FMEA潜在失效模式分析PPT[1]
合集下载
潜在失效模式分析FMEA第五版教材ppt课件
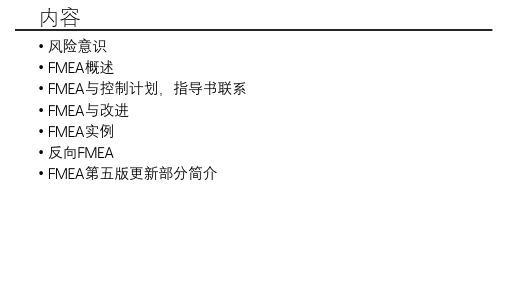
内容
• 风险意识 • FMEA概述 • FMEA与控制计划,指导书联系 • FMEA与改进 • FMEA实例 • 反向FMEA • FMEA第五版更新部分简介
P1/30
做任何事都可能失败,所以你必须提前做好预防! 生活中:做饭糊,起晚,迟到,丢东西,感冒。。。 工作中:算错账,发错货,忙到忘记重要的工作。。。 设备:跳闸,断电,未知原因的停止工作。。。 教育训练:内容不合适,讲解不到位,学员跑神。。。
Baby拿个杯子8--更容易掉
P15/30
FMEA概述
频度(O)
P16/30
FMEA概述
探测度(D)
杯子碎了我听不见也看不见
P17/30
FMEA概述
探测度(D)
P18/30
FMEA概述
风险顺序数(RPN)
综合的考虑三要素 严重度、频度、探测度 RPN=S×O×D
P19/30
FMEA概述
替代
用
系统分析
功能分析
• 定义功能 • 转化要求 • 顾客语言转化未技
术术语
失效分析
• 识别失效及其结构 • 识别变差源(原因) • 定义风险优先级
风险分析
• 预防及探测控制 • SOD打分 • 定义风险优先级
改进措施
• 基于风险优先级确 定该叫你措施
• 风险降低 • 持续改进
失效分析及风险降低
第五版取消RPN风险顺序数,增加了AP
验证所有失效模式之 后,考虑创造和发现 PFMEA中为考虑到的 新的失效模式
是
所有的失
否
效模式都
验证了吗?
P26/30
FMEA内容(第五版)
格式变更(六步法)
范围定义:确认项目
• 风险意识 • FMEA概述 • FMEA与控制计划,指导书联系 • FMEA与改进 • FMEA实例 • 反向FMEA • FMEA第五版更新部分简介
P1/30
做任何事都可能失败,所以你必须提前做好预防! 生活中:做饭糊,起晚,迟到,丢东西,感冒。。。 工作中:算错账,发错货,忙到忘记重要的工作。。。 设备:跳闸,断电,未知原因的停止工作。。。 教育训练:内容不合适,讲解不到位,学员跑神。。。
Baby拿个杯子8--更容易掉
P15/30
FMEA概述
频度(O)
P16/30
FMEA概述
探测度(D)
杯子碎了我听不见也看不见
P17/30
FMEA概述
探测度(D)
P18/30
FMEA概述
风险顺序数(RPN)
综合的考虑三要素 严重度、频度、探测度 RPN=S×O×D
P19/30
FMEA概述
替代
用
系统分析
功能分析
• 定义功能 • 转化要求 • 顾客语言转化未技
术术语
失效分析
• 识别失效及其结构 • 识别变差源(原因) • 定义风险优先级
风险分析
• 预防及探测控制 • SOD打分 • 定义风险优先级
改进措施
• 基于风险优先级确 定该叫你措施
• 风险降低 • 持续改进
失效分析及风险降低
第五版取消RPN风险顺序数,增加了AP
验证所有失效模式之 后,考虑创造和发现 PFMEA中为考虑到的 新的失效模式
是
所有的失
否
效模式都
验证了吗?
P26/30
FMEA内容(第五版)
格式变更(六步法)
范围定义:确认项目
FMEA潜在失效模式及后果分析(PPT 77张)
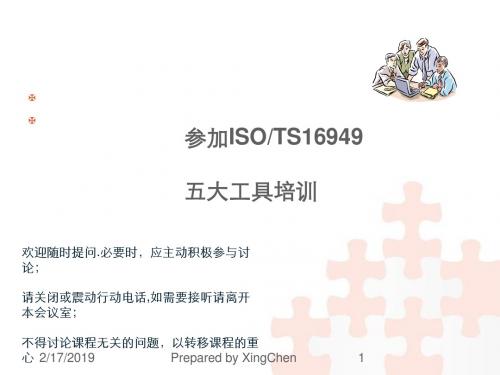
后果是 什么? 功能、特 性或要求 是什么?
有多 糟糕 ? 起因是 什么? 发生的频 率如何?
能做些什么? -设计更改 -过程更改 -特殊控制 -标准、程序或 指南的更改
会是什么问题? -无功能 -部分功能/功能 过强/功能降级 -功能间歇 -非预期功能
2/17/2019
怎样能得到 预防和探测? 该方法在 探测时 有多好?
2/17/2019
Prepared by XingChen
10
2/17/2019
Prepared by XingChen
11
下图描述了进行 FMEA的顺序。这并不是简单地填写一下表
格,而是要理解FMEA的过程,以便消除风险并策划适宜的 控制方法以确保顾客满意。
2/17/2019
Prepared by XingChen
24
8)核心小组 列出有权确定和/或执行任务的责任部门的名称和个人的姓名(建议所 有参加人员的姓名、部门、电话、地址等都应记录在一张分发表上。) 9)项目/功能 填入被分析项目的名称和其他相关信息(如编号、零件级别等)。利 用工程图纸上标明的名称并指明设计水平。在初次发布(如在概念阶 段)前,应使用试验性编号。用尽可能简明的文字来说明被分析项目 满足设计意图的功能,包括该系统运行环境(规定温度、压力、湿度 范围、设计寿命)相关的信息(度量/测量变量)。如果该项目有多种 功能,且有不同的失效模式,应把所有的功能单独列出。
16
DFMEA考虑的内容:
设计 FMEA 针对设计意图并且 假定该设计将按此意图进行生 产/装配。 制造或装配过程中可能发生的 潜在失效模式和 / 或其原因 / 机 理不需、但也可能包括在设计 FMEA当中。 当这些未包含在设计 FMEA 当 中时,它们的识别、后果及控 制应包括在过程FMEA当中。
FMEA-潜在失效模式分析(ppt 175页)
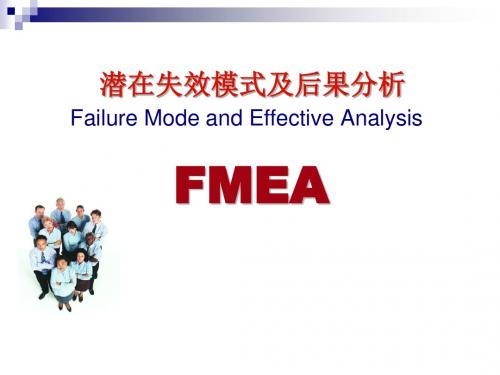
设计FMEA初始阶段的工作
l 在进行设计FMEA开始时,负责设计的工程师应 列出设计希望做什么?不希望做什么?
— 充分理解、明了设计意图 — 顾客要求和需求,其来源如:通过质量功 能展开、车辆要求文件、已知的产品要求和/或制 造、装配、服务、回收利用等要求。 期望特性的定义越明确,就越容易识别潜在的 失效模式,以采取预防防和纠正措施。
评估和分析的部分是关于分析的评估。最重要 的是对有关设计(产品或功能),功能评估和应 用方面的任何更改,以及潜在失效导致的风险进 行讨论。
每一种FMEA都应该确保对在产品或装配中的 每个部件给予关注。与风险和安全相关的部件或 过程应给予更高的优先权。
FMEA程序成功执行的最重要因素之一是及时 性。这意味着它是一种事前行为,而不是一种事 后演习。要取得最大成效,FMEA必须在存在潜 在失效模式的产品或过程执行前进行,适当预先 花时间完成FMEA,产品/过程的更改会在最容易 和最低成本情况下,并且将降低后期更改风险。 FMEA措施将减轻或消除执行更改产生更大关注 点的机会。
*识别和评估风险:
FMEA过程的重要步骤之一是评价风险。风险用三种 方法来评价,严重度、发生率和探测度。
严重度是失效对顾客产生影响的级别一种评估。 发生率是失效的要因可能发生的频繁程度。 探测度是对产品或过程控制探测失效要因会失效模式 程度的一种评价。
*建议措施和结果;
建议措施的意图是降低综合风险和失效模式发生的可 能性,建议措施阐述严重度、发生率和探测度降低。
问题在于: 自觉与不自觉 科学法则与自然法则 注意性与随意性 借鉴型与抛弃型 螺旋提高与闭环解决
FMEA简史
50年代初
60年代中
70年代中
美国Grumman 公司把FMEA思 想用于一种战斗 机操纵系统的设 计分析
培训课件潜在的失效模式及后果分析fmea

FMEA 的特点(2)
协作性:
虽然 FMEA 的编制责任通 常都指派到某个人,但是 FMEA 的输入应该是小组的努力。
小组成员应由知识丰富的 人员组成(如设计、分析/试验 、制造、装配、服务、质量及 可靠性等方面的有丰富经验的 工程师)
7
潜在失效模式及后果分析 FMEA
主观性
FMEA 的特点(3)
31
(22)
过程 FMEA 的開發
5 )車型年/車輛類型
填入將使用和/或正被分析的設計所影響的預期車型年
及車輛類型。 (如果已知的話)
过 程 FMEA
系统
X 子系统 ______部件 01.03/车身密封 (2) 车型年/车辆类型 199X/狮牌 4门/旅行车 (5) 核心小组: T.芬德-轿车产品开发部、切利得斯-制造部、J.福特-总
建議 措施
責任及目標 完成日期
措施結果
采取 的措施
R S ODP
N
功能、特性或 要求是什么?
綴彆岆 妦繫ˋ
衄嗣 媎詹ˋ
岆妦繫ˋ
楷汜腔 ˋ
能做些什么? - ??更改 - ?程更改
特殊控制 - ?准、程序或
指南的更改
?有什么??? - ?功能 - 部分功能/功能
?? /功能降? - 功能?歇 - 非?期功能
2
潜在失效模式及后果分析 FMEA
3
潜在失效模式及后果分析
FMEA
4
潜在失效模式及后果分析 FMEA 什么是 FMEA
FMEA 一組系統化的活動
(a)發現、評價產品/過程中潛在的失效及其後果 (b)找出能夠避免或減少這些潛在失效發生的措施 (c)全部過程形成文件
5
潜在失效模式及后果分析 FMEA
协作性:
虽然 FMEA 的编制责任通 常都指派到某个人,但是 FMEA 的输入应该是小组的努力。
小组成员应由知识丰富的 人员组成(如设计、分析/试验 、制造、装配、服务、质量及 可靠性等方面的有丰富经验的 工程师)
7
潜在失效模式及后果分析 FMEA
主观性
FMEA 的特点(3)
31
(22)
过程 FMEA 的開發
5 )車型年/車輛類型
填入將使用和/或正被分析的設計所影響的預期車型年
及車輛類型。 (如果已知的話)
过 程 FMEA
系统
X 子系统 ______部件 01.03/车身密封 (2) 车型年/车辆类型 199X/狮牌 4门/旅行车 (5) 核心小组: T.芬德-轿车产品开发部、切利得斯-制造部、J.福特-总
建議 措施
責任及目標 完成日期
措施結果
采取 的措施
R S ODP
N
功能、特性或 要求是什么?
綴彆岆 妦繫ˋ
衄嗣 媎詹ˋ
岆妦繫ˋ
楷汜腔 ˋ
能做些什么? - ??更改 - ?程更改
特殊控制 - ?准、程序或
指南的更改
?有什么??? - ?功能 - 部分功能/功能
?? /功能降? - 功能?歇 - 非?期功能
2
潜在失效模式及后果分析 FMEA
3
潜在失效模式及后果分析
FMEA
4
潜在失效模式及后果分析 FMEA 什么是 FMEA
FMEA 一組系統化的活動
(a)發現、評價產品/過程中潛在的失效及其後果 (b)找出能夠避免或減少這些潛在失效發生的措施 (c)全部過程形成文件
5
潜在失效模式及后果分析 FMEA
潜在失效模式及后果分析(FMEA)
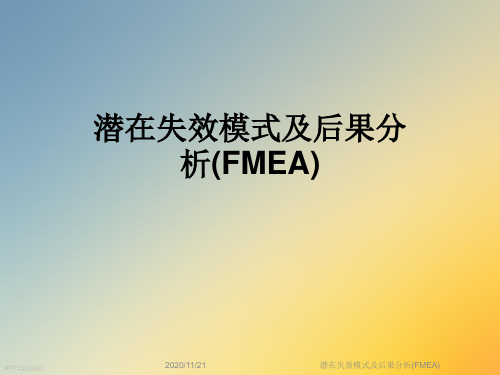
PPT文档演模板
2020/11/21
潜在失效模式及后果分析(FMEA)
•FMEA 在质量体系中
•顾客满意度的改进过程
•获得顾客需求输入
•DFMEA
•PFMEA
•更新PFMEA •控制计划 •反应计划
•过程怎样改变
•控制计划
•过程变量
•产品特性
•数据收集
PPT文档演模板
•进行适当的比较
2020/11/21
潜在失效模式及后果分析(FMEA)
•失效链
•水箱支架断裂
•1 失效原因
•水箱后倾
•1 失效模式
•2 失效原因
•水箱与风扇碰撞
•1 失效后果
•2 失效模式
•水箱冷却水管被风扇刮伤
•2 失效后果
•3 失效原因
•水箱冷却液泄漏
•冷却系统过热
•3 失效后果
PPT文档演模板
•时间
•发动机气缸损坏
2020/11/21
PPT文档演模板
2020/11/21
潜在失效模式及后果分析(FMEA)
•FMEA和FMA、FTA
• FMEA是一种事前行为:
• FMA(Failure Mode Analysis)是一种事后行 为。
• FMA是对产品/过程已经发生的失效模式分析 其产生的原因,评估其后果及采取纠正措施的一 种活动。
潜在失效模式及后果分析(FMEA)
•什么是 FMEA?
•2.术语定义
(影响的)严重度( Severity )- 影响对顾客要求 的重要程度 - 如果失败发生,也可以和安全及其他 风险相关(1=不严重,10=非常严重)
(要因的)发生率( Occurrence )- 给定要因发
FMEA潜在失效模式及后果分析.ppt
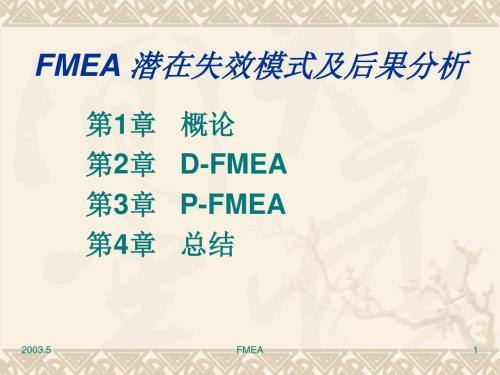
QS9000中明确规定FMEA是质量体系和设计
控制要素中的要求。QS9000要求使用APQP 手册进行质量策划。而DFMEA和PFMEA又 是APQP规定的输入、输出要素。同时PPAP 手册也明确规定了FMEA的要求。因此, FMEA是必须进行的一项活动。
2003.5
FMEA
21
第3章 PFMEA
2003.5 FMEA 14
第 1 章 概论
1.5 什么时候做FMEA?
FMEA是一个动态文件,在整个产品寿命周期内,
根据反馈信息,在进行设计修改时对FMEA进行 重新评审和修改。
2003.5
FMEA
15
第 1 章 概论
1.6 失效链
一个潜在的失效事件的发生,如果没有采取或 来不及采取或事实上不可能采取措施,而使 之引起下游系统或相关系统产生连锁失效事 件,我们称之为“失效链”。
1.5 什么时候做FMEA?
FMEA旨在及早识别出潜在的失效,因此愈早开
始愈好。一般说来,在一个设计概念形成,设计 方案初步确定时应该开始FMEA初稿的编制。 随着设计活动的展开,在设计的各个重要阶段, 对FMEA的初稿进行评审,不断进行修改。 FMEA作为设计活动的一部分,应该在设计任务 完成(如设计图样完成、过程设计文件完成)之 时完成FMEA工作。
FMEA 30
第3章 PFMEA
潜在失效模式及后果分析
( 过程 FMEA)
项目名称: FMEA 编号: 核心小组
2003.5
FMEA
16
第 1 章 概论
失效链举例
不平道 路引起 的振动 与车体 扭转
水箱支架断裂
根源模式
环境 条件
控制要素中的要求。QS9000要求使用APQP 手册进行质量策划。而DFMEA和PFMEA又 是APQP规定的输入、输出要素。同时PPAP 手册也明确规定了FMEA的要求。因此, FMEA是必须进行的一项活动。
2003.5
FMEA
21
第3章 PFMEA
2003.5 FMEA 14
第 1 章 概论
1.5 什么时候做FMEA?
FMEA是一个动态文件,在整个产品寿命周期内,
根据反馈信息,在进行设计修改时对FMEA进行 重新评审和修改。
2003.5
FMEA
15
第 1 章 概论
1.6 失效链
一个潜在的失效事件的发生,如果没有采取或 来不及采取或事实上不可能采取措施,而使 之引起下游系统或相关系统产生连锁失效事 件,我们称之为“失效链”。
1.5 什么时候做FMEA?
FMEA旨在及早识别出潜在的失效,因此愈早开
始愈好。一般说来,在一个设计概念形成,设计 方案初步确定时应该开始FMEA初稿的编制。 随着设计活动的展开,在设计的各个重要阶段, 对FMEA的初稿进行评审,不断进行修改。 FMEA作为设计活动的一部分,应该在设计任务 完成(如设计图样完成、过程设计文件完成)之 时完成FMEA工作。
FMEA 30
第3章 PFMEA
潜在失效模式及后果分析
( 过程 FMEA)
项目名称: FMEA 编号: 核心小组
2003.5
FMEA
16
第 1 章 概论
失效链举例
不平道 路引起 的振动 与车体 扭转
水箱支架断裂
根源模式
环境 条件
2019年潜在的失效模式与效应分析(fmea).ppt

偵 測 度
R P N
建議措施
責任與 目標 完成日期
措施結果
嚴 難 偵 R
採行措施 重 檢 測 P
度 度 度 N
效應為何?
有多不好?
功能, 特徵 或要求為何?
原因為何?
其發生 頻率為何?
改善風險程度 能夠做什麼? -- 設計變更 -- 製程變更 -- 特別管制 -- 標準, 程序書 或指引變更 -- 導入防呆措施 -- 加強設備保養 -- 加強參數控制 -- 加強工作技能
3
FMEA
Failure Mode (cause) Effect Analysis 在有限resource的狀況下, 從失效最多的狀況開始著手, 此即Failure Mode
E: Effect
影響
Effect談三種:
1.Local effect
(對本身的立即影響)
2.Next high level effect
在規定條件下不能完成其規定的功能, 或參數不能保持在規定範圍內, 或操作者失誤,造成產品功能失效, 及因應環境力變化導致功能喪失。
2
FMEA
Failure Mode (cause) Effect Analysis 在所有失效中,出現最多的 (眾數)
M: Mode
例:2, 3, 3, 3, 4, 5, 5, 6, 7 在組織有限的資源下,從失效最多的狀況、最高的頻 率開始著手,此即Failure Mode
工具、 工作站 生產線 作業員訓練 製程 及量具
目標: 使製程品質 、可靠性、成本 及維護性 提昇至最佳狀態 13
何謂設計 FMEA ?
設計的潛在 FMEA 是一種分析技術,係由負責設計 的工程師或小組使用,在儘可能的範圍內用來確保 所有潛在的失效模式及其原因均已納入考量並予以 處理。
- 1、下载文档前请自行甄别文档内容的完整性,平台不提供额外的编辑、内容补充、找答案等附加服务。
- 2、"仅部分预览"的文档,不可在线预览部分如存在完整性等问题,可反馈申请退款(可完整预览的文档不适用该条件!)。
- 3、如文档侵犯您的权益,请联系客服反馈,我们会尽快为您处理(人工客服工作时间:9:00-18:30)。
(4)现行控制的应用。 (5)风险等级。 (6)风险降低。 在FMEA文件开始前,小组必须定义项目范围,收集有效和有效率地进 行FMEA开发过程的必要信息。 五、FMEA的时间顺序 D-FMEA开始早于过程,完成时间在早期的图样完成,但在任何工具的 制造开始之前。P-FMEA开始于基本的操作方法讨论完成时,完成时间早 于生产计划制订和生产批准之前。 D-FMEA 概念 初始设计 P-FMEA 设计完成 样件制造 设计/过程 生产开始
(五)失效给企业带来的后果 失效会给企业带来很严重的后果,如图所示:
失 效 给 企 业 带 来 的 后 果
客户不满意 销售降低 产品质量下降
亏钱 产品也不可能打入 国际市场 公司利润减少
亏更多的钱
(六)失效的损失程度 在不同阶段的失效,其损失程度也是不一样的,所以,尽早发现并消除失 效是减少损失的最佳选择。
提供优质产品
赚更多的钱
ห้องสมุดไป่ตู้
增加公司利润
二、FMEA的应用范围 (一)设计FMEA (1)针对产品本身,产品设计、开发时期的分析技术。 (2)主要是设计工程师和其小组应用。 设计FMEA主要用于确定影响产品性能的重要质量特性,发现影响产品寿命的 重要特性指标和重要安全零部件的潜在失效模式以及后果分析上,以便对这些特 性有效控制来满足顾客的需求和期望,并用于评价设计变更的风险和对设计的不 足采取相应的改进措施。 (二)过程FMEA (1)针对产品的实现过程,过程开发设计的分析技术。 (2)主要是过程(制造)工程师和其小组应用。 过程FMEA主要用于区分影响顾客的重要业务过程或工艺流程的潜在风险,并 对此进行排序,以确定需要立项的改进项目,实现工艺的动态控制和工艺文件的 持续改进,确保质量同险的及时、有效避免。 (三)程序/项目FMEA 针对程序/项目,程序/项目开发设计的分析技术。
(二)P-FMEA的输入与输出 (1)过程/零件潜在失效模式的清单; ()潜在关键特性和重要特性清单; ()消除或减少产品失效模式出现频次的过程改进措施清单; ()提供全成的过程控制策略。 六、P-FMEA的建立要领 (一)P-FMEA建立的文件准备 负责制程工程师应有一个方案,确定哪些文件会在准备P-FMEA时需 要用到,应将P-FMEA中哪些过程需要纳入P-FMEA,哪些不需要列入都 加以说明。 P-FMEA的作业首先要将过程流程图完成,并鉴别产品/制造特性;如 果有过程流程图的话,则应包括相关的D-FMEA中鉴别出来的某些产品的 效应。 (二)主要日期 此日期不应超过预定的产品开始量产日期。以供货商而言,初次PFMEA的预定日期不应该超过顾客所要求的生产零件及核准过程提交日期。
(三)制程功能/要求 小组应审查适当的性能、材料、制程、环境以及安全标准,并尽可能 精确地指出此制程或操作程序的目的,包括有关系统、子系统或零组件的 设计信息。如果特定制程包含多项的操作程序(如组装)且有不同的潜在 失效模式,是好是把这些操作程序列为单独的项目分析。 (四)潜在失效模式 在准备P-FMEA作业中,会假定进料/零件均没有瑕疵,除非P-FMEA 小组依据历来的数据显示进料的品质有缺点,则可纳入分析。 七、P-FMEA标准格式介绍 P-FMEA的标准表格与我们日常所用的一致。 (一)表头填写:要求比较简单,在此不多述,下面重点对以下栏目的填 写做详细介绍: (二)过程功能/要求 填入被分析过程或工序的简要说明(如车削、钻孔、功丝、焊接、装配 等)。另外,建议记录所分析的步骤的相关过程/工序编号。小组应评审适 用的性能、材料、过程、环境和安全标准,以尽可能简洁的方式指明所分 析的过程或工序的目的,包括有关系统、子系统或部件的设计信息。如果 过程包括许多具有不同潜在失效模式的工序,那么,可以把这些工序作为
(4)建立新产品的失效模式清单,是一种创造性和预防性的工作,分析、评 价各种可能发生的情况。 (5)对现存产品而言,可从产品或作业的质量记录中列出符合实际的失效模 式清单。 (6)可从标准表格中选出失效模式,以强调统一性。 (7)可以根据产品零件族而产生。 (8)检查工序可不考虑进行FMEA分析。 2、确定失效模式时思考的问题: 过程工程师应能够提出并回答下列问题: (1)过程/零件怎样不满足要求? (2)无论工程规范如何,顾客认为的可拒收的条件是什么? 以对类似过程的比较和对顾客对类似部件的索赔研究为起点。另外,也有 必要对设计意图加以了解。 3、典型的失效模式 典型的失效模式可能是但不局限于下列情况: 弯曲、毛刺、孔错位、断裂、开孔太深、漏开孔、转运损坏、脏污、变形、 表面太粗糙、贴错标签等等。 注:潜在失效模式应以规范化或技术术语来描述,不同于顾客察觉的现象。
(四)失效模式的潜在影响(潜在失效后果) 失效的潜在后果是指失效模式对顾客产生的影响。 要根据顾客可能发现或经历的情况来描述失效的后果,要记住顾客既可能是 内部的顾客也可能是最终用户。如果失效模式可能影响安全性或对法规的符合性, 要清楚地予以说明。在这里,顾客可以是下道工序,后续工序或工位、经销商或客 户。当评价潜在失效后果时,这些因素都必须予以考虑。 (1)对于最终使用者来说,失效的后果应一律采用产品或系统的性能来描述。 例如:噪音、粗糙、工作不正常、费力、异味、不能工作、牵引阻力、外观不良、 泄露、返工/返修、报废、顾客不满意、车辆控制减弱、不稳定等等。 (2)如果顾客是下一道工序或后续工序/工位,失效的后果应用过程/工序性能来 描述。例如:无法紧固、无法钻孔/攻丝、无法安装、无法加工表面、损坏设备、 不能配合、不能连接、引起工装过度磨损、危害操作者等等。 注意:要尽可能地思考:在产品上会出现该失效模式时对顾客有什么影响、会 造成什么后果。 (五)严重度:是潜在失效模式对顾客影响的严重程度评价 严重度是一给定失效模式最严重的影响后果的级别,严重度是单一的FMEA范 围内的相对定级结果,严重度数值的降低只有通过设计更改或重新设计才能够实现。
失效的表现如下图所示:
产品在工作范围内,导致零部件的破裂、卡 死、损坏现象
在规定条件(环境、操作、时间)下,不能 完成既定功能
在规定条件下,产品参数值不能维持在规定 的上下限之间
(三)产品失效出现在哪里 产品失效通常出现在生产过程中和客户那里,如下表所示: 生产 采购的材料及部件 操作员工作区 局部装配 组装 检验 (四)失效的产生由谁造成 失效的产生是由多方面形成的,如:操作工、制造环节、组织、客户、 以上所有的环节。 客户 客户的工厂 终端用户
独立过程列出。过程功能/要求要与工艺流程中的作业编号和说明相同,标明确切 的过程目的(如车削、钻孔、键槽等)。 可增加产品特性栏,有助于系统地分析所有特性的失效模式。 (三)潜在失效模式 所谓潜在失效模式是指过程有可能不能满足过程功能/要求栏中所描述的过程 要求或设计意图,它是对该特定工序上的不符合的描述。它可能是下一工序的某 个潜在失效模式的一个相关起因或者是前一工序的某个潜在失效模式的一个相关 后果。然而,在准备P-FMEA时,应假定所接收的零件/材料是正确的。当历史数 据表明进货零件质量有缺陷时,FMEA小组可做例外处理。 按照部件、子系统、系统或过程特性,列出特定工序的每一个潜在失效模式, 前提是这种失效模式可能发生,但不一定发生。 1、失效模式的确定要求 (1)失效状态是以作业为单元进行。 (2)只有以作业为审查单元时,才能把失效模式与产品/过程特性相联系,上游 作业中的失效模式应在其所处的那一层进行表述。 (3)跨功能小组应讨论先前作业的失效模式,并假定先前的失效模式不带入本 作业。
P-FMEA的应用
P-FMEA是由负责制造/装配的工程师/小组主要采用的一种分析技术, 用以最大限度地保证各种潜在失效模式及其相关的起因/机理已得到充分 的考虑和论述。 一、P-FMEA过程失效模式和影响分析目的 P-FMEA的主要目的是减少制造风险: (1)帮助分析新/更改(或改进的需要)的制造和装配过程; (2)确保存在的和潜在的制造或装配过程失效模式和影响都要考虑; (3)确定过程缺陷,提出可能的原因,针对原因提出控制措施; (4)消除或降低生产不可接受产品的频率; (5)增强对不可接受产品的可探测度; (6)确定关键特性和重要特性,以便编制完整的过程控制计划; (7)建立过程改进的优先顺序; (8)提供过程开发文件,为今后开发制造和装配过程提供指导。
二、P-FMEA建立/更新的时机 (1)新的/更改的零部件; (2)在各个开发阶段中,当产品/过程设计有变化或得到其他信息时; (3)改进产品/过程设计时; (4)D-FMEA要及时反映最新的产品更改级别、最新的相关实施措施; (5)客户投诉时。对于新产品/过程开发,其进度时间应在可行性分析之前或 之时,在生产工装准备之前; (6)建立P-FMEA时,要假定设计的产品会满足设计要求,因设计缺陷产生的 失效模式不需包含,但也可包含,它们的影响及避免措施由D-FMEA来解决。 三、开展P-FMEA时可使用的方法和工具 开展P-FMEA时,应采用各种问题解决方法和调查工具,包括: (1)脑力风暴; (2)因果图; (3)DOE试验设计; (4)柏拉图; (5)回归分析(散布图); (6)其他方法。
FMEA的人员组成 责任工程师
设计 质量 制造 服务 可靠性 设计 质量 制造 服务 可靠性 顾客
FMEA
共同评审
四、FMEA的基本结构 不论是设计FMEA还是过程FMEA,它的开发都可使用以下共同的方法 来处理: (1)潜在的产品或过程对达到期望的失效。 (2)潜在后果。 (3)失效模式的潜在原因。
失效损失的比例 1:10:1000 设计开发阶段发生的失效 生产制造阶段发生的失效 售后阶段发生的失效
(七)FMEA的目的 FMEA是一组系统化的工作,其目的是: (1)发现、评价产品(过程)中潜在的失效及后果。 (2)找到能够避免或减少这些潜在失效的控制措施。 (3)将以上过程文件化,作为过程控制计划的输入。 企业实施FMEA的最终目的是增加企业的实力,如下图所示: 使客户满意 实施 FMEA 的目 的 增加销售 赚钱 挺进国际市场
三、FMEA的参与者 对任何公司而言, FMEA都是非常重要的活动, FMEA的开发是一个涉及 整个产品实现过程的多方论证的活动,它的有效实施依赖于良好的策划,这个 过程需要大量的时间并且对所需资源的承诺至关重要。 FMEA开发的关键就是过程所有者以及高级管理者的承诺。 (一) FMEA的实施方法 虽然FMEA原则是相同的,但实施方法会根据公司的规模和架构而变化: (1)范围应涵盖公司以及多个层级供应商的FMEA。 (2)适用时,覆盖设计FMEA和过程 FMEA。 (3) 使FMEA过程成为APQP过程的一个不可缺少的部分。 (4)是工程技术评审的一部分。 (5)是产品和过程设计例行审定和批准的一部分。 (二) FMEA的人员组成 FMEA由多功能小组开发,小组规模会根据设计的复杂性和公司规模大小 而有所不同。小组成员要有相关的技术知识,足够的时间,以及管理者批准的 权限,应实施一个综合性的培训方案,包括对管理者、使用者及供应商的培训。