模具设计实例解析
ug注塑模具设计实例

ug注塑模具设计实例以下是一个简单的注塑模具设计实例,模具设计的基本概念和步骤。
设计案例:一个简单的塑料瓶盖模具1. 确定产品尺寸和形状产品是一个简单的塑料瓶盖,直径为20mm,高度为3mm。
瓶盖表面有纹理,以增加摩擦力,方便开启。
2. 确定模具结构模具采用典型的双板模结构,由动模板和定模板组成。
动模板上设有型腔,定模板上设有浇口和流道。
3. 确定型腔布局由于瓶盖尺寸较小,可以采用一模一腔的布局。
型腔布置在动模板上,浇口和流道布置在定模板上。
4. 设计浇口和流道浇口和流道的设计需要考虑塑料的填充和流动。
本例中,采用点浇口,浇口直径为1mm,流道直径为4mm。
5. 设计推出机构推出机构用于将成型后的产品从模具中推出。
本例中,采用推杆推出,推杆直径为8mm,数量为4个。
推杆安装在动模板上,推出时推动瓶盖脱离型腔。
6. 设计冷却系统冷却系统用于将成型过程中的热量从模具中带走,防止产品变形和开裂。
本例中,采用水管冷却,水管直径为4mm,布置在动模板和定模板上。
7. 设计排气系统排气系统用于将成型过程中的气体从模具中排出,防止气体的积聚和压力的升高。
本例中,采用排气槽,排气槽直径为2mm,数量为4个。
排气槽布置在定模板上。
8. 设计模具零件加工工艺性模具零件的加工需要考虑其工艺性。
本例中,采用数控加工中心进行加工,材料选择不锈钢。
9. 设计模具装配工艺性模具装配需要考虑其工艺性。
本例中,采用螺钉连接动模板和定模板,并使用定位销进行定位。
以上是一个简单的注塑模具设计实例,希望能帮助您更好地理解模具设计的基本概念和步骤。
钣金模具设计实例

评审与修改
对设计结果进行评审,根据评审 意见进行必要的修改和完善。
需求分析
明确设计任务和目标,收集相关 资料和数据,进行初步的需求分 析。
出图与归档
完成最终的设计图纸,整理相关 文件和资料,进行归档保存。
02
钣金模具设计实例解析
实例一:手机外壳模具设计
手机外壳模具设计需要考 虑的因素包括材料、结构、 工艺和外观等。
经济性
在满足功能和性能要求的前提 下,应尽可能降低模具制造成 本。
可持续性
设计时需考虑环保和可持续性 ,优先选择环保材料和工艺,
降低能耗和资源消耗。
钣金模具的应用领域
航空航天
钣金模具在航空航天领域中广泛应用于制造 飞机、卫星等复杂结构件。
家用电器
钣金模具在家用电器领域用于生产电视、冰 箱、空调等产品的外壳和内部结构件。
外观方面要求模具设计简洁、美 观,符合市场和用户需求。
03
钣金模具设计中的常见 问题与解决方案
问题一:模具强度不足
总结词
模具强度不足可能导致生产过程中出现变形、断 裂等问题,影响产品质量和生产效率。
2. 结构设计不合理
优化模具结构,合理布置加强筋、支撑柱等结构, 提高整体强度。
ABCD
1. 材料选择不当
钣金模具设计实例
目 录
• 钣金模具设计概述 • 钣金模具设计实例解析 • 钣金模具设计中的常见问题与解决方案 • 钣金模具设计的未来发展趋势
01
钣金模具设计概述
设计理念与原则
创新性
钣金模具设计应注重创新,通 过独特的设计理念和原则,实 现产品的高效、美观和实用性
。
功能性
设计时应充分考虑钣金模具的 功能需求,确保其能够满足生 产过程中的各种要求。
双色注射模具设计10个实例(经典案例)

双⾊注射模具设计10个实例(经典案例)这是⼀款⼿机护套,如下图产品分析:此款为某品牌⼿机的外圈护套,由⼆种塑料(PC+TPE)组成。
由于要求外形美观光滑,分模线必须做在内侧圆弧切点,所以外模要四⾯滑开,再看内侧,四周全部是内扣的,必须全⽅位内抽芯,也就是俗称的“爆炸芯”。
关于“爆炸芯”的模具结构,假如是普通的注塑模具,已经有⾮常经典的机构,我下⾯将有详细的介绍。
现在问题是双⾊模具,有⼆组动模和⼆组定模,⼆组动模的所有部件是完全⼀致的,要在双⾊注塑机的转盘上进⾏180度旋转,⼆种不同的塑料分别射进模腔,注射硬胶(PC)时动模的顶出机构和抽芯机构不动作,再注射软胶(TPE)并开模后,对准软胶料筒的⼀侧的动模的抽芯机构和顶出机构才开始动作,将完整的双⾊制品顶出。
由于动模旋转后,交换⼜合模后的浇⼝必须在同⼀位置,所以软胶和硬胶的浇⼝的处理显得令⼈困惑。
由于模具必须四周都要进⾏“内外同抽”,内、外滑块怎样排列,轨道设置在哪⾥?这个问题同样有被逼⼊墙⾓的感觉。
且不谈模具滑块机构的复杂性,我们从双⾊模具的基本原理来考虑,硬胶部分的成型和内外同抽机构是⼀定要设置在定模⼀侧的,软胶部分的成型机构也要设置在定模。
⽽且这个部分是由内外同抽的机构组成的凸起插⼊到动模的凹槽中。
转盘旋转180度后,这组凸起刚好插⼊到另外⼀个动模的凹槽中。
也就是说,⼆个定模上的由内外同抽滑块组成的凸起的外部形状和尺⼨是完全相同的。
仅仅是成型软胶和硬胶的型⾯不同⽽已。
问题的难点是,这个凸起会分成上下⼆层,⼀层向外移动,另⼀层向内移动,也就是俗称的“内外同抽”,合成的凸起的侧⾯是⼀个统⼀的斜⾯,但是,传统的滑块必须要有滑动轨道等必要的条件,怎样设置轨道?这便成了本案例的核⼼问题。
我是这样设置动模部分的凹槽和定模部分凸起的。
动模的凹槽是这样的。
下⾯我们来探讨定模部分的设计1.01定模内外同抽的设计基本机构是这样的当A板和定模底板分开35mm后拨块拨动内滑块,同时通过齿轮的传动,外滑块向外移动。
单分型面模具设计实例
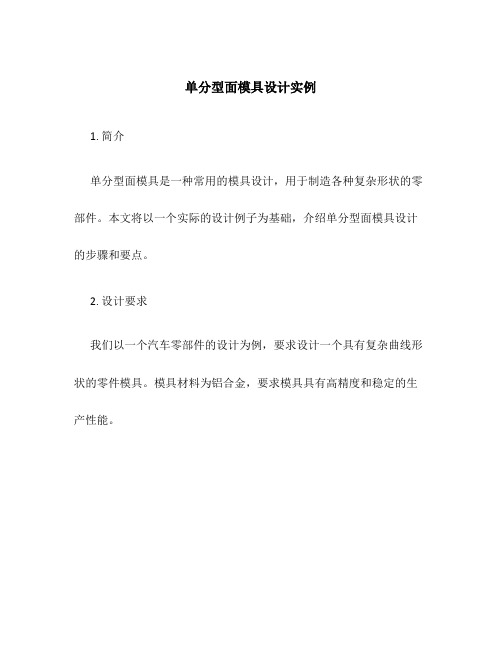
单分型面模具设计实例1. 简介单分型面模具是一种常用的模具设计,用于制造各种复杂形状的零部件。
本文将以一个实际的设计例子为基础,介绍单分型面模具设计的步骤和要点。
2. 设计要求我们以一个汽车零部件的设计为例,要求设计一个具有复杂曲线形状的零件模具。
模具材料为铝合金,要求模具具有高精度和稳定的生产性能。
3. 设计步骤3.1 零件分析首先,对需要制造的零件进行分析,了解其几何形态,特点和使用要求。
在本例中,我们的零件具有复杂的曲线形状,并且需要满足一定的轴向和半径的公差要求。
3.2 模具结构设计根据零件分析结果,设计模具的整体结构。
在单分型面模具中,通常包括模具底部、活动模块和固定模块。
在本例中,我们将采用三板式模具结构,即模具底部、活动模块和两个固定模块。
3.3 分型面设计分型面是单分型面模具的核心部分,其决定了零件的截面形状和尺寸。
在本例中,我们需要设计一个能够精确复制零件曲线形状的分型面。
分型面设计要考虑到材料的收缩率和模具使用寿命等因素。
3.4 模具部件设计根据模具结构和分型面的设计,设计模具的各个部件,包括模具底部、活动模块和固定模块。
在本例中,我们将采用铝合金材料设计模具底部和活动模块,固定模块采用钢材料。
3.5 组装与调试在完成模具部件的设计和制造后,进行模具的组装与调试。
对于单分型面模具,主要调试工作包括调整分型面的几何形态和尺寸,以及模具的开合动作和精度。
4. 模具制造和使用4.1 模具制造根据设计完成的模具图纸,进行模具的制造。
模具制造涉及到材料的选择、切割、铣削、研磨、打磨等工艺步骤。
在铝合金模具部分,需要考虑材料的热处理和表面处理工艺。
4.2 模具使用在模具制造完成后,将其安装在注塑或压铸设备上进行零件的生产。
在使用过程中,需要对模具进行定期维护和保养,以保证模具的精度和寿命。
5. 总结通过以上的设计步骤和要点,我们可以看出单分型面模具设计的流程和关键技术。
在实际应用中,根据不同的零件形状和要求,还可以对单分型面模具进行改进和优化。
注塑模具设计实例
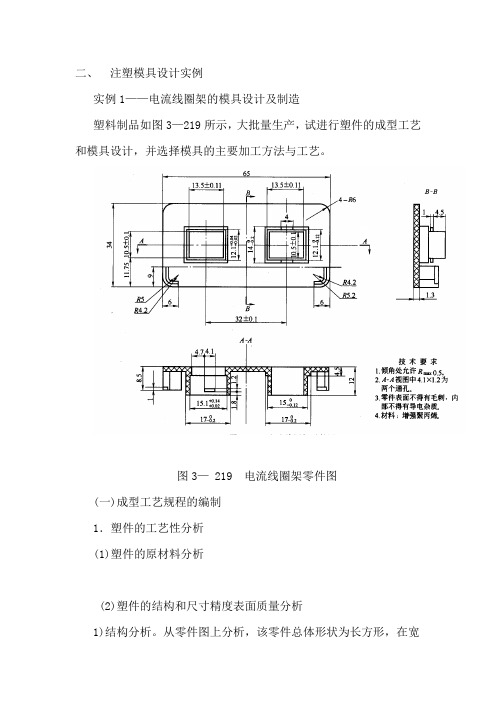
二、注塑模具设计实例实例1——电流线圈架的模具设计及制造塑料制品如图3—219所示,大批量生产,试进行塑件的成型工艺和模具设计,并选择模具的主要加工方法与工艺。
图3— 219 电流线圈架零件图(一)成型工艺规程的编制1.塑件的工艺性分析(1)塑件的原材料分析(2)塑件的结构和尺寸精度表面质量分析1)结构分析。
从零件图上分析,该零件总体形状为长方形,在宽度方向的一侧有两个高度为8.5mm ,R5mm 的两个凸耳,在两个高度为12mm 、长、宽分别为17mm 和13.5mm 的凸台上,一个带有的凹槽(对称分布),另一个带有4.lmmXl .2 mm 的凸台对称分布。
因此,模具设计时必须设置侧向分型抽芯机构,该零件属于中等复杂程度。
2)尺寸精度分析。
该零件重要尺寸如:012.01.12-mm 、04.002.01.12++mm 、14.002.01.15++mm 、012.01.15-mm 等精度为3级(Sj1372—78),次重要尺寸如:13.5±0.11、02.017-mm 、10.5±0.1mm 、02.014-mm 等的尺寸精度为4~5级(Sj 1372—78)。
由以上分析可见,该零件的尺寸精度中等偏上,对应的模具相关零件的尺寸加工可以保证。
从塑件的壁厚上来看,壁厚最大处为1.3mm ,最小处为0.95mm ,壁厚差为0.35mm ,较均匀,有利于零件的成型。
3)表面质量分析。
该零件的表面除要求没有缺陷、毛刺,内部不得有导电杂质外,没有特别的表面质量要求,故比较容易实现。
综上分析可以看出,注射时在工艺参数控制得较好的情况下,零件的成型要求可以得到保证。
(3)计算塑件的体积和质量计算塑件的质量是为了选用注射机及确定型腔数。
经计算塑件的体积为V =4087mm 3;计算塑件的质量:根据设计手册可查得增强聚丙烯的密度为ρ=1.04g /cm 3。
故塑件的质量为W =V ρ=4.25g采用一模两件的模具结构,考虑其外形尺寸、注射时所需压力和工厂现有设备等情况,初步选用注射机为XS—Z—60型。
模具设计实例解析

模具设计实例解析
模具设计是一个复杂的过程,需要经验丰富的工程师对模具设计进行精细化操作。
在这篇文章中,我们将解析几个有代表性的模具设计实例,来展示模具设计的流程和注意事项。
首先,我们将讨论一下塑料模具的设计。
塑料模具是指用于生产塑料制品的模具。
根据不同的塑料制品,模具的设计方法和注意事项也有所不同。
例如,对于比较脆的塑料制品,需要在模具设计时采用间接成型,这种方法可以减少模具对制品的冲击力,从而减少制品的破碎率。
另外,在模具设计时还要考虑塑料制品的结构,比如是否需要支撑杆和排气孔等结构,这些因素都会影响到制品的质量。
其次,我们将讨论一下金属模具的设计。
金属模具是指用于生产金属制品的模具。
在金属模具设计中,有很多需要考虑的因素,比如厚度、硬度、尺寸等。
同时,还需要考虑到金属的变形和缩水等因素,这些因素都会影响到制品的尺寸和质量。
因此,设计时需要有很好的工程知识和技术经验,才能保证模具的准确度和生产效率。
最后,我们将讨论一下橡胶模具的设计。
橡胶模具是指用于生产橡胶制品的模具。
在橡胶模具设计中,需要考虑到橡胶材料的硬度、弹性、收缩率等因素。
设计的模具需要有一定的弹性和韧性,以保证制品的吸附力和平整度。
同时,设计时还需要考虑到模具的大小和形状,以保证制品的准确度和质量。
总之,模具设计是一个复杂的过程,需要工程师有丰富的经验和技术知识,才能确保模具的准确度和生产效率。
在不同的制品生产中,需要考虑到不同的因素和细节。
只有经过精心设计和细心施工,才能生产出符合要求的高质量制品。
冲压模具设计实例讲解

冲压模具设计实例讲解1. 引言冲压模具是用于制作零部件的工具,广泛应用于汽车、电子、家电等行业。
本文将通过一个冲压模具设计实例,为读者介绍冲压模具设计的根本流程和本卷须知。
2. 设计背景我们以一款汽车车门为例,说明冲压模具的设计过程。
车门是汽车的重要部件之一,需要经过冲压加工来获得所需的形状和尺寸。
3. 设计流程3.1 确定产品要求在冲压模具设计之前,首先要明确产品的要求。
包括车门的尺寸、形状、材料以及制造工艺要求等。
3.2 制定模具设计方案根据产品要求,我们可以开始制定模具设计方案。
主要包括冲头、模座、模具顶板等部件的尺寸、形状和结构设计。
3.3 3D建模在制定模具设计方案后,我们可以使用CAD软件进行3D建模。
这样可以更直观地了解模具的结构、尺寸和装配关系。
3.4 模具加工制造根据3D模型,我们可以进一步进行模具零部件的加工制造。
主要包括数控加工、电火花加工、磨削等工艺。
3.5 模具装配和调试将加工好的模具零部件进行装配,并进行模具调试。
确保模具的各个部位协调运转,到达设计要求。
4. 冲压模具设计的本卷须知4.1 材料选择在冲压模具设计中,材料的选择非常重要。
一般情况下,应选用高强度、高韧性、耐磨损的材料,以保证模具的使用寿命和精度。
4.2 精度要求冲压模具对产品的精度要求很高,因此在设计过程中要考虑到产品的尺寸、形状等因素,并进行适宜的修正和优化。
4.3 加工工艺冲压模具的加工工艺对模具的质量和性能起着决定性的作用。
因此,在制造过程中要选择适宜的加工工艺,并确保加工精度和质量。
4.4 模具保养模具使用后需要定期进行保养和维护,以延长模具的使用寿命。
包括清洁、润滑、更换易损件等工作。
5. 总结冲压模具的设计过程需要考虑产品要求、制定设计方案、进行3D建模、加工制造、装配和调试等多个环节。
同时要注意材料选择、精度要求、加工工艺和模具保养等方面的问题。
通过本文的实例讲解,读者可以更深入地了解冲压模具设计的根本流程和本卷须知。
模具设计实例解析(doc 19页)

模具设计实例解析(doc 19页)模具设计实例1——相机外壳模具设计本单元讲解的实例为按摩器上盖模具设计,按相机外壳模型如图1所示。
图1 相机外壳模型1具体设计步骤1.1启动PRO/E4.0,建立模具文件(1)启动PRO/E。
选择下拉菜单“文件”,“设置工作目录”命令,选择一个合适的工作目录。
(2)选择下拉菜单中“文件”,“新建”命令,弹出1-1所示的“新建”对话框,在“类型”选项组中选择“制造”选项,在“子类型”选项组中选择“模具型腔”选项,在“名称”文本框中输入文件名“anmo”,取消“使用缺省模板”,单击“确定”按钮,弹出”新文件选项“对话框。
图1-1 “新建”对话框(3)在“新文件选项”对话框中选择“mmns_mfg_mold”,然后单击“确定”按钮,则进入PRO/MOLDDESIGN设计模式。
(4)单击“模具制造”工具栏上的“模具型腔布局”按钮,弹出“打开”对话框,同时弹出“布局”对话框,如图1-2所示。
(5)在“打开”对话框中选择“anmo.prt”零件后,单击“打开”按钮,弹出“创建参照模型”对话框,如图1-3所示。
在“创建参照模型”对话框中选择“按参照合并”单选框,单击“确定”按钮接受默认的参照模型名称。
图1-2“布局”对话框图1-3“创建参考模型”对话框(6)单击“布局”对话框中的“参照模型起点与定向”选项区域中的拾取箭头,出现浮动参照模型窗口,同时出现“坐标系类型”菜单管理器,如图1-4所示图1-4浮动参照模型窗口和“坐标系类型”菜单(7)在“坐标系类型”菜单中选择“动态”命令,进入“参照模型方向”对话框如图1-5所示,选择“坐标系移动/定向”按钮,选择“轴”输入数值90。
单击“确定”按钮,返回“布局”对话框,单击“确定”完成参照模型的加载,如图1-6所示。
图1-5 参照模型方向菜单图1-6 参照零件布局结果1.2设置收缩率(1)单击“模具制造”工具栏上的“按比例收缩”按钮,弹出“选取”对话框,按照提示单击任何一个参照模型,选中的模型变成红色。
塑料模具设计步骤与实例精解
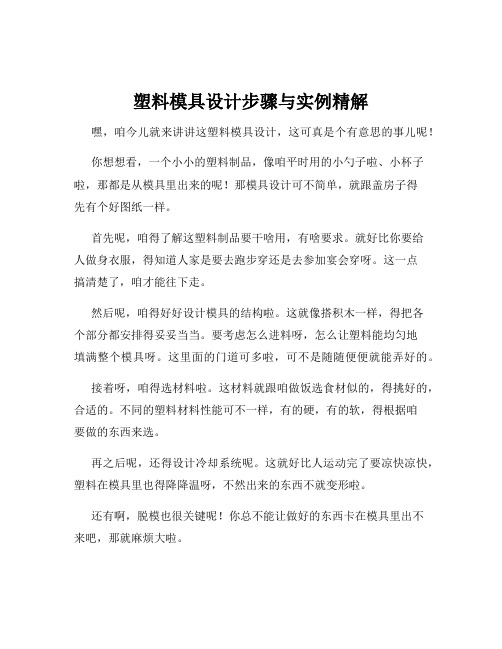
塑料模具设计步骤与实例精解嘿,咱今儿就来讲讲这塑料模具设计,这可真是个有意思的事儿呢!你想想看,一个小小的塑料制品,像咱平时用的小勺子啦、小杯子啦,那都是从模具里出来的呢!那模具设计可不简单,就跟盖房子得先有个好图纸一样。
首先呢,咱得了解这塑料制品要干啥用,有啥要求。
就好比你要给人做身衣服,得知道人家是要去跑步穿还是去参加宴会穿呀。
这一点搞清楚了,咱才能往下走。
然后呢,咱得好好设计模具的结构啦。
这就像搭积木一样,得把各个部分都安排得妥妥当当。
要考虑怎么进料呀,怎么让塑料能均匀地填满整个模具呀。
这里面的门道可多啦,可不是随随便便就能弄好的。
接着呀,咱得选材料啦。
这材料就跟咱做饭选食材似的,得挑好的,合适的。
不同的塑料材料性能可不一样,有的硬,有的软,得根据咱要做的东西来选。
再之后呢,还得设计冷却系统呢。
这就好比人运动完了要凉快凉快,塑料在模具里也得降降温呀,不然出来的东西不就变形啦。
还有啊,脱模也很关键呢!你总不能让做好的东西卡在模具里出不来吧,那就麻烦大啦。
咱来举个例子哈,就说做个简单的塑料碗。
咱得先想好这碗多大呀,多深呀,形状得好看吧。
然后设计模具,让塑料能顺利地流进去,填满每个角落。
材料得选那种结实又安全的,可不能有害物质超标呀。
冷却系统得保证碗能快速冷却成型,脱模的时候得轻轻松松就能把碗拿出来。
你说这塑料模具设计神奇不神奇?这可都是技术活呀!要是没设计好,那做出来的东西不是有瑕疵就是用不了,多浪费呀。
所以啊,这模具设计师可得有真本事,得细心,还得有创意。
咱平时用的那些塑料制品,可都是经过模具设计师精心设计出来的呢。
他们就像魔法师一样,能把一堆塑料变成各种各样有用的东西。
所以呀,可别小看了这塑料模具设计,这里面的学问大着呢!咱得尊重这些设计师的劳动成果,好好珍惜咱用的每一个塑料制品呀。
怎么样,现在是不是对塑料模具设计有了更深的了解啦?嘿嘿!。
冲压模具设计实例讲解
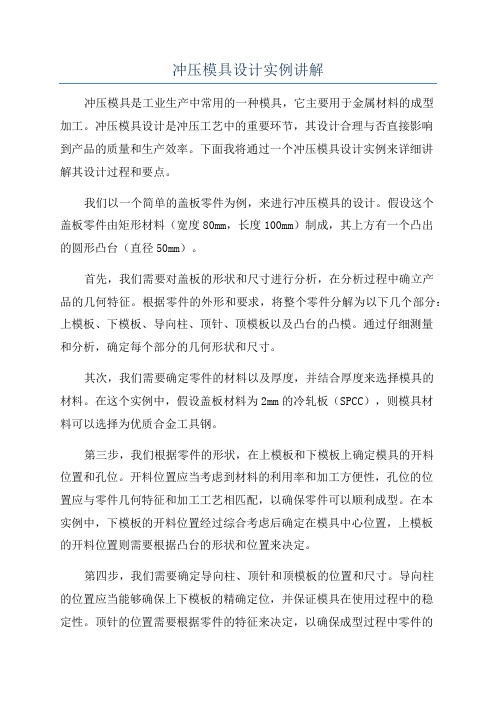
冲压模具设计实例讲解冲压模具是工业生产中常用的一种模具,它主要用于金属材料的成型加工。
冲压模具设计是冲压工艺中的重要环节,其设计合理与否直接影响到产品的质量和生产效率。
下面我将通过一个冲压模具设计实例来详细讲解其设计过程和要点。
我们以一个简单的盖板零件为例,来进行冲压模具的设计。
假设这个盖板零件由矩形材料(宽度80mm,长度100mm)制成,其上方有一个凸出的圆形凸台(直径50mm)。
首先,我们需要对盖板的形状和尺寸进行分析,在分析过程中确立产品的几何特征。
根据零件的外形和要求,将整个零件分解为以下几个部分:上模板、下模板、导向柱、顶针、顶模板以及凸台的凸模。
通过仔细测量和分析,确定每个部分的几何形状和尺寸。
其次,我们需要确定零件的材料以及厚度,并结合厚度来选择模具的材料。
在这个实例中,假设盖板材料为2mm的冷轧板(SPCC),则模具材料可以选择为优质合金工具钢。
第三步,我们根据零件的形状,在上模板和下模板上确定模具的开料位置和孔位。
开料位置应当考虑到材料的利用率和加工方便性,孔位的位置应与零件几何特征和加工工艺相匹配,以确保零件可以顺利成型。
在本实例中,下模板的开料位置经过综合考虑后确定在模具中心位置,上模板的开料位置则需要根据凸台的形状和位置来决定。
第四步,我们需要确定导向柱、顶针和顶模板的位置和尺寸。
导向柱的位置应当能够确保上下模板的精确定位,并保证模具在使用过程中的稳定性。
顶针的位置需要根据零件的特征来决定,以确保成型过程中零件的成型质量。
顶模板则需要根据零件的形状和材料选择合适的凸模形状和尺寸,以确保零件的成型质量。
最后一步,我们需要根据上述设计结果进行模具的绘图制作。
绘图要求精确、准确,需要包含所有的模具建构要素和加工尺寸等信息,以便制造部门进行模具加工和组装。
综上所述,冲压模具设计涉及到多个方面的考虑和决策,需要综合考虑零件的特征、工艺要求、材料特性等多个因素。
通过合理的设计和制作,可以保证模具的质量和使用效果,提高产品的生产效率和质量。
冲压模具设计和制造实例
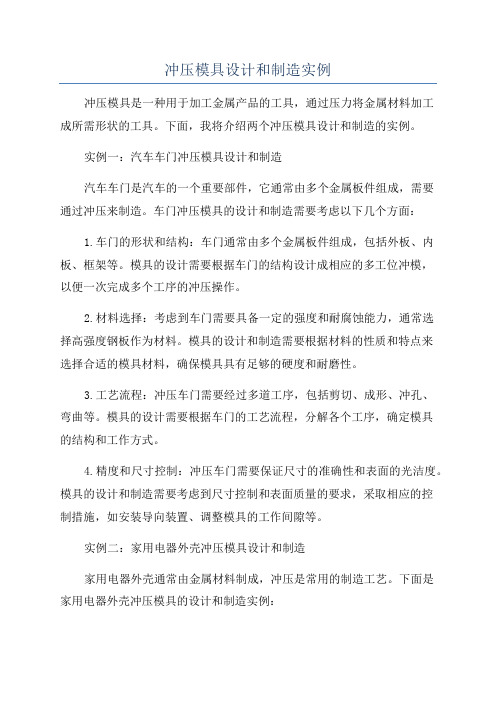
冲压模具设计和制造实例冲压模具是一种用于加工金属产品的工具,通过压力将金属材料加工成所需形状的工具。
下面,我将介绍两个冲压模具设计和制造的实例。
实例一:汽车车门冲压模具设计和制造汽车车门是汽车的一个重要部件,它通常由多个金属板件组成,需要通过冲压来制造。
车门冲压模具的设计和制造需要考虑以下几个方面:1.车门的形状和结构:车门通常由多个金属板件组成,包括外板、内板、框架等。
模具的设计需要根据车门的结构设计成相应的多工位冲模,以便一次完成多个工序的冲压操作。
2.材料选择:考虑到车门需要具备一定的强度和耐腐蚀能力,通常选择高强度钢板作为材料。
模具的设计和制造需要根据材料的性质和特点来选择合适的模具材料,确保模具具有足够的硬度和耐磨性。
3.工艺流程:冲压车门需要经过多道工序,包括剪切、成形、冲孔、弯曲等。
模具的设计需要根据车门的工艺流程,分解各个工序,确定模具的结构和工作方式。
4.精度和尺寸控制:冲压车门需要保证尺寸的准确性和表面的光洁度。
模具的设计和制造需要考虑到尺寸控制和表面质量的要求,采取相应的控制措施,如安装导向装置、调整模具的工作间隙等。
实例二:家用电器外壳冲压模具设计和制造家用电器外壳通常由金属材料制成,冲压是常用的制造工艺。
下面是家用电器外壳冲压模具的设计和制造实例:1.外壳结构和形状:家用电器外壳通常具有盒状结构,需要通过冲压来成形。
模具的设计需要根据外壳的尺寸和形状,设计成相应的单工位或多工位冲模。
2.材料选择:外壳通常采用不锈钢或者冷轧钢板作为材料,以保证外壳的强度和耐腐蚀能力。
模具的设计和制造需要选用适当的模具材料,以确保模具具有足够的硬度和耐磨性。
3.工艺流程:外壳冲压通常包括剪切、成形、冲孔、折弯等工序。
模具的设计需要分解各个工序,确定模具的结构和工作方式,以便一次完成所有工序。
4.精度和表面质量:外壳冲压需要保证尺寸的准确性和表面的光洁度。
模具的设计和制造需要考虑到尺寸控制和表面质量的要求,采取相应的控制措施,如安装导向装置、选用合适的冲头等。
冲压模具结构设计及实例

冲压模具结构设计及实例冲压模具是指用于冲压工艺的模具,它是冲压工艺中的重要组成部分。
冲压模具的结构设计对于冲压工艺的质量和效率具有重要影响。
本文将从冲压模具的结构设计和实例两个方面进行探讨。
一、冲压模具的结构设计冲压模具的结构设计是冲压工艺的关键环节之一。
一个优秀的冲压模具需要具备以下几个方面的设计要素:1. 合理的结构布局:冲压模具的结构布局应该合理,能够满足冲压工艺的要求,并且方便操作和维护。
通常包括上下模座、导向装置、冲头、顶出装置等部分。
2. 合适的材料选择:冲压模具需要承受较大的冲击和摩擦力,因此材料的选择非常重要。
常用的材料有优质合金钢、工具钢等,具有较高的硬度和耐磨性。
3. 合理的导向装置:导向装置能够确保上下模具的准确对位,以保证冲压工艺的精度。
常见的导向装置有滑块导向、销针导向等。
4. 适当的顶出装置:顶出装置能够将冲制件从模具中顶出,以便进行下一步的操作。
顶出装置的设计需要考虑冲制件的形状和尺寸等因素。
5. 合理的冲头设计:冲头是冲压模具的重要组成部分,其设计需要考虑冲制件的形状和尺寸等因素。
同时,冲头的材料选择和热处理也非常重要。
二、冲压模具结构设计实例以下是一个钣金冲压模具的结构设计实例:该冲压模具用于加工一种带有凹槽的钣金零件。
该零件的厚度为2mm,材料为优质冷轧板。
根据对该零件的要求,设计出了以下的冲压模具结构:1. 上模座:采用整体式上模座,材料为优质合金钢。
上模座上设置有导向装置,确保上下模具的准确对位。
2. 下模座:采用整体式下模座,材料为优质合金钢。
下模座上设置有顶出装置,以便将冲制件顶出。
3. 冲头:冲头采用硬质合金材料制造,并经过热处理,以提高其硬度和耐磨性。
冲头的形状和尺寸与钣金零件的凹槽相匹配。
4. 引导装置:在上模座和下模座上设置有引导装置,确保上下模具的准确对位,以保证冲制件的精度。
通过以上的结构设计,该冲压模具能够满足钣金零件的冲压工艺要求。
冲制过程中,上下模具准确对位,冲头能够将钣金材料冲剪成带有凹槽的零件,并通过顶出装置将零件顶出,以便进行下一步的操作。
冲压模具设计实例
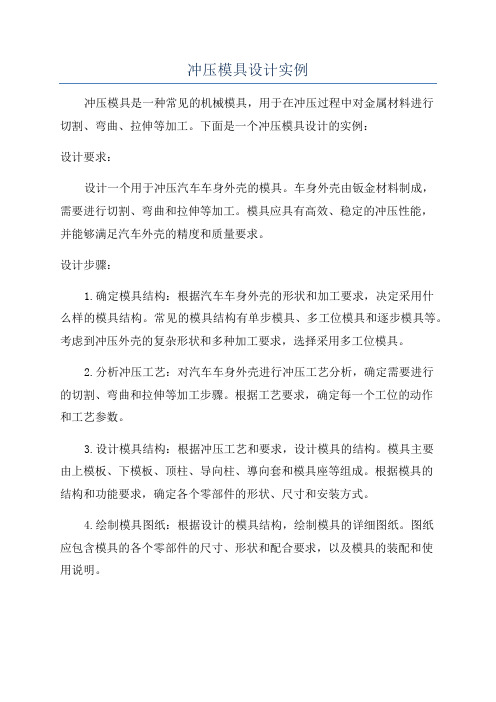
冲压模具设计实例冲压模具是一种常见的机械模具,用于在冲压过程中对金属材料进行切割、弯曲、拉伸等加工。
下面是一个冲压模具设计的实例:设计要求:设计一个用于冲压汽车车身外壳的模具。
车身外壳由钣金材料制成,需要进行切割、弯曲和拉伸等加工。
模具应具有高效、稳定的冲压性能,并能够满足汽车外壳的精度和质量要求。
设计步骤:1.确定模具结构:根据汽车车身外壳的形状和加工要求,决定采用什么样的模具结构。
常见的模具结构有单步模具、多工位模具和逐步模具等。
考虑到冲压外壳的复杂形状和多种加工要求,选择采用多工位模具。
2.分析冲压工艺:对汽车车身外壳进行冲压工艺分析,确定需要进行的切割、弯曲和拉伸等加工步骤。
根据工艺要求,确定每一个工位的动作和工艺参数。
3.设计模具结构:根据冲压工艺和要求,设计模具的结构。
模具主要由上模板、下模板、顶柱、导向柱、導向套和模具座等组成。
根据模具的结构和功能要求,确定各个零部件的形状、尺寸和安装方式。
4.绘制模具图纸:根据设计的模具结构,绘制模具的详细图纸。
图纸应包含模具的各个零部件的尺寸、形状和配合要求,以及模具的装配和使用说明。
5.进行模具加工:根据模具图纸,制作和加工模具的各个零部件。
根据材料的选择和工艺要求,采用不同的加工方式,包括铣削、车削、镗削和磨削等。
6.完成模具装配:将加工好的各个零部件进行装配,确保零部件的配合精度和工作性能。
对模具进行调试和试用,保证模具的稳定性和工艺性能。
7.进行模具试产:使用设计好的模具对汽车车身外壳进行试产。
根据试产效果和质量,对模具进行优化和改进。
对模具的结构和工艺参数进行调整,以提高冲压效率和产品质量。
8.进行产量生产:在模具试产通过后,开始进行批量生产。
根据生产计划,进行模具的换模和调试,确保每个模具的稳定性和工艺性能。
对产量进行检测和控制,保证产品的质量和工艺要求。
以上是一个冲压模具设计的实例。
在实际设计中,还需要考虑材料、设备和加工工艺等因素。
模具设计案例分析

图中红色面在前后模方向为倒扣
2、方案分析
方案一: 此处作一
个斜顶和一个内 行位,顶出前内 行位先退开,斜 顶再顶出
斜顶
后模内行位
方案二: 此处作两个靠在
一起的斜顶,顶出时 两斜顶同时顶出
因方案一中后模内行 位需用油缸先抽,或 是顶出前B板先弹开; 结构较复杂,所以本套 模具采用方案二
斜顶1
斜顶2
公司斜顶设计要点:
1、斜顶常见形式 公司常用斜顶形AB板原身留时采用联杆式
整体式
联杆式
2、斜顶角度的确定 一)、斜顶行程必须大于扣位距离3MM以上,如产品较大且塑料缩 水率较大时,斜顶行程还需考虑塑料缩水率 二)、以扣位距离最大处的斜顶行程和模具顶出行程作直角三角形 的两直角边,得到斜顶的角度A,A需小于等于12度,如果A 大于12度则需加大模具顶出行程,以减小斜顶角度;如果A必 须大于12度时,斜顶需加辅助杆
直身面高度H
L
当前后模开模L2时,行位
在斜导柱作用下后退S1,
必须保证L≥L1+S1+3MM,
L1
否则在合模时A点易撞B点
L2
B
A
弹针背部尽量做成两平面 滑动,不做成球头,以避 免点受力较大而损坏铲鸡 面
弹针压块上的 弹针孔不避空
弹针需作平面 定位防转
1、产品分析 如右图所示,产品
在行位处肋骨较多, 产品易粘行位时,常 在行位上加弹针,以 避免产品被行位拉伤 或拉变形
2、行位弹针3D图示
弹针 弹簧 弹针压块
3、行位弹针设计要点
弹针行程S1 常取5-10MM
直身面高度H需保证前 后模开模H后,行位后 退的行程S2需要小于 弹针的行程S1,否则 弹针会撞坏
冲压模具设计实例

冲压模具设计实例设计实例:汽车车门内板冲压模具1.需求分析首先进行需求分析,了解客户对产品的要求。
在这个实例中,我们的客户要求生产汽车车门内板,需要模具能够冲压出符合要求的车门内板。
2.零件设计根据客户需求,设计车门内板零件。
考虑到实际生产中的材料和工艺要求,确定车门内板的形状、尺寸和厚度等。
3.工艺设计根据车门内板的形状和材料特性,确定冲压工艺。
包括冲压次数、冲压力度、冲裁布局等。
4.模具设计根据上述工艺要求,开始进行冲压模具的设计。
主要步骤如下:(1)模具结构设计:确定模具的结构形式,包括上模座、下模座、导柱、导套等部件。
(2)模具材料选择:根据模具的使用要求和生产批量确定模具材料。
汽车车门内板的生产通常使用耐磨性、强度高的工具钢。
(3)模具零件设计:根据模具结构设计的要求,设计模具的每个零件,包括上模、下模、剪切刀等。
(4)组件装配设计:将每个零件进行装配设计,确保零件可以精准地定位和配合。
(5)冲裁布局设计:根据冲裁过程的要求,确定上模、下模和冲裁刀的位置和布局,确保冲裁过程稳定和准确。
(6)模具热处理设计:由于模具在冲压过程中受到较大的应力和摩擦力,需要进行热处理,提高其硬度和耐磨性。
(7)模具安装设计:考虑到模具的使用和维护,设计合理的模具安装方式,方便更换模具和进行维护。
5.模具加工制造根据模具设计图纸,进行模具加工制造。
包括数控加工、磨削、电火花等工艺。
确保模具加工精度和质量。
6.模具调试和试产完成模具制造后,进行模具的调试和试产。
包括模具的安装和调整,冲压参数的调整等。
确保模具运行稳定和冲压产品质量合格。
通过以上步骤,完成一套汽车车门内板冲压模具的设计和制造。
在实际生产中,可以根据需求进行相应的改进和优化。
冲压模具设计是一门综合性较强的工程技术,需要综合考虑材料、工艺、机械、加工等方面的知识。
只有通过科学合理的设计,才能制造出高质量的冲压模具。
模具设计实例解析(doc 19页)
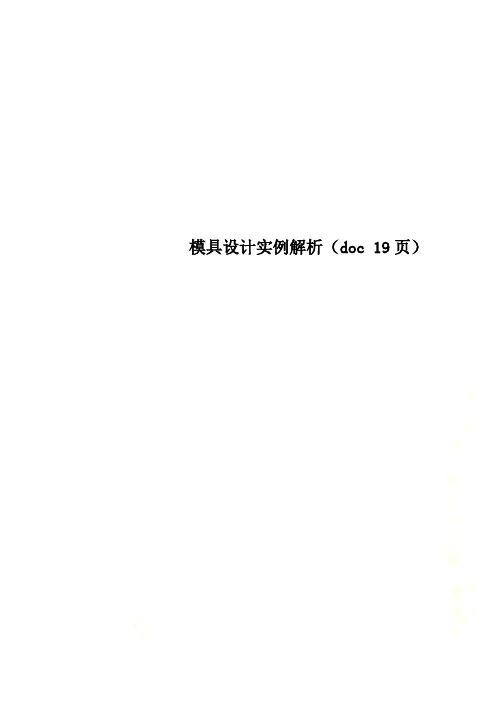
模具设计实例解析(doc 19页)模具设计实例1——相机外壳模具设计本单元讲解的实例为按摩器上盖模具设计,按相机外壳模型如图1所示。
图1 相机外壳模型1具体设计步骤1.1启动PRO/E4.0,建立模具文件(1)启动PRO/E。
选择下拉菜单“文件”,“设置工作目录”命令,选择一个合适的工作目录。
(2)选择下拉菜单中“文件”,“新建”命令,弹出1-1所示的“新建”对话框,在“类型”选项组中选择“制造”选项,在“子类型”选项组中选择“模具型腔”选项,在“名称”文本框中输入文件名“anmo”,取消“使用缺省模板”,单击“确定”按钮,弹出”新文件选项“对话框。
箭头,出现浮动参照模型窗口,同时出现“坐标系类型”菜单管理器,如图1-4所示图1-4浮动参照模型窗口和“坐标系类型”菜单(7)在“坐标系类型”菜单中选择“动态”命令,进入“参照模型方向”对话框如图1-5所示,选择“坐标系移动/定向”按钮,选择“轴”输入数值90。
单击“确定”按钮,返回“布局”对话框,单击“确定”完成参照模型的加载,如图1-6所示。
图1-5 参照模型方向菜单图1-6 参照零件布局结果1.2设置收缩率(1)单击“模具制造”工具栏上的“按比例收缩”按钮,弹出“选取”对话框,按照提示单击任何一个参照模型,选中的模型变成红色。
(2)在弹出的“按比例收缩”对话框中选择“1+S”收缩率公式,选中参照模型中的坐标系PRT_CSYS_DEF,在“收缩率”文本框中输入0.005,如图1-7所示。
(3)单击“按比例收缩”对话框中的“确定”按钮,即可完成全部零件的收缩率设置。
图1-7 设置按比例收缩参数1.3创建工件创建工件步骤如下:(1)选择“模具”菜单管理器中的“模具模型”,“创建”,“工件”,“自动”命令,将弹出“自动工件”对话框,选择MOLD_DEF_CSYS坐标系作为模具原点,从“形状”下拉列表中选择工件的形状为“标准矩形”,单位为mm,并接受默认的工件名称,图形区中将显示包容零件的工件,如图1-8所示。
模具设计案例分析-纯干货
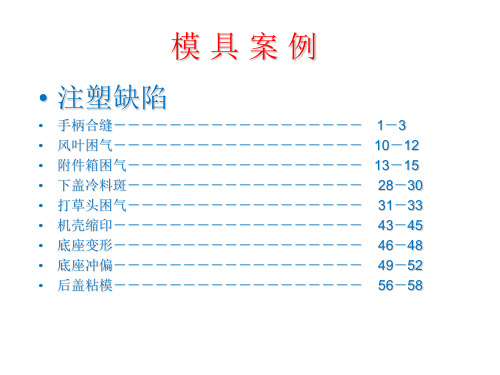
结果: 问题解决。
注塑缺陷
零件代号 零件名称 产品尺寸 出数 注塑机
GT01FM.30.01 打草头 Φ81*43 1*2 128T
产品介绍: 本产品为风叶,筋板多,而且薄.
问题点: 注塑过程中筋板打不饱。
注塑缺陷
改善前 1,改善前,试模后观察产品哪些筋板注 塑过程中出现不饱的,在其位置加排气镶 针.
性较差。风扇各扇叶较深,且有较高的动平衡 要求。
问题点:
由于PA+GF30%流动性较差,且扇叶较 深,在成型时需要较高的注射压力才能将其 注满,但扇叶的最末端会出现困气现象,中 间装电机轴的位置在模具上强度如果不够也 会产生变形,导致无法满足同心度要求。
注塑缺陷
改善前
1,简化三板模,细水口。 2,产品筋板较多,需要较大注塑压力,模具 中间的镶针在高压的状态下容易变形。 3,筋板较细,容易困气。
注塑缺陷
改善前 由于产品外观要求的局限性,产品结构无法 改变。变形不可避免。
改善后 在产品内部增加横向筋板并增加空心柱与下 盖过盈配合。
注塑缺陷
分析: 上下手柄由于外观设计的限制,上下手柄横向与纵向比例相差较大,两边有
较大弧度,筋板的支撑无法控制产品的变形。上手柄没有横向筋板,产品不可避 免地会向中间收缩。而下手柄有足够的横向筋支撑,模向的变形相对较小,所以 上下手柄合起来时会产生合缝。
注塑缺陷
零件代号 零件名称 产品尺寸 出数 注塑机
VK01SR.10.05 VK01SR.10.04
上手柄
下手柄
200*50*61
188*49*57
1*2
1*2
150T
150T
产品介绍: 上下手柄采用止口配合,材料为PP。
- 1、下载文档前请自行甄别文档内容的完整性,平台不提供额外的编辑、内容补充、找答案等附加服务。
- 2、"仅部分预览"的文档,不可在线预览部分如存在完整性等问题,可反馈申请退款(可完整预览的文档不适用该条件!)。
- 3、如文档侵犯您的权益,请联系客服反馈,我们会尽快为您处理(人工客服工作时间:9:00-18:30)。
模具设计实例1——相机外壳模具设计本单元讲解的实例为按摩器上盖模具设计,按相机外壳模型如图1所示。
图1 相机外壳模型1具体设计步骤1.1启动PRO/E4.0,建立模具文件(1)启动PRO/E。
选择下拉菜单“文件”,“设置工作目录”命令,选择一个合适的工作目录。
(2)选择下拉菜单中“文件”,“新建”命令,弹出1-1所示的“新建”对话框,在“类型”选项组中选择“制造”选项,在“子类型”选项组中选择“模具型腔”选项,在“名称”文本框中输入文件名“anmo”,取消“使用缺省模板”,单击“确定”按钮,弹出”新文件选项“对话框。
图1-1 “新建”对话框(3)在“新文件选项”对话框中选择“mmns_mfg_mold”,然后单击“确定”按钮,则进入PRO/MOLDDESIGN设计模式。
(4)单击“模具制造”工具栏上的“模具型腔布局”按钮,弹出“打开”对话框,同时弹出“布局”对话框,如图1-2所示。
(5)在“打开”对话框中选择“anmo.prt”零件后,单击“打开”按钮,弹出“创建参照模型”对话框,如图1-3所示。
在“创建参照模型”对话框中选择“按参照合并”单选框,单击“确定”按钮接受默认的参照模型名称。
图1-2“布局”对话框图1-3“创建参考模型”对话框(6)单击“布局”对话框中的“参照模型起点与定向”选项区域中的拾取箭头,出现浮动参照模型窗口,同时出现“坐标系类型”菜单管理器,如图1-4所示图1-4浮动参照模型窗口和“坐标系类型”菜单(7)在“坐标系类型”菜单中选择“动态”命令,进入“参照模型方向”对话框如图1-5所示,选择“坐标系移动/定向”按钮,选择“轴”输入数值90。
单击“确定”按钮,返回“布局”对话框,单击“确定”完成参照模型的加载,如图1-6所示。
图1-5 参照模型方向菜单图1-6 参照零件布局结果1.2设置收缩率(1)单击“模具制造”工具栏上的“按比例收缩”按钮,弹出“选取”对话框,按照提示单击任何一个参照模型,选中的模型变成红色。
(2)在弹出的“按比例收缩”对话框中选择“1+S”收缩率公式,选中参照模型中的坐标系PRT_CSYS_DEF,在“收缩率”文本框中输入0.005,如图1-7所示。
(3)单击“按比例收缩”对话框中的“确定”按钮,即可完成全部零件的收缩率设置。
图1-7 设置按比例收缩参数1.3创建工件创建工件步骤如下:(1)选择“模具”菜单管理器中的“模具模型”,“创建”,“工件”,“自动”命令,将弹出“自动工件”对话框,选择MOLD_DEF_CSYS坐标系作为模具原点,从“形状”下拉列表中选择工件的形状为“标准矩形”,单位为mm,并接受默认的工件名称,图形区中将显示包容零件的工件,如图1-8所示。
(2)“偏移”选项区的数字由灰色变成可操作的黑色,在统一“统一偏距”文本中输入20,单击ENTER键,在图形区显示各方向尺寸边界。
在“整体尺寸”区的“X,Y+Z型腔,-Z型腔”文本框中输入1-9所示的数据,单击“确定”按钮,完成工件的设置。
图1-8 包容零件工件图1-9 设置整体参数及其工件结果1.4创建模具体积块1.创建动模体积块(1)单击“模具制造”工具栏上的“模具体积快”按钮,进入体积块工作界面。
(2)选择下来菜单中“编辑”,“属性”命令,打开“属性”对话框,然后在“名称”文本框中输入体积快名称“core_insert_1”,如图1-10所示。
最后单击对话框底部的“确定”按钮,退出对话框。
图1-10 设置体积块名称(3)按“滑块体积块”对话框的,则Pro/e系统会自动计算出卡钩的两个方形孔为干涉曲面,同时显示在画面上。
如图1-11和图1-12所示:图1-11 滑块体积块图1-12 干涉曲面(4)按住键盘的Ctrl键选取两个干涉曲面面组1及面组2,再按,按对话框下方投影栏框的,然后点选工件正面为投影面,如图1-13所示:图1-13按“滑块体积块”对话框的,即可见滑块体积块如图1-14图1-14 侧滑块1.5 产生棱线,作为分型线按主窗口右侧自动化创建分型线的图标由于滑块将额外独立处理,因此将滑块的棱线从分型线中排除(1)由侧面影像曲线对话框选取“环选取”,然后在按“定义”如图1-15图1-15(2)在出现选取环对话框,点选“编号4”的环,则滑块部分的线段被选取如图,在按排除,按选项“卡链”,选取点选“编号5—1”的环,则孔的上环被选中,在按“下部”,如图1-16,在按“确定”。
图1-16 定义分型线1.6 以裙边曲面创建分型面按主窗口右侧分型面的图标在按裙边曲面的图标(1)选取如图所示的棱线作为分型线,然后按完成,以完成线条选取如图1-16所示图1-16 选取分型线(2)由裙边曲面对话框选取“延伸”,然后按“定义”如图1-17,按延伸控制对话框中下方的“添加”如图1-18,按住“标左键”,框选参照零件右后的两个点如图1-19,然后按“确定”,在按“完成”,以完成点的选取,点选工件的背面,以指定延伸方向垂直与此平面在按“确定”,以确定延伸方向朝后。
同样定义零件右前的两个点。
图1-17图1-18图1-19(3)按延伸控制对话框的确定,按裙边曲面对话框的确定,已完成裙边的曲面的定义,在按主窗口右侧的图标,完成分型面的定义,如图1-20:图1-20 分型面1.7创建浇道系统(1)创建浇口选取下拉式菜单插入下的旋转,按住鼠标右键,由快捷菜单中选取定义内部草绘,以Front为参考平面按草绘对话框的草绘,绘制如图草绘如图1-21:,按草绘中,在按主窗口。
图1-21 草绘浇口(2)创建流道选取下拉菜单插入下的“流道”。
选取“倒圆角”,输入流道直径“6”,按键盘的“回车”。
选取上次的草绘平面,如图1-22绘制一条直线,按主窗口右侧的。
图1-22 草绘流道在相交对话框中按“自动添加’,即可见在模型名称栏框显示出与流道有相交的零件为工件,如图。
在按相交组件对话框的“确定”。
按流道对话框的“确定”,以结束流道的创建。
(3)创建注道选取下拉式菜单插入下的旋转。
按住鼠标右键,由快捷菜单中选取定义内部草绘,选取上次的草绘平面,按草绘对话框的草绘,绘制如图1-23的草绘平面。
按图标板的,以完成注道的创建。
图1-23 草绘注道1.8 创建水路(1)在凸模创建水路选取下拉式菜单插入下的等高线,水路直径8,按键盘回车。
以下列方式作选取以Right平面向上平移30作为一个基准平面,绘制草绘图。
如图1-24:图1-24凸模水路草绘图在相交组件对话框中按自动添加,按组件相交对话框的确定。
按等高线的对话框的确定,以结束的创建。
(2)在凹模创建水路。
方法同上,以下列方式作选取以Right平面向下平移20作为一个基准平面,以凸模水路为参照绘制草绘。
图如1-25:图1-25 凹模水路草绘图在相交组件对话框中按自动添加,按组件相交对话框的确定。
按等高线的对话框的确定,以结束的创建。
如图1-26:图1-26 水路1.9以分型面分割出凸模及凹模的体积分割体积块1.分割体积块core_insert_1(1)单击“模具遮蔽对话框工具栏上的“遮蔽/取消遮蔽”,打开对话框。
然后单击“取消遮蔽”按钮,切换到“取消遮蔽”选项卡。
单击“过滤”区域中的按钮,切换到“体积块”过滤类型。
然后单击按钮,选中所有体积块,并单击按钮,将其显示出来。
单击对话框底部的“关闭”按钮,退出对话框。
(2)单击“模具制造”工具栏上的“分割工件”按钮,然后弹出“分割体积块”菜单中单击“一个体积块“,”所有工件”,“完成”命令,打开“分割”对话框。
(3)在图形窗口中选择如图1-27所示的“core_insert_1”,然后单击“选取”对话框中的“确定”按钮,并在弹出的“岛列表”中选中“岛1”选项。
(4)单击“岛列表”菜单中“完成选取”命令,返回“分割”对话框。
然后单击对话框中的“确定”按钮,此时,系统加亮显示分割生成的体积块,并弹出“属性”对话框。
(5)在对话框中输入体积块名称“temp_1”,然后单击对话框底部的“确定”按钮,完成分割操作。
图1-27 选取core_insert_1体积块2.分割动定模(1)单击“模具制造”工具栏上的“分割工件”按钮,然后弹出“分割体积块”菜单中单击“两个体积块”,“模具体积块”,“完成”命令,打开“搜索工具”对话框。
(2)在对话框中的“找到的项目”l列表中选中“temp_1”,然后单击按钮,将其放置到“选定的项目”列表中。
最后单击对话框中的“关闭”按钮,打开“分割”对话框。
(3)在图形窗口中选择如图1-28所示的分型曲面,然后单击“选取”对话框中的“确定”按钮,返回“分割”对话框。
图1-28 选取分型曲面(4)单击对话框底部的“确定”按钮,此时,系统加亮显示分割生成的体积块,并弹出“属性”对话框。
(5)在对话框中输入体积块名称“core”,然后单击“着色”按钮,如1-29所示。
(6)单击对话框底部的“确定”按钮,系统会加亮显示分割生成的另一个体积块,并弹出“属性”对话框。
然后在该对话框中输入体积块名称“cavity”,并单击“着色”按钮,着色体积块如图1-30所示。
(7)单击对话框底部的“确定”按钮,完成分割操作。
图1-29 着色“core”体积块图1-30 着色“cavity”体积块2.0分割体积块(1)单击“模具”工具栏上的图标按钮,打开“创建模具元件”对话框。
然后按住“CTRL”键不放,并选中如图1-31所示的模具体积块。
图1-31 “创建模具元件”对话框(1)单击“高级”选项前面的三角形符号,然后在弹出的“高级”区域中单击按钮,选中所有的模具体积块。
(2)单击对话框底部的“确定”按钮,完成抽取模具元件操作。
2.1 铸模(1)单击“模具”菜单管理器重的“铸模”选项,在弹出的下拉菜单中选择“创建”命令。
在消息区中“输入零件名称”后的文本框中输入“molding”后,单击右侧的按钮。
(2)在消息区中“输入模具零件公用名称”后的文本框中输入“mold”后,单击“ENTER”键,即完成浇注件的生成,如图1-32所示。
图1-32 生成浇注件6.1.9 仿真开模(1)单击“模具遮蔽对话框”工具栏上的按钮,打开“遮蔽-取消遮蔽”对话框。
遮蔽体积块,分型面,参照模型和工件。
(2)单击右侧“模具”菜单中的“模具进料孔”,“定义间距”,“定义移动”命令,然后在图形窗口中选择如图1-33所示的“cavity”元件,并单击“选取”对话框中的“确定”按钮。
(3)在图形窗口中选取1-33所示的面,此时“cavity”元件上会出现一个红色箭头,表示移动方向。
(4)在消息区中的文本框中输入数值“100”,然后单击右侧的按钮,返回“定义间距”菜单。
此时,“cavity”元件将向上移动。
图1-33 移动“cavity”元件图1-34 移动“core”元件(5)单击“定义间距”菜单中“定义移动”命令,然后在图形区中选择如图1-34所示的“core”元件。