2011水雾化铁粉的粒径对工艺性能的影响
水雾化纯铁粉生产工艺技术研究与实践

水雾化纯铁粉生产工艺技术研究与实践黎 辉(山东鲁银新材料科技有限公司 济南 271105)摘 要:结合生产实际,通过优化配料、熔炼、精炼、雾化以及二次还原等主要流程的工艺参数和技术研究,提高了钢水的纯净度和雾化铁粉的质量,提升了水雾化纯铁粉的化学、物理指标及综合性能。
关键词:水雾化;纯铁粉;工艺参数优化;钢水纯净度;综合性能RESEARCH AND PRACTICE ON PRODUCTION TECHNOLOGY OF WATER ATOMIZED PURE IRONPOWDERLi Hui(Shandong Luyin New Materials Technology Co., Ltd., Jinan 271105, China)Abstract: In combination with the production practice, the purity of molten steel and the quality of atomized iron powder as well as the chemical and physical indexes and comprehensive properties of atomized pure iron powder are improved by optimizing the technological parameters and technical research of major processes such as batching, smelting, refining, atomization and secondary reduction.Key words:water atomization; pure iron powder; optimization of process parameter; purity of molten steel; comprehensive performance作者:黎辉,男,49岁,工程师收稿日期:2020-10-09和技术研究,提高了钢水的纯净度,提升了水雾化纯铁粉的化学、物理指标及综合性能。
雾化电解高纯球形铁粉

雾化电解高纯球形铁粉近年来,随着科技的不断进步,各种新颖而有实用性的材料被不断研发出来,其中在化学科技方面涉及到的材料也不断质变。
其中,一种在电解雾化技术方面被广泛应用的材料,便是雾化电解高纯球形铁粉。
一、雾化电解高纯球形铁粉的优势1、纯度高:雾化电解高纯球形铁粉是由高纯铁原料雾化而成,因此其质量较高,纯度也相对较高,可达到99.9%以上。
2、球形度好:雾化电解高纯球形铁粉颗粒形状呈圆珠状,颗粒表面光滑,具备优异的球形度,满足高品质及高要求的材料的需求。
3、晶粒尺寸均匀:雾化电解高纯球形铁粉的颗粒尺寸均匀,晶粒分布较为均匀,适用于高品质的材料制备,让相关产业得以更好的提高生产效益和产品品质。
4、良好的流动性:雾化电解高纯球形铁粉经过特殊处理后,颗粒表面光滑,颗粒相对较轻,具有优异的流动性,这一特点使雾化电解高纯球形铁粉在批量生产时比较优秀。
二、雾化电解高纯球形铁粉的应用领域1、磁性材料:雾化电解高纯球形铁粉具有高纯度和均匀的晶粒尺寸,快速的反应动力学和良好的烧结性,因此被广泛应用于制造高性能、高品质的磁性材料。
2、彩色陶瓷材料:在生产彩色陶瓷材料时,雾化电解高纯球形铁粉可以被用来制备高纯度的金属颜料,以达到彩色效果,提高陶瓷的审美价值,赢得消费者的喜欢。
3、先进制造业领域:雾化电解高纯球形铁粉也广泛应用于先进制造业领域,例如,制备高质量硬质合金,高温陶瓷制品,日用陶瓷等。
三、雾化电解高纯球形铁粉在工业中的应用案例近年来,雾化电解高纯球形铁粉已经被广泛应用于多个领域,例如:1、在制造国防军工方面,雾化电解高纯球形铁粉经常用作制造高压涡轮的原料,这种高压涡轮的性能非常优越,可以用于各种军用及民用飞行器中。
2、雾化电解高纯球形铁粉也被广泛应用于陶瓷制造业中。
特殊的雾化电解高纯球形铁粉制成的金属颜料可以很好地应用于高品质的陶瓷生产中,提高了陶瓷的审美价值。
3、雾化电解高纯球形铁粉在汽车制造业中同样有着广泛应用。
粒度影响粉末涂料的性能

粒度对粉末涂料性能的影响
在粉末涂料行业衡量粉末质量的主要技术参数有外观、密度、流出性(流度)、挥发物含量、筛余物、胶化时间、安息角、粒度分布、流动性及上粉率等,一些标准还引入体积电阻率、软化温度、磁性物含量、固化时间等参数。
其中更为密切相关的参数是粒度分布、密度、流出性、安息角、流动性、上粉率。
粒度分布对粉末涂料的产品质量有较大影响,包括外观、流平性、上粉率、稳定性、回收率等众多方面。
一般来说,粉末粒径越小,粉末固化时流平性越好,外观越平整光滑,但粉末太细带电性降低,涂装施工效率会下降,超细粉(粒径<10μm)基本上不带电,同时粉末太细也会加大粉末生产成本。
粉末上粉率主要取决于粉末颗粒带电的多少,而粉末的带电量和粉末颗粒粒径的平方成正比。
增大颗粒粒径,粉末带电量增加,上粉率提高。
但粉末颗粒的粒径也不能太大,粒径太大,大颗粒粉末的重力超过空气动力和静电力,粉末涂料在飞行过程中,由于重力作用未达到工件表面就已经落下,反而会使上粉率降低。
同时,若粉末中10μm以下的超细粉含量太多,会使得粉末极易吸潮、结团,稳定性下降。
粉末涂料生产厂和粉末涂料涂装厂都存在回收粉末涂料的问题,通常,粉末粒径<10μm的超细粉回收率低,当粉末粒径>10μm时粉末涂料回收率迅速上升,并且粉末的回收率随着粒径的增大而增加。
涂料研磨 粒径

涂料研磨粒径全文共四篇示例,供读者参考第一篇示例:涂料研磨是指在涂料制备过程中,通过研磨设备将原料中的颗粒粉碎、分散、混合,以提高涂料的质量和性能。
粒径是一个关键参数,它直接影响着涂料的质地、均匀度和终端使用效果。
在涂料工业中,粒径的控制是非常重要的,下面我们就来探讨一下涂料研磨中粒径的意义、影响以及常见的调控方法。
一、粒径的意义1. 影响颗粒分布在涂料中,颗粒的大小是不均匀的,有大有小。
通过研磨可以去除颗粒中的大颗粒,使颗粒更加均匀地分布在涂料中,提高涂料的均匀性。
2. 影响涂层的光泽度颗粒的大小会影响涂层的光泽度,一般来说,颗粒越细,涂层的光泽度越好。
3. 影响涂料的流动性颗粒的大小也会影响涂料的流动性,颗粒越细,涂料流动性越好,对涂装过程的稳定性和效果都有一定影响。
二、粒径的影响1. 粒径不均匀如果涂料中的颗粒粒径分布不均匀,会导致涂层的光泽度不均匀、颜色不均匀等问题,影响涂层的整体效果。
2. 粒径过大涂料中颗粒过大会导致其在搅拌、喷涂等过程中容易堵塞设备,影响生产效率和涂层的均匀性。
3. 粒径过小颗粒过小的情况下,易造成团聚现象,使颗粒之间发生结合,影响颗粒的分散性,导致涂料质地不均匀,影响涂层的质量。
三、粒径的调控方法1. 通过选择合适的研磨设备不同的颗粒大小需要不同的研磨设备来进行粉碎。
一般来说,颗粒细小的情况下可以选择珠砂研磨机进行研磨,颗粒较大时可以选择球磨机等设备。
2. 通过改变研磨时间研磨时间的长短也会影响颗粒的粒径,通常情况下,研磨时间过长会导致颗粒过细,因此在研磨过程中要根据颗粒的大小和要求合理控制研磨时间。
3. 通过添加助剂在研磨过程中添加一定的助剂,可以有效地影响颗粒的形态和粒径分布,达到调控颗粒粒径的目的。
粒径在涂料研磨过程中扮演着非常重要的角色,它直接影响着涂料的性能和质量。
在涂料生产过程中,必须要重视粒径的控制,采取有效的措施来确保颗粒的均匀性和适当的粒径分布,以获得优质的涂料产品。
水雾化与气雾化合金粉末性能及成本的比较

水雾化与气雾化制作合金粉末的方法,虽然制粉的原理相同,但制得的粉末的物理性能相差还是很大的,特别是形状。
由于气体的热容量要比水小,所以采用气雾化时,合金受到的激冷度低,受到雾化介质冲击时,雾化成细小液滴的合金液不会马上凝固,这给了合金液滴在下落过程中收缩成球的时间,所以容易获得球形合金粉末。
水雾化时情形正好相反,由于水对雾化成细小合金液滴的激冷作用,几乎是在一瞬间,就凝固成了合金粉末,这使得那些表面张力较小的合金形成的合金粉末,呈土豆状或不规则形状,只有那些表面张力较大的合金,例如镍基合金,才能做成球形合金粉末。
通过调整雾化参数和雾化时合金液的过热度,采用水雾化也能做出近似球形的合金粉末,满足热喷涂的需要。
用于管状焊丝的中间合金粉末,形状上没有特别的要求,水雾化比较适合。
化学成份不论是采用水雾化还是采用气雾化,制作出的合金粉末的化学成份不会因为制作方法的不同而产生差异。
金相组织采用气雾化制作的合金粉末,合金的过冷度要比采用水雾化做的小许多,所以相同的化学成份,采用不同的雾化方法做出的合金粉末的金相组织会不一样。
合金粉末的氧含量合金粉末的氧含量,与合金本身对氧的敏感性和雾化时的雾化环境中的氧含量有关。
如果合金本身对氧非常敏感,则不仅在雾化时要采取措施,在熔化时最好也采用真空熔炼。
对于大多数合金,只要在雾化时采取减少与氧的接触,就能达到降低合金粉末中氧的含量的目的。
气雾化时,通常是使用氮气作为雾化介质,大量的氮气充满了雾化区,将雾化区的氧气驱逐掉了,所以能保护合金液滴在雾化及冷却时很少氧化。
当一炉熔融的合金液被雾化成金属粉末时,它的表面积在雾化的一瞬间增大了无数倍,换言之,其与氧结合的面积也增大了,有更多的金属表面暴露在雾化环境中。
所以,水雾化时,如果不采取措施,是无法避免合金液滴的氧化的。
为了在水雾化时,能让雾化环境少氧或无氧,首先,必须将雾化筒体密封起来,将雾化环境与周围的环境隔绝开来。
其次,是要将已封闭起来的雾化筒体中的氧气排除掉。
铁基粉末冶金零件热处理
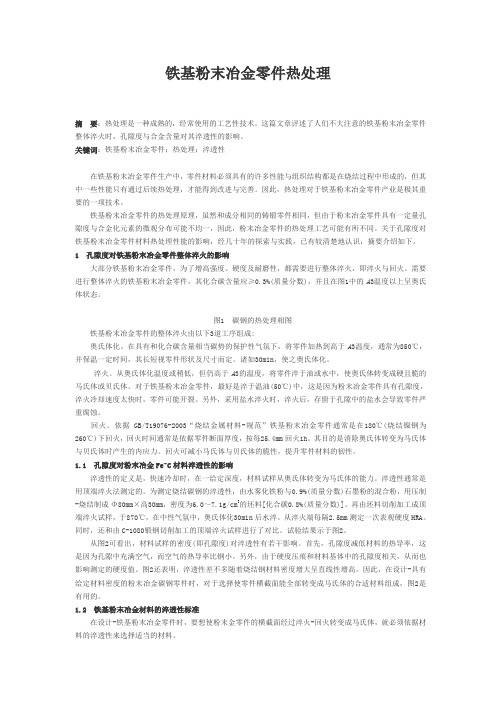
铁基粉末冶金零件热处理摘要:热处理是一种成熟的,经常使用的工艺性技术。
这篇文章评述了人们不大注意的铁基粉末冶金零件整体淬火时,孔隙度与合金含量对其淬透性的影响。
关键词:铁基粉末冶金零件;热处理;淬透性在铁基粉末冶金零件生产中,零件材料必须具有的许多性能与组织结构都是在烧结过程中形成的,但其中一些性能只有通过后续热处理,才能得到改进与完善。
因此,热处理对于铁基粉末冶金零件产业是极其重要的一项技术。
铁基粉末冶金零件的热处理原理,虽然和成分相同的铸锻零件相同,但由于粉末冶金零件具有一定量孔隙度与合金化元素的微观分布可能不均一,因此,粉末冶金零件的热处理工艺可能有所不同。
关于孔隙度对铁基粉末冶金零件材料热处理性能的影响,经几十年的探索与实践,已有较清楚地认识,摘要介绍如下。
1 孔隙度对铁基粉末冶金零件整体淬火的影响大部分铁基粉末冶金零件,为了增高强度、硬度及耐磨性,都需要进行整体淬火,即淬火与回火。
需要进行整体淬火的铁基粉末冶金零件,其化合碳含量应≥0.3%(质量分数),并且在图1中的A3温度以上呈奥氏体状态。
图1 碳钢的热处理相图铁基粉末冶金零件的整体淬火由以下3道工序组成:奥氏体化。
在具有和化合碳含量相当碳势的保护性气氛下,将零件加热到高于A3温度,通常为850℃,并保温一定时间,其长短视零件形状及尺寸而定。
诸如30min,使之奥氏体化。
淬火。
从奥氏体化温度或稍低,但仍高于A3的温度,将零件淬于油或水中,使奥氏体转变成硬且脆的马氏体或贝氏体。
对于铁基粉末冶金零件,最好是淬于温油(50℃)中,这是因为粉末冶金零件具有孔隙度,淬火冷却速度太快时,零件可能开裂。
另外,采用盐水淬火时,淬火后,存留于孔隙中的盐水会导致零件严重腐蚀。
回火。
依据GB/T19076-2003“烧结金属材料-规范”铁基粉末冶金零件通常是在180℃(烧结镍钢为260℃)下回火,回火时间通常是依据零件断面厚度,按每25.4mm回火1h。
急冷水雾化工艺对金属粉末性能的影响
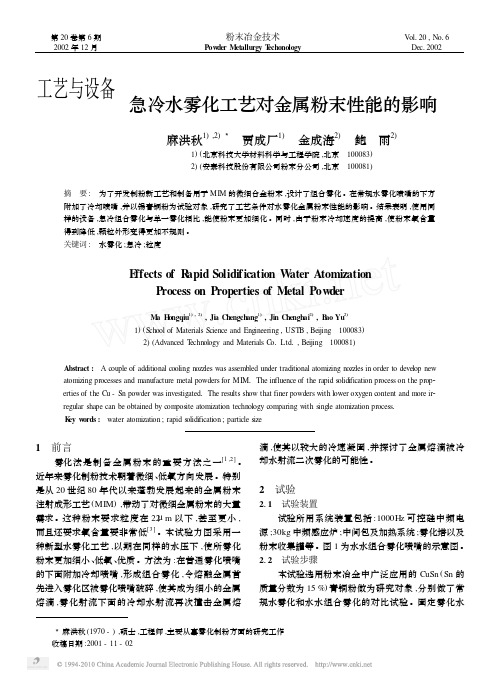
1 前言
雾化法是制备金属粉末的重要方法之一[1 ,2] 。 近年来雾化制粉技术朝着微细 、低氧方向发展 。特别 是从 20 世纪 80 年代以来蓬勃发展起来的金属粉末 注射成形工艺 (MIM) ,带动了对微细金属粉末的大量 需求。这种粉末要求粒度在 22μm 以下 ,甚至更小 , 而且还要求氧含量要非常低[3] 。本试验力图采用一 种新型水雾化工艺 ,以期在同样的水压下 ,使所雾化 粉末更加细小、低氧、优质。方法为 :在普通雾化喷嘴 的下面附加冷却喷嘴 ,形成组合雾化 ,令熔融金属首 先进入雾化区被雾化喷嘴破碎 ,使其成为细小的金属 熔滴 ,雾化射流下面的冷却水射流再次撞击金属熔
图 2 水 、水组合雾化对 CuSn 锡青铜合金粉的粒度影响
喷嘴是雾化工艺的关键部件 , 依据 d = A / ( V · sinα) [4] 的雾化模型 ,雾化粉末的粒度 d 不仅与雾化 射流的速度 V 以及喷射角度 a 有关 ,还与喷嘴的设计 和结构紧密相关 ,即喷嘴的雾化效率直接影响上式中 的系数 A 值 ,喷嘴效率高 ,则 A 值就大。雾化过程中 雾化介质的动能转换为粉末的比表面能 ,在这个转化 过程中 ,雾化介质与熔融金属液流的接触面积越大 ,
图 4 水组合雾化对 CuSn 及 Sn 粉显微结构的影响
从所制备的粉末的二次枝晶间距照片上可以定
性地看出水水组合雾化所制粉末比同样条件下单纯
普通水雾化所制粉末的二次枝晶间距λ2 要小 ,取λ2 近似从 118μm 减小到 1μm 左右 ,取 B 为 38 ,取 n 为
1/ 3 ,依据式 (1) 估算粉末冷却速度 ,由 103 K/ S 提高到
1) (北京科技大学材料科学与工程学院 ,北京 100083) 2) (安泰科技股份有限公司粉末分公司 ,北京 100081)
粉末粒度对热压Ti-6Al-4V合金微观组织和力学性能的影响

粉末粒度对热压Ti-6Al-4V合金微观组织和力学性能的影响邹黎明;毛新华;刘辛;蔡一湘【摘要】以4种不同粒径的球形Ti-6Al-4V粉末为原料,采用真空热压法进行成形固结.利用X射线衍射仪(XRD)、金相显微镜、扫描电镜、万能材料试验机分别分析粉末Ti-6Al-4V合金的物相组成、微观组织、断口形貌以及力学性能,研究粉末粒度及其组成对烧结体微观组织和力学性能的影响.研究结果表明:热压烧结Ti-6Al-4V样品致密度均可达到98%以上.不同粒度粉末烧结后的合金均为网篮排列层片状组织.合金塑性主要受原始粉末粒度影响,随原始粉末粒度增大,烧结样品的晶粒尺寸增大,从而导致合金的塑性降低.粉末粗细搭配相比于原始粗粉,有助于提高合金的塑性,从而有效降低粉末钛合金的成本.【期刊名称】《粉末冶金材料科学与工程》【年(卷),期】2016(021)002【总页数】6页(P217-222)【关键词】钛合金;热压;粒径;力学性能;Ti-6Al-4V【作者】邹黎明;毛新华;刘辛;蔡一湘【作者单位】广东省科学院广东省材料与加工研究所,广州 510650;广东省科学院广东省材料与加工研究所,广州 510650;广东省科学院广东省材料与加工研究所,广州 510650;广东省科学院广东省材料与加工研究所,广州 510650【正文语种】中文【中图分类】TF124钛由于具有比强度高、耐腐蚀性能好、生物相容性优异等特点被广泛应用于航空航天、生物医用等行业[1−2]。
但传统钛及钛合金加工工艺复杂,生产成本高,严重阻碍了钛的进一步市场应用。
粉末冶金作为一种近净成形方法,可以降低生产成本,尤其适合于钛这样昂贵的材料,因此,目前钛及钛合金的粉末冶金技术已成为研究热点[3−5]。
航空航天、生物医用等高新技术行业对粉末钛合金性能要求高,原材料一般需采用高品质的球形钛合金粉末。
钛由于具有加工硬化速率高的特点,采用传统模压方法比较难以致密化。
尤其是高品质的球形钛合金粉末更是难以致密化,一般需采用热等静压进行成形固结,成本非常高[6]。
铁粉
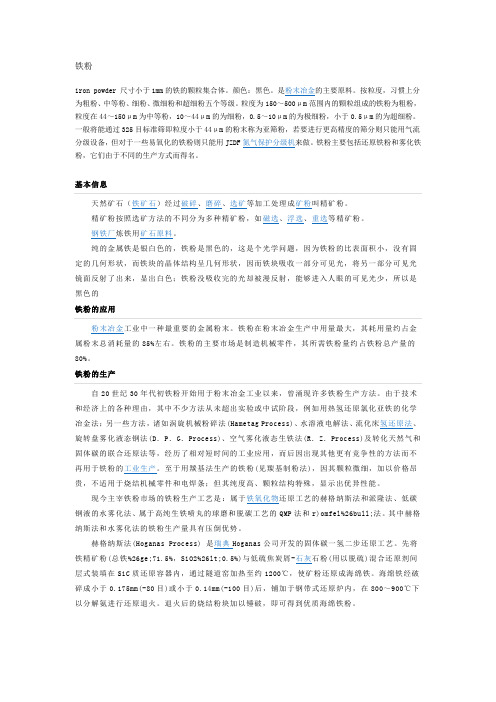
铁粉iron powder 尺寸小于1mm的铁的颗粒集合体。
颜色:黑色。
是粉末冶金的主要原料。
按粒度,习惯上分为粗粉、中等粉、细粉、微细粉和超细粉五个等级。
粒度为150~500μm范围内的颗粒组成的铁粉为粗粉,粒度在44~150μm为中等粉,10~44μm的为细粉,0.5~10μm的为极细粉,小于0.5μm的为超细粉。
一般将能通过325目标准筛即粒度小于44μm的粉末称为亚筛粉,若要进行更高精度的筛分则只能用气流分级设备,但对于一些易氧化的铁粉则只能用JZDF氮气保护分级机来做。
铁粉主要包括还原铁粉和雾化铁粉,它们由于不同的生产方式而得名。
派隆法(Pyron Process) 将低碳沸腾钢的轧钢铁鳞破碎至小于0.147mm后,置于多炉床焙烧炉内在980℃下氧化成Fe2O3。
然后将Fe2O3粉喂送至带式炉内,在温度不超过1050℃下通以氢气使之还原成铁粉。
低碳钢液水雾化法低碳废钢通过熔化造渣除去或减少磷、硅和其他杂质元素后,通过漏嘴流入雾化器中,同时喷入高压(约8.3MPa)水流击碎金属流而成液滴,液滴落入底下的水槽冷却而凝固成粉。
粉末经磁选、脱水和干燥后,送入带式炉,在800~1000℃下以分解氨气予以还原退火处理,即得纯度高的水雾化铁粉。
QMP法为加拿大Quebec Metal Powder公司所开发。
将高纯的熔融生铁水(含碳量约为3.3%~3.8%)注入漏包,从漏嘴流下的铁水被水平喷射的高压水流击碎成粒(约3.2mm)后,落入一吸入空气的水冷容器中,使之部分氧化。
经干燥的铁粒用球磨法加以粉碎,然后将过筛至小于0.147mm 的粉末送入有分解氨气保护的带式炉内,在800~1040℃下利用自身所含的氧进行脱碳退火,再用分解氨气体另行还原退火,即可得粉末冶金用铁粉。
铁粉的粉碎气流粉碎法:利用JZDB氮气保护粉碎机进行氮气环境下的超微粉碎,防止氧化。
使用气流粉碎的目的是能使高硬度的铁粉粉碎至微米级别,使用氮保系统来进行粉碎则是为了防止氧化和爆炸。
粉末重点
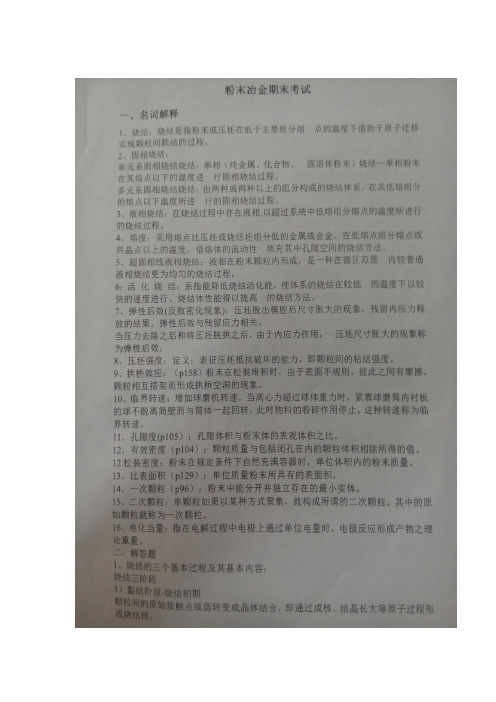
问答题与简答题1、粉末冶金技术与传统技术相比的优势缺点重要优点:* 能够制备部分其他方法难以制备的材料,如难熔金属,假合金、多孔材料、特殊功能材料(硬质合金);* 因为粉末冶金在成形过程采用与最终产品形状非常接近的模具,因此产品加工量少而节省材料;* 对于一部分产品,尤其是形状特异的产品,采用模具生产易于,且工件加工量少,制作成本低 , 如齿轮产品。
重要缺点:* 由于粉末冶金产品中的孔隙难以消除,因此粉末冶金产品力学性能较相同铸造加工产品偏低;* 由于成形过程需要模具和相应压机,因此大型工件或产品难以制造;* 规模效益比较小2 、气体雾化制粉过程可分解为几个区域,每个区域的特点是什么?( 10 分)气体雾化制粉过程可分解为金属液流紊流区,原始液滴形成区,有效雾化区和冷却区等四个区域。
其特点如下:金属液流紊流区:金属液流在雾化气体的回流作用下,金属流柱流动受到阻碍,破坏了层流状态,产生紊流;原始液滴形成区:由于下端雾化气体的冲刷,对紊流金属液流产生牵张作用,金属流柱被拉断,形成带状 - 管状原始液滴;有效雾化区:音高速运动雾化气体携带大量动能对形成带状 - 管状原始液滴的冲击,使之破碎,成为微小金属液滴;冷却区。
此时,微小液滴离开有效雾化区,冷却,并由于表面张力作用逐渐球化3、分析还原制备钨粉的原理和钨粉颗粒长大的因素。
( 10 分)解:钨粉由氢气还原氧化钨粉的过程制得,还原过程中氧化物自高价向低价转变,最后还原成钨粉,WO3—WO2 —W ;其中还有 WO2 。
90—WO2 。
72 等氧化物形式。
由于当温度高于 550 度时,氢气即可还原 WO3 ,由于当温度高于 700 度时,氢气即可还原 WO2 。
因为在这种条件下水分子的氧离解压小于WO3 , WO2 离解压,水分子相对稳定, WO3 , WO2 被还原,同时由于温度的作用,疏松粉末中还原产物容易经扩散排走,还原动力学条件满足,导致氧化钨被氢气还原;由于 WO3 ,和 WO2 在含有水分子的氢气中具有较大的挥发压,而且还原温度越高,挥发压越大,进入气相中的氧化钨被还原后,沉降在以还原的钨粉颗粒上导致钨粉颗粒长大。
粉末冶金原理知识要点

1粉末冶金的特点:粉末冶金在技术上和经济上具有一系列的特点。
从制取材料方面来看,粉末冶金方法能生产具有特殊性能的结构材料、功能材料和复合材料。
(1)粉末冶金方法能生产普通熔炼法无法生产的具有特殊性能的材料:1)能控制制品的孔隙度;2)能利用金属和金属、金属和非金属的组合效果,生产各种特殊性能的材料;3)能生产各种复合材料;(2)粉末冶金方法生产的某些材料,与普通熔炼法相比,性能优越:1)高合金粉末冶金材料的性能比熔铸法生产的好;2)生产难熔金属材料和制品,一般要依靠粉末冶金法;从制造机械零件方面来看,粉末冶金法制造的机械零件时一种少切削、无切削的新工艺,可以大量减少机加工量,节约金属材料,提高劳动生产率。
总之,粉末冶金法既是一种能生产具有特殊性能材料的技术,又是一种制造廉价优质机械零件的工艺。
2粉末冶金的工艺过程(1)生产粉末。
粉末的生产过程包括粉末的制取、粉料的混合等步骤。
为改善粉末的成型性和可塑性通常加入汽油、橡胶或石蜡等增塑剂。
(2)压制成型。
粉末在500~600MPa压力下,压成所需形状。
(3)烧结。
在保护气氛的高温炉或真空炉中进行。
烧结不同于金属熔化,烧结时至少有一种元素仍处于固态。
烧结过程中粉末颗粒间通过扩散、再结晶、熔焊、化合、溶解等一系列的物理化学过程,成为具有一定孔隙度的冶金产品。
(4)后处理。
一般情况下,烧结好的制件可直接使用。
但对于某些尺寸要求精度高并且有高的硬度、耐磨性的制件还要进行烧结后处理。
后处理包括精压、滚压、挤压、淬火、表面淬火、浸油、及熔渗等。
现代粉末冶金的主要工艺过程生产粉末制坯烧结3、粉末冶金发展中的三个重要标志:第一是克服了难熔金属(如钨、钼等)熔铸过程中产生的困难第二是本世纪30年代用粉末冶金方法制取多孔含油轴承取得成功第三是向更高级的新材料新工艺发展。
4、怎样理解“粉末冶金技术既古老又年轻”?粉末冶金是一项新兴技术,但也是一项古老技术。
根据考古学资料,远在纪元前3000年左右,埃及人就在一种风箱中用碳还原氧化铁得到海绵铁,经高温锻造制成致密块,再锤打成铁的器件。
铁粉粒径和硅树脂含量对铁基复合磁粉芯软磁性能的影响

文章编号:1001-9731(2014)06-06006-05铁粉粒径和硅树脂含量对铁基复合磁粉芯软磁性能的影响∗张㊀蕾,杨㊀白,曹㊀莹,于荣海(北京航空航天大学材料科学与工程学院,北京100191)摘㊀要:㊀将不同粒径铁粉颗粒和适量高温硅树脂进行充分混合,在铁粉颗粒表面上均匀包覆一层硅树脂,采用粉末压实成型工艺将铁粉-硅树脂复合粉末制备成致密的铁基复合磁粉芯㊂系统研究铁粉粒径和硅树脂包覆量对磁粉芯密度及软磁性能的影响,探索最佳铁粉粒径大小和硅树脂包覆量㊂研究表明,在相同粒径下,磁粉芯的密度㊁涡流损耗和磁感应强度均随硅树脂包覆量增加而降低㊂在相同硅树脂包覆量下,磁粉芯的密度和涡流损耗随粒径增大而增加,磁滞损耗却随着粒径增大而降低㊂在平均粒径为120μm的铁粉表面上均匀包覆0.5%硅树脂可制备出高密度㊁低损耗和较高磁感应强度的复合磁粉芯,在大功率条件下,较好软磁性能参数为P s(B=1T,f=400Hz)=69W/k g, B4k(H=4000A/m)=0.96T㊂关键词:㊀铁粉粒径;硅树脂包覆量;铁基复合磁粉芯;密度;软磁性能中图分类号:㊀TM271;TB33文献标识码:A DOI:10.3969/j.issn.1001-9731.2014.06.0021㊀引㊀言软磁材料是一类具有较低矫顽力和较高磁导率的磁性材料㊂在外加磁场的作用下,软磁材料表现出既易于磁化又易于退磁的特点,软磁材料作为磁电转换领域的重要功能材料之一,在电子设备㊁通信和电器等领域有着广泛的应用㊂复合软磁材料由于具有金属软磁材料高饱和磁感应强度和软磁铁氧体高电阻率的特点,在工业技术和日常生活中的应用日益增多,一直以来受到人们的重视并得到广泛的研究[1-3]㊂复合软磁材料一般是以金属软磁粉末为原料,在颗粒表面进行有机或无机绝缘处理后,再采用粉末冶金工艺将复合粉末压制成型得到块状软磁材料[4]㊂与传统的金属软磁材料相比,复合软磁材料具有较高的电阻率,可以减少涡流损耗,提高材料的使用频率㊂选择合适金属磁粉进行有效包覆或绝缘处理,可以制备出同时具有高饱和磁感应强度㊁高磁导率和低损耗等特性的复合软磁材料,在大功率电机等领域有着潜在的应用前景[5-7]㊂近年来,国内外研究人员在复合软磁材料的制备工艺和性能研究方面取得了较好的进展㊂瑞典赫格纳斯公司(Hög anäs)研究人员采用磷酸盐作为包覆前驱体,采用化学法在铁粉颗粒表面形成一层Fe3P包覆层,制备出具有较高磁导率和低磁损耗的Fe-Fe3P复合软磁材料[8]㊂日本研究人员采用热蒸发法,在铁粉表面包覆一层50nm左右的M g O绝缘层,制备出具有低矫顽力和低磁损耗的Fe-M g O复合软磁材料[9]㊂四川大学钟小溪等将FeSiAl粉末置于H2-N2气氛中,通过表面选择性氮化氧化技术在FeSiAl颗粒表面生成混合的AlN和Al2O3绝缘层,混合绝缘层可以提高材料的电阻率从而降低磁损耗,提高频率稳定性和品质因数[10]㊂在使用性能上,高性能大功率应用复合软磁材料要求具有高密度㊁高饱和磁感应强度㊁高磁导率㊁低损耗及良好温度稳定性㊂在目前研究及工程应用中,复合材料的制备工艺多集中在对金属或合金的磁性颗粒表面进行有机或无机物包覆[9-15],或采用磁性颗粒基体-高电阻率纤维连续复合法制备复合粉体[16],然后采用粉末冶金法制备磁粉芯㊂相对金属软磁材料而言,复合软磁材料的电阻率一般能得到提高,从而在一定程度上降低磁损耗㊂但由于低密度包覆层导致了成型后磁粉芯密度较低,从而使得磁粉芯的饱和磁感应强度和磁导率也较低㊂此外,多数有机或无机包覆层具有非磁性特征,与金属磁性颗粒复合之后,在一定程度上也降低了材料的饱和磁化强度㊂目前在制备高性能复合软磁材料工艺上,选择成分和粒径合适的金属磁性颗粒,包覆适量无机物或有机物,通过有效的成型工艺,在提高材料电阻率和降低磁损耗的同时,保持较高密度和饱和磁化强度,是亟待解决的工艺问题㊂本文以不同粒径的铁粉为研究对象,在其表面包覆不同含量的高温硅树脂,采用粉末冶金压实工艺制备致密的复合磁粉芯㊂研究铁粉粒径和硅树脂包覆量对复合磁粉芯密度㊁直流和交流软磁性能的影响㊂探索同时获得高密度和良好直流㊁交流磁性能磁粉芯所需的最佳粒径大小和包覆层含量㊂600602014年第6期(45)卷∗基金项目:国家自然科学基金资助项目(51101007);国家重点基础研究发展计划(973计划)资助项目(2010CB934602);北京市自然科学基金资助项目(2132039)收到初稿日期:2013-05-28收到修改稿日期:2013-10-23通讯作者:杨㊀白,E-mail:b y an g@作者简介:张㊀蕾㊀(1990-),女,山东滨州人,硕士研究生,师承杨白讲师,从事磁性材料研究㊂2㊀实㊀验实验中选用3种市售的不同粒径高纯铁粉(化学纯度基本相同,质量分数>99%)作为原料铁粉,其规格如表1所示㊂表1㊀高纯铁粉型号规格Table1T yp e and s p ecification of hi g h-p urit y iron p owders铁粉样品名平均粒径/μm生产厂商S1107加拿大魁北克公司S2120瑞典赫格纳斯有限公司S3172日本丰田汽车公司㊀㊀将适量的上述铁粉与高温硅树脂充分混合,高温硅树脂与铁粉的质量百分比为0.2%~1.5%㊂为了确保硅树脂在铁粉颗粒表面上形成均匀完整的包覆层,将铁粉置于溶解有硅树脂的丙酮溶液中搅拌30~ 60min,在室温~50ħ温度中干燥,获得铁粉表面包覆硅树脂的复合颗粒㊂采用粉末压片机在压力为750~ 850MPa的条件下压制成外径为22mm㊁内径为14mm和厚度为5mm的环状样品㊂采用排水法测量环形复合磁粉芯的密度㊂用X 射线衍射仪(Cu,Kα)测量软磁复合粉末的相组成,用振动试样磁力计(VSM)测试材料的室温磁滞回线,最大测量磁场为1T㊂采用中国计量科学研究院研制的交流(AC)和直流(DC)B-H软磁测量磁滞回线仪分别测量环形复合磁粉芯的磁损耗和不同外加磁场下的磁感应强度㊂在交流条件下,测量外加磁场为1T,测量频率范围为50~1000Hz;在直流条件下,测量最大外加磁场分别为1200,4000,5000和10000A/m㊂3㊀结果与讨论3.1㊀铁粉-硅树脂复合软磁材料的结构与内禀磁性图1为纯铁粉和包覆不同含量硅树脂复合软磁颗粒的X射线衍射谱㊂图1㊀纯铁粉和包覆不同含量硅树脂复合软磁颗粒XRD图谱Fi g1XRD p atterns of p ure iron p owders and silicon resin coated iron p owders从图1可以看出,包覆硅树脂后的复合颗粒衍射峰与纯铁粉基本相同,说明铁粉在包覆过程没有发生氧化㊂在实验中,进一步采用透射电镜观察复合软磁颗粒,在颗粒边缘可以观察到硅树脂薄膜均匀完整地包覆在铁粉颗粒表面上㊂表2为采用排水法测量的铁粉表面包覆不同含量硅树脂磁粉芯的密度㊂表2㊀高纯铁粉及其表面包覆硅树脂后磁粉芯的密度Table2The densit y of Fe-based ma g netic p owder cores样品名及制备条件密度/g㊃cm-3S27.48S2+0.2%高温硅树脂7.46S2+0.5%高温硅树脂7.30S2+0.6%高温硅树脂7.26S2+0.8%高温硅树脂7.23S2+1.0%高温硅树脂7.14S2+1.2%高温硅树脂7.12S2+1.5%高温硅树脂7.01S1+0.5%高温硅树脂7.28S3+0.5%高温硅树脂7.40㊀㊀从表2可以看出,在同一粒径铁粉颗粒表面包覆不同含量的硅树脂,在相同成型条件下获得的磁粉芯的密度随着硅树脂含量的增加而降低,这是因为硅树脂的密度相对较低㊂在不同粒径铁粉颗粒表面上包覆相同含量的硅树脂,磁粉芯的密度随粒径减小而减小㊂对磁粉芯而言,密度是使用性能上一个重要参数,同一类磁粉芯在获得相同磁通量的情况下,密度越高,所需器件的体积越小,一般要求磁粉芯的密度越高越好[14]㊂进一步实验发现,铁粉粒径过大,可能导致硅树脂不完全包覆在颗粒表面上,从而导致磁损耗增大;而且在较大的铁粉粒径下,压制到完全致密状态需要更大的压力㊂图2为铁粉表面包覆不同含量硅树脂复合软磁颗粒的磁滞回线㊂图2㊀铁粉表面包覆不同含量硅树脂复合磁性颗粒的室温磁滞回线Fi g2H y steresis loo p s of iron p owders coated with different content of silicon resin从图2可以看出,硅树脂包覆复合粉末具有良好软磁性能,相对纯铁粉而言,包覆后铁粉的饱和磁化强度M s有所降低,并且随着硅树脂含量的增加而减少,这是因为非磁性硅树脂对磁粉芯的磁稀释作用[15]㊂在S2铁粉颗粒表面上分别包覆0.5%,0.6%和70060张㊀蕾等:铁粉粒径和硅树脂含量对铁基复合磁粉芯软磁性能的影响1.0%高温硅树脂获得复合磁粉的M s值分别为219.42,216.63和210.53A㊃m2/k g,样品的矫顽力基本相同㊂实验表明不同粒径铁粉表面上包覆相同含量硅树脂获得复合颗粒的M s值基本相同㊂3.2㊀硅树脂包覆量对复合磁粉芯交流和直流磁性能的影响用闭合回路法测量磁粉芯的交流和直流磁性能㊂图3为同一粒径铁粉颗粒表面包覆不同硅树脂含量的磁粉芯在外加磁场为1T时总损耗P s随频率f变化曲线㊂从图3可以看出,所有样品的总损耗P s随着测量频率增加而增大㊂当测量频率<200Hz时,复合磁粉芯与纯铁粉芯的总损耗相差不大,当测量频率高于400Hz时,硅树脂包覆对降低总损耗的作用明显㊂而在不同频率下,硅树脂包覆量对复合磁粉芯总损耗的影响不同㊂如图3中插图所示,当测量频率为400Hz 时,硅树脂包覆量为1.5%的复合磁粉芯的总磁损耗比1.2%的总磁损耗要大,而当测量频率增加到800Hz时,包覆量为1.2%的样品总损耗却超过了1.5%相应的值㊂其原因主要是硅树脂含量不同,复合磁粉芯的涡流损耗和磁滞损耗变化不一样,详细分析见后续讨论㊂图3㊀铁粉芯及其复合磁粉芯在外加磁场为1T时总损耗P s随频率f变化曲线Fi g3Core loss versus fre q uenc y for ma g netic p owder cores with different content silicon resin软磁材料在交流磁场中的总磁损耗一般包括涡流损耗㊁磁滞损耗和剩余损耗,在大功率使用场合下(工作时磁感应强度为1T,外场频率为50~1000Hz),其剩余损耗可以忽略不计㊂根据经验公式,磁粉芯的总磁损耗可以表示为[17]P s=P e+P h=eB2m f2+fηB1.6m(1)W=P s f=eB2m f+ηB1.6m(2)㊀㊀式(1)和(2)中,P e为涡流损耗,P h为磁滞损耗,e 和η分别为涡流损耗和磁滞损耗系数,两者都为常数㊂根据式(1)和(2),可以将材料的涡流损耗和磁滞损耗进行分离㊂图4为铁粉芯和复合磁粉芯在外加磁场为1T时P e和P h随频率f变化的曲线㊂从图4(a)可以看出,所有样品涡流损耗随频率呈指数关系增大;在相同测量频率下,复合磁粉芯涡流损耗随着硅树脂含量增加而减小㊂硅树脂包覆量越多,对降低复合磁粉芯涡流损耗越明显,这是由于硅树脂包覆层增厚导致磁粉芯电阻率增加㊂从图4(b)可见,磁滞损耗也随频率增加呈线性关系增大㊂在相同测量频率下,磁滞损耗随着包覆量增加而有所增加,但其随硅树脂包覆量的变化趋势没有涡流损耗明显㊂硅树脂包覆层越厚,铁粉-硅树脂复合颗粒在压实致密过程中复合磁粉芯内部产生的内应力可能会越大,可能导致磁粉芯的矫顽力增大,从而使得磁滞损耗随着包覆量的增加而增大㊂图4㊀铁粉芯和复合磁粉芯在外加磁场为1T时涡流损耗P e和磁滞损耗P h随频率f变化的曲线Fi g4Edd y loss and ma g netic h y steresis loss versus fre q uenc y for ma g netic p owder cores with dif-ferent content of silicon resin结合图4(a)和(b)可以看出,硅树脂包覆量对磁粉芯涡流损耗和磁滞损耗的影响截然相反,即对相同铁粉粒径的复合磁粉芯,其涡流损耗随着包覆量的增加而降低,而磁滞损耗却随包覆量的增加而增加㊂因此,对于制备高性能复合磁粉芯而言,需要选择合适硅树脂包覆量达到减小涡流损耗的同时,又不会过量增加材料的磁滞损耗,从而使得磁粉芯具有较低总损耗㊂从图4还可以看出,在测量外场为1T和测量频率< 1000Hz时,磁粉芯的磁滞损耗值占总磁损耗值的主要部分,但其涡流损耗随频率变化呈指数形式增加,随着频率的增大涡流损耗增加较快,将会使得总磁损耗发生较大的变化,因此如图3插图所示,在频率为400Hz时,硅树脂包覆量为1.5%的复合磁粉芯的总磁损耗比1.2%时要大,而当频率增加到了800Hz 时,两者相反㊂图5为复合磁粉芯在直流闭路测量获得的不同测量场下的磁感应强度值,可以看出,磁粉芯800602014年第6期(45)卷的磁感应强度随包覆量增加而明显降低㊂结合图3㊁4和5对磁粉芯磁损耗和磁感应强度的变化分析可以发现,在铁粉颗粒表面包覆0.5%(质量分数)的硅树脂,可以获得具有较高密度㊁高磁感应强度和低损耗的磁粉芯㊂图5㊀复合磁粉芯在不同测量场的磁感应强度曲线Fi g5Ma g netic induction of ma g netic p owder cores for different ma g netic field3.3㊀铁粉粒径大小对复合磁粉芯交流和直流磁性能的影响本文选用3种市售不同粒径的铁粉作为研究对象,在颗粒表面上包覆0.5%(质量分数)的高温硅树脂,在相同的成型条件下制备成的复合磁粉芯的密度参见表1㊂在粉末压制成型过程中,粉末颗粒将发生变形和转动,直至颗粒之间形成良好的结合,最后达到致密化㊂一般情况下,在一定的尺寸范围内,粉末颗粒越大,压制过程更易于致密化,更容易获得较高的密度㊂对于磁粉芯而言,仅从提高密度考虑,适宜选用颗粒较大的铁粉作为原料㊂图6为3种不同粒径铁粉表面包覆0.5%硅树脂的复合磁粉芯在外磁场为1T的P e和P h随频率f 变化曲线㊂从图6(a)可以看出,铁粉粒径越大,复合磁粉芯的涡流损耗越大,而且随着测量频率增大随指数增加趋势越明显㊂从图6(b)可见,复合磁粉芯磁滞损耗随着颗粒尺寸增加而减小㊂涡流损耗变化原因在于,当铁粉颗粒完全包覆硅树脂之后,颗粒之间基本绝缘,颗粒之间的涡流损耗很小,在交流情况下,涡流损耗主要来自颗粒内部[11]㊂单个颗粒越大,颗粒内部涡流损耗将越大㊂而复合磁粉芯的磁滞损耗随粒径增加而增加,可能原因是由于压制过程产生的内应力随着粒径增加而增加,从而导致磁粉芯矫顽力增加㊂结合表1和图6可以看出选择合适粒径的铁粉制备复合磁粉芯,可以在获得高密度的同时获得较低的磁损耗㊂综上实验结果表明,在平均粒径为120μm的铁粉颗粒表面包覆0.5%(质量分数)的硅树脂可以获得具有高密度和良好软磁性能的复合软磁材料,在大功率使用条件下,获得的较好软磁性能参数为P s(B=1T,f=400Hz)= 69W/k g,B4k(H=4000A/m)=0.96T㊂在相同测量条件下,高纯铁粉-硅树脂复合磁粉芯的磁损耗低于瑞典赫格纳斯公司已商业化产品Somalo y TM500(Fe-Fe3P复合磁粉芯,P s(B=1T,f=400Hz)=72W/k g,B4k(H=4000A/m)= 0.96T)相应的值[8],两者的磁感应强度相同㊂图6㊀不同粒径铁粉表面包覆0.5%硅树脂的复合磁粉芯在外磁场为1T的涡流损耗P e和磁滞损耗P h随频率f变化曲线Fi g6Edd y loss and ma g netic h y steresis loss versus fre q uenc y for Fe-based ma g netic p owder coreswith different iron p owder p article size4㊀结㊀论(1)㊀对于同一粒径铁粉颗粒,复合磁粉芯的密度随硅树脂包覆量增加而降低㊂对于相同硅树脂包覆量,复合磁粉芯的密度随着铁粉粒径的增大而增加㊂(2)㊀在同一铁粉粒径下,复合磁粉芯的涡流损耗随硅树脂包覆量的增加而降低,而磁滞损耗却随包覆量的增加而增加,磁感应强度随包覆量增加而降低㊂(3)㊀在相同硅树脂包覆量下,复合磁粉芯的涡流损耗随着铁粉粒径增大而增加,磁滞损耗随着颗粒尺寸增大而降低㊂(4)㊀实验表明,选择合适粒径的高纯铁粉在其表面上包覆适量的高温硅树脂可以制备出具有高密度㊁低磁损耗和高饱和磁感应强度的复合软磁材料㊂在平均粒径为120μm铁粉表面上均匀包覆质量分数为0.5%硅树脂制备的复合磁粉芯,在大功率使用条件下,获得的较好软磁性能参数为:P s(B=1T,f=400Hz)= 69W/k g,B4k(H=4000A/m)=0.96T㊂参考文献:[1]㊀刘亚丕,何时金,包大新,等.软磁材料的发展趋势[J].磁性材料及器件,2003,34(3):26-32.[2]㊀邹联隆,易建宏,付应生,等.纯铁磁粉芯的磁特性研究90060张㊀蕾等:铁粉粒径和硅树脂含量对铁基复合磁粉芯软磁性能的影响[J].磁性材料及器件,1999,30(1):58-61.[3]㊀Jian g Kunlian g,Liu Xianson g,Wan g Chao,et al.Thep re p aration and characterization of iron cores with a tri-p le-coated la y er[J].Journal of Functional Materials, 2012,43(16):2153-2155.[4]㊀李发长,李㊀一,贾成厂,等.铁基软磁复合材料的制备工艺研究[C]//第七届中国功能材料及其应用学术会议论文集,2010.262-264.[5]㊀Shokrollahi H,Jan g horban K.Soft ma g netic com p ositematerials(SMCs)[J].Journal of Materials Processin gTechnolo gy,2007,(189):1-12.[6]㊀Hultman L O,Jack A G.Soft ma g netic com p osites-mate-rials and a pp lications[J].Electric Machines and DrivesConference,IEEE International,2003,(1):516-522. [7]㊀Hamler A,Gorican V,Sustarsic B,et al.The use of softma g netic com p osite materials in s y nchronous electric mo-tor[J].Journal of Ma g netism and Ma g netic Materials, 2006,(304):e816-e819.[8]㊀Andersson O,Hofecker P.Advances in soft ma g neticcom p osites materials and a pp lications[EB/OL].(2009-07-01)[2012-05-24].htt p://www.ho g /en/News-Center/Published-Articles/Advances-in-Soft-Ma g netic-Com p osites-Materials-and-A pp lications/[9]㊀Uozumi G,Watanabe M,Naka y ama R,et al.Pro p erties ofsoft ma g netic com p osite with eva p orated M g O insulationcoatin g for low iron loss[J].Materials Science Forum, 2007,(534-536):1361-1364.[10]㊀Zhon g Xiaoxi,Liu Yin g,Li Jun,et al.Structure andma g netic p ro p erties of FeSiAl-based soft ma g netic com-p osite with AlN and Al2O3insulatin g la y er p re p ared b yselective nitridation and oxidation[J].Journal of Ma g-netism and Ma g netic Materials,2012,(324):2631-2636.[11]㊀Bai Y,Zhan g ben W,Zhi y u Z,et al.Hi g h-p erformanceFe/SiO2soft ma g netic com p osites for low-loss and hi g h-p ower a pp lications[J].Journal of Ph y sics D:A pp liedPh y sics,2010,(43):365003-365009.[12]㊀Li Chan g fa,Li Yi,Liu Xue q uan,et al.Influence of ironp owder p urit y and p article size on the ma g netic p ro p er-ties of p hos p hated iron soft ma g netic com p osites[J].Journal of Functional Materials,2012,43(18):2488-2491.[13]㊀Peri g o E A,Nakahara S,Pittini-Yamada Y,et al.Ma g neticp ro p erties of soft ma g netic com p osites p re p ared with cr y s-talline and amor p hous p owders[J].Journal of Ma g netismand Ma g netic Materials,2011,(323):1938-1944. [14]㊀Neamtu B V,Geoffro y O,Chicinas I,et al.AC ma g net-ic p ro p erties of the soft ma g netic com p osites based onsu p ermallo y nanocr y stalline p owder p re p ared b y me-chanical allo y in g[J].Materials Science and En g ineerin g,2012,(177):661-665.[15]㊀吴㊀深,孙爱芝,李㊀强,等.硅酮树脂包覆铁粉制备的软磁复合材料[C]//第七届中国功能材料及其应用学术会议,2010.18-20.[16]㊀Liu J R,Itoh M,Horikawa T,et al.Iron based carbonnanocom p osites for electroma g netic wave absorber withwide bandwidth in GHz ran g e[J].A pp lied Ph y sics A:Materials Science and Processin g,2006,(82):509-513.[17]㊀宛德福,罗世华.磁性物理[M].北京:电子工业出版社,1987.270.Effects of p article size and content of silicon resin on the softma g netic p ro p erties of Fe-based ma g netic p owder coresZHANG Lei,YANG Bai,CAO Yin g,YU Ron g-hai(School of Materials Science and En g ineerin g,Beihan g Universit y,Bei j in g100191,China) Abstract:Fe-based ma g netic p owder cores b y coatin g different size of p ure iron p articles with different content of silicon resin have been fabricated via p owder com p actin g moldin g p rocess.The Effects of p article size and content of silicon resin on densit y,DC and AC ma g netic p ro p erties of ma g netic p owder cores were studied s y s-tematicall y.The best p article size and content of silicon resin were searched in order to p re p are hi g h-p erform-ance ma g netic p owder cores with hi g h densit y,low loss and hi g h ma g netic induction.The investi g ation showed that,for coatin g the same p article size of the iron p articles,the edd y loss of ma g netic p owder cores decreased with increasin g the coatin g content of silicon resin.The densit y of the ma g netic cores was also lower with the increasin g content of silicon resin,which resulted in the decrease of saturation ma g netic induction.With the same content of silicon resin,both the densit y and the edd y loss of ma g netic p owder cores increased accom p a-nied b y the increased p article size of p ure iron p articles.While the ma g netic h y steresis loss decreased with in-creasin g the p article size.The results revealed that hi g h-p erformance ma g netic p owder cores with hi g h densit y and g ood soft ma g netic p ro p erties could be s y nthesized when coatin g the p ure iron p articles of the size for 120μm with the silicon resin content of0.5wt%.Hi g h ma g netization B4k(H=4000A/m)of0.96T and low loss P s(B=1T,f=400Hz)of69W/k g were obtained for Fe-based ma g netic p owder cores in this work.Ke y words:p article size of iron p owders;coatin g content of silicon resin;Fe-based ma g netic p owder cores;densit y;soft ma g netic p ro p erties010602014年第6期(45)卷铁粉粒径和硅树脂含量对铁基复合磁粉芯软磁性能的影响作者:张蕾, 杨白, 曹莹, 于荣海, ZHANG Lei, YANG Bai, CAO Ying, YU Rong-hai 作者单位:北京航空航天大学 材料科学与工程学院,北京,100191刊名:功能材料英文刊名:Journal of Functional Materials年,卷(期):2014(6)本文链接:/Periodical_gncl201406002.aspx。
《粉体制备技术》单元设计6-水雾化化生产钢铁粉末
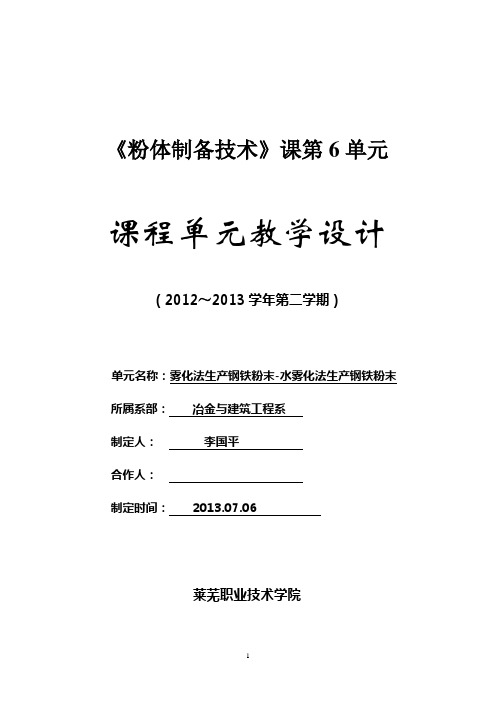
《粉体制备技术》课第6单元课程单元教学设计(2012~2013学年第二学期)单元名称:雾化法生产钢铁粉末-水雾化法生产钢铁粉末所属系部:冶金与建筑工程系制定人:李国平合作人:制定时间:2013.07.06莱芜职业技术学院《粉体制备技术》课程单元教学设计附件:教学教案项目二:雾化法生产钢铁粉末子项目1:水雾化法生产钢铁粉末指导教师:李国平莱芜职业技术学院冶金与建筑工程系2013.07.06任务1:雾化法制取金属粉末及合金粉末基础1.1 水雾化铁粉图片莱钢粉末冶金厂水雾化铁粉莱钢粉末厂水雾化纯铁粉LAP100.29金石水雾化铁粉JSW200水雾化粉未制品未腐蚀(100×)水雾化粉未制品腐蚀(100×)水雾化粉未制品腐蚀(400×)莱钢粉末厂雾化制粉电炉(15吨)学院雾化设备水雾化喷盘浇注及烤包莱钢粉末厂浇包-生产型1.2 雾化法制取金属与合金粉末的优点1.2.1 基本知识雾化法是利用高速流体直接击碎液体金属或合金而制得金属粉末的方法,应用较广泛。
用雾化法可生产熔点低于1700℃的各种金属及合金粉末。
锡、铟、铅、铝、铜、镍、铁以及各种铁合金、铝合金、镍合金、低合金钢、不锈钢、高速钢和高温合金等都能用雾化法制成粉末。
制造过滤器用的球形青铜粉、不锈钢粉、镍粉几乎全是采用雾化法生产的。
用雾化法制取金属与合金粉末具有下列特点:①雾化时金属呈熔融状态,由于在熔炼过程中较易添加各种合金元素,因而可以制得各种成分的合金粉末。
②每个粉末颗粒具有相同和均匀的化学成分,没有偏析,即每个颗粒体内不存在化学成分的微观不均匀性。
③粉末颗粒的形状、大小和结构,以及粒度分布可通过改变雾化工艺和调节工艺参数,在较宽的范围内调整。
④雾化粉末的非金属夹杂物较少,纯度较高,适于制造高强度、高密度、高性能的粉末冶金制品。
⑤粉末氧化的可能性主要在颗粒表面,粉末的氧化程度,可通过调节雾化工艺参数进行调整。
采用先进的雾化装置,严格的雾化工艺条件,可获得含氧量低于0.01%的优质合金粉末。
粉末冶金复习

一、 绪论1、 粉末冶金的特点1〕经济性 2〕性能优越性 3〕独特性2、粉末冶金与铸造相比:减少合金成分偏聚,消除粗大、不均匀的铸造组织〔含碳量及合金元素含量高,熔铸形成大量骨骼状碳化物偏析〕,硬度更高,韧性和耐磨性好,热处理变形小,使用寿命长二、粉末冶金的粉末制备球形粉:气雾化法,压坯密度高,压坯强度低树枝状: 电解法, 压坯密度低,压坯强度高生产过滤器的青铜粉偏向于粗颗粒,原因是颗粒越大,空隙越大;硬质合金需要粉末非常细,空隙度越小。
1、机械研磨法1〕加工原料要求:适于加工脆性粉末:陶瓷粉末、碳钢、硬质合金塑性材料的研磨方法:✓ 经特殊处理使其具有脆性(氢脆/氧脆)→脱氢/氧✓ 气流研磨(旋涡研磨、冷气流粉碎等)2〕粉末形状不规那么状(多角状、片状)研磨过程的四种作用力:压缩,剪切,冲击〔破碎脆性粉末主要依赖冲击〕,磨耗3〕气流研磨法:优势:颗粒自动分级,粒度较均匀;纯度高〔无研磨球及研磨介质污染〕;充入惰性气体或复原气体可防氧化;更分散,团聚更少,没有大颗粒存在✓ 分类:旋涡研磨、冷流冲击、流态化床气流磨✓ 特点:颗粒极细,粒径可到达0.1μm 以下,粒度分布窄、粒子外表光滑、形状规那么、纯度高、活性大、分散性好4★潜在计算题: 半径越小,所需冲击应力越大5★潜在计算题::,D:.Partide Sizeδ⎧⎪⎪⎨⎪⎪⎩冲击应力E:材料弹模.Elastic Modalus r:缺陷尺寸.Defect.裂纹尖端曲率半径裂纹扩展粉末尺寸n A < n 工作 < n 临界工作经历表示:✓ n =0.75n 临界:球体发生抛落,冲击力大→只能制取较粗、性脆的粉末✓ n =0.6n 临界:球以滚动为主,Colliding + Slipping action →可制取细粉✓ n<<0.6n 临界时,球以滑动为主6〕物料粉碎遵循的规律★潜在计算题:Sm 粉末极限研磨后的比外表积S0粉末研磨前的比外表积S 粉末研磨后的外表积t 研磨时间, k 常数◆潜在简答题:3.为什么会有极限研磨的颗粒大小存在“逆粉碎现象〞物料在超细粉碎过程中,随着粉碎时间的延长,颗粒粒度的减小,比外表积的增加,颗粒的外表能增大,颗粒之间的相互作用增强,团聚现象增加,到达一定时间后,颗粒的粉碎与团聚到达平衡。