焊装生产线简介
焊装输送线简介
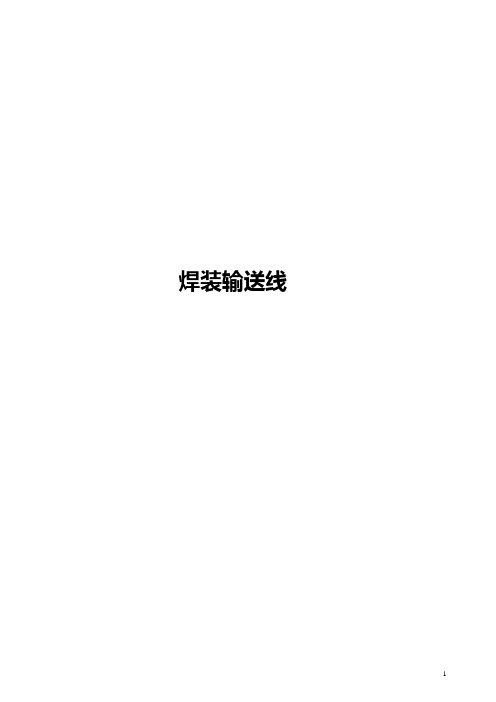
焊装输送线焊装输送线2009.6.24修改都韧刚车身焊装输送线是装焊生产线的一个重要组成部分。
是实现各工位之间的制件传送的装置。
是汽车制造过程中一个十分重要的生产环节。
随着现代汽车工业的飞速发展,对制造工艺过程的机械自动化要求愈来愈高。
为了提高生产率,减轻工人的劳动强度,提高汽车的质量和产量,应当尽量采用并且不断研制先进的机械自动化生产设备。
输送装置提高了生产率,改善了劳动条件,保证了作为产品的汽车的质量和产量。
根据输送线与装焊制件的空间相对位置,可以分为底置输送线和顶置输送线。
顶置输送线又称为空中往复式,一般分为吊具直送式和上夹具平移式。
吊具直送式是在每个工位上方安装一套吊具,利用这些吊具在空中轨道上的同步往复运动来输送制件。
每当一个装焊循环完成后,吊具自动抓住制件使其脱离升降台,并将制件送至下一工位的升降台面上,然后吊具回位。
上夹具平移式是在每个工位上方安装一套带提升装置的上夹具。
每当一个制件的装焊循环完成后,提升装置下降,通过上夹具将工件夹紧提升至平移高度,平移装置带动提升装置将制件平移至下一工位。
输送到位后提升装置下降,上夹具松开,将制件放入夹具体定位后,提升装置再升起,与上夹具返回初始位置。
这种输送方式对于某些底面形状复杂、不宜用往复杆输送的大总成如:轿车底板、中、轻型载重车的驾驶室等,比较适用。
但是,因为输送装置整体安装在空中桁架上,位于制件的上方,故对厂房高度上有要求。
同时,从安全角度考虑,应该在空中设置安全护网,防止制件掉落伤害工作人员。
底置输送线是常用的输送形式,根据输送线的结构形式,大体可以分为:举升直送式、滑橇输送式、工艺小车输送式、滚床输送式、自动导向小车输送式及往复杆输送。
由于底置输送的常用性以及结构形式的多样性,下面着重就底置输送的各种形式进行介绍。
一、举升直送式举升直送式是安装在夹具举升支架上的输送体升起后,将制件举起脱离夹具,直接将制件输送至下一工位的输送方式。
根据输送体的不同,可以分为滚轮输送和皮带输送。
焊装生产线的概况及机器人的应用

汽车发展来看 , 在初期阶段 , 主要 应 用 直 通 式 生 产 线 , 在6 0年 代 和7 0年 代 初 期 , 曾经较多 地采用随行 夹具生产线 , 但 由 于 随 行 夹具 体 积 大 、 结构 复杂 、 运 动惯性大 。 难 以 实 现 多 品种 生 产 及 机 器人配套使用等缺点 , 因而 。 到 了 7 O年 代 中后 期 , 各 主要 汽 车 厂 在 技 术 改 造 中 又 重新 发展 了 贯 通式 生 产 线 。特别 是 随 着 市 场 对 汽 车 产 品 多 样 化 的要 求 及 机 器 人 大 量 应 用 于 汽 车 车 身 的 焊 接 。更 为 贯 通 式 生 产
高焊接质量 、 降低焊接成 本 。 实 现 焊 接 自动 化 方 面 扮 演 着 重 要 角
色。
步。 从 国 外 引进 了轻 型 车 、 面包 车 、 轿 车 等各 类 车 型 的 汽 车 。 各 主 要 汽 车 厂 家 形 成 了 一 定 的 生 产 规 模 。基 本 上 具 备 了一 整 套 较 为 完善的生产 、 管 理 及 技 术 保 证 体 系 。纵 观各 汽 车 厂 的 状 况 可 知 , 现阶段主要依靠进 1 3 1 国外 的 硬 件 以 保 证 企 业 的生 产 .这 种 情 况 在 车 身 焊 装 中更 为 明显 。靠 从 国外 全 套 引 进 的方 式 维 持 汽 车 工
随 着 汽 车 工 业 的发 展 。 焊 接线 的形 式 也 发 生 了 变化 。 从 国外
三、 焊 装 夹 具 的 安 装调 试 及 设 计 配 合 服务
焊 装 夹 具 的 安 装 调 试 是 保 证 焊 装 夹 具 用 于 生 产 的 重 要 一
一体自动化焊接生产线

一体自动化焊接生产线一体自动化焊接生产线是一种高效、精确、可靠的焊接设备,能够实现对工件的自动化焊接操作。
该生产线采用先进的机械、电气和控制技术,能够提高焊接质量和生产效率,降低人工成本和生产周期。
一体自动化焊接生产线由多个工作站组成,每一个工作站都具有特定的功能和任务。
下面将详细介绍每一个工作站的功能和工作流程:1. 工件上料站:工件上料站是生产线的起始点,用于将待焊接的工件放置在焊接夹具上。
该工作站通常配备有自动上料机器人,能够准确地将工件从传送带上取下并放置在焊接夹具上。
同时,工件上料站还可以通过视觉识别系统对工件进行检测和定位,确保工件的正确放置。
2. 焊接工作站:焊接工作站是生产线的核心部份,用于实现工件的自动化焊接。
该工作站通常配备有多个焊接机器人,能够根据预设的焊接程序和路径对工件进行焊接。
焊接机器人具有高精度和高速度的特点,能够实现对工件的复杂焊接操作。
在焊接过程中,还可以通过传感器对焊接质量进行监测和控制,确保焊接接头的质量。
3. 检测工作站:检测工作站用于对焊接接头进行质量检测和评估。
该工作站通常配备有视觉检测系统和超声波检测系统,能够对焊接接头的外观和内部进行检测。
通过图象处理和信号分析,可以判断焊接接头是否存在缺陷和变形。
同时,检测工作站还可以记录检测结果并生成相应的报告,便于后续的质量追溯和分析。
4. 下料工作站:下料工作站用于将焊接完成的工件从焊接夹具上取下,并进行后续的处理和包装。
该工作站通常配备有自动下料机器人,能够快速而准确地将工件取下并放置在传送带上。
同时,下料工作站还可以进行工件的清洁、打磨和包装,确保工件的表面质量和保护。
除了以上几个主要工作站外,一体自动化焊接生产线还可以根据具体的生产需求配置其他辅助工作站,如工件装配站、焊缝磨削站等。
这些工作站可以根据生产线的布局和工艺流程进行灵便组合和调整,以满足不同类型和规格的工件焊接需求。
总结:一体自动化焊接生产线通过机械、电气和控制技术的集成应用,实现了工件的自动化上料、焊接、检测和下料等工艺操作。
焊装生产线规划及布置概述

焊装生产线规划及布置概述焊装工艺作为汽车行业四大工艺之一,其重要性不言而喻,其肩负着车身成型,为整车提供支撑框架的重要使命,除了要保证外观造型之外,还必须保证总装所有零部件安装点的精度,故其工艺远比其他三大工艺复杂,生产线的规划及布置不仅需从精度保证、生产效率、配送物流、仓储存放诸多方面权衡考虑,也受限于厂房面积及结构、涂装连廊等现有条件。
没有十全十美的布置方案,只有当前最合适的布置方案。
作为四大工艺中最复杂的工艺,生产线规划及布置概括起来主要从几个步骤着手:(1)产能计算及节拍确定;(2)主线输送方式选择;(3)工序拆分及工位数量确定;(4)侧围总成配送方式;(5)总拼工位结构方式;(6)物流仓储规划;(7)平面布置及仿真验证。
1.产能计算及节拍确定规划第一步,必须有市场部及公司战略规划部门输入的年产能要求,根据产能要求计算出生产节拍及单工位作业时间,作为工序拆分及工位数量确定的主要数据,其计算方法如下:生产节拍(JPH)——每小时生产台数。
生产天数——365个自然天数,扣除国家法定节假日及双休日,年生产天数大致按251天计算。
每天生产时间——单班生产时间8小时、双班16小时、三班22.5小时计算。
设备开动率——设备有效开动比例,焊装车间设备开动率规划时一般设定为90%。
2.主线输送方式选择主线输送方式决定了输送时间及效率,决定了工位的有效作业时间,是工序拆分及工位数量确定的依据。
主线输送方式目前常用的有往复杆输送、滚床滑撬输送、随行夹具输送3种方式,具体选用哪种方式需结合效率、节拍、成本综合考虑。
(1)往复杆输送优点:价格低廉,输送可靠,占地面积小。
缺点:输送效率较低,一般往复杆的输送时间达到28s(含举升、输送、下降、回退动作),只能直线输送,如工位数较多是只能分段布置,输送精度较差,需配合定位夹具使用。
适用范围:一般用于低节拍、工位数量相对较少的生产线,如输送工位超过10个不建议选用。
(2)滚床滑撬输送优点:价格适中,输送可靠,输送效率较高(输送时间可达到16s 左右),输送不受距离限制,可任意转弯、布置灵活。
汽车车身焊装生产线和焊装夹具简介

汽车车身焊装生产线和焊装夹具简介赵静1张俊华2李春植2邓早春3(1.烟台大学机电汽车工程学院04级研究生,烟台264005;2.烟台大学机电汽车工程学院,烟台264005;3.烟台富士沃森技术有限公司,烟台264005)摘要:对汽车车身焊装生产线和车身焊装中的夹具进行综述,其中包括焊装生产线的发展、组成等和焊装夹具的作用、特点、分类和设计要求等。
关键词:车身焊接焊装生产线焊装夹具ProductionLineofWeldingforAutoBodyandWeldingJigZHAOJing1,ZHANGJunhua2,LIChunzhi2,DENGZaochun3(1.SchoolofElectromechanicalandAutomobileEngineering,YantaiUniversity,Yantai264005;2.SchoolofElectromechanicalandAutomobileEngineering,YantaiUniversity,Yantai264005;3.FUJIWILSONENGINEERINGCO.LTD)Abstract:Thepapersimplyintroducedtheproductionlineofweldingforautobodyandweldingjig,includingdevelopment,makingupoftheformerandthefunction,characteristic,classanddesignrequireofthelatter.Keywords:Body,Welding,Productionlineofwelding,Weldingjig引言汽车是重要的运输工具,是科学技术发展水平的标志。
汽车工业在世界制造业的进步中起着特别重要的作用。
由于它的超大生产规模、资金和技术的高度密集以及强大的经济和辐射带动作用,使它在机械制造业中扮演着举足轻重的角色。
焊装生产线简介

焊装生产线简介焊装生产线是一种用于汽车制造等行业的生产工艺流程。
它是将不同零部件通过焊接和装配等工艺连接在一起,最终形成一个完整的产品。
焊装生产线是一个自动化程度较高的生产线。
它通常由多个工作站和各种设备组成,包括焊接机器人、传送带、夹具等。
每个工作站都有特定的任务,例如焊接、装配、检测等。
在整个生产过程中,零部件会按照预定的顺序从一个工作站传送到另一个工作站,经过各种工艺处理,最终形成一个成品。
焊装生产线具有高效率和高质量的特点。
由于采用了自动化设备,生产线的生产效率会大大提高,可以实现连续、稳定的生产。
而且,焊接机器人的使用可以保证焊接质量的一致性和精度,避免了人为因素对焊接质量的影响。
这样不仅可以提高产品的质量,还可以减少因人为操作而带来的错误和浪费。
焊装生产线还具有灵活性和可扩展性。
由于生产线的设备和工作站之间是相互连接的,所以可以根据需要对生产线进行灵活调整和扩展。
如果需要增加产能,只需要增加相应的设备和工作站,而不需要对整个生产线进行大规模改造。
这样可以更好地适应市场需求的变化,提高企业的竞争力。
为了保证焊装生产线的正常运行,需要对其进行维护和管理。
维护包括设备的定期保养和检修,以确保设备的正常运行和延长设备的使用寿命。
管理包括对生产线的调度和监控,以确保生产线的高效率和高质量。
此外,还需要对操作人员进行培训,提高他们的操作技能和安全意识,以确保生产线的安全运行。
焊装生产线是一种高效率、高质量的生产工艺流程,可以大大提高产品的生产效率和质量。
它具有灵活性和可扩展性,可以根据需要进行调整和扩展。
通过维护和管理,可以确保焊装生产线的正常运行和安全性。
在未来的发展中,焊装生产线有望继续发展和完善,为各个行业的生产提供更好的支持和保障。
焊装车间介绍

1.3、焊接检验
• 介绍: • 破检设备,
• 功能: • 对车身的焊接质量进行检验的设备
,主要采用破钳对随机抽取的车身 进行破坏性检验,检查每一个焊接 焊点的质量。保证焊接强度,提高
车身焊接强度使用
1.4、焊接过程气体压力的控制
• 介绍: • 对焊接过程采用的压缩空气的压力
保证。
2.2、柔性化车身生产线
• 介绍: • 焊装三车间为两个平台的车型,S和
M平台,其中S平台三中车型S12、 S16和S21,三款车型共用一条主线 生产,实现主线的车身夹具的柔性 化共用,该主线为韩国的VETEC公 司设计的主线夹具;M11和M12两 款车型共用一条柔性化主线,共用 的夹具为意大利柯马公司生产的。
德国的德玛格品牌。 • 功能:
• 重物的搬运采用机械化,减少操作 者的工作强度,同时也减少了员工 搬运过程中造成零件的变形和磕碰 的质量问题。
2.4、自动化转运
• 介绍: • 主线的车身的自动化转运采用的是
滑橇的方式,左右侧围的搬运采用 的沈阳新松的搬运小车,白车身总 成的搬运采用是摩擦链的方式,主 要是在安全性方面,噪音方面有很
1.2、螺栓螺母的防错漏装
• 介绍: • 该设备叫螺柱焊焊接计数器,螺栓
螺母的装配和焊接通常都是人工操 作的,在人工操作的安装设备和焊 接设备上安装PLC,实现焊接的计 数功能,焊接一次,此设备计数一
次,并有错误报警功能。 • 功能:
• 螺柱焊的焊接设备上安装螺柱焊焊 接计数器,实现员工焊接防错功能 ,保证任何一个车身上不会出现漏 螺柱焊的错漏装问题。 • 注:
都可提供无限的便携性。 功能:
• 对车身车辆数据达到0.001mm的 测 量要求,完全满足焊装车间工装的 日常标定
焊装介绍

参观讲稿——焊装车间篇(责任编辑张家栋)概况轿车二厂焊装车间于2003年7月开始动工,2004年7月正式投产,车间占地面积120,550 m2,现有员工5198人,目前主要生产PQ34平台的宝来,PQ35平台的速腾、高尔夫A6、GTI 及PQ46平台的迈腾和CC车型。
车间设计产能为33万辆/年,通过不断地技术改造和产能优化提升,目前车间产能已达到约1600辆/天。
焊装车间是整车制造四大工艺(冲压、焊装、油漆、总装)中的第二环节,通过焊接、压合、装配等工艺完成白车身的制造。
简单来说,焊装车间输入的是各种零散的零件,包含我们冲压车间生产的自制件,配套厂家提供给我们的的外委件和外协件,以及直接国外进口的CKD 件,经过点焊、激光焊等一系列工艺后,焊装车间将三种来源不同的零散的零件最终组合成一部完整的白车身整车,提供给整车制造的下一道工序——涂装车间。
工艺、技术和设备亮点焊装车间白车身的制造工艺流程为:在下部工段将前后地板及四根纵梁组成下部一总成,下部一总成加上左右前后四个轮罩及仪表板支架和后围板,组成下部二总成,下部二总成通过空中滑橇运输到主焊线,在主焊线上进行整个下部及左右侧围和顶盖的合成焊接,焊接完后的白车身骨架送到装配线上进行四个车门、前后盖及翼子板的装配,同时进行间隙和平度的调整,装配线调整完之后将白车身送往修磨线进行表面质量及焊接质量的检查、调整及修磨,检查调整合格后,通过空中滑橇将白车身总成发往涂装(油漆)车间。
焊装车间目前总共有激光焊机57台,FANUC、KUKA、SEF等机器人共362台,无论是设备的数量还是设备的先进程度,焊装车间都处于国内一流的水平。
车间通过机器人点焊、激光焊、螺柱焊、MIG焊、MAG焊、自动涂胶、TOX铆接等先进的工序和工艺,确保了我们所有大众车白车身的精确性、可靠性和安全性。
如我们现在看到的迈腾(高六)侧围工段,就采用了先进的热成型钢板和激光焊接技术,这些颜色为黑色的钢板就是传说中的热成型钢板,它采用欧洲钢铁巨头帝森-克虏伯的技术,通过将强度达800-900 MPa的特殊钢板经过950℃高温约4分钟的热处理后由模具成形,再由激光切割设备加工所需的孔与外形尺寸,最近达到1300-1600 MPa的强度,即每平方厘米可以承受10吨的压力不变形。
焊装生产线简介

焊装生产线焊装生产线一、车身装焊生产线的形式1、装焊生产线的组成一条装焊生产线是汽车白车身全部成型的总称。
它由总成线和许多分总成组成。
每一条总成线或分总成线是由若干个工位组成,线间、工位间是通过搬运机、机器人等搬送设备实现上下料和零部的输送,以保证线内工位工作的连贯性。
分总成线包括许多独立的组件焊装工位,每个工位由定位夹紧夹具、自动焊接设备及检测装置等设备组成,另外还有一些供气供水供电装置。
2、装焊生产装线的形式及发展现有的装焊生产线可归纳为下列几种基本形式。
椭圆形贯通式地面环形装焊生产线环形地下环形矩形转台式“门框”式随着汽车工业的发展,装焊线的形式也发生了变化。
在初期阶段,主要用直通式生产线(相当于简化的贯通式生产线),在60年代~70年代曾较多的采用环形生产线。
但是由于随行夹具体积大、运动惯性大、结构复杂,难以实现多品种生产及机器人配套。
到了80年代,各汽车生产公司重新发展了贯通式生产线。
特别是随着市场对汽车产品多样化的要求及机器人大量应用于汽车车身焊接,更为贯通式生产线提供了新的应用范围及发展领域。
现在贯通式为应用得最广泛的生产方式。
二、各种装焊生产线的特点1、贯通式生产线贯通式生产线是指制件的定位夹紧系统与工位间输送系统成分离状态。
生产线包括:制件的定位夹紧系统(焊接夹具)、工位间输送系统、输送杆、驱动系统、自动上下料的机械化系统等。
工作时,制件被输送系统中贯通式往复杆的移动输送至下一工位的夹具中,而所有的装夹定位的工装都分别固定在工位上。
其特点为:a、它适应于多点焊机配置,能满足悬挂点焊机的手工焊接、半自动焊接、全自动焊接等多种操作方式。
b、当车身横向流水时,更有利于分总成的机械化自动上下料。
便于提高自动化程度。
c、输送系统中驱动和输送部分结构较简单,便于调试。
d、焊接夹具固定在工位上,利于保证车身焊接质量。
e、占地面积较小,有利于合理布局和物流。
v1.0 可编辑可修改图1为吉利厂总装线的一部分:图1鉴于贯通式生产线这么多优点,它不但是现在,也是今后一段时间里国内外各汽车公司采用的主要方式之一。
汽车车身焊装线

各个工位的base板通过连接板连在一起构成了整个汽车焊装线的支撑装置,它既要支撑整个传输装置又要支撑焊装夹具。此外,为了保证夹具与车身零件的基准一致,在base板上按照设计基准画出基准刻度线。图中的调平装置主要起到对整个传输装置调平作用。
base板结构
1 base板2调平装置3 base板连接板
汽车车身焊装线
一、汽车车身焊装线的组成
汽车车身焊装生产线是轿车、微型客车等车型生产过程中的重要生产线之一,从汽车工业的发展历史来看,车身焊装线经历了20世纪50~60年代手工焊接线→20世纪70年代的自动化刚性焊装线→20世纪80年代以后的机器人柔性焊装线阶段。
就每条焊装线而言,它由焊接夹具、传输装置、焊接设备(焊枪、焊接机器人)构成;就整个汽车车身焊装线而言,它大体包括车身侧围总成线、车身门盖总成线、底板总成线、车身焊装主线等(目前尚无绝对的概括)。其中每部分又有相应的主线、子线、左右对称线和独立岛。根据生产节拍、自动化程度及生产方式等的不同,每条线又分为若干个工位;各工位间通过传输装置连为一体,每工位负责完成一部分工作。具体如图1:
以上所介绍的是传输装置的主要结构,通过除此以外还有一些辅助装置:
6,缓冲锁紧装置(如下图)
缓冲锁紧装置
1汽缸支撑架2限位块3汽缸4缓冲器5缓冲器支架6行程开关
焊装线传输装置共设置了4个缓冲锁紧装置分别分布于顶升框架的两端,主要是对“移动滑板”的水平运动起到缓冲和锁紧作用。具体过程是:当“移动滑板”快要运动到传输装置的末端时,便与缓冲器接触从而减缓运动速度;当“移动滑板”运动到传输装置的末端后,行程开关命令汽缸夹紧固定在移动滑板上的限位块从而起到锁紧作用。该装置实现了汽车焊装线传输装置慢启、慢停的进退动作要求,保证了传输装置运行安全、可靠。
焊装车间简介

2015年6月31日
一工厂焊装车间
一、焊装车间简介
一工厂焊装车间于2004
年7月15日建成投产。面积约3.7 万平方米,总投资6.5亿元,年 生产纲领为26万辆,现生产能力 26万辆。引进了世界先进的日本 自动化焊接、压合生产线共11条, 共有112台机器人;德国伺服电 动压合线12条。 目前车间有奔腾、马自达二条 生产线,现可混流生产8大品种 的车型,生产节拍1.08分,两班 制日产能900台。 车间现有员工1126人,双班生产; 男员工:1060人, 女员工:66人。 车间主任/副主任:共3人 维修、工艺技术人员:7人 专项管理:8人 办事员:2人; 班长:34人 生产工人:1062人
一工厂焊装车间
车间目前生产马自达 J56、马自达 J61、奔腾 B70 、奔腾 B50 四种车型,马自 达 J56 车身共有焊点 4176 个,螺柱焊 49 个、凸焊螺栓及螺母 106个,二氧 化碳焊焊缝长 1.07 米,涂胶长度 23.4 米;奔腾轿车采用与 M6 类似的生产 工艺,点焊4368点,二氧化碳焊焊缝长1.23米,涂胶23.6米。采用具有国 际先进水平的电动伺服压机进行门、盖总成压合,包边质量优异。 主焊线关键工序采用伺服焊机,焊接质量稳定。调整线四门两盖的装调工位 依据专门的内间隙样板、楔形尺、段差尺等进行间隙和平面度控制,保 证每一台从焊装车间流出的白车身完全符合质量标准。 现有工种13个:维修钳工 维修电工 电焊工 气焊工 二氧气体保护焊 工序 点焊工 调整工 修磨工 螺柱焊工 机器人操作工 擦净工 钣金装配工 电 动牵引车操作工。
一工厂焊装车间
4、压合工艺
机器人滚轮压合
伺服电动专机压合
机器人点焊
机器人二氧弧焊
一工厂焊装车间
焊接生产线

第三章 车身装配焊接生产线§ 3.1 焊接生产线基础§ 3.2车身装焊生产线一、贯通式装焊线一、焊接生产线的组成 二、焊接生产的类别和特点1.固定式装焊:单件生产 2.简易的装焊线:适用于小批量生产 3.多工位流水式装焊线:中、大批生产三、焊接生产线基本要求由固定装配台,悬挂式点焊机及间隙式双轮链式传动机构组成。
全线有六个工位,四个装焊台,一个电弧焊转台、一个翻转电弧焊台。
线上配有16台悬挂式点焊机和两台直流弧焊机。
生产节奏为4min/辆, 全线共18-20人。
工作内容: 1工位:地板总成、前、后围骨架总成装焊到一起,以地板及门洞定 位,点10点,再装门铰 2工位:电弧焊工位,设有顶起及回转夹具。
骨架总成加强处的焊接。
3工位:焊接地板和发动机挡板连接处。
4工位:覆盖件装焊工位,前围(上、左、右盖板总成)、顶盖总、下 后围及风窗支柱等装配到驾驶室骨架总成上,并焊接门洞及前风窗口 的焊点。
5工位:装配焊接左、右门槛总成,并焊接后风窗口,前围盖板和发动 机挡板连接处,下后围和地板连接处。
6工位:翻转90º,焊接门槛和前、后围连接处,并用电弧焊加固地板连 接板、发动机挡板和地板处。
二、环形线装焊线 一次性装配定位,装焊件与夹具一起运动,夹具又叫随行 夹具。
夹具易调整,质量稳定,但夹具数量多,且电、气、 液等动力连接问题复杂,造价很高。
环形装焊线 ①地下环形 节省车间面积,造价高②地面环形 占地面积大,造价低1PDF created with pdfFactory Pro trial version ③转台式装焊线 转台式装焊线适于轻的、工位少的中小型件装焊④ “门框 ”式装焊线 用于轿车,装左右侧围 “门框 ”式特点: ( 1)大大简化了车身装焊线夹具 ( 2)侧围、车身调整都集中在一起,同步生产,节省面积 ( 3)从侧围到组装只需一次定位,保证质量精度 ( 4)适应车身的改进改型时,只顺换侧围 “门框 ”,而不需 更换随行夹具三、柔性装焊线2PDF created with pdfFactory Pro trial version § 3.3车身装焊生产线的发展趋势机器人装焊 用计算机控制,机器人操作 优点: 1.由于机器人的动作是可编程序的,因此改型生产的适应性 好 2.机器人可以焊一些人工不易焊的部位,即节省了人力、又 提高了自动化程度 3.点焊质量稳定、焊点的点距规则3PDF created with pdfFactory Pro trial version 。
一体自动化焊接生产线

一体自动化焊接生产线一体自动化焊接生产线是一种高效、精确且可靠的焊接生产线,能够实现对各种金属工件的自动焊接操作。
本文将详细介绍一体自动化焊接生产线的标准格式,包括其定义、组成部份、工作原理、优势和应用领域等方面的内容。
一、定义一体自动化焊接生产线是指将焊接机器人、焊接设备、输送设备、控制系统等多个组成部份有机地结合在一起,形成一个完整的自动化焊接生产线。
通过集成化的设计和自动化的操作,实现对工件的高效、精确和连续焊接,提高生产效率和产品质量。
二、组成部份一体自动化焊接生产线通常由以下几个组成部份组成:1. 焊接机器人:负责完成焊接操作的机器人,具有高精度和高速度的特点,能够根据预设的程序完成焊接任务。
2. 焊接设备:包括焊接电源、焊枪、气体保护系统等,用于提供焊接所需的能量和材料。
3. 输送设备:用于将待焊工件从一个工作站输送到另一个工作站,实现焊接过程的连续进行。
4. 控制系统:用于控制整个焊接生产线的运行,包括机器人控制、设备控制、输送控制等。
三、工作原理一体自动化焊接生产线的工作原理如下:1. 工件上料:待焊工件通过输送设备从上料区域送入焊接区域。
2. 焊接操作:焊接机器人根据预设的程序,将焊枪对准工件进行焊接操作。
焊接设备提供所需的能量和材料,实现焊接过程。
3. 检测与质量控制:通过传感器和视觉系统对焊接质量进行检测,确保焊接质量符合要求。
4. 工件下料:焊接完成后,工件通过输送设备从焊接区域送入下料区域。
四、优势一体自动化焊接生产线具有以下优势:1. 高效性:通过自动化操作和连续化生产,大大提高了焊接生产效率。
2. 精确性:焊接机器人具有高精度和高重复性,能够实现精确的焊接操作。
3. 可靠性:通过集成化的设计和自动化的控制,减少了人为因素的干扰,提高了焊接质量的稳定性和可靠性。
4. 安全性:自动化操作减少了人员的直接参预,降低了工作风险,提高了工作安全性。
五、应用领域一体自动化焊接生产线广泛应用于各个行业的焊接生产中,特殊是对焊接质量和生产效率要求较高的领域,如汽车创造、航空航天、电子设备、家电创造等。
焊装车间介绍范文

焊装车间介绍范文焊装车间是制造业中的重要环节之一,主要负责产品的焊接和装配工作。
本文将对焊装车间的相关内容进行介绍。
一、焊装车间的作用焊装车间是将材料通过焊接工艺进行连接,形成一个整体的工作场所。
焊接是一种常用的工艺,用于将两个或多个金属部件连接在一起,使其具有一定的强度和稳定性。
焊装车间的作用包括:1.进行产品的焊接工作,保证产品的质量和稳定性。
2.进行产品的装配工作,使产品具备完整的功能。
3.进行产品的表面处理工作,提高产品的外观和质感。
4.进行产品的检测和质量控制工作,确保产品符合标准和需求。
二、焊装车间的设备和工艺1.设备:焊装车间需要配备一系列的设备,如焊接机、割炬机、切割设备、钢板剪切机、卷板机、压力机等。
这些设备将极大地提高焊装工作的效率和质量。
2.工艺:焊装车间需要根据产品的要求选择适当的焊接工艺,如手工焊接、气体保护焊接、电弧焊接等。
同时,还需要合理安排焊装工序、流程和操作步骤,确保产品的一致性和稳定性。
三、焊装车间的工作流程焊装车间的工作流程可以分为以下几个步骤:1.材料准备:包括材料的选型和采购,以及对材料进行切割、成型等工艺处理。
2.焊接准备:包括对焊接设备进行调整和预热,以及焊材的准备、检查和配置等。
3.焊接加工:按照产品的要求进行焊接工艺的操作,完成焊接连接。
4.装配调试:对焊接完成的产品进行装配和调试,确保产品的功能正常。
5.检测和质量控制:对焊接和装配完成的产品进行检测和质量控制,确保产品符合标准和需求。
6.表面处理:对产品的表面进行处理,如喷涂、镀层等,提高产品的外观和质感。
7.包装出库:对产品进行包装和出库,保证产品的安全度和完整度。
四、焊装车间的管理和优化焊装车间的管理和优化是确保产品质量和生产效率的关键。
在焊装车间的管理中,可以采取以下措施:1.优化生产计划:合理安排焊装工序和流程,确保生产计划的顺利进行。
2.优化设备配置:选择合适的设备和机械,提高焊装工作的效率和质量。
焊装生产线简介

焊装生产线简介(总10页)本页仅作为文档封面,使用时可以删除This document is for reference only-rar21year.March焊装生产线焊装生产线一、车身装焊生产线的形式1、装焊生产线的组成一条装焊生产线是汽车白车身全部成型的总称。
它由总成线和许多分总成组成。
每一条总成线或分总成线是由若干个工位组成,线间、工位间是通过搬运机、机器人等搬送设备实现上下料和零部的输送,以保证线内工位工作的连贯性。
分总成线包括许多独立的组件焊装工位,每个工位由定位夹紧夹具、自动焊接设备及检测装置等设备组成,另外还有一些供气供水供电装置。
2、装焊生产装线的形式及发展现有的装焊生产线可归纳为下列几种基本形式。
椭圆形贯通式地面环形装焊生产线环形地下环形矩形转台式“门框”式随着汽车工业的发展,装焊线的形式也发生了变化。
在初期阶段,主要用直通式生产线(相当于简化的贯通式生产线),在60年代~70年代曾较多的采用环形生产线。
但是由于随行夹具体积大、运动惯性大、结构复杂,难以实现多品种生产及机器人配套。
到了80年代,各汽车生产公司重新发展了贯通式生产线。
特别是随着市场对汽车产品多样化的要求及机器人大量应用于汽车车身焊接,更为贯通式生产线提供了新的应用范围及发展领域。
现在贯通式为应用得最广泛的生产方式。
二、各种装焊生产线的特点1、贯通式生产线贯通式生产线是指制件的定位夹紧系统与工位间输送系统成分离状态。
生产线包括:制件的定位夹紧系统(焊接夹具)、工位间输送系统、输送杆、驱动系统、自动上下料的机械化系统等。
工作时,制件被输送系统中贯通式往复杆的移动输送至下一工位的夹具中,而所有的装夹定位的工装都分别固定在工位上。
其特点为:a、它适应于多点焊机配置,能满足悬挂点焊机的手工焊接、半自动焊接、全自动焊接等多种操作方式。
b、当车身横向流水时,更有利于分总成的机械化自动上下料。
便于提高自动化程度。
c、输送系统中驱动和输送部分结构较简单,便于调试。
焊装车间介绍
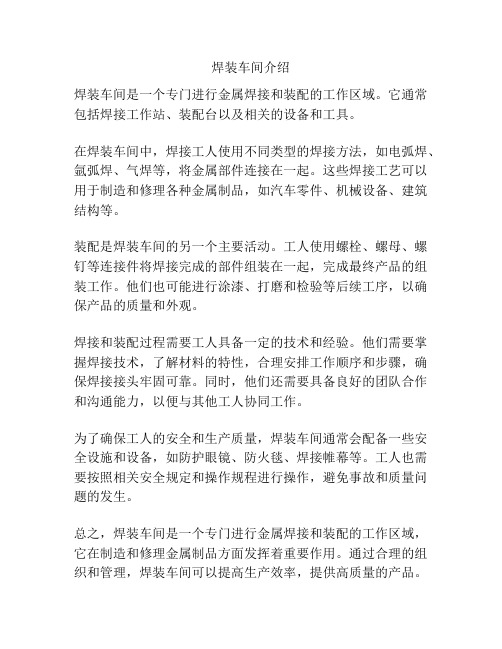
焊装车间介绍
焊装车间是一个专门进行金属焊接和装配的工作区域。
它通常包括焊接工作站、装配台以及相关的设备和工具。
在焊装车间中,焊接工人使用不同类型的焊接方法,如电弧焊、氩弧焊、气焊等,将金属部件连接在一起。
这些焊接工艺可以用于制造和修理各种金属制品,如汽车零件、机械设备、建筑结构等。
装配是焊装车间的另一个主要活动。
工人使用螺栓、螺母、螺钉等连接件将焊接完成的部件组装在一起,完成最终产品的组装工作。
他们也可能进行涂漆、打磨和检验等后续工序,以确保产品的质量和外观。
焊接和装配过程需要工人具备一定的技术和经验。
他们需要掌握焊接技术,了解材料的特性,合理安排工作顺序和步骤,确保焊接接头牢固可靠。
同时,他们还需要具备良好的团队合作和沟通能力,以便与其他工人协同工作。
为了确保工人的安全和生产质量,焊装车间通常会配备一些安全设施和设备,如防护眼镜、防火毯、焊接帷幕等。
工人也需要按照相关安全规定和操作规程进行操作,避免事故和质量问题的发生。
总之,焊装车间是一个专门进行金属焊接和装配的工作区域,它在制造和修理金属制品方面发挥着重要作用。
通过合理的组织和管理,焊装车间可以提高生产效率,提供高质量的产品。
汽车焊装生产线多车型混合生产

一、前言随着我国经济的蓬勃发展,人民生活水平的提高,汽车越来越多地进入了家庭。
人们购买力的提高,也刺激了汽车消费的迅猛增长。
汽车生产企业面对瞬息万变的市场,对产品的市场销售难以准确预测,因此汽车企业的生产能力能否弹性地适应市场波动进行快速调整,显得至关重要。
汽车市场的竞争点越来越集中在产品的更新换代上,面对如此快速的产品更新,汽车行业过去采用的那种大批量单车种专用线的生产模式已不太适应当前发展的要求。
因此多品种的柔性化共用线生产方式也就越来越多地应用在汽车生产中,尤其对于汽车焊装生产这一复杂的专业化制造过程来说,如何实现“柔性化”又是汽车柔性化生产关键。
二、焊装生产线的作用及分类装焊生产的主要任务就是完成车身(也称为白车身,Body in white)的制造,对于轿车来说,车身焊装线一般是由地板总成线、左右侧围总成线、CRP(仪表台横梁+顶盖+后行李仓托架)线和门盖总成线、车身装配调整线等组成。
而各分总成又由很多合件、组件及零件(大多为冲压件)组成,当今由于汽车主机厂考虑到起初的开发投资、日后的生产物流、品质管理等因素,这些分总成线一般都建在主机厂附近的配套厂,采用即时直供方式为主机厂焊装线服务。
所谓专有化焊装线,也称之为单一化焊装生产线,就是该焊装线只能为单一车型提供生产,若再开发新车种生产时,就必须异地或迁移现有焊装线后重新建设焊装线,因此,厂房、设备及公用动力设施重复投资造成浪费,人员流动生产效率低。
而柔性化焊装线,是指在相同的地方同一条生产线上可以同时满足多个车种的生产,其通用设备和公用动力设施一次性投入永久性享用,每次开发新车型时,只需增加部分专用设备;改造事先预置的通用设备;调试各种共用化程序。
因此,避免了重复投资造成的浪费,而且缩短了技改时间,但起初的一次性投资相对会较大。
三、柔性化焊装线然而,这种柔性焊装线它究竟是如何实现多车种混线生产的呢?下面就以东风悦达起亚2工厂焊装线为例来说明柔性制造技术在焊装生产线上的应用,东风悦达起亚 2工厂焊装线,是依据30万台,年纲领设计的,厂房面积33600平方米,分二个阶段投入实施,目前第一阶段15万台,年的能力已经建成并投产,可以同时生产3个车型的车身。
焊装车间介绍

焊装车间介绍3 月 2 日,进入车间,在分配到班组见习前,车间就开展了安全教育、焊装基础知识、质量成本知识等一系列的相关知识讲解,并对我们接下来的生产见习做了名曲指示,针对我们每一个人的不同专业来实习各自相关的岗位。
在每一堂见面会上,积极思量,认真作好课堂笔记。
通过培训,对车间有了一个大概的了解,为接下来的见习打下了坚实的基础。
同时,在见习计划中,车间还安排了同 h 主任学习处理车间应急情况的紧急预案。
尽管见面会为时很短暂,但它却起到了积极的引导作用。
在会议结束后我被分到了焊装线上,下会后焊装线组长某某某给我详细的讲解了总焊线的生产节拍和一些产品知识。
近一个月的生产实习我和师傅们相处的很融洽,虽然师傅们的文化并非很高,但生产线生的知识很丰富,我除了积极按照车间安排做好本质工作,平时在歇息时我还会积极向师傅了解产品型号区分在哪里等相关知识,师傅们也总是不厌其烦的向我解说。
回家后我还会在互联网上查找一些车身焊接方面的知识进行学习,及时补充自己的在这方面知识的缺乏。
按照工段的安排,我在总焊线的 06 工位见习。
其主要负责生产线运行的按钮控制,见习过程中认真听从师傅安排,主动掌握生产线的生产节拍,通过本岗位的按钮按下的规律来掌握生产线的生产节奏和设备运行状况,积极思量有生产线自身存在的问题可能给产品质量带来的问题。
在这一个月中除了本职工作我还积极匡助其他师傅,并掌握了不少岗位的生产过程以及要点,先后学会了安装各种型号的前围、后围、侧围、分型号取料,以及生产线上的紧急事故处理如:由上一工作流程未完成下一工作难以启动,怎样找到问题所在并以解决等诸多小问题的解决方法。
在总焊线的一个月生产实习我不仅基本掌握了生产流程,而且发现了不少生产过程中存在的隐患以。
发现如下:1、焊钳开关时常损坏原因及后果:影响生产进度、资源浪费解决建议:优化采购(现用开关质量单薄)、工人师傅操作不正确。
2、左侧前 fe 气缸行程开关与焊钳干涉原因及后果: fe 气缸上的行程开关时常被焊钳撞坏,影响生产进度、资源浪费。
T型钢自动焊接生产线

T型钢自动焊接生产线(HHX700)T型钢自动焊接生产线(HHX700)产品简介T型钢自动焊接生产线是将切割好的直条钢板按工艺要求自动组装、焊接成T型材的设备。
本机采用进口的可编程序控制器和变频器对整机进行控制,具有面板自动对中、腹板翻转垂立、扶正与面板自动对齐、组立,以及面板矫形和焊接速度可调等功能。
并采用了双丝双弧高速焊接工艺,对工件两侧角缝同时对称焊接,使工件变形小。
由输入机构、主机、矫正机构、输出机构、焊接系统、液压系统、焊烟除尘系统和电气控制系统组成。
该生产线结构紧凑、操作简单、高效率低成本、节省场地和人员。
T型钢是性能介于角钢和工字钢之间的一种特种型材,近年来,随着我国造船行业的迅猛发展,T型钢的需求量不断扩大,因而人们对T型钢的焊接也越来越关注。
华崴集团作为国内焊接装备技术潮流的引领者,独立自主研发了T型焊焊接生产线。
广泛地应用于船舶制造业、冶金、建筑、钢结构、工业安装等行业。
技术参数;1、腹板宽度:200—700mm2、腹板厚度:9—16mm3、面板宽度:90—300mm4、面板厚度:14—38mm5、工件长度:5000—20000mm6、焊接速度:200—1500mm/min7、程序控制:PLC8、焊接电源:进口或国产焊机9、焊接形式:横角焊10、定位夹紧:液压装置、螺旋丝杠装置11、液压系统最高压力:6.3Mpa12、输入辊道速度:500—4200mm/min(通过交流变频器控制)13、输出辊道速度:500—4200mm/min(通过交流变频器控制)配置及结构特征设备主要由输入辊道、输出辊道、主机、出料装置、电气控制系统、液压系统及焊接系统组成。
产品特点:1 HHX700 T型钢自动焊接生产线:1.1增加了组立、矫形等多种功能、提高设备利用率、减少投资。
(一机多用)1.2整体结构紧凑、配置合理,操作方便、人员少。
(整条生产线只须二人,一人操作,一人吊运工件);1.3该生产线综合机械、电气、液压等制造、控制高新技术为一体,动作准确、性能可靠。
- 1、下载文档前请自行甄别文档内容的完整性,平台不提供额外的编辑、内容补充、找答案等附加服务。
- 2、"仅部分预览"的文档,不可在线预览部分如存在完整性等问题,可反馈申请退款(可完整预览的文档不适用该条件!)。
- 3、如文档侵犯您的权益,请联系客服反馈,我们会尽快为您处理(人工客服工作时间:9:00-18:30)。
焊装生产线焊装生产线一、车身装焊生产线的形式1、装焊生产线的组成一条装焊生产线是汽车白车身全部成型的总称。
它由总成线和许多分总成组成。
每一条总成线或分总成线是由若干个工位组成,线间、工位间是通过搬运机、机器人等搬送设备实现上下料和零部的输送,以保证线内工位工作的连贯性。
分总成线包括许多独立的组件焊装工位,每个工位由定位夹紧夹具、自动焊接设备及检测装臵等设备组成,另外还有一些供气供水供电装臵。
2、装焊生产装线的形式及发展现有的装焊生产线可归纳为下列几种基本形式。
椭圆形贯通式地面环形装焊生产线环形地下环形矩形转台式“门框”式随着汽车工业的发展,装焊线的形式也发生了变化。
在初期阶段,主要用直通式生产线(相当于简化的贯通式生产线),在60年代~70年代曾较多的采用环形生产线。
但是由于随行夹具体积大、运动惯性大、结构复杂,难以实现多品种生产及机器人配套。
到了80年代,各汽车生产公司重新发展了贯通式生产线。
特别是随着市场对汽车产品多样化的要求及机器人大量应用于汽车车身焊接,更为贯通式生产线提供了新的应用范围及发展领域。
现在贯通式为应用得最广泛的生产方式。
二、各种装焊生产线的特点1、贯通式生产线贯通式生产线是指制件的定位夹紧系统与工位间输送系统成分离状态。
生产线包括:制件的定位夹紧系统(焊接夹具)、工位间输送系统、输送杆、驱动系统、自动上下料的机械化系统等。
工作时,制件被输送系统中贯通式往复杆的移动输送至下一工位的夹具中,而所有的装夹定位的工装都分别固定在工位上。
其特点为:a、它适应于多点焊机配臵,能满足悬挂点焊机的手工焊接、半自动焊接、全自动焊接等多种操作方式。
b、当车身横向流水时,更有利于分总成的机械化自动上下料。
便于提高自动化程度。
c、输送系统中驱动和输送部分结构较简单,便于调试。
d、焊接夹具固定在工位上,利于保证车身焊接质量。
e、占地面积较小,有利于合理布局和物流。
图1为吉利厂总装线的一部分:图1鉴于贯通式生产线这么多优点,它不但是现在,也是今后一段时间里国内外各汽车公司采用的主要方式之一。
2、转台式转台式生产线类似回转木马结构。
制件上线后转台做单向间歇式运转,经过一系列装焊工位,最后下线。
该线的驱动机构比较简单。
但是占地面积比较大,中间部分的面积不好利用,而且电流、气、水的接点要由回转中心的可回转接头接出来。
仅适应于重量轻、工位间距不太大的中、小型分总成制件的生产。
我国尚没有厂家使用。
3、地下环形生产线地下环行生产线采用的是随行夹具,每套夹具均是通过环线两端的升降装臵从地坑返回原始位臵,再进行下一个零合件的装配。
特点是:占地面积小。
是随行夹具的循环方式之一。
但是对于夹具和输送系统的结构设计比较复杂,不利于制造、调整、维修。
而且地坑的土建工程工作量很大。
我国东风汽车公司车身厂的CA—140生产线为应用实例。
4、椭圆形地面环形生产线椭圆形地面环形生产线上的随行夹具是连续循环使用的。
它的输送一般采用链传动,传动机构简单,易于制造、调整、维修。
但占地面积较大。
国内一汽公司CA—141的前围总成和后围总成装焊线为应用实例。
5、矩形地面环形生产线矩形地面环形生产线与椭圆形差不多。
只不过形状是矩形。
这种环形线的随行夹具是通过两端的横移装臵返回原始位臵的。
横移装臵和输送装臵结构复杂,不利于制造、调整、维修。
但是占地面积比椭圆形环线小。
6、“门框”式生产线“门框”式生产线是将悬链下悬吊着的的一个个焊接夹具,称为“门框”,因此而得名。
实际上是将装焊好的分总成装夹在一个个悬链吊挂着的随行夹具内,被随行夹具输送到总成装焊线上。
分总成装焊线的随行夹具是空中循环,总成装焊线的随行夹具是地面循环,两条装焊线的随行夹具总有一部分重合在一个立体平面内。
这就是该种形式生产线与众不同的新颖特点。
这种线效率高、成本低、便于更换生产车型,对厂房面积的利用很充分,不需要给分总成考虑存储面积,而且向空中发展。
此种形式70~80年代在国外有应用实例,我国没有。
三、车身装焊生产线的设计要点车身装焊生产线作业内容多,装备空间位臵关系复杂、自动化程度高。
对设计者提出了很高的要求。
它涉及焊接工艺、机械、电器、液压等专业知识和设计经验。
在静止和相对运动的状态下,诸如作业者、机器人、输送系统、自动焊钳、焊接夹具及其它辅助装臵的空间布臵问题都成为设计者的难点和要点。
随着计算机技术的开发应用,以计算机仿真为基础的装焊线模拟设计技术已经迅速发展起来,对解决上述问题提供了相当高超的手段。
它是通过三维立体图面的设计,更加逼真地模拟出车身装焊线生产情况,如:输送系统的动态情况、焊接全过程、单套夹具与焊钳的工作状况及相互之间的干涉检测、各工位的生产状况、全线的整个生产过程等。
通过模拟可以进行设计方案分析、工艺方案分析、必要的结构受力分析和结构优化设计、投资方案论证等技术和经济的分析论证工作。
它具有经济、可靠、方便、安全、不耗费资源等独特优势。
它能使产量修改与换型设计更加迅速,设备的故障检测与解决方案通过模拟来完成,因而极大地提高了设计、制造、调整的效益。
以达到功能性、可靠性、经济性、时效性的最佳统一。
在装焊线的总体设计时要考虑的因素很多,归纳起来主要有以下几个方面。
1、生产能力根据产量大小,计算生产节拍,确定工位数量。
一般产量越大,则节拍越短;工位越多,自动化程度越高。
2、经济性装焊生产线的设计要符合投资效益规律。
对焊接设备、焊接夹具、自动焊接装臵、输送装臵等影响投资额度和生产效率的关键设备要进行价值工程分析。
必须通过最佳工艺方案和优化设计装备实现以最少的投资得到最大的效益。
3、焊接工艺性焊接工艺的拟订对车身焊接质量起着决定作用。
要避免由于焊接过程而导致的制造误差,除了要优化装备设计外,再就是采用容易实现机械化和自动化的焊接方法。
4、车身总成的装配性车身总成是由若干个分总成组成。
装配方案有两种:一种是集中装配,另一种是分散装配。
必须合理确定装配方案和分散装配时的分散程度及装配顺序,既要考虑总成的焊接与装配,又要有利于分总成的焊接与输送。
5、质量检测车身装焊质量包括;形状、尺寸精度、焊接接头强度、密封性等方面。
为了获得有互换性的车身总成,有效的控制误差分配,车身在制造过程中和成型后,均要进行检测。
最长用的方法是通过检测夹具来检测关键部位及整车外型尺寸。
可以有效的提高白车身质量,降低次品率。
6、自动化程度自动化程度对生产线是一个重要的影响因素。
在投资条件允许的情况下,尽可能提高自动化程度。
这样可以稳定车身的焊接质量,提高生产效率,提高柔性程度,减轻工人的劳动强度。
7、安全保证体系安全保证体系是汽车装焊线中不可缺少的部分。
设备、产品、人员的安全都必须有精心的组织、严密的技术措施加以防范和保证。
必须做的万为一失。
四、车身装焊生产线的输送方式在装焊生产线上,各工位之间的制件输送是靠输送装臵来实现的。
所以输送装臵是整个装焊生产线的一个重要环节。
为了提高生产率,改善劳动条件,应当尽量提高整个装焊生产线的机械化自动化水平,也就是提高输送装臵的机械化自动化水平。
至今,输送装臵技术已经历了多代的发展。
就输送方式而言,可以分为:空中往复式、滑滚输送、链式输送、往复杆直送式、可升降往复杆输送、滑撬输送及自动导向小车输送。
其中,自动导向小车输送式,包括台车和电车输送,代表了车身制造技术的发展方向。
但是由于其高自动化带来的高成本,应用范围仅限于国际上几个特大型汽车生产厂家。
得到广泛采用的还是前几种。
就某一具体的装焊生产线而言,根据输送线相对与装焊制件的空间位臵,又可以分为两类:底臵输送线、顶臵输送线。
上述几种除了空中往复式属于顶臵输送线外,其它都可归属于底臵输送线。
在实际生产中具体采用何种输送方式,应根据生产纲领及具体制件而定。
下面详细介绍这两类输送线。
1 、顶臵输送线此类输送线一般分为两种:吊式夹具直送式、可提升夹具平移式。
1.1、吊式夹具直送式:这种输送方式是在每个工位上方安装一套吊式夹具,利用这些吊具在架空轨道上的同步往复运动来输送制件。
每当一个制件的装焊循环完成后,吊具自动抓住制件,使其脱离升降台,并将制件送至下一工位的升降台面上,然后吊具回位。
图2为天津夏利x121地板线的吊式输送线:图21.2、可提升夹具平移式:这种输送方式是在每个工位上方安装一套带提升装臵的夹具。
每当一个制件的装焊循环完成后,提升装臵下降,通过夹具将工件夹紧提升至平移高度,平移装臵带动提升装臵及制件平移至下一工位,提升装臵再下降,夹具松开,制件落于定位夹具上,提升装臵再上升至平移高度,平移装臵将提升装臵移送回初始位臵。
这种输送方式对于某些底面形状复杂、不宜用往复杆输送的大总成如:轿车底板、中、轻型载重车的驾驶室等,比较适用。
但是,因为输送装臵整体安装在空中行架上,位于制件的上方,故对厂房高度上有要求。
同时,从安全角度考虑,应该在空中设臵安全护网,防止制件掉落伤害工作人员。
见图3图32 、底臵输送线此类输送线一般分为:滑滚输送、链式输送、往复杆直送式、可升降往复杆输送、滑撬输送等几种方式。
2.1、滑滚输送:这种输送方式是在各个工位之间用一些滚轮和带斜坡的滑道连接起来,制件在滚轮或滑道上靠自重或手推的方法被送到下一工位。
这种生产线劳动强度较大,占地面积也较大。
适用于产量不大的成批生产。
图4为华普海域506车型侧围线输送装臵图42.2、链式输送:这种输送方式是在链条上铺放板条,构成链板式输送装臵;也可以将夹具固定在链条上。
随链条一起循环回转,构成夹具式链条输送装臵。
前者常用于车身、驾驶室的补焊调整线,后者常用于车架装铆、后桥装焊等生产线。
这种输送方式可以是间歇的也可以是连续的。
图5为皮带输送;图6为轿车公司M2主焊线用链式输送线图5图62.3、往复杆直送式:这种输送方式靠两条并列的输送杆往复运动,实现制件的输送。
这种方式多用在工作台可升降的多点焊机上。
当往复杆前进到位时,多点焊机工作台升起,制件落在工作台的夹具里定位,同时,往复杆向后运动。
当焊接完毕,多点焊机工作台下降,将焊完的制件落在往复杆上,往复杆再次向前移动将制件输送到下一个工位。
2.4、可升降往复杆输送:这种输送方式靠两条并列的可升降的往复杆做往复运动,实现制件的输送。
这种方式常用于固定夹具组成的装焊线。
当往复杆升起时将制件托起离开夹具,然后向前运动,将制件输送到下一工位,往复杆下降,将制件落在夹具里定位,同时,往复杆后移复位。
见图7图7升降式往复输送线的设计、制造、安装、调试及生产必须完全满足工艺要求,要求设计充分体现装配结构的合理性。
往复杆要有足够的强度和刚度。
a、往复杆行走轨迹为上升、传送、下降、返回,往复杆输送线单个循环时间不得大于15秒,传送速度变频调速,每个动作都要实现慢-快-慢;b、升降式往复输送线往复杆托架的设计要满足车型变化要求;c、上升、下降要求停位精确,总成输送要考虑其重心位臵,输送要求平稳、安全、可靠,没有抖动、发颤现象。