05 材料的断裂
第05章 金属的疲劳1

(1)基本特征: 呈现贝壳花样或海滩花样,它是以疲
劳源区为中心,与裂纹扩展方向相垂直的 呈半圆形或扇形的弧形线,又称疲劳弧线。
疲劳弧线是裂纹扩展过程中,其顶端 的应力大小或状态发生变化时,在断裂面 上留下的塑性变形的痕迹。
47
(2)贝纹花样的形成: 是由载荷变动引起的,因为机器运转时
不可避免地常有启动、停歇、偶然过载等, 均可留下塑性变形的痕迹——贝纹线(疲 劳弧线)。
r=-1称为对称循环应力;
r=0(或r=-∽)这种非对称循环又称为 脉动循环。这种载荷是一种最危险的载荷。
r偏离-1越远,应力对称性越差,疲劳 极限越高。
29
(2)循环应力的种类
(交变当)r应=-力1,;即σmin=-σmax时,称为对称循环
当r=0,即σmin=0时,称为脉动循环应力。
2
1、金属疲劳破坏的形成过程 在正常使用机械时,重复的推、拉、扭
或其他的外力情况都会造成机械部件中金 属的疲劳。
这是因为机械受压时,金属中原子的排 列会大大改变,从而使金属原子间的化学 键断裂,导致金属裂开。
3
构件承受交变应力的大小超过一定限 度,并经历了多次的循环重复后,在构件 内部应力最大处或材质薄弱处将产生细微 裂纹(称为疲劳源),这种裂纹随着应力 交变次数增加而不断向四周扩展。
53
(5)不同情况下贝纹线的形状
① 当轴类机件拉压疲劳时, 轴向应力包括拉-拉或拉-压疲劳。它的疲劳
源一般也在表面形成,只有内部有缺陷时才在缺 陷处形成。
54
若表面无应力集中(无缺口),则裂纹因截 面上应力均等而沿截面等速扩展,贝纹线呈一簇 平行的圆弧线;
55
若机件表面存在应力集中(环形缺口), 则因截面表层的应力比中间的高,裂纹沿表层 的扩展快于中间区;高应力时,瞬断区面积相 对较大,疲劳裂纹扩展区面积小,裂纹沿两边 及中间扩展差别不大。
ansys 5A05材料力学性能设置
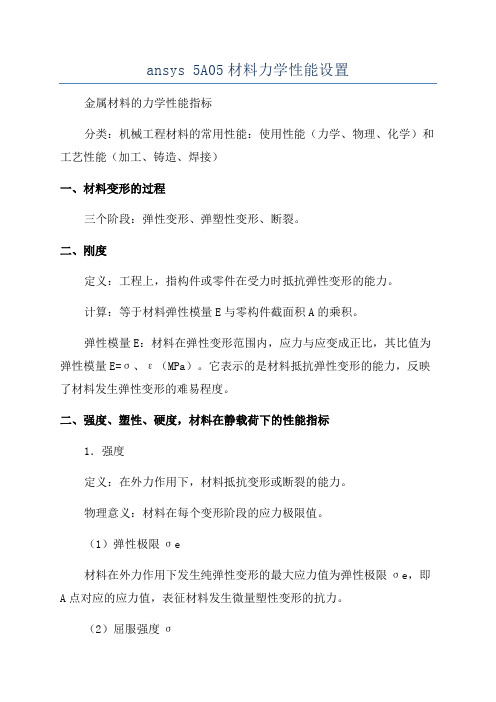
ansys 5A05材料力学性能设置金属材料的力学性能指标分类:机械工程材料的常用性能:使用性能(力学、物理、化学)和工艺性能(加工、铸造、焊接)一、材料变形的过程三个阶段:弹性变形、弹塑性变形、断裂。
二、刚度定义:工程上,指构件或零件在受力时抵抗弹性变形的能力。
计算:等于材料弹性模量E与零构件截面积A的乘积。
弹性模量E:材料在弹性变形范围内,应力与应变成正比,其比值为弹性模量E=σ、ε(MPa)。
它表示的是材料抵抗弹性变形的能力,反映了材料发生弹性变形的难易程度。
二、强度、塑性、硬度,材料在静载荷下的性能指标1.强度定义:在外力作用下,材料抵抗变形或断裂的能力。
物理意义:材料在每个变形阶段的应力极限值。
(1)弹性极限σe材料在外力作用下发生纯弹性变形的最大应力值为弹性极限σe,即A点对应的应力值,表征材料发生微量塑性变形的抗力。
(2)屈服强度σ试样发生屈服现象时的应力值,屈服点S的应力值称为屈服强度σS,表征材料开始发生明显的塑性变形。
没有明显的屈服现象发生的材料,用试样标距长度产生0。
2%塑性变形时的应力值作为该材料的屈服强度,用σ0。
2表示,称为条件屈服强度。
意义同σS。
(3)抗拉强度σb材料在拉伸载荷作用下所能承受的最大应力值σb称为抗拉强度或强度极限,表征材料的断裂抗力。
强度是零件设计和选材的主要依据。
2.塑性定义:材料在外力作用下,产生塑性变形而不破断的能力称为塑性。
指标:工程上常用延伸率δ和断面收缩率ψ作为材料的塑性指标。
材料的δ和ψ值越大,塑性越好。
3.硬度定义:指材料表面抵抗局部塑性变形的能力,是表征材料软硬程度的一种性能。
通常材料的强度越高,硬度也越高,耐磨性也越好。
硬度指标:与试验方法有关。
生产上,常用静载压入法,常用方法有:布氏硬度、洛氏硬度和维氏硬度。
布氏硬度HBS:淬火钢球压头,压痕大,不能测太硬度的材料,适用于测量退火和正火钢、铸铁、有色金属等材料的硬度。
洛氏硬度HRC:锥角为120°的金刚石圆锥体压头,适用于调质钢、淬火钢、渗碳钢等硬度的测量。
最新05 材料的断裂韧性

设钢材的几何形状因子Y=1.5,最大裂纹尺寸 C=2mm,问:选择哪种材料较合适?
思考题:
5.3 裂纹尖端塑性区的大小及修正
➢ 由弹性应力场公式:
y
KI 2 r
➢ r 0时,σy ∞,但对韧性材料,当σ>σs时,发生塑性变 形,其结果是材料在裂纹扩展前,其尖端附近出现塑性变形 区 适,用塑。性区内应力应变关系不是线性关系,上述KI判据不再
Ⅰ型中心贯穿裂纹
KI Y
a (KI量纲:MPa·m1/2
或 MN·m-3/2 )
➢ a—裂纹半长;σ-外应力; ➢ Y-形状系数,与裂纹形状、试样尺寸和加载方式有关,
为无量纲量,一般Y=1~2
➢KⅠ综合反映了试样尺寸、外加应力和裂纹长度对裂纹尖 端应力场强度的影响,可以看作是推动裂纹扩展的动力。
y
(
x
2
y
)2
2 xy
2
x
2
y
(
x
2
y
)2
2 xy
3 0(平 面 应 力 )
3 ( 1 2() 平 面 应 变 )
x
y
xy
K I co s (1 sin sin 3 )
2 r 2
2
2
K I co s (1 sin sin 3 )
2 r 2
22
K I sin co s co s 3
➢形状系数 Y的计算很复杂,实际应用中,可根据裂纹形 状、试样尺寸和加载方式查手册。
中心穿透I 型裂纹
应力强度因子KI和断裂韧性
➢KI是描述裂纹尖端应力场强度的一个力学参量;
➢ 当σ和a单独或共同增大时,KI和裂纹尖端的各应力 分量等随之增大;
材料力学中的断裂力学

材料力学中的断裂力学材料力学是研究物质在外力作用下变形、损伤和破坏行为的一门学科。
断裂力学是材料力学中的一个重要分支,研究的是材料在受到外力作用时出现破坏的现象及其规律。
断裂力学对于理解和预测材料破坏行为,具有重要的理论和实践意义,本文将就此展开讨论。
一、破坏的基本形式材料的破坏可分为两种基本形式:拉伸断裂和压缩断裂。
拉伸断裂是指在材料受到拉伸作用时,断口发生的破坏行为;压缩断裂是指在材料受到压缩作用时,断口发生的破坏行为。
除此之外,还有剪切断裂、扭转断裂、弯曲断裂等不同的破坏形式。
二、断裂力学的基本概念1.断裂应力材料在破坏前,能够承受的最大应力称为断裂应力。
断裂应力的大小与材料的强度、形状、尺寸、载荷方向等因素有关。
2.断裂韧性材料在破坏前能够吸收的最大能量称为断裂韧性。
断裂韧性的大小与材料的抗裂性能有关。
3.断裂强度材料在破坏前实际承受的最大应力称为断裂强度。
断裂强度与断裂应力的概念相似,但断裂强度是在材料实际破坏后测定得出的。
4.断裂韧度材料在破坏前能够吸收的最大能量密度称为断裂韧度。
断裂韧度与断裂韧性的概念类似。
三、断裂表征参数1.伸长率材料在破坏前拉伸变形的程度,也称为材料的变形量。
伸长率是指材料在拉伸断裂前的额定延长量比上原长度所得的比值。
2.缩颈率在材料拉伸断裂时,当材料的横截面积开始缩小,称为缩颈。
缩颈率是指材料在拉断时的截面积缩小量比上原截面积所得的比值。
3.断口形貌材料断口的形态与破坏机理有密切关系,通过观察断口形貌,可以较为直观地判断破坏机制。
四、断裂损伤机理材料的断裂破坏是一个复杂和多层次的过程,其损伤机理可以分为微观和宏观两个层次。
1.微观层次在微观层次上,材料的破坏主要是由裂纹的扩展和材料局部的塑性变形共同作用导致的。
材料的破坏前,裂纹的长度会随着载荷的增加而逐渐增加,当裂纹的长度达到一定程度时,就会出现快速扩展和破坏。
2.宏观层次在宏观层次上,材料的破坏主要是由断面剪切和拉伸引起的。
构造地质学05第五章岩石力学性质

τmax= τ0 …(1)
τ0为抗剪强度极限
理论上,破裂面应沿最大剪应力面产生,形成棋 盘格式构造。剪裂角< 450?
库伦解释是岩石抗剪强度与剪应力和正应力有 关,因此将(1)式改为:
De/dt 常量
撤出应力
t0 t1 t2
t3
时间
永久应变
t4 t5
松弛——保持应变不变,应力随时间而减小。 (相当于降低了岩石的弹性极限) (1)、应力随时间减小,松弛速度急剧下降。 (2)、应力经很长时间后可趋于一极限值
实践证明:在地质上岩石能否在很长时间的极 小差异应力下不断变形,需要一定的温度和压 力条件,因为它一般发生在地壳深层或它具备 有利于蠕变之条件的地方,如某些强变形带中。
剪切 脆性
挠曲
压扁
流动 温度
韧性
熔融 围 压
岩石随P-T条件的变化而呈现 变形习性及相应的主要变形机制
显理 示想 了的 各地 构壳 造一 层段 次剖 构面 造, 样剖 式面
三.岩石变形的时间因素
在地质条件下,岩石变形是长期的,通常要 以百万年为单位,因此评价时间因素对岩石变 形的效应具有关键意义。
σy=0
完全塑性材料。没
有载荷,变形继续
增大。
如果超过屈服点,继 续塑性变形,需施加 更大的应力超过屈服 应力,这个过程称应 变硬化或加工硬化。 经过一段应变硬化的 塑性变形后卸载,应 力-应变曲线回到e2 表明总的永久变形。
应变硬化
σy>0 σy=0
如果将同样应力继续 加上去,应力-应变 曲线则沿以前路径回 到塑性变形P位置上 ,好像增大了弹性范 围和增高了屈服应力 (σy/)。因此应变 硬化可以看作屈服强 度随递进变形而连续 升高。
第05讲:线弹性断裂力学的塑性修正

作业
1. 小范围屈服条件下为什么要进行应力强度因 子的塑性修正,如何修正?
2. 试样的厚度与应力状态和塑性区尺寸有何关 系,它是如何影响断裂韧性的? 3. 写出R阻力曲线上裂纹失稳扩展的条件?
本讲内容
1
塑性区模型
平面应力状态与平面应变状态
厚度效应 平面应力断裂和R曲线
(未考虑产生塑性区应力后的应力平衡)
Irwin塑性区模型
② 第二次近似值 考虑到塑性区内应力平衡则有 R rp*
* R r dr ys p ys y 0
* r p
将 y
KI 2r
* p
代入上式得到
2 2
R ys 2 r F a ys
塑性区方程:
2 K 3 2 I r ( θ ) 1 sin cos 平面应力 p 2 4 2 ys 2 K 3 2 2 I r ( θ ) sin ( 1 2 ) ( 1 cos ) 平面应变 p 2 4 2 ys
2
3 4
裂纹尖端塑性区
原因:塑性区影响材料的断裂模式和材料对裂纹扩 展的抗力。 目的:确定塑性区的形状和大小,从而在小范围屈服 的前提下对应力强度因子进行修正,以便更加 准确的描述裂尖的状态。
方法:采用简化模型估算
Irwin塑性区模型
第一次近似
第二次近似
Irwin塑性区模型
①第一近似值 r p* 裂纹尖端应力场
Irwin提出,将裂纹长度增加一微量Δa,其效果与裂 纹尖端的塑性区的效果相似。 将裂纹长度由 a 增加到 a rp
K F ( a r) I
(整理)硅片隐裂痕的粗浅分析--choo-05-07.

硅片隐裂痕的粗浅分析---Choo 2008-05-07 由共价键结合而成的硅是典型的脆性材料,其主解理面为{111}面,而S125和S156硅片大多为{100}晶面族,如果硅片在工艺过程中积累了过多的解理裂痕,则裂痕会产生扩展并脆断,所以就有很多沿解理面或非解理面的穿晶断裂出现。
经观察与粗略统计,大多数硅片的断裂部位位于对角线约1/8处(如图1.图2.),所以不妨以1/8处碎片作为研究对象,而对那些潜在于工艺环节中的,可造成隐裂痕的,设备操作或人工操作方法进行分析。
以下从公司现有设备角度和生产工具的使用角度着手,统计了整个电池片生产过程中几乎所有可造成隐裂痕的工艺环节。
图1. 皇明碎片1 图2.皇明碎片2一.从生产工具角度分析作为典型的脆性材料,常温下,单晶硅的裂纹一旦形成,便会以极快的速度扩展,而厚度只有200微米左右的单晶硅片,其解理胚形成后,稍有应力集中裂痕便会扩展为裂纹从而发生断裂,所以在这次分析过程中,凡是遇到与硅片接触或对硅片产生力的作用的环节都将被视为隐患。
,可能造成隐裂痕的工具为:1. 晶片盒:晶片盒是与硅片接触最为频繁的工具,其与硅片下方的接触处虽然为点接触,但是由于放硅片时,过早的松开镊子或松手会导致的硅片自由落体式的坠落,这是使位于硅片外边缘隐裂痕的扩大方法之一,同时也可能造成崩边现象。
如图1.1、图1.2.,(红色圆圈处,硅片边角已经断裂;黄色圆圈处,硅片与晶片盒正常接触)图1.1 硅片与晶片盒接触图图1.2 硅片与晶片盒接触图局部放大2. 镊子:镊子本身结构无可厚非,但是线上使用镊子夹硅片的方法大多是:用镊子夹住硅片的一角,这样硅片的重量力矩完全集中在镊子与硅片相接触的一点或一条线,所以视为隐患。
如图1.3图1.3 扩散上片时,镊子的使用方法3. 吸笔:造成隐裂痕的道理与镊子类似,也是习惯性的用吸笔吸住硅片的一角,图1.4图1.4 去PSG段吸笔的使用方法4. 石英舟:方形石英舟,造成隐裂痕的道理与晶片盒类似,但是石英舟的硬度更高,如果,插片时过早的松手,硅片坠落后会与石英舟产生互残式的磕碰,不但能产生碎片或隐裂痕,而且会出现崩边;菱形石英舟,其结构决定了硅片只能以相邻两边的四个点作为支撑,所以个人感觉当硅片在菱形舟上时,假如舟的凹槽不是跟硅片外边缘平行,则硅片肯定会受到一个不垂直外边缘的力,如果硅片跟石英舟之间有较大的震动或碰撞,而力的方向又是沿〈111〉方向,则硅片很容易缺角。
05材料力学-轴向拉伸与压缩
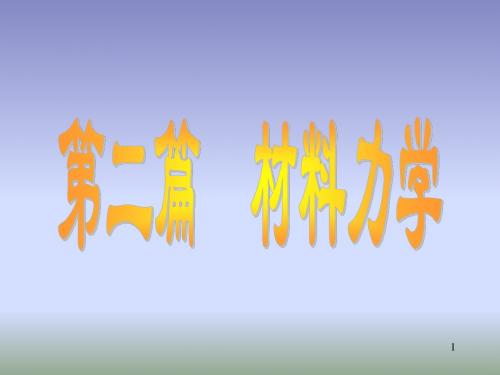
§5.2 拉、压杆的强度计算
保证构件不发生强度破坏并有一定安全余量的条件准则。
N ( x) max max( ) A( x)
依强度准则可进行三种强度计算: ① 校核强度:
其中:[]—许用应力, max—危险点的最大工作应力。
max
P
② 设计截面尺寸: Amin N max
1
引
言
构件是各种工程结构组成单元的统称。机械中的轴、杆
件,建筑物中的梁、柱等均称为构件。当工程结构传递运动或
承受载荷时,各个构件都要受到力的作用。为了保证机械或建 筑物的正常工作,构件应满足以下要求: 强度要求 所谓强度,是指构件抵抗破坏的能力。 刚度要求 所谓刚度,是指构件抵抗变形的能力。
稳定性要求 所谓稳定性,是指构件保持其原有平衡形态的
22
均匀材料、均匀变形,内力当然均匀分布。 2. 拉伸应力:
P
N(x)
N ( x) A
轴力引起的正应力 —— : 在横截面上均布。
3. 危险截面及最大工作应力: 危险截面:内力最大的面,截面尺寸最小的面。 危险点:应力最大的点。
N ( x) max max( ) A( x)
23
能力。 构件的强度、刚度和稳定性问题与其所选用材料的力学性
质有关,而材料的力学性质必须通过实验来测定。
2
杆件在不同的外力作用下将产生不同形式的变形,主要有: 1.轴向拉伸和压缩 :其受力特点是:作用在杆件的力,大 小相等、方向相反,作用线与杆件的轴线重合,因此在这种外 力作用下,变形特点是:杆件的长度发生伸长或缩短。起吊重 物的钢索、桁架的杆件、液压油缸的活塞杆等的变形,都属于
larc05准则

LaRC05准则是一种复合材料失效准则,它被用于预测复合材料在受到外部载荷作用时的损伤起始和扩展。
LaRC05准则主要考虑了复合材料的基体开裂、纤维拉伸和压缩失效等失效模式。
在往期的Abaqus版本中,要应用LaRC05失效准则,用户需要根据一定的规则手动编辑关键词,但从Abaqus 2021版本开始,LaRC05失效准则已经被整合进Abaqus CAE,使得用户可以直接在CAE界面中输入参数来调用这一准则,极大简化了操作流程。
LaRC05准则的几个主要表达式涵盖了如下失效模式:1. 基体开裂:当基体材料承受的应力超过其拉伸强度时,基体会发生开裂。
2. 纤维拉伸:当纤维受到的拉伸应力超过其拉伸强度时,纤维会发生断裂。
3. 纤维压缩:当纤维受到的压缩应力超过其压缩强度时,纤维会发生破坏。
在Abaqus/CAE的操作流程中,用户需要在Property模块下选择材料编辑选项,然后进入Mechanical Damage for Fiber-Reinforced Composites,选择LaRC05 Damage。
完成相关参数的输入后,Abaqus会在inp文件中生成对应的关键字。
这些参数的物理意义如下:- XT:纵向拉伸强度- XC:纵向压缩强度- YT:横向拉伸强度- YC:横向压缩强度- SL:面内剪切强度- 0:默认的横向压缩工况下的断裂角- M:压缩失效时的偏折角- L:纵向剪切摩擦系数- T:横向剪切摩擦系数- ST:横向剪切强度如果L和T未定义,Abaqus会根据特定的公式来计算这两个值。
总的来说,LaRC05准则是复合材料力学领域重要的失效预测工具,被广泛用于工程分析和设计中,以评估复合材料结构在复杂载荷下的性能和寿命。
在最新的SIMULIA 2023中,LaRC05失效准则的集成使得工程师可以更加方便快捷地进行复合材料的失效分析。
复合材料的断裂和韧性
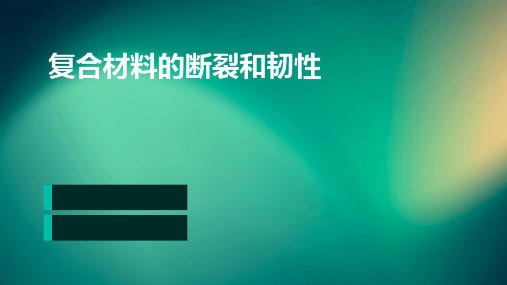
工程应用
复合材料的断裂和韧性研究对于指导 工程实践具有重要意义。例如,在航 空航天领域,需要确保复合材料在极 端环境下的安全性和可靠性;在汽车 领域,需要提高复合材料的抗冲击性 能和耐久性。通过深入研究复合材料 的断裂和韧性,可以为这些工程应用 提供有力的理论支持和实践指导。
02 复合材料断裂行为
多功能复合材料探索
未来复合材料将不仅局限于力学性能的提升,还将探索多功能性,如自修复、自适应、智能响应等。
绿色环保复合材料发展
面对日益严峻的环境问题,未来复合材料的发展将更加注重环保性,致力于开发低污染、可回收、生 物降解的复合材料。
对行业影响及建议
推动产业升级
复合材料的断裂和韧性研究将推动相关产业 升级,提高产品质量和性能,降低成本,增 强市场竞争力。
基于复合材料微观结构,建立描述断 裂过程中纤维、基体和界面行为的力 学模型。
利用有限元方法模拟复合材料在不同 加载条件下的断裂过程,预测裂纹扩 展路径和韧性。
断裂力学理论
应用线弹性断裂力学(LEFM)和非 线性断裂力学(NLFM)理论,分析 裂纹扩展和断裂韧性。
实验验证与数据分析
材料制备与测试
制备具有不同纤维含量、类型和 排列方式的复合材料试样,进行 拉伸、弯曲和冲击等力学性能测
弯曲试验
通过三点或四点弯曲试验评估 复合材料的弯曲性能和韧性。
断口形貌分析
利用扫描电子显微镜(SEM) 等手段观察断口形貌,分析断 裂机制和影响因素。
拉伸试验
通过拉伸试验测定复合材料的 强度、延伸率等力学性能指标。
压缩试验
通过压缩试验了解复合材料在 压缩载荷下的性能表现。
界面性能表征
采用界面剪切强度测试、剥离 试验等方法评估复合材料的界 面性能。
无机材料的断裂及裂纹扩展课件

裂纹的萌生和扩展
初始裂纹在外部载荷的作 用下逐渐扩大并萌生新的 裂纹,这些裂纹相互作用 并形成裂纹扩展的路径。
最终断裂
当裂纹扩展到一定程度时 ,材料发生最终断裂。
裂纹扩展的速率控制
应力强度因子
应力强度因子是控制裂纹扩展速 率的一个重要参数,它表征了裂
01
线弹性断裂力学是研究材料在弹性范围内发生的断裂行为,适
用于材料在断裂前没有发生塑性变形的情形。
应力和应变的关系
02
在材料发生断裂前,应力和应变的关系是线性的,遵循胡克定
律。
弹性模量和泊松比
03
描述材料在弹性范围内对变形响应的两个重要参数是弹性模量
和泊松比。
弹塑性断裂力学
01
弹塑性断裂力学的定义和适用范围
,越不容易发生断裂。
应力集中
应力集中是指在材料中存在的 一些缺陷或不平整区域,这些 区域容易产生应力集中,降低 材料的强度。
温度和湿度
温度和湿度也会影响材料的强 度和韧性,进而影响材料的断 裂性能。
加载速度
加载速度越快,材料的断裂时 间越短,越容易发生脆性断裂
。
02
无机材料的裂纹扩展
裂纹扩展的机制
无机材料的断裂及裂纹扩展课件
目录
• 无机材料断裂概述 • 无机材料的裂纹扩展 • 无机材料的断裂力学 • 无机材料的断裂及裂纹扩展实验研究 • 无机材料的断裂及裂纹扩展研究进展 • 无机材料的断裂及裂纹扩展在工程中的应
用
01
无机材料断裂概述
断裂定义与分类
断裂定义
断裂是指材料在应力或温度等外 部因素作用下,内部应力超过材 料强度,导致材料结构破坏的现 象。
05_断裂力学基础知识
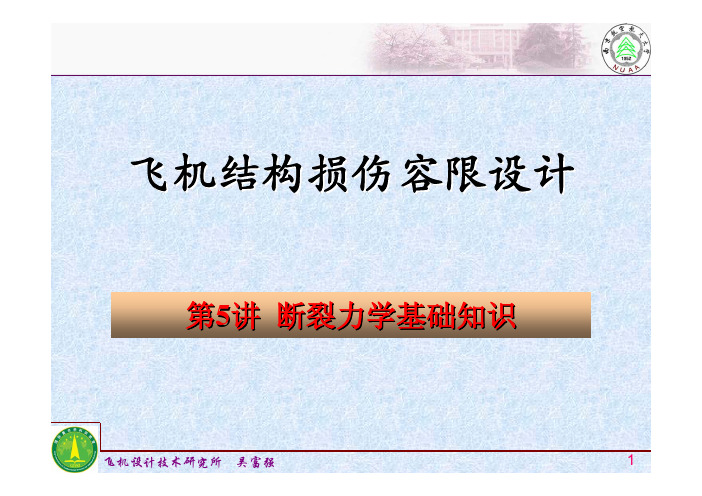
飞机结构损伤容限设计第5讲断裂力学基础知识内容概要1.断裂力学简介2.能量平衡理论3.应力强度因子理论4.裂纹尖端塑性区5.复合型准则6.断裂韧度试验结构断裂,起源于裂纹。
断裂力学:采用弹、塑性理论和新的试验技术研究裂纹尖端附近的应力、应变场和裂纹扩展的一门学科。
研究对象:带裂纹的材料和结构。
裂纹的生成裂纹的亚临界扩展断裂开始断裂传播断裂停止1921年Griffith探索“为什么玻璃等材料的实际断裂强度比用分子结构理论所预期的强度低得多?”通过系列研究,他认为物体内部存在细小的缺陷或裂纹,在外载作用下物体内部能量释放所产生的裂纹驱动力导致了裂纹的增长,同时物体内部也存在阻止形成新裂纹面积的阻力,即在裂纹增长过程中物体中驱动裂纹增长的动力与阻止裂纹增长的阻力是平衡的。
Griffith的上述研究分析促使了断裂力学的形成!Griffith 根据Inglis 对开孔薄板的应力场、位移场计算公式,计算出椭圆孔短轴尺寸趋于零(理想裂纹尖端)时,含孔裂纹板应变能的改变为:22224a tA U E E πσπσ==2A at =裂纹单侧自由表面的面积。
裂纹扩展动力!裂纹扩展后,形成两个新的自由表面,则其表面能增加了,设γ为表面能密度,则两个自由表面总的表面能为:2A γΓ=则含裂纹板相对于初始状态的总势能为:裂纹扩展阻力!2224A P U A E πσγ=−+Γ=−+裂纹处于不稳定平衡状态时,有:0P A∂=∂220P A ∂<∂有:22204P A A Etπσγ∂=−+=∂222AEtπσγ=Griffith 理论研究结果仅适用于完全脆性材料,而绝大多数金属材料断裂前都存在塑性区域,该理论不适用,这是Griffith 理论长期得不到重视的原因。
Orowan 对金属材料裂纹扩展过程进行研究后,指出裂纹扩展前在其尖端附件会产生一个塑性区,因而提供给裂纹扩展的能量不仅用于形成新的表面所需要的表面能,还用于引起塑性变形所需的能量,即“塑性功”,则:22224A P U A A E πσϕγ=−+Γ+Ψ=−++ψ为塑性功率。
05-石油管环境断裂案例及尚未解决的难题

1998~2003年 其中一口井718芯轴断裂发现过程如下:完井测试后,关井30小时待压
井。再过4小时,发现环空带压,立即关井下安全阀,同时关闭平台上 所有其它开发井,切断平台总阀。起油管后未发现油管有问题,又重 下入油管,对环空水试压。发现与C110抗硫套管联接的套管挂718芯 轴内螺纹最末完全扣开裂,断口长约为周长的一半,断口中心部呈脆 性状,其余为韧性断裂。
偶尔个别井检测到极微量硫化氢,一般15—200ppm,一次测到4000ppm,另一次测
到8000ppm
二、双向钢油管环境断裂有:
氢脆和应力腐蚀开裂; 电偶诱发氢应力开裂; 卤化盐应力腐蚀开裂
双向钢油管氢脆和应力腐蚀开裂
1998年: 投产后约12个月,发现A环空带压,关井取油管修井。 5” 25Cr—130ksi油管,井口下6根油管外壁点蚀严重,第
三根在内压下纵向开裂。 油套环空保护液:。顶部汽化后升
压,多次放压后形成汽液动液面。注冷却剂时管线漏,空气 中氧混入,加剧点蚀。
教训:加缓蚀剂氯化钙水溶液不可用
硫化氢氢脆开裂
2000年: 投产后发现,B环空也带压,说明相互窜通 关井和关闭平台,人员撤离。怀疑技套下地层会破裂,平台下冒气。 16天后压井,修井取出油管,井发现扣根横向破裂,导致A环 空带压。 油管挂短节母扣硫化氢氢脆开裂, 718微相检测,发论晶间 相,
事前无征兆、突发事故可能操作慌乱,或伤人。
在油气井设计和完井作业中,可能的环 境断裂种类或机理
第一类,氢脆和应力腐蚀开裂 由地层中产出的湿硫化氢或酸化作业酸反应生成的氢离子
进入钢材,导致材料脆化。应力腐蚀和氢脆之间并没有严 格的区分,二者可同时发生,也可以说氢脆是应力腐蚀的 本质因素或机理之一。 在含硫气井设计中氢脆和应力腐蚀开裂有明确和严格的标 准或技术法规,ISO/NACE 15156, ISO/API 11960
ASTM测试标准:金属疲劳与断裂标准一览

ASTM美国材料实验协会(American Society of Testing Materials )前身是国际材料试验协会(International Association for Testing Materials, IATM)。
19世纪80年代,为解决采购商与供货商在购销工业材料过程中产生的意见和分歧,有人提出建立技术委员会制度,由技术委员会组织各方面的代表参加技术座谈会,讨论解决有关材料规范、试验程序等方面的争议问题。
ASTM是美国最老、最大的非盈利性的标准学术团体之一。
经过一个世纪的发展,ASTM现有33669个(个人和团体)会员,其中有22396个主要委员会会员在其各个委员会中担任技术专家工作。
ASTM的技术委员会下共设有2004个技术分委员会。
有105817个单位参加了ASTM标准的制定工作,主要任务是制定材料、产品、系统、和服务等领域的特性和性能标准,试验方法和程序标准,促进有关知识的发展和推广。
下面是金属疲劳与断裂标准一览:B645-02 铝合金的平面应变断裂韧性试验 Standard Practice forPlane-Strain Fracture Toughness Testing of Aluminum AlloysB646-04 铝合金断裂韧性试验 Standard Practice for Fracture Toughness Testing of Aluminum AlloysE6-03 有关力学试验方法的标准术语 Standard Terminology Relating to Methods of Mechanical TestingE23-02a 金属材料切口试棒的冲击试验方法 Standard Test Methods for Notched Bar Impact Testing of Metallic MaterialsE139-00e1 金属材料蠕度、蠕变断裂和应力断裂试验 Standard Test Methods for Conducting Creep, Creep-Rupture, and Stress-Rupture Tests of Metallic MaterialsE292-01 材料断裂时间的凹口张力试验 Standard Test Methods for Conducting Time-for-Rupture Notch Tension Tests of Materials E328-02 材料和结构件的应力松弛试验 Standard Test Methods for Stress Relaxation Tests for Materials and StructuresE338-03 高强度薄板材料的锐切口张力试验方法 Standard Test Method of Sharp-Notch Tension Testing of High-Strength Sheet MaterialsE340-00e1 金属和合金宏观腐蚀的测试方法 Standard Test Method for Macroetching Metals and AlloysE399-05 金属材料水平变形断裂强度的测试方法 Standard Test Method for Plane-Strain Fracture Toughness of Metallic MaterialsE436-03 铁素体钢的坠重破裂试验方法 Standard Test Method forDrop-Weight Tear Tests of Ferritic SteelsE466-96(2002)e1 金属材料上进行的恒定振幅轴向疲劳试验 Standard Practice for Conducting Force Controlled Constant Amplitude Axial Fatigue Tests of Metallic MaterialsE467-05 轴向负载疲劳试验机中恒振幅动态负载检验 Standard Practice for Verification of Constant Amplitude Dynamic Forces in an Axial Fatigue Testing SystemE468-90(2004)显示金属材料定幅疲劳试验结果的方法 Standard Practice for Presentation of Constant Amplitude Fatigue Test Results for Metallic MaterialsE561-05 R-曲线测定 Standard Practice for R-Curve DeterminationE602-03 圆柱形试样的锐切口张力的试验方法 Standard Test Method for Sharp-Notch Tension Testing with Cylindrical SpecimensE604-83(2002) 金属材料的动态断裂试验方法 Standard Test Method for Dynamic Tear Testing of Metallic MaterialsE606-92(2004)e1 应变控制环疲劳试验 Standard Practice forStrain-Controlled Fatigue TestingE646-00 金属薄钢板材料的拉伸应变硬化指数(n值)的测试方法 Standard Test Method for Tensile Strain-Hardening Exponents (n-Values) of Metallic Sheet MaterialsE647-05 疲劳裂缝增大率测量用测试方法 Standard Test Method for Measurement of Fatigue Crack Growth RatesE739-91(2004) 线性或线性化应力寿命(S-N)和应变寿命(e-N)疲劳数据的统计分析 Standard Practice for Statistical Analysis of Linear or LinearizedStress-Life (S-N) and Strain-Life (ε-N) Fatigue DataE740-03 用表面破裂张力试样做断裂试验 Standard Practice for Fracture Testing with Surface-Crack Tension SpecimensE812-91(1997) 高强度金属材料制慢弯预裂落摆冲击试样的破裂强度的测试方法 Standard Test Method for Crack Strength of Slow-Bend Precracked Charpy Specimens of High-Strength Metallic MaterialsE813-91 断裂韧性JIC测定的标准试验方法 Standard Test Method For JIC,A Measure Of Fracture ToughnessE992 使用等效能量法确定钢的断裂韧度的惯例 Practice for Determination of Fracture Toughness of Steels Using Equivalent Energy Methodology E1049-85(1997) 疲劳分析的周期计数 Standard Practices for Cycle Counting in Fatigue AnalysisE1152 Test Method for Determining J-R Curves3E1169-02 耐久性试验的实施 Standard Guide for Conducting Ruggedness TestsE1221-96(2002) 测定Kla铁素体钢的平面应变,断裂抑制,破裂韧性的试验方法 Standard Test Method for Determining Plane-Strain Crack-Arrest Fracture Toughness, KIa, of Ferritic SteelsE1290-02 测量裂缝尖端开口位移(CTOD)裂缝韧性的试验方法 Standard Test Method for Crack-Tip Opening Displacement (CTOD) Fracture Toughness MeasurementE1304-97(2002) 金属材料平面应变(V型槽口)断裂韧度的测试方法(代替SAE ARP 1704) Standard Test Method for Plane-Strain (Chevron-Notch) Fracture Toughness of Metallic MaterialsE1457-00 测量金属蠕变开裂增长速度的试验方法 Standard Test Method for Measurement of Creep Crack Growth Rates in MetalsE1681-03 恒定载荷下金属材料环境促使裂纹的阈应力强度系数测定标准试验方法 Standard Test Method for Determining a Threshold Stress Intensity Factor for Environment-Assisted Cracking of Metallic MaterialsE1737-1996 断裂韧性J积分的表征 J-INTERGRAL CHARACTERIZATION OF FRACTURE TOUGHNESSE1820-01 断裂韧性测定的标准试验方法 Standard Test Method for Measurement of Fracture ToughnessE1823-96(2002) 疲劳和裂纹试验相关的标准术语 Standard Terminology Relating to Fatigue and Fracture TestingE1921-05 测定铁素体钢在转变范围内基准温度的标准试验方法 Standard Test Method for Determination of Reference Temperature, To’, for Ferritic Steels in the Transition RangeE1942-98(2004) 周期性疲劳和断裂力学试验中采用的数据采集系统的评定标准导则 Standard Guide for Evaluating Data Acquisition Systems Used in Cyclic Fatigue and Fracture Mechanics TestingE2207-02 用薄壁管状样本进行张力控制轴向扭力疲劳试验惯例 Standard Practice for Strain-Controlled Axial-Torsional Fatigue Testing with Thin-Walled Tubular SpecimensE2368-04 张力受控的热机械疲劳测试惯例 Standard Practice for Strain Controlled。
汽车零部件断裂失效分析简述(岑举
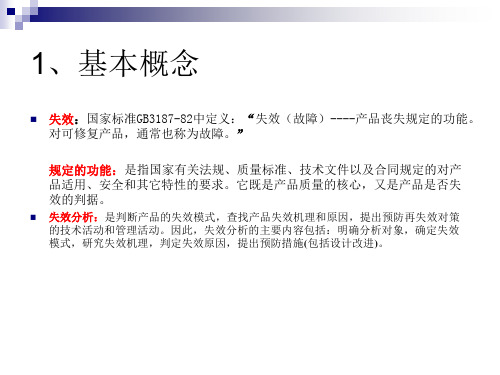
结构和配合的特性、载荷的性质和幅值、大多的内在质量缺陷、工作 和运行的状态、应力状态等等,都属于力学分析的范畴。他们不仅决 定了是否开裂,还总体上决定了以什么形式或在什么部位开裂。
设计的使用应力(各种指标)和强度(各种指标)技术条件;
关注实际的使用应力(工况)及制造质量分布的偏移和变化; 两者分布曲线相交则产生失效。 目前的失效分析和认知程度、评价主要还是在定性的水平上。
技术条件 设计应力
制造质量 使用应力、工况
2.5 断裂分析要素
从可靠性理论中断裂的应力模型得知,应力和强度是断裂分析的两大 要素,两个要素中哪一个贡献较大?最为活跃?如何地感知和评价是 断裂分析中的一个焦点;
关于灰色系统
是对内部结构可以部分了解或可以综合运用逻辑推理的方法进行 分析的系统。
从人类实践的绝对性来看,人类可以穷尽对机电失效规律及其预 防的认识,但从对失效分析的个别实践和认识来看,又总是在有 限的空间内进行的。因此,对失效特点和规律的认识又往往是有 限的和相对的,这就决定了失效分析的研究和发展总是处于一 个灰色系统内。 (失效分析的持续性、阶段性、可认知性和无止境性) (失效分析的病理学研究方法和流行病学研究方法)
式等原因引发局部产生微动磨损现 象,导致疲劳开裂。这类问题在轴 孔配合结构中最多体现。
疲劳断裂
案例20、某连杆销孔疲劳开裂 在挤压载荷作用下的疲劳开裂; 表现出了对油孔边缘处应力集中
的敏感性。
疲劳断裂
案例22、剪切应力疲劳开裂
半轴、钢板弹簧等零件,产生在高强韧性的零件中; 属于应变疲劳的性质,也称为高应力低周疲劳; 扭转的应力状态更有部件及断裂失效特性
金属材料的断裂准则及断裂行为数值模拟
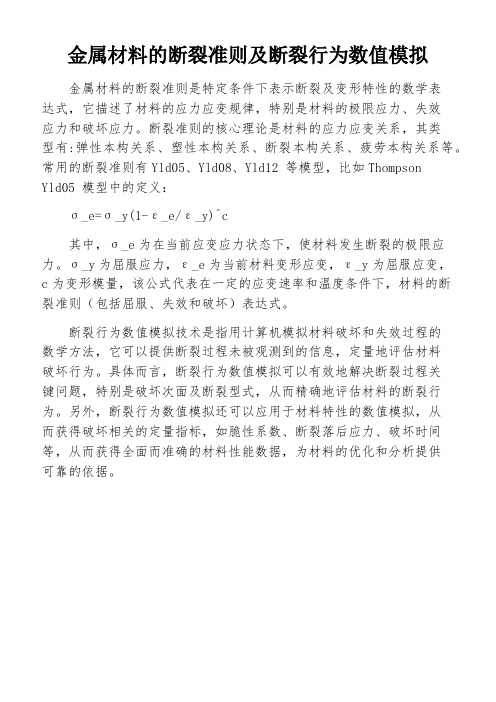
金属材料的断裂准则及断裂行为数值模拟
金属材料的断裂准则是特定条件下表示断裂及变形特性的数学表
达式,它描述了材料的应力应变规律,特别是材料的极限应力、失效
应力和破坏应力。
断裂准则的核心理论是材料的应力应变关系,其类
型有:弹性本构关系、塑性本构关系、断裂本构关系、疲劳本构关系等。
常用的断裂准则有Yld05、Yld08、Yld12 等模型,比如Thompson
Yld05 模型中的定义:
σ_e=σ_y(1-ε_e/ε_y)^c
其中,σ_e为在当前应变应力状态下,使材料发生断裂的极限应力。
σ_y为屈服应力,ε_e为当前材料变形应变,ε_y为屈服应变,
c为变形模量,该公式代表在一定的应变速率和温度条件下,材料的断
裂准则(包括屈服、失效和破坏)表达式。
断裂行为数值模拟技术是指用计算机模拟材料破坏和失效过程的
数学方法,它可以提供断裂过程未被观测到的信息,定量地评估材料
破坏行为。
具体而言,断裂行为数值模拟可以有效地解决断裂过程关
键问题,特别是破坏次面及断裂型式,从而精确地评估材料的断裂行为。
另外,断裂行为数值模拟还可以应用于材料特性的数值模拟,从
而获得破坏相关的定量指标,如脆性系数、断裂落后应力、破坏时间等,从而获得全面而准确的材料性能数据,为材料的优化和分析提供
可靠的依据。
材料力学中的断裂行为

材料力学中的断裂行为材料力学是研究材料在外力作用下的力学性能和变形行为的学科。
其中,断裂行为是材料力学研究的重点之一。
断裂行为是指材料在外力作用下出现破裂现象的过程和特点。
材料的断裂行为是由其内部微观结构和宏观形态的相互作用所决定的,因此,其研究具有很高的理论和实践意义。
1. 断裂行为的基本概念和分类断裂行为可以分为韧性破裂、脆性破裂以及疲劳破裂三种类型。
其中,韧性破裂是指材料在外力作用下,从初始破裂点开始不断进行新的断裂过程,直到完全破断的过程。
韧性破裂的特点是材料的破断过程比较缓慢,破断过程中会发生延性变形,并且破断前的塑性变形比较明显。
脆性破裂是指材料在外力作用下,破断过程比较急速,并且几乎没有塑性变形,一旦材料破断就形成不可逆的断裂口。
疲劳破裂是指材料在外力作用下,长期受到交替作用,导致材料失效。
2. 断裂韧性的评价在实际工程中,对于许多金属和合金材料,我们都需要考虑它们的断裂韧性。
断裂韧性是指材料在受到外力作用时,能够承受大的破坏能量,以及在破坏前能够发生更多的形变和变形。
断裂韧性的评价方法有很多种,最常用的是通过断口形貌来进行判断和评估。
一般来说,越具有韧性的材料,其断口形貌越平缓,而越缺乏韧性的材料,则其断口形貌越微裂纹和锐利。
3. 断裂机理材料的断裂机理是指材料在受到外力作用下,其内部微观结构发生变化的过程和规律。
一般来说,断裂机理包括微观裂纹、裂纹扩展和联合断裂等多个阶段。
微观裂纹是指在材料内部形成的微小裂纹,一般在材料的劣化或者外力作用下产生。
裂纹扩展是指微观裂纹因受到外力作用而不断扩展,直至材料破断。
联合断裂是指材料在受到多个外力作用下,发生多处韧性破裂并联合形成的断口。
4. 断裂行为的影响因素材料的断裂行为受多个因素的影响。
主要有材料的力学性质、微观结构、温度、速率和热处理等。
其中,材料的力学性质是影响断裂行为的决定性因素之一。
比如说强度和韧性是材料决定其断裂行为的最重要的性能指标。
- 1、下载文档前请自行甄别文档内容的完整性,平台不提供额外的编辑、内容补充、找答案等附加服务。
- 2、"仅部分预览"的文档,不可在线预览部分如存在完整性等问题,可反馈申请退款(可完整预览的文档不适用该条件!)。
- 3、如文档侵犯您的权益,请联系客服反馈,我们会尽快为您处理(人工客服工作时间:9:00-18:30)。
-Griffith公式
σc是含裂纹板材的实际断裂强度,与裂纹尺寸的平方根成反比。
(将理论断裂强度公式中a0以πa / 2代替即变 成Griffith公式。)
¾当裂纹长度a一定,σ>σc时,裂纹即失稳扩展。 ¾当承受拉伸应力σ一定时,则临界裂纹ac为:
a > 2ac时,裂纹自动扩展,发生断裂; a<2ac时,不会发生断裂。 对于厚板:
¾Griffith理论的前提是材料中已存在着裂纹,但不涉及 裂纹来源。对于不存在裂纹的金属,Griffith理论无法解 释它们实际强度低的原因。后来人们根据这类金th裂纹长度时,就会发生断裂。
思考题:
1、一薄板内有一条长3mm 的裂纹,且 a0 =3×10-8 mm,试求脆性断裂时的断 裂应力 σC(设 σ th =E/10=2×105 MPa )。 2、有一材料 E=2×1011 N/m2,γS =8N/m,试计算在 7×107 N/m2 的拉力 作用下,该材料的临界裂纹长度。
韧性断裂与脆性断裂
¾ 韧性断裂:断裂前有明显宏观塑性变形,断裂 是一个缓慢撕裂过程,裂纹扩展过程中,不断 消耗能量; ¾ 脆性断裂:断裂前不发生明显塑性变形,无明 显征兆,危害性大。 ¾ 实际上,金属的脆性断裂与韧性断裂并无明显 的界限,一般规定,断面收缩率小于5%者为脆 性断裂,大于5%者,为韧性材料。
碳化物开裂的力学条件:
碳化物裂纹向铁素体 中扩展的力学条件:
σc ≥ [
4 E (γ f + γ c )
π (1 −ν )c0
2
]
1 2
c0为碳化物厚度
二、脆性断裂的微观特征
(1)解理断裂(cleavage fracture)
¾解理断裂是穿晶的脆性断裂。 ¾由于多晶体的位向取向不一,解理断裂后 形成许多无规则取向的晶粒大小为单位“小刻 面” ,在强光照射下出现金属闪光,宏观上 常形容为“结晶状”断口。 ¾解理断裂的三个微观特征:解理台阶、河 流花样、舌状花样。
σm=λE/2πa0
Eγ s σm = ( ) a0
1 2
这就是理想晶体脆性(解理)断裂的理论断 裂强度。可见,σm与表面能γs有关,解理 面往往是表面能最小的面,可由此式得到理 解。
公式
Eγ s 1 σm = ( )2 a0
的应用:
例:铁的E=2×105 MPa,a0=2.5×10-10 m, γs=1 J/m2, 则σm=28.3 GPa。
如果在弹性状态下晶体被破坏,位移x很小,则
σ=σm(2πx/λ)
根据虎克定律,在弹性状态下: σ=Eε=Ex/a0
σm=λE/2πa0
式中E为弹性模量;a0为原子间的平衡距离。
断裂发生过程中,必须提供足够的能量以形成两 个新表面。如材料的单位表面能为γs,即外力作 功消耗在断口形成上的能量至少等于2γs:
不动位错
该位错反应是能量降低的过 程,因而裂纹成核是自动进行 的,但对fcc来说,也有类似的 位错反应,但不是能量降低的 过程,所以fcc没有这样的裂纹 成核机理。
(3)史密斯(Smith)理论(脆性第二相开裂理论)
考虑显微组织不均匀造成的影 响,史密斯提出低碳钢中因铁素 体塑性变形导致晶界碳化物开裂 形成解理裂纹的理论:铁素体中 的位错源在切应力作用下开动, 位错运动至晶界碳化物处受阻而 形成塞积,在塞积头处拉应力作 用下使碳化物开裂。
4) 块体材料和晶须材料的强度 Fe Cu 冶金熔炼材料 300MPa 140MPa 晶须 35000MPa 28000MPa
二、材料的实际断裂强度(Griffith理论)
¾固体材料中裂纹的存在,导致其实际断裂强度 与理论强度至少相差一个数量级。为了解决裂纹 体的断裂强度问题, Griffith在1921年从能量平衡 的观点出发,研究了陶瓷、玻璃等脆性材料的断 裂问题。 ¾Griffith假定在实际材料中存在着裂纹,当条件 应力还很低时,裂纹尖端的局部应力已达到很高 的数值,从而使裂纹快速扩展,并导致脆性断 裂。在此基础上提出了裂纹理论,后来逐渐成为 脆性断裂的主要理论基础。
第五章 材料的断裂
§ 5.1 断裂分类与宏观断口特征 § 5.2 断裂强度 § 5.3 脆性断裂 § 5.4 韧性断裂 § 5.6 缺口效应 § 5.7 材料的低温脆性
¾机械和工程构件三种主要失效形式:
磨损、腐蚀、断裂
¾ 断裂是材料的一种十分复杂的行为,不仅出现在高 应力和高应变条件下,也发生在低应力和无明显塑 性变形条件下,所以在不同的力学、物理和化学环 境下,会有不同的断裂形式,如静载断裂、冲击断 裂、冷脆断裂、疲劳断裂、蠕变断裂、应力腐蚀断 裂和氢脆断裂。 ¾ 研究断裂的主要目的是防止断裂,以保证构件在服 役过程中的安全。
¾Griffith公式适用于陶瓷、玻璃、超高强度钢等脆性材料。
对于塑性材料,由于在裂纹尖端处产生较大塑性变 形,吸收大量的变形功,这部分变形功是裂纹扩展 需要克服的主要阻力,所以Griffith公式修正为:
--Griffith-Orowan-Irwin公式
式中,γp为单位面积裂纹表面吸收的塑性变形功, 2γs+γp称为有 效表面能。一般γp比表面能大几个数量级。上式是塑性金属材料的 断裂判据。
滑移面
70.5° 解理裂纹
解理面
FCC滑移系多,塞积群少,应力集中不大,所以不易形成解 理裂纹。
¾形成裂纹的有效切应力τ
− τ i 必须满足以下关系式:
¾裂纹扩展并导致解理断裂的条件是外加正应力σ达到临界 应力σc :
其中G为切变模量, Ky 是Hall − Petch关系式中的钉扎常数。
由上式可以看出,晶粒越小,断裂应力提高,材料脆性降低。
(2)柯垂尔(Cottrell)理论(位错反应理论)
在bcc晶体中,有两个相交的 滑移面 (101)和(101)与解理面 (001)相交,三面交线为 a a [111] [010]。现有位错群 2 和 2 [111] 相遇于[010]轴,并产生下列 反应:
a a [111] + [111] → a[001] 2 2
解理裂纹形成机理:
(1) 甄纳-斯特罗(Zener-Stroh)理论(位错塞积理论)
甄纳和斯特罗认为,在切 应力作用下,滑移面上的 刃型位错运动遇到障碍 (晶界或者第二相颗 粒),产生位错塞积,当 塞积头的应力集中不能通 过塑性变形得到松弛时, 塞积端点处的最大拉应力 可以达到理论断裂强度而 形成楔行裂纹。
一、晶体的理论断裂强度
¾从原子间的结合力入手,当克 服了原子间的结合力,材料断 裂。
9原子间距随应力的增加 而增大,在某点处,应力 克服了原子之间的作用 力,达到一个最大值,这 一最大值即为理论断裂强 度σm 。
作为一级近似,该曲线可用 正弦曲线表示:
σ=σmsin(2πx/λ)
式中x为原子间位移,λ为正弦曲线的波长。
Griffith裂纹模型
整个系统的能量变化为:
Ue+W=4aγs-πσ2a2/E
由图可知,当裂纹增长到2ac 后,若再增长,则系统的总能 量下降。从能量观点来看,裂 纹长度的继续增长将是自发过 程,则临界状态为:
系统能量随裂纹半长a的变化
∂(Ue+W)/ ∂ a =4γs-2πσ2a/E =0
裂纹失稳扩展的临界应力为:
正断与切断
¾ 正断:断口与最大正应力相垂直; ¾ 切断:宏观断口的取向与最大切应力方向平 行。 注意:正断不一定就是脆性断裂,正断也 可以有明显的塑性变形。而切断一定是韧性 断裂。
二、断口的宏观特征
¾ 宏观断口:肉眼或20倍以下的放大镜观察的断口; ¾ 微观断口:用光学显微镜或扫描电镜观察的断口。
5.3 脆性断裂
¾ 脆性断裂的宏观特征,理论上讲,是断裂前不发生 塑性变形,而裂纹的扩展速度往往很快,接近音速。 ¾ 脆性断裂前无明显的征兆可寻,且断裂是突然发生 的,因而往往引起严重的后果。因此,要防止脆断。
一、脆性断裂机理
¾ 脆性断裂的两种主要机理:解理断裂和沿晶断裂。 ¾ 对解理断裂:实验结果表明,尽管解理断裂是典型的 脆性断裂,但解理裂纹的形成却与材料的塑性变形有 关,而塑性变形是位错运动的结果,因此,为了探讨 解理裂纹的产生,不少学者采用位错理论来解释解理 裂纹形成机理。
试验证据:
1)Griffith发现刚拉制玻璃棒的弯曲强度为6GPa;而 在空气中放置几小时后强度下降为0.4 GPa。其原因是 由于大气腐蚀形成了表面裂纹。 2) 约飞等人用温水溶去氯化钠表面的缺陷,强度即由 5MPa提高到1.6×103MPa,提高了300多倍。 3) 有人把石英玻璃纤维分割成几段不同的长度,测其强 度时发现,长度为12cm时,强度为275MPa;长度为 0.6cm时,强度可达760MPa。这是由于试件长,含有危 险裂纹的机会增多。
¾ 设想有一单位厚度的无限宽薄板,对其施加一拉应 力σ后将其两端固定,并与外界隔绝能源。
¾板材每单位体积的弹性能为σ2/2E;
¾割开一长度为2a的裂纹, 则原来弹性拉紧的平板就要 释放弹性能。根据弹性理论 计算,释放出来的弹性能 为:
Ue= -πσ2a2/E
¾形成新表面所需的表面能为:
W=4aγs
穿晶断裂与沿晶断裂
¾穿晶断裂:裂纹穿过晶内 (韧断或脆断) ¾沿晶断裂:裂纹沿晶界扩 展(多为脆断) ¾沿晶断裂产生原因: 晶界上的一薄层连续或不 连续脆性第二相、夹杂物破 坏了晶界的连续性;或杂质 元素向晶界偏聚引起。
纯剪切断裂与微孔聚集型断裂、解理断裂
⑴ 剪切断裂:在切应力作用下沿滑移面分离而造成的滑 移面分离断裂。 ¾ 纯剪切断裂:完全由滑移流变造成断裂(如纯金属尤 其是单晶体); ¾ 微孔聚集型断裂:通过微孔形核、长大聚合而导致分 离(如常用金属材料) ⑵ 解理断裂:金属材料在一定条件下(如低温等),当 外加正应力达到一定数值后,以极快速率沿一定晶体 学平面(解理面)产生的穿晶断裂——脆断。 ¾ 解理断裂常见于bcc和hcp金属中。 ¾ 解理面一般是低指数晶面或表面能最低的晶面,如 bcc金属的解理面为(100) 。