THB6064H IC instructions
4646-X400 VAC传感器
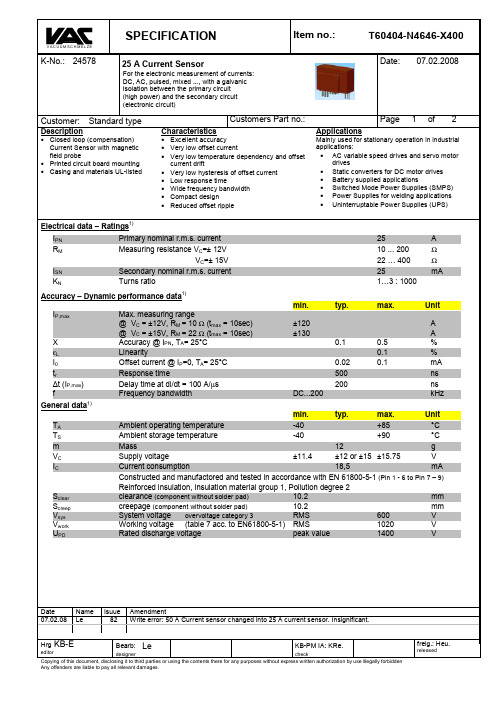
Page
1
of
2
• Closed loop (compensation) Current Sensor with magnetic field probe • Printed circuit board mounting • Casing and materials UL-listed
Mainly used for stationary operation in industrial applications: • AC variable speed drives and servo motor drives • Static converters for DC motor drives • Battery supplied applications • Switched Mode Power Supplies (SMPS) • Power Supplies for welding applications • Uninterruptable Power Supplies (UPS)
(@ TA = 85°C, R M = 22 Ω) primary resistance RP [mΩ] wiring
output current turns ratio RMS IS (IP) [mA] KN
.
1 25 130 25 1:1000 0,12
> > >
1
3
.
2 10 65 20 2:1000 0,54
25 10 ... 200 22 … 400 25 1…3 : 1000 max.
A Ω Ω mA
Accuracy – Dynamic performance data1) Unit A A % % mA ns ns kHz IP,max Max. measuring range @ VC = ±12V, RM = 10 Ω (tmax = 10sec) @ VC = ±15V, RM = 22 Ω (tmax = 10sec) Accuracy @ IPN, TA= 25°C Linearity Offset current @ IP=0, TA= 25°C Response time Delay time at di/dt = 100 A/µs Frequency bandwidth
THB6064H IC instructions
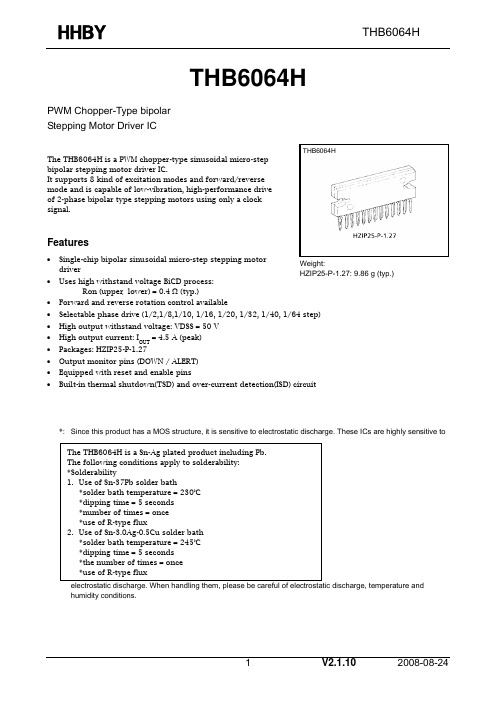
THB6064HPWM Chopper-Type bipolar Stepping Motor Driver ICTHB6064HThe THB6064H is a PWM chopper-type sinusoidal micro-step bipolar stepping motor driver IC.It supports 8 kind of excitation modes and forward/reverse mode and is capable of low-vibration, high-performance drive of 2-phase bipolar type stepping motors using only a clock signal.Features• Single-chip bipolar sinusoidal micro-step stepping motordriver Weight:HZIP25-P-1.27: 9.86 g (typ.)• Uses high withstand voltage BiCD process:Ron (upper lower) = 0.4 Ω (typ.) • Forward and reverse rotation control available• Selectable phase drive (1/2,1/8,1/10, 1/16, 1/20, 1/32, 1/40, 1/64 step) • High output withstand voltage: VDSS = 50 V • High output current: IOUT= 4.5 A (peak)• Packages: HZIP25-P-1.27• Output monitor pins (DOWN / ALERT) • Equipped with reset and enable pins• Built-in thermal shutdown(TSD) and over-current detection(ISD) circuit*: Since this product has a MOS structure, it is sensitive to electrostatic discharge. These ICs are highly sensitive to electrostatic discharge. When handling them, please be careful of electrostatic discharge, temperature and humidity conditions.2. Use of Sn-3.0Ag-0.5Cu solder bath*solder bath temperature = 245°C *dipping time = 5 seconds *the number of times = once *use of R-type flux1. Use of Sn-37Pb solder bath*solder bath temperature = 230°C *dipping time = 5 seconds *number of times = once *use of R-type fluxThe THB6064H is a Sn-Ag plated product including Pb. The following conditions apply to solderability: *SolderabilityBlock DiagramV DOWN ALERT V SGND PGNDA ENABLE PGNDB。
CY62256 32K x 8 位 CMOS 静态 RAM 数据手册说明书
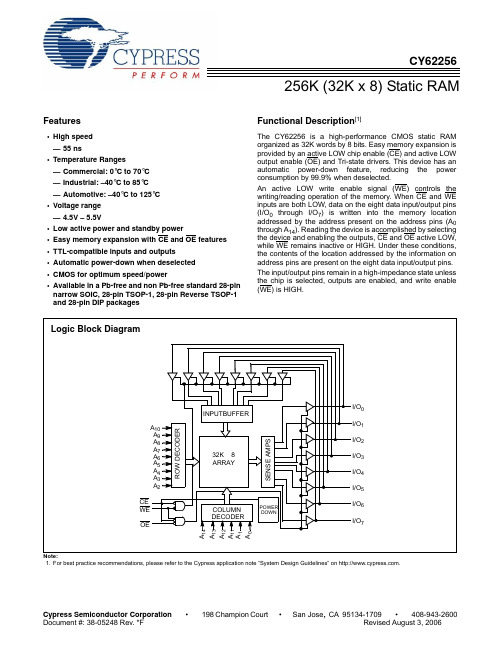
256K (32K x 8) Static RAMCY62256Features•High speed —55ns •Temperature Ranges —Commercial: 0°C to 70°C —Industrial: –40°C to 85°C —Automotive: –40°C to 125°C •Voltage range —4.5V – 5.5V•Low active power and standby power•Easy memory expansion with CE and OE features •TTL-compatible inputs and outputs •Automatic power-down when deselected •CMOS for optimum speed/power•Available in a Pb-free and non Pb-free standard 28-pin narrow SOIC, 28-pin TSOP-1, 28-pin Reverse TSOP-1 and 28-pin DIP packagesFunctional Description [1]The CY62256 is a high-performance CMOS static RAM organized as 32K words by 8 bits. Easy memory expansion is provided by an active LOW chip enable (CE) and active LOW output enable (OE) and Tri-state drivers. This device has an automatic power-down feature, reducing the power consumption by 99.9% when deselected.An active LOW write enable signal (WE) controls the writing/reading operation of the memory. When CE and WE inputs are both LOW, data on the eight data input/output pins (I/O 0 through I/O 7) is written into the memory location addressed by the address present on the address pins (A 0through A 14). Reading the device is accomplished by selecting the device and enabling the outputs, CE and OE active LOW,while WE remains inactive or HIGH. Under these conditions,the contents of the location addressed by the information on address pins are present on the eight data input/output pins.The input/output pins remain in a high-impedance state unless the chip is selected, outputs are enabled, and write enable (WE) is HIGH.Note:1.For best practice recommendations, please refer to the Cypress application note “System Design Guidelines” on .A 9A 8A 7A 6A 5A 4A 3A 2COLUMN DECODERR O W D E C O D E RS E N S E A M P SINPUTBUFFERPOWER DOWNWE OEI/O 0CE I/O 1I/O 2I/O 3I/O 7I/O 6I/O 5I/O 4A 10A 13A 11A 12A A 14A 1Logic Block Diagram32K × 8ARRAYPin ConfigurationsProduct PortfolioProductV CC Range (V)Speed (ns)Power DissipationOperating, I CC(mA)Standby, I SB2(µA)Min.Typ.[2]Max.Typ.[2]Max.Typ.[2]Max.CY62256L Com’l/Ind’l 4.55.05.555/702550250CY62256LL Commercial 7025500.15CY62256LL Industrial 55/7025500.110CY62256LLAutomotive5525500.11512345678910111415162019181721242322Top ViewNarrow SOIC 121325282726GNDA 6A 7A 8A 9A 10A 11A 12A 13WE V CC A 4A 3A 2A 1I/O 7I/O 6I/O 5I/O 4A 14A 5I/O 0I/O 1I/O 2CE OE A 0I/O 322232425262728125101115141312161918173420217689OEA 1A 2A 3A 4WE V CC A 5A 6A 7A 8A 9A 0CE I/O 7I/O 6I/O 5GND I/O 2I/O 1I/O 4I/O 0A 14A 10A 11A 13A 12I/O 3TSOP I Top View (not to scale)Reverse Pinout 22232425262728125101115141312161918173420217689OE A 1A 2A 3A 4WE V CC A 5A 6A 7A 8A 9A 0CE I/O 7I/O 6I/O 5GND I/O 2I/O 1I/O 4I/O 0A 14A 10A 11A 13A 12I/O 3TSOP I Top View (not to scale)12345678910111415162019181721242322Top ViewDIP 121325282726GNDA 6A 7A 8A 9A 10A 11A 12A 13WE V CC A 4A 3A 2A 1I/O 7I/O 6I/O 5I/O 4A 14A 5I/O 0I/O 1I/O 2CE OE A 0I/O 3Pin DefinitionsPin Number Type Description1–10, 21, 23–26Input A 0–A 14. Address Inputs11–13, 15–19, Input/Output I/O 0–/O 7. Data lines. Used as input or output lines depending on operation27Input/Control WE . When selected LOW, a WRITE is conducted. When selected HIGH, a READ is conducted20Input/Control CE . When LOW, selects the chip. When HIGH, deselects the chip22Input/ControlOE . Output Enable. Controls the direction of the I/O pins. When LOW, the I/O pins behave as outputs. When deasserted HIGH, I/O pins are Tri-stated, and act as input data pins14GroundGND . Ground for the device28Power Supply V CC . Power supply for the deviceNote:2.Typical specifications are the mean values measured over a large sample size across normal production process variations and are taken at nominal conditions (T A = 25°C, V CC ). Parameters are guaranteed by design and characterization, and not 100% tested.Maximum Ratings(Above which the useful life may be impaired. For user guide-lines, not tested.)Storage Temperature .................................–65°C to +150°C Ambient Temperature withPower Applied.............................................–55°C to +125°C Supply Voltage to Ground Potential(Pin 28 to Pin 14)..............................................–0.5V to +7V DC Voltage Applied to Outputsin High-Z State[3]....................................–0.5V to V CC + 0.5V DC Input Voltage[3]................................–0.5V to V CC + 0.5V Output Current into Outputs (LOW).............................20 mA Static Discharge Voltage.......................................... > 2001V (per MIL-STD-883, Method 3015)Latch-up Current.................................................... > 200 mA Operating RangeRange Ambient Temperature (T A)[4]V CC Commercial0°C to +70°C 5V± 10% Industrial–40°C to +85°C 5V± 10% Automotive–40°C to +125°C 5V± 10%Electrical Characteristics Over the Operating RangeParameter Description Test ConditionsCY62256−55CY62256−70Unit Min.Typ.[2]Max.Min.Typ.[2]Max.V OH Output HIGH Voltage V CC = Min., I OH = −1.0 mA 2.4 2.4V V OL Output LOW Voltage V CC = Min., I OL = 2.1 mA0.40.4VV IH Input HIGH Voltage 2.2V CC+0.5V 2.2V CC+0.5VVV IL Input LOW Voltage–0.50.8–0.50.8V I IX Input Leakage Current GND < V I < V CC–0.5+0.5–0.5+0.5µA I OZ Output Leakage Current GND < V O < V CC, Output Disabled–0.5+0.5–0.5+0.5µAI CC V CC Operating SupplyCurrent V CC = 5.5V,I OUT = 0 mA,f = f Max = 1/t RCL25502550mALL25502550I SB1Automatic CEPower-down Current—TTL Inputs V CC = 5.5V, CE > V IH,V IN > V IH or V IN < V IL,f = f MaxL0.40.60.40.6mALL0.30.50.30.5I SB2Automatic CEPower-down Current—CMOS Inputs V CC = 5.5V,CE > V CC− 0.3VV IN > V CC− 0.3V, orV IN < 0.3V, f = 0L250250µALL - Com’l0.150.15LL - Ind’l0.1100.110LL - Auto0.115Capacitance[5]Parameter Description Test Conditions Max.UnitC IN Input Capacitance T A = 25°C, f = 1 MHz, V CC = V CC(typ.)6pFC OUT Output Capacitance8pF Thermal Resistance[5]Parameter Description Test Conditions DIP SOIC TSOP RTSOP UnitΘJA Thermal Resistance(Junction to Ambient)Still Air, soldered on a 4.25 x 1.125 inch,2-layer printed circuit board75.6176.5693.8993.89°C/WΘJC Thermal Resistance(Junction to Case)43.1236.0724.6424.64°C/WNotes:3.V IL (min.)= −2.0V for pulse durations of less than 20 ns.4.T A is the “Instant-On” case temperature.5.Tested initially and after any design or process changes that may affect these parameters.AC Test Loads and WaveformsData Retention CharacteristicsParameter DescriptionConditions [6]Min.Typ.[2]Max.Unit V DR V CC for Data Retention 2.0V I CCDRData Retention CurrentL V CC = 2.0V , CE > V CC − 0.3V ,V IN > V CC − 0.3V , or V IN < 0.3V250µA LL - Com’l 0.15µA LL - Ind’l 0.110µA LL - Auto0.110µA t CDR [5]Chip Deselect to Data Retention Time 0ns t R [5]Operation Recovery Timet RCnsData Retention WaveformNote:6.No input may exceed V CC + 0.5V .3.0V 5V OUTPUTR1 1800ΩR2990Ω100pF INCLUDING JIG AND SCOPEGND90%10%90%10%<5ns<5ns5V OUTPUTR1 1800ΩR2990Ω5pFINCLUDING JIG AND SCOPE (a)(b)OUTPUT1.77VEquivalent to:THE VENIN EQUIVALENTALL INPUT PULSES 639ΩV CC(min)V CC(min)t CDRV DR >2V DATA RETENTION MODEt RCEV CCSwitching Characteristics Over the Operating Range[7]Parameter DescriptionCY62256−55CY62256−70Unit Min.Max.Min.Max.Read Cyclet RC Read Cycle Time5570nst AA Address to Data Valid5570nst OHA Data Hold from Address Change55nst ACE CE LOW to Data Valid5570nst DOE OE LOW to Data Valid2535nst LZOE OE LOW to Low-Z[8]55nst HZOE OE HIGH to High-Z[8, 9]2025nst LZCE CE LOW to Low-Z[8]55nst HZCE CE HIGH to High-Z[8, 9]2025nst PU CE LOW to Power-up00nst PD CE HIGH to Power-down5570ns Write Cycle[10, 11]t WC Write Cycle Time5570nst SCE CE LOW to Write End4560nst AW Address Set-up to Write End4560nst HA Address Hold from Write End00nst SA Address Set-up to Write Start00nst PWE WE Pulse Width4050nst SD Data Set-up to Write End2530nst HD Data Hold from Write End00nst HZWE WE LOW to High-Z[8, 9]2025nst LZWE WE HIGH to Low-Z[8]55ns Notes:7.Test conditions assume signal transition time of 5 ns or less, timing reference levels of 1.5V, input pulse levels of 0 to 3.0V, and output loading of the specifiedI OL/I OH and 100 pF load capacitance.8.At any given temperature and voltage condition, t HZCE is less than t LZCE, t HZOE is less than t LZOE, and t HZWE is less than t LZWE for any given device.9.t HZOE, t HZCE, and t HZWE are specified with C L = 5 pF as in (b) of AC Test Loads. Transition is measured ±500 mV from steady-state voltage.10.The internal Write time of the memory is defined by the overlap of CE LOW and WE LOW. Both signals must be LOW to initiate a Write and either signal canterminate a Write by going HIGH. The data input set-up and hold timing should be referenced to the rising edge of the signal that terminates the Write.11.The minimum Write cycle time for Write Cycle #3 (WE controlled, OE LOW) is the sum of t HZWE and t SD.Switching WaveformsRead Cycle No. 1 (Address Transition Controlled)[12, 13]Read Cycle No. 2 (OE Controlled)[13, 14]Write Cycle No. 1 (WE Controlled)[10, 15, 16]Notes:12.Device is continuously selected. OE, CE = V IL .13.WE is HIGH for Read cycle.14.Address valid prior to or coincident with CE transition LOW.15.Data I/O is high impedance if OE = V IH .16.If CE goes HIGH simultaneously with WE HIGH, the output remains in a high-impedance state. 17.During this period, the I/Os are in output state and input signals should not be applied.ADDRESSDATA OUTPREVIOUS DATA VALIDDATA VALIDt RCt AAt OHA50%50%DATA VALIDt RCt ACEt DOEt LZOEt LZCE t PUHIGH IMPEDANCEt HZOE t HZCEt PDIMPEDANCEICCISBHIGH DATA OUTOECEV CC SUPPLY CURRENTt HDt SDt PWEt SAt HAt AWt WCt HZOEDATA IN VALIDNOTE 17DATA I/OADDRESSCEWEOEWrite Cycle No. 2 (CE Controlled)[10, 15, 16]Write Cycle No. 3 (WE Controlled, OE LOW)[11, 16]Switching Waveforms (continued)t WCt AWt SAt HAt HDt SDt SCEDATA IN VALIDWEDATA I/OADDRESSCEt HD t SDt LZWEt SAt HAt AWt WCt HZWEDATA IN VALIDNOTE 17DATA I/OADDRESSWECETypical DC and AC Characteristics1.21.41.00.60.40.24.04.55.05.56.01.61.41.21.00.8−5525125−55251251.21.00.8N O R M A L I Z E D t A A120100806040200.01.02.03.04.0O U T P U T S O U R C E C U R R E N T (m A )SUPPLY VOLTAGE (V)NORMALIZED SUPPLY CURRENT vs.SUPPLY VOLTAGENORMALIZED ACCESS TIME vs.AMBIENT TEMPERATURE AMBIENT TEMPERATURE (°C)NORMALIZED SUPPLY CURRENT vs.AMBIENT TEMPERATUREAMBIENT TEMPERATURE (°C)OUTPUT VOLTAGE (V)OUTPUT SOURCE CURRENT vs.OUTPUT VOLTAGE 0.00.81.41.11.00.94.04.55.05.56.0N O R M A L I Z E D t A ASUPPLY VOLTAGE (V)NORMALIZED ACCESS TIME vs.SUPPLY VOLTAGE 120140*********0.01.02.03.04.0O U T P U T S I N K C U R R E N T (m A )080OUTPUT VOLTAGE (V)OUTPUT SINK CURRENT vs.OUTPUT VOLTAGE0.60.40.20.0N O R M A L I Z E D I C CN O R M A L I Z E D I C C , I S BI CCI CCV CC = 5.0VV CC = 5.0V T A = 25°CV CC = 5.0V T A = 25°CI SBT A = 25°C0.60.801.31.2V IN = 5.0V T A = 25°C1.4V CC = 5.0V V IN = 5.0V−55251052.52.01.5CURRENT vs.AMBIENT TEMPERATUREAMBIENT TEMPERATURE (°C)1.00.50.0–0.5I SB3.0STANDBY V CC = 5.0V V IN = 5.0VI S B 2 µATruth TableCE WE OE Inputs/Outputs ModePowerH X X High-Z Deselect/Power-down Standby (I SB )L H L Data Out Read Active (I CC )L L X Data In WriteActive (I CC )LHHHigh-ZOutput DisabledActive (I CC )Typical DC and AC Characteristics (continued)3.02.52.01.51.00.50.01.02.03.04.0N O R M A L I Z E D I P OSUPPLY VOLTAGE (V)TYPICAL POWER-ON CURRENT vs.SUPPLY VOLTAGE 30.025.020.015.010.05.00200400600800D E L T A t (n s )AA CAPACITANCE (pF)TYPICAL ACCESS TIME CHANGE vs.OUTPUT LOADING1.251.000.7510203040N O R M A L I Z E D I C CCYCLE FREQUENCY (MHz)0.05.00.010000.50V CC = 4.5V T A = 25°CV CC =5.0V T A = 2 5°C V IN = 0.5VNORMALIZED I CC vs. CYCLE TIMEOrdering InformationSpeed(ns)Ordering Code PackageDiagram Package TypeOperatingRange55CY62256LL−55SNI51-8509228-pin (300-mil Narrow Body) SNC Industrial CY62256LL−55SNXI28-pin (300-mil Narrow Body) SNC (Pb-free)CY62256LL−55ZXI51-8507128-pin TSOP I (Pb-free)CY62256LL−55SNE51-8509228-pin (300-mil Narrow Body) SNC AutomotiveCY62256LL−55SNXE28-pin (300-mil Narrow Body) SNC (Pb-free)CY62256LL−55ZE51-8507128-pin TSOP ICY62256LL−55ZXE28-pin TSOP I (Pb-free)CY62256LL−55ZRXE51-8507428-pin Reverse TSOP I (Pb-free)70CY62256LL−70PC51-8501728-pin (600-Mil) Molded DIP Commercial CY62256LL−70PXC28-pin (600-Mil) Molded DIP (Pb-free)CY62256L−70SNC51-8509228-pin (300-mil Narrow Body) SNCCY62256L−70SNXC28-pin (300-mil Narrow Body) SNC (Pb-free)CY62256LL−70SNC28-pin (300-mil Narrow Body) SNCCY62256LL−70SNXC28-pin (300-mil Narrow Body) SNC (Pb-free)CY62256LL−70ZC51-8507128-pin TSOP ICY62256LL−70ZXC28-pin TSOP I (Pb-free)CY62256L–70SNI51-8509228-pin (300-mil Narrow Body) SNC IndustrialCY62256L–70SNXI28-pin (300-mil Narrow Body) SNC (Pb-free)CY62256LL−70SNI28-pin (300-mil Narrow Body) SNCCY62256LL−70SNXI28-pin (300-mil Narrow Body) SNC (Pb-free)CY62256LL−70ZXI51-8507128-pin TSOP I (Pb-free)CY62256LL−70ZRI51-8507428-pin Reverse TSOP ICY62256LL−70ZRXI28-pin Reverse TSOP I (Pb-free)Please contact your local Cypress sales representative for availability of these partsPackage DiagramsPackage Diagrams (continued)28-pin Thin Small Outline Package Type 1 (8 x 13.4 mm) (51-85071)51-85071-*GDocument #: 38-05248 Rev. *F Page 13 of 14All product and company names mentioned in this document are the trademarks of their respective holders.Package Diagrams (continued)51-85074-*F28-pin Reverse Thin Small Outline Package Type 1 (8x13.4 mm) (51-85074)Document History PageDocument Title: CY62256, 256K (32K x 8) Static RAM Document Number: 38-05248REV.ECN NO.IssueDateOrig. ofChange Description of Change**11345403/06/02MGN Change from Spec number: 38-00455 to 38-05248Remove obsolete parts from ordering info, standardize format*A11522705/23/02GBI Changed SN Package Diagram*B11650609/04/02GBI Added footnote 1Corrected package description in Ordering Information table*C238448See ECN AJU Added Automotive product information*D344595See ECN SYT Added Pb-free packages on page# 10*E395936See ECN SYT Changed address of Cypress Semiconductor Corporation on Page# 1 from“3901 North First Street” to “198 Champion Court”Added CY62256L–70SNXI package in the Ordering Information on Page # 10 *F493277See ECN VKN Updated Ordering Information table。
WTN6 系列语音芯片说明书

广州唯创电子有限公司MP3录音模块WTN6系列语音芯片说明书V1.15Note:WAYTRONIC ELECTRONIC CO.,LTD.reserves the right to change this document without prior rmation provided by WAYTRONIC is believed to be accurate and reliable.However,WAYTRONIC makes no warranty for any errors which may appear in this document.Contact WAYTRONIC to obtain the latest version of device specifications before placing your orders.No responsibility is assumed by WAYTRONIC for any infringement of patent or other rights of third parties which may result from its use.In addition,WAYTRONIC products are not authorized for use as critical components in life support devices/systems or aviation devices/systems,where a malfunction or failure of the product may reasonably be expected to result in significant injury to the user,目录1.概述: (2)2.功能简述: (2)3.管脚描述: (2)3.1管脚分布图 (3)4.极限参数: (3)5.直流特性: (3)6.一线串口通讯: (4)6.1管脚分配: (4)6.2一线语音地址对应关系: (5)6.3一线语音及命令码对应表: (5)6.4一线串口时序图: (6)7.两线串口通讯: (7)7.1管脚分配: (7)7.2语音地址对应关系: (7)7.3语音及命令码对应表: (7)7.4两线串口时序图: (8)8.数脉冲控制方式: (9)8.1管脚分配: (9)8.2语音地址对应关系: (9)8.3数脉冲控制时序: (10)9、按键控制模式 (10)10.程序范例 (12)10.1一线串口控制程序 (12)10.2二线串口控制程序 (13)10.3数脉冲控制程序 (14)11.应用电路 (15)11.1一线串口应用电路 (15)11.2两线串口应用电路 (16)11.3数脉冲应用电路 (18)11.4按键应用电路 (19)12.封装管脚图 (21)1.概述:WTN6系列为多功能,低功耗,高性能的CMOS语音芯片。
关于THB6064H(AH)应用注意事项
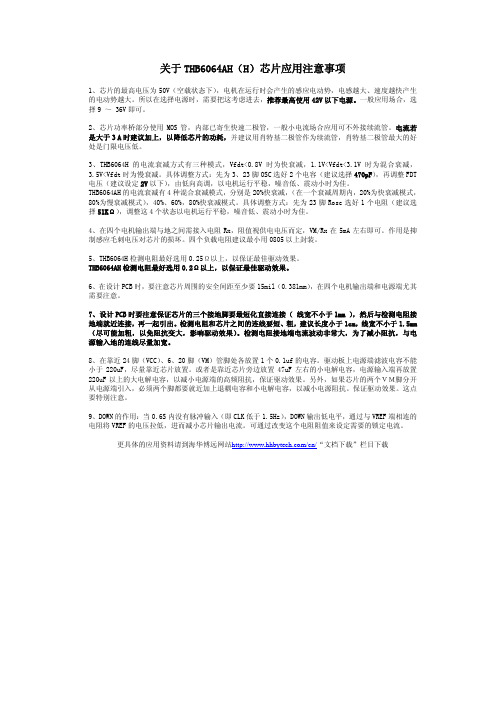
关于THB6064AH(H)芯片应用注意事项1、芯片的最高电压为50V(空载状态下),电机在运行时会产生的感应电动势,电感越大、速度越快产生的电动势越大。
所以在选择电源时,需要把这考虑进去,推荐最高使用42V以下电源。
一般应用场合,选择9 ~ 36V即可。
2、芯片功率桥部分使用MOS管,内部已寄生快速二极管,一般小电流场合应用可不外接续流管。
电流若是大于3 A时建议加上,以降低芯片的功耗,并建议用肖特基二极管作为续流管,肖特基二极管最大的好处是门限电压低。
3、THB6064H的电流衰减方式有三种模式,Vfdt<0.8V时为快衰减,1.1V<Vfdt<3.1V时为混合衰减,3.5V<Vfdt时为慢衰减。
具体调整方式:先为3、23脚OSC选好2个电容(建议选择470pF),再调整FDT 电压(建议设定2V以下),由低向高调,以电机运行平稳,噪音低、震动小时为佳。
THB6064AH的电流衰减有4种混合衰减模式,分别是20%快衰减,(在一个衰减周期内,20%为快衰减模式,80%为慢衰减模式),40%、60%,80%快衰减模式。
具体调整方式:先为23脚Rosc选好1个电阻(建议选择51KΩ),调整这4个状态以电机运行平稳,噪音低、震动小时为佳。
4、在四个电机输出端与地之间需接入电阻Rx,阻值视供电电压而定,VM/Rx在5mA左右即可。
作用是抑制感应毛刺电压对芯片的损坏。
四个负载电阻建议最小用0805以上封装。
5、THB6064H检测电阻最好选用0.25Ω以上,以保证最佳驱动效果。
THB6064AH检测电阻最好选用0.2Ω以上,以保证最佳驱动效果。
6、在设计PCB时,要注意芯片周围的安全间距至少要15mil(0.381mm),在四个电机输出端和电源端尤其需要注意。
7、设计PCB时要注意保证芯片的三个接地脚要最短化直接连接( 线宽不小于1mm ),然后与检测电阻接地端就近连接,再一起引出。
THB6064H 芯片说明书

THB6064H大功率、高细分两相混合式步进电机芯片式驱动器一、特性:● 双全桥MOSFET驱动,低导通电阻R on=0.4Ω(上桥+下桥)● 高耐压50VDC,大电流4.5A(峰值)● 多种细分可选(1/2、1/8、1/10、1/16、1/20、1/32、1/40、1/64)● 自动半流锁定功能● 衰减方式连续可调● 内置温度保护及过流保护重量: 9.86 g (typ.)二、框图:V DD DOWN ALERT V MA SGND PGNDA ENABLEPGNDB三、管脚说明:管脚 编号 输入/输出符号 功 能 描 述1 输出 ALERT 温度保护及过流保护输出端(常态为1,过流保护时为0)2 — SGND 信号地外部与电源地相连3 — OSC1B B相斩波频率控制端4 输入 PFD 衰减方式控制端5 输入 Vref 电流设定端(0—3V)6 输入 VMB 电机驱动电源 B相电源与A相电源相连7 输入 M1 细分数选择端(详见附表)8 输入 M2 细分数选择端(详见附表)9 输入 M3 细分数选择端(详见附表)10 输出 OUT2B B相功率桥输出端211 — NFB B相电流检测端应连接大功率检测电阻,典型值0.25Ω/2W12 输出 OUT1B B相功率桥输出端113 — PGNDB B相驱动电源地与A相电源地及信号地相连14 输出 OUT2A A相功率桥输出端215 — NFA A相电流检测端应连接大功率检测电阻,典型值0.25Ω/2W16 输出 OUT1A A相功率桥输出端117 — PGNDA 驱动电源地线18 输入 ENABLE 使能端ENABLE=0所有输出为0,ENABLE=1正常工作19 输入 RESET 上电复位端20 输入 VMA A相电机驱动电源与A相电源相连21 输入 CLK 脉冲输入端22 输入 CW/CCW 电机正反转控制端23 — OSC1A A相斩波频率控制端24 输入 VDD 5V电源芯片工作电源要求稳压25 输出 Down 半流锁定控制端四、电器参数:最高额定值Absolute Maximum Ratings (Ta = 25°C)参数符号额定值单位V DD 6最高电源电压VV MA/B50最大输出电流I O (PEAK) 4.5(Note 1)每相最高芯片工作电压V IN 5.5V工作温度范围T opr−30 to 85 °C储存温度范围T stg−55 to 150 °C正常运行参数范Operating Range (Ta =30 to 85°C)围参数符号测试条件最小典型. 最大单位芯片工作电压V DD⎯ 4.5V5.55.0电源电压V MA/B V MA/B≥ V DD 4.5 ⎯ 42 V 输出电流I OUT⎯⎯⎯ 4 A 输入端口电压V IN⎯ 0⎯ 5.5V 电流设定端V ref⎯ 0.5⎯3输入脉冲f CLK⎯⎯⎯100 kHz电器特性Electrical Characteristics (Ta = 25°C, V DD = 5 V, V M = 24 V参数符号测试条件最小 典型 最大 单位高 V IN (H) 2.0 ⎯V DD输入电压低V IN (L)M1, M2, M3, CW/CCW, CLK, RESET, ENABLE−0.2⎯ 0.8VI IN (H)M1, M2, M3, CW/CCW, CLK, RESET, ENABLE V IN = 5.0 V ⎯ 55 (80)输入电流I IN (L)V IN = 0 V⎯⎯ 1μA I DD1输出开路, RESET: H, ENABLE: H M1:L, M2:L, M3:L (半步模式) ⎯ 3 (7) I DD2RESET: L, ENABLE: H ⎯ 2 (7) 静态功耗I DD3RESET: L, ENABLE: L ⎯ 2 (7) mAI M1RESET: H/L, ENABLE: L ⎯ 0.5V M supply currentI M2RESET: H/L, ENABLE: H⎯1mA慢衰减模式 3.5 ⎯ V DD混合式衰减模式 (0.9) 1.1 (3.3)衰减方式 输入电压范围 V PFD 块衰减模式⎯⎯ 0.8V最小脉冲宽度 t W (CLK)⎯ 10 ⎯μs温度保护 TSD ⎯ 170 ⎯ °C 关断时间T OFF1A , C OSC1A, C OSC1B = 1000pF16 23 35 μsecT OFF1B半流锁定时间典型值 (0.75) 1.5 (3.0) Hz输出参数Output Block参数符号测试条件最小 典型 最大 单位输出电阻 Ron H + Ron L I OUT = 4 A ⎯ 0.4 (0.6) Ω t r ⎯ 0.1 ⎯ R L = 2 Ω, V NF = 0 V,C L = 15 pF开关特性t f⎯ 0.1 ⎯μs五、使用说明1.M1、M2、M3可选择八种不同细分状态M1 M2 M3 细分数0 0 0 1/20 0 1 1/80 1 0 1/100 1 1 1/161 0 0 1/201 0 1 1/321 1 0 1/401 1 1 1/642.PFD:为衰减方式控制端,调节此端电压可以选择不同的衰减方式,从而获得更好的驱动效果:衰减方式V PFD慢衰减3.5<V PFD<V DD混合式衰减1.1V<V PFD<3.1VV PFD<0.8V 快衰减3.Vref:电流设定端,调整此端电压即可设定驱动电流值Io(100%)=Vref*(1/3)*(1/Rs)Vref取值范围:0.5V—3.0V【Rs为检测电阻】 推荐值为0.25Ω/2W4.Down:半流锁定控制,电机锁定时降低功耗的功能。
ControlLogix 類比 I O 模組 1756-IF16、1756-IF6CIS、1756-

敦泰触摸IC参数对照表
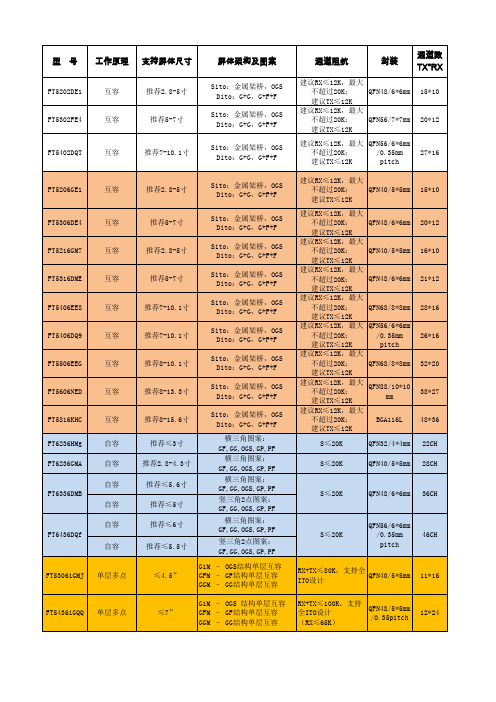
20*12
FT5402DQT
互容
推荐7-10.1寸
27*16
FT5206GE1
互容
推荐2.8-5寸
Sito:金属架桥,OGS Dito:G+G,G+F+F Sito:金属架桥,OGS Dito:G+G,G+F+F Sito:金属架桥,OGS Dito:G+G,G+F+F Sito:金属架桥,OGS Dito:G+G,G+F+F Sito:金属架桥,OGS Dito:G+G,G+F+F Sito:金属架桥,OGS Dito:G+G,G+F+F Sito:金属架桥,OGS Dito:G+G,G+F+F Sito:金属架桥,OGS Dito:G+G,G+F+F Sito:金属架桥,OGS Dito:G+G,G+F+F 横三角图案: GF,GG,OGS,GP,PF 横三角图案: GF,GG,OGS,GP,PF 横三角图案: GF,GG,OGS,GP,PF 竖三角2点图案: GF,GG,OGS,GP,PF 横三角图案: GF,GG,OGS,GP,PF 竖三角2点图案: GF,GG,OGS,GP,PF G1M – OGS结构单层互容 GFM – GF结构单层互容 GGM – GG结构单层互容 G1M – OGS 结构单层互容 GFM – GF结构单层互容 GGM – GG结构单层互容
工作电流:6mA 待机电流:4mA 睡眠电流:30uA
工作温度: -20~+85 储存温度: -55~+150 工作温度: -20~+85 储存温度: -55~+150
深圳贝特莱电子科技有限公司 BL2290 指纹识别传感器数据手册说明书
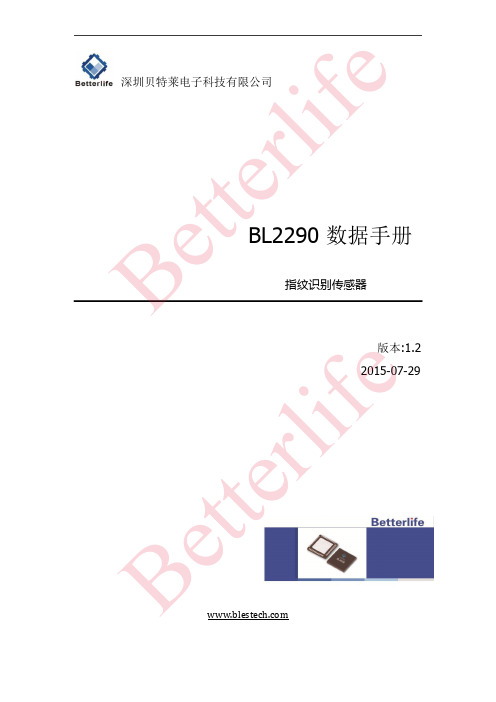
深圳贝特莱电子科技有限公司BL2290 数据手册指纹识别传感器版本:1.2 2015-07-29Be t t er l i f eB et t er l if e1. 概述BL2290是一款圆形按压式指纹识别传感器。
BL2290应用第三代射频指纹识别技术,传感器发出射频信号穿透手指的表皮层检测里层的纹路来获取最佳指纹图像。
BL2290检测灵敏度高,可产生高质量的图像,从而增加认证的可靠性,同时只检测人的真皮皮肤,有效杜绝假手指。
BL2290采用最新型的表面平坦化注塑封装技术,传感器指纹采集阵列表面由注塑材料所保护,抗静电、耐磨损、耐腐蚀等特性优异。
BL2290具有超低功耗,内置振荡器电路、OCP 电路和上电复位电路并使用SPI 接口,可应用于手机、平板电脑、PAD 等移动终端设备。
1.1 特点● 4.8 mm x 5.6 mm 采集面积;● 表面平坦化 LGA 塑封封装:圆形Φ9.55mm ; ● 112 x 96 pixels 传感器阵列;● 508 DPI 分辨率,8bit 灰度等级;● 50 帧/sec 快速采集速度@24MHz SPI speed ;● 塑封+表面保护涂层,可耐受上百万次的磨损; ● 内置 24MHz 振荡器;● 内置上电复位电路;● 内置OCP(Over-Current-Protection)过流保护电路;● SPI Slaver 接口;● >15KV 的表面 ESD ;● 工作电流< 3mA ,手指检测模式< 20uA ; ● 认假率(FAR ):< 0.0005%; ● 拒真率(FRR ):< 1%;● 比对时间:< 0.5秒;Be t t er l i f eB et t er l if e1.2 应用● 电脑周边● 手机、平板电脑、超级本 ● MP3、USB-Key 、PADs ● 手持设备 ● 访问控制设备 ● 门禁和考勤 ● 便携设备 ● 指纹门锁 ● 无线设备 ● 安全应用● 医疗设备及存储Be t t er l i f eB et t er l if e2. 芯片说明2.1 芯片内部构架图 2-1 芯片核心构架图BL2290由全定制的数模混合电路构建,内置振荡器电路、OCP 电路、上电复位电路,能够显著节省BOM 单成本,并进一步减少整体解决方案所需的电路板面积。
7406芯片

Hitachi CodeJEDECEIAJWeight (reference value)DP-14ConformsConforms0.97 gUnit: mmHitachi CodeJEDECEIAJWeight (reference value)FP-14DA—Conforms0.23 gUnit: mm*Dimension including the plating thickness Base material dimension° – 8°Hitachi Code JEDEC EIAJ Weight (reference value)FP-14DN Conforms Conforms0.13 gUnit: mm°– 8°*Pd platingCautions 1.Hitachi neither warrants nor grants licenses of any rights of Hitachi’s or any third party’s patent,copyright, trademark, or other intellectual property rights for information contained in this document.Hitachi bears no responsibility for problems that may arise with third party’s rights, includingintellectual property rights, in connection with use of the information contained in this document.2.Products and product specifications may be subject to change without notice. Confirm that you havereceived the latest product standards or specifications before final design, purchase or use.3.Hitachi makes every attempt to ensure that its products are of high quality and reliability. However,contact Hitachi’s sales office before using the product in an application that demands especially high quality and reliability or where its failure or malfunction may directly threaten human life or cause risk of bodily injury, such as aerospace, aeronautics, nuclear power, combustion control, transportation,traffic, safety equipment or medical equipment for life support.4.Design your application so that the product is used within the ranges guaranteed by Hitachi particularlyfor maximum rating, operating supply voltage range, heat radiation characteristics, installationconditions and other characteristics. Hitachi bears no responsibility for failure or damage when used beyond the guaranteed ranges. Even within the guaranteed ranges, consider normally foreseeable failure rates or failure modes in semiconductor devices and employ systemic measures such as fail-safes, so that the equipment incorporating Hitachi product does not cause bodily injury, fire or other consequential damage due to operation of the Hitachi product.5.This product is not designed to be radiation resistant.6.No one is permitted to reproduce or duplicate, in any form, the whole or part of this document withoutwritten approval from Hitachi.7.Contact Hitachi’s sales office for any questions regarding this document or Hitachi semiconductor products.Hitachi, Ltd.Semiconductor & Integrated Circuits.Nippon Bldg., 2-6-2, Ohte-machi, Chiyoda-ku, Tokyo 100-0004, Japan Tel: Tokyo (03) 3270-2111 Fax: (03) 3270-5109Copyright ' Hitachi, Ltd., 1999. All rights reserved. Printed in Japan.Hitachi Asia Pte. Ltd.16 Collyer Quay #20-00Hitachi Tower Singapore 049318Tel: 535-2100Fax: 535-1533URL NorthAmerica : http:/Europe : /hel/ecg Asia (Singapore): .sg/grp3/sicd/index.htm Asia (Taiwan): /E/Product/SICD_Frame.htm Asia (HongKong): /eng/bo/grp3/index.htm Japan : http://www.hitachi.co.jp/Sicd/indx.htmHitachi Asia Ltd.Taipei Branch Office 3F, Hung Kuo Building. No.167, Tun-Hwa North Road, Taipei (105)Tel: <886> (2) 2718-3666Fax: <886> (2) 2718-8180Hitachi Asia (Hong Kong) Ltd.Group III (Electronic Components)7/F., North Tower, World Finance Centre,Harbour City, Canton Road, Tsim Sha Tsui,Kowloon, Hong Kong Tel: <852> (2) 735 9218Fax: <852> (2) 730 0281 Telex: 40815 HITEC HXHitachi Europe Ltd.Electronic Components Group.Whitebrook ParkLower Cookham RoadMaidenheadBerkshire SL6 8YA, United KingdomTel: <44> (1628) 585000Fax: <44> (1628) 778322Hitachi Europe GmbH Electronic components Group Dornacher Stra§e 3D-85622 Feldkirchen, Munich Germany Tel: <49> (89) 9 9180-0Fax: <49> (89) 9 29 30 00Hitachi Semiconductor(America) Inc.179 East Tasman Drive,San Jose,CA 95134Tel: <1> (408) 433-1990Fax: <1>(408) 433-0223For further information write to:。
X11 AOM-TPM-9670V AOM-TPM-9670H AOM-TPM-9670V(H)-S

TPM for X11AOM-TPM-9670V AOM-TPM-9670HAOM-TPM-9670V(H)-SUSER’S MANUAL1.2aManual Revision 1.2aRelease Date: October 13, 2022Unless you request and receive written permission from Super Micro Computer, Inc., you may not copy any part of this document.Information in this document is subject to change without notice. Other products and companies referred to herein are trademarks or registered trademarks of their respective companies or mark holders.Copyright © 2022 by Super Micro Computer, Inc.All rights reserved. Printed in the United States of AmericaThe information in this user’s guide has been carefully reviewed and is believed to be accurate. The vendor assumes no responsibility for any inaccuracies that may be contained in this document, and makes no commitment to update or to keep current the information in this manual, or to notify any person or organization of the updates. Please Note: For the most up-to-date version of this manual, please see our web site at .Super Micro Computer, Inc. ("Supermicro") reserves the right to make changes to the product described in this manual at any time and without notice. This product, including software and docu-mentation, is the property of Supermicro and/or its licensors, and is supplied only under a license. Any use or reproduction of this product is not allowed, except as expressly permitted by the terms of said license.IN NO EVENT WILL SUPER MICRO COMPUTER, INC. BE LIABLE FOR DIRECT, INDIRECT, SPECIAL, INCIDENTAL, SPECULATIVE OR CONSEQUENTIAL DAMAGES ARISING FROM THE USE OR INABILITY TO USE THIS PRODUCT OR DOCUMENTATION, EVEN IF ADVISED OF THE POSSIBILITY OF SUCH DAMAGES. IN PARTICULAR, SUPER MICRO COMPUTER, INC. SHALL NOT HAVE LIABILITY FOR ANY HARDWARE, SOFTWARE, OR DATA STORED OR USED WITH THE PRODUCT, INCLUDING THE COSTS OF REPAIRING, REPLACING, INTEGRATING, INSTALLING OR RECOVERING SUCH HARDWARE, SOFTWARE, OR DATA.Any disputes arising between manufacturer and customer shall be governed by the laws of Santa Clara County in the State of California, USA. The State of California, County of Santa Clara shall be the exclusive venue for the resolution of any such disputes. Supermicro's total liability for all claims will not exceed the price paid for the hardware product.FCC Statement: Refer to Supermicro's website for FCC Compliance Information.California Best Management Practices Regulations for Perchlorate Materials: This Perchlorate warning applies only to products containing CR (Manganese Dioxide) Lithium coin cells. “Perchlorate Material-special handling may apply. See /hazardouswaste/perchlorate”.PrefaceAbout This User's GuideThis user's guide is written for system integrators, IT professionals, and knowl-edgeable end users who wish to add additional data security mechanisms to their systems to protect highly sensitive applications. It provides detailed information on configuring, provisioning, and using the Trusted Platform Module (TPM).User's Guide OrganizationChapter 1 provides an overview of the TPM, including its features and uses.Chapter 2 provides detailed instructions on installing, provisioning, and using the TPM.Conventions Used in This User's GuidePay special attention to the following symbols for proper TPM configuration.Warning: Important information given to avoid TPM configuration errors.Note: Additional information given to ensure correct and proper TPM configuration setup.PrefaceSuper TPM User's GuideContacting SupermicroHeadquartersAddress:Super Micro Computer, Inc.980 Rock Ave.San Jose, CA 95131 U.S.A.Tel:+1 (408) 503-8000Fax:+1 (408) 503-8008Email:************************(GeneralInformation)************************(SalesInquiries)***********************************(Gov.SalesInquiries)**********************(TechnicalSupport)******************(RMASupport)************************(Webmaster)Website:EuropeAddress:Super Micro Computer B.V.Het Sterrenbeeld 28, 5215 ML's-Hertogenbosch, The NetherlandsTel:+31 (0) 73-6400390Fax:+31 (0) 73-6416525Email:***************************(SalesInquiries)*****************************(TechnicalSupport)*************************(RMASupport) Website:www.supermicro.nlAsia-PacificAddress:Super Micro Computer, Inc.3F, No. 150, Jian 1st Rd.Zhonghe Dist., New Taipei City 235Taiwan (R.O.C)Tel:+886-(2) 8226-3990Fax:+886-(2) 8226-3992PrefaceAsia-PacificEmail:*************************.tw(SalesInquiries)**********************.tw(TechnicalSupport)******************.tw(RMASupport)Website:Super TPM User's GuideTable of ContentsPreface (3)Chapter 1 Introduction ..............................................................................1-1 1.1 Overview of the Trusted Platform Module (TPM) ...........................................1-1 1.2 Supermicro TPM Features ..............................................................................1-2 1.3 Motherboards Supported for TPM ..................................................................1-3 1.4 Intel® TXT ........................................................................................................1-3 Chapter 2 Deploying and Using the TPM ...............................................2-1 2.1 Installing the TPM Onto the Motherboard .......................................................2-1 2.2 Enabling the TPM via the BIOS and Intel® Provision Utility ...........................2-2 2.3 An Important Note to the User ........................................................................2-9Chapter 1: IntroductionChapter 1Introduction1.1 Overview of the Trusted Platform Module (TPM)The Trusted Platform Module (TPM9670) is a special add-on module that may be installed onto Supermicro X11 dual and single processor motherboards that support CPU Socket 3674 only.Types of TPMsNote: TPM module must be provisioned in order to support Intel® TrustedExecution Technology (TXT). Please contact Supermicro Technical Sup-port to get more details about the Intel tool.The TPM-9670 series add-on modules use TCG (Trusted Computing Group) ver-sion 2.0 firmware.The following SKUs are available:• AOM-TPM-9670V, a vertical TPM module• AOM-TPM-9670H, a horizontal TPM moduleHorizontal vs. Vertical: Generally, whether you should use a TPM with a horizontal or vertical form factor depends on the physical space available. Horizontal TPMs are used in 1U chassis. Vertical TPMs are used in 2U or taller chassis, which are designed with a smaller footprint to occupy less space on the motherboard.Server vs. Client: To use the TXT function, each TPM has been provisioned as a server model or client model. Be sure to use the appropriate TPM for your needs.Both server TPM and client TPM are designed to support motherboards with Socket P (LGA3647) processors installed.Super TPM User's Manual1.2 Supermicro TPM Features1. TCG2.0 compliance2. SPI interface3. Microcontroller in 0.22/0.09-µm CMOS technology4. Compliant embedded software5. EEPROM for TCG firmware enhancements and for user data and key support6. Hardware accelerator for SHA-1 and SHA-256 hash algorithm7. True Random Number Generator (TRNG)8. Tick counter with tamper detection9. Protection against dictionary attack10. Infineon's TPM 2.0 is Common Criteria (CC) certified at Evaluation AssuranceLevel (EAL) 4 Moderate11. General-purpose I/O12. Intel® Trusted Execution Technology (TXT) support13. AMD® Secure Virtual Machine Architecture support14. Full personalization with Endorsement Key (EK) and EK certificate15. Power-saving sleep mode16. 3.3V power supply17. WHQL dual-mode 1.1b + 1.2 TPM Windows Kernel Mode DriverChapter 1: Introduction1.3 Motherboards Supported for TPMPlease refer to the Supermicro website (/) for a complete and most up-to-date list of the motherboards that can support the TPM. As a general rule, besides the X11 motherboards, the list includes most X9 motherboards, all X10 motherboards, and some AMD motherboards. These motherboards will come with a specially designated JTPM1 connector on every board, which will be listed in the respective motherboard's manual.1.4 Intel® TXTThe Intel Trusted Execution Technology (TXT) is a software tool that may be used in conjunction with the TPM to provide additional security for pre-launch firmware of clusters and clouds, including but not limited to the BIOS, IPMI, SAS firmware, and CMM firmware. It is optional, but the TPM is required for it to be provisioned.It will further enhance system security by protecting firmware against malicious attacks on vulnerable areas.It works by matching hypervisor measures with encryption keys upon system launch.If the hypervisor does not match the keys, the hypervisor will be prevented from starting up.To use the TXT, you need to enable TXT support after provisioning the TPM.Note: TXT is only supported on Intel platforms that support TPM use.How the TXT WorksThe Intel TXT, when enabled, follows a step-by-step process to ensure the security of pre-launch components.1. Measures the hypervisor launch upon system startup2. Checks for a match3. If matched: The TXT signals "trusted," and the launch is allowed to proceed.4. If mismatched: The TXT signals "untrusted," and the launch is blocked.Chapter 2: Deploying and Using the TPMChapter 2Deploying and Using the TPMFollow the instructions below to begin using the TPM.2.1 Installing the TPM Onto the MotherboardTo install the Trusted Platform Module onto your motherboard, follow the steps below.1. Find the 9-pin male JTPM1 connector on the motherboard. If you need helplocating this connector, consult your motherboard manual. If the board doesnot have this feature, then it does not support the TPM.2. Using the key pin as a reference, orient, and align your TPM with the connec-tor.key pin3. Carefully insert the TPM into the connector on the motherboard, making surenot to damage the pins.Note: The orientation of the TPM to be installed depends on whether ithas a horizontal or vertical form factor. The vertical TPM is intended to"stand" perpendicular to the motherboard, while the horizontal TPM liesflat (parallel) on the motherboard. See the below two images for the cor-rect orientation.Horizontal TPM Vertical TPMSuper TPM User's Manual2.2 Enabling the TPM via the BIOS and Intel® ProvisionUtilityThere are two components to the process of enabling the TPM. After you have installed the TPM onto the motherboard, you must first "verify" the TPM for the motherboard. This is done through the BIOS, which can also be used to enable TXT support. You then will need to "lock" the TPM in the firmware. This is done through the provision utility provided by Intel.A. Enabling the TPM in the BIOS1. Enter the BIOS setup screen. You may do this either from the IPMI remoteconsole or from the server directly using KVM. Reboot the system, and pressthe <Del> key as the system boots until you reach the BIOS screen.2. You will be presented with the BIOS Setup main screen. Using your arrowkeys, navigate to the "Advanced" tab. From there, navigate down and selectthe "CPU Configuration" option. Press <Enter>.3. You will then be taken to the CPU Configuration page. Using your arrow keys,navigate down to the "Intel Virtualization Technology" option, as shownbelow, and press <Enter>. If this item is not already enabled, select Enableand press <Enter>.Chapter 2: Deploying and Using the TPM4. Once you have enabled virtualization support, press your <Esc> key until youare back to the "Advanced" tab. Navigate down to the "Trusted Computing"option and press <Enter>.The Trusted Computing window will appear.Note: By default, "SHA-1 PCR Bank" and "SHA-256 PCR Bank” areEnabled.5. Disable "PH Randomization" and "TXT Support" only. Using the arrowkeys, select each option, press the <Enter> key to select Disabled, andpress the <Enter> key again.Super TPM User's Manual7. Use the arrow keys to select "Save Changes ". Press the <Enter > key.6. Press the <Esc > key to bring you back to the "Advanced " tab options. Usethe arrow keys to toggle to the "Save & Exit " tab.Chapter 2: Deploying and Using the TPMB. Provisioning Intel TXT (Server)Next, you will need to provision Intel TXT in the UEFI shell.Note: If the TPM part number is AOM-TPM-9670V-S or AOM-TPM-9670H-S, you do not need to get the Intel® Provisioning Tool. Please go aheadand enable the Intel TXT feature in the BIOS.1. Select "UEFI: Built-in EFI Shell" in the BIOS. The system will boot into theUnified Extensible Firmware Interface (UEFI) with a list of available USBdevices.2. Each USB device has its own code. Type the code for the USB device thatyou want to use into the command line at the bottom of the screen. and press the <Enter> key.Note: The device used for the purposes of this user guide had a codeof fs0. Replace this code with the code that corresponds to your device.3. In the command line at the bottom of the screen, follow these steps belowafter typing “FS0”.Super TPM User's Manual4. After the provisioning process has been completed, you will need to go backinto the BIOS and enable "TXT Support". To do this, type "exit" in the com-mand line at the bottom of the screen and press the <Enter> key.Chapter 2: Deploying and Using the TPMC. Enabling TXT SupportThe last step is enabling TXT Support in the BIOS and UEFI shell.1. Go back to the "Advanced" tab in the BIOS and enable Platform Hierarchy,Storage Hierarchy, Endorsement Hierarchy, PH Randomization, and TXTSupport.2. Go back to the "Save & Exit" tab and select "UEFI: Built-in EFI Shell" inthe BIOS. When the confirmation window appears, select <Yes>.Super TPM User's Manual3. After Enabling TXT Support in the BIOS, you will need to run TXT in theUEFI shell. In the Command line at the bottom of the page, type “get-sec64_v2.0.11.efi -l sen -a” and press the <Enter> key. TXT support is now enabled.4. To Exit from the TXT Environment, type “getsec64_v2.0.11.efi -l sexit” inthe command line at the bottom of the screen and press the <Enter> key.Chapter 2: Deploying and Using the TPM2.3 An Important Note to the UserThe graphics shown in this user's guide were based on the latest information available at the time of publishing of this guide. The TPM screens shown on your computer may or may not look exactly like the screen shown in this user's guide.For any further assistance, please refer to our website for details.(Disclaimer Continued)The products sold by Supermicro are not intended for and will not be used in life support systems, medi-cal equipment, nuclear facilities or systems, aircraft, aircraft devices, aircraft/emergency communication devices or other critical systems whose failure to perform be reasonably expected to result in significant injury or loss of life or catastrophic property damage. Accordingly, Supermicro disclaims any and all li-ability, and should buyer use or sell such products for use in such ultra-hazardous applications, it does so entirely at its own risk. Furthermore, buyer agrees to fully indemnify, defend and hold Supermicro harmless for and against any and all claims, demands, actions, litigation, and proceedings of any kind。
THB6064H测试板说明书

THB6064H测试板使用说明书THB6064H测试板是专门针对步进电机驱动芯片THB6064H量身定做的开发板。
其本身就是一款可以直接使用的步进电机驱动器,用户可以直接用来驱动步进电机,同时,还可以为使用THB6064H芯片开发步进电机驱动器的广大用户提供参考及测试平台,用户可以在其基础上设计、调试、定做出自己的驱动器产品。
其主要参数和性能指标如下:1. 信号输入:采用光电隔离器件,直接采用单脉冲和方向信号译码控制模;有CP、DIR、EN,分别为步进脉冲输入、方向信号输入、使能信号输入;2. 电流0.36A~3.45A可调;3. 电流衰减模式可调;4. 两相正弦细分步进电机驱动,细分1/2,1/8,1/10,1/16,1/20,1/32,1/40,1/64可调;5. 电压输入:功率电压DC24~42V,逻辑电压:DC5V;6. 可实现正反转控制;7. 有复位功能;8. 芯片内部有过热保护(TSD)和过流检测电路。
一、引脚说明输入:CLK+/CLK-为脉冲信号输入脚CWW+/CWW-为方向控制信号ENA+/ENA-为脱机控制信号输出:ALERT:工作异常输出信号OUT1A/OUT2A:电机A 相绕组OUT1B/OUT2B:电机B 相绕组电源:VM:电机驱动电源(VM≤42V)GND:电源地二、拨码开关设置细分由三位拨码开关设置的,共有8 档细分选择。
三、驱动电流控制电位器VREF 顺时针旋转Vref 加大,可控制驱动电流增大,反之减小。
此测试板的电流设置范围为:0.36A~3.45A(峰值)。
Io(MAX)=Vref/(3*Rs)Rs 为检测电阻四、衰减模式设定电位器FDT 顺时针旋转Vpfd 加大。
当3.5V<Vpfd<VCC时,为慢衰减模式1.1V<Vpfd<3.1V时,为混合式衰减模式当0<Vpfd<0.8V时,为快衰减模式。
磁性技术的魔法:MT613X omni方向低功耗360度开关IC说明书

3 Product Overview of MT613XOmni-polar, Low Power, 360 Degree Switch ICMT613X1 Product DescriptionThe MT613X family is produced with monolithic technology ,which builds AMR sensor &ASIC on one chip.The IC internally includes a Wheatstone bridge with magnetic film ,a current regulator for operating with supply voltage from 1.65V to 5.0V,a sleep/awake logic for low power consumption requirement,small signal amplifier and Schmitt trigger comparator with dynamic offset cancellation,and an output driver with push pull output.When combined with a magnet,it becomes a non-contact switch with low power consumption,high sensitivity and high reliability.All directions of horizontal magnetic field parallel to the electrode of the package can be detected by an arbitrary polarity.The MT613X family provide SOT-23for surface mount ,RoHS compliant.Part No.DescriptionMT613XATSOT-23, tape & reel (3000pcs/bag)4 Application■Home appliances, Industrial ■Position Detection ■Proximity Switch ■Smart Meter ■Speed Detection ■Handheld Device ■Consumer Device2 Features■Monolithic Technology■360Degree AMR (Anisotropic Magneto Resistance)■Omni-polar Switch■ 1.65~5.0V Operating Vcc Range■-40℃~125℃Operating Temperature ■Package Option:SOT-23■Magnetic Sensitivity Option:B OP =±18Gs,B RP =±13Gs■Push Pull &Open Drain Output Option:MT6131&MT6132:Push Pull MT6133&MT6135:Open Drain ■Operation Frequency Option:MT6131&MT6133:20Hz MT6132&MT6135:1KHz ■Low Power Consumption■RoHS Compliant:(EU)2015/8635. Pin Configurationand FunctionsV CCOut GND SOT-23123DescriptionPowerOutputPush Pull or Open DrainGroundFigure.1Pin Configuration & Functions 按钮SOT-23Top-ViewTO-92Top-ViewOUTVccGND321Table of Contents1Product Description (1)2Features (1)3Product Overview of MT613X (1)4Applications (1)5Pin Configuration and Functions (1)6Definition of Switching Function (3)7Function Description (3)8Feature Description (3)9Functional Block Diagram (4)10Electrical and Magnetic Characteristics (5)10.1Absolute Maximum Ratings (5)10.2Electrical Specifications (5)10.3Magnetic Characteristics (6)10.4ESD Ratings (6)10.5Characteristic Performance (6)10.6Typical Output Waveform (7)11Typical Application Circuit (7)12Power on Output Waveform (8)13Package Material Information (9)13.1SOT-23Package Information (9)14 Copy Rights and Disclaimer (10)Reversion History1Originally Version2 1.1 Version Update supply currentUpdate the marking spec of SOT-236 Definition of Switching FunctionVccNorthSouthFigure.2Omni-polar Switching FunctionFigure.2 shows the device functionality and hysteresis7 Function DescriptionB OP : Operating Point, Magnetic flux density applied on the branded side of the package which turns the output driver ON (V OUT =Low)B RP : Releasing Point, Magnetic flux density applied on the branded side of the package which turns the output driver OFF (V OUT =High )B HYST : Hysteresis Window, |B OP -B RP |8 Feature DescriptionThe MT613X series is sensitive to the magnetic field that is parallel to the package (X & Y axis). To operate the MR switch, the magnetic field should be applied to the sensor parallel to the package. MT613X series detect the magnetic field in any parallel direction, but it does not respond to magnetic field in the vertical direction.Figure.3Detection of magnetic fieldB OP N B RP N B OP SB RP S GND 按钮OUTVcc321Direction of magnetic field(N or S)9 Functional Block DiagramFigure.4Functional Block Diagram (MT6131&MT6132)VccOutGNDRegulatorSleep/AwakeLogicDynamic Offset CancellationAMP COMP Output DriverESDAMRAMRRegulatorSleep/AwakeLogicDynamic Offset CancellationAMP COMP Output DriverESDAMRAMRVccOutGNDFigure.5Functional Block Diagram (MT6133&MT6135)10.2 Electrical SpecificationsAt T A =-40~125℃, V CC =1.65V~5.0V (unless otherwise specified)Symbol Parameters Test Condition Min Typ Max Unit V CCSupply VoltageOperating1.65 3.60 5.00V I CC Supply CurrentMT6131 & MT6133, V CC =3.6V, ∣B∣<∣B RP ∣- 1.0 1.5uA MT6132 & MT6135, V CC =3.6V, ∣B∣<∣B RP ∣-11.015.0uA V OH Output High Voltage MT6131 & MT6132, V CC =5V,I OUT =5mA, ∣B∣>∣B OP ∣4.6--V V OL Output Low Voltage V CC =5V,I OUT =-5mA, ∣B∣>∣B OP ∣--0.4V I OFFOutput Leakage Current V OUT =5V, ∣B∣<∣B RP ∣--0.1uA T POPower on Time dV CC /dt>3.6V/us, B>B OP (MAX)-80120us F OPOperation Frequency MT6131 & MT6133, V CC =3.6V 1020-Hz MT6132 & MT6135, V CC =3.6V 0.5K 1K -Hz T AW Awake Time V CC =3.6V-16-us T SL Sleep Time MT6131 & MT6133, V CC =3.6V -50-ms MT6132 & MT6135, V CC =3.6V -1-ms D.C.Duty CycleMT6131 & MT6133, V CC =3.6V -0.03-%MT6132 & MT6135, V CC =3.6V- 1.50-%R THThermal Resistance of SOT-23-301-℃/W10 Electrical and Magnetic Characteristics 10.1 Absolute Maximum RatingsAbsolute maximum ratings are limited values to be applied individually, and beyond which theserviceability of the circuit may be impaired. Functional operability is not necessarily implied. Exposure to absolute maximum rating conditions for an extended period of time may affect device reliability.Symbol Parameters Min Max Units V CC Supply Voltage-7V V RCC Reverse Battery Voltage -0.4-V V OUT Output Voltage-7V I OUT Continuous Output Current -20mA T A Operating Ambient Temperature -40125℃T S Storage Temperature -50150℃T J Junction Temperature -165℃BMagnetic Flux Density1200Gs10.5 Characteristic PerformanceFigure.6Supply Current vs. TemperatureFigure.7Magnetic Characteristics vs. Temperature (B OP & B RP ) (At V CC =3.6V)Magnetic Field @ 90Degree & 180 DegreePart No.Symbol Min Typ Max Unit MT613X SeriesB OP -±18±28Gs B RP ±3±13-Gs B HYST-5-Gs10.3 Magnetic CharacteristicsAt T A =25℃, V CC =1.65V~5.0V (unless otherwise specified)10.4 ESD Ratings Symbol Reference Values Unit V ESDHuman-body model (HBM)AEC-Q100-0024000V Charged-device model (CDM)AEC-Q100-0111000VMagnetic Characteristics vs. Temperature (B HYST ) (At V CC =3.6V)Magnetic Field @ 90 Degree & 180 DegreeFigure.85101520253035-402585125150M a g n e t i c F i e l d I n t e n s i t y (G s )Bop (90 Degree)Brp (90 Degree)Bop (180 Degree)Brp (180 Degree)℃3691215-402585125150M a g n e t i c F i e l d I n t e n s i t y (G s )Bhyst (90 Degree)Bhyst (180 Degree)℃0.511.522.533.544.55-402585125150S u p p l y C u r r e n t (u A )Vcc=1.65V Vcc=3.6V Vcc=5.0V10.6 Typical Output WaveformMT6131AT as exampleBVTTHighLowFigure.10Digital Output vs. Magnetic Flux Density & Sampling PulseB OP SB RP S B RP N B OP NOnOffM a g n e t i c F l u xS a m p l i n g P u l s eO u t p u tFigure.9360 Degree Magnetic Characteristics (At V CC =3.6V, T A =25 ℃)10.5 Characteristic Performance (continued)Note: Output is not immediately updated until the chip wakes up from sleep mode and samples the input510152025153045607590105120135150165180195210225240255270285300315330345Bop Brp12 Power on Output WaveformV CC rise time < 1us, T PO is the time from the stable point of V CC to the valid point of outputFigure.13Power on Output Waveform∣B∣>∣B OP ∣∣B∣<∣B RP ∣T POM a g n e t i c F l u x V C CO u t p u t11 Typical Application CircuitFigure.11Typical Application Circuit Push Pull Output MT6131 & MT 6132OUTVccGND按钮321C 1=100nFC 2=1nFVccOutGNDFigure.12Typical Application Circuit Open Drain Output MT6133 & MT 6135OUTVccGND按钮321C 1=100nFC 2=1nFVccOutGNDR L = 100k Ω13 Package Material Information (For Reference Only –Not for Tooling Use )13.1 SOT-23 Package InformationFigure.14SOT-23 Chip Marking SpecFigure.15SOT-23 Package DrawingSensing CenterSymbolDimensions in Millimeters Dimensions in Inches MinMaxMinMaxA 1.050 1.2500.0410.049A10.0000.1000.0000.004A2 1.050 1.1500.0410.045b 0.3000.5000.0120.020c 0.1000.2000.0040.008D 2.820 3.0200.1110.119E 1.500 1.7000.0590.067E1 2.6502.9500.1040.116e 0.950 TYP0.037TYPe1 1.800 2.0000.0710.079L 0.3000.6000.0120.024θ0︒8︒0︒8︒x 1.460TYP 0.057 TYP y 0.800 TYP 0.032TYP z0.600 TYP0.024 TYPGND按钮按钮XXXXOUTVcc321Y WXXXX YWDateCode: Y: Year W: Week Product ID14 Copy Rights and Disclaimer1.This document may not be reproduced or duplicated, in any form, in whole or in part without priorwritten consent of MagnTek. Copyrights © 2019, MagnTek Incorporated.2.MagnTek reserves the right to make changes to the information published in this document atanytime without notice.3.MagnTek’s products are limited for use in normal commercial applications. MagnTek’s products arenot to be used in any device or system, including but not limited to medical life support equipment and system.For the latest version of this document, please visit our website: 。
InFit 76Xe系列说明书

InFit®761e/InFit®764e Instruction Manual© It is forbidden to reprint this Instruction Manual in w hole or part. No part of this manual may be repro d u-ced in any form, or modified, copied or distributed using electronic systems, in particular in the form of photo -copies, photographs, magnetic or other recordings, w ithout written consent of Mettler-Toledo GmbH, Process Analytics, CH-8902 Urdorf, Switzerland.All rights reserved, in particular reproduction, trans -lation and patenting/registration.InFit®761e/InFit®764e Instruction ManualExplanation of housing designationsThe generic term InFit 76X e Series used in this Instruction Manual refers to:–InFit 761e– Insertion housing for pH/ Redox electrodes with gel-type or polymer electrolyte, O2, CO2, turbidity and con -ductivity sensors (with 12 mm diameter and Pg 13.5 thread).–InFit 764e– Insertion housing for pressu-rized pH/Redox electrodes with liquide lectrolyte (such as InPro 2000).Use in Ex classified areas (hazardous areas) Ex classification II 1/2GD IIC T6/T5/T4/T3 IP6X T 69 °C / T 81 °C / T 109 °C / T 161 °C4 Installation and start-up (45)4.1 Preparation of the equipment (45)4.2 Fitting and installation work (47)4.2.1 Fitting the housing (47)4.2.1.1 Fitting with a weld-in socket (47)4.2.1.2Fitting with a flange (48)4.2.1.3Fitting via NPT external thread (48)4.2.1.4Fitting with Tri-Clamp andVarivent flange connection (48)4.2.1.5Installation with NPSM thread (49)4.2.2Fitting the electrode/sensor (49)4.2.2.1InFit 761 e (49)4.2.2.2 InFit 764 e (51)4.3 Startup procedures for housings (53)4.4 Dismantling work (54)4.4.1 Removing the insertion housing (54)4.4.2 Removing the electrode/sensor (54)4.5 Sterilization (57)5 Operation (58)5.1 Important information for everyday operation (58)5.2 Inspection work in everyday operation (58)5.3 Cleaning the electrode/sensor (59)5.4 Calibrating the measuring system (59)6 Maintenance (60)6.1 Important information on maintenance (60)6.2 Topping up reference electrolyte (61)6.3 Replacement of medium-wetted seals (61)7Trouble shooting (64)8Product specifications (66)8.1 Technical data (66)8.1.1Technical specifications InFit 761 e (66)8.1.2Technical specifications InFit 764 e (68)8.2 Spare parts and accessories (70)9 Terms of warranty (74)10 Decommissioning, storage, disposal (75)10.1 Decommissioning (75)10.1.1 Proceed as described in Section 4.4«Dismantling work» (75)10.1.2 Repair (75)10.2 Storage (75)10.3 Disposal (76)11 Appendices (77)11.1 Electrode/sensor selection (77)wetted parts made of metallic material.Ex classification: II 1/2GD IIC T6/T5/ T4/T3 IP6X T 69 °C/T 81 °C/T 109 °C/ Ex classification II 1/2GD IIC T6/ 4/T3 IP6X T 69°C/T 81 °C/T 109°C/1.2.1Ex classification «FM Approved»(drawing)2.3.2 Type conformity (Module C1) inaccordance with directive 97/23/ECCertificate according to ATEX (page 2 of 2)FM certificate (page 2 of 7):FM certificate (page 4 of 7):FM certificate (page 6 of 7):2.6 Housing designationsHousing designation as well as part andserial numbers can be noted from the typep late and used for clear identification whencommunicating with the manufacturer.Attention:The specifications shown on thet ype plate are dependent on the design and theindividual type of housing and have nogeneral validity for the complete InFit productrange.Label type 1:Type plate in accordance with Ex directiveLabel type 2:Type plate for Ex housings in accordanceLabel type 3:Type plate for non-Ex housings in accordanceLabel type 4:Type plate for non-Ex housings inaccordance with PED directive 97/23/ECsymbolplate have received approval for operation inDanger!Plastic housings may not be used in applications subject to high mechanical stress as this could break the protective cage.2.12.4 Installation in pressurized systemsAttention:The specified maximum tempe -rature and pressure must not be exceeded. The respective specifications depend on the design and type of housing and are given on the i ndividual type plates.Danger!If temperature and pressure limits are exceeded, there is a risk to the integrity of the system, thus presenting a potential threat to human life and to the environment.Attention:Ample specifications of maximum admissible temperature and pressure are g iven in «Section 8».2.12.5 Installation in potentially explosiveareas (hazardous areas)Attention:–It should be considered to include the METTLER TOLEDO insertion housing InFit 76X e and the process connections inyour recurring pressure test program for thecomplete plant as a whole.–The operator must ensure that the housing can be used safely in conjunction witho ther associated plant resources.–The insertion housing and the processc onnections must be connected to the main potential equalization system of theplant (see drawing below).Connection of the housing to the potentialequalization system of the plant.InFit®76X e Series37Electrode/sensor type1pH/Redox electrodes, O 2, CO 2, turbidity and conductivity s 4pH/Redox electrodes with liquid electrolyteProtecti ve cage W S ensor holder with protective cageN S ensor holder without protective cageSensor h olderY Ø 19 mm sha f tS Ø 25 mm sha f tC Ø 25 mm C I P sha f t without protective cageK N P T sha f tImmersion lengt h =H, (depending on002525 mm immersion len03333 mm immersion len004040 mm immersion len007070 mm immersion len0100100 mm immersion le0150150 mm immersion le0175175 mm immersion le0200200 mm immersion le0275275 mm immersion le0375375 mm immersion lM aterial (w etted4435C 22−T I −−P P −−P V D FInFit ///8910111213141516171819202121)Cap nut made of DIN 1.4435 (height = 18), cap nut mad and for the sensor holder type «C» made of DIN 1.4435 (2)Hexagon nut made of DIN 1.4305 (height = 18)3)Cap nut made of brass (height = 18)sensors (Ø 12 mm and Pg 13.5 thread)v ersion w it h/w it h out protecti v e cage ±5mm) ngth (only f or sensor holder type «C»)ngth (only f or sensor holder type «C»)ngthngthengthengthengthengthengthlengthparts)D IN 1.4435D IN 2.4602/A lloy C22T itaniumPolypropylenePolyvinylidene f luorideProcess connectionsD00I ngold D N25 1)D10I ngold D N25 2)D11I ngold D N25 3)D04F lange D N50-P N16 (Ø 25 mm sha f t)P01S oc k et D N19M26x1P023/4" R/N P S M (Ø 19 mm sha f t)P29S oc k et D N25 groove pos. 43.6 (type «C»)N0 4 N P T3/4"N01N P T 1"T01T ri-Clamp f lange 1.5" straightT02T ri-Clamp f lange 2" straightT03T ri-Clamp f lange 1.5" inclinedV01V arivent f lange D N50 straightV02V arivent f lange D N50 inclinedO-ring materialV i F K M V iton®F D AE P E P D MF D AK a FF K M K alre z®6230F D A/U S P Class V IS i M V Q S ilicone F D A/U S P Class V IO-ring position−no groove222.4 groove distance424.5groove distance929 groove distanceS S pecial groove distanceSpecial−S tandardS S pecial//222324252627282930A ppropriate sensor lengthsf or the immersion lengths,please re f er to the S ection 11«E lectrode/sensor selection». de of plastic, cap nut for security socketheight = 22)。
MAX32680 芯片评估板用户指南说明书

MAX32680EVKIT#Evaluates: MAX32680MAX32680 Evaluation Kit General DescriptionThe MAX32680 evaluation kit (EV kit) provides a plat-form for evaluation capabilities of the MAX32680 micro-controller, which is an advanced system-on-chip (SoC) designed for industrial and medical sensors. Power regu-lation and management is provided by a single-inductor multiple-output (SIMO) buck regulator system and con-tains the latest generation Bluetooth ® 5.2 Low Energy (LE) radio.EV Kit Contents●MAX32680 EV Kit Containing a MAX32680 with aPreprogrammed Demo ●MAX32625PICO Debugger w/Cables ●One USB Standard-A-to-Micro-B CableFeatures●SMA Connector for Attaching an External BluetoothAntenna ●128 x 128 (1.45in) Color TFT Display with SPIInterface ●Two Selectable On-Board, High-Precision VoltageReferences ●USB 2.0 Micro B to Serial UARTs●UART1 and LPUART0 Interface is SelectableThrough On-Board Jumpers ●All GPIOs Signals Accessed Through 0.1in Headers ●Access to Four Analog Inputs Through SMAConnectors Configured as Differential●Access to Eight Analog Inputs Through 0.1in HeadersConfigured as Single-End ●Optional Discrete Filter for the Twelve Analog Inputs ●DAC Accessed Through SMA Connector or T est Point ●10-Pin SWD Connector ●10-Pin RV JTAG Connector ●Board Power Provided by USB Port●On-Board 3.3V LDO Regulator to Power MAX32680Internal SIMO ●Test Loops Provided to Supply Optional VCOREPower Externally ●Individual Power Measurement on All IC RailsThrough Jumpers ●Two General Purpose LEDs and Two GeneralPurpose Pushbutton Switches319-100801; Rev 0; 8/21Ordering Information appears at end of data sheet.The Bluetooth word mark and logos are registered trademarks owned by Bluetooth SIG, Inc. and any use of such marks by Maxim is under license.Click here to ask about the production status of specific part numbers.Evaluates: MAX32680 MAX32680 Evaluation KitQuick StartRequired Equipment●MAX32680 EV kit containing a MAX32680 with apreprogrammed demo●One USB Standard-A-to-Micro-B cable ProcedureThe EV kit is fully assembled and tested. Follow the steps below to verify board operation:1) While observing safe electrostatic discharge (ESD)practices, carefully remove the MAX32680 EV kitboard out of its packaging. Inspect the board toensure that no damage occurred during shipment.Jumpers/shunts are preinstalled prior to testing andpackaging.2) Power up the board by plugging in the providedUSB cable to connector CN1. Verify that the VBUSblue LED (DS1) and the 3V3 (DS2) green LED areilluminated.3) The MAX32680 is preprogrammed with a demoprogram. The program now initiates and displays the Maxim logo upon successful completion.Detailed Description of Hardware(or Software)Bluetooth 5.2 InterfaceThe SMA connector (J2) is provided to attach an external Bluetooth 2.4GHz antenna.Power SupplyThe EV kit is powered by +5V which is made available through VBUS on the Micro-USB type-B connector CN1. When the power switch SW3 is in the on position, the blue VBUS LED (DS1) and the green 3.3V LED (DS2) illuminate. The 3.3V powers the SIMO of the MAX32680. Current MonitoringA two-pin header VBAT EN (JP1) provides a convenient current monitoring point for the 3.3V LDO powering the MAX32680. If the jumper is removed, power can be sourced externally.Low-Power Mode Current MeasurementsTo accurately achieve the low power current values, the EV kit needs to configure such that no outside influence (i.e., pullups, external clock, debugger connector, etc.)causes a current source or sink on that GPIO. MAX32680 EV Kit BoardEvaluates: MAX32680 MAX32680 Evaluation KitFor these measurements, the board is needed to be con-figured as follows:1) Remove jumpers JP8, JP9, JP10, JP11, JP12, JP14,JP22, JP23, and JP24.2) Unplug the SWD connector at JH10.3) Unplug the RV JTAG connector at JH11.ClockingThe MAX32680 clocking is provided by an external 32MHz crystal (Y1).Voltage Reference SelectionThe external voltage reference inputs REF0P, REF0N, REF1P, and REF1N for the analog-to-digital converters (ADCs) can be sourced externally by high precision exter-nal reference sources, MAX6071 (U2 and U3), REF0P (JP2), and REF1P (JP6) or internally by VDDA.JTAG Serial Wire Debug (SWD) SupportThe SWD debug can be accessed through a Cortex®10-pin connector (JH10). Logic levels are set to 1.8V (VDDIO_AUX).JTAG RISC V Debug (SWD) SupportThe JTAG RISC V debug can be accessed through a Cortex 10-pin connector (JH11). Logic levels are set to 1.8V (VDDIO_AUX).UART InterfaceThe EV kit provides a USB-to-UART bridge chip, FTDI FT230XS-R. This bridge eliminates the requirement for a physical RS-232 COM port. Instead, the IC’s UART access is through the Micro-USB type-B connector, CN1. The USB-to-UART bridge can be connected to the ICs UART1 or LPUART with jumpers JP22 (RX) and JP23 (TX). Virtual COM port drivers and guides for installing Windows® drivers are available at the FTDI chip website.GPIO and Alternate Function HeadersThe GPIO and Alternate Function signals from the MAX32680 can be accessed through 0.1in spaced headers JH1 through JH5.Analog HeadersThe four analog inputs (AIN0–AIN3) are accessed through differential SMA connectors J3 and J4 or test loops TP3 through TP5. The eight analog inputs (AIN4–AIN11) are accessed single-ended through 0.1in head-ers JH6 and JH7.DAC12 OUTThe DAC12 output can be accessed through SMA connector J1 or test loop (TP1).I2C PullupsThe I2C ports can be independently pulled up to 1.8V (VDDIO_AUX) or 3.3V through JP8 and JP9.Reset PushbuttonThe IC can be reset by pushbutton SW4.Indicator LEDsGeneral purpose indicators LED D1 (red) is connected to GPIO P0.24 and LED D2 (green) is connected to GPIO P0.25.GPIO Pushbutton SwitchesThe two general purpose pushbuttons SW1 and SW2 are connected to GPIO P0.26 and P0.27, respectively. If the pushbutton is pressed, the attached port pin is pulled low.Cortex is a registered trademark of ARM Limited (or its subsidiaries) in the US and/or elsewhere. Windows is a registered trademark and registered service mark of Microsoft Corporation.Evaluates: MAX32680 MAX32680 Evaluation KitTable 1. MAX32680 EV Kit Jumper SettingsJUMPER SIGNAL SETTINGS DESCRIPTIONJP1VREGIOpen Disconnects 3.3V power from the MAX32680 SIMO Close*Connects 3.3V power to the MAX32680 SIMOJP2REF0P 2-1*Connects the external high-precision voltage refernce to REF0P 2-3Connects the internal voltage refernce to REF0PJP3REF0N Open*Disconnects REF0N from ground Close Connects REF0N to groundJP4VDDIO_AUX Open*Disconnects VDDIO_AUX from pull-ups and reference voltages Close Connects VDDIO_AUX to pull-ups and reference voltagesJP5VDDIOH Open*Connects VREGO_A to VDDIOHClose Connects the 3.3V from the estrenal LDO to VDDIOHJP6REF1P 2-1*Connects the external high-precision voltage refernce to REF1P 2-3Connects the internal voltage refernce to REF1PJP7REF1N Open*Disconnects REF1N from ground Close Connects REF1N to groundJP8I2C0_SDAI2C0_SCL2-1Connects I2C0 pullups to VDDIO_AUX (1.8V)2-3Connects I2C0 pullups to 3.3VJP9I2C1_SDAI2C1_SCL2-1Connects I2C1 pullups to VDDIO_AUX (1.8V)2-3Connects I2C1 pullups to 3.3VJP10P0_24Open Disconnects red LED D1 from P0_24 Close*Connects red LED D1 to P0_24JP11P0_25Open Disconnects green LED D2 from P0_25 Close*Connects green LED D2 to P0_25JP12FSK_IN Open Disconnects FSK_IN from HART analog circuitry Close*Connects FSK_IN to HART analog circuitryJP13RCV_FSK Open*Disconnects RCV_FSK from CC LOOP Close Connects RCV_FSK to CC LOOPJP14FSK_OUT Open Disconnects FSK_OUT from HART analog circuitry Close*Connects FSK_OUT to HART analog circuitryJP15RCV_FSK Open Disconnects RCV_FSK from XFMR LOOP Close*Connects RCV_FSK to XFMR LOOPJP16RLOAD Open*Disconnects 249 ohm resistor shunt from CC LOOP Close Connects 249 ohm resistor shunt to CC LOOPJP17FSK AMP GAIN Open*Enables FSK variable amp gain Close Disables FSK variable amp gainJP18AMP BYPASS 2-1*Enables FSK amp 2-3Bypasses FSK ampJP19FSK AMP GAIN Open*Enables FSK fixed amp gain Close Disables FSK fixed amp gainEvaluates: MAX32680MAX32680 Evaluation Kit Table 1. MAX32680 EV Kit Jumper Settings (continued)*Default position.#Denotes RoHS compliance.JUMPER SIGNAL SETTINGS DESCRIPTIONJP20HART_RTS Open*Enables HART_RTS optical transceiver Close Bypasses HART_RTS optical transceiverJP21RLOAD Open Disconnects 249 ohm resistor shunt from XFMR LOOP Close*Connects 249 ohm resistor shunt to XFMR LOOPJP22UART0_RX 2-1*Disconnects the USB - serial bridge from UART1_RX (P0.12)2-3Connects the USB - serial bridge to LPUART_RX (P2.6)JP23UART0_TX 2-1*Disonnects the USB - serial bridge from UART1_TX (P0.13)2-3Connects the USB - serial bridge to LPUART_TX (P2.7)JP24HART_IN Open Disconnects TX of USB - serial bridge from HART_IN (P0.1)HART_IN 1-2*Connects TX of USB - serial bridge to HART_IN (P0.1)HART_OUTOpen Disconnects RX of USB - serial bridge from HART_OUT (P0.0)HART_OUT 2-3*Connects RX of USB - serial bridge to HART_OUT (P0.0)HART_RTS Open Disconnects RTS of USB - serial bridge from HART_RTS (P0.3)HART_RTS 3-4*Connects TX of USB - serial bridge to HART_RTS (P0.3)HART_OCD Open Disconnects RTS of USB - serial bridge from HART_OCD (P0.2)HART_OCD4-5*Connects TX of USB - serial bridge to HART_OCD (P0.2)JP25RSTNOpen*Disconnects DUT_3V3_RSTN from RSTN CloseConnects DUT_3V3_RSTN to RSTNPART TYPE MAX32680EVKIT#EV KitOrdering InformationEvaluates: MAX32680 MAX32680 Evaluation KitMAX32680 EV Kit Bill of MaterialsQTY VALUE PART REFERENCE BOM_DESCRIPTION MANUFACTURER_PN MANUFACTURER 12100nF C1 C2 C5 C13 C14 C21 C33 C42 C46 C58 C68 C70CAP CER 0.1UF 16V 10% X7R 0402GRM155R71C104KA88D Murata Electronics 121uF C3 C11 C12 C15 C16 C17 C18 C20 C23 C26 C49 C56CAP CER 1UF 16V 10% X5R 0402GRT155R61C105KE01D Murata Electronics 147uF C4CAP CER 47UF 6.3V 20% X5R 0805C2012X5R0J476M125AC TDK Corporation1 3.3nF C6CAP CER 3300PF 16V 10% X7R 0402GRM15XR71C332KA86D Murata Electronics422uF C7 C8 C9 C10CAP CER 22UF 6.3V 20% X5R 0603C1608X5R0J226M080AC TDK Corporation 3100nF C19 C22 C24CAP CER 0.1UF 6.3V 10% X5R 0201GRM033R60J104KE19D Murata1100pF C25CAP CER 100PF 50V +/-1% NP0 040204025A101FAT2A AVX Corporation 212pF C27 C29CAP CER 12PF 50V 5% NP0 0402CL05C120JB5NNNC Samsung Electro1 4.7uF C28CAP CER 4.7uF 10V 10% X5R 0603C0603C475K8PACTU Kemet21nF C30 C31CAP CER 1000PF 10V 10% X7R 0402C0402C102K8RACTU Kemet13DNI C32 C34 C35 C36 C37 C38 C39 C40 C41 C43 C44 C45 R41DNI1 2.2nF C47CAP CER 2200PF 50V 5% NP0 0805GRM2165C1H222JA01D Murata Electronics110nF C48CAP CER 10000PF 50V 5% NP0 0805GRM2195C1H103JA01D Murata Electronics2 4.7uF C50 C52CAP CER 4.7UF 25V 10% X7R 0805CGA4J1X7R1E475K125AC TDK Corporation333nF C51 C53 C59CAP CER 0.033UF 10V 10% X7R 0603C0603C333K8RACTU Kemet1 2.2uF C54CAP CER 2.2uF 10V 10% X5R 0603C0603C225K8PACTU Kemet1 2.2uF C55CAP CER 2.2UF 50V 10% X7R 1206GRM31CR71H225KA88L Murata Electronics1100nF C57CAP CER 0.1uF 16V 10% X7R 0603C0603C104K4RACTU Kemet110nF C60CAP CER 10000PF 25V 10% X7R 0603CL10B103KA8NNNC Samsung Electro 110uF C61CAP CER 10UF 6.3V 20% X5R 0603GRM188R60J106ME84D Murata Electronics 4100nF C62 C63 C64 C67CAP CER 0.1UF 10V 10% X5R 0402GRM155R61A104KA01D Murata11uF C65CAP CER 1UF 35V 10% X5R 0603GMK107BJ105KA-T Taiyo Yuden110uF C66CAP CER 10UF 6.3V 20% X5R 0402GRJ155R60J106ME11D Murata Electronics 110nF C69CAP CER 10000PF 16V 10% X7R 0402GRM155R71C103KA01D Murata Electronics 1MICRO USB B R/A CN1CONN RCPT 5POS MICRO USB B R/A47346-0001Molex1RED D1LED 660NM RED WTR CLR 1206 SMD SML-LX1206SRC-TR Lumex Opto2GRN D2 DS2LED 565NM WTR CLR GREEN 1206 SMD SML-LX1206GC-TR Lumex Opto2SMCJ36CA D3 D4TVS DIODE 36VWM 58.1VC SMC SMCJ36CA Littelfuse Inc1BLUE DS1LED 469NM BLUE DIFF 1206 SMD HSMR-C150Avago Technologies 6DNI H1 H2 H3 H4 H5 H6DNI MTG 125DRL 300PAD3SMA RA J1 J3 J4CONN SMA JACK R/A 50 OHM PCB142-0701-301Cinch Connectivity 1SMA J2CONN SMA JACK STR 50 OHM PCB901-10112Amphenol RF 1503480-1000J5CONN FFC FPC 10POS 0.50MM R/A503480-1000 Molex, LLC49P 1x9JH1 JH2 JH3 JH4CONN HEADER .100 SINGL STR 9POS PEC09SAAN Sullins15P 1x5JH5CONN HEADER .100 SINGL STR 5POS PEC05SAAN Sullins26P 1x6JH6 JH7CONN HEADER .100 SINGL STR 6POS PEC06SAAN Sullins22P 3.5mm JH8 JH9TERM BLOCK 3.5MM VERT 2POS PCB OSTTE020161On Shore Technology 210P CORTEX DEBUG JH10 JH11IDC BOX HEADER 0.050 10 POS SMD3220-10-0300-00CNC Tech16JUMPER JP1 JP3 JP4 JP7 JP10 JP11 JP12 JP13 JP14 JP15 JP16 JP17JP19 JP20 JP21 JP25CONN HEADER .100 SINGL STR 2POS PEC02SAAN Sullins73P 3x1JP2 JP5 JP6 JP8 JP9 JP22 JP23CONN HEADER .100 SINGL STR 3POS PEC03SAAN Sullins13P JUMPER JP18CONN HEADER .100 SINGL STR 3POS PEC03SAAN Sullins18P 2x4JP24CONN HEADER .100 DUAL STR 8POS PEC04DAAN Sullins1 2.2uH L1FIXED IND 2.2UH 1A 150 MOHM SMD 0805MLP2012H2R2MT0S1TDK Corporation1HZ1206C202R-10L2FERRITE CHIP SIGNAL 2000 OHM SMD HZ1206C202R-10Laird-Signal Integrity 1BLM21PG221SN1D L3FERRITE CHIP 220 OHM 0805BLM21PG221SN1D Murata Electronics 1PCB PCB11FDV304P Q1MOSFET P-CH 25V 460MA SOT-23FDV304P Fairchild1TLP3545(F)Q2PHOTOCOUPLER PHOTORELAY 6-DIP TLP3545(F)ToshibaEvaluates: MAX32680 MAX32680 Evaluation KitMAX32680 EV Kit Bill of Materials (continued)QTY VALUE PART REFERENCE BOM_DESCRIPTION MANUFACTURER_PN MANUFACTURER190R1 R6 R7 R8 R10 R11 R12 R13 R14 R15 R16 R17 R18 R19 R20R22 R23 R29 R54RES SMD 0 OHM JUMPER 1/10W 0603RC0603JR-070RL Yageo4 2.21K R2 R3 R4 R5RES SMD 2.21K OHM 1% 1/10W 0402ERJ-2RKF2211X Panasonic2 4.75K R9 R21RES 4.75K OHM 1/10W 1% 0603 SMD ERJ-3EKF4751V Panasonic2100R24 R25RES SMD 100 OHM 1% 1/10W 0603RC0603FR-07100RL Yageo2470R26 R50RES 470 OHM 1/10W 1% 0603 SMD ERJ-3EKF4700V Panasonic2332R27 R52RES 332 OHM 1/10W 1% 0603 SMD ERJ-3EKF3320V Panasonic110K R28RES 10K OHM 1/10W 1% 0603 SMD ERJ-3EKF1002V Panasonic10R30RES SMD 0 OHM JUMPER 1/10W 0603RC0603JR-070RL Yageo1 1.58K R31RES 1.58K OHM 1/10W 1% 0603 SMD ERJ-3EKF1581V Panasonic1221K R32RES 221K OHM 1/10W 1% 0603 SMD ERJ-3EKF2213V Panasonic1301K R33RES 301K OHM 1/10W 1% 0603 SMD ERJ-3EKF3013V Panasonic210R34 R42RES 10 OHM 1/10W 1% 0603 SMD ERJ-3EKF10R0V Panasonic2249R35 R40RES 249 OHM 1W 1% 2512 SMD MCR100JZHF2490Rohm Semiconductor 149.9R36RES 49.9 OHM 1/10W 1% 0603 SMD ERJ-3EKF49R9V Panasonic1100K R37TRIMMER 100K OHM 0.125W SMD3223W-1-104E Bourns Inc.2100K R38 R44RES 100K OHM 1/10W 1% 0603 SMD ERJ-3EKF1003V Panasonic110K R39RES 10K OHM 1/10W 1% 0603 SMD ERJ-3EKF1002V Panasonic21K R43 R45RES 1K OHM 1/10W 1% 0603 SMD ERJ-3EKF1001V Panasonic227R46 R47RES 27 OHM 1/10W 1% 0603 SMD ERJ-3EKF27R0V Panasonic1 1.5K R48RES SMD 1.5K OHM 1% 1/10W 0402ERJ-2RKF1501X Panasonic11M R49RES SMD 1M OHM 5% 1/8W 0805ERJ-6GEYJ105V Panasonic1 2.7K R51RES 2.7K OHM 1/10W 1% 0603 SMD ERJ-3EKF2701V Panasonic110K R53RES SMD 10K OHM 1% 1/16W 0402RC0402FR-0710KL Yageo6DNI SH1 SH2 SH3 SH4 SH5 SH6DNI 2 NET SHORT3B3S-1000P SW1 SW2 SW4SWITCH TACTILE SPST-NO 0.05A 24V B3S-1000P Omron Electronics1SPDT 3A SW3SWITCH TOGGLE SPDT 3A 120V ET01MD1AGE C&K Components1MET-26T1TRANSFORMER 1KCT:1KCT 3.0MADC MET-26Tamura1BRWN TP1TEST POINT PC MULTIPURPOSE BRWN5125Keystone Electronics 2BLUE TP2 TP3TEST POINT PC MULTI PURPOSE BLUE5127Keystone Electronics 2YLW TP4 TP5TEST POINT PC MULTI PURPOSE YEL5014Keystone Electronics 3BLK TP6 TP7 TP8TEST POINT PC MULTI PURPOSE BLK5011Keystone Electronics 1GRN TP9TEST POINT PC MULTI PURPOSE GRN5126Keystone Electronics 1WHT TP10TEST POINT PC MULTI PURPOSE WHT5012Keystone Electronics 1MAX32680 88P LGA U1MAX32680 88P LGA MAX32680 Maxim Integrate2MAX6071AAUT21+T U2 U3IC VREF SERIES 0.04% SOT23-6MAX6071AAUT21+T Maxim Integrated1DS1233AZ-10+T&R U4IC SUPERVISOR 1 CHANNEL SOT223-3DS1233AZ-10+T&R Maxim Integrate1CFAF128128B1-0145T U5LCD TFT Full Color 1.45" 128x128CFAF128128B1-0145T Crystalfontz1MAX4166EUA+U6IC OPAMP GP 5MHZ RRO 8UMAX MAX4166EUA+Maxim Integrated1FT2232D-REEL U7IC USB FS DUAL UART/FIFO 48-LQFP FT2232D-REEL FTDI1MAX3207EAUT+T U8ESD PROT DIFF SOT23-6MAX3207EAUT+T Maxim Integrated1MAX1806EUA33+U9IC REG LDO 3.3V/ADJ 0.5A 8UMAX MAX1806EUA33+Maxim Integrated1NL27WZ07DFT2G U10IC BUFFER NON-INVERT 5.5V SC88NL27WZ07DFT2G ON Semiconductor 132 MHZ Y1CRYSTAL 32.00 MHZ 12PF SMD FA-20H 32.0000MF12Y-W3EPSON16MHz Y2CRYSTAL 6MHZ 18PF SMD ABMM-6.000MHZ-B2-T Abracon CorpEvaluates: MAX32680 MAX32680 Evaluation KitEvaluates: MAX32680 MAX32680 Evaluation KitMaxim Integrated cannot assume responsibility for use of any circuitry other than circuitry entirely embodied in a Maxim Integrated product. No circuit patent licenses are implied. Maxim Integrated reserves the right to change the circuitry and specifications without notice at any time.REVISION NUMBER REVISION DATEDESCRIPTIONPAGESCHANGED8/21Initial release—Revision HistoryFor pricing, delivery, and ordering information, please visit Maxim Integrated’s online storefront at https:///en/storefront/storefront.html.MAX32680EVKIT#。
MEMORY存储芯片MT46V32M8TG-6TC中文规格书

Electrical SpecificationsStresses greater than those listed may cause permanent damage to the device. This is astress rating only, and functional operation of the device at these or any other condi-tions above those indicated in the operational sections of this specification is not im-plied. Exposure to absolute maximum rating conditions for extended periods may affectreliability.Table 7: Absolute Maximum RatingsTable 8: DC Electrical Characteristics and Operating ConditionsNotes: 1.All voltages referenced to V SS .2.The minimum specifications are used only to indicate cycle time at which proper opera-tion over the full temperature range is ensured; (0°C ื T A ื +70°C (commercial), –40°C ืT A ื +85°C (industrial), and –40°C ื T A ื +105°C (automotive)).3.An initial pause of 100˩s is required after power-up, followed by two AUTO REFRESHcommands, before proper device operation is ensured. (V DD and V DDQ must be poweredup simultaneously. V SS and V SSQ must be at same potential.) The two AUTO REFRESHcommand wake-ups should be repeated any time the t REF refresh requirement is excee-ded.4.V IH overshoot: V IH,max = V DDQ + 2V for a pulse width ื3ns, and the pulse width cannotbe greater than one-third of the cycle rate. V IL undershoot: V IL,min = –2V for a pulsewidth ื3ns.64Mb: x4, x8, x16 SDRAM Electrical SpecificationsElectrical Specifications – AC Operating ConditionsTable 12: Electrical Characteristics and Recommended AC Operating Conditions64Mb: x4, x8, x16 SDRAM Electrical Specifications – AC Operating Conditions。
MEMORY存储芯片MT46V16M16TG-6TITF中文规格书
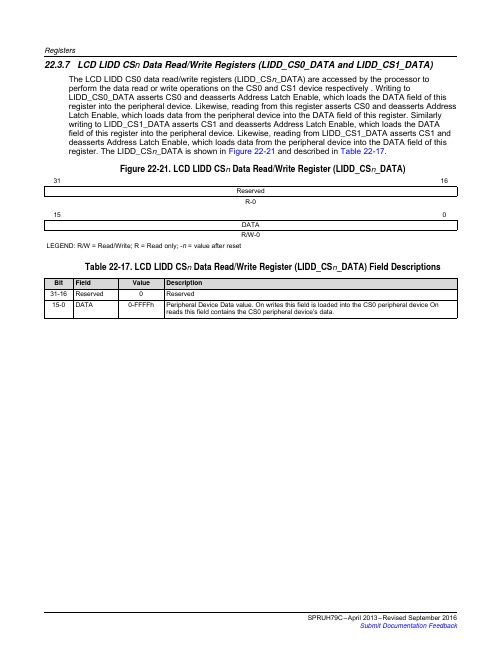
Registers22.3.7LCD LIDD CS n Data Read/Write Registers(LIDD_CS0_DATA and LIDD_CS1_DATA)The LCD LIDD CS0data read/write registers(LIDD_CS n_DATA)are accessed by the processor toperform the data read or write operations on the CS0and CS1device respectively.Writing toLIDD_CS0_DATA asserts CS0and deasserts Address Latch Enable,which loads the DATA field of this register into the peripheral device.Likewise,reading from this register asserts CS0and deasserts Address Latch Enable,which loads data from the peripheral device into the DATA field of this register.Similarly writing to LIDD_CS1_DATA asserts CS1and deasserts Address Latch Enable,which loads the DATAfield of this register into the peripheral device.Likewise,reading from LIDD_CS1_DATA asserts CS1and deasserts Address Latch Enable,which loads data from the peripheral device into the DATA field of this register.The LIDD_CS n_DATA is shown in Figure22-21and described in Table22-17.Figure22-21.LCD LIDD CS n Data Read/Write Register(LIDD_CS n_DATA) 3116ReservedR-0150DATAR/W-0LEGEND:R/W=Read/Write;R=Read only;-n=value after resetTable22-17.LCD LIDD CS n Data Read/Write Register(LIDD_CS n_DATA)Field Descriptions Bit Field Value Description31-16Reserved0Reserved15-0DATA0-FFFFh Peripheral Device Data value.On writes this field is loaded into the CS0peripheral device Onreads this field contains the CS0peripheral device's data.SPRUH79C–April2013–Revised September2016Submit Documentation FeedbackLCD_PCLKLCD_D[x:0]LCD_HSYNCLCD_VSYNCLCD_PCLKLCD_D[x:0]LCD_HSYNCLCD_VSYNCRegistersSPRUH79C–April 2013–Revised September 2016Submit Documentation Feedback22.3.8.3TFT_STN (TFT_STN)The TFT_STN (TFT_STN)bit selects whether the LCD controller operates in passive (STN)or active(TFT)display control mode.When TFT_STN =0,passive or STN mode is selected.LCD data flows from the frame buffer memory,via the LCD dedicated DMA channel,to the palette (the palette is bypassed for the 12and 16BPP modes),to the dithering logic and the output FIFO before being output on the LCD data pins.The clock and data pin behaviors is shown for the monochrome passive mode (Figure 22-23)and for the color passive mode (Figure 22-24).Figure 22-23.Monochrome Passive Mode Pixel Clock and Data Pin TimingFigure 22-24.Color Passive Mode Pixel Clock and Data Pin Timing。
PANASONIC TH63 TH64 说明书

Rated operating voltage Part No. Rated operating voltage Part No. Rated operating voltage Part No.
TH63 types (without reset)
100V AC 200V AC 12V AC
TH631 TH632 TH633
24V AC 48V AC 110V AC
TH634 TH635 TH636
115 to 120V AC 220V AC 240V AC
TH637 TH638 TH639
TH64 types (with reset)
100V AC 200V AC 12V AC
TH641 TH642 TH643
24V AC 48V AC 110V AC
the
panel.
2. Swing the mounting spring to the rear
of the hour meter and fit the hour
meter into the panel opening. (There
is no need to detach the mounting
Min 98 m/s2 {10 G} (4 times on 3 axes) Min 980 m/s2 {100 G} (5 times on 3 axes)
–10 to +50°C +14 to +122°F Max. 85% RH
Approx. 80 g 2.82 oz
PRODUCT TYPE
Type
TYPICAL APPLICATIONS
Management of small generators and food processing machines; hour counting for leased equipment; maintenance management of various equipment, etc.
GMA3600,Windows64bitssupport

GMA3600,Windows64bitssupportDiegoThis means, you guys have 64 bit drivers! Already exists! Proof has been made.Now, yes it was buggy but you guys had to already use it as a base line template code to produce the 64 bit drivers for the graphics core in the newer Intel Atom z whatever which is PowerVR architecture. The exact VERY SAME architecture that is the GMA 3650. In fact, the GMA 3650 is mere a faster and slightly better HARDWARE wise in that it has a higher clock rate and a superior overall technical specifications.So, why is it that Intel doesn't get the _____ done!First off.... basic computer science 101 for you, all drivers for a video chip boils down to communicating to machine level and transmitting values to the graphics chip (in this case, integrated onto the same die as the cpu but it is not the cpu, EITHER ) registers. When you write drivers on a multitask OS, you go through APIs which all boils down to ultimately to the registers of the video chip. Since we are talking about a 'GPU' then we are talking about something kind of like an ADVANCED form of the TMS9918 Video Display Processor - an early pioneer of 'Graphic Processors'. Unlike other video display chips of its time and even for several years since its introduction, it was a 'PROCESSOR' vs. simply a memory mapped register switch 'table'. You actually had a 'graphic processor machine language' much like a microprocessor. After all, the TMS 9918 was essentially a microprocessor like the TMS9900 microprocessor with which the 9918 had special registers and instructions and functionality particularly designed and built for graphics. Fast forward some30+ years and today's graphics are in themselves actual 'processors' and not just a bunch of registers that can be given values and do something. There is an actual graphic processor 'machine language' to these graphic chips. From my understanding, the PowerVR based graphics processor is speaking the same 'machine language' in current intel atom processors and the GMA3650 graphic processor integrated in the Intel D2700. Besides memory mapped registers and GPU processing languages are in most part the same. The drivers should almost work right out of the box for any PowerVR based GPUs.FWIW: WDDM is simply an abstraction layer. You guys already made WDDM 1.2 compliant drivers for current PowerVR-based graphics. So, what's the deal? Why can't it work? Come on? Your very source code for graphics drivers for Intel z2760 is already 95-99% correct for making the D2700 work. You just need to relabel some IDs so as to match the D2700 'id' and maybe a few modest changes and timing adjustments to deal with the clock rate difference of the D2700's GMA3650 and the z2760.You may also have a few register memory mapped location differences but come on. Easy to make the changes for.... for a software programmer.REALLY... what's the barrier. After all, you have 32-bit drivers for Windows 7... oh.. wait.. that's WDDM WDDM 1.1. Seriously, we all know that there is video cards with WDDM 1.2 compliant drivers that don't make any more uses of features already available and supported in WDDM 1.1.No more excuses from you guys. Get the drivers ready by Christmas holiday season. It shouldn't take more than maybe 1-2 months to actually get it done and working.You already have a good working code base. Turn off driver features present in z2760 that isn't present in the D2700. Also, there is already good working CPU processor driver code for Windows 8 for the actual Intel Atom D2700 microprocessor core itself. It is the graphic drivers component. The only other features that I can think of in the z2760 that isn't in the d2700 is irrelevant to graphics itself. I see no practical difference in the GPU for any reason that would prevent it from working on Windows 8. In fact, you are using the SAME graphic processor in all essence and that the d2700's gpu is really a faster version clocked at 640MHz (IIRC) compared to 533 MHz.Other than a little bit faster clock rate, there is no reason that you guys can't make the graphics drivers for the z2760 work on the d2700 atom. Binarily, they are basically the same processor just like using the drivers codes for programming a TMS9918 would drive the V9958 and driver code to drive the v9958 would largely drive the TMS9918 where they are the same. In the case of the TMS9918/V9958... there is more degree of difference than the d2700's GMA3650 and the PowerVR used in the z2760. Seriously, lets quit the b.s. story and jerking us around. Tell this and forward my message to the powers at be. It should be a simple task.It would have likely cost less money to have made the drivers than all this time dealing with all these threads.It is insanely silly that Intel... a multi-BILLION dollar corporation couldn't spend the minute amount of money to make the driver. It would probably cost less than $250,000... less than what it cost to buy a modest house. I seriously would think it would be easily done in less than 1/3 of the price. I doubt morethan $50K would even need to be spent.Either provide the very exact technical reason why it can not be done.... I don't mean some executive jerkoff as the reason. If it is some management/executive that is the problem... give the jerk the pink sheet. If there is no technical reason to reasonably do it then it get it done or provide me the following:1. Source code to drivers for d2700 and pertinent driver source code for z27602. All documents necessary to perform the work.3. Authorization to distribute the information to parties necessary to organize a driver set development team4. Access to direct communication with CederTrail & CloverTrail devs including software driver devs for CedarTrail and also CloverTrail so we can resolve the matters of the drivers for the D2700 and possibly a number of other drivers. The Intel team would need to be involved for Quality Assurance testing of the drivers and overall guidance because of their involvement and knowledge of the matters.Considering it would be a 'derivative work', it would also be CLEARLY understood that the proprietary rights for the source code and new drivers would ultimately belong to Intel.It would be nice if we get some working cooperation or Intel gets the drivers made.I can not POSSIBLY find any real hardware reason why d2700's GMA3650 would not work in Windows 8 64-Bit. The cpu was a true 64-bit 'x86-64' cpu after all. Unlike most other Atom's INCLUDING the z2760. It runs Windows 8 Pro - 64 BIT EDITION.The GMA 3650 should work fine. After all.... z2760 uses a PowerVR SGX545 core. The GMA 3650 is a PowerVR SGX545 based gpu core. What's the difference?Intel staff.... don't waste my time or anyone's time with pre-canned statements like 'we'll forward it appropriate department for future consideration' or 'We thank you for your feedback, we are aware of the situation...' or pointing us to a particular thread link about Intel official support... blah blah blah OR anything similar to the above. I want serious response from the techs and those with decision making authority. I don't want circle-jerking or anything like that.... yeah... placed in the circular file for future consideration as if anyone ever really looks into the circular file for future consideration. Don't b.s. me with lies. We KNOW better than that. No one looks to the trash can for things of future consideration so seriously... I only know that someone with the authority to make decisions OR part of the technical department if they personally respond specifically to the comment.I would want these people to stop hiding behind human shields like a bunch of wusses and actually are man enough to face the customers.。
6键高抗干扰6感应通道6路触摸触控IC-VK3606D,常用于台扇工控触摸开关面板电子秤等

6键高抗干扰6感应通道6路触摸触控IC-VK3606D,常用于台扇工控触摸开关面板电子秤等VINKA/永嘉微电的VK3606D SOP16是一种具有自动校准功能,低待机电流,抗电压波动等特性的,6按键电容式触摸触控检测IC,适用于温控器,86面板触摸开关,智能家居等抗干扰场所KPP2415概述VK3606D具有6个触摸按键,可用来检测外部触摸按键上人手的触摸动作。
该芯片具有较高的集成度,仅需极少的外部组件便可实现触摸按键的检测。
提供了6路1对1直接输出低电平有效。
最长输出时间10S。
芯片内部采用特殊的集成电路,具有高电源电压抑制比,可减少按键检测错误的发生,此特性保证在不利环境条件的应用中芯片仍具有很高的可靠性。
此触摸芯片具有自动校准功能,低待机电流,抗电压波动等特性,为各种6触摸按键+IO输出的应用提供了一种简单而又有效的实现方法。
特点:· 工作电压 2.4-5.5V· 待机电流7uA/3.0V,14uA/5V· 上电复位功能(POR)· 低压复位功能(LVR)· 触摸输出响应时间:工作模式 48mS ,待机模式160mS· 单键1对1直接输出低电平有效· 防呆功能,有效键最长输出时间:10S· 通过CS脚接对地电容调节整体灵敏度(1-47nF)· 各触摸通道单独接对地小电容微调灵敏度(0-50pF).· 上电0.25S内为稳定时间,禁止触摸· 上电后4S内自校准周期为64mS,4S无触摸后自校准周期为1S · 封装SOP16(150mil)(9.9mm x 3.9mm PP=1.27mm)。
- 1、下载文档前请自行甄别文档内容的完整性,平台不提供额外的编辑、内容补充、找答案等附加服务。
- 2、"仅部分预览"的文档,不可在线预览部分如存在完整性等问题,可反馈申请退款(可完整预览的文档不适用该条件!)。
- 3、如文档侵犯您的权益,请联系客服反馈,我们会尽快为您处理(人工客服工作时间:9:00-18:30)。
THB6064HPWM Chopper-Type bipolar Stepping Motor Driver ICTHB6064HThe THB6064H is a PWM chopper-type sinusoidal micro-step bipolar stepping motor driver IC.It supports 8 kind of excitation modes and forward/reverse mode and is capable of low-vibration, high-performance drive of 2-phase bipolar type stepping motors using only a clock signal.Features• Single-chip bipolar sinusoidal micro-step stepping motordriver Weight:HZIP25-P-1.27: 9.86 g (typ.)• Uses high withstand voltage BiCD process:Ron (upper lower) = 0.4 Ω (typ.) • Forward and reverse rotation control available• Selectable phase drive (1/2,1/8,1/10, 1/16, 1/20, 1/32, 1/40, 1/64 step) • High output withstand voltage: VDSS = 50 V • High output current: IOUT= 4.5 A (peak)• Packages: HZIP25-P-1.27• Output monitor pins (DOWN / ALERT) • Equipped with reset and enable pins• Built-in thermal shutdown(TSD) and over-current detection(ISD) circuit*: Since this product has a MOS structure, it is sensitive to electrostatic discharge. These ICs are highly sensitive to electrostatic discharge. When handling them, please be careful of electrostatic discharge, temperature and humidity conditions.2. Use of Sn-3.0Ag-0.5Cu solder bath*solder bath temperature = 245°C *dipping time = 5 seconds *the number of times = once *use of R-type flux1. Use of Sn-37Pb solder bath*solder bath temperature = 230°C *dipping time = 5 seconds *number of times = once *use of R-type fluxThe THB6064H is a Sn-Ag plated product including Pb. The following conditions apply to solderability: *SolderabilityBlock DiagramV DOWN ALERT V SGND PGNDA ENABLE PGNDBPin FunctionsPin No. I/O Symbol Functional DescriptionRemark1 OutputALERTTSD / ISD monitor pin2 ⎯ SGND Signal ground3 ⎯ OSC1B B channel Capacitor connection pin for off-time setting 4InputFDTVoltage input pin for mixed decay ratio setting5 Input Vref Voltage input for 100% current level6 Input V MB Motor power supply pin for B channel7InputM1Excitation mode setting input pinBuilt-in pull-down resistor 8 Input M2 Excitation mode setting input pin Built-in pull-down resistor 9 Input M3 Excitation mode setting input pin Built-in pull-down resistor 10 Output OUT2B B channel output 211⎯N FBB channel output current detection pin Connect external resistor 12 Output OUT1B B channel output 1 13⎯ PGNDB Power ground 14 Output OUT2A A channel output 215⎯N FAB channel output current detection pin Connect external resistor 16 Output OUT1A A channel output 1 17 ⎯ PGNDA Power ground18 Input ENABLE Enable signal input pin H: Enable, L: all output off 19InputRESETReset signal input pin20 Input V MA Motor power supply pin for A channel 21 Input CLK CLK pulse input pin22 Input CW/CCW Forward/reverse control pinL: Forward, H: reverse 23⎯OSC1AA channel Capacitor connection pin for off-time setting 24 Input V DD Control side power pin. 25OutputDOWNCLK frequency monitor pin<Terminal circuits>Absolute Maximum Ratings (Ta = 25°C)UnitRatingCharacteristic SymbolV DD 6VPower supply voltageV MA/B50Output current I O (PEAK) 4.5(Note 1)A/phaseI TSD1 mADrain current (TSD, DOWN)I DOWNInput voltage V IN 5.5V5 (Note 2)WPower dissipation P D43 (Note 3)Operating temperature T opr−30 to 85 °CStorage temperature T stg−55 to 150 °CNote 1: T = 100msNote 2: Ta = 25°C, No heat sink.Note 3: Ta = 25°C, with infinite heat sink (HZIP25).Operating Range (Ta =−30 to 85°C)Characteristic Symbol Test Condition Min Typ. Max UnitV DD⎯ 4.5 5.0 5.5 V Power supply voltageV MA/B V MA/B ≥V DD 4.5 ⎯42 V Output current I OUT⎯⎯⎯ 4 AV IN⎯0 ⎯ 5.5V Input voltageV ref⎯0.5 ⎯3 Clock frequency f CLK⎯⎯⎯100 kHz OSC frequency f OSC⎯⎯⎯100 kHzElectrical Characteristics (Ta = 25°C, V DD = 5 V, V M = 24 V)Control circuitCharacteristic Symbol Test Condition Min Typ. Max UnitHigh V IN (H) 2.0 ⎯V DDInput voltageLow V IN (L)−0.2⎯ 0.8VInput hysteresis voltageV H M1, M2, M3, CW/CCW, CLK, RESET, ENABLE⎯ 400 ⎯ mV I IN (H)M1, M2, M3, CW/CCW, CLK, RESET, ENABLE V IN = 5.0 V ⎯ 55 (80)Input currentI IN (L)V IN = 0 V⎯⎯ 1μA I DD1Output open, RESET: H, ENABLE: H M1:L, M2:L, M3:L (1/2-step mode)⎯ 3 (7) I DD2RESET: L, ENABLE: H ⎯ 2 (7) VDD supply currentI DD3RESET: L, ENABLE: L ⎯ 2 (7) mAI M1RESET: H/L, ENABLE: L ⎯ 0.5V M supply current I M2RESET: H/L, ENABLE: H ⎯1mAInput current I IN(ref)Vref=3.0V⎯⎯μA Vref inputcircuitDivider ratio V ref /V NF Maximum current : 100%3⎯ Input currentI IN(FDT)⎯⎯μASlow decay mode3.5 ⎯ V DD Mixed decay mode(Peak voltage) (2.9) 3.1 (3.3) Mixed decay mode(Bottom voltage)(0.9) 1.1(1.3)Mixed-decaycomparator Input voltage rangeV FDT Fast decay mode⎯⎯ 0.8VMinimum CLK pulse width t W (CLK)⎯ 10 ⎯ μsV OL DOWN Output residual voltageV OL ALERTI OL = 1 mA⎯⎯ 0.5 VTSD operation temperature(Note) TSD (Design target value) ⎯ 170 ⎯ °C TSD hysteresis (Note) TSDhys (Design target value) ⎯ 40 ⎯ °C Off time (Note )T OFF1A , T OFF1B C OSC1A, C OSC1B = 1000pF (Design target value) 16 23 35 μsecOscillationcircuit forCLK monitorDetection CLKfrequencyfdetectusing built-in capacitor (0.75) 1.5 (3.0) HzNote: Pre-shipment testing is not performed.Output BlockCharacteristic Symbol Test Condition MinTyp. Max UnitOutput ON resistor Ron H + Ron L I OUT = 4 A⎯ 0.4 (0.6) Ω t r ⎯ 0.1 ⎯ Output transistor switchingcharacteristics t fR L = 2 Ω, V NF = 0 V, C L = 15 pF ⎯ 0.1 ⎯ μsUpper side I LH⎯ ― 1Output leakage currentLower sideI LLV M = 50 V⎯― 1μADescription of Functions1. Excitation SettingsYou can use the M1, M2 and M3 pin settings to configure four different excitation settings. (Thedefault is 2-phase excitation using the internal pull-down.)Please be sure to set up ‘Low’ or ‘High’ always at M1, M2 and M3 terminals.Although M1、M2 and M3 terminals have built-in pull-down resistors, please do not keep M1、M2 and M3 terminals open.InputM1 M2 M3Mode (Excitation)L L L 1/2L L H 1/8L H L 1/10L H H 1/16H L L 1/20H L H 1/32H H L 1/40H H H 1/642. FunctionWhen the ENABLE signal goes Low level, it sets an OFF on the output. The output changes to the Initial mode shown in the table below when the RESET signal goes Low level. In this mode, the status of the CLK and CW/CCW pins are irrelevant.3. Initial ModeWhen RESET is used, the phase currents are as follows.Excitation Mode A Phase Current B Phase Current1/2 step 100% 0%1/8 step 100% 0%1/10 step 100% 0%1/16 step 100% 0%1/20 step 100% 0%1/32 step 100% 0%1/40 step 100% 0%1/64 step 100% 0%4. OSC circuitOscillating waveform of chopping wave is generated by connecting the capacitor (C OSC1A and C OSC1B ) between OSC1A , OSC1B and GND terminal.The fixed off-time (T OFF1A and T OFF1B ) can be calculated by the following equation:T OFF1A ≒ C OSC1A ÷ ( 4.4 × 10-5) [sec]T OFF1B ≒ C OSC1B ÷ ( 4.4 × 10) [sec]-5(A gap is between actual values because this is an approximate expression.)The recommended value for T OFF1A and T OFF1B is from 15μs to 35μs. The recommended value for C OSC1A and C OSC1B is from 680pF to 1000pF.*) t1*:t2*=30:15. Decay modeBy comparing the input voltage of FDT terminal and the OSC chopping wave, the rate of thefast-decay time and the slow-decay time in the mixed-decay mode can be set up.V FDT [V] Decay mode3.5 < V FDT < V DD Slow decay1.1 < V FDT < 3.1 Mixed-decay0 < V FDT < 0.8 Fast decayWhen FDT is from 1.1V to 3.1V, it moves to the mixed-decay mode.PWM turns on and the coil current increases in synchronizing with the timing of the peak voltage of Vosc. When the coil current reaches the setup current, PWM turns off and it moves to the slow-decay mode. And the coil current decreases. After that, it switches from the slow-decay mode to thefast-decay mode in the timing that Vosc reaches VFDT and the motor current decreases. Then, in the timing that Vosc reaches peak voltage, PWM turns on again and the coil current increases. There is reverse-current protection in fast decay mode by zore-detection.V OSC [V]Ipeak [A]V FDT [V] V OSC [V] Ipeak [A]decaydecayFDT [V] < 0.8VWhen VFDT is more than 3.5V , it moves to the slow-decay mode.When the coil current reaches set up value, it moves to the slow–decay mode and the coil current decreases.In synchronizing with the peak voltage of Vosc, PWM turns on and the coil current increases.V FDT [V] > 3.5VV OSC [V]3.1V (Typ.)Ipeak [A]6. 100% current Settings (Current Value)100% current value is determined by Vref inputted from external part and the external resistance for detecting output current.Vref is doubled 1/3 inside IC, and compared with VRS. Io(100%) = Vref x 1/3 x 1/RsThe average current is lower than the calculated value because this IC has the method of peak current detection.7. Thermal Shut-Down circuitThe IC incorporates a thermal shutdown circuit. When the junction temperature (T j ) reaches 170°C (typ.), the output power MOSFETs are turned off.The output power MOSFETs are turned on automatically. The IC has 40°C of temperature hysteresis. TSD = 170°C (target spec) (Note) ΔTSD = 40°C (target spec) (Note)Note:Pre-shipment testing is not performed.8. ISD (Over current detection)Current that flow through output power MOSFETs are monitored individually. If over-current is detected in at least one of all output power MOSFETs, all output power MOSFETs are turned off then this status is kept until ENABLE signal is input. Target value in design is 6A and dispersion of ±1.5A should be considered.ISD = 6A (typ.) ±1.5A (Note)Note: Pre-shipment testing is not performed.Junction temperature ALERT output H LOutput power MOSFETdrain currentALERT outputH L ENABLE inputH L9. Low voltage detection (UVLO) circuitOutputs are shutoff by operating at 3.9V (Typ.) of V DD or less.It has a hysteresis of 0.1V(Typ.) and recover to output when V DD reaches 4.0V(Typ.).・The state of internal IC when the ULVO circuit is drivingThe states of the internal IC, outputs, and the IC after recovery correspond to the enable mode.10. ALERT outputALERT pin outputs the state of TSD and ISD. When TSD or ISD circuit operates, ALERT pin state changes from high impedance to low. V ALERT = 0.5V (max.) at 1mATSD ISD ALERT pinUnder TSD opeartionOpen-drain connectionUnder ISD opeartion NormalUnder ISD operationUnder TSD opeartionNormalLowNormal Normal Z11. DOWNWhen IC detects CLK frequency less than 1.5Hz, output of DOWN pin turns to LOW.Pin State DOWN Lowf CLK ≦ 1.5HzZ f CLK > 1.5HzRelationship between Enable, RESET and Output (OUT)Ex-1: ENABLE 1/2-step mode(M1: L, M2: L, M3: L)The ENABLE signal at Low level disables only the output signals. Internal logic functions proceed inaccordance with input clock signals and without regard to the ENABLE signal. Therefore output current is initiated by the timing of the internal logic circuit after release of disable mode.Ex-2: RESET 1/2-step mode (M1: L, M2: L, M3: L)When the RESET signal goes Low level, output goes Initial state (Initial state: A Channel output current is 100%).Once the RESET signal returns to High level, output continues from the next state after Initial from the next raise in the Clock signal.CLK ENABLE RESET100 (%) 0−10071−71 I ACWCLK ENABLE RESET100(%)0−100t 0t 1t 2t 3t 7t 8t 4t 5t 2t 371−71t 6I ACWSequences of output waveform I A /I B at each excitation mode1/2-step Excitation Mode (M1: L, M2: L, M3: L, CW Mode)CLK100 (%) 0 −100t 0t 1t 2t 3t 7t 8t 4t 5t 671−71 I A100 (%) 0 −10071−71 I B1/2-step Excitation Mode (M1: L, M2: L, M3: L, CCW Mode)CLK100(%)0−100t 0t 1t 2t 3t 7t 8t 4t 5t 671−71I A100(%)0−10071−71I BCLKt 0t 1t 2t 3t 7t 8t 4t 5t 12t 13t 6100 (%) 98 92 83 71 56 38 200 −20 −38 −56 −71 −92 −98 −100 100 (%) 98 92 83 71 56200 −20 −38 −56 −71 −98 −100t 9t 10t 11t 14t 17t 18t 15t 16t 19t 20t 21t 22t 27t 28t 24t 25t 29t 30t 31t 32t 23t 26I AI BCLK100 (%) 98 92 83 71 56 38 200 −20 −38 −56 −71 −92 −98 −100 100 (%) 98 92 83 71 56200 −20 −38 −56 −71 −98 −100t 0t 1t 2t 3t 7t 8t 4t 5t 12t 13t 6t 9t 10t 11t 14t 17t 18t 15t 16t 19t 20t 21t 22t 27t 28t 24t 25t 29t 30t 31t 32t 23t 26I AI B-100-80-60-40-200 20 40 60 80100t0・・・・・・・・・・・・・・・・・・・・・・・・・・・・・・・・・・・・・・・・・・・・・・・・・・・・・・・・・・・・・・・・・・・・・・・・・・・・・・・・・・・・・・・・・・・・・・・・・・・・t40Ct0・・・・・・・・・・・・・・・・・・・・・・・・・・・・・・・・・・・・・・・・・・・・・・・・・・・・・・・・・・・・・・・・・・・・・・・・・・・・・・・・・・・・・・・・・・・・・・・・・・・・t40 -100100-80-60-40-200 20 40 60 80CLK [% 98100 9296 8388 77 71 63 56 47 38 29 20 10 −10 −20 −29 38 −47 −56 −63 −71 −77 −83 −92−100−980−96−88−] t0・・・・・・・・・・・・・・・・・・・・・・・・・・・・・・・・・・・・・・・・・・・・・・・・・・・・・・・・・・・・・・・・・・・・・・・・・・・・・・・・・・・・・・・・・・・・・・・・・・・・・・・・・・・・・・・・・・・・・・・t64CLK [% 98100 9296 8388 77 71 63 56 47 38 29 20 10 −10 −20 −29 38 −47 −56 −63 −71 −77 −83 −92−100−980−96−88−] t0・・・・・・・・・・・・・・・・・・・・・・・・・・・・・・・・・・・・・・・・・・・・・・・・・・・・・・・・・・・・・・・・・・・・・・・・・・・・・・・・・・・・・・・・・・・・・・・・・・・・・・・・・・・・・・・・・・・・・・・t64-100-80-60-40-2020406080100-100-80-60-40-2020406080100-100-80-60-40-2020406080100CLK-100-80-60-40-2020406080100CLKCurrent Draw-out Path when ENABLE is Input in Mid OperationWhen all the output transistors are forced OFF during Slow mode, the coil energy is drawn out in the following modes:Note: Parasitic diodes are indicated on the designed lines. However, these are not normally used in MixedDecay mode.As shown in the figure above, an output transistor has parasitic diodes.Normally, when the energy of the coil is drawn out, each transistor is turned ON and the power flows in the opposite-to-normal direction; as a result, the parasitic diode is not used. However, when all the output transistors are forced OFF, the coil energy is drawn out via the parasitic diode.U2L2OFFCharge Mode Slow Mode Force OFF ModeOutput Stage Transistor Operation ModeOutput Stage Transistor Operation FunctionsCLK U1 U2 L1 L2 CHARGE ON OFF OFF ON SLOW OFF OFF ON ON FAST OFF ON ON OFFNote: The above chart shows an example of when the current flows as indicated by the arrows in the above figures. If the current flows in the opposite direction, refer to the following chart:CLK U1 U2 L1 L2 CHARGE OFFONONOFFSLOW OFF OFF ON ON FAST ON OFF OFF ONUpon transitions of above-mentioned functions, a dead time of about 300 ns is inserted respectively.Charge Mode Slow Mode Fast ModeMeasurement WaveformFigure 1 Timing Waveforms and NamesCLKV MGNDPower DissipationTHB6064H1. How to Turn on the PowerTurn on V DD . When the voltage has stabilized, turn on V MA/B .In addition, set the Control Input pins to Low when inputting the power. (All the Control Input pins are pulled down internally.)Once the power is on, the CLK signal is received and excitation advances when RESET goes high and excitation is output when ENABLE goes high. If only RESET goes high, excitation won't be output and only the internal counter will advance. Likewise, if only ENABLE goes high, excitation won't advance even if the CLK signal is input and it will remain in the initial state. The following is an example:<Recommended Control Input Sequence>Internal current SettingOUT ENABLECLKInternal current setting: InvariableOutput OFFInternal current setting: VariableRESET2. Power DissipationThe IC power dissipation is determined by the following equation:P = V DD × I DD + I OUT × I OUTx Ron × 2 driversThe higher the ambient temperature, the smaller the power dissipation.Check the PD-Ta curve, and be sure to design the heat dissipation with a sufficient margin.3. Heat Sink Fin ProcessingThe IC fin (rear) is electrically connected to the rear of the chip. If current flows to the fin, the IC will malfunction. If there is any possibility of a voltage being generated between the IC GND and the fin, either ground the fin or insulate it.Application exampleNotes on Contents1. Block DiagramsSome of the functional blocks, circuits, or constants in the block diagram may be omitted or simplified for explanatory purposes.2. Equivalent CircuitsThe equivalent circuit diagrams may be simplified or some parts of them may be omitted for explanatory purposes.3. Timing ChartsTiming charts may be simplified for explanatory purposes.4. Application CircuitsThe application circuits shown in this document are provided for reference purposes only. Thorough evaluation is required, especially at the mass production design stage.Toshiba does not grant any license to any industrial property rights by providing these examples of application circuits.5. Test CircuitsComponents in the test circuits are used only to obtain and confirm the device characteristics. These components and circuits are not guaranteed to prevent malfunction or failure from occurring in the application equipment.IC Usage ConsiderationsNotes on handling of ICs[1] The absolute maximum ratings of a semiconductor device are a set of ratings that must not beexceeded, even for a moment. Do not exceed any of these ratings.Exceeding the rating(s) may cause the device breakdown, damage or deterioration, and may result injury by explosion or combustion.[2] Use an appropriate power supply fuse to ensure that a large current does not continuously flowin case of over current and/or IC failure. The IC will fully break down when used underconditions that exceed its absolute maximum ratings, when the wiring is routed improperly or when an abnormal pulse noise occurs from the wiring or load, causing a large current tocontinuously flow and the breakdown can lead smoke or ignition. To minimize the effects of the flow of a large current in case of breakdown, appropriate settings, such as fuse capacity, fusing time and insertion circuit location, are required.[3] If your design includes an inductive load such as a motor coil, incorporate a protection circuitinto the design to prevent device malfunction or breakdown caused by the current resulting from the inrush current at power ON or the negative current resulting from the backelectromotive force at power OFF. IC breakdown may cause injury, smoke or ignition.Use a stable power supply with ICs with built-in protection functions. If the power supply is unstable, the protection function may not operate, causing IC breakdown. IC breakdown may cause injury, smoke or ignition.[4]Do not insert devices in the wrong orientation or incorrectly.Make sure that the positive and negative terminals of power supplies are connected properly.Otherwise, the current or power consumption may exceed the absolute maximum rating, and exceeding the rating(s) may cause the device breakdown, damage or deterioration, and may result injury by explosion or combustion.In addition, do not use any device that is applied the current with inserting in the wrongorientation or incorrectly even just one time.Package DimensionsWeight: 9.86 g (typ.)。