转炉炼钢技术的发展与展望
炼钢工艺发展的趋势
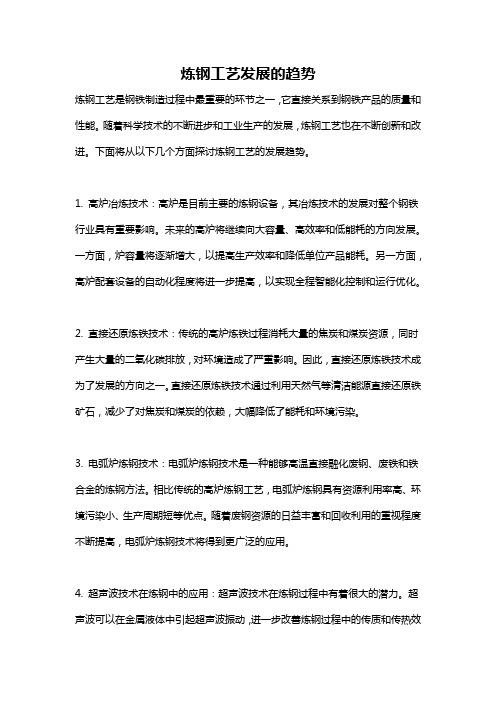
炼钢工艺发展的趋势炼钢工艺是钢铁制造过程中最重要的环节之一,它直接关系到钢铁产品的质量和性能。
随着科学技术的不断进步和工业生产的发展,炼钢工艺也在不断创新和改进。
下面将从以下几个方面探讨炼钢工艺的发展趋势。
1. 高炉冶炼技术:高炉是目前主要的炼钢设备,其冶炼技术的发展对整个钢铁行业具有重要影响。
未来的高炉将继续向大容量、高效率和低能耗的方向发展。
一方面,炉容量将逐渐增大,以提高生产效率和降低单位产品能耗。
另一方面,高炉配套设备的自动化程度将进一步提高,以实现全程智能化控制和运行优化。
2. 直接还原炼铁技术:传统的高炉炼铁过程消耗大量的焦炭和煤炭资源,同时产生大量的二氧化碳排放,对环境造成了严重影响。
因此,直接还原炼铁技术成为了发展的方向之一。
直接还原炼铁技术通过利用天然气等清洁能源直接还原铁矿石,减少了对焦炭和煤炭的依赖,大幅降低了能耗和环境污染。
3. 电弧炉炼钢技术:电弧炉炼钢技术是一种能够高温直接融化废钢、废铁和铁合金的炼钢方法。
相比传统的高炉炼钢工艺,电弧炉炼钢具有资源利用率高、环境污染小、生产周期短等优点。
随着废钢资源的日益丰富和回收利用的重视程度不断提高,电弧炉炼钢技术将得到更广泛的应用。
4. 超声波技术在炼钢中的应用:超声波技术在炼钢过程中有着很大的潜力。
超声波可以在金属液体中引起超声波振动,进一步改善炼钢过程中的传质和传热效果,提高钢的纯净度和均匀性。
此外,超声波还可以用于检测和监测钢铁产品中的缺陷和杂质,提高质量控制的准确性和效率。
5. 粉煤气化技术:粉煤气化技术是一种利用煤炭资源进行炼钢的新技术。
通过对煤炭进行气化,产生合成气,再利用合成气进行炼钢,既能够提高煤炭资源的利用率,又能够减少对传统能源的依赖和环境污染。
粉煤气化技术属于绿色环保型炼钢工艺,对于改善钢铁行业的能源结构和减少碳排放具有重要意义。
总体来说,炼钢工艺的发展趋势是朝着高效、环保、智能化和资源综合利用的方向发展。
大型转炉的发展趋势

大型转炉的发展趋势大型转炉是钢铁工业中的一种重要设备,用于钢铁冶炼的过程中。
随着钢铁工业的发展,大型转炉也在不断发展和改进,以满足钢铁生产的需要。
以下是大型转炉的发展趋势。
1. 技术水平的提高随着科学技术的不断发展,大型转炉的技术水平也在不断提高。
传统的大型转炉采用的是碱性炼钢方法,这种方法有一定的局限性,如钢水中的含硫量较高,耐火材料的磨损严重等。
而现代大型转炉采用的是酸性炼钢方法,可以有效降低钢水中的含硫量,改善炉况和提高工艺效率。
2. 节能减排大型转炉在发展中越来越注重节能减排。
传统的大型转炉冶炼过程中需要大量燃料,造成能源浪费和环境污染。
而现代大型转炉则采用了高效燃烧技术和先进的废气处理设备,使能源利用率得到提高,减少燃料消耗和废气排放。
3. 自动化控制随着科技的进步,大型转炉的生产也越来越自动化。
传统的大型转炉生产过程中需要大量人工操作,并且存在一定的安全隐患。
而现代大型转炉则采用了先进的自动控制系统,可以实现对转炉温度、氧含量、炉况等参数的实时监测和控制,提高生产效率和安全性。
4. 多功能综合利用传统的大型转炉主要用于炼钢,而现代大型转炉则具有多功能综合利用的特点。
除了炼钢外,大型转炉还可以用于冶金焦生产、废钢回收、炼铁以及钢铁工业中的其他工艺过程。
这样一来,不仅可以提高资源利用率,还可以减少环境污染和能源浪费。
5. 多炉联用为了提高生产效率和降低成本,大型转炉在发展中越来越倾向于多炉联用。
传统的大型转炉一次只能处理一定量的钢水,而现代大型转炉则采用多炉联用的方法,将多个转炉串联在一起。
这样一来,可以实现连续生产,提高钢水的产量,同时降低成本。
总之,大型转炉的发展趋势主要体现在技术水平的提高、节能减排、自动化控制、多功能综合利用和多炉联用等方面。
随着钢铁工业的不断发展,相信大型转炉会有更加广阔的应用前景和更高的发展水平。
2024年电炉炼钢市场前景分析
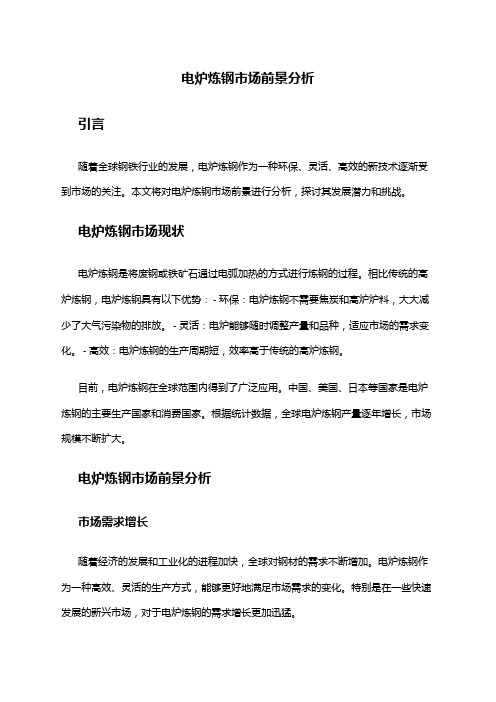
电炉炼钢市场前景分析引言随着全球钢铁行业的发展,电炉炼钢作为一种环保、灵活、高效的新技术逐渐受到市场的关注。
本文将对电炉炼钢市场前景进行分析,探讨其发展潜力和挑战。
电炉炼钢市场现状电炉炼钢是将废钢或铁矿石通过电弧加热的方式进行炼钢的过程。
相比传统的高炉炼钢,电炉炼钢具有以下优势: - 环保:电炉炼钢不需要焦炭和高炉炉料,大大减少了大气污染物的排放。
- 灵活:电炉能够随时调整产量和品种,适应市场的需求变化。
- 高效:电炉炼钢的生产周期短,效率高于传统的高炉炼钢。
目前,电炉炼钢在全球范围内得到了广泛应用。
中国、美国、日本等国家是电炉炼钢的主要生产国家和消费国家。
根据统计数据,全球电炉炼钢产量逐年增长,市场规模不断扩大。
电炉炼钢市场前景分析市场需求增长随着经济的发展和工业化的进程加快,全球对钢材的需求不断增加。
电炉炼钢作为一种高效、灵活的生产方式,能够更好地满足市场需求的变化。
特别是在一些快速发展的新兴市场,对于电炉炼钢的需求增长更加迅猛。
环保压力推动发展随着全球环保意识的增强,传统高炉炼钢面临着严重的环境污染问题。
电炉炼钢作为一种清洁生产方式,能够有效降低大气污染物排放并减少废渣的产生,受到环保法规的支持和鼓励。
因此,电炉炼钢在未来的发展中将有望得到更多的政府支持和资金投入。
技术创新驱动发展随着科技的进步,电炉炼钢技术不断创新,生产效率和产品质量得到了提升。
新一代电炉炼钢设备的推出,使得生产过程更加自动化和智能化。
同时,材料研发和工艺改进也为电炉炼钢的发展提供了新的机遇和挑战。
电炉炼钢市场的挑战成本压力与传统的高炉炼钢相比,电炉炼钢的投资和运营成本较高。
尤其是在电力资源紧张的地区,电炉炼钢的能耗成本较高,从而限制了其发展规模。
因此,如何降低电炉炼钢的成本是一个亟待解决的问题。
市场竞争加剧随着电炉炼钢市场的发展,越来越多的企业进入这一行业,市场竞争加剧。
面对来自国内外的竞争对手,企业需要提高技术水平和产品质量,不断创新以获取市场份额。
2024年炼钢转炉市场规模分析
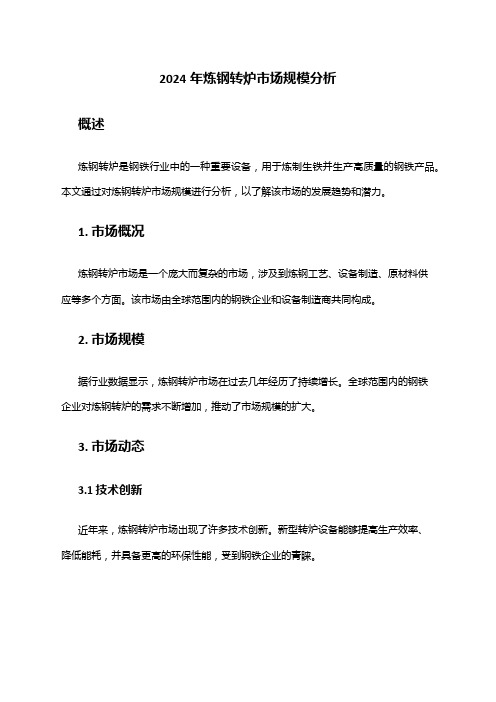
2024年炼钢转炉市场规模分析概述炼钢转炉是钢铁行业中的一种重要设备,用于炼制生铁并生产高质量的钢铁产品。
本文通过对炼钢转炉市场规模进行分析,以了解该市场的发展趋势和潜力。
1. 市场概况炼钢转炉市场是一个庞大而复杂的市场,涉及到炼钢工艺、设备制造、原材料供应等多个方面。
该市场由全球范围内的钢铁企业和设备制造商共同构成。
2. 市场规模据行业数据显示,炼钢转炉市场在过去几年经历了持续增长。
全球范围内的钢铁企业对炼钢转炉的需求不断增加,推动了市场规模的扩大。
3. 市场动态3.1 技术创新近年来,炼钢转炉市场出现了许多技术创新。
新型转炉设备能够提高生产效率、降低能耗,并具备更高的环保性能,受到钢铁企业的青睐。
3.2 区域分布全球范围内,炼钢转炉市场的主要集中在亚洲地区。
亚洲地区以其庞大的钢铁产能和不断增长的钢铁需求,成为世界上最大的炼钢转炉市场。
3.3 市场竞争炼钢转炉市场竞争激烈,主要的竞争者包括国内外的钢铁企业和设备制造商。
市场上存在大型综合企业和专业化设备制造商两种不同类型的竞争格局。
4. 市场前景炼钢转炉市场在未来有望继续呈现增长态势。
以下因素将推动市场规模的进一步扩大: - 不断增长的钢铁需求,特别是新兴市场的快速发展; - 钢铁产能结构调整和绿色发展的要求,使得企业对炼钢转炉设备的更新换代需求增加; - 技术创新和设备制造商的积极推动,将为市场提供更多高性能、高效能的炼钢转炉设备。
结论炼钢转炉市场作为钢铁行业的重要组成部分,对全球经济发展和钢铁产品供应起着至关重要的作用。
市场规模的持续扩大和技术创新将为钢铁企业带来更多的机会和挑战。
在未来,炼钢转炉市场有望继续保持稳定增长,为行业发展带来更多可能性。
试论转炉炼钢的现状和发展

试论转炉炼钢的现状和发展摘要:转炉炼钢是我国主要的炼钢模式,目前我国绝大多数钢材均为转炉钢,并且我国生产的转炉钢占世界转炉钢的1/4左右。
近年来,我国的转炉数量不断增多,并且转炉炼钢工艺更加成熟,无论是转炉钢的产量还是转炉钢的质量都有所提升。
为了进一步提升转炉钢的产量与品质,未来需要针对那些条件较好的转炉钢厂进行改造升级,提升转炉钢厂的生产设备性能以及生产工艺水平,在保障转炉钢产量和质量的同时,降低能耗,减少对环境造成的不利影响,保障转炉炼钢的可持续发展。
基于此,本文分析了转炉炼钢的现状,并就转炉炼钢的发展进行探究,仅供大家参考。
关键词:转炉炼钢;现状;发展引言:转炉炼钢是我国主要的炼钢方式,在建国初期,平炉是我国主要的炼钢设备。
改革开放以来,社会经济的快速发展,使得钢材需求量不断提升,这在很大程度上推动了炼钢产业的发展。
在此背景下,转炉炼钢也得到了快速发展的有利时机。
经过多年的发展,目前我国绝大多数钢材均为转炉钢,并且转炉炼钢工艺更加完善。
但转炉炼钢依然存在着能耗高以及环境污染严重等方面的不足,因此应积极探索更加科学的转炉炼钢发展策略,保障转炉炼钢的可持续发展。
1转炉炼钢现状分析1.1转炉钢产量和比例近年来,随着转炉数量的增加以及转炉炼钢工艺的完善,使得转炉钢的产量不断提升,相应在我国钢产量中,转炉钢所占比例也在不断增加。
在2000年以来,我国转炉钢产量增幅明显,远远领先于世界平均水平。
近年来我国转炉钢的占比始终处于80%以上,而在2016年我国转炉钢占比则达到89.9%,这一比例是电炉钢的9倍左右,由此可见,我国转炉钢的占比较高。
1.2主要技术经济指标分析1.2.1钢铁料消耗目前,在一些大中型钢铁企业转炉炼钢过程中,对钢铁料的消耗比例不断下降,2006年的平均水平1081.67kg/t,并且呈逐年下降趋势。
有的先进的钢铁企业,对钢铁料的消耗比例已经降至1060kg/t左右,这样的钢铁料消耗水平已经达到了世界先进水平。
国内外电炉炼钢技术现状与发展趋势
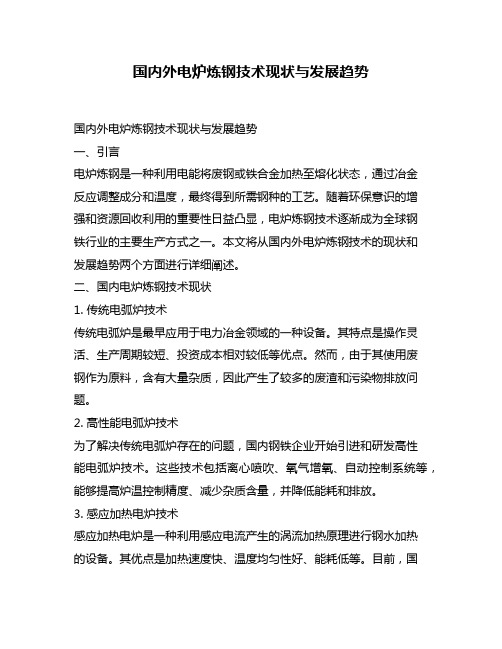
国内外电炉炼钢技术现状与发展趋势国内外电炉炼钢技术现状与发展趋势一、引言电炉炼钢是一种利用电能将废钢或铁合金加热至熔化状态,通过冶金反应调整成分和温度,最终得到所需钢种的工艺。
随着环保意识的增强和资源回收利用的重要性日益凸显,电炉炼钢技术逐渐成为全球钢铁行业的主要生产方式之一。
本文将从国内外电炉炼钢技术的现状和发展趋势两个方面进行详细阐述。
二、国内电炉炼钢技术现状1. 传统电弧炉技术传统电弧炉是最早应用于电力冶金领域的一种设备。
其特点是操作灵活、生产周期较短、投资成本相对较低等优点。
然而,由于其使用废钢作为原料,含有大量杂质,因此产生了较多的废渣和污染物排放问题。
2. 高性能电弧炉技术为了解决传统电弧炉存在的问题,国内钢铁企业开始引进和研发高性能电弧炉技术。
这些技术包括离心喷吹、氧气增氧、自动控制系统等,能够提高炉温控制精度、减少杂质含量,并降低能耗和排放。
3. 感应加热电炉技术感应加热电炉是一种利用感应电流产生的涡流加热原理进行钢水加热的设备。
其优点是加热速度快、温度均匀性好、能耗低等。
目前,国内一些大型钢铁企业已经开始采用感应加热电炉进行生产。
三、国外电炉炼钢技术现状1. 电弧顶吹转底吹技术欧洲一些先进的钢铁企业采用了电弧顶吹转底吹技术,即在高温下通过底部喷吹气体将冶金反应进行到底部。
这种技术可以提高冶金反应效率,减少杂质含量,并且可以利用多种原料进行冶金。
2. 水冷壳体技术美国的一些电炉炼钢企业采用了水冷壳体技术,通过在电炉壳体内部设置水冷设备,有效降低了电炉温度,减少了能耗,并且延长了设备寿命。
四、国内外电炉炼钢技术发展趋势1. 环保型电炉技术随着环保意识的增强,国内外钢铁企业开始重视电炉炼钢过程中的排放问题。
未来的发展趋势将是开发和应用更加环保的电炉技术,减少废气、废水和固体废弃物排放。
2. 智能化控制系统随着信息技术的快速发展,智能化控制系统在电炉炼钢领域得到了广泛应用。
未来的发展趋势将是进一步提高控制精度和自动化程度,实现智能化生产。
贝塞麦转炉炼钢法
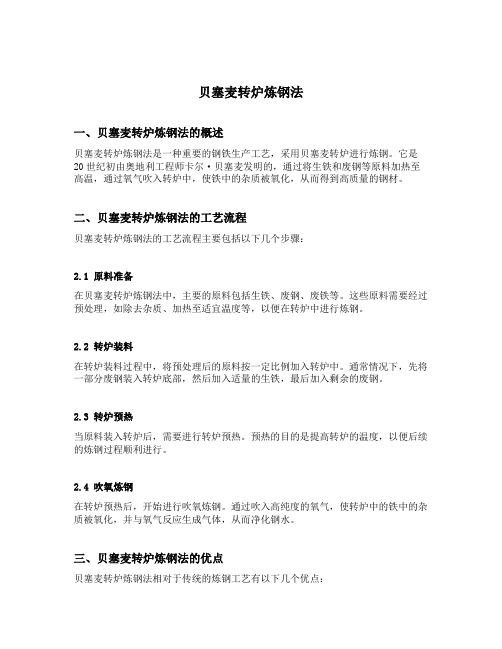
贝塞麦转炉炼钢法一、贝塞麦转炉炼钢法的概述贝塞麦转炉炼钢法是一种重要的钢铁生产工艺,采用贝塞麦转炉进行炼钢。
它是20世纪初由奥地利工程师卡尔·贝塞麦发明的,通过将生铁和废钢等原料加热至高温,通过氧气吹入转炉中,使铁中的杂质被氧化,从而得到高质量的钢材。
二、贝塞麦转炉炼钢法的工艺流程贝塞麦转炉炼钢法的工艺流程主要包括以下几个步骤:2.1 原料准备在贝塞麦转炉炼钢法中,主要的原料包括生铁、废钢、废铁等。
这些原料需要经过预处理,如除去杂质、加热至适宜温度等,以便在转炉中进行炼钢。
2.2 转炉装料在转炉装料过程中,将预处理后的原料按一定比例加入转炉中。
通常情况下,先将一部分废钢装入转炉底部,然后加入适量的生铁,最后加入剩余的废钢。
2.3 转炉预热当原料装入转炉后,需要进行转炉预热。
预热的目的是提高转炉的温度,以便后续的炼钢过程顺利进行。
2.4 吹氧炼钢在转炉预热后,开始进行吹氧炼钢。
通过吹入高纯度的氧气,使转炉中的铁中的杂质被氧化,并与氧气反应生成气体,从而净化钢水。
三、贝塞麦转炉炼钢法的优点贝塞麦转炉炼钢法相对于传统的炼钢工艺有以下几个优点:3.1 原料适应性强贝塞麦转炉炼钢法可以利用多种原料进行炼钢,如生铁、废钢、废铁等。
这使得钢铁企业可以更加灵活地选择原料,同时也能够有效地回收利用废钢等资源。
3.2 炼钢效率高贝塞麦转炉炼钢法采用高温吹氧的方式进行炼钢,可以快速氧化和除去铁中的杂质。
这使得炼钢过程更加高效,能够大幅提高钢水的质量和产量。
3.3 环保性好由于贝塞麦转炉炼钢法采用氧气吹炼的方式,相比传统的炼钢工艺,其燃烧产生的废气中含有较少的有害物质。
这有助于减少对环境的污染,符合现代环保要求。
四、贝塞麦转炉炼钢法的应用贝塞麦转炉炼钢法在钢铁行业得到了广泛的应用。
它已成为现代钢铁生产的重要工艺之一,主要应用于以下几个方面:4.1 高炉炼钢转向转炉炼钢传统的钢铁生产工艺主要依靠高炉进行炼钢,但高炉炼钢存在一些缺点,如燃料消耗大、环境污染等。
炼钢短流程工艺国内外现状及发展趋势

炼钢短流程工艺国内外现状及发展趋势一、引言炼钢短流程工艺是一种高效、节能、环保的炼钢技术,近年来在钢铁行业得到了越来越广泛的应用。
本文将从国内外炼钢短流程工艺的现状和发展趋势两方面展开探讨,旨在全面了解炼钢短流程工艺在钢铁生产中的地位和未来发展的方向。
二、炼钢短流程工艺的定义炼钢短流程工艺,顾名思义,即指采用高效、快捷的生产流程,通过电弧炉、转炉等设备,将废钢、废铁等原料快速熔化,然后经过连铸、轧制等工艺,最终生产出优质的钢材。
相比传统的炼钢工艺,短流程工艺具有炼钢周期短、能耗低、环境友好等优点。
三、国内外炼钢短流程工艺的现状1. 国内炼钢短流程工艺的现状从国内炼钢短流程工艺的发展历程来看,经过不断的技术创新和装备升级,我国在炼钢短流程领域已取得了长足的进步。
目前,国内许多钢铁企业已经采用了炼钢短流程工艺,如宝钢、武钢等,他们在炼钢短流程工艺上的投入和研究也取得了一定的成果。
2. 国外炼钢短流程工艺的现状与国内相比,国外在炼钢短流程工艺领域的发展历史较长。
欧美等发达国家早在20世纪80年代就开始大力推广炼钢短流程工艺,目前已建立健全了一套成熟的炼钢短流程工艺体系。
日本、韩国等亚洲国家也在炼钢短流程工艺方面取得了一些重要的进展。
四、炼钢短流程工艺的发展趋势1. 技术创新是推动炼钢短流程工艺发展的关键随着科技的不断进步,炼钢短流程工艺也在不断进行技术创新。
新型的炼钢设备、智能化的生产管理系统等技术的应用,将进一步提高炼钢效率,降低成本,推动炼钢短流程工艺向更高效、更环保的方向发展。
2. 绿色炼钢是未来发展的主流趋势随着环保意识的增强和国际环保标准的不断提高,绿色炼钢必将成为未来炼钢工艺发展的主流趋势。
炼钢短流程工艺作为一种清洁生产技术,将在未来得到更广泛的应用,成为钢铁行业的主要发展方向。
五、结语炼钢短流程工艺作为一种新兴的炼钢技术,已经在国内外得到了广泛的关注和应用。
通过对国内外炼钢短流程工艺的现状和发展趋势的分析,我们可以清晰地看到炼钢短流程工艺在钢铁行业的重要地位以及未来发展的方向。
转炉炼钢技术的发展与展望
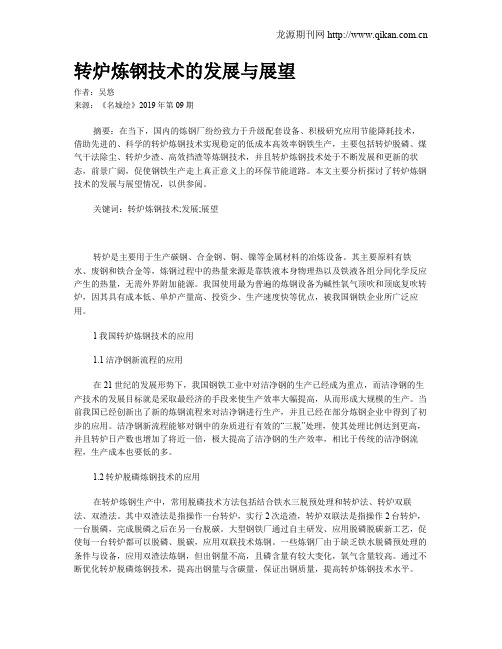
转炉炼钢技术的发展与展望作者:吴悠来源:《名城绘》2019年第09期摘要:在当下,国内的炼钢厂纷纷致力于升级配套设备、积极研究应用节能降耗技术,借助先进的、科学的转炉炼钢技术实现稳定的低成本高效率钢铁生产,主要包括转炉脱磷、煤气干法除尘、转炉少渣、高效挡渣等炼钢技术,并且转炉炼钢技术处于不断发展和更新的状态,前景广阔,促使钢铁生产走上真正意义上的环保节能道路。
本文主要分析探讨了转炉炼钢技术的发展与展望情况,以供参阅。
关键词:转炉炼钢技术;发展;展望转炉是主要用于生产碳钢、合金钢、铜、镍等金属材料的冶炼设备。
其主要原料有铁水、废钢和铁合金等,炼钢过程中的热量来源是靠铁液本身物理热以及铁液各组分间化学反应产生的热量,无需外界附加能源。
我国使用最为普遍的炼钢设备为碱性氧气顶吹和顶底复吹转炉,因其具有成本低、单炉产量高、投资少、生产速度快等优点,被我国钢铁企业所广泛应用。
1我国转炉炼钢技术的应用1.1洁净钢新流程的应用在21世纪的发展形势下,我国钢铁工业中对洁净钢的生产已经成为重点,而洁净钢的生产技术的发展目标就是采取最经济的手段来使生产效率大幅提高,从而形成大规模的生产。
当前我国已经创新出了新的炼钢流程来对洁净钢进行生产,并且已经在部分炼钢企业中得到了初步的应用。
洁净钢新流程能够对钢中的杂质进行有效的“三脱”处理,使其处理比例达到更高,并且转炉日产数也增加了将近一倍,极大提高了洁净钢的生产效率,相比于传统的洁净钢流程,生产成本也要低的多。
1.2转炉脱磷炼钢技术的应用在转炉炼钢生产中,常用脱磷技术方法包括结合铁水三脱预处理和转炉法、转炉双联法、双渣法。
其中双渣法是指操作一台转炉,实行2次造渣,转炉双联法是指操作2台转炉,一台脱磷,完成脱磷之后在另一台脱碳。
大型钢铁厂通过自主研发、应用脱磷脱碳新工艺,促使每一台转炉都可以脱磷、脱碳,应用双联技术炼钢。
一些炼钢厂由于缺乏铁水脱磷预处理的条件与设备,应用双渣法炼钢,但出钢量不高,且磷含量有较大变化,氧气含量较高。
2024年炼钢转炉市场分析现状

2024年炼钢转炉市场分析现状引言炼钢转炉作为一种重要的冶金设备,在钢铁行业中发挥着关键的作用。
通过对炼钢转炉市场的分析,可以了解目前市场的现状,并为相关企业提供参考。
本文将对炼钢转炉市场的现状进行分析,并提供一些市场发展趋势的展望。
1. 炼钢转炉市场概述炼钢转炉市场是钢铁行业的一个重要细分市场。
炼钢转炉可以将生铁或废钢进行炼钢,并将其转变为高质量的钢材产品。
炼钢转炉的市场需求受到了全球经济状况、工业发展、钢铁行业需求等因素的影响。
2. 炼钢转炉市场现状2.1 市场规模目前,全球炼钢转炉市场规模庞大。
据统计,2019年全球炼钢转炉市场规模达到XX美元。
### 2.2 市场竞争格局炼钢转炉市场存在着一些主要的竞争企业。
这些企业通过提供先进的技术和设备,不断提高产品的品质和性能,争夺市场份额。
目前,市场竞争激烈,企业需要通过不断创新和提高产品质量来获得竞争优势。
### 2.3 市场发展趋势炼钢转炉市场发展呈现以下趋势: - 高效、节能环保:随着环保意识的提高,市场对于高效、节能环保型炼钢转炉的需求逐渐增加。
- 技术创新:新型技术的不断涌现,推动了炼钢转炉市场的发展。
例如,利用先进的炼钢转炉煤气净化技术能够提高产品的品质和环境友好度。
- 自动化控制:随着自动化技术的进步,市场对于能够实现自动化控制的炼钢转炉的需求逐渐增加。
- 市场多元化:随着全球经济的发展,炼钢转炉市场也将趋向于多元化,不仅仅局限于钢铁行业,还包括其他行业的需求。
3. 影响炼钢转炉市场发展的因素3.1 经济状况炼钢转炉市场的发展与全球经济状况密切相关。
当经济状况好时,工业生产增加,对炼钢转炉的需求相应增加;而当经济状况不佳时,工业生产下降,对炼钢转炉的需求也相应减少。
### 3.2 环保政策环保政策对于炼钢转炉市场的发展起着重要的影响。
环保要求越来越严格,市场对于节能环保型炼钢转炉的需求不断增加。
同时,环保政策的改变也可能会影响企业的生产布局和技术升级。
我国转炉炼钢技术发展现状与趋势分析

我国转炉炼钢技术发展现状与趋势1、转炉炼钢技术发展现状目前,转炉炼钢仍是世界上最主要的炼钢方法,其钢产量占世界钢总产量的65%以上。
由于我国废钢资源短缺,电力缺乏,电价偏高,因此电炉钢的产量增长受到一定程度的制约,而随着生铁资源的充裕也给转炉钢产量的增长提供了良好条件。
因此,转炉钢产量近年来获得了快速增长。
2905年我国转炉钢产量为3.14亿吨,到2013年提高到7.65亿吨。
随着转炉钢产量的增加,转炉炼钢生产工艺技术也得到迅速发展。
转炉炼钢技术进步主要体现在以下几个方面。
1.1、转炉装备日趋大型化2001年我国100吨以上大型转炉只有30座,产能为3602万吨。
至2013年增长到345座,产能超过5.08亿吨,13年间大型转炉的生产能力增长了14倍。
其中300吨转炉从3座增加到11座,产能从678万吨增长到2759万吨以上。
从数量上来看,我国现有转炉中以100-199吨的转炉数量最多,而200吨及以上的转炉数量最少,我国仍然保有一定数量的30吨以下的转炉。
因此,淘汰落后产能任务艰巨。
目前,我国100吨及以上转炉的产能约占全部转炉产能的67.5%。
随着淘汰落后产能力度的加大,我国转炉将进一步朝着大型化方向发展。
1.2、转炉生产工艺进一步优化提高钢材洁净度是21世纪钢材质量发展的重大技术方向。
为提高钢材质量且扩大冶炼钢种,我国大、中型转炉炼钢厂都相继增建了铁水脱硫装置和二次精炼装置。
近年来新建的转炉炼钢厂大多配置了铁水脱硫装置,并根据冶炼钢种的要求配置了相应的炉外精炼装置,一般多采用LF精炼,有些转炉炼钢厂还配置了Ⅵ)精炼装置,从而为高附加值钢种的生产提供了有利条件。
我国自主设计建设的京唐公司300吨转炉采用了国际上最先进的脱磷炉与脱碳炉分工、联合生产的工艺,京唐公司是国际上最早采用这一先进工艺的300吨转炉大型炼钢厂。
经过近两年的技术攻关,脱磷炉生产周期28min,脱碳炉32min;单炉班产炉数从7-8炉次提高至16炉次,转炉生产效率提高1倍,出钢温度平均降低20℃。
转炉脱磷少渣炼钢工艺技术发展与现状概述

转炉脱磷少渣炼钢工艺技术发展与现状概述引言钢铁是现代社会重要的基础材料之一,而磷是钢铁中的一个有害杂质。
传统的炼钢工艺中,磷的含量往往难以控制,导致钢材性能下降。
为了解决这个问题,转炉脱磷少渣炼钢工艺被广泛应用。
本文将对转炉脱磷少渣炼钢工艺的发展与现状进行概述。
转炉脱磷少渣炼钢工艺的原理转炉脱磷少渣炼钢工艺是通过将含有磷的原料在高温下与氧化剂反应,将磷转化为易脱离熔渣的磷酸盐,从而实现脱磷的目的。
其基本原理如下:1.熔融脱磷:在高温条件下,钢中的磷溶解于熔渣中,通过加入适量的熔剂,形成易分离的磷酸盐熔渣。
2.氧化脱磷:在高温条件下,将空气、氧气或含氧气的气体通入转炉中,氧化钢中的磷,将其转化为磷酸盐。
3.过渡氧化脱磷:在转炉炉脱磷过程中,通过在转炉中加入适量的铁素体,将磷转化为铁磷,再将其转化为磷酸盐。
转炉脱磷少渣炼钢工艺的发展历程转炉脱磷少渣炼钢工艺起源于20世纪50年代,经过多年的研究和改进,逐渐成熟并得到广泛应用。
其发展历程主要包括以下几个阶段:1.早期工艺的发展:早期的转炉脱磷少渣炼钢工艺主要采用人工喷镁的方式进行脱磷,但由于操作不稳定、生产效率低等问题,限制了其在实际生产中的应用。
2.化学脱磷工艺的应用:20世纪60年代,化学脱磷工艺开始应用于转炉脱磷少渣炼钢中。
该工艺是通过加入一定比例的化学试剂,如石灰石、白云石等,与熔渣中的磷反应,形成易分离的磷酸盐。
3.氧化脱磷工艺的引入:20世纪70年代,随着氧气和氧气枪在炼钢工艺中的应用,氧化脱磷工艺得到了推广。
该工艺是通过在转炉中加入氧气,氧化钢中的磷,将其转化为磷酸盐。
4.过渡氧化脱磷工艺的发展:20世纪80年代,随着对转炉脱磷少渣炼钢工艺的进一步研究和优化,过渡氧化脱磷工艺得到了广泛应用。
该工艺是通过在转炉中加入铁素体,将磷转化为铁磷,再将其转化为磷酸盐。
5.现代工艺的创新与应用:近年来,随着科技的进步和钢铁工业的发展,转炉脱磷少渣炼钢工艺逐渐采用自动化控制、机器学习等现代技术,提高了工艺的稳定性和生产效率。
浅谈转炉炼钢技术的应用和革新途径

浅谈转炉炼钢技术的应用和革新途径转炉炼钢技术是钢铁生产中的一种主流工艺,它是利用氧气吹炼炉内的铁水来脱除杂质和调整成分,从而得到高质量的钢材。
该技术具有成本低廉、现场环境友好等优点,在工业生产中得到广泛应用。
本文将从应用和革新两方面对转炉炼钢技术进行讨论。
1. 炼钢成本低廉转炉炼钢技术使用廉价的废钢和铁水为原料,氧气吹炼过程中水泥窑含铁偏高,能将废钢和铁水中的碳、硅等杂质快速脱除,使得成品钢的纯度和质量得到大幅提升。
2. 生产过程环境友好传统的炼钢工艺需要使用高炉或电炉等高能耗设备,同时还需要大量燃料和化学物品来降低氧气含量和脱除杂质,因此其产生的二氧化碳和有害气体对环境危害极大。
而转炉炼钢技术可节约能源、降低化学物品的使用量,对环境友好,生产过程中减少了废气排放。
3. 灵活性高转炉炼钢技术生产线可根据要求进行灵活的操作和调整,能满足不同产品的生产需求,为生产企业带来更灵活、更快速的生产流程和更加优秀的产品。
1. 新型转炉设计针对传统转炉炼钢技术中的一些问题,如生产效率低、铁水的脱硫需要加长时间等问题,现有技术途径和设计方法已经逐渐得到改进。
科学家们正在探索采用新型转炉,如高效能转炉、高炉复合转炉等设计,以提高生产效率和产量。
2. 高温物理学控制技术高温物理学控制技术旨在利用高精度传感器和数据采集技术,对转炉生产过程进行精准化控制,从而达到更高的生产效率和实施更有效的质量控制。
同时,该技术还能够实现物料流量的控制,改善现有的生产流程和设备。
3. 先进的燃料和氧气供应技术先进的燃料和氧气供应技术,如高效燃烧和回收技术,可减少能源消耗和二氧化碳排放量。
这些技术在生产工艺和环保方面得到了广泛应用,在转炉炼钢技术中也有很好的应用前景。
总之,转炉炼钢技术是钢铁生产中非常重要的工艺之一,它的应用和发展具有明显的优势。
而在革新途径方面,新型转炉设计、高温物理学控制技术、以及先进的燃料和氧气供应技术都是有望推动该技术及其产业革新的关键领域。
国内外电炉炼钢技术现状与发展趋势
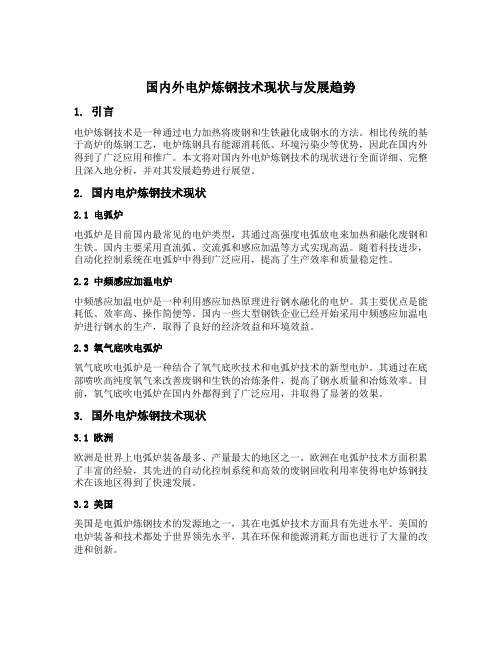
国内外电炉炼钢技术现状与发展趋势1. 引言电炉炼钢技术是一种通过电力加热将废钢和生铁融化成钢水的方法。
相比传统的基于高炉的炼钢工艺,电炉炼钢具有能源消耗低、环境污染少等优势,因此在国内外得到了广泛应用和推广。
本文将对国内外电炉炼钢技术的现状进行全面详细、完整且深入地分析,并对其发展趋势进行展望。
2. 国内电炉炼钢技术现状2.1 电弧炉电弧炉是目前国内最常见的电炉类型,其通过高强度电弧放电来加热和融化废钢和生铁。
国内主要采用直流弧、交流弧和感应加温等方式实现高温。
随着科技进步,自动化控制系统在电弧炉中得到广泛应用,提高了生产效率和质量稳定性。
2.2 中频感应加温电炉中频感应加温电炉是一种利用感应加热原理进行钢水融化的电炉。
其主要优点是能耗低、效率高、操作简便等。
国内一些大型钢铁企业已经开始采用中频感应加温电炉进行钢水的生产,取得了良好的经济效益和环境效益。
2.3 氧气底吹电弧炉氧气底吹电弧炉是一种结合了氧气底吹技术和电弧炉技术的新型电炉。
其通过在底部喷吹高纯度氧气来改善废钢和生铁的冶炼条件,提高了钢水质量和冶炼效率。
目前,氧气底吹电弧炉在国内外都得到了广泛应用,并取得了显著的效果。
3. 国外电炉炼钢技术现状3.1 欧洲欧洲是世界上电弧炉装备最多、产量最大的地区之一。
欧洲在电弧炉技术方面积累了丰富的经验,其先进的自动化控制系统和高效的废钢回收利用率使得电炉炼钢技术在该地区得到了快速发展。
3.2 美国美国是电弧炉炼钢技术的发源地之一,其在电弧炉技术方面具有先进水平。
美国的电炉装备和技术都处于世界领先水平,其在环保和能源消耗方面也进行了大量的改进和创新。
3.3 日本日本是世界上电弧炉装备密度最高的国家之一。
日本在电弧炉技术方面注重节能减排,通过采用高效的冷却系统、优化的气体循环等手段降低能耗和环境污染。
同时,日本还致力于提高钢水质量和冶炼效率,不断推动电炉炼钢技术向更高水平发展。
4. 电炉炼钢技术发展趋势4.1 自动化控制系统随着科技进步和人工智能技术的发展,自动化控制系统在电炉炼钢中将发挥越来越重要的作用。
炼钢行业发展现状及未来趋势分析

炼钢行业发展现状及未来趋势分析【引言】炼钢行业是现代工业中至关重要的部分,其发展对于国家经济和社会发展具有重要影响。
本文将对炼钢行业的现状进行分析,并展望其未来的发展趋势。
【发展现状】1. 全球炼钢行业的现状全球炼钢行业目前处于竞争激烈的环境中。
中国、印度和日本是世界上最大的炼钢生产国家,它们的炼钢产量占全球总量的60%以上。
这些国家不仅拥有大规模的钢铁生产能力,而且在技术创新方面也具备一定优势。
然而,近年来,由于经济增长放缓和环保压力增加,这些国家的炼钢产量出现了下降趋势。
2. 中国炼钢行业现状中国是世界上最大的炼钢生产国家。
然而,近年来,受到环保限产政策的影响,中国的炼钢业面临一些挑战。
一方面,由于环境压力,炼钢企业不得不进行减产或停产,这导致了钢铁供应短缺和钢价上涨。
另一方面,中国政府积极推动炼钢产能的优化升级,以提高能源效率和减少环境污染。
3. 炼钢行业的技术创新炼钢行业在技术创新方面取得了很大的进展。
新技术的应用提高了炼钢工艺的效率和质量。
例如,转炉炼钢技术和炼铁炉连铸技术的应用,使得炼钢过程更加节能高效。
此外,数字化技术的应用也使得生产过程更加自动化和智能化。
【未来趋势分析】1. 绿色发展是必然趋势随着全球对环境保护的关注度不断提高,绿色发展已成为炼钢行业的必然趋势。
各国政府将进一步加强对炼钢行业的环保监管,推动企业进行绿色转型。
炼钢企业需要采用更加环保的生产技术,并加强对废气、废水和固体废弃物的处理,以减少对环境的污染。
2. 技术创新将推动行业发展在未来,技术创新将成为推动炼钢行业发展的关键因素。
新材料、新工艺和新设备的应用将进一步提高炼钢过程的效率和质量。
例如,高效燃烧技术的应用可以减少能源消耗和二氧化碳的排放。
此外,数字化技术的应用将促进炼钢企业进行智能化升级,提高生产过程的自动化水平。
3. 供应链协同将成为重要趋势炼钢行业的供应链是支撑其正常运转的基石。
未来,供应链协同将成为行业发展的重要趋势。
转炉炼钢目标
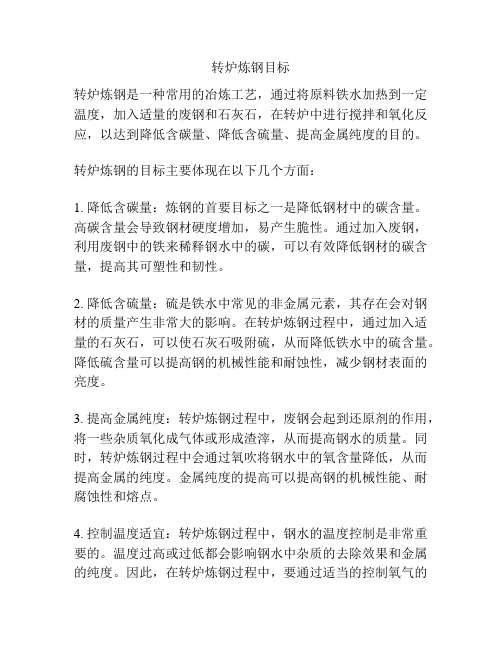
转炉炼钢目标转炉炼钢是一种常用的冶炼工艺,通过将原料铁水加热到一定温度,加入适量的废钢和石灰石,在转炉中进行搅拌和氧化反应,以达到降低含碳量、降低含硫量、提高金属纯度的目的。
转炉炼钢的目标主要体现在以下几个方面:1. 降低含碳量:炼钢的首要目标之一是降低钢材中的碳含量。
高碳含量会导致钢材硬度增加,易产生脆性。
通过加入废钢,利用废钢中的铁来稀释钢水中的碳,可以有效降低钢材的碳含量,提高其可塑性和韧性。
2. 降低含硫量:硫是铁水中常见的非金属元素,其存在会对钢材的质量产生非常大的影响。
在转炉炼钢过程中,通过加入适量的石灰石,可以使石灰石吸附硫,从而降低铁水中的硫含量。
降低硫含量可以提高钢的机械性能和耐蚀性,减少钢材表面的亮度。
3. 提高金属纯度:转炉炼钢过程中,废钢会起到还原剂的作用,将一些杂质氧化成气体或形成渣滓,从而提高钢水的质量。
同时,转炉炼钢过程中会通过氧吹将钢水中的氧含量降低,从而提高金属的纯度。
金属纯度的提高可以提高钢的机械性能、耐腐蚀性和熔点。
4. 控制温度适宜:转炉炼钢过程中,钢水的温度控制是非常重要的。
温度过高或过低都会影响钢水中杂质的去除效果和金属的纯度。
因此,在转炉炼钢过程中,要通过适当的控制氧气的供给量和搅拌速度,使得钢水的温度保持在适宜的范围内。
同时,转炉炼钢过程中还需要加入一定量的冷却剂,以控制钢水的温度。
在转炉炼钢的过程中,除了以上目标外,还需要考虑到资源的利用和环保因素。
废钢的利用不仅可以减少资源的浪费,还可以减少对环境的压力。
此外,转炉炼钢过程中也需要对产生的废气和废渣进行合理处理,以减少对环境的污染。
因此,在转炉炼钢过程中要注重实现经济效益和环境效益的双重目标。
总之,转炉炼钢的目标是通过加入废钢和石灰石,利用适当的氧化反应和搅拌,降低含碳量、含硫量,提高金属纯度,控制温度适宜,同时考虑资源利用和环境因素,实现优质炼钢的目标。
通过不断的技术创新和工艺改进,转炉炼钢的目标可以得到更好的实现。
转炉炼钢系统技术与设备的发展分析

转炉炼钢系统技术与设备的发展分析摘要:近年来,在社会经济快速发展的带动下,我国各个行业的发展都取得了显著的成绩,为钢铁行业的发展带来了诸多的机遇,为各项专业技术的发展奠定了坚实的基础。
炼钢技术以及设备的发展为新型工业化发展起到了积极的助动作用,促使我国成为了世界钢铁大国。
但是因为我国钢铁生产中存在吨钢能耗高、劳动生产率低下的问题,这样就对我国钢铁行业的发展带来了诸多的阻碍,鉴于此我们还需要进一步的转炉炼钢技术和先进炼钢设备进行优化和完善。
关键词:转炉炼钢;发展;展望引言钢铁产业在我国社会经济发展中起到了至关重要的作用,其生产技术水平的稳步提升为我国钢铁产业的发展给予了良好的辅助。
这篇文章主要围绕我国转炉炼钢技术的发展展开深入细致的研究分析,希望能够对我国综合国力的未来持续健康发展有所帮助。
1现代转炉炼钢存在的问题1.1废钢资源问题废钢资源问题长期以来都是人们所关注的重点,当下我国大陆的钢材回收周期因为受到多方面因素的影响有所增加,没有形成较为严重的废钢问题,再加上转炉炼钢中会遇到无法避免的消耗等问题,所以导致废钢的转化率相对较低。
相对于很多其他国家,我国废钢产量较少,并且因为我国存在严重的废钢资源利用不足,所以导致我国还没有彻底的解决废钢资源匮乏的问题。
1.2转炉炼钢也会造成不容忽视的环保问题在转炉炼钢的过程中通常都会产生诸多的粉灰污染,并且因为近些年我国环保监控工作没有得到了良好的重视,这样就导致炼钢的成本在逐渐的增加。
尽管我国大陆对于除尘设备在不断地优化,并且也创建了大量的除尘系统的,但是还是无法满足当前人们对于环保工作的需要,这样就对转炉炼钢产业的发展造成了诸多的限制。
1.3炼钢除尘中的环境问题在上世纪八十年代,国内外转炉炼钢技术水平得以不断地提升,在这种形势下装备水平随之逐渐的完善,我国转炉除尘技术随之不断地发展。
在当前新的历史阶段,炼钢除尘工作越发的收到了人们的重视,并且也取得了良好的成绩,怎样彻底的解决炼钢除尘中所涉及到的环境问题,还需要我们进一步的进行研究分析。
钢铁冶炼工艺的发展趋势
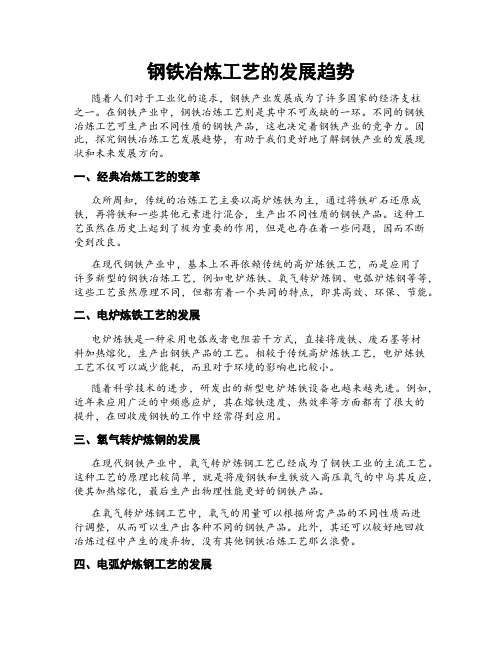
钢铁冶炼工艺的发展趋势随着人们对于工业化的追求,钢铁产业发展成为了许多国家的经济支柱之一。
在钢铁产业中,钢铁冶炼工艺则是其中不可或缺的一环。
不同的钢铁冶炼工艺可生产出不同性质的钢铁产品,这也决定着钢铁产业的竞争力。
因此,探究钢铁冶炼工艺发展趋势,有助于我们更好地了解钢铁产业的发展现状和未来发展方向。
一、经典冶炼工艺的变革众所周知,传统的冶炼工艺主要以高炉炼铁为主,通过将铁矿石还原成铁,再将铁和一些其他元素进行混合,生产出不同性质的钢铁产品。
这种工艺虽然在历史上起到了极为重要的作用,但是也存在着一些问题,因而不断受到改良。
在现代钢铁产业中,基本上不再依赖传统的高炉炼铁工艺,而是应用了许多新型的钢铁冶炼工艺,例如电炉炼铁、氧气转炉炼钢、电弧炉炼钢等等,这些工艺虽然原理不同,但都有着一个共同的特点,即其高效、环保、节能。
二、电炉炼铁工艺的发展电炉炼铁是一种采用电弧或者电阻若干方式,直接将废铁、废石墨等材料加热熔化,生产出钢铁产品的工艺。
相较于传统高炉炼铁工艺,电炉炼铁工艺不仅可以减少能耗,而且对于环境的影响也比较小。
随着科学技术的进步,研发出的新型电炉炼铁设备也越来越先进。
例如,近年来应用广泛的中频感应炉,其在熔铁速度、热效率等方面都有了很大的提升,在回收废钢铁的工作中经常得到应用。
三、氧气转炉炼钢的发展在现代钢铁产业中,氧气转炉炼钢工艺已经成为了钢铁工业的主流工艺。
这种工艺的原理比较简单,就是将废钢铁和生铁放入高压氧气的中与其反应,使其加热熔化,最后生产出物理性能更好的钢铁产品。
在氧气转炉炼钢工艺中,氧气的用量可以根据所需产品的不同性质而进行调整,从而可以生产出各种不同的钢铁产品。
此外,其还可以较好地回收冶炼过程中产生的废弃物,没有其他钢铁冶炼工艺那么浪费。
四、电弧炉炼钢工艺的发展电弧炉炼钢工艺是将铁铁加热到一定温度后,用电极在其之上进行电弧放电,使其熔化,再加入合适的合金元素,使钢铁达到一定性质的工艺。
转炉炼钢设备与工艺
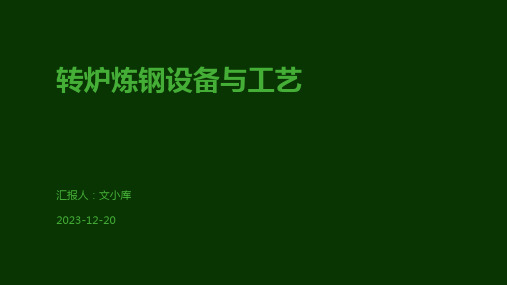
转炉炼钢设备应用领域
钢铁工业
用于生产高质量钢材,满足汽车、建筑、机械制 造等领域的需求。
国防建设
用于生产特殊钢材,满足武器装备制造的需求。
其他领域
还可应用于航空航天、能源等领域。
02
转炉炼钢工艺流程
原料准备与配料
原料准备
准备铁水、废钢、合金等原料,确保 原料质量和成分符合要求。
配料计算
根据钢种和冶炼要求,计算出各种原 料的加入量,确保钢水成分和温度的 稳定。
1 2
设备检查
操作前应对转炉设备进行全面检查,确保设备处 于良好状态。
严格遵守操作规程
按照规定的操作步骤进行操作,避免违规操作。
3
定期维护保养
对设备进行定期维护保养,确保设备正常运行。
转炉炼钢工艺环保要求及措施
减少废气排放
采用低硫、低磷、低氮 等环保型炼钢原料,降 低废气排放。
废水处理
对产生的废水进行分类 处理,实现废水零排放 。
维修保养
根据设备的使用情况和维修计划,进 行维修和保养工作,确保设备的正常 运行。
定期检查
定期对设备进行检查,包括关键部位 的检查和测量,确保设备处于良好状 态。
转炉炼钢设备故障排除方法
故障诊断
对设备出现的故障进行诊断,确 定故障的原因和部位。
排除故障
根据故障诊断结果,采取相应的措 施排除故障,恢复设备的正常运行 。
根据钢种和冶炼要求,向钢水中加入合金元素(如铬、镍、钨等),调整钢水成 分,以满足产品要求。
浇注与凝固过程
浇注
将脱氧和合金化后的钢水浇注到钢锭模或连铸结晶器中,形 成钢锭或连铸坯。
凝固
通过控制冷却速度和温度,使钢锭或连铸坯在凝固过程中形 成合理的晶粒结构和机械性能。
中国转炉炼钢工艺的发展史
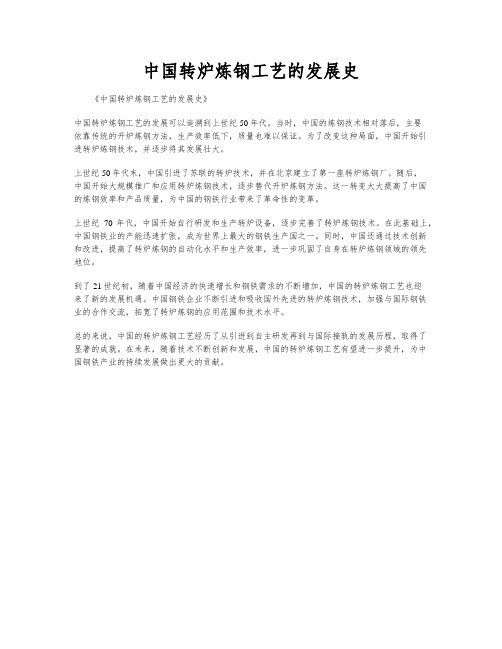
中国转炉炼钢工艺的发展史
《中国转炉炼钢工艺的发展史》
中国转炉炼钢工艺的发展可以追溯到上世纪50年代。
当时,中国的炼钢技术相对落后,主要
依靠传统的开炉炼钢方法,生产效率低下,质量也难以保证。
为了改变这种局面,中国开始引进转炉炼钢技术,并逐步将其发展壮大。
上世纪50年代末,中国引进了苏联的转炉技术,并在北京建立了第一座转炉炼钢厂。
随后,
中国开始大规模推广和应用转炉炼钢技术,逐步替代开炉炼钢方法。
这一转变大大提高了中国的炼钢效率和产品质量,为中国的钢铁行业带来了革命性的变革。
上世纪70年代,中国开始自行研发和生产转炉设备,逐步完善了转炉炼钢技术。
在此基础上,中国钢铁业的产能迅速扩张,成为世界上最大的钢铁生产国之一。
同时,中国还通过技术创新和改进,提高了转炉炼钢的自动化水平和生产效率,进一步巩固了自身在转炉炼钢领域的领先地位。
到了21世纪初,随着中国经济的快速增长和钢铁需求的不断增加,中国的转炉炼钢工艺也迎
来了新的发展机遇。
中国钢铁企业不断引进和吸收国外先进的转炉炼钢技术,加强与国际钢铁业的合作交流,拓宽了转炉炼钢的应用范围和技术水平。
总的来说,中国的转炉炼钢工艺经历了从引进到自主研发再到与国际接轨的发展历程,取得了显著的成就。
在未来,随着技术不断创新和发展,中国的转炉炼钢工艺有望进一步提升,为中国钢铁产业的持续发展做出更大的贡献。
- 1、下载文档前请自行甄别文档内容的完整性,平台不提供额外的编辑、内容补充、找答案等附加服务。
- 2、"仅部分预览"的文档,不可在线预览部分如存在完整性等问题,可反馈申请退款(可完整预览的文档不适用该条件!)。
- 3、如文档侵犯您的权益,请联系客服反馈,我们会尽快为您处理(人工客服工作时间:9:00-18:30)。
内容提要
20世纪转炉炼钢技术的发展历程 现代转炉炼钢的重大技术 21世纪转炉炼钢技术的发展 节能与环境保护
一、20世纪转炉炼钢技术的发展历程
氧气转炉炼钢是目前世界上最主要的炼钢方法。 2l世纪的前期,转炉钢的生产比例仍将保持在
60~70%。 回顾50年氧气转炉炼钢发展史,可划分为三个
2.2 顶底复吹转炉吹炼的工艺特点
顶底复吹转炉结合了顶吹、底吹转炉的优点: • 反应速度快,热效率高,可实现炉内二次燃烧 • 吹炼后期强化熔池搅拌,使钢—渣反应接近平衡 • 保持顶吹转炉成渣速度快和底吹转炉吹炼平稳的双重
优点 • 进一步提高了熔池脱磷脱硫的冶金效果 • 冶炼低碳钢(C=0.01~0.02%),避免了钢渣过氧化
• 渣中含铁量降低2.5~5.0% • 金属收得率提高0.5~1.5% • 残锰提高0.02~0.06% • 磷含量降低0.002% • 石灰消耗降低3~10kg/t • 氧气消耗减少4~6Nm3/t • 提高炉龄,减少耐火材料消耗
复吹转炉的经济效益,因冶炼的品种、炉子的大小 和各钢厂的具体情况下同而有差异。一般说来,在欧 洲约为2~3.6马克/t;在美国约为0.25~1.5美元/t; 在中国为6~15元/t。
转炉煤气成分、热值和回收气体量
宝钢、武钢三炼钢、君津钢厂煤气回收效果
2.4 负 能 炼 钢
当炉气回收的总热量>转炉生产消耗的能量时
(如动力电、钢包烘烤燃料、氧气等),实现了 转炉工序“ 负能炼钢”。
当炉气回收的总热量>炼钢厂生产消耗的总能量 时(包括炼钢、精炼、连铸等工序的能量消耗,
实现了炼钢厂的“ 负能炼钢”。
2.6 转炉长寿技术
转炉技术完善化时期(1970~1990年)
这一时期,由于连铸技术的迅速发展,出现了全连铸的 炼钢车间。
对转炉炼钢的稳定性和终点控制的准确性,提出更高的 要求。
为了改善转炉吹炼后期钢渣反应远离平衡,实现平稳吹 炼的目标,综合顶吹、底吹转炉的优点,研究开发出各 种顶底复合吹炼工艺,在全世界迅速推广。
2.3 煤气回收技术原理
氧气转炉炼钢过程产生大量气体,转炉 煤气温度约为1400~1500℃(物理热),煤 气热值(化学潜热)约为2000kcal/Nm3, 煤气量97~115 Nm3 /t。采用煤气回收技术 回收转炉烟气的化学潜热;采用余热锅炉回收 烟气的物理热.
煤气回收效果
当炉气回收的总热量>转炉生产消耗的能量 时,实现了转炉工序“负能炼钢”;当炉气回 收的总热量>炼钢厂生产消耗的总能量时,实现 了炼钢厂“负能炼钢”。日本君津钢厂、我国 宝钢、武钢三炼钢厂均已实现炼钢厂“负能炼
顶底复合吹炼技术的分类
顶吹氧,底吹惰性气体搅拌工艺:
代表方法有:LBE、LD-KG、LD-OTB、NK-CB、LD技术A特B等征。:
• 顶吹100%氧气,可采用二次 燃烧技术提高熔池热效率;
• 底吹惰性气体搅拌,前期吹N2 气后期切换为Ar气;
• 供气强度波动在0.03~0.12 Nm3/t.min范围。
二、现代转炉炼钢的重大技术
2.1 转炉大型化技术
实现转炉大型化具有以下优点:
• 显著提高生产效率和劳动生产率 • 吹炼平稳,易于实现煤气回收,终点动态控制 • 热损失小,成分稳定,有利于改善钢质量 • 易于与精炼特别是真空精炼相匹配
转炉大型化的核心技术
• 大型转炉(≥250t)的设计制造技术 • 水冷托圈与悬挂倾动—传动装置 • 多孔拉瓦尔氧气喷枪 • OG法除尘与煤气回收技术 • 镁碳砖生产工艺与制造技术 • 污水、污泥处理净化技术 • 综合砌炉与护炉工艺(喷补、挂粘渣等) • 吹炼静态模型控制技术 • 终点副枪动态控制技术
我国宝钢、武钢已实现了转炉工序“ 负能炼 钢”,而宝钢已实现了炼钢厂“ 负能炼钢”。
2.5炼钢厂节能的技术措施
降低铁钢比。每降低0.1%铁钢比,可降低吨钢能耗 70~85kg标准煤;
提高连铸比。和模铸相比,连铸可降低能耗50~80%, 提高成材率7~18%,折合标准煤63~162kg/t;
回收利用转炉煤气,可降低吨钢能耗3~11kg标准煤; 提高连铸坯热送比,可降低吨钢能耗1.9~2.1kg标准煤; 提高转炉作业率,可降低工序能耗3kg标准煤。
发展时期。
转炉大型化时期(1950~1970年)
这一历史时期,以转炉大型化为技术核心,逐 步完善转炉炼钢工艺与设备。
开发了大型转炉设计制造技术、除尘与煤气回 收技术、计算机静态与副枪动态控制技术、镁 碳砖综合砌炉与喷补挂渣等护炉技术。转炉炉 龄达到2000炉。
转炉吹炼制度为“ 三吹二”或“ 二吹一”
二、现代转炉炼钢的重大技术
转炉大型化技术
装备技术 工艺控制技术 节能与环保技术
合理的 H/D,合理的炉容比 全悬挂倾动机构,水冷托圈、耳轴、炉帽、汽水冷却 上料,称量与下料程序控制 下渣检查与有效的渣铁分离装置 统、长寿喷嘴与大气量调节强化 搅拌功能 炉渣、炉气与钢液的在线动态检测 全自动吹炼控制与信息管理系统 除尘与煤气回收,二次除尘设施,尽可能采取干法系统 炉口微压差控制与余热锅炉 炉衬厚度检测与炉体维护设施 拆、砌炉机械
这一时期转炉炉龄达到 5000炉,吹炼制度转变为“ 二 吹二”或“ 三吹三”。
转炉综合优化时期(1990~2010年)
建立起一种全新的、能大规模廉价生产纯净钢的 生产体系。
围绕纯净钢生产,研究开发出铁水“ 三脱”预 处理、高效转炉生产、全自动吹炼控制与长寿炉 龄等重大新工艺技术。
转炉炉龄超过10,000炉,初步实现“ 一座转炉 吹炼制”,形成炼钢——轧钢短流程生产线。
顶底复合吹氧工艺
代表方法: BSC-BAP、LD-OB、LD-HC、STB、STB-P、
K-BOP等
技术特征: 顶吹氧60~95%;底吹氧5~40%; 供气强度波动在0.2~2.0Nm3/t.min范围。 底吹供气元件采用双层套管结构,中心管吹 O2,环缝吹天然气或Ar气冷却保护喷咀。
复吹转炉的经济效益