TnPM 基础知识 ppt课件
TNPM-全员规范化生产维修知识讲座

解决方案 --规范 SOLUTION ------ NORMALIZATION
3 Regulation: can be changed to meet the requirement of TPM. In other words, if the operator maintain the equipment according to the normalization, then the regulation permits.
company or trans-trade, standard is true to every company. 2 Normalization is dynamic and changeable, the normalization can be alternated along with the progress of personnel and equipment. However, the standard is stable in a longer period.
3 制度:制度当然可以改变以适应TPM的
需要。也就是说,只要按照规范执行, 制度就是支持(允许)的。
The difference between normalization and standard
规范与标准有什么不同?
1 规范是企业内部规定,不同企业可以有所不同。而标 准则是跨行业、跨企业的。 2 规范是动态可调的,应随设备进步,人员素质进步及 时加以调整。标准则有相对较长时间的稳定性。 1 Normalization is the inner regulation, different companies may have different normalization. However, standard is trans-
TnPM知识培训
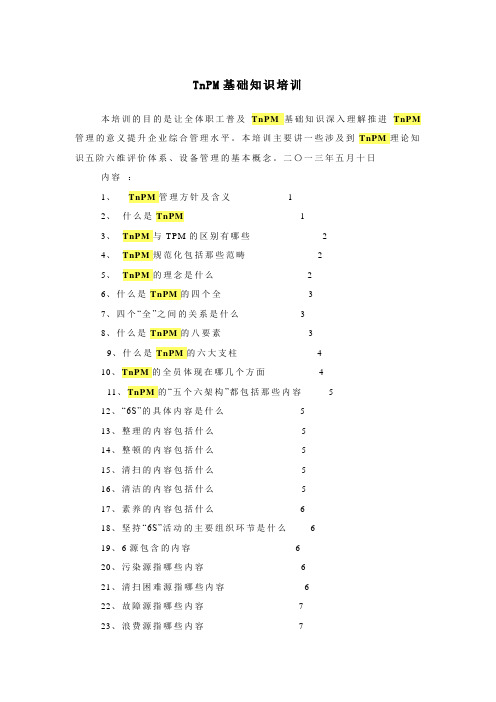
TnPM基础知识培训本培训的目的是让全体职工普及TnPM基础知识深入理解推进TnPM 管理的意义提升企业综合管理水平。
本培训主要讲一些涉及到TnPM理论知识五阶六维评价体系、设备管理的基本概念。
二〇一三年五月十日内容:1、TnPM管理方针及含义 (1)2、什么是TnPM (1)3、TnPM与TPM的区别有哪些 (2)4、TnPM规范化包括那些范畴 (2)5、TnPM的理念是什么 (2)6、什么是TnPM的四个全 (3)7、四个“全”之间的关系是什么 (3)8、什么是TnPM的八要素 (3)9、什么是TnPM的六大支柱 (4)10、TnPM的全员体现在哪几个方面 (4)11、TnPM的“五个六架构”都包括那些内容 (5)12、“6S”的具体内容是什么 (5)13、整理的内容包括什么 (5)14、整顿的内容包括什么 (5)15、清扫的内容包括什么 (5)16、清洁的内容包括什么 (5)17、素养的内容包括什么 (6)18、坚持“6S”活动的主要组织环节是什么 (6)19、6源包含的内容 (6)20、污染源指哪些内容 (6)21、清扫困难源指哪些内容 (6)22、故障源指哪些内容 (7)23、浪费源指哪些内容 (7)24、缺陷源具体指哪些内容 (8)25、危险源具体指哪些内容 (8)26、TnPM的6S活动和6H活动如何结合 (9)27、“6I”是什么及其内容 (9)28、“6Z”是什么其内容包括那几点 (10)29、“6T”是什么及其包含的内容 (10)30、什么是TnPM五阶六维 (10)31、引入TnPM五阶六维体系的意义 (11)32、什么是TnPM五阶六维评价体系的五阶 (11)33、什么是TnPM五阶六维评价体系的六维 (12)34、TnPM的五阶六维评价体系五阶的划分 (12)35、TnPM推进的三个阶段如何划分 (12)36、生产现场作业规范四位一体及六步闭环体系图··1337、什么是自主维修体系 (13)38、TnPM自主维修的七个步骤是什么 (13)39、什么是点检定修 (14)40、点检定修制四项标准是什么 (14)41、什么是点检标准“六定” (14)42、实施点检包括哪五步 (15)43、什么是设备润滑的“五定” (15)44、PDCA循环过程中的PDCA指什么 (15)45、什么是单点课 (15)46、单点课程可以包括哪些内容 (15)47、单点课教材的要点是什么 (15)48、OPL闭环管理体系包括哪几个环节 (15)49、现场管理四要素 (15)50、什么是TnPM推进八大忌 (16)TnPM知识问答:1、TnPM管理方针及含义方针:全员参与规范管理全面实现设备健康稳定运行含义全员参与规范管理是指厂全体职工按照《五阶六维千分评价体系》中的要求全过程、全面、规范地参与设备的各项管理活动做到事事有章可循并体现不断改善的过程全面实现设备健康稳定运行就是以TnPM管理为主线全面提升设备管理水平从而实现设备健康运行的最佳状态。
《TnPM知识培训》课件

TnPM知识培训将帮助您深入了解TnPM(Total Network Performance Management),它的应用场景以及在各行业中的价值和意义。
一、介绍
什么是TnPM?TnPM(Total Network Performance Management)是一种集成的 网络性能管理解决方案,用于监控和优化大规模网络的性能和可用性。
五、总结和展望
TnPM的未来发展方向
探索新的技术和方法,提升TnPM 的功能和性能,以应对不断变化 程,从传统的 网络管理到现代的网络性能监控 和优化。
TnPM的市场前景
评估TnPM在不同行业中的应用前 景,为企业决策者提供参考依据。
三、TnPM数据分析和监控
1
TnPM的运行状态监控
通过实时监测网络的各项指标,识别和解决潜在的问题,确保网络稳定运行。
2
TnPM的性能和容量分析
分析网络的性能和容量使用情况,识别瓶颈和优化机会,提升网络效能。
3
TnPM的故障诊断和排除
利用TnPM提供的故障诊断工具,快速识别和排除网络故障,减少服务中断时间。
TnPM的数据流
数据从数据收集节点传输到性能分析节点进行处 理和分析,然后提供给管理节点进行监控和报告。
TnPM的关键模块介绍
包括性能监控、故障诊断、容量规划和性能优化 等关键模块,帮助企业进行全面的网络性能管理。
TnPM的安装和配置
了解如何安装、配置和初始化TnPM系统,以便 能够有效地进行网络性能管理。
TnPM的应用场景广泛,涵盖了电信、金融、物流等行业,在提高网络效能、 故障排除和性能优化方面发挥重要作用。 TnPM的价值和意义在于提供实时监控、数据分析和故障诊断能力,帮助企业 确保网络正常运行并优化业务流程。
TnPM
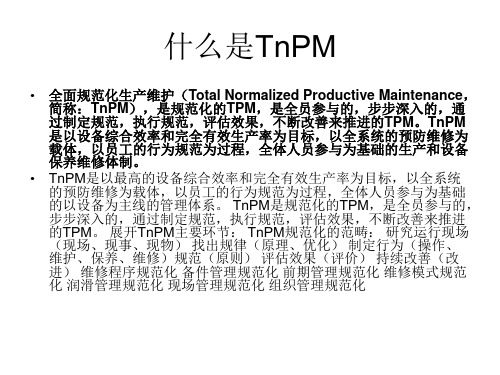
目录
– 一.TnPM体系要素
– – – – – (一)TnPM八个要素 (二)TnPM四个“全” (三)TnPM五个“六” (四)SOON模式 (五)FROG体系
– – – –
二.TnPM体系推进流程 三.TnPM规范化体系与其它标准化体系的关系 四.TnPM对JIT准时生产 五 TnPM对 6σ管理的支持
• (二)TnPM四个“全” • 1. 以设备综合效率和完全有效生产率为目 标 • 2. 以全系统的预防维修体制为载体 • 3. 以员工的行为全规范化为过程 • 4. 以全体人员参与为基础
• • • • • • • • • • • • • • • • • • • • • • • • • • • • • •
• • • • 图1-1 SOON 体系框架 这是一套比较严密的设备防护体系设计。首先,根据不同设备类型及设 备的不同役龄,选择不同的维修策略;然后通过现场的信息收集,包括依赖 人类五感的点巡检、依靠仪器仪表的状态检测以及依赖诊断工具箱的逻辑推 理,以此对设备状况和故障倾向进行管理;下一步是维修活动的组织, 包括 维修组织结构设计、维修资源的配置等;最后是维修行为的规范和维修质量 的评价。宝钢的点检——定修和作业长制就包含在 SOON体系的两个 O中。
• •
• • • • • • • • • •
(八)第七步以规范化为主线,创建样板机台 在生产现场建立“设备工艺作业规范”和“清扫点检维护保养作业规范”两个作业指导书;在 维修部门建立“设备维修作业规范”和“设备点巡检作业规范”两个作业指导书;其他部门建立相 应的作业规范,形成事事讲究,规范一切,一切规范的管理体系。规范从选择的样板机台(装置) 开始,样板的选择注意典型、带动性和机台责任者的参与热情。 (九)第八步样板示范,全面推广 领导主持样板机台的示范和推广会,以点带面,促进全公司规范化体系的建立。与此同时,设 备管理与维修部门开始进行 SOON 体系的总体设计,包括维修模式的选择、资源配置比例的确定、 流程组合维修模式设计以及相关管理流程策划。 (十) 第九步现场改善、合理化提案和 OPL活动 设计改善合理化提案和员工“单点课程” (OPL)的管理闭环流程,调动员工的参与意识,深 入挖掘员工的智力资源。 (十一) 第十步展开“员工未来能力持续成长”活动——FROG 通过员工能力分析、成长约束分析、积极思维的引导、自我成长计划、四维培训计划以及单点 课程体系的建立,让员工同企业一同成长。 (十二)第十一步建立TnPM考核评估体系和激励机制 全面设计变权的 TnPM绩效考核评估体系,依此建立员工激励机制,以变化的权重引导 TnPM 的良性发展。 (十三)第十二步与其他标准化体系衔接 将TnPM与企业相应的质量、安全、环境与健康标准化体系衔接,将TnPM的相应文件融入各类 标准化文件,与各类标准化体系无缝连接。同时建立以设备为中心的五阶评价体系。总结第一阶段 推进成绩和经验,制订新目标和新计划,总结第一阶段成果,表彰先进团队,研究经验教训和改善 之处,制定新目标和新计划。
TnPM理论知识

精益求精 持续改善
TnPM推进组·价值流优化专业委员会
精益生产就是识别和消除浪费,保留价值活动
Identification and Elimination of Waste
精益生产就是识别和消除浪费
➢ 消除浪费可以有效降低成本 –精益生产方式的特征
➢ 消除浪费的前提在于是否发现浪费 –目视管理可以有效发现浪费 –思维方式的逆转可以有效发现浪费
TnPM
全面生产性维护(TnPM)
TnPM推进组 2015.03
绪论 价值流改善与TnPM
精益求精 持续改善
TnPM推进组·价值流优化专业委员会
企业经营的目的是什么?
制造产品?
制造利润?
如何获得最大的利润是企业运行的
头等大事!!!
精益求精 持续改善
TnPM推进组·价值流优化专业委员会
不同时期,企业对获得利润的思考方法
❖ 1960年前后,工业技术不断进步,人们开始需要不发生故障的设备。维护从设计、制 作、安装开始—— MP维修预防 (Maintenance Prevention)。
❖ 1960年后,美国GE公司综合上述保全方法,提出一套系统的保全方案,即TPM的前 身PM——PM生产维修 (Productive maintenance)。
1. 故障的损失
设备失效需要执行维护操作。其原因有:
–机器过载 –过渡磨损 –污染物
-螺钉和螺帽松开 -缺少润滑油
3. 启动/停机的损失
设备从静态到正常运行所需要的时间。 其原因有:
–设备要平缓加速/降速 –设备升温到设定温度
2. 更换品种/设置/调整的损失
从一种产品(批次)到另一种产品
(批次)换产的时间损失,或运行时对设
中国企业之TnPM-巡讲课件4

纳入状态维修 策略的设备 专业维修团队 关键设备 点巡检标准
状态值读数定义及 监测手段
实际读数异常 触发
异常汇总 滚动台帐 分析 诊断
车间维修组工作重点
检修计划清单 点巡检 运行单 异常 报告单
改造计划清单 视需要 参与
纳入事后维修 策略的设备
广州学府设备管理工程顾问有限公司
美国民航在过去30年间,做了大量关于设备可靠性的研究,发现在设备从使用到淘汰, 故障特征曲线呈6种不同形状:
导入最符合中国企业的TnPM——全面规范化生产维护管理模式
广州学府设备管理工程顾问有限公司
例
S-维修策略
TnPM设备检维修体系的工作流程
超过能力范围 操作运行人员 清扫点检 维保 运行表 异常 纳入六 源管理 案例 集
OPL
维修 资源 车间 技术员 备件资材 计划 车间 维修组
维 修 预 防 -MP 闭 环
小问题,自主维护解决
O-现场 信息收 集分析
视需要修订原有维修策略
故障逻辑分 析方法和维 修知识库
PPM DV
厂内外 协-机修 社会外 协-委外
每日检修例会、设备技术鉴定、检修现场管理、验收管理 检修总结分析
修中管理 修后管理
导入最符合中国企业的TnPM——全面规范化生产维护管理模式
广州学府设备管理工程顾问有限公司
检修前期工作流程
装置停工前 120天 装置停工前 110天 装置停工前 100天 装置停工前 90天 装置停工前 60天 装置停工前 30天 装置停工前 20天
广州学府设备管理工程顾问有限公司
导入最符合中国企业的TnPM——全面规范化生产维护管理模式
TnPM知识培训ppt课件

四阶
员工有责任感,能够执行操作、保养规范,能够积极参与6S与清除六源活动, 工作主动,踊跃参与提案活动,有系统培训,OPL活跃开展,开始有自主维修。
五阶
员工有责任感,能够自觉执行操作、保养规范,能够积极参与6S与清除六源 活动,工作主动,踊跃参与提案活动,有五维系统培训,OPL活跃、广泛 开展,自主维修比较活跃。
5
利益4
通过 OPS(合理化建议), 使员工的智慧和潜能 得到发掘,能为组织
带来多方面的效益,且 能提高员工的工作 热情,使员工有 成就感。
TnPM知识培训
6
利益5
通过设备一生的规范化 管理,可减少设备前期 管理失误,减少设备使用 中的故障,使设备更好
服务于生产。
TnPM知识培训
7
利益6
通过设备检维修系统解决 方案设计,使设备的维修策略 科学化,设备信息采集和诊断 灵活化、有效化,维修组织 和资源配置合理化,维修行为 规范化。进一步达到提高检修
TnPM知识培训
32
5.2 设备信息与知识资产管理五阶评价标准
设备信息与知识资产管理评价阶梯:
一阶
有基本计算机管理,但尚未达到内部联网管理,管理的设备及维修信息领域 不完全,且单机运行,缺乏对外部设备信息的计算机管理,对企业内部与
外部的知识资产管理尚未提到议事日程。
二阶
内部联网进行计算机管理,能对大部分设备与维修信息领域进行管理,缺乏对外部 设备相关信息的计算机管理,对企业内部与外部的知识资产管理尚未提到议事日程。
一阶
公司有部分操作、保养和维修规范,缺乏建立规范的指南,无闭环管理流 程,规范结构本身不完善,覆盖领域不完全,员工不认同,执行不到位。
二阶 三阶
公司有操作、保养和维修规范,形成了规范指南,闭环管理流程不完善, 规范本身结构基本合理,覆盖领域不完全,员工不够认同,执行不理想。
TNPM全面生产维护系统(共44张)

Grease,Multipurpose grease or equivalent Heat-resistance Grease Lens cleaner and lens cleaning paper Pre-Scale paper
4. Categories of preventive Maintenance The preventative maintenance in general is classified into:
Philips MDS
7
第7页,共44页。
PvM: Preventive Maintenance (预防(yùfáng)保养)
预防保养: 是指依计划实施点检、调查让设备
在故障轻微,甚至异常发生前即予以预防。包括设备 的调整、清扫、修理等。若以实际作业来区分,则可
以分为定期和预知保养两类。
Philips MDS
计成免保(Maintenance Free)。
Philips MDS
16
第16页,共44页。
2、预防(yùfáng)保养:
(同上)
Philips MDS
17
第17页,共44页。
3、改良(gǎiliáng)保养:
( Corrective Maintenance, 简称 C.M.) : 针对设备本体改良,以提高信赖度及易维护性。
B
B
B
B
B
SA756-20
OSAKI * *
B
B
B
B
B
B
B
SA756-21
PHILIPS * *
B
B
B
B
B
B
B
SA756-22
PHILIPS * *
- 1、下载文档前请自行甄别文档内容的完整性,平台不提供额外的编辑、内容补充、找答案等附加服务。
- 2、"仅部分预览"的文档,不可在线预览部分如存在完整性等问题,可反馈申请退款(可完整预览的文档不适用该条件!)。
- 3、如文档侵犯您的权益,请联系客服反馈,我们会尽快为您处理(人工客服工作时间:9:00-18:30)。
常用方法:中医理论-望闻问切
听、摸、闻、看
ppt课件
15
2.2
自主保全-7步骤
ppt课件
16
2.2 自主保全-自主保全基准书
车间通过初期清扫、两源改 善等活动,大家积极参与编写 “自主保全基准书”截止2016 年底共编制23份自主保全基准书, 其中: ◆初制车间:6份 ◆提取车间:9份 ◆包装车间:8份 右图:提取设备自主保全基准书
有现场部门重视 5S,可以潜移默
化影响人。
循序渐进---从基础作起 基石一:彻底的5S活动
全员参与---从基层作起 基石二:岗位重复小组活动
ppt课件
7
TnPM思想
TnPM = PM + ZD + SG
预防 哲学
“0” 目标
小组 活动
预防哲学(Preventive Maintenance) 确立预防的条件(分析问题,防止未然) 排除物理性、心理性缺陷 排除强制劣化 消灭慢性不良 延长原有寿命 “0”目标(Zero Defect) 如果追求“0”的目标在竞争中一定会胜利 如果同行也追求“0”那么速度是胜败的关键 全员参与经营(Small Group Activity) 提高组织成员的能力 组织成果的最大化
以专业维修人员为主,对设备和工装依据特定的针对性计划,凭 借专业技术和工具,对设备进行保养、检查、更换、校准、恢复、 改善等一系列活动。
计划保全形式:
ppt课件
20
2.3 计划保全-开展步骤
STEP 计划保全(重要零部件样板)
1 重点零部件的选定
2 现状保全方法的改善 3 保全基准的做成 4 寿命延长,弱点对策 5 点检,诊断的效率化 6 设备综合诊断 7 设备的极限使用
ppt课件
9
TnPM的框架 世界最高竞争力公司
目标“0”化
八 大 活 动
两大基石
□ 创造高效率生产系统 □ 培养设备专家级操作员工 □ 保养员的专业化(电器/机械)
零故障, 零不良, 零灾害, 零废弃
个 自 计 教 初 品事环 别 主 划 育 期 质务境 改 保 保 训 管 保改安 善 养 养 练 理 养善全
Total Productive Management新的TPM TnPM(1998)
Total Progressive Movement
现代的TPM
ppt课件
4
TnPM发展关键节点
■ TPM起源于美国,发展完善于日本。 ■ 1998 年,李葆文教授将TPM的精髓与中国实际结合,提出了 规范化的全面生产性维护的理论体系。 ■ 2000年开始,TPM已经跨行业国际化发展 。TPM并不是只 属于日本的产业界,世界各地对TPM的关心逐年升高。这时也 不是在某个企业实施,它逐渐向服务、流通等行业发展,逐步 优化供应链系统。
ppt课件
5
1.2 TnPM的定义及内涵
全面规范化生产维护 (Total Normalized Productive Maintenance, 简称:TnPM),是规范化的TPM,是全员参与的, 步步深入的,通过制定规范,执行规范,评估效果, 不断改善来推进的TPM。
ppt课件
6
TnPM两大基石
计划保全(设备样板) 推进内容
基本条件及现状 的差异分析
制作设备账目及维护 现象把握 设备评价实施 设定保全目标 故障等级定义及设定
基本条件及现状 的差异对策
基本条件整理 防止类似事故的再发 薄弱点改善及延长寿命
ppt课件
12
2.1 保全基础知识-零故障思维
设备的故障是人为引起的 改变人的的思考方式或行动,就能实现设备零故障
旧的思考方式
设备必然会故障
R/M努力消除故障
新的思考方式
设备可以零故障
ppt课件
全员消除缺陷
13
2.1 保全基础知识-故障分类
故障
自然劣化
(固有寿命)
强制劣化
(人为劣化)
延长寿命
计划保全
①提高操作性防止失误 ②提高保全及修理水准 ③提高安全性及信赖性
排除要因
自主保全
①清扫:灰尘、污染 ②加油:错油、缺油 ③紧固:螺帽等脱落
ppt课件
14
2.2 自主保全-定义及内容
自主保全:
由设备操作者自主进行的防止设备人为劣化的维护活动。
活动内容: 1、防止劣化(清扫、加油、紧固等) 2、对劣化进行测定(点检) 3、对劣化进行复原(异常处理)
ppt课件
17
2.2
自主保全-改善案例
案例1: 在设备缝隙处安装有机玻璃板防止粉尘落入,保持清洁。
改善前
F: 11
ppt课件
F:12
改善后
18
2.2
自主保全-改善案例
案例2: xx包装机加热线管由硬质胶管改为软连接,既减少磨损又美观。
改善前
ppt课件
改善后
19
2.3 计划保全-定义及内容
计划保全活动:
ppt课件
8
TnPM理念
改善人的体质 改善设备的体质 改善环境的体质
1、设备操作者:自主维修能力。
2、维修技术人员:消除事实故障的预防 性维修规划和改进能力。
1、现有设备:解决设备LOSS,效率最大化。
2、新增设备:生产能力最快速度的爬升。
1、设备环境:改善运行环境,消除强制劣化。 2、人员环境:改善人员操作环境和安全 条件,实现人机协调和谐。
预防故障
PM—预防保全 Preventive Maintenance
设计设备
MP—保全预防 Maintenance Prevention
综合保全
PM—生产保全 Productive Maintenance
生产人员参与保全 整个集团的效率改善 追求创新的活动
旧的TPM Total Productive Maintenance
全面生产性维护
ppt课件
1
第一讲:TnPM概论
第二讲:设备保全
目 录
第三讲:个别改善
第四讲:工具应用
第五讲:注意事项
ppt课件
2
1
TnPM概论
ppt课件
3
1.1 TnPM发展演变史
1950 1960 1970 1980 1990 2000
修理为主 改进设备
BM—事后保全 Break down Maintenance CM—改良保全 Corrective Maintenance
重复性小组活动 彻底的5S活动
ppt课件
企业的 体质改善
现场的 体质改善
人员的 体质改善
10
2
设备保全
ppt课件
11
2.1 保全基础知识-缺陷成长理论
设备在故障和劣化前已经有很多迹象表现出来了,
即缺陷。
明显 缺陷
大缺陷(故障)
潜在 缺陷
中缺陷 微缺陷
* 即使大缺陷没有, 但缺陷还在成长 (小缺陷 --> 中缺陷 --> 大缺陷的顺序)