AT79C1020中文资料
EPSON RC+ 7.0 选件 Force Guide 7.0 SPEL+ Language Re
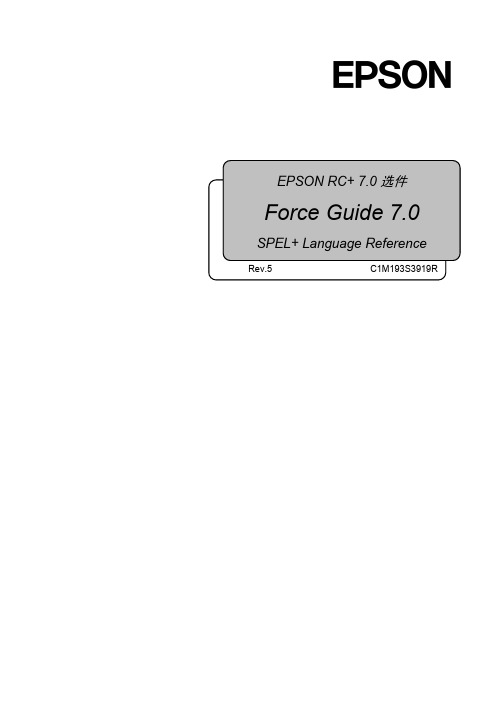
EPSON RC+ 7.0选件Force Guide 7.0 SPEL+ Language Reference Rev.5EPSON RC+ 7.0选件Force Guide 7.0SPEL+ Language ReferenceRev.5Copyright © 2015-2018 SEIKO EPSON CORPORATION. All rights reserved.Force Guide 7.0 SPEL+ Language Reference Rev.5 i前言感谢您购买本公司的机器人系统。
本手册记载了正确使用Force Guide 7.0所需的事项。
使用该软件时请仔细阅读本手册与其他相关手册。
阅读之后请妥善保管,以便随时取阅。
保修本机器人及其选装部件是经过本公司严格的质量控制、测试和检查,并在确认性能满足本公司标准之后出厂交付的。
在交付产品的保修期内,本公司仅对正常使用时发生的故障进行免费修理。
(有关保修期事项,请咨询您的区域销售办事处。
)但在以下情况下,将对客户收取修理费用(即使在保修期内):1.因不同于手册内容的错误使用以及使用不当而导致的损坏或故障。
2.客户未经授权进行拆卸导致的故障。
3.因调整不当或未经授权进行修理而导致的损坏。
4.因地震、洪水等自然灾害导致的损坏。
警告、小心、使用:1.如果机器人或相关设备的使用超出本手册所述的使用条件及产品规格,将导致保修无效。
2.本公司对因未遵守本手册记载的“警告”与“注意”而导致的任何故障或事故,甚至是人身伤害或死亡,均不承担任何责任,敬请谅解。
3.本公司不可能预见所有可能的危险与后果。
因此,本手册不能警告用户所有可能的危险。
ii Force Guide 7.0 SPEL+ Language Reference Rev.5商标Microsoft、Windows、Windows标识、Visual Basic及Visual C++为美国MicrosoftCorporation在美国和/或其它国家的注册商标或商标。
AT27C020中文资料
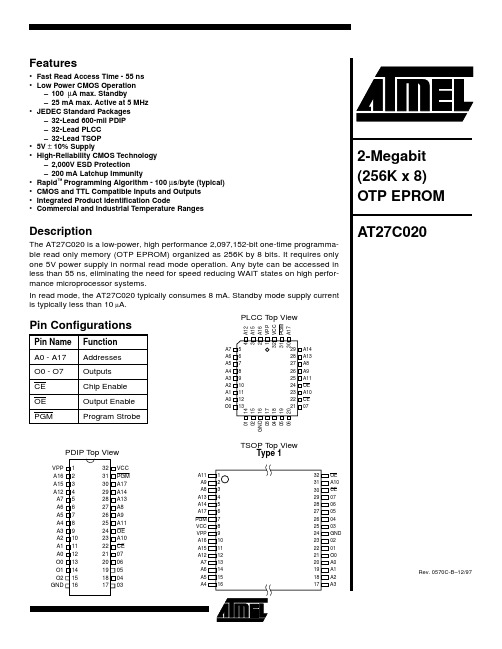
The AT27C020 is available in a choice of industry standard JEDEC-approved one-time programmable (OTP) plastic PDIP, PLCC, and TSOP packages. All devices feature two-line control (CE, OE) to give designers the flexibility to pre-vent bus contention.With 256K byte storage capability, the AT27C020 allows firmware to be stored reliably and to be accessed by the system without the delays of mass storage media. Atmel’s 27C020 have additional features to ensure high quality and efficient production use. The Rapid™Program-ming Algorithm reduces the time required to program the part and guarantees reliable programming. Programming time is typically only 100 µs/byte. The Integrated Product Identification Code electronically identifies the device and manufacturer. This feature is used by industry standard programming equipment to select the proper programming algorithms and voltages.System ConsiderationsSwitching between active and standby conditions via the Chip Enable pin may produce transient voltage excursions. Unless accommodated by the system design, these tran-sients may exceed data sheet limits, resulting in device non-conformance. At a minimum, a 0.1 µF high frequency, low inherent inductance, ceramic capacitor should be uti-lized for each device. This capacitor should be connected between the V CC and Ground terminals of the device, as close to the device as possible. Additionally, to stabilize the supply voltage level on printed circuit boards with large EPROM arrays, a 4.7 µF bulk electrolytic capacitor should be utilized, again connected between the V CC and Ground terminals. This capacitor should be positioned as close as possible to the point where the power supply is connected to the array.Block DiagramAbsolute Maximum Ratings*T emperature Under Bias.......................-55°C to +125°C *NOTICE:Stresses beyond those listed under “Absolute Maximum Ratings” may cause permanent damage to the device. This is a stress rating only and functional operation of the device at these or any other conditions beyond those indicated in the operational sections of this specification is not implied. Exposure to abso-lute maximum rating conditions for extended periods may affect device reliability.Note:1.Minimum voltage is -0.6V DC which mayundershoot to -2.0V for pulses of less than 20 ns. Maximum output pin voltage is V CC + 0.75V DC which may overshoot to +7.0V for pulses of less than 20 ns.Storage T emperature............................-65°C to +150°C Voltage on Any Pin withRespect to Ground...............................-2.0V to +7.0V (1)Voltage on A9 withRespect to Ground ............................-2.0V to +14.0V (1)V PP Supply Voltage withRespect to Ground.............................-2.0V to +14.0V (1)Operating ModesNotes:1.X can be V IL or V IH.2.Refer to Programming Characteristics.3.V H = 12.0 ± 0.5V .4.T wo identifier bytes may be selected. All Ai inputs are held low (V IL ), except A9 which is set to V H and A0 which is toggledlow (V IL ) to select the Manufacturer’s Identification byte and high (V IH ) to select the Device Code byte.Mode/Pin CE OE PGM Ai V PP Outputs ReadV IL V IL X (1)Ai X D OUT Output Disable X V IH X X X HighZ Standby V IH X X X X High Z Rapid Program (2)V IL V IH V IL Ai V PP D IN PGM Verify V IL V IL V IH Ai V PP D OUT PGM InhibitV IH X X X V PP High Z Product Identification (4)V ILV ILXA9 = V H (3)A0 = V IH or V IL A1 - A17 = V ILXIdentification CodeAC Characteristics for Read OperationNote:1.2, 3, 4, 5. See AC Waveforms for Read Operation diagram.Symbol ParameterAT27C020Units -55-70-90-12-15Condition Min Max MinMax MinMax MinMax MinMax t ACC (3)Address to Output Delay CE =OE = V IL 557090120150ns t CE (2)CE to Output Delay OE = V IL 557090120150ns t OE (2)(3)OE to Output Delay CE = V IL2030353540ns t DF(4)(5)OE or CE High to Output Float,whichever occurred first 1820203040nst OH Output Holdfrom Address,CE or OE,whichever occurred first77000nsDC and AC Operating Conditions for Read OperationAT27C020-55-70-90-12-15Operating T emperature (Case)Com.0°C - 70°C 0°C - 70°C 0°C - 70°C 0°C - 70°C 0°C - 70°C Ind.-40°C - 85C -40°C - 85C -40°C - 85C -40°C - 85C -40°C - 85C V CC Power Supply5V ± 10%5V ± 10%5V ± 10%5V ± 10%5V ± 10%DC and Operating Characteristics for Read OperationNotes:1.V CC must be applied simultaneously or before V PP , and removed simultaneously or after V PP .2.V PP may be connected directly to V CC except during programming. The supply current would then be the sum of I CC and I PP .Symbol Parameter ConditionMinMax Units I LI Input Load Current V IN = 0V to V CC (Com., Ind.)±1.0µA I LO Output Leakage Current V OUT = 0V to V CC (Com., Ind.)±5.0µA I PP (2)V PP (1) Read/Standby Current V PP = V CC±10µA I SB V CC (1) Standby Current I SB1 (CMOS), CE = V CC ± 0.3V 100µA I SB2 (TTL), CE = 2.0 to V CC + 0.5V 1.0mA I CC V CC Active Current f = 5 MHz, I OUT = 0 mA, CE = V IL25mA V IL Input Low Voltage -0.60.8V V IH Input High Voltage 2.0V CC + 0.5V V OL Output Low Voltage I OL = 2.1 mA 0.4V V OH Output High VoltageI OH = -400 µA2.4VAC Waveforms for Read Operation (1)Notes: 1.Timing measurement references are 0.8V and 2.0V . Input AC drive levels are 0.45V and 2.4V , unless otherwise specified.2.OE may be delayed up to t CE - t OE after the falling edge of CE without impact on t CE.3.ACC - t OE after the address is valid without impact on t ACC .4.This parameter is only sampled and is not 100% tested.5.Output float is defined as the point when data is no longer driven.Input Test Waveforms and Measurement LevelsFor -55 devices only:t R , t FFor -70,-90,-12,-15 devices only:t R , t F < 20 ns (10% to 90%)Pin Capacitancef = 1 MHz, T = 25°C (1)Note:1.T ypical values for nominal supply voltage. This parameter is only sampled and is not 100% tested.TypMax Units Conditions C IN 48pF V IN = 0V C OUT812pFV OUT = 0VOutput Test Load (1)Note: 1.CL = 100 pF including jig capacitance except -55 devices where CL = 30 pF.Programming Waveforms (1)Notes: 1.The Input Timing reference is 0.8V for V IL and 2.0V for V IH.2.t OE and t DFP are characteristics of the device but must be accommodated by the programmer.3.When programming the A T27C020, a 0.1 µF capacitor is required across V PP and ground to suppress voltage transients.DC Programming CharacteristicsT A = 25 ± 5°C, V CC = 6.5 ± 0.25V, V PP = 13.0 ± 0.25VSymbol Parameter Test ConditionsLimitsUnits Min MaxI LI Input Load Current V IN = V IL, V IH±10µA V IL Input Low Level-0.60.8V V IH Input High Level 2.0VCC+ 1.0V V OL Output Low Voltage I OL = 2.1 mA0.4V V OH Output High Voltage I OH = -400 µA 2.4V I CC2V CC Supply Current (Program and Verify)40mA I PP2V PP Supply Current CE = PGM = V IL20mA V ID A9 Product Identification Voltage11.512.5VAC Programming CharacteristicsT A = 25 ± 5°C, V CC = 6.5 ± 0.25V,V PP = 13.0 ± 0.25VNotes:1.V CC must be applied simultaneously or before V PP and removed simultaneously or after V PP .2.This parameter is only sampled and is not 100% tested. Output Float is defined as the point where data is no longer driven— see timing diagram.3.Program Pulse width tolerance is 100 µs ± 5%.Symbol ParameterTest Condition (1)LimitsUnits Min Max t AS Address Setup Time Input Rise and Fall Times:(10% to 90%) 20 ns.Input Pulse Levels:0.45V to 2.4V Input Timing Reference Level:0.8V to 2.0V Output Timing Reference Level:0.8V to 2.0V2µs t CES CE Setup Time 2µs t OES OE Setup Time 2µs t DS Data Setup Time 2µs t AH Address Hold Time 0µs t DH Data Hold Time2µst DFP OE High to Output Float Delay (2)0130ns t VPS V PP Setup Time 2µs t VCS V CC Set up Time2µs t PW PGM Program Pulse Width (3)95105µs t OE Data Valid from OE150ns t PRTV PP Pulse Rise Time During Programming50nsAtmel’s 27C020 Integrated Product Identification CodePinsCodes A0O7O6O5O4O3O2O1O0Hex DataManufacturer 0000111101E Device T ype111186Rapid Programming AlgorithmA 100 µs PGM pulse width is used to program. The address is set to the first location. V CC is raised to 6.5V and V PP is raised to 13.0V. Each address is first programmed with one 100 µs PGM pulse without verification. Then a verification / reprogramming loop is executed for each address. In the event a byte fails to pass verification, up to 10 successive 100 µs pulses are applied with a verification after each pulse. If the byte fails to verify after 10 pulses have been applied, the part is considered failed. After the byte verifies properly, the next address is selected until all have been checked. V PP is then lowered to 5.0V and V CC to 5.0V. All bytes are read again and compared with the origi-nal data to determine if the device passes or fails.Ordering Informationt ACC (ns)I CC (mA)Ordering Code Package Operation Range Active Standby55250.1A T27C020-55JCA T27C020-55PCA T27C020-55TC 32J32P632TCommercial(0°C to 70°C)250.1A T27C020-55JIA T27C020-55PIA T27C020-55TI 32J32P632TIndustrial(-40°C to 85°C)70250.1A T27C020-70JCA T27C020-70PCA T27C020-70TC 32J32P632TCommercial(0°C to 70°C)250.1A T27C020-70JIA T27C020-70PIAT27C020-70TI 32J32P632TIndustrial(-40°C to 85°C)90250.1A T27C020-90JCA T27C020-90PCA T27C020-90TC 32J32P632TCommercial(0°C to 70°C)250.1A T27C020-90JIA T27C020-90PIAT27C020-90TI 32J32P632TIndustrial(-40°C to 85°C)120250.1A T27C020-12JCA T27C020-12PCA T27C020-12TC 32J32P632TCommercial(0°C to 70°C)250.1A T27C020-12JIA T27C020-12PIA T27C020-12TI 32J32P632TIndustrial(-40°C to 85°C)150250.1A T27C020-15JCA T27C020-15PCA T27C020-15TC 32J32P632TCommercial(0°C to 70°C)250.1A T27C020-15JIA T27C020-15PIA T27C020-15TI 32J32P632TIndustrial(-40°C to 85°C)Package Type32J32-Lead,Plastic J-Leaded Chip Carrier (PLCC)32P632-Lead, 0.600" Wide, Plastic Dual Inline Package (PDIP) 32T32-Lead, Plastic Thin Small Outline Package (TSOP)。
Eaton GHC1020 产品说明说明书

Eaton GHC1020Eaton Series C complete molded case circuit breaker, G-frame, GHC, Complete breaker, Fixed thermal, fixed magnetic trip type, Single-pole, 20A, 277 Vac, 125 Vdc, 14 kAIC at 277 Vac, 50/60 HzGeneral specificationsEaton Series C complete molded case circuit breakerGHC10207866791739612.63 in 4.88 in 1 in 0.75 lb Eaton Selling Policy 25-000, one (1) year from the date of installation of the Product or eighteen (18) months from the date of shipment of the Product, whichever occurs first.UL Listed Product NameCatalog Number UPCProduct Length/Depth Product Height Product Width Product Weight WarrantyCertificationsSeries C14 kAIC at 277 VacGGHC50/60 HzComplete breaker277 Vac, 125 Vdc20 AFixed thermal, fixed magnetic Single-pole Application of Multi-Wire Terminals for Molded Case Circuit Breakers Application of Tap Rules to Molded Case Breaker TerminalsUL listed 100%-rated molded case circuit breakersCircuit breaker motor operators product aidMotor protection circuit breakers product aidMulti-wire lugs product aidMOEM MCCB Product Selection GuideStrandAble terminals product aidCurrent limiting Series C molded case circuit breakers product aid Plug-in adapters for molded case circuit breakers product aid Power metering and monitoring with Modbus RTU product aid Breaker service centersMolded case circuit breakers catalogEaton's Volume 4—Circuit ProtectionG-frame Molded Case Circuit Breaker DrawingSeries C GC/GHC Circuit Breaker - ILSeries C GB/GHB/GDB Circuit Breakers - ILCircuit Breakers ExplainedCircuit breakers explainedSeries C J-Frame molded case circuit breakers time current curves MOEM MCCB product selection guideSeries C G-Frame molded case circuit breakers time current curves Eaton Specification Sheet - GHC1020Series C G-Frame Time Current CurvesSeries C F-Frame molded case circuit breakersType GHB/GHC/GD/GPS 2 and 3-pole, 15-100A Time CurveSeriesInterrupt ratingFrameCircuit breaker type Frequency ratingCircuit breaker frame type Voltage rating Amperage RatingTrip TypeNumber of poles Application notesBrochuresCatalogsDrawingsInstallation instructions MultimediaSpecifications and datasheets Time/current curvesEaton Corporation plc Eaton House30 Pembroke Road Dublin 4, Ireland © 2023 Eaton. All Rights Reserved. Eaton is a registered trademark.All other trademarks areproperty of their respectiveowners./socialmedia。
HI 93701-0和HI 957淀粉测定器手册说明书

1•Turn the meter on by pressing ON/OFF .2•When the beeper sounds briefly, the LCDdisplays dashes and “P1” (Chlorine Low Range) or “P2” (Chlorine Ultra High Range)the meter is ready. The code that appears on the secondary display is the one of the RANGE/GLP/ indicates that the instrument needs to be zeroed first.3•Fill the cuvette with 10 mL of unreactedsample, up to the mark, and replace the cap.4•Place the cuvette into the cuvette holderand ensure that the notch on the cap is positioned securely into the groove.5•Press ZERO/CFM and the lamp, cuvetteand detector icons will appear on the display, depending on the measurement phase.6•After a few seconds the display will show“-0.0-”. The meter is now zeroed and ready for measurement.7•Remove the cuvette.8•Add the content of the packets for thespecific test reagents:Chlorine LR: 1 packet of HI 93701-0Chlorine UHR:1 packet of HI 95771A-0and 1 packet of HI 95771B-0.9•Replace the cap and shake gently for20 seconds.10•Replace the cuvette into the cuvette holderand ensure that the notch on the cap is positioned securely into the groove.11•Press and hold READ/ for threeseconds .countdown prior to measurement. The beeper is playing a beep at the end of countdown period.press READ//TIMER .In both cases the lamp, cuvette and detector icons will appear on the display,depending on the measurement phase.1.key: press to change the parameter. Press and hold GLP mode . In calibration mode press to edit the date and time.2.CAL CHECK key: press to perform the validation of the meter, or press and hold for three seconds to enter calibration mode .3.ZERO/CFM key: press to zero the meter prior to measurement, to confirm edited values or to confirm factory calibration restore.4.READ/ key: In measurement mode , press to make a pre-programmed countdown prior to measurement. In GLP mode press to view the next screen.5.ON/OFF key: to turn the meter on and off.6.Liquid Crystal Display (LCD)7.Cuvette alignment indicator8.Cuvette holderDISPLAY ELEMENTS DESCRIPTIONINSTRUCTION MANUALHI 96771Free Chlorine &Chlorine Ultra High RangeISMPreliminary examinationPlease examine this product carefully. Make sure that the instrument is not damaged. If any damage occured during shipment, please notify your Dealer.Each HI 96771 Ion Selective Meter is supplied complete with:•Two Sample Cuvettes and Caps •9V Battery•Instruction ManualNote:save all packing material until you are sure that the instrumentworks correctly. Any defective item must be returned in its original packing.For more details about spare parts and accessories see “Accessories”.Dear Customer,Thank you for choosing a Hanna product. This manual will provide you with the necessary information for the correct use of the instrument. Please read it carefully before using the meter. If you need additional technical information,*******************************************.Functional description Light High: There is too much light to perform a measurement. Please check the preparation of the zero cuvette.Light Low: There is not enough light to perform a measurement. Please check the preparation of the zero cuvette.No Light: The instrument cannot adjust the light level. Please check that the sample does not contain any debris.Inverted cuvettes: The sample and the zero cuvette are inverted.Zero: A zero reading was not taken. Follow the instructions of the measurement procedure for zeroing the meter.Under range: A blinking “0.00” indicates that the sample absorbs less light than the zero reference.Check the procedure and make sure you use the same cuvette for reference (zero) and measurement.1.The measuring scheme (lamp, cuvette, detector), appears during different phases of zero or reading measurement2.Error messages and warnings3.The battery icon indicates the charge state of the battery4.The hourglass appears when an internal check is in progress5.Status messages6.The chronometer appears when the reaction timer is running7.The month, day and date icons appear when a date is displayed8.Four digit main display9.Measuring units10.Four digit secondary displayON SAMPLE READINGBattery low: The battery must be replaced soon.Dead battery: This indicates that the battery is dead and must be replaced. Once this indication is displayed, normal operation of the instrument will be interrupted. Change the battery and restart the meter.Cooling lamp: The instrument waits for the lamp to cool down.DURING CALIBRATION PROCEDUREOTHER ERRORS AND WARNINGSCap error: Appears when external lightenters in the analysis cell. Assure that the cuvette cap is present.Over Range: A flashing value of the maximum concentration indicates an over range condition.The concentration of the sample is beyond the programmed range: dilute the sample and re-run the test.Standard Low: The standard reading is less than expected.Standard High: The standard reading is higher than expected.Errors and warningsON ZERO READINGMeasurement procedureTechnical specifications:Range 0.00 to 5.00 mg/L for Chlorine LR 0 to 500 mg/L for Chlorine UHRResolution0.01 mg/L from 0.00-3.50 mg/L; 0.10 mg/L above 3.50 mg/L for Chlorine LR1 mg/L from 0 to 200 mg/L; 10 mg/L above 200 mg/L for Chlorine UHRAccuracy ±0.03 mg/L ±3% of reading at 25°C for Chlorine LR ±3 mg/L ±3% of reading at 25°C for Chlorine UHRTypical EMC Dev.±0.01 mg/L for Chlorine LR±1 mg/L for Chlorine UHR Light Source Tungsten lampLight Detector Silicon Photocell with narrow band interference filter @ 525 nmMethod Adaptation of Standard Methods for the Examination of Water and Wastewater, 20th edition, 4500-Cl.Environment 0 to 50°C (32 to 122°F);max 95% RH non-condensing Battery Type 1 x 9 voltAuto-Shut offAfter 10' of non-use in measurement mode; after 1 hour of non-use in calibration mode; with last reading reminder.Dimensions 192 x 104 x 69 mm (7.6 x 4.1 x 2.7”)Weight360 g (12.7 oz.).FACTORY CALIBRATION RESTORE It is possible to delete the calibration and restore factory calibration.1•Press and hold for three secondsRANGE/GLP/GLP mode .2•Press READ/ to enter in thefactory calibration restore screen. The instrument asks for confirmation of user calibration delete.3•Press ZERO/CFM to restore the factorycalibration or press RANGE/GLP/ again 4•The instrument briefly indicates “donE”upon restoration of factory calibration prior to returning to measurement mode .or dirt and that they are inserted correctly.12•Then the date of last calibration (e.g.:“01.08.2009”) appears on the display, or “01.01.2009” if the factory calibration was selected before. In both cases the year number is blinking, ready for date input.13•Press RANGE/GLP/ to edit the desiredyear (2009-2099). If the key is kept pressed,the year number is automatically increased.14•ZERO/CFM or READ//TIMER to confirm.Now the display will show the month blinking.15•Press RANGE/GLP/ to edit the desiredmonth (01-12). If the key is kept pressed,the month number is automatically increased.16•When the correct month has been set, pressZERO/CFM or READ//TIMER to confirm.Now the display will show the day blinking.17•Press RANGE/GLP/the day number is automatically increased.Note:It is possible to change the editing fromday to year and to month by pressing READ/18•Press ZERO/CFM to save the calibrationdate.19•The instrument displays “Stor ” for onesecond and the calibration is saved.20•The instrument will return automaticallyto the measurement mode by displaying dashes on the LCD.9•At the end of the measurement the displaywill show the validation standard value.The reading should be within specifications as reported on the CAL CHECK™Standard Certificate. If the value is found out of specifications, please check that the cuvettes are free of fingerprints, oil or dirt and repeat validation. If results are still found out of specifications then recalibrate the instrument.CALIBRATIONNote:It is possible to interrupt the calibrationprocedure at any time by pressing CAL CHECK or ON/OFF keys.When calibrating, only the selected range is affected.1•Turn the meter on by pressing ON/OFF .2•When the beeper sounds briefly and theLCD displays dashes, the meter is ready.3•To change the range, simply pressRANGE/GLP/4•Press and hold CAL CHECK for threeseconds to enter calibration mode. The display will show “CAL ” during calibration procedure. The blinking “ZERO ” asks for instrument zeroing.5•Place the CAL CHECK™ StandardHI96771-11 Cuvette A into the cuvette holder and ensure that the notch on the cap is positioned securely into the groove.6•Press ZERO/CFM and the lamp, cuvetteand detector icons will appear on the display,depending on the measurement phase.7•After a few seconds the display will show“-0.0-”. The meter is now zeroed and ready for calibration. The blinking “READ ”asks for reading calibration standard.8•Remove the cuvette.9•Place the specific CAL CHECK TM StandardHI96771-11 Cuvette B into the cuvette holder, for and ensure that the notch on the cap is positioned securely into the groove.10•Press READ/ and the lamp,the display, depending on the measurement phase.11•The instrument will show for three secondsthe CAL CHECK™ standard value.Note:If the display shows “STD HIGH ”, thestandard value was too high. If the display shows “STD LOW ”, the standard value was too low. Verify that both CAL CHECK™ Standard HI96771-11Cuvettes, A and B are free from fingerprintsLAST CALIBRATION DATE1•Press RANGE/GLP/GLP mode .on the main display and the year on the secondary display.2•If no calibration was performed, the factorycalibration message, “F.CAL” will appear on the main display and the instrument returns to measurement mode after three seconds.In the GLP mode , the last calibration date can be verified and the factory calibration can be restored.To save battery, the instrument shuts down after 10 minutes of non-use in measurement mode and after 1 hour of non-use in calibration mode.If a valid measurement was displayed before auto shut off, the value is displayed when the instrument is switched on. The blinking “ZERO ”means that a new zero has to be performed.One fresh battery lasts for around 750 measurements, depending on the light level.The remaining battery capacity is evaluated at the instrument startup and after each measurement.The instrument displays a battery indicator with three levels as follows:• 3 lines for 100 % capacity • 2 lines for 66 % capacity • 1 line for 33 % capacity•Battery icon blinking if the capacity is under 10 %.If the battery is empty and accurate measurements can’t be taken any more, the instrument shows “dEAd bAtt ” and turns off.To restart the instrument, the battery must be replaced with a fresh one.To replace the instrument’s battery, follow the steps:•Turn the instrument off by pressing ON/OFF .•Turn the instrument upside down and remove the battery cover by turning it counterclockwise.•Extract the battery from its location and replace it with a fresh one.•Insert back the battery cover and turn it clockwise to close.R EAGENT SETSHI 93701-01Reagents for 100 Free Chlorine tests HI 93701-03Reagents for 300 Free Chlorine testsHI 95771-01Reagents for 100 Chlorine Ultra High Range tests HI 95771-03Reagents for 300 Chlorine Ultra High Range tests OTHER ACCESSORIESHI 96771-11CAL CHECK ™ Standard Cuvettes (1 set)HI 7213109V battery (10 pcs)HI 731318Cloth for wiping cuvettes (4 pcs)HI 731331Glass cuvettes (4 pcs)HI 731335Caps for cuvettes (4 pcs)HI 93703-50Cuvette cleaning solution (230 mL).Battery managementWarrantyHI 96771 is warranted for two years against defects in workmanship and materials when used for its intended purpose and maintained according to the instructions.This warranty is limited to repair or replacement free of charge.Damages due to accident, misuse, tampering or lack of prescribed maintenance are not covered.If service is required, contact your dealer. If under warranty, report the model number, date of purchase, serial number and the nature of the failure. If the repair is not covered by the warranty, you will be notified of the charges incurred.If the instrument is to be returned to Hanna Instruments, first obtain a Returned Goods Authorization Number from the Customer Service Department and then send it with shipment costs prepaid. When shipping any instrument, make sure it is properly packaged for complete protection.To validate your warranty, fill out and return the enclosed warranty card within 14 days from the date of purchase.Recommendations for UsersBefore using these products, make sure that they are entirely suitable for your specific application and for the environment in which they are used.Operation of these instruments may cause unacceptable interferences to other electronic equipments, this requiring the operator to take all necessary steps to correct interferences.Any variation introduced by the user to the supplied equipment may degrade the instrument’s EMC performance.To avoid damages or burns, do not put the instrument in microwave oven. For yours and the instrument safety do not use or store the instrument in hazardous environments.Hanna Instruments reserves the right to modify the design, construction and appearance of its productswithout advance notice.For additional information, contact yourdealer or the nearest Hanna Customer Service Center.To find the Hanna Office in your area,visit our web siteIST96771 11/10Factory Calibration AccessoriesCalibrationGLPLast Calibration12•The instrument directly displays concentrationin mg/L of free chlorine and the rangenumber on the LCD.INTERFERENCES FOR CHLORINE LR•Positive error: Bromine, Oxidized Manganese and Chromium, Chlorine dioxide, Ozone and Iodine.•Alkalinity above 250 mg/L CaCO 3or acidity above 150 mg/L CaCO 3 will not reliablydevelop the full amount of color or it may rapidly fade. To resolve this, neutralize the sample with diluted HCl or NaOH.•In case of water with hardness greater than500 mg/L CaCO 3, shake the sample forapproximately 2 minutes after adding the powder reagent.INTERFERENCES FOR CHLORINE UHR•Positive error: Bromine, Oxidized Manganeseand Chromium, Chlorine dioxide, Ozone andIodine.Warning: do not validate or calibrate the instrument with standard solutions other than the Hanna CAL CHECK™ Standards, otherwise erroneous results will be obtained.For accurate validation and calibration results, please perform tests at room temperature (18 to 25°C; 64.5 to 77.0°F).Validation and Calibration proceduresVALIDATIONNote:The validation is performed only for theselected parameter. For full validation of the instrument, the following procedure must be performed for each parameter.1•Turn the meter on by pressing ON/OFF .2•When the beeper sounds briefly and theLCD displays dashes, the meter is ready.3•Place the CAL CHECK™ StandardHI96771-11 Cuvette A into the cuvette holder and ensure that the notch on the cap is positioned securely into the groove.4•Press ZERO/CFM and the lamp, cuvetteand detector icons will appear on the display,depending on the measurement phase.5•After a few seconds the display will show“-0.0-”. The meter is now zeroed and ready for validation.6•Remove the cuvette.7•Place the specific CAL CHECK TM StandardHI96771-11 Cuvette B into the cuvette holder, for and ensure that the notch on the cap is positioned securely into the groove.8•Press CAL CHECK key and the lamp,cuvette and detector icons together with “CAL CHECK ” will appear on the display,depending on the measurement phase.Use the Hanna CAL CHECK™ cuvettes (see “Accessories”) to validate or calibrate instruments.。
ATC20中文资料
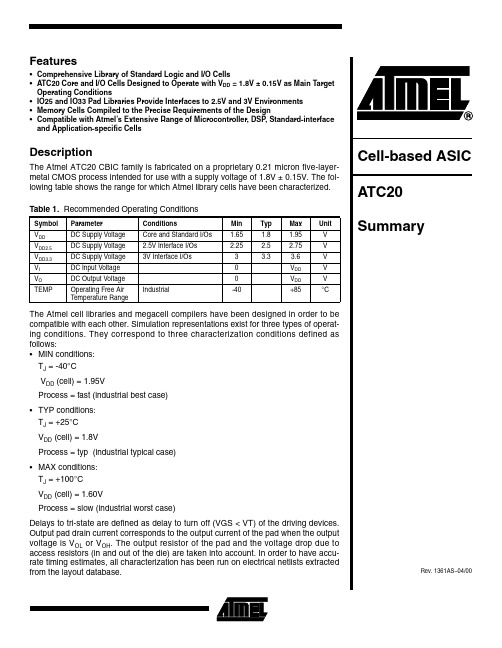
Voltage Levels
The IO18lib library is made up exclusively of low-voltage chip interface circuits powered by a voltage in the range of 1.65V to 1.95V. The library is compatible with the SClib 1.8-volt standard cells library.
•
DEPRQx • DENRQx
DENRBx
DECRQx
•
Enabled D Input
• • • •
1x Drive
• • • • • • • • • • •
2x Drive
• • • • • • • • • • •
Single Output
•
• • • •
Table 5. Scan Flip-flops
NOR Gate OR-AND-Invert Gate OR-AND-OR-Invert Gates OR Gate OR-AND Gate
Multiplexed Scan D Flip-Flop Multiplexed Scan Enable D Flip-Flop Set/Reset Latches with NAND input Subtractor Exclusive NOR Gate Exclusive OR Gate
Cell-based ASIC ATC20 Summary
Rev. 1361AS–04/00
1
元器件交易网
Standard Cell Library SClib
The Atmel Standard Cell Library, SClib, contains a comprehensive set of combinational logic and storage cells. The SClib library includes cells which belong to the following categories: • Buffers and Gates • Multiplexers • Flip-flops • Scan Flip-flops • Latches • Adders and Subtractors
AT89C2051中文资料

AT89C2051中文资料特性:·与MCS-51产品兼容·2K字节可重编程闪存-耐久性:1000次读/写周期·工作电压2.7V至V·全静态运行:0Hz至24MHz·两级程序锁存·128×8位内部RAM·15个可编程I/O口·两个16位定时器/计数器·六个中断源·可编程串行UART(= Universal Asynchronous Receiver Transmitter通用异步收发器)通道·可直接驱动LED的输出·芯片级模仿比较器·低功耗空闲模式和微功耗模式(Power-down mode)说明A T89C2051是一种低电压、高性能的8位CMOS微型计算机。
带2K字节的闪存和可擦可编程只读存储器(EPROM)。
该器件应用爱特美尔(Atmel)的高密度非易失性技术生产,与工业级MCS51架构组相兼容。
将一片通用的8位CPU与闪存集成在单块芯片上,爱特美尔A T89C2051是一种功能强盛的微型计算机。
它为许多嵌入式控制提供了高灵活性低成本的解决方案。
A T89C2051的标准特性如下:2K字节闪存,128字节RAM,15个I/O口,两个16位定时器/计数器,一个五失量两级中断结构,一个全双工串行通信口,一个精准模拟比较器,芯片级振荡器和时钟电路。
另外,A T89C2051用静态逻辑设计,可在低至零频下工作,支持两种软件可选节能模式。
空闲模式下CPU不工作,而RAM,定时器/计数器,串口和中断系统继承工作。
微功耗模式(power-down mode)下保存RAM的内容,但冻结振荡器,禁止其它所有的芯片功能直到下一个硬件复位到来。
特定指令的限制A T89C2051是爱特美尔微控制器家族中经济划算的一款产品。
它包含2K字节的闪速程度存储器。
它与MCS-51架构完全兼容,并且可以使用MCS-51指令组来编程。
AT6CLC资料
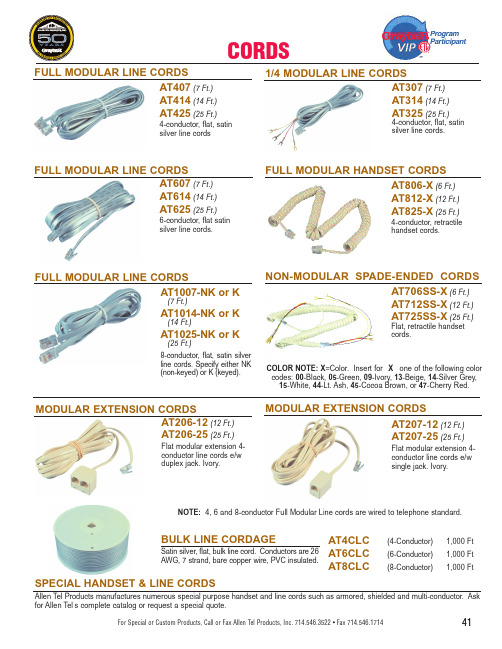
For Special or Custom Products, Call or Fax Allen Tel Products, Inc. 714.546.3522 • Fax 714.546.1714CORDS1/4 MODULAR LINE CORDSFULL MODULAR LINE CORDSFULL MODULAR LINE CORDSFULL MODULAR LINE CORDSFULL MODULAR HANDSET CORDSNON-MODULAR S PADE-ENDED CORDSCOLOR NOTE: X =Color. Insert for X one of the following color codes: 00-Black, 05-Green,09-Ivory, 13-Beige, 14-Silver Grey,15-White, 44-Lt. Ash, 45-Cocoa Brown, or 47-Cherry Red.MODULAR EXTENSION CORDSMODULAR EXTENSION CORDSNOTE: 4, 6 and 8-conductor Full Modular Line cords are wired to telephone standard.BULK LINE CORDAGESatin silver, flat, bulk line cord. Conductors are 26AWG, 7 strand, bare copper wire, PVC insulated.AT307(7 Ft.)AT314(14 Ft.)AT325(25 Ft.)4-conductor, flat, satin silver line cords.AT806-X (6 Ft.)AT812-X (12 Ft.)AT825-X (25 Ft.)4-conductor, retractile handset cords.AT407(7 Ft.)AT414(14 Ft.)AT425(25 Ft.)4-conductor, flat, satin silver line cordsAT607(7 Ft.)AT614(14 Ft.)AT625(25 Ft.)6-conductor, flat satin silver line cords.AT1007-NK or K(7 Ft.)AT1014-NK or K(14 Ft.)AT1025-NK or K(25 Ft.)8-conductor, flat, satin silver line cords. Specify either NK (non-keyed) or K (keyed).AT706SS-X (6 Ft.)AT712SS-X (12 Ft.)AT725SS-X (25 Ft.)Flat, retractile handset cords.AT206-12(12 Ft.)AT206-25(25 Ft.)Flat modular extension 4-conductor line cords e/w duplex jack. Ivory.AT207-12(12 Ft.)AT207-25(25 Ft.)Flat modular extension 4-conductor line cords e/w single jack. Ivory.AT4CLC (4-Conductor)1,000 Ft AT6CLC (6-Conductor)1,000 Ft AT8CLC(8-Conductor)1,000 FtSPECIAL HANDSET & LINE CORDSAllen Tel Products manufactures numerous special purpose handset and line cords such as armored, shielded and multi-conductor. Ask for Allen Tel s complete catalog or request a special quote.41元器件交易网。
AT89C2051中文资料(非常完整)

A T89C2051中文资料电子驿站http:// E-mail: support@AT89C2051是美国ATMEL公司生产的低电压,高性能CMOS 8位单片机,片内含2k bytes的可反复擦写的只读程序存储器(PEROM)和128 bytes的随机存取数据存储器(RAM),器件采用ATMEL公司的高密度、非易失性存储技术生产,兼容标准MCS-5l指令系统,片内置通用8位中央处理器和Flash存储单元,功能强大。
AT89C2051单片机可为您提供许多高性价比的应用场合。
·与MCS-51产品指令系统完全兼容·2k字节可重擦写闪速存储器·1000次擦写周期·2.7V-6V的工作电压范围·全静态操作:0Hz-24MHz·两级加密程序存储器·128×8字节内部RAM·15个可编程I/O口线·2个l6位定时/计数器·6个中断源·可编程串行UART通道AT89C2051 ·可直接驱动LED的输出端口·内置一个模拟比较器·低功耗空闲和掉电模式功能特性概述:AT89C2051提供以下标准功能:2k字节Flash闪速存储器,128字节内部RAM,15个I/O口线,两个16位定时/计数器,—个5向量两级中断结构,一个全双工串行通信口,内置—个精密比较器,片内振荡器及时钟电路。
同时,AT89C2051可降至0HZ的静态逻辑操作,并支持两种软件可选的节电工作模式。
空闲方式停止CPU的工作,但允许RAM,定时/计数器,串行通信口及中断系统继续工作。
掉电方式保存RAM中的内容,但振荡器停止工作并禁止其它所有部件工作直到下一个硬件复位。
方框图引脚功能说明·Vcc:电源电压·GND:地·P1口:P1口是一组8位双向I/O口,P1.2-P1.7提供内部上拉电阻,P1.0和P1.1内部无上拉电阻,主要是考虑它们分别是内部精密比较器的同相输入端(AIN0)和反相输入端(AIN1),如果需要应在外部接上拉电阻。
中文数据手册AT24C系列
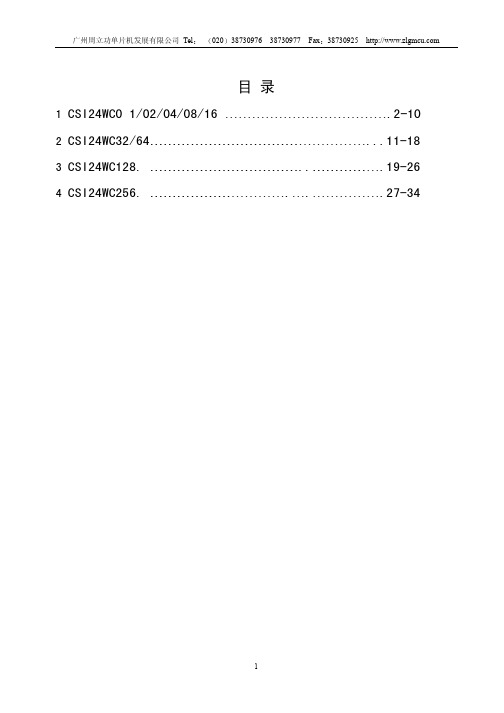
最小 1,000,000 100 2000 100
最大
单位 周期/字节 年 V mA
参考测试模式 MIL-STD-883 测试方法 1033 MIL-STD-883 测试方法 1008 MIL-STD-883 测试方法 3015 JEDEC 标准 17
3
广州周立功单片机发展有限公司 Tel
020
38730976
38730977
Fax 38730925
直流操作特性 Vcc=+1.8V 符号 ICC ISB ILI ILO VIL VIH VOL1 VOL2 +6.0V 除非特别说明 最小 典型 最大 3 0 10 10 1 Vcc 0.7 Vcc 0.3 Vcc+0.5 0.4 0.5 单位 mA A A A V V V V IOL=3 mA IOL=1.5 mA 测试条件 FSCL=100KHz VIN=0 ~Vcc VIN=0 ~Vcc VOUT=0 ~Vcc 参数 电源电流 备用电流(Vcc=5.0V) 输入漏电流 输出漏电流 输入低电压 输入高电压 输出低电压 输出低电压
1
广州周立功单片机发展有限公司 Tel
020
38730976
38730977
Fax 38730925
CAT24WC01/02/04/08/16 1K/2K/4K/8K/16K 位串行 E PROM
2
特性
I2C 总线协议
I2C 总线协议定义如下
5
广州周立功单片机发展有限公司 Tel
020
38730976
38730977
Fax 38730925
1 只有在总线空闲时才允许启动数据传送 2 在数据传送过程中 钟线为高电平时 起始信号 时钟线保持高电平期间 数据线电平从高到低的跳变作为 I2C 总线的起始信号 停止信号 时钟线保持高电平期间 数据线电平从低到高的跳变作为 I2C 总线的停止信号 图1 总线时序 当时钟线为高电平时 数据线必须保持稳定状态 不允许有跳变 时 数据线的任何电平变化将被看作总线的起始或停止信号
AT76C510中文资料
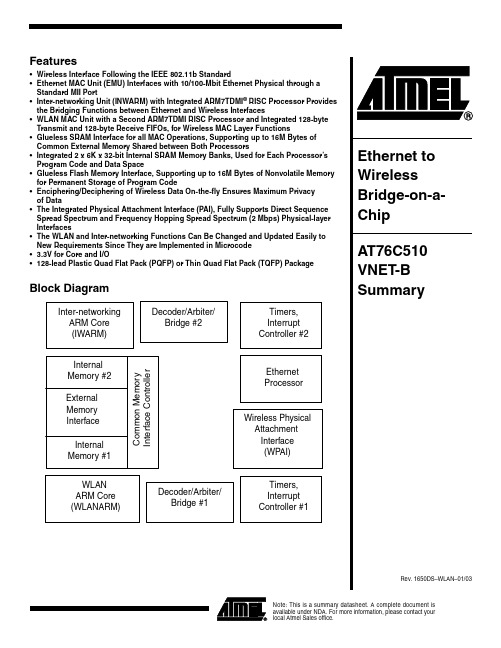
1Note:This is a summary datasheet.A complete document is available under NDA.For more information,please contact your local Atmel Sales office.Features•Wireless Interface Following the IEEE 802.11b Standard•Ethernet MAC Unit (EMU)Interfaces with 10/100-Mbit Ethernet Physical through a Standard MII Port•Inter-networking Unit (INWARM)with Integrated ARM7TDMI ®RISC Processor Provides the Bridging Functions between Ethernet and Wireless Interfaces•WLAN MAC Unit with a Second ARM7TDMI RISC Processor and Integrated 128-byte Transmit and 128-byte Receive FIFOs,for Wireless MAC Layer Functions•Glueless SRAM Interface for all MAC Operations,Supporting up to 16M Bytes of Common External Memory Shared between Both Processors•Integrated 2x 6K x 32-bit Internal SRAM Memory Banks,Used for Each Processor’s Program Code and Data Space•Glueless Flash Memory Interface,Supporting up to 16M Bytes of Nonvolatile Memory for Permanent Storage of Program Code•Enciphering/Deciphering of Wireless Data On-the-fly Ensures Maximum Privacy of Data•The Integrated Physical Attachment Interface (PAI),Fully Supports Direct Sequence Spread Spectrum and Frequency Hopping Spread Spectrum (2Mbps)Physical-layer Interfaces•The WLAN and Inter-networking Functions Can Be Changed and Updated Easily to New Requirements Since They are Implemented in Microcode • 3.3V for Core and I/O•128-lead Plastic Quad Flat Pack (PQFP)or Thin Quad Flat Pack (TQFP)PackageBlock Diagram2AT76C5101650DS –WLAN –01/03OverviewWireless to Ethernet Bridge (VNET-B)is the Inter-networking device for interconnecting a Wireless LAN with other Wireless LANs (WLAN)and legacy LANs.VNET-B based bridges act as Access Points (AP)to the WLAN and communicate pack-ets that are destined outside the WLAN using IP over Ethernet.In case the WLAN user is mobile,roaming functions are also supported at the VNET-B bridges.The data transactions over this unified environment are categorized according to the type of end-to-end devices.End Stations TransactionsWhen two end stations communicate (irrespective to the type of network they belong)the inter-networking between the different networks should be transparent.Inter-networking Device TransactionsThe VNET-B device implements all necessary communication protocols for supporting inter-networking functions,implements logical grouping of users independent of their physical location and provides secure links by implementing encryption algorithms.on recycled paper.ATMEL ®is the registered trademarks of Atmel.ARM7TDMI ®is the registered trademark ARM,Ltd.Other terms and product names may be the trademarks of others.©Atmel Corporation 2003.Atmel Corporation makes no warranty for the use of its products,other than those expressly contained in the Company ’s standard warranty which is detailed in Atmel ’s Terms and Conditions located on the Company ’s web site.The Company assumes no responsibility for any errors which may appear in this document,reserves the right to change devices or specifications detailed herein at any time without notice,and does not make any commitment to update the information contained herein.No licenses to patents or other intellectual property of Atmel are granted by the Company in connection with the sale of Atmel products,expressly or by implication.Atmel ’s products are not authorized for use as critical components in life support devices or systems.Atmel HeadquartersAtmel OperationsCorporate Headquarters2325Orchard Parkway San Jose,CA 95131USATEL 1(408)441-0311FAX 1(408)487-2600EuropeAtmel SarlRoute des Arsenaux 41Case Postale 80CH-1705Fribourg SwitzerlandTEL (41)26-426-5555FAX (41)26-426-5500AsiaRoom 1219Chinachem Golden Plaza 77Mody Road Tsimshatsui East Kowloon Hong KongTEL (852)2721-9778FAX (852)2722-1369Japan9F,Tonetsu Shinkawa Bldg.1-24-8ShinkawaChuo-ku,Tokyo 104-0033JapanTEL (81)3-3523-3551FAX (81)3-3523-7581Memory2325Orchard Parkway San Jose,CA 95131TEL 1(408)441-0311FAX 1(408)436-4314Microcontrollers2325Orchard Parkway San Jose,CA 95131TEL 1(408)441-0311FAX 1(408)436-4314La Chantrerie BP 7060244306Nantes Cedex 3,France TEL (33)2-40-18-18-18FAX (33)2-40-18-19-60ASIC/ASSP/Smart CardsZone Industrielle13106Rousset Cedex,France TEL (33)4-42-53-60-00FAX (33)4-42-53-60-011150East Cheyenne Mtn.Blvd.Colorado Springs,CO 80906TEL 1(719)576-3300FAX 1(719)540-1759Scottish Enterprise Technology Park Maxwell BuildingEast Kilbride G750QR,Scotland TEL (44)1355-803-000FAX (44)1355-242-743RF/AutomotiveTheresienstrasse 2Postfach 353574025Heilbronn,Germany TEL (49)71-31-67-0FAX (49)71-31-67-23401150East Cheyenne Mtn.Blvd.Colorado Springs,CO 80906TEL 1(719)576-3300FAX 1(719)540-1759Biometrics/Imaging/Hi-Rel MPU/High Speed Converters/RF DatacomAvenue de Rochepleine BP 12338521Saint-Egreve Cedex,France TEL (33)4-76-58-30-00FAX (33)4-76-58-34-80e-mailliterature@Web Site1650DS –WLAN –01/03xM。
AT89C52单片机介绍

AT89C52单片机介绍n to AT89C52 MicrocontrollerAmong the many microcontroller series。
AT89C52 is a low-power。
high-performance CMOS 8-bit microcontroller with 8K programmable Flash memory in the series。
Manufactured using Atmel's high-density non-volatile memory technology。
it is fully compatible with the industrial 80C51 product ns and pins。
The on-chip Flash allows for system programmable memory and is also suitable for nal programming。
With a nimble 8-bit CPU and system programmable Flash on a single chip。
the AT89C52 ___.The AT89C52 has the following standard features: 8K bytes of Flash。
256 bytes of RAM。
32-bit I/O lines。
three 16-bit timers/counters。
a loud 2-level interrupt structure。
full-duplex serial port。
on-chip oscillator and clock circuit。
In n。
theAT89C52 can be ced to 0Hz static logic n and supports two are-selectable power-saving modes。
C1010中文资料

Schematic:Top View
Absolute Maximum Ratings
Parameter Input Forward current Peak forward current Reverse voltage Power dissipation Output Collector-emitter voltage Emitter-collector voltage Collector current Collector power dissipation Total power dissipation Isolation voltage 1 minute Operating temperature Storage temperature Soldering temperature 10 second Symbol IF IFM VR PD VCEO VECO IC PC Ptot Viso Topr Tstg Tsol Rating 50 1 6 70 70 6 50 150 200 5000 -30 to +115 -55 to +125 260 Unit mA A V mW V V mA mW mW Vrms °C °C °C
Collector Current Ic (mA)
Forward Current IF (mA)
Ambient Temperature Ta (°C)
Ambient Temperature Ta (°C)
c
2004
cosmo ELECTRONICS CORPORATION
Fig.7 Relative Current Transfer Ratio vs. Ambient Temperature
2SA1020中文资料(secos)中文数据手册「EasyDatasheet - 矽搜」

1.60 Max
E 0.35 0.65 M 0.00 0.40
F 0.30 0.51 N
4.00 Min
G
1.50 TYP.
(T = 25°C除非另有说明)
符号 V V V I P
T ,T
额定值
-50 -50 -5 -2 900 150, -55~150
单元
V V V A mW °C
(T = 25°C除非另有说明)
31日 - 12月2010修订版B
基地
发射器
REF.
Millimeter Min. Max.
REF.
Millimeter Min. Max.
A 5.50 6.50 H 1.70 2.05
B 8.00 9.00 J 2.70 3.20
C 12.70 14.50 K 0.85 1.15
D 4.50 5.30 L
170205270320085115160max000040400min绝对最大额定值绝对最大额定值25c除非另有说明参数参数集电极基极电压集电极到发射极电压发射器基极电压连续集电极电流集电极耗散功率结存储温度符号符号额定值额定值50505290015055150单元单元电气特性电气特性25c除非另有说明参数参数集电极基击穿电压集电极到发射极击穿电压发射器基极击穿电压集电极截止电流发射极截止电流dc电流增益集电极到发射极饱和电压基地发射极饱和电压转换频率集电极输出电容开启时间贮存时间下降时间符号符号min
y.
第1页3
芯片中文手册,看全文,戳 特性曲线
2SA1020
-2A, -50V PNP塑封三极管
31日 - 12月2010修订版B
Any changes of specification will not be informed individually.
at89c1051中文资料

ØÙÚVk)Il rÛÁÜÃ ±´Î !ÛÁÜÃ ±´Î ÝÞßJàáV»ÒÓ
Ô Ð XÁÂâ ã äå £æ±
ç{»¼½ ¾¿À è Ð XÈÉÜ \zÁÜà èÈÉ Ð¤£ Ф¥ (zÁÜ{éáVÓ
\ ØêëVÒÓ
RS¨©
w yô|}áV$% õö 8ô|}áV di ëz:ôJ
2(. /45 ^5 {³ |2à}ÒO45IJìÜ45\~3454i{³ PJ; à2( N Z=*!IJ¨© èÏ2(45.¨©PJ
ÆÇ
www.tai-yan.co ÈÉ?ÊË m §ÌÌ
·
/b ÍÎÀ Ï bs Ð X Ð X^Ñ ¯ f_ ´µ¶ X Ф£ Ф¥ DEVÒÓ
wK&Vj452(ÒOk^^l rl eÂZ=*f8cÈmôghÂi tú:b2(
6n&cd:op23:bqrsÏ.
w ÛO45 $%
t RSV$% :l uvw*xfúV
电子器件采购平台: IC资料查询网站: 电子工程技术论坛:/bbs
# ( ÈÉU^ 2VÏ.]$ ® X#Q^WðñRS # »¼ |êeV>$%# ®)ô»îï ®)îï93 îï!Ü v\ï½
X
ê
t mn àgz\ }ZW ¡¢PÒ
W ¡¢B & Wmn\p¡¢
v è
ai
tribon错误代码中文对照
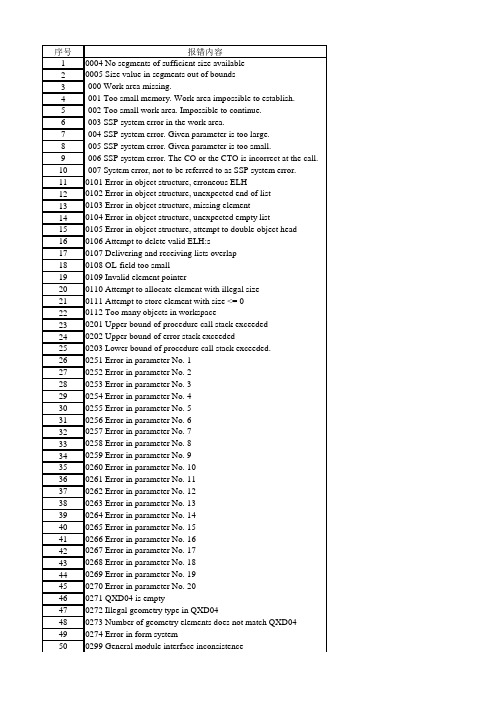
序号报错内容10004 No segments of sufficient size available20005 Size value in segments out of bounds3-000 Work area missing.4-001 Too small memory. Work area impossible to establish.5-002 Too small work area. Impossible to continue.6-003 SSP system error in the work area.7-004 SSP system error. Given parameter is too large.8-005 SSP system error. Given parameter is too small.9-006 SSP system error. The CO or the CTO is incorrect at the call. 10-007 System error, not to be referred to as SSP system error. 110101 Error in object structure, erroneous ELH120102 Error in object structure, unexpected end of list130103 Error in object structure, missing element140104 Error in object structure, unexpected empty list150105 Error in object structure, attempt to double object head 160106 Attempt to delete valid ELH:s170107 Delivering and receiving lists overlap180108 OL-field too small190109 Invalid element pointer200110 Attempt to allocate element with illegal size210111 Attempt to store element with size <= 0220112 Too many objects in workspace230201 Upper bound of procedure call stack exceeded240202 Upper bound of error stack exceeded250203 Lower bound of procedure call stack exceeded.260251 Error in parameter No. 1270252 Error in parameter No. 2280253 Error in parameter No. 3290254 Error in parameter No. 4300255 Error in parameter No. 5310256 Error in parameter No. 6320257 Error in parameter No. 7330258 Error in parameter No. 8340259 Error in parameter No. 9350260 Error in parameter No. 10360261 Error in parameter No. 11370262 Error in parameter No. 12380263 Error in parameter No. 13390264 Error in parameter No. 14400265 Error in parameter No. 15410266 Error in parameter No. 16420267 Error in parameter No. 17430268 Error in parameter No. 18440269 Error in parameter No. 19450270 Error in parameter No. 20460271 QXD04 is empty470272 Illegal geometry type in QXD04480273 Number of geometry elements does not match QXD04 490274 Error in form system500299 General module interface inconsistence510301 Overflow in object520302 New object name already in use530303 Object does not exist540304 Invalid object pointer550305 Open failure on input file560306 Invalid format on input file570307 Invalid object name (too long)580308 Write failure on file590321 Invalid logical data bank unit600322 Logical data bank unit already in use610323 Data bank table full620324 Lock entry found instead of object630325 Logical data bank unit not connected640326 Object already exists in working area650327 Object not found in the data bank660328 Object not locked670329 Data file has invalid format680330 Object currently locked by another user690331 Too many objects are already locked700332 Object has invalid format710333 Object already exists in data bank720334 No room in data bank730335 Unsupported object structure740336 Virtual data bank already conneced750337 Virtual data bank not connected760338 Databank may not be of type "sequential db directory" 770339Attempt to store a non-picture object in a sequential db directory780340 Open failure of directory file790341 Close failure of directory file800342 Record not found in the directory file810343 Record locked820344 Fatal error in directory file830345 Error creating directory file840346 Record already exists in directory file850347 No room on output device when updating directory file 860348 Data bank currently locked by another user.870349 Attempt to lock an object in a sequential db directory 880350 Open failure of data file890351 Close failure of data file900352 Record not found in the data file910353 Record locked920354 Fatal error in data file930355 Error creating data file940356 No room on output device when updating data file950357 Two revisions of the same object not allowed in workspace 960358 Allocation map has invalid format970360 Open failure of sequential data bank980361 Close failure of sequential data bank990362 End of file of sequential data bank1000364 Fatal error in sequential data bank1010365 Error creating sequential data bank1020366 No room on output device when updating sequential data bank 1030367 Error in object code1040368 Restored object size does not match the stored size. 1050369 Attribute type not recognized1060370 Access to object not allowed1070371 M2 can not read objects of version 41080372 Project not enabled to store objects of version 41090401 Too big contour, element maximum size exceeded1100402 Error in record (card) decoding1110403 Unknown record (card) type1120404 Wrong order of picture elements1130405 Unexpected end of file1140406 Erroneous input term, should be record type1150407 Unexpected new object, old one not completed1160408 Unexpected geometry element1170409 Erroneous term - violates input syntax1180410 Unexpected component element1190411 Unexpected subcomponent element1200412 Syntax error in input1210413 Data missing in input for component1220414 Data missing in input for subcomponent1230415 Data missing in input for text element1240416 Unexpected subpicture element1250417 Data missing in input for subpictures1260418 Set of rules is not initiated1270419 Number for placing rules is not found for specific parameter 1280501 Empty component1290502 Wrong level for subcomponent1300503 Empty subcomponent1310504 Unknown data type for geometry element1320505 Wrong level for geometry1330506 Empty picture object1340507 Unallowed scale factor1350508 The element is not a subpicture1360509 Unallowed level1370510 Unallowed number of subpicture levels1380511 Unallowed start level for identification1390512 Unallowed end level for identification1400513 Subordinate element missing1410514 Empty picture1420515 Transformation information missing1430516 The element is not a subcomponent1440517 Illegal font number1450518 Symbol font file does not exist1460524 Indicated segment does not exist1470525 Points on the contour not given in the direction of the contour 1480526 Indicate element does not exist1490527 Wrong type of element given1500529 Object not initialized1510530 Subordinate level not open1520531 Element on superior level not open1530532 Symbol does not exist 1540533 Size of element too big 1550534Mismatch between the opened subcomponent and the given 1560535 Text font file does not exist or out of range (8-99)1570536 Error in text font file (8-99)1580537 Error when loading text font file (8-99)1590538 Vector font file does not exist or out of range (1-99)1600539 Vector font does not exist 1610540 Vector font does exist but language not assigned 1620541 Internal symbol font error 1630701 Erroneous object head (ELH-error)1640702 Empty picture object 1650703 Attempt to identify an element not being a component 1660801 Error in activity code 1670802 First file does not exist 1680803 First message array too small 1690804 First index array too small 1700805 Second file does not exist 1710806 Second message array too small 1720807 Second index array too small 1730808 Message file not available 1740809 Impossible to open plotter file 1750810 Read error on first message file 1760811 Read error on second message file 1770812 Denoted message does not exist 1780901 Communication breakdown 1791001 CAT-object does not exist 1801002 Contour does not exist 1811003 Table row does not exist 1821004 Member does not exist 1831005 Segment part does not exist 1841006 Error in contour representation 1851007 Error in activity code specifying the contour to be treated 1861008Error in activity code specifying the part of the contour to be treated 1871009Error in activity code specifying the part of the table to be treated 188-100 Incorrect total name.1891010Error in activity code specifying the part of the table row to be treated 1901011Error in activity code specifying the table member to be treated 1911012Error in activity code specifying the part of the table member to be treated 1921013 Invalid segment number 1931014Error in activity code specifying the part of the segment to be treated 1941015 Error in specifying the attribute to be treated 1951016Error in location parameter defining the kind of attribute to be treated 1961017Error in location parameter defining the position of the wanted element 1971018 Invalid current CAT-object number1981019 Pointer in QCATPT of QWC030 to owner element not valid 199-101 Total name too long.2001020 The object is not a CAT-object 2011021 Error in attribute size 2021022 Erroneous segment type 2031023 Dimensions not equal in receiving and delivering contours 2041024Error in activity code specifying the part of a segment to be saved 2051025Error in activity code specifying the part of a contour to be saved 2061026 Given point is outside contour 2071027 Error in representation (must be 2 or 3)2081028Given representation does not correspond to the original representation in 2091029 Given data not sufficient to define the new coordinate system 210-102 Type too long.2111030Error in activity code specifying how to create a transformation matrix 2121031 Error in parameter defining the coordinate axis 2131032 Error in parameter defining the coordinate plane 2141033 Transformation matrix is not invertible 2151034 Error in activity code defining point or vector 2161035Error in activity code specifying storing of attribute data (common area of 2171036 Segment given from input is a zero segment 2181037 Beta given from input does not belong to (0,1)2191038 Tangent vector undefined 2201039 Equation root < 0221-103 Attribute name too long.2221040 Vector along line is the zero vector 2231041 Vector perpendicular to plane is the zero vector 2241042 The contour is not closed 2251043 Transformation not possible because the transformation matrix includes a 2261044 Points not given in the direction of the contour 2271045 Error in activity code controlling tangent calculations 2281046 Error in tangent code 2291047 Too many point attributes 2301048 Given activity code does not allow equal contours 2311049 The contour does not contain any segments 232-104 Incorrect pointer.2331050 The contour is closed 2341051 Impossible to insert contour 2351052Error in activity code (PTYPE)specifying the type of projection 2361053The centre of projection lies in the projection plane (central projection)2371054The projecting lines are parallel to the projection plane (parallel 2381055 Input object and resulting object must not be equal 2391056 Error in contour code 12401057 Error in object code 22411058 2-attribute at contour level not found 2421059 2-attribute at object level not found 243-105 The first of the given objects in the parameter list is missing.2441060 Space curve improperly stored2451061 Wrong geometry type for R2-contour2461062 Impossible tangent vectors2471063 Intersection point missing2481064 Too many intersection points2491065 Impossible to create fillet2501066 Argument array too small2511067 Array too small2521068 Unallowed value of scewness factor2531069 Undefined tangent vector254-106The second of the given objects in the parameter list is missing.2551070 Bad combination of data for a BC-segment (surface problem) 2561071 Coordinate outside given limits2571072 Impossible to create curve2581073 Intersection curve missing2591074 Given length longer than contour length2601075 Upper bound of attribute data structure exceeded261-107 Object missing.262-108 The given object is not a geometry object.263-109 The given object is not a table object.264-110 The given objects are of different kinds.265-111 Empty object at the call.266-112 Contour 0 empty at the call.267-113 The given contour number too large.268-114 The given contour 0 at the call closed.269-115 The last segment of the CO-0 at the call is not a line segment. 270-116The last segment of the CO-0at the call is parallel to the given line.271-117The end point of the CO-0at the call lies inside the given circle.272-118 The given segment does not exist.273-119 Incorrect orientation of the given segments.274-120 The given length is too large.275-121 The given point does not lie on the given segment.276-122 Incorrect end point selection (f = 0 and f = 1).277-123 One or several breakpoints outside KRANGE.278-124 Amplitude outside KRANGE.279-125The given amplitude is larger than half the distance between the end points280-126 Central angle greater than 360.281-127 Number of distinct points less than 2.282-128 Intersection point number not equal to + 1 or + 2. 283-129 The length of the interval is zero.284-130 Integer parameter outside the range.285-131 Incorrect location code.286-132 Too large attribute.287-133 Attribute of wrong format.288-134 Incorrect code number for part selection of contour. 289-135 Point on contour with given coordinate missing. 290-136 Incorrect boundary conditions.291-137 Incorrect intersection point designation.292-138 Incorrect storing of points in the CTO.293-139 Incorrect parameter data type.294-140 Table row missing.295-141 Improper storing of table. 296-142 The given radius is too large.297-143The second of the given objects in the parameter list existed at the call.298-144 Incorrect password.299-145 Incorrect number of parameters.300-146 Unallowed value of input parameters.301-147 Attribute number out of range.302-148 Table member missing.303-149 Input string is empty.304-150 Unallowed inclination angle.3052001 Unallowed record number in text input3062002 Wrong order among records in text input3072004 No object is current3082005 Current subpicture not panel3092006 Information about current measurement element missing 3102007 Erroneous table structure311-200 Attribute type out of bounds.312-201 Attribute head without attribute.313-202 Type out of bounds.314-203 I/O buffer too small.315-204 Row head without elements.316-205 Incomplete type 5 attribute.317-206 Impossible to unpack I/O buffer.31822000 Name of current deck is missing in modal storage. 31922001 Projection attribute is missing in picture object. 32022002 Transformation attribute is missing in picture object. 32122003 Erroneous item attribute.32222004 Name of deck is missing in picture object. 32322005 Name of room is missing in picture object. 32422006 No current room.32522007 Hole id out of range.32622008 Erroneous start element.32722009 Invalid identification number.32822010 Invalid data type.32922011 Error in conversion of a point from 2D to 3D. 33022012 Projection is not axis-parallel.33122013 Error transforming an arrangement.33222014 Copy an item failed.33322015 Unknown item type to recreate.33422016 Failed to identify a room.33522017 Erroneous type of item.33622018 Erroneous height axis.33722019 Pointer to the deck not found.33822020 Erroneous number of intersections.33922021 Copy geometry element failed.34022100 Erroneous type of item.34122300 Name of deck is missing in model object.34222301 Erroneous directrix.34322600 Error in form handling.34422601 Prohibited component type.34522602 Prohibited table.34622603 Erroneous table dimension.34722604 Prohibited table item.34822605 Incorrect data type of table value.34922606 Erroneous type of information.35022607 Erroneous description object.35122608 Error occured in the LIB$SET_LOGICAL function. 35223000 Invalid identification number.35323001 Error in form handling.35423002 Undefined symbolic name for test sequence directory. 35523003 File specification syntax error.3562501 Impossible to create default file.3572502 Mismatch between 01 and 04 objects in parts generation 3582503 Incorrect type of CAT-object3592504 Incorrect type of picture object3602505 Incorrect combination of objects3612506 Incorrect storing of 02-object3622507 Attribute describing detail missing or incorrect in 02-object 3632508 Incorrect type of subpicture in 03-element (ID missing) 3642509 Attribute 101 missing or incorrect in 01-object3652510 Attribute 101 missing or incorrect in 02-object3662511Attribute containing transformation matrix missing or incorrect in3672512 Undefined CAT-object3682513 Undefined picture object3692514 Illegal format on data file containing part names3702515 Parent plate missing in 03-object3712516 Subcomponent corresponding to attribute missing3722517 Contour attribute 101 missing3732518 Standard hook file has illegal format or does not exist 3742519 Component corresponding to attribute is missing3752520 Start order attributes do not correspond to the start attributes3762521Auxiliary function attribute found on segment level is missing on object3772522Gap attribute found on segment level is missing on object level3782523 Internal attribute arrays exceeded3792524 Inconsistency in plate structure3802525 Attribute not found3812526 Incorrect attribute3822527 Plate part contour missing or erroneous3832528 Verified path outside raw plate3842529 Impossible to create chamfer file3852530 Impossible to evaluate CVBA angle3863001 SLABEL too big. Impossible to put in index tables3873002 Information about SLABEL does not exist3883003 Invalid index to IDENT-table3893004 ID is not found in IDENT-table3903005 ID-table is full3913006Information about SLABEL exists,must be deleted before "put".3923007 No current scheme3933008 Editor not in system3943009 Any of the index table attributes missing395-300 One or more breakpoints outside KRANGE.3963010 Scheme name in attribute 199 "not =" current scheme name. 3973011 No picture object found3983012 Error opening scheme file for writing3993013 Error writing scheme file line4003014 Error converting scheme for writing4013015 Panel already occupied by scheme generation402-301 Amplitude outside KRANGE.403-302The amplitude is larger than half the distance between the starting point404-303 Intersection point missing.405-304 Intersection point before the given point missing. 406-305 Intersection point after the given point missing.407-306The last line segment of the CO-0at the call is not touched by the bending408-307 The given point lies on the contour 0 of the given description. 409-308 Incorrect boundary conditions.410-309 Part of CAT object missing.4113100 Failed to verify the shell curve object.4123101 Failed to verify the seam object.4133102 31024143103 The curve is outside the default box.4153104 Failed to verify the point object.4163105 Failed to verify the plane object.4173106 Failed to verify the cylinder object.4183107 Corrupt point object, the root attribute does not exist. 4193108 Corrupt seam object, the root attribute does not exist. 4203109 Corrupt curve object, the root attribute does not exist.421-310 Data file not open for reading.4223110 Corrupt cylinder object, the root attribute does not exist. 4233111 Corrupt plane object, the root attribute does not exist. 4243112 Corrupt object, a point attribute is missing.4253113 Corrupt object, a plane attribute is missing.4263114 Corrupt object, a curve attribute is missing.4273115 Corrupt object, a cylinder attribute is missing.4283116 Corrupt object, a surface attribute is missing.4293117 A referenced surface object was not found.4303118 A referenced curve object was not found.4313119 A referenced point object was not found.432-311 Data file not open for writing.4333120 A referenced plane object was not found.4343121 A referenced cylinder object was not found.4353122 Corrupt object, invalid definition data.4363123 Failed to intersect the surface with the plane.4373124 Failed to intersect the shell curve with the plane.4383125 Failed to convert a Lines Fairing curve to a space curve. 4393126 Failed to expand the point object.4403127 Failed to expand the plane object.4413128 Failed to expand the curve object.4423129 Failed to intersect the two curves.443-312 Data file already open for sequential processing.4443130 Could not define a parameter axis for proper space curve. 4453131 Failed to trim the curve with the default box.4463132 Corrupt object, invalid or missing root attribute.4473133 Failed to reduce object.4483134 Conversion failed: Could not find a parameter axis. 4493135 Failed to verify the shell profile object.4503136 Failed to verify the shell stiffener object.4513137 A referenced shell stiffener object was not found.4523138 Maximum number of points exceeded.4533139 Failed to verify the feature.454-313 Demanded unit missing.4553140 Failed to verify the hull curve object.4563141 Limit table object missing or incorrect.4573142 Mismatch in limit table.4583143 A referenced panel was not found.4593144 A referenced shell profile was not found.4603145 A referenced seam was not found.4613146The shell stiffener overlaps another stiffener in the shell profile.4623147 The point cannot be moved outside the curve.4633148 Failed to intersect the shell curves.464-314 Intersection point missing when n = 0.465-315 Impossible to write (e.g. secondary areas filled).466-316 Data file already closed.467-317 Spline calculations interrupted. Check input points.468-318Plane curve not single-valued with respect to the given coordinate.469-319 Record locked.4704001 PCDB - No component slot available4714002 PCDB - Component not found in the data bank4724003 PCDB - Component currently locked by another user 4734004 PCDB - Component already exists on the data bank 4744005 PCDB - Component has invalid format4754006 PCDB - Invalid current component number4764007PCDB-Component not current under given current component number4774008 PCDB - Invalid activity code4784009 PCDB - Object found instead of a component4794201 PCDB - Search object already exists4804202 PCDB - Search data not defined4814203 PCDB - Search data not defined at connection one4824301 PSDB - Failure creating lock entry4834302 PSDB - Named element already exists4844303 PSDB - Superior environment is not active4854304 PSDB - Already active in QWQ124864305 PSDB - Invalid data type4874306 PSDB - One or two project object missing4884307 PSDB - Invalid status encountered in QWQ124894308 PSDB - Object not locked when attempting to delete or update 4904309 PSDB - Attribute not found4914310 PSDB - Part not found4924311 PSDB - External part cannot be updated4934312 PSDB - Name missing in name table 4944313 PSDB - Impossible part4954314 PSDB - Erroneous data in attribute4964315 PSDB - Keyword not found in syntax definition4974316PSDB-Arguments do not match the application(is syntax definition4984317 PSDB - Error in deleting connection attribute4994318 PSDB - Error during deletion of a part5004319 PSDB - Error when restoring part5014320 PSDB - Failure deleting subview (interactive modelling) 5024321 PSDB - Transformation data for view missing5034322 PSDB - Failure copying subview (interactive modelling) 5044323 PSDB - Name attribute missing (interactive modelling) 5054324 PSDB - Interactive component choice menu not initiated 5064325 PSDB - Error in logical references5074326 PSDB - Branch element not found5084327 PSDB - Error in object pointer of part5094328 PSDB - Error when creating new branch5104329 PSDB - Referenced ppdb object not found5114330 PSDB - Pipe length not defined where it should be defined 5124331 PSDB - Unexpected element pointer5134332 PSDB - Branch not found5144333 PSDB - Failure open model subview5154334 PSDB - Impossible connection number5164335 PSDB - Invalid object name5174336 PSDB - Extra connection information attribute not found 5184337 PSDB - Conflicting co-ordinate data5194338 PSDB - Bad call of lock co-ordinate routines5204339 PSDB - Failure converting to equipment5214350 PSDB - Previously stored attribute is missing5224610 PPDB - Erroneous element pointer5234611 PPDB - Erroneous element type5244612 PPDB - Erroneous element size5254613 PPDB - Erroneous element structure5264620 PPDB - Error creating object name (names too long) 5274621 PPDB - Error splitting object name5284640 PPDB - Project not current5294641 PPDB - Position not current5304642 PPDB - Function not current5314643 PPDB - Pipe not current5324644 PPDB - Pipe sketch not current5334660 PPDB - Project already exists5344661 PPDB - Position already exists5354662 PPDB - Function already exists5364663 PPDB - Pipe already exists5374664 PPDB - Pipe sketch already exists5384670 PPDB - Project does not exist5394671 PPDB - Position does not exist5404672 PPDB - Function does not exist5414673 PPDB - Pipe does not exist5424674 PPDB - Pipe sketch does not exist5434680 PPDB - Subordinate element current5444681 PPDB - Object and reference element do not correspond 5454682 PPDB - Erroneous component limit5464683 PPDB - Element with spec. ID already exists5474684 PPDB - Element with spec. ID does not exist5484685 PPDB - Erroneous connection reference5494686 PPDB - Too many part elements in one material 5504690 PPDB - Referenced part not found in PSDB5514691 PPDB - Sketch limit not allowed5524692 PPDB - PSDB not current5534693 PPDB - Element not found in PSDB5544694 PPDB - Part not found in PSDB5554695 PPDB - PCM-attribute not found in PSDB5564801 PPDB - Erroneous font number5574802 PPDB - Contour attribute not found5584803 PPDB - Error in reading drawing form5594804 PPDB - Invalid format of bending machine attribute 5604901 PPDB - Pipe reference in common area QWP60 not found5614902PPDB-Maximum number of reference points in pipe sketch exceeded5624903 PPDB - More than three connections5635000 PCDB - Invalid component type5645001 PCDB - Invalid component group5655002 PCDB - Invalid component subgroup5665003 PCDB - Invalid pressure class5675004 PCDB - Failure reading component5685005 PCDB - Failure deleting component5695006 PCDB - Failure reading search object5705007 PCDB - Failure deleting search object5715008 PCDB - Failure storing component5725009 PCDB - Failure listing component573-500 Empty geometry object.5745010 PCDB - Failure storing search object5755011 PCDB - Nominal diameter could not be calculated5765012 PCDB - No search mask exists for given component type 5775013 PCDB - Search object not found5785014 PCDB - Failure creating MIS input579-501 Empty table object.580-502 The given points are collinear.581-503 Undefined axis.582-504 Incorrect storing of plane.583-505 Coordinates in wrong order.584-506 Incorrect storing of space curve.585-507 The space curve consists of more than one curve branch.586-508Space curve not single-valued with respect to the given coordinate.587-509 Undefined direction.588-510 No part of the curve inside the given interval.589-511 Incorrect storing of cylinder.590-512 Incorrect storing of surface or surface element.591-513 Intersection curve missing.592-514 Attribute 1 missing.。
TS79L08CT中文资料

TS79L00 series3-Terminal Low Current Negative Voltage RegulatorVoltage Range - 5V to - 24V Output Current up to 100mAGeneral DescriptionThe TS79L00 Series of negative voltage regulators are inexpensive, easy-to-use devices suitable for a multitude of applications that require a regulated supply of up to 100mA. Like their higher power TS7900 and TS79M00 Series cousins, these regulators feature internal current limiting and thermal shutdown making them remarkably rugged. No external components are required with the TS79L00 devices in many applications.These devices offer a substantial performance advantage over the traditional zener diode-resistor combination, as output impedance and quiescent current are substantially reduced.This series is offered in 3-pin TO-92, SOT-89 and 8-pin SOP-8 package.FeaturesOutput current up to 100mA No external components required Internal thermal overload protection Internal short-circuit current limitingOutput transistor safe-area compensationOutput voltage offered in 4% toleranceOrdering InformationNote: Where xx denotes voltage option.Part No.Operating Temp.(Ambient)PackageTS79LxxCT TO-92TS79LxxCY SOT-89TS79LxxCS -20 ~ +85 o C SOP-8 Standard ApplicationA common ground is required between the input and theoutput voltages. The input voltage must remain typically 2.0V above the output voltage even during the low point on the Input ripple voltage. XX = these two digits of the type number indicate voltage.* = Cin is required if regulator is located an appreciabledistance from power supply filter.** = Co is not needed for stability; however, it doesimprove transient response.Pin AssignmentPin No.TS79L00CT TS79L00CY TS79L00CSPin Description3 3 1 Output 222, 3, 6, 7Input1 1 5 Ground 4, 8 Non connectedAbsolute Maximum RatingInput Voltage Vin * - 35 V Input Voltage Vin ** - 40 V Power Dissipation TO-92TO-89 SOP-8 Pd0.6250.50.5WOperating Junction Temperature Range T J0 ~ +125 o C Storage Temperature Range T STG-65 ~ +150 o C Note : * TS79L05 to TS79L18** TS79L24TS79L05 Electrical Characteristics(Vin= -10V, Iout=40mA, 0 o C≤Tj≤125 o C, Cin=0.33uF, Cout=0.1uF; unless otherwise specified.)Parameter Symbol TestConditions MinTypMaxUnitTj=25 o C - 4.80 - 5 - 5.20Output voltage Vout -7.5V≤Vin≤ -20V,5mA≤Iout≤100mA - 4.75 - 5 - 5.25VLine Regulation REGline Tj=25 o C -7.5V≤Vin≤ -20V,Io=40mA-- 50 150 5mA≤Iout≤100mA -- 20 60Load Regulation REGload Tj=25 o C5mA≤Iout≤40mA --1030mVQuiescent Current Iq Iout=0, Tj=25 o C --36-8V≤Vin≤ -20V -- -- 1.5Quiescent Current Change ∆Iq1mA≤Iout≤40mA ----0.1mAOutput Noise Voltage Vn 10Hz≤f≤100KHz, Tj=25 o C -- 40 -- uVRipple Rejection Ratio RR f=120Hz, -8V≤Vin≤ -18V 41 49 -- dBVoltage Drop Vdrop Tj=25 o C -- 1.7 -- VPeak Output Current Io peak Tj=25 o C --0.15--A z Pulse testing techniques are used to maintain the junction temperature as close to the ambient temperature aspossible, and thermal effects must be taken into account separately.z This specification applies only for DC power dissipation permitted by absolute maximum ratings.TS79L06 Electrical Characteristics(Vin= -11V, Iout=40mA, 0 o C≤Tj≤125 o C, Cin=0.33uF, Cout=0.1uF; unless otherwise specified.)ParameterTestConditionsMinTypMaxUnitTj=25 o C - 5.76 - 6 - 6.24Output voltage Vout -8.5V≤Vin≤ -21V,5mA≤Iout≤100mA - 5.70 - 6 - 6.30VLine Regulation REGline Tj=25 o C -8.5V≤Vin≤ -21V,Io=40mA-- 50 150 5mA≤Iout≤100mA -- 20 60Load Regulation REGload Tj=25 o C5mA≤Iout≤40mA -- 1030mVQuiescent Current Iq Iout=0, Tj=25 o C --36-9V≤Vin≤ -21V -- -- 1.5Quiescent Current Change ∆Iq1mA≤Iout≤40mA ----0.1mAOutput Noise Voltage Vn 10Hz≤f≤100KHz, Tj=25 o C -- 40 -- uVRipple Rejection Ratio RR f=120Hz, -9V≤Vin≤ -19V 41 49 -- dBVoltage Drop Vdrop Tj=25 o C -- 1.7 -- VPeak Output Current Io peak Tj=25 o C --0.15--A TS79L08 Electrical Characteristics(Vin= -14V, Iout=40mA, 0 o C≤Tj≤125 o C, Cin=0.33uF, Cout=0.1uF; unless otherwise specified.)Parameter Symbol TestConditions MinTypMaxUnitTj=25 o C - 7.69 - 8 - 8.32Output Voltage Vout -10.5V≤Vin≤ -23V,5mA≤Iout≤100mA - 7.61 - 8 - 8.40VLine Regulation REGline Tj=25 o C -10.5V≤Vin≤ -23V,Io=40mA-- 80 160 5mA≤Iout≤100mA -- 25 80Load Regulation REGload Tj=25 o C5mA≤Iout≤40mA -- 10 40mVQuiescent Current Iq Iout=0, Tj=25 o C --36-11V≤Vin≤ -23V -- -- 1.5Quiescent Current Change ∆lq1mA≤Iout≤40mA ----0.1mAOutput Noise Voltage Vn 10Hz≤f≤100KHz, Tj=25 o C -- 60 -- uVRipple Rejection Ratio RR f=120Hz, -13V≤Vin≤ -23V 37 57 -- dBVoltage Drop Vdrop Tj=25 o C -- 1.7 -- VPeak Output Current Io peak Tj=25 o C --0.15--A z Pulse testing techniques are used to maintain the junction temperature as close to the ambient temperature aspossible, and thermal effects must be taken into account separately.z This specification applies only for DC power dissipation permitted by absolute maximum ratings.TS79L09 Electrical Characteristics(Vin= -15V, Iout=40mA, 0 o C≤Tj≤125 o C, Cin=0.33uF, Cout=0.1uF; unless otherwise specified.)Parameter Symbol TestConditions MinTypMaxUnitTj=25 o C - 8.65 - 9 - 9.36Output Voltage Vout -11.5V≤Vin≤ -24V,5mA≤Iout≤100mA - 8.57 - 9 - 9.45VLine Regulation REGline Tj=25 o C -11.5V≤Vin≤ -24V,Io=40mA-- 90 180 5mA≤Iout≤100mA -- 30 90Load Regulation REGload Tj=25 o C5mA≤Iout≤40mA -- 15 45mVQuiescent Current Iq Iout=0, Tj=25 o C --36-12V≤Vin≤ -24V -- -- 1.5Quiescent Current Change ∆lq5mA≤Iout≤40mA ----0.1mAOutput Noise Voltage Vn 10Hz≤f≤100KHz, Tj=25 o C -- 60 -- uVRipple Rejection Ratio RR f=120Hz, -14V≤Vin≤ -24V 37 57 -- dBVoltage Drop Vdrop Tj=25 o C -- 1.7 -- VPeak Output Current Io peak Tj=25 o C --0.15--A TS79L12 Electrical Characteristics(Vin= -19V, Iout=40mA, 0 o C≤Tj≤125 o C, Cin=0.33uF, Cout=0.1uF; unless otherwise specified.)Parameter Symbol TestConditions MinTypMaxUnitTj=25 o C - 11.53- 12 - 12.48Output Voltage Vout -14.5V≤Vin≤ -27V,5mA≤Iout≤100mA - 11.42- 12 - 12.60VLine Regulation REGline Tj=25 o C -14.5V≤Vin≤ -27V,Io=40mA-- 120 240 mV 5mA≤Iout≤100mA -- 40 120Load Regulation REGload Tj=25 o C5mA≤Iout≤40mA -- 20 60Quiescent Current Iq Tj=25 o C, Iout=0 -- 3 6.5-16V≤Vin≤ -27V -- -- 1.5Quiescent Current Change ∆lq5mA≤Iout≤40mA ----0.1mAOutput Noise Voltage Vn 10Hz≤f≤100KHz, Tj=25 o C -- 80 -- uVRipple Rejection Ratio RR f=120Hz, -15V≤Vin≤ -25V 37 42 -- dBVoltage Drop Vdrop Tj=25 o C -- 1.7 -- VPeak Output Current Io peak Tj=25 o C --0.15--A z Pulse testing techniques are used to maintain the junction temperature as close to the ambient temperature aspossible, and thermal effects must be taken into account separately.z This specification applies only for DC power dissipation permitted by absolute maximum ratings.TS79L15 Electrical Characteristics(Vin= -23V, Iout=40mA, 0 o C≤Tj≤125 o C, Cin=0.33uF, Cout=0.1uF; unless otherwise specified.)Parameter Symbol TestConditions MinTypMaxUnitTj=25 o C - 14.42- 15 - 15.60Output Voltage Vout -17.5V≤Vin≤ -30V,5mA≤Iout≤100mA - 14.28- 15 - 15.75VLine Regulation REGline Tj=25 o C -17.5V≤Vin≤ -30V,Io=40mA-- 150 300 mV 5mA≤Iout≤100mA -- 50 150Load Regulation REGload Tj=25 o C5mA≤Iout≤40mA -- 25 75Quiescent Current Iq Tj=25 o C, Iout=0 -- 3 6.5-20V≤Vin≤ -30V -- -- 1.5Quiescent Current Change ∆lq5mA≤Iout≤40mA ----0.1mAOutput Noise Voltage Vn 10Hz≤f≤100KHz, Tj=25 o C -- 90 -- uVRipple Rejection Ratio RR f=120Hz, -18V≤Vin≤ -28V 34 39 -- dBVoltage Drop Vdrop Tj=25 o C -- 1.7 -- VPeak Output Current Io peak Tj=25 o C --0.15--A TS79L18 Electrical Characteristics(Vin= -27V, Iout=40mA, 0 o C≤Tj≤125 o C, Cin=0.33uF, Cout=0.1uF; unless otherwise specified.)Parameter Symbol TestConditions MinTypMaxUnitTj=25 o C - 17.30- 18 - 18.72Output Voltage Vout -21V≤Vin≤- 33V,5mA≤Iout≤100mA - 17.14- 18 - 18.90VLine Regulation REGline Tj=25 o C -21V≤Vin≤ -33V,Io=40mA-- 180 360 mV 5mA≤Iout≤100mA -- 60 180Load Regulation REGload Tj=25 o C5mA≤Iout≤40mA -- 30 90Quiescent Current Iq Tj=25 o C, Iout=0 -- 3 6.5-21V≤Vin≤ -33V -- -- 1.5Quiescent Current Change ∆lq5mA≤Iout≤40mA ----0.1mAOutput Noise Voltage Vn 10Hz≤f≤100KHz, Tj=25 o C --150--uVRipple Rejection Ratio RR f=120Hz, -23V≤Vin≤ -33V 33 48 -- dBVoltage Drop Vdrop Tj=25 o C -- 1.7 -- VPeak Output Current Io peak Tj=25 o C --0.15--A z Pulse testing techniques are used to maintain the junction temperature as close to the ambient temperature aspossible, and thermal effects must be taken into account separately.z This specification applies only for DC power dissipation permitted by absolute maximum ratings.TS79L24 Electrical Characteristics(Vin= -33V, Iout=40mA, 0 o C≤Tj≤125 o C, Cin=0.33uF, Cout=0.1uF; unless otherwise specified.)Parameter Symbol TestConditions MinTypMaxUnitTj=25 o C - 23.07- 24 - 24.96Output Voltage Vout -27V≤Vin≤ -38V,5mA≤Iout≤100mA - 22.85- 24 - 25.20VLine Regulation REGline Tj=25 o C -27V≤Vin≤ -38V,Io=40mA-- 200 400 mV 5mA≤Iout≤100mA -- 80 240Load Regulation REGload Tj=25 o C5mA≤Iout≤40mA -- 40 120Quiescent Current Iq Iout=0, Tj=25 o C --47-28V≤Vin≤ -38V -- -- 1.5Quiescent Current Change ∆lq5mA≤Iout≤40mA ----0.1mAOutput Noise Voltage Vn 10Hz≤f≤100KHz, Tj=25 o C --200--uVRipple Rejection Ratio RR f=120Hz, -29V≤Vin≤ -35V 31 45 -- dBVoltage Drop Vdrop Tj=25 o C -- 1.7 -- VPeak Output Current Io peak Tj=25 o C --0.15--A z Pulse testing techniques are used to maintain the junction temperature as close to the ambient temperature aspossible, and thermal effects must be taken into account separately.z This specification applies only for DC power dissipation permitted by absolute maximum ratings.。
AT88SC102-09AT-xx资料
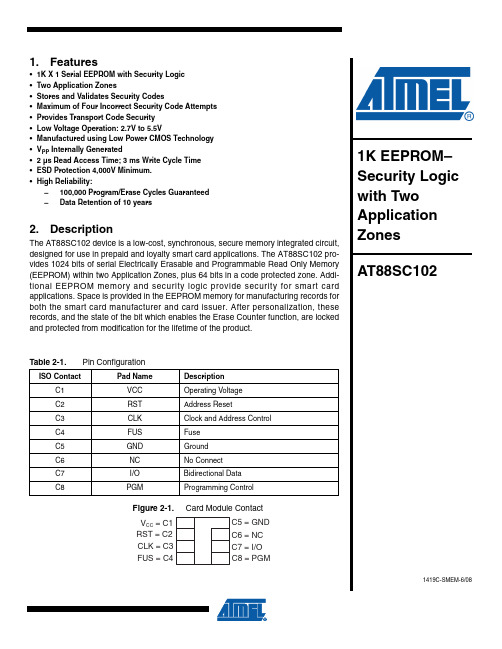
1.Features•1K X 1 Serial EEPROM with Security Logic •Two Application Zones•Stores and Validates Security Codes•Maximum of Four Incorrect Security Code Attempts •Provides Transport Code Security •Low Voltage Operation: 2.7V to 5.5V•Manufactured using Low Power CMOS Technology •V PP Internally Generated• 2 µs Read Access Time; 3 ms Write Cycle Time •ESD Protection 4,000V Minimum.•High Reliability:– 100,000 Program/Erase Cycles Guaranteed – Data Retention of 10 years2.DescriptionThe AT88SC102 device is a low-cost, synchronous, secure memory integrated circuit,designed for use in prepaid and loyalty smart card applications. The AT88SC102 pro-vides 1024 bits of serial Electrically Erasable and Programmable Read Only Memory (EEPROM) within two Application Zones, plus 64 bits in a code protected zone. Addi-tional EEPROM memory and security logic provide security for smart card applications. Space is provided in the EEPROM memory for manufacturing records for both the smart card manufacturer and card issuer. After personalization, these records, and the state of the bit which enables the Erase Counter function, are locked and protected from modification for the lifetime of the product.Figure 2-1.Card Module ContactTable 2-1.Pin ConfigurationISO ContactPad Name Description C1VCC Operating Voltage C2RST Address ResetC3CLK Clock and Address Control C4FUS Fuse C5GND Ground C6NC No Connect C7I/O Bidirectional Data C8PGMProgramming Control1K EEPROM–Security Logic with Two Application Zones AT88SC1021419C-SMEM-6/0821419C–SMEM–6/08AT88SC1023.TerminologyThe following terms have specific definitions for the AT88SC102.3.1EraseErase is a program operation that results in an EEPROM data bit being set to a logic “1” state.Outside the application zones, all erase operations are performed on 16-bit words. An erase operation performed on any bit within a word will execute an erase of the entire word. Inside the application zones, erase operations are controlled by the SV flag, EZ passwords, and EC2EN fuse. These operations are defined in the “Device Operation” section of the data sheet.3.2WriteWrite is a program operation that results in an EEPROM bit or word being set to a logic “0” state.An unwritten bit is defined as erased or set to a logic “1” state. Write operations in the AT88SC102 may be performed on individual bits after security code validation. In Security Level 2, write operations also require that the P1 or P2 bit within the application zone is set to “1”.3.3ProgramProgram is an EEPROM function that activates internally timed, high-voltage circuitry and results in a data bit or word being set to either a logic “0” or “1” state.3.4BitA bit is a single data element set to either a logic “0” or “1” state. All bit addresses within the application zones (AZ1, AZ2) may be written individually.3.5ByteA byte is eight consecutive data bits. A byte boundary will begin on an address that is evenly divisible by eight. The AT88SC102 has no capability for byte write operations.3.6WordA word is sixteen consecutive data bits. A word boundary will begin on an address that is evenly divisible by 16. Erase operations will always operate on 16-bit words when applied to addresses outside the application zones. In Security Level 1, erase operations within the application zones also operate on 16-bit words. In Security Level 2, erase operations within the application zones operate on the entire zone. Write operations function on single bits, not words, in both security levels.3.7BlownIn reference to an AT88SC102 internal EEPROM fuse, the blown state is a logic “0”.3.8UnblownIn reference to an AT88SC102 internal EEPROM fuse, the unblown state is a logic “1”.3.9VerificationAT88SC102 operations are controlled by the state of several internal flags. The flags SV, E1,and E2 are set after verification of an associated password (security code or EZ1 or EZ2 respec-tively). Verification is accomplished by executing an INC/CMP operation, which correctly31419C–SMEM–6/08AT88SC102matches the password bit by bit as the CLK increments the address through the password mem-ory addresses.Figure 3-1.Block DiagramThe AT88SC102 is manufactured using low-power CMOS technology and features its own inter-nal high-voltage pump for single voltage supply operation. The devices are guaranteed to 100,000 erase/write cycles and 10-year data retention. The AT88SC102 supports the ISO/IEC 7816-3 synchronous protocol.4.Security FeaturesThe security features of Atmel’s AT88SC102 include:•Data access only after validation of the security code.•Permanent invalidation of the device after four consecutive false security code presentations.•Read/write protection of certain memory zones.•Secure transport of devices using transport code compare sequence.•Unique customer identification number written and locked into every device for protection against duplication or counterfeiting.4.1Security Levels and Memory Access to AT88SC102Access to the memory is controlled by the state of the issuer fuse and by the voltage supplyapplied on the FUS pad.Table 1.FUS Pad Issuer FuseSecurity LevelLogic “0”X 2Logic “1”11Logic “1”241419C–SMEM–6/08AT88SC1024.1.1Level 1: Security During PersonalizationAT88SC1003 die and modules are delivered with the issuer fuse intact. Issuer personalization is completed at this level. Security code validation is required to allow access to personalize the EEPROM memory. During personalization, the manufacturer fuse may be blown to lock the manufacturer’s zone.See “Memory Access Rules During Personalization” (Table 9-1 on page 10).Conditions:Issuer fuse = “1” (not blown)FUS pin = “1” (required)4.1.2Level 2: Security After PersonalizationEEPROM memory zones are protected by the various flags and passwords. After issuer person-alization, Security Level 2 is implemented by blowing the issuer fuse. The device can also be placed in Security Level 2 by taking the FUS pin low, independent of the state of the issuer fuse.This function of the FUS pin enables the card issuer to simulate Security Level 2 during applica-tion development without permanently blowing the issuer fuse.See “Memory Access Rules After Personalization” (Table 10-1 on page 11).Conditions:Issuer fuse = “0” (blown)FUS pin = “X”orIssuer fuse = “1” (not blown)FUS pin = “0”51419C–SMEM–6/08AT88SC1025.Memory MapTable 5-1.AT88SC102 Memory DiagramBit AddressDescriptionBits Words 0–15Fabrication Zone (FZ) 16116–79Issuer Zone (IZ) 64480–95Security Code (SC)16196–111Security Code Attempts counter (SCAC)161112–175Code Protected Zone (CPZ)644176–687Application Zone 1 (AZ1)51232688–735Application Zone 1 Erase Key (EZ1)483736–1247Application Zone 2 (AZ2)512321248–1279Application Zone 2 Erase Key (EZ2)3221280–1407Application Zone 2 Erase Counter (EC2)12881408–1423Memory T est Zone (MTZ)1611424–1439Manufacturer’s Zone (MFZ)1611440–1455Block Write/Erase1611456–1471MANUFACTURER’S FUSE1611529EC2EN FUSE (Controls use of EC2)11552 - 1567ISSUER FUSE1616.Memory ZonesTable 6-1.Memory ZonesZoneDefinitionFabrication Zone FZ (16 bits)The 16-bit fabrication zone is programmed when the chip is manufactured and cannot be changed. Application software may check this fabrication zone code to assure that the device was manufactured by Atmel.Issuer Zone IZ (64 bits)The 64-bit issuer zone is programmed by the card issuer during the personalization phase. It will contain issuer-specific information, such as serial numbers and dates. This area becomes read-only after the issuer fuse has been blown. Read access is always allowed in the issuer zone.Security Code SC (16 bits)The card security code is initially set by Atmel to protect the card during transportation to the card issuer. During personalization, this code must be verified by the A T88SC102 to allow access to the EEPROM memory. After the security code has been verified, the code itself may be changed in either security mode. While in personalization mode (Security Level 1), the security code gives erase and write access to both the application zones and the code protected zone. In Security Level 2, the security code gives write access to both the application zones and the code protected zone. Erase access requires verification of both the security code and the erase key (EZ1 or EZ2). Verification of the security code will set the internal flag SV to “1”. Atmel ships the device with a security code (transportation code) pre-programmed. This protects against the unauthorized use of an unpersonalized device and should be written to a new value during initialization.61419C–SMEM–6/08AT88SC102Security Code Attempts Counter SCAC (16 bits)The protocol for verification of the security code requires that the user write one of the first four bits of the SCAC to a logic “0”. This allows the SCAC to count the number of consecutive incorrectpresentations of the security code. After four consecutive incorrect security code presentations, the first four bits of the SCAC will all be written to “0”, and the user is permanently blocked from access to the application zones, as well as other areas controlled by the security code. After a successful presentation of the security code, the entire 16-bit SCAC, including the four active bits, should be erased. This verifies that the correct security code has been presented, since an erase operation in this area is not allowed without SC verification. It also clears the SCAC bits in preparation for the next use of the card. This erase operation will also clear the remaining twelve bits of the 16-bit SCAC word. These twelve bits may be used in an application, although the entire 16-bit word will be erased if any bit in the SCAC is erased.Code Protected Zone CPZ (64 bits)Read access to this area is always allowed and does not require SC validation. The security code must be correctly presented to allow write or erase access to the code protected zone.Application Zones 1 and 2AZ1 and AZ2 (512 bits each)The application zones (AZ1 and AZ2) are intended to hold user application data. P1 (address 176) controls write access, and R1 (address 177) controls read access within AZ1. P2 (address 736) controls write access and R2 (address 737) controls read access within AZ2. In Security Level 1, an entire 16-bit word will be erased if an erase is performed on any single bit within that word. In Security Level 2, erase operations are controlled by both the SV flag and the erase keys (EZ1 and EZ2). See the Device Operation ERASE definition for specific details. The number of erase operations performed in AZ2 may be limited by leaving the EC2EN fuse set to “1”. The A T88SC102 allows unlimited erase operations of AZ1.Application Zone Erase Keys EZ1 (48 bits)EZ2 (32 bits)(Enabled in Security Level 2 only) The erase keys are passwords used to control erase operations within the application zones, after the issuer fuse has been blown (Security Level 2). The erase key passwords are written by the issuer during personalization (Security Level 1), after verification of the security code. EZ1 and EZ2 can not be changed after the issuer fuse is blown. In Security Level 2, the A T88SC102 allows only block erasure of an entire application zone. AZ1 can be erased only after both the SC and the EZ1 password have been validated. Verification of EZ1 will set the internal flag E1 to “1”. AZ2 can be erased only after both the SC and the EZ2 password have been validated. Verification of EZ1 will set the internal flag E1 to “1”. Verification of EZ2 will set the internal flag E2 to “1”.Application Zone 2Erase Counter EC2(128 bits)(Enabled in Security Level 2 only) The Application Zone 2 Erase Counter (EC2) is enabled only in Security Mode 2 and only when the EC2EN fuse is set to “1”. If both of these conditions are true, the user will be limited to 128 erase operations in Application Zone 2. EC2 is used to count these erase cycles. The erase protocol for the A T88SC102 Application Zone 2 requires one bit in EC2 to be written to “0”. After 128 erase operations, all 128 bits in EC2 will be “0” and the user will be blocked from erasing AZ2. The erase counter is only writeable and cannot be erased. When the EC2EN fuse = “0”, the EC2 operation is disabled. In that case there is no limit to the number of times AZ2 can be erased, and EC2 has no function.Memory Test Zone MTZ (16 bits)All operations are allowed for this zone (write, erase, read). The purpose of this zone is to provide an area in the product memory which is not restricted by security logic. It is used for testing purposes during the manufacturing process, and may also be used in the product application if desired, although no security protection exists for the MTZ.Manufacturer’s Zone MFZ (16 bits)The MFZ is intended to hold data specific to the smart card manufacturer (like assembly lot codes, dates, etc.). Read operations within this zone are always allowed. Write or erase operations within this zone are allowed after the SC has been verified. After the data is entered by the card manufacturer, the manufacturer’s fuse can be blown and the data within the MFZ will become read-only. Blowing the issuer fuse will also lock the data in the MFZ.6.Memory ZonesTable 6-1.Memory ZonesZoneDefinition71419C–SMEM–6/08AT88SC102EC2EN Fuse (1 bit)This single-bit EEPROM fuse selects whether the EC2 counter is used to limit the number of AZ2 erase operations in Security Mode 2. If the EC2EN fuse is unblown (“1”), the number of eraseoperations allowed in AZ2 is limited to 128. If the EC2EN fuse is blown (“0”), there is no limit to the number of erase operations in AZ2. After the issuer fuse is blown, the state of the EC2EN fuse is locked and cannot be changed.Issuer Fuse (16 bits)This EEPROM fuse is used to change the security mode of the A T88SC102 from Security Mode 1 (“1”) to Security Mode 2 (“0”). Initialization of the A T88SC102 for use by the end customer occurs in Security Mode 1. Access conditions in Security Mode 1 are described in T able 1. Access conditions in Security Mode 2 are described in Table 2.Manufacturer’s Fuse (1 bit)This single-bit EEPROM fuse is used to lock the data stored in the manufacturer’s zone after personalization has been completed.6.Memory ZonesTable 6-1.Memory ZonesZoneDefinition81419C–SMEM–6/08AT88SC1026.1Internal FlagsTable 6-2.Definition of AT88SC102 Internal FlagsZoneDefinitionOperationFunctionSV Security Validation FlagThe SV flag is set by correctly matching the 16-bit security code bit-by-bit from address 80 through 95 as CLK increments the address counter. The security code matching operation must be followedimmediately by a validation operation within the Security Code Attempts Counter (SCAC). Thisvalidation operation requires the user to find a bit in the first eight bits of the SCAC (addresses 96–103) that is a logic “1”. A write operation is performed, followed by an erase. The A T88SC102 will validate that the comparison was correct by outputting a logic “1”, and SV will be set. After the erase, all 16 bits in the SCAC will also be erased. The SV flag remains set until power to the card is turned off. If thecomparison was in error, or part of the validation was not performed correctly, the A T88SC102 will output a logic “0”, showing that the SV flag has not been set. After eight consecutive incorrect security code presentations, the card is permanently locked.This flag is the master protection for the memory zones. See Tables 1 and 2.P1Application Zone 1 Write FlagIf Bit 176 has been programmed to a logic “1”, this flag is set after Bit 176 has been addressed. The flag remains set until power to the device is turned off, even if this bit is written to “0” by a subsequent operation.P1 and SV must both be set in order to enable a write command in the application zone (Security Mode 2).R1Application Zone 1 Read FlagIf Bit 177 has been programmed to a logic “1”, this flag is set after Bit 177 has been addressed. The flag remains set until power to the device is turned off, even if this bit is written to “0” by a subsequent operation.R1 or SV must be set in order to enable Application Zone 1 to be read.P2Application Zone 2 Write FlagIf Bit 736 has been programmed to a logic “1”, this flag is set after Bit 736 has been addressed. The flag remains set until power to the device is turned off, even if this bit is written to “0” by a subsequent operation.P2 and SV must both be set in order to enable a write command in Application Zone 2 (Security Mode 2).R2Application Zone 2 Read FlagIf Bit 737 has been programmed to a logic “1”, this flag is set after Bit 737 has been addressed. The flag remains set until power to the device is turned off, even if this bit is written to “0” by a subsequent operation.R2 or SV must be set in order to enable Application Zone 2 to be read.91419C–SMEM–6/08AT88SC1027.Definition of AT88SC102 PasswordsTable 7-1.Definition of Passwords8.Definition of AT88SC102 Fuses•Manufacturer FuseThis fuse is used to control writes and erases of the Manufacturer Zone (MFZ). When the secu-rity code has been validated and both the issuer fuse and the manufacturer fuse are unblown,writes and erases of the MFZ are allowed. Blowing the issuer fuse will also disable the manufac-turer fuse if it has not been blown previously.E1Application Zone 1 Erase FlagThe E1 flag is set by correctly matching theApplication Zone 1 Erase Key (EZ1) bit by bit as pin CLK increments the address counter. To complete an erase operation of AZ1 in Security Level 2, an erase operation must be performed on Bit 736 after E1 is set. The E1 flag is reset when the address counter = 0.Application Zone 1 (Bits 176–687) will be erased when E1 is set and an erase is performed on Bit 736. This operation erases all bits in Application Zone 1. There is no limit to the number of erase operations that can be performed on AZ1.E2EC EnabledApplication Zone 2 Erase Flag with Erase Counter operation enabled. (EC2EN FUSE = “1”)This flag is set by correctly matching the Application Zone 2 Erase Key (EZ2) bit by bit as pin CLKincrements the address counter. Then a validation operation must be completed. This operationrequires the user to find a bit in Application Zone 2 Erase Counter (EC2), addresses 1280–1407, that is a logic “1”. A write must then be performed, followed by an erase. The A T88SC102 will validate that the comparison was correct and Application Zone 2 will be erased. This flag is also reset when the address counter = 0.Application Zone 2 (Bits 736–1237) is erased when E2 is set and an erase is performed after the validation operation in EC2 described above. This operation erases all bits in Application Zone 2.E2ECDisabledApplication Zone 2 Erase Flag with Erase Counter operation disabled. (EC2EN FUSE = “0”)E2 is set when the Application Zone 2 Erase Key comparison is valid. It is reset when the address counter = 0.Application Zone 2 (bits 736–1247) is erased when E2 is set and an erase is performed on Bit 1280. This operation erases all bits in Application Zone 2 but does not affect the word containing Bit 1280.Table 6-2.Definition of AT88SC102 Internal Flags (Continued)ZoneDefinitionOperationFunctionTable 1.Password DefinitionSecurity Code (SC )Bits 80–95(16 bits)This password is used to set the Security Validation (SV) flag and is used in determining what operations are allowed in each zone (see Tables 1 and 2).Application Zone 1 Erase Key (EZ1)Bits 688–735(48 bits)This password must be programmed during issuer personalization. It is used to eraseApplication Zone 1 in Security Level 2. Verification of EZ1 will set the internal flag E1 to “1”.Application Zone 2 Erase Key (EZ2)Bits 1248–1279(32 bits)This password must be programmed during issuer personalization. It is used to eraseApplication Zone 2 in Security Level 2. Verification of EZ2 will set the internal flag E2 to “1”.101419C–SMEM–6/08AT88SC102•EC2EN FuseThis fuse selects whether the EC2 counter is used to limit the number of Application Zone 2erases allowed in Security Mode 2. If the EC2EN fuse is “unblown”, then the Application Zone 2erases are limited to 128. If the EC2EN fuse is “blown”, the application zone erases are unlim-ited. After the issuer fuse is blown, the state of the EC2EN fuse is locked and cannot be changed.•Issuer FuseThis fuse is used to personalize the AT88SC102 for end use. It is an additional EEPROM bit that can be programmed to a logic “0”. This is its “blown” state. Security of the device when the issuer fuse is a logic “1” is described in Table 1. The device is in Security Level 2 when the issuer fuse is blown. The device can also be placed in Security Level 2 by taking the FUS pin low independent of the state of issuer fuse. Memory access rules of the device in Security Level 2 are described in Table 2.9.Memory Access Rules During Personalization – Security Mode 1(1)Notes:1.Security Mode 1 Conditions:EC2EN = “1” or “0”Issuer Fuse = “1”FUS Pin = “1” (required)2.SV = “1” after validation of the security codeTable 9-1.Access Conditions During Personalization (issuer fuse not blown)Zone SV (2)R1(3)R2(4)MF (5)Read Erase Write CompareFZ x x x x yes no no no IZ 01x x x x x x yes yes no yes no yes no no SC 01x x x x x x no yes no yes no yes yes no SCAC 01x x x x x x yes yes no yes yes yes no no CPZ01x x x x x x yes yes no yes no yes no no AZ100101x x x x x x x no yes yes no no yes no no yes no no no EZ101x x x x x x no yes no yes no yes no no AZ2001x x x 01x x x x no yes yes no no yes no no yes no no no EZ201x x x x x x no yes no yes no yes no no EC201x x x x x x yes yes no yes yes yes no no MTZ x x x x yes yes yes no MFZ 011x x xx x xx 01yes yes yesno no yesno no yesno no no111419C–SMEM–6/08AT88SC1023.R1: 2nd bit of Application Zone 1 (Bit 177)4.R2: 2nd bit of Application Zone 2 (Bit 737)5.MF: Manufacturers Fuse = “0” when blown10.Memory Access Rules After Personalization – Security Mode 2(1)Notes:1.Security Mode 2 Conditions:Manufacturer Fuse = “X”EC2EN Fuse = “1” or “0”Issuer Fuse = “0”FUS Pin = “X”2.SV = “1” after validation of the security code3.P1: 1st bit of Application Zone 1 (Bit 176)4.R1: 2nd bit of Application Zone 1 (Bit 177)5.P2: 1st bit of the Application Zone (Bit 736)6.R2: 2nd bit of the Application Zone 2 (Bit 737)7.E1 = “1” after a valid presentation of the Application Zone 1 Erase Key (EZ1)8.E2 = “1” after a valid presentation of the Application Zone 2 Erase Key (EZ2)Table 10-1.Access Conditions After Personalization (issuer fuse blown)Zone SV (2)P1(3)R1(4)P2(5)R2(6)E1(7)E2(8)Read Erase Write CompareFZ x x x x x x x yes no no no IZ x x x x x x x yes no no no SC 01x x x x x x x x x x x x no no no yes no yes yes no SCAC 01x x x x x x x x x x x x yes yes no yes yes yes no no CPZ01x x x x x x x x x x x x yes yes no yes no yes no no AZ1001111x x 001101x x x x x x x x x x x x x x x x x x 0101x x x x x x no yes yes yes yes yes no no no yes no yes no no no no yes yes no no no no no no EZ1x x x x x x x no no no yes AZ2001111x x x x x x x x x x x x x x 001101x x x x x x x x x x x x 0101no yes yes yes yes yes no no no yes no yes no no no no yes yes no no no no no no EZ2x x x x x x x no no no yes EC2x x x x x x x yes no yes no MTZ x x x x x x x yes yes yes no MFZ xxxxxxxyesnonono121419C–SMEM–6/08AT88SC10211.Micro OperationsThe AT88SC102 circuit operation modes are selected by the input logic levels on the control pins PGM, CLK, and RST and by the internal address. Timing for these operations is specified in the AC Characteristics section.2.The two instructions INC/READ and INC/CMP share the same control signal states.3.The circuit will distinguish between the INC/READ and INC/CMP instructions by testing the internal address counter.(CMP can only be done with the addresses corresponding to the security code or to an erase key).4.The internal address counter counts up to 1567. An additional CLK pulse resets the address to “0”.Table 11-1.Micro Operations131419C–SMEM–6/08AT88SC10212.Device Functional OperationTable 12-1.Device Functional OperationNameFunctional Operation SequencePOROPERA TION:POR (power-on reset) is initiated as the device power supply ramps from 0V up to a valid operating voltage.FUNCTION:POR resets all flags, and the address is reset to “0”.RESETOPERA TION:With CLK low, a falling edge on the RST pin will reset the address counter to address “0”. FUNCTION:The address is reset to “0”, and the first bit of the memory is driven by the A T88SC102 on I/O after a reset. Only E1 and E2 are reset when the address is reset to 0. The Reset operation has no affect on any of the other flags (SV , P1, R1, P2, R2).ADDRESSINGOPERA TION:Addressing is handled by an internal address counter. The address is incremented on the falling edge of CLK. Reset must be low while incrementing the address. A falling edge of reset clears the counter to address “0”.FUNCTION:Addressing of the A T88SC102 is sequential. Specific bit addresses may be reached by completing a reset, then clocking the device (INC/READ) until the desired address is reached. The A T88SC102 will determine which operations are allowed at specific address locations. These operations are specified in Tables 1 and 2.For instance, to address the issuer zone (IZ), execute a reset operation, then clock the device 16 times. The device now outputs the first bit of the IZ. After the address counter counts up to 1567, the next CLK pulse resets the address to “0”.READOPERA TION:RST and PGM pins must be low. If a read operation is allowed, the state of the memory bit being addressed is output on the I/O pin. The I/O buffer is an open drain, and the output of a logic “0” therefore causes the device to pull the pin to ground. The output of a logic “1” causes the device to place the pin in a high impedance state. So to sense a logic “1”, an external pull-up must be placed between the I/O pin and VCC. The address counter is incremented on the falling edge of CLK.FUNCTION:Non-application Zones:As the address counter is incremented, the contents of the memory are read out on the I/O pin. The read operation is inhibited for addresses where security prevents a read operation (see Tables 1 and 2).Application Zones:Application Zone 1 can be read when: SV = “1” or R1 = “1”.Application Zone 2 can be read when: SV = “1” or R2 = “1”.141419C–SMEM–6/08AT88SC102WRITEA WRITE operation sets the bit(s) to a logic “0”OPERA TION:CLK = “0”PGM “0” → “1” (I/O switches to an input) I/O = “0” (input = “0” for write operation)CLK “0”→ “1” (rising edge of CLK starts the write operation)PGM “1”→ “0”I/O “0”→ “Z” (high-impedance)Wait t CHP (see “AC Electrical Characteristics”)CLK “1”→ “0” (falling edge of CLK ends the WRITE operation)Note: The falling edge of CLK that ends the write operation does not increment the address counter.FUNCTION:Non-application Zones:The write operation is inhibited for addresses where security prevents a write operation (see Tables 1 and 2).Application Zones:The Application Zones can be written when:Security Level 1: SV = “1”Security Level 2: SV = “1”and P1 = “1” for AZ1. SV = “1” and P2 = “1” for AZ2ERASE Operation SequenceCLK = “0”PGM “0” → “1” (I/O switches to an input) I/O = “1” (input = “1” for erase operation)CLK “0” → “1” (rising edge of CLK starts the erase operation) PGM “1” → “0”I/O “1” → “Z” (high-impedance)Wait t CHP (see “AC Electrical Characteristics”)CLK “1” → “0” (falling edge of CLK ends the erase operation)Note: The falling edge of CLK that ends the erase operation does not increment the address counter.ERASE (Non-Application Zones)An erase operation sets the bits to logic “1”. The EEPROM memory is organized into 16 bit words. Although erases are performed on single bits, the erase operation clears an entire word in the memory (except for the application zones in Security Level 2). Therefore, performing an erase on any bit in the word will clear all 16 bits of that word to logic “1”. OPERA TION:Perform “Erase Operation Sequence” as specified above.FUNCTION:The erase operation is inhibited for addresses where security prevents an erase operation (see Tables 1 and 2.)ERASE (Application Zones)Security Level 1Security level 1: (Issuer Fuse = “1” and FUS pin = “0”)The Application Zone can only be erased when SV = “1”.OPERA TION:Increment address counter to any bit within AZ1 or AZ2. Perform “Erase Operation Sequence” as specified above.FUNCTION:This operation will erase the entire 16-bit word containing the bit.Table 12-1.Device Functional Operation (Continued)NameFunctional Operation Sequence。
AT24C01资料的中文翻译
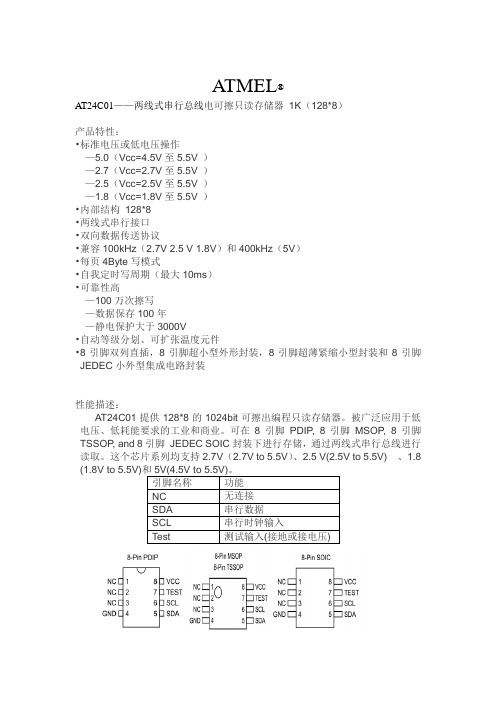
ATMEL®AT24C01——两线式串行总线电可擦只读存储器1K(128*8)产品特性:•标准电压或低电压操作—5.0(Vcc=4.5V至5.5V )—2.7(Vcc=2.7V至5.5V )—2.5(Vcc=2.5V至5.5V )—1.8(Vcc=1.8V至5.5V )•内部结构128*8•两线式串行接口•双向数据传送协议•兼容100kHz(2.7V 2.5 V 1.8V)和400kHz(5V)•每页4Byte写模式•自我定时写周期(最大10ms)•可靠性高—100万次擦写—数据保存100年—静电保护大于3000V•自动等级分划、可扩张温度元件•8引脚双列直插,8引脚超小型外形封装,8引脚超薄紧缩小型封装和8引脚JEDEC小外型集成电路封装性能描述:AT24C01提供128*8的1024bit可擦出编程只读存储器。
被广泛应用于低电压、低耗能要求的工业和商业。
可在8引脚PDIP, 8引脚MSOP, 8引脚TSSOP, and 8引脚JEDEC SOIC封装下进行存储,通过两线式串行总线进行读取。
这个芯片系列均支持2.7V(2.7V to 5.5V)、2.5 V(2.5V to 5.5V) 、1.8 (1.8V to 5.5V)和5V(4.5V to 5.5V)。
引脚名称功能NC 无连接SDA 串行数据SCL 串行时钟输入Test 测试输入(接地或接电压)绝对最大功率:运行温度…………-55°至+125°存储温度…………-65°至+150°引脚承受最高电压…………-1V至+7V运行最大电压…………6.25V直流最大电流…………5.0mA*注意:超过上述参数工作会损坏本元件,这是唯一的功能操作参数,超过此功率将不被支持。
按照额定功率工作将使元件更加可靠。
模块图引脚描述:SERIAL CLOCK (SCL):SCL引脚在电压上升沿时输入数据,下降沿时输出数据SERIAL DATA (SDA):SDA引脚用作双向传送数据,高电平驱动可能与其它任何引脚或元件进行线或运算。
AT89C51单片机简介

AT89C51单片机简介at89c51单片机简介2021/05/2503:35at89c51单片机简介AT89C51是一种具有4K字节的闪存可编程可擦除只读存储器(fperom―falshprogrammableanderasablereadonlymemory)的低电压,高性能cmos8位微处理器,俗称单片机。
at89c2051是一种带2k字节闪烁可编程可擦除只读存储器的单片机。
单片机的可擦除只读存储器可以反复擦除100次。
该器件采用atmel高密度非易失存储器制造技术制造,与工业标准的mcs-51指令集和输出管脚相兼容。
由于将多功能8位cpu和闪烁存储器组合在单个芯片中,atmel的at89c51是一种高效微控制器,at89c2051是它的一种精简版本。
at89c单片机为很多嵌入式控制系统提供了一种灵活性高且价廉的方案。
图片见下图:要查看轮廓图和大图,请单击此处1.主要特性:与MCS-51兼容4k字节可编程闪烁存储器寿命:1000写/擦循环数据保留时间:10年全静态工作:0hz-24hz三级程序存储器锁定128*8位内部ram32可编程i/o线两个16位定时器/计数器5个中断源可编程串行通道低功耗的闲置和掉电模式片上振荡器和时钟电路2.管脚说明:VCC:电源电压。
接地:接地。
p0口:p0口为一个8位漏级开路双向i/o口,每脚可吸收8ttl门电流。
当p1口的管脚第一次写1时,被定义为高阻输入。
p0能够用于外部程序数据存储器,它可以被定义为数据/地址的第八位。
在fiash编程时,p0口作为原码输入口,当fiash进行校验时,p0输出原码,此时p0外部必须被拉高。
端口P1:端口P1是一个具有内部上拉电阻的8位双向I/O端口。
端口P1的缓冲器可以接收输出的4ttl栅极电流。
P1端口的引脚写入1后,它在内部被拉高,可以用作输入。
P1端口被外部拉低至低电平,并将输出电流,这是由于内部上拉。
在闪存编程和验证期间,P1端口作为第八位地址接收。
- 1、下载文档前请自行甄别文档内容的完整性,平台不提供额外的编辑、内容补充、找答案等附加服务。
- 2、"仅部分预览"的文档,不可在线预览部分如存在完整性等问题,可反馈申请退款(可完整预览的文档不适用该条件!)。
- 3、如文档侵犯您的权益,请联系客服反馈,我们会尽快为您处理(人工客服工作时间:9:00-18:30)。
Features Array•Supports Four 10/100/1000 Mbps Ethernet Ports with GMII/MII Interface
•IEEE 802.3ab CSMA/CD Compliant
•Full and Half Duplex Mode of Operation
•Speed and Duplex Mode Auto-negotiation Through MDIO
•Self-address Learning Mechanism Supports 512-MAC Addresses
•Automatic Address Aging with 300 seconds Default
•512-kbit Packet Buffer Memory Embedded
•Serial Port Interface Employed to Communicate with MCU
•IEEE 802.3ab Flow Control for Full Duplex Operation
•Supports Store-and-Forward Mode of Operation
•0.18 Micron, 1.8V CMOS Technology Packaged in 160-pin PQFP
• 3.3V I/O
•Available in a Variety of Packages Depending on Customer Requirements
Description
This Layer 2 Switch provides an ideal solution for the design of unmanaged full wire-
speed multi-port Gigabit Ethernet (GbE) switches. Each port supports either
10/100/1000Mbps data rate. Flow controls, back pressure in half-duplex mode and
PAUSE frame in full-duplex mode are employed to solve the HOL (Head of Line)
blocking.
This Layer 2 Switch integrates four half/full duplex mode 1000BASE Gigabit Ethernet
MACs, wire speed switching engines, MAC address based address parsing algorithms
and packet buffer memory.
Figure 1. Ethernet Level 2 Switch Block Diagram
is available under NDA. For more information, please con-
tact your local Atmel sales office.
Disclaimer: Atmel Corporation makes no warranty for the use of its products, other than those expressly contained in the Company’s standard warranty which is detailed in Atmel’s Terms and Conditions located on the Company’s web site. The Company assumes no responsibility for any errors which may appear in this document, reserves the right to change devices or specifications detailed herein at any time without notice, and does not make any commitment to update the information contained herein. No licenses to patents or other intellectual property of Atmel are granted by the Company in connection with the sale of Atmel products, expressly or by implication. Atmel’s products are not authorized for use as critical components in life support devices or systems.
Atmel Corporation
Atmel Operations
2325 Orchard Parkway San Jose, CA 95131, USA Tel: 1(408) 441-0311Fax: 1(408) 487-2600
Regional Headquarters
Europe
Atmel Sarl
Route des Arsenaux 41Case Postale 80CH-1705 Fribourg Switzerland
Tel: (41) 26-426-5555Fax: (41) 26-426-5500
Asia
Room 1219
Chinachem Golden Plaza 77 Mody Road Tsimshatsui East Kowloon Hong Kong
Tel: (852) 2721-9778Fax: (852) 2722-1369
Japan
9F, Tonetsu Shinkawa Bldg.1-24-8 Shinkawa
Chuo-ku, Tokyo 104-0033Japan
Tel: (81) 3-3523-3551Fax: (81) 3-3523-7581
Memory
2325 Orchard Parkway San Jose, CA 95131, USA Tel: 1(408) 441-0311Fax: 1(408) 436-4314
Microcontrollers
2325 Orchard Parkway San Jose, CA 95131, USA Tel: 1(408) 441-0311Fax: 1(408) 436-4314
La Chantrerie BP 70602
44306 Nantes Cedex 3, France Tel: (33) 2-40-18-18-18Fax: (33) 2-40-18-19-60
ASIC/ASSP/Smart Cards
Zone Industrielle
13106 Rousset Cedex, France Tel: (33) 4-42-53-60-00Fax: (33) 4-42-53-60-01
1150 East Cheyenne Mtn. Blvd.Colorado Springs, CO 80906, USA Tel: 1(719) 576-3300Fax: 1(719) 540-1759
Scottish Enterprise Technology Park Maxwell Building
East Kilbride G75 0QR, Scotland Tel: (44) 1355-803-000Fax: (44) 1355-242-743
RF/Automotive
Theresienstrasse 2Postfach 3535
74025 Heilbronn, Germany Tel: (49) 71-31-67-0
Fax: (49) 71-31-67-2340
1150 East Cheyenne Mtn. Blvd.Colorado Springs, CO 80906, USA Tel: 1(719) 576-3300Fax: 1(719) 540-1759
Biometrics/Imaging/Hi-Rel MPU/High Speed Converters/RF Datacom
Avenue de Rochepleine BP 123
38521 Saint-Egreve Cedex, France Tel: (33) 4-76-58-30-00Fax: (33) 4-76-58-34-80
Literature Requests
/literature
3434BS–NETST–3/04
© Atmel Corporation 2004. All rights reserved. Atmel ® and combinations thereof, are the registered trademarks of Atmel Corporation or its subsidiaries. Other terms and product names may be the trademarks of others.。