试述智能炼钢技术在120吨转炉上的研究与应用
转炉智能化炼钢技术应用问题探讨

转炉智能化炼钢技术应用问题探讨摘要:本文主要阐述在智能化炼钢技术开发过程遇到的瓶颈问题,通过调试和试验,优化管理,从硬件和软件方面采取有效措施,解决了各工序存在的问题,最终实现了智能化炼钢技术,对后续各钢铁企业加快智能化炼钢技术应用步伐起到指导作用。
关键词:智能化炼钢动态控制一键炼钢动态冶炼模型技术应用背景:氧气顶吹转炉炼钢目前已成为世界上主要的炼钢方法。
其冶炼特点是炉内反应速度快,冶炼周期短,影响因素多而反应复杂,人工操作控制不稳定。
国外从60年代开始就采用了计算机控制,到70年代已从静态控制发展为动态控制,吹炼终点的命中率目前已达到90%以上。
在国内,除宝钢、首钢等少数转炉采用计算机动态控制外,大多数钢企转炉的控制水平还比较低。
陕西龙门钢铁有限责任公司为提高企业自动化、智能化控制水平,2019年初开始筹备智能化炼钢技术开发,作为重要研究课题与镭目公司合作开发此技术,为后续实现转炉一键炼钢技术奠定基础。
1.现状:目前龙钢公司转炉冶炼过程均为人工利用经验判断进行操作,操作稳定性受外界因素影响较大,加之废钢料型种类多达10种,控制过程波动性大,冶炼周期不稳定,关键经济技术指标提升空间受限,同时龙钢炼钢自动化程度较先进钢厂已经有一定差距,靠人工经验炼钢已经处于瓶颈期。
智能化炼钢技术的研究,可以实现生产、成本、技术上的新突破,利用先进的检测手段,收集大数据背后的隐形效益,降低生产制造成本,提高转炉作业效率,可为今后开展洁净、环保、低耗的生产制造工艺奠定基础,提升企业智能化水平,提高企业知名度。
2.技术路线:通过大数据的收集和分析,结合现场操作建立不同原料条件下的静态冶炼模型,在实际生产过程继续进行模型优化、固化,利用声呐化渣、烟气分析、高清火焰图像分析系统实时反映炉内渣料熔化、温度控制、碳含量控制、渣厚情况、烟气浓度,实现氧枪智能控制和加料智能控制的智能化自动操作和动态调整,终点预测熔池钢水成分、温度情况,根据设定终点目标智能控制冶炼全过程,终点碳、温度精确命中,同时智能化炼钢系统具有“自学习”引导功能。
转炉自动化炼钢技术应用分析
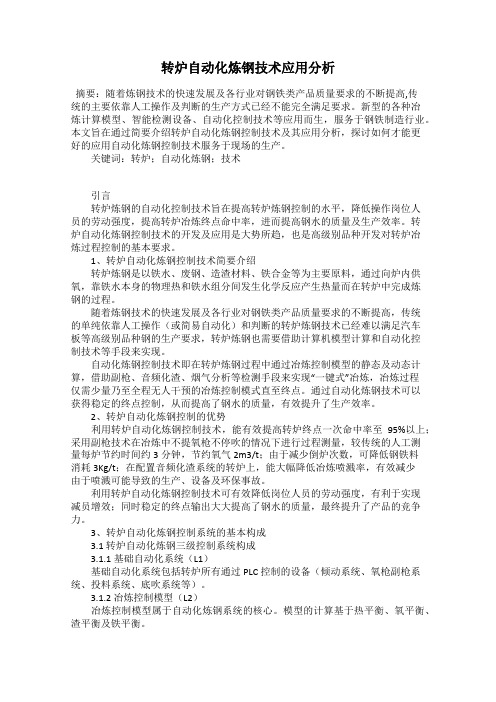
转炉自动化炼钢技术应用分析摘要:随着炼钢技术的快速发展及各行业对钢铁类产品质量要求的不断提高,传统的主要依靠人工操作及判断的生产方式已经不能完全满足要求。
新型的各种冶炼计算模型、智能检测设备、自动化控制技术等应用而生,服务于钢铁制造行业。
本文旨在通过简要介绍转炉自动化炼钢控制技术及其应用分析,探讨如何才能更好的应用自动化炼钢控制技术服务于现场的生产。
关键词:转炉;自动化炼钢;技术引言转炉炼钢的自动化控制技术旨在提高转炉炼钢控制的水平,降低操作岗位人员的劳动强度,提高转炉冶炼终点命中率,进而提高钢水的质量及生产效率。
转炉自动化炼钢控制技术的开发及应用是大势所趋,也是高级别品种开发对转炉冶炼过程控制的基本要求。
1、转炉自动化炼钢控制技术简要介绍转炉炼钢是以铁水、废钢、造渣材料、铁合金等为主要原料,通过向炉内供氧,靠铁水本身的物理热和铁水组分间发生化学反应产生热量而在转炉中完成炼钢的过程。
随着炼钢技术的快速发展及各行业对钢铁类产品质量要求的不断提高,传统的单纯依靠人工操作(或简易自动化)和判断的转炉炼钢技术已经难以满足汽车板等高级别品种钢的生产要求,转炉炼钢也需要借助计算机模型计算和自动化控制技术等手段来实现。
自动化炼钢控制技术即在转炉炼钢过程中通过冶炼控制模型的静态及动态计算,借助副枪、音频化渣、烟气分析等检测手段来实现“一键式”冶炼,冶炼过程仅需少量乃至全程无人干预的冶炼控制模式直至终点。
通过自动化炼钢技术可以获得稳定的终点控制,从而提高了钢水的质量,有效提升了生产效率。
2、转炉自动化炼钢控制的优势利用转炉自动化炼钢控制技术,能有效提高转炉终点一次命中率至95%以上;采用副枪技术在冶炼中不提氧枪不停吹的情况下进行过程测量,较传统的人工测量每炉节约时间约3分钟,节约氧气2m3/t;由于减少倒炉次数,可降低钢铁料消耗3Kg/t;在配置音频化渣系统的转炉上,能大幅降低冶炼喷溅率,有效减少由于喷溅可能导致的生产、设备及环保事故。
解析转炉全封闭智能炼钢技术的开发和应用

解析转炉全封闭智能炼钢技术的开发和应用摘要:随着对转炉炼钢技术要求的提高,全封闭智能炼钢技术的作用日益突出。
文章首先结合实例阐述了智能化炼钢技术的工艺流程,然后就其研发中的不足进行了分析,并提出了相应的解决措施。
关键词:转炉炼钢;全封闭智能化炼钢技术;自动化控制随着工业的发展,钢铁需求量骤增,转炉炼钢技术凭借成本低、产量高、速度快的优势受到高度重视。
为满足新形势的要求,需进一步加强科技炼钢,不断引进新设备和新技术。
人工炼钢效率较低,且容易出现质量问题,从当前的生产力来看,需实现自动化、大规模生产。
计算机的应用推动了智能化技术的进步,使得转炉炼钢科技含量更高,是当前研究的重点,也是未来的必然趋势。
1 实例分析某炼钢厂建于2003年,占地面积37.5万m2,生产的钢材主要有管线钢、普碳钢、大型H型钢、冷轧用钢。
经过两年的发展,在2005年添了4台120 t 的氧气顶底复吹转炉,2台150 t的钢包精炼炉,2台板坯连铸机,以及宽厚板连铸机1台。
年生产量增至4.6×106 t,厂规模也有所扩大,为其带来了更多经济效益。
自2006年起,当地炼钢厂数量逐渐增多,整个钢铁市场竞争加剧,为进一步提高生产效率,必须研发新工艺和新技术,智能化炼钢被高层领导重视。
2008年,该厂从国外引进先进的转炉副枪技术,同时组织技术人员成立科研小组,专攻转炉全封闭智能炼钢技术的研究。
次年取得佳绩,并在1号转炉试验成功。
随后其他3台转炉也相继实现了智能化生产。
近些年来,该厂对智能化生产技术进行了多次改动,日益成熟,为企业的长期发展提供了技术保障。
2 转炉全封闭智能炼钢技术该技术以计算机技术为基础,实现了智能化生产。
通过副枪测量手段,结合相应的静态、动态模型,对钢铁冶炼过程进行全智能化的控制。
依靠计算机系统,可改善人工控制中的很多不足,使得冶炼时间把握更准,对细节也非常重视,有利于提高生产效率和质量。
转炉炼钢的主要原料包括废钢、铁水、铁合金等,采用该技术,转炉操作室接收调度指令后,会自动向废钢、铁水系统发出对应的要求;原料系统根据生产需要合理地进行配比,同时,计算机操作系统自动采集各种原料的信息并加以整理。
自动化炼钢的原理及应用

自动化炼钢的原理及应用自动化炼钢是指利用先进的计算机技术和自动化控制系统,对炼钢生产过程进行智能化、自动化管理和控制的一种技术手段。
它通过实时监测和控制炼钢过程中的各个参数,提高生产效率、产品质量和安全性,降低生产成本,实现炼钢过程的智能化和自动化。
一、自动化炼钢的原理1. 传感器技术:自动化炼钢过程中,通过安装各种传感器,实时监测和采集炉温、氧含量、压力、流量等多个参数的数据。
传感器将这些数据传输给计算机系统,以便进行分析和控制。
2. 控制系统:自动化炼钢过程中,采用先进的控制系统,如PLC(可编程逻辑控制器)、DCS(分布式控制系统)等,对炉温、冶炼时间、添加剂的投入量等进行精确控制。
控制系统根据传感器采集到的数据,通过计算和算法,自动调整各个参数,实现炼钢过程的自动化控制。
3. 数据分析与优化:自动化炼钢过程中,计算机系统会对传感器采集到的数据进行实时分析和处理,利用先进的算法和模型,对炉温、成份、温度梯度等参数进行优化控制。
通过数据分析和优化,可以提高炼钢过程的效率和质量。
二、自动化炼钢的应用1. 提高生产效率:自动化炼钢技术能够实现炼钢过程的实时监测和控制,可以减少人工干预,提高生产效率。
通过自动控制系统对炉温、冶炼时间等参数进行精确控制,可以缩短炼钢周期,提高产量。
2. 提高产品质量:自动化炼钢技术能够实时监测和控制炼钢过程中的各个参数,可以及时发现和纠正生产过程中的异常情况,保证产品的质量稳定性。
通过数据分析和优化,可以提高产品的化学成份均匀性、机械性能等指标。
3. 降低生产成本:自动化炼钢技术可以减少人工干预,降低人工成本。
通过精确控制炉温、冶炼时间等参数,可以减少能源消耗,降低生产成本。
同时,自动化炼钢技术还可以减少废品率,提高资源利用率,进一步降低生产成本。
4. 提高安全性:自动化炼钢技术能够实时监测和控制炼钢过程中的各个参数,可以及时发现和处理生产过程中的安全隐患。
通过自动控制系统对炉温、压力等参数进行精确控制,可以降低事故发生的概率,提高生产安全性。
钢铁冶炼自动化控制系统研究与应用

钢铁冶炼自动化控制系统研究与应用钢铁是现代社会的基础材料之一,也是国家经济发展的重要支柱。
钢铁冶炼过程中的自动化控制系统技术对于提高生产效率、降低生产成本、保证产品质量以及环保等方面具有非常重要的意义和作用。
本文将重点探讨钢铁冶炼自动化控制系统的研究与应用,分析其技术原理和运用效果。
一、钢铁冶炼自动化控制系统的发展历程随着科技的不断进步和工业化程度的提高,钢铁冶炼过程中的自动化控制系统也得到了不断的完善和发展。
从最初的传统的手工操作到现在的全自动化控制系统,钢铁冶炼自动化控制系统经历了一个漫长而又充实的发展历程。
在20世纪60年代,钢铁冶炼自动化控制系统开始应用于炉前自动化、全面自动化操纵等方面。
随着计算机技术的发展和普及,钢铁冶炼自动化控制系统开始向数据化、网络化、智能化的方向发展。
90年代,钢铁冶炼自动化控制系统开始引入模糊控制、神经网络控制等新技术,大大提高了系统的自动化水平和控制精度。
目前,钢铁冶炼自动化控制系统已经实现了覆盖整个生产过程,从原料进厂到成品出厂的全过程实现智能控制和自动化操作,为企业的科学管理和生产运作提供了有力的支持。
二、钢铁冶炼自动化控制系统的原理与技术钢铁冶炼自动化控制系统的基本原理是通过工业控制系统实现对生产过程的自动控制和调节,使得钢铁生产过程工艺参数能够在合适的范围内保持稳定,从而实现高效、稳定、优质的生产运行。
钢铁冶炼自动化控制系统包括机械、电子、传感、计算机、软件等多种技术,其中最主要、最关键的是计算机控制技术。
钢铁冶炼自动化控制系统通过大规模集成电路、模拟量、数字量转换、程序控制器等技术手段将物理量转换成数字信号,通过计算机软件分析和处理后通过控制器对设备进行控制,实现自动化控制。
钢铁冶炼自动化控制系统的技术革新主要集中在以下三个方面:(1)生产线的自动化控制生产线的自动化控制意味着整个生产过程变得更加清晰、高效,生产效率和生产质量得到了有效提升。
自动化控制技术主要包括PLC控制技术、数字逻辑控制技术、信息化控制技术、云计算技术、物联网技术等。
自动化炼钢的原理及应用

自动化炼钢的原理及应用自动化炼钢是指利用计算机技术和自动化控制系统,对炼钢过程中的各个环节进行自动化控制和监测,以提高生产效率、降低生产成本、提高产品质量和安全性。
本文将详细介绍自动化炼钢的原理和应用。
一、自动化炼钢的原理1. 自动化控制系统自动化炼钢的核心是自动化控制系统,它由计算机、传感器、执行机构和监控设备等组成。
传感器用于实时监测炼钢过程中的温度、压力、流量等参数,将数据传输给计算机。
计算机根据预设的控制策略,通过执行机构控制炼钢过程中的各个参数,实现自动化控制。
2. 数据采集与处理自动化炼钢过程中,需要采集大量的数据,包括原料成分、温度、压力、流量等参数。
这些数据经过采集后,通过计算机进行处理和分析,得出相应的控制策略,并将控制信号传递给执行机构,实现对炼钢过程的自动化控制。
3. 控制策略优化自动化炼钢过程中的控制策略需要不断优化,以提高炼钢过程的效率和产品质量。
通过对历史数据的分析和模型建立,可以优化控制策略,并根据实时数据进行调整,以实现更加精确的控制。
二、自动化炼钢的应用1. 炉温控制自动化炼钢系统可以实时监测炉温,并根据设定的温度范围进行控制。
当炉温超过预设范围时,自动化系统可以通过调整燃料供应和风量等参数,实现炉温的自动控制,提高炼钢过程的稳定性和产品质量。
2. 化学成分控制自动化炼钢系统可以对原料的化学成分进行实时监测,并根据产品要求进行自动控制。
通过调整原料供应和添加剂的投入量等参数,可以实现对炼钢过程中的化学成分进行精确控制,提高产品质量的稳定性和一致性。
3. 能耗优化自动化炼钢系统可以通过对炉温、燃料供应和风量等参数进行实时监测和调整,实现能耗的优化。
通过优化炉温控制和燃料利用率,可以降低能耗,提高生产效率和经济效益。
4. 安全监测与报警自动化炼钢系统可以对炼钢过程中的安全参数进行实时监测,并在出现异常情况时进行报警。
例如,当炉温超过安全范围或压力异常时,系统会自动发出报警信号,以保障生产安全。
自动化炼钢的原理及应用

自动化炼钢的原理及应用自动化炼钢是指利用先进的控制系统和自动化设备,实现钢铁生产过程中的自动化操作和控制。
它通过集成和优化各种自动化技术,提高生产效率、质量稳定性和安全性,降低生产成本,实现炼钢过程的智能化和数字化。
一、自动化炼钢的原理1. 传感器技术:自动化炼钢过程中,传感器技术起到了关键作用。
通过安装在设备和生产线上的传感器,可以实时监测和测量各种参数,如温度、压力、流量、浓度等。
传感器将收集到的数据传输给控制系统,从而实现对生产过程的实时监控和控制。
2. 控制系统:自动化炼钢中的控制系统是整个过程的核心。
控制系统可以根据传感器收集到的数据,对炼钢过程中的各种参数进行实时调节和控制。
控制系统一般采用PLC(可编程逻辑控制器)或DCS(分布式控制系统)等技术,具有高度的可编程性和灵活性。
3. 数据处理与分析:自动化炼钢中的数据处理与分析是指对传感器收集到的数据进行处理和分析,以获取有用的信息并作出相应的决策。
通过对数据的处理和分析,可以实现对生产过程的优化和改进,提高生产效率和质量。
4. 自动化设备:自动化炼钢过程中,各种自动化设备的应用也是非常重要的。
例如,自动化输送系统可以实现原料的自动输送和配料;自动化控制阀可以实现对流体流量和压力的自动调节;自动化机器人可以实现对炉渣的自动清理等。
二、自动化炼钢的应用1. 生产效率提升:自动化炼钢可以实现生产过程的高度自动化和智能化,减少人力操作的参与,提高生产效率。
例如,自动化输送系统可以实现原料的自动供给,减少了人工搬运的时间和劳动强度;自动化机器人可以实现对炉渣的自动清理,提高了炉渣处理的效率。
2. 质量稳定性提升:自动化炼钢可以通过实时监测和控制各种参数,确保生产过程的稳定性和一致性,提高产品质量的稳定性。
例如,通过对温度、压力等参数的实时监测和控制,可以减少生产过程中的温度偏差和压力波动,提高产品的一致性。
3. 安全性提升:自动化炼钢可以减少人员接触高温、高压等危险环境,降低了事故风险,提高了生产过程的安全性。
转炉炼钢智能制造关键技术开发与运用研究

转炉炼钢智能制造关键技术开发与运用研究摘要:文章分析炼钢智能化开发的必要性,重点探讨实际开发运用情况。
根据转炉炼钢过程的关键工艺,例举副枪、精炼及连铸三个环节,借助智能化手段的运用,控制生产成本,提升制造品质及效率。
关键词:转炉炼钢;智能控制;副枪引言:在转炉炼钢加工中,运用智能制造,使得成品质量得以稳定,提高企业的生产水平,落实柔性组织模式,有效压缩制造成本。
利于推动规模化炼钢与定制化生产,增强企业竞争力。
一、炼钢制造工艺智能化开发的必要性炼钢领域中,产品质量及等级要求逐渐提高,当前相关制造企业主体,需借助更优质的工艺与机组,提升自身的制造管控水平,进一步推进生产线朝着规范化、智能化、高稳定性的方向发展,由此适应如今高端产品市场,对于成品质量稳定性的要求。
所以,相关公司主体,应基于转炉、连铸等工艺环节,提高产品制造工艺水平,并尽力开发出高适用性的技术、智能化控制方法,确保炼钢生产有序高效落实,减少人为因素引发的产品低下问题。
二、智能制造关键技术的开发运用分析(一)转炉副枪在追求炼钢自动化的过程中,借助副枪技术,完成熔池探测,以确定炼钢制造期间,熔池中生产条件的波动情况。
通过运用计算机系统,加强对炼钢过程的控制力度,继而把握终点值,降低开展二次吹炼的概率。
基于副枪系统及动静态的系统模型,以达到本地在污染物排放方面的要求标准,同时也为生产工人创造低风险且舒适的环境。
一方面,副枪系统。
模型控制系统基于若干高性能的服务器,各自控制脱硫及转炉炼钢、连铸等诸多生产环节工序。
而针对炼钢过程的控制模型,一般是炼钢二级机。
具体来讲,自动化系统可分成静态模型与动态模型两个部分,前者完成静态控制任务,此模型实际包含出钢温度参数,可细分出目标温度、热平衡及溶剂等多个计算模型。
对于转炉生产技术的控制模型参数,操作人员能借助系统的全过程维护画面,进行监控,适时进行参数调整,确保生产过程有序进行。
同样,动态模型负责动态控制的部分,其按照转炉中,产生的冶炼末期数据,按照计算结果,选择是否添加冷却剂与供氧,并确定各自的用量,对吹炼技术的全过程进行跟踪管理。
自动化炼钢的原理及应用

自动化炼钢的原理及应用自动化炼钢是指利用先进的控制系统和自动化设备,实现钢铁生产过程的自动化操作和控制。
它通过集成各种传感器、执行器和控制器,实现对炼钢过程中各个环节的监测、调节和控制,提高生产效率、降低能耗和人力成本,提升产品质量和安全性。
一、自动化炼钢的原理1. 传感器技术:自动化炼钢过程中,各种传感器起到了关键作用。
温度传感器、压力传感器、测量仪表等能够实时监测炼钢过程中的温度、压力、流量等参数,将这些参数转化为电信号,并传输给控制系统进行处理和分析。
2. 控制系统:自动化炼钢的控制系统是整个自动化生产过程的核心。
它由计算机控制器、PLC、DCS等组成,能够接收传感器传来的信号,根据预设的控制策略进行计算和判断,并通过执行器控制各个设备的运行状态和参数,实现对炼钢过程的自动化控制。
3. 执行器:执行器主要包括电动阀门、机电、液压装置等,通过控制信号的输入和输出,实现对炼钢过程中各个设备的开关、调节和控制。
例如,根据控制系统的指令,电动阀门可以自动调节介质的流量和压力,机电可以控制设备的启停和转速。
二、自动化炼钢的应用1. 炉前自动化控制:通过传感器监测炉内温度、压力等参数,控制系统能够实时调节燃料供给、风量控制、氧气喷吹等,实现炉内温度的精确控制,提高炉温均匀性和炉况稳定性。
2. 连铸自动化控制:自动化炼钢中的一个重要环节是连铸过程的自动化控制。
通过传感器监测铸坯温度、结晶器水流量等参数,控制系统能够实时调节结晶器冷却水流量和连铸速度,实现铸坯的凝固控制和尺寸控制。
3. 能源管理与优化:自动化炼钢系统能够对能源的使用进行实时监测和调节,通过优化能源的利用,降低能耗和排放,提高钢铁生产的能源利用效率。
4. 质量控制与检测:自动化炼钢系统能够对钢铁生产过程中的各项指标进行实时监测和分析,通过自动化控制,能够提高产品的质量稳定性和一致性。
5. 安全监控与报警:自动化炼钢系统能够对生产过程中的安全隐患进行实时监测和报警,及时采取措施,保障生产过程的安全性。
钢铁行业智能炼钢技术

钢铁行业智能炼钢技术近年来,随着科技的不断发展和进步,智能化应用已经深入到各个行业中。
钢铁行业作为我国重要的基础产业之一,也不例外。
智能炼钢技术的引入和应用,为钢铁行业带来了新的发展机遇,促进了行业的转型升级。
一、智能炼钢技术的背景与意义钢铁行业是我国经济发展的重要支柱产业,对于国家的发展和国防建设具有重要意义。
但传统的炼钢技术存在一些问题,如资源消耗大、能源利用率低、环境污染等。
智能化技术的引入,可以提高钢铁生产的效率和质量,减少资源的浪费和环境的污染,从而实现可持续发展的目标。
二、智能炼钢技术的应用与案例1. 智能化设备控制系统智能化设备控制系统是实现智能炼钢的基础。
通过先进的传感器和控制技术,可以实时监测和控制炼钢过程中的温度、压力、流量等参数,保证炼钢过程的稳定性和精确性。
2. 智能炉温控制技术利用智能炉温控制技术,可以提高炼钢过程的温度控制精度和稳定性。
通过先进的算法和模型预测,以及对炉温的自动调整和反馈控制,可以有效提高炼钢的质量和生产效率。
3. 智能化质量检测技术智能化质量检测技术可以实时监测和分析炼钢产品的质量参数,包括成分、硫含量、氧含量等。
通过智能化质量检测技术,可以实现自动化检测和数据分析,提高产品质量的稳定性和可靠性。
4. 智能炼钢过程优化技术利用先进的数据分析和智能算法,可以对炼钢过程进行建模和优化。
通过实时监测和分析炼钢过程中的关键参数,调整和优化生产工艺,可以提高钢铁生产的效率和能源利用率,降低生产成本。
三、智能炼钢技术的影响与前景1. 提高生产效率引入智能炼钢技术可以提高生产效率,减少人工操作,提高生产线的稳定性和连续性。
通过数据的自动采集和分析,可以发现生产线中的问题和瓶颈,优化生产过程,提高生产能力和利润。
2. 降低生产成本智能炼钢技术可以实现对炼钢过程的精细化控制,减少资源的浪费和能源的消耗。
通过自动化设备和智能化管理,可以降低生产成本,提高经济效益。
3. 保护环境智能炼钢技术可以实现对废气和废水的处理,减少环境污染。
自动化炼钢的原理及应用

自动化炼钢的原理及应用自动化炼钢是指利用先进的控制系统和自动化设备,实现钢铁生产过程中的自动化操作和控制。
它通过集成各种传感器、执行器和控制器,实现对炼钢过程中的温度、压力、流量等参数的实时监测和调节,从而提高生产效率、降低能耗、提高产品质量。
一、自动化炼钢的原理1. 数据采集与处理:自动化炼钢系统通过传感器实时采集炼钢过程中的各种数据,如温度、压力、流量等,然后将这些数据传输到控制系统中进行处理和分析。
2. 控制策略与算法:控制系统根据炼钢过程的要求和目标,通过预设的控制策略和算法,对炼钢过程中的各种参数进行调节和控制,以实现最佳的生产效果。
3. 执行器控制:控制系统通过执行器控制设备,如阀门、电机等,对炼钢过程中的各种操作进行自动化控制,如调节温度、控制流量等。
4. 监测与反馈:自动化炼钢系统通过监测设备对炼钢过程中的各种参数进行实时监测,并将监测结果反馈给控制系统,以便进行调整和优化。
5. 故障诊断与处理:自动化炼钢系统还能通过故障诊断功能,对炼钢过程中可能出现的故障进行检测和诊断,并及时采取相应的措施进行处理,以确保生产的连续性和稳定性。
二、自动化炼钢的应用1. 生产效率提升:自动化炼钢系统能够实现对炼钢过程中的各个环节进行自动化控制和调节,从而提高生产效率和产能。
通过实时监测和自动调节,可以减少人工干预的时间和成本,提高生产线的运行效率。
2. 能源消耗降低:自动化炼钢系统通过对能源的精确控制和优化利用,可以有效降低能源消耗。
通过实时监测和调节温度、压力等参数,可以减少能源的浪费和损耗,提高能源利用率。
3. 产品质量提升:自动化炼钢系统能够实时监测和调节炼钢过程中的各种参数,从而保证产品的质量稳定性和一致性。
通过精确的控制和调节,可以避免因人为操作不准确而导致的产品质量问题,提高产品的合格率和市场竞争力。
4. 安全性提高:自动化炼钢系统能够实现对炼钢过程中的各种操作和参数进行自动化控制,减少人工操作的风险和安全隐患。
120t转炉自动化炼钢生产实践

120t转炉自动化炼钢生产实践120t转炉自动化炼钢生产实践刘德祥朱爱文(中厚板卷厂)(国贸公司)摘要:介绍了自动化炼钢系统在120t转炉上的应用情况,使用后终点命中率从65.8%提高到83%以上,获得较好的效果。
关键词:自动化炼钢终点命中率静态计算动态计算Application of Steel m aking Auto m ation for120t BOFL iu D exiang Zhu A i w en(W i de P late/Coil P l an t)(In ternational T rade Co m pany) Abstrac t:Appli cation of steel mak i ng auto m ation syste m for120t BOF is i ntroduced.T he pe rcentage of hits has raised fro m65. 8%to over83%after appli cation and sa ti sfactory results have been got.K eyword s:auto m ation;stee l m aki ng;percentage o f h its;static calcu lati on;dyna m ic ca lcu l a ti on1 概述南钢120t转炉于2004年6月份投产。
配有转炉顶底复合吹炼、副枪和二级自动化控制。
自动化炼钢系统全部由奥钢联提供。
二级自动化控制系统,实现炼钢过程的自动化控制,降低劳动强度,提高劳动生产率,为实现产品质量控制、跟踪管理创造条件。
自动化炼钢从2005年8月开始使用,从使用情况看具有改善转炉操作、延长炉龄、缩短冶炼时间、提高终点命中率等优点。
2 自动化炼钢简介2.1 静态模型2.1.1 一次计算(FCC)一次计算是利用转炉物料平衡和热平衡的原理,根据铁水成份、温度、重量和目标钢水成份、温度、重量以及终点渣成份进行初步计算。
自动化炼钢的原理及应用

自动化炼钢的原理及应用自动化炼钢是通过机器和计算机控制系统实现钢铁生产过程的自动化的一种技术。
它可以提高生产效率、降低生产成本、提高产品质量、减少劳动强度等。
本文将详细介绍自动化炼钢的原理和应用。
一、自动化炼钢的原理1. 传感器技术:自动化炼钢中的传感器技术是一个关键。
通过传感器可以实时监测炉温、炉压、气体成分、金属温度等参数,将这些数据传输给计算机控制系统进行分析和处理。
2. 控制系统:自动化炼钢的控制系统采用先进的计算机技术,通过对传感器数据的分析和处理,实现对炉温、炉压、气体成分等参数的自动控制。
控制系统可以根据预设的工艺要求,自动调整炉温、炉压等参数,以达到最佳的生产效果。
3. 机器人技术:自动化炼钢中的机器人技术主要应用在钢铁生产线的操作环节。
机器人可以替代人工进行炉料的装卸、炉渣的清理、铁水的倒运等工作,提高生产效率,减少人力成本。
4. 数据分析和优化:自动化炼钢通过对大量的数据进行分析和处理,可以优化生产工艺,提高产品质量。
例如,通过对金属温度的实时监测和分析,可以调整炉温和炉压,以提高钢材的强度和韧性。
二、自动化炼钢的应用1. 高炉自动化控制:高炉是钢铁生产的核心设备之一,自动化控制可以实现高炉的稳定运行和高效生产。
通过自动化控制系统,可以实时监测和调整高炉的炉温、炉压、气体成分等参数,以提高冶炼效率和产品质量。
2. 连铸自动化控制:连铸是将炼钢炉中熔化的钢水浇铸成坯料的过程,自动化控制可以提高连铸的生产效率和产品质量。
通过自动化控制系统,可以实时监测和调整连铸的浇注速度、结晶器温度等参数,以确保坯料的形状和质量。
3. 炼钢厂自动化管理:自动化炼钢不仅可以应用于具体的生产过程,还可以应用于炼钢厂的管理和决策。
通过自动化管理系统,可以实现对生产过程的全面监控和控制,提高生产计划的准确性和执行效率。
4. 钢铁物流自动化:钢铁生产过程中的物流环节也可以实现自动化。
通过自动化物流系统,可以实现原料的自动运输、半成品的自动转运、成品的自动包装等,提高物流效率,降低物流成本。
120t转炉综合自动化系统的研究与应用

大速度运行 , 当设定值与 实际偏 差越 来越 小时 , 制速度也 随之 控 减小 , 最终使 氧 枪准 确 停止 在所 要 求 的位 置上 。要 达 到上 述要 求, 关键在 于找 出偏 差距 离与速度给定 之间的关 系。即偏差为多
控制 , 但相对独立 , 成 “ 岛”, 互之 间缺 少信 息 的传输 与 交 形 孤 相 换, 无法实现生产管理对 现场 生产 的 自动调 度 与信息 反馈 , 能 不
在银山型钢的转炉 系统 中 , 采用 了干 法 除尘 ( T 工 艺 作发
大型转炉煤 气净 化的方法 , 目前 世界 上主要 有两种 , 日本 以 O G法 为代 表的湿法净化系统 ( 以下 简称 O G法 ) 和以德 国鲁 奇与
转炉的一次除尘 , 以代替传统 的 O G湿 法除尘 。L T系统 由于其采
精炼 、 连铸技 术的发展 , 打破 了传 统 的转炉炼 钢模 式。 目前 由单
纯用转炉冶炼发 展 为铁水 预处理一复 吹转炉 吹炼一 炉外 精炼一 连铸这一新 的工艺流程 。这一流程 以设 备大型化 、 现代 化和连续 化为特点 , 在这种形 势下 , 炼钢流程 中, 转炉 区域的综合 自动化系 统 的实现就变得非常 的必要且重要 。 莱钢银 山型钢炼钢厂共有 10 转炉三座 , 2t 是莱钢 目前炉容最 大的三座转 炉 , 每炉 出钢 量达 到 10 , 4 t为后道 工序 的 2台板 坯连 铸机 , 1台异型坯连铸机 提供 优质钢水 , 在炼铁 一 钢 一轧钢的冶 炼
钢铁行业智能炼铁技术

钢铁行业智能炼铁技术近年来,随着科技的不断发展和创新,智能化技术逐渐渗透到各个行业,钢铁行业也不例外。
智能炼铁技术作为钢铁行业数字化转型的重要组成部分,对提高生产效率和质量起着关键作用。
本文将就钢铁行业智能炼铁技术的意义、应用和展望进行探讨。
1. 智能炼铁技术的意义在传统的炼铁过程中,人工操作频繁,精度受到限制,而智能炼铁技术的引入可以有效地提升炼铁过程的自动化程度和智能化水平。
通过搭建数据采集和分析平台,实时监控炉况、燃烧状态和材料性质变化等信息,可以精准控制炼铁过程中的温度、压力和化学成分等关键参数,提高产能,减少资源浪费,提高产品质量。
2. 智能炼铁技术的应用(1)物联网技术的应用:物联网技术的发展使得各种设备和传感器能够实时获取和传输数据。
在智能炼铁技术中,物联网技术可以连接各个环节的设备和传感器,将各种数据进行集中管理和分析,实现整个炼铁过程的数字化和自动化控制。
(2)大数据分析的应用:通过大数据分析,可以从庞大的数据中挖掘出有价值的信息和规律,为智能炼铁提供决策支持。
例如,利用大数据分析可以实现对原材料特性的精准预测,优化炼铁配料和工艺参数;通过对过往数据进行模型训练,可以预测故障和异常情况,提前采取措施,避免生产事故的发生。
(3)人工智能的应用:人工智能技术的发展为智能炼铁带来新的机遇。
通过机器学习和深度学习算法,智能系统可以从大量的数据中学习和模仿人工操作的经验,不断优化炼铁过程和决策,实现自动化和智能化。
3. 智能炼铁技术的展望目前,智能炼铁技术的应用虽然已经取得了一定的成果,但仍然存在一些挑战和待解决的问题。
例如,数据安全性和隐私保护问题,智能设备的可靠性和稳定性问题,以及智能化技术的推广和普及问题等。
未来,随着技术的不断进步和经验的积累,这些问题将逐步得到解决,智能炼铁技术的应用将更加广泛,效果将更加显著。
结论:智能炼铁技术作为钢铁行业数字化转型的重要手段,对提高生产效率和质量具有重要作用。
转炉智能炼钢开发及应用

科技创新导报 Science and Technology Innovation Herald1001 项目概况为了提升产品档次及市场竞争力,一炼钢厂从荷兰达涅利康力斯公司全套引进了副枪和二级计算机系统的核心静动态模型,一炼钢的钢种以品种钢为主,对钢水的质量要求很高。
对转炉钢水的碳含量、磷含量、氧含量、氮含量、夹杂物含量、钢水过热度都要求控制在很窄的范围,在前期“一键式”自动化炼钢的基础上进行完善,对系统及外方设计之初很多方面考虑不全面的地方进行攻关,还存在各种难题需要解决,具体如下。
(1)废钢重量自动传输到转炉自动化炼钢系统。
(2)钢包号无法准确地传递到转炉二级系统。
(3)无合适的氧枪操作、投料、底吹控制等模式,动静态控制模式不稳定。
针对系统中存在的各种问题,本项目为解决问题所做的创新性工作如下。
(1)开发完成废钢配比与总重系统开发,自主开发完成废钢配比与总重系统开发,废钢重量跟料斗号绑定,实现废钢重量自动传递给自动化炼钢系统,为动静态模型计算提高了准备的依据。
(2)建立了钢包和铁包系统与自动化炼钢的接口,实现钢包包况和钢包号自动传递到转炉自动化二级系统。
(3)根据现有铁水条件,增加到氧枪操作模式、30种投料模式,形成7种底吹控制模式,针对特殊高磷铁水形成专有枪位控制模式。
维护动静态模型的稳定性,摸索自主冶炼模式,解决工艺制约环节。
模型静态计算的稳定性和准确性无疑是自动化炼钢的前提条件,静态计算主要给出冶炼过程控制参数的建议值,主要有辅料加入量、耗氧量,建议值的准确性直接决定了冶炼过程的稳定性,因此对于影响模型4个主要平衡计算准确性的因素要首先解决。
其次,由于邯钢铁水温度和Si含量波动大的特点,以及炼钢辅原料种类多,变换频繁,冶炼模式需要适应这些条件的变化,对冶炼模式进行系统设计,完成计算机自动选取冶炼模式的功能。
该项目实施后,使一炼钢120吨转炉自动化炼钢生产稳定,各项指标稳步提升。
主要表现为以下方面。
自动化炼钢技术的应用与研究

自动化炼钢技术的应用与研究摘要:社会不断进步,使得炼钢技术也发生了重大的变革。
信息技术的大量应用,使自动化炼钢技术得到了更好的普及,也使钢铁的品质及生产效率有了很大的提升。
通过自动化炼钢技术的应用与研究分析,了解自动化炼钢技术应用的重要意义,自动化炼钢技术应用的关键技术,自动化炼钢技术应用的有效措施,使自动化炼钢技术能够更加合理的应用,为我国的经济建设提供更加的助力。
关键词:转炉炼钢;自动化控制技术;应用研究当前,我国钢铁工业在炼钢技术上的研发和应用依旧不足,使得我国钢铁工业的发展受到了一定的限制,整个钢铁行业也正面临着新的考验与挑战,再加上我国对环境保护和绿色化生产的要求,我国的钢铁工业需要在炼钢技术上不断进行改进和革新,采取一些新型的炼钢技术来提升自身生产力,确保满足国家需求。
在钢铁工业炼钢技术中,转炉炼钢技术是非常重要的技术之一,对转炉炼钢技术的革新与研发,是钢铁工业未来重要的发展方向。
1自动化炼钢技术概述钢铁工业以传统重工业冶炼为主,加以自动化机械化技术应用,主要包括铁水预处理自动化、氧气转炉自动化、炉外精炼、连续造钢等技术,涉及设备检测、电力转动控制系统、模型设定等各个方面。
目前我国炼钢技术企业在整体系统运转的基础上,已经普及自动化信息技术并处在大力发展的过程中,生产过程控制及通过整体系统也得到一定程度的发展,数学模型建设的完善也将有利于生产过程效率的提高,除此之外,生产过程执行系统作为自动化炼钢技术最重要的一部分,在整体流程中起决定作用,是实现传统炼钢与自动化信息化技术相结合的关键。
当前我国炼钢技术很大程度上依赖于简单机械,基础自动化和生产自动化仍需大力建设,才能早日实现钢铁企业信息化数据化管理及有效控制。
2自动化炼钢技术应用在21世纪的发展形势下,我国钢铁工业中对洁净钢的生产已经成为重点,而洁净钢的生产技术的发展目标就是采取最经济的手段来使生产效率大幅提高,从而形成大规模的生产。
当前我国已经创新出了新的炼钢流程来对洁净钢进行生产,并且已经在部分炼钢企业中得到了初步的应用。
智能制造技术在钢铁冶炼中的应用与优化

智能制造技术在钢铁冶炼中的应用与优化随着现代化科技的不断发展,智能制造技术已经逐渐融入到各个领域中。
其中,钢铁冶炼行业是一个尤为重要的领域,智能制造技术在这个领域中的应用与优化也备受关注。
本文将探讨智能制造技术在钢铁冶炼中的应用与优化以及对行业的影响。
一、智能制造技术在钢铁冶炼中的应用1. 机器学习技术机器学习技术可以帮助生产企业在现有工艺情况下不断优化生产效率,提升生产质量。
在钢铁冶炼过程中,机器学习技术可以分析监测数据,以便更准确地预测和控制冶炼过程中重要参数的变化。
例如,对熔铁物流和温度控制进行优化,使生产线自动适应工艺参数变化,控制生产过程中的微小波动。
这种自适应机制有助于保持最佳的操作模式,从而提供更加稳定的产品质量,提高生产效率。
2. 传感器技术传感器技术也是智能制造技术在钢铁冶炼行业的应用之一。
传感器可以检测重要的冶炼参数,例如温度、压力、流量等。
这些传感器可以将数据自动记录下来,进而对生产过程进行实时监测和控制。
此外,传感器还可以帮助企业进行能源消耗分析,优化能源使用,降低了能源成本,提高了经济效益。
3. 云计算技术钢铁冶炼行业需要处理大量的数据,智能制造技术的云计算技术可以帮助这些数据自动收集、存储、管理和分析,这有助于工业企业更好地进行数据分析,以便更好地了解生产过程和设备信息。
云计算技术也可以用于建立自动化决策系统,为钢铁冶炼提供技术支持。
二、智能制造技术在钢铁冶炼中的优化除了应用之外,智能制造技术在钢铁冶炼中还可以实现进一步的优化。
1. 数据分析通过对监测和采集的数据进行分析,可以帮助钢铁生产企业更好地把握生产过程,包括发现和发掘潜在的问题,纠正生产过程中存在的缺陷,以及掌握与生产相关的管理和决策方法等。
数据分析可以帮助钢铁生产企业更好地理解生产过程,并根据数据分析结果来采取相应的改进措施。
2. 设备集成智能制造技术可以将传感器、工艺控制、设备监测和数据收集集中在一起,以形成一个全面的设备集成系统。
自动化炼钢的原理及应用

自动化炼钢的原理及应用自动化炼钢是指通过计算机控制和自动化设备实现炼钢过程中的各个环节的自动化操作。
它利用先进的传感器、控制系统和执行机构,实现对炼钢过程中的温度、压力、流量、浓度等参数的实时监测和控制,提高生产效率、产品质量和工作环境的安全性。
一、自动化炼钢的原理1. 传感器技术:自动化炼钢过程中,通过使用温度传感器、压力传感器、流量传感器等各种传感器,实现对炉温、气压、液流等参数的实时监测。
传感器将采集到的数据传输给控制系统,以便进行后续的数据处理和控制。
2. 控制系统:自动化炼钢的关键是控制系统。
控制系统通过接收传感器传来的数据,根据预设的控制策略进行数据处理,并输出相应的控制信号。
控制系统可以分为上位机和下位机两部份,上位机负责数据处理和控制策略的制定,下位机负责执行控制信号。
3. 执行机构:自动化炼钢过程中,执行机构根据控制系统的指令,对各个环节进行自动化操作。
常见的执行机构包括电动阀门、液压缸等。
通过控制执行机构的动作,可以实现对炉温、气压、液流等参数的精确控制。
二、自动化炼钢的应用1. 炉温控制:自动化炼钢系统可以通过温度传感器对炉内温度进行实时监测,并通过控制系统对炉温进行精确控制。
这样可以提高炉温的稳定性,减少温度波动对炼钢过程的影响,提高产品质量。
2. 气体控制:自动化炼钢系统可以通过压力传感器对炉内气体压力进行实时监测,并通过控制系统对气体流量进行精确控制。
这样可以保持炉内气体的稳定流动,提高炉内气氛的均匀性,提高炼钢效率。
3. 液流控制:自动化炼钢系统可以通过流量传感器对液流进行实时监测,并通过控制系统对液流进行精确控制。
这样可以保持液流的稳定性,提高炉内液体的均匀性,提高产品质量。
4. 数据分析:自动化炼钢系统可以将传感器采集到的数据进行存储和分析,以便进行生产过程的优化和问题的排查。
通过对数据的分析,可以发现炼钢过程中的潜在问题,并及时采取措施进行调整,提高生产效率和产品质量。
自动化炼钢的原理及应用

自动化炼钢的原理及应用自动化炼钢是指利用先进的控制系统和自动化设备来实现炼钢过程的自动化操作和控制。
它通过集成先进的传感器、仪表、控制器和执行器等设备,实现对炼钢过程的实时监测、数据采集、分析和控制。
自动化炼钢技术的应用可以提高生产效率、降低生产成本、提高产品质量,并且能够减少人为操作的风险和劳动强度。
一、自动化炼钢的原理1. 数据采集与监测自动化炼钢系统通过安装在炉子、转炉、连铸机等设备上的传感器,实时采集炼钢过程中的温度、压力、流量、振动等数据。
这些数据通过信号传输到控制系统中,进行实时监测和记录。
2. 过程控制与优化控制系统根据采集到的数据,通过先进的算法和控制策略,对炼钢过程中的温度、化学成分、流速等参数进行实时控制和优化。
例如,控制系统可以根据目标温度和化学成分,自动调整氧气、燃料和加料的比例,实现炉温的精确控制和炼钢过程的优化。
3. 自动化设备与执行器自动化炼钢系统还包括各种自动化设备和执行器,如自动加料机、自动倒渣机、自动控制阀等。
这些设备和执行器能够根据控制系统的指令,自动完成炼钢过程中的加料、倒渣、调节流量等操作,实现炼钢过程的自动化和智能化。
二、自动化炼钢的应用1. 提高生产效率自动化炼钢系统能够实现炼钢过程的自动化操作和控制,减少了人工操作的时间和劳动强度,提高了生产效率。
例如,自动化加料系统可以根据炼钢过程的需要,自动控制加料的时间和比例,避免了手动加料的误差和延迟。
2. 降低生产成本自动化炼钢系统能够通过实时监测和控制炼钢过程中的温度、化学成分等参数,优化炼钢过程,降低能源消耗和原料损耗,从而降低生产成本。
例如,控制系统可以根据实时的温度和化学成分数据,自动调整炉温和燃料的比例,实现能源的有效利用。
3. 提高产品质量自动化炼钢系统能够实时监测和控制炼钢过程中的温度、化学成分等参数,确保产品质量的稳定和一致性。
例如,控制系统可以根据产品要求,自动调整炉温和燃料的比例,控制炼钢过程中的温度和化学成分,从而保证产品的质量。
- 1、下载文档前请自行甄别文档内容的完整性,平台不提供额外的编辑、内容补充、找答案等附加服务。
- 2、"仅部分预览"的文档,不可在线预览部分如存在完整性等问题,可反馈申请退款(可完整预览的文档不适用该条件!)。
- 3、如文档侵犯您的权益,请联系客服反馈,我们会尽快为您处理(人工客服工作时间:9:00-18:30)。
试述智能炼钢技术在120吨转炉上的研究与应用
摘要钢铁制造工业中,炼钢是最为核心的技术,关系到钢铁的使用质量。
鉴于此,本文针对120吨转炉生产环节的不足和智能炼钢技术的相关理论,提出了研究和应用方法。
关键词智能炼钢技术;120吨转炉;应用方法
前言
社会经济的高速发展,带动了工业、建筑业等行业的发展,对高质量钢铁的需求量也指数上升,引入新的智能化技术进行高效的自动生产是重点的发展方向和趋势。
而120吨转炉是炼钢的主要设备种类,如何技术有效的应用于实际的生产环节,对钢铁质量和企业的发展具有现实的意义。
1 智能炼钢技术的必要性
从实际的生产情况来看,智能炼钢技术应用十分必要。
一是,炼钢时需要对铁水的成分和温度进行检测,但检测的地点与转炉的操控场所不处于同一个地点,常会出现铁水检测数据不能及时汇集到转炉操作室的问题,严重地影响了正常的转炉工作。
二是,生产环节铁水和废钢的记录和观察,大部分都是以人工检测的形式进行,误差问题无法得到有效的控制和解决,给转炉的操作准确性带来了一定的难度。
三是,添加的散料和对加料的控制多是以经验决定,容易受到操作人员的影响,导致抢位控制不准、散料的添加数量有出入等状况的发生,甚至会引起大型的严重大喷事故。
因这些问题的存在,智能炼钢技术的研究和应用至关重要[1]。
2 研究和应用智能炼钢技术的方法
2.1 加大研发力度,优化和升级智能化系统
经过长期的炼钢实践来看,原料存在问题是影响智能化炼钢技术效果的重要因素,而且现有的炼制程序简单、转炉设备的控制效果不佳等问题也是制约钢铁上生产质量的因素。
这就要求,智能炼钢技术的应用要研究和优化智能化的系统,可从两点出发。
(1)原材料操作模式的确定
一般情况下,原材料的比例条件要保证铁水中硅元素的含量不得过高,根据各厂家的原燃料、技术水平等来决定,一般来说0.4左右算是低硅,底于0.3算超低硅,稳定的范围就在0.3%~0.7%之间,温度的控制也应在1250摄氏度到1330摄氏度之间。
120吨转炉的炼制工艺研究,要对热量的失衡和平衡情况分别考虑,其中主要的研究内容就是热量失衡。
首先,选择冷料。
炼钢的过程中,热
量的不稳定会给技术操作带来影响,需要添加一定的冷却剂,可使用烧结矿。
在添加了冷却剂时,分成前期和中后期温度控制两个方面。
前期的温度控制,添加两批渣料,冷料添加一半。
中后期的温度控制,要分批次的多次添加冷却材料,转枪的位置控制要采用变枪的方式,以保证转炉的温度上升的速度和过程稳定。
其次,转炉底吹模式参数的优化。
(2)智能操作系统的建立
智能炼钢技术的应用需要相配套的系统支持,智能炼钢系统的设计可以设计为矩阵的形式,建立两级管理系统。
其中,系统的时间设定上要包含炼钢的全天不同原料下的不同情况,以便支持不同的炼制情况,如炼钢模式(SPHC)的铁水含量为0.13%~0.4%之间,温度小于1250摄氏度智能炼钢的表现为CA-LAIGANG2.1。
2.2 炼钢过程的智能化
钢铁的炼制过程是智能化技术研究和应用的最重要时段,实际的研究和应用过程,需要控制好两个方面。
第一方面,改变人工检测方式,引入智能化自动流量仪表。
目前,配套使用的流量仪表主要是平衡流量计以及超声波流量计。
在钢铁行业的应用主要是用来测量铁水、污染物排放以及温度的变化数据。
超声波流量计在进行铁水检测的过程中,使用径距取压的方法改善以往使用孔板的检测方式中常出现的取压口堵塞的状况。
而平衡流量计对于实现钢铁行业节能减排的目标,精确地控制加料数量有着重要的作用。
首先,它的装置结构属于上下对称的样式,没有在孔板的下部设置斜角,正因为如此可以从双向对流量检测,尤其是对特殊的制造流程的检测有着巨大的作用。
如制造转炉的炼制工作,实际的检测中需要对实时的蒸汽温度进行测量,但由于内部装置的差异性出现了双向流,这时就可以使用此流量仪表对正向和反向的温度流量同时测量。
在安装平衡流量仪表时,要根据不同的情况选择,如果雙向流量的最大值相同就可以选择装配一台变送器,不同时则要选择两台。
第二方面,氧枪的自动识别系统。
120吨转炉的氧枪的控制对智能炼钢技术的实现有重要的效用,而智能化技术下,可采用编码器实现位置的自动识别。
安装时,必须在设备的主要轴上安装两个编码器,以防因故障的发生无法正常读数,选择的编码器最好为可自动校准的型号,提高检测的准确度。
2.3 应用智能炼钢技术的成效
智能技术在炼钢生产中的应用,对质量和成本有着重要的作用。
从成本的角度来看,我国目前主要的炼钢工艺为转炉炼钢,一般需配置10%~15%的废钢。
炼钢工艺中因为耗电量的增加、合金的加入以及维检费用的上升使得除主要原料外的其他费用占到炼钢总成本的18%左右,而智粗钢吨制造成本=(0.96×生铁+0.15×废钢)/0.82。
而智能炼钢技术的应用,以节约吨(碳)钢成本2-6美元、吨(不锈)钢成本20美元。
从质量的角度来看,也得到了有效提高和优化,如炼钢的生产环节,底吹的参数中,如果兑铁的装料为261m3,吹炼期就要分成
三分钟、八分钟和十二分钟三个阶段[2]。
例如,120t转炉底吹系统智能化前后,效果就出现了不同。
之前的底吹气源N2,Ar,底吹供气压力0.8/2.0(N2/Ar)Mpa,底吹供气强度0.01~0.03Nm3/(t.min),智能化转变后,底吹气源N2,Ar,压缩空气,底吹供气压力1.4/2.0(N2/Ar)Mpa,底吹供气强度0.03~0.08Nm3/(t.min)。
3 结束语
综上所述,智能炼钢技术是新时期钢铁行业的发展趋势,有利于质量和效率的提高,安全和稳定性也得以提升。
在研究和应用于120吨转炉的过程中,可以借鉴建立智能操作系统、确定原材料操作模式等方法,推进钢铁行业的智能化发展进程。
参考文献
[1] 郭伟达,李强笃,任科社.转炉全流程智能炼钢控制技术开发与应用[J].山东冶金,2018,40(01):4-7.
[2] 路镇,高志滨,一键式智能炼钢技术在小型转炉中的应用[J].自动化应用,2015,46(10):54-55,60.。