模具设计之模具篇-C.ppt
合集下载
模具设计标准PPT课件

3
1.模胚的类型:
二.模胚
1.1. 卧式成型机〕:根据模具的大小和选用成型机不同,选用直身模胚或工字型模胚。
1.2. C型成型机〕:选用左右工字型模胚
2.模具编号位置:
3. 模胚的加工要求:
3.1. 导柱外面要加导套〔防止敲导柱拉伤模胚的孔〕;导柱要做油槽,导套后面做 开排气槽
3.2. 导柱和导套外表光洁度到达以上〔外表用肉眼看不到刀纹〕
3.3. 导柱和导套的配合问隙为〔双边〕
深,并且开通导套
3.4. 导柱和衬套之间的间隙为〔双边〕
导套
Ød
导柱 衬套
外表(内 外)光洁 度到达以 上
Ød+00.020
ØD1 0
导套挂台处 排气槽
5
3.5. A板和B板基准边错位最大 3.6. A板和B板直角度在以内 3.7. A板和B板框基准边的尺寸相差在以内
高的内模四边加直身导柱/导柱. 4.前后模型芯:采用斜度四个方向定位〔前后左右〕 5.前后模型芯镶件:采用直斜度四个方向定位〔前后左右〕 6.精定位尽量在模仁上原身留,拆镶件增加误差,结构性不强 7.精定位必须设计斜面,防止烧伤 8.模胚挖框和边锁由模胚厂加工〔预防挖框后模胚变形〕 9.零位和基准面要一致〔一套模具标数基准要一致〕,图面标数注意配合公差 10.层层定位要注意加工顺序,一层定位加工完后再加工另一层
IN“, 〞OUT“字样左来自图左边接运水17
模具做转水口
转水口镶件
18
4.16.模具加一百万次计数器,指定计数器(我司实际安装右图所示计数器〕,并 安装在操作面这边 我司所使用计数器规格 25
48 53
19
4.17.模胚出线槽局部倒圆角
20
4.18.前模胚边要做避空(红色区域避空0.5MM) 防止插伤后模模仁边
1.模胚的类型:
二.模胚
1.1. 卧式成型机〕:根据模具的大小和选用成型机不同,选用直身模胚或工字型模胚。
1.2. C型成型机〕:选用左右工字型模胚
2.模具编号位置:
3. 模胚的加工要求:
3.1. 导柱外面要加导套〔防止敲导柱拉伤模胚的孔〕;导柱要做油槽,导套后面做 开排气槽
3.2. 导柱和导套外表光洁度到达以上〔外表用肉眼看不到刀纹〕
3.3. 导柱和导套的配合问隙为〔双边〕
深,并且开通导套
3.4. 导柱和衬套之间的间隙为〔双边〕
导套
Ød
导柱 衬套
外表(内 外)光洁 度到达以 上
Ød+00.020
ØD1 0
导套挂台处 排气槽
5
3.5. A板和B板基准边错位最大 3.6. A板和B板直角度在以内 3.7. A板和B板框基准边的尺寸相差在以内
高的内模四边加直身导柱/导柱. 4.前后模型芯:采用斜度四个方向定位〔前后左右〕 5.前后模型芯镶件:采用直斜度四个方向定位〔前后左右〕 6.精定位尽量在模仁上原身留,拆镶件增加误差,结构性不强 7.精定位必须设计斜面,防止烧伤 8.模胚挖框和边锁由模胚厂加工〔预防挖框后模胚变形〕 9.零位和基准面要一致〔一套模具标数基准要一致〕,图面标数注意配合公差 10.层层定位要注意加工顺序,一层定位加工完后再加工另一层
IN“, 〞OUT“字样左来自图左边接运水17
模具做转水口
转水口镶件
18
4.16.模具加一百万次计数器,指定计数器(我司实际安装右图所示计数器〕,并 安装在操作面这边 我司所使用计数器规格 25
48 53
19
4.17.模胚出线槽局部倒圆角
20
4.18.前模胚边要做避空(红色区域避空0.5MM) 防止插伤后模模仁边
模具设计基础知识培训PPT(34张)

1.参考模型的组装 选择【MOLD MODEL(模具模型)】→【Assemble(装配)】→【Ref Model(参照模型)】, 选取设计模型零件,定义调入零件的装配约束关系并使其放置在模具模型中。 (1)按参照合并:将设计零件复制到参考零件中,且把基准平面信息从设计模型复 制到参照模型。其设计零件中的所有改变将自动反映到参考零件中。 (2)同一模型:直接选定设计模型用作模具的参考模型,两者为相同模型。 (3)继承:参考零件继承设计零件中的所有几何和特征信息。 系统还允许以布局方式来组装参考模型,实现以阵列方式排列参考零件 。
10.1.3 模具设计的基本流程
1.建立或调入设计模型,形成模具设计的参考模型 2.模型检验:对参考模型进行拔模斜度检测、厚度检测等 3.建立工件:用来定义所有模具元件体积的 4.在模具模型上创建缩水率:可以等向或非等向增加在指定特征尺寸上 5.加入模具装配特征,设计浇道系统 6.定义分型面及模块体积 7.建立模具实体元件:抽取完成的模块体积,将曲面几何转换为实体几何 8.填充模具型腔,建立浇注件:利用工件体积减去抽取的模具元件体积 9.模拟开模,并进行干涉检测 10.装配模座元件,并进行所有元件的细部设计
10.2.3 设置收缩率
2.按比例收缩 【By Scaling(按比例)】表示允许相对于某个坐标系按比例收缩零件几何,并 且可以分别指定x、y和z坐标的不同收缩率。在模具模块中应用按比例收缩时, 其仅作用于参考零件几何,而不影响设计模型。 选择【SHRINKAGE(收缩)】→【Shrink Info(收缩信息)】,将弹出“信息窗 口”并显示设计模型的收缩信息。
已建立有曲面特征时,选择【Feature(特征)】→【Cavity Assem(型腔组件)】→ 【Surface(曲面)】命令,利用“面组曲面”菜单可增加分型面的曲面或者对已有 分型面的曲面特征进行编辑。
10.1.3 模具设计的基本流程
1.建立或调入设计模型,形成模具设计的参考模型 2.模型检验:对参考模型进行拔模斜度检测、厚度检测等 3.建立工件:用来定义所有模具元件体积的 4.在模具模型上创建缩水率:可以等向或非等向增加在指定特征尺寸上 5.加入模具装配特征,设计浇道系统 6.定义分型面及模块体积 7.建立模具实体元件:抽取完成的模块体积,将曲面几何转换为实体几何 8.填充模具型腔,建立浇注件:利用工件体积减去抽取的模具元件体积 9.模拟开模,并进行干涉检测 10.装配模座元件,并进行所有元件的细部设计
10.2.3 设置收缩率
2.按比例收缩 【By Scaling(按比例)】表示允许相对于某个坐标系按比例收缩零件几何,并 且可以分别指定x、y和z坐标的不同收缩率。在模具模块中应用按比例收缩时, 其仅作用于参考零件几何,而不影响设计模型。 选择【SHRINKAGE(收缩)】→【Shrink Info(收缩信息)】,将弹出“信息窗 口”并显示设计模型的收缩信息。
已建立有曲面特征时,选择【Feature(特征)】→【Cavity Assem(型腔组件)】→ 【Surface(曲面)】命令,利用“面组曲面”菜单可增加分型面的曲面或者对已有 分型面的曲面特征进行编辑。
第二章-冲裁工艺与冲裁模具设计PPT课件

沿工件全部外形冲裁,工件间、工件与板料边
都有搭边。材料利用率低,但能保证冲裁件质量,
模具寿命较高。
少废料排样
模具只沿工件部分外形轮廓冲裁,只有局部有
搭边。废料较少,工件质量不高,模具摩损快。
无废料排样
工件间、工件与条料间均没有搭边的存在。模具刃口
沿板料依次切下获取工件。材料利用率高,工件质量差,
模具易损坏。
裁板
纵裁
联合裁
横裁
21
冲压工艺力和压力中心的计算
概 念:
~是冲裁时压力机应具有的最小压力,是完成分离
所必需的力和其它附加力(卸料力、推料力、顶料力)的
总和。它是设计模具、选择压力机的重要依据。
冲裁力的计算
使板料发生分离的力称为冲裁力。一般平刃冲裁模的冲裁
力P可用下式计算:
= KLt
(K-系数,取1.3)
合理冲裁间隙值的确定:
❖ 工件断面质量无严格要求时,应取大间隙值;
❖ 工件的断面质量和制造精度较高时,应取较小间隙值;
❖ 在设计冲模刃口尺寸时,应考虑模具摩损因素,冲裁
间隙应取最小值。
6
方法1:理论确定法
如右图所示,可得冲裁间隙为:
= 2( − ℎ0 )tan = 2(1 − ℎ0 Τ)tan
能与其冲压时定位 基准重合 ,
并选择在冲裁过程中基本上下
不变动的面或线上。
9
凸、凹模刃口尺寸的计算
重要性:
冲模刃口处的尺寸及制造公差直接影响工件的尺寸
精度,合理的冲裁间隙也靠其保证。
前提:
尺寸
计算
的原
则:
因冲裁间隙的存在,落下的料和冲出的孔都带有锥
度,且落料件的大端尺寸与凹模刃口尺寸相近,冲出
都有搭边。材料利用率低,但能保证冲裁件质量,
模具寿命较高。
少废料排样
模具只沿工件部分外形轮廓冲裁,只有局部有
搭边。废料较少,工件质量不高,模具摩损快。
无废料排样
工件间、工件与条料间均没有搭边的存在。模具刃口
沿板料依次切下获取工件。材料利用率高,工件质量差,
模具易损坏。
裁板
纵裁
联合裁
横裁
21
冲压工艺力和压力中心的计算
概 念:
~是冲裁时压力机应具有的最小压力,是完成分离
所必需的力和其它附加力(卸料力、推料力、顶料力)的
总和。它是设计模具、选择压力机的重要依据。
冲裁力的计算
使板料发生分离的力称为冲裁力。一般平刃冲裁模的冲裁
力P可用下式计算:
= KLt
(K-系数,取1.3)
合理冲裁间隙值的确定:
❖ 工件断面质量无严格要求时,应取大间隙值;
❖ 工件的断面质量和制造精度较高时,应取较小间隙值;
❖ 在设计冲模刃口尺寸时,应考虑模具摩损因素,冲裁
间隙应取最小值。
6
方法1:理论确定法
如右图所示,可得冲裁间隙为:
= 2( − ℎ0 )tan = 2(1 − ℎ0 Τ)tan
能与其冲压时定位 基准重合 ,
并选择在冲裁过程中基本上下
不变动的面或线上。
9
凸、凹模刃口尺寸的计算
重要性:
冲模刃口处的尺寸及制造公差直接影响工件的尺寸
精度,合理的冲裁间隙也靠其保证。
前提:
尺寸
计算
的原
则:
因冲裁间隙的存在,落下的料和冲出的孔都带有锥
度,且落料件的大端尺寸与凹模刃口尺寸相近,冲出
模具设计PPT课件

2021/3/9
20
第三章 模具设计
抽取模具元件
❖ 创建完模具体积块后,可以从工件抽取它们 以产生模具元件
2021/3/9
21
第三章 模具设计
铸模
❖ 可以通过浇道、流道和浇口来模拟填充模具 型腔,从而创建铸模,如图所示分别是参照 零件和铸模,铸模的上面有浇注系统。
❖ 铸模可以用于检查前面设计的完整性和正确 性,如果出现不能生成铸模文件的现象,极 有可能是先前的模具设计有差错或者参照零 件有几何交错的现象,应当向前检查。
❖ 6. 提取模具体积块以生成模具元件。提取完毕后模具元件即 成为功能齐全的Pro/ENGINEER零件,它可在零件模式中调 出可在绘图中使用也可用Pro/NC进行加工
❖ 7. 创建表示已填充模具型腔的模制件系统将根据减去提取部 分后工件中剩余的体积块来自动创建模制件(铸模)
❖ 8. 定义模具开口的步骤在每步中检查与静态零件的干涉必要 时修改模具元件
❖ 对于塑料模具,浇注系统一般由主流道、分流道、 冷料井和浇口组成
❖ 浇注系统的设计方法 :使用【实体】特征中切割材
料方式来建立浇注系统,; 或直接利用模具特征中
的【流道】特征建立浇注系统,利用流道特征可以 快速创建标准流道。
2021/3/9
25
第三章 模具设计
侧浇口
❖ 侧浇口
2021/3/9
26
2021/3/9
4
第三章 模具设计
❖ 3.1.2 创建模具文件
2021/3/9
5
第三章 模具设计
3.2 加载参照模型
❖ 根据型腔数目的多少,模具可以分为单腔模 具和多腔模具
2021/3/9
6
第三章 模具设计
VISI五金模具设计PPT课件
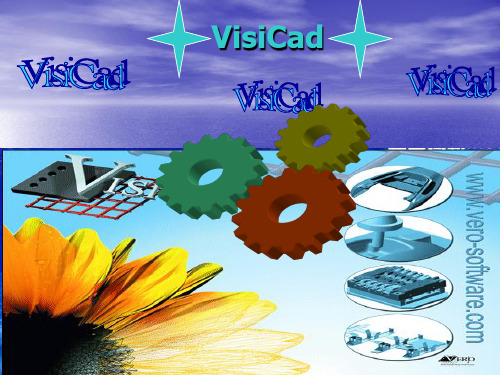
7
Bend 1:change from90 °to 45 °
增 加 步 驟
逐 步 展 開 圖
標
8
第一 步折 90°展 開后
到45
°
第二 步折
45° 展開 圖
9
•
第三 步兩 邊折 90° 展開 后到 45 °
第三 步兩 邊折 90° 展開 后到 45 °
點擊此處將增 加下一步。
10
•
第三步兩邊
折90°展開后 到45 °
點擊此折彎處點 右鍵將出現右圖 所示對話框 °
11
第四 步兩 邊折 45° 展開 圖.
第四 步兩 邊折 45° 展開 圖.
12
第五 步折 90° 展開 圖.
13
*所有展開完后后點 擊此鍵重建3D制品*
•
14
15
•
(3)將料帶放于此 后﹐點擊ESC鍵后 將出現料帶
(2)由資料 庫載入料
在工步數后面點擊右鍵出現如圖所示的 對話框稍﹐然后貼上需要插入的成型
20
21
22
展開圖
沖孔后的料帶圖 插入成型后的料帶圖
產品23
24
Prepare By: XIAO2L5AN
VisiCad
1
•
2
展開時點擊 此零件分析
3
(3)確定基准點 即﹕<2>所選平 面上任一一點
(2)選取實體制品的 基准面(非毛邊面)
(1)點擊分析 制品架構
分析制品過程中
4
(1)點擊此
•
(2)點擊此
5
•
料厚(自動顯 示)
選擇該產品 折彎系數
6
(2)點擊自動 最優化圖標
模具型腔布局PPT课件
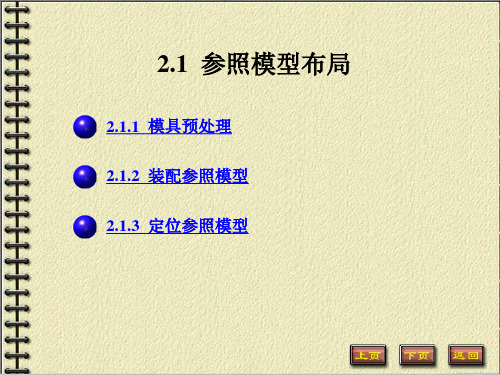
3. 复制实体曲面
为了避免模具设计过程中可能出现的分模失败问题, 可以通过复制实体曲面功能和曲面“实体化”命令,为后 续模具设计创建设计模型。
复制实体曲面需在组件设计模式下进行,复制得到的 曲面经过实体化,成为真正的实体零件(.prt),并以元 件的形式存在于装配体中。
在选取曲面时,可先从模型上选取一个曲面作为种子 曲面,然后按住【Shift】键选取另外一个曲面作为边界 曲面,释放【Shift】键后,再按住【Ctrl】键将边界曲面 选中,由此可快速将模型上的所有曲面选中。
在“模具”菜单管理 器中选择“收缩”菜 单
弹出“收缩”菜单栏, 选择“按比例”菜单
打开“按比例收缩”对话框, 从“公式”栏中选取一种用于 计算收缩系数的公式,选取一 个用于收缩的参照坐标系(如 “PRT_CSYS_DEF”),在 “收缩率”文本框中输入一个 收缩率值(如“0.005”),然 后单击“应用”按钮,即可将 比例收缩应用到参照模型
在“模具模型”菜单栏中选择“定 位参照零件”菜单,或者单击模具 工具栏中的“模具型腔布局”按钮, 系统将打开此“布局”对话框(即 模具型腔布局工具),利用该对话 框可以添加、定位和阵列排布参照 模型,以创建不同类型的多腔模布
局,如矩形布局、圆形布局等
下面使用模具型腔布局工具创建一个多腔模布局。
在“模具”菜单 管理器中选择 “模具模型”菜 单
首先来学习在模具设计环境下装配参照模型的方法。
在“模具”菜单管理器 中选择“模具模型”菜 单
弹出“模具模 型”菜单栏, 选择“装配” 菜单
弹出“打开”对话框,选取设计 模型文件,然后单击“打开”按 钮
弹出“模具模型类型”菜 单栏,选择“参照模型” 菜单
系统弹出“元件放置”操控面板, 按照装配组件元件的方法放置参 照模型,注意参照模型的坐标系 一般要与模具模型的坐标系对齐, 这里选择“缺省”约束类型,然 后单击“应用”按钮
注塑工艺与模具设计PPT课件

水冷装置;
模具设计
注塑模具设计思路 本钱设计:模具材料本钱,成型产品本钱,标准件使用本钱等。 模具维护设计:维修配件结构、备用配件、可拆装性配件、复原性能;
模具设计
30%加工
切割加工、热处理、 放电、慢走 丝、氧化性、 组装等
35%销售管 理试模杂费
20%设计费
15%材料费
模具制作费用
破损与修理费用
注塑工艺根底
流动性快
进料点
先冷却, 流动 性慢
模具冷料 井
注塑工艺根底
压力如何影响产品结构及外观 压力会使分子紧靠在一起,收缩性变小,密度变小; 压力缺乏会导致产品不饱模/缩水,会限制注射速度控制系统提供快速射
出的能力; 压力过大会导致产品毛边/批峰/冲胶。
注塑工艺根底
结晶结构 • 模具温度越高,结晶时间越长,结晶体越大,收缩越大,不均匀结晶
〔产品胶料用量〕压力过小,机器喷嘴与模具未对准。可根据实际情 况调试相关参数进行改善。
现场问题
毛边、批峰 • 塑胶熔体流入分模面或镶件合面将产生毛边批峰。 • 熔体的粘度、压力和间隙的宽度决定是否出现毛边。绝大多数胶料来
说,在的间隙一般都不会产生毛边。熔体尽量进入,但立刻凝固,堵 住流动。
现场问题
注塑马 达
注塑成型工艺根底—设备介绍
上段温 度
调整
中段温 度
度调整
下段温 度
度调整
工作台
冷却水循环 器
开模高度 设定钮
慢速关模 设定阀
高压关模 设定阀
射胶时 间
调整
松退时 间
调整
冷却时 间
调整
注塑成型工艺根底—设备介绍
射出速 度调整
背压调 整阀
模具设计
注塑模具设计思路 本钱设计:模具材料本钱,成型产品本钱,标准件使用本钱等。 模具维护设计:维修配件结构、备用配件、可拆装性配件、复原性能;
模具设计
30%加工
切割加工、热处理、 放电、慢走 丝、氧化性、 组装等
35%销售管 理试模杂费
20%设计费
15%材料费
模具制作费用
破损与修理费用
注塑工艺根底
流动性快
进料点
先冷却, 流动 性慢
模具冷料 井
注塑工艺根底
压力如何影响产品结构及外观 压力会使分子紧靠在一起,收缩性变小,密度变小; 压力缺乏会导致产品不饱模/缩水,会限制注射速度控制系统提供快速射
出的能力; 压力过大会导致产品毛边/批峰/冲胶。
注塑工艺根底
结晶结构 • 模具温度越高,结晶时间越长,结晶体越大,收缩越大,不均匀结晶
〔产品胶料用量〕压力过小,机器喷嘴与模具未对准。可根据实际情 况调试相关参数进行改善。
现场问题
毛边、批峰 • 塑胶熔体流入分模面或镶件合面将产生毛边批峰。 • 熔体的粘度、压力和间隙的宽度决定是否出现毛边。绝大多数胶料来
说,在的间隙一般都不会产生毛边。熔体尽量进入,但立刻凝固,堵 住流动。
现场问题
注塑马 达
注塑成型工艺根底—设备介绍
上段温 度
调整
中段温 度
度调整
下段温 度
度调整
工作台
冷却水循环 器
开模高度 设定钮
慢速关模 设定阀
高压关模 设定阀
射胶时 间
调整
松退时 间
调整
冷却时 间
调整
注塑成型工艺根底—设备介绍
射出速 度调整
背压调 整阀