低碳多孔状物质,其化学成分稳定,杂质含量少,主要用作电炉炼钢的原料,也可作为转炉炼钢的冷却剂,如果经二次还原还可供粉末冶金用。
二、直接还原铁生产工艺概述1、什么是直接还原炼铁法?直接还原炼铁法是在低于矿石熔化温度下,通过固态还原,把铁矿石炼制成铁的工艺过程。
2、常用的直接还原炼铁法有哪些?在工业上应用较多的有铁磷还原法,铁精矿粉还原法等,即将轧钢氧化铁磷或精矿粉经还原铁压块机压制成块后,装入焙烧管进窑焙烧,生产出了优质还原铁。
直接还原铁经粗破(将直接还原铁锭破成块状)中破(将块状直接还原铁破碎成0〜15mm勺颗粒状)后,再经过磁选,去除SiO2、、CaS和游离碳等杂质。
用户可再次使用还原铁压块机压制直接还原铁颗粒,使直接还原铁颗粒成型并达到一定的堆比重g/cm3要求。
直接还原铁破碎颗粒直接影响压块物理特性(压缩性、成型性、堆比重g/cm3)对特钢生产起到至关重要的作用。
三、铁磷还原法概述1、什么是铁磷?铁鳞又称氧化铁皮、氧化皮。
在钢材加热和轧制过程中,由于表面受到氧化而形成氧化铁层,剥落下来的鱼鳞状物。
铁鳞可用作氧化剂和制铁粉的原料。
轧钢氧化铁磷是钢材在加热炉中加热后在轧制过程中,其表面氧化层自行脱落而产生的。
2、为什么用氧化铁磷?有什么注意事项?还原海绵铁可采用热轧沸腾钢氧化铁磷作原料,因为沸腾钢氧化铁磷中的TFe C S P化学成分含量,能满足还原海绵铁生产的技术要求。
在还原海绵铁中最好不要以高碳钢或合金钢氧化铁磷为原料。
3、什么是铁磷还原法?有哪些类型?铁鳞还原法就是以铁鳞为原料的直接还原法生产工艺。
铁鳞还原法生产过程可分为粗还原与精还原。
在粗还原过程中,铁氧化物被还原,铁粉颗粒烧结与渗碳。
增高还原温度或延长保温时间皆有利于铁氧化物还原、铁粉颗粒烧结,但会生产部分渗碳。
鉴于在精还原过程中脱碳困难,在粗还原过程中,控制铁氧化物还原到未渗碳的程度是必要的。
还原温度约为1100C。
粗还原得到的海绵铁的含铁量>95%含碳量<0.5%。
随后,在精还原过程中,将粗还原的海绵铁粉碎到小于100目,于氨分解气氛或纯氢中,在800 ------ 1000°C的温度下进行精还原,即退火与脱碳。
在精还原过程中,轻微烧结的铁粉块,经粉碎、筛分、调整粒度,即制成最终产品一一铁粉。
精还原铁粉含铁量>98%四、回转窑直接还原法概述1、什么是回转窑直接还原法?回转窑直接还原法是以连续转动的回转窑作反应器,以固体碳作还原剂,通过固相还原反应把铁矿石炼成铁的直接还原炼铁方法。
生产炼钢海绵铁的主要方法有SL/RN法、CODIF法、DRC TDR ACCA等。
2、回转窑直接还原法工艺简介回转窑直接还原是在950〜1100C进行的固相碳还原反应,窑内料层薄,有相当大的自由空间,气流能不受阻碍的自由逸出,窑尾温度较高,有利于含铁多元共生矿实现选择性还原和气化温度低的元素和氧化物以气态排出,然后加以回收,实现资源综合利用。
由于还原温度较低,矿石中的脉石都保留在产品里,未能充分渗碳。
由于还原失氧形成大量微气孔,产品的微观类似海绵,故也称海绵铁。
3、回转窑直接还原法工艺流程回转窑法工艺流程,一般如下图所示。
回转窑是与水平稍呈倾斜放置在几组支撑托轮上、内衬耐火材料可连续旋转的筒形高温反应器。
作业时,将一定粒度的铁矿石(块矿、球闭矿)、部分还原煤(包括返回炭)和脱硫剂按比例连续从窑加料端(尾端)加入,随着窑体转动(0.5〜1.2r/min),物料受摩擦力被带起一定高度并因重力作用翻滚落下,同时向窑排料端(低端)前移一小距离。
在窑排料端还设有还原煤喷送装疆,靠高压空气将适宜粒度的还原煤送入窑内,调节喷送空气量能有效地控制喷入距离和分布。
窑内物料加热和反应热由排料端和沿窑长装设的伸入窑内的供风管送入空气(一次风和二次风),燃烧窑内还原煤释放的挥发 分、还原反应生成的co 和碳提供。
如热量不足,可在窑头增设煤粉烧嘴补充。
物料在前移过程中逐渐被逆向的热气流加热,完成干燥、预热、碳酸盐分解、脱 硫、铁氧化物(或其他元素)还原和渗碳反应等。
调节各风管供风量、煤粉和还原 煤数量、粒度和分布,可灵活的控制窑内温度和分布。
使入窑铁矿石在窑内停留 8〜10小时和950〜1100C 下转变成海绵铁。
运出*有些回转窑为扩大高温还原带长度, 在预热段安有埋入烧嘴,空气送入料层 燃烧窑尾还原煤释放的挥发分,提高预热段温度。
从排料端排出的高温料通过溜 槽落入冷却筒。
靠筒外喷水(或内、外同时喷水)将料冷却到120C 以下。
为改善 物料运动强化冷却,筒内装有扬料板。
在回转窑卸料端及冷却筒两端安装有密封 装置,生产时维持微正压,防止空气吸入发生再氧化。
冷却后的物料经筛分分级、 磁选分离得出磁性颗粒料(直接还原铁)、磁性粉料、非磁性颗粒料和非磁性粉。
磁性粉料拌加黏结剂后压成块,与直接还原铁一起供电炉炼钢。
非磁性颗粒料含 较高固定碳,可作还原剂重新利用。
4、回转窑直接还原法技术指标 四|~1> H 瞧尘锅炉A 25mmearn 遢性料 非世性料尾潦仓15 + (20%) 3 + I TBEU 磁性料I-Rso%) [mTn 水轴分IL t5+5m m (65%) (35牛彳运出]◎畑) _1 -5mm - Inim因回转窑还原温度较高(950〜1100C),产品比较安定,通常不需钝化处理。
回转窑直接还原铁含碳低(0.05 %〜0.3 %), S、P均<0.03 %、金属化率按要求控制在88%〜93%。
5、回转窑直接还原法工作原理经预热装置或直接进入回转窑简体的物料与窑头的燃烧气体按逆流方式进行热交换。
物料从窑尾至出料端经过干燥、预热、分解、煅烧及冷却等段带。
燃烧装置设在窑头,喷入燃料,燃烧的烟气受排烟装置(烟囱或排烟机)造成的负压的影响沿筒体上升流动,与物料逆向相遇进行热交换,并从窑尾排出。
回转窑简体呈3%〜3. 5%的斜度安装,并以1〜2r /min慢速旋转,自窑尾端加入的物料沿窑体以翻滚及滑动的方式朝窑头出料端移动,最后从出料端卸出。
窑内各段带的分配及其长度随加入物料的性质及其在加热过程中的物理化学变化不同而有所差异。
煅烧带以辐射传热为主,预热带则以对流和传导传热为主。
从窑尾排出的烟气温度较高,一般可达900〜1100C。
为了有效地利用余热,可在窑的加料端设置各种原料预热装置或余热锅炉。
出窑的熟料温度有的高达1000〜1300C。
在窑的出料端设置熟料冷却装置,以便回收余热。
熟料冷却至250C以下时进入下一工序。
6、回转窑设备组成回转窑设备主要由筒体、滚圈、支承装置、传动装置、窑头罩、密封装置、集尘室、燃烧装置及热烟室等部分构成,详见下图:1 一胃体 *2 I 4 f < S-l l;>i 6-7 a-懐僥*1 > »-««(1) 筒体。
回转窑的筒体由钢板卷成,从铆接已发展为全部焊接。
筒体应具有足够的刚度和强度,以保证在安装和运转中轴线的直线性和截面的圆度。
筒体内衬耐火材料,起保护简体和减少散热的作用,简体衬砖应能满足操作条件的要求。
预热带一般采用粘土砖,烧成带根据煅烧温度、化学侵蚀等因素选择。
煅烧粘土的回转窑一般采用粘土砖或3等高铝砖砌筑;高铝矶土回转窑一般采用高铝砖砌筑;镁质、镁质合成砂、白云石砂、活性石灰回转窑则采用碱性砖砌筑。
筒体两端设有窑口护板,防止筒体因受灼热物料或高温烟气作用而变形开裂以及导致筒体的窑衬脱落。
由于窑口工作温度有时高达1000〜1300C,故窑口护板应由可以更换的耐热、耐磨材料制成,必要时还采用风冷或水冷措施。
(2) 滚圈。
简体上装有若干个滚圈(轮带),将筒体分成数跨。
简体、窑衬、物料及窑皮等所有回转部分的重量均通过滚圈传递到支承装置上。
滚圈由耐磨性好,接触疲劳强度高的碳钢、合金钢铸成或锻造。
滚圈截面形状有矩形和箱形两种,当前多数采用矩形截面滚圈。
滚圈与筒体之间留有适度的间隙,既可增强筒体刚度,又不致使筒体和滚圈产生较大的热应力。
(3) 支承装置。
承受着回转设备的全部重量。
对简体起着轴向与径向定位作用,使其能安全平稳的运转。
支承装置由托轮、托轮轴、托轮轴承、挡轮及底座等部分构成。
托轮直接与滚圈接触。
各组托轮轴线必须与简体中心线平行,且两组托轮中心与筒体断面中心的三点连线应形成等边三角形。
托轮宽度略宽于滚圈,由耐磨铸钢制成,托轮断面有单轮幅、双轮幅及三轮幅等3种结构,安装方式有心轴式和转轴式2种。
转轴式托轮轴一般是热配合装配。
托轮轴承结构形式分滑动轴承、滚动轴承及滑动一滚动轴承等,大多采用滑动轴承。
滑动轴承的瓦衬镶在球面瓦上,形成球面接触,能自动调心,油勺带油润滑,球面瓦窜水冷却,轴端设有止推盘,轴肩有止推环以承受轴向推力。
轴承固定在型钢底座上,并有调整托轮位置用的顶丝。
滚动轴承虽具有结构简单,摩擦阻力小,电耗低等优点,但大型轴承的一次性投资大,寿命较滑动轴承低。
除前苏联在大直径回转窑的支承装置上采用滚动轴承外,美国、丹麦和日本等国的回转窑均采用滑动轴承,中国仅在中小型回转窑上有的采用滚动轴承。
挡轮的作用是限制或控制筒体轴向窜动。
窑体支承装置的组数称为窑的档数。
可在一档或数档支承装置上装有挡轮,称为带挡轮支承装置,除液压挡轮外,一般只在靠大齿圈附近的滚圈两旁装一组挡轮。
挡轮按其功能分为“信号挡轮”,“推力挡轮”及“液压挡轮”。
“信号挡轮”多数用在旧式窑上,它不是防止窑体轴向窜动的止挡装置,只起信号作用。
“推力挡轮”承受窑体下滑力,限制筒体轴向窜动。
“液压挡轮”是通过液压装置推动挡轮,迫使简体作轴向运动,保证滚圈和托轮在全宽度上均匀磨损及简体直线性以减少动力消耗。
这种装置可同时采用几个小型液压挡轮,共同承受窑体轴向窜动力,特别适用于大直径多挡数的回转窑。
(4) 传动装置。
通过减速机构将动力传递给用弹簧板固定在简体上的大齿圈,使筒体作慢速回转。
由于运输和安装的要求,齿圈为两半剖分式,其齿数均为偶数。
弹簧板有切向和纵向两种。
窑传动装置特点是传动比大,要求平滑无级调速,起动力矩大。
分为主传动和辅助传动两个系统。
主传动系统多数由主电动机、主减速机、齿轮和大齿圈组成,亦可中间再加一级半敞开齿轮或皮带传动,或采用两套电动机和减速机构的双传动方式。
主电动机应有调速功能。
辅助传动系统的作用是当主电动机或主电源发生故障时定期转动窑体,避免筒体产生变形与弯曲,在窑体砌砖或检修时亦使用。
由辅助电动机带动辅助减速机,通过离合器与主减速机的高速轴相连。
辅助电动机与主电动机分别用不同电源供电。
辅助电动机也可用柴油发动机代替。
(5) 窑头罩。
连接筒体窑头端与冷却装置,罩内砌有粘土砖,并设有监视窑内燃料和物料燃烧情况的看火孔和检修门。