合成氨生产主要分为几个工序
合成氨

合成氨的主要原料可分为固体原料、液体原料和气体原料。
经过近百年的发展,合成氨技术趋于成熟,形成了一大批各有特色的工艺流程,但都是由三个基本部分组成,即原料气制备过程、净化过程以及氨合成过程。
工艺路线:造气-> 半水煤气脱硫-> 压缩机1 ,2 工段-> 变换-> 变换气脱硫-> 压缩机3 段-> 脱硫-> 压缩机4 ,5 工段-> 铜洗-> 压缩机 6 段-> 氨合成-> 产品NH3 1. 合成氨的工艺流程(1) 原料气制备:将无烟煤(或焦炭)由炉顶加入固定床层煤气发生炉中,并交替向炉内通入空气和水蒸汽,燃料气化所生成的半水煤气经燃烧室、废热锅炉回收热量后送入气柜。
半水煤气由气柜进入电除尘器,除去固体颗粒后依次进入压缩机的Ⅰ、Ⅱ、Ⅲ段,加压到 1.9~2.0Mpa ,送入脱硫塔,用 A.D.A. 溶液或其他脱硫溶液洗涤, 以除去硫化氢,随后,气体经饱和塔进入热交换器,加热升温后进入一氧化碳变换炉,用水蒸汽使气体中的一氧化碳变为氢。
变换后的气体,返回热交换器进行降温,并经热水塔的进一步降温后,进入变换器脱硫塔,以除去变换时产生的硫化氢。
然后,气体进入二氧化碳吸收塔,用水洗法除去大部分二氧化碳。
脱碳后的原料进入压缩机Ⅳ、Ⅴ段,升压到压缩机12.09~13.0Mpa后,依次进入铜洗塔和碱洗塔,使气体中残余的一氧化碳和二氧化碳含量进一步降至20 (ppm )以下,以满足合成氨的要求。
净化后的原料气进入压缩机的最后一段,升压到30.0~32.0 MPa 进入滤油器,在此与循环压缩机来的循环气混合,经除油后,进入冷凝塔和氨冷器的管内,再进入冷凝塔的下部,分离出液氨。
分离出液氨后的气体进入冷凝塔上部的管间,与管内的气体换热升温后进入氨合成塔。
在高温高压并有催化剂存在的条件下,将氮氢气合成氨。
出合成塔的气体中,约含氨10~20% ,经水冷器与氨冷器将氨液化并分离后,其气体进入循环压缩机循环使用。
合成氨工艺流程简介

合成氨工艺流程简介在200MPa的高压和500℃的高温和催化剂作用下,N2+3H2==2NH3,经过压缩冷凝后,将余料在送回反应器进行反应,合成氨指由氮和氢在高温高压和催化剂存在下直接合成的氨。
世界上的氨除少量从焦炉气中回收副产外,绝大部分是合成的氨。
合成氨主要用作化肥、冷冻剂和化工原料。
生产方法生产合成氨的主要原料有天然气、石脑油、重质油和煤(或焦炭)等。
①天然气制氨。
天然气先经脱硫,然后通过二次转化,再分别经过一氧化碳变换、二氧化碳脱除等工序,得到的氮氢混合气,其中尚含有一氧化碳和二氧化碳约0.1%~0.3%(体积),经甲烷化作用除去后,制得氢氮摩尔比为3的纯净气,经压缩机压缩而进入氨合成回路,制得产品氨。
以石脑油为原料的合成氨生产流程与此流程相似。
②重质油制氨。
重质油包括各种深度加工所得的渣油,可用部分氧化法制得合成氨原料气,生产过程比天然气蒸气转化法简单,但需要有空气分离装置。
空气分离装置制得的氧用于重质油气化,氮作为氨合成原料外,液态氮还用作脱除一氧化碳、甲烷及氩的洗涤剂。
③煤(焦炭)制氨。
随着石油化工和天然气化工的发展,以煤(焦炭)为原料制取氨的方式在世界上已很少采用。
用途氨主要用于制造氮肥和复合肥料,氨作为工业原料和氨化饲料,用量约占世界产量的12%。
硝酸、各种含氮的无机盐及有机中间体、磺胺药、聚氨酯、聚酰胺纤维和丁腈橡胶等都需直接以氨为原料。
液氨常用作制冷剂。
贮运商品氨中有一部分是以液态由制造厂运往外地。
此外,为保证制造厂内合成氨和氨加工车间之间的供需平衡,防止因短期事故而停产,需设置液氨库。
液氨库根据容量大小不同,有不冷冻、半冷冻和全冷冻三种类型。
液氨的运输方式有海运、驳船运、管道运、槽车运、卡车运合成氨是以碳氨为主要原料, 我司可承包的合成氨生成成套项目, 规模有 4×104 吨/年, 6×104 吨/年, 10×104 吨/年, 30×104 吨/年, 其产品质量符合中国国家标准.1. 工艺路线:以无烟煤为原料生成合成氨常见过程是:造气 -> 半水煤气脱硫 -> 压缩机1,2工段 -> 变换 -> 变换气脱硫 ->压缩机3段 -> 脱硫 ->压缩机4,5工段 -> 铜洗 -> 压缩机6段 -> 氨合成 -> 产品NH3采用甲烷化法脱硫除原料气中CO. CO2 时, 合成氨工艺流程图如下:造气 ->半水煤气脱硫 ->压缩机1,2段 ->变换 -> 变换气脱硫 -> 压缩机3段 ->脱碳 -> 精脱硫 ->甲烷化 ->压缩机4,5,6段 ->氨合成 ->产品NH32.技术指标:(1) 原料煤: 无烟煤: 粒度15-25mm 或25-100mm固定75%蒸汽: 压力0.4MPa, 1-3MPa(2) 产品: 合成氨:氨含量(99.8%)残留物含量(0.2%)3. 消耗定额: ( 以4×104 吨/年计算)(1) 无烟煤( 入炉) : 1,300kg(2) 电: 1,000KWH( 碳化流程), 1,300KWH( 脱碳流程)(3) 循环水: 100M3(4) 占地: 29,000M24. 主要设备:(1) 造气炉(2) 压缩机(3) 铜洗(4) 合成塔。
合成氨生产工艺简介
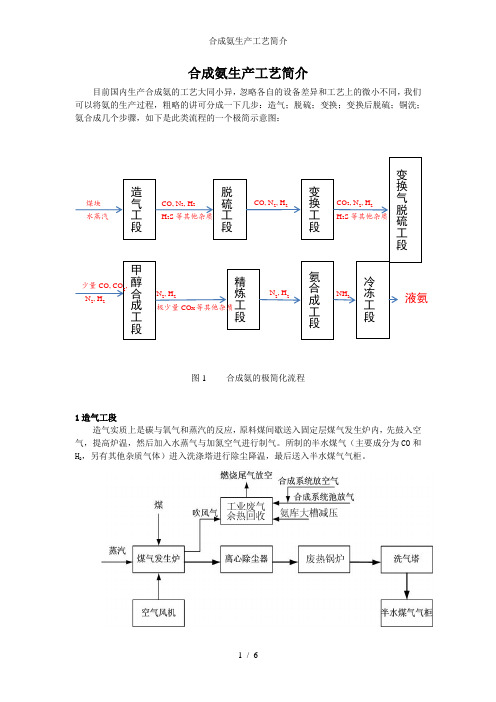
合成氨生产工艺简介目前国内生产合成氨的工艺大同小异,忽略各自的设备差异和工艺上的微小不同,我们可以将氨的生产过程,粗略的讲可分成一下几步:造气;脱硫;变换;变换后脱硫;铜洗;氨合成几个步骤,如下是此类流程的一个极简示意图:图1 合成氨的极简化流程1造气工段造气实质上是碳与氧气和蒸汽的反应,原料煤间歇送入固定层煤气发生炉内,先鼓入空气,提高炉温,然后加入水蒸气与加氮空气进行制气。
所制的半水煤气(主要成分为CO和H2,另有其他杂质气体)进入洗涤塔进行除尘降温,最后送入半水煤气气柜。
造气工段脱硫工段变换工段煤块水蒸汽CO, N2, H2H2S等其他杂质CO, N2, H2变换气脱硫工段CO2, N2, H2H2S等其他杂质甲醇合成工段少量CO, CO2,N2, H2精炼工段N2, H2极少量CO X等其他杂质氨合成工段N2, H2冷冻工段NH3液氨图2 造气工艺流程示意图2脱硫工段煤中的硫在造气过程中大多以H2S的形式进入气相,它不仅会腐蚀工艺管道和设备,而且会使变换催化剂和合成催化剂中毒,因此脱硫工段的主要目的就是利用DDS脱硫剂脱出气体中的硫。
气柜中的半水煤气经过静电除焦、罗茨风机增压冷却降温后进入半水煤气脱硫塔,脱除硫化氢后经过二次除焦、清洗降温送往压缩机一段入口。
脱硫液再生后循环使用。
图3 脱硫工艺流程图3变换工段气体从脱硫工艺中处理过后,已不含H2S等有毒气体。
变换工段的主要任务是将半水煤气中的CO在催化剂的作用下与水蒸气发生放热反应,生成CO2和H2。
经过两段压缩后的半水煤气进入饱和塔升温增湿,并补充蒸汽后,经水分离器、预腐蚀器、热交换器升温后进入中变炉回收热量并降温后,进入低变炉,反应后的工艺气体经回收热量和冷却降温后作为变换气送往压缩机三段入口。
说明:合成气的中的CO(一氧化碳)经蒸汽转换成CO2(二氧化碳)与H2,转换后气体称为“变换气”。
图4 变换工艺流程图4变换气脱硫与脱碳经变换后,气体中的有机硫转化为H2S,需要进行二次脱硫,使气体中的硫含量在25mg/m3。
合成氨工艺

贮运商品氨中有一部分是以液态由制造厂运往外地。此外,为保证制造厂内合成氨和氨加工车间之间的供需平衡,防止因短期事故而停产,需设置液氨库。液氨库根据容量大小不同,有不冷冻、半冷冻和全冷冻三种类型。液氨的运输方式有海运、驳船运、管道运、槽车运、卡车运。直接合成氨。于1908年申请专利,即“循环法”,在此基础上,他继续研究,于1909年改进了合成,氨的含量达到6%以上。这是目前工业普遍采用的直接合成法。反应过程中为解决氢气和氮气合成转化率低的问题,将氨产品从合成反应后的气体中分离出来,未反应气和新鲜氢氮气混合重新参与合成反应。
工艺简介:工艺流程图如下:
中温变换护的正常操作应该是将各段催化剂的温度控制在适宜的范围内,以充分发挥催化剂的活性。同时用最低的蒸汽消耗实现最高的CO变换率。影响中变炉催化剂床层温度变化的因素很多,如蒸汽的加入量、蒸汽的温度、进入催化剂前反应气体的温
(4)中置锅炉液位;
(5)中置锅炉压力;
(6)冷凝塔液位;
(7)分离器液位;
(8)蒸发器液位。
其中触媒温度控制可采用全系数法自适应控制,其他回路采用PID控制。
二 主要控制方案
(一)造气工段控制
工艺简介:
固定床间歇气化法生产水煤气过程是以无烟煤为原料,周期循环操作,在每一循环时间里具体分为五个阶段;(1)吹风阶段约37s;(2)上吹阶段约39s;(3)下吹阶段约56s;(4)二上吹阶段约12s;(5)吹净阶段约6s.
化学肥料,20%作为其它化工产品的原料。
合成氨工艺

合成氨工艺陈昶君化九三20090118921.合成氨生产工艺流程图(1)煤为源头工艺路线:以无烟煤为原料生成合成氨常见过程是:造气->半水煤气脱硫->压缩机1,2工段->变换->变换气脱硫->压缩机3段->脱硫->压缩机4,5工段->铜洗->压缩机6段->氨合成->产品NH3造气过程为以煤为原料,用间歇式固定层常压气化法,反应方程为煤+氧气→二氧化碳二氧化碳+煤→一氧化碳煤+水蒸气→一氧化碳+氢气(2)天然气为源头采用天然气、焦化千气力原料的合成氨生产工艺流程包括:脱硫、转化、变换、脱碳、甲烷化、氨的合成、吸收制冷及输入氨库和氨吸收八个工序(一)脱琉原料气进入后,首先进入三段脱硫塔.第一、二段分别采用5—6%Na0H和10。
12%Na0H碱洗,第三段采用水洗。
在脱硫塔内。
气体中大部分无机硫和部分有机硫被碱液吸收,湿法脱硫后的焦化干气由压缩机道往一段转化炉对流段,加热至340—3500C后,进人干法脱硫槽。
干法脱硫剂通常采用氧化锰、氧化锌或钴—铜催化剂。
经干法脱硫后。
焦化干气中的总硫量要求低于3ppm.这里需要进行痕量硫的测定。
(二)转化经脱硫合格的焦化干气返回对流五段与来自废热锅炉的蒸汽混合,加热至500.610%后,进入一段转化炉(简称一段炉),控制共水碳比为3.5.4.0。
在催化刘作用下原料气转化为氢气、一氧化碳和二氧化碳。
反应所需的大量热能由转化炉两倜均匀分布的无焰燃烧喷嘴供给,反应温度控制在760—7的℃;出口气中残余甲烷含量要求小于10%。
一段沪出口气与空气压缩机送来的空气相混合,进人二段转化炉(简称二段炉)内燃烧,温度达到900一950。
C,在催化捌作用下,甲烷转化成一氧化碳和二氧化碳;二段炉出口气中残余甲烷应小于0.3%。
同时获取合成气所需的氮气,并控制氢、氮比在2.8—3.1之问。
在整个转化过程要进行原料气的总碳分析和一、二段炉出口气残余甲烷的分析。
合成氨与尿素生产工艺

合成氨与尿素生产工艺
一、合成氨及尿素的生产工艺
1、氮气合成工艺:
氮气合成是合成氨工艺的前期工序,它是一种利用多种原料,以固定
压力和温度下的反应,将原料转化为氮气的过程。
氮气合成一般采用流动
态铭朱-必利宁反应器,其原料有天然气和空气,原料由高压力投入反应器,在固定的温度及压力下,产物是氮气和水蒸汽,氮气分别在滤筒及吸
收塔中分离产物,最后通过真空泵和低温冷凝法回收氮气。
2、氨合成工艺:
氨合成是合成氨工艺的核心步骤,若采用的是甲烷加氮反应法合成氨,主要采用连续流体层析塔(FCC)-必利宁反应器,原料有氮气、甲烷和水,先将甲烷和氮气在高压力下投入反应器内,在固定的温度及压力下进行反应,反应产物是氨气和水蒸汽,氨气经过滤筒等分离设备中分离产物,最
后由真空泵及低温冷凝法回收氨气。
3、尿素合成工艺:
尿素合成是合成氨工艺的后期工序,常采用的是氨气合成尿素的方法,主要采用的是热交换反应器,其原料有氨气、二氧化碳和水,氨气和二氧
化碳在高压力下输入反应器,在适当的温度和压力下进行反应,反应产物
是尿素气体,尿素气体经过滤筒及吸收塔中分离产物,最后由真空泵及低
温冷凝法回收尿素气体。
合成氨生产过程包含的主要工序
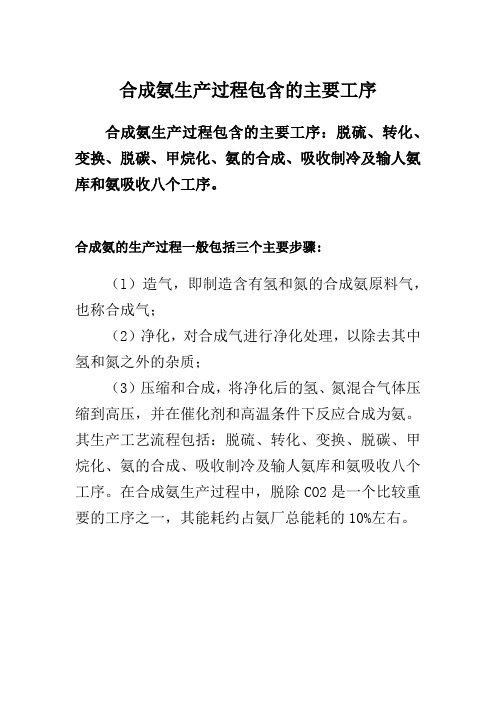
合成氨生产过程包含的主要工序
合成氨生产过程包含的主要工序:脱硫、转化、变换、脱碳、甲烷化、氨的合成、吸收制冷及输人氨库和氨吸收八个工序。
合成氨的生产过程一般包括三个主要步骤:
(l)造气,即制造含有氢和氮的合成氨原料气,也称合成气;
(2)净化,对合成气进行净化处理,以除去其中氢和氮之外的杂质;
(3)压缩和合成,将净化后的氢、氮混合气体压缩到高压,并在催化剂和高温条件下反应合成为氨。
其生产工艺流程包括:脱硫、转化、变换、脱碳、甲烷化、氨的合成、吸收制冷及输人氨库和氨吸收八个工序。
在合成氨生产过程中,脱除CO2是一个比较重要的工序之一,其能耗约占氨厂总能耗的10%左右。
合成氨工艺

合成氨工艺————————————————————————————————作者:————————————————————————————————日期:合成氨工艺流程(1)原料气制备将煤和天然气等原料制成含氢和氮的粗原料气。
对于固体原料煤和焦炭,通常采用气化的方法制取合成气;渣油可采用非催化部分氧化的方法获得合成气;对气态烃类和石脑油,工业中利用二段蒸汽转化法制取合成气。
(2)净化对粗原料气进行净化处理,除去氢气和氮气以外的杂质,主要包括变换过程、脱硫脱碳过程以及气体精制过程。
①一氧化碳变换过程在合成氨生产中,各种方法制取的原料气都含有CO,其体积分数一般为12%~40%。
合成氨需要的两种组分是H2和N2,因此需要除去合成气中的CO。
变换反应如下:CO+H2OH→2+CO2 =-41.2kJ/mol 0298HΔ由于CO变换过程是强放热过程,必须分段进行以利于回收反应热,并控制变换段出口残余CO含量。
第一步是高温变换,使大部分CO转变为CO2和H2;第二步是低温变换,将CO含量降至0.3%左右。
因此,CO变换反应既是原料气制造的继续,又是净化的过程,为后续脱碳过程创造条件。
②脱硫脱碳过程各种原料制取的粗原料气,都含有一些硫和碳的氧化物,为了防止合成氨生产过程催化剂的中毒,必须在氨合成工序前加以脱除,以天然气为原料的蒸汽转化法,第一道工序是脱硫,用以保护转化催化剂,以重油和煤为原料的部分氧化法,根据一氧化碳变换是否采用耐硫的催化剂而确定脱硫的位置。
工业脱硫方法种类很多,通常是采用物理或化学吸收的方法,常用的有低温甲醇洗法(Rectisol)、聚乙二醇二甲醚法(Selexol)等。
粗原料气经CO变换以后,变换气中除H2外,还有CO2、CO和CH4等组分,其中以CO2含量最多。
CO2既是氨合成催化剂的毒物,又是制造尿素、碳酸氢铵等氮肥的重要原料。
因此变换气中CO2的脱除必须兼顾这两方面的要求。
一般采用溶液吸收法脱除CO2。
常见的合成氨工艺流程图有 哪些?
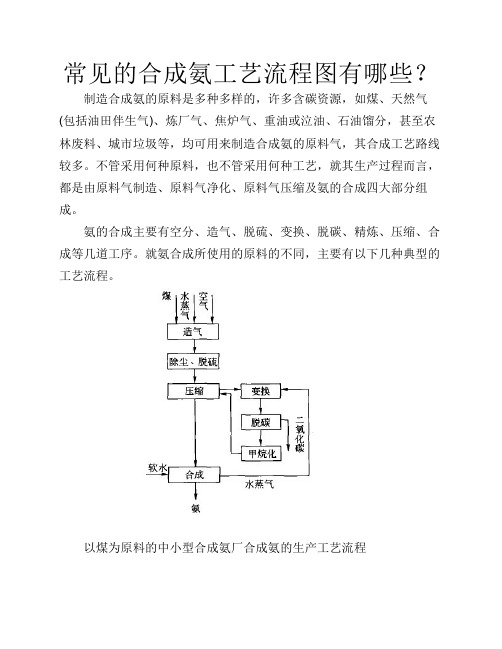
常见的合成氨工艺流程图有哪些? 制造合成氨的原料是多种多样的,许多含碳资源,如煤、天然气(包括油田伴生气)、炼厂气、焦炉气、重油或泣油、石油馏分,甚至农林废料、城市垃圾等,均可用来制造合成氨的原料气,其合成工艺路线较多。
不管采用何种原料,也不管采用何种工艺,就其生产过程而言,都是由原料气制造、原料气净化、原料气压缩及氨的合成四大部分组成。
氨的合成主要有空分、造气、脱硫、变换、脱碳、精炼、压缩、合成等几道工序。
就氨合成所使用的原料的不同,主要有以下几种典型的工艺流程。
以煤为原料的中小型合成氨厂合成氨的生产工艺流程
以天然气为原料的合成氨生产工艺流程
以焦炉气为原料的合成氨生产工艺流程
以渣油为原料的合成氨生产工艺流程。
合成氨工艺流程
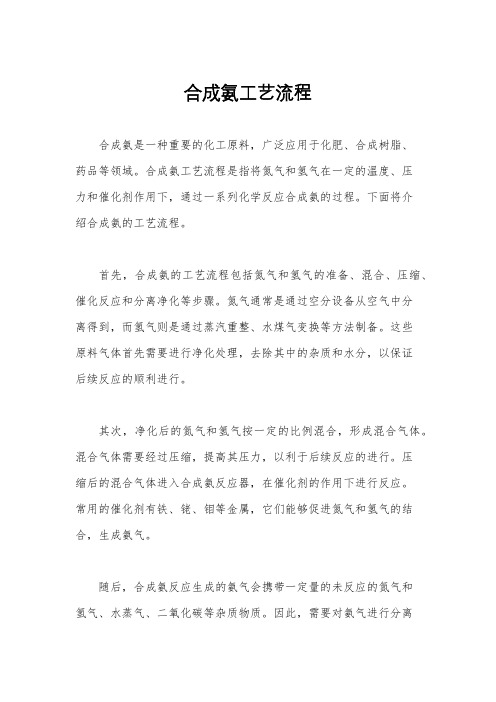
合成氨工艺流程合成氨是一种重要的化工原料,广泛应用于化肥、合成树脂、药品等领域。
合成氨工艺流程是指将氮气和氢气在一定的温度、压力和催化剂作用下,通过一系列化学反应合成氨的过程。
下面将介绍合成氨的工艺流程。
首先,合成氨的工艺流程包括氮气和氢气的准备、混合、压缩、催化反应和分离净化等步骤。
氮气通常是通过空分设备从空气中分离得到,而氢气则是通过蒸汽重整、水煤气变换等方法制备。
这些原料气体首先需要进行净化处理,去除其中的杂质和水分,以保证后续反应的顺利进行。
其次,净化后的氮气和氢气按一定的比例混合,形成混合气体。
混合气体需要经过压缩,提高其压力,以利于后续反应的进行。
压缩后的混合气体进入合成氨反应器,在催化剂的作用下进行反应。
常用的催化剂有铁、铑、钼等金属,它们能够促进氮气和氢气的结合,生成氨气。
随后,合成氨反应生成的氨气会携带一定量的未反应的氮气和氢气、水蒸气、二氧化碳等杂质物质。
因此,需要对氨气进行分离净化,以获得高纯度的合成氨产品。
分离净化通常包括吸附分离、蒸馏分离、冷凝分离等工艺,将杂质物质从氨气中分离出去,得到纯净的合成氨。
最后,经过分离净化的合成氨可以用于制备各种化工产品。
除了用作化肥原料外,合成氨还可以用于生产硝化剂、合成尿素、合成氨基酸等化工产品。
因此,合成氨工艺流程的稳定运行对于化工生产具有重要意义。
总之,合成氨工艺流程是一个复杂的化学过程,需要严格控制各个环节的参数,确保反应的高效进行。
只有通过科学的工艺设计和严格的操作管理,才能获得高质量的合成氨产品,满足化工生产的需求。
化工工艺学简答题含答案

化工工艺学简答题含答案第一章合成氨1.合成氨的主要生产工序,各工序的作用和任务?答:1.原料气制备,制备含有氢、氮的原料气。
用煤、原油或自然气作原料,制备含氮、氢气的原料气。
2.净化,由于无论用何种方法造气,原料气中都含有对合成氨反响过程有害的各种杂质,必需实行适当的方法除去这些杂质,主要包括变换过程、脱硫脱碳过程以及气体精制过程。
3.压缩和合成,将纯洁的氢、氮混合气压缩到高压,在铁催化剂的作用下合成氨。
2.写出烃类蒸汽转化的主要反响。
CH 4+H 2O(g)=CO+3H 2,CH 4=2 H 2+C3.简述常用脱硫方法及技术特点以及适用流程。
答:干法脱硫(氧化锌法脱硫;钴钼加氢脱硫法)是用固体吸取剂吸取原料气体中的硫化物一般只有当原料气中硫化氢质量浓度不高标准状态下在3-5g/m 3才适用。
特点:能脱除有机硫和无机硫而且可以把脱得很精细,但脱硫剂不能再生而且设备浩大占地多,不适用于脱除大量无机硫,只有自然气、油田气等含硫低时才使用;湿法脱硫〔化学吸取法,物理吸取法,化学-物理综合吸取法〕特点:脱硫剂是便于运输的液体物料,脱硫剂是可以再生并且能回收的硫磺,适用于脱除大量无机硫。
4.改进 ADA 法脱硫的主要化学反响和脱硫原理是什么?ADA 法脱硫主要化学反响及脱硫原理:在脱硫塔中用PH 为 8.5--9.2 的稀碱溶液吸取硫化氢并生成硫化氢物:液相中的硫化氢物进一步与偏钒酸钠反响,生成复原性焦性偏钒酸钠盐并析出无素硫复原性焦性偏钒酸钠盐接着与氧化态 ADA 反响,生成复原态的 ADA 和偏钒酸盐复原态的 ADA 被空气中的氧气氧化成氧化态的 ADA ,其后溶液循环使用 4.少量 CO 的脱除方法有哪些?答:铜氨液洗涤法、甲烷化法、液氮洗涤法。
5.以自然气为原料生产合成气过程有哪些主要反响?答:主反响:CO+H 2O(g)=H 2+CO 2 ,CH 4+H 2O(g)=CO+3H 2副反响:CH 4=2 H 2+C ,2CO=C+CO 2,CO+H 2=H 2O+C6.简述一段转化炉的炉型构造。
张希

生产实习报告应化一班张希 08032050120本次生产实习是用东方仿真软件对合成氨生产的进行模拟操作,在这里面合:成氨的生产主要分为三个工序,依次是:合成氨装置净化工段、合成氨装置转化工段、合成氨装置合成工段。
下面就依次对每个工段的内容与操作进行详细的介绍。
一、合成氨装置净化工段合成氨装置净化工段的工艺流程1、脱碳变换气中的CO2是氨合成触媒(镍的化合物)的一种毒物,因此,在进行氨合成之前必须从气体中脱除干净。
工艺气体中大部分CO2是在CO2吸收塔101-E中用活化aMDEA溶液进行逆流吸收脱除的。
从变换炉(104-D)出来的变换气(温度60℃、压力2.799MPa),用变换气分离器102-F将其中大部分水分除去以后,进入CO2吸收塔101-E下部的分布器。
气体在塔101-E内向上流动穿过塔内塔板,使工艺气与塔顶加入的自下流动的贫液(解吸了CO2的aMDEA溶液,40℃(TI_24))充分接触,脱除工艺气中所含CO2,再经塔顶洗涤段除沫层后出CO2吸收塔,出CO2吸收塔101-E后的净化气去往净化气分离器121-F,在管路上由喷射器喷入从变换气分离器(102-F)来的工艺冷凝液(由LICA17控制),进一步洗涤,经净化气分离器(121-F)分离出喷入的工艺冷凝液,净化后的气体,温度44℃,压力2.764MPa,去甲烷化工序(106-D),液体与变换冷凝液汇合液由液位控制器LICA26调节去工艺冷凝液处理装置。
CO2吸收塔101-E出来的富液(吸收了CO2的aMDEA溶液)先经溶液换热从器(109-CB1/2)加热、再经溶液换热器(109-CA1/2),被CO2汽提塔102-E(102-E 为筛板塔,共10块塔板)出来的贫液加热至105℃(TI109),由液位调节器LIC4控制,进入CO2汽提塔(102-E)顶部的闪蒸段,闪蒸出一部分CO2,然后向下流经102-E汽提段,与自下而上流动的蒸汽汽提再生。
合成氨工艺流程图

合成氨合成氨指由氮和氢在高温高压和催化剂存在下直接合成的氨,世界上的氨除少量从焦炉气中回收副产外,绝大部分是合成的氨。
合成氨主要用作化肥、冷冻剂和化工原料。
①天然气制氨。
天然气先经脱硫,然后通过二次转化,再分别经过一氧化碳变换、二氧化碳脱除等工序,得到的氮氢混合气,其中尚含有一氧化碳和二氧化碳约0.1 %~0.3 %(体积),经甲烷化作用除去后,制得氢氮摩尔比为 3 的纯净气,经压缩机压缩而进入氨合成回路,制得产品氨。
以石脑油为原料的合成氨生产流程与此流程相似。
②重质油制氨。
重质油包括各种深度加工所得的渣油,可用部分氧化法制得合成氨原料气,生产过程比天然气蒸气转化法简单,但需要有空气分离装置。
空气分离装置制得的氧用于重质油气化,氮作为氨合成原料外,液态氮还用作脱除一氧化碳、甲烷及氩的洗涤剂。
③煤(焦炭)制氨。
随着石油化工和天然气化工的发展,以煤(焦炭)为原料制取氨的方式在世界上已很少采用。
o 合成氨工艺流程图o 合成氨的在线分析检测点序检测点被测组分典型量程备注号A1 半水煤气O2 0~1%A2 脱硫H2S、SO2 0~5%A3 中变出口CO 0~5%A4 低变出口CO 0~1%A5 脱碳出口CO2 0~2%A6 再生CO2(入口)O2 0~15%A7 精练气(甲烷化)出口CO2+CO2 0~50ppmA8 合成塔入口新鲜气H2 50~80%CH4 0~15%A9 合成循环气H2 40~70%A10 天然气制氢一段炉CH4 0~15%A11 天然气制氢二段炉CH4 0~1%A12 重油制氢汽化炉CH4 0~10%。
合成氨工厂实习报告

合成氨工厂实习报告一、实习概述本次实习是在合成氨工厂进行的,为期一个月。
工厂是国内较大的化工企业,主要从事氨的生产与销售。
本次实习的目的是了解合成氨生产的基本原理、工艺流程以及实际操作过程,并对工厂的运行管理进行观察和学习。
二、合成氨工艺流程1.原料准备:工厂使用大气氮气和合成气作为原料,同时还需要进一步处理原料,确保其纯度和适应生产要求。
2.合成氨反应器:原料经过处理后进入反应器,通过高温高压的条件进行合成氨的反应。
反应器内采用特殊的催化剂,促进氮气和氢气的结合生成氨气。
3.合成氨分离:合成氨反应后,需要进行分离和净化处理。
通过一系列的分离工序,将反应产生的氨气与未反应的原料气体进行分离,并净化产生高纯度的合成氨。
4.合成氨压缩:分离净化后的合成氨由低压输送至合成氨压缩机,进行压缩处理使其达到所需压力,并送至储气罐进行储存。
5.合成氨储存与输送:合成氨通过管道输送至储气罐进行储存,用于下游工艺使用或销售。
同时需要定期进行检测和维护,确保储气罐的安全运行。
三、工厂实际操作1.原料处理:实习期间,我参与了原料的处理工作。
首先进行原料的过滤和脱水处理,以确保原料的纯净度。
然后利用分子筛吸附装置对原料进行进一步净化,去除杂质。
2.反应器操作:我在反应器部门进行了实际操作,监控反应器的运行状态,检测反应温度和压力,并及时调整控制参数以提高反应效率。
3.分离与净化:我参与了分离与净化工艺的操作。
通过分离装置,将合成氨中的杂质和未反应的原料气体进行分离,并通过吸附装置去除其中的水分和氧气。
4.储气罐运行检测:我还了解了储气罐的运行检测,包括定期检查储气罐的安全阀和压力表,以及检测储气罐的内部温度和压力。
5.安全生产管理:在工厂实习期间,我还学习了工厂的安全生产管理制度。
参与了每日的安全例会和安全培训,了解了化工生产过程中的危险源和防范措施。
四、实习心得通过这次实习,我对合成氨的生产工艺和实际操作有了更深入的了解。
合成氨工艺流程详解
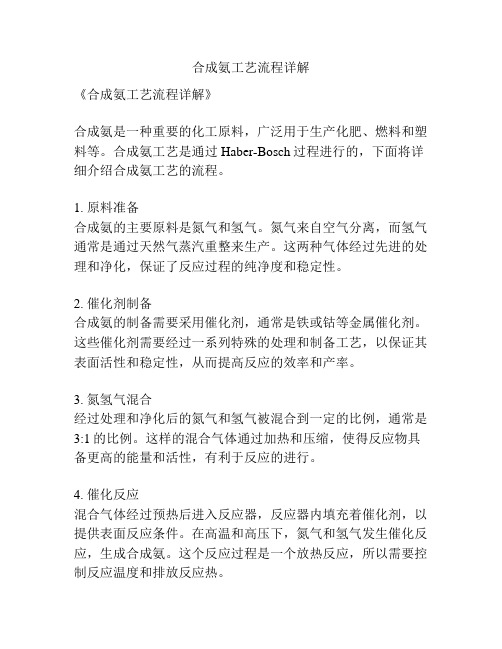
合成氨工艺流程详解
《合成氨工艺流程详解》
合成氨是一种重要的化工原料,广泛用于生产化肥、燃料和塑料等。
合成氨工艺是通过Haber-Bosch过程进行的,下面将详细介绍合成氨工艺的流程。
1. 原料准备
合成氨的主要原料是氮气和氢气。
氮气来自空气分离,而氢气通常是通过天然气蒸汽重整来生产。
这两种气体经过先进的处理和净化,保证了反应过程的纯净度和稳定性。
2. 催化剂制备
合成氨的制备需要采用催化剂,通常是铁或钴等金属催化剂。
这些催化剂需要经过一系列特殊的处理和制备工艺,以保证其表面活性和稳定性,从而提高反应的效率和产率。
3. 氮氢气混合
经过处理和净化后的氮气和氢气被混合到一定的比例,通常是3:1的比例。
这样的混合气体通过加热和压缩,使得反应物具备更高的能量和活性,有利于反应的进行。
4. 催化反应
混合气体经过预热后进入反应器,反应器内填充着催化剂,以提供表面反应条件。
在高温和高压下,氮气和氢气发生催化反应,生成合成氨。
这个反应过程是一个放热反应,所以需要控制反应温度和排放反应热。
5. 分离和提纯
产生的混合气体经过冷却后进入分离装置,将产生的合成氨和未反应的氮氢气体进行分离。
分离得到的合成氨会进一步进行脱水和提纯处理,使其符合工业用途的级别。
通过以上的工艺流程,合成氨可以有效地得到,而且具有较高的产率和纯度。
这个工艺流程成为了化工工业中的一种重要生产方式,为生产化肥和其他化工产品提供了重要的原料支持。
化工工艺学期末复习题答案

合成氨1. 合成氨生产过程主要分为哪几个工序?以煤为原料以天然气为原料2. 天然气水蒸汽转化制气的主反应和副反应有哪些?抑制副反应的策略如何?主要反应 主要副反应 抑制副反应:为控制积碳,增加水蒸汽用量以调整气体组成和选择适当的温度、压力来解决. 从反应平衡及副反应来看,水碳比高,残余甲烷含量降低,且可防止析碳。
因此一般采用较高的水碳比,约3。
0~3。
5转化为可逆反应,温度越高,平衡转化率越高,从组成计算看出,1000℃以上CH4含量才小于0。
5%,要求设备的耐高温性能。
3.为什么采用两段转化?两段转化的供热方式各有什么不同?如何确定和控制二段转化的温度?全部采用高温转化,设备费用和操作费用太高,所以采用低温(700~800℃)转化和高温(1200℃)转化的两段方式。
一段温度对合金钢管要求低,用合金钢管保证传热和供热;二段采用砖内衬的绝热设备,并通入一定比例的空气与一段的H2反应产生热量和高温(1200~1400℃),保证CH4转化彻底,同时加入了合成氨需要的原料N2。
二段炉温度:按甲烷控制指标来确定。
压力和水碳比确定后,按甲烷平衡浓度来确定温度,要求yCH4<0。
005,出口温度应为1000℃左右.凯洛格(Kellogg)甲烷蒸汽转化工艺流程mol kJ H CO O H CH 4.2063)1(224-++=mol kJ H CO O H CO /2.41)2(222+++=124.9.742--+mol kJ C H CH =12.4.1722-++=mol kJ C CO CO 122.36.131-+++mol kJ C O H H CO =1—钴钼加氢反应器;2—氧化锌脱硫罐;3—对流段;4—辐射段(一段炉);5-二段转化炉;6-第一废热锅炉;7—第二废热锅炉;8-汽包;9—辅助锅炉;10—排风机4.天然气中的硫成分有哪些?干法脱硫和湿法脱硫的主要方法有哪些?其适用范围有何区别?硫化氢(H2S),同时此外还可能有一些有机硫化物,如硫醇(C2H5SH )、硫醚(CH3SCH3)及噻吩(C4H4S )、二硫化碳(CS2)等.• 干法脱硫:一般适用于含S 量较少的情况 氧化锌法、钴钼加氢法、氢氧化铁法、活性碳法等• 湿法脱硫:一般适用于含S 量较大的场合 化学吸收法、物理吸收法和化学物理综合吸收法等5。
- 1、下载文档前请自行甄别文档内容的完整性,平台不提供额外的编辑、内容补充、找答案等附加服务。
- 2、"仅部分预览"的文档,不可在线预览部分如存在完整性等问题,可反馈申请退款(可完整预览的文档不适用该条件!)。
- 3、如文档侵犯您的权益,请联系客服反馈,我们会尽快为您处理(人工客服工作时间:9:00-18:30)。
中温变换:温度350-550℃,催化剂以Fe2O3为主体,以Cr203为主要添加物的多成分铁铬系催化剂,出口CO含量3%左右?低温变换:温度200-280℃,催化剂以氧化铜为主体,还原后的活性组分是细小的铜结晶。?出口CO含量0.3%左右。
5.(1)吹风阶段 空气从炉底吹入,自下而上以提高煤层温度,然后将吹风气经回收热量后
CO+H2O→H2+CO2 ,ΔH=-41.2kJ/mol 由于CO变换过程是强放热过程,必须分段进行以利于回收反应热,并控制变换段出口残余CO含量。第一步是高温变换,使大部分CO转变为CO2和H2;第二步是低温变换,将CO含量降至0.3%左右。因此,CO变换反应既是原料气制造的继续,又是净化的过程,为后续脱碳过程创造条件。
20:40
2作为生产合成氨用的半水煤气,要求气体中(H 2 +CO)与 N 2 的比例为 3.1~3.2。,可采用下列方法: 外热法 如利用原子能反应堆余热或其它廉价高温热源,用熔融盐、熔融铁的介质为热载体直接加 热反应系统,或预热气化剂,以提供气化过程所需的热能。但这种方法尚处于研究阶段。 富氧空气气化法 为了调整生成的煤气中氮的含量,用富氧空气代替空气是行之有效的方法;也可用纯氧代 替空气,此法可连续制气。但作为合成氨原料气,尚应在下游工序中补加纯氮,使氢氮比 符合要求。 蓄热法(也称间歇制气法) 用空气和蒸汽分别送入燃料层。先送入空气以提高燃料层温度,生成气体(吹风气)大部 分放空;然后,送入蒸汽进行气化反应,此时引起燃料层温度下降。所得水煤气配入部分 吹风气即成半水煤气。
(3)脱碳过程 粗原料气经CO变换以后,变换气中除H2外,还有CO2、CO和CH4等组分,其中以CO2含量最多。CO2既是氨合成催化剂的毒物,又是制造尿素、碳酸氢铵等氮肥的重要原料。因此变换气中CO2的脱除必须兼顾这两方面的要求。 一般采用溶液吸收法脱除CO2。根据吸收剂性能的不同,可分为两大类。一类是物理吸收法,如低温甲醇洗法(Rectisol),聚乙二醇二甲醚法(Selexol),碳酸丙烯酯法。一类是化学吸收法,如热钾碱法,低热耗苯菲尔法,活化MDEA法,MEA法等。
(5) 空气吹净 目的是回收存在炉子上部及管道中残余的煤气,此部分吹风气应加以回收,作为半水煤气中N2 的来源。
1. 合成氨生产主要分几个工序?各部分任务如何?
答:1)原料气制备 即制备含有氢、氮的原料气。用煤、原油、或天然气作原料, 制备含氮、氢气的原料气。(将煤和天然气等原料制成含氢和氮的粗原料气。一般焦炭、无烟煤等固体燃料通常采用气化的方法制取合成气;对气态烃类和石脑油,工业中利用二段蒸汽转化法制取合成气。 渣油可采用非催化部分氧化的方法获得合成气。)
4.?反应原理:CO+H2O=CO2+H2该反应既能把大部分CO变为易于清除的二氧化碳,而且又制得了等量的氢。?
主要任务:在合成氨生产中,各种方法制取的原料气都含有CO,其体积分数一般为12%~40%。合成氨需要的两种组分是H2和N2,因此需要除去合成气中的CO。变换反应如下:?CO+H2O→H2+CO2?,ΔH=-41.2kJ/mol?,CO变换反应既是原料气制造的继续,又是净化的过程,为后续脱碳过程创造条件。?
3.?脱硫的主要方法有哪些?天然气为原料的厂和煤焦为原料的厂,脱硫工序安排的流程顺序为什么不同?
主要方法有1)干法脱硫,(1)氧化锌法脱硫;(2)钴钼加氢脱硫法;2)湿法脱硫(化学吸收法,物理吸收法,化学-物理综合吸收法),(1)改良ADA法?。以煤为原料的煤气硫含量比较高,脱除煤气中的硫主要防止变换、合成触媒中毒同时也防止铜液生成硫化铜沉淀,增加铜耗。所以,以煤为原料的企业将脱硫工序布置在造气后、变换以前,而且大部分采用湿法脱硫。 而以天然气为原料的合成氨装置,脱硫主要防止转化、造气、触媒中毒,也有防止变换、合成触媒中毒,同时也防止铜液生成硫化铜沉淀,增加铜耗的作用。所以,脱硫工序一般布置在转化造气之前,且一般天然气中硫含量比较低,特殊情况除外。
2)净化 因为无论用何种方法造气,原料气中都含有对合成氨反应过程有害的各种杂质,必须采取适当的方法除去这些杂质,主要包括变换过程、脱硫脱碳过程以及气体精制过程。 (1)脱硫过程 无论以焦炭还是天然气为原料获得的原料气中,都含有一氧化碳、二氧化碳、硫化物等不利于合成反应的成分,需要在进入合成塔之前除去。其中硫化物对蒸气转化都是有害的,故在原料气进入界区后,首先进行脱硫。氧化锌脱硫就是H2S气体在固体ZnO上进行反应,生成H2O进入气相,ZnS则沉积在ZnO固体表面上。脱无机硫温度约200℃。 (2)一氧化碳变换过程 在合成氨生产中,各种方法制取的原料气都含有CO,其体积分数一般为12%~40%。合成氨需要的两种组分是H2和N2,因此需要除去合成气中的CO。变换反应如下:
3)压缩和合成 将纯净的氢、氮混合气压缩到高压,在催化剂的作用下合成氨。氨的合成是提供液氨产品的工序,是整个合成氨生产过程的核心部分。氨合成反应在较高压力和催化剂存在的条件下进行,由于反应后气体中氨含量不高,一般只有10%~20%,故采用未反应氢氮气循环的流程。氨合成反应式如下: N2+3H2→2NH3(g) ,ΔH=-92.4kJ/mol
放空。
(2)蒸汽一次上吹 水蒸气自下而上送入煤层进行气化反应,此时煤层下部温度下降,而上部温度升高,被煤气带走的显热增加。
(3) 蒸汽下吹 水蒸气自引出系统。
(4) 蒸汽二次上吹 蒸汽下吹制气后煤层温度已显著下降,且炉内尚有煤气,如立即吹入空气势必引起爆炸。为此,先以蒸汽进行二次上吹,将炉子底部煤气排净,为下一步吹风创造条件。
原因:a、由于CO变换过程是强放热过程,必须分段进行以利于回收反应热,并控制变换段出口残余CO含量。第一步是高温变换,使大部分CO转变为CO2和H2;第二步是低温变换,将CO含量降至0.3%左右。B、因平衡变换率随温度升高而降低,但反应速度却随着温度升高而增加,为了既保持较高的反应速度,又尽量提高平衡变换率,工业上常采用先较高温度(400-450℃)变换后较低温度(200-250)变换后的两段变换工艺,前者为中温变换,后者为低温变换。