品质异常停线处理作业办法
品质异常处理作业流程图
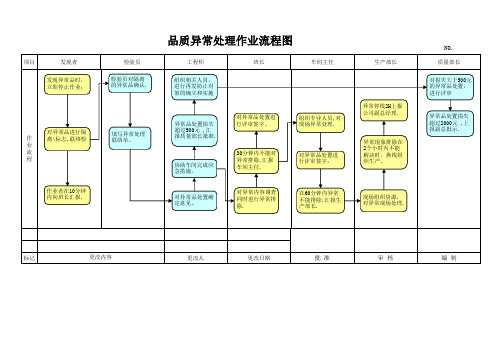
异常品处置损失 超过500元 ,汇 报质量部长批准.
对异常品处置进 行评审签字。
组织专业人员,对 现场异常处理.
异常品处置损失 超过2000元 ,上 异常现象排除在 2个小时内不能 解决时,换线组
30分钟内不能对 异常排除,汇报 协助车间完成应
对异常品处置进 行评审签字。
作业者在10分钟 内向班长汇报.
品质异常处理作业流程图
项目 发现者
发现异常品时, 立即停止作业;
NO.
车间主任 生产部长 质量部长
检验员
检验员对隔离 的异常品确认.
工程师
班长
组织相关人员, 进行再发防止对 异常停线2H上报 公司副总经理.
对损失大于500元 的异常品处置,
作 业 流 程
对异常品进行隔 离\标志,联络检
填写异常处理 联络单。
对异常品处置确 定意见。
对异常内容调查 同时进行异常排 除.
在60分钟内异常 不能排除,汇报生
现场组织资源, 对异常现场处理.
标记
更改内容
更改人
更改日期
批Hale Waihona Puke 准审 核编 制
品质异常处理流程

使用表单
3
开据《不合格 品评审表》
成品 检验员
1、对成品包装前的异常进行处理; 2、开据《不合格品评审表》; 3、分析原因,区分责任。
产品判定
开据《不合格
1、对出货前产品发现异常进行处
4
品评审表》
出货 检验员
材
1、组织隔离产品;
4
材料处理
料 不 合
车间 主任
2、向计划调度和生产部长进行汇报; 3、对生产异常进行记录;
格
4、组织材料退库。
处
理
1、通知进料检验员,对库存不合格
5
计划 调度
材料进行封存; 2、通知采购组织新的合格材料;
3、开据领料(补料)手续。
6
合格材料
进料 检验员
1、点验同类材料库存数量; 2、通知供货商; 3、对材料进行评审。
3、立刻通知当班负责人进行调试。
车间主任
1、调试后,对产品进行自检,合格后,
3
当班 负责人
送检验员确定; 2、检验员确认合格停止调试,否则继
续调试,直至达到要求为止。
调试
N
N
判定
1、判定合格的,取消异常标示,通知
4
Y
过程检 作业员恢复生产;
验员 3、判定不合格的,要求调试员继续调
试,ቤተ መጻሕፍቲ ባይዱ至合格为止。
判定
打印条形码 打印麦头
发货 /
5
恢复生产
作业员 根据检验员意见,恢复生产。
不合格品处理(退货退查)流程
序 号
作业流程
①零星报废品; 需二序返工处理;
品质异常处理作业流程图

对异常品处置确 定意见。
对异常品处置进 行评审签字。
30分钟内不能对 异常排除,汇报 车间主任.
对异常内容调查 同时进行异常排 除.
组织专业人员,对 现场异常处理.
对异常品处置进 行评审签字。
在60分钟内异常 不能排除,汇报生 产部长.
生产部长
异常停线2H上报 公司副总经理.
项目
发现者
发现异常品时, 立即停止作业;
对异常品进行隔
作
离\标志,联络检
业
流
程
作业者在10分钟 内向班长汇报.
检验员 检验员对隔离 的异常品确认.
填写异常处理 联络单。
品质异常处理作业流程图
工程师
组织相关人员, 进行再发防止对 策的确立和实施
班长
车间主任
异常品处置损失 超过500元 ,汇 报质量部长批准.
异常现象排除在 2个小时内不能 解决时,换线组 织生产。
现场组织资源, 对异常现场处理.
NO.
质量部长
对损失大于500元 的异常品处置, 进行评审
异常品处置损失 超过2000元 ,上 报副总批示.
标记
更改内容
更改人
更改日期
批准
审核
编制
品质异常处理流程

品质异常处理流程1.目的Purpose为规范公司制程品质异常处理流程,对制程中出现的品质异常及时处理,确保制程中的产品,品质得到有效控制,满足客户要求。
适用于制程品质异常处理3.定义Definitions3.1品质异常3.1.1IQC检验:超出允收水准,具体按照《进料检验作业规定》定义为准4.1.2巡检(单机台):外观单项不良:连续不良23pcs;尺寸单项不良:连续不良22pcs;功能单项不良:检验不良2Ipcs3.1.3全检:外观单项不良23%,尺寸单项不良21虬4.1.4抽检:违反3F(成型/适配/功能):检验不良21pcs.4.职责Responsibility4.1生产部4.1.1班组长:对不良品进行确认,对异常进行初步原因分析。
4.1.2课长:对生产管理人员作业层面等原因造成的异常,主导原因分析并推动改善。
5.2ME/生技:对非生产管理及作业层面的异常,主导原因分析并推动改善。
5.3品保单位4.3.1IPQC:对整个生产过程进行监控,将线上的异常向有关部门进行汇报,对改善行动进行跟踪,做好首件/巡检检查等。
4.3.2QE:对制程异常提出应急措施,并进行初步原因分析,跟进改善对策执行的有效性。
4.3.3SQE:对制程中确认的来料问题进行原因分析并推动供应商改善。
5.流程及说明ProcessFlowAndDescription5.1品质异常处理流程:6.2进料检验品质异常IQC进料检验发现的品质异常,依照《进料检验作业规定》处理。
6.3制程品质异常6.3.1作业员自检/互检发现之品质异常作业员依据作业指导书进行自检和互检,当发现品质异常时立即通知班组长进行确认处理。
6.3.2IPQC检验发现之制程异常6.3.2.1IPQC巡检发现品质异常时,通知生产单位确认并分析改善,将制程异常情况填写在《IPQC巡检记录表》和《IPQC尺寸检验记录表》中,初步统计不良数量,不良项目等信息,同时通知相关单位改善、处理。
OCAP品质异常处理流程图
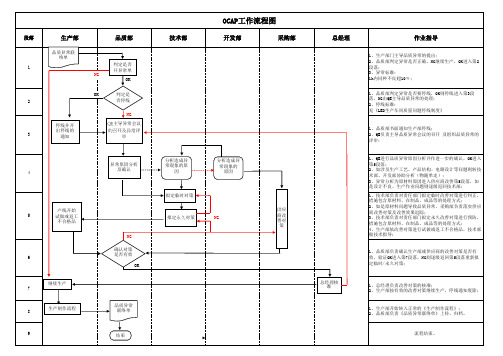
段落
1 2 3
生产部
品质异常联 络单
停线并开 出停线的
通知
品质部
判定是否
开异常单 NG
OK
OK
判定是
否停线
NG
QE主导异常会议 的召开及异常评
1、品质部负责确认生产部或供应商的改善对策是否有 效,验证OK进入第7段落,NG则逐级返回第5段落重新拟 定临时/永久对策;
1、总经理负责改善对策的核准; 2、生产部按有效的改善对策继续生产,停线通知废除;
1、生产部开始转入正常的《生产制作流程》; 2、品质部负责《品质异常联络单》上传、归档。
流程结束。
审
异常原因分析
4
及确认
产线开始
5
试做或返工
不合格品
6
继续生产 7
8
生产制作流程
9
NG 确认对策 是否有效
OK
品质异常
开发部
采购部
分析造成异 常現象的原
因
分析造成异 常現象的
原因
拟定临时对策
拟定永久对策
NG
供应 商改 善对
策
总经理
总经理核 准
作业指导
1、生产部门主导品质异常的提出; 2、品质部判定异常是否正确,NG继续生产,OK进入第2 段落; 3、异常标准: 1h内同种不良超10﹪;
1、品质部判定异常是否要停线,OK则停线进入第3段 落,NG由QE主导品质异常的处理; 2、停线标准: 见《LED生产车间质量问题停线制度》
1、品质部书面通知生产部停线; 2、QE负责主导品质异常会议的召开 及组织品质异常的 评审;
OQC异常及停复线处理程序

OQC异常及停复线处理程序1.目的:为建立一个完善的OQC异常及停复线处理流程,按照正确的路径作业,使之合理化、统一化、规范化及促进异常处理作业的有序进行.2.范围:本标准适用于OQC3.相关资料:3.1 不合格品管制办法3.2 矫正预防措施管理办法3.3 OQC抽样计划3.4 OQC检验规范3.5 AQ单处理流程作业规范3.6 Error code 不良代码4.定义:4.1 AQ(Abnormal Quality)单: 质量异常单电子化窗体4.2 Error Code:不良代码4.3 PCR: 制程变更需求4.4 PCN: 制程变更通知5.作业程序与权责:5.1 权责5.1.1 发生单位(OQC):异常处理,召集各单位参加会议,并追踪异常直至结案5.1.2 技术单位(硬件工程,软件工程,机构工程,工业工程):5.1.2.1 找出异常的初步原因, 并定义电测不良机台Sorting 方式5.1.2.2 根据责任单位给出的短期及预防对策进行评估.5.1.2.3 对于原材不良,送厂分析厂商回复NTF部分,技术单位应对其进行判断是否合理,并找出异常真因.5.1.2.4 计算Sorting和停线工时及费用.5.1.2.5 PCN/PCR导入时修正SOP.5.1.3 制造单位配合执行异常会议之相关决议.5.1.4 生管单位:5.1.4.1 停线或复线后,生产排程因应的调节与安排。
5.1.4.2 不良影响到成品出货时,生管确认订单出货时间及订单的出货调整5.1.4.3 不良重工及Sorting的安排5.1.5 责任单位:异常及停线原因的追查以及对策实施5.1.6 品保单位(PQA&QSM)5.1.6.1 发现异常时,PQA做系统Rework5.1.6.2 对策导入设计到制程变更时,PQA开PCN导入会议5.1.6.3 异常或停复线需Highlight客户时,QSM将异常或停复线讯息反馈给客户5.1.7 FPM若不良机台未下对策,但客人由于其他原因同意特采出货时,FPM开立特单5.2 作业程序:5.2.1 异常处理程序5.2.1.1 OQC发现异常, 立即记录不良发生的相关信息,并通知相关单位确认不良5.2.1.2 相关单位一起将不良回流产线,确认产线是否可以卡下不良5.2.1.3 OQC将不良机台贴上OQC Reject单,并召开一次会议5.2.1.4 依抽样计划要求制造Sorting b台(b=i/3)机台, Sorting无不良则依异常处理流程处理,Sorting 发现≧2台不良时,立即停线处理5.2.1.5 Sorting过程中发现1pcs同现象不良,则扩大Sorting i台, Sorting无不良则依异常处理流程处理,若Sorting过程中发现≧1台同现象不良时,立即停线处理5.2.1.6 技术单位在未拆机台30分钟或拆机台60分钟内给出短期对策(分析出人为或原材造成不良).并在3~4小时内分析出问题真因,并发出分析报告.5.2.1.7 经分析涉及到主板时,必须回流SMT看是否可以将不良卡下.5.2.1.8 OQC根据工程分析的真因确定不良影响范围并召开二次异常会议5.2.1.9 经分析为人为原因造成时,责任单位在30分钟之内给出短期对策.5.2.1.10 经分析为原材时不良,请MQC到现场确认,MQC请厂商进厂确认,厂商3hs内到厂,3天内回复初步分析报告,7天回复最终报告.5.2.1.11 MC确认是否有替代料及替代料库存是否满足产线需求,若替代料可满足产线需求则换替代料上线5.2.1.12 若无替代,则MQC 找厂商进厂Sorting原材上线, WIP工程单位提供短期预防对策5.2.1.13 若异常涉及停线及影响出货时, 需通知生管做相应处理,OQC对成品进行机台Hold,并在适当时机解除Hold.5.2.1.14 不良机台经维修解碼回流产线后,必须经OQC复判方可入库. 5.2.1.15 若对策需长期导入时,PQA开PCN/PCR导入会议.5.2.1.16 OQC开出AQ单电子文件.追踪责任单位AQ单回复状况,并确认对策有效性.5.2.5停线处理程序:5.2.5.1 OQC 12小时内抽检到两台以上(含两台)同机种同现象异常时,立刻纪录不良发生的相关讯息,产线立即停线,并通知相关部门参加会议.5.2.5.2 发生1pcs烧板,烧机或safety问题时,产线立即停线.5.2.5.3 抽到1pcs异常,Sorting b台(b=i/3)时发现≧2台同现象不良时,产线立即停线5.2.5.4 抽到1pcs异常,Sorting b台时发现1pcs不良,追加sorting i台时发现≧1同一不良时,产线立即停线.5.2.5.5 抽到1pcs HSF超标时,产线立即停线.5.2.5.6 停线发生时, OQC召开停线会议,相关单位需于5mins内到会议区参加会议,停线0.5hr需通知到厂级主管,1hr需通知到客户. 5.3 OQC异常处理流程图(见第5页):5.4 OQC停复线处理流程上述内容,如客户有特别要求,则根据客户要求进行相应的调整和修改6.附件6.1 OQC Reject单6.2 OQC品质异常通知单品质异常处理单TO:□生产部□工程部□品质部□PMC □仓库□其它。
品质异常停线、恢复生产的管理规定

资料范本本资料为word版本,可以直接编辑和打印,感谢您的下载品质异常停线、恢复生产的管理规定地点:__________________时间:__________________说明:本资料适用于约定双方经过谈判,协商而共同承认,共同遵守的责任与义务,仅供参考,文档可直接下载或修改,不需要的部分可直接删除,使用时请详细阅读内容品质异常停线、恢复生产的管理规定一、目的:建立公司品质预警机制,督导产品整个生产环节的品质异常及时处理,推动全员品质意识的提升,做到防患于未然,减少失效成本与浪费。
二、范围:适用于公牛集团所有产品生产加工过程中的品质异常停线和恢复生产的流程管理三、处理流程和职责:3.1 品管/工程/生产组长以上管理者对不符合品质抽检标准(AQL)或违背制程工艺、作业标准(SIP/SOP),导致返工、无效劳动或导致品质合格率下降等异常事实,均有权对线组长发出《停线通知单》.QE/PE工程师须对异常事实做出分析,明确责任部门,并组织职能部门紧急评审、做出决议,经课长或经理以上审核后,发给相关部门执行纠正措施;对批量特采、降级使用、让步放行、恢复生产的最低审核权为总监级别,原则上国标产品由总经理作最后批准,外贸产品由常务副总作最后批准;四、停线原则4.1材料与BOM要求不符不能替代的异常,4.2超出AQL允收比率的任何材料异常,4.3擅自变更产品安规设计、材料材质要求,导致产品安全隐患的异常;4.4不遵守工艺标准的和设备操作规程,造成品质不良率达到5%的异常;4.5造成制程工序巡查、成品抽查品质一次性合格率小于90%的异常;4.6可能造成下工序生产批量返工,形成无效劳动和材料报废的异常;4.7其他设备和环境因素造成市场重大投诉与返修召回等异常风险。
五、恢复生产原则5.1 当上述异常原因分析与对策措施,均得到及时纠正和有效改善时;5.2设计缺陷、模具修改不能及时改善时,且没有库存时,或改善成本过高(超出5万元);5.3不会导致客户投诉、不造成安全隐患、降级和特采应得到逐级审批时.六、运用表单《停线通知单》、《恢复生产申请单》一式两份七、本规定从2010年12月23日起开始实施。
OCAP品质异常处理流程图-经典

分析造成异 常現象的 原
因
拟定临时对策
拟定永久对策
NG
供应 商改 善对 策
总经理
总经理核 准
作业指导
1、生产部门主导品质异常的提出; 2、品质部判定异常是否正确,NG继续生 产,OK进入第2段落; 3、异常标准: 1h内同种不良超10﹪;
1、品质部判定异常是否要停线,OK则停线进入第 3段落,NG由QE主导品质异常的处理; 2、停线标准: 见《LED生产车间质量问题停线制度》
段落
1 2 3
生产部
品质异常联 络单
停线并开出
品质部
判定是否
开异常单 NG
OK
OK
判定是否
停线
NG QE主导异常会议
异常原因分析 及确认
4
产线开始
5
试做或返工
不合格品
6
继续生产 7
8
生产制作流程
9
NG 确认对策 是否有效
OK
品质异常 联络单
结束
技术部
OCAP工作流程图
开发部
采购部
分析造成异 常現象的原
1、总经理负责改善对策的核准; 2、生产部按有效的改善对策继续生产, 停线通知废除;
1、生产部开始转入正常的《生产制作流 程》; 2、品质部负责《品质异常联络单》上传 、归档。
流程结束。
1、技术部负责对责任部门拟定临时改善 对策进行纠正,措施包含原材料、在制品 、成品等的处理方式; 2、如是原材料问题导致品质异常,采购 部负责落实供应商改善对策及改善效果追 踪; 3、技术部负责对责任部门拟定永久改善 对策进行预防,措施包含原材料、在制品 、成品等的处理方策是否有效,验证OK进入第7段落, NG则逐级返回第5段落重新拟定临时/永 久对策;
- 1、下载文档前请自行甄别文档内容的完整性,平台不提供额外的编辑、内容补充、找答案等附加服务。
- 2、"仅部分预览"的文档,不可在线预览部分如存在完整性等问题,可反馈申请退款(可完整预览的文档不适用该条件!)。
- 3、如文档侵犯您的权益,请联系客服反馈,我们会尽快为您处理(人工客服工作时间:9:00-18:30)。
探探修订履历※探Revision HistoryCatalogue1 目的(Purpose)制定合理的生产停线和停止出货的基准,确保不良品得到有效管控制。
2 适用范围(Scope)此档应用於IPPD印表机产品。
3 定义(Define )无4 职责(Responsibility )4.1 制造:负责将待CSA抽检的印表机移交给CSA及QC抽检等。
4.2 QC:负责制程品质检测和判定,及责任部门改善效果确认。
4.3 PE:负责印表机产品不良异常分析处理。
4.4 EE:负责处理电子元器件/元件不良分析。
4.5 TE: 负责分析测试程式引起的所有异常分析处理。
NPI: 负责协助相关部门工程人员分析异常和提供有效建议。
5 过程描述 ( Process Description ) 5.1当产线出现以下品质异常时,要求品质部门提出停线或停止出货:5.1.6 客户抱怨和 RMA 问题4.6 4.7SQE/IQC: 负责处理来料不良异常处理。
4.8 ME:负责制造生产或检测设备仪器异常处理。
4.9I E :负责主持重工会议且负责制定临时重工 SOP 。
4.10 维修 :负责协助经工程人员分析後非重工作业处理的不良进行修复。
4.11IT:负责SFC 系统管控和日常维护。
产品生产操作无生产作业指导书,作业员无相关机种/相关站别的上岗证,产线不按正常生产流程生5.1.15.1.2 产,私自变更工位。
产线生产时,工治具设备发现异常、测试程式错误、版本错误、参数设定错误等。
产线生产之机种混料使用(非替代料),生产用错料,使用超过保质期的物料生产。
5.1.3 首件不良为批量性不良生产时,或使用不符合 RoHS 或非安规认证物料等环保要求物料。
5.1.4CSA 测试工站发现异常:5.1.55.1.4.1 5.1.4.2 5.1.4.3 5.1.4.4 SOR SOR SOR SOR 之前: 之前: 之後: 之後: 产线不良品:5.1.5.1 如每条线每班发现 如每条线每班发现 如每条线每班发现 如每条线每班发现 生产线材料、制程作业不良率达到台功能不良时或发现 3 台相同的功能不良时停线。
台 Workmanship 要求产线停线 10 分钟教育。
台功能不良时或发现 2 台相同的功能不良时停线。
台 Workmanship 要求产线停线 10 分钟教育。
8% 时(每 1 小时统计资料)。
5.1.5.2 功能测试站测试不良达到 5% (每 1 小时统计资料)。
5.1.5.3 当某一生产线不良品 1 小时内累积达到 15 台时,或连续出现 5 台同一功能不良品时。
5.1.5.4 SPC 设置的控制图显示异常时。
5.1.6.1 当客户有抱怨时,工厂没有有效的纠正措施,要求停产。
5.1.6.2 当RMA 品经海外FAE 等回馈分析显示事先风险系数RPN 偏大超过100 ,无及时有效的临时对策时。
5.1.7 CSA按系统要求抽检不合格时而再次追加抽检N (N=不良数*15 )台时,仍然有不良时需要停线整顿、改善。
5.1.8 PPPL(MAVS+PPP)测试不合格,客户要求方面要求停线改善整顿时。
5.2 出货停止5.2.1 产品在出货时因搬运和堆叠造成产品不良时。
5.2.2 在包装时使用错误物料和方式等。
5.2.3 产品在储存时有受潮和发霉等现象。
5.2.4 在客户、用户端、检测中心显示环保管控有害物质检测、安规检测失效。
5.2.5 在客户对工厂进行过程审核、产品审核失效时,有要求停产改善整顿。
5.2.6 当发生停线处理异常时,SFC 自动提示或品保、客户要求停止出货时。
5.2.7 当SOR 试产阶段到大批量生产前各个部门汇集问题点无法解决,且得不到客户认可时。
5.2.8 制程不良发生未按公司不良或疑似不良品批重工处置且重检合格时,及不良品流到成品仓库时,仓库应根据SFC 系统提示或QC 要求实施挡货,停止出货。
5.2.9 判定其他任何重大品质问题时。
5.3 停线或停止出货实施时,QC 首先发出《停线或停止出货通知单》,如一般停线(指各别线体停线)要第一时间汇报到品保主管(专理或以上)级,如全面停线则要第一时间通知到品保最高主管(协理或以上)级,并联络相关责任部门(MFG、ENG、IQC、PP、TQM )一起会议检讨对策,再由TQM通知HP 客户。
《停线或停止出货通知单》由各部门会签确认後由QC 保管。
5.4 所有停线或停止出货异常,必需进行不良、异常原因分析及改善报告,并进行效果确认,直至改善OK。
5.4.1 制造部门违反作业流程规定作业等,由制造自身检讨,回复负责不良原因分析、制定改善措施,在提岀有效的应急临时对策後方可恢复生产。
在24小时内回复QC开岀“ PDCS "《制成品质异常回馈单》,QC收到制造回复的制程异常纠正预防措施单後,会同QC工程师一起确认改善对策实施效果,决定是否关闭该异常问题点。
5.4.2 制程不良由PE负责不良原因分析并提岀改善措施建议,或者根据初步分析结果要求做更深一EE/SQE/TE 步分析,QC 根据工程人员最终分析报告判定责任单位。
责任部门必需针对具体品质异常制定并实施有效改善措施。
在责任单位提出有效的应急临时对策後方可恢复生产。
收到QC 开出“PDCS ”《制成品质异常回馈单》,後必需在24 小时内回复,并定期向产品专案组人员和随线工程人员报告改善进度和措施实施效果。
QC 接收到责任单位回复的制程异常纠正预防措施单後,会同QC工程师一起确认改善对策实施效果,决定是否关闭该异常问题点。
5.4.3 测试软体问题、烧录程式问题引起不良由TE 负责不良原因分析并提出重工、改善措施建议,QC根据分析报告判定责任单位,责任部门负责针对具体品质异常制定并实施有效改善措施,收到QC开出“ PDCS ”《制成品质异常回馈单》,後必需在24 小时内回复,并定期向产品专案组人员和随线工程人员报告改善进度和措施实施效果。
QC接收到责任单位回复的制程异常纠正预防措施单後,会同QC工程师一起确认改善对策实施效果,决定是否关闭该异常问题点。
5.4.4 来料不良、或不符合RoHS 等环保、安规要求时,由SQE 联络、要求供应商进行不良原因分析和提出并实施有效改善对策,并定时向工厂内部相关部门报告异常处理进度及效果。
在必要时要求供应商或IQC 进行选别来救济生产。
5.4.5 生产工治具、设备、参数设定错误或运行异常或导致不良产生时,由ME 负责异常原因分析,并针对具体异常制定并实施有效改善措施,收到QC开岀“ PDCS "《制成品质异常回馈单》,後必需在24小时内回复,并定期向产品专案组人员和随线工程人员报告改善进度和措施实施效果。
QC接收到ME回复的制程异常纠正预防措施单後,会同QC工程师一起确认改善对策实施效果,决定是否关闭该异常问题点。
546 在SOR试产阶段直至大批量生产期间,NPI负责协助相关部门进行不良原因分析,提岀改善措施建议,必要时经公司高层同意後联络客户请求支援改善方案,如在产品设计进行改善或产品要求方面进行调整。
5.5 恢复生产和恢复岀货5.5.1 制造部门停线整顿期间在QC确认改善对策有效、可行後,提交《产线恢复生产/岀货恢复申请》。
QC 工程师收到後会同其他工程人员实施评估,在品保专理/制造专理/工程专理/人员会签同意恢复生产,制造将批准後的《产线恢复生产/岀货恢复申请》,复印发放给QC等相关部门。
制造部门即可正式恢复生产。
5.6 产线在制品和仓库库存需要重工处理时,必需遵守执行以下:5.6.1 由责任部门通知所有相关人员岀席重工会议。
5.6.2 由IE负责主持重工会议且负责制定临时重工SOP。
5.6.3 分析工程人员在会议上提岀重工流程和注意事项。
5.6.4 QC 工程师与其他工程人员一起审核重工流程和提出注意事项或要求。
5.6.5 制造部门负责实施重工作业,重工完成後通知QC 人员再次检测。
5.6.6 QC 负责对制造重工完成品进行抽检或全检和判定,并记录相关检测结果。
5.7 改善对策有效行确认:5.7.1 改善对策效果确认范围/ 期限:在改善对策提出、实施後生产的3lots/ 实施4 个星期。
5.7.2 有效性标准:由QC工程师评估的事先风险系数RPN在改善对策实施明显下降。
5.7.3 不能出现同一不良原因引起的其他不良或同一类不良现象再次发生。
否则判定对策无效或需要组建改善专案组通过QCC 或6Sigma ( DAMIC )活动来加以持续改进。
6 记录的保存(Records Retention)本作业文件长期有效直到产品生命周期终结, 检查报告及相关记录最少要保留三个月.7 参考文件Reference7.1 《RoHS 实施管理办法》7.2 《产品重工及特殊作业办法》8 附件及附表Attachment产线异常处理流程图Flow Chart《停线或停止出货通知单》附件一:品质异常停线处理流程图:广因品质异常造成停线〃亭 止出货发生L.品保部门负责联络召集相关 责任部门(MFG 、ENG 、IQC 、PP 、TQM )一起会议 检讨对策如一般停线(指各别线体停 线)要第一时间汇报到品保主 管(专理或以上)一级各责任部门问题点总结, 避免类似问题发生PDCS否是如需重工作业参照《重工作 业处理流程》实施如全面停线则要第一时间通知 到品保最高主管(协理或以 上)一级临时对策判 生产是如需 工作业处理流程》实施*由ENG 部门分析原因并给出 ‘临时有效的改善措施要求ENGI 新 对策MF 依据临时对策恢复生产业参照《重 保根据ENGB 口品保根据EN 部门提 的临时对策评估判定能门提岀的临时对 策评估判定能否提出的责任部门给出有效的改善 对策并回复PDC 单品保判定改善 措施是否有效退件要求重 新对策QC 首先发出《停线或 停止出货通知单》同时第一时间向上级 汇报停线或异常情况 由TQM 通知HP 客户 ,反馈异常状况。