PF法直接还原铁新工艺工业性试验成功
钢铁行业关键、共性、前沿技术
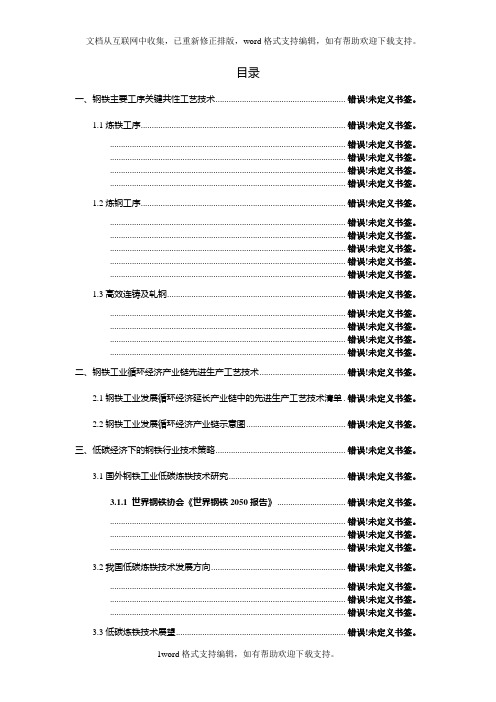
目录一、钢铁主要工序关键共性工艺技术........................................................... 错误!未定义书签。
1.1炼铁工序............................................................................................. 错误!未定义书签。
........................................................................................................... 错误!未定义书签。
........................................................................................................... 错误!未定义书签。
........................................................................................................... 错误!未定义书签。
........................................................................................................... 错误!未定义书签。
1.2炼钢工序............................................................................................. 错误!未定义书签。
........................................................................................................... 错误!未定义书签。
隧道窑生产直接还原铁工艺研究

po oe l e lc a o e ea i t n a d[ rpsd o o e h ut t not t lai t a t s v t f u i fh m lz o r e n S]oD I f R.
K e or u n lkl ; yW ds t n e i DRI r d c r n ;e u e
从表 1 以看 出 ,1 可 )当还原剂 的C固≤7 % ,s 2 含量为 ≥08 .%时 ,直接还原铁 的M、S 均未达 到国家
通 过试 验得 出 :隧道窑 生产 直接 还原铁 用煤 粉 还原 剂必须达 到c 固≥7 %,S< .%的质量要求 。 5 08 同时还原 剂 的配 比也 要加 于控制 ,以能满足 铁矿粉 还原需要 为准 ,以免带 入更多s 含量 ,本试验还原剂
1 前 言
我 国是一 个 废钢 利 用大 国 ,废 钢 的需求 远 大 于 市场 供 给 ,大 量废 钢需 要 从 国外进 口。直 接还 原铁 替代 废钢 是缓 解炼 钢 过程 中废 钢供 应 紧张 的有 效方 法 。昆 钢建有 隧 道窑 直接 还 原铁 生产 线 ,并致 力 于
开展 转 炉使用 隧 道窑 直接 还原 铁 的工 业性试 验 ,并
取得 一 定 的成效 。但 隧道 窑 生产 的直 接还 原铁 始 终 存在 直 接还 原铁 质量 不稳 定 的 问题 ,其 中主要 是金
属化 率 和含硫 量 的波 动过 大 ,直接 影 响到 炼钢 对直 接还 原 铁 的使 用 。为 了解 决 隧道 窑工 艺生 产 直接 还
直接还原铁生产工艺及发展方向

直接还原铁(海绵铁)生产工艺及发展方向习惯上,我们把铁矿石在高炉中先还原冶炼成含碳高的生铁,而后在炼钢炉内氧化,降低含碳量并精炼成钢,这项传统工艺,称作间接炼钢方法;在低于矿石熔化温度下,通过固态还原,把铁矿石炼制成铁的工艺,称作直接炼铁(钢)法或者直接还原法,用这种方法生产出的铁也就称作直接还原铁(即DRI)。
由于这种铁保留了失氧时形成的大量微气孔,在显微镜下观察形似海绵,所以直接还原铁也称之为海绵铁。
一、直接还原铁(海绵铁)的用途直接还原铁是精铁粉在炉内经低温还原形式的低碳多孔状物质,其化学成分稳定,杂质含量少(碳、硅含量低),主要用作电炉炼钢的原料,也可作为转炉炼钢的冷却剂,如果经二次还原还可供粉末冶金用。
一次还原铁粉(海绵铁)的主要用途有:①作为粉末冶金制品的原料,耗用量约占铁粉总耗用量的60~80%;②作为电焊条的原料,在药皮中加入10~70%铁粉可改进焊条的焊接工艺并显著提高熔敷效率;③作为火焰切割的喷射剂,在切割钢制品时,向氧-乙炔焰中喷射铁粉,可改善切割性能,扩大切割钢种的范围,提高可切割厚度;④还可作为有机化学合成中的还原剂、复印机油墨载体等。
近年来由于钢铁产品朝小型轻量化、功能高级化、复合化方向发展,故钢材中非金属材料和有色金属使用比例增加,致使废钢质量不断下降。
废钢作为电炉钢原料,由于其来源不同,化学成分波动很大,而且很难掌握、控制,这给电炉炼钢作业带来了极大的困难。
如果用一定比例的直接还原铁(30~50%)作为稀释剂与废钢搭配不仅可增加钢材的均匀性,还可以改善和提高钢的物理性质,从而达到生产优质钢的目的。
因此,直接还原铁(海绵铁)不仅仅是优质废钢的替代物,还是生产优质钢材必不可少的高级原料(天津无缝钢管公司国外设计中就明确要求必须配50%的直接还原铁(海绵铁))。
根据国外报导,高功率电炉冶炼时,炉料搭配30~50%直接还原铁,生产率提高10~25%,作业率提高25~30%。
直接还原铁生产工艺的分析

直接还原铁生产工艺的分析世界上直接还原铁生产技术已经成熟, 技术发展极为迅速, 根据Midrex 公司预测, 2010年全世界直接还原铁产量将超过7300万t。
于高炉流程存在着生产成本过高和环境污染的两大难题, 炼铁工艺由高炉流程逐步向直接还原铁短流程过渡已成为定局。
当今的钢铁企业对这一革命性技术工艺越早开发越能占据主动; 不敢承担风险, 迟疑不前, 必将处于被动和落后的局面。
因此, 直接还原铁的开发不是“有所为”和“有所不为”的问题, 而是生产工艺的选择问题。
1 世界直接还原铁生产技术现状1.1 生产工艺发展态势由于某些国家天然气资源丰富, 直接还原铁生产技术在南美洲、南非和东南亚诸国的发展极为迅速,而印度则后来居上; 特别是委内瑞拉、墨西哥等国, 生产历史已超过20余年, 生产规模不断扩大, 直接还原铁产量已占本国钢铁产量的绝对份额; 而奥钢联、韩国合作开发的直接还原与熔融还原技术与日俱进; 浦项钢铁公司的直接还原铁生产大有代替高炉炼铁之势。
对这样的发展态势, 作为世界钢铁生产大国的中国, 我们绝不可掉以轻心。
1.2 世界直接还原铁主要生产工艺??? 世界直接还原铁生产工艺大致可分为两大类: 一种是气基竖炉生产工艺; 一种是煤基回转窑生产工艺。
前者生产量约占总产量的92%, 而后者约占总产量的8%。
在这两种生产技术的基础上, 又发展了熔融还原生产技术。
近年来, 将直接还原与熔融还原技术加以组合, 形成了COREX-Midrex联合流程, 颇受人们的关注。
直接还原铁主要生产工艺见表1。
??? 应该指出, 世界上Midrex法和HYL法应用的比较普遍, 各项技术经济指标亦趋稳定, 生产工艺成熟可靠。
特别是墨西哥的HYL法, 生产技术不断创新, 由于开发了“自重整”技术, 使建设费用减少了26% , 电炉的耗电降低了5%~6%。
印度由于缺乏天然气, 但精煤的资源丰富, 因此多采用煤基回转窑的生产方法。
直接还原铁进高炉
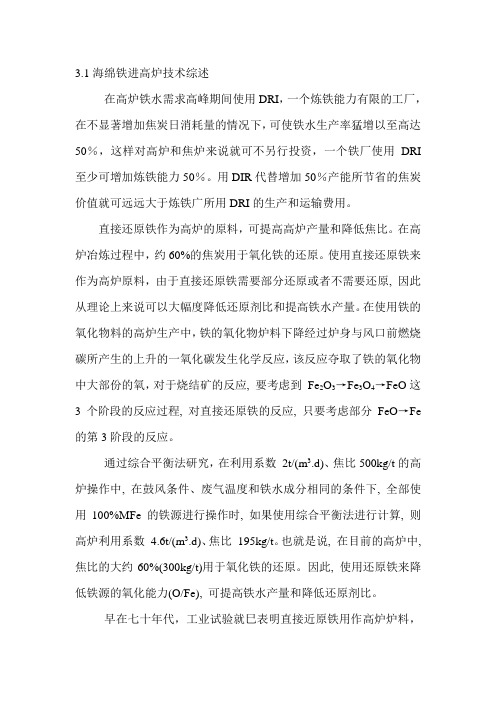
3.1海绵铁进高炉技术综述在高炉铁水需求高峰期间使用DRI,一个炼铁能力有限的工厂,在不显著增加焦炭日消耗量的情况下,可使铁水生产率猛增以至高达50%,这样对高炉和焦炉来说就可不另行投资,一个铁厂使用DRI 至少可增加炼铁能力50%。
用DIR代替增加50%产能所节省的焦炭价值就可远远大于炼铁广所用DRI的生产和运输费用。
直接还原铁作为高炉的原料,可提高高炉产量和降低焦比。
在高炉冶炼过程中,约60%的焦炭用于氧化铁的还原。
使用直接还原铁来作为高炉原料,由于直接还原铁需要部分还原或者不需要还原, 因此从理论上来说可以大幅度降低还原剂比和提高铁水产量。
在使用铁的氧化物料的高炉生产中,铁的氧化物炉料下降经过炉身与风口前燃烧碳所产生的上升的一氧化碳发生化学反应,该反应夺取了铁的氧化物中大部份的氧,对于烧结矿的反应, 要考虑到Fe2O3→Fe3O4→FeO这3个阶段的反应过程, 对直接还原铁的反应, 只要考虑部分FeO→Fe 的第3阶段的反应。
通过综合平衡法研究,在利用系数2t/(m3.d)、焦比500kg/t的高炉操作中, 在鼓风条件、废气温度和铁水成分相同的条件下, 全部使用100%MFe 的铁源进行操作时, 如果使用综合平衡法进行计算, 则高炉利用系数4.6t/(m3.d)、焦比195kg/t。
也就是说, 在目前的高炉中, 焦比的大约60%(300kg/t)用于氧化铁的还原。
因此, 使用还原铁来降低铁源的氧化能力(O/Fe), 可提高铁水产量和降低还原剂比。
早在七十年代,工业试验就巳表明直接近原铁用作高炉炉料,可以降低焦比和提高产量。
1964年一1965年,美国矿业局、美国钢铁公司的试验高炉和安大赂的汉密尔加拿大钢铁公司的商业性生产规模高炉都进行丁试验,探求DIR对铁水生产率和高炉熊比的影响,1970年比利时列日的矮形高炉以及日本新日铁、苏联等也进行了相似试验。
1964年美国矿业局在宾州Bruceton,用一座试验用小高炉进行的试验指出,用金属化率90%左右的直接还原铁球团代替高炉炉料中部分氧化球团矿,可以使铁水生产率明显增加和焦比大为下降。
转底炉生产金属化球团工业性试验
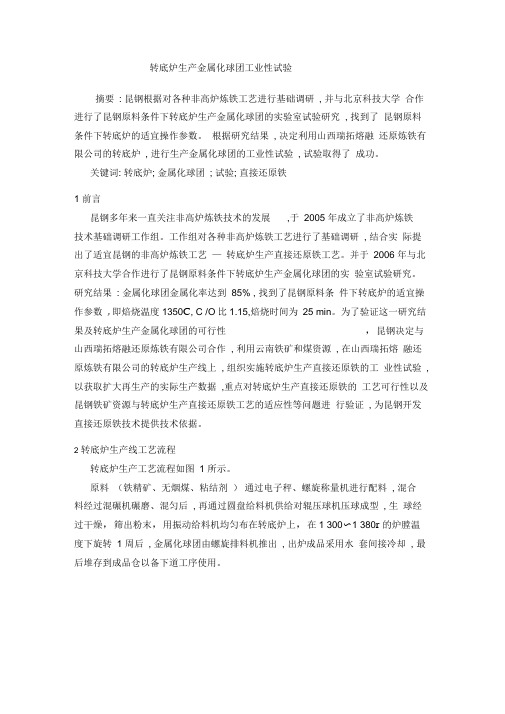
转底炉生产金属化球团工业性试验摘要: 昆钢根据对各种非高炉炼铁工艺进行基础调研, 并与北京科技大学合作进行了昆钢原料条件下转底炉生产金属化球团的实验室试验研究, 找到了昆钢原料条件下转底炉的适宜操作参数。
根据研究结果, 决定利用山西瑞拓熔融还原炼铁有限公司的转底炉, 进行生产金属化球团的工业性试验, 试验取得了成功。
关键词: 转底炉; 金属化球团; 试验; 直接还原铁1 前言昆钢多年来一直关注非高炉炼铁技术的发展,于2005 年成立了非高炉炼铁技术基础调研工作组。
工作组对各种非高炉炼铁工艺进行了基础调研, 结合实际提出了适宜昆钢的非高炉炼铁工艺—转底炉生产直接还原铁工艺。
并于2006 年与北京科技大学合作进行了昆钢原料条件下转底炉生产金属化球团的实验室试验研究。
研究结果: 金属化球团金属化率达到85% , 找到了昆钢原料条件下转底炉的适宜操作参数,即焙烧温度1350C, C /O比1.15,焙烧时间为25 min。
为了验证这一研究结果及转底炉生产金属化球团的可行性,昆钢决定与山西瑞拓熔融还原炼铁有限公司合作, 利用云南铁矿和煤资源, 在山西瑞拓熔融还原炼铁有限公司的转底炉生产线上, 组织实施转底炉生产直接还原铁的工业性试验, 以获取扩大再生产的实际生产数据,重点对转底炉生产直接还原铁的工艺可行性以及昆钢铁矿资源与转底炉生产直接还原铁工艺的适应性等问题进行验证, 为昆钢开发直接还原铁技术提供技术依据。
2 转底炉生产线工艺流程转底炉生产工艺流程如图 1 所示。
原料(铁精矿、无烟煤、粘结剂)通过电子秤、螺旋称量机进行配料, 混合料经过混碾机碾磨、混匀后, 再通过圆盘给料机供给对辊压球机压球成型, 生球经过干燥,筛出粉末,用振动给料机均匀布在转底炉上,在1 300〜1 380r 的炉膛温度下旋转 1 周后, 金属化球团由螺旋排料机推出, 出炉成品采用水套间接冷却, 最后堆存到成品仓以备下道工序使用。
T朗輯]]嵌辅如I [煤粉I哥I山茜刘底炉1.艺漬即示童用3原料准备试验原料为云南产的铁精矿、无烟煤,粘结剂由山西瑞拓公司提供。
直接还原铁工艺技术的对比分析论述

直接还原铁工艺技术的对比分析论述张建国【期刊名称】《资源再生》【年(卷),期】2018(000)002【总页数】5页(P57-61)【作者】张建国【作者单位】北京瀚川鑫冶工程技术有限公司【正文语种】中文在低于矿石融化状态下,通过固态还原,把铁矿石炼制成铁的工艺称作直接还原法,用这种方法生产出的铁也叫作直接还原铁(DRI),由于这种铁保留了失去氧时形成的大量微小气孔,在显微镜下观察形似海绵,所以直接还原铁也称为海绵铁。
直接还原铁是精铁粉在炉内经低温还原形成的低碳多孔状物质,其化学成分稳定,杂质含量少,主要用作电炉炼钢的原料,也可作为转炉炼钢的冷却剂,如果经过二次还原还可供给粉末冶金用。
从上世纪80年代末以来,我国一直宣传推广使用直接还原技术,并对直接还原技术进行了广泛的开发研究,取得了众多成果,为直接还原技术发展奠定了基础。
但是,因铁矿、煤炭、气源等原燃料条件限制,中国直接还原发展的实际成效不大,与钢材、生铁等行业相比还有相当差距。
一、直接还原铁的应用优势直接还原铁生产是指在低于熔化温度之下将铁矿石还原成海绵铁的过程,与传统高炉炼铁方法相比取消了焦炉、烧结等工序,具有流程短、污染小、消耗少,不受炼焦煤短缺影响等优点。
同时海绵铁中硫、磷、硅等有害杂质含量低,有利于电炉冶炼优质纯净钢种。
近年来,由于钢铁产品向小型轻量化、功能高级化、复合化方向发展,因此钢材产品中的非金属材料和有色金属的使用比例在增加,在废钢的破碎分拣过程中,又不能完全有效的剔除非金属和有色金属材料,况且,即使是纯粹完全的黑色废钢料,由于来源不同,化学成分波动也是较大的。
致使加工后的成品入炉废钢的质量很难掌握控制,给电炉炼钢作业带来一定的困难。
如果用一定比例的直接还原铁(30~50%)作为稀释剂与废钢搭配使用,不仅可增加钢的均匀性,还可以改善和提高钢的物理性质,从而达到生产优质钢的目的。
因此,直接还原铁不仅仅是优质废钢的替代品,还是生产优质钢必不可少的高级原料(如天津无缝钢管公司的国外产品设计中就明确要求,必须配置50%的直接还原铁)。
50万吨直接还原炼铁中试放大基地情况简介

50万吨直接还原炼铁中试放大基地情况简介XX热能技术有限公司2007年9月12日目录一、承担单位简介 (2)二、项目摘要 (3)三、项目实施的必要性 (3)3.1 高炉炼铁与直接还原炼铁的比较分析 (3)3.2 我国焦妒煤气综合利用现状 (6)3.3 实施本项目的必要性 (6)四、焦炉煤气用于气基竖炉直接还原炼铁工艺简介 (7)4.1 工艺原理 (7)4.2 主要设备 (9)五、焦化厂工艺技术方案 (11)5.1 工艺流程说明 (12)5.1.1 备煤 (12)5.1.2 炼焦、熄焦 (13)5.1.3 贮焦 (15)5.1.4 冷鼓、电捕 (16)5.1.5 脱硫及硫回收 (17)5.1.6 硫铵 (17)5.1.7 洗脱苯 (18)5.2 仪表和自动化 (18)5.3 主要设备选择 (18)5.3.1 概述 (18)5.3.2 煤气处理主要设备选择 (18)5.4 公用生产辅助设施及行政生活设施 (19)5.5 原料、燃料、辅助材料及动力供应 (19)5.5.1 主要原料、燃料的供应 (19)5.5.2 辅助材料供应 (19)5.5.3 动力供应 (19)六、项目实施的意义 (20)6.1 优化钢铁产业结构 (20)6.2 伴生矿的综合利用 (21)6.3 符合国家战略(政策)需求 (22)七、环境保护、安全措施及消防 (22)7.1 环境保护 (22)7.2 安全措施 (23)7.3 消防设施 (25)八、项目实施(考核)目标 (25)九、项目承担单位的基础和优势 (25)十、项目创新点 (26)十一、项目实施的风险分析 (26)十二、项目实施计划 (27)十三、项目成果提供形式 (27)一、承担单位简介本项目由XX热能技术有限公司承建。
XX热能技术有限公司成立于1995年。
十余年来,公司依托拥有自主知识产权的节能专利技术和自有资金,一直致力于化石燃料(煤炭、石油、天然气等)节能燃烧技术的研究与产品推广,具有自主知识产权的核心技术包括高温空气燃烧技术、蓄热式辐射管燃烧器、煤气化技术、直接还原冶金技术等。
熔融还原炼铁技术综述

目录1.概述 (1)2.国际熔融还原技术发展 (3)2.1.工业化的COREX工艺 (5)2.2.进入示范性工厂试验的Hismelt技术 (7)2.3.FINEX技术 (8)2.4.第三代炼铁法--ITmk3 (9)3.国内熔融还原(非高炉炼铁)技术发展现状 (11)3.1.概述 (11)3.2.2T/h的半工业联动热态试验装置-COSRI (11)3.3.宝钢Corex 3000 (14)3.4.20万吨纯氧非高炉炼铁工业试验装置 (14)3.5.8m3一步法熔融还原试验装置 (18)3.6.基于氢冶金的熔融还原炼铁新工艺 (20)3.6.1.万吨级两级循环流化床示范装置-营口中板厂 (21)3.6.2.宝钢万吨级两级冷态循环流化床装置建设 (24)3.7.直接还原在国内的发展 (24)3.8.几种非高炉炼铁的综合分析 (26)4.炼铁技术的发展方向 (28)4.1.欧盟——ULCOS超低CO2排放钢铁技术研究 (28)4.2.日本——COURSE50技术研究 (30)4.3.中国——新一代可循环钢铁流程工艺技术技 (30)5.具有自主知识产权的熔融还原炼铁技术发展建议 (31)5.1.建立长期开发组织机构与募集资金 (31)5.2.加强合作、充分利用现有成果深入研究 (31)5.3.新一代具有自主知识产权的熔融还原流程建议 (32)熔融还原炼铁技术综述全强1.概述改革开放30年来,中国钢铁冶炼技术取得了巨大的进步。
在炼铁领域,技术进步的主要表现是装备的大型化、操作的自动化信息化、生产的高效与清洁化,高风温技术、富氧技术、喷煤技术、煤气干式除尘技术、煤气余压发电、煤气燃气技术、高炉长寿技术、与高炉废弃物的综合利用等方面的应用取得明显的进步。
据2010年的统计,国内炼铁产量已超过5.9亿吨,约占世界产量的40%。
其中大于1000m3以上高炉的产量约为60%,也就是说,按照国家产业政策的要求,有40%的产能需要进行技术改造。
经验证的钢厂废料回收利用工艺

FASTMET经验证的钢厂废料回收利用工艺James M.Mc clelland,Jr.P.EManager-Techincal SalesMidrex Technologes,Incorproated2725 Water Ridge ParkwayCharlotte,North Carolina,28217USATel:704-378-3359Fax:704-373-1611:jmcclellandmidrex.关键词:FASTMET;FASTMELT®;转底炉;直接还原;铁氧化物;电炉粉尘;钢厂废料;锌的回收利用。
摘要:两个用于回收利用钢铁厂废料的FASTMET流程工厂现在已处于商业运作。
这些FASTMET流程设备正在将钢铁厂废料转变为有用的铁产品和有价值的副产品。
本文将通过这两个工厂来讨论包括废弃燃料油操作,产品质量,锌的回收利用和排放物的测试等操作经验。
绪论Midrex技术公司和它的母公司神户钢铁公司合作,已经开发出了一种以固体炭为基础的还原技术FASTMET流程:这种流程可应用于加工铁矿石,也可应用于加工含有铁氧化物的材料,比如钢厂的废料。
将一台电化铁炉添加到FASTMET 流程就得到了FASTMELT®----------一种生产高质量铁水的经济的方法。
大多数钢铁厂都正在寻求一种合适的方式来回收利用包括高炉和碱性氧化顶吹转炉粉尘、淤泥、轧钢皮、电弧炉粉尘在内的各种钢铁生产废弃物。
电弧炉炼钢粉尘的积聚以及对它们的处理已成为了一个世界性课题。
电弧炉粉尘的回收利用包含两个方面:一方面是回收利用有价值的资源,回收含铁料来炼钢,粗氧化锌用于回收有色金属;另一方面是降低对环境的污染。
从经济与环保两方面来考虑,FASTMET流程都是一种十分吸引人的电弧炉粉尘回收利用技术。
在将粉尘回收起来做电弧炉和碱性氧气顶吹转炉的原料方面,这个流程有两个主要目标。
一个是为了提高铁氧化物的金属化率,这样可以减轻熔化过程的负担。
直接还原铁

直接还原铁直按还原铁和熔融还原铁的生产直接还原铁和熔融还原铁的冶炼统称为非高炉法炼铁。
(一)直接还原法生产生铁直接还原法是指在低于熔化温度之下将铁矿石还原成海绵铁的炼铁生产过程,其产品为直接还原铁(即DRI),也称海绵铁。
该产品未经熔化,仍保持矿石外形,由于还原失氧形成大量气孔,在显微镜下观察团形似海绵而得名。
海绵铁的特点是含碳低(<1%),并保存了矿石中的脉石。
这些特性使其不宜大规模用于转炉炼钢,只适于代替废钢作为电炉炼钢的原料。
直接还原法分气基法和煤基法两大类。
前者是用天然气经裂化产出H2和CO气体,作为还原剂,在竖炉、罐式炉或流化床内将铁矿石中的氧化铁还原成海绵铁。
主要有Midrex法、HYL Ⅲ法、FIOR法等。
后者是用煤作还原剂,在回转窑、隧道窑等设备内将铁矿石中的氧化铁还原。
主要有FASMET法等。
直接还原法的优点有:(1)流程短,直接还原铁加电炉炼钢;(2)不用焦炭,不受炼焦煤短缺的影响;(3)污染少,取消了焦炉、烧结等工序;(4)海绵铁中硫、磷等有害杂质与有色金属含量低,有利于电炉冶炼优质钢种。
直接还原法的缺点有:(1)对原料要求较高:气基要有天然气;煤基要用灰熔点高、反应性好的煤;(2)海绵铁的价格一般比废钢要高。
直接还原法已有上百年的发展历史,但直到20世纪60年代才获得较大突破。
进入20世纪90年代,其生产工艺日臻成熟并获得长足发展。
其主要原因是:(1)天然气的大量开发利用,特别是高效率天然气转化法的采用,提供了适用的还原煤气,使直接还原法获得了来源丰富、价格相对便宜的新能源。
(2)电炉炼钢迅速发展以及冶炼多种优质钢的需要,大大扩展了对海绵铁的需求。
(3)选矿技术提高,可提供大量高品位精矿,矿石中的脉石量降低到还原冶炼过程中不需加以脱除的程度,从而简化了直接还原技术。
当前世界上直接还原铁量的90%以上是采用气基法生产的。
我国天然气主要供应化工和民用,不可能大量用于钢铁工业。
我国煤基直接还原炼铁工艺发展
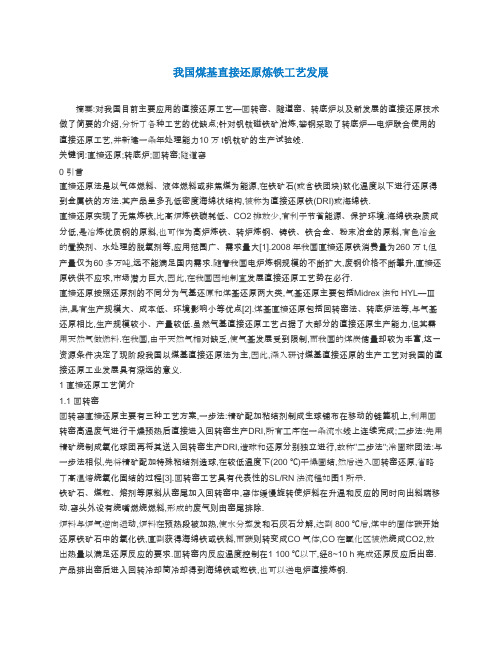
我国煤基直接还原炼铁工艺发展摘要:对我国目前主要应用的直接还原工艺—回转窑、隧道窑、转底炉以及新发展的直接还原技术做了简要的介绍,分析了各种工艺的优缺点;针对钒钛磁铁矿冶炼,攀钢采取了转底炉—电炉联合使用的直接还原工艺,并新建一条年处理能力10万t钒钛矿的生产试验线.关键词:直接还原;转底炉;回转窑;隧道窑0 引言直接还原法是以气体燃料、液体燃料或非焦煤为能源,在铁矿石(或含铁团块)软化温度以下进行还原得到金属铁的方法.其产品呈多孔低密度海绵状结构,被称为直接还原铁(DRI)或海绵铁.直接还原实现了无焦炼铁,比高炉炼铁碳耗低、CO2排放少,有利于节省能源、保护环境.海绵铁杂质成分低,是冶炼优质钢的原料,也可作为高炉炼铁、转炉炼钢、铸铁、铁合金、粉末冶金的原料,有色冶金的置换剂、水处理的脱氧剂等,应用范围广、需求量大[1].2008年我国直接还原铁消费量为260 万t,但产量仅为60多万吨,远不能满足国内需求.随着我国电炉炼钢规模的不断扩大,废钢价格不断攀升,直接还原铁供不应求,市场潜力巨大,因此,在我国因地制宜发展直接还原工艺势在必行.直接还原按照还原剂的不同分为气基还原和煤基还原两大类,气基还原主要包括Midrex法和HYL—Ⅲ法,具有生产规模大、成本低、环境影响小等优点[2].煤基直接还原包括回转窑法、转底炉法等,与气基还原相比,生产规模较小、产量较低.虽然气基直接还原工艺占据了大部分的直接还原生产能力,但其需用天然气做燃料.在我国,由于天然气相对缺乏,使气基发展受到限制,而我国的煤炭储量却较为丰富,这一资源条件决定了现阶段我国以煤基直接还原法为主,因此,深入研讨煤基直接还原的生产工艺对我国的直接还原工业发展具有深远的意义.1 直接还原工艺简介1.1 回转窑回转窑直接还原主要有三种工艺方案,一步法:精矿配加粘结剂制成生球铺布在移动的链篦机上,利用回转窑高温废气进行干燥预热后直接进入回转窑生产DRI,所有工序在一条流水线上连续完成;二步法:先用精矿烧制成氧化球团再将其送入回转窑生产DRI,造球和还原分别独立进行,故称"二步法";冷固球团法:与一步法相似,先将精矿配加特殊粘结剂造球,在较低温度下(200 ℃)干燥固结,然后送入回转窑还原,省略了高温焙烧氧化固结的过程[3].回转窑工艺具有代表性的SL/RN法流程如图1所示.铁矿石、煤粒、熔剂等原料从窑尾加入回转窑中,窑体缓慢旋转使炉料在升温和反应的同时向出料端移动.窑头外设有烧嘴燃烧燃料,形成的废气则由窑尾排除.炉料与炉气逆向运动,炉料在预热段被加热,使水分蒸发和石灰石分解,达到800 ℃后,煤中的固体碳开始还原铁矿石中的氧化铁,直到获得海绵铁或铁料,而碳则转变成CO气体,CO在氧化区被燃烧成CO2,放出热量以满足还原反应的要求.回转窑内反应温度控制在1 100 ℃以下,经8~10 h完成还原反应后出窑.产品排出窑后进入回转冷却筒冷却得到海绵铁或粒铁,也可以送电炉直接炼钢.与高炉工艺相比较,回转窑工艺设备简单,投资少,适用于地方钢铁工业,弥补了高炉—转炉工艺的不足,此外,回转窑还适用于复合矿冶炼,冶金灰尘及各种工业废渣的回收利用,减少环境污染,降低了钢铁生产能耗.同时,回转窑工艺也存在一些缺点,包括窑内结圈、还原温度低(1 100 ℃以下)、流程长、对块矿或球团矿冷强度要求高、要求使用低硫煤等[4].我国山东鲁中矿山公司通过采取提高冷固烧结球团的冷热态强度、加强还原煤的选择和管理、优化回转窑的送风、抛煤、控温温度等措施,预防并降低回转窑结圈,取得了较好的收效.图1 SL/RN法工艺流程1.2 隧道窑隧道窑工艺即将精矿粉、煤粉、石灰石粉,按照一定的比例和装料方法,分别装入还原罐中,然后把罐放在罐车上,推入条形隧道窑中或把罐直接放到环形轮窑中,料罐经预热到1 150 ℃加热焙烧和冷却之后,得到直接还原铁.目前江苏永钢集团拥有两条260 m长煤气隧道窑,为亚洲最长隧道窑.隧道窑生产海绵铁工艺流程如图2所示.图2 隧道窑生产海绵铁工艺流程煤基隧道窑直接还原工艺具有技术成熟、作简单的特点,可因地制宜采用此工艺,利用当地小型分散的铁矿及煤矿资源优势,发展直接还原铁生产,为电炉提供优质原料.但是,总体上讲,我国隧道窑直接还原中存在生产规模较小、能耗高、污染严重、缺乏稳定的原料供应渠道等问题[5],所以,提高机械化程度、改变原料入炉方式、改进燃料及其燃烧、增设余热回收等成为各厂家不断努力改进工艺的方向.我国已建成或正在建设的隧道窑有100多座,约70多个单位规划建设产能5~30 万t/a的隧道窑直接还原铁厂,在不断总结实践经验的基础上,改进现行工艺,开发出诸如大型隧道窑直接还原、AMR—CBI隧道窑直接还原工艺、宽体球状海绵铁隧道窑、L-S快速还原工艺等多种新技术,掀开了隧道窑工艺规模扩大、产能提高、机械及自动化提升的序幕.1.3 转底炉转底炉煤基直接还原是最近几十年间发展起来的炼铁新技术,代表工艺为Fastmet,它由美国Midrex公司与日本神户制钢于20世纪60年发,是采用环形转底炉生产直接还原铁的一种方法.经过多年的半工业性试验和深入的可行性研究,现已完成工艺作参数和装置设计的优化.Fastmelt和ITmk3工艺是在此基础上增加对直接还原铁的处理.图3显示了这三种以转底炉为主体的直接还原工艺流程.图3 转底炉直接还原工艺流程煤粉与铁精粉按比例混匀制成球团,干燥后以1~3层球铺放在转底炉床面,随着炉底的旋转,炉料依次经过预热区、还原区和冷却区.还原区内球团被加热到1 250~1 350 ℃,由于煤粉与铁氧化物紧密接触,铁氧化铁被碳迅速还原成DRI,成品在800~1 000 ℃左右连续从转底炉卸出.球团矿在炉底停留8~30 min,这取决于原料特性、料层厚度及其他因素,成品可作电炉热装炉料或者转炉炉料,也可冷却或生产热压块(HBI).Fastmet工艺技术特点:①在高温敞焰下加热实现快速还原,反应时间只需10~20 min,生产效率高;②原料来源广泛,铁原料方面,除使用高品位粉矿、精矿外,还可用氧化铁皮、代油铁泥、炼钢粉尘、含En、Pb、As等有害杂质的铁矿等;还原剂方面,除煤以外焦末、沥青均可利用,不必担心出现结圈问题;③炉料相对炉底静止,对炉料强度要求不高;④废气中含有大量显热,可用作预热空气、干燥原料等[6]. Fastmelt工艺流程基本与Fastmet一致,只是在后续添加一个熔炉来生产高质量的液态铁水.Itmk3工艺是使金属化球团在转底炉中还原时熔化,生成铁块(Nuggets),同时脉石也熔化,形成渣铁分离.当然转底炉也存在着设备复杂、炉内气氛难控制、传热效率低以及对还原剂硫含量要求严格的缺点.就目前转底炉工艺开发的水平和规模而论,与高炉还有较大差距,但仍存在发展的广阔空间,天津荣程联合钢铁集团已兴建一条100万t级Fastmet生产线,建成目前世界最大的转底炉.另外,用转底炉可处理一些特殊铁矿,如含锌、铅、砷等有害杂质,或含镍、钒、钛等有用元素,均可利用转底炉的工艺优势,或高温挥发,或选择性还原,配合后续工艺,实现资源综合利用.马钢尘泥脱锌转底炉工程项目于2008年5月开工建设,2009年7月6日正式竣工投产,建成了整套转底炉(RHF)脱锌工艺技术装置,不仅解决了含锌尘泥循环利用的后顾之忧,而且将综合利用技术上升到高品质资源化水平.1.4 其他新工艺1.4.1 PF法煤基竖炉直接还原工艺中冶集团北京冶金设备研究设计总院,结合国内情况创新发明了PF法竖炉直接还原工艺.PF法是在吸收K-M法外热式竖炉煤基直接还原工艺的经验基础上,设计的以一种中国特色的罐式还原炉为主反应器的直接还原法.这种工艺技术可靠,技术经济指标在各种煤基直接还原工艺中属先进水平.PF法直接还原工艺流程如图4所示.图4 PF法直接还原工艺流程PF法直接还原工艺主要特点[1]:1)主体设备选用外热式竖炉,预热、还原、冷却三段根据不同的作用和温度选用不同材质和结构,便于传热和化学反应进行,提高热效率和设备寿命.2)原燃料适用性强,对精矿、还原剂和燃料没有特殊要求.3)采用外配碳工艺,还原剂适当过量,扩大了煤的选用范围,造球工艺也因不定量配入煤粉而简化,球团强度较高,DRI质量较好.4)多个反应罐可并列组成任意规模的还原设备,设计和组织生产灵活.1.4.2 低温快速还原新工艺2004年钢铁研究总院提出了低温快速冶金新工艺.新工艺利用纳米晶冶金技术的特点将铁矿的还原温度降低到700 ℃以下.新流程分为气基和煤基两种方法,工艺流程如图5、图6所示.图5 煤基低温快速还原新工艺图6 气基低温快速还原新工艺煤基法使用煤粉为还原剂,在700℃左右快速还原铁精矿粉;气基法使用还原性气体还原铁精矿粉,还原温度可低于600℃.新工艺具有能耗低、环境友好等特点,省去了烧结或造球工艺,缓解了钢铁行业对焦煤的依赖,符合我国国情[7].2 攀钢现状钒钛磁铁矿是攀西地区的特色资源,与普通矿相比,钒钛矿直接还原温度较高、还原时间较长,还原过程产生特有的膨胀粉化现象,因此,存在竖炉结瘤、流化床失流和黏结、回转窑结圈等技术难题.高炉流程冶炼钒钛矿,只回收了铁和钒,钛进入高炉渣没有回收,造成钛资源的大量流失.2005年以来,攀钢科研人员在充分吸收、借鉴新流程及相关研究成果的基础上,通过大量的试验研究,针对钒钛磁铁矿特点,提出并验证了钒钛磁铁矿"转底炉直接还原—电炉深还原—含钒铁水提钒—含钛炉渣提钛"工艺路线,彻底打通了钒钛矿资源综合利用新工艺流程,稳定获得了质量满足要求的低碳生铁、达到GB3283-87要求的片状V2O5和PTA121质量要求的钛白产品.依托该研究成果,攀钢集团攀枝花钢铁研究院于2008年5月4日正式启动了攀钢10 万t/a钒钛矿资源综合利用新工艺中试线工程项目,新建一条转底炉—熔分电炉联合使用,年处理能力10万t钒钛矿的试验生产线,为更深入地研究实践,实现转底炉处理钒钛矿的规模化生产提供了广阔的平台.中试线工艺流程如图7所示.本流程采用硫含量较低的白马铁精矿,还原剂采用无烟煤煤粉,粘结剂为有机粘结剂,原料混合后经高压压球机压球,生球烘干后进入转底炉系统.球团在转底炉内停留10~30 min后出料,金属化球团直接热装进入熔分电炉,在一定温度下还原后,产出含钒铁水及含钛炉渣.继续对铁水进行脱硫、提钒后,得到半钢、脱硫渣及钒渣,半钢进入铸铁机铸铁,生产出铸铁块.钛渣制取钛白,实验室条件下钛回收率达到80%以上;钒渣制取钒氧化物(V2O5),实验室条件下,钒回收率达到65%以上.与高炉流程相比,转底炉流程采用100%钒钛矿冶炼,克服了高炉流程必须配加普通矿的不足,在当前铁资源紧张的形势下,有助于充分发挥攀西地区资源优势,拉动区域经济发展.此外,转底炉流程的铁精矿不需烧结处理,不使用焦炭,从根本上避免了烧结烟气脱硫、焦煤资源采购困难以及环保压力大等问题.3 结语图7 资源综合利用中试线工艺流程煤炭资源总量丰富、焦煤短缺,铁矿资源储量大、富矿少、贫矿和共生矿多是中国钢铁工业面临的现实状况.这种能源、资源结构给煤基直接还原法生产海绵铁的发展提供了机遇.转底炉直接还原技术由于在生产率、规模化、投资费用、单位成本等方面都占有明显的优势,可作为发展直接还原技术的首选工艺.鉴于转底炉处理钒钛磁铁矿技术尚属世界首创,并无较多的经验借鉴,因此要大力开展针对钒钛磁铁矿直接还原的基础研究工作,在实践中借鉴各种直接还原方法已取得的成果,开拓创新,开创钒钛矿直接还原新纪元.参考文献[1] 陈守明,黄超,张金良.煤基竖炉直接还原工艺//2008年非高炉炼铁年会文集.中国金属学会,2008:132-135.[2] 杨婷,孙继青.世界直接还原铁发展现状及分析.世界金属导报,2006.[3] 刘国根,邱冠周,王淀佐.直接还原炼铁中的粘结剂.矿产综合利用,2001(4):27-30.[4] 韩跃新,高鹏,李艳军.白云鄂博氧化矿直接还原综合利用前景.金属矿山,2009 (5):1-6.[5] 魏国,赵庆杰,沈峰满,等.非高炉生产技术进步//2004年全国炼铁生产技术暨炼铁年会文集.2004:878-882.[6] 陶晋. 环形转底炉直接还原工艺现状及发展趋势. 冶金信息工作, 1997.6.[7] 郭培民,赵沛,张殿伟.低温快速还原炼铁新技术特点及理论研究.炼铁,2007,26(1): 57-60.来源:攀枝花钢铁研究院网站。
直接还原铁热装热送新装备技术开发

直接还原铁热装热送新装备技术开发①潘宏涛② 李少英 王少臣 李佳辉(中冶京诚工程技术有限公司 北京100176)摘 要 直接还原铁(Directreductioniron,DRI)热装热送是降低电弧炉电能消耗的重要措施。
本文研究了不同DRI、废钢比例条件下,电弧炉电能消耗与DRI热送温度的关系,结果表明,当DRI取代废钢进行电弧炉冶炼时,DRI入炉温度每增高100℃,每吨钢可节省电能约25kW·h。
此外以“输送能耗最低、输送装置简单”为原则,提出了新型直接还原铁热装热送设备的设计思路,该设备具有转运过程中所需的密闭、保温和计量的功能,同时也实现了造渣料与DRI分层协同加料的功能,设备结构简单可靠,输送能耗低、效率高,解决了当前热装热送设备动能消耗大、设备磨损快、物料流速难以控制、易卡料等问题,为实现直接还原铁高效热装热送创造了重要条件。
关键词 直接还原铁 热装热送 氢基竖炉 电弧炉中图法分类号 TF321 TF702 TF803.21 文献标识码 ADoi:10 3969/j issn 1001-1269 2023 04 004DevelopmentofNewEquipmentTechnologyforHotDirectReductionIronChargingandDeliveryPanHongtao LiShaoying WangShaochen LiJiahui(MCCCapitalEngineering&ampResearchIncorporationLimited,Beijing100176)ABSTRACT Directreducediron(DRI)hotchargingandhotdeliveryisanimportantmeasuretoreduceelectricenergyconsumptioninelectricarcfurnaces.Tosolvetheproblemsofthecurrenthotchargingandhotconveyingequipment,suchashighkineticenergyconsumption,fastequipmentwear,difficultcontrolofmaterialflowrate,andextremelysusceptibletojamming,anewtypeofhotchargingandhotconveyingequipmentfordirectreducedironisdesigned.Theequipmenthasthefunctionsofsealing,heatpreservationandmeteringrequiredinthetransferprocess,andalsorealizesthefunctionoflayeredcollaborativefeedingofslagformingmaterialsandDRI.Theequipmentissimpleandreliableinstructure,lowinenergyconsumptionandhighinefficiency,whichhascreatedimportantconditionsforachievingefficienthotchargingandhotdeliveryofdirectreducediron.KEYWORDS Directreducediron Hotchargingandhotdelivery Hydrogenbasedverticalfurnace Electricarcfurnace1 前言在“碳达峰、碳中和”的战略背景下,钢铁产业高端化、绿色化、低碳化发展是时代的必然要求。
浅议我国直接还原铁技术今后的发展
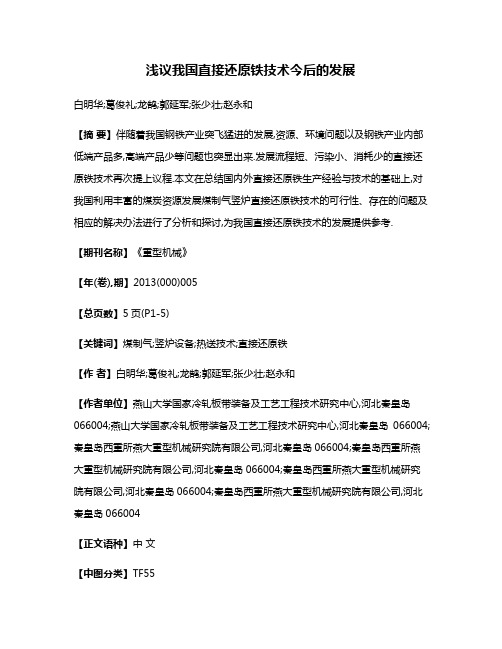
浅议我国直接还原铁技术今后的发展白明华;葛俊礼;龙鹄;郭延军;张少壮;赵永和【摘要】伴随着我国钢铁产业突飞猛进的发展,资源、环境问题以及钢铁产业内部低端产品多,高端产品少等问题也突显出来.发展流程短、污染小、消耗少的直接还原铁技术再次提上议程.本文在总结国内外直接还原铁生产经验与技术的基础上,对我国利用丰富的煤炭资源发展煤制气竖炉直接还原铁技术的可行性、存在的问题及相应的解决办法进行了分析和探讨,为我国直接还原铁技术的发展提供参考.【期刊名称】《重型机械》【年(卷),期】2013(000)005【总页数】5页(P1-5)【关键词】煤制气;竖炉设备;热送技术;直接还原铁【作者】白明华;葛俊礼;龙鹄;郭延军;张少壮;赵永和【作者单位】燕山大学国家冷轧板带装备及工艺工程技术研究中心,河北秦皇岛066004;燕山大学国家冷轧板带装备及工艺工程技术研究中心,河北秦皇岛066004;秦皇岛西重所燕大重型机械研究院有限公司,河北秦皇岛066004;秦皇岛西重所燕大重型机械研究院有限公司,河北秦皇岛066004;秦皇岛西重所燕大重型机械研究院有限公司,河北秦皇岛066004;秦皇岛西重所燕大重型机械研究院有限公司,河北秦皇岛066004【正文语种】中文【中图分类】TF550 前言在世界当代钢铁行业的发展中,利用直接还原铁生产与电炉炼钢相结合生产洁净钢的技术获得了快速发展。
直接还原铁生产是指在低于熔化温度之下将铁矿石还原成海绵铁的过程,与传统高炉炼铁方法相比取消了焦炉、烧结等工序,具有流程短、污染小、消耗少、不受炼焦煤短缺影响等优点。
同时海绵铁中硫、磷、硅等有害杂质含量低,有利于电炉冶炼优质纯净钢种。
该技术对我国节能减排、保护环境、调整钢铁产品结构,提高钢铁产品质量等方面有着重要意义。
然而,2012年国内直接还原铁产量不超过60万t,不到世界直接还原铁产量7 402万t的1%。
我国的铸锻件行业也正处于结构调整与发展期[1],用于电站、冶金、石油化工、航空及船用设备的特殊模锻件的需求量大大增加。
印度的直接还原铁工艺

像SL/RN.ACCAR,CODIR,TDR等使用回转 窑作为反应器、煤作为还原剂的直接还原工艺已经 在世界范围内得到了开发。印度由于有很大的非焦
煤储量,所以已在选用该煤作为能源进行I)RI生产 方面表现出了很大的兴趣。基于气体还原剂的工艺 放限制在那些天然气很丰富并且价格合理的区域 内,广泛使用重整天然气作为还原剂且已投入市场 的工艺是Midrex和HyI,。
上述的工艺各有其优点和缺点。一般而言,气体 作为还原剂的工艺的优点是较高的生产率.较低的 能耗(10.5~14.5GJ/t)而且产品中的碳含量较高。 另一方面,煤作为还原剂的工艺有较低的经济成本, 高的能耗(16.Or 21.0 GJ/t)并且产品中的碳含量
较低。
DRI已得到了广泛的认可并且已为印度的钢铁 制造提供了可实现的炉料。合金钢和特殊钢的生产 者更喜欢使用DRI而非废钢。DRI的成分可以根据 矿石和还原剂的质量以及还原的工艺来改变。要区 分DRI和它的竞争对手是相当容易的,这些含铁炉 料的主要特征对比见表5[I“。 5印度的DRl现状
中间排渣”1。一些感应炉甚至在加入料中使用100
%的DRI|】”。 其他钢铁生产反应器:
t1)在热化铁炉中进行的熔化试验表明.在持
续加入甚至全部加入DRI时,可以不费劲就使之熔 化了。在化铁炉中,DRI的尺寸很重要,而且大块 DRI或熟炉料可以代替生铁块。DRI用在化铁炉中 主要的是为了浇注sI级产品。
印度钢铁工业分为两类:①主要部分是由总设 计生产能力为l 780万t的7个钢铁联合工厂组成; ②第二部分是由熔化能力约2000万t(表4)的电炉 和感应炉组成。第二部分的巨大发展可以归结为以 下原因,即与高炉流程相比,电炉是与环境友好的, 并具有高灵活性,能够生产几乎所有级别的长材和 扁平材。目前,印度是继中国之后的第二个快速发展 的钢铁市场。估计到2001年~2002年和2006年~ 2007年对成品钢的需求量将分别是3 270万t和
直接还原铁简介及伊朗ARFA直接还原铁厂实例

直接还原铁简介及伊朗ARFA直接还原铁厂实例张风杰(中国22冶集团有限公司,唐山)【摘要】国际钢铁协会统计2009年全球粗钢产量12.197亿吨,中国粗钢产量为5.678亿吨,至此中国已连续14年位居世界第一。
显然我们早已步入了钢铁大国行列,但我们离钢铁强国还有很长距离,在某些冶金技术领域相当滞后,尤其直接还原铁方面还我们还处于起步阶段。
学习和了解国际先进的直接还原铁技术,发现和弥补我们的不足迎头赶上,中国直接还原铁前景广阔。
【关键字】直接还原铁优势气基竖炉法施工发展空间直接还原铁(DRI-Direct Reduced Iron),精铁粉或氧化铁在炉内低于融化温度的条件下还原成为多孔状物质,还原失氧形成大量气孔,在显微镜下观察形似海绵而又名海绵铁。
其化学成分稳定,杂质含量少,可直接用作电炉炼钢的原料,也可作为转炉炼钢的冷却剂,它还是冶炼优质钢和特种钢的必备原材料。
作为一种非高炉炼铁工艺,它越来越得到世界各国的重视。
美国米德雷克斯公司(Midrex)的统计数据显示,2008年世界直接还原铁产量达到6845万吨。
自1990年全球还原铁产量从1768万吨增长到2008年的6845万吨,平均年增长幅度在6.0%,这已是直接还原铁产量连续30年增长,即使在2009年严峻的经济环境下,世界直接还原铁产量仍保持在6200万吨。
除中国外,在1994~2010年间,全世界新增的炼铁生产能力有一半是基于直接还原流程。
具体到各个国家,2008年印度已经连续6年保持世界最大的直接还原铁生产国地位,当年产量为2120万吨,占世界总产量的31%;伊朗位居第二,产量为744万吨;委内瑞拉位居第三,产量为687万吨;这些国家具有充足的铁矿石和燃料资源,具备发展直接还原铁充分条件。
另外,近年来俄罗斯直接还原铁产量增长较快,2008年较上年增长33.7%。
2004年,我国直接还原铁产量为43万吨,2005年为41万吨,2006年为40万吨,2007年为60万吨,2008年产量为60万吨。
高效低耗的新型直接还原工艺开发

气氛控制
调整炉内气氛,保持适 宜的还原性气氛,避免
氧化和结块现象。
压力控制
根据反应需求,调整炉 内压力,促进气体扩散
和反应进行。
参数优化
通过试验和实践,不断优 化各项工艺参数,提高产
品质量和降低能耗。
04 节能减排技术应用与效果 评估
节能减排技术集成应用方案
高效燃烧技术
01
采用先进的燃烧器和燃烧控制系统,实现燃料的高效利用和减
能耗数据分析
运用数据分析方法,对能耗数据进行深入挖掘和 分析,找出能源消耗的规律和影响因素。
环保指标达标情况评估
排放物监测
对生产过程中的废气、废水、固废等排放物进行定期监测,确保 达标排放。
环保设施运行评估
评估环保设施的运行情况和处理效果,确保设施稳定可靠运行。
环保指标统计与分析
对环保指标进行统计和分析,评估环保工作的成效和改进方向。
项目成功后,将取得显著的社会效益和经济 效益,为企业和国家带来可观的收益。
02 工艺原理及设备介绍
直接还原工艺基本原理
01
02
03
固态碳还原
利用固态碳作为还原剂, 在高温条件下将体(如氢气、 一氧化碳等)作为还原剂, 将铁矿石中的氧化铁还原 成金属铁。
资源整合
整合企业内部资源,优 化生产流程和供应链管 理,降低生产成本,提 高产品质量和市场竞争 力。
产业链协同
加强与上下游企业的合 作与协同,形成产业链 优势,共同推动新型直 接还原工艺的工业化生 产和应用推广。
THANKS FOR WATCHING
感谢您的观看
数据分析方法
采用统计分析、图表分析等方法对整理后的数据进行分析,探究各 因素对直接还原反应的影响规律。
COSRED直接还原铁及铁水熔炼新工艺在铸造行业的应用
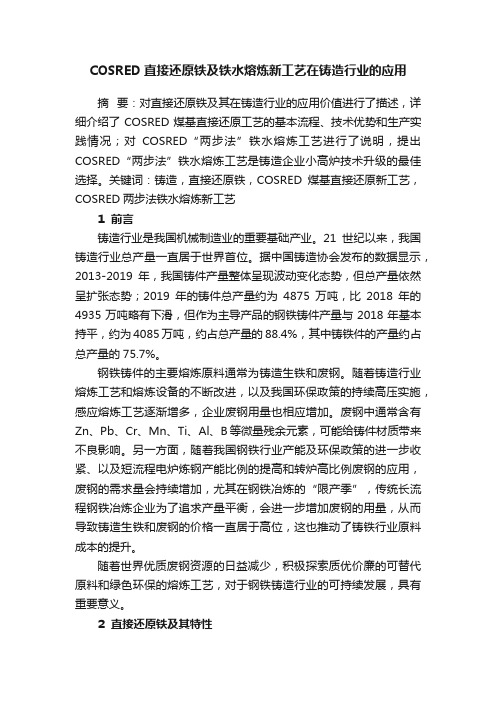
COSRED直接还原铁及铁水熔炼新工艺在铸造行业的应用摘要:对直接还原铁及其在铸造行业的应用价值进行了描述,详细介绍了COSRED煤基直接还原工艺的基本流程、技术优势和生产实践情况;对COSRED“两步法”铁水熔炼工艺进行了说明,提出COSRED“两步法”铁水熔炼工艺是铸造企业小高炉技术升级的最佳选择。
关键词:铸造,直接还原铁,COSRED煤基直接还原新工艺,COSRED两步法铁水熔炼新工艺1 前言铸造行业是我国机械制造业的重要基础产业。
21世纪以来,我国铸造行业总产量一直居于世界首位。
据中国铸造协会发布的数据显示,2013-2019年,我国铸件产量整体呈现波动变化态势,但总产量依然呈扩张态势;2019年的铸件总产量约为4875万吨,比2018年的4935万吨略有下滑,但作为主导产品的钢铁铸件产量与2018年基本持平,约为4085万吨,约占总产量的88.4%,其中铸铁件的产量约占总产量的75.7%。
钢铁铸件的主要熔炼原料通常为铸造生铁和废钢。
随着铸造行业熔炼工艺和熔炼设备的不断改进,以及我国环保政策的持续高压实施,感应熔炼工艺逐渐增多,企业废钢用量也相应增加。
废钢中通常含有Zn、Pb、Cr、Mn、Ti、Al、B等微量残余元素,可能给铸件材质带来不良影响。
另一方面,随着我国钢铁行业产能及环保政策的进一步收紧、以及短流程电炉炼钢产能比例的提高和转炉高比例废钢的应用,废钢的需求量会持续增加,尤其在钢铁冶炼的“限产季”,传统长流程钢铁冶炼企业为了追求产量平衡,会进一步增加废钢的用量,从而导致铸造生铁和废钢的价格一直居于高位,这也推动了铸铁行业原料成本的提升。
随着世界优质废钢资源的日益减少,积极探索质优价廉的可替代原料和绿色环保的熔炼工艺,对于钢铁铸造行业的可持续发展,具有重要意义。
2 直接还原铁及其特性直接还原铁(DRI:Directreduced iron)是将天然矿石(粉)或人造团块在低于熔化温度情况下还原得到的固态金属铁,在钢铁冶炼行业具有广泛的用途,通常被用作电弧炉和中频炉炼钢的优质原料,亦可作为转炉炼钢的冷却剂和高炉炼铁的炉料。
005--鲁庆-中晋太行气基竖炉还原铁技术研发和工业化实践
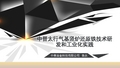
二、
历程——干重整技术
2011年2月,由于MIDREX和HYL技术的还原气气源均采用天然气,对焦炉煤 气没有研究和使用,故和中国石油大学(北京)商定推进开发焦炉煤气为气 源的还原气技术。经过一年来的调研和了解,我公司理清了技术思路:还原 气气源是我国气基还原铁工业化的最大障碍,气源技术是我国实现气基竖炉 还原铁的重大瓶颈。对我国而言,规模钢铁企业均有焦炉,焦炉煤气氢含量 很高和天然气相比,更适合做还原气。所以我们认为,焦炉煤气是我国实现 气基还原铁最易得气源。劣质煤制气、煤层气以及高炉、转炉煤气可以是我 们的后续研发内容。 在深入研究国外各种气基直接还原铁工艺特点后,中国石油大学(北京)新 能源研究院周红军教授、余长春教授和周广林教授团队决定采用最先进的干 重整技术进行还原气气源技术的研发,经过数千次的试验并成功完成,并获 得了国家发明专利。
二、
历程——工艺选择尘埃落定
2013年5月13日,我公司在晋祠宾馆国际会议中心举办了大型签约仪式。在 晋中市委书记张璞、市长吴海清的见证下,与德国MME公司、中国石油大学 (北京)签约共同合作的30万吨∕年直接还原铁项目技术引进协议。
三、工程设计
由中石化南京工程公司根据我公司焦炉 煤气干重整工艺包进行还原气制备部分 工程化设计。由江苏冶金设计院有限公 司根据我公司购买的MME的工艺包对 竖炉部分进行转化设计。 到目前为止,工程设计 完成。在设计的过程中 我们对竖炉密封气、强 制冷却等系统做了优化 设计。
形成了CSDRI气基竖炉还原铁技术方案。这是我国第一套实质上马建设的气基竖炉直
接还原铁的技术。我公司的实践和众多专家、同行在非高炉炼铁上的研究和创新,共 同汇成我国改革开放以来钢铁工业技术变革的洪流。借此机会,向各位领导、专家和 同行做一个汇报,敬请指教。
- 1、下载文档前请自行甄别文档内容的完整性,平台不提供额外的编辑、内容补充、找答案等附加服务。
- 2、"仅部分预览"的文档,不可在线预览部分如存在完整性等问题,可反馈申请退款(可完整预览的文档不适用该条件!)。
- 3、如文档侵犯您的权益,请联系客服反馈,我们会尽快为您处理(人工客服工作时间:9:00-18:30)。
PF法直接还原铁新工艺工业性试验成功
[我的钢铁] 2007-04-27 00:00:00
近日,由北京冶金设备研究设计总院研究设计的单孔罐式还原炉在河北唐山工业性试验成功。
中冶集团北京冶金设备研究设计总院教授级高工陈守明等技术人员长期坚持竖炉直接还原铁工艺研究,结合国内情况创新,发明了PF法竖炉直接还原工艺,并拥有自主知识产权。
1998年在北京科技大学做了固定罐的实验室试验,1999年在山西朔州三元碳素厂煅烧石油焦的罐式炉上进行了半工业性试验,验证了这种工艺的可靠性、主要工艺及设备参数。
2006年与唐山企业合作,不断优化设计,建设一座单孔罐式还原炉进行工业性试验。
2007年3月5日点火生产,一周内打通流程。
受试验设备和检测条件所限,操作技术未达最佳状态,生产稳定时DRI金属化率90%左右,少量达到98.2%。
如能进一步优化设计和施工、操作技术,各项技术经济指标可以达到或超过KM法指标。
PF法直接还原铁工艺流程如下:
PF法直接还原铁工艺主要特点:
容积利用系数高、设备作业率高,能耗低,大幅度降低工程投资和生产成本。
1、反应室与燃烧室分隔,气氛、温度像反应罐(隧道窑)法一样适宜生产DRI,产品金属化率高。
但罐体高得多,预热段、还原段、冷却段分别采用不同材料和结构,能连续生产,比反应罐法生产率高,能耗低;而且罐体不像隧道窑中那样反复加热、冷却,寿命长。
2、能像回转窑和转底炉一样连续生产,但炉体不动而炉料自动下落,炉气逆流上升,设备简单可靠,有利于加热和直接还原反应进行,并可方便地控制炉料还原温度和时间,利用系数高、作业率高,能源和原料消耗低;
3、直接还原与反应罐法和回转窑法一样采用外配碳,还原剂和脱硫剂可适当过量,确保还原和脱硫效果,又不增加产品灰分,使得原燃料选用范围广、工艺设备简单、产品质量好,而投资少、成本低;
4、反应室、燃烧室间隔排列,机构紧凑,每组反应罐都是一座独立的还原设备,若干组并列、组成各种生产能力的还原炉。
可根据市场和原燃料情况灵活设计和使用,生产规模可大可小,配套设备可洋可土,遇到停电或其他事故可随时停止和重新启动,适合中国和发展中国家国情;
5、适合作为煤基直接还原铁工艺主体设备,也易改造为气基法竖炉和其他工业炉窑。
试验证明,PF法是一种安全可靠的竖炉直接还原工艺,而且综合了当前几种直接还原铁工艺长处,在节能、环保和工程投资、生产成本等方面有明显改进。
这种工艺的研究开发和转化,是我国在探索先进、适用的直接还原铁工艺方面的重大进展。
相关链接:
直接还原铁(DRI),也称海绵铁,是冶炼优质钢必不可少的原料,也可作为高炉炼铁、转炉炼钢、铸造、铁合金、粉末冶金的优质炉料,有色冶金的置换剂、水处理的脱氧剂,供不应求。
更重要的是,DRI可以用天然气、煤气和非炼焦煤等作能源,实现无焦炼铁,并且比高炉炼铁碳耗低、CO2排放少,有利于节省能源资源、保护环境,被誉为绿色冶金。
随着生产发展、社会进步,资源短缺、环境污染问题日益突出,发达国家钢铁企业都在改造传统生产工艺,逐步关闭能耗高、污染大的高炉、焦炉,发展优质高效的短流程电炉钢厂,世界DRI产量近二十年翻了三番。
中国钢铁产量连续十几年高速增长,2006年已达4.2亿吨,生产能力达到6亿吨左右,但DRI生产能力只有几十万吨。
目前国家制定政策、采取措施,限制传统钢铁生产工艺低水平重复建设,鼓励发展直接还原、熔融还原非焦炼铁工艺。
直接还原铁工艺按还原剂是气体或煤,分为气基法和煤基法,按还原炉窑,有竖炉法、回转窑法、隧道窑法、转底炉法等多种。
目前全世界DRI年产量近6千万吨,90%左右是以天然气作能源、竖炉和反应罐做还原设备生产的。
但根据我国资源、能源特点和这些年的经验教训,发展DRI产业,能源须以煤和煤气为主,重点是研究开发先进适用的还原炉窑。
竖炉煤基直接还原铁工艺简单可靠。
意大利达涅利公司1968年开始研究开发KM法工艺,73年1月建起6500吨/年工业试验厂,4万吨/年工厂76年成功投产,81年83年先后在缅甸建设的两套2万吨/年工业装置,均顺利投产达标,二十多年来生产正常。
1985年7月冶金部科技司与达涅利公司签订了科技合作协议,组织广东省钢铁研究所和北京钢铁研究总院又作了一系列研究、试验,1987年12月组织全国专家进行了鉴定,肯定这种工艺技术合理、成熟可靠,在各种煤基DRI工艺中属先进水平。