第6章金属切削原理作业
《金属切削原理与刀具》知识点总结

《金属切削原理与刀具》知识点总结第一章金属切削原理金属切削原理是金属切削工艺的基础,本章主要介绍了金属切削的基本原理,包括金属切削过程、刀具与被切削材料接触形式、切削能量与热力学原理、切削硬度与切削力的关系等。
第二章刀具材料与结构刀具材料与结构对切削加工的质量和效率有重要影响,本章主要介绍了刀具材料的选择与评价,以及刀具的结构与分类。
刀具材料的选择包括一般刀具材料、质子刀具材料和陶瓷刀具材料等。
第三章切削力分析与测定切削力是切削加工过程中的重要参数,正确定量和测定切削力对于提高切削加工的效率和质量至关重要。
本章主要介绍了切削力的分析与计算方法,以及切削力的测定方法,包括间隙力法、应力传感器法、功率法和应力波法等。
第四章刨削刨削是一种通过切削工具的多齿切削运动将金属材料切割成所需形状和尺寸的加工方法。
本章主要介绍刨削的工艺流程、刨削用刀具和切削参数的选择,以及刨削的切削力分析与测定方法。
第五章车削车削是一种利用车床刀具进行切削的加工方法,广泛应用于金属加工领域。
本章主要介绍了车削的工艺流程、车削刀具的选择和切削参数的确定,以及车削的主要工艺规律和效果评定方法。
第六章铣削铣削是一种通过旋转刀具进行切削的加工方法,广泛应用于金属加工和模具制造等领域。
本章主要介绍了铣削的工艺流程、铣削刀具的选择和切削参数的确定,以及铣削中的刀具磨损与刀具寿命评价方法。
第七章钻削钻削是一种利用钻头进行切削的加工方法,广泛应用于孔加工和螺纹加工等领域。
本章主要介绍了钻削的工艺流程、钻头的选择和切削参数的确定,以及钻削中的刀具磨损与刀具寿命评价方法。
第八章线切割线切割是一种利用细金属丝进行切削的加工方法,主要用于金属板材的切割。
本章主要介绍了线切割的工艺流程、线切割刀具的选择和切削参数的确定,以及线切割中的切削质量评价方法和切削速度对切割效果的影响。
此外,本书还包括金属切削中的润滑与冷却、数控机床中的刀具管理、切削机床中的刀具装夹等内容,为读者提供了全面的金属切削工艺和刀具知识。
金属切削原理与刀具习题和答案(全)
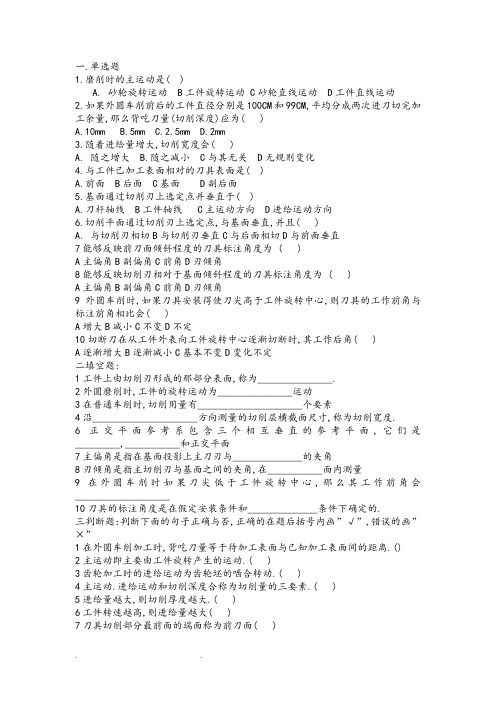
一.单选题1.磨削时的主运动是( )A.砂轮旋转运动 B工件旋转运动 C砂轮直线运动 D工件直线运动2.如果外圆车削前后的工件直径分别是100CM和99CM,平均分成两次进刀切完加工余量,那么背吃刀量(切削深度)应为( )A.10mmB.5mmC.2.5mmD.2mm3.随着进给量增大,切削宽度会( )A.随之增大B.随之减小 C与其无关 D无规则变化4.与工件已加工表面相对的刀具表面是( )A.前面 B后面 C基面 D副后面5.基面通过切削刃上选定点并垂直于( )A.刀杆轴线 B工件轴线 C主运动方向 D进给运动方向6.切削平面通过切削刃上选定点,与基面垂直,并且( )A.与切削刃相切B与切削刃垂直C与后面相切D与前面垂直7能够反映前刀面倾斜程度的刀具标注角度为 ( )A主偏角B副偏角C前角D刃倾角8能够反映切削刃相对于基面倾斜程度的刀具标注角度为 ( )A主偏角B副偏角C前角D刃倾角9外圆车削时,如果刀具安装得使刀尖高于工件旋转中心,则刀具的工作前角与标注前角相比会( )A增大B减小C不变D不定10切断刀在从工件外表向工件旋转中心逐渐切断时,其工作后角( )A逐渐增大B逐渐减小C基本不变D变化不定二填空题:1工件上由切削刃形成的那部分表面,称为_______________.2外圆磨削时,工件的旋转运动为_______________运动3在普通车削时,切削用量有_____________________个要素4沿_____________________方向测量的切削层横截面尺寸,称为切削宽度.6正交平面参考系包含三个相互垂直的参考平面,它们是_________,___________和正交平面7主偏角是指在基面投影上主刀刃与______________的夹角8刃倾角是指主切削刃与基面之间的夹角,在___________面内测量9在外圆车削时如果刀尖低于工件旋转中心,那么其工作前角会___________________10刀具的标注角度是在假定安装条件和______________条件下确定的.三判断题:判断下面的句子正确与否,正确的在题后括号内画”√”,错误的画”×”1在外圆车削加工时,背吃刀量等于待加工表面与已知加工表面间的距离.()2主运动即主要由工件旋转产生的运动.( )3齿轮加工时的进给运动为齿轮坯的啮合转动.( )4主运动.进给运动和切削深度合称为切削量的三要素.( )5进给量越大,则切削厚度越大.( )6工件转速越高,则进给量越大( )7刀具切削部分最前面的端面称为前刀面( )8主偏角即主刀刃偏离刀具中心线的角度.( )9前角即前面与基面间的夹角,在切削平面内测量.( )10刀尖在刀刃的最高位置时,刃倾角为正.( )四名词解释:1切削运动-----2切削用量-----3切削厚度-----4基面------5前角-----五计算题某外圆车削工序,切削前工件直径为80mm,要求切削后工件直径为78 mm,一次切除余量,假定工件转速为300 r/min,刀具进给速度为60mm/min,试求切削用量三要素及切削面积.刀具材料基本训练1选择题:四个选项中只有一个是正确的.将正确选项前的字母填在题后括号内。
机械加工与装配作业指导书

机械加工与装配作业指导书第1章机械加工基础知识 (4)1.1 金属切削原理 (4)1.1.1 金属切削概述 (4)1.1.2 切削用量 (4)1.1.3 切削力 (4)1.1.4 刀具材料与结构 (4)1.2 机械加工工艺规程 (4)1.2.1 工艺规程概述 (4)1.2.2 工艺路线的制定 (5)1.2.3 工序内容的制定 (5)1.2.4 切削参数的确定 (5)1.3 机械加工精度与表面质量 (5)1.3.1 机械加工精度 (5)1.3.2 表面质量 (5)1.3.3 提高加工精度和表面质量的方法 (5)1.3.4 加工误差及其控制 (5)第2章常用机械加工方法 (5)2.1 车削加工 (5)2.2 铣削加工 (5)2.3 钻削加工 (6)2.4 镗削加工 (6)第3章数控加工技术 (6)3.1 数控编程基础 (6)3.1.1 数控编程基本概念 (6)3.1.2 编程语言 (6)3.1.3 编程步骤 (6)3.2 数控车削加工 (6)3.2.1 基本原理 (7)3.2.2 工艺参数 (7)3.2.3 编程方法 (7)3.3 数控铣削加工 (7)3.3.1 基本原理 (7)3.3.2 工艺参数 (7)3.3.3 编程方法 (7)第4章特种加工技术 (7)4.1 电火花加工 (7)4.1.1 概述 (7)4.1.2 电火花加工设备 (7)4.1.3 电火花加工工艺 (8)4.1.4 电火花加工应用 (8)4.2 激光加工 (8)4.2.2 激光加工设备 (8)4.2.3 激光加工工艺 (8)4.2.4 激光加工应用 (8)4.3 电子束加工 (8)4.3.1 概述 (8)4.3.2 电子束加工设备 (8)4.3.3 电子束加工工艺 (9)4.3.4 电子束加工应用 (9)第5章零件加工工艺分析 (9)5.1 零件结构工艺性分析 (9)5.1.1 零件结构特点 (9)5.1.2 零件材料 (9)5.1.3 零件加工难度及质量要求 (9)5.2 零件加工工艺路线设计 (9)5.2.1 工艺流程规划 (9)5.2.2 工艺参数设定 (10)5.3 工艺参数选择与计算 (10)5.3.1 切削速度 (10)5.3.2 进给量 (10)5.3.3 切削深度 (10)5.3.4 磨削用量 (10)第6章机械装配基础知识 (11)6.1 装配精度与工艺 (11)6.1.1 装配精度的定义与分类 (11)6.1.2 影响应装配精度的因素 (11)6.1.3 提高装配精度的措施 (11)6.2 装配方法与工具 (11)6.2.1 装配方法的分类与选用 (11)6.2.2 常用装配工具及设备 (12)6.3 装配前的准备工作 (12)6.3.1 零部件检查 (12)6.3.2 装配前的准备工作 (12)6.3.3 装配前的技术准备 (12)第7章常见机械装配工艺 (12)7.1 螺纹连接装配 (12)7.1.1 螺纹连接概述 (12)7.1.2 螺纹连接装配工艺 (13)7.2 键、销连接装配 (13)7.2.1 键、销连接概述 (13)7.2.2 键、销连接装配工艺 (13)7.3 过盈连接装配 (13)7.3.1 过盈连接概述 (13)7.3.2 过盈连接装配工艺 (13)7.4.1 滚动轴承概述 (14)7.4.2 滚动轴承装配工艺 (14)第8章装配质量控制与检验 (14)8.1 装配质量控制措施 (14)8.1.1 建立完善的质量管理体系,保证装配过程遵循相关标准和规范。
金属切削原理课件习题

• •
• •
• • • •
1.7 什么是刀具的工作角度?确定刀具工作角度的参考系中工作基面与 工作切削平面是如何定义的?它们与刀具标注角度参考系中的基面和切 削平面的定义有什么不同? (提示:刀具的工作角度:在刀具工作角度的参考系中所确定的角度。 工作基面:过切削刃上选定点,垂直于合成切削运动方向的平面。工作 切削平面:过切削刃上选定点,与切削刃S相切并垂直于工作基面的平 面。) 1.8 试以外圆车削为例,分析刀刃上选定点安装高低对工作角度的影响。 (提示:刀刃上选定点安装高低最直接影响到工作切深前角和工作切深 后角的变化,可根据刀刃上选定点高于或低于工件中心线的数值求得和, 欲求出工作主剖面中工作前角和工作后角,需根据主剖面与切深剖面内 的角度换算公式,具体计算请参阅其他文献资料。) 1.10 什么是切削层?什么是切削层参数? (提示:切削层:由一个刀齿正在切削着的金属层。切削层参数:切削 层的截面尺寸称为切削层参数,通常在垂直于主运动方向的基面内测 量。) 1.11.什么是直角自由切削? (提示:只有直线形主切削刃参加切削工作,而副切削刃不参加切削工 作,而且切削刃垂直于合成切削运动方向的切削方式称为直角自由切削变形区的划分和金属切削变形的本质是什么? 2、影响切削变形的主要因素是什么?
3、切塑性材料时切屑有哪几种类型?切屑类型可以转化吗? 控制屑型对切削过程有什么好处?
4、何谓积屑瘤?试分析积屑瘤形成的原因及对切削加工的 影响?并简述减小或消除积屑瘤的措施。 四、切削力 1、切削力产生?
十二、拉刀
1、拉削有什么特点? 2、何谓拉削方式?以方孔加工为例分析各种拉削方式的优缺 点。
2、影响表面粗糙度的主要因素有哪些?
3、加工硬化?残余应力? 4、工件材料的哪些性能对切削温度的影响最大?为什么?
金属切削原理课后习题答案

金属切削原理课后习题答案【篇一:金属切削原理与刀具(第四版)习题册答案】 class=txt>中国劳动社会保障出版社目录第一章金属切削加工的基本知识 (1)第一节切削运动 (1)第二节切削要素 (1)第二章金属切削刀具的基本知识 (3)第一节刀具材料 (3)第二节切削刀具的分类及结构 (4)第三节刀具的几何角度 (4)第四节刀具的工作角度 (6)第三章切削加工的主要规律 (7)第一节切削变形 (7)第二节切屑的类型与控制 (7)第三节积屑瘤 ....................................................................................................... .. 9第四节切削力与切削功率 (10)第五节切削热和切削温度 (12)第六节刀具磨损与刀具耐用度 (12)第四章切削加工质量与效率 (14)第一节工件材料的切削加工性 (14)第二节已加工表面质量 (14)第三节切削用量的选择 (15)第四节切削液 (16)第五章车刀........................................................................................................ (18)第一节焊接式车刀 (18)第二节可转位车刀 (18)第三节成形车刀 (20)第六章孔加工刀具 (21)第一节麻花钻 (21)第二节深孔钻 (22)第三节铰刀 ....................................................................................................... . (23)第四节镗刀 ....................................................................................................... . (24)第五节其他孔加工刀具 (24)第七章铣刀........................................................................................................ (26)第一节铣刀的种类及用途 (26)第二节铣刀的几何参数及铣削要素 (27)第三节铣削方式 (28)第八章拉刀........................................................................................................ (30)第一节拉刀的种类 (30)第二节拉刀的结构组成及主要参数 (30)第三节拉削方式 (31)第四节拉刀的使用与刃磨 (32)第九章螺纹刀具 (34)第一节螺纹车刀 (34)第二节丝锥和板牙 (35)第三节螺纹铣刀 (35)第四节塑性变形法加工螺纹 (35)第十章齿轮加工刀具 (37)第一节齿轮刀具的种类 (37)第二节齿轮滚刀 (37)第三节蜗轮滚刀 (38)第四节插齿刀 (39)第五节剃齿刀 (40)第十一章数控机床用刀具 (41)第一节数控车床用刀具 (41)第二节数控铣床用刀具 (42)第三节数控加工中心用刀具 (43)第一章金属切削加工的基本知识第一节切削运动一、填空题1.刀具、工件、主、进给2.待加工、已加工、过渡二、判断题三、选择题*1.b *2.c 3.a *4.a *5.a *6.b *7.a四、简答题写出下表中各种切削加工方法具备的主运动。
金属切削原理

[445927570]2010金属切削原理与刀具A试卷[试卷信息]总分值:100分考点数:26个大题数:4个小题数:26个题号[考点]:4[2]6[3]127[4]12[5]13[6]14[7]17[9]19[10]23[12]32[17]35[19]52[32]56[35]58[37]60[39]63[42]66[52]69 [54]74[62]75[63]82[74]83[75]85[77]87[79]92[84]109[128]一、填空题(共12题,共33分)1、刀具由[ ]部分和[ ]部分组成。
2、由于刀具几何形状和切削运动形成的粗糙度称为[ ]粗糙度。
3、车刀标注参考系的假定条件是进给运动只考虑[ ],不考虑大小(即不考虑合成切削运动)、刀刃上选定点与[ ]等高刀杆与工件轴线[ ]。
4、刀具磨损的原因有[ ]磨损、[ ]磨损、[ ]磨损、[ ]磨损、[ ]磨损。
其中[ ]磨损通过[ ]磨损表现出来,[ ]磨损会促进[ ]磨损。
5、切断时,切削刃低于工件中心会导致,工作前角变[ ],工作后角变[ ]。
6、已加工表面的加工硬化可以用[ ]程度或[ ]深度来衡量。
7、根据材料的[ ]可将材料的切削加工性分为8级。
8、刀具磨损的过程分为[ ]阶段、[ ]阶段、[ ]阶段。
9、砂轮的破碎磨损分为[ ]破碎和[ ]破碎,在初期磨损阶段主要是[ ]破碎磨损,二期磨损阶段主要是磨耗磨损,三期磨损阶段主要是[ ]破碎磨损。
10、残余应力产生的原因有塑性变形引起的[ ]应力,切削温度引起的[ ]应力,金相改变引起的[ ]应力。
11、切削温度的高低取决于[ ]热量和[ ]热量的平衡。
12、内摩擦的实质是[ ]。
二、简答题(共6题,共30分)1、简述积屑瘤的利弊及其对粗精加工的影响。
2、简述切削热的传散途径及其对加工的影响。
3、简述主运动和进给运动的特征。
4、简述切屑的类型及其切削特征。
5、简述实现切削加工必备的三个条件。
金属切削原理与刀具 大作业

《金属切削原理与刀具》设计报告 2019 — 2020 学年第 1 学期专业机械工程班级机械工程171班学号 Z07117125姓名严旭指导教师徐正亚机械工程学院碳纤维复合材料制孔相关问题研究摘要:碳纤维复合材料具有高的比强度、比模量、耐化学腐蚀性能,广泛的应用于航空航天等各领域,碳纤维复合材料在制孔过程中容易出现各种加工缺陷,影响制孔质量。
本文主要简要简述了碳纤维复合材料,钻孔刀具的发展现状及趋势,介绍分析了碳纤维复合材料制孔的要求、制孔刀具的结构特点及刀具磨损特征及原因。
关键词:碳纤维复合材料制孔刀具刀具磨损一、碳纤维复合材料介绍碳纤维复合材料(CFRP)作为一种先进的复合材料,具有重量轻、模量高、比强度大、热膨胀系数低、耐高温、耐热冲击、耐腐蚀、吸振性好等一系列优点,在航空航天、汽车、战略性武器(导弹等)等领域已有广泛的应用。
例如火箭发动机尾喷管、喉衬,航天飞机的机翼前缘、刹车盘等均可采用碳纤维复合材料。
碳纤维复合材料根据碳纤维的力学性能可分为高模量,超高模量,高强度和超高强度4种,常用的有碳纤维增强复合材料(CFRP)、碳纤维增强陶瓷基复合材料、碳/碳复合材料、碳纤维增强金属基复合材料、碳纤维增强树脂复合材料等。
碳纤维是一种高强度、高模量材料,理论上大多数有机纤维都可被制成碳纤维,实际用作碳纤维原料的有机纤维主要有三种:粘胶纤维、沥青纤维、聚丙烯腈纤维。
当前固体火箭发动机结构件用的碳纤维大多由聚丙烯腈纤维制成“J。
碳纤维的开发始于二十世纪六十年代,起初用于耐烧蚀喉衬、扩张段材料,后来逐渐在其它结构件上应用。
自八十年代以来,碳纤维发展较大:①性能不断提高。
七、八十年代主要以3000MPa的碳纤维为主,九十年代初普遍使用的IM7、IM8纤维强度达到5300MPa,九十年代末T1000纤维强度达到7000MPa,并已开始工程应用。
②品种不断增多。
以H本东丽公司为例,1983年生产的碳纤维品种只有4种,到1995年碳纤维品种达21种之多。
金属切削原理PPT课件
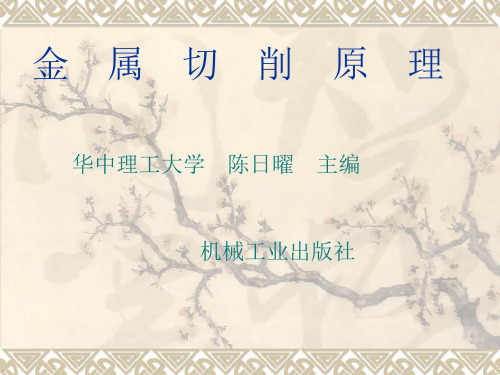
3. 背吃刀量 对外圆车削(图1-1) 和平面刨削(图1-2)而言,背吃刀量等于已 加工表面与待加工表面间的垂直距离;其中外圆 车削的背吃刀量:
总之,任何切削加工方法都必须有一个主运 动,可以有一个或几个进给运动。主运动和进给 运动可以由工件或刀具分别完成,也可以由刀具 单独完成(例如在钻床上钻孔或铰孔)。
二 工件上的加工表面
在切削过程中,通常工件上存在三个表面, 以图1-1的外圆车削和图1-2的平面刨削为 例,它们是:
1.待加工表面 它是工件上即将被切去的
三 切削用量
所谓切削用量是指切削速度,进给量和背吃 刀量三者的总称。它们分别定义如下:
1. 切削速度v 它是切削加工时,刀刃上选
定点相对于工件的主运动的速度.刀刃上各点的 切削速度可能是不同的。
当主运动为旋转运动时,刀具或工件最大直 径处的切削速度由下式确定:
式中 d——完成主运动的刀具或工件的最大直径 (mm);
(一)刀具在正交平面参考系中的标注角度
刀具标注角度的内容包括两个方面:一是确
定刀具上刀刃位置的角度;二是确定前刀面与后 面位置的角度。以外圆车刀为例(图1-9), 确定车刀主切削刃位置的角度有二:
主偏角 它是在基面上,主切切削忍与 基面的夹角。当刀尖在主切削刃上为最低的点时, 为负值;反之,当刀尖在主切削刃上为最高的点 时, 为正值。必须指出,这个规定是根据IS O标注,同过去某些书上关于正负号的规定恰好 相反。
实际上,除了由上述切削平面和基面组成的 参考平面系以外,还应该有一个平面作为标注和 测量刀具前,后刀面角度用的 “测量平面”。通 常根据刃磨和测量的需要与方便,可以选用不同 的平面作为测量平面。在刀刃上同一选定点测量 其角度时,如果测量平面选得不同,刀具角度的 大小也就不同。
金属切削原理
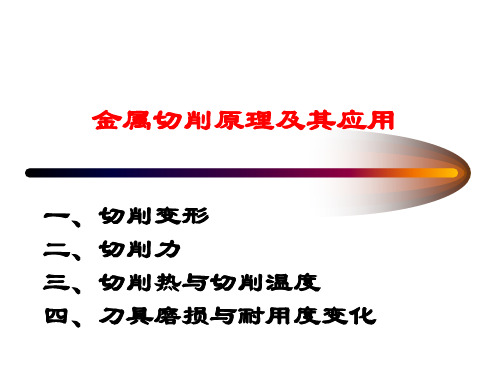
切削时消耗的功率
金属切削原理及其应用
一、切削变形 二、切削力 三、切削热与切削温度 四、刀具磨损与耐用度变化
1.1 金属切削过程的基本规律
一、切削变形 变形Ⅰ,Ⅱ,Ⅲ区, 剪切面间距0.02-0.2mm。
1. 切屑的形成
图为金属切削过程中的滑移线
1.1 金属切削过程的基本规律.
• (1)第一变形区 从OA线开始发生塑性变形,到 OM线金属晶粒的剪切滑移基本完成。OA线和OM 线之间的区域(图中Ⅰ区)称为第一变形区。
碳素钢,合金钢,铜 铝合金; 黄铜,低速切削钢; 铝; 铸鉄,黄铜
图为切屑类型
2. 积屑瘤
图为积屑瘤与切削刃的金 相显微照片
2. 积屑瘤
积屑瘤高度及其实际工作前角
2. 积屑瘤
(1)积屑瘤对切削过程的影响: 1) 积屑瘤包围着切削刃,可以代替前面、后面和切
削刃进行切削,从而保护了刀刃,减少了刀具的磨 损。 2) 积屑瘤使刀具的实际工作前角增大,而且,积屑 瘤越高,实际工作前角越大,刀具越锋利。 3) 积屑瘤前端伸出切削刃外,直接影响加工尺寸精 度。 4) 积屑瘤直接影响工件加工表面的形状精度和表面 粗糙度。
Fx Fxy sin r
3. 影响切削力的因素
3)刀具几何参数对切削力的影响。
c)刃倾角ls 对切削力的影响; ls↑ 背前角gp↑ 侧前角gf↓
Fp↓ Ff↑
3. 影响切削力的因素
3)刀具几何参数对切削力的影响。
d)刀尖圆弧半径r 对切削力的影响;
3. 影响切削力的因素
3)刀具几何参数对切削力的影响。 e)使用切削液 对切削力的影响;
v a 273
f 0.26 0.07
c
0.01
《金属切削原理》课件
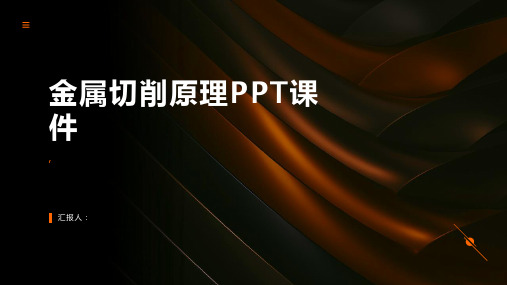
金属切削在机械制造中的应用
加工精度:金属切削可以精确地加工出各种形状和尺寸的零件 加工效率:金属切削可以提高生产效率,缩短生产周期 加工范围:金属切削可以加工各种金属材料,包括钢、铝、铜等 加工质量:金属切削可以保证加工质量,提高产品的可靠性和耐用性
金属切削在航空航天领域的应用
飞机制造:金属 切削用于制造飞 机机身、机翼、 发动机等部件
新材料硬度 高,耐磨性 好,对刀具 寿命和加工 效率产生影 响
新材料热导 率低,切削 过程中热量 难以散发, 对刀具和工 件产生影响
新材料化学 活性强,易 与刀具材料 发生化学反 应,影响刀 具寿命和加 工质量
新材料加工 难度大,对 刀具材料和 加工工艺提 出更高要求
新材料加工 过程中产生 的废料处理 问题,对环 保和资源利 用提出挑战
切削热的ห้องสมุดไป่ตู้生与散失
切削热的产生:刀具与工件之间的摩擦和剪切作用 切削热的散失:通过刀具、工件和切屑的传导、对流和辐射等方式 切削热的影响:影响刀具寿命、工件加工精度和表面质量 切削热的控制:通过优化刀具材料、切削参数和冷却方式等手段
切削表面的形成与变化
切削过程:刀具与工件之间的相对运动 切削力:刀具与工件之间的相互作用力 切削温度:刀具与工件之间的摩擦热 切削表面:刀具与工件之间的接触面
火箭制造:金属 切削用于制造火 箭发动机、燃料 箱、控制系统等 部件
卫星制造:金属 切削用于制造卫 星外壳、太阳能 电池板、天线等 部件
空间站制造:金 属切削用于制造 空间站外壳、太 阳能电池板、生 命支持系统等部 件
金属切削在汽车工业领域的应用
汽车零部件制造:金属切削用于生产汽车发动机、变速箱、底盘等零部件 汽车车身制造:金属切削用于生产汽车车身、车门、车窗等车身部件 汽车模具制造:金属切削用于生产汽车模具,如冲压模具、注塑模具等 汽车维修与保养:金属切削用于汽车维修与保养,如更换损坏的零部件、修复车身损伤等
金属切削原理 (陈日瞿)提纲
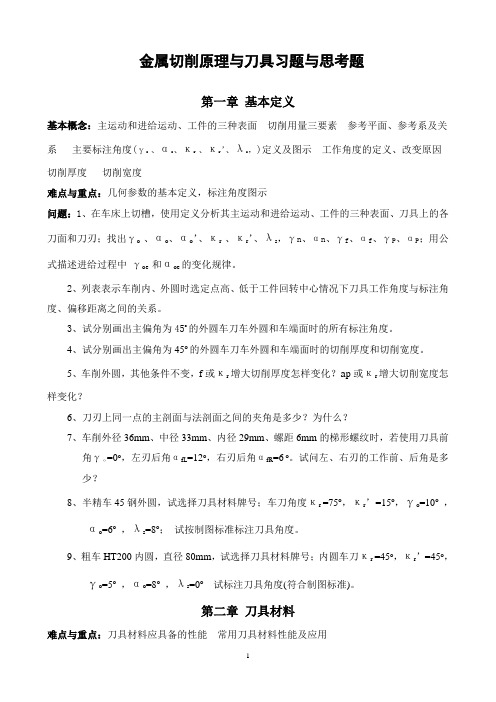
金属切削原理与刀具习题与思考题第一章基本定义基本概念:主运动和进给运动、工件的三种表面切削用量三要素参考平面、参考系及关系主要标注角度(γo 、αo、κr 、κr’、λs,)定义及图示工作角度的定义、改变原因切削厚度切削宽度难点与重点:几何参数的基本定义,标注角度图示问题:1、在车床上切槽,使用定义分析其主运动和进给运动、工件的三种表面、刀具上的各刀面和刀刃;找出γo 、αo、αo’、κr 、κr’、λs,γn、αn、γf、αf、γP、αP;用公式描述进给过程中γoe 和αoe的变化规律。
2、列表表示车削内、外圆时选定点高、低于工件回转中心情况下刀具工作角度与标注角度、偏移距离之间的关系。
3、试分别画出主偏角为45o的外圆车刀车外圆和车端面时的所有标注角度。
4、试分别画出主偏角为45o的外圆车刀车外圆和车端面时的切削厚度和切削宽度。
5、车削外圆,其他条件不变,f或κr增大切削厚度怎样变化?a p或κr增大切削宽度怎样变化?6、刀刃上同一点的主剖面与法剖面之间的夹角是多少?为什么?7、车削外径36mm、中径33mm、内径29mm、螺距6mm的梯形螺纹时,若使用刀具前角γο=0o,左刃后角αfL=12o,右刃后角αfR=6 o。
试问左、右刃的工作前、后角是多少?8、半精车45钢外圆,试选择刀具材料牌号;车刀角度κr =75o,κr’=15o,γo=10o,αo=6o,λs=8o;试按制图标准标注刀具角度。
9、粗车HT200内圆,直径80mm,试选择刀具材料牌号;内圆车刀κr =45o,κr’=45o,γo=5o,αo=8o,λs=0o试标注刀具角度(符合制图标准)。
第二章刀具材料难点与重点:刀具材料应具备的性能常用刀具材料性能及应用问题:1、刀具材料是在什么条件下工作的?应具备哪些性能?2、对比高速钢和硬质合金性能指标。
3、常用高速钢有哪些型号?用在哪些场合?列举5种高速钢刀具。
4、常用硬质合金有哪几类?各有哪些常用牌号?其性能特点如何?加工钢料和加工铸铁、粗加工和精加工应如何选择硬质合金?为什么?5、简述YT 、YG两类硬质合金的牌号及应用范围;6、解释YT15 、YT30 、YG6、YG3牌号的含义。
金属切削原理PPT全套课件

实际上,除了由上述切削平面和基面组成的 参考平面系以外,还应该有一个平面作为标注和 测量刀具前,后刀面角度用的 “测量平面”。通 常根据刃磨和测量的需要与方便,可以选用不同 的平面作为测量平面。在刀刃上同一选定点测量 其角度时,如果测量平面选得不同,刀具角度的 大小也就不同。
测量平面和参考平面系就组成了所谓的刀具 标注角度参考系。目前各个国家由于选用的测量 平面不同,所以采用的刀具标注角度参考系也不 完全同意。现在以常用的外圆车刀为例,来说明 几种不同的刀具标注角度参考系。
三 切削用量
所谓切削用量是指切削速度,进给量和背吃 刀量三者的总称。它们分别定义如下:
1. 切削速度v 它是切削加工时,刀刃上选
定点相对于工件的主运动的速度.刀刃上各点的 切削速度可能是不同的。
当主运动为旋转运动时,刀具或工件最大直 径处的切削速度由下式确定:
式中 d——完成主运动的刀具或工件的最大直径 (mm);
度参考平面的切削平面和基面定义如下:
1. 切削平面是通过刀刃上选定点,切于工 件过渡表面的平面。在切削平面内包含有刀刃在 该定点的切线,和由主运动与进给运动合成的切 削运动向量(简称合成切削运动向量)。
2. 基面是通过刀刃上选定点,垂直于该点 合成切削运动向量的平面。显然,刀刃上同一点 的基面和切削平面是相互垂直的。
在基本技能方面,应具有根据加工条件合理 选择刀具材料,刀具几何参数的能力;应具有根 据加工条件,和用资料,手册及公式,计算切削 力和切削功率的能力;应具有根据加工条件,从 最大生产率或最低加工成本出发,合理选择切削
用量的能力;应初步具有利用常用仪器设备进行 切削变形,切削力,切削温度,刀具磨损和砂轮 磨损等测试的技能,并具有对实验数据进行处理 和分析的能力。
金属切削原理

金属切削原理1. 引言金属切削是一种常见的金属加工方法,广泛应用于制造业领域。
本文将深入探讨金属切削原理,包括切削过程的基本概念、切削力的产生机制、刀具和工件的相互作用以及切削力的影响因素等内容。
2. 切削过程的基本概念2.1 切削的定义切削是指通过刀具对工件进行切削行为,将工件的某部分削除或形成所需形状的加工过程。
2.2 切削的分类根据切削速度和切削温度的不同,切削可以分为常规切削和高速切削两种。
常规切削适用于低切削速度和温度的条件下,而高速切削则适用于高速和高温的情况。
2.3 切削力的定义切削力是指刀具在切削过程中对工件施加的力,通常包括主切削力、侧切削力和切削力矩等。
3. 切削力的产生机制切削力的产生是由刀具与工件之间的相互作用所引起的。
在切削过程中,刀具对工件施加的切削力可以分解为切削力和切削阻力两个方向。
4. 刀具和工件的相互作用刀具和工件之间的相互作用对切削过程的效果具有重要影响。
刀具的选择应根据工件的材料和几何形状来确定,不同的刀具结构和刀具材料将产生不同的切削效果。
5. 切削力的影响因素切削力的大小受多种因素的影响,包括刀具、切削条件、工件材料和几何形状等。
了解这些影响因素将有助于优化切削过程,提高加工效率和质量。
5.1 刀具的影响因素•刀具材料和硬度•刀具尺寸和几何形状•刀具刃口的磨损情况5.2 切削条件的影响因素•切削速度•进给量•切削深度5.3 工件材料的影响因素•材料的硬度和强度•材料的塑性和韧性5.4 工件几何形状的影响因素•工件的形状复杂程度•工件表面的光滑度6. 切削过程的优化与发展趋势为了提高切削过程的效率和质量,不断进行切削过程的优化是非常重要的。
随着技术的发展,一些新的切削方法和工具逐渐被引入,例如高速切削、超硬刀具和涂层刀具等。
结论金属切削原理是金属加工的核心内容之一,通过对切削过程的研究和了解,可以有效提高切削过程的效率和质量。
切削过程涉及多个因素,包括刀具和工件的相互作用、切削力的产生机制以及切削力的影响因素等。
金属切削原理 6第六章 刀具磨损、破损和刀具耐用度

金属切削原理与刀具Principle of Metal Cutting and Cutting Tools 第六章刀具磨损、破损和刀具耐用度第六章刀具磨损、破损和刀具耐用度6.1 刀具磨损的形态6.2 刀具磨损的原因6.3 刀具磨损过程及磨钝标准6.4 刀具耐用度的经验公式及刀具耐用度的分布6.5 合理耐用度的选用原则6.6 刀具的破损磨损:切削时的摩擦使得刀具材料逐渐磨钝,造成切削部分形状和尺寸改变切削力增加;切削温度上升;切削颜色改变;产生振动;工件尺寸超差;已加工表面质量明显恶化刀具损坏形式主要有:磨损和破损。
磨损损坏是连续的逐渐磨损;破损包括脆性破损和塑性破损刀片磨损车削用金属陶瓷刀片刀尖半径处后刀面磨损和月牙洼磨损第六章刀具磨损、破损和刀具耐用度6.1 刀具磨损的形态一、前刀面磨损切削塑性材料时,如果切削速度和切削厚度较大,在刀具前刀面上经常会磨出一个月牙洼。
前刀面月牙洼磨损值以其最大深度KT表示。
图6-1 刀具的磨损形态二、后刀面磨损加工脆性材料或在切削速度较低、切削厚度较小(<0.1mm)的塑性材料,前刀面上刀屑间的作用相对较弱,主要发生后刀面磨损,后刀面磨损带往往不均匀。
刀尖处VC,主切削刃靠近工件外皮处的后刀面VN,中间部位磨损较均匀VB、VBmax。
图6-3 刀具磨损的测量位置三、边界磨损切削钢料时,常在主切削刃靠近工件外皮处以及刀尖处的后刀面上,磨出较深的沟纹,这就是边界磨损(图6-4)。
加工铸、锻等外皮粗糙的工件,也容易发生边界磨损。
发生边界磨损的原因:(1)应力梯度,引起很大的剪应力。
(2)加工硬化作用,边界处切削厚度为零,刀刃打滑。
刀具的磨损方式1.前刀面为主,后刀面轻微的磨损2.后刀面为主,前刀面轻微的磨损3.前刀面、后刀面同时磨损4.切削刃口变圆钝化1. 前刀面为主,后刀面轻微的磨损•切削塑性材料;•切削速度较高;•切削厚度较大;•负前角;•产生积屑瘤时2. 后刀面为主,前刀面轻微的磨损•切削脆性材料;•塑性材料切削速度较低;•塑性材料切削厚度较小;•增大前角,减小后角时更明显;•切削韧性大、导热性差的材料(不锈钢)3. 前刀面、后刀面同时磨损•切削塑性金属时,如果切削厚度适中4. 切削刃口变圆钝化•耐磨性、红硬性好的刀具精加工导热性差的材料;•切削韧性大、导热性差的材料第六章刀具磨损、破损和刀具耐用度5.2 刀具磨损的原因一、硬质点磨损(磨料磨损)二、粘结磨损三、扩散磨损四、氧化磨损一、硬质点磨损(磨料磨损)1. 概念工件材料中含有硬度极高的硬质点在刀具表面刻划出沟纹(机械磨损)。
第6章金属切削原理作业

第6章金属切削原理作业•相关推荐第6章金属切削原理作业第六章金属切削原理作业1.切削加工由哪些运动组成?它们各有什么作用?答:切削加工由主运动和进给运动组成。
主运动是直接切除工件上的切屑层,使之转变为切屑,从而形成工件新包表面。
进给运动是不断的把切削层投入切削,以逐渐切出整个工件表面的运动。
2.切削用量三要素是什么?答:切削用量三要素的切削速度,进给量,和背吃刀量。
3.刀具正交平面参考系由哪些平面组成?它们是如何定义的?答:刀具正交平面参考系由正交平面Po,基面Pr,切削平面Ps组成;正交平面是通过切削刃上选定点,且与该点的基面和切削平面同时垂直的平面;基面是通过切削刃上选定点,且与该点的切削速度方向垂直的平面;切削平面是通过切削刃上选定点,且与切削刃相切并垂直与基面的平面。
4.刀具的工作角度和标注角度有什么区别?影响刀具工作角度的主要因素有哪些?答:刀具的标注角度是刀具设计图上需要标注的刀具角度,它用于刀具的制造、刃磨和测量;而刀具的工作角度是指在切削过程中,刀具受安装位置和进给运动的影响后形成的刀具角度。
影响刀具工作角度的主要因素有:横向和纵向进给量增大时,都会使工作前角增大,工作后角减小;外圆刀具安装高于中心线时,工作前角增大,工作后角减小;刀杆中心线与进给量方向不垂直时,工作的主副偏角将增大或减小。
5.什么是积屑瘤?试述其成因、影响和避免方式。
答:积屑瘤在以低速加工塑性金属材料时,在刀具前面靠近切削刃处粘着一小块剖面呈三角形的硬块(硬度通常是工件材料的2~3倍),叫着积屑瘤。
切削时,由于粘结作用,使得切屑底层与切屑分离并粘结在刀具前面上,随着切屑连续流出,切屑底层依次层层堆积,使积屑瘤不断长大。
积屑瘤稳定时可以保护切削刃,代替切削,但由于积屑瘤形状不稳定,对精加工不利,且其破裂可能加剧刀具的磨损。
避免方式:加切削液;不在中速区进行切削;增大刀具前角等。
6.金属切削层的三个变形区各有什么特点?答:第一变形区的特征是沿滑移面的剪切变形,以及随之而来的加工硬化;第二变形区的特征是切屑与刀具之间的强烈的挤压和磨擦所引起的切屑层金属的剧烈变形和切屑与刀具界面温度的升高,形成积屑瘤;第三变形区是在已加工表面形成过程中受到挤压、磨擦使表面层金属产生变形,并伴随切削热的作用。
金属切削原理习题[1].doc
![金属切削原理习题[1].doc](https://img.taocdn.com/s3/m/43977149cf84b9d528ea7a97.png)
金属切削原理习题与思考题第一章 基本定义一、基本概念主运动和进给运动 切削用量三要素工件的三种表面 刀具角度参考系的种类及组成刀具主要角度(前角、后角、主偏角、副偏角、刃倾角)定义及图示刀具工作角度的定义、改变原因和改变值刀具标注角度的换算切削层参数 金属切除率二、思考题和习题1.1 试用本章阐述的基本定义,分析在钻床上用麻花钻钻孔时的主运动、进给运动、工件上的加工表面和麻花钻的各刀面与刀刃。
1.2 例举外圆车刀在不同参考系中的主要标注角度及其定义。
1.3 写出切削用量三要素的单位和计算方法。
1.4 试分别画出主偏角为45o 和90o 的外圆车刀的所有标注角度。
1.5 试分别画出主偏角为45o 的外圆车刀车外圆和车端面时的所有标注角度和切削厚度和切削宽度。
1.6 刀刃上同一点的主剖面与法剖面之间的夹角是多少?1.7 车削外径36mm 、中径33mm 、内径29mm 、螺距6mm 的梯形螺纹时,若使用刀具前角 0=o γ,左刃后角 12=oL α,右刃后角 6=oR α。
试问左、右刃的工作前、后角是多少?1.8 端面车削时,刀尖高(或低)于工件中心时工作角度(前、后角)有何变化?1.9 试述刀具的标注角度与工作角度的区别。
为什么横向切削时进给量不能过大?1.10 车削外径36mm 的外圆,刀尖上一点低于工件中心0.8mm ,该点的工作前角相对于标注前角改变了多少?增大还是减小?1.11 切削层参数指的是什么?与背吃刀量、进给量和刀具角度有何关系?第二章 刀具材料思考题和习题2.1 刀具在什么条件下工作?刀具材料必须备哪些性能?为什么?2.2 高速钢、硬质合金、陶瓷金刚石立方氮牌号化硼各有何性能特点?适用于哪些场合?2.3 常用高速钢有哪些牌号?其化学成分及性能特点如何?提高高速钢的切削性能有哪些途径?2.4 常用的硬质合金有哪几类?各有哪些常用牌号?其性能特点如何?2.5 粗、精加工加工钢料和铸铁应如何选用硬质合金?为什么?2.6 按下列条件选用刀具材料的种类或牌号:a.粗车45钢锻件;b.精车HT200铸件;c.低速精车合金钢蜗杆;d.高速精车调质钢长轴;e.高速精密镗削铝合金缸套;f.中速车削淬硬钢轴;g.加工65HRC 冷硬铸铁第三章金属切削的变形过程一、基本概念切削过程的三个变形区剪切角变形系数相对滑移前刀面上的挤压、摩擦及其对切屑变形的影响积屑瘤切屑的类型及变化规律切屑的卷曲与折断二、问题1、切削变形程度及其衡量指标;2、切削变形的影响因素;3、切屑种类及其形成条件;4、切屑与前刀面的摩擦特性;5、积屑瘤的成因及对切削的影响;三、习题3.1 研究金属切削变形机理对生产有何意义?3.2 研究金属切削变形的方法有哪些?3.3 衡量切削变形的指标有哪些?你认为哪个更合理些?3.4 变形系数、剪应变和剪切角的定义?3.5 影响切削变形的因素有哪些?它们是如何影响的?3.6 剪切角只与刀具前角有关系吗?为什么?3.7 车削45钢可能形成哪几种切屑?改变哪几种条件可以使切屑形态转化?3.8 分析积屑瘤产生的条件、对加工质量的影响和控制措施。
- 1、下载文档前请自行甄别文档内容的完整性,平台不提供额外的编辑、内容补充、找答案等附加服务。
- 2、"仅部分预览"的文档,不可在线预览部分如存在完整性等问题,可反馈申请退款(可完整预览的文档不适用该条件!)。
- 3、如文档侵犯您的权益,请联系客服反馈,我们会尽快为您处理(人工客服工作时间:9:00-18:30)。
第六章金属切削原理作业
1.切削加工由哪些运动组成?它们各有什么作用?
答:切削加工由主运动和进给运动组成。
主运动是直接切除工件上的切屑层,使之转变为切屑,从而形成工件新包表面。
进给运动是不断的把切削层投入切削,以逐渐切出整个工件表面的运动。
2.切削用量三要素是什么?
答:切削用量三要素的切削速度,进给量,和背吃刀量。
3.刀具正交平面参考系由哪些平面组成?它们是如何定义的?
答:刀具正交平面参考系由正交平面Po,基面Pr,切削平面Ps组成;正交平面是通过切削刃上选定点,且与该点的基面和切削平面同时垂直的平面;基面是通过切削刃上选定点,且与该点的切削速度方向垂直的平面;切削平面是通过切削刃上选定点,且与切削刃相切并垂直与基面的平面。
4.刀具的工作角度和标注角度有什么区别?影响刀具工作角度的主要因素有哪些?
答:刀具的标注角度是刀具设计图上需要标注的刀具角度,它用于刀具的制造、刃磨和测量;而刀具的工作角度是指在切削过程中,刀具受安装位置和进给运动的影响后形成的刀具角度。
影响刀具工作角度的主要因素有:横向和纵向进给量增大时,都会使工作前角增大,工作后角减小;外圆刀具安装高于中心线时,工作前角增大,工作后角减小;刀杆中心线与进给量方向不垂直时,工作的主副偏角将增大或减小。
5.什么是积屑瘤?试述其成因、影响和避免方式。
答:积屑瘤在以低速加工塑性金属材料时,在刀具前面靠近切削刃处粘着一小块剖面呈三角形的硬块(硬度通常是工件材料的2~3倍),叫着积屑瘤。
切削时,由于粘结作用,使得切屑底层与切屑分离并粘结在刀具前面上,随着切屑连续流出,切屑底层依次层层堆积,使积屑瘤不断长大。
积屑瘤稳定时可以保护切削刃,代替切削,但由于积屑瘤形状不稳定,对精加工不利,且其破裂可能加剧刀具的磨损。
避免方式:加切削液;不在中速区进行切削;增大刀具前角等。
6.金属切削层的三个变形区各有什么特点?
答:第一变形区的特征是沿滑移面的剪切变形,以及随之而来的加工硬化;第二变形区的特征是切屑与刀具之间的强烈的挤压和磨擦所引起的切屑层金属的剧烈变形和切屑与刀具界面温度的升高,形成积屑瘤;第三变形区是在已加工表面形成过程中受到挤压、磨擦使表面层金属产生变形,并伴随切削热的作用。
7.各切削力对加工过程有何影响?
答:主切削力Fc :是计算机床动力,校核刀具.夹具的强度和刚变的主要依据之一;轴向力Fc :是计算和校验机床进给系统的动力.强度和刚度的主要依据之一;径向力Fp:是用来计算与加工精度有关的工作扰度.刀具和机床零件的强度等。
8.切削热是如何产生的?它对切削过程有什么影响?
答:切削热主要来自切削区域的三个变形区,即切削层金属发生弹性和塑性变形产生的热;刀具前刀面与切削底部摩擦产生的热;刀具后刀面与工件已加工表面摩擦产生的热。
影响:大量的切削热使切削温度升高,切削温度能改变工件材料的性能;改变前刀面的摩擦系数和切削力的大小;影响刀具磨损和积屑瘤的形成与消退;也影响工件的加工精度和已加工表面质量等。
9.刀具磨损的形式有哪些?磨损的原因有哪些?
答:(1)形式:前刀面磨损,后刀面磨损,前刀面和后刀面同时磨损或边界磨损。
(2)原因:硬质点磨损-硬质点磨损是由于工件基体组织中的碳化物、氮化物、氧化物等硬质点及积屑瘤碎片在刀具表面的刻划作用而引起的机械磨损。
在各种切削速度下,刀具都存在硬质点磨损。
硬质点磨损是刀具低速切削时发生磨损的主要原因,因为其它形式的磨损还不显著。
粘结磨损-在高温高压作用下,切屑与前刀面、已加工表面与后刀面之间的磨擦面上,产生塑性变形,当接触面达到原子间距离时,会产生粘结现象。
硬质合金刀具在中速切削工件时主要发生粘结磨损。
扩散磨损-切削过程中,由于高温、高压的作用,刀具材料与工件材料中某些化学元素可能互相扩散,使两者的化学成分发生变化,削弱刀具材料的性能,
形成扩散磨损。
硬质合金中的Co、C、W等元素扩散到切屑中被带走,切屑中的铁也会扩散到硬质合金中,使刀面的硬度和强度降低,磨损加剧。
扩散磨损是硬质合金刀具在高速切削时磨损的主要原因之一。
化学磨损-在一定温度下,刀具材料与某些周围介质(如空气中的氧,切削液中的添加剂硫、氯等)发生化学反应,生成硬度较低的化合物而被切屑带走,或因刀具材料被某种介质腐蚀,造成刀具的磨损。
10.什么是刀具的磨钝标准?什么是刀具的耐用度?
答:刀具磨损到一定限度后就不能继续使用,这个磨损限度称为磨钝标准。
刀具耐用度是指刀具由刃磨后开始切削,一直到磨损量达到磨钝标准所经过的总切削时间。
11.何谓工件材料的切削加工性?它与哪些因素有关?
答:切削加工性是在一定条件下,某种材料切削加工的难易程度。
材料加工的难易,不仅取决于材料本身,还取决于具体的切削条件。
影响因素:(1)材料的强度和硬度。
工件材料的硬度和强度越高,切削力越大,消耗的功率也越大,切削温度刀就越高,刀具的磨损加剧,切削加工性就越差。
(2)材料的韧性。
韧性大的材料,在切削变形时吸收的能量较多,切削力和切削温度较高,并且不易断屑,故其切削加工性能差。
(3)材料的塑性。
材料的塑性越大,切削时的塑性变形就越大,刀具容易产生粘结磨损和扩散磨损;在中低速切削塑性较大的材料时容易产生积屑瘤,影响表面加工质量;塑性大的材料,切削时不易断屑,切削加工性较差。
(4)材料的导热率。
材料的导热系数越高,切削热越容易传出,越有利于降低切削区的温度,减小刀具的磨损,切削加工性也越好。
但温升易引起工件变形,且尺寸不易控制。
12.试对碳素结构钢中含碳量大小对切削加工性的影响进行分析。
答:高炭钢的硬度高,塑性低,导热性差,故切削力大,切削温度高,刀具耐用度低,切削加工性差。
中碳钢的切削加工性较好,但经热轧或冷轧,或经正火或调值后,其加工性也不相同,低碳钢硬度低,塑性和韧性高,故切削变形大,
切削温度高,断屑困难,易粘屑,不易得到小的表面粗糙值,切削加工性差。
13.说明前角和后角的大小对切削过程的影响。
答:增大前角可减小切削变形,切削热,降低切削功率的消耗还可以抑制积屑瘤和鳞刺的产生,提高加工质量。
增大前角,会使楔角减小,切削刃与刀头强度降低,易造成崩刃,还会使刀头的散热面积容热体积减小,使切削区局部温度上升,易造成刀具的磨损,刀具难用度下降。
增大后角可减小刀具后面与已加工表面间的摩擦,减小刀具磨损,还可使切削刃钝圆半径减小,提高刃口锋利程度,改善表面加工质量。
但后角过大,将削弱切削刃的强度,减小散热体积使散热条件恶化,降低刀具难用度。
14.说明刃倾角的作用。
答:影响切屑的流出方向;当λs=0°时,切屑沿主切削刃方向流出;当λ
s>0°时,切屑流向待加工表面;当λs<0°时,切屑流向已加工表面。
影响刀尖强度和散热条件;当λs<0°时,切削过程中远离刀尖的切削刃处先接触工件,刀尖可免受冲击,同时,切削面积在切入时由小到大,切出时由大到小逐渐变化,因而切削过程比较平稳,大大减小了刀具受到的冲击和崩刃的现象。
影响切削刃的锋利程度。
当刃倾角的绝对值增大时,可使刀具的实际前角增大,刃口实际钝圆半径减小,增大切削刃的锋利性。
15.切削液的主要作用是什么?
答:(1)冷却作用。
切削液能从切削区域带走大量切削热,使切削温度降低。
其中冷却性能取决于它的导热系数、比热、汽化热、汽化速度、流量和流速等。
(2)润滑作用。
切削液能渗入到刀具与切屑、加工表面之间形成润滑膜或化学吸附膜,减小摩擦。
其润滑性能取决于切削液的渗透能力、形成润滑膜的能力和强度。
(3)清洗作用。
切削液可以冲走切削区域和机床上的细碎切屑和脱落的磨粒,防止划伤已加工表面和导轨。
清洗性能取决于切削液的流动性和使用压力。
(4)防锈作用。
在切削液中加入防锈剂,可在金属表面形成一层保护膜,起到防锈作用。
防锈作用的强弱,取决于切削液本身的成分和添加剂的作用。