模具设计实例
ug注塑模具设计实例

ug注塑模具设计实例以下是一个简单的注塑模具设计实例,模具设计的基本概念和步骤。
设计案例:一个简单的塑料瓶盖模具1. 确定产品尺寸和形状产品是一个简单的塑料瓶盖,直径为20mm,高度为3mm。
瓶盖表面有纹理,以增加摩擦力,方便开启。
2. 确定模具结构模具采用典型的双板模结构,由动模板和定模板组成。
动模板上设有型腔,定模板上设有浇口和流道。
3. 确定型腔布局由于瓶盖尺寸较小,可以采用一模一腔的布局。
型腔布置在动模板上,浇口和流道布置在定模板上。
4. 设计浇口和流道浇口和流道的设计需要考虑塑料的填充和流动。
本例中,采用点浇口,浇口直径为1mm,流道直径为4mm。
5. 设计推出机构推出机构用于将成型后的产品从模具中推出。
本例中,采用推杆推出,推杆直径为8mm,数量为4个。
推杆安装在动模板上,推出时推动瓶盖脱离型腔。
6. 设计冷却系统冷却系统用于将成型过程中的热量从模具中带走,防止产品变形和开裂。
本例中,采用水管冷却,水管直径为4mm,布置在动模板和定模板上。
7. 设计排气系统排气系统用于将成型过程中的气体从模具中排出,防止气体的积聚和压力的升高。
本例中,采用排气槽,排气槽直径为2mm,数量为4个。
排气槽布置在定模板上。
8. 设计模具零件加工工艺性模具零件的加工需要考虑其工艺性。
本例中,采用数控加工中心进行加工,材料选择不锈钢。
9. 设计模具装配工艺性模具装配需要考虑其工艺性。
本例中,采用螺钉连接动模板和定模板,并使用定位销进行定位。
以上是一个简单的注塑模具设计实例,希望能帮助您更好地理解模具设计的基本概念和步骤。
钣金模具设计实例

评审与修改
对设计结果进行评审,根据评审 意见进行必要的修改和完善。
需求分析
明确设计任务和目标,收集相关 资料和数据,进行初步的需求分 析。
出图与归档
完成最终的设计图纸,整理相关 文件和资料,进行归档保存。
02
钣金模具设计实例解析
实例一:手机外壳模具设计
手机外壳模具设计需要考 虑的因素包括材料、结构、 工艺和外观等。
经济性
在满足功能和性能要求的前提 下,应尽可能降低模具制造成 本。
可持续性
设计时需考虑环保和可持续性 ,优先选择环保材料和工艺,
降低能耗和资源消耗。
钣金模具的应用领域
航空航天
钣金模具在航空航天领域中广泛应用于制造 飞机、卫星等复杂结构件。
家用电器
钣金模具在家用电器领域用于生产电视、冰 箱、空调等产品的外壳和内部结构件。
外观方面要求模具设计简洁、美 观,符合市场和用户需求。
03
钣金模具设计中的常见 问题与解决方案
问题一:模具强度不足
总结词
模具强度不足可能导致生产过程中出现变形、断 裂等问题,影响产品质量和生产效率。
2. 结构设计不合理
优化模具结构,合理布置加强筋、支撑柱等结构, 提高整体强度。
ABCD
1. 材料选择不当
钣金模具设计实例
目 录
• 钣金模具设计概述 • 钣金模具设计实例解析 • 钣金模具设计中的常见问题与解决方案 • 钣金模具设计的未来发展趋势
01
钣金模具设计概述
设计理念与原则
创新性
钣金模具设计应注重创新,通 过独特的设计理念和原则,实 现产品的高效、美观和实用性
。
功能性
设计时应充分考虑钣金模具的 功能需求,确保其能够满足生 产过程中的各种要求。
模具毕业设计实例冲裁模设计举例

冲裁模设计举例图2.69所示零件为电视机安装架下板展开坯料,材料为1Cr 13,厚度mm t 3=,未注圆角半径mm R 1=,中批量生产,确定产品的冲裁工艺方案并完成模具设计。
图2.69 零件图1. 冲裁件工艺性分析零件的加工涉及冲孔和落料两道工序。
除孔中心尺寸公差为±0.1mm 和孔径尺寸公差为+0.2mm 外,其余尺寸均为未注公差,查表2.4可知,冲裁件内外形的达到的经济精度为IT12~IT14级。
符合冲裁的工艺要求。
查表2.2可知,一般冲孔模冲压该种材料的最小孔径为d ≥1.0t ,t =3mm,因而孔径ø8mm 符合工艺要求。
由图可知,最小孔边距为:d =4mm ,大于材料厚度3mm ,符合冲裁要求。
2. 确定冲裁工艺方案及模具结构形式该冲裁件对内孔之间和内孔与外缘之间有较高的位置精度的要求,生产批量较大,为保证孔的位置精度和较高的生产效率,采用冲孔落料复合冲裁的工艺方案,且一次冲压成形。
模具结构采用固定挡料销和导料销对工件进行定位、弹性卸料、下方出料方式的倒装式复合冲裁模结构形式。
3. 模具设计与计算(1)排样设计排样设计主要确定排样形式、条料进距、条料宽度、材料利用率和绘制排样图。
1)排样方式的确定。
根据冲裁件的结构特点,排样方式可选择为:直排。
2)送料进距的确定。
查表2.7,工件间最小工艺搭边值为mm 2.2,可取mm a 31=。
最小工艺边距搭边值为mm 5.2,取mm a 3=。
送料进距确定为mm h 44.199=。
3)条料宽度的确定。
按照无侧压装置的条料宽度计算公式,查表2.8、表2.9确定条料与导料销的间隙和条料宽度偏差分别为mm mm b 0.1,0.10=∆=。
()()0100093132862-∆-∆-=+⨯+=++=b a L B4)材料利用率的确定。
%08.91%10044.1999344.19686=⨯⨯⨯==Bh A η 4)绘制排样图。
双色注射模具设计10个实例(经典案例)

双⾊注射模具设计10个实例(经典案例)这是⼀款⼿机护套,如下图产品分析:此款为某品牌⼿机的外圈护套,由⼆种塑料(PC+TPE)组成。
由于要求外形美观光滑,分模线必须做在内侧圆弧切点,所以外模要四⾯滑开,再看内侧,四周全部是内扣的,必须全⽅位内抽芯,也就是俗称的“爆炸芯”。
关于“爆炸芯”的模具结构,假如是普通的注塑模具,已经有⾮常经典的机构,我下⾯将有详细的介绍。
现在问题是双⾊模具,有⼆组动模和⼆组定模,⼆组动模的所有部件是完全⼀致的,要在双⾊注塑机的转盘上进⾏180度旋转,⼆种不同的塑料分别射进模腔,注射硬胶(PC)时动模的顶出机构和抽芯机构不动作,再注射软胶(TPE)并开模后,对准软胶料筒的⼀侧的动模的抽芯机构和顶出机构才开始动作,将完整的双⾊制品顶出。
由于动模旋转后,交换⼜合模后的浇⼝必须在同⼀位置,所以软胶和硬胶的浇⼝的处理显得令⼈困惑。
由于模具必须四周都要进⾏“内外同抽”,内、外滑块怎样排列,轨道设置在哪⾥?这个问题同样有被逼⼊墙⾓的感觉。
且不谈模具滑块机构的复杂性,我们从双⾊模具的基本原理来考虑,硬胶部分的成型和内外同抽机构是⼀定要设置在定模⼀侧的,软胶部分的成型机构也要设置在定模。
⽽且这个部分是由内外同抽的机构组成的凸起插⼊到动模的凹槽中。
转盘旋转180度后,这组凸起刚好插⼊到另外⼀个动模的凹槽中。
也就是说,⼆个定模上的由内外同抽滑块组成的凸起的外部形状和尺⼨是完全相同的。
仅仅是成型软胶和硬胶的型⾯不同⽽已。
问题的难点是,这个凸起会分成上下⼆层,⼀层向外移动,另⼀层向内移动,也就是俗称的“内外同抽”,合成的凸起的侧⾯是⼀个统⼀的斜⾯,但是,传统的滑块必须要有滑动轨道等必要的条件,怎样设置轨道?这便成了本案例的核⼼问题。
我是这样设置动模部分的凹槽和定模部分凸起的。
动模的凹槽是这样的。
下⾯我们来探讨定模部分的设计1.01定模内外同抽的设计基本机构是这样的当A板和定模底板分开35mm后拨块拨动内滑块,同时通过齿轮的传动,外滑块向外移动。
注塑模具设计实例
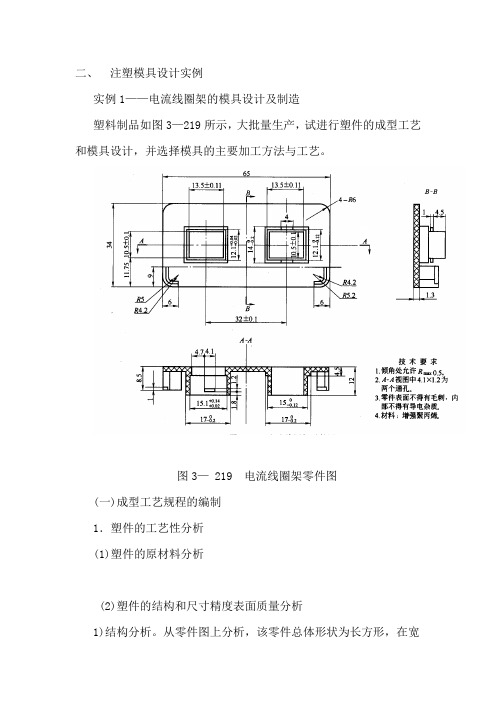
二、注塑模具设计实例实例1——电流线圈架的模具设计及制造塑料制品如图3—219所示,大批量生产,试进行塑件的成型工艺和模具设计,并选择模具的主要加工方法与工艺。
图3— 219 电流线圈架零件图(一)成型工艺规程的编制1.塑件的工艺性分析(1)塑件的原材料分析(2)塑件的结构和尺寸精度表面质量分析1)结构分析。
从零件图上分析,该零件总体形状为长方形,在宽度方向的一侧有两个高度为8.5mm ,R5mm 的两个凸耳,在两个高度为12mm 、长、宽分别为17mm 和13.5mm 的凸台上,一个带有的凹槽(对称分布),另一个带有4.lmmXl .2 mm 的凸台对称分布。
因此,模具设计时必须设置侧向分型抽芯机构,该零件属于中等复杂程度。
2)尺寸精度分析。
该零件重要尺寸如:012.01.12-mm 、04.002.01.12++mm 、14.002.01.15++mm 、012.01.15-mm 等精度为3级(Sj1372—78),次重要尺寸如:13.5±0.11、02.017-mm 、10.5±0.1mm 、02.014-mm 等的尺寸精度为4~5级(Sj 1372—78)。
由以上分析可见,该零件的尺寸精度中等偏上,对应的模具相关零件的尺寸加工可以保证。
从塑件的壁厚上来看,壁厚最大处为1.3mm ,最小处为0.95mm ,壁厚差为0.35mm ,较均匀,有利于零件的成型。
3)表面质量分析。
该零件的表面除要求没有缺陷、毛刺,内部不得有导电杂质外,没有特别的表面质量要求,故比较容易实现。
综上分析可以看出,注射时在工艺参数控制得较好的情况下,零件的成型要求可以得到保证。
(3)计算塑件的体积和质量计算塑件的质量是为了选用注射机及确定型腔数。
经计算塑件的体积为V =4087mm 3;计算塑件的质量:根据设计手册可查得增强聚丙烯的密度为ρ=1.04g /cm 3。
故塑件的质量为W =V ρ=4.25g采用一模两件的模具结构,考虑其外形尺寸、注射时所需压力和工厂现有设备等情况,初步选用注射机为XS—Z—60型。
模具设计实例解析(doc 19页)

模具设计实例解析(doc 19页)模具设计实例1——相机外壳模具设计本单元讲解的实例为按摩器上盖模具设计,按相机外壳模型如图1所示。
图1 相机外壳模型1具体设计步骤1.1启动PRO/E4.0,建立模具文件(1)启动PRO/E。
选择下拉菜单“文件”,“设置工作目录”命令,选择一个合适的工作目录。
(2)选择下拉菜单中“文件”,“新建”命令,弹出1-1所示的“新建”对话框,在“类型”选项组中选择“制造”选项,在“子类型”选项组中选择“模具型腔”选项,在“名称”文本框中输入文件名“anmo”,取消“使用缺省模板”,单击“确定”按钮,弹出”新文件选项“对话框。
图1-1 “新建”对话框(3)在“新文件选项”对话框中选择“mmns_mfg_mold”,然后单击“确定”按钮,则进入PRO/MOLDDESIGN设计模式。
(4)单击“模具制造”工具栏上的“模具型腔布局”按钮,弹出“打开”对话框,同时弹出“布局”对话框,如图1-2所示。
(5)在“打开”对话框中选择“anmo.prt”零件后,单击“打开”按钮,弹出“创建参照模型”对话框,如图1-3所示。
在“创建参照模型”对话框中选择“按参照合并”单选框,单击“确定”按钮接受默认的参照模型名称。
图1-2“布局”对话框图1-3“创建参考模型”对话框(6)单击“布局”对话框中的“参照模型起点与定向”选项区域中的拾取箭头,出现浮动参照模型窗口,同时出现“坐标系类型”菜单管理器,如图1-4所示图1-4浮动参照模型窗口和“坐标系类型”菜单(7)在“坐标系类型”菜单中选择“动态”命令,进入“参照模型方向”对话框如图1-5所示,选择“坐标系移动/定向”按钮,选择“轴”输入数值90。
单击“确定”按钮,返回“布局”对话框,单击“确定”完成参照模型的加载,如图1-6所示。
图1-5 参照模型方向菜单图1-6 参照零件布局结果1.2设置收缩率(1)单击“模具制造”工具栏上的“按比例收缩”按钮,弹出“选取”对话框,按照提示单击任何一个参照模型,选中的模型变成红色。
ug注塑模具设计实例

ug注塑模具设计实例(实用版)目录1.UG 注塑模具设计简介2.UG 注塑模具设计实例介绍3.设计实例的具体步骤4.设计实例的优点与不足5.总结正文【1.UG 注塑模具设计简介】UG 注塑模具设计是一种利用 UG(Unigraphics)软件进行注塑模具设计的方法。
UG 是一款强大的三维建模软件,广泛应用于机械设计、制造等领域。
通过 UG 注塑模具设计,可以实现产品的快速开发、降低生产成本、提高生产效率。
【2.UG 注塑模具设计实例介绍】本文将以一个简单的实例介绍 UG 注塑模具设计的具体流程。
实例为一个长方体的注塑模具设计,长方体的尺寸为 100mm×100mm×100mm,材料为聚丙烯(PP)。
【3.设计实例的具体步骤】(1)创建模具模型:首先,在 UG 软件中创建一个新的模具模型文件,并导入长方体产品的三维模型。
(2)设置收缩率:根据聚丙烯材料的收缩率,设置模具的收缩率,以保证模具在注塑过程中能够顺利脱模。
(3)创建模具坐标系:建立模具的坐标系,用于定义模具的各个组件的位置和方向。
(4)创建模具零件:根据模具的结构要求,创建模具的各个零件,如模具主体、冷却系统、喷嘴等。
(5)装配模具零件:将各个模具零件装配到模具坐标系中,并调整它们的位置和方向,以满足模具的功能要求。
(6)定义模具操作:定义模具的开模、合模、注射、保压等操作,以及相关的运动轨迹和时间。
(7)模拟注塑过程:通过软件模拟注塑过程,检查模具设计的合理性,如模具的填充、冷却、脱模等过程是否正常。
(8)修改模具设计:根据模拟结果,对模具设计进行相应的修改,以达到最佳的注塑效果。
【4.设计实例的优点与不足】优点:通过 UG 注塑模具设计,可以快速地创建模具模型,减少设计周期;同时,可以模拟注塑过程,预测潜在的问题,提高产品的设计质量。
不足:UG 注塑模具设计对操作者的技术水平要求较高,需要掌握一定的三维建模和注塑工艺知识;另外,软件操作较为复杂,需要一定的学习成本。
冲压磨具结构设计的十大经典案例

冲压磨具结构设计的十大经典案例案例一:汽车车身冲压件的多工位磨具汽车车身冲压件的磨具设计具有独特的特点和挑战。
为了提高生产效率和质量,设计师通常需要设计多工位磨具。
多工位磨具可以在一次夹紧的情况下完成多个冲压工序,大大提高了冲压生产线的效率。
案例二:飞机翼罩冲压模具飞机翼罩是航空领域中关键的部件之一,其冲压模具设计要求非常高。
翼罩的形状复杂且精度要求高,需要考虑到翼罩的强度、刚度和表面光洁度等因素。
设计师经过精心的磨具结构设计,保证了飞机翼罩的质量和性能。
案例三:家电外壳冲压磨具家电外壳冲压磨具的设计要求外壳的造型美观,同时要满足耐用性和制造成本的要求。
设计师通过合理的冲压工艺和磨具结构设计,实现了家电外壳的高效生产和质量控制。
案例四:电子产品金属外壳冲压模具电子产品金属外壳的冲压模具设计要考虑到外壳的精度、尺寸稳定性和表面处理要求。
设计师通过合理的模具结构设计和冲压工艺,实现了电子产品外壳的高质量和高效生产。
案例五:手机壳冲压模具手机壳的冲压模具设计要考虑到外观要求,如曲面和切割边缘的处理。
设计师通过创新的磨具结构设计和冲压工艺,实现了手机壳的设计复杂性和高质量要求。
案例六:钢铁行业冲压磨具设计钢铁行业的冲压磨具设计要考虑到材料的硬度和可加工性。
设计师通过合理的磨具结构设计和冲压工艺,提高了钢铁行业的生产效率和产品质量。
案例七:航天器零部件冲压模具航天器零部件的冲压模具设计要求非常高,需要考虑到零部件的材料性能、结构复杂度和重量要求等因素。
设计师通过优化的磨具结构设计和精细的制造工艺,实现了航天器零部件的高质量和可靠性。
案例八:新能源汽车零部件冲压模具新能源汽车零部件的冲压模具设计要考虑到其特殊材料和结构要求。
设计师通过创新的磨具结构设计和精细的制造工艺,实现了新能源汽车零部件的高质量和可靠性。
案例九:家具五金件冲压模具家具五金件的冲压模具设计要考虑到五金件的形状复杂度和表面质量要求。
设计师通过合理的磨具结构设计和冲压工艺,实现了家具五金件的高质量和高效生产。
冲压模设计经典案例
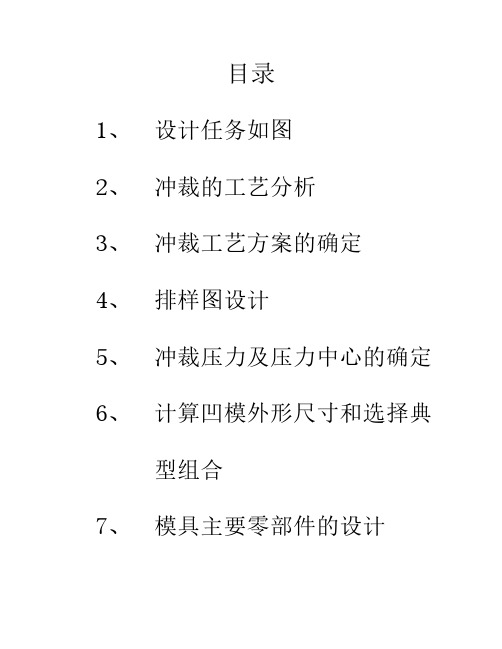
工序号 1 2
3 3 4
5 6
工序名称 备料 钳工
铣 磨 线切割
热处理 检验
工序内容
设备
铣削各面142*82*13
铣床
1、 画螺纹孔、销钉孔、型孔的中 铣床 心线和打线切割孔中心线
2、 钻螺纹孔并攻丝、钻销钉孔并 绞孔、钻线切割孔
铣固定凸模的沉孔
铣床
140*80*12 保证高的两面的粗糙度 磨床
(2)查《冷冲模国家标准》
选取如下尺寸(本因尽量避
免括号内的尺寸,但因其规
格的组合与计算结果相差太
大故勉强取之)
零件名称
尺寸
数量
垫板(上) 140*80*6 1
固定板(上) 140*80*14 1
凹模 140*80*16 1
卸料板 140*80*12 1
中间板 140*80*10 1
固定板(下) 140*80*16 1
凹模板
工艺过程卡
材料名称及 牌号
T10A
产品名称 落寸
工序号 1 2
150×100×20
凹模板
工序名称
工序内容
备料
铣削、保证毛坯142*82*18
钳工
(1)、划型孔、螺钉、销钉中心 线,
(2)、钻螺纹底孔并攻丝; 钻、绞型孔;钻线切割中心孔
3
铣
保证尺寸140.5*80.5*16.5
目录
1、 设计任务如图 2、 冲裁的工艺分析 3、 冲裁工艺方案的确定 4、 排样图设计 5、 冲裁压力及压力中心的确定 6、 计算凹模外形尺寸和选择典
型组合 7、 模具主要零部件的设计
8、 凹凸模刃口尺寸计算 9、 编制工艺规程 10、 装配图、零件图 11、 致谢 12、 附录参考资料
模具设计入门实例

模具设计入门实例本实例内容完全,讲解清晰清晰明了,使读者能快速地操纵冲压模具设计的各类全然操作和技能。
图示零件材料是Q235钢,大年夜批量临盆,厚度2mm。
试设计冲压模具,编制工艺规程。
1. 冲压件工艺分析2. 工艺筹划及模具构造类型3. 排样设计4.冲压力与压力中间运算5.工作零件刃口尺寸运算落料部分以落料凹模为基准运算 ,落料凸模按间隙值配制;冲孔部分以冲孔凸模为基准运算,冲孔凹模按间隙值配制。
既以落料凹模、冲孔凸模为基准,凸凹模按间隙值配制。
刃口尺寸运算见表1。
表 1 刃口尺寸运算6.工作零件构造尺寸7.其它模具零件构造尺寸依照倒装复合模情势特点: 凹模板尺寸并查标准JB/T-6743.1-94,确信其它模具模板尺寸列于表2:依照模具零件构造尺寸 ,查标准GB/T2855.5-90拔取后侧导柱125×25标准模架一副。
8.冲床选用依照总冲压力 F总=352KN,模具闭合高度,冲床工作台面尺寸等,并结合现有设备,选用J23-63开式双柱可倾冲床,并在工作台面上备制垫块。
其重要工艺参数如下:公称压力: 630KN滑块行程: 130mm行程次数: 50 次∕分最大年夜闭合高度: 360mm连杆调剂长度: 80mm工作台尺寸(前后×阁下):480mm × 710mm9.冲压工艺规程10.模具总装配图图 4 模具装配图11.模具零件图图 5 凸凹模图 6 冲孔凸模图 7 落料凹模板图 8 上模座板图 9 下模座板图 10 上垫板图 11 下垫板图 12 凸模固定板图 13 空心垫板图 14 推件块图 15 卸料板图 16 凸凹模固定板1. 重要模具零件加工工艺过程落料凹模加工工艺过程材料 :Gr12 硬度 : 60 ~ 64 HRC冲孔凸模加工工艺过程材料: T10A 硬度: 56 ~ 60HRC凸凹模加工工艺过程材料 :Gr12 硬度 : 60 ~ 64 HRC凸模固定板加工工艺过程材料 :45# 硬度 : 24 ~ 28 HRC凸凹模固定板加工工艺过程材料 :45# 硬度 : 24 ~ 28 HRC卸料板加工工艺过程材料 :45# 硬度 : 24 ~ 28 HRC上垫板加工工艺过程材料 :T8A 硬度 : 54 ~ 58 HRC下垫板加工工艺过程材料 :T8A 硬度 : 54 ~ 58 HRC空心垫板加工工艺过程材料 :45# 硬度 : 24 ~ 28 HRC上模座加工工艺过程材料 :HT200下模座加工工艺过程材料: HT200推件块加工工艺过程材料 :45# 硬度 : 24 — 28 HRC。
冲压模具设计和制造实例
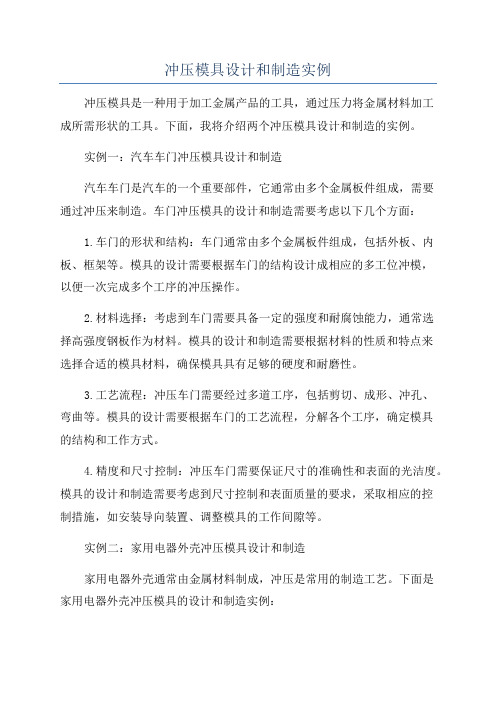
冲压模具设计和制造实例冲压模具是一种用于加工金属产品的工具,通过压力将金属材料加工成所需形状的工具。
下面,我将介绍两个冲压模具设计和制造的实例。
实例一:汽车车门冲压模具设计和制造汽车车门是汽车的一个重要部件,它通常由多个金属板件组成,需要通过冲压来制造。
车门冲压模具的设计和制造需要考虑以下几个方面:1.车门的形状和结构:车门通常由多个金属板件组成,包括外板、内板、框架等。
模具的设计需要根据车门的结构设计成相应的多工位冲模,以便一次完成多个工序的冲压操作。
2.材料选择:考虑到车门需要具备一定的强度和耐腐蚀能力,通常选择高强度钢板作为材料。
模具的设计和制造需要根据材料的性质和特点来选择合适的模具材料,确保模具具有足够的硬度和耐磨性。
3.工艺流程:冲压车门需要经过多道工序,包括剪切、成形、冲孔、弯曲等。
模具的设计需要根据车门的工艺流程,分解各个工序,确定模具的结构和工作方式。
4.精度和尺寸控制:冲压车门需要保证尺寸的准确性和表面的光洁度。
模具的设计和制造需要考虑到尺寸控制和表面质量的要求,采取相应的控制措施,如安装导向装置、调整模具的工作间隙等。
实例二:家用电器外壳冲压模具设计和制造家用电器外壳通常由金属材料制成,冲压是常用的制造工艺。
下面是家用电器外壳冲压模具的设计和制造实例:1.外壳结构和形状:家用电器外壳通常具有盒状结构,需要通过冲压来成形。
模具的设计需要根据外壳的尺寸和形状,设计成相应的单工位或多工位冲模。
2.材料选择:外壳通常采用不锈钢或者冷轧钢板作为材料,以保证外壳的强度和耐腐蚀能力。
模具的设计和制造需要选用适当的模具材料,以确保模具具有足够的硬度和耐磨性。
3.工艺流程:外壳冲压通常包括剪切、成形、冲孔、折弯等工序。
模具的设计需要分解各个工序,确定模具的结构和工作方式,以便一次完成所有工序。
4.精度和表面质量:外壳冲压需要保证尺寸的准确性和表面的光洁度。
模具的设计和制造需要考虑到尺寸控制和表面质量的要求,采取相应的控制措施,如安装导向装置、选用合适的冲头等。
冲压模具结构设计200例
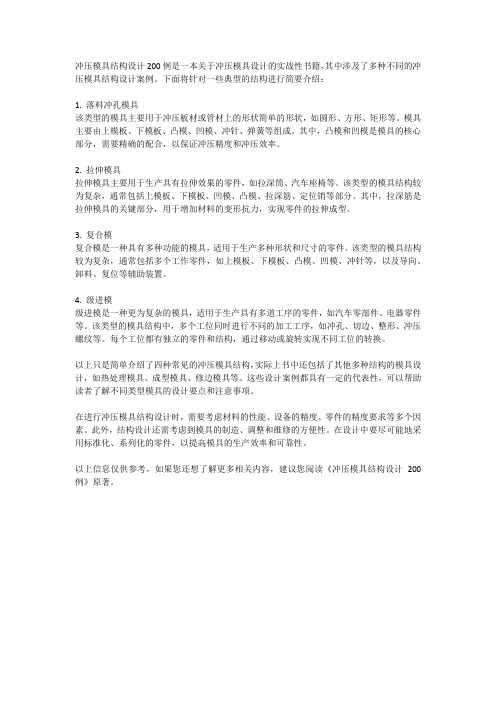
冲压模具结构设计200例是一本关于冲压模具设计的实战性书籍,其中涉及了多种不同的冲压模具结构设计案例。
下面将针对一些典型的结构进行简要介绍:1. 落料冲孔模具该类型的模具主要用于冲压板材或管材上的形状简单的形状,如圆形、方形、矩形等。
模具主要由上模板、下模板、凸模、凹模、冲针、弹簧等组成。
其中,凸模和凹模是模具的核心部分,需要精确的配合,以保证冲压精度和冲压效率。
2. 拉伸模具拉伸模具主要用于生产具有拉伸效果的零件,如拉深筒、汽车座椅等。
该类型的模具结构较为复杂,通常包括上模板、下模板、凹模、凸模、拉深筋、定位销等部分。
其中,拉深筋是拉伸模具的关键部分,用于增加材料的变形抗力,实现零件的拉伸成型。
3. 复合模复合模是一种具有多种功能的模具,适用于生产多种形状和尺寸的零件。
该类型的模具结构较为复杂,通常包括多个工作零件,如上模板、下模板、凸模、凹模、冲针等,以及导向、卸料、复位等辅助装置。
4. 级进模级进模是一种更为复杂的模具,适用于生产具有多道工序的零件,如汽车零部件、电器零件等。
该类型的模具结构中,多个工位同时进行不同的加工工序,如冲孔、切边、整形、冲压螺纹等。
每个工位都有独立的零件和结构,通过移动或旋转实现不同工位的转换。
以上只是简单介绍了四种常见的冲压模具结构,实际上书中还包括了其他多种结构的模具设计,如热处理模具、成型模具、修边模具等。
这些设计案例都具有一定的代表性,可以帮助读者了解不同类型模具的设计要点和注意事项。
在进行冲压模具结构设计时,需要考虑材料的性能、设备的精度、零件的精度要求等多个因素。
此外,结构设计还需考虑到模具的制造、调整和维修的方便性。
在设计中要尽可能地采用标准化、系列化的零件,以提高模具的生产效率和可靠性。
以上信息仅供参考,如果您还想了解更多相关内容,建议您阅读《冲压模具结构设计200例》原著。
26套经典模具结构案例分享

26套经典模具结构案例分享
1、前模行位模
2、热流道设计(DME标准)-1
3、热流道设计(DME标准)-2
4、前模行位模-开模步骤1
5、前模行位模-开模步骤2
6、后模行位模
7、热唧咀模-热流道
8、热唧咀模-冷流道
9、行位运水设计
10、热唧咀模-清除冷流道
11、前模内行位设计1
12、前模内行位设计2
13、热唧咀模-闭锁式唧咀
14、斜顶设计1
15、斜顶设计2
16、斜顶设计3
17、热唧咀模-无流道
18、闭锁式热流道设计
19、螺杆模
20、螺杆模设计1
21、螺杆模设计2
22、螺杆模设计3
23、螺杆模
24、合金模-后模行位
25、锌合金模设计
26、铝合金模设计
附录A 常用注射成型塑料名称及成型特性
附录B常用钢材
附录C各种螺丝牙度及所用之赞咀附录D常用模具零件名称。
注塑模具结构及设计-8(斜顶强脱)
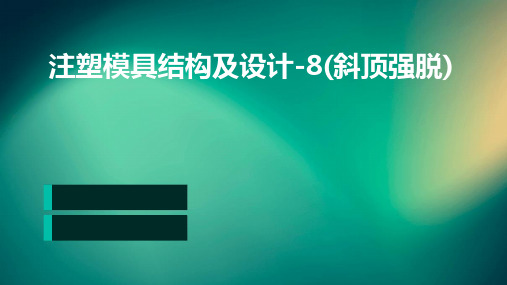
02 注塑模具的基本结构
主流道设计
01
主流道是模具中直接与注塑机喷 嘴接触的部分,通常设计为圆锥 形,便于塑料流动。
02
主流道应与喷嘴紧密配合,防止 溢料,同时要求耐磨、耐高温。
分流道设计
分流道是连接主流道与模具型腔的通 道,用于将塑料均匀分配到各个型腔 。
分流道截面形状有圆形、梯形、U形 等,长度和截面尺寸根据塑料性质和 模具大小而定。
详细描述
斜顶行程的计算需要精确,因为行程过大会导致塑料件顶出时位置不稳定,行程过小则可能导致斜顶无法完全顶 出塑料件。计算斜顶行程时,需要考虑塑料件的高度、模具的开模距离以及斜顶的角度和长度等因素。
斜顶的润滑与排气
总结词
斜顶的润滑和排气是提高模具使用寿命 和确保塑料件质量的重要措施。
VS
详细描述
为了减小摩擦和磨损,提高斜顶的滑动顺 畅度,需要定期对斜顶进行润滑。同时, 为了防止气体在模具腔内积聚,影响塑料 件的成型质量,需要合理设计排气结构, 确保气体能够顺利排出模具。
05 斜顶强脱结构的实例分析
实例一:手机外壳模具设计
总结词
复杂度高、尺寸精度要求高
详细描述
手机外壳模具设计通常采用斜顶强脱结构,因为手机外壳的形状复杂,需要高精度的尺 寸和形状。斜顶强脱结构能够满足高复杂度和高精度要求,确保生产出的手机外壳符合
设计要求。
实例二:汽车零件模具设计
总结词
大型、结构复杂
斜顶强脱结构通过斜向顶出元件的顶 出力,在塑件与型腔表面之间形成分 力,以强制分离塑件。斜顶的倾斜角 度通常为30°~45°,
斜顶强脱结构适用于形状复杂、不易 自动脱落的塑件,尤其在中小型精密 塑件的生产中应用广泛。
冲压模具设计和制造实例

冲压模具设计与制造实例例:图1所示冲裁件,材料为A3,厚度为2mm,大批量生产.试制定工件冲压工艺规程、设计其模具、编制模具零件的加工工艺规程. 零件名称:止动件 生产批量:大批 材料:A3 材料厚度:t=2mm一、 冲压工艺与模具设计1.冲压件工艺分析①材料:该冲裁件的材料A3钢是普通碳素钢,具有较好的可冲压性能. ②零件结构:该冲裁件结构简单,并在转角有四处R2圆角,比较适合冲裁. ③尺寸精度:零件图上所有未注公差的尺寸,属自由尺寸,可按IT14级确定工件尺寸的公差.孔边距12mm 的公差为,属11级精度.查公差表可得各尺寸公差为:零件外形:65 mm 24 mm 30 mm R30 mm R2 mm零件内形:10 mm孔心距:37±0.31mm 结论:适合冲裁. 2.工艺方案及模具结构类型该零件包括落料、冲孔两个工序,可以采用以下三种工艺方案:+①先落料,再冲孔,采用单工序模生产.②落料-冲孔复合冲压,采用复合模生产.③冲孔-落料连续冲压,采用级进模生产.方案①模具结构简单,但需要两道工序、两套模具才能完成零件的加工,生产效率较低,难以满足零件大批量生产的需求.由于零件结构简单,为提高生产效率,主要应采用复合冲裁或级进冲裁方式.由于孔边距尺寸12 mm有公差要求,为了更好地保证此尺寸精度,最后确定用复合冲裁方式进行生产.工件尺寸可知,凸凹模壁厚大于最小壁厚,为便于操作,所以复合模结构采用倒装复合模及弹性卸料和定位钉定位方式.3.排样设计查冲压模具设计与制造表 2.5.2,确定搭边值:两工件间的搭边:a=2.2mm工件边缘搭边:a1=2.5mm步距为:32.2mm条料宽度B=D+2a1=65+2=70确定后排样图如2所示一个步距内的材料利用率η为:η=A/BS×100%=1550÷70××100%=%查板材标准,宜选900mm×1000mm的钢板,每张钢板可剪裁为14张条料70mm×1000mm,每张条料可冲378个工件,则η为:η=nA1/LB×100%=378×1550/900×1000×100%=%即每张板材的材料利用率为%4.冲压力与压力中心计算⑴冲压力落料力 F总=τ=××2×450=KN其中τ按非退火A3钢板计算.冲孔力 F冲=τ=×2π×10×2×450=KN其中:d 为冲孔直径,2πd为两个圆周长之和.卸料力 F卸=K卸F卸=×=KN推件力 F推=nK推F推=6××=KN其中 n=6 是因有两个孔.总冲压力:F总= F落+ F冲+ F卸+ F推=+++=KN⑵压力中心如图3所示:由于工件X方向对称,故压力中心x0=32.5mm=13.0mm其中:L1=24mm y1=12mmL2=60mm y2=0mmL3=24mm y1=12mmL4=60mm y4=24mmL5=60mm y5=27.96mmL6=60mm y6=24mmL7=60mm y7=12mmL8=60mm y8=12mm计算时,忽略边缘4-R2圆角.由以上计算可知冲压件压力中心的坐标为,135.工作零件刃口尺寸计算落料部分以落料凹模为基准计算,落料凸模按间隙值配制;冲孔部分以冲孔凸模为基准计算,冲孔凹模按间隙值配制.即以落料凹模、冲孔凸模为基准,凸凹模按间隙值配制.刃口尺寸计算见表16.工作零件结构尺寸落料凹模板尺寸:凹模厚度:H=kb≥15mmH=×凹模边壁厚:c≥~2H=~2×=~mm 实取c=30mm凹模板边长:L=b+2c=65+2×30=125mm查标准JB/T :凹模板宽B=125mm故确定凹模板外形为:125×125×18mm.将凹模板作成薄型形式并加空心垫板后实取为:125×125×14mm.凸凹模尺寸:凸凹模长度:L=h1+h2+h=16+10+24=50mm其中:h1-凸凹模固定板厚度h2-弹性卸料板厚度h-增加长度包括凸模进入凹模深度,弹性元件安装高度等凸凹模内外刃口间壁厚校核:根据冲裁件结构凸凹模内外刃口最小壁厚为7mm,根据强度要求查冲压模具设计与制造表2.9.6知,该壁厚为4.9mm即可,故该凸凹模侧壁强度足够.冲孔凸模尺寸:凸模长度:L凸= h1+h2+h3=14+12+1440mm其中:h1-凸模固定板厚 h2-空心垫板厚 h3-凹模板厚凸模强度校核:该凸模不属于细长杆,强度足够.7.其它模具零件结构尺寸根据倒装复合模形式特点:凹模板尺寸并查标准JB/,确定其它模具模板尺寸列于表2:根据模具零件结构尺寸,查标准GB/选取后侧导柱125×25标准模架一副.8.冲床选用根据总冲压力 F总=352KN,模具闭合高度,冲床工作台面尺寸等,并结合现有设备,选用J23-63开式双柱可倾冲床,并在工作台面上备制垫块.其主要工艺参数如下:公称压力:63KN滑块行程:130mm行程次数:50次/分最大闭合高度:360mm连杆调节长度:80mm工作台尺寸前后×左右:480mm×710mm二、模具制造1、主要模具零件加工工艺过程制件:柴油机飞轮锁片材料:Q235料厚:1.2mm该制件为大批量生产,制品图如下:一冲裁件的工艺分析1、冲裁件为Q235号钢,是普通碳素钢,有较好的冲压性能,由设计书查得τ=350Mpa.2、该工作外形简单,规则,适合冲压加工.3、所有未标注公差尺寸,都按IT14级制造.4、结论:工艺性较好,可以冲裁.方案选择:方案一:采用单工序模.方案二:采用级进模.方案三:采用复合模.单工序模的分析单工序模又称简单模,是压力机在一次行程内只完成一个工序的冲裁模.工件属大批量生产,为提高生产效率,不宜采用单工序模,而且单工序模定位精度不是很高,所以采用级进模或复合模.级进模的分析级进模是在压力机一次行程中,在一副模具上依次在几个不同的位置同时完成多道工序的冲模.因为冲裁是依次在几个不同的位置逐步冲出的,因此要控制冲裁件的孔与外形的相对位置精度就必须严格控制送料步距,为此,级进模有两种基本结构类型:用导正销定距的级进模和用侧刃定距的级进模.另外级进模有多个工序所以比复合模效率低.复合模的分析复合模是在压力机一次工作行程中,在模具同一位置同时完成多道工序的冲模.它不存在冲压时的定位误差.特点:结构紧凑,生产率高,精度高,孔与外形的位置精度容易保证,用于生产批量大.复合模还分为倒装和正装两种,各有优缺点.倒装复合模但采用直刃壁凹模洞口凸凹模内有积存废料账力较大,正装复合模的优点是:就软就薄的冲裁件,冲出的工件比较平整,平直度高,凸凹模内不积存废料减小孔内废料的胀力,有利于凸凹模减小最小壁厚.经比较分析,该制件的模具制造选用导料销加固定挡料销定位的弹性卸料及上出件的正装复合模.二排样图设计及冲压力和压力中心的计算由3-6,3-8表可查得:a1=,a=,△=查书391.料宽计算: B=D+2a=62+2=64mm2.步距:A=D=a1=62+=62.8mm3.材料利用率计算:η=A/BS×100%=πR2-πR2+12/64=312-+/64×100%=%其中a是搭边值,a1是工作间隙,D是平行于送料方向冲材件的宽度,S是一个步距内制件的实际面积,A是步距,B是料宽,R1是大圆半径,R2是小圆半径,12×是方孔的面积,η为一个步距内的材料的利用率4.冲裁总压力的确定:L=231+2+12+2=周边总长计算冲裁力:F=KLtτ查设计指导书得τ=350MpaF=350≈180KN落料力:F落=τ=231350=卸料力:F卸=kF落==冲孔力:F冲=τ+12+2350=顶件力:F顶=-k2F落==冲裁总压力:F∑=F落+F卸+F冲+F顶=+++=F压=~F∑=246KN说明:K为安全系数,一般取;k为卸料力系数,其值为~,在上式中取值为;k2为顶件力系数,其值为~,式中取值为5.压力机的初步选用:根据制件的冲裁的公称压力,选用开式双柱可倾式压力机,公称压力为350k N 形号为J23-35 满足:F压≥F∑。
模具设计实例解析(doc 19页)
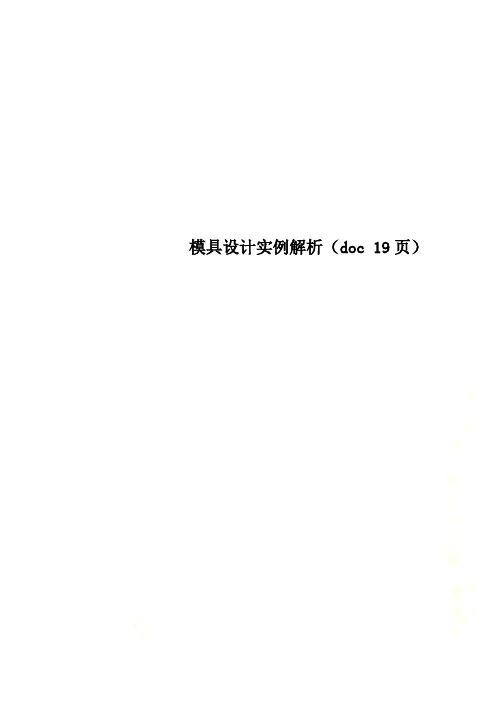
模具设计实例解析(doc 19页)模具设计实例1——相机外壳模具设计本单元讲解的实例为按摩器上盖模具设计,按相机外壳模型如图1所示。
图1 相机外壳模型1具体设计步骤1.1启动PRO/E4.0,建立模具文件(1)启动PRO/E。
选择下拉菜单“文件”,“设置工作目录”命令,选择一个合适的工作目录。
(2)选择下拉菜单中“文件”,“新建”命令,弹出1-1所示的“新建”对话框,在“类型”选项组中选择“制造”选项,在“子类型”选项组中选择“模具型腔”选项,在“名称”文本框中输入文件名“anmo”,取消“使用缺省模板”,单击“确定”按钮,弹出”新文件选项“对话框。
箭头,出现浮动参照模型窗口,同时出现“坐标系类型”菜单管理器,如图1-4所示图1-4浮动参照模型窗口和“坐标系类型”菜单(7)在“坐标系类型”菜单中选择“动态”命令,进入“参照模型方向”对话框如图1-5所示,选择“坐标系移动/定向”按钮,选择“轴”输入数值90。
单击“确定”按钮,返回“布局”对话框,单击“确定”完成参照模型的加载,如图1-6所示。
图1-5 参照模型方向菜单图1-6 参照零件布局结果1.2设置收缩率(1)单击“模具制造”工具栏上的“按比例收缩”按钮,弹出“选取”对话框,按照提示单击任何一个参照模型,选中的模型变成红色。
(2)在弹出的“按比例收缩”对话框中选择“1+S”收缩率公式,选中参照模型中的坐标系PRT_CSYS_DEF,在“收缩率”文本框中输入0.005,如图1-7所示。
(3)单击“按比例收缩”对话框中的“确定”按钮,即可完成全部零件的收缩率设置。
图1-7 设置按比例收缩参数1.3创建工件创建工件步骤如下:(1)选择“模具”菜单管理器中的“模具模型”,“创建”,“工件”,“自动”命令,将弹出“自动工件”对话框,选择MOLD_DEF_CSYS坐标系作为模具原点,从“形状”下拉列表中选择工件的形状为“标准矩形”,单位为mm,并接受默认的工件名称,图形区中将显示包容零件的工件,如图1-8所示。
模具设计案例分析-纯干货
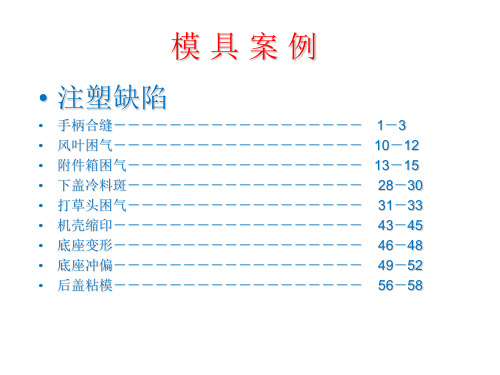
结果: 问题解决。
注塑缺陷
零件代号 零件名称 产品尺寸 出数 注塑机
GT01FM.30.01 打草头 Φ81*43 1*2 128T
产品介绍: 本产品为风叶,筋板多,而且薄.
问题点: 注塑过程中筋板打不饱。
注塑缺陷
改善前 1,改善前,试模后观察产品哪些筋板注 塑过程中出现不饱的,在其位置加排气镶 针.
性较差。风扇各扇叶较深,且有较高的动平衡 要求。
问题点:
由于PA+GF30%流动性较差,且扇叶较 深,在成型时需要较高的注射压力才能将其 注满,但扇叶的最末端会出现困气现象,中 间装电机轴的位置在模具上强度如果不够也 会产生变形,导致无法满足同心度要求。
注塑缺陷
改善前
1,简化三板模,细水口。 2,产品筋板较多,需要较大注塑压力,模具 中间的镶针在高压的状态下容易变形。 3,筋板较细,容易困气。
注塑缺陷
改善前 由于产品外观要求的局限性,产品结构无法 改变。变形不可避免。
改善后 在产品内部增加横向筋板并增加空心柱与下 盖过盈配合。
注塑缺陷
分析: 上下手柄由于外观设计的限制,上下手柄横向与纵向比例相差较大,两边有
较大弧度,筋板的支撑无法控制产品的变形。上手柄没有横向筋板,产品不可避 免地会向中间收缩。而下手柄有足够的横向筋支撑,模向的变形相对较小,所以 上下手柄合起来时会产生合缝。
注塑缺陷
零件代号 零件名称 产品尺寸 出数 注塑机
VK01SR.10.05 VK01SR.10.04
上手柄
下手柄
200*50*61
188*49*57
1*2
1*2
150T
150T
产品介绍: 上下手柄采用止口配合,材料为PP。
ug模具设计教程实例
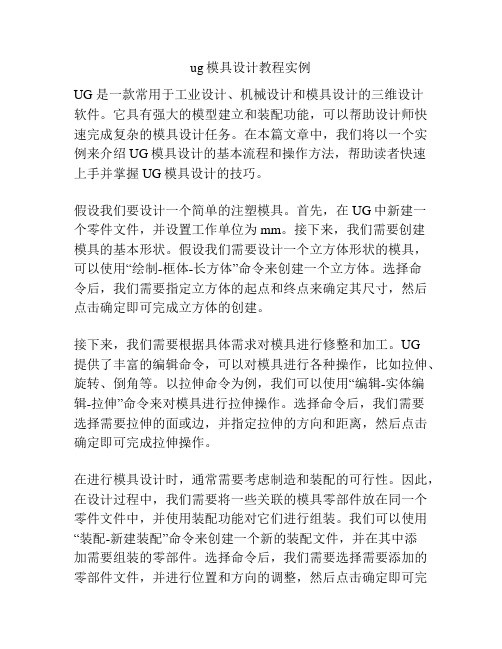
ug模具设计教程实例UG 是一款常用于工业设计、机械设计和模具设计的三维设计软件。
它具有强大的模型建立和装配功能,可以帮助设计师快速完成复杂的模具设计任务。
在本篇文章中,我们将以一个实例来介绍UG模具设计的基本流程和操作方法,帮助读者快速上手并掌握UG模具设计的技巧。
假设我们要设计一个简单的注塑模具。
首先,在UG中新建一个零件文件,并设置工作单位为mm。
接下来,我们需要创建模具的基本形状。
假设我们需要设计一个立方体形状的模具,可以使用“绘制-框体-长方体”命令来创建一个立方体。
选择命令后,我们需要指定立方体的起点和终点来确定其尺寸,然后点击确定即可完成立方体的创建。
接下来,我们需要根据具体需求对模具进行修整和加工。
UG提供了丰富的编辑命令,可以对模具进行各种操作,比如拉伸、旋转、倒角等。
以拉伸命令为例,我们可以使用“编辑-实体编辑-拉伸”命令来对模具进行拉伸操作。
选择命令后,我们需要选择需要拉伸的面或边,并指定拉伸的方向和距离,然后点击确定即可完成拉伸操作。
在进行模具设计时,通常需要考虑制造和装配的可行性。
因此,在设计过程中,我们需要将一些关联的模具零部件放在同一个零件文件中,并使用装配功能对它们进行组装。
我们可以使用“装配-新建装配”命令来创建一个新的装配文件,并在其中添加需要组装的零部件。
选择命令后,我们需要选择需要添加的零部件文件,并进行位置和方向的调整,然后点击确定即可完成零部件的组装。
完成模具的基本设计后,我们可以开始进行更详细的设计和优化。
UG 提供了丰富的分析和仿真功能,可以对模具进行各种性能和强度的分析。
我们可以使用“分析-应力分析”命令来对模具的强度进行分析。
选择命令后,我们需要指定需要分析的零部件,设置加载和边界条件,然后点击确定即可进行应力分析。
根据分析结果,我们可以对模具进行调整和优化,以满足设计要求。
在完成模具设计后,我们可以使用UG 提供的绘图功能生成模具图纸。
UG 自带了一套丰富的绘图工具和符号库,可以帮助设计师快速制作高质量的模具图纸。
冲压模具设计与制造实例
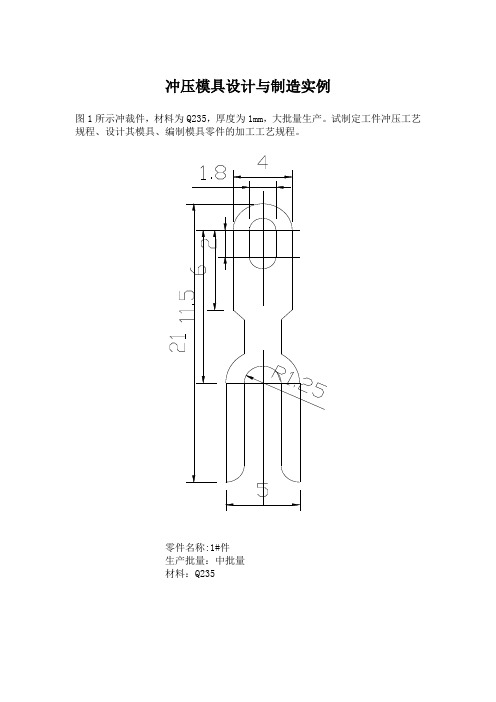
冲压模具设计与制造实例图1所示冲裁件,材料为Q235,厚度为1mm,大批量生产。
试制定工件冲压工艺规程、设计其模具、编制模具零件的加工工艺规程。
零件名称:1#件生产批量:中批量材料:Q2351. 冲压件工艺分析2. 工艺方案及模具结构类型3. 排样设计4.冲压力与压力中心运算工件如图找到坐标运算得24*12+60*0+24*12+14.5*24+38.6*27.97+14.5*24+31.4*12+31.4*12Y= ——————————————————————————————=2.5 24+60+24+14.5+38.5+14.5+34.1+31.4X=8.35.工作零件刃口尺寸运算落料部分以落料凹模为基准运算 ,落料凸模按间隙值配制;冲孔部分以冲孔凸模为基准运算,冲孔凹模按间隙值配制。
既以落料凹模、冲孔凸模为基准,凸凹模按间隙值配制。
刃口尺寸运算见表1。
表 1 刃口尺寸运算6.工作零件结构尺寸7.其它模具零件结构尺寸依照倒装复合模形式特点: 凹模板尺寸并查标准JB/T-6743.1-94,确定其它模具模板尺寸列于表2:依照模具零件结构尺寸 ,查标准GB/T2855.5-90选取后侧导柱125×25标准模架一副。
8.冲床选用依照总冲压力 F总=352KN,模具闭合高度,冲床工作台面尺寸等,并结合现有设备,选用J23-63开式双柱可倾冲床,并在工作台面上备制垫块。
其要紧工艺参数如下:公称压力:1630KN滑块行程: 120mm行程次数: 60 次∕分最大闭合高度: 140mm连杆调剂长度: 50mm工作台尺寸(前后×左右): 63*639.冲压工艺规程切料63*25的板料排样图设计10.模具总装配图图 4 模具装配图11.模具零件图上模座下模座凹模凸模垫板下模座板卸料板卸料螺钉挡料销螺钉导套凹模垫板1. 要紧模具零件加工工艺过程落料凹模加工工艺过程材料 :Gr12 硬度 : 60 ~ 64 HRC冲孔凸模加工工艺过程材料: T10A 硬度: 56 ~ 60HRC凸凹模加工工艺过程材料 :Gr12 硬度 : 60 ~ 64 HRC凸模固定板加工工艺过程材料 :45# 硬度 : 24 ~ 28 HRC凸凹模固定板加工工艺过程材料 :45# 硬度 : 24 ~ 28 HRC卸料板加工工艺过程材料 :45# 硬度 : 24 ~ 28 HRC上垫板加工工艺过程材料 :T8A 硬度 : 54 ~ 58 HRC下垫板加工工艺过程材料 :T8A 硬度 : 54 ~ 58 HRC空心垫板加工工艺过程材料 :45# 硬度 : 24 ~ 28 HRC上模座加工工艺过程材料 :HT200下模座加工工艺过程材料: HT200推件块加工工艺过程材料 :45# 硬度 : 24 — 28 HRC2. 加工过程:详见素材资源库中的视频。
- 1、下载文档前请自行甄别文档内容的完整性,平台不提供额外的编辑、内容补充、找答案等附加服务。
- 2、"仅部分预览"的文档,不可在线预览部分如存在完整性等问题,可反馈申请退款(可完整预览的文档不适用该条件!)。
- 3、如文档侵犯您的权益,请联系客服反馈,我们会尽快为您处理(人工客服工作时间:9:00-18:30)。
山西农业大学工学院
(1)排样分析
由排样图的几何关系,可以近似算出两排中心距为41mm。
= A1 A2 A3 100%
42.4 41 420.54 527.52 279.70 = 100% 42.4 41 =70.6%
其中 A1=∏(r12-r22)=420.54mm2,r1=20mm,r2=17mm,零件一的表面积; A2=∏(r22-R32)=527.52mm2,r3=11mm,零件二的表面积; A3=∏(r32-R42)=279.70mm2,r4=5.65mm,零件三的表面积。
山西农业大学工学院
因为本模具采用的是弹性卸料装置 和下出料方式,所以总冲压力F为 F=FK+FL+FX+FT =43106+82293+3703+7113 =136215(N) =136.215(kN)
山西农业大学工学院
(2)压力中心的计算与确定
模具压力中心为冲裁力合力的作用点或多工序模各工序冲压 力的合力作用点。设计时,模具压力中心应与压力机滑块中心一 致,否则会在冲压时产生偏裁,导致模具以及压力机滑块与导轨 的急剧磨损,降低模具和压力机的使用寿命。 依据形状对称件的压力中心即位于零件图形的几何中心。由 零件图可以看出,零件是形状对称件,故压力中心:x=10.5mm; y=10.5mm 即压力中心坐标为:(10.5,10.5)
材料名称 45、T7、T8 (退火)、65 钢 Zmax 0.06 0.10
冲裁模初始双面间隙(mm)
10、15、20、冷轧钢带、 Q215、Q235钢板 30钢板 Zmin 0.03 0.06 Zmax 0.05 0.08 Zmin 0.02 0.04 Zmax 0.04 0.06
厚度t(mm) Zmin 0.3 0.5 0.04 0.08
山西农业大学工学院
解:⑴ 查《模具结构设计》表1-6,确定搭边值: 两工件间的搭边:a=1mm; 工件边缘搭边: a1=1mm 步距为: H=11mm; 条料宽度为: B=(L+2a1)=10+2*1=12mm; 确定后排样图如下图所示: 一个步距内的材料利用率为; η=(5×5)×3.14÷11÷12= 59.5%
dp=(d+xΔ)=(5.3+0.75×0.03)=5.32
mm
0.020 0
dd=(d+xΔ+Zmin)=(5.3+0.75×0.03+0.03)=5.35
mm
山西农业大学工学院
• 任务要求 • ⑴ 材料:Q235; ⑵ 生产批量:大批生产; ⑶ 材料厚度:0.5mm; 针对该零件,请做如下分析: (1)排样分析:排样方式及 排样图、材料利用率的计算 (2)确定工艺方案 (3)冲裁力的计算 (4)压力机公称压力的确定 (5)模具工作部分尺寸计算 (1) (2) (3) 一模多件零件图和三维模型
=
1 3.14 10 .5 10 .5 25 22 .5
100%
=61.5% 式中 A---冲裁件面积(包括冲出的小孔在内) n---一个进距内冲件数目 b---条料宽度 h---进距
山西农业大学工学院
选择900mm×1000mm的钢板。 900 36 ,即可裁剪36张条料;
结论:该零件适合冲裁。
山西农业大学工学院
工艺方案及模具结构类型
冲裁该垫圈包括落料,冲孔两个基本工序,可以采用 以下三种方案: (1)先落料,再冲孔,采用单工序模生产。 (2)落料—冲孔复合冲压,采用复合模生产。 (3)冲孔—落料连续冲压,采用级进模生产。
由于零件结构简单,为了提高生产效率,主要应采用 复合冲裁或级进冲裁方式。为了更好地保证此尺寸的精度, 最后确定用复合冲裁方式进行生产。 依据零件的尺寸要求,为便于操作,所以复合模结构 采用倒装复合模。
(参见P87)
山西农业大学工学院
工作零件刃口尺寸计算
尺寸计算原则 在冲裁过程中,冲孔件尺寸决定于凸模刃口尺寸, 落料件尺寸决定于凹模尺寸。因此,确定冲裁模刃口尺 寸时应遵循以下原则:①落料模先确定凹模刃口尺寸, 其公称尺寸应取接近或等于制件的最小极限尺寸,凸模 刃口公称尺寸比凹模小一个最小合理间隙;②冲孔模先 确定凸模刃口尺寸,其公称尺寸应取接近或等于制件的 最大极限尺寸,凹模刃口公称尺寸比凸模大一个最小合 理间隙;③在选择模具刃口制造公差时,要考虑制件精 度与模具精度的关系,既要保证制件的精度要求,又要 保证有合理的间隙值,一般冲模精度较制件精度高2~3 级。
山西农业大学工学院
压力机的选用
压力机选用的根据,主要是冲压工艺的性质、生 产批量的大小、模具的外形尺寸以及工厂现有设备等 情况。 压力机的冲压力要留有充分的余地,使完成冲裁 过程各种力之和最好在压力机额定能力的70%~80%以 内,并保证操作方便、安全。模具的闭合高度和压力 机的闭合高度要相适应,压力中心原则上应与压力机 中心一致。 136.215/(70%~80%)=170.3~194.6(kN) 根据以上计算数据,查《冲压模具简明设计手册》 初步选择压力机为开式固定台压力机,型号为JH21-25, 标称压力为250kN。
山西农业大学工学院
1、25—推杆 2—模柄 3、 15—内六角螺钉 4—推板 5—上模座 6、18—垫板 7—凸模固定板 8—落料 凹模 9—推件板 10—导 套 11—卸料板 12—橡 胶 13—导柱 14—卸料螺 钉 16—下模座 17、 26—圆柱销 19—凸凹模 固定板 20—弹簧 21—定位销 22—凸凹模 23—挡料销 24—冲孔凸模
山西农业大学工学院
⑵ 已知Zmin=0.03, Zmax=0.04
落料 Dd=(D-xΔ) Dp=(D-xΔ-Zmin)
由于零件基本尺寸为10 mm,10<18,所以δd=0.020 mm, δp=0.020 mm。x =0.75
Dd=(D-xΔ)=(10-0.75×0.03)=9.98
d 0
0 0.020
=11.215 0 mm 0.020 dd=(d+xΔ+Zmin) 0 0.020 =(11+0.5×0.43+0.26) 0 0.020 =11.475 0 mm
d
山西农业大学工学院
式中 Dd 、Dp---分别为落料凹、凸模刃口公称尺寸 dd 、dp---分别为冲孔凹、凸模刃口公称尺寸 D---落料件公称尺寸 d---冲孔件公称尺寸 Δ---制件制造公差 Zmin---凸、凹模最小合理间隙 x---磨损系数 磨损系数 x查《模具结构设计》表2-6,根据材料 厚度及材料形状查得x=0.5
25
1000 44 .4 22 .5
,即每张条料可冲44个工件。
则一张板料上的材料利用率为:
NA 100 % bL
=
44 3.14 10.5 10.5 100 % 25 1000
=60.9%
式中 N---一张板料上冲件总数目 L---板材长度
山西农业大学工学院
山西农业大学工学院
(2)确定工艺方案
工步一 冲孔落料
工步二 冲孔落料
工步三 冲孔落料
方案一:采用三套单工序模具进行冲裁: 工序 l——先用复合模冲出零件一; 工序2——然后用复合模冲出零件二; 工序3——最后用复合模冲出零件三。 方案二:用一套复合模进行冲压,如图所示。 工步1——先用复合模冲出零件一,工步2——然后复合模冲出零件二; 工步3——最后复合模冲出零件三,压力机一次行程生产三个不同的环形转冲片零件。
山西农业大学工学院
张静
山西农业大学工学院
垫圈冲压模具设计
材料:OCr18Ni9不锈钢 材料厚度:2mm 生产批量:大批量
山西农业大学工学院
垫圈的工艺分析
(1)该垫圈的材料为OCr18Ni9不锈钢,具有良好的冲压 性能。 (2)工件结构:该零件结构简单,是规则的对称图形, 比较适合冲裁。 (3)尺寸精度:根据零件上的尺寸标注,由标准公差 表可确定零件的表面精度为IT14,孔的精度为IT12,形 状精度要求不高。
山西农业大学工学院
排样设计
确定搭边值: 制件间:a=1.5mm 侧 面:a1=2mm 进 距:H=(21+a)=22.5mm 条料宽度:B=(21+2a1)=21+2×2=25mm
山西农业大学工学院
一个进距内的材料利用率η为 η=
nA bh 100%
山西农业大学工学院
落料力:FL=1.3πdLtτ
=1.3×3.14×21×2×480
=82293.12 ≈82293(N)
式中
dL---落料直径
t---材料厚度 τ---材料的抗剪强度
卸料力:FX=KXFL =0.045×82293 =3703.185
≈3703(N) 式中 KX---卸料力系数 KX=0.04~0.05 取KX为0.045 推件力: FT=nKTFK =3×0.055×43106 ≈ 7113(N) 式中 KT---推件力系数(KT=0.055) =7112.49
0.020 0
mm
0 0.020
Dp=(D-xΔ-Zmin)=(10-0.75×0.03-0.03)=9.95 冲孔 dp=(d+xΔ) dd=(d+xΔ+Zmin)