模具设计的一般流程(doc 20页)
压铸模具开发流程

压铸模具开发流程
1. 设计与概念阶段
- 与客户就产品要求进行沟通和确认
- 定义产品的功能和性能参数
- 进行产品的外观设计和结构设计
2. 模具设计阶段
- 根据产品设计进行模具结构设计
- 选择合适的模具钢材料
- 设计浇口、冷却系统、顶出系统等模具功能部件 - 进行模流分析和应力分析,优化模具设计
3. 模具制造阶段
- 加工模具零件
- 装配和调试模具
- 进行模具试模和优化改进
- 对模具进行热处理和机加工
4. 模具试生产阶段
- 安装模具在压铸机上
- 调试压铸工艺参数
- 生产小批量试制品
- 对产品进行检测和评估,并对模具进行修改完善
5. 量产阶段
- 正式投产
- 持续监控产品质量和模具状态
- 定期对模具进行维护保养
- 根据需求对模具进行改造或更新
在整个压铸模具开发过程中,需要密切关注客户需求,严格执行质量控制,确保模具的精度和性能,以满足产品的功能和质量要求。
同时,也要注重成本控制和工艺优化,提高模具的使用寿命和生产效率。
模具设计及制作流程及管理办法
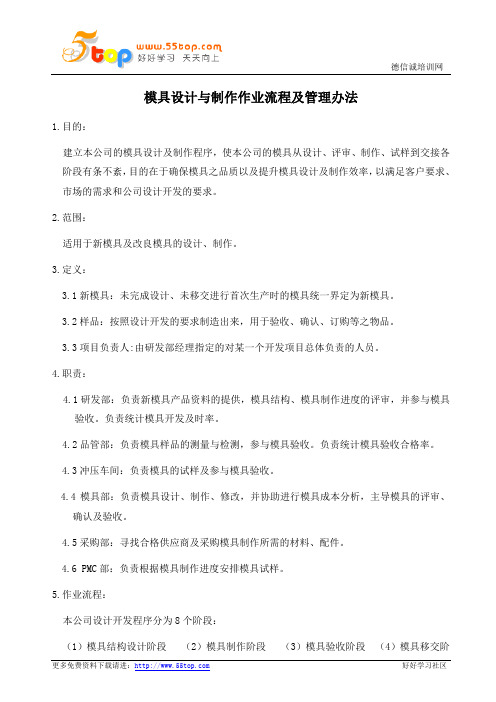
模具设计与制作作业流程及管理办法1.目的:建立本公司的模具设计及制作程序,使本公司的模具从设计、评审、制作、试样到交接各阶段有条不紊,目的在于确保模具之品质以及提升模具设计及制作效率,以满足客户要求、市场的需求和公司设计开发的要求。
2.范围:适用于新模具及改良模具的设计、制作。
3.定义:3.1新模具:未完成设计、未移交进行首次生产时的模具统一界定为新模具。
3.2样品:按照设计开发的要求制造出来,用于验收、确认、订购等之物品。
3.3项目负责人:由研发部经理指定的对某一个开发项目总体负责的人员。
4.职责:4.1研发部:负责新模具产品资料的提供,模具结构、模具制作进度的评审,并参与模具验收。
负责统计模具开发及时率。
4.2品管部:负责模具样品的测量与检测,参与模具验收。
负责统计模具验收合格率。
4.3冲压车间:负责模具的试样及参与模具验收。
4.4模具部:负责模具设计、制作、修改,并协助进行模具成本分析,主导模具的评审、确认及验收。
4.5采购部:寻找合格供应商及采购模具制作所需的材料、配件。
4.6 PMC部:负责根据模具制作进度安排模具试样。
5.作业流程:本公司设计开发程序分为8个阶段:(1)模具结构设计阶段(2)模具制作阶段(3)模具验收阶段(4)模具移交阶段各阶段内容如下:5.1模具结构设计阶段:5.1.1《模具开发申请单》经总经理批准后,研发部将申请单及相关技术文件及设计要求交模具部。
模具部经理对申请单、技术资料、相关要求进行确认。
5.1.2经模具部经理确认可行的,指定模具设计工程师进行模具设计。
模具设计工程师根据客户要求、产品图纸、设计要求设计模具结构。
并出具模具结构图。
5.1.3模具设计工程师设计出模具结构图后,交模具部经理审核。
经模具部经理审核的模具图纸,由模具设计工程师召集品管部、研发部进行模具结构评审。
评审的结果须形成《模具评审表》,对各部门在评审过程中提出的问题,模具部须制定出改善对策进行纠正,在现在技术能力、设备等因素无法解决的,则模具部经理报总工程师进行确认。
模具的使用流程

模具的使用流程1. 确定模具的用途•首先,需要明确模具的使用目的和用途,以便确定采用的模具类型和规格。
模具可以用于制造各种物品,如塑料制品、金属制品等,因此,根据具体需求选择合适的模具非常重要。
2. 设计模具图纸•在确定了模具的用途之后,需要进行模具的设计。
可以利用计算机辅助设计软件(CAD)绘制模具的图纸,包括模具的结构、尺寸、零件数量等信息。
在设计过程中需要考虑材料的选择、工艺要求以及模具的使用寿命等因素。
3. 制作模具•制作模具一般分为以下几个步骤:–模具材料选择:根据图纸上的要求,选择合适的材料进行模具的制作。
常见的模具材料有钢材、铝材等,不同的材料具有不同的特性,需要根据具体情况选择合适的材料。
–模具加工:根据设计图纸,使用机械加工设备进行模具的加工。
加工过程中需要注意精度和尺寸的控制,确保模具的质量。
–模具组装:将加工好的各个零件组装在一起,形成完整的模具。
在组装过程中需要注意零件的配合尺寸和紧固件的安装等细节,以确保模具的正常运行。
–模具调试:对组装好的模具进行调试,以确保模具的稳定性和功能正常。
–模具面处理:根据需要,对模具表面进行处理,如喷涂防锈剂、涂层处理等,以延长模具的使用寿命。
–模具测试:对制作好的模具进行测试,验证其使用效果和质量是否符合要求。
4. 使用模具•在模具制作完成并经过调试测试后,可以开始使用模具进行生产。
使用模具包括以下几个步骤:–模具安装:将模具安装在相应的设备或机器上,确保固定稳定。
–准备材料:准备好生产所需的材料,并按照要求进行投料。
–模具调整:根据产品要求,调整模具的参数,如温度、压力等,以确保产品的质量。
–生产操作:根据操作流程,使用设备或机器进行生产操作。
操作过程中需要注意安全和质量控制,及时处理异常情况。
–模具维护:在使用过程中需要定期对模具进行维护保养,包括清洁、润滑、更换耗损零件等,以延长模具的使用寿命。
5. 模具质量控制与改进•在使用过程中,需要对产品进行质量控制。
注塑模具设计操作流程
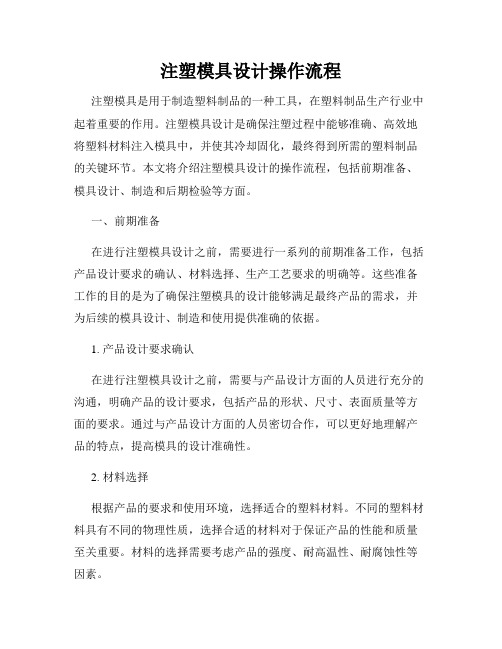
注塑模具设计操作流程注塑模具是用于制造塑料制品的一种工具,在塑料制品生产行业中起着重要的作用。
注塑模具设计是确保注塑过程中能够准确、高效地将塑料材料注入模具中,并使其冷却固化,最终得到所需的塑料制品的关键环节。
本文将介绍注塑模具设计的操作流程,包括前期准备、模具设计、制造和后期检验等方面。
一、前期准备在进行注塑模具设计之前,需要进行一系列的前期准备工作,包括产品设计要求的确认、材料选择、生产工艺要求的明确等。
这些准备工作的目的是为了确保注塑模具的设计能够满足最终产品的需求,并为后续的模具设计、制造和使用提供准确的依据。
1. 产品设计要求确认在进行注塑模具设计之前,需要与产品设计方面的人员进行充分的沟通,明确产品的设计要求,包括产品的形状、尺寸、表面质量等方面的要求。
通过与产品设计方面的人员密切合作,可以更好地理解产品的特点,提高模具的设计准确性。
2. 材料选择根据产品的要求和使用环境,选择适合的塑料材料。
不同的塑料材料具有不同的物理性质,选择合适的材料对于保证产品的性能和质量至关重要。
材料的选择需要考虑产品的强度、耐高温性、耐腐蚀性等因素。
3. 生产工艺要求明确在确定了产品的设计要求和材料选择之后,需要明确生产工艺要求。
生产工艺要求涉及到注塑过程中的各个环节,包括注塑机的选择、注塑温度的控制、注塑时间的控制等。
明确生产工艺要求可以帮助设计师更好地进行模具的设计。
二、模具设计模具设计是注塑模具设计操作流程中的核心环节,包括模具结构设计和模腔设计。
1. 模具结构设计模具结构设计是根据产品的形状和要求,确定模具的结构,包括模具的分模方式、模具的开合方式、配件的布置等。
模具结构设计需要考虑到产品的复杂性、生产效率等因素,确保模具能够满足生产需求。
2. 模腔设计模腔设计是模具设计的关键环节之一,是根据产品的形状和尺寸来确定模腔的形状和尺寸。
模腔的设计需要考虑到产品的收缩率、表面质量等因素,通过合理的模腔设计可以提高产品的成型质量。
模具制造的工艺流程
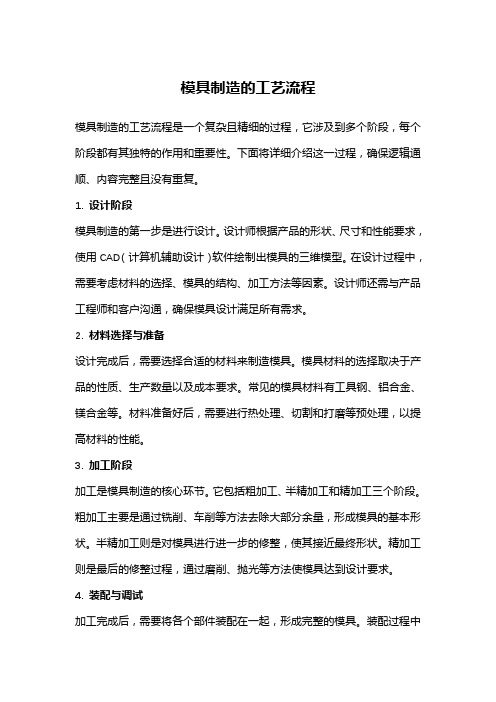
模具制造的工艺流程模具制造的工艺流程是一个复杂且精细的过程,它涉及到多个阶段,每个阶段都有其独特的作用和重要性。
下面将详细介绍这一过程,确保逻辑通顺、内容完整且没有重复。
1. 设计阶段模具制造的第一步是进行设计。
设计师根据产品的形状、尺寸和性能要求,使用CAD(计算机辅助设计)软件绘制出模具的三维模型。
在设计过程中,需要考虑材料的选择、模具的结构、加工方法等因素。
设计师还需与产品工程师和客户沟通,确保模具设计满足所有需求。
2. 材料选择与准备设计完成后,需要选择合适的材料来制造模具。
模具材料的选择取决于产品的性质、生产数量以及成本要求。
常见的模具材料有工具钢、铝合金、镁合金等。
材料准备好后,需要进行热处理、切割和打磨等预处理,以提高材料的性能。
3. 加工阶段加工是模具制造的核心环节。
它包括粗加工、半精加工和精加工三个阶段。
粗加工主要是通过铣削、车削等方法去除大部分余量,形成模具的基本形状。
半精加工则是对模具进行进一步的修整,使其接近最终形状。
精加工则是最后的修整过程,通过磨削、抛光等方法使模具达到设计要求。
4. 装配与调试加工完成后,需要将各个部件装配在一起,形成完整的模具。
装配过程中需要注意各部件之间的配合间隙和位置精度。
装配完成后,需要进行调试,检查模具的动作是否顺畅、尺寸是否合格等。
5. 试模与修正调试合格后,开始进行试模。
试模是在生产条件下模拟实际生产过程,以检验模具的性能和可靠性。
试模过程中可能会发现一些问题,如尺寸超差、表面质量不佳等。
这时需要对模具进行修正,直至达到生产要求。
6. 验收与交付修正完成后,模具需要进行验收。
验收包括外观检查、尺寸测量、性能测试等多个方面。
验收合格后,模具就可以交付给客户使用了。
交付时,需要提供相关的技术文件和操作说明书,以便客户能够正确地使用和维护模具。
7. 维护与保养模具在使用过程中,需要定期进行维护和保养。
这包括清洁模具表面、检查模具的磨损情况、润滑模具的运动部件等。
模具设计知识总结

模具设计知识总结模具设计知识总结一、模具加工工艺流程1.开料:前模料、后模模料、镶件料、行位料、斜顶料;2.开框:前模模框、后模模框;3.开粗:前模模腔开粗、后模模腔开粗、分模线开粗;4.铜公:前模铜公、后模铜公、分模线清角铜公;5.线切割:镶件分模线、铜公、斜顶枕位;6.电脑锣:精锣分模线、精锣后模模芯;7.电火花:前模粗、铜公、公模线清角、后模骨位、枕位;8.钻孔、针孔、顶针;9.行位、行位压极;10.斜顶11.复顶针、配顶针;12.其它:①唧咀、码模坑、垃圾钉(限位钉);②飞模;③水口、撑头、弹簧、运水;13.省模、抛光、前模、后模骨位;14.细水结构、拉杆螺丝拉钩、弹簧15.淬火、行位表面氮化;16.修模刻字。
二、模具设计知识(一)设计依据1.尺寸精度与其相关尺寸的正确性。
2.根据塑胶制品的整个产品上的具体要和功能来确定其外面质量和具体尺寸属于哪一种:3.外观质量要求较高,尺寸精度要求较低的塑胶制品,如玩具;4.功能性塑胶制品,尺寸要求严格;5.外观与尺寸都要求很严的塑胶制品,如照相机。
6.脱模斜度是否合理。
7.脱模斜度直接关系到塑胶制品的脱模和质量,即关系到注射过程中,注射是否能顺利进行:8.脱模斜度有足够;9.斜度要与塑胶制品在成型的分模或分模面相适应;是否会影响外观和壁厚尺寸的精度;10.是否会影响塑胶制品某部位的强度。
(二)设计程序1.对塑料制品图及实体(实样)的分析和消化:a、制品的几何形状;b、尺寸、公差及设计基准;c、技术要求;d、塑料名称、牌号e、表面要求2.型腔数量和型腔排列:a、制品重量与注射机的注射量;b、制品的投影面积与注射机的锁模力;c、模具外形尺寸与注射机安装模具的有效面积,(或注射机拉杆内间距)d、制品精度、颜色;e、制品有无侧轴芯及其处理方法;f、制品的生产批量;g、经济效益(每模的生产值)型腔数量确定之后,便进行型腔的排列,即型腔位置的布置,型腔的排列涉及模具尺寸,浇注系统的设计、浇注系统的平衡、抽芯(滑块)机构的设计、镶件及型芯的设计、热交换系统的设计,以上这些问题又与分型面及浇口位置的选择有关,所以具体设计过程中,要进行必要的调整,以达到比较完美的设计。
模具开发流程

模具开发流程模具开发是一种将产品设计成模具再制造出产品的加工技术,模具开发流程包括产品设计、模具设计、模具制造、模具试产、模具调试和模具修理等多个环节。
下面将详细介绍模具开发流程。
首先是产品设计阶段。
在这个阶段,需要根据市场需求和产品定位进行产品设计,确定产品的形状、尺寸、结构等相关要素,制定产品的设计图纸和技术要求。
产品设计要考虑到产品的可生产性,即产品是否可以通过模具加工出来,并且要注意产品的结构设计是否合理,以便于之后的模具制造。
接下来是模具设计阶段。
在这个阶段,需要根据产品的设计图纸和技术要求,进行模具的设计。
模具设计要考虑到产品的形状、尺寸、结构等要素,确定模具的结构类型和加工工艺。
同时,还需要根据模具的设计要求,绘制模具零件图纸和总装图纸,并编制相关的工艺文件和工装夹具。
然后是模具制造阶段。
在这个阶段,需要根据模具的设计图纸和技术要求,进行模具的制造。
模具制造包括模具零件的加工、模具的装配、模具的热处理和模具的表面处理等多个环节。
模具的加工工艺要根据模具的材料和加工要求进行选择,并且要保证模具的尺寸和形状的精度要求。
接着是模具试产阶段。
在这个阶段,需要使用已经制造好的模具进行试产,检验模具的加工和装配质量,以及产品的加工质量。
如果模具存在质量问题,需要进行修理或调整,直到模具能够正常使用并满足产品加工质量的要求。
最后是模具调试阶段。
在这个阶段,需要对模具进行调试,以确保模具能够正常运行,并且能够稳定地加工产品。
模具调试需要根据产品的加工要求进行参数的调整,包括注塑参数、模具温度和模具开合速度等。
通过模具调试,可以确保模具能够正常生产产品,并且能够达到产品加工质量的要求。
在整个模具开发流程中,还需要进行模具修理的工作。
模具使用一段时间后,可能会出现磨损、变形或损坏等问题,需要进行修理或更换模具零件。
模具修理要根据模具的问题进行诊断和处理,包括修复、调整或更换零件。
综上所述,模具开发流程包括产品设计、模具设计、模具制造、模具试产、模具调试和模具修理等多个环节,每个环节都需要严格按照技术要求和工艺流程进行操作,以保证模具能够正常生产出满足产品要求的产品。
模具制作流程

模具制作流程一、同意任务书成型塑料制件的任务书通常由制件设计者提出,其内容如下:1. 通过审签的正规制制件图纸,并注明使用塑料的牌号、透明度等。
2. 塑料制件说明书或者技术要求。
3. 生产产量。
4. 塑料制件样品。
通常模具设计任务书由塑料制件工艺员根据成型塑料制件的任务书提出,模具设计人员以成型塑料制件任务书、模具设计任务书为根据来设计模具。
二、收集、分析、消化原始资料收集整理有关制件设计、成型工艺、成型设备、机械加工及特殊加工资料,以备设计模具时使用。
1. 消化塑料制件图,熟悉制件的用途,分析塑料制件的工艺性,尺寸精度等技术要求。
比如塑料制件在外表形状、颜色透明度、使用性能方面的要求是什么,塑件的几何结构、斜度、嵌件等情况是否合理,熔接痕、缩孔等成型缺陷的同意程度,有无涂装、电镀、胶接、钻孔等后加工。
选择塑料制件尺寸精度最高的尺寸进行分析,看看估计成型公差是否低于塑料制件的公差,能否成型出合乎要求的塑料制件来。
此外,还要熟悉塑料的塑化及成型工艺参数。
2. 消化工艺资料,分析工艺任务书所提出的成型方法、设备型号、材料规格、模具结构类型等要求是否恰当,能否落实。
成型材料应当满足塑料制件的强度要求,具有好的流淌性、均匀性与各向同性、热稳固性。
根据塑料制件的用途,成型材料应满足染色、镀金属的条件、装饰性能、必要的弹性与塑性、透明性或者者相反的反射性能、胶接性或者者焊接性等要求。
3. 确定成型方法使用直压法、铸压法还是注射法。
4、选择成型设备根据成型设备的种类来进行模具,因此务必熟知各类成型设备的性能、规格、特点。
比如关于注射机来说,在规格方面应当熟悉下列内容:注射容量、锁模压力、注射压力、模具安装尺寸、顶出装置及尺寸、喷嘴孔直径及喷嘴球面半径、浇口套定位圈尺寸、模具最大厚度与最小厚度、模板行程等,具体见有关参数。
要初步估计模具外形尺寸,推断模具能否在所选的注射机上安装与使用。
5. 具体结构方案(一)确定模具类型如压制模(敞开式、半闭合式、闭合式)、铸压模、注射模等。
模具设计与管理程序文件
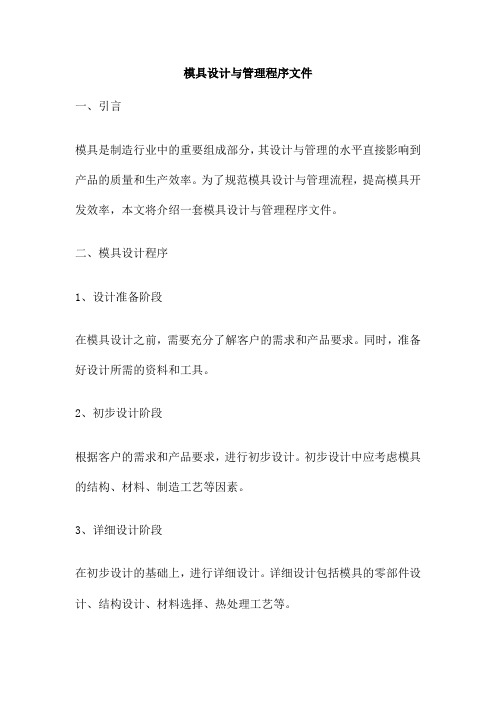
模具设计与管理程序文件一、引言模具是制造行业中的重要组成部分,其设计与管理的水平直接影响到产品的质量和生产效率。
为了规范模具设计与管理流程,提高模具开发效率,本文将介绍一套模具设计与管理程序文件。
二、模具设计程序1、设计准备阶段在模具设计之前,需要充分了解客户的需求和产品要求。
同时,准备好设计所需的资料和工具。
2、初步设计阶段根据客户的需求和产品要求,进行初步设计。
初步设计中应考虑模具的结构、材料、制造工艺等因素。
3、详细设计阶段在初步设计的基础上,进行详细设计。
详细设计包括模具的零部件设计、结构设计、材料选择、热处理工艺等。
4、审核与修改阶段完成详细设计后,需经过专业人员审核和修改,确保模具设计的合理性和可行性。
三、模具管理程序1、模具采购管理根据生产计划和需求,制定模具采购计划。
采购过程中要严格控制模具的质量和交货期。
2、模具库存管理建立完善的模具库存管理制度,包括模具的入库、保管、出库等环节。
确保模具库存的准确性和安全性。
3、模具维护与保养定期对模具进行检查、维护和保养,延长模具的使用寿命。
对于损坏的模具,应及时进行修复和更换。
4、模具报废管理对于无法修复或无使用价值的模具,应进行报废处理。
报废处理应遵循公司的相关规定。
四、总结本文介绍了一套完整的模具设计与管理程序文件。
通过这套程序文件,可以规范模具设计与管理的流程,提高模具开发效率和质量。
也有利于公司的成本控制和生产计划的顺利进行。
程序文件模具管理程序标题:医疗器械购销合同样本一、合同概述医疗器械购销合同是医疗器械生产商与销售商之间,或医疗机构与销售商之间,就医疗器械买卖而签订的书面协议。
该合同旨在明确双方的权利和义务,规范交易行为,确保医疗器械的质量和安全。
以下是医疗器械购销合同的样本。
二、合同主体甲方(采购方):__________医院乙方(供应方):__________医疗器械有限公司三、合同内容1、医疗器械名称、规格、型号、数量及价格:详细列出采购的医疗器械清单,包括名称、规格、型号、数量及单价等。
模具加工流程

模具加工流程模具加工是一种工艺复杂的加工过程,主要是通过先进的机器设备对模具材料进行切削、成型和加工等步骤,最终制造出具有特定形状和尺寸的模具产品。
下面是一般模具加工的流程概述:1. 设计和制定加工方案:根据客户提供的产品图纸和需求,加工工程师进行设计和制定加工方案。
这包括材料选择、工艺规程、设备选择和加工工具计划等。
2. 材料准备:根据加工方案,选择适当的材料,并从供应商处采购。
常用的模具材料有钢、铝合金、铜合金等。
在购买材料之前,需要进行一系列测试以确保其质量满足要求。
3. 材料切割:根据图纸标识的尺寸要求,将所选材料切割成所需的大小块状。
这可以通过剪切机、锯床、电火花等加工设备完成。
4. 粗加工:通过使用机床设备,如铣床、车床、钻床等,对材料进行粗加工。
根据加工方案,在模具上进行定位和夹紧,以确保精度和稳定性。
5. 精加工:通过精密的机床设备,如CNC(计算机数控)铣床、CNC钻床、CNC车床等,对模具进行进一步的精加工。
这些高精度的设备可以将材料加工成所需的形状和尺寸。
6. 表面处理:根据需要,对模具的表面进行处理。
这可以包括磨砂、抛光、电镀、喷砂等。
这些工艺可以改善模具表面的光洁度和耐腐蚀性。
7. 装配和调试:根据设计要求,将模具的各个零部件进行装配。
然后,对模具进行调试。
这包括安装模具零件,检查和调整尺寸,以确保模具的正常工作和性能。
8. 检验和质量控制:对加工完成的模具进行检验和测试,以确保其质量符合要求。
这可以通过三坐标测量机、投影仪等设备进行,以检查尺寸、形状和表面质量。
9. 交付和售后服务:完成模具加工后,根据客户要求和约定,将模具交付给客户。
此外,模具制造商还通常提供售后服务,包括模具维护、修理和更新等。
综上所述,模具加工是一个复杂且琐碎的过程,需要严格遵循工艺流程和质量控制,以确保加工出高质量的模具产品。
制品模具制作流程及注意事项

制品模具制作流程及注意事项嘿,宝子们!今天咱们来唠唠制品模具制作流程及注意事项呀。
**一、制作流程**1. 设计阶段哎呀呀,这可是非常关键的一步呢!首先得根据制品的要求进行设计。
设计师要考虑制品的形状、尺寸、精度要求哇,这些都是重中之重呀!比如说,如果是一个形状特别复杂的塑料制品,那模具的设计可就不简单了呢!设计的时候还要考虑脱模的便利性,要是脱模不方便,那后面可就麻烦大了呀!这个阶段要用到专业的设计软件,像CAD、UG之类的,设计师要在软件里把模具的各个部分精确地画出来呢。
2. 材料准备哇,材料的选择也很有讲究呢!不同的制品可能需要不同的模具材料。
一般来说,有钢材、铝材等。
如果是制作高精度、高负荷的模具,那肯定得选择优质的钢材啦,像Cr12MoV这种钢材就很不错呢!在准备材料的时候,要确保材料的质量符合要求呀。
可不能有裂缝或者杂质之类的问题哦,不然做出来的模具质量肯定不过关呢!3. 加工制造这一步可复杂啦!加工制造包括切割、铣削、钻孔等工序呢。
切割的时候要按照设计的尺寸精确切割呀,哎呀,差一点都不行呢!铣削是为了把模具的各个面加工得光滑平整,就像给它做美容一样呢。
钻孔呢,是为了安装一些配件,比如说顶针之类的。
在加工过程中,要不断地测量尺寸,确保加工的精度呀。
要是精度不够,那做出来的模具可能就装不上,或者制品会出现尺寸偏差呢!这可就糟糕了呀!4. 组装调试嘿,到了这一步,就像是把各个零件拼凑成一个完整的艺术品一样呢!把加工好的各个部件按照设计要求组装起来。
组装的时候要注意各个部件的配合精度哦。
然后就是调试阶段啦,调试的时候要试模,看看做出来的制品是否符合要求。
如果有问题,比如说制品有飞边、缺料等现象,那就得分析原因,是模具装配有问题呢,还是加工精度有问题呢?要及时调整呀!**二、注意事项**1. 精度控制哇,精度真的是模具制作中非常非常重要的一点呢!不管是在设计阶段还是加工制造阶段,都要严格控制精度。
模具设计评审流程及相关要求
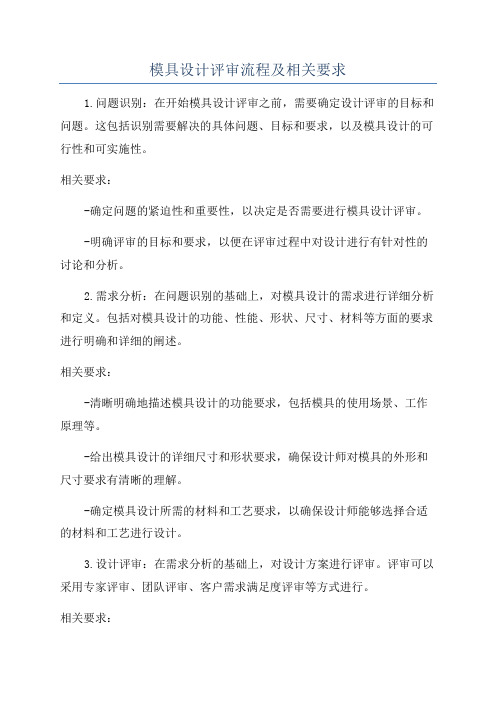
模具设计评审流程及相关要求1.问题识别:在开始模具设计评审之前,需要确定设计评审的目标和问题。
这包括识别需要解决的具体问题、目标和要求,以及模具设计的可行性和可实施性。
相关要求:-确定问题的紧迫性和重要性,以决定是否需要进行模具设计评审。
-明确评审的目标和要求,以便在评审过程中对设计进行有针对性的讨论和分析。
2.需求分析:在问题识别的基础上,对模具设计的需求进行详细分析和定义。
包括对模具设计的功能、性能、形状、尺寸、材料等方面的要求进行明确和详细的阐述。
相关要求:-清晰明确地描述模具设计的功能要求,包括模具的使用场景、工作原理等。
-给出模具设计的详细尺寸和形状要求,确保设计师对模具的外形和尺寸要求有清晰的理解。
-确定模具设计所需的材料和工艺要求,以确保设计师能够选择合适的材料和工艺进行设计。
3.设计评审:在需求分析的基础上,对设计方案进行评审。
评审可以采用专家评审、团队评审、客户需求满足度评审等方式进行。
相关要求:-评审人员应具备相关领域的专业知识和经验,以能够对设计方案进行全面、准确的评估。
-评审过程应具备针对设计方案的参数、性能、可行性等方面进行的评估和分析。
-评审过程中应注意客户需求的满足度,确保设计方案符合客户的要求和期望。
4.优化改进:根据评审结果,对设计方案进行优化改进。
可以通过修改设计方案、更换材料、优化工艺等方式来提升设计方案的性能和质量。
相关要求:-设计师应能够根据评审结果,提出合理、具体的优化改进方案。
-优化改进的方案应能够在不影响设计方案整体性能的前提下,提高其性能和质量并满足客户需求。
-评审人员应对优化改进方案进行评估和分析,确保改进方案的可行性和有效性。
5.最终确定:经过优化改进后,对设计方案进行最终确定。
这需要得到相关部门和客户的认可和审批。
相关要求:-最终确定的设计方案应满足问题识别和需求分析中的要求,并经过评审和优化改进的验证。
-最终确定的设计方案应经过客户的认可和审批,确保其符合客户的要求和期望。
模具设计的详细流程

模具设计的详细流程产品的前期处理很多同学在学习的时候进入了一个学习误区(拿着一个产品就开始急急忙忙的分模)首先我们拿到一个产品后,先不要急着分模,最重要的一件事就是先检查产品结构,产品公差的修改,拔模,一些产品还会有段差的出现.当你前期处理完后那么产品的分型面,结构基本就能确定出来了,以及浇口的位置。
当然这些最终还是要跟客户确认的。
确认产品的不合理处有些同学可能会问,是不是我分析好了产品结构后,就可以开始设计模具了呢,答案当然是不能。
要想在设计时少走弯路,修修改的话,那么一定要了解客户对模具的要求,这些是一定要达到客户要求的.客户用来生产的注塑机的吨位及型号类型。
这个确认不好,你就没法确认你模具的浇口套的入口直径以及定位圈的直径,顶出孔的大小跟位置,甚至模架的大小,模具的高度等等.你辛辛苦苦的设计好了一套好的模具结构,你也颇有成就感,可模具到了客户那里没法生产,模具大小厚度跟客户的注塑机对不上,客户是不会验收你设计好的模具,估计那时你会有种欲哭无泪的感觉。
分析产品的问题点,以及产品夹线,产品材料及收缩率。
不要想当然的认为ABS的塑料收缩率就一定是0.5%,这个一定要跟客户确认好,要知道他们最终用于生产的材料是什么牌号的,有没有添加什么改性材料等等。
有条件时,最好能熟知产品的装配关系以及产品的用途等等,这些信息对于将来的模具结构设计是非常有帮助的。
因为了解了这些,你就知道哪些是外观面,哪些是非外观,哪些地方的拔模角度是可以随便加大的,哪些地方是不能改的。
甚至包括一些产品的结构,如果你了解了产品的实际装配关系以及用途,你就知道哪些倒扣结构是可以取消或改成另外一种简单形式的。
一定要牢记,做模具的过程就是把复杂问题简单化的过程。
常看到一些人做了一套多么多么复杂的结构而感到骄傲自豪,我觉得那是非常得无知。
因为很多产品工程师可能会由于自身的经验问题,设计了一些不太合理的结构,如果作为下游工序,不能帮他们指正的话,他们可能永远都觉得那样设计是没问题的。
- 1、下载文档前请自行甄别文档内容的完整性,平台不提供额外的编辑、内容补充、找答案等附加服务。
- 2、"仅部分预览"的文档,不可在线预览部分如存在完整性等问题,可反馈申请退款(可完整预览的文档不适用该条件!)。
- 3、如文档侵犯您的权益,请联系客服反馈,我们会尽快为您处理(人工客服工作时间:9:00-18:30)。
模具设计的一般流程(doc 20页).模具设计———成品篇 1 利用Pro/E 进行模具设计的一般流程2 成品检查及处理2.1 肉厚检查对于塑料模来说,肉厚不均会严重影响到最终的射出成型。
因此,成品检查及处理利用Pro/E 拆模倒钩处理模仁处理滑斜入顶肉厚脱模角缩水拿到一个成品,我们最先要做的是肉厚检查。
对于有肉厚不均的现象要及早通知客户, 以及时寻求解决方案。
进行成品肉厚分析的方法:Pro/E main menu → Analysis → Model Analysis弹出如图2-1所示对话框:(右图为选取Slices 后的对话框)图2-1选择分分析指定层状显选取分析結显示所清除显保存分显示分设定最设定最选取方设定层设定1)选取Thickness:2)选择Slices 在Slices Offset中输入103)根据成品要求及塑料特性输入最大肉厚(本例为2.4)与最小肉厚(1.8)4)选取起始位置点与终止位置点5)选择方向平面,点取Compute分析结果中红色圈内表示肉厚过厚,蓝色圈内表示肉厚过薄,即在允许的肉厚范围之外。
点Show all , Pro/E将显示图标结果; 点Clear,将清除图标结果显示;可以用Info来查看相关文字信息。
本例分析结果如图2-2所示:图2-22.2 脱模角检查为了保证成品的顺利脱出,使模具开模时不至于有粘模现象,需要在平行于开模方向的壁上有一定的脱模角度。
进行脱模角检查的方法:Pro/E main menu: → Analysis → Surface Analysis弹出如图2-3所示对话框:图2-3点取Display 后出现对话框如图2-4所示:选择分选择分选择中选择脱最大脱要检查脱模显示方图2-41)选取Draft Check:2)选择分析对象为Part:3)选择脱模中性面,指定分析脱模方向4)确定要检查单侧还是双侧,指定最小的脱模角(本例中为0.5)5)选取显示方式图2-5为用三种颜色显示的脱模角检查结果,窗口左上角显示的为颜色和角度对照表。
图2-5全色显三种颜色显示结果显示的2.3 缩水处理(Shrinkage)塑料在冷却过程中会收缩,从而影响成品的外观。
为了保证成品的外形,在拆模前需对成品加些预加量,即作缩水处理。
菜单调用步骤如图2-6所示:放缩水的方式有Formula 、By Dimension 、By Scaling 三种。
图2-6选择By Scaling ,X 、Y 、Z 为方向因子,即在X 、Y 、Z 三个方向上均作Shrinkage 处理。
根据提示选择基准坐标系,再依次输入X 、Y 、Z 三个方向上的Shrinkage 系数(此系数由塑料特性决定)。
完成缩水处理后的成品除尺寸较原始成品要大外,从外形看不出差别。
为根据按尺按比示区别可另存一个档案,并以”_shk”作为标识。
3 用Pro/E拆模经上述处理后,可以进到Assembly中开始拆模,步骤如下:1)建立组立档,组立放过缩水的成品进来Component →Assemble (选用Coord Sys对齐)2)创建两个Part档作为公母模仁Component →Create →Part →Solid输入Part名Fix01Locale Default Datums →Align Csys To Csys选择组立档的Csys用同样的方法建立另一个Part,取名为Move013)进入Fix01拷贝母模面Modify →Mod Part →Sel By Menu 选取Fix01用Copy →Surf & Bnd拷贝母模面,再用Copy、Boundaries、Flat、Merge等方式缝合母模面。
注:母模面是否完全闭合,可打成线架构看其黄色边界是否只有一条。
单独打开Fix01 Part档,完整的母模面如图3-7所示:图3-74)在Fix01中用Protrusion长一个长方体注:其大小为最后加工时的模仁大小,尺寸以能完全包住刚拷贝的母模面,再圆整成整数为原则。
5)依次延伸母模边界到刚建的长方体四周Extend →Along Dir →Up To Plane6)用Cut →Use Quilt切出母模仁完成后的母模仁如图3-8所示:图3-87)回到组立档,用Mod Part进入Move018)用Protrusion长个长方体,作为公模仁9)Cut Out出公模仁Component →Adv Utils →Cut OutSel By Menu 选择Mover01作为被Cut Out的对象→Done SelSel By Menu依次选择Fix01、Design作为要切除的对象→Done Sel进入Move01查看公模仁,完成的公模仁如图3-9所示:图3-910)在组立图里将公模仁打成线架构,检视完成的公母模仁View →Model SetUp →Component Display →Create 图3-10→Wireframe 选择公模仁,结果如图3-10所示:公成图3-10母4倒钩处理4.1滑块在母模侧上部有个凸起(对应于成品上部的天线孔),如图4-11所示,很显然将会影响到成品的脱出。
为了保证能顺利开模,需要将凸起的倒钩部分做成滑块,使其在开模时能顺利脱开。
图4-11滑块的具体做法是:1)单独打开Fix012)Cut出滑块头部的外形,如图4-12所示:圖3)另存新档为Fix024)打开组立档,利用Coord Sys将Fix02组立进来5)在母模上Cut Out掉滑块,完成后的母模如图4-13所示:图4-13注:对于留在成品外部的倒钩,可做成滑块形式。
4.2斜销在公模侧的下部有个凹陷(对应于成品下部的卡钩),同样会影响到成品的脱出,如图4-14中红色所示部份。
为了能将成品顺利从公模上取出,需要对此卡钩部位做些处理。
由于倒钩出现在成品内部,很显然不能做成滑块的形式,这时我们可以将其处理成斜梢。
斜梢的做法同滑块基本一样,具体操作介绍如下:单独打开Move011)将倒钩部份整块Cut下来(厚度取整数),如图4-15所示图4-14图4-152)以图4-15红色箭头所指面作为草绘平面,Cut出斜梢的形状。
注:由于卡钩部份是在成品内侧,要使成品能从卡钩部分脱出,必需在水平方向上有个运动分量。
所以将斜梢做成与开模方向上有个夹角,使开模时卡钩部位能沿水平方向退开。
完成后的斜梢如图4-16所示:图4-163)另存新档为Move024)打开组立档,利用Coord Sys将Move02组立进来5)在公模上Cut Out掉斜梢,此时的公模如图4-17所示图4-175模仁处理5.1入子模仁的成型面主要靠NC铣床及放电来加工,由于受刀具及电极的影响,模仁上的深孔及凸起过高部分很难加工,而且成本很高。
如图5-18红圈所圈起来的几个BOSS成形部位。
这时可以将这些部位从模仁上分割下来单独加工,即做成入子。
图5-18入子的制作比较简单,主要要考虑加工的可行性及经济性,一般原则是能用NC加工的部位不做入子。
1)单独打开Move032)Cut出入子外形,如图5-19左图所示:注:入子外形选用原则:孔易于线割加工,而入子周围的轮廊线不会影响到成品的外观。
如图5-19右图所示之入子就不合理。
图5-193)另存新档名为Move034)重复前三步操作,依次完成另个四个入子Move04 、Move05、Move06、Move075)打开组立档,利用Coord Sys将五个入子组立进来6)从公模上Cut Out掉五个入子,此时的公模如图5-20所示至此,模仁部分的设计基本完成。
在实际的模具设计中还有很多的辅助机构,诸如顶针、浇道、水路、排气孔、模座等。
由于这些机构的制作都大同小异,这里不作过多的介绍。
在本章的最后一节将就顶针部分作些简要介绍,剩下部分由读者自行学习。
图5-205.2顶针顶针对于塑料模具来说具有很重要的作用,完成射塑后的成品在冷却过程中会收缩,在一些侧壁较深的地方会产生较大的抱紧力,从而无法将成品顺利取出。
如图5-21所示,蓝色线架构部分为成品,其四周侧壁都较深,因而开模时这些地方会产生较大的抱紧力。
为了解决这个问题,通常的做法是在抱紧力较大的地方排一些顶针。
在开模时,通过顶出板带动顶针,从而将成品从公模仁上顶出,使成品完全脱离模仁。
顶针的作用很大,但制作却极为简单,实际生产中一般采用标准顶针。
在用Pro/E进行模具设计时,只需切出相应的部位即可,方法同入子。
具体操作介绍如下:图5-211)单独打开Move012)按标准件的尺寸Cut出顶针外形,如图5-22所示:图5-22 注:为了加工方便,顶针的位置尺寸一般要圆整为整数,以不干涉其它机构为原则。
3)另存新檔为Pin01 4)用同样的方法完成其它几个顶针 5) 打开Assembly 檔,利用Coord Sys 将这些顶针组立进来6) 从公模仁中Cut Out 出各个顶针图6-23为全部完成后爆炸状态的模具组立图: 公滑成斜頂母入。