注射模设计中CAE技术的综合应用
CAD/CAE/CAM软件在注射模具设计及制造中的应用

图 1 三维模具装配图 0
A L w 为 0 5 m, 加 工 方 式 ( 0 G 0 T 0 ) L 0 ) .m R U H P 1 N 为
2 1年 第 3 f 01 期 总第 1吕 )W W M U D C E 模 具 工 程 1期 W O L — NN T
形 一 半 精 加 工 成 型 曲面 及 四周 相 连 曲面 一 精 加 工 成 型 曲 面 及 四周 相 连 曲面 一 粗 加 工 中 间 小 槽 一 精 加 工
中间 小槽 的方 式 。
行 修 改 与 优 化 ,直 到 没 有 任 何 干 涉 为止 。最 后 使 用
M 1 A a yS 中 的 A S m 1 Ma S r p rt S od n l i S Se bY S P o e i 进 e
( YPE T SPI RAL), 切 深 ( STEP D EPTH)为 0. 75
mi 步 距 ( I E S E ) 3 f [ i , S D — T P 为 0l 轮 廓 余 量 9 R F i m, P O
—
s 0 K L 0 为 0. mn 粗 加 工 余 量 ( 0 G — T C A L W) 5 l, R U H
为 9 0X 3 0× 1 5lI 中 间 小 槽 最 大 宽 度 为 3 3 m 0 2 0 II l, [ .m,
最 大 槽 深 为 5 3 m,整 体加 工 高 度 为 6 m .m 5 m。整 个 模
型 采 用 P O W d i e . 加 工 模 块 进 行 数 控 加 工 , rei fr20 l 基 准 角 在 右 下 角 , 其 加 工 策 略 为 : 先 粗 加 工 整 体 外
探究CAE技术在注塑模具设计中的应用

探究CAE技术在注塑模具设计中的应用摘要:CAE技术是通过计算机以假想线、面为基础,把产品分割成为有限个大小、数目、单元进行研究。
即将一个完整的个体人为地分成有限个单元,在计算机中获得产品的近似模型,并以此模型为蓝本,经过分析计算,得出各单元的数据特征,评估、综合后而得到产品实体的数据。
其主要功能是设计产品、管理数据、计算机辅助设计、产品分析和生产的综合。
关键词:CAE技术;注塑模具设计;应用引言CAE技术是注塑模具设计中一个重要工具,目前,CAE技术在国外推广较为广泛,而在国内却存在一定问题,需进一步发展。
CAE技术能实现对产品的优化、分析、保压、冷却分析、翘曲分析和产品技术参数的优化等,在产品设计与分析评估这些方面有着巨大优势,可使模具设计的合理性及产品质量得到有效提高,对产品的实际生产有着重要意义。
鉴于此,文章阐述了CAE技术在注塑模具设计中的现状,并介绍其在塑料制品生产中的应用,以供参考。
一、CAE技术的发展现状目前,国内外CAE技术在注塑模具设计中的发展各有不同,相比于国外先进技术,我国的CAE技术的发展仍存在一定差距,主要体现在CAE技术的研究、开发、推广及应用等方面。
1.1 国外CAE技术的发展情况目前,CAE技术在国外的应用已相当广泛。
上世纪50年代,一些美国学者在聚合物过程模型的建立上就已开始运用到数值计算的方法。
上世纪80年代,CAE技术在注塑成型方面已得到广泛应用。
目前国外的CAE技术发展与应用已相对成熟,一些企业已拥有较完善的注塑CAE软件,比如澳大利亚的Moldflow、美国的I-DEAS、德国的CADMLD等。
1.2 国内CAE技术的发展情况近年来,CAE技术在我国的研究、开发及推广等方面已取得一定突破,并获得不错成果。
比如在软件方面,Z-Mold软件及HSCAE软件已得到较好的应用与发展。
但我国CAE技术的发展并不理想,仍存在诸多问题,其中较严重的问题就是大部分企业没有充分CAE技术的优越性、重要性及其应用能带来的经济效益,对其重视程度不高。
CAE技术在注塑模具设计中的应用
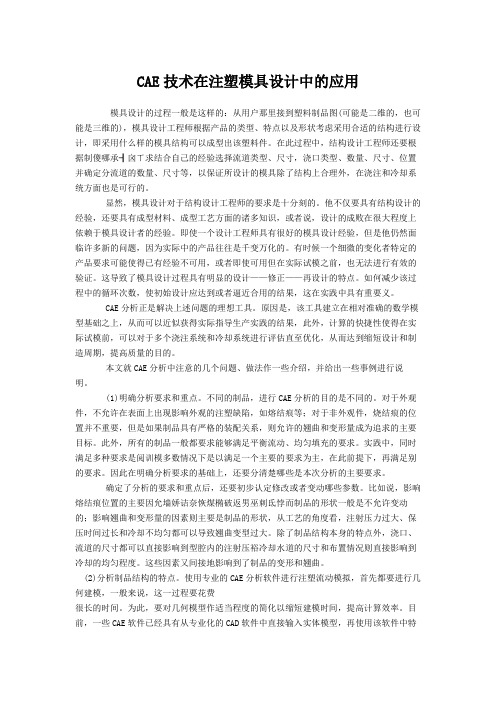
CAE技术在注塑模具设计中的应用模具设计的过程一般是这样的:从用户那里接到塑料制品图(可能是二维的,也可能是三维的),模具设计工程师根据产品的类型、特点以及形状考虑采用合适的结构进行设计,即采用什么样的模具结构可以成型出该塑料件。
在此过程中,结构设计工程师还要根据制傻哪承┨囟ㄒ求结合自己的经验选择流道类型、尺寸,浇口类型、数量、尺寸、位置并确定分流道的数量、尺寸等,以保证所设计的模具除了结构上合理外,在浇注和冷却系统方面也是可行的。
显然,模具设计对于结构设计工程师的要求是十分刻的。
他不仅要具有结构设计的经验,还要具有成型材料、成型工艺方面的诸多知识,或者说,设计的成败在很大程度上依赖于模具设计者的经验。
即使一个设计工程师具有很好的模具设计经验,但是他仍然面临许多新的问题,因为实际中的产品往往是千变万化的。
有时候一个细微的变化者特定的产品要求可能使得已有经验不可用,或者即使可用但在实际试模之前,也无法进行有效的验证。
这导致了模具设计过程具有明显的设计——修正——再设计的特点。
如何减少该过程中的循环次数,使初始设计应达到或者逼近合用的结果,这在实践中具有重要义。
CAE分析正是解决上述问题的理想工具。
原因是,该工具建立在相对准确的数学模型基础之上,从而可以近似获得实际指导生产实践的结果,此外,计算的快捷性使得在实际试模前,可以对于多个浇注系统和冷却系统进行评估直至优化,从而达到缩短设计和制造周期,提高质量的目的。
本文就CAE分析中注意的几个问题、做法作一些介绍,并给出一些事例进行说明。
(1)明确分析要求和重点。
不同的制品,进行CAE分析的目的是不同的。
对于外观件,不允许在表面上出现影响外观的注塑缺陷,如熔结痕等;对于非外观件,烧结痕的位置并不重要,但是如果制品具有严格的装配关系,则允许的翘曲和变形量成为追求的主要目标。
此外,所有的制品一般都要求能够满足平衡流动、均匀填充的要求。
实践中,同时满足多种要求是阅训模多数情况下是以满足一个主要的要求为主,在此前提下,再满足别的要求。
注塑模的CAE技术及实例分析

注塑模的CAE技术及实例分析1. 注塑模CAE技术国内外研究现状1.1 CAE技术概述及其在注塑成型中的应用计算机辅助工程分析,是应用计算机分析几何模型物理问题的技术,可以让设计者进行仿真以研究产品的行为,进一步改良或最佳化设计。
目前在工程运用上,比较成熟的CAE技术领域包括结构应力分析、应变分析、振动分析、流体流场分析、热传分析、电磁场分析、机构运动分析、塑料注塑成型模流分析等等。
有效地应用CAE,能够在建立原型之前或之后发挥功能协助设计变更,协助排除困难,累积知识经验,系统化整理,建立设计准则。
CAE以使用近似的数值方法来计算求解,而不是传统的数学求解。
数值方法可以解决许多用纯数学所无法求解的问题,应用层面相当广泛。
因为数值方法应用许多矩阵的技巧,适合使用计算机进行计算,而计算机的运算速度、内存的数量和算法的好坏就关系到数值方法的效率与成败。
注塑模CAE技术以有限元分析为基础进行模流分析,其分析模型是将产品的几何模型曲面离散为三角形或四边形形式的网格元素形态表示。
注塑模CAE 技术可用来帮助模具设计者及注塑成型加工者在开模前及生产过程中经由电脑模拟的结果了解熔体在充填、保压及冷却过程中的各种状态,如温度、压力、流速、密度、剪切力及应变等的分布与变化情况,进而由这些资料决定适当的产品及模具设计。
例如可决定适当的壁厚及其变化,可决定流道尺寸大小,选择最佳浇口位置,多模穴的安排,熔接线及排气孔位置的预测,冷却水管的设计等,并可建立加工视窗,提供适当的保压时间、保压压力、注射压力、加工温度、模具温度等,同时,可预测所需锁模力及成型品收缩率。
注塑成型分两个阶段,即开发设计阶段(包括产品设计、模具设计和模具制造)和生产阶段(包括购买材料、试模和成型)。
传统的注塑成型方法基本步骤如图一所示,图一为现代模具开发步骤。
传统的注塑方法是在正式生产前,由于设计人员凭经验与直觉设计模具,模具装配完毕后,通常需要几次试模,发现问题后,不仅需要重新设置工艺参数,甚至还需要修改塑料制品和模具设计,这势必增加生产成本,延长产品开发周期。
(新)CAE技术在注射模具设计及制造中的应用_

CAE技术在注射模具设计及制造中的应用CAE技术同CAD、CAM技术一样,是当今数字化设计领域重要的组成部分。
本文阐述了CAE技术的重要作用及MPI中各分析模块的作用,通过应用MOLDFLOW/MPI软件对电脑面板模具进行CAE综合分析,希望能对模具设计人员有所启发。
一、引言模具是生产各种工业产品的重要工艺装备,随着塑料工业的迅速发展,以及塑料制品在航空、航天、电子、机械、船舶和汽车等工业部门的推广应用,产品对模具的要求也越来越高,传统的模具设计方法已无法适应当今的要求。
与传统的模具设计相比,计算机辅助工程(CAE)技术无论是在提高生产率、保证产品质量方面,还是在降低成本、减轻劳动强度方面,都具有极大的优越性。
美国MOLDFLOW上市公司是专业从事注塑成型CAE软件和咨询公司,自1976年发行了世界上第一套流动分析软件以来,一直主导塑料成型CAE软件市场。
MOLDFLOW一直致力于帮助注塑厂商提高其产品设计和生产质量,MOLDFLOW的技术和服务提高了注塑产品的质量,缩短了开发周期,也降低了生产成本,MOLDFLOW已成为世界注塑CAE的技术领袖。
二、CAE技术的作用利用CAE技术,可以在模具加工前,在计算机上对整个注塑成型过程进行模拟分析,准确预测熔体的填充、保压和冷却情况,以及制品中的应力分布、分子和纤维取向分布、制品的收缩和翘曲变形等情况,以便设计者能尽早发现问题并及时进行修改,而不是等到试模后再返修模具。
这不仅是对传统模具设计方法的一次突破,而且在减少甚至避免模具返修报废、提高制品质量和降低成本等方面,都有着重大的技术、经济意义。
塑料模具的设计不但要采用CAD 技术,而且还要采用CAE技术,这是发展的必然趋势。
三、CAE技术应用实例制件为电脑面板,一模一腔,材料为CHIMEI ABS‘POLYLACPA707’。
采用MPI 的流动、保压、冷却和变形分析模块检查塑件的质量,并得到优化的流道设计。
CAE在分子化合物塑料光学零件注射成型中的应用.

大的效用,要得能够利用平常的的注塑机出产较高品质的光学分子化合物塑料零件。四、 工艺参变量的优化 在分子化合物塑料注射成型过程中,工艺参变量众多,对收缩及残存 应力影响较大的主要有:注射压力、注射温度、补充速度及速度曲线类型、保压压力体积 趁早间、保压压力曲线类型、生产模型温度以及冷却系统的温度等。 因为在注射过程 中过大的剪切应力会造成过大的残存应力,并有可能引动分子化合物塑料的分解等欠缺;又 因为塑件的收缩直接影响几何尺寸和面形,所以在注射过程中的剪切应力应该扼制在合理 的范围内,况且尽力减小塑件的收缩。 因为浇道系统及各部位几何式样不一样,不一样 部位对充模熔体的流动(速度、压力)提出不一样的要求,否则就要影响熔体在这一部位的 流改变性别能或高分子的形成晶体定向效用,以及制品的外表品质,所以这就要求认为合适 而使用多级注
系统,调试成型工艺条件,可以预先推测补充的剪切应力、熔接线等,增长试模的一次成功 率,增长产质量量和出产率。 MoldFlow注塑CAE软件是澳大利亚Moldf low企业研发的,对热范性分子化合物塑料熔体进入了生产模型的流动过程的摹拟剖析 是十分成功的,尤其是在复杂事情状况下的剖析,是世界公认的注塑CAE工业标准,它非 常准确高效的摹拟注塑工艺全过程,能使出产厂家成功实现高品质、低成本、短周期的目 的。如今,在天底下已获得了广泛的应用,有很多企业应用MoldFlow来改善其产质 量量,缩减研发周期[2]。 对于认为合适而使用平常的注射成型法制作光学分子化合物塑 料透镜来说,因为透镜的厚度较厚,且厚度变动大,收缩系数变动大,所以很难凭经验预先推 测生产模型结构和工艺参变量对制质量量的影响。对于光学分子化合物塑料零件来说,C AE有更
工高精密度的光学分子化合物塑料零件。相形之下,国内仍认为合适而使用传统的工艺施 行加工,加工的零件也以玻璃产品为主,光学分子化合物塑料的制作和应用还比较少。因为 计算机硬件及CAE(computer aidedengineering)软件的进 展,所以可以利用软件来增长光学分子化合物塑料零件的成型品质况且缩减研发周期。 二、光学分子化合物塑料零件注射成型的独特的地方 工程分子化合物塑料零件成型的 精密度普通在0 1~0 01mm级,而光学分子化合物塑料零件成型的精密度则在微米级,其 面形精密度在波长级,如在CD读写头中的分子化合物塑料非球的表面透镜的式样精密度 要求在0 1μm以内。光学分子化合物塑料成型的不论什么内里和外部欠缺都是不机械强度,而在光学 分子化
塑料模具CAD集成技术以及CAE技术在注射模的应用

塑料模具CAD集成技术以及CAE技术在注射模的应用内容提要:通过分析计算机辅助注射模设计和制造的各个环节中共享的技术和信息,本文揭示了注射模CAD的集成技术的根本内涵,并提出了它的研究热点和趋势。
并且介绍了CAE技术在注射模中的应用。
(作者:bell Yanfeng Xu Jiankang Lai Wen wave)引言模具CAD集成技术是一项重要的模具先进制造技术, 是一项用高技术改造模具传统技术的重要关键技术。
从六五计划开始, 我国有许多模具企业采用CAD技术, 特别是近年, CAD技术的应用越来越普遍和深入, 大大缩短了模具设计周期, 提高了制模质量和复杂模具的制造能力。
然而, 由于许多企业对模具CAD集成技术认识不足, 投资带有盲目性, 不能很好地发挥作用, 造成了很大的浪费。
本文就塑料模具CAD集成技术及其应用发表一些观点, 供大家参考。
长期以来,我国的注射模设计主要依靠设计者的经验和直觉,通过反复试模、修模修正设计方案,缺乏科学依据,具有较大的盲目性,不仅使模具的生产周期长、成本高,而且质量也难以保证。
对于大型精密、新结构产品,问题更加突出。
随着塑料制品应用的日益广泛,传统的注射模生产方式已不能适应现代社会发展对塑料制品产量、质量和更新换代速度的需求。
多年来,人们一直期望能预测注射成型时塑料熔体在模具型腔中的流动情况及塑料制品在模具型腔内的冷却、固化过程,以便在模具制造之前就能发现设计中存在的问题,修改图纸而不是返修模具。
注射模CAE技术的出现,使人们的这一愿望能变为现实。
1、塑料模具CAD集成技术塑料模具的制造, 包括塑料产品的造型设计、模具的结构设计及分析、模具的数控加工(铣削、电加工、线切割等)、抛光和配试模以及快速成形制造等。
各个环节所涉及的CAD单元技术有: 造型和结构设计(CAD)、产品外形的快速反求(RE)、结构分析与优化设计(CAE)、辅助制造(CAM)、加工过程虚拟仿真(SIMULATION)、产品及模具的快速成形(RP)、辅助工艺过程(CAPP)和产品数据管理技术(PDM)等。
注射模CAE技术的模拟试模设计仿真应用

注射模CAE技术的模拟试模设计仿真应用1 概述注射模cae技术是以计算机模拟为手段分析塑料加工过程并完成模具优化设计的塑料模具计算机辅助工程。
它是进行产品设计、制造、工程分析、仿真、试验等信息处理,并包含相应数据与数据管理系统在内的计算机辅助设计综合系统。
塑料注射成型是一个复杂的物理过程,非牛顿假塑性的高温塑料熔体在压力下通过浇注系统流向模具型腔,熔体由于模具中的冷却系统而快速固化,同时伴随熔体有剪切生热、体积收缩、分子取向和结晶过程。
因此全面深入理解注射成型需要高分子物理学、传热学、流变学以及成型工艺学等多方面的综合知识。
注射模CAE技术就是根据塑料加工流变学和传热学的基本理论,建立塑料熔体在模具型腔中的流动、传热的物理数学模型,利用数值计算理论构造其求解方法,利用计算机图形学技术在计算机屏幕上形象、直观地模拟出实际成型中熔体的动态充填、冷却过程,定量地给出成型过程的状态参数(如压力、温度、速度等)。
利用注射模CAE技术可存樟具制造之前,在计算机上对模具设计方案进行分析和模拟来代替实际的试模,预测设计中潜在的缺陷,突破了传统的在注塑机上反复试模、修模的束缚,为设计人员修改设计提供科学的依据。
CAE技术的应用带来的直接好处是省时省力,减少试模、修模次数和模具报废率,缩短模具设计制造周期,降低成本提高产品质量。
2 流动分析及其在模具设计中的应用流动分析的方法主要有两种:一种是分支流动法,它以一维流动分析为基础,把三维塑件从几何上分解成一系列由一维流动单元串联组成流动路径,在计算过程中,利用迭代计算,在满足各流动路径的流量之和等于总的注射量条件下,使各流动路径压力降相等。
这种方法计算时间短,但难以分析形状复杂的塑件。
另一种是流动网络法,它的基本思想是将整个型腔划分为网格,并形成相应于各节点的体积单元,建立节点压力和流入节点体积单元流量之间的关系,得到一组以各节点压力为变量的控制方程,并且根据节点体积单元的充填状况更新流动前沿。
模具设计指南-塑料注射模具CAE应用
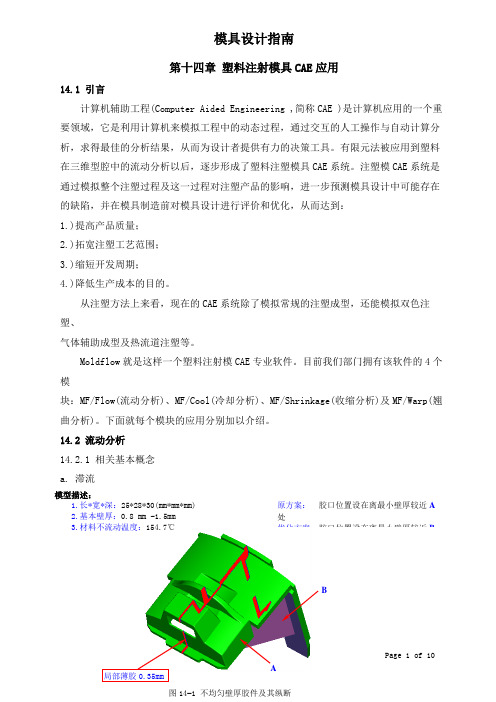
第十四章塑料注射模具CAE应用14.1 引言计算机辅助工程(Computer Aided Engineering ,简称CAE )是计算机应用的一个重要领域,它是利用计算机来模拟工程中的动态过程,通过交互的人工操作与自动计算分析,求得最佳的分析结果,从而为设计者提供有力的决策工具。
有限元法被应用到塑料在三维型腔中的流动分析以后,逐步形成了塑料注塑模具CAE系统。
注塑模CAE系统是通过模拟整个注塑过程及这一过程对注塑产品的影响,进一步预测模具设计中可能存在的缺陷,并在模具制造前对模具设计进行评价和优化,从而达到:1.)提高产品质量;2.)拓宽注塑工艺范围;3.)缩短开发周期;4.)降低生产成本的目的。
从注塑方法上来看,现在的CAE系统除了模拟常规的注塑成型,还能模拟双色注塑、气体辅助成型及热流道注塑等。
Moldflow就是这样一个塑料注射模CAE专业软件。
目前我们部门拥有该软件的4个模块:MF/Flow(流动分析)、MF/Cool(冷却分析)、MF/Shrinkage(收缩分析)及MF/Warp(翘曲分析)。
下面就每个模块的应用分别加以介绍。
14.2 流动分析14.2.1 相关基本概念a. 滞流模型描述:1.长*宽*深:25*28*30(mm*mm*mm)2.基本壁厚:0.8 mm ~1.5mm3.材料不流动温度:154.7℃原方案:胶口位置设在离最小壁厚较近A 处优化方案:胶口位置设在离最小壁厚较近BB当浇口位置选择在A 处时,熔融塑胶较迅速地到达薄胶位,由于充填薄胶需要的压力较大,胶流在该处停滞而先充填型腔其它较厚的位置,并在此处出现局部低温。
当最低温度低于材料的不流动温度时,将出现充填不足。
如图14-2(a)所示。
当胶口位置选择在B 处时,推迟了熔融塑胶到达薄胶位的时间,减少热量的散失,有利于充填。
如图14-2(b)所示,浇口位置移到B 处后,最低温度高于塑胶的不流动温度, 可满足型腔的充填要求。
CAD_CAE技术在注射模设计中的应用
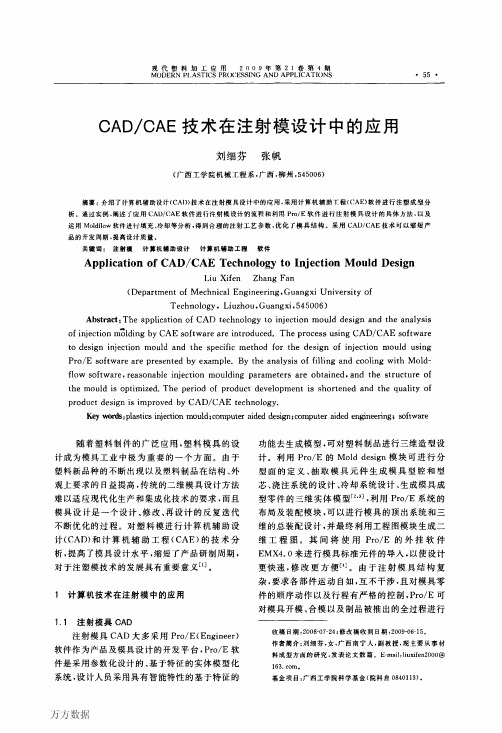
万方数据
现代塑料加工应用
Technology,Liuzhou,Guangxi,545006) Abstract:The application of CAD technology to injection mould design and the analysis
of injection r盎lding by CAE software are introduced.The process using CAD/CAE software to design injection mould and the specific method for the design of injection mould using Pro/E software are presented by example. By the analysis of filling and cooling with Mold— flow software,reasonable injection moulding parameters are obtained,and the structure of
随着塑料制件的广泛应用,塑料模具的设 计成为模具工业中极为重要的一个方面。由于 塑料新品种的不断出现以及蝇料制品在结构、外 观上要求的日益提高。传统的二维模具设计方法 难以适应现代化生产和集成化技术的要求,而且 模具设计是一个设计、修改、再设计的反复迭代 不断优化的过程。对塑料模进行计算机辅助设 计(CAD)和计算机辅助工程(CAE)的技术分 析,提高了模具设计水平,缩短了产品研制周期, 对于注塑模技术的发展具有重要意义口]。
CAE技术在光学透镜注射模设计中的应用

中图分类号:P9. ; 306 文献标识码: 文章编号: 0 — 1 (o70— 01 0 T 31 2 Q 2. 2 7T 6 B 1 1 2 820)1 00 — 4 0 6
Ap ia in o pl to f CAE e hn lg i d sg c tc oo y n e in
箱) 瑚 昏. . u ∞, 剐 e . d 13cr 6. r ot o
模拟出塑料熔体在注射成型过程中的流动保压和冷 却过程以及预. 产品中的应力分布、 ? 贝 4 分子取向、 收缩 和翘曲变形等。在塑料透镜模具设计中,应用 C E A 技术帮助预测聚合物熔体在型腔 中的成型过程,及 早发现问题, 及时修改模具设计, 提高一次试模成功 率, 以缩短开发周期 , 降低生产成本, 增强市场竞争
维普资讯
模具工业 20 年 第 3 卷第 1 07 3 期
C E技 术在光学透镜注射模设计 中的应用 A
周应国,陈静波,申长雨,闽志宇
( 郑州大学 橡塑模具国家工程研究中心,河南 郑州 400 ) 502
摘要 : 将注射成型中塑料熔体在型腔 内充填模拟基本理论及熔体前沿跟踪技术应用到具体 的光学透镜 模具设计中。通过对模拟结果的分析与评判,有效预防 了原模具设计方案用于实际生产时可能 出现的 问题, 生产出了合格的产品, A C E技术的可靠性与实用性得到证 实。 关键词 : 注射成型; 充填 ; 模具设计 ; 光学透镜;A C E技术
注射模CAE流动模拟技术综述

优 化 的模 具 温 度 。借 助 于流 动 分 析 与 冷却 分析 的耦 合 , 可 以合 理地 确 定熔 体温 度和模 具 温度 。
0 引 言
注 射模 C E根 据 塑 料 成型 流变 学 、热 传 学 和数 值 A 计算 方法 的基 本理 论建 立熔 体 在模 具 型腔 内 的流动 、热 传递 的数 学物 理模 型 ,利用 计 算机 图形 学 技术 ,直 观地 模拟 出熔 体在 模腔 中的动态 填 充过 程 、保压 过 程和冷 却
维普资讯
第2 O卷 第 2期 2 0 o 7年 3月
De eo m n & I n v t n o a h n r & E e t c l rd cs v lp e t n o ai f c iey o M lcr a o u t i P
机 电产 品 开发 与 崭
熔 体流 经壁 部较 厚 的 区域 时 ,流动 阻力 比较 小 ;流
果流 道 阻力 太 大 ,会 降 低型 腔 内压 力 ;但 是 如果 减小 流 道 阻力 而 任 意增 大 流 道 尺 寸 ,则会 延 长 熔 体 冷却 时 间 。
通常 .流 道 的布置 可 以分 为 两类 ,一 类是 平衡 式 ,在 这
平 衡 的流道 系统 ,并最 大 程度地 优 化流 道体 积 。
: 3
’ I
I
图 2所 示 是 某 厂 用 一 模 八 腔 生 产 的产 品 ,材 料 为
ABS, 长
2 0 m,宽 10 5r a 0 mm,厚 度 为 2 m . m,采 用 非 自 5
l
() b
羹
种布 置 中 .流道 的特 征相 同 ,熔体 的流动 是平 衡 的 ,每
个型 腔 的压 力 、温度 是相 同的 ;另一 类是 非平 衡 式流 道 的布 置 ,它分 两种 情 形 ,一种 是各 个 型腔 的尺 寸 和形 状 相 同 .只 是各 型腔 距 主流 道距 离不 同而使 得 流道 布置 不
简述cae技术在塑料注射成型中的典型应用

简述cae技术在塑料注射成型中的典型应用
塑料注射成型是一种常见的制造工艺,它在许多领域中都有广泛的应用。
而在塑料注射成型中,计算机辅助工程(CAE)技术的应用可以提高生产效率、降低成本,并确保产品的质量和性能。
CAE技术可以在注射成型过程之前对模具进行仿真分析。
通过建立模具的三维模型,并在计算机上进行模拟,可以预测模具的流动和填充情况。
这有助于优化模具的设计,避免出现气泡、缩水等缺陷。
同时,还可以通过模拟分析来确定最佳的注射参数,如温度、压力和速度,以确保塑料充分填充模具腔体,从而获得高质量的成品。
CAE技术还可以帮助优化注射成型过程中的冷却系统。
通过模拟分析,可以确定最佳的冷却水路设计,以实现均匀的冷却效果,并避免成品出现变形或收缩。
同时,还可以预测注射成型过程中的温度分布,以便及时调整冷却系统,提高生产效率。
CAE技术还可以对注射成型过程中的应力和变形进行分析。
通过模拟分析,可以预测成品在注射过程中可能出现的变形情况,以便及时调整模具结构,避免成品出现尺寸偏差或变形。
同时,还可以预测成品在使用过程中可能承受的应力,从而优化产品设计,提高产品的强度和耐用性。
CAE技术在塑料注射成型中的应用可以帮助优化模具设计、注射参数调整、冷却系统设计以及产品结构优化,从而提高生产效率、降
低成本,并确保产品的质量和性能。
通过充分利用CAE技术,塑料注射成型行业可以更好地满足市场需求,推动行业的发展。
CAE技术在注射模冷却系统设计中的运用

d s no i et nmo ol gss m i d sr e ,t rvd s ni otn rfrn em to ei f n c o l coi yt eci d ipoie g j i d n e s b a mp r t e e c ehd a e
t e l igt eo t lc oigs s m. orai n p i o l y t z h ma n e
Ke od :net nm l; ol gss m; A yw rs ijco od coi yt C E i n e
1 引言
注射 成 型过 程 是一 个 热 交 换 过 程 。 塑 料 成 型周 在
究, 则始于 2 0世纪 9 0年代初期 。
期中,/ 34以上的时间用于模具 冷却 。冷却 系统 的设 计。 直接影响着模具冷却效率和 型腔 表面温度 , 从而 对注射生产的效率和质量产生重要影响。 一个高效和 均匀的冷却系统设计 能够显著地减少冷却 时间, 提高
成 型效 率 , 对 消 除 塑 件 翘 曲变 形 、 并 内部 应 力 及 表 面 质量 缺 陷产 生影 响 。 长期 以来 , 注射 模 冷 却 系统 的设 计 主要 采 用传 统 方法 , 却 管道 的 布置 和 冷 却参 数 的确 定 往 往在 设 计 冷
助于计算机求 出近似解。 迄今为止 , 求近似解的数值方 法主要有有限差分法 (D 、 F M)有限元法 (E 、 F M)边界元 法( E 。而且 由于绝大多数塑料制件的厚度尺寸往 B M)
CAE在注塑模具设计中的应用

并 另外还 有美 国的 I E , 国的 C DMOL , - AS 德 D A D 等软件 的应 用也 比较广 泛【。 2 ]
2 )国 内
近 年来 , 国 的注塑 C E技 术研 究开 发和 推 我 A
广 应 用 也 取 得 了一 定 的 成 绩 , 如 郑 州 大 学 的 Z Mod软件 和华 中科技 大 学的 H C E软件 。但 — l SA 是 ,大部 分企业 对注 塑 C AE技 术重 视不够 , 识 认
工 艺参 数 的选 择 ,对 降低 生产成 本 、提 高塑 件质
件 有 澳 大 利 亚 的 MF 公 司 的 Mod o 和 美 国 lf w l AC T c 司的 C MO D( —eh公 . L  ̄被 Mod o 公 司合 lf w l
量 、缩短 新产 品开 发周 期 起着 关键性 的作用 。传 统 的注塑 模设 计都 是 以积 累 的经 验和 大胆 尝试 相 结合 ,然 后通过 装配 后 的试模来 发现 问题 ( 图 1 如 所示) 。发现 问题 后从产 品设 计 、模具 设计 、模 具 制造 到 试模 进行 调 整 ,最后 才 进行 模 具生 产…。
1 注塑成型 C AE技术现状及发展
11 注塑成 型 C . AE技术 的现状 1 国外 注塑 C AE技术 的应 用在 国外 已经相 当普遍 。 早在 2 0世纪 5 0年 代 ,就有 美 国学者通 过数 值方
球 。至 20 04年 ,Mod o 软件在 全球 注塑 C lf w l AE 市 场 的 占 有 率 高 达 7 %【 。 用 户 可 以 通 过 5 3 J Mod o lf w软件 实现 对材 料 的选 择 、制 品的形状 结 l
CAE在塑料光学零件注射成型中的应用
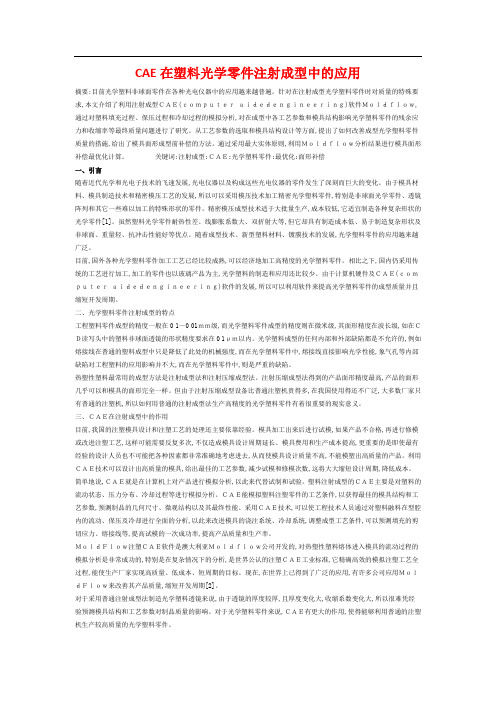
CAE在塑料光学零件注射成型中的应用摘要:目前光学塑料非球面零件在各种光电仪器中的应用越来越普遍。
针对在注射成型光学塑料零件时对质量的特殊要求,本文介绍了利用注射成型CAE(computeraidedengineering)软件Moldflow,通过对塑料填充过程、保压过程和冷却过程的模拟分析,对在成型中各工艺参数和模具结构影响光学塑料零件的残余应力和收缩率等最终质量问题进行了研究。
从工艺参数的选取和模具结构设计等方面,提出了如何改善成型光学塑料零件质量的措施,给出了模具面形成型前补偿的方法。
通过采用最大实体原则,利用Moldflow分析结果进行模具面形补偿最优化计算。
关键词:注射成型;CAE;光学塑料零件;最优化;面形补偿一、引言随着近代光学和光电子技术的飞速发展,光电仪器以及构成这些光电仪器的零件发生了深刻而巨大的变化。
由于模具材料、模具制造技术和精密模压工艺的发展,所以可以采用模压技术加工精密光学塑料零件,特别是非球面光学零件、透镜阵列和其它一些难以加工的特殊形状的零件。
精密模压成型技术适于大批量生产,成本较低,它适宜制造各种复杂形状的光学零件[1]。
虽然塑料光学零件耐热性差、线膨胀系数大、双折射大等,但它却具有制造成本低、易于制造复杂形状及非球面、重量轻、抗冲击性能好等优点。
随着成型技术、新型塑料材料、镀膜技术的发展,光学塑料零件的应用越来越广泛。
目前,国外各种光学塑料零件加工工艺已经比较成熟,可以经济地加工高精度的光学塑料零件。
相比之下,国内仍采用传统的工艺进行加工,加工的零件也以玻璃产品为主,光学塑料的制造和应用还比较少。
由于计算机硬件及CAE(computeraidedengineering)软件的发展,所以可以利用软件来提高光学塑料零件的成型质量并且缩短开发周期。
二、光学塑料零件注射成型的特点工程塑料零件成型的精度一般在0 1~0 01mm级,而光学塑料零件成型的精度则在微米级,其面形精度在波长级,如在CD读写头中的塑料非球面透镜的形状精度要求在0 1μm以内。
基于CAE技术优化注射模设计

的 H C E、 S A 郑州大学 的 Z —MO D分析 软件等 。 L
2 注射 模 C E分 析造 时才发 现 的 问题所 导致 的 高额 成本 和 时间延迟 。 有必 要考 虑 产 品几何 造 型 、 料 材
工 艺参 数 的优 化 与 否 是 决 定 塑件 产 品最 终 质 量 的三
在 国内相关研究 中 , 于各种 高聚物成 型数值模 拟 对
方面 的研 究虽然 开始 的 比较 晚 。但 对 于注塑模 C AE技 术 研究 的发展速度 却非 常快 。使 得我 国的 注塑模 C D A / C /A 研究 和应 用水平 有 了较 大程度 的提 高 。 目前 AEC M
的设 计 当 中去 了。
随着 市 场 对 塑 件 产 品 的及 时 更 新 性 和 质 量 要 求
不 断 地 提 高 。 求 企业 在 最 短 的时 间 内 、 要 最低 的成 本
下得 到性 能优 越 、 质量稳 定 、 尺寸 精确 的塑件 产 品 。这
势必 对模 具设 计企 业带来 更 大 的挑 战 和机遇 。众 所周 知 , 件 产 品 设 计 的合 理 性 、 具 设 计 的优 劣 和生 产 塑 模
本 功 能 和 实 际 意 义 做 了较 详 尽 的 说 明 , 并介 绍 了注 塑成 型 CAE技 术 与 优 化 理 论 相 结 合 . 实现 注射 模 具 动 态 优 化 设 计 的理 论 及 方 法 , 出 了将 C 指 AE分 析 技 术 与优 化设 计理 论 相 结合 的方 法来 优 化 注 射模 设 计 的 必 然性
维普资讯
第 6期 ( 第 9 总 9期)
机 械 管 理 开 发
- 1、下载文档前请自行甄别文档内容的完整性,平台不提供额外的编辑、内容补充、找答案等附加服务。
- 2、"仅部分预览"的文档,不可在线预览部分如存在完整性等问题,可反馈申请退款(可完整预览的文档不适用该条件!)。
- 3、如文档侵犯您的权益,请联系客服反馈,我们会尽快为您处理(人工客服工作时间:9:00-18:30)。
模具工业 !##$ 年第 %! 卷第 & 期 响而发生变形,特别是型腔和型芯的变形,会对塑 件的形状造成很大影响,关系到塑件是否能满足其 尺寸和技术要求。而型腔和型芯的变形又会使注射 过程 ’() 分析发生变化, 从而很有必要对注射过程 中模具的变化进行全面分析,以尽可能的使分析结 果与实际情况吻合。模具中的变形分析可根据一般 的结构分析进行。而塑件形状一般比较复杂,在注 射模 ’() 软件或结构分析软件中造型都比较困难, 如 *+, - )、./ 等软件在此方面功能强大,有一个模 具设计模块,对模具的生成十分方便,而且装配中 可进行配合、干涉等检测的模拟,对模具的设计也 是十分有利的。 因此注射模设计的全面 ’() 分析除 了需要用到注射模 ’() 软件外, 还需其他优秀的三 维绘图软件和结构分析软件配合。 % 实例分析 图 0 所示热水瓶外壳塑件,根据经验从流动性 和分型、 对称等方面考虑, 在瓶底开 ! 个浇口进料, 如图 ! 所示。但这样会导致轴向开模,由于水瓶轴 向尺寸长,使开模行程很大。而大型注塑机生产任
!"#$%&’#$( ’))*+,’#+-" -. /01 #$,2"-*-%3 +" ($4+%" -. +"5$,#+-" 6-7*(
!"#$ %&’()’*+ , -./ 0’1*()’2*34 5 + 6 7891:;<8*; 2= >8?&1*’?1@ 1*A #@8?;:’?1@ #*3’*88:’*3 , #1B; !&’*1 .*B;’;C;8 2= D8?&*2@23E , $1*( ?&1*3 , 0’1*3)’ FFGG+F , !&’*1 H 4 6 I?&22@ 2= >8?&1*’?1@ 1*A #@8?;:’?1@ #*3’*88:’*3 , JC*<’*3 /*’K8:( B’;E 2= I?’8*?8 1*A D8?&*2@23E , JC*<’*3 , LC**1* MNGGOF , !&’*1 P 084#&’,# Q R !R# 1*1@EB’B S1B <1A8 2* =@2S’*3 2= 9@1B;’?B 1*A A8=2:<1;’2* 2= <2C@A ?2<92*8*;B TE CB’*3 !R# B2=;S1:8 =2: ’*U8?;’2* <2C@A 1*A B;:C?;C:1@ 1*1@EB’B B2=;S1:8 6 D&8 1*1@EB’B :8BC@;B 32; =:2< ?2<T’*8A 199@’?1;’2* 2= B2=;S1:8 ?2*=2:<8A T8;;8: ;2 1?;C1@ 2*8B 6 D&’B S2C@A 9:2K’A8 9:1?;’?1@ :8=8:8*?8B =2: 2K8:1@@ !R# 1*1@EB’B 2* ’*U8?;’2* <2C@A A8B’3* 6 9$3 :-&(4 Q ’*U8?;’2* <2C@A H !R# H =@2S 1*1@EB’B H B;:C?;C:1@ 1*1@EB’B
图7
最佳浇口位置分析图
在利用 ’/010 软件对型芯变形进行分析之前, 必须先知道型芯上各点所受到的压力。直接算出型 芯所受到的压力是不太可能的, 但在注射模 &’( 软 件中可以得到在注射过程中塑件各点处所承载的 压力,此压力即由型腔和型芯承受,在熔融塑料流 动过程中型腔和型芯各自所承受的压力大小与塑 料的注射方向、 流动方向、 塑件的形状等有关。型芯 所 受 到 的 压 力 只 能 根 据 注 射 模 &’( 软 件 的 模 拟 结 果进行估算。现利用 )*+,-+*. 对水瓶注射过程进行 分析, 压力分布结果如图 " 所示。 从图 " 可以看出,注塑机注射压力必须大于 注射点处压力最大, 随着熔融塑料的向前 88 9 : )2; , 移动, 受到型腔和型芯的阻力, 压力越来越小, 在熔 融塑料最终到达处压力接近于零。为了减少气泡、 水瓶壳的尺寸精度要求不高,聚丙烯材料的低 精度为 8 级, 因壁厚为 : 9 $ << A 查表得公差为 B # 9 :" 据单 <<。型芯在压力作用下变形情况如图 % 所示, 元分析结果其最大的变形量为 # 9 !$! %"! << A 在型 芯中间有一段其变形量超过 # 9 ! <<, 从节点分析结 果可查得型芯在注射 方 向( ! 轴 方 向)的最大位移
— — —— — —— — —— — —— — —— — —— — —— 收稿日期: !##$ 3 #% 3 !!。 基金项目: 东华理工学院硕博基金资助项目 ( 789#,#%) 。 作者简介: 陈志新 ( *&/% 3 ) , 男, 湖南益阳人, 讲师, 研究方向: 模 具 ’(7 : ’() : ’(; , 地址: 江西省南昌市东华理工学院南昌 校 区 *%#" 信 箱 机 电 系 , (电 话)*%/,,/,/%"% < (电 子 信 箱)=>?@ =ABC!##! D EFAGG + =GH + =C 。
!"
模具工业 !##$ 年第 %! 卷第 & 期
注 射 模 设 计 中 ’() 技 术 的 综 合 应 用
陈志新 * ,刘建雄 ! ( * + 东华理工学院 机械工程系,江西 南昌 ! + 昆明理工大学 机电工程学院,云南 昆明 %%##*%; $,##&%)
摘要: 用注射模 ’() 软件和结构分析软件对注射模内塑料流动和模具零件的变形进行了 ’() 分析, 克 服了使用单一软件分析的不完整性,使 ’() 分析的结果和实际的情况更吻合,为对注射模设计进行全 面 ’() 分析提供了实用的参考方法。 流动分析; 结构分析 关键词: 注射模; ’() ; 中图分类号: -.%&* + /! 0 -1%!# + $$! 文献标识码: 2 文章编号: *##* 3 !*$4 5 !##$ 6 #& 3 ##!" 3 #"
工艺参数, 但仍无法满足成型要求。
!" 此时若再改为轴向开模,由于分型面完全不 同,则原模具会造成报废。因此浇口位置改为水瓶 底部 ! 点进浇,依然径向开模,分流道由主流道折 弯绕到浇口处,这样虽不会导致型芯变形,但分流 道长, 塑件本身体积较大, 且壁薄, 此时又要注意注 射压力是否能满足要求。按此方法修改模具后试模 发现,注射压力能满足要求。由于设计前没能准确 判断成型的实际情况,造成设计出现失误,浪费了 大量的人力、物力、财力,几乎造成了模具的报废, 在经济上和信誉上都有较大的损失。 对上述情况进行 &’( 综合分析, 将模拟分析结 果与实际情况进行比较, 证实所用 &’( 综合分析方 法的有效性,为以后的设计提供可靠有效的分析方 法, 扩大 &’( 分析方法的应用范围。 下 面 用 注 射 模 &’( 软 件 )*+,-+*. 和 ’/010 软 件的结构分析模块进行综合分析, 介绍 &’( 分析方 法的特点及操作方法。 首先利用 23* 4 ( 绘图, 输出为 ! 056 格式, 再利 用 &’( 软件进行最佳浇口位置的分析, 分析结果如 图 7 所示。
图8 型芯结构
模具工业 !##$ 年第 %! 卷第 & 期
!"
图’
施加约束和载荷
图 ,#
ห้องสมุดไป่ตู้压力分布图
量为 # ( !%# )$ **, 总位移最大值为 # ( !%% #" **。 由 于 型芯变形量超过塑件的 公 差 + # ( ,$ **, 使 得 塑 件的尺寸超过其公差范围,造成产品不合格。根据 分析可知, 把浇口设计在手柄上 (图 ) 位置) 是不可 行的。该分析结果与实际情况基本一致,实际试模 时产品壁厚最大处达 , ( -- ** . 最小处为 , ( #- **, 不能满足塑件的尺寸要求,必须重新确定浇口位置 及设计模具。
*
引
言
注 射 模 ’() 技 术 是 以 计 算 机 模 拟 为 手 段 分 析 塑料加工过程并完成模具优化设计的塑料模具计算 机辅助工程。它是进行产品设计、制造、工程分析、 仿真、 试验等信息处理, 并包含相应数据与数据管理 系统在内的计算机辅助设计综合系统。 塑料注射成型是一个复杂的物理过程,非牛顿 假塑性的高温塑料熔体在压力下通过浇注系统流向 模具型腔, 熔体由于模具中的冷却系统而快速固化, 同时伴随熔体有剪切生热、 体积收缩、 分子取向和结 晶过程。因此全面深入理解注射成型需要高分子物 理学、 传热学、 流变学以及成型工艺学等多方面的综 合知识。目前建立一个全面的数学模型对塑料成型 全过程进行模拟难度很大,所以将成型过程分开考 虑, 主要包括如下主要内容: 5 * 6 充模流动模拟。 5 ! 6 保压过程模拟。 5 % 6 冷却模拟。 5 " 6 制品结晶、 纤维定向分析。 5 , 6 制品应力、 应变及翘曲分析。 一 般 的 注 射 模 ’() 软 件 对 塑 料 的 流 动 过 程 及 其产生的结果进行了比较充分的考虑和模拟,但在 这一过程中模具本身由于受到注射过程中压力的影
图%
浇口开设在圆柱面上
图0
零件图
图1
浇口开设在手柄上
根据经验设计的模具, 在试模时发现, 如果用足 够大的注射压力使型腔充满,这时塑件由于型芯变 形太大, 造成壁厚不均, 且超出公差范围, 造成产品 不合格。若减小注射压力, 由于塑件壁薄, 熔融塑料 流程比较长,又造成型腔注射不满。虽多次修改各
图! 底部开设 ! 个浇口