header for SPIE use MIRAGE read-in-integrated-circuit testing results
flutter sticky header 原理

flutter sticky header 原理
Flutter中的Sticky Headers是一个强大的插件,它允许开发者在滚动内容中添加粘性头部组件。
这个组件通常用于在滚动列表中固定某些头部元素,以便用户可以轻松地找到和访问这些元素,而不必滚动整个列表。
Sticky Headers的工作原理主要依赖于Flutter的自定义滚动行为。
它通过修改滚动容器的子节点,使得头部元素在滚动时能够停留在屏幕的顶部,从而实现了粘性效果。
具体来说,Sticky Headers在滚动内容中添加了一个额外的固定区域,用于放置头部元素。
当用户开始滚动时,Sticky Headers会检测头部元素的位置,并在适当的时候将其固定在屏幕顶部。
同时,它还会调整其他滚动内容的布局,以适应头部元素的固定位置。
为了实现这个效果,Sticky Headers需要与Flutter的布局系统进行紧密的配合。
它需要监听滚动事件,并根据滚动位置动态调整布局。
此外,它还需要处理滚动容器的子节点,以便在头部元素被固定时隐藏其他内容。
通过使用Sticky Headers,开发者可以轻松地实现粘性头部效果,从而改善用户体验。
用户可以更方便地访问列表中的重要元素,而无需频繁滚动屏幕。
这不仅可以提高应用程序的易用性,还可以增强应用程序的视觉效果和吸引力。
总之,Sticky Headers是Flutter中一个非常有用的插件,它通过修改滚动容器的子节点和监听滚动事件,实现了粘性头部效果。
这个效果可以提高应用程序的用户体验和吸引力,是移动应用程序开发中常用的技术之一。
HP Color LaserJet Enterprise MFP M776用户指南说明书
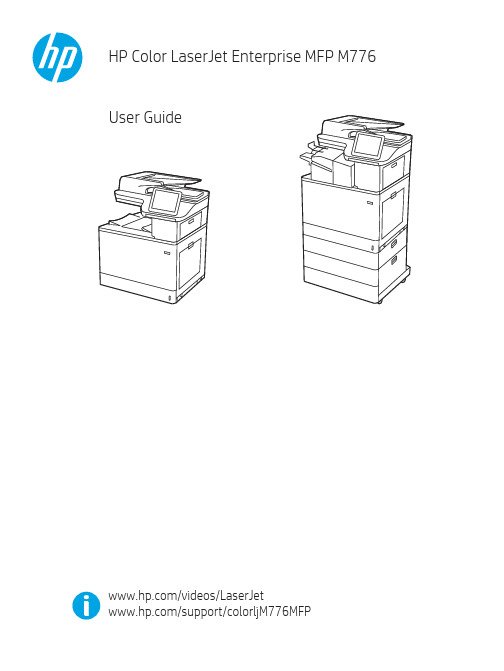
Legal informationCopyright and License© Copyright 2019 HP Development Company, L.P.Reproduction, adaptation, or translation without prior written permission is prohibited, except as allowedunder the copyright laws.The information contained herein is subject to change without notice.The only warranties for HP products and services are set forth in the express warranty statementsaccompanying such products and services. Nothing herein should be construed as constituting anadditional warranty. HP shall not be liable for technical or editorial errors or omissions contained herein.Edition 1, 10/2019Trademark CreditsAdobe®, Adobe Photoshop®, Acrobat®, and PostScript® are trademarks of Adobe Systems Incorporated.Apple and the Apple logo are trademarks of Apple Inc., registered in the U.S. and other countries.macOS is a trademark of Apple Inc., registered in the U.S. and other countries.AirPrint is a trademark of Apple Inc., registered in the U.S. and other countries.Google™ is a trademark of Google Inc.Microsoft®, Windows®, Windows® XP, and Windows Vista® are U.S. registered trademarks of MicrosoftCorporation.UNIX® is a registered trademark of The Open Group.iiiT able of contents1 Printer overview (1)Warning icons (1)Potential shock hazard (2)Printer views (2)Printer front view (2)Printer back view (4)Interface ports (4)Control-panel view (5)How to use the touchscreen control panel (7)Printer specifications (8)T echnical specifications (8)Supported operating systems (11)Mobile printing solutions (12)Printer dimensions (13)Power consumption, electrical specifications, and acoustic emissions (15)Operating-environment range (15)Printer hardware setup and software installation (16)2 Paper trays (17)Introduction (17)Load paper to Tray 1 (multipurpose tray) (17)Load Tray 1 (multipurpose tray) (18)Tray 1 paper orientation (19)Use alternative letterhead mode (24)Enable Alternative Letterhead Mode by using the printer control-panel menus (24)Load paper to Tray 2 (24)Load Tray 2 (24)Tray 2 paper orientation (26)Use alternative letterhead mode (29)Enable Alternative Letterhead Mode by using the printer control-panel menus (29)Load paper to the 550-sheet paper tray (30)Load paper to the 550-sheet paper tray (30)550-sheet paper tray paper orientation (32)Use alternative letterhead mode (35)Enable Alternative Letterhead Mode by using the printer control-panel menus (35)ivLoad paper to the 2 x 550-sheet paper trays (36)Load paper to the 2 x 550-sheet paper trays (36)2 x 550-sheet paper tray paper orientation (38)Use alternative letterhead mode (41)Enable Alternative Letterhead Mode by using the printer control-panel menus (41)Load paper to the 2,700-sheet high-capacity input paper trays (41)Load paper to the 2,700-sheet high-capacity input paper trays (41)2,700-sheet HCI paper tray paper orientation (43)Use alternative letterhead mode (45)Enable Alternative Letterhead Mode by using the printer control-panel menus (45)Load and print envelopes (46)Print envelopes (46)Envelope orientation (46)Load and print labels (47)Manually feed labels (47)Label orientation (48)3 Supplies, accessories, and parts (49)Order supplies, accessories, and parts (49)Ordering (49)Supplies and accessories (50)Maintenance/long-life consumables (51)Customer self-repair parts (51)Dynamic security (52)Configure the HP toner-cartridge-protection supply settings (53)Introduction (53)Enable or disable the Cartridge Policy feature (53)Use the printer control panel to enable the Cartridge Policy feature (54)Use the printer control panel to disable the Cartridge Policy feature (54)Use the HP Embedded Web Server (EWS) to enable the Cartridge Policy feature (54)Use the HP Embedded Web Server (EWS) to disable the Cartridge Policy feature (55)Troubleshoot Cartridge Policy control panel error messages (55)Enable or disable the Cartridge Protection feature (55)Use the printer control panel to enable the Cartridge Protection feature (56)Use the printer control panel to disable the Cartridge Protection feature (56)Use the HP Embedded Web Server (EWS) to enable the Cartridge Protection feature (56)Use the HP Embedded Web Server (EWS) to disable the Cartridge Protection feature (57)Troubleshoot Cartridge Protection control panel error messages (57)Replace the toner cartridges (58)T oner-cartridge information (58)Remove and replace the cartridges (59)Replace the imaging drums (62)Imaging drum information (62)Remove and replace the imaging drums (63)Replace the toner-collection unit (66)T oner-collection unit information (66)vRemove and replace the toner-collection unit (67)Replace the staple cartridge (M776zs model only) (70)Staple cartridge information (70)Remove and replace the staple cartridge (71)4 Print (73)Print tasks (Windows) (73)How to print (Windows) (73)Automatically print on both sides (Windows) (74)Manually print on both sides (Windows) (74)Print multiple pages per sheet (Windows) (75)Select the paper type (Windows) (75)Additional print tasks (76)Print tasks (macOS) (77)How to print (macOS) (77)Automatically print on both sides (macOS) (77)Manually print on both sides (macOS) (77)Print multiple pages per sheet (macOS) (78)Select the paper type (macOS) (78)Additional print tasks (79)Store print jobs on the printer to print later or print privately (79)Introduction (79)Create a stored job (Windows) (79)Create a stored job (macOS) (80)Print a stored job (81)Delete a stored job (81)Delete a job that is stored on the printer (81)Change the job storage limit (82)Information sent to printer for Job Accounting purposes (82)Mobile printing (82)Introduction (82)Wi-Fi, Wi-Fi Direct Print, NFC, and BLE printing (82)Enable wireless printing (83)Change the Wi-Fi Direct name (83)HP ePrint via email (83)AirPrint (84)Android embedded printing (85)Print from a USB flash drive (85)Enable the USB port for printing (85)Method one: Enable the USB port from the printer control panel (85)Method two: Enable the USB port from the HP Embedded Web Server (network-connectedprinters only) (85)Print USB documents (86)Print using high-speed USB 2.0 port (wired) (86)Method one: Enable the high-speed USB 2.0 port from the printer control panel menus (86)Method two: Enable the high-speed USB 2.0 port from the HP Embedded Web Server (network-connected printers only) (87)vi5 Copy (88)Make a copy (88)Copy on both sides (duplex) (90)Additional copy tasks (92)6 Scan (93)Set up Scan to Email (93)Introduction (93)Before you begin (93)Step one: Access the HP Embedded Web Server (EWS) (94)Step two: Configure the Network Identification settings (95)Step three: Configure the Send to Email feature (96)Method one: Basic configuration using the Email Setup Wizard (96)Method two: Advanced configuration using the Email Setup (100)Step four: Configure the Quick Sets (optional) (104)Step five: Set up Send to Email to use Office 365 Outlook (optional) (105)Introduction (105)Configure the outgoing email server (SMTP) to send an email from an Office 365 Outlookaccount (105)Set up Scan to Network Folder (108)Introduction (108)Before you begin (108)Step one: Access the HP Embedded Web Server (EWS) (108)Step two: Set up Scan to Network Folder (109)Method one: Use the Scan to Network Folder Wizard (109)Method two: Use Scan to Network Folder Setup (110)Step one: Begin the configuration (110)Step two: Configure the Scan to Network Folder settings (111)Step three: Complete the configuration (118)Set up Scan to SharePoint (118)Introduction (118)Before you begin (118)Step one: Access the HP Embedded Web Server (EWS) (118)Step two: Enable Scan to SharePoint and create a Scan to SharePoint Quick Set (119)Scan a file directly to a SharePoint site (121)Quick Set scan settings and options for Scan to SharePoint (122)Set up Scan to USB Drive (123)Introduction (124)Step one: Access the HP Embedded Web Server (EWS) (124)Step two: Enable Scan to USB Drive (124)Step three: Configure the Quick Sets (optional) (125)Default scan settings for Scan to USB Drive setup (126)Default file settings for Save to USB setup (126)Scan to email (127)Introduction (127)Scan to email (127)Scan to job storage (129)viiIntroduction (129)Scan to job storage on the printer (130)Print from job storage on the printer (132)Scan to network folder (132)Introduction (132)Scan to network folder (132)Scan to SharePoint (134)Introduction (134)Scan to SharePoint (134)Scan to USB drive (136)Introduction (136)Scan to USB drive (136)Use HP JetAdvantage business solutions (138)Additional scan tasks (138)7 Fax (140)Set up fax (140)Introduction (140)Set up fax by using the printer control panel (140)Change fax configurations (141)Fax dialing settings (141)General fax send settings (142)Fax receive settings (143)Send a fax (144)Additional fax tasks (146)8 Manage the printer (147)Advanced configuration with the HP Embedded Web Server (EWS) (147)Introduction (147)How to access the HP Embedded Web Server (EWS) (148)HP Embedded Web Server features (149)Information tab (149)General tab (149)Copy/Print tab (150)Scan/Digital Send tab (151)Fax tab (152)Supplies tab (153)Troubleshooting tab (153)Security tab (153)HP Web Services tab (154)Networking tab (154)Other Links list (156)Configure IP network settings (157)Printer sharing disclaimer (157)View or change network settings (157)Rename the printer on a network (157)viiiManually configure IPv4 TCP/IP parameters from the control panel (158)Manually configure IPv6 TCP/IP parameters from the control panel (158)Link speed and duplex settings (159)Printer security features (160)Introduction (160)Security statements (160)Assign an administrator password (160)Use the HP Embedded Web Server (EWS) to set the password (160)Provide user access credentials at the printer control panel (161)IP Security (161)Encryption support: HP High Performance Secure Hard Disks (161)Lock the formatter (161)Energy-conservation settings (161)Set the sleep timer and configure the printer to use 1 watt or less of power (161)Set the sleep schedule (162)Set the idle settings (162)HP Web Jetadmin (163)Software and firmware updates (163)9 Solve problems (164)Customer support (164)Control panel help system (165)Reset factory settings (165)Introduction (165)Method one: Reset factory settings from the printer control panel (165)Method two: Reset factory settings from the HP Embedded Web Server (network-connectedprinters only) (166)A “Cartridge is low” or “Cartridge is very low” message displays on the printer control panel (166)Change the “Very Low” settings (166)Change the “Very Low” settings at the control panel (166)For printers with fax capability (167)Order supplies (167)Printer does not pick up paper or misfeeds (167)Introduction (167)The printer does not pick up paper (167)The printer picks up multiple sheets of paper (171)The document feeder jams, skews, or picks up multiple sheets of paper (174)Clear paper jams (174)Introduction (174)Paper jam locations (174)Auto-navigation for clearing paper jams (175)Experiencing frequent or recurring paper jams? (175)Clear paper jams in the document feeder - 31.13.yz (176)Clear paper jams in Tray 1 (13.A1) (177)Clear paper jams in Tray 2 (13.A2) (182)Clear paper jams in the fuser (13.B9, 13.B2, 13.FF) (188)ixClear paper jams in the duplex area (13.D3) (194)Clear paper jams in the 550-sheet trays (13.A3, 13.A4) (199)Clear paper jams in the 2 x 550 paper trays (13.A4, 13.A5) (206)Clear paper jams in the 2,700-sheet high-capacity input paper trays (13.A3, 13.A4, 13.A5, 13.A7) (213)Resolving color print quality problems (220)Introduction (220)Troubleshoot print quality (221)Update the printer firmware (221)Print from a different software program (221)Check the paper-type setting for the print job (221)Check the paper type setting on the printer (221)Check the paper type setting (Windows) (221)Check the paper type setting (macOS) (222)Check toner-cartridge status (222)Step one: Print the Supplies Status Page (222)Step two: Check supplies status (222)Print a cleaning page (222)Visually inspect the toner cartridge or cartridges (223)Check paper and the printing environment (223)Step one: Use paper that meets HP specifications (223)Step two: Check the environment (223)Step three: Set the individual tray alignment (224)Try a different print driver (224)Troubleshoot color quality (225)Calibrate the printer to align the colors (225)Troubleshoot image defects (225)Improve copy image quality (233)Check the scanner glass for dirt and smudges (233)Calibrate the scanner (234)Check the paper settings (235)Check the paper selection options (235)Check the image-adjustment settings (235)Optimize copy quality for text or pictures (236)Edge-to-edge copying (236)Improve scan image quality (236)Check the scanner glass for dirt and smudges (237)Check the resolution settings (238)Check the color settings (238)Check the image-adjustment settings (239)Optimize scan quality for text or pictures (239)Check the output-quality settings (240)Improve fax image quality (240)Check the scanner glass for dirt and smudges (240)Check the send-fax resolution settings (242)Check the image-adjustment settings (242)Optimize fax quality for text or pictures (242)Check the error-correction setting (243)xSend to a different fax machine (243)Check the sender's fax machine (243)Solve wired network problems (244)Introduction (244)Poor physical connection (244)The computer is unable to communicate with the printer (244)The printer is using incorrect link and duplex settings for the network (245)New software programs might be causing compatibility problems (245)The computer or workstation might be set up incorrectly (245)The printer is disabled, or other network settings are incorrect (245)Solve wireless network problems (245)Introduction (245)Wireless connectivity checklist (245)The printer does not print after the wireless configuration completes (246)The printer does not print, and the computer has a third-party firewall installed (246)The wireless connection does not work after moving the wireless router or printer (247)Cannot connect more computers to the wireless printer (247)The wireless printer loses communication when connected to a VPN (247)The network does not appear in the wireless networks list (247)The wireless network is not functioning (247)Reduce interference on a wireless network (248)Solve fax problems (248)Checklist for solving fax problems (248)What type of phone line are you using? (249)Are you using a surge-protection device? (249)Are you using a phone company voice-messaging service or an answering machine? (249)Does your phone line have a call-waiting feature? (249)Check fax accessory status (249)General fax problems (250)The fax failed to send (250)No fax address book button displays (250)Not able to locate the Fax settings in HP Web Jetadmin (250)The header is appended to the top of the page when the overlay option is enabled (251)A mix of names and numbers is in the recipients box (251)A one-page fax prints as two pages (251)A document stops in the document feeder in the middle of faxing (251)The volume for sounds coming from the fax accessory is too high or too low (251)Index (252)xiPrinter overview1Review the location of features on the printer, the physical and technical specifications of the printer,and where to locate setup information.For video assistance, see /videos/LaserJet.The following information is correct at the time of publication. For current information, see /support/colorljM776MFP.For more information:HP's all-inclusive help for the printer includes the following information:●Install and configure●Learn and use●Solve problems●Download software and firmware updates●Join support forums●Find warranty and regulatory informationWarning iconsUse caution if you see a warning icon on your HP printer, as indicated in the icon definitions.●Caution: Electric shock●Caution: Hot surface●Caution: Keep body parts away from moving partsPrinter overview1●Caution: Sharp edge in close proximity●WarningPotential shock hazardReview this important safety information.●Read and understand these safety statements to avoid an electrical shock hazard.●Always follow basic safety precautions when using this product to reduce risk of injury from fire orelectric shock.●Read and understand all instructions in the user guide.●Observe all warnings and instructions marked on the product.●Use only a grounded electrical outlet when connecting the product to a power source. If you do notknow whether the outlet is grounded, check with a qualified electrician.●Do not touch the contacts on any of the sockets on the product. Replace damaged cordsimmediately.●Unplug this product from wall outlets before cleaning.●Do not install or use this product near water or when you are wet.●Install the product securely on a stable surface.●Install the product in a protected location where no one can step on or trip over the power cord.Printer viewsIdentify certain parts of the printer and the control panel.Printer front viewLocate features on the front of the printer.2Chapter 1 Printer overviewPrinter front view3Printer back viewLocate features on the back of the printer.Interface portsLocate the interface ports on the printer formatter. 4Chapter 1 Printer overviewControl-panel viewThe control panel provides access to the printer features and indicates the current status of the printer.NOTE:Tilt the control panel for easier viewing.The Home screen provides access to the printer features and indicates the current status of the printer.screens.NOTE:The features that appear on the Home screen can vary, depending on the printerconfiguration.Control-panel view5Figure 1-1Control-panel view?i 12:42 PM6Chapter 1 Printer overviewHow to use the touchscreen control panelPerform the following actions to use the printer touchscreen control panel.T ouchT ouch an item on the screen to select that item or open that menu. Also, when scrolling T ouch the Settings icon to open the Settings app.How to use the touchscreen control panel 7SwipeT ouch the screen and then move your finger horizontally to scroll the screen sideways.Swipe until the Settings app displays.Printer specificationsDetermine the specifications for your printer model.IMPORTANT:The following specifications are correct at the time of publication, but they are subject to change. For current information, see /support/colorljM776MFP .T echnical specificationsReview the printer technical specifications.Product numbers for each model ●M776dn - #T3U55A ●Flow M776z - #3WT91A ●Flow M776zs - #T3U56APaper handling specificationsPaper handling features Tray 1 (100-sheet capacity)Included Included Included Tray 2 (550-sheet capacity)IncludedIncludedIncluded8Chapter 1 Printer overview550-sheet paper trayOptional Included Not included NOTE:The M776dn models accept one optional550-sheet tray.Optional Included Included2 x 550-sheet paper tray and standNOTE:The M776dn models accept one optional550-sheet tray that may be installed on top of thestand.Optional Not included Not included2,700-sheet high-capacity input (HCI) paper trayand standNOTE:The M776dn models accept one optional550-sheet tray that may be installed on top of theoptional printer stand.Printer standOptional Not included Not included NOTE:The M776dn models accept one optional550-sheet tray that may be installed on top of theoptional printer stand.Inner finisher accessory Not included Not included Included Automatic duplex printing Included IncludedIncludedIncluded Included Included10/100/1000 Ethernet LAN connection with IPv4and IPv6Hi-Speed USB 2.0Included Included IncludedIncluded Included IncludedEasy-access USB port for printing from a USBflash drive or upgrading the firmwareIncluded Included Included Hardware Integration Pocket for connectingaccessory and third-party devicesHP Internal USB Ports Optional Optional OptionalOptional Optional OptionalHP Jetdirect 2900nw Print Server accessory forWi-Fi connectivity and an additional Ethernet portOptional IncludedIncludedHP Jetdirect 3100w accessory for Wi-Fi, BLE, NFC,and proximity badge readingPrints 45 pages per minute (ppm) on Letter-sizepaper and 46 ppm on A4-size paperEasy-access USB printing for printing from a USBIncluded Included Includedflash driveT echnical specifications9Included Included Included Store jobs in the printer memory to print later orprint privatelyScans 100 pages per minute (ppm) on A4 andIncluded Included Included letter-size paper one-sidedIncluded Included Included 200-page document feeder with dual-headscanning for single-pass duplex copying andscanningNot included Included Included HP EveryPage T echnologies including ultrasonicmulti-feed detectionNot included Included Included Embedded optical character recognition (OCR)provides the ability to convert printed pages intotext that can be edited or searched using acomputerIncluded Included Included SMART Label feature provides paper-edgedetection for automatic page croppingIncluded Included Included Automatic page orientation for pages that haveat least 100 characters of textIncluded Automatic tone adjustment sets contrast,Included Includedbrightness, and background removal for eachpageIncluded Included Includedfolders on a networkIncludedSend documents to SharePoint®Included IncludedIncluded Included Included NOTE:Memory reported on the configurationpage will change from 2.5 GB to 3 GB with theoptional 1 GB SODIMM installed.Mass storage: 500 GB hard disk drive Included Included IncludedSecurity: HP Trusted Platform Module (TPM)Included Included IncludedT ouchscreen control panel Included Included IncludedRetractable keyboard Not included Included Included 10Chapter 1 Printer overviewFax Optional Included IncludedSupported operating systemsUse the following information to ensure printer compatibility with your computer operating system.Linux: For information and print drivers for Linux, go to /go/linuxprinting.UNIX: For information and print drivers for UNIX®, go to /go/unixmodelscripts.The following information applies to the printer-specific Windows HP PCL 6 print drivers, HP print driversfor macOS, and to the software installer.Windows: Download HP Easy Start from /LaserJet to install the HP print driver. Or, go tothe printer-support website for this printer: /support/colorljM776MFP to download the printdriver or the software installer to install the HP print driver.macOS: Mac computers are supported with this printer. Download HP Easy Start either from /LaserJet or from the Printer Support page, and then use HP Easy Start to install the HP print driver.1.Go to /LaserJet.2.Follow the steps provided to download the printer software.Windows 7, 32-bit and 64-bit The “HP PCL 6” printer-specific print driver is installed for this operating system aspart of the software installation.Windows 8.1, 32-bit and 64-bit The “HP PCL-6” V4 printer-specific print driver is installed for this operating systemas part of the software installation.Windows 10, 32-bit and 64-bit The “HP PCL-6” V4 printer-specific print driver is installed for this operating systemas part of the software installation.Windows Server 2008 R2, SP 1, 64-bit The PCL 6 printer-specific print driver is available for download from the printer-support website. Download the driver, and then use the Microsoft Add Printer tool toinstall it.Windows Server 2012, 64-bit The PCL 6 printer-specific print driver is available for download from the printer-support website. Download the driver, and then use the Microsoft Add Printer tool toinstall it.Windows Server 2012 R2, 64-bit The PCL 6 printer-specific print driver is available for download from the printer-support website. Download the driver, and then use the Microsoft Add Printer tool toinstall it.Windows Server 2016, 64-bit The PCL 6 printer-specific print driver is available for download from the printer-support website. Download the driver, and then use the Microsoft Add Printer tool toinstall it.Windows Server 2019, 64-bit The PCL 6 printer-specific print driver is available for download from the printer-support website. Download the driver, and then use the Microsoft Add Printer tool toinstall it.Supported operating systems11macOS 10.13 High Sierra, macOS 10.14 MojaveDownload HP Easy Start from /LaserJet , and then use it to install the print driver.NOTE:Supported operating systems can change.NOTE:For a current list of supported operating systems and HP’s all-inclusive help for the printer, go to /support/colorljM776MFP .NOTE:For details on client and server operating systems and for HP UPD driver support for this printer, go to /go/upd . Under Additional information , click Specifications .●Internet connection●Dedicated USB 1.1 or 2.0 connection or a network connection● 2 GB of available hard-disk space ●1 GB RAM (32-bit) or2 GB RAM (64-bit)●Internet connection●Dedicated USB 1.1 or 2.0 connection or a network connection●1.5 GB of available hard-disk spaceNOTE:The Windows software installer installs the HP Smart Device Agent Base service. The file size is less than 100 kb. Its only function is to check for printers connected via USB hourly. No data is collected. If a USB printer is found, it then tries to locate a JetAdvantage Management Connector (JAMc) instance on the network. If a JAMc is found, the HP Smart Device Agent Base is securelyupgraded to a full Smart Device Agent from JAMc, which will then allow printed pages to be accounted for in a Managed Print Services (MPS) account. The driver-only web packs downloaded from for the printer and installed through the Add Printer wizard do not install this service.T o uninstall the service, open the Control Panel , select Programs or Programs and Features , and then select Add/Remove Programs or Uninstall a Programto remove the service. The file name isHPSmartDeviceAgentBase.Mobile printing solutionsHP offers multiple mobile printing solutions to enable easy printing to an HP printer from a laptop, tablet, smartphone, or other mobile device.T o see the full list and to determine the best choice, go to /go/MobilePrinting .NOTE:Update the printer firmware to ensure all mobile printing capabilities are supported.●Wi-Fi Direct (wireless models only, with HP Jetdirect 3100w BLE/NFC/Wireless accessory installed)●HP ePrint via email (Requires HP Web Services to be enabled and the printer to be registered with HP Connected)●HP Smart app ●Google Cloud Print12Chapter 1 Printer overview。
Arduino编程参考手册中文版(带目录适合打印)
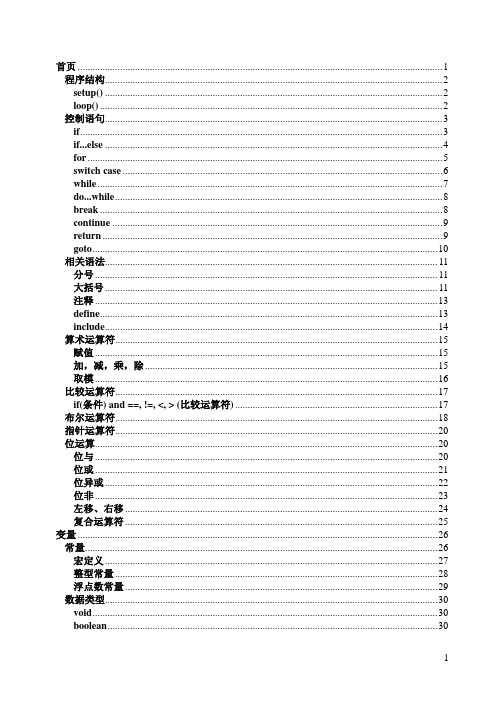
! (逻辑非)
指针运算符
* 指针运算符
& 地址运算符
位运算
& (位与)
| (位或)
^ (位异或)
~ (位非)
<< (左移)
>> (右移)
复合运算符
++ (自加)
-- (自减)
+= (复合加)
-= (复合减)
*= (复合乘)
/= (复合除)
&= (复合与)
|= (复合或)
范围
HIGH | LOW
int checkSensor(){
if (analogRead(0) > 400) {
return 1;
else{
return 0;
}
}
return关键字对测试一段代码很方便,不需“注释掉”大段的可能是错误的代码。
void loop(){
//在此测试代码是个好想法
return;
// 这里是功能不正常的代码
for
for语句
描述
for语句用于重复执行被花括号包围的语句块。一个增量计数器通常被用来递增和终止循环。for语句对于任何需要重复的操作是非常有用的。常常用于与数组联合使用以收集数据/引脚。for循环的头部有三个部分:
for (初始化部分; 条件判断部分; 数据递增部分) {
//语句块
。。。
}
初始化部分被第一个执行,且只执行一次。每次通过这个循环,条件判断部分将被测试;如果为真,语句块和数据递增部分就会被执行,然后条件判断部分就会被再次测试,当条件测试为假时,结束循环。
示例:
for (x = 0; x < 255; x ++)
eclipse报错eclipse启动报错解决方法

eclipse报错eclipse启动报错解决⽅法Version 1.4.2_03 of the JVM not suitable for this product.Version1.5 or geeater is required⼤概意思好像说我的JVM虚拟机的环境 1.4版本过低,让我⽤1.5版本以上的,很疑惑。
我安装的jdk是1.7的。
不过jvm是;C:\Documents and Settings\Administrator>java -versionjava version "1.7.0_07"Java(TM) SE Runtime Environment (build 1.7.0_07-b11)Java HotSpot(TM) Client VM (build 23.3-b01, mixed mode, sharing)C:\Documents and Settings\Administrator>!SESSION 2012-11-27 20:26:37.326 -----------------------------------------------eclipse.buildId=I20110613-1736java.version=1.4.2_03java.vendor=Sun Microsystems Inc.BootLoader constants: OS=win32, ARCH=x86, WS=win32, NL=zh_CNCommand-line arguments: -os win32 -ws win32 -arch x86!ENTRY org.eclipse.osgi 2 1 2012-11-27 20:26:37.779!MESSAGE NLS unused message: ECLIPSE_OSGI_NAME in: org.eclipse.osgi.framework.internal.core.ExternalMessages!ENTRY org.eclipse.osgi 2 1 2012-11-27 20:26:37.779!MESSAGE NLS unused message: OSGI_VERSION in: org.eclipse.osgi.framework.internal.core.ExternalMessages!ENTRY org.eclipse.osgi 2 1 2012-11-27 20:26:37.795!MESSAGE NLS unused message: ECLIPSE_COPYRIGHT in: org.eclipse.osgi.framework.internal.core.ExternalMessages!ENTRY org.eclipse.osgi 2 1 2012-11-27 20:26:37.795!MESSAGE NLS unused message: BUNDLE_CLASSPATH_ENTRY_NOT_FOUND_EXCEPTION in:org.eclipse.osgi.framework.internal.core.ExternalMessages!ENTRY org.eclipse.osgi 2 1 2012-11-27 20:26:37.795!MESSAGE NLS unused message: BUNDLE_FRAGMENT_IMPORT_CONFLICT in: org.eclipse.osgi.framework.internal.core.ExternalMessages !ENTRY org.eclipse.osgi 2 1 2012-11-27 20:26:37.795!MESSAGE NLS unused message: FILTER_INVALID in: org.eclipse.osgi.framework.internal.core.ExternalMessages!ENTRY org.eclipse.osgi 2 1 2012-11-27 20:26:37.795!MESSAGE NLS unused message: LAUNCHER_ADAPTOR_ERROR in: org.eclipse.osgi.framework.internal.core.ExternalMessages!ENTRY org.eclipse.osgi 2 1 2012-11-27 20:26:37.795!MESSAGE NLS unused message: LAUNCHER_INVALID_PORT in: org.eclipse.osgi.framework.internal.core.ExternalMessages!ENTRY org.eclipse.osgi 2 1 2012-11-27 20:26:37.795!MESSAGE NLS unused message: LAUNCHER_COMPONENT_MISSING in: org.eclipse.osgi.framework.internal.core.ExternalMessages!ENTRY org.eclipse.osgi 2 1 2012-11-27 20:26:37.795!MESSAGE NLS unused message: LAUNCHER_COMPONENT_JAR in: org.eclipse.osgi.framework.internal.core.ExternalMessages!ENTRY org.eclipse.osgi 2 1 2012-11-27 20:26:38.170!MESSAGE NLS unused message: COMMIT_INVALID_TIMESTAMP in: org.eclipse.osgi.internal.resolver.StateMessages!ENTRY org.eclipse.equinox.p2.reconciler.dropins 4 0 2012-11-27 20:26:38.170!MESSAGE FrameworkEvent ERROR!STACK 0org.osgi.framework.BundleException: ⽆法解析束。
premature end of stream readuint

premature end of stream readuint
"Premature end of stream readuint" 这个错误通常与数据流或文件读取有关,尤其是当尝试从一个不完整或已损坏的数据源中读取无符号整数(uint)时。
这个错误意味着在读取预期长度的数据之前,数据流意外地结束了。
在处理这种情况时,开发者需要仔细检查几个方面:
数据源完整性:确保你正在读取的文件或数据流是完整的,没有被截断或损坏。
这可以通过校验和、文件大小比较或其他完整性检查来实现。
读取逻辑:检查你的读取代码,确保它正确处理了所有可能的情况,包括文件末尾、空数据块等。
有时候,错误的读取逻辑会导致程序在不应该停止的地方停止读取。
异常处理:在读取数据时,应该添加适当的异常处理逻辑来捕获和处理任何可能出现的错误。
这包括“Premature end of stream”错误,以及其他可能的I/O错误。
并发和同步问题:如果你的应用程序涉及多线程或并发处理,确保在读取和写入数据时有适当的同步机制。
数据竞争条件或线程不安全的访问可能导致数据损坏或读取错误。
外部因素:考虑任何可能影响数据读取的外部因素,如网络连接中断、磁盘错误等。
这些因素可能导致数据流意外结束。
解决“Premature end of stream readuint”错误通常需要仔细分析代码和数据源,以及使用调试工具来跟踪问题的根源。
一旦确定了问题的原因,就可以采取适当的措施来修复它,例如修复损坏的文件、调整读取逻辑或增加错误处理代码。
无线网卡ra0配置命令

⽆线⽹卡ra0配置命令=================================================================================================== ATE Test Command Format for station driver****** IMPORTANT ******If you are not familiar with hardware, it is recommanded not to modify hardware default value.It may damage hardware.=================================================================================================== Usage:iwpriv ra0 [act] [parameters]=[val]where[act] [parameters] [val] constraints explaination----- ------------- ----------------- --------------------------------=====================================1. Set ATE actions.Value:ATESTART - Start ATE function and stop station function.ATESTOP - Stop ATE function and start station function.TXCONT - Start continuous TX, for power mask.TXCARR - Start carrier test, for frequency calibration.TXFRAME - Transmit frame, for EVM.RXFRAME - Continuous RX, for PER/FER.1.1 ATEDASet ATE frame header destination address.Value:xx:xx:xx:xx:xx:xx ; hex1.2 ATESASet ATE frame header source addr.Value:xx:xx:xx:xx:xx:xx ; hex1.3 ATEBSSIDSet ATE frame header BSSID.Value:xx:xx:xx:xx:xx:xx ; hex1.4 ATECHANNELSet ATE Channel, deimal.Value:802.11b/g: 1 ~ 14 depends on CountryRegion setting1.5 ATETXPOW0Set ATE Tx power for Antenna 1.Value:0 ~ 31 ; 2.4GHz, deimal-7 ~15 ; 5.5GHz, deimal1.6 ATETXPOW1Set ATE Tx power for Antenna 2.Value:0 ~ 31 ; 2.4GHz, decimal-7 ~15 ; 5.5GHz, deimal1.7 ATETXFREQOFFSETSet ATE RF frequency offset.Value:0 ~ 63 ; unit: 2KHz, decimal1.8 ATETXLENSet ATE frame length.Value:24 ~ 2312 ; decimal1.9 ATETXCNTSet ATE frame Tx count.Value:1 ~ ; 32-bit, decimal1.10 ATETXMODE (Refer to TxMode)Set ATE Tx Mode.Value:0: CCK 802.11b1: OFDM 802.11g2: HT_MIX 802.11b/g/n3: Green Field 802.11n1.11 ATETXBW (Refer to TxMode)Set ATE Tx and Rx Bandwidth.Value:0: 20MHz1: 40MHz1.12 ATETXGI (Refer to TxMode)Set ATE Tx Guard Interval.Value:0: Long1: Short1.13 ATETXMCS (Refer to TxMode)Set ATE Tx MCS type.Value:0 ~ 151.14 ATETXANTSet ATE TX antenna.Value:0: All1: Antenna one2: Antenna two1.15 ATERXANTSet ATE RX antenna.Value:0: All1: Antenna one2: Antenna two3: Antenna three1.16 ATERXFERSet ATE to periodically reset and show up RxCount (per-second) and RxTotalCount. Value:0: Disable counter visability1: Enable counter visability1.17 ATESHOWShow all parameters of ATE.Value:11.18 ATEHELPList all commands of ATE.Value:11.19 ResetCounterReset statistic counter.Value:11.20 ATERRFRead all of the RF registers.Value:11.21 ATEWRF1Writethe RF register 1.Value:xxxxxxxx ;32-bit, hex1.22 ATEWRF2Write the RF register 2.Value:xxxxxxxx ;32-bit, hex1.23 ATEWRF3Write the RF register 3.Value:xxxxxxxx ;32-bit, hex1.24 ATEWRF4Write the RF register 4.Value:xxxxxxxx ;32-bit, hex1.25 ATELDE2POverwrite all EEPROM contentsValue:1E.g.iwpriv ra0 set ATELDE2P=11.26 ATERE2PDisplay all EEPROM content.Value:1E.g.iwpriv ra0 set ATERE2P=1=================================================================================================== 2. Examples:=========2.1 Check EVM & Poweriwpriv ra0 set ATE=ATESTARTiwpriv ra0 set ATEDA=00:11:22:33:44:55iwpriv ra0 set ATESA=00:aa:bb:cc:dd:eeiwpriv ra0 set ATEBSSID=00:11:22:33:44:55iwpriv ra0 set ATECHANNEL=1 ; set Channeliwpriv ra0 set ATETXMODE=1 ; set TX-Mode.iwpriv ra0 set ATETXMCS=7 ; set MCS type.iwpriv ra0 set ATETXBW=0 ; set Bandwidthiwpriv ra0 set ATETXGI=0 ; set Long GI.iwpriv ra0 set ATETXLEN=1024 ; set packet length.iwpriv ra0 set ATETXPOW0=18iwpriv ra0 set ATETXPOW1=18iwpriv ra0 set ATETXCNT=100000iwpriv ra0 set ATE=TXFRAMEiwpriv ra0 set ATETXPOW0=19iwpriv ra0 set ATETXPOW0=20iwpriv ra0 set ATE=ATESTART2.2 Check Carrieriwpriv ra0 set ATE=ATESTARTiwpriv ra0 set ATECHANNEL=1 ; set Channeliwpriv ra0 set ATETXMODE=1 ; set TX-Mode.iwpriv ra0 set ATETXMCS=7 ; set MCS type.iwpriv ra0 set ATETXBW=0 ; set Bandwidthiwpriv ra0 set ATETXCNT=200 ; Tx frame count(decmial)iwpriv ra0 set ATE=TXFRAME ; Start Tx Frame(inform BBP to change, modulation mode) iwpriv ra0 set ATE=TXCARR ; Start Tx carrier, Measure carrier with instrumentiwpriv ra0 set ATETXPOW0=05iwpriv ra0 set ATETXPOW1=05iwpriv ra0 set ATETXFREQOFFSET=19iwpriv ra0 set ATE=ATESTART2.3 Check specturm maskiwpriv ra0 set ATE=ATESTARTiwpriv ra0 set ATECHANNEL=1 ; set Channeliwpriv ra0 set ATETXMODE=1 ; set TX-Mode.iwpriv ra0 set ATETXMCS=7 ; set MCS type.iwpriv ra0 set ATETXBW=0 ; set Bandwidthiwpriv ra0 set ATETXCNT=200 ; Tx frame count(decmial)iwpriv ra0 set ATE=TXFRAME ; Start Tx Frame(inform BBP to change, modulation mode) iwpriv ra0 set ATE=TXCONT ; Start continuous TX, Measure specturm mask with instrument iwpriv ra0 set ATETXPOW0=5iwpriv ra0 set ATETXPOW1=5iwpriv ra0 set ATE=ATESTART2.4 Frequency offset tuningiwpriv ra0 set ATE=ATESTARTiwpriv ra0 set ATECHANNEL=1 ; set Channeliwpriv ra0 set ATETXMODE=1 ; set TX-Mode.iwpriv ra0 set ATETXMCS=7 ; set MCS type.iwpriv ra0 set ATETXCNT=200 ; Tx frame count(decmial)iwpriv ra0 set ATETXFREQOFFSET=0 ; Set frequency offset 0(decimal)iwpriv ra0 set ATE=TXFRAME ; Start Tx Frameiwpriv ra0 set ATE=TXCARR ; Start Tx carrier, Measure carrier frequency with instrumentiwpriv ra0 set ATETXFREQOFFSET=10 ; Dynamic turning frequency offset, 10(decimal) iwpriv ra0 set ATETXFREQOFFSET=20 ; Dynamic turning frequency offset, 20(decimal) iwpriv ra0 set ATE=ATESTART ; Stop, Store the tuning result to EEPROM2.5 Rxiwpriv ra0 set ATE=ATESTARTiwpriv ra0 set ATECHANNEL=1 ; set Channeliwpriv ra0 set ResetCounter=1 ; Reset statistic counteriwpriv ra0 set ATETXFREQOFFSET=value ;To use the ¨value〃(decimal) you got in tx calibration iwpriv ra0 set ATETXMODE=1 ; set TX-Mode.iwpriv ra0 set ATETXMCS=7 ; set MCS type.iwpriv ra0 set ATETXBW=0 ; set Bandwidthiwpriv ra0 set ATE=RXFRAME ; Start Rx,iwpriv ra0 set ATERXFER=1 ; show RxCnt and RSSI/per-antenna, Transmit test packetsiwpriv ra0 set ATE=ATESTART ; Stopiwpriv ra0 stat ; get statistics counteriwpriv ra0 set ATERXFER=1iwpriv ra0 set ATERXANT=1iwpriv ra0 set ATE=ATESTARTiwpriv ra0 set ATERXANT=0iwpriv ra0 set ATE=RXFRAME2.6 Show all ate parametersiwpriv ra0 set ATESHOW=1Mode=4TxPower0=0TxPower1=0TxAntennaSel=0RxAntennaSel=0BBPCurrentBW=0GI=0MCS=7TxMode=1Addr1=00:11:22:aa:bb:ccAddr2=00:11:22:aa:bb:ccAddr3=00:11:22:aa:bb:ccChannel=1TxLength=1024TxCount=40000TxRate=11RFFreqOffset=02.7 Online helpiwpriv ra0 set ATEHELP=1ATE=ATESTART, ATESTOP, TXCONT, TXCARR, TXFRAME, RXFRAMEATEDAATESAATEBSSIDATECHANNEL, range:0~14(unless A band !).ATETXPOW0, set power level of antenna 1.ATETXPOW1, set power level of antenna 2.ATETXANT, set TX antenna. 0: all, 1: antenna one, 2: antenna two.ATERXANT, set RX antenna.0: all, 1: antenna one, 2: antenna two, 3: antenna three. ATETXFREQOFFSET, set frequency offset, range 0~63.ATETXBW, set BandWidth, 0:20MHz, 1:40MHz.ATETXLEN, set Frame length, range 24~2312.ATETXCNT, set how many frame going to transmit.ATETXMCS, set MCS, reference to rate table.ATETXMODE, set Mode 0: CCK, 1: OFDM, 2: HT-Mix, 3: GreenField, reference to rate table. ATETXGI, set GI interval, 0: Long, 1: Short.ATERXFER, 0: disable Rx Frame error rate. 1: enable Rx Frame error rate.ATERRF, show all RF registers.ATEWRF1, set RF1 register.ATEWRF2, set RF2 register.ATEWRF3, set RF3 register.ATEWRF4, set RF4 register.ATELDE2P, load EEPROM from .bin file.ATERE2P, display all EEPROM content.ATESHOW, display all parameters of ATE.ATEHELP, online help.2.8 Display Rx Packet Count and RSSIiwpriv ra0 set ATERXANT=0 ==> Enable All Three Rx Antennasiwpriv ra0 set ATERXFER=1 ==> Enable Rx Frame Error Rate: RxCnt/RxTotaliwpriv ra0 set ATE=RXFRAME ==> Start RxMlmePeriodicExec: Rx packet cnt = 2/4MlmePeriodicExec: Rx AvgRssi0=-88, AvgRssi1=-80, AvgRssi2=-91MlmePeriodicExec: Rxpacket cnt = 2/6MlmePeriodicExec: Rx AvgRssi0=-86, AvgRssi1=-77, AvgRssi2=-89iwpriv ra0 set ATERXANT=1 ==> Enable Three Rx Antenna-1iwpriv ra0 set ATERXFER=1 ==> Enable Rx Frame Error Rate: RxCnt/RxTotaliwpriv ra0 set ATE=RXFRAME ==> Start RxMlmePeriodicExec: Rx packet cnt = 0/7MlmePeriodicExec: Rx AvgRssi=-87MlmePeriodicExec: Rx packet cnt = 7/14MlmePeriodicExec: Rx AvgRssi=-90=================================================================================================== 3. Hardware Access=======================================================3.1 iwpriv ra0 bbp [parameters]=[Value]Read/Write BBP registers by ID number.BBPID3.1.1 Read BBP register, BBPID only, no ¨=〃 symbol.BBPID:0 ~ xx ; decimal, 8-bitBBPID=Value3.1.2 Write BBP register.BBPID:0 ~ xx ; decimal, 8-bitValue:00 ~FF ; hexdecimal, 8-bit=====================================3.2 iwpriv ra0 mac [parameters]=[val]Read/Write MAC registers by offset.MAC_OFFSET3.2.1 Read MAC register, MAC_OFFSET only, no ¨=〃 symbol.MAC_OFFSET:0000 ~ FFFF ; hexdecimal, 16-bitMAC_OFFSET=Value3.2.2 Write MAC register.MAC_OFFSET:0000 ~ FFFF ; hexdecimal, 16-bitValue:0000 ~FFFF ; hexdecimal, 32-bit=====================================3.3 iwpriv ra0 e2p [parameters]=[val]Read/Write EEPROM content by address.EEP_ADDR3.3.1 Read EEPROM content, EEP_ADDR only, no ¨=〃 symbol.EEP_ADDR:00 ~ FF ; hexdecimal, 16-bit alignment (0, 2, 4, 6, 8, A, C, )EEP_ADDR=Value3.3.2 Write EEPROM content.EEP_ADDR:00 ~ FF ; hexdecimal, 16-bit alignment (0, 2, 4, 6, 8, A, C, )Value:0000 ~FFFF ; hexdecimal, 16-bit=====================================3.4 Example3.4.1 Hardware accessiwpriv ra0 bbp 0 # read BBP register 0iwpriv ra0 bbp 0=12 # write BBP register 0 as 0x12iwpriv ra0 mac 0 # read MAC register 0iwpriv ra0 mac 0=1234abcd # write MAC register 0 as 0x1234abcdiwpriv ra0 e2p 0 # read E2PROM 0iwpriv ra0 e2p c=12ab # write E2PROM 0xc as 0x12ab3.4.2 Statistic counter operationiwpriv ra0 stat # read statistic counteriwpriv ra0 set ResetCounter=0 # reset statistic counterSuggestion:1. To turn on ATE functionality, you have to add compile flag "RALINK_ATE" to Makefile2. Before doing ATE testing, please stop AP function3. If you want to test another ATE action, prefer to stop AP & ATE function4. All ATE function settings will lose efficacy after reboot.5. Before hardware register access, please reference hardware spec.Note.In ATE mode, the channel must set via "ATECHANNEL"=================================================================================================== 4. ated=======4.1 IntroductionThe ated is an optional user space component for RT28xx Linux driver.When Windows GUI starts, AP enters ATE mode (i.e.,ATESTART) immediately.It behaves as a proxy between Windows GUI and RT28xx Linux driver when ATE process proceeds.The ated will be killed automatically when Windows GUI is closed.You can kill it manually, too(for example, type '$killall ated').RT28xx linux driver will leave ATE mode either ated is killed or Windows GUI is closed.4.2 Environment setup1. Connect the platform you want to test directly with a Windows host by ether network line.2. In the Windows host, run WinPcap_4_0.exe for the QA GUI or ./RT2880_ATE/RaUI.exe(please unrar "RT2880_ATE.rar" to get it).4.3 How to use ated for ATE purpose0. First you should set both "HAS_ATE=y" and "HAS_QA_SUPPORT=y" in the file ~/Module/os/linux/config.mk and compile the driver.1. Modify the Makefile according to our target "PLATFORM".2. Change the path of "CROSS_COMPILE" if needed.3. Then type 'make' command to compile the source code of the daemon.4. After the driver interface has started up, attach both of the wireless interface and the ethernet interface to the bridge interface.5. If you have no bridge interface, please give an IP address to the ethernet interface.(for example : '$ated -beth0')6. After the interfaces have entered forwarding states, manually start ated, type '$ated -bbrX -iraX'.7. If your WLAN interface and Bridge interface is "ra0" and "br0" respectively, just type $ated.(For further usage of options, type $ated -h)8. In the Windows host, run RT28xxQA_ATE.exe or ./RT2880_ATE/RaUI.exe.9. Select the wired network adapter, then press OK and wait for a moment.10.If the Windows host cannot tolerate such a broadcast storm from ated,please run ated with option -u.(for example : '$ated -ira1 -u')11.If your target platform concerns its network security, please run RT28xxQA_unicast.exe instead of RT28xxQA_ATE.exe. Note :a. The names of WLAN interface(default is "ra0") and Bridge interface(default is "br0") must be specified manually(for example : '$ated -bbr1 -ira2') if your WLAN interface or Bridge interface is not "ra0" or "br0" respectively !b. Please make sure no other RaUI is running before you excute ./RT2880_ATE/RaUI.exe.。
STM32f10固件库使用手册中文版
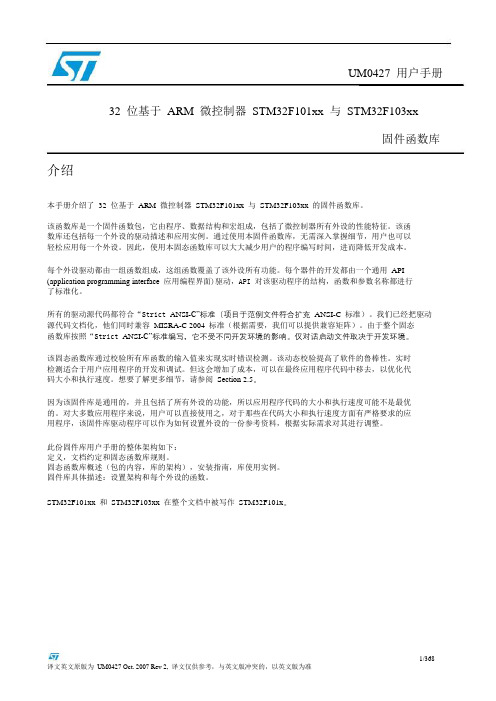
UM0427 用户手册32 位基于ARM 微控制器STM32F101xx 与STM32F103xx固件函数库介绍本手册介绍了32 位基于ARM 微控制器STM32F101xx 与STM32F103xx 的固件函数库。
该函数库是一个固件函数包,它由程序、数据结构和宏组成,包括了微控制器所有外设的性能特征。
该函数库还包括每一个外设的驱动描述和应用实例。
通过使用本固件函数库,无需深入掌握细节,用户也可以轻松应用每一个外设。
因此,使用本固态函数库可以大大减少用户的程序编写时间,进而降低开发成本。
每个外设驱动都由一组函数组成,这组函数覆盖了该外设所有功能。
每个器件的开发都由一个通用API (application programming interface 应用编程界面)驱动,API 对该驱动程序的结构,函数和参数名称都进行了标准化。
所有的驱动源代码都符合“Strict ANSI-C”标准(项目于范例文件符合扩充ANSI-C 标准)。
我们已经把驱动源代码文档化,他们同时兼容MISRA-C 2004 标准(根据需要,我们可以提供兼容矩阵)。
由于整个固态函数库按照“Strict ANSI-C”标准编写,它不受不同开发环境的影响。
仅对话启动文件取决于开发环境。
该固态函数库通过校验所有库函数的输入值来实现实时错误检测。
该动态校验提高了软件的鲁棒性。
实时检测适合于用户应用程序的开发和调试。
但这会增加了成本,可以在最终应用程序代码中移去,以优化代码大小和执行速度。
想要了解更多细节,请参阅Section 2.5。
因为该固件库是通用的,并且包括了所有外设的功能,所以应用程序代码的大小和执行速度可能不是最优的。
对大多数应用程序来说,用户可以直接使用之,对于那些在代码大小和执行速度方面有严格要求的应用程序,该固件库驱动程序可以作为如何设置外设的一份参考资料,根据实际需求对其进行调整。
此份固件库用户手册的整体架构如下:定义,文档约定和固态函数库规则。
relocation against stdout in read-only section

relocation against stdout in read-only section "relocation against stdout in read-only section" 是一个在编译和链接过程中可能出现的错误消息。
它通常出现在尝试将代码或数据段标记为只读,但链接器(linker)在尝试解析符号引用时遇到了问题。
简单地说,当你尝试在一个只读(或受保护)的内存区域中写入数据时,就可能会遇到这种错误。
在许多操作系统和保护模式下,只读内存区域是为了防止意外或恶意的写操作而设计的。
这个错误可能由多种原因引起,包括但不限于:
代码或数据段的错误配置:你可能错误地将某些段设置为只读,而它们实际上需要可写权限。
链接器错误:链接器在解析符号引用时可能出现错误,导致将代码或数据放在不正确的位置。
动态链接库(DLL)问题:如果你在动态链接库(DLL)中遇到此问题,可能是由于DLL中的某些代码或数据段被错误地配置为只读。
解决此类问题通常需要检查和调整代码和数据段的内存属性,确保它们被正确地配置在适当的内存区域中。
你可能需要与你的编译器和链接器文档进行深入的阅读,以确
保你了解如何正确地设置这些属性。
EM4205_EM4305完整数据手册
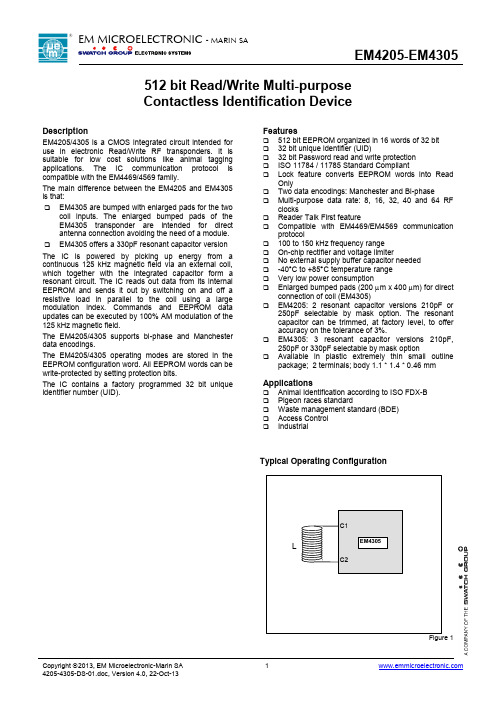
Typ.
8.4
Max.
9.1UnitV 源自PEM4205 EM4305
EEPROM data retention EEPROM write cycles
Note 1: Note 2: Note 3: Note 4:
TRET NCY
TOP = 55°C VDD = 3.6 V
202 240 189 225 297 10 1000
Table 1
Handling Procedures
This device has built-in protection against high static voltages or electric fields. However, due to the unique properties of this device, anti-static precautions should be taken as for any other CMOS component. Unless otherwise specified, proper operation can only occur when all terminal voltages are kept within the supply voltage range.
210 250 210 250 330
218 260 231 275 363
pF pF pF pF pF years cycles
Note (1) Note (1) Note (2) Note (2) Note (2-3) Note (4)
Table 3 Resonant Capacitor trimming is only offered standard for the EM4205. In case that the trimming of the resonant capacitor is not done, tolerance range is the same as in EM4305. Statistics show a variation of capacitance within a wafer of 3% The 330pF resonant capacitor version only available in EM4305 Based on 1000 hours at 150°C.
在HTTPRequest中加入特定的Header
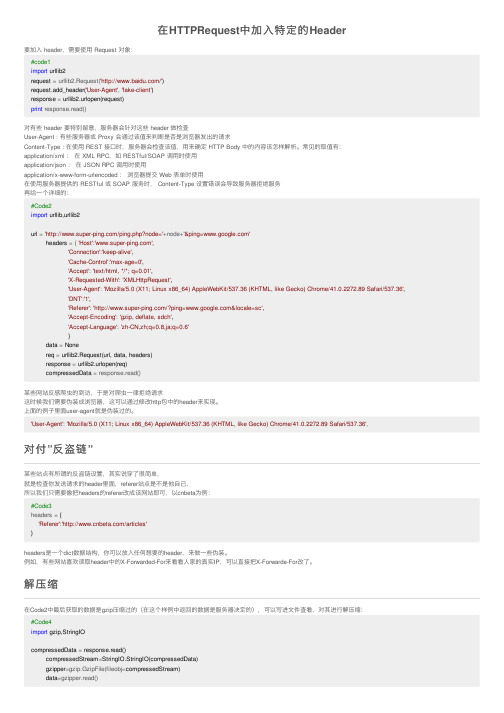
在HTTPRequest中加⼊特定的Header要加⼊ header,需要使⽤ Request 对象:#code1import urllib2request = urllib2.Request('/')request.add_header('User-Agent', 'fake-client')response = urllib2.urlopen(request)print response.read()对有些 header 要特别留意,服务器会针对这些 header 做检查User-Agent : 有些服务器或 Proxy 会通过该值来判断是否是浏览器发出的请求Content-Type : 在使⽤ REST 接⼝时,服务器会检查该值,⽤来确定 HTTP Body 中的内容该怎样解析。
常见的取值有:application/xml :在 XML RPC,如 RESTful/SOAP 调⽤时使⽤application/json :在 JSON RPC 调⽤时使⽤application/x-www-form-urlencoded :浏览器提交 Web 表单时使⽤在使⽤服务器提供的 RESTful 或 SOAP 服务时, Content-Type 设置错误会导致服务器拒绝服务再给⼀个详细的:#Code2import urllib,urllib2url = '/ping.php?node='+node+'&ping='headers = { 'Host':'','Connection':'keep-alive','Cache-Control':'max-age=0','Accept': 'text/html, */*; q=0.01','X-Requested-With': 'XMLHttpRequest','User-Agent': 'Mozilla/5.0 (X11; Linux x86_64) AppleWebKit/537.36 (KHTML, like Gecko) Chrome/41.0.2272.89 Safari/537.36','DNT':'1','Referer': '/?ping=&locale=sc','Accept-Encoding': 'gzip, deflate, sdch','Accept-Language': 'zh-CN,zh;q=0.8,ja;q=0.6'}data = Nonereq = urllib2.Request(url, data, headers)response = urllib2.urlopen(req)compressedData = response.read()某些⽹站反感爬⾍的到访,于是对爬⾍⼀律拒绝请求这时候我们需要伪装成浏览器,这可以通过修改http包中的header来实现。
viewforheaderinsection 用法(一)
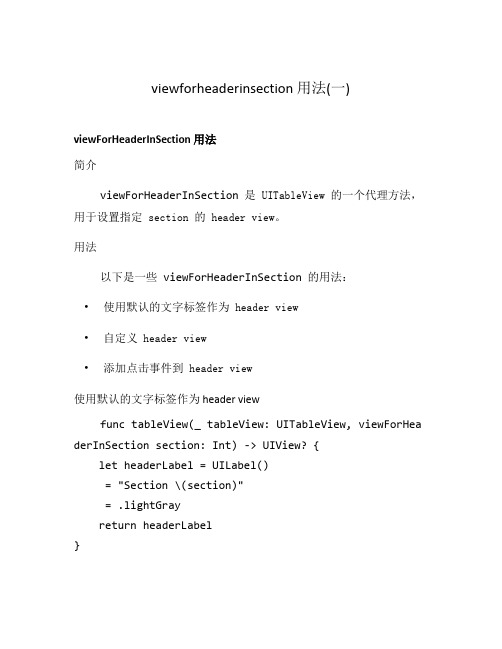
viewforheaderinsection 用法(一)viewForHeaderInSection 用法简介viewForHeaderInSection是 UITableView 的一个代理方法,用于设置指定 section 的 header view。
用法以下是一些viewForHeaderInSection的用法:•使用默认的文字标签作为 header view•自定义 header view•添加点击事件到 header view使用默认的文字标签作为 header viewfunc tableView(_ tableView: UITableView, viewForHea derInSection section: Int) -> UIView? {let headerLabel = UILabel()= "Section \(section)"= .lightGrayreturn headerLabel}上述代码将在每个 section 头部显示一个带有文本的 header view。
自定义 header viewfunc tableView(_ tableView: UITableView, viewForHea derInSection section: Int) -> UIView? {let headerView = UIView(frame: CGRect(x: 0, y: 0, wi dth: , height: 50))= .lightGraylet headerLabel = UILabel(frame: CGRect(x: 10, y: 10, width: - 20, height: - 20))= "Section \(section)"= .white(headerLabel)return headerView}上述代码将创建一个自定义的 header view,包含一个灰色背景和带有文本的白色标签。
混淆保留接口参数
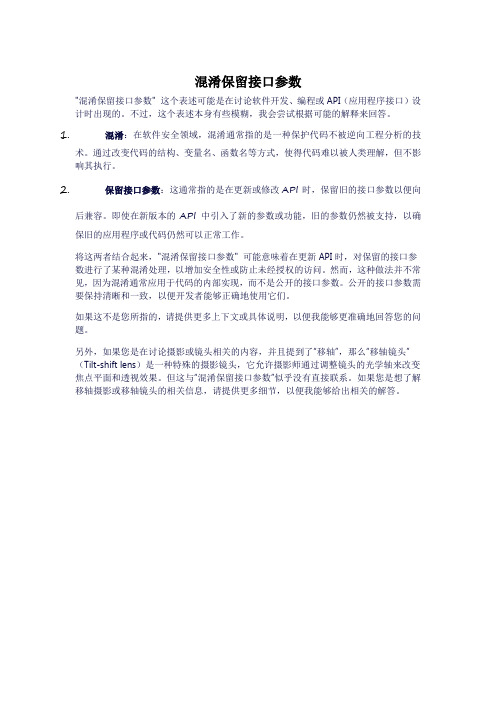
混淆保留接口参数
"混淆保留接口参数" 这个表述可能是在讨论软件开发、编程或API(应用程序接口)设计时出现的。
不过,这个表述本身有些模糊,我会尝试根据可能的解释来回答。
1.混淆:在软件安全领域,混淆通常指的是一种保护代码不被逆向工程分析的技
术。
通过改变代码的结构、变量名、函数名等方式,使得代码难以被人类理解,但不影响其执行。
2.保留接口参数:这通常指的是在更新或修改API时,保留旧的接口参数以便向
后兼容。
即使在新版本的API中引入了新的参数或功能,旧的参数仍然被支持,以确保旧的应用程序或代码仍然可以正常工作。
将这两者结合起来,"混淆保留接口参数" 可能意味着在更新API时,对保留的接口参数进行了某种混淆处理,以增加安全性或防止未经授权的访问。
然而,这种做法并不常见,因为混淆通常应用于代码的内部实现,而不是公开的接口参数。
公开的接口参数需要保持清晰和一致,以便开发者能够正确地使用它们。
如果这不是您所指的,请提供更多上下文或具体说明,以便我能够更准确地回答您的问题。
另外,如果您是在讨论摄影或镜头相关的内容,并且提到了“移轴”,那么“移轴镜头”
(Tilt-shift lens)是一种特殊的摄影镜头,它允许摄影师通过调整镜头的光学轴来改变焦点平面和透视效果。
但这与“混淆保留接口参数”似乎没有直接联系。
如果您是想了解移轴摄影或移轴镜头的相关信息,请提供更多细节,以便我能够给出相关的解答。
Philips aCMQ 快速指南 Ultrasound QLAB 10.8说明书
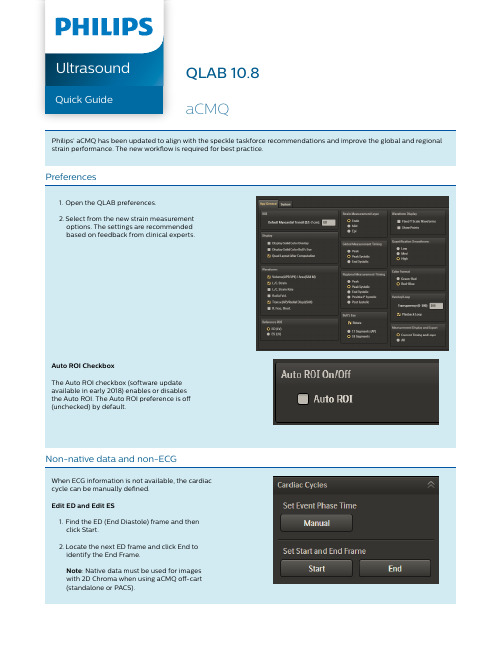
Quick Guide Ultrasound Non-native data and non-ECGPhilips’ aCMQ has been updated to align with the speckle taskforce recommendations and improve the global and regional strain performance. The new workflow is required for best practice.When ECG information is not available, the cardiaccycle can be manually defined.Edit ED and Edit ES1. Find the ED (End Diastole) frame and thenclick Start.2. Locate the next ED frame and click End toidentify the End Frame.Note: Native data must be used for imageswith 2D Chroma when using aCMQ off-cart (standalone or PACS).Auto ROI CheckboxThe Auto ROI checkbox (software updateavailable in early 2018) enables or disablesthe Auto ROI. The Auto ROI preference is off(unchecked) by default.Select the loop associated with the LV AP3 and confirm by selecting LV AP3. (If utilizing a SmartExam, this step is automated.)If Auto ROI is enabled (checked), then points will be placed automatically.Selecting draw (recommended method) allows users to place the basal and apical points resulting in a Manual ROI.Note: Always analyze the LV AP3 view first.AP3Edit ED AP4AP2Place the reference points onthe blood pool / tissue borderat the mitral valve leafletinsertion, the LVOTand theapex.Place the reference points on the blood pool / tissue border at the left and right mitral valve leaflet insertion,and the apex.Place the reference points on the blood pool / tissue border at the left and right mitral valve leaflet insertion, and the apex.Edit ED and Edit ESEdit ED (End Diastole) and Edit ES (End Systole)allow the user to confirm placement of the ROIover the underlying tissue matching the insideedge of the ROI to the blood tissue interface.Click Edit ED and confirm the placement ofthe annular and apical points. Edit if needed.Click Edit ES and confirm the placement of theannular and apical points. Edit if needed.Click Accept to confirm results.Complete aCMQ by performing the stepsabove on the LV AP4 and LV AP2.Please consult the user manual for further information.© 2019 Koninklijke Philips N.V. All rights are reserved. Philips reserves the right to make changes in specifications and/or to discontinue any product at any time without notice or obligation and will not be liable for any consequences resulting from the use of this publication. Trademarks are the property of Koninklijke Philips N.V. or their respective Printed in The Netherlands. 4522 991 44681 * JAN 2019。
UITableView中关于viewForHeaderInSection的一点小坑

UITableView中关于viewForHeaderInSection的⼀点⼩坑新⼿⼊门,在保持兴趣的前提下,最直接的办法就是照着例⼦⼿动敲⼀遍代码,然后将⽰例跑起来,这样能最直观的看到效果。
但是,⼀般的⾯向初学者的教程或实例,技术⾯都相对于浅显,实现的效果也⽐较Low,就像开发商刚盖出的房⼦⼀样,也叫房⼦,但那是⽑坯房。
相对于有其他语⾔开发经验或项⽬经验的初学者(Ps:例如我~)来说,往往会以点带⾯,会主动去挖掘与教程相关的“姿势点”,想尽办法⽤已掌握的新技能去将这些实例完善、扩展,想⼀次就做出精装修的房⼦。
⼜因为对于⼀门刚接触的新语⾔,了解的不够深⼊,所以也会难免陷⼊⼀个个⼩坑中。
这两天做的实例是编码实现UITableView,还是⽼样⼦,不拖控件、不使⽤Auto Layout布局,要求兼容苹果不同分辨率的三种设备,暂不考虑iPad。
功能很简单,很容易就搞出来了。
但是表头很丑,看着很不爽,寻思着是不是给它弄好看⼀点。
// 普通设置表头- (NSString *)tableView:(UITableView *)tableView titleForHeaderInSection:(NSInteger)section{return@"婴幼⼉奶粉品牌列表(默认表头)";}如下图:我想要做的是将表头弄漂亮⼀点,增加⼀点⾃定义的元素,⽐如说加个⼩icon,加个背景⾊什么的。
// ⾃定义表头- (UIView*) tableView:(UITableView *)_tableView viewForHeaderInSection:(NSInteger)section {UIView *headerView = [[UIView alloc] initWithFrame:CGRectMake(0, 0, _tableView.frame.size.width, 50)];// left iconUIImageView *icon = [[UIImageView alloc] initWithFrame:CGRectMake(5, 5, 40, 40)];icon.image = [UIImage imageNamed:@"250x250"];// right textUILabel *label = [[UILabel alloc] initWithFrame:CGRectMake(45, 0, _tableView.frame.size.width-50, 50)];label.textColor = [UIColor orangeColor];label.text = @"婴幼⼉奶粉品牌列表(⾃定义表头)";label.textAlignment = NSTextAlignmentCenter;// 消息⽅式设置背景⾊(UIColor最后要转成CGColor类型)[yer setBackgroundColor:[UIColor colorWithRed:230.0/255.0 green:230.0/255.0 blue:250.0/255.0 alpha:1].CGColor];// 属性⽅式设置背景⾊//headerView.backgroundColor = [UIColor colorWithRed:230.0/255.0 green:230.0/255.0 blue:250.0/255.0 alpha:1];[headerView addSubview:icon];[headerView addSubview:label];return headerView;}原以为到这⾥,差不多就实现我想的效果:表头左边有个⼩icon,右边是⽂字描述。
Python3中使用urllib的方法详解(header,代理,超时,认证,异常处理)

Python3中使⽤urllib的⽅法详解(header,代理,超时,认证,异常处理)我们可以利⽤urllib来抓取远程的数据进⾏保存哦,以下是python3 抓取⽹页资源的多种⽅法,有需要的可以参考借鉴。
1、最简单import urllib.requestresponse = urllib.request.urlopen('/')html = response.read()2、使⽤ Requestimport urllib.requestreq = urllib.request.Request('/')response = urllib.request.urlopen(req)the_page = response.read()3、发送数据#! /usr/bin/env python3import urllib.parseimport urllib.requesturl = 'http://localhost/login.php'user_agent = 'Mozilla/4.0 (compatible; MSIE 5.5; Windows NT)'values = {'act' : 'login','login[email]' : 'yzhang@','login[password]' : '123456'}data = urllib.parse.urlencode(values)req = urllib.request.Request(url, data)req.add_header('Referer', '/')response = urllib.request.urlopen(req)the_page = response.read()print(the_page.decode("utf8"))4、发送数据和header#! /usr/bin/env python3import urllib.parseimport urllib.requesturl = 'http://localhost/login.php'user_agent = 'Mozilla/4.0 (compatible; MSIE 5.5; Windows NT)'values = {'act' : 'login','login[email]' : 'yzhang@','login[password]' : '123456'}headers = { 'User-Agent' : user_agent }data = urllib.parse.urlencode(values)req = urllib.request.Request(url, data, headers)response = urllib.request.urlopen(req)the_page = response.read()print(the_page.decode("utf8"))5、http 错误#! /usr/bin/env python3import urllib.requestreq = urllib.request.Request('https:// ')try:urllib.request.urlopen(req)except urllib.error.HTTPError as e:print(e.code)print(e.read().decode("utf8"))6、异常处理1#! /usr/bin/env python3from urllib.request import Request, urlopenfrom urllib.error import URLError, HTTPErrorreq = Request("https:// /")try:response = urlopen(req)except HTTPError as e:print('The server couldn't fulfill the request.')print('Error code: ', e.code)except URLError as e:print('We failed to reach a server.')print('Reason: ', e.reason)else:print("good!")print(response.read().decode("utf8"))7、异常处理2#! /usr/bin/env python3from urllib.request import Request, urlopenfrom urllib.error import URLErrorreq = Request("https:// /")try:response = urlopen(req)except URLError as e:if hasattr(e, 'reason'):print('We failed to reach a server.')print('Reason: ', e.reason)elif hasattr(e, 'code'):print('The server couldn't fulfill the request.')print('Error code: ', e.code)else:print("good!")print(response.read().decode("utf8"))8、HTTP 认证#! /usr/bin/env python3import urllib.request# create a password managerpassword_mgr = urllib.request.HTTPPasswordMgrWithDefaultRealm() # Add the username and password.# If we knew the realm, we could use it instead of None.top_level_url = "https:// /"password_mgr.add_password(None, top_level_url, 'rekfan', 'xxxxxx') handler = urllib.request.HTTPBasicAuthHandler(password_mgr)# create "opener" (OpenerDirector instance)opener = urllib.request.build_opener(handler)# use the opener to fetch a URLa_url = "https:// /"x = opener.open(a_url)print(x.read())# Install the opener.# Now all calls to urllib.request.urlopen use our opener.urllib.request.install_opener(opener)a = urllib.request.urlopen(a_url).read().decode('utf8')print(a)9、使⽤代理#! /usr/bin/env python3import urllib.requestproxy_support = urllib.request.ProxyHandler({'sock5': 'localhost:1080'}) opener = urllib.request.build_opener(proxy_support)urllib.request.install_opener(opener)a = urllib.request.urlopen("https:// ").read().decode("utf8") print(a)10、超时#! /usr/bin/env python3import socketimport urllib.request# timeout in secondstimeout = 2socket.setdefaulttimeout(timeout)# this call to urllib.request.urlopen now uses the default timeout# we have set in the socket modulereq = urllib.request.Request('https:// /')a = urllib.request.urlopen(req).read()print(a)总结以上就是这篇⽂章的全部内容,希望本⽂的内容对⼤家学习或使⽤python能有所帮助,如果有疑问⼤家可以留⾔交流。
unityheader用法

unityheader用法
`UnityHeader` 可能指的是`Unity 游戏引擎` 中的`Unity 头文件`。
它是一个包含了游戏引擎中常用的类、结构体和常量定义的文件。
使用`UnityHeader` 文件的目的是为了方便开发者在编写代码时引用游戏引擎中的类和常量,避免重复定义和拼写错误。
在使用`UnityHeader` 文件时,只需要在代码中包含该文件即可,无需在每个文件中重复引用游戏引擎中的类和常量。
以下是使用`UnityHeader` 文件的示例代码:
```csharp
using UnityEngine;
```
在上面的代码中,我们使用了`using` 关键字来引用`Unity` 命名空间,这样就可以在代码中使用`Unity` 游戏引擎中的类和常量了。
需要注意的是,不同版本的`Unity` 游戏引擎可能会使用不同的`UnityHeader` 文件,因此在使用时需要根据实际情况选择正确的文件。
- 1、下载文档前请自行甄别文档内容的完整性,平台不提供额外的编辑、内容补充、找答案等附加服务。
- 2、"仅部分预览"的文档,不可在线预览部分如存在完整性等问题,可反馈申请退款(可完整预览的文档不适用该条件!)。
- 3、如文档侵犯您的权益,请联系客服反馈,我们会尽快为您处理(人工客服工作时间:9:00-18:30)。
header for SPIE useMIRAGE read-in-integrated-circuit testing resultsTheodore R. Hoelter, Blake A. Henry, John H. Graff, Naseem Y. AzizIndigo Systems Corporation, 5385 Hollister Avenue #103, Santa Barbara, CA 93111ABSTRACTThis paper describes the test results for the MIRAGE read-in-integrated-circuit (RIIC) designed by Indigo Systems Corporation. This RIIC, when mated with suspended membrane, micro-machined resistive elements, forms a highly advanced emitter array. This emitter array is used by Indigo and Santa Barbara Infrared Incorporated in a jointly developed product for infrared scene generation, called MIRAGE. The MIRAGE RIIC is a 512 x 512 pixel design which incorporates a number of features that extend the state of the art for emitter array RIIC devices. These innovations include an all-digital interface for scene data, snapshot image updates (all pixels show the new frame simultaneously), frame rates up to 200 Hz, operating modes that control the device output, power consumption, and diagnostic configuration. Tests measuring operating speed, RIIC functionality and D/A converter performance were completed. At 2.1 x 2.3 cm, this die is also the largest non-stitched device ever made by Indigo’s foundry, American Microsystems Incorporated. As with any IC design, die yield is a critical factor that typically scales with the size and complexity. Die yield, and a statistical breakdown of the failures observed will be discussed.Keywords: Infrared, Scene generation, Scene simulation, Hard-Ware-In-the-Loop, HWIL, MIRAGE, Emitter, Microstructure, RIIC1.INTRODUCTIONThe value of infrared (IR) scene simulation in the development and ongoing testing of IR systems is widely recognized by both government and industry. Reduction in the cost of missile systems is realized through hardware in the loop testing that allows the full signal path to be dynamically exercised in a laboratory setting, reducing the need for costly missile test firings. The ability to perform accurate simulations in a lab setting also offers the promise of shorter development cycles for IR based imaging systems by giving developers more immediate access to data. As IR focal plane technology advances, there is a need for corresponding advances in the capability of scene simulation hardware. With increasing focal plane array sizes and frame rates, the data rate required for scene simulation increases. FPA features such as snapshot integration, where all the pixels in the FPA integrate at the same time, have become standard and place additional requirements on scene simulation hardware. Last year, Indigo Systems Corporation and Santa Barbara Infrared Inc. along with Rockwell Science Center announced the joint development of MIRAGE (Multi-spectral Infrared Animation Generation Equipment), a new scene simulation system1. MIRAGE applies Rockwell’s proprietary process for microstructure fabrication to emitter elements and utilizes a newly designed RIIC with a number of important advances over prior RIIC designs. The MIRAGE RIIC, fabricated in the second quarter of 1998, is the first to incorporate an all-digital interface and snapshot frame updates. In addition, special attention was paid to reducing scene dependent non-uniformity, resulting in a unique approach to power handling. This paper begins with a description of the MIRAGE RIIC design in section two. Sections three and four describe the test set-up and wafer level characterization results from probe testing, including yield of operable die for the first lot of wafers.2.MIRAGE RIIC DESIGN2.1. Emitter overviewThe MIRAGE RIIC is designed to be mechanically mated to a 512 x 512 array of suspended membrane, resistively heated micro-emitters. Each micro-emitter element is electrically connected to one of the 512 x 512 RIIC unit cells, allowing individual control of the current driven through each emitter element during scene generation. The electrical connection to the emitter from the RIIC also serves as the mechanical support for the emitter structure and provides the thermal path for heat flow during operation. Figure 1 is a schematic representation of a single emitter showing the resistive portion of the emitter (1) suspended above the RIIC substrate (2) by the electrical connection (3).Figure 1. A schematic representation of a single emitter2.2. RIIC signal chainTo generate a scene, the RIIC must be supplied with required bias voltages, timing, and formatted digital scene data. Figure 2places the various RIIC functional blocks in the signal chain. The signal path starts with digital data input to one of the two 16 bit DAC’s. These two DAC’s work in parallel to generate analog voltages corresponding to emitter pixel radiance values.Each DAC generates voltages for a 512 row by 256 column area. The output voltage from each DAC is routed to one of 1024column buffers where the voltage is sample and held and then driven up the column bus. The column buffers are organized in pairs by column. One buffer in the pair drives signals to odd rows, while the other buffer drives signals to the even rows.Figure 2. RIIC signal chain diagramAs the scene data for one row is received, converted, and routed to the appropriate column buffers (odd or even) the other set of buffers are writing the previous row of data up the column buses to individual unit cells. In this way, each buffer has an entire line time to allow the signal to settle, while the other set of buffers is being filled by the two DAC’s. Right before each column buffer begins to drive its signal up the column bus, the row-enable switch in the appropriate unit cell along that column closes, allowing the signal to be received by that unit cell’s sample and hold capacitor. Right before each column buffer is switched off, the row-enable switch closes, storing a voltage on the sample and hold capacitor. At the end of aDAC LOGIC Temp Sensor X2 DAC VOLTAGE TEST (DACVLT)DAC VOLTAGE TEST(DACVRT)CLK DRV(SNAPSHOT)frame, when all 512 x 512 sample and hold capacitors are charged, the snapshot switches are simultaneously closed in every unit cell. Charge is shared between the sample and hold capacitor and the snapshot capacitor, creating a new drive voltage on each emitter driver and resulting in a new emitter radiant output.In addition to the RIIC functional blocks that comprise the signal chain, there are a number of test circuits and different RIIC operating modes that may be accessed through six mode control bits. During normal operation these mode control bits allow the RIIC to operate in snapshot mode or alternately in rolling display mode by holding the snapshot switch closed all the time. The mode bits also allow the RIIC to operate in one of two current dissipation conditions. In the default operating condition, the total current through each unit cell is held constant, with more or less current shunted away from the emitter, depending on the voltage on the snapshot capacitor. The other current handling condition, current on demand, supplies to each unit cell only the current required to heat the emitter. Other mode bits allow the RIIC to be put into test configurations, where different parts of the signal chain may analyzed. Figure 2 shows lines that may be activated for DAC settling time testing or DAC output voltage testing. Figure 2 also shows a test shift register with a buffered output. The test shift register may be used to test the drive capability of each column buffer and to verify the current draw through any particular unit cell.3.TEST SET-UP AND CONDITIONS3.1. General DescriptionAll initial MIRAGE RIIC characterization testing was performed at the wafer level. A probe card was used to make electrical contact with the RIIC bonding pads. This approach to characterization allowed much of the work done on initial design verification to be easily incorporated into the wafer probe screen testing of RIIC’s for emitter array production. Testing was performed in a portable clean room at room temperature. Data was acquired by measuring the output from the various RIIC test points and by measuring the RIIC inputs during operation to find current draw or determine if proper operating voltages were maintained. Measurements were stored in either electronic format or in a laboratory notebook.3.2.Test EquipmentTable 1 lists the equipment used during characterization testing.Item Part # / Serial #Test Station #2N/AElectroglas Prober (8 in.)2001XVXI Interface Card– Indigo Custom250-0003-09 Rev 1.0 / 0004HP Switcher3488A / 245389212Probe Card – Indigo Custom250-0002-09 Rev 1.0 / 0002Fluke DMM77 / Any in labTektronix Oscilloscope TDS 754C /HP Parameter Analyzer4145A / 2515J02393Probe Card Jumper List & Supplements N/ATable 1. RIIC characterization test equipment3.2.1.Test Station DescriptionThe test station used for characterization testing is one of three identical test stations designed to allow flexible characterization and production testing of mixed signal integrated circuits. The primary components of the test station are programmable power supplies, a timing generator, a switch matrix, a precision volt/current meter, and an analog to digital converter. These test station components are all connected and controlled by a VXI backplane, allowing computer interface control.4.CHARACTERIZATION TEST RESULTSCharacterization testing for the MIRAGE RIIC can be divided into three general areas of investigation: verification of functionality, signal chain measurements, and miscellaneous testing. Verification of functionality consists of measurement of current draw on the various bias supplies, and the verification of proper response to input timing and proper operation of RIIC logic for selecting the various operating modes. The signal chain measurements consist of DAC output voltage measurements, DAC settling time, column buffer output measurements, and unit cell current measurements. Other measurements include characterization of the on-chip temperature sensors and measurement of the electrical resistance of the current return path through the RIIC substrate.4.1.RIIC timing and logicThe timing and logic are verified by direct and indirect means. The row and column shift registers have test outputs that can be monitored. Timing that is sent to the RIIC clock input pads will result in signals that come out on the test inputs. This verifies that timing is reaching the shift registers properly. Additionally, changes in the timing will affect the operation of the RIIC. When these changes are made and the RIIC performs as expected, the logic is verified. The types of changes made include changing the number of “dead” clocks at the end of a line of timing, performing a frame reset before a full frame has been clocked out, and increasing or decreasing the pixel clock frequency.For all of these tests, the RIIC operated exactly as expected. During the course of this aspect of characterization, the logic was verified over frame rates from 1 Hz to over 200 Hz. The operating modes of the RIIC were also verified. This verification was an integral part of the overall characterization, since many of the possible operating modes allow the RIIC to operate in a specific test output mode. Table 2 summarizes the results of these verification tests.Function Pass / FailFrame reset PassRow shift register PassColumn shift register PassPixel clock PassMode bits 0-5PassTest shift register PassTable 2. Summary of test results for timing and logic verification4.2.Current draw measurementsCurrent draw is a critical test of general RIIC functionality. Insufficient current on a particular bias line can indicate a design problem or the potential for decreased output levels in an otherwise functional design. Greatly increased power draw on a specific bias voltage can indicate an IC processing defect that results in a short circuit between power supply lines and their returns. Power draw on the VDACPOS, VPOS, and VPD bias lines were measured and fell within the expected range based on initial simulations. While the primary purpose of characterization testing is IC design validation, some data was also obtained on failure rates. Measurements on the first wafer (44 die) show no current draw failures, indicating that the fabrication process at the foundry has very low defect levels.Bias Voltage Name Simulation Current Measured Pass / FailVDACPOS< 200 mA140 mA ± 20 mA PassVPOS & VPD< 30 mA20 mA ± 5 mA PassTable 3. Comparison between measured current values and initial RIIC simulations4.3.Temperature sensor characterizationThe RIIC has two temperature sensors located on opposite sides of the IC. These temperature sensors will be used to maintain a stable emitter substrate operating temperature. This is a critical feature of the RIIC, since emitter fill factor of roughly 50%, allows the substrate temperature to contribute to the overall radiance of the generated scene. Both temperature sensors are functional and have output that can be used for temperature control. The plot of temperature versus output voltage shows that the output is linear as expected and has a gain of -6 mV/ °C. This gain is somewhat lower than the expected value of –8 mV/ °C obtained through simulation, but it is within tolerances associated with this part of the IC design. More importantly, the temperature sensor will serve its purpose as part of the MIRAGE emitter substrate temperature control circuit. Figure 1 shows a plot of the temperature sensor output as a function of the wafer temperature. The dotted line is a least squares fit to those data points. The line’s equation shows a slope of -6.1 mV/ °C.Figure 3. Graph of temperature sensor output voltage versus RIIC temperature4.4.Resistance of current return pathThe emitter current return path runs from the emitter return leg, down into the RIIC active circuitry, and out through the RIIC silicon substrate. The exact resistance is an important aspect of the design, since it determines how much of the voltage drop in the emitter drive current will occur in the emitter and how much will occur in the RIIC substrate. Initial modeling of the resistance indicated a value of roughly 1000 ohms per unit cell. Measurement of this value across 5 die on wafer # 1 resulted in an average value of 675 ohms. This value will allow even more of the emitter drive power than was initially modeled, to be dissipated in the emitter, resulting in slightly higher maximum temperatures.4.5.DAC output voltage measurementsThe RIIC has two 16 bit on-chip digital to analog converters (DAC’s) that take as input a 16 bit word from the scene generation hardware and output a voltage that is used to drive individual emitters. Two test pads on the RIIC allow the output from each DAC to be characterized. Several aspects of the output were measured, including output voltage range, DAC bit steps, and a qualitative assessment of linearity4.5.1.Output Voltage Range and LinearityThe output voltage range was predicted to be 0.5 to 3.55 volts. This range is a nominal value since there is also on-chip adjustment for the DAC current (which affects the output range) and DAC offset level. The output range for every RIIC die measured was either within the nominal range with no adjustment required or could easily be adjusted to fit within the nominal range. Figure 4 below shows a DAC’s output voltage response to an input voltage ramp. The total output range for this DAC is shown to be 0.61 to 3.57 volts and is typical of the output response to an input ramp. The linearity of the output can also be seen in this plot. A coarse examination of the output plot shows a slight deviation from a straight line at the upper end of the range. This output corresponds to the expected output generated by the simulation.One deviation from the simulation that was noted and investigated was an offset of 0.2 – 0.3 volts between the right and left DAC outputs. With normal grounding via the two VSUB pads, the right DAC output’s zero level (all bits zero) was lower than the left DAC. The total dynamic range was typically 0.1 volts greater for the right DAC. Experiments in which one or the other VSUB grounds was removed yielded inconclusive results except that grounding seems to be at the heart of this anomaly. It is thought that the VSUB ground used during operation will eliminate this offset effect. If the effect remains, it will result in roughly a 10% reduction in system dynamic range.Figure 4. DAC output response to input data ramp4.5.2.DAC Bit MeasurementsIn addition to the ramp, each bit of the DAC was enabled singly (that bit on and all the others off) and that level was programmed into the DAC for an entire row of output. This was done to determine that all the bits were present, to compare the bit step sizes, and to verify that the upper 8 bits and the lower 8 bits overlapped in output level. The overlapping of the upper and lower bits was an intentional aspect of the design. Figure 5 shows the stair step output of the upper bits toggled singly. Also visible in figure 5 is the beginning of the voltage ramp. The lower 8 bits are in the output but can not be resolved in this plot. Figure 6 shows the overlap in output range between the lower 8 bits and the upper 8 bits. Figure 7 shows the lowest 6 bits in the DAC output range. The LSB level in this test is only settled for a short time. Figure8 resolves the LSB level better by programming that level into the middle of the output of bit nine.4.6.DAC settling timeDAC settling time is an important aspect of the RIIC performance since the settling time places an upper limit on the fastest frame rate that can be displayed by the MIRAGE system. Based on a design goal of 200 Hz, the rise time and fall times for the DAC need to be less than 37 nanoseconds. The measured values for the rise and fall times were 19 and 18 nanoseconds respectively. Figures 9 and 10 show the DAC rise and fall time for a transition between the maximum output level and the minimum output level. While there is considerable noise on the signal, the transition is clearly visible for both measurements.Figure 5. Each bit toggled singly Figure 6. Overlap between upper and lower 8 bitsFigure 7. Lowest six bits resolved Figure 8. LSB bit enabled on top of bit 9Figure 9. DAC rise timeFigure 10. DAC fall timeLSB Bit toggledon here.4.7.Column buffer output measurementsThe buffers that drive the DAC voltage signal up the column bus lines can be tested by using the COLOUTTST test pad on the RIIC. By placing the RIIC into the column test mode and monitoring the output of this test pad, the next step in the signal path can be characterized. The output range of these buffers was measured by sending a DAC signal of maximum to every buffer and then the minimum value to each buffer. The offset between the left and right DAC outputs was again noticed in this test. The signal difference was compared to the simulation and was within the range of values expected for that part of the circuit. This test will also be used to screen die for column buffer defects during production testing. Figure 11 shows the output for the full column test that exercises all 1024 of the buffer amplifiers. Figure 12 shows the output for the first several column buffers. The sixth buffer shows a reduced output level of roughly 0.25 volts, indicating a problem with that channel. This type of defect was only observed on one die during initial characterization testingFigure 11. Column buffers show expected dynamic range Figure 12. Sixth column, odd row, buffer shows output variation. 4.8.Unit cell current measurementsThe RIIC unit cell test mode allows current to be passed through a test transistor (instead of an emitter). This test allows a measurement of the full scale current draw in the unit cell. This is an important measurement, since the current through the unit cell must not limit the voltage that can be applied to the emitter. The nominal value for this current draw is roughly 100 micro-amps of current. During production testing, this current test can be applied to every unit cell to verify proper function and ensure high emitter operability. For characterization testing, this value was measured for individual pixels to validate the design. The measured value for the current was 96 microamps. This value is close to the 100 microamps and sufficiently validates the design. Additionally, the exact current in the unit cell can be changed through a unit cell current adjustment pad on the RIIC. Figure 13 shows the current demand full scale range of roughly 96 mV. In this measurement, one millivolt corresponds to one microamp of current.4.9.Constant current verificationIn most operating scenarios, the RIIC will be operated in constant current mode as described in section 2.2. However, under probe test conditions, testing the constant power mode is not practical due to limitations in heat sinking and in supplying the required current. The verification of constant current was made by integrating an RIIC die onto a specially designed fanout board, allowing the necessary heat sinking and supplying a low impedance path for the required current. As simulated, the RIIC draws 30 amps of current when operated in constant current mode.Figure 13. Current draw (96 millivolts = 96 microamps)4.10. Operability of engineering lotThe MIRAGE RIIC design was fabricated on 8-inch wafers at containing 44 die per wafer. An initial engineering lot of five wafers was made in the first production run. Each die was tested for proper current draw, DAC operability, and column buffer full scale range. The yield for these first wafers was 87%, resulting in 192 usable die out of 220 possible. The most common defect was a failure of one or more column buffers to pass the full scale swing requirement.5.CONCLUSIONThe MIRAGE RIIC is very different from previous RIIC designs because of its all digital interface and unique constant current operating capacity. Characterization of the design provided the needed confidence to begin work on emitter array fabrication. This work is proceeding. The data gathered during characterization testing on DAC settling time provides assurance that system level design decisions to operate up to 200 Hz are in line with expected performance. Data gathered on the temperature sensor output has been valuable as a verification tool for interim system level integration. Subsequent data on operability provides confidence that the present design is producible and could easily be scaled to larger devices without jeopardizing RIIC yield.REFERENCES1.R. Lane, J. Heath, Innovations in IR Scene Simulator Design, SPIE Vol. 3368, p. 78-87, Orlando, Florida, 1998.。