金属工艺学(邓文英, 郭晓鹏, 邢忠文主编) 06第六章
金属工艺学_邓文英_第五版_课后习题参考答案

金属工艺学_邓文英_第五版_课后习题参考答案第一章(p11)1.什么是应力?什么是应变?答:应力是试样单位横截面的拉力;应变是试样在应力作用下单位长度的伸长量2.缩颈现象在拉伸实验中当载荷超过拉断前所承受的最大载荷时,试样上有部分开始变细,出现了“缩颈”。
缩颈发生在拉伸曲线上bk段。
不是,塑性变形在产生缩颈现象前就已经发生,如果没有出现缩颈现象也不表示没有出现塑性变形。
布氏硬度法和洛氏硬度法各有什么优缺点?下列材料或零件通常采用哪种方法检查其硬度?库存钢材硬质合金刀头锻件台虎钳钳口洛氏硬度法测试简便,缺点是测量费时,且压痕较大,不适于成品检验。
布氏硬度法测试值较稳定,准确度较洛氏法高。
;迅速,因压痕小,不损伤零件,可用于成品检验。
其缺点是测得的硬度值重复性较差,需在不同部位测量数次。
硬质合金刀头,台虎钳钳口用洛氏硬度法检验。
库存钢材和锻件用布氏硬度法检验。
第五题下列符号所表示的力学性能指标名称和含义是什么b抗拉强度它是指金属材料在拉断前所能承受的最大应力.屈服点它是指拉伸试样产生屈服时的应力。
0.2规定残余拉伸强度1疲劳强度它是指金属材料在应力可经受无数次应力循环不发生疲劳断裂,此应力称为材料的疲劳强度。
应力它指试样单位横截面的拉力。
aK冲击韧度它是指金属材料断裂前吸收的变形能量的能力韧性。
HRC洛氏硬度它是指将金刚石圆锥体施以100N的初始压力,使得压头与试样始终保持紧密接触,然后,向压头施加主载荷,保持数秒后卸除主载荷。
以残余压痕深度计算其硬度值。
HBS布氏硬度它是指用钢球直径为10mm,载荷为3000N为压头测试出的金属的布氏硬度。
HBW布氏硬度它是指以硬质合金球为压头的新型布氏度计。
第二章(p23)(1)什么是“过冷现象”过冷度指什么?答:实际结晶温度低于理论结晶温度(平衡结晶温度),这种线性称为“过冷”。
理论结晶温度与实际结晶温度之差,称为过冷度。
(2)金属的晶粒粗细对其力学性能有什么影响?细化晶粒的途径有哪些?答:金属的晶粒粗细对其力学性能有很大影响。
《金属工艺学》,邓文英版

3 .金属工艺学的课程特点 金属工艺学的课程特点 (1)是一门综合技术基础课,它除了包括传统 )是一门综合技术基础课, 的加工工艺,还包括了其它学科的诸多内容。 的加工工艺,还包括了其它学科的诸多内容。 (2)传统机械制造工艺的发展和改变,出现了 )传统机械制造工艺的发展和改变, 数字化、专业化、柔性化综合发展的新局面。 数字化、专业化、柔性化综合发展的新局面。 (3)金属工艺学是机械(电)类各专业必修的 )金属工艺学是机械( 技术基础课。在学习中,要完成传授知识、 技术基础课。在学习中,要完成传授知识、训 练技能和培养能力三个方面的任务。 练技能和培养能力三个方面的任务。
拉伸试验的方法是将图1—1(a)所示的标 准试样安装在拉伸试验机上,并对试样 施加一个缓慢增加的轴向拉力.随着拉 力增加,试样产生变形,直到断裂,如 图l—1(b)、(c)所示。用绝对伸长量L为 横坐标,外力p为纵坐标绘制出外力与伸 长量的关系曲线。图l—2为普通低碳钢的 拉伸曲线。
变形特点分析: ① OE段,变形与外力成正比,试样只产生弹性变形, 即当外力去除后,试样就恢复到原始长度。材料在弹 性范围内所能承受的最大应力称为弹性极限,用σe 表 示
六、疲劳强度 许多机械零件,如曲轴、齿轮、连杆、弹簧等,是在 交变载荷下的作用下工作的。虽然零件所受的应力远 低于材料的抗拉强度,甚至远低于屈服点,但在使用 中往往会发生突然断裂,这种现象称为疲劳破坏。据 统计,约有80%的机械零件的失效是属于疲劳造成的 。金属材料在无数次重复交变载荷作用下不致引起断 裂的最大应力称为疲劳强度。应力愈高,则断裂前所 承受的循环次数愈低,应力愈低,则断裂前所承受的 循环次数愈高,如图1—8所示。
式中:δ-一试样的伸长率,%; L0——试样的原始标距长度,mm; Lk——试样拉断后的标距长度,mm
金属工艺学课后习题答案
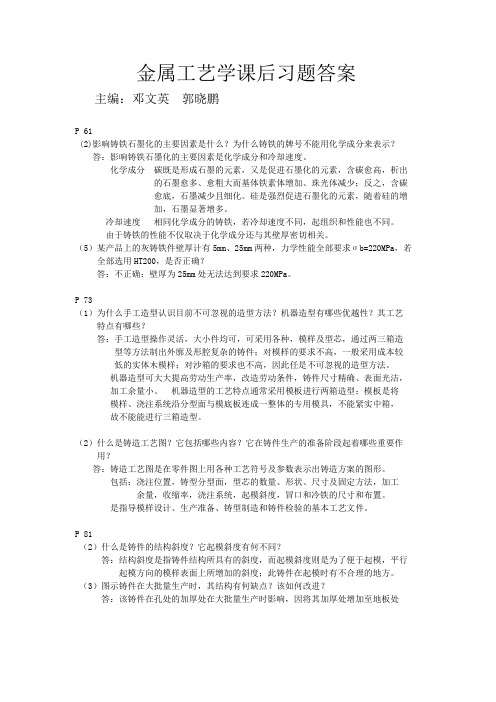
金属工艺学课后习题答案主编:邓文英郭晓鹏P 61(2)影响铸铁石墨化的主要因素是什么?为什么铸铁的牌号不能用化学成分来表示?答:影响铸铁石墨化的主要因素是化学成分和冷却速度。
化学成分碳既是形成石墨的元素,又是促进石墨化的元素,含碳愈高,析出的石墨愈多、愈粗大而基体铁素体增加、珠光体减少;反之,含碳愈底,石墨减少且细化。
硅是强烈促进石墨化的元素,随着硅的增加,石墨显著增多。
冷却速度相同化学成分的铸铁,若冷却速度不同,起组织和性能也不同。
由于铸铁的性能不仅取决于化学成分还与其壁厚密切相关。
(5)某产品上的灰铸铁件壁厚计有5mm、25mm两种,力学性能全部要求σb=220MPa,若全部选用HT200,是否正确?答:不正确;壁厚为25mm处无法达到要求220MPa。
P 73(1)为什么手工造型认识目前不可忽视的造型方法?机器造型有哪些优越性?其工艺特点有哪些?答:手工造型操作灵活,大小件均可,可采用各种,模样及型芯,通过两三箱造型等方法制出外廓及形腔复杂的铸件;对模样的要求不高,一般采用成本较低的实体木模样;对沙箱的要求也不高,因此任是不可忽视的造型方法。
机器造型可大大提高劳动生产率,改造劳动条件,铸件尺寸精确、表面光洁,加工余量小。
机器造型的工艺特点通常采用模板进行两箱造型;模板是将模样、浇注系统沿分型面与模底板连成一整体的专用模具,不能紧实中箱,故不能能进行三箱造型。
(2)什么是铸造工艺图?它包括哪些内容?它在铸件生产的准备阶段起着哪些重要作用?答:铸造工艺图是在零件图上用各种工艺符号及参数表示出铸造方案的图形。
包括:浇注位置,铸型分型面,型芯的数量、形状、尺寸及固定方法,加工余量,收缩率,浇注系统,起模斜度,冒口和冷铁的尺寸和布置。
是指导模样设计、生产准备、铸型制造和铸件检验的基本工艺文件。
P 81(2)什么是铸件的结构斜度?它起模斜度有何不同?答:结构斜度是指铸件结构所具有的斜度,而起模斜度则是为了便于起模,平行起模方向的模样表面上所增加的斜度;此铸件在起模时有不合理的地方。
《金属工艺学》课程教学大纲

《金属工艺学》课程教学大纲一、课程基本信息课程代码:050155课程名称:金属工艺学英文名称:Metal Technology课程类别:学科基础课学时: 40学分:2适用对象: 机械设计制造及其自动化专业考核方式:测试先修课程:《机械制图》,《工程材料》。
二、课程简介金属工艺学是机械类、材料类及其他近机类各专业学生必修的一门综合性的专业基础课,是研究工程材料加工方法的一门学科。
1.主要内容包括:铸造、塑性成型、焊接和金属切削加工四大部分的基础知识,涉及工程材料加工工艺的各个方面。
通过本课程的学习,可以后为续课程的学习及毕业后从事相关工作打下坚实的基础。
The metal technology is mostly all-around course of enginery profession, material profession et cetera near enginery profession. Its mostly content have casting, plasticity shaping, welding, metal cutting. Dealing with engineering materials processing technical. By learning the course, it can enhance student’s adaptability to the course on and after and mechanical skill work of finish school.三、课程性质和教学目的课程的性质:金属工艺学是一门研究金属加工方法的一门科学,是高等工科院校机械类各专业必修的技术基础课。
教学目的:学生通过本课程的学习,获得常用金属材料及其加工工艺方面的知识,为学习其他有关课程及以后从事机械和加工制造方面的工作奠定必要的基础。
通过教学使学生掌握下列知识:1、掌握各种主要加工方法的基本原理和工艺特点。
金属工艺学 下册(第六版) 邓文英 宋力宏 课后题答案
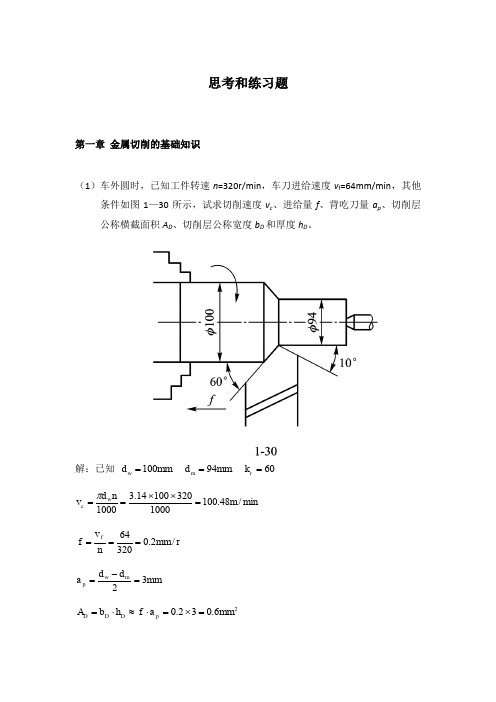
Fc1 Kc1 ap f 1118 4 0.3 1341.6N
Pm1 103 Fc1 vc 103 1341.6 100 60 2.236kw 查表 1-2 铝合金 LY12(淬火及时效,107HBS)kc2=834Mpa Fc2 Kc2 ap f 834 4 0.3 1000.8N
(6)柔性机械制造系统(FMS)的柔性指的是什么?为什么要求机械制造系统具 有一定的柔性? 解:FMS 中“柔性”主要是指制造系统对内部及外部环境的一种适应能力。 它主要表现为设备柔性、工艺柔性、工序柔性、路径柔性、产品柔性、批 量柔性、扩展柔性。 只有具有一定的柔性的机械制造系统才能扩大系统的适应范围,满足多品 种、变批量的生产。
液压传动系统中使用安全阀可以自动的防止过载,从而保护整个传动 系统。
(4)为什么说多品种、中小批生产将是机械制造业发展的趋势?应以何种途径 来解决这类生产自动化的问题? 解:在当今国际国内激烈竞争的市场上,产品日新月异,企业为了持久占 领市场,竞相推出一些生产周期短而生产数量少的产品,形成多品种中小 批量生产方式,这是当今制造业生产的主要特征。 解决多品种中小批量生产自动化的有效途径,采用数控机床,设计柔性
54
-Ⅴ(主轴)
1、 主轴Ⅴ转速级数:4×(1+2)=12 级 2、 主轴Ⅴ的最高转速和最低转速:
=1440× × × × ×1=200r/min
=1440× × × × × × =4.58r/min
金属工艺学

等四个部分按顺序组成。
例如:Q235-A· F即表示屈服点数值为235 MPa的A级沸腾钢。
b.优质碳素结构钢 使用时一般均需热处理以提高其力学性能,常用来制 造比较重要的零件。 优质碳素结构钢的牌号以两位数字表示,数字代表该钢平均含碳量的万分 数,例如钢号45,其平均含碳量为0.45%的优质碳素结构钢。 10~25号钢:含碳量低,强度低,塑性和韧性好,并且有良好的焊接性能, 常用作承载不大、韧性要求高的零件,还常做冲压件、焊接件。 30~55号钢:经热处理后具有较高的强度和韧性,广泛用来制造在机器结 构中受力的齿轮、轴、键、重要的螺钉等。 60号以上的钢:经热处理后具有高的强度、硬度和好的弹性,主要用来制
硬而脆
(三)机械混合物
由两种以上的相按一定比例混合而成。 例如:F和Fe3C以片层相间的形式混合,C=0.77%。 F Fe3C 这是钢中的一种重要组织,叫做珠光体(P)。 珠光体是两相组织。
造弹簧。
c.碳素工具钢 这类钢用来制造低速切削刀具、量具和冲压或冷拉模具。
因此,必须具有高的硬度和耐磨性,这只有在含碳量足够高的钢经淬火后 才能获得,故碳素工具钢都是高碳钢。
牌号:由汉语拼音字母“T”和数字组成,数字表
示平均含碳量的千分之几。
例如:T7表示平均含碳量为0.7%的碳素工具钢。 高级优质碳素工具钢在牌号后而再附以字母“A”,
b.按钢的质量分类
ws≤0.045% wP ≤0.045% 优质钢: ws≤0.035% wP ≤0.035% 特殊优质钢: ws≤0.020% wP ≤0.020%
普通钢: 结构钢: 工具钢: 沸腾钢: 镇静钢:
c.按钢的用途分类
d.按脱氧程度分类
半镇静钢: 特殊镇静钢:
《金属工艺学》上册 邓文英 郭小鹏版

7、缩孔、缩松的防止: (1)通过控制铸件的凝固方式使之符合“顺序凝固”或“同时凝固”原则; (2)合理确定浇注的引入位置和浇注工艺; (3)冒口、冷铁的综合应用,扩大有效补缩距离; (4)加压补缩; (5)悬浮浇注,细化结晶组织。 8、按照内应力的产生原因,可分为热应力和机械应力。 (1)热应力:它是由于铸件的壁厚不均匀、各部分的冷却速度不同,以致在同一时期内 铸件各部分收缩不一致而引起的。预防热应力的基本途径:尽量减少铸件各部分间的温 差,使其均匀冷却,为此,可将浇道开在薄壁处或者在壁厚出安放冷铁,即采用同时凝 固原则。 (2)机械应力:它是合金的固态收缩受到铸型或型芯的机械阻碍而形成的内应力。这种 应力在铸件落砂之后便可自行消除。 9、为防止铸件产生变形,在铸件设计时尽可能使铸件的壁厚均匀、形状对称;在铸 造工艺上采用同时凝固原则,以便冷却均匀;对于长而易变形的铸件,还可以采用“反变 形”工艺。 10、当铸造内应力超过金属的强度极限时,铸件便将产生裂纹。裂纹可分为热裂和冷裂。 (1)热裂:在高温下形成的裂纹。其形状特征是:缝隙宽、形状曲折、缝内呈氧化色。
奥氏体——碳溶入 - Fe 中所形成的固溶体,呈面心立方晶格,以符号 A 表示,铁碳合金中 奥氏体属于高温组织。
11、金属化合物——各组元按一定整数比例结合而成、并具有金属性质的均匀物质,属 于单相组织,例如:渗碳体( Fe3C ),硬度极高,塑性和韧性极低。
12、机械混合物——是由结晶过程所形成的两相混合组织。 珠光体——铁素体和渗碳体的混合,以 P 表示;珠光体在显微镜下呈层片状,白
《金属工艺学》上册 邓文英 郭小鹏版 期末复习资料汇总
金属工艺学第五版答案(3篇)

第1篇第一章绪论一、填空题1. 金属工艺学是研究金属材料的加工、成形和性能的科学。
2. 金属工艺学的研究对象包括金属材料的加工、成形和性能。
3. 金属工艺学的研究内容包括金属材料的制备、加工、成形和性能评价。
二、选择题1. 金属工艺学的研究对象是()。
A. 金属材料的制备B. 金属材料的加工C. 金属材料的成形D. 以上都是答案:D2. 金属工艺学的研究内容包括()。
A. 金属材料的制备B. 金属材料的加工C. 金属材料的成形D. 金属材料的性能评价答案:D三、简答题1. 简述金属工艺学的研究内容。
答:金属工艺学的研究内容包括金属材料的制备、加工、成形和性能评价。
具体如下:(1)金属材料的制备:研究金属材料的冶炼、铸造和粉末冶金等制备方法。
(2)金属材料的加工:研究金属材料的切割、变形、热处理等加工方法。
(3)金属材料的成形:研究金属材料的冲压、弯曲、拉伸等成形方法。
(4)金属材料的性能评价:研究金属材料的力学性能、物理性能、化学性能等。
2. 简述金属工艺学的研究意义。
答:金属工艺学的研究意义如下:(1)提高金属材料的加工效率和质量,降低生产成本。
(2)拓宽金属材料的加工领域,满足不同行业的需求。
(3)推动金属工艺技术的发展,提高金属材料的性能和寿命。
(4)促进金属加工行业的科技进步和产业升级。
第二章金属材料的制备一、填空题1. 金属材料的制备主要包括冶炼、铸造和粉末冶金等。
2. 冶炼是将金属从矿石中提取出来的过程。
3. 铸造是将金属熔化后浇注成一定形状的过程。
二、选择题1. 金属材料的制备方法中,属于热加工工艺的是()。
A. 冶炼B. 铸造C. 粉末冶金D. 以上都是答案:D2. 下列哪种金属材料的制备方法属于热加工工艺()。
A. 钢铁冶炼B. 铝合金铸造C. 钛合金粉末冶金D. 铜合金挤压答案:B三、简答题1. 简述冶炼的过程。
答:冶炼是将金属从矿石中提取出来的过程,主要包括以下几个步骤:(1)选矿:从矿石中分离出有价值的金属矿物。
(完整word版)金属工艺学(邓文英)经典知识点总结(word文档良心出品)

1. 熔模铸造的特点和适用范围: 1 铸件精度高,表面光洁。 2 可制造形状复杂的薄壁铸件 3 适用于各种合金铸件 4 生产批量无限制 5 工艺复杂,周期长,铸件成本高。
2. 金属型可分为整体式、垂直分型式、水平分型式和复合分型式。 3. 金属型铸造的特点和适用范围:
1 可一型多铸,生产率高 2 铸件的精度和表面质量高 3 力学性能得到显著提高 4 制造成本高、周期长,易出现浇不足、冷隔、裂纹等铸造缺陷 4. 压力铸造的特点和适用范围: 1 铸件的精度及表面质量较其它铸造方法均高 2 可压铸形状复杂的薄壁件 3 铸件的强度和硬度都较高 4 压铸的生产率较其它铸造方法均高。 5 便于采用镶铸。 6 但设备投资大,制造周期长,高熔点合金压型寿命低等
3.适用于有色金属零件的精加工 4.刀具简单 钻削的工艺特点:1.容易产生“引偏” 2.排屑困难 3.切削热不易传散 刨削的工艺特点:1.通用性好 2.生产率较低
拉削的工艺特点:1 生产率高 2 加工精度高、表面粗糙度值较小 3 拉床结构和操作比较简单 4 拉刀价格昂贵 5 加工范围较广
铣削的工艺特点:1.生产率较高 2.容易产生振动 3.刀齿散热条件较好
5. 浇注位置选择原则: 1 铸件的重要加工面应朝下。 2 铸件大的平面应朝下。 3 为防止铸件薄壁部分产生浇不足或冷隔缺陷,应将面积较大的薄壁部分置 于铸型的下部或使其处于垂直或倾斜位置。
4 铸件圆周表面要求质量高,应进行立铸。 6. 铸件分型面的选择原则:
1 应使造型工艺简化,分型面平直、数量少。 2 避免不必要的活块和型芯。 3 应尽量使铸件全部或大部分置于下箱。 7.选定分模面的原则: 1 应保证模锻件能从模膛中取出来。 2 应使上下两模沿分模面的模膛轮廓一致,以便在安装锻模和生产中容易发 现错模现象,及时而方便地调整锻模位置。
金属工艺学课程教学大纲
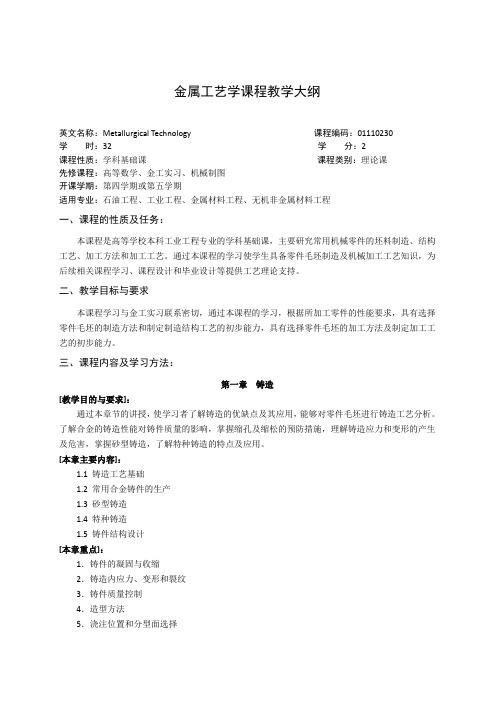
金属工艺学课程教学大纲英文名称:Metallurgical Technology 课程编码:01110230学时:32 学分:2课程性质:学科基础课课程类别:理论课先修课程:高等数学、金工实习、机械制图开课学期:第四学期或第五学期适用专业:石油工程、工业工程、金属材料工程、无机非金属材料工程一、课程的性质及任务:本课程是高等学校本科工业工程专业的学科基础课,主要研究常用机械零件的坯料制造、结构工艺、加工方法和加工工艺。
通过本课程的学习使学生具备零件毛坯制造及机械加工工艺知识,为后续相关课程学习、课程设计和毕业设计等提供工艺理论支持。
二、教学目标与要求本课程学习与金工实习联系密切,通过本课程的学习,根据所加工零件的性能要求,具有选择零件毛坯的制造方法和制定制造结构工艺的初步能力,具有选择零件毛坯的加工方法及制定加工工艺的初步能力。
三、课程内容及学习方法:第一章铸造[教学目的与要求]:通过本章节的讲授,使学习者了解铸造的优缺点及其应用,能够对零件毛坯进行铸造工艺分析。
了解合金的铸造性能对铸件质量的影响,掌握缩孔及缩松的预防措施,理解铸造应力和变形的产生及危害,掌握砂型铸造,了解特种铸造的特点及应用。
[本章主要内容]:1.1 铸造工艺基础1.2 常用合金铸件的生产1.3 砂型铸造1.4 特种铸造1.5 铸件结构设计[本章重点]:1.铸件的凝固与收缩2.铸造内应力、变形和裂纹3.铸件质量控制4.造型方法5.浇注位置和分型面选择6.铸件结构设计[本章难点]:1.铸件的凝固与收缩2.铸造内应力、变形和裂纹3.浇注位置和分型面选择第二章金属压力加工[教学目的与要求]:通过本章节的讲授,使学习者能够理解金属塑性变形的实质,理解金属塑性变形对金属组织和性能的影响,了解锻造方法特点及工艺,了解板料冲压的特点及应用。
[本章主要内容]:2.1 金属的塑性变形2.2 锻造2.3 板料冲压2.4 特种压力加工方法简介[本章重点]:1.塑性变形对金属组织和性能的影响2.自由锻和模锻3.锻造工艺规程制定4.锻件结构的工艺性5.板料冲压的分离工序6.板料冲压的变形工序[本章难点]:1.塑性变形对金属组织和性能的影响2.锻造工艺规程制定3.板料冲压分离和变形工序第三章焊接[教学目的与要求]:通过本章节的讲授,使学习者了解焊接的概念及电弧的结构,理解焊接接头的组织与性能,了解焊接应力与变形,了解电焊条的组成、作用、种类及选用原则,了解常用的焊接方法及特点。
金属工艺学---教学大纲
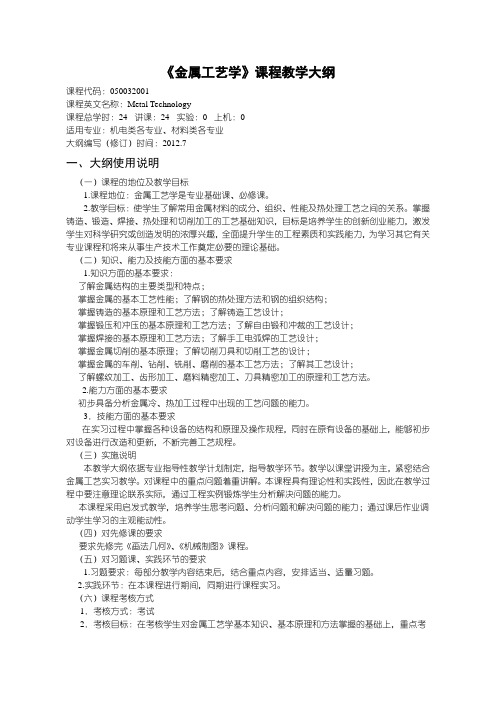
《金属工艺学》课程教学大纲课程代码:050032001课程英文名称:Metal Technology课程总学时:24 讲课:24 实验:0 上机:0适用专业:机电类各专业、材料类各专业大纲编写(修订)时间:2012.7一、大纲使用说明(一)课程的地位及教学目标1.课程地位:金属工艺学是专业基础课、必修课。
2.教学目标:使学生了解常用金属材料的成分、组织、性能及热处理工艺之间的关系。
掌握铸造、锻造、焊接、热处理和切削加工的工艺基础知识,目标是培养学生的创新创业能力,激发学生对科学研究或创造发明的浓厚兴趣,全面提升学生的工程素质和实践能力,为学习其它有关专业课程和将来从事生产技术工作奠定必要的理论基础。
(二)知识、能力及技能方面的基本要求1.知识方面的基本要求:了解金属结构的主要类型和特点;掌握金属的基本工艺性能;了解钢的热处理方法和钢的组织结构;掌握铸造的基本原理和工艺方法;了解铸造工艺设计;掌握锻压和冲压的基本原理和工艺方法;了解自由锻和冲裁的工艺设计;掌握焊接的基本原理和工艺方法;了解手工电弧焊的工艺设计;掌握金属切削的基本原理;了解切削刀具和切削工艺的设计;掌握金属的车削、钻削、铣削、磨削的基本工艺方法;了解其工艺设计;了解螺纹加工、齿形加工、磨料精密加工、刀具精密加工的原理和工艺方法。
2.能力方面的基本要求初步具备分析金属冷、热加工过程中出现的工艺问题的能力。
3.技能方面的基本要求在实习过程中掌握各种设备的结构和原理及操作规程,同时在原有设备的基础上,能够初步对设备进行改造和更新,不断完善工艺规程。
(三)实施说明本教学大纲依据专业指导性教学计划制定,指导教学环节。
教学以课堂讲授为主,紧密结合金属工艺实习教学。
对课程中的重点问题着重讲解。
本课程具有理论性和实践性,因此在教学过程中要注意理论联系实际,通过工程实例锻炼学生分析解决问题的能力。
本课程采用启发式教学,培养学生思考问题、分析问题和解决问题的能力;通过课后作业调动学生学习的主观能动性。
金属工艺学课后习题答案

精心整理
金属工艺学课后习题答案
主编:邓文英郭晓鹏
P.141
(1)何为生产过程、工艺过程、工序?
答:生产过程:由原材料制成各种零件并装配成机器的全过程,包括原材料的运输 保管、生产准备、制造毛坯、切削加工、装配、检验及试车、油漆
和包装等;
工艺过程:在生产过程中,直接改变原材料(或毛坯)的形状、尺寸或性能, 使之变成成品的过程,又包括若干道工序。
程。
(8(9(6).a (3(2(3(4)粗车另一端外圆至φ18*64
(5)半精车该外圆至φ16*65
(6)精车该外圆至φ16*65
铣立式铣床粗-精铣方头
热淬火后低温回火35HRC
钳修研中心孔。
金属工艺学+邓文英主编

金属工艺学教案机械系.机械教研室授课时间:班级:本课课题:绪论教学目的和要求:1.了解本课程的性质、任务和在生产中的地位。
2.了解本课程内容和机械产品制造全过程的概念。
3.熟悉学习本课程的基本要求和方法。
重点与难点:了解本课程的性质及意义。
教学方法:讲授法和录像观摩。
课型:理论课金属工艺学(邓文英主编)教学过程绪论一、为什么要学金属工艺学(机械工程材料工艺学)?金属工艺学是一门传授有关制造金属零件工艺方法的综合性技术基础课。
它主要传授各种工艺方法本身的规律性及其在机械制造中的应用和相互关系;金属零件的加工工艺过程和结构工艺性;常用金属材料性能对加工工艺的影响;工艺方法的综合比较等。
研究的对象:常用的工程材料、材料的各种加工处理工艺。
例如:钢铁、铝合金、铜合金、塑料等材料及热处理工艺、焊接工艺、铸造工艺、切削加工工艺等加工处理工艺。
举例:常用主轴材料:45。
技术要求:调质处理。
箱体材料:HT200。
技术要求:退火。
国家工业发展的三大支柱:材料、信息、微机。
1.工程材料是国家工业发展的物质基础。
工业和日常生活都离不开工程材料的使用,研究材料最终是为人类的文明进步而服务。
2.作为工科类专业所必须掌握的一门功课。
基础课→(桥梁)→专业课机械工程材料工艺学是一门技术基础课,对专业课和基础课起着桥梁的作用。
二、机械工程材料工艺学课程有什么特点?1.本课程同实践紧密相联系,是一门实践性很强的学科。
2.通过生产实践才能融会贯通地学习掌握(安排了钳工、金工实习)。
3.为了弥补实践方面的不足,采用录像教学以及到工厂参观和实习,通过师生的相互努力来学好这门功课。
三、怎样才能学好机械工程材料工艺学?1.注意各章节的联系、学习、复习、巩固、应用、总结。
2.要理解、要提问题、不能累计问题。
3.抓住主要内容:金属材料及热处理基本知识,铸造、锻造、焊接、切削加工基本常识。
随着科学技术和生产力的不断发展,金属工艺学的内容构成也有所发展。
金属工艺学 邓文英(全套课件上)
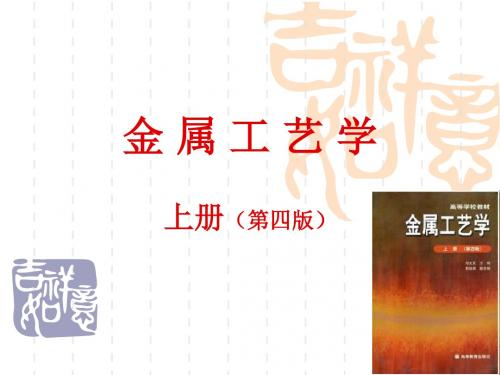
洛氏硬度试验原理图
布氏硬度与洛氏硬度的特点比较
布氏硬度的特点: 布氏硬度因压痕面积较大,HB值的 代表性较全面,而且实验数据的重复性 也好,但由于淬火钢球本身的变形问题, 不能试验太硬的材料,一般在HB450以 上的就不能使用。 由于压痕较大,成品检验也有困难。 通常用于测定铸铁、有色金属、低合 金结构钢等材料的硬度。
1. 高纯材料—优异的软磁性、良好的耐腐蚀性、高残余电阻率,用
于高真空容器、核反应堆等。
2. 高强度材料—可减轻重量,用于航空航天、深海潜艇、原子能
等领域。
3. 超易切削钢—提高刀具寿命30倍,降低成本、节约能源。
4. 硬质合金与金属陶瓷—高硬度、高耐磨性、耐高温、抗氧化,
用于刀具、磨具、轧辊、轴承等领域。
三、金属的工艺性能
工艺性能是物理、化学、力学性能的综合。按 工艺方法的不同,可分为铸造性能、可锻性、焊接 性和切削加工性等 1 金属在铸造成形过程中获得外形准确、内部健 全铸件的能力称为铸造性能。铸造性能包括流动性、 吸气性、收缩性和偏析等。在金属材料中灰铸铁和 青铜的铸造性能较好。 2、 金属材料利用锻压加工方法成形的难易程度称 为锻造性能。锻造性能的好坏主要同金属的塑性和 变形抗力有关。塑性越好,变形抗力越小,金属的 锻造性能越好。
计机械和选择、评定金属材料时有重要意 义 。 机械零件多以σs作为强度设计的依据。 对于脆性材料,在强度计算时,则以σb为 依据。
塑性指标
(1)伸长率δ
δ= (L1-L0)/L0 ×100%
式中: L0—试样原标距的长度(mm)
L1—试样拉断后的标距长度(mm)
(2) 断面收缩率φ 断面收缩率是指试样拉断后断面处横截面积 的相对收缩值。 φ= (A0-A1)/A0 ×100% 式中:A0—试样的原始截面积(mm2) A1—试样断面处的最小截面积(mm2) δ和φ愈大,则塑性愈好。良好的塑性是金 属材料进行塑性加工的必要条件。
金属工艺学教学设计
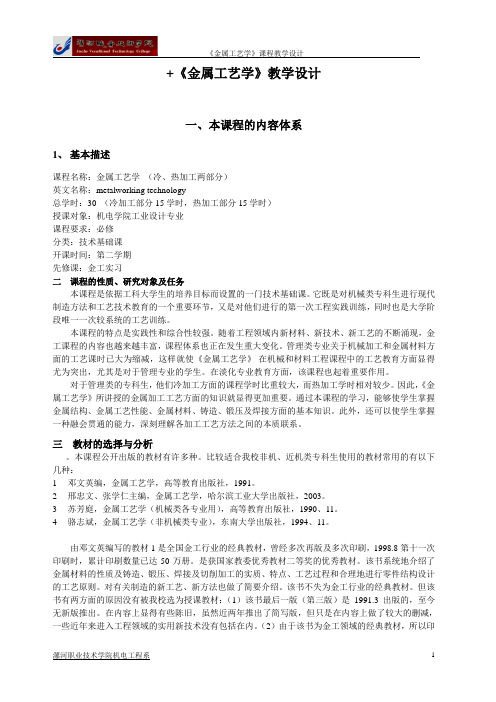
+《金属工艺学》教学设计一、本课程的内容体系1、基本描述课程名称:金属工艺学(冷、热加工两部分)英文名称:metalworking technology总学时:30 (冷加工部分15学时,热加工部分15学时)授课对象:机电学院工业设计专业课程要求:必修分类:技术基础课开课时间:第二学期先修课:金工实习二课程的性质、研究对象及任务本课程是依据工科大学生的培养目标而设置的一门技术基础课。
它既是对机械类专科生进行现代制造方法和工艺技术教育的一个重要环节,又是对他们进行的第一次工程实践训练,同时也是大学阶段唯一一次较系统的工艺训练。
本课程的特点是实践性和综合性较强。
随着工程领域内新材料、新技术、新工艺的不断涌现,金工课程的内容也越来越丰富,课程体系也正在发生重大变化。
管理类专业关于机械加工和金属材料方面的工艺课时已大为缩减,这样就使《金属工艺学》在机械和材料工程课程中的工艺教育方面显得尤为突出,尤其是对于管理专业的学生。
在淡化专业教育方面,该课程也起着重要作用。
对于管理类的专科生,他们冷加工方面的课程学时比重较大,而热加工学时相对较少。
因此,《金属工艺学》所讲授的金属加工工艺方面的知识就显得更加重要。
通过本课程的学习,能够使学生掌握金属结构、金属工艺性能、金属材料、铸造、锻压及焊接方面的基本知识。
此外,还可以使学生掌握一种融会贯通的能力,深刻理解各加工工艺方法之间的本质联系。
三教材的选择与分析。
本课程公开出版的教材有许多种。
比较适合我校非机、近机类专科生使用的教材常用的有以下几种:1邓文英编,金属工艺学,高等教育出版社,1991。
2邢忠文、张学仁主编,金属工艺学,哈尔滨工业大学出版社,2003。
3苏芳庭,金属工艺学(机械类各专业用),高等教育出版社,1990、11。
4骆志斌,金属工艺学(非机械类专业),东南大学出版社,1994、11。
由邓文英编写的教材1是全国金工行业的经典教材,曾经多次再版及多次印刷,1998.8第十一次印刷时,累计印刷数量已达50万册。
- 1、下载文档前请自行甄别文档内容的完整性,平台不提供额外的编辑、内容补充、找答案等附加服务。
- 2、"仅部分预览"的文档,不可在线预览部分如存在完整性等问题,可反馈申请退款(可完整预览的文档不适用该条件!)。
- 3、如文档侵犯您的权益,请联系客服反馈,我们会尽快为您处理(人工客服工作时间:9:00-18:30)。
(2)划线工序的安排 形状较复杂的铸件、锻件和焊接件等,在单件
小批生产中,为了给安装和加工提供依据,一般在 切削加工之前安排划线工序。
有时为了加工的需要,在切削加工工序之间, 可能还要进行第二次或多次划线。
为了保证精基准的精度,在加工底面和导向面时,以加工 后的顶面为辅助精基准。并且在粗加工和时效之后,又以精加 工后的顶面为精基准,对底面和导向面进行精刨和精细加工( 刮研),进一步提高精加工阶段定位基准的精度,利于保证加 工精度。
4. 工艺过程
表 6-6 续
表 6-6 续
四、成形零件数控加工工艺
表6-4 单件小批生产轴的工艺过程
工 序 号
工序 名称
工序内容
加工简图
Ⅰ
车
倒头车两端面, 钻中心孔
设备 卧式车床
1.粗车、半精车右端φ40、
φ25外圆、槽和倒角,留
Ⅱ
车
磨削余量1mm; 2. .粗车、半精车左端
φ30、φ25外圆、槽和倒
角,留磨削余量1mm
卧式车床
Ⅲ
铣
粗、精铣键 槽
Ⅳ
热处 理
调质 40~45HRC
在机械加工中,要完全确定工件的
正确位置,必须有六个相应的支承点,
来限定工件的六个自由度,称为工件
的“六点定位原理”。
在Oxy平面上,限制
三个
自由度;在Oxz平面上,限制
两个自由度;在Oyz平面上,限制
一个自由度。
超定位或过定位 前后顶尖已限了制了 五个自由度,而三
爪卡盘又限制了 两个 自由度,在 两个自由 度上,定位点多于一个。
现以下图所示轴类零件的数控加工为例,说明轴 类零件数控车削加工的工艺过程。
图 6-21 轴
材料为铝合金6061
1.零件图工艺分析 (1)该零件表面需加工螺纹、圆锥、圆柱、凹 凸圆弧、槽及倒角; (2)零件图尺寸标注完整,轮廓描述清楚; (3)零件材料为铝合金6061,无热处理要求, 毛坯为φ 55mm长117mm的圆棒料。
(3)其余要求不高的螺纹孔、紧固孔及油孔等,可放 在最后加工。 (4)整个加工过程分为粗加工和精加工两个阶段。 (5)整个工艺过程中都应遵循“先面后孔”的原则, 各纵向主要孔的加工应在一次安装中完成,并可采用 镗模夹具。
3. 基准的选择
(1)粗基准的选择 为了保证主轴轴承孔的加工余量分布均匀,并保证装
Ⅴ 钳 修研中心孔
表 6-4 续
立式 铣床
1.粗磨、精
磨右端φ40、
φ25外圆至
Ⅵ
磨
要求尺寸; 2.粗磨、精
磨左端φ30、
φ25外圆至
要求尺寸。
Ⅶ
检
按图纸要求 检验
表 6-4 续
外圆 磨床
二、套类零件
1. 零件的主要技术要求
2. 工艺分析
精度相当于IT7,采用粗车——精车的工艺。
小端外圆面φ45对孔φ52轴
图6-17 传动轴
2. 工艺分析 精度 相当于IT7; 采用如下的加工方案: 粗车—半精车—热处理—粗磨—精磨; 轴上的键槽,可以用键槽铣刀在立式铣床上铣出。
3. 基准选择 用轴两端的中心孔作为粗、精加工的定位基准。
这样,既符合基准同一和基准重合的原则,也有利于 生产率的提高。为了保证定位基准的精度和表面粗糙 度,热处理后应修研中心孔。
然后,以粗车后的小端外圆面和台阶端面C为定位基准 (精基准),在一次安装中加工大端各表面,以保证所要求 的位置精度。
精车小端时,则利用可胀心轴,以孔φ52和大端端面D
为定位基准。
4. 工艺过程
表 6-5 续
三、箱体类零件
1. 床头箱箱体的结构特点和主要技术要求
床头箱箱体的结构特点是壁薄、中空、形状复杂。加工面 多为平面和孔,它们的尺寸精度、位置精度要求较高,表面粗 糙度值较小。主要技术要求 有以下几个方面: (1)作为装配基准的底面和导向面的平面度、表面粗糙度; (2)主轴轴承孔及其余轴承孔的尺寸精度、表面粗糙度; (3)轴承孔轴线间距离的尺寸精度; (4)不同箱壁上孔的同轴度; (5)工件材料HT200 。
第六章 工艺过程的基本知识
第一节 基本概念
一、生产过程和工艺过程
1. 生产过程 由原料制成各种零件并装配成机器的全过程。 2. 工艺过程 生产过程中,直接改变原材料(或毛坯)的
形状、尺寸或性能,使之变为成品的过程。 3. 工序 在一个工作地点对一个或一组工件所连续完成的
那部分工艺过程。
图6-1所示半联轴器的工艺过程,可以分为如 下三道工序: 工序Ⅰ:在车床上车外
入箱体中的齿轮、轴等零件,与不加工的箱体内壁间有足 够的间隙,以免相互干涉,常常首先以主轴轴承孔和与之 相距最远的一个孔为基准,兼顾底面和顶面的余量,对毛 坯进行划线和检查。之后,按划线找正粗加工顶面。这种 方法,实际上就是以主轴轴承孔和与之相距最远的一个孔 为粗基准。
(2)精基准的选择
以该箱体的装配基准——底面和导向面为统一的精基准, 加工各纵向孔、侧面和端面。
2 . 工艺分析
工件毛坯为铸件,应经过清理和退火处理,粗加工后应 进行适当的时效处理。
主要工艺过程可作如下考虑: (1)底面、顶面、侧面和端面可采用粗刨—精刨工艺。 (2)直径小于40~50mm的孔可采用钻—扩(或半精镗)— 铰(或精镗)的工艺。已铸出的孔,可采用粗镗—半精镗— 精镗(用浮动镗刀片)的工艺。
线的同轴度,台阶端面C
对孔φ52轴线的垂直度,
可以在精车小端时,以孔
φ52和与孔在一次安装中车
出大端端面D定位来保证。 这就要用定位精度较高的
可胀心轴(图6-19)定位。
3.基准选择
为了给粗车—精车大端时提供一个精基准,先以工件 毛坯大端外圆面作粗基准,粗车小端外圆面和端面。这样也 保证了加工大端时余量均匀一致。
作,妨碍机器的正常运行。
五、工艺文件的编制
工艺过程拟定之后,要以图表或文字的形式 写成工艺文件。
工艺文件通常有如下几种: 1. 机械加工工艺过程卡片 用于单件小批生 产,格式如表6-3所示,主要作用是概略地说明机 械加工的工艺路线。
2. 机械加工工序卡片 大批大量生产中,要求工艺文件更加完整和详 细,每个零件的各个加工工序都要有工序卡片。它 是针对某一工序编制的,要画出该工序的工序图, 以表示本工序完成后工件的形状、尺寸及其技术要 求,还要表示出工件的装夹方式、刀具的形状及其 位置等。
对毛坯开始进行机械加工时, 第一道工序只能以毛坯表面定位。 这种基准面称为粗基准(或毛基准)。
粗基准选择的具体原则如下: 1)选取不加工的表面作为粗基准;
2)选取要求加工余量均匀的表面 作为粗基准;
3)对于所有表面都要加工的零件, 应选择余量和公差最小的表面 作为粗基准;
4)选取光洁、平整、面积足够大、 装夹稳定的表面;
2. 夹具的主要组成部分
图6-3所示的在轴上钻孔所用的一 种简单的专用夹具,可以概括为如下 几个部分: (1)定位元件
图 6-4 平面定位用的定位原件
图 6-3 在轴上钻孔的 夹具
(2)夹紧机构
(3)导向元件 用来对刀和引导刀具进入正确加工位置 的零件
(4)夹具体和其他部分
第三节 工艺规程的拟定
(3)热处理工序的安排 1)预备热处理 是指为了改善金属的组织和切削
加工性而进行的热处理。如退火、正火等,一般安 排在加工之前。
调质也可以作为预备热处理,但若以提高材料 的力学性能为主要目的,则应放在粗加工之后、精 加工之前进行。
2)时效处理 是为了消除残余内应力对加工精度的 影响,大而结构复杂的铸件,或者精度要求很高的 非铸件类工件,需在粗加工前后各安排一次人工时 效。 3)最终热处理 是指为提高零件表层硬度和强度而 进行的热处理,如淬火、氮化等,一般安排在工艺 过程的后期。
(4)检验工序的安排 除加工过程中操作者的自检外,在下列情况下还
应安排检验工序: 1)粗加工阶段之后; 2)关键工序前后; 3)特种检验(如磁力探伤、密封性试验、动平衡试
验)之前; 4)从一个车间转到另一个车间加工之前; 5)全部加工结束之后。
(5)其他辅助工序的安排 例如: 1)零件的表面处理; 2)去毛刺、倒棱边、去磁、清洗等。 这些辅助工序不能忽略,否则会影响装配工
2. 工件的基准 在设计和制造零件的过程中,要确定一些点、线或面
的位置作为依据,这些点、线或面称为基准。 按照作用的不同,基准分为
1)设计基准 2)工艺基准 工艺基准又分为
1)定位基准 2) 度量基准 3)装配基准
3. 定位基准的选择 选择定位基准的总原则,应该是从有位置精度要求的表
面中进行选择。 (1)粗基准的选择
圆,车端面,镗孔 和内孔倒角; 工序Ⅱ:在钻床上钻6个 φ 20的小孔; 工序Ⅲ:在插床上插键 槽。
在同一道工序中,工件可能要经过几次安装。如 在工序Ⅰ中可能要安装两次:
第一次安装:用三爪卡盘夹住φ 102外圆,车端 面B,镗内孔φ 60,内孔倒角,车φ 223外圆;
第二次安装:调头用三爪卡盘夹住φ 223外圆, 车端面A,内孔倒角。
5)粗基准只能在第一道工序中使 用一次,不能重复使用。
(2)精基准的选择
在第一道工序之后,应当以加工过的表面作为定位基准, 这种定位基准称为精基准。
精基准选择原则如下: 1)基准重合原则 就是尽可能选用设计基准作为定位基准。
2)基准同一原则 位置精度要求较高的某些表面加工时,尽可能选
用同一的定位基准; 3)选择精度较高、安装稳定可靠的表面作为精基准
三、定位基准的选择
任何一个没有约束的物 体,在空间都有六个自由度, 即沿三个相互垂直坐标轴的移 动(用 表示)和绕这三个 坐标轴的转动(用 表示) 1. 工件的六点定位原理