ZG50Mn2热处理工艺
铸钢件常见热处理工艺
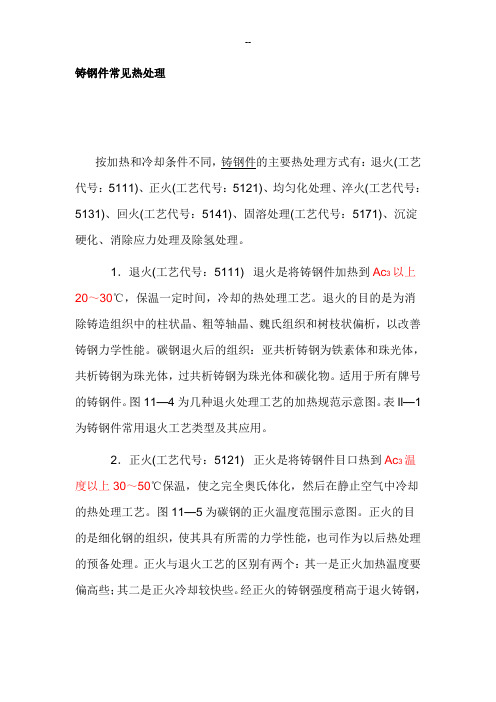
铸钢件常见热处理按加热和冷却条件不同,铸钢件的主要热处理方式有:退火(工艺代号:5111)、正火(工艺代号:5121)、均匀化处理、淬火(工艺代号:5131)、回火(工艺代号:5141)、固溶处理(工艺代号:5171)、沉淀硬化、消除应力处理及除氢处理。
1.退火(工艺代号:5111) 退火是将铸钢件加热到Ac3以上20~30℃,保温一定时间,冷却的热处理工艺。
退火的目的是为消除铸造组织中的柱状晶、粗等轴晶、魏氏组织和树枝状偏析,以改善铸钢力学性能。
碳钢退火后的组织:亚共析铸钢为铁素体和珠光体,共析铸钢为珠光体,过共析铸钢为珠光体和碳化物。
适用于所有牌号的铸钢件。
图11—4为几种退火处理工艺的加热规范示意图。
表ll—1为铸钢件常用退火工艺类型及其应用。
2.正火(工艺代号:5121) 正火是将铸钢件目口热到Ac3温度以上30~50℃保温,使之完全奥氏体化,然后在静止空气中冷却的热处理工艺。
图11—5为碳钢的正火温度范围示意图。
正火的目的是细化钢的组织,使其具有所需的力学性能,也司作为以后热处理的预备处理。
正火与退火工艺的区别有两个:其一是正火加热温度要偏高些;其二是正火冷却较快些。
经正火的铸钢强度稍高于退火铸钢,其珠光体组织较细。
一般工程用碳钢及部分厚大、形状复杂的合金钢铸件多采用正火处理。
正火可消除共析铸钢和过共析铸钢件中的网状碳化物,以利于球化退火;可作为中碳钢以及合金结构钢淬火前的预备处理,以细化晶粒和均匀组织,从而减少铸件在淬火时产生的缺陷。
3.淬火(工艺代号:5131) 淬火是将铸钢件加热到奥氏体化后(Ac。
或Ac•以上),保持一定时间后以适当方式冷却,获得马氏体或贝氏体组织的热处理工艺。
常见的有水冷淬火、油冷淬火和空冷淬火等。
铸钢件淬火后应及时进行回火处理,以消除淬火应力及获得所需综合力学性能。
图11—6为淬火回火工艺示意图。
铸钢件淬火工艺的主要参数:(1)淬火温度:淬火温度取决于铸钢的化学成分和相应的临界温度点。
ZG50SiMn钢起重机车轮水淬油冷热处理工艺

ZG50SiMn钢起重机车轮水淬油冷热处理工艺张淑杭山东石横特钢集团有限公司 山东泰安 271612摘要:采用水淬油冷热处理工艺代替传统的调质+表面淬火的热处理工艺,应用于ZG50SiMn钢起重机车轮的热处理。
试验结果表明:此工艺能满足设计和JB/T 6392—2008《起重机车轮》的使用要求,具有工艺设备操作简单、热处理成本低廉、起重机车轮使用寿命延长等优点。
关键词:ZG50SiMn钢;起重机车轮;水淬油冷;热处理1 序言起重机是钢铁行业应用最普遍、最广泛的重要运输机械设备之一,由于使用频繁、使用环境比较恶劣,起重机车轮在工作过程中不断承受周期性变化的应力作用,是易损件,每半年或一年就要进行检修,这就影响了生产,增加了维修费用,造成了一定的经济损失。
根据起重机车轮的使用特点,对其踏面硬度要求较高,并且有一定的深度和过渡层,以提高承载能力、耐磨性和抗疲劳强度等性能[1]。
合理的热处理工艺,能够充分发挥材料的潜力,提高力学性能,延长材料的使用寿命,节约能源。
因此,选择合理的热处理工艺对起重机车轮的使用尤为重要。
传统起重机车轮热处理工艺一般是先经过调质处理后再进行表面淬火,但是由于表面淬火硬度过渡层不好控制,容易剥落和轮缘磨损严重,经过较长时间的工作后,在交变应力的作用下,起重机车轮踏面容易产生裂纹或突然断裂,导致疲劳失效,严重影响起重机车轮的质量和使用寿命。
2 工艺分析铸钢与锻钢相比,具有对产品结构适应性强、材料利用率高、价格低廉、加工周期短等优点,但铸钢铸态组织晶粒粗大,有魏氏组织和成分偏析等很多不可避免的缺陷,对热处理工序产生不利的影响。
魏氏组织的存在使铸钢的塑性,特别是冲击韧度下降,因此铸钢件需要在淬火前进行热处理以消除魏氏组织。
组织晶粒粗大,容易在淬火时产生开裂,必须在淬火前进行退火或正火处理,为细化晶粒和淬火作组织准备[2]。
图1为ZG50SiMn钢直接调质,用4%硝酸酒精溶液腐蚀后的魏氏组织。
耐磨钢铸件的热处理

1.耐磨高锰钢铸件的固溶热处理——水韧处理耐磨高锰钢的铸态组织中有大量析出的碳化物,因而其韧度较低,使用中易断裂。
高锰钢铸件固溶热处理的主要目的,是消除铸态组织中晶内和晶界上的碳化物,得到单相奥氏体组织,提高高锰钢的强度和韧度,扩大其应用范围。
图11—24是Fe—Mn—C三元系含w(Mn)13%的截面相图,要消除其铸态组织的碳化物,须将钢加热至1040。
C以上,并保温适当时间,使其碳化物完全固溶于单相奥氏体中,随后快速冷却得到奥氏体固溶体组织。
这种固溶热处理又称为水韧处理。
(1)水韧处理的温度:水韧温度取决于高锰钢成分,通常为1050~1100。
C。
含碳量高或者合金含量高的高锰钢应取水韧温度的上限,如ZGMnl3钢和GXl20Mnl7钢。
但过高的水韧温度会导致铸件表面严重脱碳,并促使高锰钢的晶粒迅速长大,影响高锰钢的使用性能。
图ll-25为高锰钢在1100。
C保温2h 后铸件表面碳和锰元素的变化。
-(2)加热速率:高锰钢比一般碳钢的导热性差,高锰钢铸件在加热时应力较大而易开裂,因此其加热速率应根据铸件的壁厚和形状而定。
一般薄壁简单铸件可采用较快速率加热;厚壁铸件则宜缓慢加热。
为减少铸件在加热过程中变形或开裂,生产上常采用预先在650。
C左右保温,使厚壁铸件内外温差减小,炉内温度均匀,之后再快速升到水韧温度的处理工艺。
图ll—26为典型高锰钢件的热处理工艺规范。
(3)保温时间:保温时间主要取决于铸件壁厚,以确保铸态组织中的碳化物完全溶解和奥氏体的均匀化。
通常保温时间可按铸件壁厚25mm保温lh计算。
图ll—27为保温时间对高锰钢表面脱碳层深度的影响。
(4)冷却:冷却过程对铸件的性能指标及组织状态有很大的影响。
图11—28为不同冷却条件下高锰钢的组织。
水韧处理时铸件入水前的温度在950。
C必上,以免碳化物重新析出。
为此,铸件从出炉到A水时间不应超过30s;水温保持在30。
C以下.淬火后最高水温不超过60。
50Si2Mn弹簧钢的热处理工艺
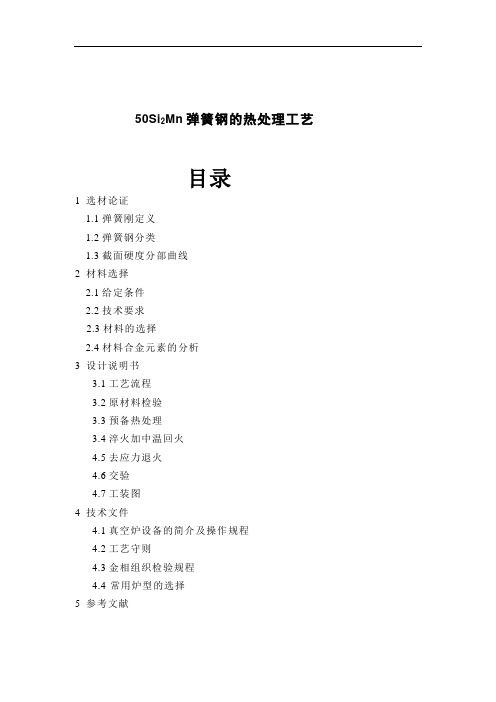
50Si2Mn弹簧钢的热处理工艺目录1 选材论证1.1弹簧刚定义1.2弹簧钢分类1.3截面硬度分部曲线2 材料选择2.1给定条件2.2技术要求2.3材料的选择2.4材料合金元素的分析3 设计说明书3.1工艺流程3.2原材料检验3.3预备热处理3.4淬火加中温回火4.5去应力退火4.6交验4.7工装图4 技术文件4.1真空炉设备的简介及操作规程4.2工艺守则4.3金相组织检验规程4.4 常用炉型的选择5 参考文献摘要通用合金弹簧钢是用途最广、最重要的弹簧材料.分析了标准合金弹簧钢的合金化特点及常用合金系列.标准合金弹簧钢使用的合金元素不够广泛,合金系列比较简单,未能充分利用多元合金化的效应.分析和研究了弹簧钢合金化的最新发展趋势.其特点是在更广泛和深入地研究合金元素作用、合金系列及合金化理论的基础上,扩大了合金元素的使用范围,特别是使用了很多以前未曾用过的微量合金元素,发展了大量多元(甚至七元或更多)合金系列,充分利用合金元素的复合合金化效果,明显改善了弹簧钢的性能关键词:弹簧合金钢热处理1选材论证1.1弹簧钢定义:弹簧钢是指由于在淬火和回火状态下的弹性,而专门用于制造弹簧和弹性元件的钢。
钢的弹性取决于其弹性变形的能力,即在规定的范围之内,弹性变形的能力使其承受一定的载荷,在载荷去除之后不出现永久变形。
弹簧钢应具有优良的综合性能,如力学性能(特别是弹性极限、弹性极限、屈强比)、抗弹减性能(即抗弹性减退性能,又称抗松弛性能)、疲劳性能、淬透性、物理化学性能(耐热、耐低温、抗氧化、耐腐蚀等)。
为了满足上述性能要求,弹簧钢具有优良的冶金质量(高的纯洁度和均匀性)、良好的表面质量(严格控制表面缺陷和脱碳)、精确的外形和尺寸。
根据GB/T 13304《钢分类》标准,按照基本性能及使用特性一,弹簧钢属于机械结构用钢;按照质量等级,属于特殊质量钢,即在生产过程中需要特别严格控制质量和性能的钢。
按照我国习惯,弹簧钢属于特殊钢,制作弹簧钢的时候技术要求比较高,技术的过硬直接决定品质的高低1.2弹簧钢分类1.2.1按照化学成分分类根据GB/T 13304 标准,弹簧钢按照其化学成分分为非合金弹簧钢(碳素弹簧钢)和合金弹簧钢。
热处理工艺规范

随着铸造件产品种类增多,对外业务增大,方便更好的管理铸造件产品,特制定本规定,要求各部门严格按照规定执行。
1 目的:为确保铸钢产品的热处理质量,使其达到国家标准规定的力学性能指标,以满足顾客的使用要求,特制定本热处理工艺规范。
2 范围本规范合用于本公司生产的各种精铸、砂铸产品的热处理,材质为各种低碳钢、中碳钢、低合金钢、中合金钢、高合金钢、铸铁及有色合金。
3 术语退火:指将铸钢产品加热到规定的温度范围,经保温一段时间后,降温出炉的操作工艺。
正火:指将铸钢产品加热到规定的温度范围,经保温一段时间后,从炉中取出,在空气中冷却下来的操作工艺。
淬火:指将铸钢产品加热到规定的温度范围,经保温一段时间后,快速冷却的操作工艺。
回火:指将淬火后的铸钢产品加热到规定的温度范围,经保温一段时间后出炉,冷却到室温的操作工艺。
调质:淬火+回火4 职责热处理操作工艺由公司技术部门负责制订。
热处理操作工艺由生产部门负责实施。
热处理操作者负责教填写热处理记录,并将自动记录曲线转换到热处理记录上。
检验员负责热处理试样的力学性能检测工作,负责力学性能检测结论的记录以及其它待检试样的管理。
5 工作程序每次装炉前应对设备进行检查,把炉底板上的氧化渣清除干净,错位炉底板应将其复位后再装,四周应留有足够的间隙,轻拿轻放,装炉应结实,摆放合理。
装炉时大铸件产品放在下面,对易产生热处理变形的铸件,必须作好防变形或者反变形处理,力学性能试样应装在高温区,对特殊小的铸件采用铁桶或者其它框类工装集中盛放。
炉车上的铸钢件入炉时,应缓慢推进,子细观察铸钢件是否与炉壁碰撞,关闭炉门,通电后应时常观察炉内工作状况。
作好铸件产品后续热处理的准备工作,严格控制出炉温度,对水淬铸件应控制入水时间,水池应有足够水量,以保证淬火质量。
作业计划应填写同炉热处理铸件产品的材质、名称、规格、数量、时间等要素,热处理园盘记录纸可多次使用,但每处理一次都必须与热处理工艺卡上的记录曲线保持一致。
50Si2Mn弹簧钢的热处理工艺
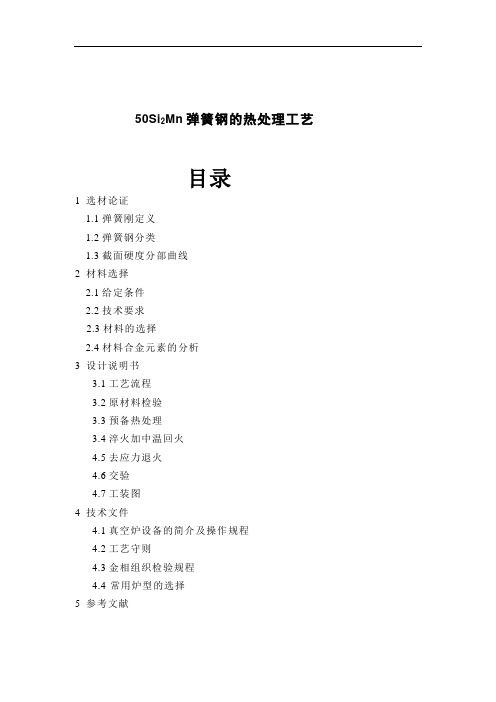
50Si2Mn弹簧钢的热处理工艺目录1 选材论证1.1弹簧刚定义1.2弹簧钢分类1.3截面硬度分部曲线2 材料选择2.1给定条件2.2技术要求2.3材料的选择2.4材料合金元素的分析3 设计说明书3.1工艺流程3.2原材料检验3.3预备热处理3.4淬火加中温回火4.5去应力退火4.6交验4.7工装图4 技术文件4.1真空炉设备的简介及操作规程4.2工艺守则4.3金相组织检验规程4.4 常用炉型的选择5 参考文献摘要通用合金弹簧钢是用途最广、最重要的弹簧材料.分析了标准合金弹簧钢的合金化特点及常用合金系列.标准合金弹簧钢使用的合金元素不够广泛,合金系列比较简单,未能充分利用多元合金化的效应.分析和研究了弹簧钢合金化的最新发展趋势.其特点是在更广泛和深入地研究合金元素作用、合金系列及合金化理论的基础上,扩大了合金元素的使用范围,特别是使用了很多以前未曾用过的微量合金元素,发展了大量多元(甚至七元或更多)合金系列,充分利用合金元素的复合合金化效果,明显改善了弹簧钢的性能关键词:弹簧合金钢热处理1选材论证1.1弹簧钢定义:弹簧钢是指由于在淬火和回火状态下的弹性,而专门用于制造弹簧和弹性元件的钢。
钢的弹性取决于其弹性变形的能力,即在规定的范围之内,弹性变形的能力使其承受一定的载荷,在载荷去除之后不出现永久变形。
弹簧钢应具有优良的综合性能,如力学性能(特别是弹性极限、弹性极限、屈强比)、抗弹减性能(即抗弹性减退性能,又称抗松弛性能)、疲劳性能、淬透性、物理化学性能(耐热、耐低温、抗氧化、耐腐蚀等)。
为了满足上述性能要求,弹簧钢具有优良的冶金质量(高的纯洁度和均匀性)、良好的表面质量(严格控制表面缺陷和脱碳)、精确的外形和尺寸。
根据GB/T 13304《钢分类》标准,按照基本性能及使用特性一,弹簧钢属于机械结构用钢;按照质量等级,属于特殊质量钢,即在生产过程中需要特别严格控制质量和性能的钢。
按照我国习惯,弹簧钢属于特殊钢,制作弹簧钢的时候技术要求比较高,技术的过硬直接决定品质的高低1.2弹簧钢分类1.2.1按照化学成分分类根据GB/T 13304 标准,弹簧钢按照其化学成分分为非合金弹簧钢(碳素弹簧钢)和合金弹簧钢。
锯片钢50Mn2v退火板

锯片刚50Mn2V退火板是一款应用范围非常广泛的钢材产品,市场关注度也相对较高。
在本文内,南京和菱贸易有限公司将会就该钢材产品的相关特性来进行详细说明。
50Mn2V属于合金结构钢板经热处理后应具有良好的基体强度、耐磨性能和焊接性能,易校平,用做锯片基体、轻质模具、弹簧等。
表面质量良好;板形好、尺寸精度高;淬透性良好。
金刚石和锯片基体材料通过胎体材料结合就可成为金刚石锯片,因其具有优越的切削性能和耐磨性能,被广泛用于石材加工、公路基建等。
通常的金刚石锯片基体材料是65Mn,但因淬火变形大、焊接性能差等缺陷影响了锯片的寿命。
近几年研制成功了金刚石锯片基体材料50Mn2V,由于该材料添加了0.08%-0.16%的钒,改善了淬火性能;同时增加了锰含量、降低了碳含量,这些都助于改善钢的各项力学和机械性能,延长锯片寿命。
50Mn2V的主体生产工艺流程是转炉冶炼—连铸—轧制。
相对而言50Mn2V的碳含量还是较高,这需要在冶炼—连铸防止时裂纹断裂产生,在轧制时要工艺合理在变形抗力符合范围内轧制。
研究发现,50Mn2V的塑性区域为830-980℃,可依据此制定合理的二次冷却及连铸制度,防止裂纹产生;另一方面,50Mn2V属中碳钢,强度高,铸坯内应力大,导热性能较差,连铸坯冷却过程中应采用缓冷,避免温度波动过大,导致断裂产生。
同时轧制试验表明,想比于典型的高变形抗力板带热轧钢DB785、3Cr2Mo,在1060-780℃范围内,3Cr2Mo钢的变形力大,其次为DB785,50Mn2V小。
可以认定50Mn2V的变形抗力小于或相当于DB785钢。
凡能生产3Cr2Mo和DB785钢的冶金企业现有设备能力完全可以用来生产金刚石锯片基体材料50Mn2V。
如果您有实际的采购需要,欢迎致电联系南京和菱贸易有限公司。
南京和菱贸易有限公司,位于六朝古都南京的鼓楼区中储生产资料市场,为钢材市场诚信单位,公司地理位置优越,交通便利。
我公司资源丰富,价格合理,服务周到,可按照客户要求,加工开平,可待定期货。
ZG50Mn2钢齿板表面淬火工艺改进

ZG50Mn2钢齿板表面淬火工艺改进李威;黄圣玲;于梅;黄玉多;刘旭东【摘要】本文针对烧结机齿板ZG50Mn2钢表面淬火产生微裂纹,从感应器及淬火温度等因素进行综合分析,查找出了微裂纹产生的原因.通过优化工艺方案解决了表面淬火微裂纹的问题,保证了产品质量.【期刊名称】《热处理技术与装备》【年(卷),期】2016(037)002【总页数】3页(P23-25)【关键词】淬火裂纹;单回路感应器;表面淬火【作者】李威;黄圣玲;于梅;黄玉多;刘旭东【作者单位】北方重工集团有限公司热处理分公司,辽宁沈阳 110141;北方重工集团有限公司煤矿机械分公司,辽宁沈阳 110141;北方重工集团有限公司热处理分公司,辽宁沈阳 110141;北方重工集团有限公司热处理分公司,辽宁沈阳 110141;北方重工集团有限公司热处理分公司,辽宁沈阳 110141【正文语种】中文【中图分类】TG157烧结机是我公司的主要产品,其中的核心零件给排矿链轮每侧均由七件二齿板和一件三齿板组成,齿板形状似特大模数齿轮,齿面与啮辊啮合推动烧结台车运行。
齿板在运行中承受巨大的弯曲、摩擦和交变应力载荷,这就要求工件具有高的耐磨性和抗接触疲劳强度。
因此齿板基体需要具有较高的综合性能并且齿面具有高的表面硬度和合理的有效硬化层深度。
我公司出口的烧结机齿板材料为ZG50Mn2钢,技术要求调质处理,齿面表面淬火,硬度50~55 HRC,有效硬化层深3~6 mm。
二齿板示意图如图1。
通常齿板调质后对齿面进行中频感应加热淬火。
以前受旧设备额定功率限制,齿面淬火采用仿形双回路感应器连续加热喷水方式[1],如图2所示。
对于ZG50Mn2钢该工艺方法时常出现局部表面淬火微裂纹,见图3。
经过分析认为,首先ZG50Mn2材质含碳量和锰量较高,奥氏体化加热时晶粒容易长大,过热倾向大,金相照片如图4所示,该金相组织按照 JB/T 9204—2008标准评级为较粗马氏体2级;其次由于齿板齿部结构相对复杂,双回路感应器加热时电场分布不均,造成工件表面温度均匀性相对较差,导致齿面淬火时局部加热温度偏高,易于诱发淬火微裂纹[2-3]。
50Mn钢制轴承密封座热处理工艺

50Mn钢制轴承寮封座热处理工艺
西北轴承股份有黻公司(宁夏锻川750021)陈克福孙建棒
l裁言
6拜×12—1206D、6巧x 12一1206z是为莺补 某公司生产的两种饿路轴承密封麇散件,两种零 件的彤状、尺寸分别如图1、图2所赫。
阵克福男,48岁, 高簸工程辉,事韭于走连 理蒜盘学特粹工程幕,现 在西北轴承股份有限套 司幔水中心,从事奢属材 料凰轴承零井热她理技 术工辞,是多项宁蔑辩装 成兼焚课题组成员。
温度过低,奥氏体化不充分,淬火后工件的硬度、 较低的介质,故选取KZ一2快速淬火油及乳化液
强度等性能指标达不到要求。因此,要得到优良 作为50Mn钢的淬火介质进行试验.从中确定最
的组织,充分发挥钢材潜在的良好性能,就必须在 佳介质。
矛盾着的因素中选择出最佳的淬火温度。
2 4回火温度的选择
根据50Mn钢的合金元素与亚共析钢的加热
在试验中实际测定,现仅选择保温时间。
火时间为4 h。
保温时间依据薄壁工件的加热经验,按下式 选取:
按以上所选择的热处理工艺参数,对50Mn 钢制试样进行淬回火加工.硬度检测结果列人表
t=(1.8~2 O)D
2。
表2 试祥淬火试验硬度检测结果
试样 绾e
温度,℃
淬火工艺 保温/robl 总时间/mln 玲却介质
0.6 ram。
睡表 万4方硬数赛据撩符鳟结果发蒜蒲3新幂热娃建
按产品辫纸足寸爰密辩廛謦赫余蘸车耩褥种 轴承密封座。采甩表3热处理最傣工落参数以投 芏亭同热娃鬻技术要求避褥淬鞠火。淬灭设备挺 薅PdX一75—9电炉,装炉撩为3。件,炉;秘火设 备使用台率式电阻炉。
热娃理精,对两种密封糍进行垒蠛按誊滞举
灰铁、球铁热处理工艺指导书
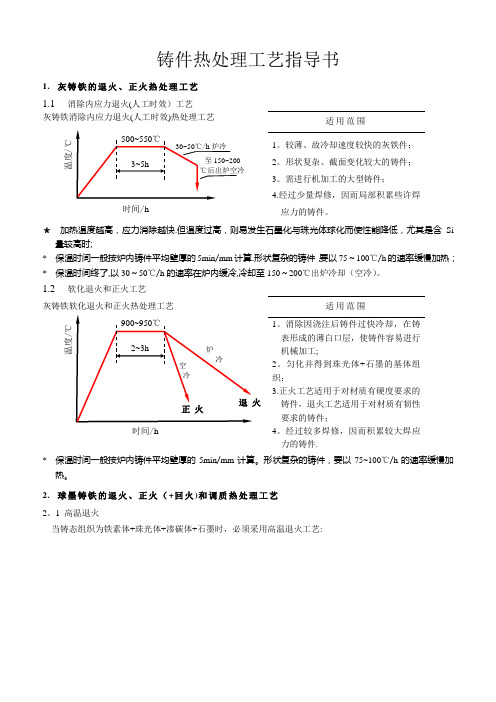
铸件热处理工艺指导书1.灰铸铁的退火、正火热处理工艺1.1消除内应力退火(人工时效)工艺灰铸铁消除内应力退火(人工时效)热处理工艺适用范围2。
形状复杂、截面变化较大的铸件;3。
需进行机加工的大型铸件;4.经过少量焊修,因而局部积累些许焊应力的铸件。
*加热温度越高,应力消除越快.但温度过高,则易发生石墨化与珠光体球化而使性能降低,尤其是含Si 量较高时;* 保温时间一般按炉内铸件平均壁厚的5min/mm计算.形状复杂的铸件,要以75~100℃/h的速率缓慢加热;* 保温时间终了,以30~50℃/h的速率在炉内缓冷,冷却至150~200℃出炉冷却(空冷)。
1.2软化退火和正火工艺灰铸铁软化退火和正火热处理工艺适用范围* 保温时间一般按炉内铸件平均壁厚的5min/mm计算。
形状复杂的铸件,要以75~100℃/h的速率缓慢加热。
2.球墨铸铁的退火、正火(+回火)和调质热处理工艺2。
1 高温退火当铸态组织为铁素体+珠光体+渗碳体+石墨时,必须采用高温退火工艺:适用范围1.获得铁素体球墨铸铁;2.分解渗碳体和珠光体,提高机械性能;3。
改善加工性能,使工件容易加工且不易变形。
*退火温度越高,渗碳体组织分解速度越快,白口现象越易消除。
但温度过高将使铸件机械性能反而变坏,发生变形和表面氧化失碳,故须严格控制温度上限.*保温时间也可按炉内铸件每15mm的有效厚度、需要保温1~2h计算,铸件白口深度大、渗碳体组织成分多时,应适当增加保温时间。
*形状复杂的铸件,要以75~100℃/h的速率缓慢加热。
保温终了,以60~80℃/h的速率在炉内缓冷,至600℃后出炉空冷。
2。
2 低温退火当铸态组织为铁素体+珠光体+石墨(没有渗碳体)时,只需采用低温退火工艺:球墨铸铁低温退火热处理工艺适用范围1。
获得铁素体球墨铸铁;2。
分解渗碳体和珠光体,提高机性能;3.改善加工性能。
*保温时间也可按炉内铸件每15mm的有效厚度、需要保温1~2h计算;* 形状复杂的铸件,要以75~100℃/h的速率缓慢加热.保温终了,以60~80℃/h的速率在炉内缓冷,至600℃后出炉空冷。
灰铸铁的热处理

灰铸铁的热处理灰铸铁的热处理退火1. 去应力退火为了消除铸件的残余应力,稳定其几何尺寸,减少或消除切削加工后产生的畸变,需要对铸件进行去应力退火。
去应力退火温度的确定,必须考虑铸铁的化学成分。
普通灰铸铁当温度起过550C 时,即可能发生部分渗碳体的石墨化和粒化,使强度和硬度降低。
当含有合金元素时,渗碳体开始分解的温度可提高到650°C左右。
通常,普通灰铸铁去应力退火温度以550C为宜,低合金灰铸铁为600C,高合金灰铸铁是可提高到650C,加热速度一般选用60〜120C/h •保温时间决定于加热温度、铸件的大小和结构复杂程度以及对消除应力程度的要求。
铸件去应力退火的冷却速度必须缓慢,以免产生二次残余内应力,冷却速度一般控制在20〜40C /h,冷却到200〜150C以下,可出炉空冷。
一些灰铸铁件的去应力退火规范示于表1.2. 石墨化退火灰铸铁件进行石墨化退火是为了降低硬度,改善加工性能,提高铸铁的塑性和韧性。
若铸件中不存在共晶渗碳体或其数量不多时,可进行低温石墨化退火;当铸件中共晶渗碳体数量较多时,须进行高温石墨化退火。
(1)低温石墨化退火,铸铁低温退火时会出现共析渗碳体石墨化与粒化,从而使铸件硬度降低,塑性增加。
灰铸铁低温石墨化退火工艺是将铸件加热到稍低于Ac1下限温度,保温一段时间使共析渗碳体分解,然后随炉冷却。
(2)咼温石墨化退火,咼温石墨化退火工艺是将铸件加热至咼于Ac1上限以上的温度,使铸铁中的自由渗碳体分解为奥氏体和石墨,保温一段时间后根据所要求的基体组织按不同的方式进行冷却。
正火灰铸铁正火的目的是提高铸件的强度、硬度和耐磨性,或作为表面淬火的预备热处理,改善基体组织。
一般的正火是将铸件加热到Ac上限+30〜50C,使原始组织转变为奥氏体,保温一段时间后出炉空冷。
形状复杂的或较重要的铸件正火处理后需再进行消除内应力的退火。
如铸铁原始组织中存在过量的自由渗碳体,则必须先加热到Ac1上限+50〜100C的温度,先进行高温石墨化以消除自由渗碳体在正火温度范围内,温度愈高,硬度也愈高。
中锰球墨铸铁热处理工艺的试验研究
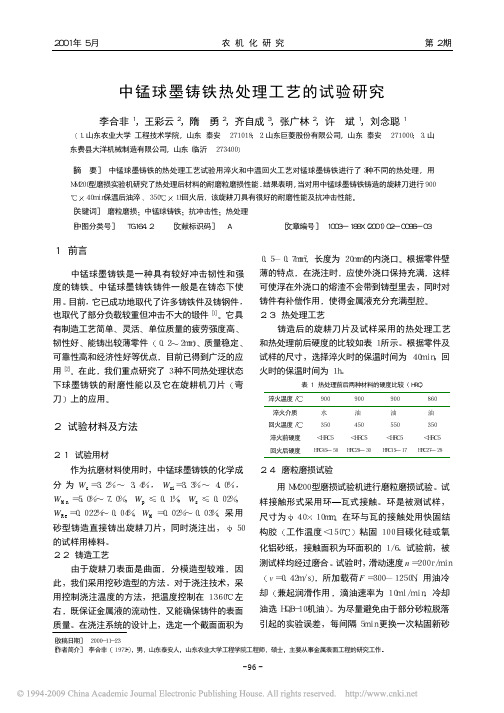
中锰球墨铸铁热处理工艺的试验研究
李合非 1 王彩云 2 隋 勇 2 齐自成 3 张广林 2 许 斌 1 刘念聪 1
1.山东农业大学 工程技术学院 山东 泰安 271018 2.山东巨菱股份有限公司 山东 泰安 271000 3.山 东费县大洋机械制造有限公司 山东 临沂 273400
表 2 不同热处理工艺下的材料在滑动 1000m 后的磨损质量损失 F=100N
900 油淬 350 回火
45 钢
中锰球墨铸铁
900 水淬 350 回火
45 钢
中锰球墨铸铁
900 油淬 550 回火
45钢
中锰球墨铸铁
79.53
70.90
79.67
73.51
80.58
73.58
79.20
70.02
3.1 试验材料的组织 热处理后的中锰球铁具有以马氏体为主的马
氏体 贝氏体 奥氏体 碳化物混合基体组织 如图 1 所示
图 1 中锰球墨铸铁经 900 油淬 350 回火后的组织 500
铸铁组织中的极少奥氏体在经受冲击条件 下 会沿晶面产生滑移 由于位错强化而使硬度显 著提高 马氏体是中锰球墨铸铁的硬相 它是高温 奥氏体快速冷却 在抑制其扩散性分解的条件下形 成的 就其本质来讲 马氏体是碳在 -Fe 中过饱 和的间隙固溶体 就其组织来讲 热处理后的中锰 球墨铸铁中的马氏体为片状马氏体 空间形态呈凸 透镜状 由于试样磨面与其相截 因此在光学显微 镜下呈针状或竹叶状 片状马氏体的显微组织特征 是马氏体片相互不平行 在一个奥氏体晶粒内 第 一片形成的马氏体往往贯穿整个奥氏体晶粒 并将 奥氏体晶粒分割成两半 使以后形成的马氏体长度 受到限制 所以片状马氏体大小不一 越是后形成 的马氏体 尺寸越小 马氏体周围往往存在残余奥 氏体 片状马氏体的最大尺寸取决于原始奥氏体晶 粒大小 奥氏体晶粒越大 则马氏体片越粗大
铸锻件调质工艺守则

铸锻件调质工艺守则1范围本标准规定了碳素钢及合金钢铸锻件调质处理的技术要求及操作规程。
本标准适用于材料为碳素钢、合金钢,截面小于800mm,硬度HB≤320的一般机器零件(如:轴、齿轮、圆盘等锻件及形状比较简单的铸件)的调质处理。
2规范性引用文件GB231-1984 金属布氏硬度试验方法GB/T699-1999 优质碳素结构钢GB/T3077-1999 合金结构钢GB/T6402-1991 钢锻件超声波检验方法GB7232-1999 金属热处理工艺术语GB7233-1987 铸钢件超声波探伤及质量评级GB8539-1987 齿轮材料及热处理检验的一般规定GB9452-1988 热处理炉有效加热区测定方法GB11352-1989 一般工程用铸造碳素钢件GB/T16923-1997 钢的正火与退火处理GB/T17394-1998 金属里氏硬度试验方法JB3877-1985 钢的淬火回火处理3名词术语3.1淬火将钢件加热到AC3或AC1点以上某一温度,保持一定时间,然后以适当速度冷却获得马氏体或贝氏体组织的热处理工艺。
3.2回火钢件淬硬后,再加热到AC1点以下某一温度,保温一定时间,然后冷却到室温的热处理工艺。
3.3调质钢件淬火后高温回火的复合热处理工艺。
3.4待调质件凡要求进行调质处理的钢材、零件坯料等统称待调质件。
3.5调质件经过调质处理的钢材或零件坯料。
4待调质件的有关规定4.1待调质件的钢种牌号适用于调质的部分钢种牌号列于表1。
表1钢组及标准号钢种牌号(1)结构钢大型碳素结构钢锻件普通含锰钢大型合金结构钢锻件35,45,55,60硅锰钢硅锰钼钒钢铬钢铬钼钢铬钼铝钢铬锰钼钢铬镍钢铬镍钼钢铬锰硅钢重型机械用弹簧钢轴承钢35SiMn,50SiMn37 SiMn2MoV40Cr, 50Cr35CrMo, 42CrMo,50 CrMo38CrMoAl40CrMnMo40CrNi, 45 CrNi34CrNiMo, 40CrNiMo30CrMnSi, 35 CrMnSi65Mn, 60Si2Mn, 50CrVAGCr15, GCr15SiMn(2) 工具钢大型锻件用碳素工具钢大型锻件用合金工具钢T7、T8、T10、T129CrSi,9Cr2,9 Cr2Mo,5 CrMnMo,5 CrNiMo,60 CrMnMo(3)特殊钢大型不锈、耐酸耐热钢锻件1 Cr13,2 Cr13,3 Cr13,4 Cr13,(4)铸钢一般工程用铸造碳钢件大型低合金钢铸件ZG270-500,ZG310-570,ZG340-640ZG40Mn2,ZG50Mn2,ZG35CrMnSi, ZG35SiMn, ZG34CrNiMo4.2 调质件的原始资料a、一般零件必须提供:钢号、预先热处理方法等。
高铬铸铁热处理工艺

高铬铸铁热处理工艺化学成分:,,,,,1、常用的高铬铸铁的热处理工艺是加热到950~1000℃,经保温空冷淬火后再进行200~260℃的低温回火;2、2、高温团球化处理1140~1180℃保温16h空冷却,可以明显提高冲击韧度和耐磨性能;高温团球化处理可使碳化物全部呈团球状,可消除或减少大块状和连续网状碳化物对基体的隔裂作用,经团球化的碳化物受到更加均匀的基体支撑,特别受到一定数量的奥氏体的支撑;如果适当减少保温时间,对薄截面零件也可以取得效果;该工艺的不足是工艺消耗热能较多;加热到1050℃,经保温空淬火后再进行 550℃的回火,效果会怎么样要控制加热速度,最好在650 750 850 时保温一定时间;我以前做过,正火就可以了;硬度能做到61----65HRC成熟工艺是:铸造后软化退火,便于加工,加工后空冷淬火加低温去应力回火;使用硬度一般要求为HRC58-62,多用于比如渣浆泵零部件等耐磨易损件;我们这里是高铬生产基地,一般提供Cr24,Cr26,Cr28,Cr15Mo3等,价格是不便宜的;价格要包括中间的软化退火和精加后的淬火及回火;楼主的材料应该叫Cr26做高铬磨球的,Cr%=~%,C%=~%,Si、S双零以下,要求硬度HRC>58我们现在用的是淬火液淬火,淬火工艺参数是:650度保温2小时,升温到960度保温小时淬火;回火温度380~400,保温4~6小时;磨球规格φ40-φ80;工艺是1050淬火+250~350回火金属耐磨材料在水泥企业的研究和应用摘要本文从金属耐磨材料的概述、水泥企业常用的耐磨材料以及根据磨损原理具体的选用金属耐磨材料,对金属耐磨材料进行了研究、分析,对其他选用金属耐磨材料给予一定的参考和借鉴;关键词金属耐磨材料水泥企业研究应用一、金属耐磨材料的概述材料的耐磨性不仅决定于材料的硬度Hm,而且更主要的是决定于材料硬度Hm和磨料硬度Ha 的比值;当Hm/Ha比值超过一定值后,磨损量便会迅速降低;当Hm/Ha≤时为硬磨料磨损,此时增加材料的硬度对材料的耐磨性增加不大;当Hm/Ha>时为软磨料磨损,此时增加材料的硬度,便会迅速地提高材料的耐磨性;金属耐磨材料一般都指的是耐磨钢,能抵抗磨料磨损的钢;这类钢还没有成为一个完全独立的钢种,其中公认的耐磨钢是高锰钢;二、水泥企业主要使用的耐磨钢在水泥工业中大多以磨料磨损为主要磨损方式;耐磨材料主要用于磨机衬板、隔仓板、篦板,球、段,破碎机锤头、板锤、反击板、颚板,立磨辊、盘等;从材质上可分为以下三大类:1.高锰钢系列该材质在八十年代前的一百余年中始终占据耐磨材料的主导地位,优点:韧性极好,在强冲击条件下产生加工硬化;缺点:易塑性变形,不耐磨;已从非强冲击条件下应用的易损件磨机衬板类中退出,但是在强冲击负荷下应用的易损件中,仍保持不可替代的优势;普通高锰钢以及为了提高屈服强度添加各种合金元素的合金高锰钢,在大型破碎机锤头、板锤、反击板、篦板、颚式破碎机颚板及圆锥破碎机内外锥等易损件中,占主导地位;超高锰钢仅限用于大型破碎机锤头和板锤;中锰钢也有部分应用;2.合金钢系列低碳中合金、中碳低合金、中碳中合金、低碳高合金等各种合金钢,由于其化学成分、热处理工艺可在很大范围内变化,最终产品的机械性能指标差距很大,硬度HRC40-60,冲击韧性ak10-100J/cm2,因此可根据易损件的应用工况条件,分析其主要磨损机制,优化和选择合金钢的化学成分和综合机械性能,达到最经济合理的选用;中碳低合金钢的优点是:合金量少,生产成本较低,依靠水淬或油淬提高硬度,满足易损件的耐磨寿命;中碳中合金钢的优点是:中等的合金含量使其基体组织得到固溶强化且有弥散碳化物,热处理工艺简单且稳定,综合机械性能较佳;与中碳低合金钢相比,即使硬度相同,耐磨性明显增高,但生产成本偏高;低碳高合金钢的优点是:低碳、高合金的化学成分配合恰当的热处理工艺,可获得非常高的韧性和较高的硬度,对受冲击负荷较大、结构复杂的易损件具有绝对的优势,缺点是生产成本高;3.抗磨白口铸铁系列该系列有高铬铸铁、中铬铸铁、低铬铸铁、镍硬铸铁及高铬铸钢等品种;总体优点:硬度高,耐磨性好;缺点:韧性不足;高铬铸铁Cr14-30%的耐磨性最好,应用范围最广,如中小型磨机衬板,球和段,小型破碎机锤头和板锤,立磨辊和盘等;大型磨机前配置了辊压机后,高铬铸铁即可扬长避短,充分发挥其优异的耐磨性,衬板使用寿命可达8年以上;低铬铸铁%的硬度、韧性均大大低于高铬铸铁,主要应用于球、段以及细磨仓衬板,优点是生产成本低,缺点是应用范围窄,综合性能和抗磨指标一般;中铬铸铁Cr8-14%仅用于铸球,降低铬含量,既可以降低生产成本,也可满足球的破碎率指标,市场中仍称之为高铬球;三、水泥企业常用耐磨材料具体选用本文以磨机为例1.粗磨仓衬板磨损机理及耐磨材料的选择粗磨仓入磨料度为15mm-25mm,研磨体平均球径φ75mm左右,最大球径φ90mm-lOOmm;磨机回转时,球和物料以较大的冲击力凿削衬板;球在下落的滑动或滚动中挤压物料,物料尖角切削衬板,因此粗磨仓衬板磨损机理是以高应力冲击凿削磨损为主,挤压切削为辅;粗磨仓衬板要求材料有足够韧性,受切削磨损要求材料具有高硬度;根据磨损原理,材料硬度Hm应为物料硬度Ha的倍以上,即H m/Ha≥,水泥熟料硬度为HV500-550,相当于HRC49-54;所以衬板材料硬度应在HRC50以上才耐磨;由于受高应力冲击凿削,冲击韧性ak≥10J/cm2才能不开裂,才满足使用要求;因此粗磨仓衬板应选择中碳中铬合金钢及其类似合金钢材料,硬度HRC48-55,冲击韧性akl5-20J/cm2,使用寿命可达2-3年;对于单螺孔衬板及沟槽衬板可参照相关标准选择高铬铸铁,使用寿命可达4-6年;对于φ3m以上的大型磨机衬板,应选择高韧性高铬铸铁,硬度HRC58-62,冲击韧性ak8-12J/cm2,使用寿命可达 6-10年;2.细磨仓村板磨损机理及耐磨材料的选择通过隔仓板进入到细磨仓的物料已变细,尖角变钝,细磨仓里的球或段直径仅为φ15mm-60mm,冲击力小,因此细磨仓衬板磨损机理是球的应力切削磨损;细磨仓衬板可以选择硬度高、韧性低的耐磨材料;如高碳合金钢,高、中、低铬铸铁,抗磨球墨铸铁等材料,硬度HRC>50,冲击韧性ak4-6J/cm2均可使用;磨机衬板不宜选择高锰钢;对粗磨仓而言,因为高锰钢的屈服强度低,易产生塑性变形,尺寸长的衬板会发生凸起变形,钢球的冲击也不能充分产生加工硬化,因此不耐磨;细磨仓衬板承受的冲击力更小,高锰钢的耐磨性更不能得到发挥;3.磨头端衬板、隔仓板、出科篦板耐磨材料的选择1磨头端衬板磨损机理及耐磨材料的选择磨头端村板在粗磨仓进料端,物料粒度大,研磨体平均球径大,受磨球和物料的侧冲击力大,是以高应力冲击凿削磨损为主、切削冲刷为辅的磨损机理;因此磨头端衬板应选择韧性高耐冲击、硬度高抗切削的材料;以前采用高锰钢,由于所受冲击不足以充分使其产生加工硬化,硬度仅能达到HB350左右,受物料切削冲刷磨损严重,使用寿命低;如果选择中碳多元合金钢衬板,硬度HRC46-50,冲击韧性ak5 J/cm2,使用寿命可比高锰钢提高一倍;φ以上大型磨机磨头端衬板在径向上分2-4块,可选择高铬铸钢,高铬铸铁类耐磨材料,使用寿命可比高锰钢高3-4倍;2隔仓板磨损机理及耐磨材料的选择粗磨仓粉磨达到一定粒度的物料是通过隔仓板篦缝到细磨仓的;物料对隔仓板蓖缝进行挤压冲刷磨损,球和物料对隔仓板进行测冲击凿削磨损,并且隔仓板为悬臂梁式安装,受力情况恶劣;因此要求材料韧性要好,冲击韧性ak≥25 J/cm2,硬度HRC45-50;高锰钢韧性好,但硬度低,不耐磨,并且易产生塑性变形,堵塞蓖缝,影响生产效率;因此隔仓板应选择中碳中铬多元合金钢及类似合金钢材料;φ3.0m以上大型磨机隔仓板是分块制作的,可选择高铬铸钢、高韧性高铬铸铁类耐磨材料,使用寿命可比高锰钢提高2-3倍;3出料篦板磨损机理及耐磨材料的选择出料蓖板在磨机的出口,主要受小球或钢段的挤压切削磨损;因此以硬度为主选择材料,可选择各类高碳合金钢、高韧性抗磨球墨铸铁等;硬度HRC50-55,冲击韧性ak8-10 J/cm2,即可满足使用要求;新型耐磨材料-Cr-Ti多元合金钢衬板,冲击韧性65-136 J/cm2,硬度HRC52-58,主要技术指标达到国外同类产品水平,其技术性能满足φ3.8m以上大型球磨机粗磨仓、细磨仓、磨头端衬板,隔仓板、出科蓖板工况条件的要求,应用范围广,寿命比高锰钢提高2-4倍,是替代高铬铸铁和传统中合金衬板的理想材料;总之,使用厂家选择理想的耐磨材料,应该考虑以下两点;第一,进行磨损失效分析,充分认识配件的工况条件,如采用干法还是湿法生产,受冲击负荷的大小,物料的种类,易磨性,粒度,物料的尖锐度等,依照磨损特性选择合适的材料;第二,进行技术经济指标对比,如果价格高,但耐磨性提高比率远大于价格比率,则应该选择质优价高的,才能提高总体经济效益;。