动态膜分离油水乳化液操作条件优化和影响因素分析
膜分离技术存在的问题及解决方法剖析
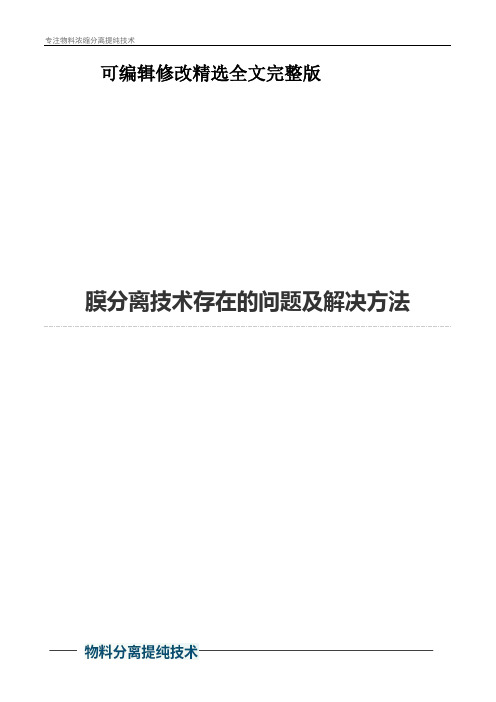
可编辑修改精选全文完整版膜分离技术存在的问题及解决方法膜分离技术作为一种新型的高新制造技术,在食品工业中的应用发展极快,成绩卓著,日益受到各界的关注,展现了广阔前景,尤其一些新的膜分离技术具有更大的潜力和更强的生命力。
下面具体介绍膜分离技术存在的问题及解决方法,一起来看看吧。
1、膜的污染问题由于食品中大都含有蛋白质、脂肪、纤维、鞣质及胶体物质,膜在操作时极易被污染和阻塞,造成膜通量锐减。
而现有的清洗方法难以达到恢复通量的目的。
所以料液的预处理及清洗成了膜技术应用的关键,另外开发新型的不易被污染的膜材料及进行膜面改良也是控制膜污染的有效措施。
2、膜的选择问题膜分离技术在生产中的应用日益广泛,但由于影响因素众多,诸如膜材料的选择、膜分离时的压力、温度、浓度、流速等,需要对其工艺条件作更深入的研究和考察。
3、浓度极化现象由于滤膜上筛孔极小,沉积在膜面的物质易形成一层等高浓度的凝胶层,使膜的通过速度和截流性能受到很大影响,称为浓度极化现象。
应采取相应措施,如降低料液黏度,在各阶段合理的调节压力,分别采用恒速和恒压过滤;或与其他分离方法如澄清法、离心法联用等。
4、膜的性能有待提高膜材料的品种少,膜孔径分布宽,性能欠稳定,如常用的亲水性膜材料对溶质吸附少,截留分子量较小,但热稳定性差,机械强度、抗化学性、抗细菌侵蚀能力通常不高,疏水性膜材料机械强度高、耐高温、耐溶剂、耐生物降解,但膜透水速度低、抗污染能力较低。
另外,由于滤膜本身的孔径不可能完全均匀一致,滤过时部分微粒、热源从较大的滤孔滤出,从而导致初滤液不合要求。
故应用时应采用多级超滤法来提高食品质量,并应研究开发性能优良的滤膜,克服其自身的缺点。
以上就是膜分离技术存在的问题及解决方法,希望对大家有所帮助。
膜分离技术存在的问题及解决方法

膜分离技术存在的问题及解决方法膜分离技术作为一种新型的高新制造技术,在食品工业中的应用发展极快,成绩卓著,日益受到各界的关注,展现了广阔前景,尤其一些新的膜分离技术具有更大的潜力和更强的生命力。
下面具体介绍膜分离技术存在的问题及解决方法,一起来看看吧。
1、膜的污染问题由于食品中大都含有蛋白质、脂肪、纤维、鞣质及胶体物质,膜在操作时极易被污染和阻塞,造成膜通量锐减。
而现有的清洗方法难以达到恢复通量的目的。
所以料液的预处理及清洗成了膜技术应用的关键,另外开发新型的不易被污染的膜材料及进行膜面改良也是控制膜污染的有效措施。
2、膜的选择问题膜分离技术在生产中的应用日益广泛,但由于影响因素众多,诸如膜材料的选择、膜分离时的压力、温度、浓度、流速等,需要对其工艺条件作更深入的研究和考察。
3、浓度极化现象由于滤膜上筛孔极小,沉积在膜面的物质易形成一层等高浓度的凝胶层,使膜的通过速度和截流性能受到很大影响,称为浓度极化现象。
应采取相应措施,如降低料液黏度,在各阶段合理的调节压力,分别采用恒速和恒压过滤;或与其他分离方法如澄清法、离心法联用等。
4、膜的性能有待提高膜材料的品种少,膜孔径分布宽,性能欠稳定,如常用的亲水性膜材料对溶质吸附少,截留分子量较小,但热稳定性差,机械强度、抗化学性、抗细菌侵蚀能力通常不高,疏水性膜材料机械强度高、耐高温、耐溶剂、耐生物降解,但膜透水速度低、抗污染能力较低。
另外,由于滤膜本身的孔径不可能完全均匀一致,滤过时部分微粒、热源从较大的滤孔滤出,从而导致初滤液不合要求。
故应用时应采用多级超滤法来提高食品质量,并应研究开发性能优良的滤膜,克服其自身的缺点。
以上就是膜分离技术存在的问题及解决方法,希望对大家有所帮助。
乳化液制剂中的乳化剂选择与优化

乳化液制剂中的乳化剂选择与优化乳化液是指由两种或多种互不相溶的液体相互均匀分散形成的乳状体系,其中一种液体以微细的液滴形式存在于另一种液体中。
乳化液广泛应用于药物、化妆品、食品等领域。
在乳化液的制备过程中,乳化剂的选择和优化至关重要。
本文将探讨乳化液制剂中的乳化剂选择与优化的相关问题。
一、乳化剂选择的基本原则乳化剂在乳化液制剂中起到稳定乳状结构、降低表面张力、抑制液滴聚集等作用。
乳化剂的选择应遵循以下原则:1. 亲水亲油平衡:乳化剂分子既具有亲水基团,又具有亲油基团,能在油水界面上吸附形成分子膜,并提供一定的界面活性。
2. 高乳化活性:乳化剂分子应具有较高的乳化活性,能有效降低油水界面的张力。
3. 稳定性:乳化剂分子应具有较好的热稳定性和化学稳定性,能够在制剂制备和贮存过程中保持乳状结构的稳定。
4. 环境友好性:乳化剂应具有良好的生物相容性和环境友好性,不对人体和环境造成不良影响。
二、乳化剂的分类与特点根据乳化剂的化学性质和作用方式,可以将乳化剂分为以下几类:1. 离子型乳化剂:离子型乳化剂包括阴离子型和阳离子型乳化剂。
阴离子型乳化剂如硫酸盐、磺酸盐等,阳离子型乳化剂如季铵盐等。
离子型乳化剂乳化活性高,但对环境和皮肤刺激性较大。
2. 非离子型乳化剂:非离子型乳化剂如聚氧乙烯醇、聚氧乙烯酯等,常用于药物和化妆品制剂中。
非离子型乳化剂具有较好的生物相容性和稳定性。
3. 阴离子-非离子复合型乳化剂:由阴离子型乳化剂和非离子型乳化剂按一定比例混合而成,既具有离子型乳化剂的高乳化活性,又具有非离子型乳化剂的较好生物相容性。
4. 生物源乳化剂:来源于天然植物或动物的乳化剂,如卵磷脂、甘油脂肪酸酯等,具有良好的生物相容性和环境友好性。
三、乳化剂选择的影响因素乳化剂的选择不仅与制剂的性质有关,还取决于以下几个因素:1. 油水界面张力:乳化剂应具有较低的油水界面张力,以利于乳化剂在制剂中的分散和稳定。
2. 流体黏度:乳化剂对乳化液的流体黏度有一定影响,过高的乳化剂浓度会导致流体黏度增加,影响制剂的使用性能。
原油脱水站油水分离效果的影响因素和改善措施
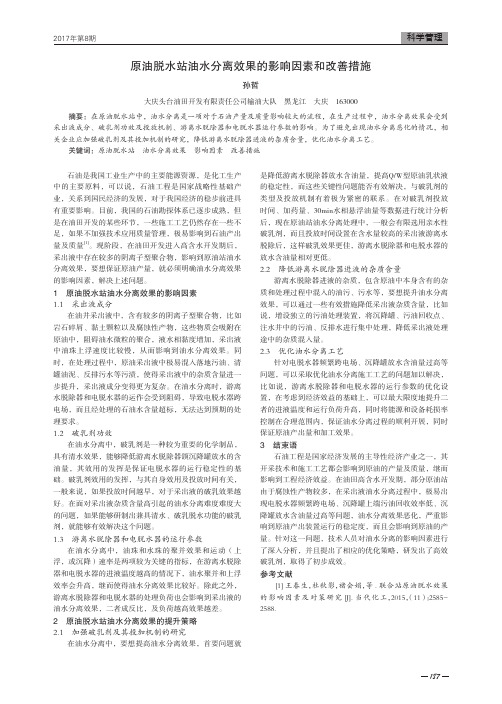
石油是我国工业生产中的主要能源资源,是化工生产中的主要原料,可以说,石油工程是国家战略性基础产业,关系到国民经济的发展,对于我国经济的稳步前进具有重要影响。
目前,我国的石油勘探体系已逐步成熟,但是在油田开发的某些环节,一些施工工艺仍然存在一些不足,如果不加强技术应用质量管理,极易影响到石油产出量及质量[1]。
现阶段,在油田开发进入高含水开发期后,采出液中存在较多的阴离子型聚合物,影响到原油站油水分离效果,要想保证原油产量,就必须明确油水分离效果的影响因素,解决上述问题。
1 原油脱水站油水分离效果的影响因素1.1 采出液成分在油井采出液中,含有较多的阴离子型聚合物,比如岩石碎屑、黏土颗粒以及腐蚀性产物,这些物质会吸附在原油中,阻碍油水微粒的聚合,液水相黏度增加,采出液中油珠上浮速度比较慢,从而影响到油水分离效果。
同时,在处理过程中,原油采出液中极易混入落地污油、清罐油泥、反排污水等污渍,使得采出液中的杂质含量进一步提升,采出液成分变得更为复杂。
在油水分离时,游离水脱除器和电脱水器的运作会受到阻碍,导致电脱水器跨电场,而且经处理的石油水含量超标,无法达到预期的处理要求。
1.2 破乳剂功效在油水分离中,破乳剂是一种较为重要的化学制品,具有清水效果,能够降低游离水脱除器颌沉降罐放水的含油量,其效用的发挥是保证电脱水器的运行稳定性的基础。
破乳剂效用的发挥,与其自身效用及投放时间有关,一般来说,如果投放时间越早,对于采出液的破乳效果越好。
在面对采出液杂质含量高引起的油水分离难度难度大的问题,如果能够研制出兼具清水、破乳脱水功能的破乳剂,就能够有效解决这个问题。
1.3 游离水脱除器和电脱水器的运行参数在油水分离中,油珠和水珠的聚并效果和运动(上浮,或沉降)速率是两项较为关键的指标,在游离水脱除器和电脱水器的进液温度越高的情况下,油水聚并和上浮效率会升高,继而使得油水分离效果比较好。
除此之外,游离水脱除器和电脱水器的处理负荷也会影响到采出液的油水分离效果,二者成反比,及负荷越高效果越差。
拓展——乳化液膜分离技术在废水处理中的研究进展

乳化液膜分离技术在废水处理中的研究进展
Hale Waihona Puke 三、ELM技术对重点工业废水的处理研究
LM 等不同学习算法的性能比较,以预测通过乳化液膜从废水中去除苯酚的效率。神经网络模型的预测值与使 用 MATLAB 程序处理的序批式处理实验的结果非常一致,关联系数(R2)为0.999,均方误差(M SE)为0.004。
乳化液膜分离技术在废水处理中的研究进展
三、ELM技术对重点工业废水的处理研究
去除金属离子 ELM 技术在金属物质的分离与提纯方面研究较多,并已成功应用于含锌废水处理与回收,分别于奥地利、
德国和荷兰等国家建成处理规模大于200m3/h的工业化装置[15]。但 ELM 技术除了能对含锌废水 有效处理,对其它金属物质的处理大多由于液膜的稳定性难题而限制了其工业化应用。目前研究者利用ELM 处理金属废水中包括镍、铬、镉、汞、铅、铀等金属离子,以及稀土金属。为了加强乳化液膜的稳定性,研究 者也从载体、内相试剂、表面活性剂、溶剂及制乳方法等方面开展了优化研究。采用ELM 分离技术处理含金 属离子的废水具有很好的去除效果,并且在实际应用中回收的金属离子再利用可对成本控制有一定的作用。
Span-80为表面活性剂,NaOH 作为剥离剂,制备的乳化液膜从水溶液中提取苯酚。实验中考察 了乳化组成的影响,即:表面活性剂浓度、膜相与内相的体积比(VM/VI)、内相中去除相的浓度,以及 两个工艺参数(进料相搅拌速度为有机酸的萃取速率)和乳液与进料的体积比(VE/VF),结果表明,在 5min内可去除98%以 上 的 苯 酚。并 利 用 神 经 网 络 模 型 中 GD、RB、GDM、GDX、CG 和
乳化液膜分离技术在废水处理中的研究进展
三、ELM技术对重点工业废水的处理研究
影响油水分离因素分析
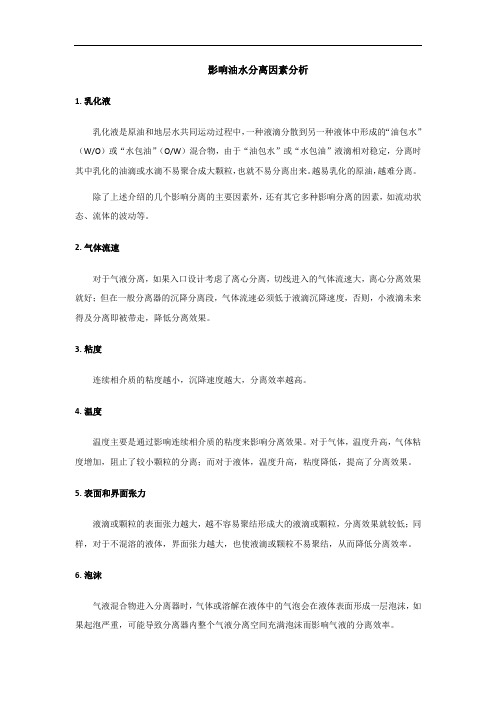
影响油水分离因素分析
1.乳化液
乳化液是原油和地层水共同运动过程中,一种液滴分散到另一种液体中形成的“油包水”(W/O)或“水包油”(O/W)混合物,由于“油包水”或“水包油”液滴相对稳定,分离时其中乳化的油滴或水滴不易聚合成大颗粒,也就不易分离出来。
越易乳化的原油,越难分离。
除了上述介绍的几个影响分离的主要因素外,还有其它多种影响分离的因素,如流动状态、流体的波动等。
2.气体流速
对于气液分离,如果入口设计考虑了离心分离,切线进入的气体流速大,离心分离效果就好;但在一般分离器的沉降分离段,气体流速必须低于液滴沉降速度,否则,小液滴未来得及分离即被带走,降低分离效果。
3.粘度
连续相介质的粘度越小,沉降速度越大,分离效率越高。
4.温度
温度主要是通过影响连续相介质的粘度来影响分离效果。
对于气体,温度升高,气体粘度增加,阻止了较小颗粒的分离;而对于液体,温度升高,粘度降低,提高了分离效果。
5.表面和界面张力
液滴或颗粒的表面张力越大,越不容易聚结形成大的液滴或颗粒,分离效果就较低;同样,对于不混溶的液体,界面张力越大,也使液滴或颗粒不易聚结,从而降低分离效率。
6.泡沫
气液混合物进入分离器时,气体或溶解在液体中的气泡会在液体表面形成一层泡沫,如果起泡严重,可能导致分离器内整个气液分离空间充满泡沫而影响气液的分离效率。
[久吾高科]膜分离技术在油田采出水处理中的应用及存在的问题
![[久吾高科]膜分离技术在油田采出水处理中的应用及存在的问题](https://img.taocdn.com/s3/m/8fbc411576c66137ee06196c.png)
石油工业是环境污染大户,要保证石油工业的可持续发展,应大力推广使用先进的技术与设备,包括膜技术的应用.目前,我国大部分油田己进入中后期开采阶段,水质也随着工艺的复杂化更加恶化,处理难度增大.目前,油田每天有70万t左右的采油废水需要处理,其中有10万t左右的废水要求精细过滤后回注.油田采出水水化学组分复杂、腐蚀性强,油和悬浮固体的去除是处理的关键,深度处理后可用作采油锅炉用水以及低渗透油田的回注水.采油废水的处理与回用是各个油田面临的重要问题,采油废水的处理和利用不仅具有重要的环境意义,同时节约水资源和回收原油,产生一定的经济效益.刘勇利用膜分离技术对油田采出水处理,出水含油量低于8mg/L,悬浮固体含量低于1mg/L.王怀林等分别采用南京化工大学和美国Filter公司生产的陶瓷微滤膜,对江苏油田真二站三相分离器出水进行了实验研究.王立国等对经过核桃壳等预处理的油田采出水采用超滤膜进行处理,并且对超滤膜的清洗做了初步的研究,结果显示,≥1.0μm悬浮固体去除率达到99%,出水悬浮固体含量和含油量都下降到1mg/L以下,达到了低渗透油层注水A1类标准的水质要求.膜技术在采出水处理中的应用已完成了室内实验和现场中试,一些工程也已陆续投产.然而膜技术处理油田采出水存在膜通量较低、出水水质经常恶化、膜污染严重而清洗频繁等问题,同时膜处理工艺的经济性还需要作进一步的确认.目前,还没有一项过硬的膜技术广泛应用于油田采出水的处理.膜通量、出水水质和清洗频率在设计上还没有明确规定,膜材料研究、膜和膜组件的开发、生产检测与膜产品在工业生产领域中的应用属于两个不同的范畴,只有发挥两方面技术人员的特长,优势互补,才能带动膜产业的迅速发展.油田含油废水成分复杂,含油量高,处理难度大,废水经处理后回注成为减少环境污染、保障油田可持续开发、提高油田的经济效益的一个重要途径.今后的发展趋势是从实际情况出发,优化各种技术的组合方式,利用最小的投入,找到高效的、经济的废水处理新技术.。
《2024年膜分离技术在油田含油污水处理中的应用研究进展》范文
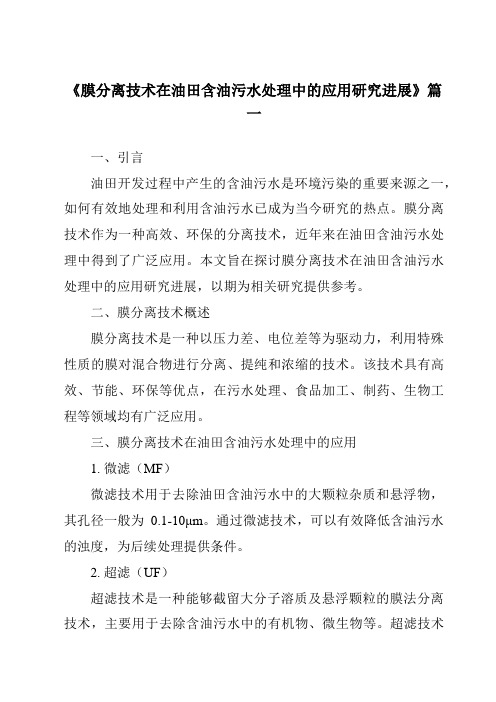
《膜分离技术在油田含油污水处理中的应用研究进展》篇一一、引言油田开发过程中产生的含油污水是环境污染的重要来源之一,如何有效地处理和利用含油污水已成为当今研究的热点。
膜分离技术作为一种高效、环保的分离技术,近年来在油田含油污水处理中得到了广泛应用。
本文旨在探讨膜分离技术在油田含油污水处理中的应用研究进展,以期为相关研究提供参考。
二、膜分离技术概述膜分离技术是一种以压力差、电位差等为驱动力,利用特殊性质的膜对混合物进行分离、提纯和浓缩的技术。
该技术具有高效、节能、环保等优点,在污水处理、食品加工、制药、生物工程等领域均有广泛应用。
三、膜分离技术在油田含油污水处理中的应用1. 微滤(MF)微滤技术用于去除油田含油污水中的大颗粒杂质和悬浮物,其孔径一般为0.1-10μm。
通过微滤技术,可以有效降低含油污水的浊度,为后续处理提供条件。
2. 超滤(UF)超滤技术是一种能够截留大分子溶质及悬浮颗粒的膜法分离技术,主要用于去除含油污水中的有机物、微生物等。
超滤技术在油田含油污水处理中具有良好的应用效果,能够有效提高出水的质量。
3. 纳滤(NF)和反渗透(RO)纳滤和反渗透技术主要应用于处理高浓度含盐废水,如油田回注水等。
这两种技术可以有效去除水中的盐分、有机物等杂质,提高水质。
4. 膜生物反应器(MBR)膜生物反应器结合了生物处理技术和膜分离技术,具有高效、节能、环保等优点。
在油田含油污水处理中,MBR可以用于去除有机物、降低浊度等,同时能够提高处理效率,降低处理成本。
四、研究进展近年来,国内外学者针对膜分离技术在油田含油污水处理中的应用进行了大量研究。
通过改进膜材料、优化操作条件等方法,提高了膜的通量、抗污染能力和使用寿命。
同时,针对不同地区、不同来源的含油污水,研究人员还开展了大量的现场试验和实际应用研究,为膜分离技术在油田含油污水处理中的应用提供了有力支持。
五、未来展望未来,随着油田开发规模的扩大和环保要求的提高,膜分离技术在油田含油污水处理中的应用将更加广泛。
动态膜分离技术

一.背景知识
• 因此,动态膜作为一项新型的特殊膜分离技术 正越来越多地受到国内外水处理技术研究者的 关注。
二.动态膜分离技术原理
动态膜是指通过预涂剂或活性污泥在膜表
面形成新的膜,也称为次生膜(second membrane)。
动态膜的形成过程本质上就是膜污染的过程。
二.动态膜分离技术原理
三.影响动态膜分离性 能的因素
——错流速度
错流速度对出水通量的影响,不同研究 者的结论不同。 一般来说,随着错流流速的增加则动态 膜的厚度会逐渐减小,使得出水通量增 加且出水水质变差。动态膜的厚度主 要是由错流所 形成的剪切力和膜两侧 的压力差共同决定。
三.影响动态膜分离性 能的因素
——错流速度
Thank you for your time!
三.影响动态膜分离性能的因素
1. 2. 3. 4. 5. pH的影响 成膜物质浓度的影响 载体性质的影响 错流速度的影响 后处理条件的影响
三.影响动态膜分离性 能的因素 ——PH值
pH 值主要对酸碱涂膜剂、有等电 点的涂膜剂以及膜基质本身带电荷的动 态膜产生影响,在不同的pH下,动态 膜因所带电荷(正负性及荷电量等)的 不同会表现出不同的性质。
若在形成过程中能找到一个平衡状态, 则所形成的动态膜厚度适中,这样膜的 出水通量才会足够大,运行时间足够长, 从而使出水水质达到标准。
三.影响动态膜分离性 能的因素 ——后处理条件
对于一定的动态膜来说,有时候后处理 是十分有必要的,相应的后处理使得预 涂动态膜的性能到明显的增强。 例如:浸泡在80 ℃纯净水中进行后处 理24 h 后, PVA 膜的通量比未经后处 理的膜高许多,而它们的蛋白质截留率 仍相当高。
油气田的油水分离方法_概述说明以及解释
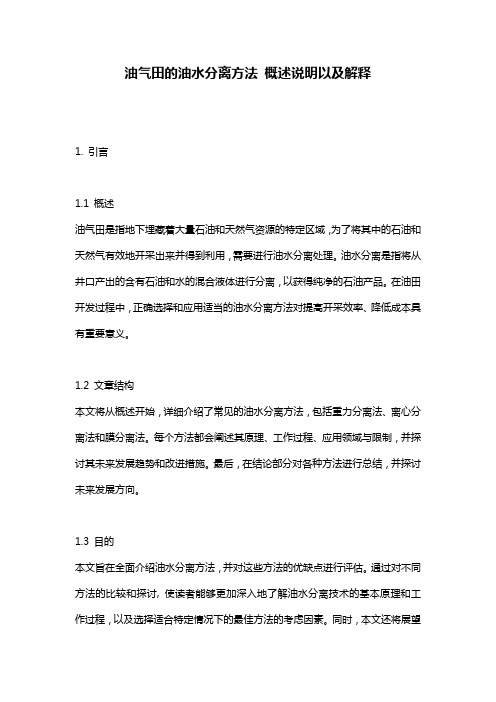
油气田的油水分离方法概述说明以及解释1. 引言1.1 概述油气田是指地下埋藏着大量石油和天然气资源的特定区域,为了将其中的石油和天然气有效地开采出来并得到利用,需要进行油水分离处理。
油水分离是指将从井口产出的含有石油和水的混合液体进行分离,以获得纯净的石油产品。
在油田开发过程中,正确选择和应用适当的油水分离方法对提高开采效率、降低成本具有重要意义。
1.2 文章结构本文将从概述开始,详细介绍了常见的油水分离方法,包括重力分离法、离心分离法和膜分离法。
每个方法都会阐述其原理、工作过程、应用领域与限制,并探讨其未来发展趋势和改进措施。
最后,在结论部分对各种方法进行总结,并探讨未来发展方向。
1.3 目的本文旨在全面介绍油水分离方法,并对这些方法的优缺点进行评估。
通过对不同方法的比较和探讨, 使读者能够更加深入地了解油水分离技术的基本原理和工作过程,以及选择适合特定情况下的最佳方法的考虑因素。
同时,本文还将展望未来油水分离方法的发展方向,为油气田开采提供更加高效和可持续的技术支持。
2. 油水分离方法概述2.1 定义和背景油气田开发中,由于地下储层中含有大量的油气和水,需要对其进行有效分离,以便提取纯净的油气资源。
油水分离是指将混合油水体系中的石油和水分离出来的过程。
该过程是油气田开发工艺中至关重要的一步。
2.2 常见的油水分离方法目前,常见的油水分离方法主要包括重力分离法、离心分离法和膜分离法。
重力分离法:利用不同密度的石油和水之间的差异,通过设置合适的装置(如沉降池或旋流器)使两者自然分层。
石油会浮在上部,而水则处于底部。
离心分离法:通过旋转设备(例如旋转式离心机),利用不同密度物质在受到向心力作用时产生不同反应速度这一原理进行分离。
由于石油和水之间密度差异较小,在高速旋转下可实现有效的物理分层。
膜分离法:利用特殊的膜材料,通过渗透、吸附和筛分等作用对石油和水进行分离。
通过选择合适的膜材料和操作条件,可以实现高效的油水分离。
膜分离技术的实验优化与应用探索

膜分离技术的实验优化与应用探索膜分离技术作为一种重要的分离技术,广泛应用于水处理、食品加工、化工、医药等领域。
本文将探讨膜分离技术的实验优化与应用探索,介绍其原理、实验优化方法以及在不同领域的应用案例。
一、膜分离技术的原理膜分离技术是利用半透膜对溶液中的溶质进行分离的一种方法。
半透膜具有选择性通透性,能够将溶质与溶剂分离开来。
其原理主要包括压力驱动、浓度差驱动和电场驱动等。
压力驱动是膜分离技术最常用的一种方法。
通过施加一定的压力,使溶液在膜上产生渗透压差,从而实现溶质与溶剂的分离。
常见的压力驱动膜分离技术有超滤、微滤和纳滤等。
浓度差驱动是指利用溶液中溶质浓度差产生的渗透压差来实现分离。
这种方法适用于浓度差较大的溶液,如蒸发结晶、气体吸附和渗透蒸发等。
电场驱动是利用电场作用于溶液中的离子,使其在膜上产生电渗流,从而实现分离。
这种方法适用于离子分离、电解质浓缩和电渗析等。
二、膜分离技术的实验优化方法为了提高膜分离技术的分离效率和经济性,需要对实验进行优化。
以下是一些常用的实验优化方法:1. 膜材料的选择:不同的膜材料具有不同的分离性能和适用范围。
根据实际需求选择合适的膜材料,可以提高分离效率。
2. 膜孔径的调控:膜孔径的大小直接影响到溶质的分离效果。
通过调控膜孔径,可以实现对不同大小的溶质的分离。
3. 操作条件的优化:包括温度、压力、pH值等操作条件的优化。
通过调节这些操作条件,可以提高膜分离的效率和选择性。
4. 膜的预处理:对膜进行预处理,如清洗、活化等,可以提高膜的分离性能和使用寿命。
5. 膜分离系统的优化:包括膜组件的设计、流体流动方式的优化等。
通过对膜分离系统的优化,可以提高分离效率和降低能耗。
三、膜分离技术在不同领域的应用案例膜分离技术在水处理、食品加工、化工、医药等领域都有广泛的应用。
以下是一些应用案例的介绍:1. 水处理:膜分离技术在水处理领域有着重要的应用。
例如,通过超滤膜可以将水中的悬浮物、胶体和微生物等去除,从而实现水的净化和回收利用。
化工装置中液体分离技术的操作方法及优化

化工装置中液体分离技术的操作方法及优化液体分离技术在化工装置中起着至关重要的作用,它能够将混合物中的不同成分分离开来,从而实现产品的纯化和提纯。
本文将介绍液体分离技术的常见操作方法,并探讨如何优化这些方法以提高分离效率和降低能耗。
一、常见液体分离技术的操作方法1. 蒸馏法蒸馏法是一种常见的液体分离技术,它利用不同组分的沸点差异来实现分离。
在蒸馏过程中,混合物被加热至其中一种组分的沸点,该组分蒸发并进入冷凝器,最终以液体形式收集。
而其他组分则留在原容器中。
蒸馏法的操作方法相对简单,但需要根据混合物的性质选择合适的操作条件,如温度、压力等。
2. 萃取法萃取法是一种通过溶剂将混合物中的目标组分分离出来的技术。
在萃取过程中,混合物与溶剂接触后,目标组分会在两相之间分配,从而实现分离。
萃取法的操作方法较为灵活,可以根据混合物的特性选择合适的溶剂和操作条件。
此外,还可以通过多级萃取来提高分离效率。
3. 结晶法结晶法是一种通过溶解度差异将混合物中的目标组分分离出来的技术。
在结晶过程中,混合物被加热至其中一种组分的溶解度,然后冷却至该组分的溶解度以下,目标组分会结晶出来。
结晶法的操作方法相对简单,但需要根据混合物的溶解度曲线选择合适的操作条件。
二、液体分离技术的优化方法1. 优化操作条件液体分离技术的效率和能耗往往与操作条件密切相关。
因此,优化操作条件是提高分离效率和降低能耗的关键。
例如,在蒸馏法中,可以通过调整温度和压力来控制沸点差异,从而提高分离效率。
在萃取法中,可以优化溶剂的选择和使用量,以减少溶剂的消耗和回收成本。
在结晶法中,可以通过调整冷却速率和搅拌强度来控制结晶过程,从而提高结晶效率。
2. 引入辅助设备为了进一步提高液体分离技术的效率,可以引入一些辅助设备。
例如,在蒸馏法中,可以使用精馏塔来增加蒸馏效果,提高分离效率。
在萃取法中,可以使用萃取塔或萃取柱来增加接触面积,提高分离效率。
在结晶法中,可以使用搅拌器或冷却器来加快结晶速率,提高结晶效率。
《微生物乳化原油的机理及影响因素研究》范文
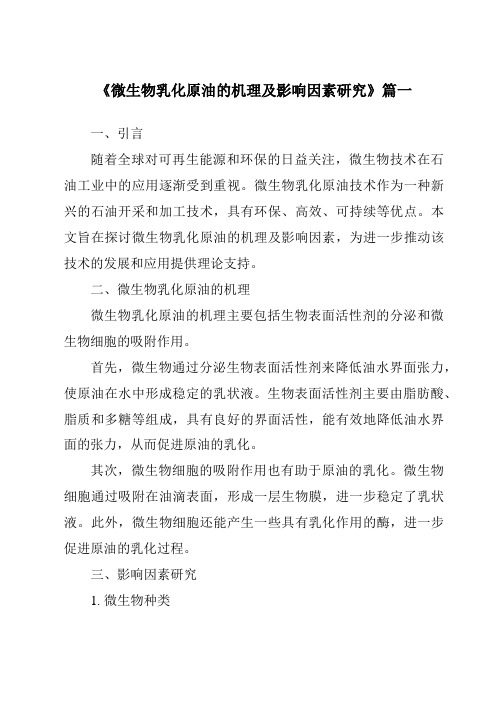
《微生物乳化原油的机理及影响因素研究》篇一一、引言随着全球对可再生能源和环保的日益关注,微生物技术在石油工业中的应用逐渐受到重视。
微生物乳化原油技术作为一种新兴的石油开采和加工技术,具有环保、高效、可持续等优点。
本文旨在探讨微生物乳化原油的机理及影响因素,为进一步推动该技术的发展和应用提供理论支持。
二、微生物乳化原油的机理微生物乳化原油的机理主要包括生物表面活性剂的分泌和微生物细胞的吸附作用。
首先,微生物通过分泌生物表面活性剂来降低油水界面张力,使原油在水中形成稳定的乳状液。
生物表面活性剂主要由脂肪酸、脂质和多糖等组成,具有良好的界面活性,能有效地降低油水界面的张力,从而促进原油的乳化。
其次,微生物细胞的吸附作用也有助于原油的乳化。
微生物细胞通过吸附在油滴表面,形成一层生物膜,进一步稳定了乳状液。
此外,微生物细胞还能产生一些具有乳化作用的酶,进一步促进原油的乳化过程。
三、影响因素研究1. 微生物种类不同种类的微生物在乳化原油的过程中具有不同的作用。
某些微生物能分泌具有较强界面活性的生物表面活性剂,从而有效地降低油水界面张力,促进原油的乳化。
因此,选择合适的微生物种类是提高原油乳化效果的关键。
2. 环境条件环境条件如温度、pH值、盐度等对微生物的生长和代谢具有重要影响,从而影响原油的乳化效果。
例如,某些微生物在适宜的温度和pH值下能更好地生长和代谢,产生更多的生物表面活性剂,从而提高原油的乳化效果。
3. 培养基组成培养基的组成对微生物的生长和代谢具有直接影响。
适宜的培养基能为微生物提供充足的营养,促进其生长和代谢,从而增强其乳化原油的能力。
此外,培养基中的某些成分如碳源、氮源等还能影响生物表面活性剂的产量和性质,进一步影响原油的乳化效果。
4. 作用时间与作用方式作用时间和作用方式也是影响原油乳化效果的重要因素。
在一定的时间内,随着作用时间的延长,微生物的代谢活动增强,生物表面活性剂的产量增加,从而增强原油的乳化效果。
乳化液泵液力端动态特性分析与结构优化的开题报告
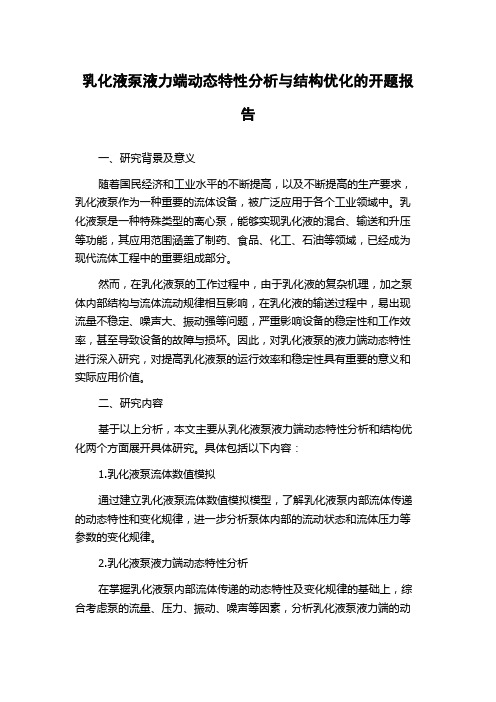
乳化液泵液力端动态特性分析与结构优化的开题报告一、研究背景及意义随着国民经济和工业水平的不断提高,以及不断提高的生产要求,乳化液泵作为一种重要的流体设备,被广泛应用于各个工业领域中。
乳化液泵是一种特殊类型的离心泵,能够实现乳化液的混合、输送和升压等功能,其应用范围涵盖了制药、食品、化工、石油等领域,已经成为现代流体工程中的重要组成部分。
然而,在乳化液泵的工作过程中,由于乳化液的复杂机理,加之泵体内部结构与流体流动规律相互影响,在乳化液的输送过程中,易出现流量不稳定、噪声大、振动强等问题,严重影响设备的稳定性和工作效率,甚至导致设备的故障与损坏。
因此,对乳化液泵的液力端动态特性进行深入研究,对提高乳化液泵的运行效率和稳定性具有重要的意义和实际应用价值。
二、研究内容基于以上分析,本文主要从乳化液泵液力端动态特性分析和结构优化两个方面展开具体研究。
具体包括以下内容:1.乳化液泵流体数值模拟通过建立乳化液泵流体数值模拟模型,了解乳化液泵内部流体传递的动态特性和变化规律,进一步分析泵体内部的流动状态和流体压力等参数的变化规律。
2.乳化液泵液力端动态特性分析在掌握乳化液泵内部流体传递的动态特性及变化规律的基础上,综合考虑泵的流量、压力、振动、噪声等因素,分析乳化液泵液力端的动态特性,明确乳化液泵在实际运行过程中存在的流量不稳定、压力脉动、噪声大等问题,为进一步的结构优化提供理论基础。
3.乳化液泵结构优化设计针对乳化液泵液力端的动态特性问题,本研究将从泵结构的角度入手,通过探究泵体内部结构与设计参数之间的联系,采用一系列优化措施,如进口导流器的优化设计、导叶的优化设计等,进行结构优化设计,并通过数值模拟和实验验证优化效果,进一步提高乳化液泵的流量稳定性和运行效率。
三、研究预期及创新点本研究主要的预期成果为:1.建立乳化液泵流体数值模拟模型,实现对乳化液泵液力端动态特性的理论分析和预测;2.深入分析乳化液泵液力端的动态特性,明确现有泵结构存在的问题及不足;3.针对现有泵结构的问题和不足,采取一系列优化措施和方法,进行乳化液泵的结构优化设计,并通过数值模拟和实验验证,实现泵的稳定性和工作效率的提高。
碳化硅动态膜分离油水乳化液的性能研究

碳化硅动态膜分离油水乳化液的性能研究王婷婷;苏琼;潘艳秋;孙初锋;苑沛霖;崔璐娟【摘要】以孔径1.0μm的管式陶瓷膜为载体制备碳化硅动态膜,对碳化硅动态膜分离油水乳化液的性能进行了研究,考察了油水乳化液的温度、压力、流量、浓度、pH值对分离效果的影响.实验结果表明,在实验考察的操作范围内,稳定渗透通量随温度、流量的增大而增大,随压力的增大先增大后减小,随浓度的增大而减小;在实验考察的操作范围内,截留率随温度、压力、流量、浓度的增大呈现减小的趋势.pH值对油水乳化液的分离影响较大,pH值为中性时分离效果最佳.【期刊名称】《西北民族大学学报(自然科学版)》【年(卷),期】2018(039)003【总页数】5页(P11-15)【关键词】动态膜;碳化硅;水包油;乳化液;油水分离【作者】王婷婷;苏琼;潘艳秋;孙初锋;苑沛霖;崔璐娟【作者单位】西北民族大学化工学院,甘肃兰州730000;西北民族大学化工学院,甘肃兰州730000;大连理工大学化工与环境生命学部,辽宁大连 116024;西北民族大学化工学院,甘肃兰州730000;西北民族大学化工学院,甘肃兰州730000;西北民族大学化工学院,甘肃兰州730000【正文语种】中文【中图分类】X703.121世纪以来,生态和环境保护备受全球的普遍关注.含油污水作为一种环境污染物,危害人类的生存环境和身体健康,亟待处理.石油资源作为非再生资源,需要加以回收并进行综合利用.乳化油污水是含油污水中最难分离的一类.常规的分离方法无法将其有效处理或能耗较大,在应用时受到限制[1-3].膜分离法以其高效、能耗低、条件温和、分离范围广、设备简单、易操作等优点得到人们的关注.动态膜(dynamic membrane,DM)技术通过在多孔载体上截留预涂液中的无机或有机物质形成一层具有超滤或微滤性质的膜层,使得整体呈现出非对称膜的结构,提高了抗污染能力,截留性能也超越了载体[4-5].动态膜的制备采用廉价的大孔载体,降低了制备成本,预涂原料丰富、制备容易、清洗方便、操作简单,越来越受到研究者的关注.许多无机和有机材料都可充当动态膜的载体,如多孔陶瓷膜、炭膜、多孔不锈钢膜、工业滤布、无纺布等无机材料以及一些高分子有机材料,如聚烯烃类膜.所涉及到的涂膜材料主要有氢氧化镁[6]、二氧化锰[7]、水合锆氧化物[8]、二氧化钛[9]、聚乙烯醇[10]、高岭土[11]等.动态膜分离油水乳化液的研究主要集中在动态膜制备及其分离油水乳化液的影响因素和分离性能方面,在机理方面也进行了一定的探讨.碳化硅作为一种性能优良的无机材料,具有优异的亲水性、生物相容性、耐酸碱性、化学惰性、机械性能和较低的热膨胀性,可在腐蚀性环境中应用,是一种前景优良的分离膜材料[12].目前,尚无学者运用碳化硅纳米颗粒制备动态膜并将其运用到油水分离当中,这是一个崭新的课题.基于此,本文拟开展此项工作,在多孔管式陶瓷膜载体上制备碳化硅动态膜,考察温度、压力、流量、浓度、pH值等对碳化硅动态膜分离油水乳化液性能的影响,以此拓宽动态膜分离油水乳化液的领域.1 材料涂膜材料碳化硅纳米颗粒购于上海超威纳米科技有限公司,平均粒径为100 μm.载体陶瓷膜管购买于广东揭西利顺科技有限公司,载体膜管外径10 mm、内径6 mm,有效管长10 cm,平均孔径为1.0 μm,平均孔隙率为39.4%.盐酸和氢氧化钠试剂购买于天津光复科技有限公司.不锈钢膜组件为自制.2 方法2.1 碳化硅动态膜的制备将载体陶瓷膜管固定在自制膜组件内,将配制好的浓度为0.75 g·L-1的碳化硅悬浮液经泵加压后送入陶瓷膜管内.膜组件两端压力控制在0.10 MPa下.随着时间的推移,在陶瓷膜管内壁上逐渐形成碳化硅动态膜.2.2 油水乳化液的制备称取一定量的发动机润滑油加入一定体积的去离子水中,在超声波震荡仪中超声6 h,肉眼观察溶液呈乳白色,在生物显微镜下观察所得的乳化液,拍摄照片见图 1所示.油滴直径分布较为均匀,直径均小于10 μm,可见为典型的水包油型乳化液.将制取的水包油型乳化液静置24 h以上仍能稳定存在.图1 油水乳化液配制过程2.3 碳化硅动态膜分离油水流程图2 动态膜分离油水流程图碳化硅动态膜分离油水流程图见图2所示.将油水乳化液用泵输送至自制膜组件中的碳化硅动态膜管内,跨膜压差由阀门调节并由自制膜组件两端的精密压力表测量.每隔一段时间接取一定体积的渗透液,计算单位时间、单位面积的渗透液量即为渗透通量.渗透通量的计算如公式1所示.渗透液的浓度用紫外分光光度计UV2600在230 nm波长下测取,截留率计算如公式2所示.(1)(2)公式(1)中J为渗透通量,单位为L·m-2·h-1;V为t时间内渗透液体积,单位为L;A是有效膜面积,单位为m2;t是渗透时间,单位为h.公式(2)中R为截留率,cf 和cp分别为料液和渗透液的浓度,单位为mg·L-1.为了保证实验结果的准确性,每组数据取三次实验结果的平均值.3 结果与讨论膜法液体分离过程中,渗透通量随着时间的推移逐步下降,到一定时间后趋于稳定,此时的渗透通量即为稳定渗透通量,此时处于膜稳定工作阶段.研究者们都通常以稳定渗透通量和截留率来考察膜的工作性能.3.1 操作压力的影响在油水浓度800 mg·L-1、流量100 L/h、温度30 ℃、pH值为7的条件下,考察了不同操作压力下,动态膜分离油水乳化液的渗透通量和截留率随时间的变化,见图3所示.可见随着操作压力的增大,油水乳化液稳定渗透通量随之先增大后减小.由于碳化硅动态膜是在0.10 MPa压力下制备的:当压力大于0.10 MPa时,碳化硅颗粒会进一步深入载体,动态膜层压得更为紧密,传质阻力增大,但由于此时仍在压力控制区,稳定渗透通量继续增大.当压力大于0.15 MPa时,操作由“压力控制区”转入“传质控制区”,稳定渗透通量变小.在后续实验中,采用的压力均为0.10 MPa.3.2 温度的影响图3 稳定渗透通量和截留率随压力的变化图4 稳定渗透通量和截留率随温度的变化在油水浓度800 mg·L-1、流量100 L/h、操作压力0.10 MPa、pH值为7的条件下,考察了温度为25 ℃、30 ℃、35 ℃、40 ℃、45 ℃时,油水乳化液稳定渗透通量和截留率随温度的变化情况,见图4.从图中可以看到,在温度范围为25 ℃~45 ℃时,稳定渗透通量随温度的增加而增大,几乎成正比关系.这是由于随着温度的升高,油水乳化液粘度降低,油水扩散系数增大且膜层阻力降低,因而稳定渗透通量增大.随着温度的升高,乳化油滴粒径变小,截留率也有所下降.3.3 流量的影响图5 稳定渗透通量和截留率随流量的变化图6 稳定渗透通量和截留率随浓度的变化在油水浓度800 mg·L-1、温度30 ℃、操作压力0.10 MPa、pH值为7的条件下,考察流量为50 L/h、75 L/h、100 L/h、125 L/h时,稳定渗透通量和截留率的变化情况,结果如图5所示.可见在实验考察的操作范围内,随着流量的增大,稳定渗透通量逐步增大.这是由于随着流量的增大,流体的湍动加剧,导致边界层变薄,传质阻力减小,稳定渗透通量随之增大.截留率随流量增大则趋于减小,这是由于流体剪切力增大造成油滴颗粒变小,因而造成截留率的下降.3.4 油水浓度的影响在流量为100 L/h、温度为30 ℃、操作压力为0.10 MPa、pH值为7的条件下,考察了油水浓度为500 mg·L-1、600 mg·L-1、800 mg·L-1、1 000 mg·L-1时,SiC动态膜分离油水乳化液的渗透通量的变化情况.结果如图6所示,随着油浓度由500 mg·L-1向1 000 mg·L-1增加,动态膜的渗透通量在下降.这是因为油水浓度变大,溶液黏度升高,随着过滤时间的推移较多的油组分覆盖在动态膜层表面上,导致了膜污染严重,渗透通量下降.3.5 pH值的影响在油水浓度800 mg·L-1、流量100 L/h、温度30 ℃、操作压力为0.10 MPa的条件下,实验用盐酸和氢氧化钠来调节油水乳化液的pH值.考察了pH值为3、5、7、9、11时,碳化硅动态膜的稳定渗透通量情况.在中性环境下,动态膜的渗透通量较大.水包油型乳化液的乳化油液滴表面带有负电荷.碳化硅的等电点为pH=4.当pH>4时,碳化硅颗粒带负电荷,碳化硅颗粒和乳化油液滴之间相互排斥,碳化硅颗粒之间的排斥力增强,碳化硅颗粒会进一步进入到载体中,造成载体孔的堵塞,因而导致渗透通量的下降.当pH<4时,碳化硅颗粒带正电荷,会吸附表面带有负电荷的乳化油液滴,在动态膜层上形成一层油膜,因而同样会导致渗透通量的下降.图7为碳化硅动态膜在不同pH值下对油水乳化液的截留率.可见,碱性条件下,截留率较高,在98.5%以上;酸性条件下,截留率较低.因而要避免碳化硅动态膜在酸性条件下截留油水乳化液.图7 不同pH值下的稳定渗透通量和截留率图4 结论碳化硅动态膜分离油水乳化液时,在实验考察的操作范围内,稳定渗透通量随温度、流量的增大而增大,随压力的增大先增大后减小,随浓度的增大而减小.在实验考察的操作范围内,截留率则随温度、压力、流量、浓度的增大呈现减小的趋势.pH 值对油水乳化液的分离影响较大,pH值为中性时,渗透通量和截留率均较高,此时的分离效果最佳.参考文献:【相关文献】[1] Y.Q. Pan, W. Wang, T.H. Wang, P.J. Yao.Fabrication of carbon membrane and microfiltration of oil-in-water emulsion: an investigation on fouling mechanisms[J]. Separation and Purification Technology, 2007, 57(2): 388-393.[2] 崔霞,张捍民,叶茂盛,等.新型动态膜预涂剂交联聚乙烯醇微球的制备及表征[J]. 环境科学,2008,29(4):960-965.[3] 李晓波,胡保安,顾平. 动态膜分离技术研究进展[J]. 膜科学与技术,2007,27(4):91-95.[4] 王婷婷,潘艳秋,王同华. 二氧化钛动态膜在油水乳化液分离中的应用研究[J]. 高校化学工程学报, 2010, 24(1): 22-28.[5] Zhao Yijiang,Tan Yi,Wong Fook-Sin, et a1. Formation of dynamic membranes for oily water separation by crossflowfiltration[J]. Separation and Purification Technology, 2005, 44(3): 212-220.[6] Chu H,Zhang Y,Zhou X,et al. Bio-enhanced powder-activated carbon dynamic membrane reactor for municipal wastewater treatment[J]. Journal of Membrane Science,2013,433(1):126-134.[7] 杨涛,马正飞,杨期勇. 高岭土/水合MnO2复合预涂动态膜的制备[J]. 膜科学与技术, 2010,30(5): 98-102.[8] 孙宏梅, 潘艳秋,柏斌,等. 炭膜基亲水性无机动态膜的制备研究[J]. 高校化学工程学报, 2011, 25(6): 1062-1067.[9] Pan YQ, Wang TT, Sun HM, et al. Preparation and application of titanium dioxide dynamic membranes in microfiltration of oil-in-water emulsions[J]. Separation and Purification Technology, 2012, 89(1):78-83.[10] Li Na, Liu Zhongzhou, Xu Shuguang. Dynamically formed poly(vinyl alcohol) ultrafiltration membranes with good anti-fouling characteristics[J]. Journal Membrance Science, 2000, 169(1): 17-28.[11] 卓琳云,李俊,陈季华,等. 高岭土动态膜的制备[J]. 膜科学与技术, 2006, 26(3): 37-40.[12] 叶世威,王贝辉,洪昱斌,等. 碳化硅陶瓷膜在油水分离中的应用研究[J]. 功能材料,2011,42(2):248-251.。
油水乳化液分离技术

油水乳化液分离技术(总1页)-CAL-FENGHAI.-(YICAI)-Company One1-CAL-本页仅作为文档封面,使用请直接删除油水乳化液分离技术电絮凝处理含油废水:在外电压作用下,利用可溶性阳极(铁或铝)产生大量阳离子,对胶体废水进行凝聚,同时在阴极上析出大量氢气微气泡,与絮粒粘附在一起上浮。
这种方法称为电凝聚电气浮。
它是基于下面的基本电化学反应。
当电极上通直流电时,电极反应如下。
阳极:阴极:在阳极产生的氧气泡和在阴极产生的氢气泡能吸附废水中的絮凝物,发生上浮现象,以除去废水中的油。
而且阳极产生初生态的[o]非常活泼,可氧化水中的污染物,处理效果比较好。
也就是说这种电解除油法是气浮法。
离心法:该法是指借助离心机械所产生的离心力,将油水分离。
离心机有卧式和立式两种。
在离心力的作用下,水相从离心机的外层排出,油相从离心机的中部排出。
膜分离:含油污水是一种较常见的污染源,其中的乳化油污水是最难分离的一类,常规的分离方法不能有效地将其处理以达到环保排放要求或处理时的能耗较大。
膜分离方法能克服常规分离方法的不足,可有效地处理乳化油污水。
乳化油的膜法分离属于超滤、微滤范围,膜的抗污染和渗透性能的高低是制约其分离效果的重要因素。
常规的乳化油污水为水包油型乳化液,所以亲水性膜对乳化油污水处理时具有抗污染能力更强、分离效果更佳的特点。
动态膜技术作为一种膜改性手段,可利用在非亲水的载体上形成的亲水性动态膜作为液体分离层,其在液体分离方面的应用越来越受到研究者的重视。
动态膜在油水乳化液分离方面研究的最早报道是在上世纪七十年代初期,研究者用 Union Carbide 开发的 ZrO2 动态膜(UCARSEP)超滤含油废水,发现透过液中含极少量的油,可以直接排放或再利用,浓缩的油可以循环或作燃料。
Cai 等用制备的 MnO2 动态膜处理硅藻土矿石废水和油精炼厂废水,发现动态膜性能稳定、浊度去除率高达 98%。
提高分离系统的分离效果

提高分离系统的分离效果提高分离系统的分离效果是化工领域中一个非常重要的课题,它直接关系到工艺的经济性、产品的质量、设备的稳定性等多个方面。
分离系统的分离效果主要受到操作条件、设备结构、物性参数等因素的影响。
本文将从这些方面着手,探讨如何提高分离系统的分离效果。
一、优化操作条件1. 温度控制温度是影响分离效果的重要因素之一,对于液体-液体、液体-气体、固体-液体等不同类型的分离系统,其最佳操作温度都是不同的。
一般来说,适当升高温度能够提高分离效果,但是过高的温度也会导致组分的热解、挥发等问题。
在实际操作中,需要进行温度的精准控制,确保在适合的温度范围内进行操作。
2. 压力控制对于气体-液体分离系统而言,压力是一个非常重要的参数,它直接影响着气体的溶解度和液体的汽化性质。
通过调节操作压力,可以改变分离系统中气体和液体的分配情况,从而实现优化分离效果的目的。
3. 搅拌速度在液液分离系统中,搅拌速度会直接影响相的分散程度和传质速率,从而影响相的分离效果。
合理的搅拌速度可以加快相间传质过程,提高分离效率,但是过高的搅拌速度也会带来悬浮物的再分散和泡沫的生成等问题。
需要通过实验和模拟等手段确定最佳的搅拌速度。
二、优化设备结构1. 分离设备对于不同类型的分离系统,需要选择合适的分离设备。
对于固液分离系统,可以选择离心机、过滤机等设备;对于液液分离系统,可以选择萃取塔、萃取器等设备。
还可以通过改良设备的结构,增加板片数量、改进分流装置等方式来提高设备的分离效果。
2. 设备配套在分离系统中,还需要考虑设备的配套性能,例如泵、阀门、管道等。
这些配套设备的性能会直接影响到分离系统的运行效果,因此需要选用性能稳定、操作方便的设备,并且保持设备的良好状态,以确保分离系统能够持续稳定地运行。
三、优化物性参数1. 质量浓度对于液液、气液等分离系统,组分之间的质量浓度差异是实现分离的基础。
在实际操作中,需要通过调节进料浓度、溶剂浓度等方式,控制组分的质量浓度,从而实现更好的分离效果。
膜分离过程的优化与控制方法研究的开题报告

膜分离过程的优化与控制方法研究的开题报告一、研究背景膜分离技术是目前应用最广泛的一种分离技术,具有分离效率高、能耗低、操作简单等特点,已广泛应用于水处理、食品加工、药品制造等领域。
然而,膜分离过程中一些问题,如膜污染、通量下降、选择性不足等,限制了其应用范围和效果,因此需要对其优化与控制方法进行研究,以提高膜分离的效率和可靠性。
二、研究目的和意义本研究旨在通过实验和理论分析,探索膜分离过程的优化和控制方法,以提高膜分离工艺的经济效益和环境效益。
具体目的如下:1. 研究膜分离过程中常见的问题,如膜污染、通量下降、选择性不足等的发生机理和控制方法;2. 优化膜分离工艺中的操作条件,如加压、压力、温度、流速等参数的控制;3. 针对特定的膜分离过程,设计最优的控制方案,以提高膜分离工艺的效率和稳定性。
通过上述研究,可为膜分离技术的应用提供一定的理论和实践指导,同时,也有助于推动膜分离技术的发展和应用。
三、研究内容和方法本研究主要从以下几个方面展开:1. 膜性能测试:通过实验测定不同材料的膜的性能指标,包括透过率、分离效率、膜通量、膜阻力等;2. 膜分离的机理与问题分析:通过对膜分离过程中的关键参数进行监测和分析,确定其发生机理和影响因素;3. 优化膜分离工艺的操作条件:通过改变膜分离工艺中的操作条件,如加压、压力、温度、流速等参数,探索最优的操作条件,以提高膜分离过程的效率和稳定性;4. 膜分离过程的控制方案设计:针对特定的膜分离工艺,设计最佳的控制方案,以实现膜分离工艺的自动化和智能化。
本研究采用实验方法和理论分析相结合的方式进行研究,通过搭建实验平台、开展实验测试和数据分析等手段,获取相应的研究数据和结论,同时,还将借助计算机辅助设计软件,对研究结果进行模拟和优化。
四、预期结果与成果通过本次研究,预计可取得以下成果:1. 获得一定的膜性能测试数据和分析结果,提供膜材料选择和工艺流程设计的参考依据;2. 探索了膜分离工艺中的关键参数和控制方法,优化了膜分离过程中的操作条件,提高了工艺效率和稳定性;3. 针对特定的膜分离工艺,设计了智能化的控制方案,实现了膜分离过程的自动化和智能化;4. 上述成果将以论文、专利等形式向学术界和工业界发布,为膜分离技术应用和推广提供一定的理论和实践指导。
- 1、下载文档前请自行甄别文档内容的完整性,平台不提供额外的编辑、内容补充、找答案等附加服务。
- 2、"仅部分预览"的文档,不可在线预览部分如存在完整性等问题,可反馈申请退款(可完整预览的文档不适用该条件!)。
- 3、如文档侵犯您的权益,请联系客服反馈,我们会尽快为您处理(人工客服工作时间:9:00-18:30)。
Pr o c e s s Op t i mi z a t i o n a nd Cha r a c t e r i z a t i o n o f Oi l — - i n — - Wa t e r Emul s i o n S e pa r a t i o n wi t h
T e c h n o l o g y , D a l i a n Un i v e r s i t y o f T e c h n o l o g y , Da l i a n 1 1 6 0 2 4 , C h i n a )
Abs t r a c t : Mi c r of il t r a t i o n of o i l — - i n . . wa t e r e mul wi t h c e r a mi c t ub e s u p p o r t e d z i r c o n i u m
a na l y z e d .Re s ul t s s h o w t h a t t h e o p t i ma l mi c r o ii f t r a t i o n c o n d i t i o n s a r e :e m ul s i o n c o n c e n t r a t i on 0. 5 g . L~,f lo w
摘 要 :用陶瓷膜基二氧化锆 动态膜分离水包 油型乳化液 ,利用 正交 实验方法优化 分离操作条件 ,并考 察压 力、乳化
液温度 、乳化液 D H 值和溶液中盐离子 种类 四大因素分别对过程 的影响 。正交 实验 结果表明 ,油水分离 最优条件为 : 乳化液浓 度 O . 5 g . L - 。 、乳化液 p H值为 5 、温度 5 0  ̄ C、流量 i 0 0 L . h - 、压力 O . 1 4 MP a 。单因素实验结 果表明,随压力
c o nd i t i o ns , a n d f a c t o r s s uc h a s t e mpe r a t u r e ,p H,s a l t i o n s p e c i e s o f t h e e mu l s i o n a n d o p e r a t i n g p r e s s u r e we r e
i n c r e a s e o f p r e s s re u u n t i l 0. 1 4 M Pa ,wh i c h r e ma i n s c o ns t a n t a f t e r wa r d s .M o r e o ve r ,t h e lu f x i n c r e a s e s i f r s t a nd
d i o x i d e( Z r O 2 )d y n a m i c me m b r a n e s . Or t h o g o n a l e x p e r i me n t a l d e s i g n w a s e mp l o y e d t o o p t i mi z e o p e r a t i n g
第2 9 卷第 5 期 2 0 1 5 年1 0月
高
校
化
学
工
程
学
报
No . 5 、 b1 . 2 9 Oc t . 2 01 5
J o u r n a l o f Che mi c a l En g i n e e r i n g o fChi ne s e Un i v e r s i t i e s
Dy na mi c M e m br a n e s
WA NG We n - j u a n ,Z HA O H a o — b a n ,P A N Y a n - q i u
( De p a r t me n t o f C h e mi c a l E n g i n e e r i n g , F a c u l t y o f C h e mi c a l , E n v i r o n me n t a l a n d Bi o l o g i c a l S c i e n c e a n d
r a t e 1 0 0 L・ h ~ a nd o p e r a t i n g p r e s s u r e 0. 1 4 MP a u n de r 5 0℃ .Th e s t e a d y p e r me a t e lu f x i nc r e a s e s wi t h t h e
文章编 号 :1 0 0 3 — 9 0 1 5 ( 2 0 1 5 ) 0 5 — 1 0 4 5 — 0 8
动态膜 分离油水乳化液操作条件 优化和影 响因素分析
王 文 娟 , 赵 昊瀚 , 潘 艳 秋
( 大连理工 大学 化 工与环境生命 学部 化工学 院,辽 宁 大连 1 1 6 0 2 4 )
增大 ,油水分离稳定渗透通量 增大 ,但是 当压 力大 于 O . 1 4 MP a 后 ,通量 几乎无变化 ;随油水 乳化液温度和 D H值的升
高,稳定渗透通量先增 大后减 小;考察 乳化 液中加入盐离子 的结 果发现 ,阳 离子 盐的渗透通量大于 阴离子盐的通量 , 并且 阳离子 电荷越 多或 阴离子 电荷越少 ,通 量越大 运用浓差极 化、双 电层和乳化 液破乳等理论可 以对以上实验现象 做 出合 理解释 关键 词:动态膜 ;微滤 ;油水乳化液 ;正交实验;优化 中图分类号 :T Q0 2 8 . 8 文献标 识码:A DO I :1 0 . 3 9 6 9  ̄ . i s s n . 1 0 0 3 — 9 0 1 5 . 2 0 1 5 . 0 5 . 0 0 4