PLC、DCS、FCS的特点和差异
DCS系统和PLC控制系统有哪些相同点和不同点
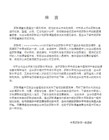
2、从系统结构来说。
PLC与DCS的基本结构是一样的。PLC发展到今天,已经全面移植到计算机系统控制上了,传统的编程器早就被淘汰。小型应用的PLC一般使用触摸屏,大规模应用的PLC全面使用计算机系统。
3、PLC和DCS的发展方向
小型化的PLC将向更专业化的使用角度发展,比如功能更加有针对性、对应用的环境更有针对性等等。大型的PLC与DCS的界线逐步淡化,直至完全融和。
2. 在网络方面,DCS网络是整个系统的中枢神经,它是安全可靠双冗余的高速通讯网络,系统的拓展性与开放性更好。而PLC因为基本上都为个体工作,其在与别的PLC或上位机进行通讯时,所采用的网络形式基本都是单网结构,网络协议也经常与国际标准不符。在网络安全上,PLC没有很好的保护措施。我们采用电源,CPU,网络双冗余。
首先,DCS和PLC 之间有什么不同?
1、从发展的方面来说:
DCS从传统的仪表盘监控系统发展而来。因此,DCS从先天性来说较为侧重仪表的控制,比如YOKOGAWA CS3000 DCS系统甚至没有PID数量的限制(PID,比例微分积分算法,是调节阀、变频器闭环控制的标准算法,通常PID的数量决定了可以使用的调节阀数量)。
DCS在发展的过程中也是各厂家自成体系,但大部分的DCS系统,比如横河YOKOGAWA、霍尼维尔、ABB等等,虽说系统内部(过程级)的通讯协议不尽相同,但操作级的网络平台不约而同的选择了以太网络,采用标准或变形的TCP/IP协议。这样就提供了很方便的可扩展能力。在这种网络中,控制器、计算机均作为一个节点存在,只要网络到达的地方,就可以随意增减节点数量和布置节点位置。另外,基于windows系统的OPC、DDE等开放协议,各系统也可很方便的通讯,以实现资源共享。
PLC、DSC、FCS三大控制系统的特点和差异
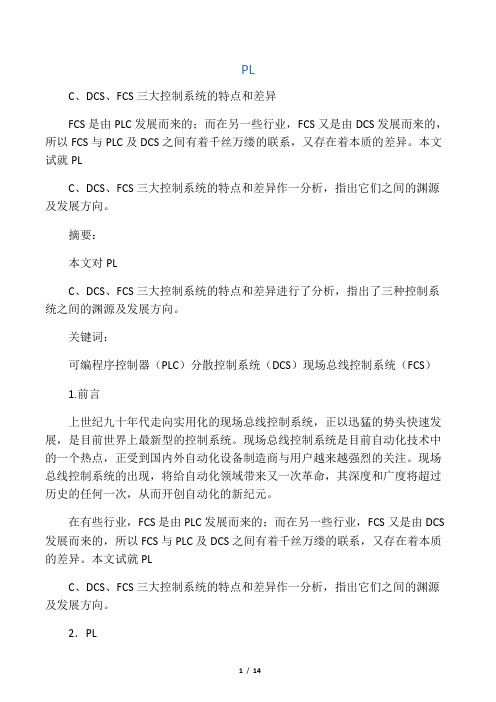
PLC、DCS、FCS三大控制系统的特点和差异FCS是由PLC发展而来的;而在另一些行业,FCS又是由DCS发展而来的,所以FCS与PLC及DCS之间有着千丝万缕的联系,又存在着本质的差异。
本文试就PLC、DCS、FCS三大控制系统的特点和差异作一分析,指出它们之间的渊源及发展方向。
摘要:本文对PLC、DCS、FCS三大控制系统的特点和差异进行了分析,指出了三种控制系统之间的渊源及发展方向。
关键词:可编程序控制器(PLC)分散控制系统(DCS)现场总线控制系统(FCS)1.前言上世纪九十年代走向实用化的现场总线控制系统,正以迅猛的势头快速发展,是目前世界上最新型的控制系统。
现场总线控制系统是目前自动化技术中的一个热点,正受到国内外自动化设备制造商与用户越来越强烈的关注。
现场总线控制系统的出现,将给自动化领域带来又一次革命,其深度和广度将超过历史的任何一次,从而开创自动化的新纪元。
在有些行业,FCS是由PLC发展而来的;而在另一些行业,FCS又是由DCS 发展而来的,所以FCS与PLC及DCS之间有着千丝万缕的联系,又存在着本质的差异。
本文试就PLC、DCS、FCS三大控制系统的特点和差异作一分析,指出它们之间的渊源及发展方向。
2.PLC、DCS、FCS三大控制系统的基本特点目前,在连续型流程生产自动控制(PA)或习惯称之谓工业过程控制中,有三大控制系统,即PLC、DCS和FCS。
它们各自的基本特点如下:2.1 PLC(1)从开关量控制发展到顺序控制、运送处理,是从下往上的。
(2)连续PID控制等多功能,PID在中断站中。
(3)可用一台PC机为主站,多台同型PLC为从站。
(4)也可一台PLC为主站,多台同型PLC为从站,构成PLC网络。
这比用PC机作主站方便之处是:有用户编程时,不必知道通信协议,只要按说明书格式写就行。
(5)PLC网格既可作为独立DCS/TDCS,也可作为DCS/TDCS的子系统。
PCS FCS DCS PLC 区别
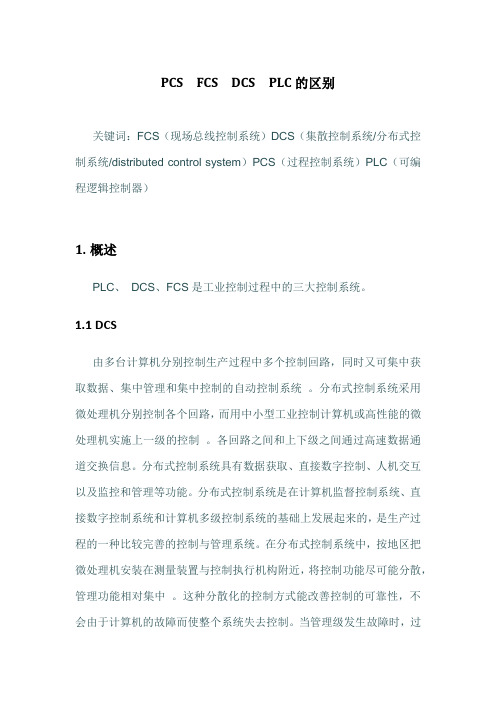
PCS FCS DCS PLC的区别关键词:FCS(现场总线控制系统)DCS(集散控制系统/分布式控制系统/distributed control system)PCS(过程控制系统)PLC(可编程逻辑控制器)1.概述PLC、DCS、FCS是工业控制过程中的三大控制系统。
1.1 DCS由多台计算机分别控制生产过程中多个控制回路,同时又可集中获取数据、集中管理和集中控制的自动控制系统。
分布式控制系统采用微处理机分别控制各个回路,而用中小型工业控制计算机或高性能的微处理机实施上一级的控制。
各回路之间和上下级之间通过高速数据通道交换信息。
分布式控制系统具有数据获取、直接数字控制、人机交互以及监控和管理等功能。
分布式控制系统是在计算机监督控制系统、直接数字控制系统和计算机多级控制系统的基础上发展起来的,是生产过程的一种比较完善的控制与管理系统。
在分布式控制系统中,按地区把微处理机安装在测量装置与控制执行机构附近,将控制功能尽可能分散,管理功能相对集中。
这种分散化的控制方式能改善控制的可靠性,不会由于计算机的故障而使整个系统失去控制。
当管理级发生故障时,过程控制级(控制回路)仍具有独立控制能力,个别控制回路发生故障时也不致影响全局。
与计算机多级控制系统相比,分布式控制系统在结构上更加灵活、布局更为合理和成本更低。
分散型控制系统(DCS)是以微处理机为基础,以危险分散控制,操作和管理集中为特性,集先进的计算机技术、通讯技术、CRT技术和控制技术即4C技术于一体的新型控制系统。
随着现代计算机和通讯网络技术的高速发展,DCS正向着多元化、网络化、开放化、集成管理方向发展,使得不同型号的DCS可以互连,进行数据交换,并可通过以太网将DCS系统和工厂管理网相连,实现实时数据上网,成为过程工业自动控制的主流。
DCS的构成方式十分灵活,可由专用的管理计算机站、操作员站、工程师站、记录站、现场控制站和数据采集站等组成,也可由通用的服务器、工业控制计算机和可编程控制器构成。
PLC与DCS、 FCS比较
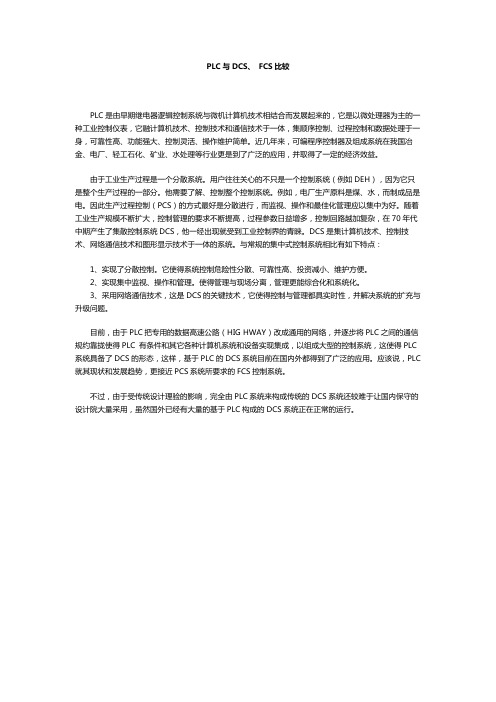
PLC与DCS、FCS比较PLC是由早期继电器逻辑控制系统与微机计算机技术相结合而发展起来的,它是以微处理器为主的一种工业控制仪表,它融计算机技术、控制技术和通信技术于一体,集顺序控制、过程控制和数据处理于一身,可靠性高、功能强大、控制灵活、操作维护简单。
近几年来,可编程序控制器及组成系统在我国冶金、电厂、轻工石化、矿业、水处理等行业更是到了广泛的应用,并取得了一定的经济效益。
由于工业生产过程是一个分散系统。
用户往往关心的不只是一个控制系统(例如DEH),因为它只是整个生产过程的一部分。
他需要了解、控制整个控制系统。
例如,电厂生产原料是煤、水,而制成品是电。
因此生产过程控制(PCS)的方式最好是分散进行,而监视、操作和最佳化管理应以集中为好。
随着工业生产规模不断扩大,控制管理的要求不断提高,过程参数日益增多,控制回路越加复杂,在70年代中期产生了集散控制系统DCS,他一经出现就受到工业控制界的青睐。
DCS是集计算机技术、控制技术、网络通信技术和图形显示技术于一体的系统。
与常规的集中式控制系统相比有如下特点:1、实现了分散控制。
它使得系统控制危险性分散、可靠性高、投资减小、维护方便。
2、实现集中监视、操作和管理。
使得管理与现场分离,管理更能综合化和系统化。
3、采用网络通信技术,这是DCS的关键技术,它使得控制与管理都具实时性,并解决系统的扩充与升级问题。
目前,由于PLC把专用的数据高速公路(HIG HWAY)改成通用的网络,并逐步将PLC之间的通信规约靠拢使得PLC 有条件和其它各种计算机系统和设备实现集成,以组成大型的控制系统,这使得PLC 系统具备了DCS的形态,这样,基于PLC的DCS系统目前在国内外都得到了广泛的应用。
应该说,PLC 就其现状和发展趋势,更接近PCS系统所要求的FCS控制系统。
不过,由于受传统设计理验的影响,完全由PLC系统来构成传统的DCS系统还较难于让国内保守的设计院大量采用,虽然国外已经有大量的基于PLC构成的DCS系统正在正常的运行。
DCS、FCS、PLC的区别
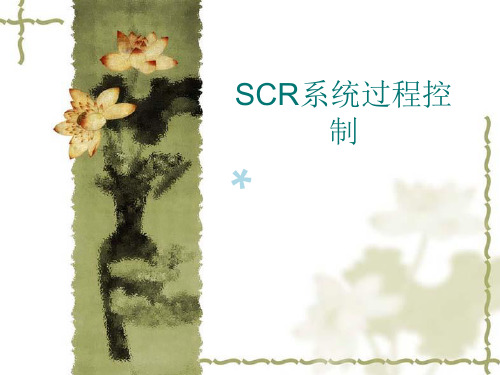
DCS的结构
❖ DCS包括过程级、操作级和管理级 ,过程级 主要由过程控制站、I/O单元和现场仪表组成, 是系统控制功能的主要实施部分。操作级包 括:操作员站和工程师站,完成系统的操作 和组态。管理级主要是指工厂管理信息系统 (MIS系统),作为DCS更高层次的应用, 目前国内纸行业应用到这一层的系统较少。
可靠性、易维护
❖ FCS采用总线连接方式替代传统的DCS一对 一的I/O连线,对于大规模的I/O系统来说, 减少了DCS由接线点造成的不可靠因素。同 时,数字化的现场设备替代模拟仪表,FCS 具有现场设备的在线故障诊断、报警、记录 功能,可完成现场设备的远程参数设定、参 数修改等工作,因而增强系统的可维护性。
❖ FCS采用全数字化、双向传输的通信方式。从最底 层的传感器、变送器和执行器就采用现场总线网络, 逐层向上直到最高层均为通信网络互联。多条分支 通信线延伸到生产现场,用来连接现场数字仪表, 采用一对N连接。
分散控制
❖ 在DCS中,生产现场的多台模拟仪表集中接于输入/输出单 元,而与控制有关的输入、输出、控制、运算等功能块都集 中于DCS的控制站内。DCS只是一个“半分散”系统。
FCS
DCS
操作员在控制室既可以 操作员在控制室既
(3)了解现场设备过现场仪 不了解模拟仪表的
失控 状态
表的工作情况,也能对 设备进行数调整,还 可以预测或寻找故障,
工作情况,也不能 对其进行参数调整, 更不能预测故障,
使设备始终处于操作员 导致操作员对仪表
的过程监控与可控状态 处于“失控”状态。
SCR系统过程控 制
热工自动化范围包括锅炉侧SCR反应区域的烟气系统控制及 脱硝氨区系统(液氨系统 包括氨储罐,蒸发罐,缓冲罐)的仪表及控制系统。
PLC、dcs、fsc控制系统

PLC、DCS、FCS控制系统介绍、特点、及比较1、PLC控制系统PLC可编程控制器即简称PLC(PROGRAMMABLE LOGIC CONTROLLER),虽然现在仍然称PLC,但已经与原来的实际意义不相符合,并不是最初简单的可编程控制器。
PLC的最初定义是一种数字控制专用电子计算机,它使用了可编程序存储器储存指令,执行诸如逻辑、顺序、计时、计数与演算等功能,并通过模拟和数字输入、输出等组件,控制各种机械或工作程序。
经过30多年的发展,PLC 已十分成熟与完善,并开发了模拟量闭环控制功能。
长期以来,PLC始终在各行各业自动化控制领域得到广泛的使用,为各种各样的自动化设备提供了非常可靠的控制应用。
主要原因在于它能够为自动化控制应用提供安全可靠和比较完善的解决方案,适合当前工业企业对自动化的需要。
目前的PLC已经不仅具有早期的逻辑运算功能,而且已经向综合控制方向发展。
新型PLC也在不断完善PID 闭环控制功能,其他各种功能也在不断得到改进。
PLC已被广泛应用于连续过程的控制领域,而且基于连续过程控制技术的发展趋势正在进一步得到增长。
通讯是PLC广泛应用的关键技术,这种技术在PLC领域已经得到扩展。
同系统一样,对PLC进行分散化处理已经成为可能,更容易进行管理,以便能够更好地集成在一起。
PLC系统的价格也在逐渐降低。
由于PLC系统最小模件单元的价格只在千元左右,甚至更低所以大部分用户已经不再对已损坏的模件修理而是直接更换新的模件,因为修理这样的故障模件也许会花费同样甚至更多的费用。
现在一些小型甚至超小型PLC系统已经向工业用户提供了模拟量I/O、PID控制回路、通讯接口,甚至与企业网络系统相连接的现场总线。
具有14个通道的I/O和4个PID 控制回路的PLC系统,其价格也只有千元左右,这种产品非常适合小系统控制应用的需要。
一些PLC供应商依托强大的应用市场发展小型PLC产品,甚至大量的工业用户已经将其看作是低端应用市场上的日用品。
dcs系统与plc哪个好_DCS与PLC的优劣对比 - dcs

dcs系统与plc哪个好_DCS与PLC的优劣对比 - dcsplc和dcs在工业自动化控制中占有举足轻重的地位,而工业自动化控制是国家工业发展战略的核心。
PLC以及DCS在工业控制的各个环节中不断的升级、完善,已经成为现代工业生产制造中不可或缺的工具。
1、DCS和PLC的定义DCS控制系统,在国内自控行业又称之为集散控制系统。
即所谓的分布式控制系统,是相对于集中控制系统而言的一种新型计算机控制系统,它是在集中控制系统的基础上发展、演变而来的。
DCS作为一个集过程控制和过程监控为一体的计算机综合系统,在通信网络的不断带动下,DCS系统已经成为了一个综合计算机,通信、显示和控制等4C技术的完整体系。
其主要特点是分散控制、集中操作、分级管理、配置灵活以及组态方便。
现如今的DCS系统可以广泛地用于工业装置的生产控制和经营管理,在化工、电力、冶金等流程自动化领域的应用已经十分普及。
PLC,即逻辑可编程控制器,是一种数字运算操作的电子系统,专为在工业环境应用而设计的。
它采用一类可编程的存储器,用于其内部存储程序,执行逻辑运算、顺序控制、定时、计数与算术操作等面向用户的指令,并通过数字或模拟式输入/输出控制各种类型的机械或生产过程,是工业控制的核心部分。
2、DCS和PLC控制器的差别DCS和PLC控制器的主要差别是在开关量和模拟量的运算上,即使后来两者相互有些渗透,但是仍然有区别。
80年代以后,PLC除逻辑运算外,也增加了一些控制回路算法,但要完成一些复杂运算还是比较困难,PLC用梯形图编程,模拟量的运算在编程时不太直观,编程比较麻烦。
但在解算逻辑方面,表现出快速的优点。
而DCS使用功能块封装模拟运算和逻辑运算,无论是逻辑运算还是复杂模拟运算的表达形式都非常清晰,但相对PLC来说逻辑运算的表达效率较低。
3、DCS和PLC在火电厂的应用在火电厂热工自动化领域,DCS和PLC是两个完全不同而又有着千丝万缕联系的概念。
DCS系统与PLC系统的区别和联系

DCS系统与PLC系统的区别和联系DCS(分布式控制系统)和PLC(可编程逻辑控制器)是工业自动化领域中常见的两种控制系统。
它们在工业生产过程中起着至关重要的作用,并在许多方面有着相似之处,但也存在一些明显的区别。
本文将探讨DCS系统与PLC系统之间的区别和联系。
一、DCS系统的定义与特点DCS系统是指一种由多个分布式控制器组成的集中控制系统。
它将分散在不同位置的控制器通过网络进行连接,形成一个统一的整体控制系统。
DCS系统的特点如下:1. 高度分布式:DCS系统中的控制器可以分布在各个工艺单元或设备上,实现更加灵活的控制与监测。
2. 大规模处理能力:DCS系统支持处理大规模设备和复杂过程的能力,可以同时对多个设备进行控制和监控。
3. 强大的数据处理能力:DCS系统能够实时采集、处理和存储大量的工艺数据,为生产优化和故障诊断提供有力支持。
4. 开放性与可扩展性:DCS系统采用标准接口和协议,可以与其他系统进行互联互通,并可以根据实际需要进行扩展。
二、PLC系统的定义与特点PLC系统是一种特定用途的数字计算机,用于自动化控制过程中的逻辑和序列控制。
它通常通过编程来控制输出设备的状态,具有以下特点:1. 高度可编程性:PLC系统采用专门的编程语言(如Ladder Diagram)来编写控制逻辑,并可根据实际需求进行修改和调整。
2. 快速的响应时间:PLC系统具有低延迟和高实时性的特点,能够快速响应输入信号并进行逻辑判断和输出控制。
3. 简单可靠的硬件结构:PLC系统通常采用模块化的硬件结构,易于安装和维护。
其硬件组件包括中央处理器、输入/输出模块、电源模块等。
4. 适用于小规模控制:PLC系统通常适用于小规模的控制任务,如机械设备、自动化生产线等。
三、DCS系统与PLC系统的区别1. 应用领域不同:DCS系统主要应用于连续过程控制,如化工、电力、石油等;而PLC系统广泛应用于离散制造业,如机械加工、物流、制药等。
DCS和FCS
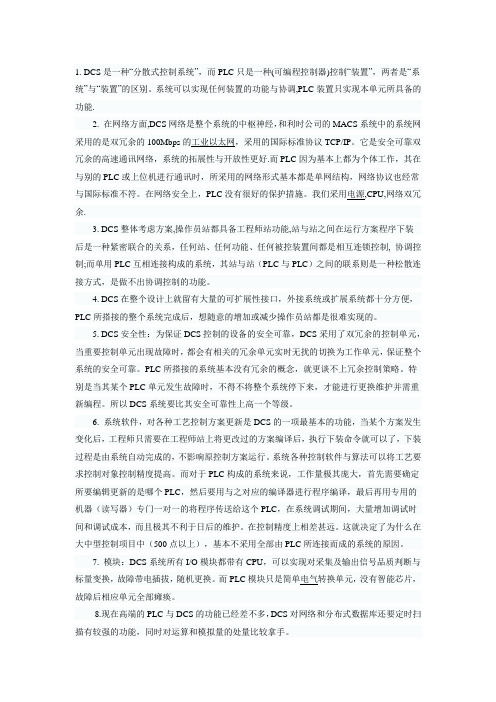
1. DCS是一种“分散式控制系统”,而PLC只是一种(可编程控制器)控制“装置”,两者是“系统”与“装置”的区别。
系统可以实现任何装置的功能与协调,PLC装置只实现本单元所具备的功能.2. 在网络方面,DCS网络是整个系统的中枢神经,和利时公司的MACS系统中的系统网冗余的高速通讯网络,系统的拓展性与开放性更好.而PLC因为基本上都为个体工作,其在与别的PLC或上位机进行通讯时,所采用的网络形式基本都是单网结构,网络协议也经常余.3. DCS整体考虑方案,操作员站都具备工程师站功能,站与站之间在运行方案程序下装后是一种紧密联合的关系,任何站、任何功能、任何被控装置间都是相互连锁控制, 协调控制;而单用PLC互相连接构成的系统,其站与站(PLC与PLC)之间的联系则是一种松散连接方式,是做不出协调控制的功能。
4. DCS在整个设计上就留有大量的可扩展性接口,外接系统或扩展系统都十分方便,PLC所搭接的整个系统完成后,想随意的增加或减少操作员站都是很难实现的。
5. DCS安全性:为保证DCS控制的设备的安全可靠,DCS采用了双冗余的控制单元,当重要控制单元出现故障时,都会有相关的冗余单元实时无扰的切换为工作单元,保证整个系统的安全可靠。
PLC所搭接的系统基本没有冗余的概念,就更谈不上冗余控制策略。
特别是当其某个PLC单元发生故障时,不得不将整个系统停下来,才能进行更换维护并需重新编程。
所以DCS系统要比其安全可靠性上高一个等级。
6. 系统软件,对各种工艺控制方案更新是DCS的一项最基本的功能,当某个方案发生变化后,工程师只需要在工程师站上将更改过的方案编译后,执行下装命令就可以了,下装过程是由系统自动完成的,不影响原控制方案运行。
系统各种控制软件与算法可以将工艺要求控制对象控制精度提高。
而对于PLC构成的系统来说,工作量极其庞大,首先需要确定所要编辑更新的是哪个PLC,然后要用与之对应的编译器进行程序编译,最后再用专用的机器(读写器)专门一对一的将程序传送给这个PLC,在系统调试期间,大量增加调试时间和调试成本,而且极其不利于日后的维护。
三大控制系统的特点和差异
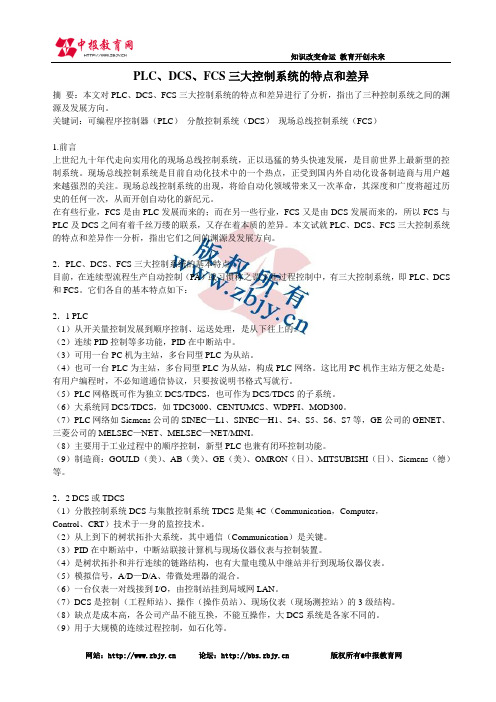
PLC、DCS、FCS三大控制系统的特点和差异摘要:本文对PLC、DCS、FCS三大控制系统的特点和差异进行了分析,指出了三种控制系统之间的渊源及发展方向。
关键词:可编程序控制器(PLC)分散控制系统(DCS)现场总线控制系统(FCS)1.前言上世纪九十年代走向实用化的现场总线控制系统,正以迅猛的势头快速发展,是目前世界上最新型的控制系统。
现场总线控制系统是目前自动化技术中的一个热点,正受到国内外自动化设备制造商与用户越来越强烈的关注。
现场总线控制系统的出现,将给自动化领域带来又一次革命,其深度和广度将超过历史的任何一次,从而开创自动化的新纪元。
在有些行业,FCS是由PLC发展而来的;而在另一些行业,FCS又是由DCS发展而来的,所以FCS与PLC及DCS之间有着千丝万缕的联系,又存在着本质的差异。
本文试就PLC、DCS、FCS三大控制系统的特点和差异作一分析,指出它们之间的渊源及发展方向。
2.PLC、DCS、FCS三大控制系统的基本特点目前,在连续型流程生产自动控制(PA)或习惯称之谓工业过程控制中,有三大控制系统,即PLC、DCS 和FCS。
它们各自的基本特点如下:2.1 PLC(1)从开关量控制发展到顺序控制、运送处理,是从下往上的。
(2)连续PID控制等多功能,PID在中断站中。
(3)可用一台PC机为主站,多台同型PLC为从站。
(4)也可一台PLC为主站,多台同型PLC为从站,构成PLC网络。
这比用PC机作主站方便之处是:有用户编程时,不必知道通信协议,只要按说明书格式写就行。
(5)PLC网格既可作为独立DCS/TDCS,也可作为DCS/TDCS的子系统。
(6)大系统同DCS/TDCS,如TDC3000、CENTUMCS、WDPFI、MOD300。
(7)PLC网络如Siemens公司的SINEC—L1、SINEC—H1、S4、S5、S6、S7等,GE公司的GENET、三菱公司的MELSEC—NET、MELSEC—NET/MINI。
FCS、DCS、PCS与PLC

FCS、DCS 、PCS、 PLCFCS (现场总线控制系统)、DCS (集散控制系统)、PCS(过程控制系统)、 PLC(可编程逻辑控制器)1.集散控制系统DCS与现场总线控制系统FCS的比较1.1 概述FCS、DCS FCS 是在DCS的基础上发展起来的,FCS顺应了自动控制系统的发展潮流,它必将替代DCS。
这已是业内人士的基本共识。
然而,任何新事物的发生,发展都是在 对旧事物的扬弃中进行的,FCS与DCS的关系必然也不例外。
FCS代表潮流与发展方向,而DCS则代表传统与成熟,也是独具优势的事物。
特别是现阶段, FCS尚没有统一的国际标准而呈群雄逐鹿之势,DCS则以其成熟的发展,完备的功能及广泛的应用而占居着一个尚不可完全替代的地位。
本人认为:现场总线控 制系统FCS应该与集散式控制系统DCS相互兼容。
无论是FCS或者是DCS,它们最终是为了满足整个生产过程而进行的系统控制(PCS)。
首先以工程成本与效益看,现场总线的根本优势是良好的互操作性;结构简单,从而布线费用低;控制功能分散,灵活可靠,以及现场信息丰富。
然而这些优势是 建立在 FCS系统初装的前提下,如果企业建立有完善的DCS系统,现在要向FCS过渡,则必须仔细考虑现有投资对已有投资的回报率。
充分利用已有的DCS设施、现有 DCS的布线以及成熟的DCS控制管理方式来实现FCS是我们应选择的方式。
虽然现场总线对已有的数字现场协议有优势可言,但向其过渡的代价与风险是必须分析清楚的。
再者,从技术的继承及控制手段上,也要求FCS与DCS应相兼容。
FCS实现控制功能下移至现场层,使DCS的 多层网络被扁平化,各个现场设备节点的独立功能得以加强,因此,在FCS 中有必要增加和完善现场子层设备间的数据通讯功能。
由于历史的原因,DCS 通常拥有大型控制柜用以协调各个设备,同时更强调层与层的数据传输。
可见,两种控制在策略上各具优势。
DCS 适用于较慢的数据传输速率;FCS则更适用于 较快的数据传输速率,以及更灵活的处理数据。
DCS、PLC、FCS三大系统比较
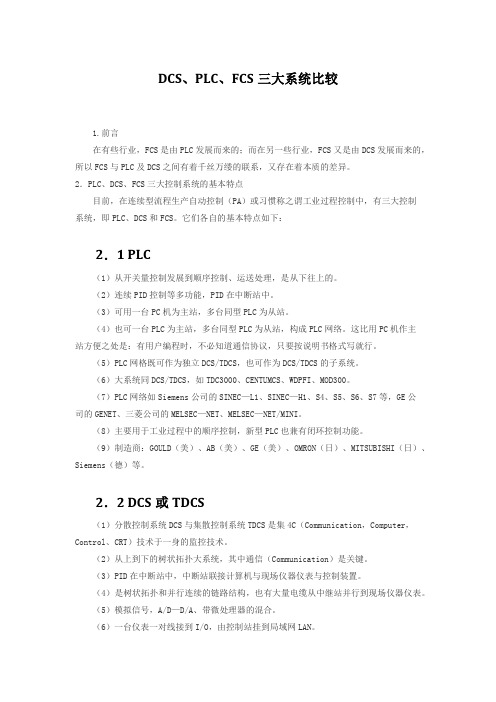
DCS、PLC、FCS三大系统比较1.前言在有些行业,FCS是由PLC发展而来的;而在另一些行业,FCS又是由DCS发展而来的,所以FCS与PLC及DCS之间有着千丝万缕的联系,又存在着本质的差异。
2.PLC、DCS、FCS三大控制系统的基本特点目前,在连续型流程生产自动控制(PA)或习惯称之谓工业过程控制中,有三大控制系统,即PLC、DCS和FCS。
它们各自的基本特点如下:2.1 PLC(1)从开关量控制发展到顺序控制、运送处理,是从下往上的。
(2)连续PID控制等多功能,PID在中断站中。
(3)可用一台PC机为主站,多台同型PLC为从站。
(4)也可一台PLC为主站,多台同型PLC为从站,构成PLC网络。
这比用PC机作主站方便之处是:有用户编程时,不必知道通信协议,只要按说明书格式写就行。
(5)PLC网格既可作为独立DCS/TDCS,也可作为DCS/TDCS的子系统。
(6)大系统同DCS/TDCS,如TDC3000、CENTUMCS、WDPFI、MOD300。
(7)PLC网络如Siemens公司的SINEC—L1、SINEC—H1、S4、S5、S6、S7等,GE公司的GENET、三菱公司的MELSEC—NET、MELSEC—NET/MINI。
(8)主要用于工业过程中的顺序控制,新型PLC也兼有闭环控制功能。
(9)制造商:GOULD(美)、AB(美)、GE(美)、OMRON(日)、MITSUBISHI(日)、Siemens(德)等。
2.2 DCS或TDCS(1)分散控制系统DCS与集散控制系统TDCS是集4C(Communication,Computer,Control、CRT)技术于一身的监控技术。
(2)从上到下的树状拓扑大系统,其中通信(Communication)是关键。
(3)PID在中断站中,中断站联接计算机与现场仪器仪表与控制装置。
(4)是树状拓扑和并行连续的链路结构,也有大量电缆从中继站并行到现场仪器仪表。
PLC与DCS的区别
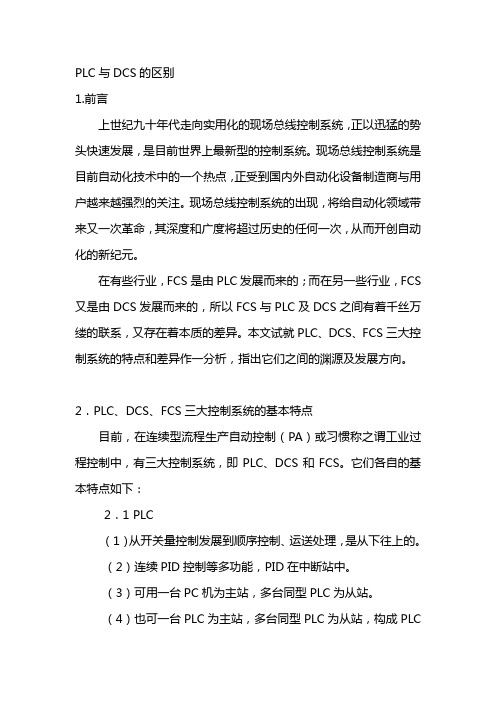
PLC与DCS的区别1.前言上世纪九十年代走向实用化的现场总线控制系统,正以迅猛的势头快速发展,是目前世界上最新型的控制系统。
现场总线控制系统是目前自动化技术中的一个热点,正受到国内外自动化设备制造商与用户越来越强烈的关注。
现场总线控制系统的出现,将给自动化领域带来又一次革命,其深度和广度将超过历史的任何一次,从而开创自动化的新纪元。
在有些行业,FCS是由PLC发展而来的;而在另一些行业,FCS 又是由DCS发展而来的,所以FCS与PLC及DCS之间有着千丝万缕的联系,又存在着本质的差异。
本文试就PLC、DCS、FCS三大控制系统的特点和差异作一分析,指出它们之间的渊源及发展方向。
2.PLC、DCS、FCS三大控制系统的基本特点目前,在连续型流程生产自动控制(PA)或习惯称之谓工业过程控制中,有三大控制系统,即PLC、DCS和FCS。
它们各自的基本特点如下:2.1 PLC(1)从开关量控制发展到顺序控制、运送处理,是从下往上的。
(2)连续PID控制等多功能,PID在中断站中。
(3)可用一台PC机为主站,多台同型PLC为从站。
(4)也可一台PLC为主站,多台同型PLC为从站,构成PLC网络。
这比用PC机作主站方便之处是:有用户编程时,不必知道通信协议,只要按说明书格式写就行。
(5)PLC网格既可作为独立DCS/TDCS,也可作为DCS/TDCS 的子系统。
(6)大系统同DCS/TDCS,如TDC3000、CENTUMCS、WDPFI、MOD300。
(7)PLC网络如Siemens公司的SINEC—L1、SINEC—H1、S4、S5、S6、S7等,GE公司的GENET、三菱公司的MELSEC—NET、MELSEC—NET/MINI。
(8)主要用于工业过程中的顺序控制,新型PLC也兼有闭环控制功能。
(9)制造商:GOULD(美)、AB(美)、GE(美)、OMRON (日)、MITSUBISHI(日)、Siemens(德)等。
PLC、DCS、FCS三大控制系统的特点及差异
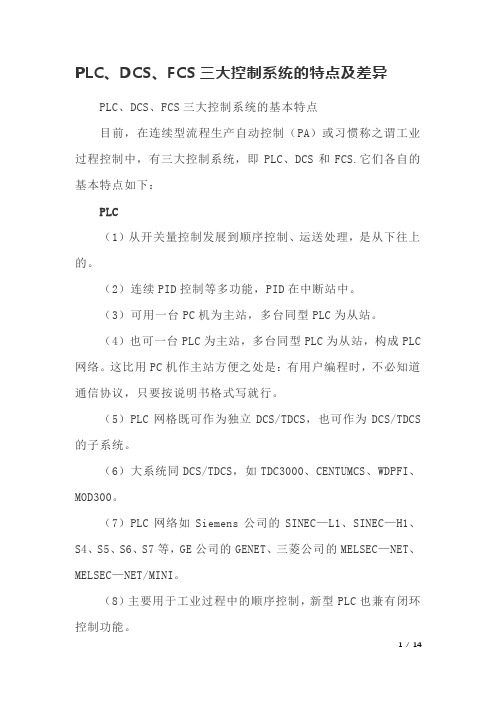
PLC、DCS、FCS三大控制系统的特点及差异PLC、DCS、FCS三大控制系统的基本特点目前,在连续型流程生产自动控制(PA)或习惯称之谓工业过程控制中,有三大控制系统,即PLC、DCS和FCS.它们各自的基本特点如下:PLC(1)从开关量控制发展到顺序控制、运送处理,是从下往上的。
(2)连续PID控制等多功能,PID在中断站中。
(3)可用一台PC机为主站,多台同型PLC为从站。
(4)也可一台PLC为主站,多台同型PLC为从站,构成PLC 网络。
这比用PC机作主站方便之处是:有用户编程时,不必知道通信协议,只要按说明书格式写就行。
(5)PLC网格既可作为独立DCS/TDCS,也可作为DCS/TDCS 的子系统。
(6)大系统同DCS/TDCS,如TDC3000、CENTUMCS、WDPFI、MOD300。
(7)PLC网络如Siemens公司的SINEC—L1、SINEC—H1、S4、S5、S6、S7等,GE公司的GENET、三菱公司的MELSEC—NET、MELSEC—NET/MINI。
(8)主要用于工业过程中的顺序控制,新型PLC也兼有闭环控制功能。
(9)制造商:GOULD(美)、AB(美)、GE(美)、OMRON(日)、MITSUBISHI(日)、Siemens(德)等。
DCS或TDCS(1)分散控制系统DCS与集散控制系统TDCS是集4C (Communication,Computer, Control、CRT)技术于一身的监控技术。
(2)从上到下的树状拓扑大系统,其中通信(Communication)是关键。
(3)PID在中断站中,中断站联接计算机与现场仪器仪表与控制装置。
(4)是树状拓扑和并行连续的链路结构,也有大量电缆从中继站并行到现场仪器仪表。
(5)模拟信号,A/D—D/A、带微处理器的混合。
(6)一台仪表一对线接到I/O,由控制站挂到局域网LAN。
(7)DCS是控制(工程师站)、操作(操作员站)、现场仪表(现场测控站)的3级结构。
PLC,DCS,FCS厂家,特点与区别

PLC的特点
• 结构灵活
– 不受环境的限制,有电即可组建网络,同时可 以灵活扩展接入端口数量,使资源保持较高的 利用率,在移动性方面可与WLAN媲美。
• 范围广
– 无所不在的电力线网络也是这种技术的优势。虽然 无线网络可以做到不破墙,但对于高层建筑来说, 其必需布设N多个AP才能满足需求,而且同样不能 避面信号盲区的存在。而电力线是最基础的网络, 它的规模之大,是其他任何网络无法比拟的。由此, 运营商就可以轻松地把这种网络接入服务渗透到每 一处有电力线的地方。这一技术一旦全面进入商业 化阶段,将给互联网普及带来极大的发展空间。终 端用户只需要插上电力猫,就可以实现因特网接入, 电视频道接收节目,打电话或者是可视电话。
DCS是一个系统包括上位软件、网络与控制器,而PLC只是一个控制 器,要构成系统还需要上位SCADA系统和与之相连的网络。对PID回 路控制,现在三菱的过程控制器也可以实现象SAMA组态一样的FBD 编程;DCS系统更大,控制的回路数目更多,有比较多的控制和算法, 可以完成比较复杂的回路间的控制。硬件可靠性差不多。DCS可以做 到I/O的冗余,PLC则不可以。相对而言,PLC构成的系统成本更低。 —— 三菱电机自动化精密控制部经理宋葭晖
DCS的特点
• (1)高可靠性
– 由于DCS将系统控制功能分散在各台计算机上 实现,系统结构采用容错设计,因此某一台计 算机出现的故障不会导致系统其它功能的丧失。 此外,由于系统中各台计算机所承担的任务比 较单一,可以针对需要实现的功能采用具有特 定结构和软件的专用计算机,从而使系统中每 台计算机的可靠性也得到提高。
• 日本OMRON公司
– CPM1A型机,P型机,H型机,CQM1、CVM、CV型 机,Ha型、F型机等
PLC、DCS、FCS三大控制系统的特点及应用

算机 控制系 统控制算式先进、 精度高、 晌应速 度快的优点, 又有仪表控制系统安全可 维 命.
护方便的优势。
FCS的三 个关键要点: (1)FCS9,统的 核心是总线协议, 即总线标
堆
那么灵活, 所以, 如果一 个项目 有密切联系 中,
的开关量控制和模拟且控制, 则采用DCS 比采
(2)从 上到下的树状拓扑大系 其中 信 统, 通 (Communicat on)是关键. i
(6)3类FCS 的 典型应用:连续的 工艺过程
自 动控制如石油化工, 其中 “ 本安防爆’技 术是绝 要的。 对重 分立的工艺动作自 动控制如
动化。
( 2 ) 逻辑控制, 定时控制、计数控制、 汽车制造机器人,汽车 . 多点控制如楼宇自 PLC具有数据处理能力、 通信和 等 联网 2 三大类型控制系统之间的差异
装置, 取代每台仪表的两根线。“ 现场控 房之间的信息往返. 可以说, 现场总线的本 制, 取代“ 分欲控制 数据的传 T 输采用“ 总线’ 质就是信息处理的现场化。
方式。
化 控制系 本文 分析了PLC, DCS, 统. 对比 FCS 三 动 大自 控制系 特点 统的 和差异, 介绍了
系统的应用及其发展前ቤተ መጻሕፍቲ ባይዱ。
互换性, (2)全教字通(a , 精度高, (3)智能化与 功能自 治性。 (4)高度 分散性,(5)很强的 适用性
等优点 ,
双向数字通信现场总线信号制, 此, 因 它可以 对现场装置(含变送器、 执行机构等)进行远 方诊断、维护和组态。但就目 前而言 F CS
在开关{ 与模拟最的混合处理方面不如 DCS t
口 的特点 CS,
系 统容易 开发, (6)用组态软件, 编程简 操 单,
PLC、DSC、FCS三大控制系统的特点和差异

PLC、DCS、FCS三大控制系统的特点和差异FCS是由PLC发展而来的;而在另一些行业,FCS又是由DCS发展而来的,所以FCS与PLC及DCS之间有着千丝万缕的联系,又存在着本质的差异。
本文试就PLC、DCS、FCS三大控制系统的特点和差异作一分析,指出它们之间的渊源及发展方向。
摘要:本文对PLC、DCS、FCS三大控制系统的特点和差异进行了分析,指出了三种控制系统之间的渊源及发展方向。
关键词:可编程序控制器(PLC)分散控制系统(DCS)现场总线控制系统(FCS)1.前言上世纪九十年代走向实用化的现场总线控制系统,正以迅猛的势头快速发展,是目前世界上最新型的控制系统。
现场总线控制系统是目前自动化技术中的一个热点,正受到国内外自动化设备制造商与用户越来越强烈的关注。
现场总线控制系统的出现,将给自动化领域带来又一次革命,其深度和广度将超过历史的任何一次,从而开创自动化的新纪元。
在有些行业,FCS是由PLC发展而来的;而在另一些行业,FCS又是由DCS发展而来的,所以FCS与PLC 及DCS之间有着千丝万缕的联系,又存在着本质的差异。
本文试就PLC、DCS、FCS三大控制系统的特点和差异作一分析,指出它们之间的渊源及发展方向。
2.PLC、DCS、FCS三大控制系统的基本特点目前,在连续型流程生产自动控制(PA)或习惯称之谓工业过程控制中,有三大控制系统,即PLC、DCS 和FCS。
它们各自的基本特点如下:2.1 PLC(1)从开关量控制发展到顺序控制、运送处理,是从下往上的。
(2)连续PID控制等多功能,PID在中断站中。
(3)可用一台PC机为主站,多台同型PLC为从站。
(4)也可一台PLC为主站,多台同型PLC为从站,构成PLC网络。
这比用PC机作主站方便之处是:有用户编程时,不必知道通信协议,只要按说明书格式写就行。
(5)PLC网格既可作为独立DCS/TDCS,也可作为DCS/TDCS的子系统。
- 1、下载文档前请自行甄别文档内容的完整性,平台不提供额外的编辑、内容补充、找答案等附加服务。
- 2、"仅部分预览"的文档,不可在线预览部分如存在完整性等问题,可反馈申请退款(可完整预览的文档不适用该条件!)。
- 3、如文档侵犯您的权益,请联系客服反馈,我们会尽快为您处理(人工客服工作时间:9:00-18:30)。
(5)PLC网格既可作为独立DCS/TDCS,也可作为DCS/TDCS的子系统。
(6)大系统同DCS/TDCS,如TDC3000、CENTUMCS、WDPFI、MOD300。
(12)3类FCS的典型
1)连续的工艺过程自动控制如石油化工,其中“本安防爆”技术是绝对重要的,典型产品是FF、World FIP、Profibus—PA;
2)分立的工艺动作自动控制如汽车制造机器人、汽车,典型产品是Profibus—DP、CANbus;
3)多点控制如楼宇自动化,典型产品是LON Work、Profibus—FMS。
为保证通信的完整,大部分DCS厂家都能提供冗余数据公路。
为了保证系统的安全性,使用了复杂的通信规约和检错技术。所谓通信规约就是一组规则,用以保证所传输的数据被接收,并且被理解得和发送的数据一样。
目前在DCS系统中一般使用两类通信手段,即同步的和异步的,同步通信依靠一个时钟信号来调节数据的传输和接收,异步网络采用没有时钟的报告系统。
(3) FCS系统的本质是信息处理现场化
对于一个控制系统,无论是采用DCS还是采用现场总线,系统需要处理的信息量至少是一样多的。实际上,采用现场总线后,可以从现场得到更多的信息。现场总线系统的信息量没有减少,甚至增加了,而传输信息的线缆却大大减少了。这就要求一方面要大大提高线缆传输信息的能力,另一方面要让大量信息在现场就地完成处理,减少现场与控制机房之间的信息往返。可以说现场总线的本质就是信息处理的现场化。
3.2 典型系统比较
通过使用现场总线,用户可以大量减少现场接线,用单个现场仪表可实现多变量通信,不同制造厂生产的装置间可以完全互操作,增加现场一级的控制功能,系统集成大大简化,并且维护十分简便。传统的过程控制仪表系统每个现场装置到控制室都需使用一对专用的双绞线,以传送4~20mA信号,现场总线系统中,每个现场装置到接线盒的双绞线仍然可以使用,但是从现场接线盒到中央控制室仅用一根双绞线完成数字通信。
从上述基本要点的描述中,我们是否注意到一点,用于过程控制的三大系统,没有一个是针对电站而开发的,或者说,在他们开发的初期,都并非以电站做系统的首选控制对象。而在这些系统的使用说明中也绝不把电站做为首选适用范围,有的在适用范围中根本就不提电站。现在奇怪的是,这三大控制系统,尤其是DCS、PLC,都在电站得到了广泛应用,而且效果也非常好。
?FCS
FCS的关键要点有三点
(1)FCS系统的核心是总线协议,即总线标准
前面的章节已经叙述,一种类型的总线,只要其总线协议一经确定,相关的关键技术与有关的设备也就被确定。就其总线协议的基本原理而言,各类总线都是一样的,都以解决双向串行数字化通讯传输为基本依据。但由于各种原因,各类总线的总线协议存在很大的差异。
3.1 差异要点
?DCS
DCS系统的关键是通信。也可以说数据公路是分散控制系统DCS的脊柱。由于它的任务是为系统所有部件之间提供通信网络,因此,数据公路自身的设计就决定了总体的灵活性和安全性。数据公路的媒体可以是:一对绞线、同轴电缆或光纤电缆。
通过数据公路的设计参数,基本上可以了解一个特定DCS系统的相对优点与弱点。
实际情况是否如上述一致,回答是否定的。目前通过的现场总线国际标准含8种类型,而原IEO国际标准只是8种类型之一,与其它7种类型总线的地位是平等的。其它7种总线,不论其市场占有率有多少,每个总线协议都有一套软件、硬件的支撑。它们能够形成系统,形成产品,而原IEC现场总线国际标准,是一个既无软件支撑也无硬件支撑的空架子。所以,要实现这些总线的相互兼容和互操作,就目前状态而言,几乎是不可能的。
通过采用现场总线控制系统,到底能节省多少电缆,编者尚未做此计算。但是,我们不可以采用DCS系统的电厂中与自动控制系统有关的所用电缆公里数看出,电缆在基建投资中所占份额。
(1)系统能处理多少I/O信息。
(2)系统能处理多少与控制有关的控制回路的信息。
(3)能适应多少用户和装置(CRT、控制站等)。
(4)传输数据的完整性是怎样彻底检查的。
(5)数据公路的最大允许长度是多少。
(6)数据公路能支持多少支路。
(7)数据公路是否能支持由其它制造厂生产的硬件(可编程序控制器、计算机、数据记录装置等)。
PLC、DCS、FCS的特点和差异
FCS是由PLC发展而来的;而在另一些行业,FCS又是由DCS发展而来的,所以FCS与PLC及DCS之间有着千丝万缕的联系,又存在着本质的差异。本文试就PLC、DCS、FCS三大控制系统的特点和差异作一分析,指出它们之间的渊源及发展方向。
1.前言
上世纪九十年代走向实用化的现场总线控制系统,正以迅猛的势头快速发展,是目前世界上最新型的控制系统。现场总线控制系统是目前自动化技术中的一个热点,正受到国内外自动化设备制造商与用户越来越强烈的关注。现场总线控制系统的出现,将给自动化领域带来又一次革命,其深度和广度将超过历史的任何一次,从而开创自动化的新纪元。
(8)缺点是成本高,各公司产品不能互换,不能互操作,大DCS系统是各家不同的。
(9)用于大规模的连续过程控制,如石化等。
(10)制造商:Bailey(美)、Westinghous(美)、HITACH(日)、LEEDS & NORTHRMP(美)、SIEMENS(德)、Foxboro(美)、ABB (瑞士)、Hartmann & Braun(德)、Yokogawa(日)、Honewell(美国)、Taylor(美)等。
2.3 FCS
(1)基本任务是:本质(本征)安全、危险区域、易变过程、难于对付的非常环境。
(2)全数字化、智能、多功能取代模拟式单功能仪器、仪表、控制装置。
(3)用两根线联接分散的现场仪表、控制装置、PID与控制中心,取代每台仪器两根线。
(4)在总线上PID与仪器、仪表、控制装置都是平等的。
2.2 DCS或TDCS
(1)分散控制系统DCS与集散控制系统TDCS是集4C(Communication,Computer, Control、CRT)技术于一身的监控技术。
(2)从上到下的树状拓扑大系统,其中通信(Communication)是关键。
(3)PID在中断站中,中断站联接计算机与现场仪器仪表与控制装置。
(10)改变传统的信号标准、通信标准和系统标准入企业管理网。
(11)制造商:美Honeywell 、Smar 、Fisher— Rosemount、 AB/Rockwell、Elsag— Bailey 、Foxboro 、Yamatake 、日Yokogawa、欧 Siemens、 GEC—Alsthom 、Schneider、 proces—Data、 ABB等。
目前,在连续型流程生产自动控制(PA)或习惯称之谓工业过程控制中,有三大控制系统,即PLC、DCS和FCS。它们各自的基本特点如下:
2.1 PLC
(1)从开关量控制发展到顺序控制、运送处理,是从下往上的。
(2)连续PID控制等多功能,PID在中断站中。
(3)可用一台PC机为主站,多台同型PLC为从站。
(7)PLC网络如Siemens公司的SINEC—L1、SINEC—H1、S4、S5、S6、S7等,GE公司的GENET、三菱公司的MELSEC—NET、MELSEC—NET/MINI。
(8)主要用于工业过程中的顺序控制,新型PLC也兼有闭环控制功能。
(9)制造商:GOULD(美)、AB(美)、GE(美)、OMRON(日)、MITSUBISHI(日)、Siemens(德)等。
现在一些带现场总线的现场仪表本身装了许多功能块,虽然不同产品同种功能块在性能上会稍有差别,但一个网络支路上有许多功能雷同功能块的情况是客观存在的。选用哪一个现场仪表上的功能块,是系统组态要解决的问题。
考虑这个问题的原则是:尽量减少总线上的信息往返。一般可以选择与该功能有关的信息输出最多的那台仪表上的功能块。
3.三大控制系统之间的差异
我们已经知道,FCS是由DCS与PLC发展而来,FCS不仅具备DCS与PLC的特点,而且跨出了革命性的一步。而目前,新型的DCS与新型的PLC,都有向对方靠拢的趋势。新型的DCS已有很强的顺序控制功能;而新型的PLC,在处理闭环控制方面也不差,并且两者都能组成大型网络,DCS与PLC的适用范围,已有很大的交叉。下一节就仅以DCS与FCS进行比较。在前面的章节中,实际上已涉及到DCS与FCS的差异,下面将就体系结构、投资、设计、使用等方面进行叙述。
(5)多变量、多节点、串行、数字通信系统取代单变量、单点、并行、模拟系统。
(6)是互联的、双向的、开放的取代单向的、封闭的。
(7)用分散的虚拟控制站取代集中的控制站。
(8)由现场电脑操纵,还可挂到上位机,接同一总线的上一级计算机。
(9)局域网,再可与internet相通。
为了使现场总线满足可互操作性要求,使其成为真正的开放系统,在IEC国际标准,现场总线通讯协议模型的用户层中,就明确规定用户层具有装置描述功能。为了实现互操作,每个现场总线装置都用装置描述DD来描述。DD能够认为是装置的一个驱动器,它包括所有必要的参数描述和主站所需的操作步骤。由于DD包括描述装置通信所需的所有信息,并且与主站无关,所以可以使现场装置实现真正的互操作性。
减少信息往返是网络设计和系统组态的一条重要原则。减少信息往返常常可带来改善系统响应时间的好处。因此,网络设计时应优先将相互间信息交换量大的节点,放在同一条支路里。
减少信息往返与减少系统的线缆有时会相互矛盾。这时仍应以节省投资为原则来做选择。如果所选择系统的响应时间允许的话,应选节省线缆的方案。如所选系统的响应时间比较紧张,稍微减少一点信息的传输就够用了,那就应选减少信息传输的方案。