数控铣床与加工中心刀具补偿讲解
加工中心对刀与刀具补偿操作教程

加工中心对刀与刀具补偿操作教程时间:2012-05-30 作者:模具联盟网点击: 1479 评论:0 字体:T|T一、对刀对刀方法与具体操作同数控铣床。
二、刀具长度补偿设置加工中心上使用的刀具很多,每把刀具的长度和到 Z 坐标零点的距离都不相同,这些距离的差值就是刀具的长度补偿值,在加工时要分别进行设置,并记录在刀具明细表中,以供机床操作人员使用。
一般有两种方法:1、机内设置这种方法不用事先测量每把刀具的长度,而是将所有刀具放入刀库中后,采用 Z 向设定器依次确定每把刀具在机床坐标系中的位置,具体设定方法又分两种。
( 1 )第一种方法将其中的一把刀具作为标准刀具,找出其它刀具与标准刀具的差值,作为长度补偿值。
具体操作步骤如下:①将所有刀具放入刀库,利用 Z 向设定器确定每把刀具到工件坐标系 Z 向零点的距离,如图 5-2 所示的 A 、 B 、 C ,并记录下来;②选择其中一把最长(或最短)、与工件距离最小(或最大)的刀具作为基准刀,如图 5-2 中的 T03 (或 T01 ),将其对刀值 C (或 A )作为工件坐标系的 Z 值,此时 H03=0 ;③确定其它刀具相对基准刀的长度补偿值,即 H01= ±│ C-A │, H02= ±│ C-B │,正负号由程序中的 G43 或 G44 来确定。
④将获得的刀具长度补偿值对应刀具和刀具号输入到机床中。
( 2 )第二种方法将工件坐标系的 Z 值输为 0 ,调出刀库中的每把刀具,通过 Z 向设定器确定每把刀具到工件坐标系 Z 向零点的距离,直接将每把刀具到工件零点的距离值输到对应的长度补偿值代码中。
正负号由程序中的 G43 或 G44 来确定。
2、机外刀具预调结合机上对刀这种方法是先在机床外利用刀具预调仪精确测量每把在刀柄上装夹好的刀具的轴向和径向尺寸,确定每把刀具的长度补偿值,然后在机床上用其中最长或最短的一把刀具进行 Z 向对刀,确定工件坐标系。
数控铣床与加工中心刀具补偿讲解

数控铣床与加工中心刀具补偿和偏置功能刀具补偿可分为刀具长度补偿和刀具半径补偿,其内容和方法已在前面章节中作了详细说明,本章拟用另外一种指令格式对刀具长度补偿功能进行介绍,目的在于进一步强调不同的数控系统对同一编程功能可能采用不同的指令格式。
5.4.1 刀具半径补偿G41、G42、G40刀具半径补偿有两种补偿方式,分别称为B型刀补和C型刀补。
B型刀补在工件轮廓的拐角处用圆弧过渡,这样在外拐角处,由于补偿过程中刀具切削刃始终与工件尖角接触,使工件上尖角变钝,在内拐角处会则引起过切。
C型刀补采用了比较复杂的刀偏矢量计算的数学模型,彻底消除了B型刀补存在的不足。
下面仅讨论C型刀补。
(1).指令格式指令格式:G17/G18/G19 G00/G01 G41/G42G41:刀具半径左补偿G42:刀具半径右补偿半径补偿仅能在规定的坐标平面内进行,使用平面选择指令G17、G18或G19可分别选择XY、ZX或YZ平面为补偿平面。
半径补偿必须规定补偿号,由补偿号L存入刀具半径值,则在执行上述指令时,刀具可自动左偏(G41)或右偏(G42)一个刀具半径补偿值。
由于刀补的建立必须在包含运动的程序段中完成,因此以上格式中,也写入了GOO(或GO1)。
在程序结束前应取消补偿。
具体的判断方法见本书第二章。
(2).刀补过程刀具补偿包括刀补建立,刀补执行和刀补取消这样三个阶段,其中刀补建立与刀补取消均应在非切削状态下进行。
程序中含有G41或G42的程序段是建立刀补的程序段,含有G40的程序段是取消刀补的程序段,在执行刀补期间刀具始终处于偏置状态。
为了在建立刀补和取消刀补时,避免发生过切或撞刀,以及在刀补执行期间掌握刀具在运动段的拐角处的运动情况,有必要对刀补过程作一简要说明。
(3).刀具偏置矢量刀具偏置矢量是二维矢量,其大小等于D代码所规定的偏置量,矢量方向的计算是依照各轴刀具进给情况而于控制单元内自动完成的。
通过该偏置矢量计算出刀具中心偏离编程轨迹的实际轨迹。
数控机床刀具补偿功能的应用

刀具长度补偿是通过调整刀具在Z轴上 的位置来实现对工件表面的加工,而刀 具半径补偿则是通过调整刀具在X轴或 Y轴上的位置来实现对工件表面的加工
。
刀具补偿功能可以提高加工精度、减少 加工时间、降低加工成本。
刀具补偿的参数设置
01
刀具补偿参数主要包括刀具类型、刀具直径、刀具长
度、刀具角度等。
面形状和尺寸的高精度控制。
数控铣床应用
在数控铣床上,刀具补偿可应用于 三维空间加工,如曲面加工、五轴 加工等,以实现复杂零件的高效加 工。
加工中心应用
在加工中心上,刀具补偿可应用于 多轴联动加工,实现复杂零件的高 效加工。
02
CATALOGUE
刀具补偿的原理与实现
刀具补偿的原理
刀具补偿的基本原理是通过对刀具位置 的调整,以实现工件表面形状和尺寸的 精确控制。补偿分为刀具长度补偿和刀
03
提高生产效率
降低成本
通过快速调整刀具补偿参数,可 以减少换刀和调试时间,提高生 产效率。
正确使用刀具补偿功能可以减少 刀具磨损和报废,降低生产成本 。
数控机床刀具补偿功能的发展趋势与前景
智能化
随着人工智能技术的发展,未来刀具补偿功能将更加智能化,能够根据加工条件和刀具磨损情况自动调整补偿参数, 提高加工精度和效率。
04
CATALOGUE
数控机床刀具补偿功能的优化与改进
刀具补偿的误差分析
01
02
03
刀具几何误差
刀具的几何形状和尺寸对 加工精度产生直接影响。
刀具磨损误差
刀具在切削过程中会逐渐 磨损,导致加工精度下降 。
受热变形误差
切削过程中产生的热量会 导致刀具和工件变形,从 而影响加工精度。
加工中心刀具长度补偿课件

通过调整刀具长度补偿值,可以 确保工件坐标系与机床坐标系之 间的正确对齐,提高加工精度和 减小误差。
刀具长度补偿的重要性
在加工过程中,由于刀具磨损、更换 刀具等原因,实际使用的刀具长度可 能与编程时设定的长度存在差异。
刀具长度补偿能够自动调整刀具长度 ,确保工件坐标系的准确性,提高加 工质量和效率。
总结词
手动补偿方法是一种传统的刀具长度补偿方法,需要操作员根据测量结果手动 调整刀具长度。
详细描述
操作员使用测量工具测量刀具的实际长度,然后根据测量结果手动调整刀具长 度补偿值。这种方法简单易行,但精度不高,容易受到人为误差的影响。
自动补偿方法
总结词
自动补偿方法是一种现代化的刀具长度补偿方法,通过高精度的测量系统和自动控制系统实现刀具长度的自动测 量和补偿。
高精度补偿技术的需求
高精度加工要求
随着制造业对产品精度要 求的提高,需要更高精度 的刀具长度补偿技术来保 证加工质量。
纳米级补偿
研发纳米级补偿技术,实 现刀具长度的精确控制, 提高加工表面的光洁度和 平整度。
动态实时补偿
在加工过程中,根据实时 监测数据,动态调整补偿 值,减小误差和提高加工 稳定性。
详细描述
自动补偿方法使用高精度的测量系统,如激光干涉仪或电容传感器等,实时测量刀具的实际长度,并将测量结果 反馈给加工中心控制系统。控制系统根据反馈结果自动调整刀具长度补偿值,实现刀具长度的自动补偿。这种方 法精度高,能够显著提高加工精度和生产效率。
实时补偿方法
总结词
实时补偿方法是一种先进的刀具长度补偿方法,通过实时的刀具长度监测和补偿系统,实现刀具长度 的动态调整。
实时监测
在加工过程中,需要实时监测补偿值 的准确性,及时调整以确保加工质量 。
数控加工中的三种补偿和补偿技巧
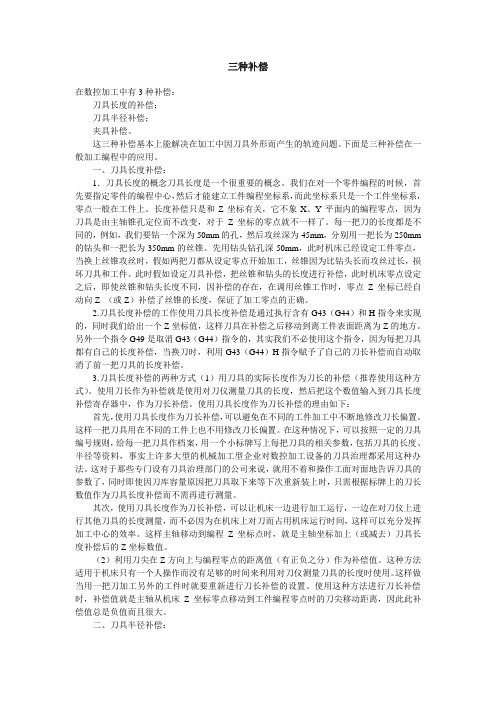
三种补偿在数控加工中有3种补偿:刀具长度的补偿;刀具半径补偿;夹具补偿。
这三种补偿基本上能解决在加工中因刀具外形而产生的轨迹问题。
下面是三种补偿在一般加工编程中的应用。
一、刀具长度补偿:1.刀具长度的概念刀具长度是一个很重要的概念。
我们在对一个零件编程的时候,首先要指定零件的编程中心,然后才能建立工件编程坐标系,而此坐标系只是一个工件坐标系,零点一般在工件上。
长度补偿只是和Z坐标有关,它不象X、Y平面内的编程零点,因为刀具是由主轴锥孔定位而不改变,对于Z坐标的零点就不一样了。
每一把刀的长度都是不同的,例如,我们要钻一个深为50mm的孔,然后攻丝深为45mm,分别用一把长为250mm 的钻头和一把长为350mm的丝锥。
先用钻头钻孔深50mm,此时机床已经设定工件零点,当换上丝锥攻丝时,假如两把刀都从设定零点开始加工,丝锥因为比钻头长而攻丝过长,损坏刀具和工件。
此时假如设定刀具补偿,把丝锥和钻头的长度进行补偿,此时机床零点设定之后,即使丝锥和钻头长度不同,因补偿的存在,在调用丝锥工作时,零点Z坐标已经自动向Z (或Z)补偿了丝锥的长度,保证了加工零点的正确。
2.刀具长度补偿的工作使用刀具长度补偿是通过执行含有G43(G44)和H指令来实现的,同时我们给出一个Z坐标值,这样刀具在补偿之后移动到离工件表面距离为Z的地方。
另外一个指令G49是取消G43(G44)指令的,其实我们不必使用这个指令,因为每把刀具都有自己的长度补偿,当换刀时,利用G43(G44)H指令赋予了自己的刀长补偿而自动取消了前一把刀具的长度补偿。
3.刀具长度补偿的两种方式(1)用刀具的实际长度作为刀长的补偿(推荐使用这种方式)。
使用刀长作为补偿就是使用对刀仪测量刀具的长度,然后把这个数值输入到刀具长度补偿寄存器中,作为刀长补偿。
使用刀具长度作为刀长补偿的理由如下:首先,使用刀具长度作为刀长补偿,可以避免在不同的工件加工中不断地修改刀长偏置。
加工中心刀具半径补偿编程举例

加工中心刀具半径补偿编程举例在数控加工领域中,加工中心是一种重要的设备,它能够高效地完成各种零件的加工任务。
而刀具半径补偿编程则是加工中心中常用的编程技术之一,它可以帮助操作者实现更加精准的切削加工效果。
下面将通过一个举例来说明加工中心刀具半径补偿编程的应用。
假设我们需要加工一个圆形孔,直径为10mm,而刀具的半径为5mm。
首先,在进行刀具半径补偿编程之前,我们需要准备好工件和刀具,并将它们安装在加工中心上。
接下来,我们进入编程界面,在进行刀具半径补偿编程之前,首先需要设置刀具半径补偿的模式。
在加工中心上,常用的刀具半径补偿模式有G41和G42。
G41代表左刀具半径补偿,即刀具路径在实际轮廓的左侧,而G42代表右刀具半径补偿,即刀具路径在实际轮廓的右侧。
根据加工需求,我们选择合适的刀具半径补偿模式。
然后,我们需要定义刀具半径补偿的具体数值。
在加工中心编程中,刀具半径补偿的数值以D开头进行定义。
例如,D10代表刀具半径补偿为10mm,D-5代表刀具半径补偿为-5mm。
根据实际情况,我们设置刀具半径补偿为5mm。
接下来,我们需要定义刀具路径。
在加工中心编程中,刀具路径通常使用G01指令进行定义。
例如,G01X100Y100表示刀具沿X轴和Y轴移动到坐标(100,100)的位置。
根据圆形孔的要求,我们定义刀具路径为G01X0Y0。
最后,我们需要进行圆形孔的切削加工。
在加工中心编程中,切削加工通常使用G02和G03指令进行定义。
G02表示顺时针切削,G03表示逆时针切削。
根据圆形孔的要求,我们定义切削加工的指令为G02X0Y0I-5J0,其中I和J表示切削圆的圆心坐标相对于起点坐标的偏移量。
通过以上的编程步骤,我们成功地完成了加工中心刀具半径补偿编程举例。
在实际操作过程中,我们可以根据不同的加工需要进行相应的调整和改进。
刀具半径补偿编程的应用可以帮助我们实现更加精准和高效的切削加工效果,提高加工质量和生产效率。
关于加工中心刀具半径补偿判定方法

加工中心刀具补偿G41/G42判定方法
判定方法:
假定操作者面向刀具前进的方向站立,刀具前进的箭头指向自己,此时,如果被加工表面在自己的左手边,则为G41(左刀补);如果被加工表面在自己的右手边,则为G42(右刀补);
切记!!G41/G42与G02/G03没有严格的对应关系,具体什么时候该用G41、G42一定要学会自己判断。
特例:如果程序中某处使用的G41/G42与上面的判定方法“相反”,则在使用CAM编程时,刀具补偿选择了“两者反向”,此时所加刀补正负值正好与上面的相反。
举例说明:
正负值的判定:与上述“判定方法”相同时:如果要求图1内孔(内轮廓)尺寸变大、图2外轮廓变小,则在机床刀具补偿值处输入相应的负值(相对当前值);例如当前刀补值为0.05(-0.05)mm,要求孔变大(外轮廓变小)0.02mm 时,应该将刀补值改为0.04(-0.06)mm(半径补偿)。
与上述“判定方法”相反时:如果要求图1内孔(内轮廓)尺寸变大、图2外轮廓变小,则在机床刀具补偿值处输入相应的正值(相对当前值);例如当前刀补值为0.05(-0.05)mm,要求孔变大(外轮廓变小)0.02mm时,应该将刀补值改为0.06(-0.04)mm(半径补偿)。
欢迎您的下载,
资料仅供参考!
致力为企业和个人提供合同协议,策划案计划书,学习资料等等
打造全网一站式需求。
数控铣床、加工中心常见对刀方法

数控铣床、加工中心常见对刀方法
数控铣床、加工中心在加工过程中,需要进行对刀才能保证加工精度和效率。
下面将
介绍常见的数控铣床、加工中心对刀方法。
一、机械对刀法
机械对刀法是最基本的对刀方法,它利用机床本身的机械结构进行对刀。
操作人员只
需将对刀仪放在加工刀具上,然后通过调整机床的移动量,使对刀仪与机床刀具位置对齐
即可完成对刀。
机械对刀法简单易操作,但精度有限,只适用于一般的加工任务。
二、光电对刀法
光电对刀法具有精度高、快速方便等优点,适用于精密加工任务。
三、感应对刀法
感应对刀法适用于各种类型的加工刀具,但需要注意的是,在进行对刀时,加工刀具
需要具有导电性。
四、摄像对刀法
以上就是常见的数控铣床、加工中心对刀方法,根据不同加工任务和机床的具体情况,可以选择最适合的方法进行对刀,以保证加工精度和效率。
加工中心刀具补偿

刀具补偿
1、刀具长度补偿:G43刀具正补偿,G44刀具负补偿,G49刀具长度取消。
G43在Z轴第一次
走刀时用,即下到Z10安全平面的时候使用,如:G43 G00 Z10 H01。
当该把刀程序执行完全结束后用G49G00Z100取消长度补偿。
2、刀具半径补偿:G41刀具左补偿,外轮廓加工:顺时针走刀,顺铣时沿刀具进刀方向看,刀具与工件左侧铣削。
内轮廓加工:逆时针走刀,G41G01X-25F200D01。
G42刀具右补偿(一般不使用)。
3、G40刀具半径补偿取消。
1、加工尺寸不正确时,修改G41半径补偿的方法:
如:要求加工100×100mm的凸台,实测为102×102mm。
参数OFFET/SETTING→刀偏(补正)→形状D→-1→+输入。
如:要求加工100×100mm的凸台,实测为98×98mm。
参数OFFET/SETTING→刀偏(补正)→形状D→1→+输入。
刀具长度补偿的理解与应用
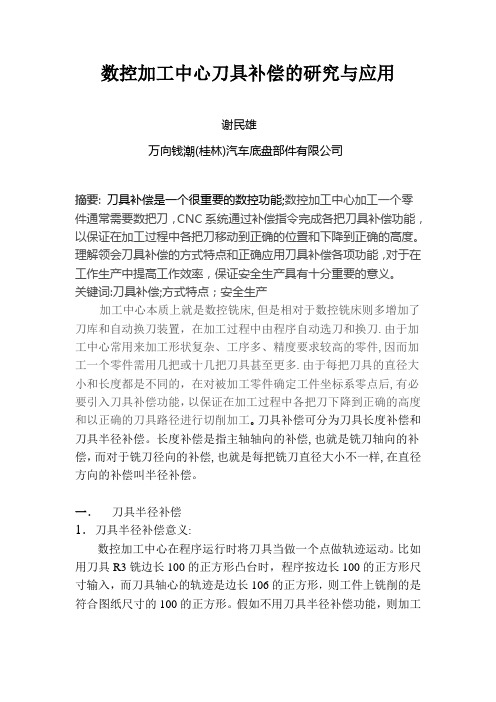
数控加工中心刀具补偿的研究与应用谢民雄万向钱潮(桂林)汽车底盘部件有限公司摘要:刀具补偿是一个很重要的数控功能;数控加工中心加工一个零件通常需要数把刀,CNC系统通过补偿指令完成各把刀具补偿功能,以保证在加工过程中各把刀移动到正确的位置和下降到正确的高度。
理解领会刀具补偿的方式特点和正确应用刀具补偿各项功能,对于在工作生产中提高工作效率,保证安全生产具有十分重要的意义。
关键词:刀具补偿;方式特点;安全生产加工中心本质上就是数控铣床,但是相对于数控铣床则多增加了刀库和自动换刀装置,在加工过程中由程序自动选刀和换刀.由于加工中心常用来加工形状复杂、工序多、精度要求较高的零件,因而加工一个零件需用几把或十几把刀具甚至更多.由于每把刀具的直径大小和长度都是不同的,在对被加工零件确定工件坐标系零点后,有必要引入刀具补偿功能,以保证在加工过程中各把刀下降到正确的高度和以正确的刀具路径进行切削加工。
刀具补偿可分为刀具长度补偿和刀具半径补偿。
长度补偿是指主轴轴向的补偿,也就是铣刀轴向的补偿,而对于铣刀径向的补偿,也就是每把铣刀直径大小不一样,在直径方向的补偿叫半径补偿。
一.刀具半径补偿1.刀具半径补偿意义:数控加工中心在程序运行时将刀具当做一个点做轨迹运动。
比如用刀具R3铣边长100的正方形凸台时,程序按边长100的正方形尺寸输入,而刀具轴心的轨迹是边长106的正方形,则工件上铣削的是符合图纸尺寸的100的正方形。
假如不用刀具半径补偿功能,则加工时刀具轴心的轨迹是边长100的正方形,则工件上铣削出的是边长为94的正方形凸台,不符合图纸尺寸的要求。
2.指令格式G17/G18/G19 G00/G01 G41/G42 IP_D_G41:刀具半径左补偿G42:刀具半径右补偿半径补偿仅能在规定的坐标平面内进行,使用平面选择指令G17、G18或G19可分别选择XY、ZX或YZ平面为补偿平面。
半径补偿必须规定补偿号,由补偿号D存入刀具半径值,则在执行上述指令时,刀具可自动左偏(G41)或右偏(G42)一个刀具半径补偿值。
数控机床刀补怎么算
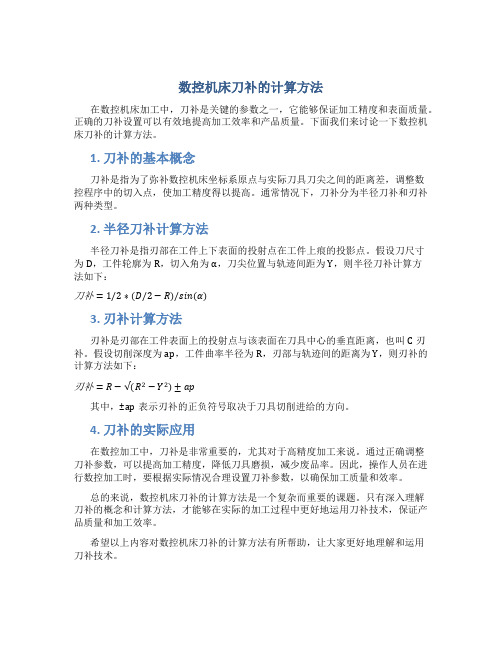
数控机床刀补的计算方法在数控机床加工中,刀补是关键的参数之一,它能够保证加工精度和表面质量。
正确的刀补设置可以有效地提高加工效率和产品质量。
下面我们来讨论一下数控机床刀补的计算方法。
1. 刀补的基本概念刀补是指为了弥补数控机床坐标系原点与实际刀具刀尖之间的距离差,调整数控程序中的切入点,使加工精度得以提高。
通常情况下,刀补分为半径刀补和刃补两种类型。
2. 半径刀补计算方法半径刀补是指刃部在工件上下表面的投射点在工件上痕的投影点。
假设刀尺寸为D,工件轮廓为R,切入角为α,刀尖位置与轨迹间距为Y,则半径刀补计算方法如下:刀补=1/2∗(D/2−R)/sin(α)3. 刃补计算方法刃补是刃部在工件表面上的投射点与该表面在刀具中心的垂直距离,也叫C刃补。
假设切削深度为ap,工件曲率半径为R,刃部与轨迹间的距离为Y,则刃补的计算方法如下:刃补=R−√(R2−Y2)±ap其中,±ap表示刃补的正负符号取决于刀具切削进给的方向。
4. 刀补的实际应用在数控加工中,刀补是非常重要的,尤其对于高精度加工来说。
通过正确调整刀补参数,可以提高加工精度,降低刀具磨损,减少废品率。
因此,操作人员在进行数控加工时,要根据实际情况合理设置刀补参数,以确保加工质量和效率。
总的来说,数控机床刀补的计算方法是一个复杂而重要的课题。
只有深入理解刀补的概念和计算方法,才能够在实际的加工过程中更好地运用刀补技术,保证产品质量和加工效率。
希望以上内容对数控机床刀补的计算方法有所帮助,让大家更好地理解和运用刀补技术。
数铣编程指令和刀具半径补偿

数控铣床编程编程指令和刀具半径补偿1.G指令:准备功能指令(1)G90 绝对方式编程(2)G91 增量方式编程(3)G54~ G59 选择工件坐标系(4)G00 快速点定位 X Y Z(5)G01 直线插补 X Y Z F(6)G02 顺圆插补 X Y R(或I J K) F (7)G03 逆圆插补 X Y R (或I J K) F(8)G41 X Y D 刀具半径左补偿(9)G42 X Y D 刀具半径右补偿(10)G40 X Y 取消刀具半径补偿(11)G17、G18、G19 选择加工平面G17—XOY 平面(缺省值) G18—XOZ平面 G19—YOZ平面G90 G80 G40 G17 G49 G21(安全语句)功能:初始化状态设定。
式中: G90 ——绝对值方式;G80 ——取消固定循环;G 代码指令2.M 指令:辅助功能 (1)M00 程序暂停 (2)M03 主轴正转 (3)M05 主轴停 (4)M08 切削液开 (5)M09 切削液停(6)M30 完成程序段指令后 返回“程序开始”(7)M98 调用子程序 (8)M99 子程序结束一、基本常用指令3.指令——fz(mm/min)进给速度vf =fz ×z × n (铣床、加工中心)4.S 指令——r/min5.程序的组成和格式和数车一样,数铣的一个完整的零件程序包括程序号、程序内容和程序结束三个部分。
%(或O )1234G90 G80 G40 G17 G49 G21(安全语句) M03S1000 G54G00Z100 X0Y0G01Z-6F200G41D01X ▁Y ▁ …… G40X ▁Y ▁ G00Z100 M05 M30程序号程序内容程序结束6.绝对值编程G90与相对值编程G91格式: G90 G X Y ZG91 G X Y ZG90为绝对值编程,每个轴上的编程值是相对于程序原点的。
G91为相对(增量)值编程,每个轴上的编程值是相对于前一位置而言的,该值等于沿轴移动的距离。
刀具半径补偿
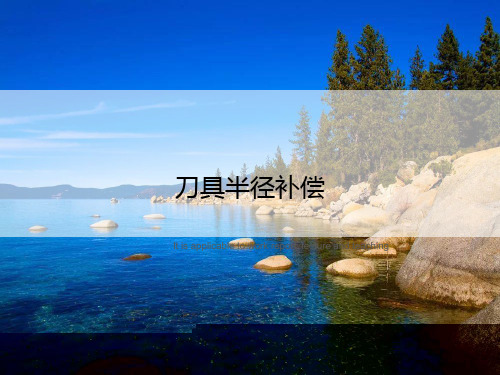
y A(X,Y)
O
α
rΔYKΔK Xα A′(X′,Y′) x
O′
图3-37 直线刀具补偿
y B′(Xb′,Yb′)
B(Xb,Yb) ΔXΔ KY
β O
R
r A′(Xa′,Ya′)
A(Xa,Ya) x
图3-38 圆弧刀具半径补偿
2. 圆弧刀具半径补偿计算
对于圆弧而言,刀具补偿后的刀具中心轨迹是一个
1. 直线刀具补偿计算
对直线而言,刀具补偿后的轨迹是与原直线平行 的直线,只需要计算出刀具中心轨迹的起点和终点坐 标值。
如图3-37所示,被加工直线段的起点在坐标原点,终 点坐标为A。假定上一程序段加工完后,刀具中心在O′ 点坐标已知。刀具半径为,现要计算刀具右补偿后直 线段O′A′的终点坐标A′。设刀具补偿矢量AA′的投影坐 标为,则
图3-41和3-42表示了两个相邻程序段为直线与直线, 左刀补G41的情况下,刀具中心轨迹在连接处的过渡形 式。图中α为工件侧转接处两个运动方向的夹角,其变 化范围为00<ɑ< 3600,对于轮廓段为圆弧时,只要用其 在交点处的切线作为角度定义的对应直线即可。
在图3-42a中,编程轨迹为FG和GH,刀具中心轨迹为AB 和BC,相对于编程轨迹缩短一个BD与BE的长度,这种 转接为缩短型。
(1)刀补建立 刀具从起刀点接近工件,在原来的 程序轨迹基础上伸长或缩短一个刀具半径值,即刀具 中心从与编程轨迹重合过渡到与编程轨迹距离一个刀 具半径值。在该段中,动作指令只能用G00或G01。
(2)刀具补偿进行 刀具补偿进行期间,刀具中心 轨迹始终偏离编程轨迹一个刀具半径的距离。在此状 态下,G00、G01、G02、G03都可使用。
一段加工轨迹对本程序段加工轨迹的影响。为解决下
数控机床刀补指令

数控机床刀补指令数控机床是一种高精度、高效率、自动化程度较高的现代化加工设备,广泛应用于各种金属、非金属零部件的加工制造过程中。
数控机床的核心部分是数控系统,而数控系统中的刀具补偿功能对加工的精度和质量起着至关重要的作用。
本文将介绍数控机床刀补指令的定义、作用及在加工中的应用。
一、概述数控机床刀补指令是数控编程中的一种重要指令,它用于对加工刀具的轨迹进行微调,以达到更高的加工精度和质量。
通过刀补指令,可以对刀具进行不同方向的补偿,使刀具的实际运动轨迹与设定的轨迹一致。
刀补指令通常由数控系统解释执行,可以在程序中灵活调用,实现对不同形状、大小的刀具进行精确加工。
二、刀补指令的分类根据不同的刀具补偿方式,刀补指令可以分为长度补偿、半径补偿和刀尖补偿等几种类型。
长度补偿主要用于修正刀具长度偏差,使加工深度更加准确;半径补偿主要用于修正刀具半径偏差,以确保加工轮廓的精度;而刀尖补偿则是用于修正刀具切削刃与轨迹的偏移,保证切削路径的正确性。
三、刀补指令的应用在数控加工中,刀补指令的应用非常普遍,它可以实现对各类形状、大小的工件进行高精度加工。
在程序编制过程中,操作人员可以根据加工要求和实际情况,通过刀补指令对刀具路径进行调整,以确保加工精度和质量。
此外,在复杂曲面加工中,刀补指令更显得尤为重要,通过对刀具的微调,可以实现对曲面的精细加工,提高加工效率和质量。
四、结语数控机床刀补指令作为数控加工中的重要一环,对于提高加工精度、减少误差至关重要。
通过合理灵活地运用刀补指令,可以实现对各类工件的高精度加工,提高生产效率和质量水平。
因此,在数控机床的操作和编程过程中,专业人士应该充分理解刀补指令的原理和应用,合理运用刀补功能,提高加工效率,满足市场对精密零部件加工的需求。
数控铣床及加工中心对刀的一些个人理解和经验

关于数控铣床及加工中心对刀的一些个人理解和经验本人从事数控铣床及加工中心3年多的时间,对这些机床的坐标系设定及对刀有一些个人的理解,并积累了一些经验,想和一些从事数控加工的初级人员交流和分享。
鉴于水平有限,有不足之处还请见谅及批评指正首先加工中心和数控铣床相比仅仅是多了个刀库,可以在一次加工中进行多把刀的加工操作,它们在本质上没什么区别。
我们就以数控铣床为例进行讲解。
我们的世界是三维世界,空间由长宽高组成,在方位上就是“东西”、“南北”、“上下”,假设我们朝北站立,对应的铣床坐标就是X、Y、Z(“东”为x正方向、“北”为y正方向、“上”为z正方向)。
Xy通常为一组(也就是G17平面),Z通常为另一组。
这是首先要建立的一个概念。
现在我们要“铣床”帮我们加工一个工件,我们把工件放在它的工作台上,夹紧后,通过程式要“铣床”加工工件的某个地方,比如说要“铣床”在G54X20Y-10的地方钻个孔。
那么现在问题就来了“铣床”它怎么知道这个G54X20Y-10是哪里咧?它不知道!因为它没长眼睛!!它怎么知道我们把工件放在了它工作台的哪个地方咧?所以我们首先要告诉它:工件到底在哪里。
我以前听过一个故事,说一个瞎子出门在外杵拐杖,还时不时要敲一下小铜锣,但在家门口却什么都不需要,可以很迅速的到要去的地方。
原因是他把家周围的东西都摸熟悉了,比如站在家门口(我们假设他家是座北朝南的)向南走100步就是条小路右拐300步可以到邻居家。
再比如站在家门口,向左200步就是打水的井,其中在第150步的时候有块大石头要向南让20步,再向左走完剩下的50步刚好到井边。
盲人没有眼睛看东西,但是他可以数自己的步伐来度量距离、从家门口走可以知道起始点和方向。
铣床也是一样,工作台运动的距离由伺服电机转的圈数来决定,方向由电机转的方向来确定。
这些在机床的电器部分是很容易做到的。
问题是从哪里开始!!我们把那个瞎子丢到我家门口(假设我家也是座北朝南),你看他还能不能找到他的邻居、还能不能找到井?不能了吧!为什么?因为起始点变了。
刀补概念

刀具补偿科技名词定义
中文名称:刀具补偿 英文名称:cutter compensation 定义:通过切削点垂直于刀具轨迹的位移补偿,用来修正刀具实际半径或直径与其程序规定值之差。 应用学科:机械工程(一级学科);切削加工工艺与设备(二级学科);自动化制造系统(三级学科) 本内容由全国科学技术名词审定委员会审定公布 目录
一、刀具补偿的提出
二、全功能数控机床系统中刀具补偿1.数控车床刀具补偿
中刀具轨迹的计算1.刀具中心(刀位点)轨迹的计算
2.数控车床假想刀尖点的偏置计算
四、结论一、刀具补偿的提出
二、全功能数控机床系统中刀具补偿 1.数控车床刀具补偿
2.加工中心、数控铣床刀具补偿
编辑本段四、结论
在数控加
工中,由于刀尖有圆弧,工件轮廓是刀具运动包络形成,因此刀位点的运动轨迹与工件的轮廓是不重合的。在全功能数控系统中,可应用其刀具补偿指令,按工件轮廓尺寸,很方便地进行编程加工。在经济型数控系统中,可以根据工件轮廓尺寸、刀具等计算出刀位点的运动轨迹,按此编程,也可按局部补偿的方法来解决
三、经济型数控机床中刀具轨迹的计算 1.刀具中心(刀位点)轨迹的计算
2.数控车床假想刀尖点的偏置计算
四、结论
展开 编辑本段一、刀具补偿的提出
用立铣刀在数控机床上加工工件,可以清楚看出刀具中心运动轨迹与工件轮廓不重合,这是因为工件轮廓是立铣刀运动包络形成的。立铣刀的中心称为刀具的刀位点(4、5坐标数控机床称为刀位矢量),刀位点的运动轨计即代表刀具的运动轨迹。在数控加工中,是按工件轮廓尺寸编制程序,还是按刀位点的运动轨迹尺寸编制程序,这要根据具体情况来处理。 数控机床立铣刀加工 在全功能数控机床中,数控系统有刀具补偿功能,可按工件轮廓尺寸进行编制程序,建立、执行刀补后,数控系统自动计算,刀位点自动调整到刀具运动轨迹上。直接利用工件尺寸编制加工程序,刀具磨损,更换加工程序不变,因此使用简单、方便。 经济型数控机床结构简单,售价低,在生产企业中有一定的拥有量。在经济型数控机床系统中,如果没有刀具补偿功能,只能按刀位点的运动轨迹尺寸编制加工程序,这就要求先根据工件轮廓尺寸和刀具直径计算出刀位点的轨迹尺寸。因此计算量大、复杂,且刀具磨损、更换需重新计算刀位点的轨迹尺寸,重新编制加工程序。
数控机床刀具补偿分析

数控机床刀具补偿分析【摘要】数控加工中刀具补偿得到了广泛应用。
在实际加工的过程中,由于不同刀具的半径都各不相同,在加工中会产生很大的加工误差。
因此,在实际加工时必须通过刀具补偿的指令,使数控车床根据实际使用的刀具尺寸,自动调整其坐标轴的移动量,如果能够合理建立和灵活的运用刀具补偿功能,就会对简化编程和提高数控加工的质量会带来极大的帮助。
本文就加工中如何的应用刀具补偿作一些探讨。
针对刀具补偿功能在数控中的应用,研究它在加工中存在的问题对此进行解决,尽量避免刀补问题的发生。
【关键词】:刀具半径补偿;功能;应用;程序;指令目录引言 (1)一、刀具半径补偿 (2)二、刀具长度补偿 (2)三、数车中刀具补偿的应用 (3)(一)数车刀尖圆弧半径补偿误差分析 (3)(二)数车刀尖圆弧半径补偿方法 (4)(三)刀尖圆弧半径补偿注意事项 (5)四、加工中心刀具补偿应用 (5)(一)刀具长度补偿引起误差分析 (6)(二)刀具长度补偿方法 (6)五、加工举例 (6)(一)加工中心刀具长度补偿实例 (6)(二)数车刀尖圆弧半径补偿实例 (8)总结 (10)参考文献 (11)谢辞 (12)引言数控刀具补偿是数控加工系统的一个基础功能,在手工编程的铣削加工中广泛使用,如何的深人掌握和应用该功能,在机床加工中有非常重要的意义,在进行轮廓加工中,由于刀具有一定的半径,刀具中心的轨迹与加工工件的轨迹常不重合。
通过刀具补偿功能指令,数控系统可以根据输入的补偿量或者实际的刀具尺寸,使机床加工出符合规格的零件。
20世纪60到70年代的数控加工中还没有刀具补偿的概念,编程人员必须根据刀具的理论路线和实际路线的相对关系从而进行数控编程,既容易产生错误,又使得编程的效率很低。
当数控刀具补偿的概念出现时并应用到数控系统中后,编程人员就可以直接按照工件的轮廓尺寸进行程序编辑。
从而建立并执行刀补后,由数控系统自动计算、自动调整刀位点到刀具的运动轨迹。
加工中心的刀具和刀具补偿

(1)编程 T__ ;刀具号:l~32000,T0表示没有刀具 说明:系统中最多同时存储32把刀具。 (2)编程举例5.39 不用M6更换刀具: N10 T1 ;刀具1 … N70 T5 ;刀具5 用M6更换刀具: N10 T5 ;预选刀具5 N15 M6 ;执行刀具更换,然后T5有效
刀尖半径补偿(切削刃半径补偿) 工件轮廓左边/右边补偿
刀尖半径补偿(切削刃半径补偿) 工件轮廓左边/右边补偿
沿着刀具的运动方向观察,刀具在工件的左侧,为左刀补用G41。刀具在工件的右侧,为右刀补用G42
刀补建立
刀补取消
刀 补 执 行
谢谢观看
单击此处添加副标题
点击此处添加正文,文字是您思想的提炼,请言简意赅的阐述您的观点。
汇报人姓名
铣销凸台轮廓程序的实例;工件如图所示,凸台高为5mm。
第七章 SIEMENS 802D加工中心的编程
单击此处添加副标题
内容摘要 刀具和刀具补偿
汇报人姓名
第四节 刀具和刀具补偿
一、刀具T 用T指令编程可以选择刀具。有两种方法来执行:一种是用T指令直接更换刀具,另一种是仅仅进行刀具的预选,换刀还必须由M06来执行。选择哪一种,必须在机床参数中确定: 1)用T指令直接更换刀具。 2)仅用T指令预选刀具,另外还要用M6指令配合才可进行刀具的更换。
第四节 刀具和刀具补偿
刀具补偿
01
0四、刀具长度补偿 刀具长度补偿基格式:T1 D1 说明:刀具更换后,程序中调用的刀具长度补偿立即生效;如未指定所调用的刀具参数号时,数控系统会自分理处调用相应刀具的第一号刀具参数值D1;如果编程D0,则刀具补偿值无效. (1)编程 T1 M06 G54 G90 G00 X100 Y100 F100 S600 M03 D1 Z20
- 1、下载文档前请自行甄别文档内容的完整性,平台不提供额外的编辑、内容补充、找答案等附加服务。
- 2、"仅部分预览"的文档,不可在线预览部分如存在完整性等问题,可反馈申请退款(可完整预览的文档不适用该条件!)。
- 3、如文档侵犯您的权益,请联系客服反馈,我们会尽快为您处理(人工客服工作时间:9:00-18:30)。
数控铣床与加工中心刀具补偿讲解数控铣床与加工中心5.4 刀具补偿和偏置功能刀具补偿可分为刀具长度补偿和刀具半径补偿,其内容和方法已在前面章节中作了详细说明,本章拟用另外一种指令格式对刀具长度补偿功能进行介绍,目的在于进一步强调不同的数控系统对同一编程功能可能采用不同的指令格式。
5.4.1 刀具半径补偿G41、G42、G40刀具半径补偿有两种补偿方式,分别称为B 型刀补和C型刀补。
B型刀补在工件轮廓的拐角处用圆弧过渡,这样在外拐角处,由于补偿过程中刀具切削刃始终与工件尖角接触,使工件上尖角变钝,在内拐角处会则引起过切。
C型刀补采用了比较复杂的刀偏矢量计算的数学模型,彻底消除了B型刀补存在的不足。
下面仅讨论C型刀补。
(1).指令格式指令格式:G17/G18/G19 G00/G01 G41/G42G41:刀具半径左补偿G42:刀具半径右补偿半径补偿仅能在规定的坐标平面内进行,使用平面选择指令G17、G18或G19可分别选择XY、ZX或YZ平面为补偿平面。
半径补偿必须规定补偿号,由补偿号L存入刀具半径值,则在执行上述指令时,刀具可自动左偏(G41)或右偏(G42)一个刀具半径补偿值。
由于刀补的建立必须在包含运动的程序段中完成,因此以上格式中,也写入了GOO(或GO1)。
在程序结束前应取消补偿。
具体的判断方法见本书第二章。
(2).刀补过程刀具补偿包括刀补建立,刀补执行和刀补取消这样三个阶段,其中刀补建立与刀补取消均应在非切削状态下进行。
程序中含有G41或G42的程序段是建立刀补的程序段,含有G40的程序段是取消刀补的程序段,在执行刀补期间刀具始终处于偏置状态。
为了在建立刀补和取消刀补时,避免发生过切或撞刀,以及在刀补执行期间掌握刀具在运动段的拐角处的运动情况,有必要对刀补过程作一简要说明。
(3).刀具偏置矢量刀具偏置矢量是二维矢量,其大小等于D代码所规定的偏置量,矢量方向的计算是依照各轴刀具进给情况而于控制单元内自动完成的。
通过该偏置矢量计算出刀具中心偏离编程轨迹的实际轨迹。
偏置计算在由G17、G18和G19确定的平面内进行,该平面称之为偏置平面。
例如在已经选择了XY平面时,仅对程序中(X、Y)或(1、J)计算偏置量,并计算偏置矢量。
不在偏置平面内的轴的坐标值不受偏置的影响。
在3轴联动控制中,投影到偏置平面上的刀具轨迹才得到偏置补偿。
(4).刀补的建立与刀补的取消刀补的建立是进入切削加工前的一个辅助程序段,刀补的取消是加工完成时要写入到程序中的辅助程序段,如果处理得好则有利于简捷快速而又安全地使刀具进入切入位置和加工完了时退出刀具。
刀补建立时的核心问题是刀具从何处下刀并进入到工件加工的起始位置,刀补取消时则主要应考虑刀具沿何方向退离工件。
系统操作说明书中讨论了各种可能遇到的情况,为简化叙述,下面仅根据习惯的编程方法讨论刀补建立与刀补取消的问题。
不使用这些方法一般也可以正确地完成刀补建立与刀补取消的过程,但特殊情况下可能出现过切或报警。
1)使用GOO或G01的运动方式均可完成刀补建立或取消的过程,事实上使用G01往往是出于安全的考虑。
而如果不把刀补的建立(包括刀补的取消)建立在加工时的Z轴高度上,而采取先建立补偿再下刀或先提刀再取消补偿的方法,则既使在GOO的方式下建立(或取消)刀补也是安全的。
2)为了便于计算坐标,可以按图5-18所示两种方式来建立刀补,图5-18a为切线进入方式,图5-18b为法线进入方式。
同样取消刀补通常也采用这种切线或法线的方式。
图5-18 两种刀补建立方式图5-19 内圆轮廓的补偿3)在不便于直接沿着工件的轮廓线切向切入和切向切出时,可再增加一个圆弧辅助程序段。
如图5-19所示的内圆轮廓形状,采用铣圆法加工。
编程时根据孔加工的余量大小及刀具尺寸等情况,取一个适当大小的圆弧,设半径为r,并由此求出圆心点A的坐标和圆弧上B、C、E点的坐标。
加工时先让刀具定位到大圆的圆心并下刀至孔深。
若孔加工的编程轨迹为O→A→B→C→0→C→E→A→O,并于A--B段建立刀补,A--E段取消刀补,则实际加工的刀心运动轨迹为O→A→B′→C′→D′→C′→E′→A→O,这样就能十分方便地实现切向切入与切向切出,使加工时不致于在内孔的C点处产生明显的刀痕。
实际处理时,∠BAC与∠EAC的值也可根据需要取30°、45°或60°,以减少空刀时间,但计算略繁。
对于外形轮廓的加工,若采用直线段实现切向切入与切向切出有困难时,也可以采用这种增加辅助圆弧程序段的办法。
(5).执行C型刀补过程中的刀心运动轨迹为了能对刀补执行过程中,编程轨迹与刀心运动轨迹的关系有一个初步的了解,图5-20示出了几种用G42编程时典型的C型刀补编程轨迹与刀心运动轨迹之间的关系,图a为α≥ 180°由直线段到直线段在拐角处的转接情况,刀具沿内侧运动至S点转到后一段加工,在拐角处不产生过切;图b为90°≤α≤180°由直线段到圆弧段的转接情况;图C为1°≤α≤90°时由圆弧段到直线段在拐角处的转接情况。
由图不难看出C 型刀补在拐角处一律采用直线转接的型式,通过伸长直线段或增加直线段的方法实现转接,这就避免了B型刀补采用圆弧转接带来的不足。
如使用G41时则刀具中心轨迹在编程轨迹的左侧,处理方法与上述一致。
图5-20 C型刀补过程的刀心运动轨迹(6).使用刀具半径补偿注意事项1) G41、G42、G40不能和G02、G03在一起程序段中使用,只能与GOO或G01一起使用,且刀具必须要移动。
2)在程序中用G42指令建立右刀补,铣削时对于工件将产生逆铣效果,故常用于粗铣;用G41指令建立左刀补,铣削时对于工件将产生顺铣效果,故常用于精铣。
3)一般情况下,刀具半径补偿量应为正值,如果补偿值为负,则G41和G42正好相互替换。
通常在模具加工中利用这一特点,可用同一程序加工同一公称尺寸的内外两个型面。
4)在补偿状态下,铣刀的直线移动量及铣削内侧圆弧的半径值要大于或等于刀具半径,否则补偿时会产生干涉,系统在执行相应程序段时将会产生报告,并停止执行。
5)若程序中建立了半径补偿,在加工完成后必须用G40指令将补偿状态取消,使铣刀的中心点回复到实际的坐标点上。
亦即执行G40指令时,系统会将向左或向右的补偿值,往相反的方向释放,这时铣刀会移动一铣刀半径值。
所以使用G40指令时最好是铣刀已远离工件。
(7).刀具半径补偿的应用①编程时直接按工件轮廓尺寸编程。
刀具在因磨损、重磨或更换后直径会发生改变,但不必修改程序,只需改变半径补偿参数。
②刀具半径补偿值不一定等于刀具半径值,同一加工程序,采用同一刀具可通过修改刀补的办法实现对工件轮廓的粗、精加工;同时也可通过修改半径补偿值获得所需要的尺寸精度。
【例5-3】:如图5-21为建立和取消刀具半径补偿示例。
程序如下:G17 G90 G54 GOO XO Y0 S400; (→O)G41 GOO X30.0 Y15.0 D01 M03; (O→P1,建立左刀补)G01 Y50.0 F150; (P1→P2)X65.O;(P2→P3)Y25.0;(P3→P4)X20.0;(P4→P5)G40 G00 XO YO M05;(P5→P6,撤销刀补)图5-21 刀具半径补偿示例图5-22 刀具走刀路线图【例5-4】:如图5-22所示,试编制加工程序,已知立铣刀为Φ16mm,半径补偿号为D01 01000;(程序号)G17 G90 G54 GOO X0 Y0 S500;(②)Z5.0 M03; (③) G41 G00 X60.0 Y30.0 D01;(④O→A)G01 Z-27.0 F2000; (⑤) Y80.0 F120; (⑥A→B)G03 X100.0 Y120.0 R40.0;(⑦B→C)G01 X180.0; (⑧C→D)Y60,0; (⑨D→E)G02 X160.0Y40.0R20,0;(⑩E→F)G01 XS0.0; (11F→G) GOO Z5.0; (12)G40 XOYO M05; (G→O) G91 G28 Z0; (Z轴回参考点)M30; (程序结束) 5.4.2 刀具长度补偿G43、G44、G49刀具长度补偿是用来补偿假定的刀具长度与实际的刀具长度之间的差值,系统规定除Z轴之外,其他轴也可以使用刀具长度补偿,但同时规定长度补偿只能同时加在一个轴上,要对补偿轴进行切换,必须先取消对前面轴的补偿。
1.指令格式:G43α___H___;(α指X、Y、Z任意一轴),刀具长度补偿“+”。
G44α___H___;刀具长度补偿“-”。
G49或H00:取消刀具长度补偿。
以上指令中用G43、G44指令偏移的方向,用H指令偏置量存储器的偏置号。
执行程序前,需在与地址H所对应的偏置量存储器中,存入相应的偏置值。
以z轴补偿为例,若指令 GOO G43 Z100.0 H01;并于H01中存入“-200.0”,则执行该指令时,将用Z坐标值100.与H01中所存“-200.”进行“+”运算,即100.0+(-200.0)=-100,并将所求结果作为Z轴移动值,取消长度补偿用G49或H00。
若指令中忽略了坐标轴,则隐含为Z轴且为Z0。
2.刀具自参考点下刀时的补偿问题一般情况下加工中心机床总是从参考点换刀的.对于立式加工中心而言,在使用G54~G59工件坐标系时,若仅于X、Y方向偏置G54坐标原点位置而Z轴方向不偏置,则Z轴方向上刀具刀位点与工件坐标系中Z=0平面之间的差值可以全部由刀具长度补偿加以解决,这是操作者在设置偏置值时一种常用的方法。
此时G54的Z0平面与机床坐标系的Z0平面是一致的,即G54的20平面通过z轴方向机床参考点。
编程人员在编写程序时全然不管操作者是怎样设置补偿值的,仍将G54的Z0平面规定在工件某一高度的位置上,操作人员不作z轴方向上的工件零点偏置的操作,而是将全部差值(包括z轴工件零点偏置值与装刀后主轴前端面到刀具刀位点的距离)让长度补偿功能一并加以解决。
以图5-23为例说明。
设编程时编程员希望刀具自参考点下刀到工件坐标系中Z40.的位置,则程序段可以写成G90 GOO G43 Z40. H01;操作人员在安装刀具和工件后,直接测量主轴自参考点下移时刀位点到(补偿面)20平面的距离,若实测刀位点自Z轴参考点出发到达程序中G92 Z0平面位移为-320,直接将该值存于H01存储器中,执行该程序段时,刀具按40.+(-320.)=-280.即按Z=-280.下刀与预期的下刀点完全一致。
图5-23 G43、G44、G49的应用这种程序编写的一般形式为:G90 G49 G54 GOO X___Y___;G43 H___Z___M03 S___;……G90 G49 G28 Z0. T01 M06……我们可以采用工件零点偏置值与刀具长度补偿值分别测量输入的方法。