加工质量控制标准
机械加工质量控制
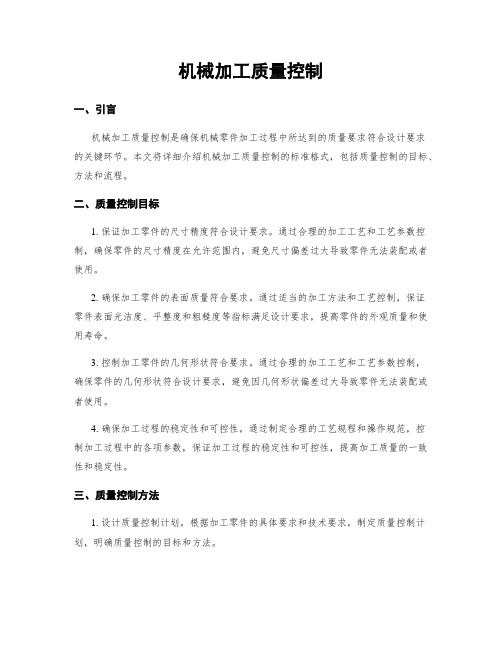
机械加工质量控制一、引言机械加工质量控制是确保机械零件加工过程中所达到的质量要求符合设计要求的关键环节。
本文将详细介绍机械加工质量控制的标准格式,包括质量控制的目标、方法和流程。
二、质量控制目标1. 保证加工零件的尺寸精度符合设计要求。
通过合理的加工工艺和工艺参数控制,确保零件的尺寸精度在允许范围内,避免尺寸偏差过大导致零件无法装配或者使用。
2. 确保加工零件的表面质量符合要求。
通过适当的加工方法和工艺控制,保证零件表面光洁度、平整度和粗糙度等指标满足设计要求,提高零件的外观质量和使用寿命。
3. 控制加工零件的几何形状符合要求。
通过合理的加工工艺和工艺参数控制,确保零件的几何形状符合设计要求,避免因几何形状偏差过大导致零件无法装配或者使用。
4. 确保加工过程的稳定性和可控性。
通过制定合理的工艺规程和操作规范,控制加工过程中的各项参数,保证加工过程的稳定性和可控性,提高加工质量的一致性和稳定性。
三、质量控制方法1. 设计质量控制计划。
根据加工零件的具体要求和技术要求,制定质量控制计划,明确质量控制的目标和方法。
2. 制定加工工艺规程。
根据加工零件的特点和要求,制定合理的加工工艺规程,包括加工工序、工艺参数、加工设备和工具等。
3. 制定操作规范。
根据加工工艺规程,制定操作规范,明确操作人员的职责和要求,确保加工过程的规范性和一致性。
4. 控制加工设备和工具的状态。
定期检查和维护加工设备和工具,保证其正常运行和准确度,避免因设备和工具的损坏或者失效导致加工质量下降。
5. 严格控制加工过程中的各项参数。
在加工过程中,严格控制加工速度、切削深度、冷却液的使用量和温度等参数,确保加工过程的稳定性和可控性。
6. 进行质量检验和测试。
在加工完成后,进行质量检验和测试,包括尺寸测量、表面质量检查和几何形状测量等,确保加工零件的质量符合要求。
7. 进行过程监控和数据分析。
通过对加工过程中的数据进行监控和分析,及时发现和解决加工质量问题,提高加工过程的稳定性和可控性。
机械加工质量控制
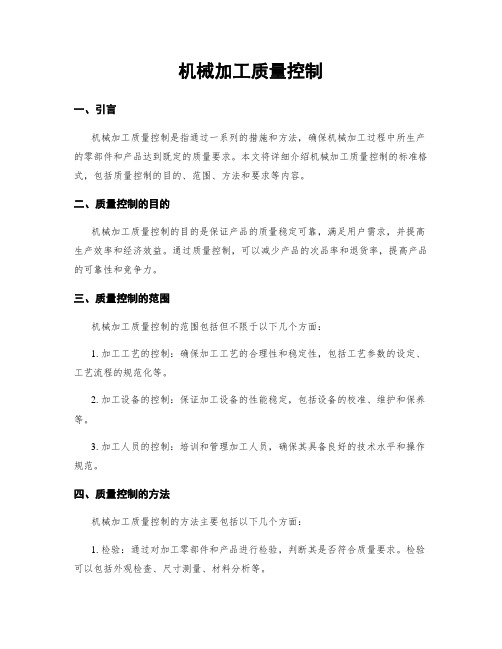
机械加工质量控制一、引言机械加工质量控制是指通过一系列的措施和方法,确保机械加工过程中所生产的零部件和产品达到既定的质量要求。
本文将详细介绍机械加工质量控制的标准格式,包括质量控制的目的、范围、方法和要求等内容。
二、质量控制的目的机械加工质量控制的目的是保证产品的质量稳定可靠,满足用户需求,并提高生产效率和经济效益。
通过质量控制,可以减少产品的次品率和退货率,提高产品的可靠性和竞争力。
三、质量控制的范围机械加工质量控制的范围包括但不限于以下几个方面:1. 加工工艺的控制:确保加工工艺的合理性和稳定性,包括工艺参数的设定、工艺流程的规范化等。
2. 加工设备的控制:保证加工设备的性能稳定,包括设备的校准、维护和保养等。
3. 加工人员的控制:培训和管理加工人员,确保其具备良好的技术水平和操作规范。
四、质量控制的方法机械加工质量控制的方法主要包括以下几个方面:1. 检验:通过对加工零部件和产品进行检验,判断其是否符合质量要求。
检验可以包括外观检查、尺寸测量、材料分析等。
2. 检测:利用各种检测设备和仪器,对加工过程中的关键参数进行实时监测和控制。
例如,使用温度传感器监测加工温度,使用压力传感器监测加工压力等。
3. 统计分析:通过统计分析加工过程中的数据,找出问题的根源,并采取相应的措施进行改进。
例如,使用控制图分析加工过程中的变异情况,找出异常点并进行调整。
五、质量控制的要求机械加工质量控制的要求主要包括以下几个方面:1. 严格遵守质量标准:加工过程中必须严格按照像关的质量标准进行操作,确保产品符合质量要求。
2. 完善的质量管理体系:建立完善的质量管理体系,包括质量目标的设定、质量文件的编制、质量记录的管理等。
3. 持续改进:通过持续改进的方式,不断提高机械加工质量控制的水平和效果。
可以采用PDCA循环模式,即计划、执行、检查和行动,进行质量管理的持续改进。
六、结论机械加工质量控制是确保产品质量的重要手段,对于提高企业的竞争力和市场占有率具有重要意义。
机械加工质量控制
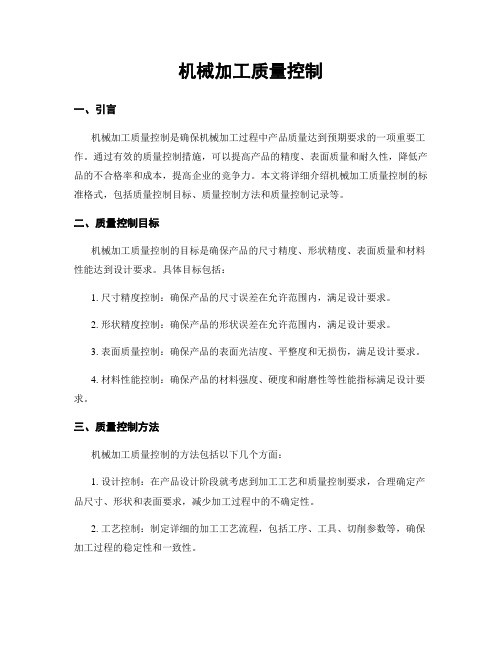
机械加工质量控制一、引言机械加工质量控制是确保机械加工过程中产品质量达到预期要求的一项重要工作。
通过有效的质量控制措施,可以提高产品的精度、表面质量和耐久性,降低产品的不合格率和成本,提高企业的竞争力。
本文将详细介绍机械加工质量控制的标准格式,包括质量控制目标、质量控制方法和质量控制记录等。
二、质量控制目标机械加工质量控制的目标是确保产品的尺寸精度、形状精度、表面质量和材料性能达到设计要求。
具体目标包括:1. 尺寸精度控制:确保产品的尺寸误差在允许范围内,满足设计要求。
2. 形状精度控制:确保产品的形状误差在允许范围内,满足设计要求。
3. 表面质量控制:确保产品的表面光洁度、平整度和无损伤,满足设计要求。
4. 材料性能控制:确保产品的材料强度、硬度和耐磨性等性能指标满足设计要求。
三、质量控制方法机械加工质量控制的方法包括以下几个方面:1. 设计控制:在产品设计阶段就考虑到加工工艺和质量控制要求,合理确定产品尺寸、形状和表面要求,减少加工过程中的不确定性。
2. 工艺控制:制定详细的加工工艺流程,包括工序、工具、切削参数等,确保加工过程的稳定性和一致性。
3. 设备控制:确保加工设备的准确度和稳定性,定期进行设备维护和校准,提高加工精度和稳定性。
4. 刀具控制:选择合适的刀具材料和刀具几何参数,确保切削过程的稳定性和切削质量。
5. 检测控制:制定详细的检测方案和检测标准,对加工过程中的关键尺寸、形状和表面进行检测和测量,及时发现问题并进行调整。
6. 过程控制:对加工过程中的关键参数进行实时监控和控制,确保加工过程的稳定性和一致性。
7. 人员控制:培训和管理加工人员,提高其加工技能和质量意识,确保操作规范和质量要求的达到。
四、质量控制记录机械加工质量控制的记录主要包括以下几个方面:1. 工艺文件:记录加工工艺流程、刀具选择和切削参数等信息。
2. 设备维护记录:记录设备的维护和校准情况,包括维护时间、维护内容和维护人员等。
机械加工质量控制
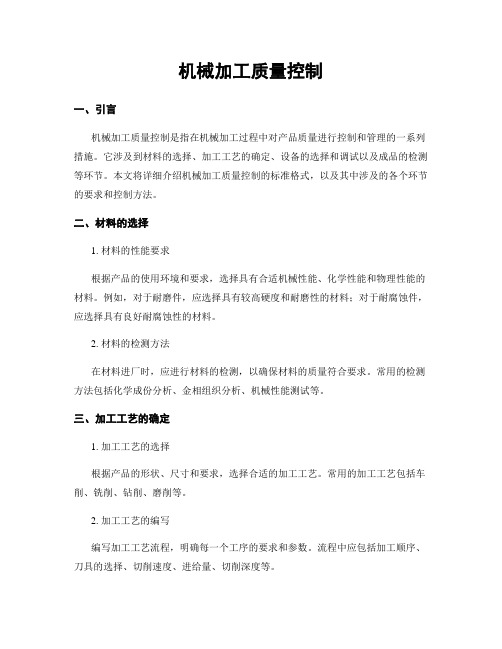
机械加工质量控制一、引言机械加工质量控制是指在机械加工过程中对产品质量进行控制和管理的一系列措施。
它涉及到材料的选择、加工工艺的确定、设备的选择和调试以及成品的检测等环节。
本文将详细介绍机械加工质量控制的标准格式,以及其中涉及的各个环节的要求和控制方法。
二、材料的选择1. 材料的性能要求根据产品的使用环境和要求,选择具有合适机械性能、化学性能和物理性能的材料。
例如,对于耐磨件,应选择具有较高硬度和耐磨性的材料;对于耐腐蚀件,应选择具有良好耐腐蚀性的材料。
2. 材料的检测方法在材料进厂时,应进行材料的检测,以确保材料的质量符合要求。
常用的检测方法包括化学成份分析、金相组织分析、机械性能测试等。
三、加工工艺的确定1. 加工工艺的选择根据产品的形状、尺寸和要求,选择合适的加工工艺。
常用的加工工艺包括车削、铣削、钻削、磨削等。
2. 加工工艺的编写编写加工工艺流程,明确每一个工序的要求和参数。
流程中应包括加工顺序、刀具的选择、切削速度、进给量、切削深度等。
四、设备的选择和调试1. 设备的选择根据产品的形状、尺寸和要求,选择适合的加工设备。
设备应具备稳定性好、精度高、刚性强等特点。
2. 设备的调试设备调试是确保机械加工质量的重要环节。
调试时应检查设备的各项参数是否符合要求,如刀具的安装是否正确、切削液的供给是否稳定等。
五、成品的检测1. 检测方法的选择根据产品的要求,选择合适的检测方法。
常用的检测方法包括三坐标测量、硬度测试、表面粗糙度测试等。
2. 检测标准的制定根据产品的要求和标准,制定相应的检测标准。
标准中应包括尺寸偏差、形状偏差、表面质量等指标。
六、质量控制的记录和分析1. 质量记录的要求在机械加工过程中,应及时记录各个环节的质量参数和检测结果。
记录应包括日期、操作人员、设备参数、加工工艺、检测结果等。
2. 质量分析的方法根据质量记录,进行质量分析,找出产生质量问题的原因,并采取相应的措施进行改进。
常用的质量分析方法包括鱼骨图、因果图、直方图等。
机械加工质量控制

机械加工质量控制一、引言机械加工质量控制是指在机械加工过程中,通过采取一系列措施和方法,确保加工零件的质量符合设计要求。
良好的机械加工质量控制能够提高产品的精度、表面质量和使用寿命,降低成本和不良率,提高客户满意度。
本文将详细介绍机械加工质量控制的标准格式。
二、加工前的准备1. 确定加工工艺:根据零件的设计要求和加工工艺手册,确定适合的加工工艺,包括加工方法、工艺参数等。
2. 准备加工设备:确保加工设备的正常运行,包括机床、刀具、夹具等。
3. 准备加工材料:选择符合设计要求的加工材料,并进行质量检查,确保材料质量符合标准。
三、加工过程的质量控制1. 加工前的检查:在进行机械加工之前,对加工设备和刀具进行检查,确保其正常运行和良好状态。
2. 加工参数的确定:根据零件的设计要求和加工工艺手册,确定加工参数,包括切削速度、进给量、切削深度等。
3. 加工过程的监控:在加工过程中,通过仪器设备对加工参数进行实时监控,确保加工过程的稳定性和精度。
4. 加工质量的检验:对加工后的零件进行质量检验,包括尺寸、形状、表面质量等指标的检测,确保加工质量符合设计要求。
5. 不良品的处理:如果发现加工出的零件存在质量问题,及时进行处理,包括修复、返工或重新加工等。
四、加工后的质量控制1. 零件的清洁:对加工完成的零件进行清洁,去除表面的污垢和切削液,确保零件的表面质量。
2. 零件的防锈处理:根据零件的材料和使用环境,对加工完成的零件进行防锈处理,防止零件在运输和存储过程中受到腐蚀。
3. 零件的包装:根据客户要求和运输方式,对加工完成的零件进行适当的包装,确保零件在运输过程中不受损坏。
五、质量记录和报告1. 质量记录:对加工过程中的关键参数和检验结果进行记录,包括加工参数、检验数据、不良品处理记录等。
2. 质量报告:根据客户要求,编制加工质量报告,包括加工过程的质量控制情况、检验结果、不良品处理情况等。
六、质量改进措施1. 定期评估:定期对机械加工质量控制的效果进行评估,发现问题并采取相应的改进措施。
农产品加工质量控制检验标准
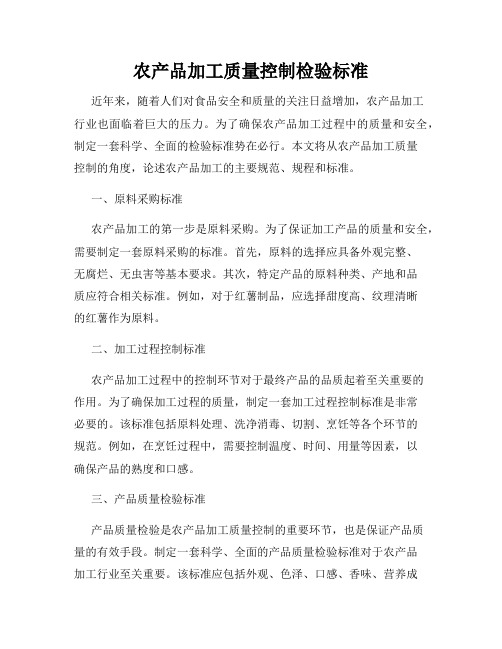
农产品加工质量控制检验标准近年来,随着人们对食品安全和质量的关注日益增加,农产品加工行业也面临着巨大的压力。
为了确保农产品加工过程中的质量和安全,制定一套科学、全面的检验标准势在必行。
本文将从农产品加工质量控制的角度,论述农产品加工的主要规范、规程和标准。
一、原料采购标准农产品加工的第一步是原料采购。
为了保证加工产品的质量和安全,需要制定一套原料采购的标准。
首先,原料的选择应具备外观完整、无腐烂、无虫害等基本要求。
其次,特定产品的原料种类、产地和品质应符合相关标准。
例如,对于红薯制品,应选择甜度高、纹理清晰的红薯作为原料。
二、加工过程控制标准农产品加工过程中的控制环节对于最终产品的品质起着至关重要的作用。
为了确保加工过程的质量,制定一套加工过程控制标准是非常必要的。
该标准包括原料处理、洗净消毒、切割、烹饪等各个环节的规范。
例如,在烹饪过程中,需要控制温度、时间、用量等因素,以确保产品的熟度和口感。
三、产品质量检验标准产品质量检验是农产品加工质量控制的重要环节,也是保证产品质量的有效手段。
制定一套科学、全面的产品质量检验标准对于农产品加工行业至关重要。
该标准应包括外观、色泽、口感、香味、营养成分等方面的指标。
例如,在果蔬加工行业中,可以通过测量产品的果汁含量、维生素含量等指标来评估产品的质量。
四、加工设备维护管理标准加工设备的正常运行和维护对于产品质量的控制至关重要。
为了确保加工设备的稳定性和安全性,制定一套加工设备维护管理标准是必不可少的。
该标准应包括定期维护、检修和清洁等方面的要求。
例如,在食品罐头加工中,需要对设备进行定期的清洗和消毒,以避免细菌污染。
五、标准操作程序规范农产品加工行业需要制定一套标准操作程序规范,以确保加工过程的一致性和可重复性。
该规范应包含原料处理、加工操作、质量检验等环节的具体操作步骤和要求。
例如,在面食加工中,需要规定面团的揉捏时间、加水量和发酵时间等操作细节,以确保产品的质量和口感。
金属加工行业中的质量控制标准与要求

金属加工行业中的质量控制标准与要求在金属加工行业中,质量控制是确保产品质量和客户满意度的重要环节。
合理的质量控制标准和要求能够有效地提高产品的精确度、可靠性和稳定性。
本文将探讨金属加工行业中的质量控制标准与要求,并阐述其在提高产品质量和生产效率方面的重要性。
1. 材料选择与测试在金属加工行业中,首先要保证所使用的原材料符合质量要求。
这包括材料的成分检测、物理性能测试以及表面质量评估等。
通过严格的材料测试,可以确保所使用的金属材料具有良好的可加工性和优异的机械性能,以满足客户的要求。
2. 设备校准与维护金属加工过程中所使用的设备和机器必须经过定期校准和维护,以确保其精度和可靠性。
这包括设备的准确校准、润滑油的更换以及零部件的检修等。
只有保持设备的良好状态,才能够保证产品加工的精度和稳定性。
3. 工艺控制金属加工过程中的工艺控制是确保产品质量的关键环节。
这包括工序的参数设定、工件的夹持和定位、刀具的选择和切削参数的调整等。
通过严格控制工艺参数,可以避免加工过程中出现的问题,如尺寸偏差和划伤等,从而提高产品的质量和加工效率。
4. 检验与测试在金属加工行业中,对于加工后的产品必须进行严格的检验和测试,以确保其符合客户的要求和行业标准。
这包括尺寸测量、表面质量评估和性能测试等。
通过检验和测试,可以及时发现产品质量问题,并采取相应措施进行调整和改进,以提高产品质量和客户满意度。
5. 数据分析与改进金属加工行业中,对于质量控制标准和要求的有效性必须进行数据分析和改进。
通过收集和分析质量数据,可以及时发现潜在问题和改进机会,进而调整和完善质量控制标准和要求。
同时,还可以通过不断改进工艺流程和设备性能来提高产品质量和生产效率。
总结起来,金属加工行业中的质量控制标准与要求是确保产品质量和客户满意度的重要保障。
通过材料选择与测试、设备校准与维护、工艺控制、检验与测试以及数据分析与改进等环节的严格把控,可以提高产品的精确度、可靠性和稳定性,从而满足客户的需求,并在竞争激烈的市场中取得竞争优势。
机械加工质量控制

机械加工质量控制一、引言机械加工是制造业中一项重要的工艺,它涉及到各种材料的切削、成型、打磨等加工过程。
为了确保机械加工产品的质量,需要进行严格的质量控制。
本文将介绍机械加工质量控制的标准格式,包括质量控制目标、质量控制方法、质量控制指标等内容。
二、质量控制目标1. 提高产品质量机械加工质量控制的首要目标是提高产品的质量。
通过控制加工过程中的各个环节,确保产品的尺寸精度、表面光洁度、装配精度等指标符合设计要求,从而提高产品的质量水平。
2. 减少不良品率不良品率是衡量机械加工质量的重要指标之一。
通过引入合理的质量控制方法和工艺流程,以及严格的质量检测标准,可以有效地减少不良品的产生,降低不良品率,提高生产效率和经济效益。
3. 提高生产效率机械加工质量控制的另一个重要目标是提高生产效率。
通过合理的工艺优化和工艺改进,减少加工时间、提高加工精度,降低生产成本,提高生产效率。
三、质量控制方法1. 设计合理的工艺流程在机械加工过程中,设计合理的工艺流程是确保产品质量的基础。
工艺流程应包括材料选择、工艺路线、工艺参数等内容,确保每个工序的加工顺序和方法都合理可行,并能满足产品的质量要求。
2. 严格执行质量检测标准质量检测是机械加工质量控制中不可或缺的环节。
根据产品的设计要求和相关标准,制定相应的质量检测标准,包括尺寸、表面质量、硬度等指标的检测方法和要求。
在每个工序结束后,进行相应的质量检测,确保产品符合标准要求。
3. 引入自动化设备和技术自动化设备和技术的应用可以提高机械加工的质量和效率。
例如,数控机床可以实现精确的加工控制,提高加工精度和稳定性;机器视觉技术可以实现对产品表面缺陷的自动检测,提高检测效率和准确性。
四、质量控制指标1. 尺寸精度尺寸精度是机械加工产品质量的重要指标之一。
它包括线性尺寸、角度、平行度、垂直度等方面的精度要求。
通过控制加工过程中的刀具选择、切削速度、进给量等参数,以及合理的夹持和定位方式,可以实现产品尺寸精度的控制。
机械加工质量控制
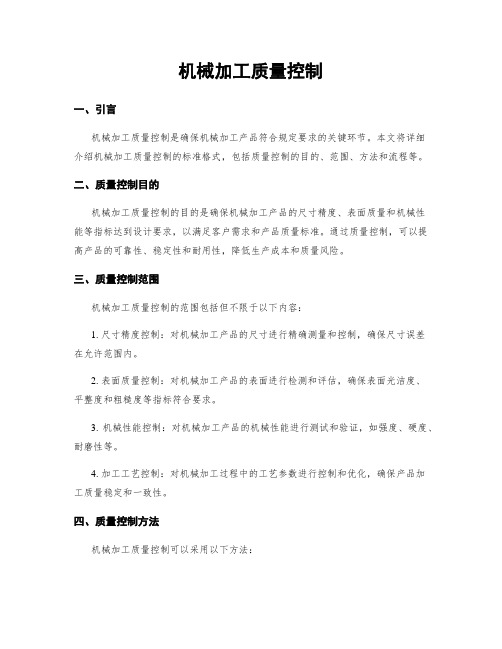
机械加工质量控制一、引言机械加工质量控制是确保机械加工产品符合规定要求的关键环节。
本文将详细介绍机械加工质量控制的标准格式,包括质量控制的目的、范围、方法和流程等。
二、质量控制目的机械加工质量控制的目的是确保机械加工产品的尺寸精度、表面质量和机械性能等指标达到设计要求,以满足客户需求和产品质量标准。
通过质量控制,可以提高产品的可靠性、稳定性和耐用性,降低生产成本和质量风险。
三、质量控制范围机械加工质量控制的范围包括但不限于以下内容:1. 尺寸精度控制:对机械加工产品的尺寸进行精确测量和控制,确保尺寸误差在允许范围内。
2. 表面质量控制:对机械加工产品的表面进行检测和评估,确保表面光洁度、平整度和粗糙度等指标符合要求。
3. 机械性能控制:对机械加工产品的机械性能进行测试和验证,如强度、硬度、耐磨性等。
4. 加工工艺控制:对机械加工过程中的工艺参数进行控制和优化,确保产品加工质量稳定和一致性。
四、质量控制方法机械加工质量控制可以采用以下方法:1. 抽样检验:根据产品的批量和重要性,采取抽样检验的方式进行质量控制。
通过抽样检验,可以评估整体批次的产品质量水平。
2. 在线检测:在机械加工过程中设置检测装置,对关键工序进行实时检测,及时发现和纠正加工质量问题。
3. 检测设备:使用合适的检测设备,如三坐标测量机、硬度计、光学显微镜等,对机械加工产品进行精确测量和评估。
4. 数据分析:通过对质量控制数据的统计和分析,发现质量问题的规律和原因,采取相应的改进措施,提高产品质量。
五、质量控制流程机械加工质量控制的流程如下:1. 制定质量控制计划:根据产品特点和客户需求,制定质量控制计划,明确质量控制的目标、方法和要求。
2. 设定质量指标:根据产品设计要求和标准,确定尺寸精度、表面质量和机械性能等指标的要求和容差范围。
3. 设计检测方案:根据质量指标和产品特点,设计合适的检测方案,确定检测方法、设备和检测点。
4. 进行质量控制:在机械加工过程中,按照质量控制计划和检测方案进行质量控制,包括工艺控制、尺寸检测、表面检测和机械性能测试等。
机械加工过程中的质量控制精简版范文

机械加工过程中的质量控制精简版范文在机械加工行业中,质量控制是工厂能否获得成功和留住客户的关键因素。
质量控制的目的是确保产品的符合设计要求,减少产品制造过程中的资源浪费和损失,提高产品的可靠性和性能。
本文将介绍机械加工过程中的质量控制精简版范文。
第一部分:质量目标和指标1.质量目标:我们的质量目标是提供高质量的机械加工产品,满足客户的需求和期望。
我们致力于零缺陷的生产,并通过提高工艺流程、提高产品设计和制造的一致性来降低产品的无效和返工率。
2.质量指标:我们将采用以下几项关键质量指标来衡量我们的质量绩效:-产品合格率:对于每批次产品,合格品的比例不能低于98%。
-产品缺陷率:对于每批次产品,缺陷品的比例不能超过2%。
-产品交付准时率:确保按照客户的要求准时交付产品,不推迟交货。
第二部分:质量控制措施1.原材料采购控制:在采购原材料时,我们将与供应商建立合作关系,并要求供应商提供质量保证和检测报告。
我们将对原材料进行入库检验,确保其符合设计要求和质量标准。
2.工艺流程控制:我们将制定详细的工艺流程和作业指导书,确保每个工序的操作规范和标准化。
所有员工必须经过培训和考核,确保他们熟悉工艺流程和要求,并能够正确操作设备。
3.设备维护和校准:我们将定期维护和校准机械设备,确保其正常运行和准确度。
我们将建立设备维护记录和校准记录,以跟踪设备的运行情况和性能。
4.在线检测和抽样检验:我们将在生产过程中进行在线检测,及时发现问题和缺陷,并采取纠正措施。
我们还将进行抽样检验,以验证产品的质量和符合性。
5.过程改进和缺陷分析:我们将建立过程改进和缺陷分析机制,不断优化工艺流程和产品设计,提高产品质量和生产效率。
我们将收集和分析不合格品的数据,并采取措施防止类似问题再次发生。
第三部分:质量管理体系和认证1.质量管理体系:我们将建立质量管理体系,包括质量手册、程序文件和记录表,以规范和记录质量控制活动。
我们将制定质量管理指导方针和目标,并进行定期评审和持续改进。
钢筋加工及码放质量控制标准

钢筋加工及码放质量控制标准
一.钢筋加工
1.再加工前,项目部必须进行技术交底从构造,加工精度提出严格要求;并将各种要
求以图文的形式反应到施工现场。
2.钢筋断料时,先严格审查料单,做到“统筹兼顾,长短结合”。
3.箍筋、梯子筋、马凳、双卡的加工先由项目技术负责人根据使用部位结构尺寸情况
画出加工详图。
4.钢筋成型后,经质检员,钢筋工长检查验收合格后方可使用。
5.经常检查机械工作状态,检查零部件是否损坏,转轴,刀口是否存在加工精度等问
题,有问题时,及时向项目部钢筋工长反映便于更换解决。
加工机械保持良好工作状态。
6.钢筋加工完成后,分类堆放,并挂好料牌布,注明钢筋的型号外型尺寸数量及使用
部位。
7.实行样板先行的制度,每种箍筋、梯子筋以实物样板挂于加工现场,并加以说明。
样板通过验收后,然后按样板加工。
二.钢筋的码放:
1.钢筋堆放场地进行硬化,并有排水措施,钢筋堆放必须放于混凝土台上,并防止钢
筋污染。
2.不同型号的钢筋分类堆放,按材料计划进场,先进的钢筋先用,材料员挂好钢筋标
示牌,注明进场日期。
3.加工完毕的成品钢筋必须分段、区、分部位码放整齐,并挂好料牌布料牌布上注明
钢筋的规格、数量。
4.钢筋现场堆放整齐堆放场地进行硬化,下垫方木。
雨天覆盖塑料布。
钢结构加工制作各工序质量控制标准
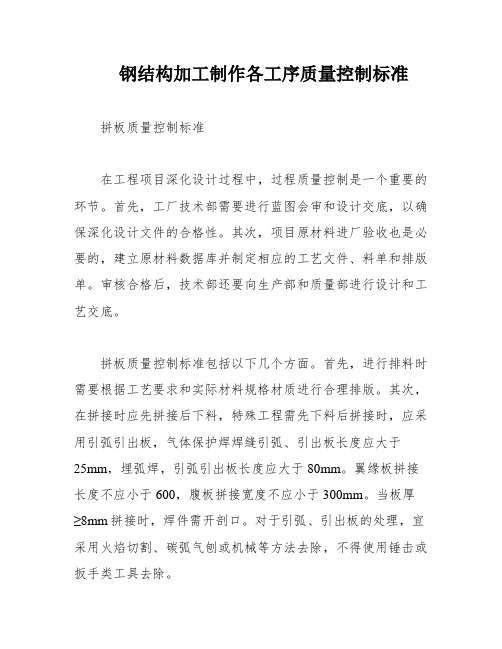
钢结构加工制作各工序质量控制标准拼板质量控制标准在工程项目深化设计过程中,过程质量控制是一个重要的环节。
首先,工厂技术部需要进行蓝图会审和设计交底,以确保深化设计文件的合格性。
其次,项目原材料进厂验收也是必要的,建立原材料数据库并制定相应的工艺文件、料单和排版单。
审核合格后,技术部还要向生产部和质量部进行设计和工艺交底。
拼板质量控制标准包括以下几个方面。
首先,进行排料时需要根据工艺要求和实际材料规格材质进行合理排版。
其次,在拼接时应先拼接后下料,特殊工程需先下料后拼接时,应采用引弧引出板,气体保护焊焊缝引弧、引出板长度应大于25mm,埋弧焊,引弧引出板长度应大于80mm。
翼缘板拼接长度不应小于600,腹板拼接宽度不应小于300mm。
当板厚≥8mm拼接时,焊件需开剖口。
对于引弧、引出板的处理,宜采用火焰切割、碳弧气刨或机械等方法去除,不得使用锤击或扳手类工具去除。
在焊接过程中,一、二级焊缝需要100%报检,UT合格,其余焊缝需要外观检查,焊接变形矫正需要报检,检验比例为30%。
成品拼装需要进行地模100%报检,钢梁、屋面梁制孔、筋板、孔板拼装成品报验,检验比例为100%。
同时,抛丸、摩擦面加工、除锈、打磨、涂装也需要进行报验,检验比例为50%。
最后,成品终检需要100%进行检验,并对编号移植和标识进行检查,发货员对构件数量清点移交100%全数检验。
合格证签发后,构件才能出厂。
以上是拼板质量控制标准的具体要求,其中包括了排料、拼板、焊接、抛丸、摩擦面加工、除锈、打磨和涂装等方面。
在拼接时需要注意各项细节,例如焊件开剖口、引弧引出板的处理等。
焊接过程中需要进行严格的检验,确保焊缝的质量。
最终成品需要进行终检,并对编号移植和标识进行检查,确保构件的质量符合标准。
5、在拼装钢梁、钢柱时,必须对准眼孔进行定位。
如果有多层牛腿在同一直线上,那么牛腿拼装面也必须在同一直线上(通过拉线检查)。
6、对于相同批量的构件,半成品拼装时必须标识构件编号和构件流水号,而成品构件则必须标识构件编号和轴线号。
机械加工质量控制
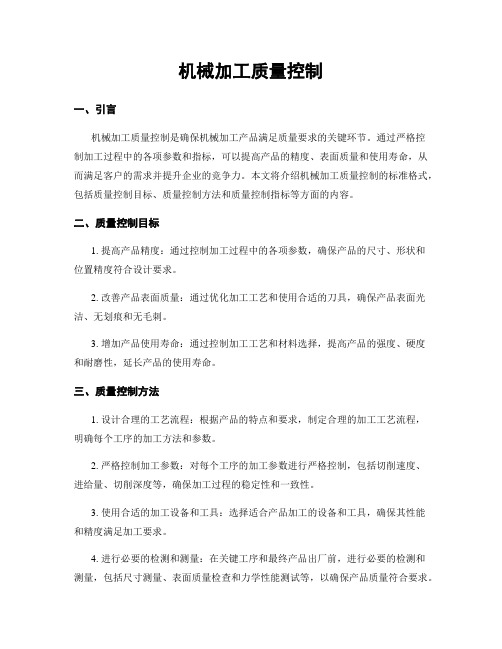
机械加工质量控制一、引言机械加工质量控制是确保机械加工产品满足质量要求的关键环节。
通过严格控制加工过程中的各项参数和指标,可以提高产品的精度、表面质量和使用寿命,从而满足客户的需求并提升企业的竞争力。
本文将介绍机械加工质量控制的标准格式,包括质量控制目标、质量控制方法和质量控制指标等方面的内容。
二、质量控制目标1. 提高产品精度:通过控制加工过程中的各项参数,确保产品的尺寸、形状和位置精度符合设计要求。
2. 改善产品表面质量:通过优化加工工艺和使用合适的刀具,确保产品表面光洁、无划痕和无毛刺。
3. 增加产品使用寿命:通过控制加工工艺和材料选择,提高产品的强度、硬度和耐磨性,延长产品的使用寿命。
三、质量控制方法1. 设计合理的工艺流程:根据产品的特点和要求,制定合理的加工工艺流程,明确每个工序的加工方法和参数。
2. 严格控制加工参数:对每个工序的加工参数进行严格控制,包括切削速度、进给量、切削深度等,确保加工过程的稳定性和一致性。
3. 使用合适的加工设备和工具:选择适合产品加工的设备和工具,确保其性能和精度满足加工要求。
4. 进行必要的检测和测量:在关键工序和最终产品出厂前,进行必要的检测和测量,包括尺寸测量、表面质量检查和力学性能测试等,以确保产品质量符合要求。
5. 定期维护和保养设备:定期对加工设备进行维护和保养,保证设备的正常运行和精度稳定。
四、质量控制指标1. 尺寸精度:包括线性尺寸精度、角度精度和形位公差等指标,根据产品的要求进行测量和评定。
2. 表面质量:包括表面光洁度、划痕和毛刺等指标,通过目视检查和触摸检测进行评定。
3. 材料性能:包括硬度、强度和耐磨性等指标,通过力学性能测试和金相分析等方法进行评定。
4. 加工工艺参数:包括切削速度、进给量和切削深度等指标,通过实际加工过程中的记录和测量进行评定。
五、总结机械加工质量控制是确保产品质量的重要环节,通过合理的质量控制目标、质量控制方法和质量控制指标,可以提高产品的精度、表面质量和使用寿命。
钢结构加工制作各工序质量控制标准
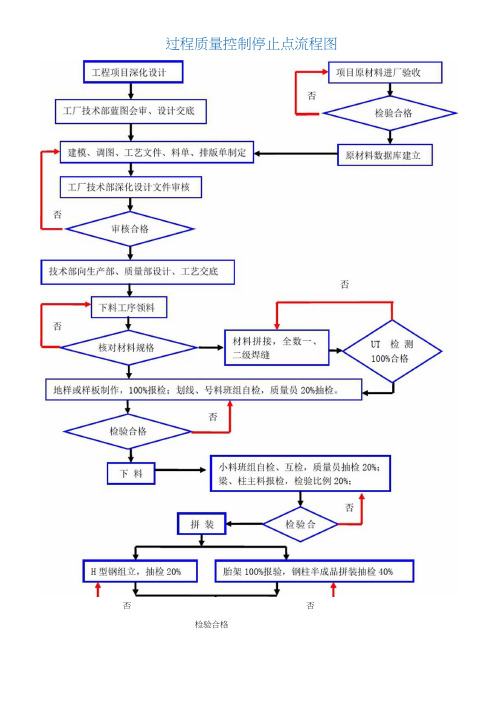
过程质量控制停止点流程图否检验合格成品拼装地模100%报检,钢梁、屋而梁制孔、筋板、孔板拼装成品报验,检验比例100%:成品钢柱牛腿、刀板拼装报验,检验比例100 %以上。
拼板质量控制标准1、排料:根据工艺要求及实际材料的规格材质进行合理排版。
2、拼板、先拼接后下料,特殊工程需先下料后拼接时,应采用引弧引出板,气体保护焊焊缝引弧、引岀板长度应大于25mm,埋弧焊,引弧引出板长度应大于80mm□、翼缘板拼接长度不应小于600,腹板拼接宽度不应小于300mm.、当板厚28mm拼接时,焊件需开剖口。
首先用碳弧气刨淸根必须刨到背面原焊缝焊肉,其次使用角磨机进行打磨(打磨至表而金属光泽无夹渣、气孔、裂纹等缺陷)时,最后进行焊接。
、引弧、引出板宜采用火焰切割、碳弧气刨或机械等方法去除,去除时不得伤及母材并将切割口处修磨至与焊缝端部平整。
严禁使用锤击或扳手类工具去除引弧引出板。
、不得在焊区以外的母材上引弧,电弧擦伤的焊疤应打磨干净:构件焊接完毕,焊工应清理焊缝表面的熔渣及两侧飞溅物。
对接焊缝缝隙两侧边不允许存在弧坑、缺口等焊接缺陷。
、对接焊缝外形尺寸规泄:下料质量控制标准下料1、放样、号料.放样下料所用的钢尺、量具须经il鱼部门检验合格后方可使用。
.严格按照放样排版图进行号料、放样,特别注意材质、板厚是否相符,且钢板号料时去除“生边”边缘5 〜10mm ..•放样和号料应根据工艺要求预留制作和安装时的焊接收缩量及切割加工余呈:。
注所下材料必须符合下列要求:焊接H型钢的翼缘板拼接缝和腹板拼接缝的间距不应小于200mm。
翼缘板拼接长度不应小于600mm;腹板拼接宽度不应小于300mm,长度不应小于600mm。
.样板、地样必须全部检查,检验合格后方可使用或切割(异形零件、部件直接在钢板上放样、划线时必须按90°坐标作图方法进行放样、划线,基准线必须用墨线淸晰弹出)。
•放样时平行线距离和分段尺寸,允许偏差± 1mm。
冷冻食品加工质量控制质量技术标准

冷冻食品加工质量控制质量技术标准一、引言随着人们对食品安全和便捷性的要求不断提高,冷冻食品在当代社会中占据了重要地位。
为了确保冷冻食品的质量和安全性,并满足消费者对食品的需求,制定冷冻食品加工质量控制的技术标准至关重要。
二、原料选择与检验1. 原料选择冷冻食品加工的质量控制首先需要选择优质的原料。
原料应符合国家相关食品安全标准,不得含有违禁添加物和有害微生物。
同时,优质原料在质地、营养成分和口感上也应达到预期要求。
2. 原料检验在进行加工前,对原料进行全面的检验是确保冷冻食品质量的关键。
原料检验应包括外观、味道、气味等指标的检测,以及营养成分、微生物和重金属等的化验分析。
三、加工工艺控制1. 温度控制冷冻食品的加工过程中,温度控制至关重要。
合理的冷冻温度能够保持食品的营养成分和口感,同时能避免细菌滋生和食品变质。
加工过程中的温度应根据具体产品而定,确保达到最佳冷冻效果。
2. 质量指标要求不同的冷冻食品具有不同的质量要求。
在制定技术标准时,应明确食品的质量指标,如外观色泽、质地、气味和口感等。
同时,对于特殊要求的冷冻食品,还需要制定相应的特殊质量指标。
四、包装和储存1. 包装要求冷冻食品的包装是保护其质量和延长保质期的重要环节。
包装材料应符合国家相关标准,无刺激性气味,能够有效防止食品的水分蒸发和氧气进入,防止细菌污染和营养成分流失。
2. 储存条件冷冻食品的储存条件直接影响其质量和安全性。
储存环境应保持干燥、清洁,温度应符合冷冻食品的要求。
同时,冷冻食品应在规定的保质期内存放,并有相应的储存记录和追溯机制。
五、质量控制管理1. 质量标准冷冻食品加工企业应制定适用于自身产品的质量标准,确保产品符合国家相关规定。
质量标准应包括原料选择和检验、加工工艺控制、包装要求和储存条件等各个环节。
2. 抽检和监控冷冻食品加工企业应建立相应的抽检和监控机制,定期对成品和原料进行抽样检验。
同时,通过对生产过程的监控,发现并纠正潜在的质量问题,确保产品质量的稳定性和可靠性。
机床加工质量控制标准

机床加工质量控制标准1. 前言机床加工是制造业中至关重要的一个环节,对于保证产品质量、提高生产效率具有重要意义。
为了确保机床加工质量的稳定和可靠,制定和执行一套规范的标准变得十分必要。
本文将从机床选型、工艺规范、设备调试、操作规程以及质量检验等方面,对机床加工质量控制标准进行论述。
2. 机床选型标准机床选型是机床加工质量的首要保障。
在选型过程中,需考虑到所加工零部件的特点、精度要求、生产批量以及加工目标等因素。
根据不同的加工需求,选择适当的机床类型和规格,确保机床能够满足加工要求。
3. 工艺规范标准在机床加工过程中,工艺规范起着关键性作用。
工艺规范包括加工工艺、工序划分、切削参数、装夹方式、刀具选择等内容。
根据不同的加工对象,确定合理的工艺规范,确保加工零部件满足技术要求和设计要求。
4. 设备调试标准设备调试是保证机床正常运行的重要环节。
在设备调试中,需要对机床进行功能性测试、精度测试、定位精度测试以及加工试验等。
这些测试能够有效评估机床性能,及时发现并解决设备存在的问题,保证机床运行的稳定和可靠性。
5. 操作规程标准机床的正常操作与维护是对机床加工质量控制不可或缺的一环。
制定出一套合理、系统的操作规程标准,能够确保操作人员正确地使用机床、保障机床正常运转,并降低因操作失误导致的质量问题。
6. 质量检验标准质量检验是对机床加工质量进行实时监控和验证的重要手段。
制定出一套完善的质量检验标准,包括检验方法、检测设备、合格标准等内容,能够确保加工零部件的尺寸、形状、表面质量以及机械性能等达到设计要求。
7. 总结机床加工质量控制标准是保证机床加工质量的重要保障。
通过机床选型标准、工艺规范标准、设备调试标准、操作规程标准以及质量检验标准的制定和执行,能够确保机床加工的稳定性、可靠性和一致性,提高产品质量水平,满足市场需求。
然而,值得注意的是,机床加工质量控制标准的制定和执行不是一成不变的,而是与时俱进的。
加工质量标准

加工质量标准一、精度控制精度控制是加工质量标准的核心,包括以下几个方面:尺寸精度:加工后的零件尺寸应符合设计要求,误差应在规定范围内。
形状精度:加工后的零件形状应符合设计要求,如圆度、直线度、平面度等。
位置精度:加工后的零件各部分之间的相对位置应符合设计要求。
表面粗糙度:加工后的零件表面应具有合适的粗糙度,以满足使用要求。
二、表面质量表面质量是评价加工质量的重要指标,包括以下几个方面:表面粗糙度:如前所述。
表面硬化层:加工后的零件表面应具有适当的硬化层,以提高耐磨性和耐腐蚀性。
表面残余应力:加工后的零件表面应无残余应力,以免在使用过程中出现变形和裂纹。
表面金相组织:应根据材料性质和加工要求,控制表面金相组织的类型和分布。
三、几何尺寸几何尺寸是评价加工质量的基本指标,包括以下几个方面:长度、宽度、高度:加工后的零件各方向尺寸应符合设计要求。
平行度、垂直度、角度:加工后的零件各方向之间应保持正确的平行度、垂直度和角度。
同轴度、对称度:对于有多个相同部分的零件,其同轴度和对称度应达到一定要求。
四、形状精度形状精度是评价加工质量的重要指标,包括以下几个方面:圆度、直线度、平面度:加工后的零件形状应符合设计要求。
圆柱度、圆锥度:加工后的零件圆柱度和圆锥度应达到一定要求。
曲线加工精度:对于复杂的曲线零件,其曲线加工精度应满足设计要求。
五、位置精度位置精度是评价加工质量的重要指标,包括以下几个方面:平行度、垂直度、角度:加工后的零件各部分之间的相对位置应符合设计要求。
同轴度、对称度:对于有多个相同部分的零件,其同轴度和对称度应达到一定要求。
位置度:加工后的零件上各要素的位置应符合设计要求。
六、清洁度清洁度是评价加工质量的重要指标,特别是对于高精度、高要求的加工场合,必须严格控制清洁度指标。
包括以下几个方面:表面清洁度:加工后的零件表面应无杂质、污物等影响使用性能的因素。
防锈处理:加工后的零件应进行适当的防锈处理,以保证长时间内不生锈。
机械加工质量控制

机械加工质量控制一、引言机械加工质量控制是指在机械加工过程中,通过一系列的控制措施和方法,确保加工件的尺寸精度、表面质量、几何形状等达到设计要求,以提高产品质量和工艺效率。
本文将详细介绍机械加工质量控制的标准格式文本。
二、加工质量控制要求1. 尺寸精度控制尺寸精度是机械加工中最基本的要求之一。
在加工过程中,必须控制好加工件的尺寸精度,以确保其符合设计要求。
具体控制要求包括:尺寸公差、尺寸偏差、尺寸误差等。
2. 表面质量控制表面质量是指加工件表面的光洁度、平整度、无划痕、无气泡等特性。
在机械加工中,需要控制好加工件的表面质量,以保证产品的外观质量和使用寿命。
具体控制要求包括:表面粗糙度、表面平整度、表面无划痕等。
3. 几何形状控制几何形状是指加工件的外形、轮廓、曲线等特征。
在机械加工中,需要控制好加工件的几何形状,以确保产品的装配性能和运动精度。
具体控制要求包括:平面度、圆度、直线度、倾斜度等。
三、加工质量控制方法1. 设计控制在机械加工前,应根据产品的设计要求,确定加工件的尺寸、表面质量和几何形状等控制要求,并编写相应的工艺文件。
设计控制是机械加工质量控制的基础,能够直接影响产品的加工质量。
2. 加工设备控制机械加工过程中,需要对加工设备进行控制,以确保其运行稳定和精度可靠。
具体控制方法包括:设备校准、设备维护、设备保养等。
3. 加工工艺控制机械加工过程中,需要对加工工艺进行控制,以确保加工件的尺寸精度、表面质量和几何形状等达到设计要求。
具体控制方法包括:加工工艺参数的选择、加工工艺流程的控制、加工工艺参数的监控等。
4. 加工检验控制机械加工过程中,需要对加工件进行检验,以确保其质量符合设计要求。
具体控制方法包括:尺寸测量、表面质量检验、几何形状检验等。
四、加工质量控制流程1. 加工前准备在机械加工前,需要进行加工前准备工作。
包括:确认加工件的设计要求、准备加工设备和工具、准备加工工艺文件等。
2. 设备校准在机械加工前,需要对加工设备进行校准,以确保其精度可靠。
加工质量分析及控制
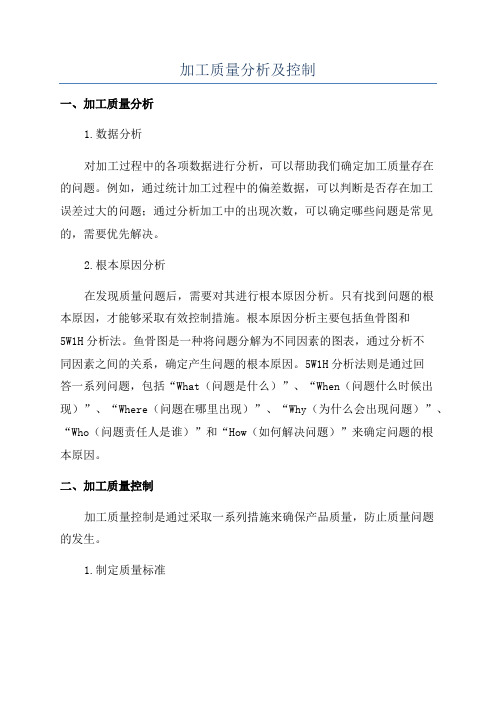
加工质量分析及控制一、加工质量分析1.数据分析对加工过程中的各项数据进行分析,可以帮助我们确定加工质量存在的问题。
例如,通过统计加工过程中的偏差数据,可以判断是否存在加工误差过大的问题;通过分析加工中的出现次数,可以确定哪些问题是常见的,需要优先解决。
2.根本原因分析在发现质量问题后,需要对其进行根本原因分析。
只有找到问题的根本原因,才能够采取有效控制措施。
根本原因分析主要包括鱼骨图和5W1H分析法。
鱼骨图是一种将问题分解为不同因素的图表,通过分析不同因素之间的关系,确定产生问题的根本原因。
5W1H分析法则是通过回答一系列问题,包括“What(问题是什么)”、“When(问题什么时候出现)”、“Where(问题在哪里出现)”、“Why(为什么会出现问题)”、“Who(问题责任人是谁)”和“How(如何解决问题)”来确定问题的根本原因。
二、加工质量控制加工质量控制是通过采取一系列措施来确保产品质量,防止质量问题的发生。
1.制定质量标准制定明确的质量标准是确保产品质量的前提。
质量标准应包括加工过程中各项关键工序的要求,如尺寸、外观、材料等。
同时,质量标准也应该明确产品的不合格判定标准,以便及时发现并解决质量问题。
2.加强工艺控制工艺控制是保证产品质量的重要手段。
加强工艺控制可以通过以下几种方法实现:设定可控制的工艺参数,如温度、时间、压力等;进行工艺参数的实时监控和记录,确保参数在合理范围内;建立工艺改进和优化机制,定期对工艺进行评估和改进。
3.培训与人员管理加工质量的控制不仅需要科学的工艺和设备,还需要有经验丰富、技术过硬的员工。
因此,培训与人员管理是加工质量控制的重要环节。
公司应该加强对员工的培训与考核,提高员工的技术水平和工作质量意识。
4.建立质量反馈和改进机制质量反馈和改进机制可以帮助企业及时了解产品质量存在的问题,并采取相应的改进措施。
企业可以通过建立质量问题反馈渠道,接收客户和员工的反馈意见;同时,企业还应建立完善的质量改进机制,确保问题能够得到及时解决。
- 1、下载文档前请自行甄别文档内容的完整性,平台不提供额外的编辑、内容补充、找答案等附加服务。
- 2、"仅部分预览"的文档,不可在线预览部分如存在完整性等问题,可反馈申请退款(可完整预览的文档不适用该条件!)。
- 3、如文档侵犯您的权益,请联系客服反馈,我们会尽快为您处理(人工客服工作时间:9:00-18:30)。
加工、出入库质量检验考核补充说明一、加工过程具体指标
加工过程质量监控标准
二、入厂(库)
1、保管见田间检验合格证后方可进行扦样。
无田间检验合
格证,保管拒绝扦样、卸车,否则产生的费用由生产、加工部门承担,质检考核时予以扣分。
2、扦样标准
散装:30吨划分为一个批次,4米扦样器至少取5个点,每增加10吨,再增加1个点,以此类推。
袋装:小麦以25吨划分为一个批次,麻袋装不少于200
袋,每5袋至少扦取1袋,200袋以上每7袋再扦取1
袋,以此类推。
3、玉米以30吨划分为一个批次,麻袋装不少于250袋,
每7袋至少扦取1袋,250袋以上每10袋再扦取1袋,以此类推。
凡不符合要求的,限期整改。
4、送样标准:不少于1㎏,少于1㎏,质检人员拒收。
送
样人和接收样品人员双方签字确认。
5、堆放标准:对露天存放种子要采取有效措施,严防发芽、
霉变。
散装原粮在100平方米范围内至少安放5个种温
计,袋装原粮在100平方米范围内至少安放2个种温计,每个品种堆放时,堆与堆之间、堆与墙之间的间距不少
于0.5米,凡不符合要求的,考核时予以扣分。
三、加工
a)加工前检验员对将要加工品种原粮进行水份、净度测
定,未测定的,考核时予以扣分。
b)加工车间必须保证成品种子净度达到≧99%的标准,否
则,考核时予以扣分并承担相应的经济损失。
c)加工过程取样标准,加工过程中要求每袋取样,每袋
取10克左右,每50袋为一个小样,每批次取10个小
样,不符合要求的,考核时予以扣分。
d)送检芽率、净度、水分的样要求至少1㎏,必须从每
批次10个小样混合样中用分样器取出1㎏,送化验室
登记检测,不符合要求的,考核时予以扣分。
四、储藏
加工厂负责人组织装卸工按要求分品种、批次码垛。
袋装种子在100平方米范围内至少安放2个种温计,库房必须防潮隔湿、便于通风,无虫害、有防鼠措施。
垛离墙0.5米存放,垛长与垛高根据实际空间设置,以安全、方便检测为原则,垛与垛之间留0.5米通风道。
五、出库
种子出库时检验员不及时签发种子出库检验合格证,装车过程中检验员不及时扦样封存的,考核时予以扣分。