影响膨化料加工质量缺陷的分析的对策
膨化食品主要质量安全问题分析

膨化食品主要质量安全问题分析作者:雷蕾靳苛苛来源:《食品安全导刊·中旬刊》2021年第07期摘要:本文闡述了膨化食品中的主要质量安全问题,对膨化食品中防腐剂超标、甜味剂超标、着色剂超标、膨松剂超标、重金属超标、酸价、过氧化值超标以及微生物超标现象进行展开分析,并提出解决策略,以期进一步促进膨化食品行业的健康发展。
关键词:膨化食品;质量;食品安全膨化食品以谷物、薯类、豆类或蔬菜为原料,添加一定比例的食品添加剂或其他辅料,采用焙烤、油炸、微波或挤压等膨化工艺而加工制成的食品。
膨化食品品种多、口感好、易携带、易消化,备受消费者的喜爱,风靡世界[1]。
虽然膨化食品在我国历史悠久,但现代化的生产时间并不长,存在一定的安全风险。
由于生活水平的逐年提升,消费者对食品质量要求也越来越高,膨化食品的质量安全问题一直备受人们关注。
为提高膨化食品质量,切实保障广大消费者的身体健康。
本文通过分析膨化食品中的主要质量安全问题,并对其提出解决策略,以期对膨化食品行业的发展提供一定参考。
1 膨化食品中的主要质量安全问题1.1 防腐剂超标目前市场上的防腐剂种类繁多,其中苯甲酸钠和山梨酸钾因成本低廉,防腐效果明显,受到厂家的青睐。
厂家通过延长食品保质期得到更大利益。
有些厂家滥用防腐剂,对食用者的健康带来巨大危害。
《食品安全国家标准食品添加剂使用标准》(GB 2760—2014)中规定膨化食品中不得使用苯甲酸和山梨酸。
人体长期摄入防腐剂,会减弱肝脏的代谢功能和肠胃的消化功能,影响人体的新陈代谢平衡[2]。
1.2 甜味剂超标膨化食品在生产过程中通常会加入糖来提升产品的口感。
为了降低成本,有些不良厂家使用糖精钠、安赛蜜、甜蜜素等甜味剂。
糖精钠价格便宜,甜度大,常被超量、超范围使用。
《食品安全国家标准食品添加剂使用标准》(GB 2760—2014)中规定膨化食品中不得使用糖精钠、安赛蜜、甜蜜素。
人体长期摄入甜味剂,扰乱肠胃消化酶的分泌,降低肠胃的消化能力,影响肝脏功能。
影响饲料颗粒性状因素的分析及对策
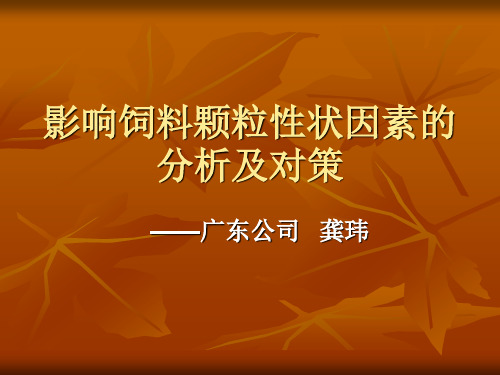
7影响水产单个颗粒或个体间颗粒颜色不一致 (即花料)的因素分析和对策
序号 1 2 原因 混合不均匀 调质水分不一致 改进方法 延长混合时间,改善混合效果 延长调质时间(低温调质),改善 调质性能
3
4 5
颗粒不均匀
7影响膨化料颗粒膨化率不高的因素的分析和对策
序号 1 2 原因 模具开孔率过高 物料中淀粉含量低 改进方法 更换合理模具 调整配方,增加淀粉含量
3
4
出模水分过低
喂料量低,产能低
调整蒸汽和水的注入量,使之合理
提高喂料转速
5
6 7
出模压力低
出模温度低 物料内含脂肪过高
提高出模时的工作压力
提高出模温度 调整配方
调整配方,增加淀粉含量 延长调质时间(检查调质器桨 叶)
7
调质水分过多
减少制粒时料的水分
4影响水产颗粒产生辐射式裂纹的因素分析和对策
序号 1 2 3 4 原因 含有较大的颗粒的原料 在冷却时不易软化 因软化程度不同而导致 收缩量差异而产生 改进方法 增加粉碎细度,控制粉状饲料粗 细度和均匀度 减少冷却风量,延长冷却时间 延长调质时间,蒸汽时间要饱和 减少冷却风量,延长冷却时间 延长调质时间,增加后熟化稳定 工序,提高调质温度 延长调质时间,蒸汽质量要饱和
7
8 9
压辊磨损不一致
模孔导料口磨损不一致 切刀不在合理位置
更换一致的压辊
修复模具,使之一致 调整切刀在切线位置上
12影响水产颗粒成品水分过高的因素分析和对策
序号 原因 改进方法
1 2
3 4 5 6 7 8 9
无烘干设备 模压缩比过低
材料加工过程中常见缺陷形成原因和控制措施

材料加工过程中常见缺陷形成原因和控制措施在材料加工的过程中,常常会出现一些缺陷,这些缺陷可能会降低材料的性能和质量。
了解这些常见的缺陷形成原因以及相应的控制措施,对于提高材料加工的效率和质量至关重要。
一、表面缺陷1. 划痕和刮痕:这些缺陷通常是由于加工过程中使用的工具和设备表面不平整或硬度不足导致的。
此外,操作不当或过度力度也可能导致划痕和刮痕的形成。
控制措施包括使用平整且硬度适当的工具和设备,并合理控制力度和操作方式,避免划痕和刮痕的产生。
2. 锈斑和氧化:这些缺陷通常是由于材料受到氧气和水的侵蚀和反应导致的。
在加工过程中,应尽量避免材料长时间暴露在潮湿的环境中,同时使用防锈剂和表面处理技术可以有效地防止锈斑和氧化的形成。
3. 气泡和孔洞:这些缺陷通常是由于材料内部存在气体或液体,在加工过程中由于温度或压力的变化导致气体或液体无法逸出,从而形成气泡和孔洞。
控制措施包括材料预处理,如真空处理以去除内部气体,并且在加工过程中要合理控制温度和压力,防止气泡和孔洞的形成。
二、尺寸缺陷1. 偏差:加工过程中,由于工具磨损、设备不稳定或操作不准确等原因,会导致零件尺寸偏离设计要求。
控制措施包括定期检查和更换工具、维护设备的稳定性,并确保操作人员接受过专业的培训,提高操作的准确性。
2. 粗糙度:材料表面的粗糙度是加工过程中另一个常见的缺陷。
粗糙的表面可能会影响零件的质量和功能。
控制措施包括选择适当的加工方法和工艺参数,如切削速度、进给速度以及刀具和夹具的选择,以获得所需的表面质量。
三、组织缺陷1. 结晶缺陷:材料加工过程中,结晶缺陷的形成通常是由于材料的冷却速度过快或冷却不均匀导致的。
这些缺陷可能包括晶界偏大、晶界分布不均匀等问题。
为了减少结晶缺陷的形成,可以采取适当的冷却措施,如控制冷却速度和温度梯度,以及进行热处理等。
2. 晶粒长大不均匀:晶粒长大不均匀往往会导致材料的性能和力学性能降低。
控制措施包括合理选择和设计加工工艺,如适当的热处理和锻造工艺,以及控制加工温度、压力和时间等参数,以实现晶粒的均匀长大。
膨化料加工质量指标要求、关键控制点、控制方法

气力输送装置:吸料器、关风器、离心卸料器(刹 克龙)和风机等
7
2、料仓
流动区 滞留区 粘壁区
料位器
漏斗流动形式
整体流动形式
8
3、粉碎 粉碎的目的是是粉碎后的饲料颗粒表面积增
大以利于养殖动物消化吸收和后续工序加工。但 是愈细耗能越大,饲养效果也会手抖啊影响。因 此粉碎细度和均匀度是颗粒饲料加工的重要指标 之一。膨化配合饲料因配方组成原料的不同而粉 碎的要求不同。
膨化料加工质量指标要求、关键控制 点、控制方法
广东海大集团股份有限公司畜牧水产研究中心
纲要: 一、膨化料概述 二、膨化工艺流程 三、膨化料指标要求 四、生产过程质量控制 五、膨化生产过程常见问题及解决饲料开始于20世纪5O年代的美国,到8O年
代膨化技术已成为国外发展速度最快的饲料加工 新技术。我们国家膨化饲料主要是在90年代开始 发展。 膨化机主要由动力传动装置、喂料装置、预调质 器、挤压部件及切割装置等组成。挤压部件是核 心部件,由螺杆、螺套及模头组成
五、膨化生产过程常见问题及解决措施
一、沉水: 1、产生原因: 1)、压力不够; 2)、加水过少;3)、熟化不够; 2、解决措施: 1)、给外夹套加温,增加管内揉搓磨擦,形成摩擦
阻压力;或模具堵孔减少出口面积; 2)、调整加水量; 3)、提高熟化温度;
37
五、膨化生产过程常见问题及解决措施
二、外表不光滑粉多 1、产生原因: 1)、加水过少;2)、熟化不够;3)、模具光洁度不够
四、生产过程质量控制
面粉、生粉、变性淀粉、小麦用量直接影响成品 的膨化度和粘弹性。生产过程温度调节和蒸汽添 加要适当,否则容易产生堵料,从而影响生产效 率。在挤压完粘度较高的原料后,再好先用含油 脂较高的物料来清理膨化腔,以保持其良好的工 作特性。
水产膨化饲料加工故障诊断与分析
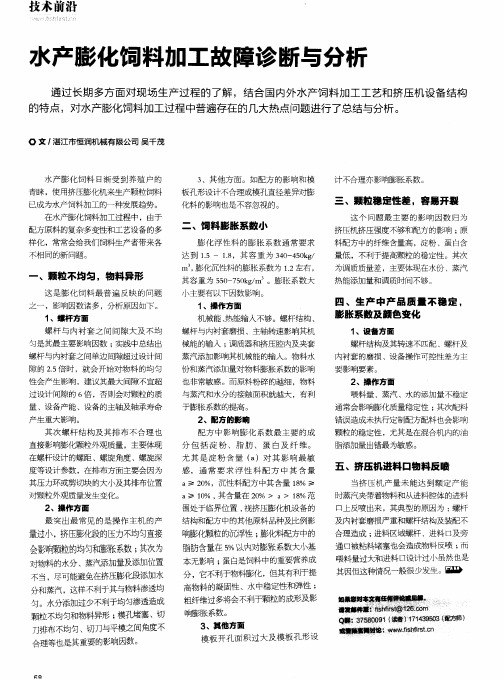
合理造成 ;进料区域螺杆 、进料 口及旁 通口被粘料堵塞也会造成物料反喷 ;而 喂料量过大和进料 口设计过 小虽然也是 其 因但这种情况一般很少发生。回 }
高物料的凝固性、水中稳定性和弹性 ;
粗纤维过多将会不利于颗粒的成形及影
响膨胀系数 。 3、其他方面 模板 开 孔面 积 过大 及模 板 孔形 设
3、其 他方面 。如配方 的影响 和模 计不合理亦影响膨胀系数。
板孔 形设计 不合理或模孔直径差异对膨
化料 的影响也是不容忽视 的。
三 、颗粒稳定性差 ,容易开裂
二 、饲料膨胀系数小
这个 问题 最 主要 的 影响 因数 归 为 挤压机挤压强度不够和配方的影响 ;原
膨化 浮 性料 的膨 胀 系数 通 常要 求 料配方 中的纤维含量高 ,淀粉 、蛋 白含
技 术前沿
、∥ 、 ㈨
、,
水产膨化饲料加工故障诊 断与分析
通 过长期 多方面对现场 生产过程 的了解 ,结 合国 内外水 产饲料加 工工艺和挤 压机设备结构 的特点 ,对水产膨化饲料加工过程 中普遍存在的几大热点 问题进行了总结与分析 。
o 文 ,湛江市恒润机械有限公司 吴干茂
达 到 1.5— 1.8,其容 重 为 340—450kg/ 量低 ,不利于提高颗粒的稳定 性。其次
m ,膨 化沉性料 的膨胀 系数为 1.2左右 , 为调 质质量差 ,主要体现在水份 、蒸汽
其容 重为 550—750kg/m。。膨胀 系数大 热能添加量和调质时间不够 。
小主要有以下 因数 影响 。 1、操 作 方 面 机械能 、热能输入不够 。螺杆结构 、
分 包 括 淀 粉 、脂 肪 、蛋 白及 纤 维 。 脂添加量 出错最 为敏感 。
影响膨化食品质量的因素浅析

Dec. 2019 CHINA FOOD SAFETY 21质量控制膨化食品是指经过熟化工艺后体积有着明显增加的食品,膨化食品在我国有着很久的历史,但是现代化的生产时间并不长。
膨化食品市场在我国体量大,我国膨化食品消费市场随着整体经济的发展也得到大幅提升,随着国人生活水平的提升,发展形势更加利好,越来越多的企业开始加入到竞争行列中。
但是,由于过程监管难度比较大,膨化食品的质量问题一直存在。
本文就主要的质量问题进行分析,就主要的应对策略进行讲述。
影响我国膨化食品市场质量的因素分析膨化食品的质量影响因素需要对其生产的全过程进行分析,从原料到生产再到包装,主要的影响因素为:原材料质量风险、膨化食品加工过程的质量风险以及包装过程中的质量风险,通过从这3个方面进行全面的 剖析。
原材料质量风险1.环境污染问题膨化食品生产需要良好的原料支撑,加工原料中可能存在许多影响原料质量的问题,使其不能满足质量要求。
在原材料风险上,环境污染是影响原材料安全的最主要因素。
环境污染的类型很多,目前最主要的是工业企业,种植区周围工厂排放的各种废水废渣,这些工业废物都会对大气、水源农田等都造成影响。
吸收了有害物资的农田的土质、水源都不利于农作物的生长,部分毒素也会进入农作物或者养殖产品,进而导致最终的食品本身质量不过关。
2.重金属污染近年来,我国膨化食品中重金属含量在各种监督抽查中经常超标,膨化食品的质量问题已成为突出问题,其次是农药残留,农药残留也会对膨化食品原料造成污染,过量使用剧毒及可能会有残留的除害剂(例如甲胺磷),可令收割后的物料含有除害剂残余。
一些生产商可能会以相对较低的价格购买基因改造物料,以降低生产成本。
此外,马铃薯、木薯等薯类作物需要贮存在5~10 ℃,如果贮存不当,它们会发芽,或者表面会变成绿色和紫色,此时其会含有大量被称为茄碱(solanine)的毒素,人和动物食用一定量的茄碱会出现急性中毒症状,如果玉米、木薯和其他原材料在贮存前没有完全干燥,长时间堆放的情况下,也很可能会产生茄碱,造成食品污染。
膨化食品质量安全影响因素分析及控制策略

加工过程
食 品 加 工 企 业 出 于 成 本 考 虑, 在 油炸工艺中,长时间不更换用油或使 用不合格的油品,导致食品出现哈喇 味,产生质量问题;或在产品中大量 添加糖精钠、甜蜜素等代糖品,以提高 食品甜度,但这些代糖品过量食用会降 低肠胃功能;还有的食品企业在原料中 超剂量添加膨松剂,如铝、明矾等,长 期食用将损伤人的大脑,使人痴呆。 包装隐患
作者简介:冯燕芳(1982—),女, 汉族,广东惠州人,大专,中级食品 工程师。研究方向:食品。
膨化食品质量安全影响因素分析及控制策略
□ 冯燕芳 广东顺德日清食品有限公司
45 Apr. 2019 CHINA FOOD SAFETY Copyright©博看网 . All Rights Reserved.
膨化食品质量安全的控制策略
增强食品安全意识
在 膨 化 食 品 的 生 产 过 程 中, 要 尽 量选择更安全的原料、配方及包装, 以提高食品的安全性能;在生产工艺 选择上尽量使用膨化挤压技术、烘焙 膨化技术、真空油炸技术及微波膨化 技术,最大限度的避免生产过程中的 有害因素。休闲食品对于平衡健康膳 食有一定的作用,在膨化食品的发展 方向上,要尽量向低糖、低脂肪、低 热量的休闲食品方向发展。 加强各环节的质量控制
为 改 进 产 品 质 量, 膨 化 食 品 企 业 要更加注重原料、加工工艺、包装等方 面的质量安全,采用新的工艺技术,尽 可能减小对人体健康的不利影响因素。
膨化食品质量安全影响因素
材料问题
① 环 境 污 染, 如 果 农 作 物 种 植 区 有大量的工业企业,那么这些企业排 放的废水、废气等将直接污染农田、 水源及空气,其中最严重的是重金属 超标。重金属不仅存在于农产品中, 还会污染水产品,例如膨化食品企业 在新型产品中添加虾粉、鱼松等水产 品进行调味,可大大增加膨化食品中 重金属超标的概率。②农药、化肥残留。 为提高农作物产量,农民会大量使用 高毒及高残留的农药,大量施用化学 肥料,导致农药、化肥中的有害物质 随原料流入食品。③黄曲霉素、龙癸 碱等。大豆、玉米在储存前未完全晾干, 长时间存放容易产生黄曲霉素。而薯 类存放温度以 5 ~ 10 ℃为宜,过度或 过低都会导致其产生龙葵素。
影响食品挤压膨化品质的因素及对策

度高会使产品产生 粘牙感。 2 1 4 膳食纤维
2 3
1 1
250 270
12 12
60~ 68 57~ 63
容重 适 中、 口感 细 腻、 耐泡性好、 不粘牙 容重 偏 轻、 色泽 较 浅、 孔洞较大
38
FOO D AND MACHI N ERY
2003
新
产
品
添加须在湿基 为 5 % ~ 12 % 之 间比 较 适合。现以不同水分含量 的三个实验为 例进行说明 ( 见表 1) 。 2 3 螺杆转速对挤压膨化品质的影响 在食品的 挤压 膨化过 程中 , 螺杆 的 转速起着 十分 关键的 作用。 转速 加快 , 导致温 度 增加 , 滞留 时 间 下 降 , 扭 矩 降 低 , 膨化度加大 , 产品色泽 变浅。不 同的 早 餐谷物 配方 , 对螺杆 转速要 求也不 相 同 , 现以 不同的 三个实 验对螺 杆转速 的 要求为例进行说 明( 见表 2) 。 2 4 喂料量对挤压膨化品质的影响 在谷物挤压 膨化中 , 不同的模具 , 喂 料量要求 不同。在 使用 同一 个模 具时 , 在其它条件不变 的情况下 , 喂料量加大 , 则压力增 大 , 膨化度 降低 , 色 泽变 深 , 影 响产品的口感及 质地。
通过 分析 影 响食 品挤 压膨 化度 的 因
素 , 找出关键 控制点 , 以提 高产 品膨 化质 量, 提高制成率。 关键词 Abstract 食品 挤压膨化 因素 控制点
2
2 1
影响挤压膨化品质的因素
物料成分对挤压膨化品质的影响 脂肪含量 研究表明 , 脂肪在挤
In order to improve t he qualit y of ex
1 雷燕怡 上的 应用 31 2 张裕中 , 王景主编 食 品挤压加工 技术与 应用 北京 : 中国轻工业出版社 , 1998 挤压 膨化 技术在 营养 早餐 生产 食 品与 机 械 , 2002 ( 3) : 29 ~
彭江-影响膨化鱼饲料加工质量关键技术控制点
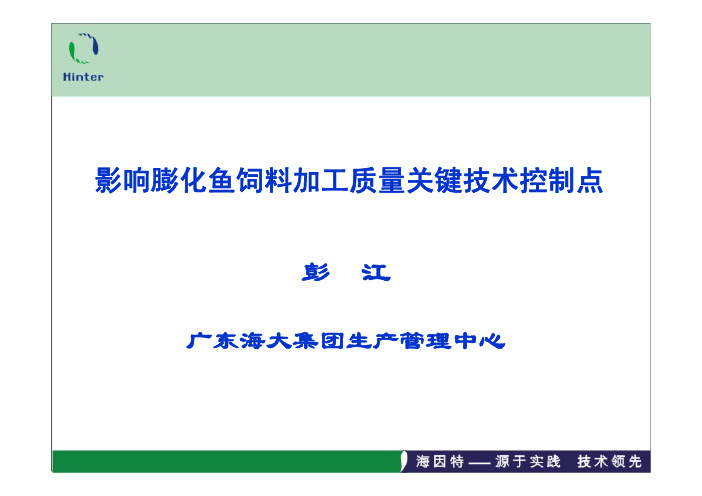
5.6 干燥工艺设备选型:
¾ 产品规格形状多样:应选床层输送式 干燥机(带自清和热风循环功能);
¾ 产品规格形状较单一生产批量大:可 用多级翻板逆流式干燥机;
¾ 产品水分均匀度要求:布/排料结构 科学稳定,产品干燥均匀度好。
注:要求保持颗粒完好性和防止工艺交 叉污染,具有热风循环节能功能。
5.7 后喷涂工艺设备要求:
¾ 物料喷涂前:须将细粉和较大颗粒 筛选清除;
¾ 后喷油量在5%以下:可选连续式滚筒 喷油机(二流体喷嘴雾化好);
¾ 后喷油量在5%以上:应选用批次真空 喷油机(单流体喷嘴);
注:需对物料与液体添加量按照配方 比例精准控制,实现均匀喷涂。
六、配方和工艺设计与操作三者间相互关系:
6.1 工艺设备 设备选型和工艺
¾ 挤压模孔Φ2.0mm以上时: 粉碎须经过12-16目筛网筛选除杂;
注:模孔径在2.0mm以下,若配方中含皮毛棉类原料比 例较大时,即便经过24目筛网筛选后,挤压生产稳定 性依然较差!
5.4 模孔结构有效压距控制:
¾ 压距设计参数: A、孔径≤1.5mm : 压距为孔径的1.2-1.5倍 B、孔径≥2.0mm : 压距为孔径的0.8-2.0倍
提纲
一、影响膨化鱼料加工质量主要环节 二、原料理化特性对挤压加工的影响 三、挤压加工对产品配方设计要求 四、产品加工质量与挤压条件控制 五、加工质量与工艺设备关键控制点 六、配方和工艺设计与操作三者间相互关系 七、现代典型的膨化水产饲料加工工艺流程
一、影响膨化鱼饲料加工质量主要环节:
1.1 产品加工质量控制侧重点:
A.挤压前 营养指标 筛选除杂 粉碎粒度 混合均匀度 防止交叉污染 调质熟化度等
B.挤压后 营养指标 颗粒均匀度 比重/浮水率 软化/耐水时间 软化后颗粒粘弹性 含粉率/外观色泽等
草鱼膨化料市场推广存在的问题及策略
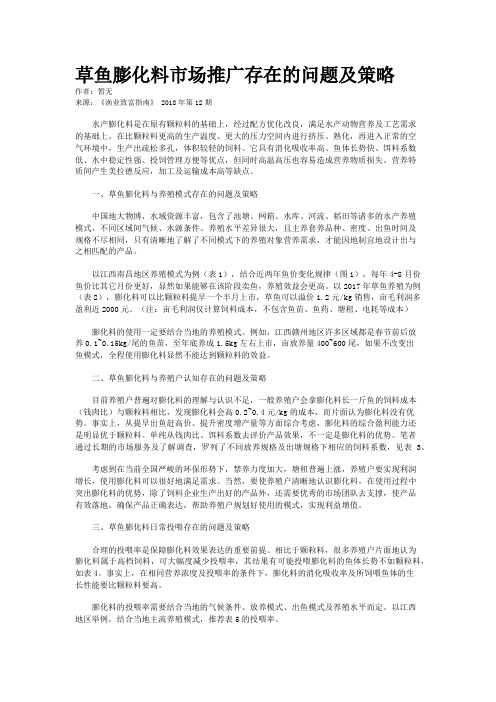
草鱼膨化料市场推广存在的问题及策略作者:暂无来源:《渔业致富指南》 2018年第12期水产膨化料是在原有颗粒料的基础上,经过配方优化改良,满足水产动物营养及工艺需求的基础上,在比颗粒料更高的生产温度、更大的压力空间内进行挤压、熟化,再进入正常的空气环境中,生产出疏松多孔,体积较轻的饲料。
它具有消化吸收率高、鱼体长势快、饵料系数低、水中稳定性强、投饲管理方便等优点,但同时高温高压也容易造成营养物质损失、营养特质间产生美拉德反应,加工及运输成本高等缺点。
一、草鱼膨化料与养殖模式存在的问题及策略中国地大物博,水域资源丰富,包含了池塘、网箱、水库、河流、稻田等诸多的水产养殖模式,不同区域间气候、水源条件、养殖水平差异很大,且主养套养品种、密度、出鱼时间及规格不尽相同,只有清晰地了解了不同模式下的养殖对象营养需求,才能因地制宜地设计出与之相匹配的产品。
以江西南昌地区养殖模式为例(表1),结合近两年鱼价变化规律(图1),每年4-8月份鱼价比其它月份更好,显然如果能够在该阶段卖鱼,养殖效益会更高。
以2017年草鱼养殖为例(表2),膨化料可以比颗粒料提早一个半月上市,草鱼可以溢价1.2元/kg销售,亩毛利润多盈利近2000元。
(注:亩毛利润仅计算饲料成本,不包含鱼苗、鱼药、塘租、电耗等成本)膨化料的使用一定要结合当地的养殖模式。
例如,江西赣州地区许多区域都是春节前后放养0.1~0.15kg/尾的鱼苗,至年底养成1.5kg左右上市,亩放养量400~600尾,如果不改变出鱼模式,全程使用膨化料显然不能达到颗粒料的效益。
二、草鱼膨化料与养殖户认知存在的问题及策略目前养殖户普遍对膨化料的理解与认识不足,一般养殖户会拿膨化料长一斤鱼的饲料成本(钱肉比)与颗粒料相比,发现膨化料会高0.2~0.4元/kg的成本,而片面认为膨化料没有优势。
事实上,从提早出鱼赶高价、提升密度增产量等方面综合考虑,膨化料的综合盈利能力还是明显优于颗粒料。
饲料加工技术中常见问题解析与应对策略

饲料加工技术中常见问题解析与应对策略饲料加工技术在畜牧养殖业中扮演着重要的角色,它直接关系到养殖业的效益和动物的健康。
然而,在饲料加工的过程中,常常会遇到一些问题,这些问题如果不及时解决,可能会导致饲料质量下降,进而影响到养殖业的发展。
本文将就饲料加工技术中常见的问题进行解析,并提供相应的应对策略。
首先,饲料加工过程中常见的问题之一是原料质量不稳定。
饲料加工所使用的原料多种多样,如玉米、豆粕、鱼粉等,而这些原料的质量往往受到季节、产地等因素的影响,导致原料的营养成分和质量存在差异。
为了解决这个问题,饲料加工企业可以采取多种策略。
首先,建立稳定的原料供应渠道,与可靠的供应商建立长期合作关系,以确保原料质量的稳定性。
其次,加强原料质量检测,建立完善的原料质量监控体系,及时发现原料质量问题并采取相应措施。
此外,饲料加工企业还可以通过调整配方,合理选用原料,以降低原料质量不稳定性对饲料质量的影响。
其次,饲料加工过程中常见的问题之二是设备故障。
饲料加工企业通常会使用各种设备进行原料的破碎、混合、造粒等加工过程。
然而,由于设备使用频繁,长时间运转,设备故障时有发生。
设备故障不仅会导致生产停工,还可能对饲料质量产生负面影响。
为了解决这个问题,饲料加工企业可以采取一系列的措施。
首先,加强设备的日常维护保养工作,定期对设备进行检查和维修,及时发现并解决潜在的故障隐患。
其次,建立设备维修保养记录,对设备使用情况进行监控和分析,及时调整设备使用方式和维修计划。
此外,饲料加工企业还可以建立设备备件库存,以应对突发设备故障。
再次,饲料加工过程中常见的问题之三是饲料质量不稳定。
饲料质量的稳定性对于养殖业的发展至关重要,而饲料质量的不稳定性可能会导致动物的生长发育不良、免疫力下降等问题。
为了解决这个问题,饲料加工企业可以采取多种策略。
首先,加强生产工艺的控制,确保饲料加工过程中各个环节的操作规范和稳定性。
其次,加强质量检测,建立完善的饲料质量监控体系,对饲料的营养成分、微生物等进行全面检测,并及时调整生产工艺和配方。
谷物膨化机在谷物食品工业发展中的瓶颈问题分析

谷物膨化机在谷物食品工业发展中的瓶颈问题分析谷物膨化技术是一种先进的食品加工技术,广泛应用于谷物食品工业中。
通过高温高压处理谷物,使其发生膨胀变形,从而改善谷物的口感和可食性。
然而,在谷物膨化机在谷物食品工业发展中的过程中,出现了一些瓶颈问题,影响了谷物膨化技术的进一步发展。
本文将对这些瓶颈问题进行分析,并提出相应的解决方案。
首先,谷物膨化机在谷物食品工业发展中面临的一个重要问题是膨化品质的稳定性。
谷物膨化过程中,需要控制合适的温度、压力和时间,以保证膨化产品的质量。
然而,由于谷物的原料特性和工艺参数的复杂性,膨化品质的稳定性难以保证。
因此,需要对谷物的物理性质和膨化机的工艺参数进行深入研究,优化膨化过程的控制方法和设备,以提高膨化品质的稳定性。
其次,谷物膨化机在谷物食品工业发展中另一个瓶颈问题是能耗过高。
谷物膨化机在进行高温高压处理时,需要消耗大量的能量,这不仅增加了生产成本,还对环境造成了不可忽视的影响。
因此,如何降低谷物膨化机的能耗是一个亟待解决的问题。
一种解决方案是优化谷物膨化机的结构和工艺参数,以提高能量利用率。
另一种解决方案是利用新型的膨化机技术,如微波膨化技术或超临界流体膨化技术,来降低能耗并提高生产效率。
另外,谷物膨化机在谷物食品工业发展中的第三个瓶颈问题是生产能力的限制。
传统的谷物膨化机通常只能一次膨化处理一小批量的谷物,生产能力有限。
这对于大规模谷物食品生产的需求来说是不足够的。
因此,需要研发高效、大容量的谷物膨化机,以满足谷物食品工业不断增长的需求。
同时,还可以考虑采用自动化控制和智能化技术,提高生产效率和生产能力。
此外,谷物膨化机在谷物食品工业发展中还面临着食品营养价值损失的问题。
传统的谷物膨化过程中,由于高温高压处理,会导致谷物中的某些营养成分流失或破坏。
因此,需要研发新的膨化技术和加工方法,以减少谷物膨化过程中的营养损失。
一种解决方案是采用低温膨化技术或真空膨化技术,以降低对谷物的热处理程度,从而减少营养成分的流失。
饲料加工技术使用中的常见问题解析与解决方法

饲料加工技术使用中的常见问题解析与解决方法饲料加工技术是农业生产中非常重要的一环,它直接关系到畜禽的生长发育和生产效益。
然而,在饲料加工技术的使用过程中,常常会遇到一些问题,这些问题可能会影响到饲料的质量和效果。
本文将对饲料加工技术使用中的常见问题进行解析,并提供一些解决方法。
一、颗粒度不均匀颗粒度不均匀是饲料加工过程中常见的问题之一。
这可能是由于设备的不合理设计或操作不当造成的。
解决这个问题的方法有两个方面:一是优化设备结构,确保饲料在加工过程中能够均匀受力,避免颗粒度不均匀的情况发生;二是加强操作人员的培训,提高其对设备操作的技能和经验,确保操作的准确性和稳定性。
二、饲料发霉饲料发霉是饲料加工过程中常见的问题之一,这可能是由于原料质量不好、储存条件不当或加工过程中受潮等原因造成的。
解决这个问题的方法有多个方面:一是加强对原料的质量检测,确保原料的干燥度和卫生状况符合要求;二是改善储存条件,确保饲料在储存过程中能够保持干燥和通风;三是在加工过程中加入适量的防霉剂,防止饲料发霉。
三、饲料营养成分不均衡饲料营养成分不均衡是饲料加工过程中常见的问题之一,这可能是由于原料的选择不当、配方不合理或加工过程中营养成分的损失等原因造成的。
解决这个问题的方法有多个方面:一是加强对原料的选择和检测,确保原料的质量和营养成分符合要求;二是优化配方,根据不同畜禽的需求进行合理的营养配比;三是加强加工过程的控制,减少营养成分的损失。
四、饲料消化率低饲料消化率低是饲料加工过程中常见的问题之一,这可能是由于原料的选择不当、加工过程中的温度过高或饲料的颗粒度不合适等原因造成的。
解决这个问题的方法有多个方面:一是加强对原料的选择,选择易消化的原料,提高饲料的消化率;二是控制加工过程中的温度,避免过高的温度对饲料的消化性能造成影响;三是调整饲料的颗粒度,确保饲料的颗粒大小适中,有利于动物的消化吸收。
总之,饲料加工技术使用中常见的问题有很多,但只要我们能够认真分析问题的原因,并采取相应的解决方法,就能够有效地解决这些问题,提高饲料的质量和效果。
饲料膨化机一般故障及排除方法

饲料膨化机一般故障及排除方法1、加工大豆时膨化腔出料口不出料原因:短时间内喂料太多,造成堵塞排除方法:减少喂料速度。
2、加工大豆时膨化出的豆粉内有豆瓣原因:原料未经过粉碎或粉碎粒度过大,筛片漏料、破损等。
排除方法:检查粉碎机,更换新筛片。
3、膨化腔内温度达不到要求的额定温度原因:压力环配比直径过小或加入的蒸汽量不足,调质温度过低,或者压力环或螺头磨损。
排除方法:换成较大的压力环或提高调质温度,调质后的物料温度应在80℃-90℃。
保持膨化腔夹套内油度:第一块表温60℃,第二块表温100℃,第三块表温125℃,第四块表温145℃。
4、加工粉状膨化料时堵塞不出料或出糊状稀料原因:供水及蒸汽压力太小或太大,蒸汽量太小。
排除方法:调整好水或蒸汽压力。
5、产量下降,达不到产能原因:锥形压力环或磨损环磨损,或者螺头磨损严重。
排除方法:更换磨损件。
6、正常工作时突然不出料原因:1)短时间内进料太多。
2)异物堵塞出料孔。
排除方法:1)减慢喂料速度。
2)停机、拆开清理。
7、膨化出的颗粒直径太大或太小原因:出料端模孔太大或太小。
排除方法:按要求配置适当的出料模孔尺寸。
8、加工大豆时膨化豆粉从进料口反喷出来原因:1)进料过快过多。
2)出料不畅或堵塞。
3)螺头与压力环配置不当。
4)膨化腔磨损严重。
排除方法:控制好进料速度和进料量,并将出料螺塞与轴端锥形钉的距离按故障1要求调整;检查后重新装配,更换新膨化腔。
9、产品排出模孔之前被堵塞原因:1)原料的粒度相对模孔尺寸来说显的太大。
2)水量不够,不足使物料产生流动。
3)挤压室结构布置不合理。
4)压力环直径有可能太大。
排除方法:1)粉碎到合适的细度。
2)在产品进入膨化筒体的初期就开始加水。
3)按合理的方式对压力环、螺头进行布置。
4)更换直径较小的压力环。
10、产品成形较差 (乳猪料)原因:1)原料配方不适当。
2)加工时温度太高或太低。
3)物料进入量不衡定(忽大或忽小)。
4)产品水份含量太高或太低。
饼干常见质量缺陷及控制办法.

饼干收缩变形
(一)原因分析 在面带压延和运送过程中面带绷得太紧。 面筋筋力过强,面团弹性过大。 面带始终沿同一方向压延,张力不均。 (二)控制方法 调制面带,在经第二和第三对轧辊时要有一 定下垂度,帆布带在传输面带时应保持面带呈松 弛状态。 可适当增加面团改良剂的用量或增加调粉时 间,并适量增加淀粉。 面带折叠时不断转向90度角。
(一)原因分析 面筋筋力过小,面团持气能力较差,成型时 易断片,产品易破碎。 加水量太少,面团过硬,压延后面片结合力 差,容易断面片、断面头,成型后生坯延展性差, 烘烤时饼坏不易起发,饼干表面光泽较差。 油脂少时会造成产品严重变形,口感差,表 面干燥无光泽。 (二)控制方法 增加使用面筋含量高的面粉。 增加水和油脂用量。
饼干起泡
(一)原因分析 烤炉前区温度太高,尤其面火温度太高。 面团弹性太大,在烘烤时面筋挡住气体通道 而引起表面起泡。 膨松剂分布不均匀。 辊轧时面带上撒粉太多。
(二)控制方法 控制烤炉温度,不可一开始就很高温度,面 火要逐渐提高。 降低面团弹性,并用带较多针孔的模具。 注意使膨松剂分布均匀,对已结块的膨松剂 应粉碎过筛后再用。 尽量不撒粉,或控制尽可能少撒粉。
饼干表面不上色
(一)原因分析 饼干中糖用量太少。
(二)控制方法 增加转化糖或饴糖的用量。
饼干冷却后不松脆
(一)原因分析 饼干太厚而炉温太高,烘烤时间短,造成皮 焦里生,内部水分太多。 烤炉排气不畅,造成后段炉温太高。
(二)控制方法 控制饼干厚度,适当调低炉温。 保持排气畅通。
饼干易碎、裂缝、表面无光泽
பைடு நூலகம்
加水量太少面团过硬压延后面片结合力差容易断面片断面头成型后生坯延展性差烘烤时饼坏不易起发饼干表面光泽较差
- 1、下载文档前请自行甄别文档内容的完整性,平台不提供额外的编辑、内容补充、找答案等附加服务。
- 2、"仅部分预览"的文档,不可在线预览部分如存在完整性等问题,可反馈申请退款(可完整预览的文档不适用该条件!)。
- 3、如文档侵犯您的权益,请联系客服反馈,我们会尽快为您处理(人工客服工作时间:9:00-18:30)。
影响膨化料加工质量缺陷的分析的对策
膨化水产饲料是顺应全球渔业养殖用饲料向着低污染、低浪费、高效率、高转化的良性发展需求,正被广大养殖户逐步接受和推广的新型水产饲料。
近年来,我国水产饲料产量增长迅速,对虾及珍贵特种水产用饲料发展很快。
在这些特种水产饲料中,挤压膨化颗粒饲料已成为主要的产品形式。
由于各挤压膨化水产饲料生产线多为近几年新建,特别是挤压膨化机的操作条件的控制技术尚不完善,国内众多饲料生产厂家对膨化水产饲料的加工工艺及生产特性尚处于不断摸索和发展阶段,所以各厂家生产的饲料产品的加工质量就会有较大的差异。
即使同一厂家在不同批次生产的同品种产品的质量也可能有较大波动。
无法保证物理特性的稳定。
经过多年的生产实践经验。
认为膨化料在加工过程中一般出现如下缺陷:
1) 颗粒大小不均、长短不均; 2) 颗粒气孔多; 3) 颗粒变形; 4) 颗粒硬度不够; 5) 颗粒耐水性不好,粘弹性差; 6) 颗粒切口不整齐、斜口; 7) 颗粒膨化胀不高;
8) 颗粒有沉水现象;
9) 颗粒一头大一头小;
10) 颗粒形成双切面内凹形;
11) 颗粒带尾巴;
12) 颗粒表面脱皮。
笔者经过多年的生产实践经验,在本文中总结了在膨化料的加工过程中常出现的一些问题,并提出相应的解决措施。
1、颗粒大小不均,长短不均
饲料颗粒大小不一,长短不均,不仅影响饲料美观,而且会影响其适口性和耐水时间的不
2、颗粒气孔多
颗粒气孔较多,外表毛糙不仅影响饲料的外观,而且饲料在运输过程中容易破碎成粉,造成不必要的浪费。
在饲料投喂过程中不易下沉,漂浮时间长。
3、颗粒变形不圆
颗粒变形,可能是由于模孔的变形,或者是由于水分过高,出模时在输送过程中被挤压变形。
所以对于刚出模的高温膨化饲料最好采用气力输送,这样不仅可以使颗粒的表面快速形成一层胶质包裹,减少颗粒的破碎,而且还可以圆整颗粒的造型。
但是气力运输过程中颗粒的水
4、颗粒硬度不够
饲料硬度是饲料对外压力所引起变形的抵抗能力。
饲料硬度不够,会导致搬运中饲料变形,从而影响饲料的外观。
导致饲料在未被摄食前就溶散在水中,也可能是水份较大,饲料不易存
5、颗粒耐水性不好,粘弹性差
饲料的耐水性是指饲料在水中的抗溶蚀能力,通常以在规定条件下饲料在水中的溶失率表示。
饲料耐水性差会导致饲料在未被摄食前就溶散在水中,造成不必要的浪费,并且污染水质。
6、颗粒切口不整齐、斜口
生产的饲料应切成外观整洁的颗粒,不规整、变形的颗粒,影响饲料的外观。
一般是切口
7、颗粒膨化率不高
饲料过硬,溶水时间过长,影响其适口性和消化率。
高含量的类脂化合物会减少膨胀,当脂肪含量在17~22%时,产品膨化不大或者不膨化。
颗粒膨化率不高会导致饲料在水中漂浮
8、颗粒有沉水现象
颗粒有沉水现象,可能是膨化系数过低,物料比过重等原因。
一些颗粒浮水料如果出现沉
9、颗粒一头大一头小
10、颗粒形成双切面内凹形
颗粒双切面内凹形,饲料膨化不均匀,水和蒸汽比例不合理,通常就会出现这种情况。
不
11、颗粒带尾巴
颗粒带尾巴,具有多方面的原因,主要是切刀的问题。
饲料颗粒带尾巴,不但影响饲料的
12、颗粒表面脱皮
饲料表面脱皮极容易在运输过程中产生粉尘,表面脱皮可能和膨化中缺少水分、有关,也可能受到加工工艺中模具、切刀的影响。
不但影响饲料的外观质量美观,还会导致饲料粉多。
水分添加过量,形成的物料又太软,容易变形,一般应在25~30%的添加水分为宜。
表面脱。