实验一 流化床反应器的特性测定
流化床反应器的机理

流化床反应器的机理
流化床反应器是一种常用于化学反应、热传递和质量传递的装置。
它采用颗粒物料床动态流化的方式来实现传递过程,具有反应速度快、传热传质效率高等优点。
其机理主要包括流化床的流动特性、颗粒物料的运动规律和反应过程中的热传递和质量传递。
流化床反应器中,床层物料通过流体动力学作用来实现动态流化。
在床层内,颗粒物料分散在气流中,并以不规则的运动方式进行流动,形成了类似于液体的流动形态。
这种流动方式对于反应过程有利,因为它可以增加反应物料的接触面积,提高反应速度。
在流化床反应器中,颗粒物料运动的规律对于反应过程也十分关键。
由于颗粒物料之间的碰撞和摩擦作用,会产生不同的运动方式,如滚动、滑动、碰撞等。
这些物料的运动方式和速度对于反应过程和传递过程都有着重要的影响。
例如,反应物料的分散程度和流动速度会影响反应速度和传质效率,而颗粒物料的摩擦和碰撞会产生热量,影响反应过程的温度。
在流化床反应器中,反应过程的热传递和质量传递也是重要的机理之一。
由于床层内的颗粒物料和气流之间的接触,会产生热量和质量的传递。
这种传递方式可以有效地将反应物料的热量和质量传递到床层内部,并提高反应速度和传递效率。
流化床反应器的机理主要包括流化床的流动特性、颗粒物料的运动规律和反应过程中的热传递和质量传递。
通过这些机理的协同作用,流化床反应器可以实现快速反应、高效传递和稳定运行等优点,是一种十分优秀的化学反应装置。
流化床反应器

s
3 mf
d p gumf
2
d
3 p
g
s 2
g
um2f
sdp
1.75
s g g
g
3 mf
dp s g 24.5g
g
化学反应工程
Re 1000
35
3
第7章 流化床反应器
• B类颗粒,称为粗颗粒。粒度较大,在100~600μm之间, 密度ρP=1400kg/m3 ~4000kg/m3 。适于流化,密相中气 、固返混较小 。砂粒是典型的B类颗粒。
• C类为超细颗粒,粒间有粘附性,颗粒间易团聚,气体容 易产生沟流,不适用于流化床。
• D类为过粗颗粒,流化时,易产生大气泡和节涌,操作难 以稳定,只在喷动床中才能较好流化。
固 定 床
起 始 流 化
散 式 )
膨 胀 床 (
聚 式 )
鼓 泡 床 (
节 涌
气 流 输
送
L Lf
L Lf
L0
L Lmf
流体 流体 流体 流体 流体 流体
10 化学反应工程
1
第7章 流化床反应器
1
流化床的基本概念
• 当通过床层的流体流量较小时,颗粒受到的升力 (浮力与曳力之和)小于颗粒自身重力时,颗粒在 床层内静止不动,流体由颗粒之间的空隙通过。此 时床层称为固定床。
雷诺准数: Remf
dPumf
umf: dP:
ρ,ρP:
Lmf: De:
μ:
初始流化速度 颗粒平均粒径 流体密度,颗粒密度 初始流化时的浓相段床高 流体的扩散系数 流体粘度
第7章 流化床反应器
25 化学反应工程
2
第7章 流化床反应器
流化床反应器的特性测定
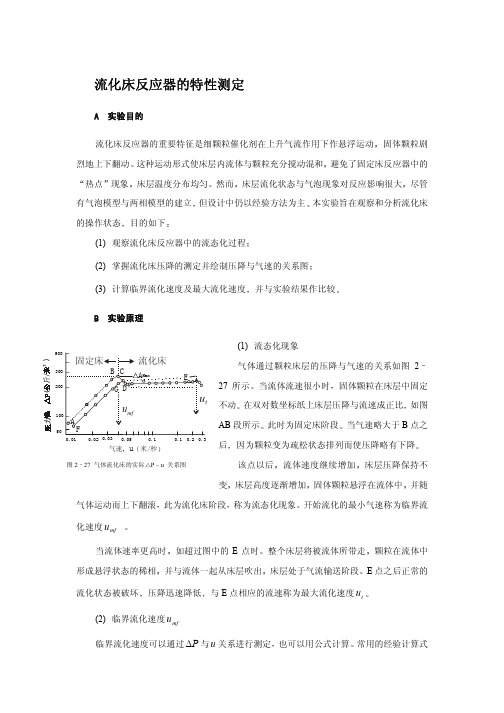
(2) 临界流化速度 u mf 临界流化速度可以通过 ∆P 与 u 关系进行测定 也可以用公式计算 常用的经验计算式
有
u mf = o.695
通过经验式计算常有一定偏差 临界流化速度 3 最大流化速度 u t
dp
1.82
(ρ
s
− ρg )
0..94
µ 0.88 ρ g 0.06
常常通过实验直接测定颗粒的
在条件满足的情下
最大流化速度 u t 亦称颗粒带出速度 下式计算
理论上应等于颗粒的沉降速度
按不同情况可用
ut =
2 (ρ s − ρ g )g dp
18µ
Re p < 0.4
4 (ρ s − ρ g )2 g ut = ρgµ 225
1 3
dp
0.4 < Re p < 500
3.1d p (ρ s − ρ g )g ut = ρg
其中
1 2
Re p > 500
Re p =
d p ut ρ g
µ
C 预习与思考 1 2 3 气体通过颗粒床层有哪几种操作状态 流化床中有哪些不正常流化现象 如何划分
各与什么因素有关 为什么
流化床反应器对固体颗粒有什么要求
流化床反应器的特性测定
A 实验目的 流化床反应器的重要特征是细颗粒催化剂在上升气流作用下作悬浮运动 固体颗粒剧
烈地上下翻动 这种运动形式使床层内流体与颗粒充分搅动混和 避免了固定床反应器中的 热点 现象 床层温度分布均匀 然而 床层流化状态与气泡现象对反应影响很大 尽管 有气泡模型与两相模型的建立 但设计中仍以经验方法为主 本实验旨在观察和分析流化床 的操作状态 目的如下
下行式循环流化床反应器气固传热特性研究

誓 ㈤ ( ㈤一 ) ]
卢:
(c 一 )
=
( ㈩ j
动规律方 面¨ J而对 下 行 床传 递 特 性 的研 究 仅 , 有少量 的气 固传 质 特 性 方 面 的报 导 , 行 床 下
=
O时 , T:
=
.
传热特 眭的研 究 文献 目前还 很 少 。作 为下 行床 反 应器基础 研究 的重 要课题 , 下行 床 气 固传 热特 性 , 是决定 工业 反 应 器设 计 放 大 、 的反 应 过 程 开 发 颏 和保证 反应 器 操 作 的 关 键之 一 , 此 对 下行 床 传 耳 热 特 睦进行研 究 是十分 必要 的 。本 研 究采 用稳 态
工 时 .’: … . 7
由 模 型 基 本 方 程 组 ( )口 求 得 F行 床 气 截 1 -
面平均传 热 系数 h 及表 观传热系数 h的表达式
!
^ ) ( :
() 2
实验方法 , 下行床 中气固传热特性 进行 了实验 对
研 究 , 定 了轴 向温 度 分 布 , 立 了传 热 模 型 , 测 建 对 实验结 果进 行 了关联 , 析 了下行 床 中气 固传 热 分 特性 及其影 响参 数 。
主 题词 : 流 并 向下 流化床反应器 气体 固体 传 热 系 数
并流 下行式 循 环流化 床 反应 器 ( 称下 行床 ) 简
一
=
是一 种新 型流 化床 反 应 器 , 有 许 多提 升 管反 应 具
卢
器 不具 备的优点 , 因而有 着广 泛 的工业 应 用前 景 。
特 别是 在石 油 加 工业 , 行 床 被 视 为催 化 裂 化 的 下 气 斟超短 接触 时 间提升 管反 应器 的换代 装 置 而钹 业界所 关注 。 目前对下 行 床的基础 研究 主要 集 中于 气 固运
实验气固流化床反应器流化特性测定

Bo l实验四 气固流化床反应器的流化特性测定一、实验目的1. 观察了解气固流化床反应器中不同气速下固体粒子的流化状况,建立起对流态化过程的感性认识。
2. 了解和掌握临界流化速度 U mf 和起始鼓泡速度 U mb 的测量原理、方法和步骤,明确细粒子流化床的基本特性。
3. 通过对 U mf 和 U mb 的测定,进一步理解两相理论以及临界流化速度与起始鼓泡速度的区别。
二、实验原理△1.在气固流化床反应器中,气体通过床层的压力降 P 与空床速度 U 0 之间的关系能够 很好地描述床层的流化过程。
如图 1 所示:气体自下向上流过床层。
当气速很小时,气体通过床层的压力降 △P 与空床速度 U 0 在对数坐标图上呈直线关系(图 1 中的 AB 段);当气速逐渐增大到 △P 大致等于 单位面积的重量时, △P 达到一极值(图 1 中 P 点);流速继续增大时,△P 略有降低;此后床层压力降 △P 基本不随流速而变。
此时将流速慢慢降低,开始时与前一样△P 基本不变, 直到 D 点以后, △P 则随流速的降低而降低,不再出现 △P 的极大值,最后,固体粒子又互相接触,而成静止的固定床。
2.在一正常速度下,处于正常流化的流化床,如果突然关闭气源,则由于床层中有气泡存在,以气泡形式存在的气体首先迅速逸出床层,床层高度迅速下降;而后是浓相中的气体逸出,床层等速下降;最后是粒子的重量将粒子间的部分气体挤出,床层高度变化很小。
由此可得其床层高度随时间变化的崩溃曲线(如图 2 所示)。
因此,可以设想,如果床层中△PgAPlog U图 1 △P ~ U 关系1 / 4DH THDHD300290280270260123456t(sec)图2H T~t关系没有气泡,则床层一开始就随时间等速下降,所以,将上述崩溃曲线中的等速部分外推到t=0处时的床层高度,即为浓相床层的高度H。
这样,只要重复上述过程,多做几条崩溃曲线,D总可以找到一条曲线,这条曲线正好无气泡逸出段,开始就是等速下降的起点。
实验4 流化床基本特性的测定

实验四流化床基本特性的测定流化床反应器是一种利用气体或液体通过颗粒状固体层而使固体颗粒处于悬浮运动状态,并使固体颗粒具有某些流体特征的一种床型,它是流态化现象的具体应用,已在化工、能源、冶金、轻工、环保、核工业等部门得到广泛应用。
化工领域中,加氢、烯烃氧化、丙烯氨氧化、费-托合成及石油的催化裂化等均采用了该技术。
因此,它是极为重要的一种操作过程。
流化床反应器的重要特征是细颗粒催化剂在上升气流作用下作悬浮运动,固体颗粒剧烈地上下翻动。
这种运动形式使床层内流体与颗粒充分搅动混和、物料连续、结构紧凑、传质速度快、传热效率高、床层温度分布均匀,避免了固定床反应器中的热点现象,但操作中会造成固体磨损、床层粒子返混严重、反应中转化率不高等现象。
一、实验目的1.通过冷模观察聚式和散式流态化的实验现象,建立起对流态化过程的感性认识。
2.了解流化床的压降分布原理,通过冷模测定流化床的特定曲线。
3.通过冷模观察得到临界流化速度和带出速度,并计算出费劳德数Fr、膨胀比和流化数。
4.掌握流化床液体停留时间分布的测定方法及实验结果分析。
二、实验原理1.流化现象流体从床层下方流入,通过图1中虚线所示的分布板而进入颗粒物料层时,随着流体流速u0的不同,会出现不同的流化现象(图1)。
(a)(b)(c)(d)(e)固定床临界流态化散式流态化聚式流态化稀相流态化图1 流化现象(1)固定床阶段流体流速较低时,固体颗粒静止不动,即未发生流化,床层属于固定床阶段(图1(a)),阻力随流体流速增大而增大。
(2)临界流化阶段流体流速继续增大,颗粒在流体中的浮力接近或等于颗粒所受重力及其在床层中的摩擦力时,颗粒开始松动悬浮,床层体积开始膨胀,当流速继续增大,几乎所有的粒子都会悬浮在床层空间,床层属于初始流化或临界流化阶段(图1(b))。
此时的流速称为临界流化速度或最小流化速度u mf。
(3)流化阶段对于液固流化床,当液速u f>u mf时,由于液体与固体粒子的密度相差不大,此种床层从开始膨胀直到气力输送,床内颗粒的扰动程度是平缓的加大的,床层的上界面较为清晰,即床层膨胀均匀且波动较小,床层属于散式流化阶段(图1(c))。
流化床实验报告(1)(1)(1)
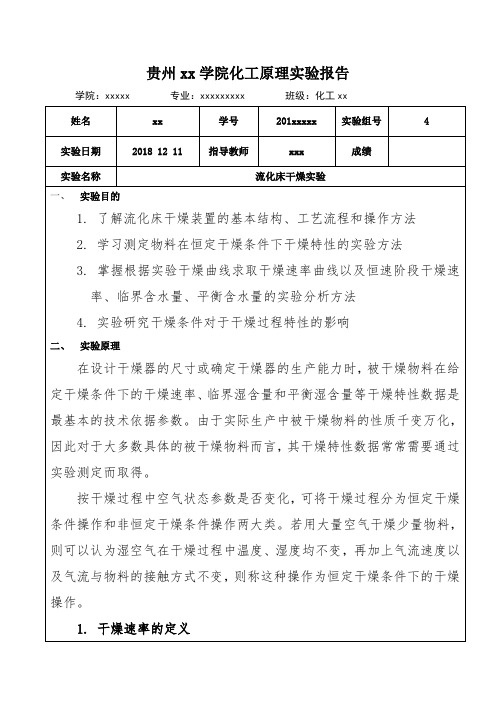
贵州xx学院化工原理实验报告学院:xxxxx 专业:xxxxxxxxx 班级:化工xx利用床层的压降来测定干燥过程的失水量。
(1)准备0.5~1kg 的湿物料,待用。
(2)开启风机,调节风量至40~60m 3/h ,打开加热器加热。
待热风温度恒定后(通常可设定在70~80℃),将湿物料加入流化床中,开始计时,此时床层的压差将随时间减小,实验至床层压差()恒定为止。
则物料中瞬间含水率为(11-3)式中,—时刻时床层的压差。
计算出每一时刻的瞬间含水率,然后将对干燥时间作图,如图11-1,即为干燥曲线。
图11-1恒定干燥条件下的干燥曲线上述干燥曲线还可以变换得到干燥速率曲线。
由已测得的干燥曲线求出不同下的斜率,再由式11-1计算得到干燥速率,将对作图,就是干燥速率曲线,如图11-2所示。
e p ∆i X eei p p p X ∆∆-∆=p ∆τi X i X i τi X iid dX τU U X图11-2恒定干燥条件下的干燥速率曲线将床层的温度对时间作图,可得床层的温度与干燥时间的关系曲线。
3. 干燥过程分析预热段见图11-1、11-2中的AB段或A′ B段。
物料在预热段中,含水率略有下降,温度则升至湿球温度t W,干燥速率可能呈上升趋势变化,也可能呈下降趋势变化。
预热段经历的时间很短,通常在干燥计算中忽略不计,有些干燥过程甚至没有预热段。
恒速干燥阶段见图11-1、11-2中的BC段。
该段物料水分不断汽化,含水率不断下降。
但由于这一阶段去除的是物料表面附着的非结合水分,水分去除的机理与纯水的相同,故在恒定干燥条件下,物料表面始终保持为湿球温度t W,传质推动力保持不变,因而干燥速率也不变。
于是,在图11-2中,BC段为水平线。
只要物料表面保持足够湿润,物料的干燥过程中总处于恒速阶段。
而该段的干燥速率大小取决于物料表面水分的汽化速率,亦即决定于物料外部的空气干燥条件,故该阶段又称为表面汽化控制阶段。
实验4 流化床基本特性的测定

下降,流体速度继续增加,床层压降保持不变,床层高度逐渐增加,固体颗粒悬浮在流体中,并随
气流上下流动,此为流化床阶段,在B点的流速就是临界流化速度umf。 (2)最大流化速度
当流体速度大于固体粒子在流体中的沉降速度时,粒子将被流体带出床层,这个速度称为最大
流化速度或粒子的带出速度ut,它是流化床流速的上限。此时如不连续补充固体颗粒,床层迅速消 失,所以在压力降图上曲线急剧下降(图2中的GH段)。颗粒在流体中沉降,受到重力、浮力和流
ut
3.1(
s
f
f
)gd p
1/ 2
(12) 式中:Re——雷诺数,Re= dP f ut/;
dp——颗粒当量直径,m; ρf—流体密度,kg/m3; ρS—颗粒密度,kg/m3; µ—流体粘度,kg ⋅m−1⋅s−1; ut—最大流化速度,m/s; umf—临界流化速度,m/s。 最大流化速度除了可用经验式计算外,也可通过实验直接测定。由图2可知,如果再加大流速
2
——方差或散度。
2
2
ˆt 2
2 Pe
2 1 2 Pe
1 e Pe
(19)
通过实验测得
c(τ)与
τ
的关系数据,然后由式(17)求得
tˆ
,由式(18)求得
2
,通过式
(19)求出模型参数 Pe 的值。
三、实验装置与流程
实验四 流化床基本特性的测定
流化床反应器是一种利用气体或液体通过颗粒状固体层而使固体颗粒处于悬浮运动状态,并使 固体颗粒具有某些流体特征的一种床型,它是流态化现象的具体应用,已在化工、能源、冶金、轻 工、环保、核工业等部门得到广泛应用。化工领域中,加氢、烯烃氧化、丙烯氨氧化、费-托合成 及石油的催化裂化等均采用了该技术。因此,它是极为重要的一种操作过程。
流化床反应器(1)

1 气固流化床设计基础数据流化床反应器的操作工艺参数为:反应温度为400 ℃,反应压力为 0.3 MPa (绝压),甲醇操作空速为 1~51h -。
MTO 成型催化剂粒径范围为50~140μm ,平均粒径为 80μm 。
颗粒密度为 1200 kg/m3,堆密度为 700 kg/m3。
甲醇在400℃下的粘度根据常压下气体粘度共线图查得为 0.021m Pa.s ,甲醇 400℃下的密度根据理想气体状态方程估算为 1.715kg/m3。
甲醇原料中水含量为 1%。
流化床催化反应器主要包括以下几个组成部分:反应器壳体尺寸、气体分布装置、换热装置、气固分离装置、内部构件、以及催化剂颗粒的加入和卸出装置。
MTO 反应为放热反应,工业装置中为避免反应器床层温度过高,需设置内取热或外取热器,由于小型固定流化床反应器尺度较小,散热效应较大,应考虑在反应器外设置加热炉保持 MTO 反应温度恒定,不必设置取热器。
我们在确定了操作条件(T :400 ℃,P :0.3 MPa )、反应器内气体原料和固体催化剂物化性质的条件下,计算了催化剂装填量、操作气速和反应器主体尺寸,并对气体分布器、气固分离装置和催化剂加卸料口的设置进行了简要介绍。
2 操作气速2.1 最小流化速度计算当流体流过颗粒床层的阻力等于床层颗粒重量时,床层中的颗粒开始流动起来,此时流体的流速称为起始流化速度,记作mf U 。
起始流化速度仅与流体和颗粒的物性有关,其计算公式如下式所示: 对于p mf ep d U R ρμ=20<的小颗粒2()1650p p mf d gU ρρμ-= (1) 对于1000p mf ep d U R ρμ=>的大颗粒1/2()[]24.5p p mf d gU ρρρ-= (2)式中: p d 为颗粒的平均粒径;.p ρρ分别为颗粒和气体的密度; μ为气体的粘度。
本流化床雷诺数:ep R <20将已知数据代入公式(1),25235()(810)(1200 1.715) 2.210/16501650(2.110)p p mf d gU m s ρρμ----⨯⨯-===⨯⨯⨯558100.0022 1.715202.110p mf ep d U R ρμ--⨯⨯⨯==<⨯ 将mf U 代入弗鲁德准数公式 2mf mf p U F d g =作为判断流化形式的依据。
下行式循环流化床反应器气固传热特性研究
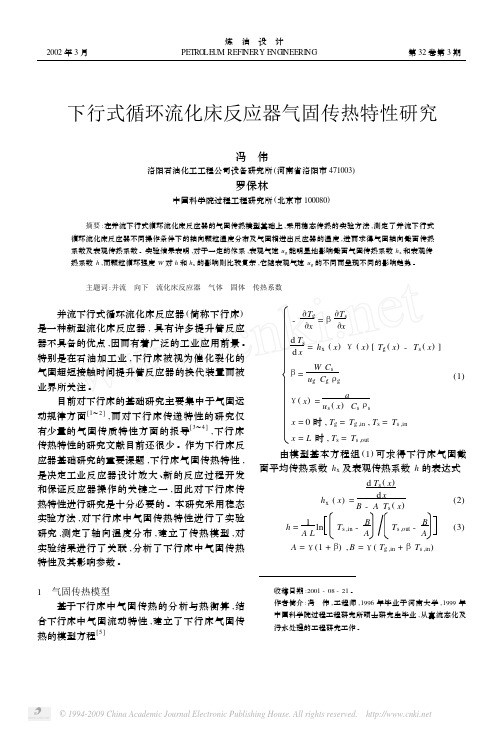
3 实验结果及分析 3. 1 颗粒温度的轴向变化规律
如图 2 所示 ,随着气固相并行下流 ,由于气固 相传热 ,新鲜颗粒在入口发展段 (第一 、第二加速 段) 被迅速加热 , 颗粒温度迅速上升 ,颗粒相温度 沿床层轴向的变化曲线较为陡峭 ;在稳定段内 ,颗 粒温度的变化曲线由陡峭渐趋平缓 。在入口发展 段内 ,气固相温差大 ,气固相间的传热推动力较 大 ,加之入口发展段处气固相在轴 、径向的混合较 为剧烈 ,气固相传热快 ,从而使颗粒相温度迅速上 升 。由于气固相间传热及向壁面传热 ,在入口发 展段气相温度下降幅度较大 ,颗粒相温度上升很 快 ,使稳定段内气固相间温差变小 ,且气固相间的 混合也主要是径向混合 ,远没有入口发展段处剧 烈 ,气固相间传热速率较小 ,因而稳定段内颗粒相 温度上升幅度不大 。
在入口发展段内 , W 对 hx 存在两种相反趋势 的影响 : ①W 增大 ,颗粒浓度增大 ,床层空隙率变 小 ,气固相间传热推动力在床层轴向的下降梯度 变大 ,同时颗粒间的团聚趋势加强 ,气体与颗粒间 有效接触减少 ,使得同一轴向截面上气固相传热 系数减小 。 ②W 增大时 ,床层内湍动程度增大 ,传 热边界层变薄 ,传热阻力变小 ,从而改善气固相间 传热 ,使 hx 有增大的趋势 。 ①和 ②两种影响趋势 的大小随着床层操作条件 (如 ug 和 W 等) 的不同 而不同 ,如图 5 (a) 所示 。实验结果表明 , W 和 hx 一样 ,对稳定段内 hx 的影响不是很显著 ,且随着 W 的增大 , hx 呈下降趋势 ,如图 5 ( b) 所示 。其原 因在于稳定段内气固两相滑移速度的变化量趋于 零 ,湍动与混合较弱 ,且由于经历了入口发展段的
主题词 :并流 向下 流化床反应器 气体 固体 传热系数
并流下行式循环流化床反应器 (简称下行床) 是一种新型流化床反应器 , 具有许多提升管反应 器不具备的优点 ,因而有着广泛的工业应用前景 。 特别是在石油加工业 ,下行床被视为催化裂化的 气固超短接触时间提升管反应器的换代装置而被 业界所关注 。
实验一 流化床反应器的特性测定
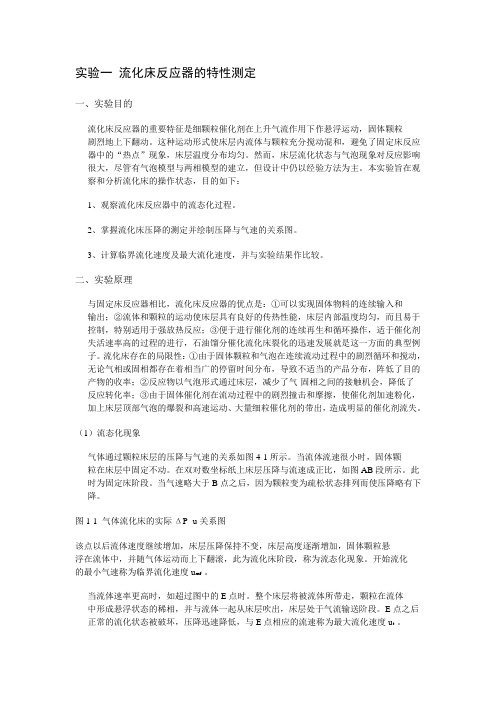
实验一流化床反应器的特性测定一、实验目的流化床反应器的重要特征是细颗粒催化剂在上升气流作用下作悬浮运动,固体颗粒剧烈地上下翻动。
这种运动形式使床层内流体与颗粒充分搅动混和,避免了固定床反应器中的“热点”现象,床层温度分布均匀。
然而,床层流化状态与气泡现象对反应影响很大,尽管有气泡模型与两相模型的建立,但设计中仍以经验方法为主。
本实验旨在观察和分析流化床的操作状态,目的如下:1、观察流化床反应器中的流态化过程。
2、掌握流化床压降的测定并绘制压降与气速的关系图。
3、计算临界流化速度及最大流化速度,并与实验结果作比较。
二、实验原理与固定床反应器相比,流化床反应器的优点是:①可以实现固体物料的连续输入和输出;②流体和颗粒的运动使床层具有良好的传热性能,床层内部温度均匀,而且易于控制,特别适用于强放热反应;③便于进行催化剂的连续再生和循环操作,适于催化剂失活速率高的过程的进行,石油馏分催化流化床裂化的迅速发展就是这一方面的典型例子。
流化床存在的局限性:①由于固体颗粒和气泡在连续流动过程中的剧烈循环和搅动,无论气相或固相都存在着相当广的停留时间分布,导致不适当的产品分布,阵低了目的产物的收率;②反应物以气泡形式通过床层,减少了气-固相之间的接触机会,降低了反应转化率;③由于固体催化剂在流动过程中的剧烈撞击和摩擦,使催化剂加速粉化,加上床层顶部气泡的爆裂和高速运动、大量细粒催化剂的带出,造成明显的催化剂流失。
(1)流态化现象气体通过颗粒床层的压降与气速的关系如图4-1所示。
当流体流速很小时,固体颗粒在床层中固定不动。
在双对数坐标纸上床层压降与流速成正比,如图AB段所示。
此时为固定床阶段。
当气速略大于B点之后,因为颗粒变为疏松状态排列而使压降略有下降。
图1-1 气体流化床的实际ΔP -u关系图该点以后流体速度继续增加,床层压降保持不变,床层高度逐渐增加,固体颗粒悬浮在流体中,并随气体运动而上下翻滚,此为流化床阶段,称为流态化现象。
气固相催化反应乙醇脱水流化床实验报告
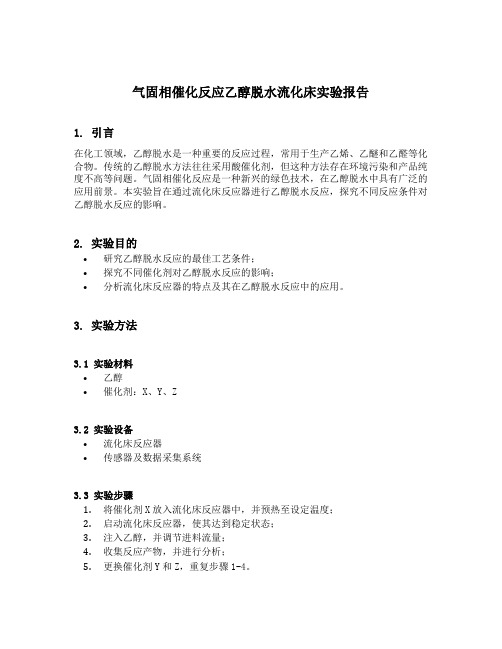
气固相催化反应乙醇脱水流化床实验报告1. 引言在化工领域,乙醇脱水是一种重要的反应过程,常用于生产乙烯、乙醚和乙醛等化合物。
传统的乙醇脱水方法往往采用酸催化剂,但这种方法存在环境污染和产品纯度不高等问题。
气固相催化反应是一种新兴的绿色技术,在乙醇脱水中具有广泛的应用前景。
本实验旨在通过流化床反应器进行乙醇脱水反应,探究不同反应条件对乙醇脱水反应的影响。
2. 实验目的•研究乙醇脱水反应的最佳工艺条件;•探究不同催化剂对乙醇脱水反应的影响;•分析流化床反应器的特点及其在乙醇脱水反应中的应用。
3. 实验方法3.1 实验材料•乙醇•催化剂:X、Y、Z3.2 实验设备•流化床反应器•传感器及数据采集系统3.3 实验步骤1.将催化剂X放入流化床反应器中,并预热至设定温度;2.启动流化床反应器,使其达到稳定状态;3.注入乙醇,并调节进料流量;4.收集反应产物,并进行分析;5.更换催化剂Y和Z,重复步骤1-4。
4. 实验结果与讨论4.1 不同催化剂对乙醇脱水反应的影响通过实验我们发现,催化剂对乙醇脱水反应具有显著影响。
在催化剂X的作用下,乙醇脱水反应产物中主要为乙烯。
而催化剂Y和Z则分别导致乙醚和乙醛的生成。
这说明不同催化剂具有不同的催化活性,可以选择合适的催化剂来控制反应产物的选择性。
4.2 乙醇脱水反应的最佳工艺条件我们进一步研究了乙醇脱水反应的最佳工艺条件。
通过调节反应温度和进料流量,我们发现在温度为300°C、进料流量为X时,乙烯的收率最高。
这表明在一定的温度和进料流量范围内,乙烯的产生达到了峰值。
4.3 流化床反应器的特点及其在乙醇脱水反应中的应用流化床反应器具有良好的传质与传热性能,能够提高反应速率和产物选择性。
在乙醇脱水反应中,流化床反应器能够有效控制反应温度和催化剂的分散性,提高反应效果。
此外,流化床反应器还具有连续生产的优势,适用于工业化生产。
5. 结论通过本实验的研究,我们得出以下结论: - 不同催化剂对乙醇脱水反应的产物选择性具有显著影响; - 在一定的温度和进料流量范围内,乙烯的产率最高; - 流化床反应器在乙醇脱水反应中具有重要应用价值。
非均相光芬顿体系的建立与内循环流化床反应器的研究

非均相光芬顿体系的建立与内循环流化床反应器的研究一、本文概述随着环境保护和可持续发展的日益重视,高效、绿色的废水处理技术成为了研究的热点。
在众多高级氧化技术中,光芬顿反应以其强大的氧化能力和环境友好性受到了广泛关注。
然而,传统的均相光芬顿体系存在反应速率慢、催化剂难以回收、易产生二次污染等问题。
为了解决这些问题,本文提出了一种非均相光芬顿体系,并深入研究了内循环流化床反应器在该体系中的应用。
本文首先概述了非均相光芬顿体系的基本原理和研究现状,指出了传统均相光芬顿体系存在的问题和挑战。
然后,详细介绍了非均相光芬顿体系的建立过程,包括催化剂的选择、制备和表征,以及反应条件的优化。
在此基础上,进一步探讨了内循环流化床反应器的设计原理和结构特点,并通过实验验证了其在非均相光芬顿体系中的应用效果。
本文的研究旨在为非均相光芬顿体系在实际废水处理中的应用提供理论基础和技术支持,为推动绿色、高效的废水处理技术发展提供新的思路和方法。
本文的研究成果也有助于促进环境保护和可持续发展的实现,具有重要的社会意义和经济价值。
二、非均相光芬顿体系理论基础非均相光芬顿体系是一种高级氧化技术,结合了光催化与芬顿反应的优势,旨在提高污染物的降解效率和矿化度。
其理论基础主要源自光催化、芬顿反应以及两者的协同作用。
光催化过程中,光敏催化剂如TiO₂在受到光能激发后,会产生电子-空穴对。
这些电子-空穴对具有很高的氧化还原活性,可以引发一系列氧化还原反应。
当这些反应发生在水溶液中时,可以产生羟基自由基(·OH)等强氧化剂,从而实现对有机污染物的降解。
芬顿反应则是一种利用亚铁离子(Fe²⁺)和过氧化氢(H₂O₂)在酸性条件下发生反应,产生高活性的羟基自由基(·OH)。
羟基自由基具有很强的氧化能力,可以无选择性地氧化大多数有机污染物,甚至可以将它们完全矿化为二氧化碳和水。
在非均相光芬顿体系中,光催化与芬顿反应相互协同,共同促进污染物的降解。
化学反应工程第八章流化床反应器
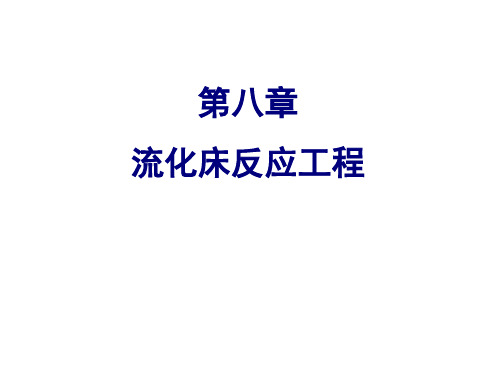
2. 聚式流态化与散式流态化 使用不同的流体介质,固体流态化可分为:
散式流态化(particulate fluidization) 聚式流态化(aggregative fluidization)
2. 聚式流态化与散式流态化
理想流态化是固体颗粒之间的距离随着流体流速增加而 均匀地增加,颗粒均匀地悬浮在流体中,所有的流体都 流经同样厚度的颗粒床层,保证了全床中的传质、传热 和固体的停留时间都均匀,对化学反应和物理操作都十 分有利。理想流态化的流化质量(fluidization quality) 是最高的。 在实际的流化床中,会出现颗粒及流体在床层中的非均 匀分布,越不均匀,流化质量越差。 液体作流化介质时,液体与颗粒间的密度差较小,在很 大的液速操作范围内,颗粒都会较均匀地分布在床层中, 比较接近理想流态化,称为散式流态化。
(2) 聚式流态化
由于气泡在床层径向截面上不均匀分布,诱发了床内密 相的局部以致整体的循环流动,气体的返混加剧。这种 流型称为 鼓泡流态化 (bubbling fluidization),气-固接 触效率和流化质量比散式流态化低得多。 气泡上升到床层表面时的破裂将部分颗粒弹出床面。在 密相床上面形成一个含有少量颗粒的自由空域 (freeboard)。 一部分在自由空域内的颗粒在重力作用下返回密相床, 而另一部分较细小的颗粒就被气流带走,只有通过旋风 分离器的作用才能被捕集下来,经过料腿而返回密相床 内。
快 床 颗 粒 的 径 向 分 布
颗粒含率 高 度 实际分布 模型分布
气流输送 快床 湍流床 鼓泡流化床 0.2 0.4 0.6 密度
图:各种状态 流化床沿床高密度变化
2. 高气速气-固流态化中的流型
流化床反应器
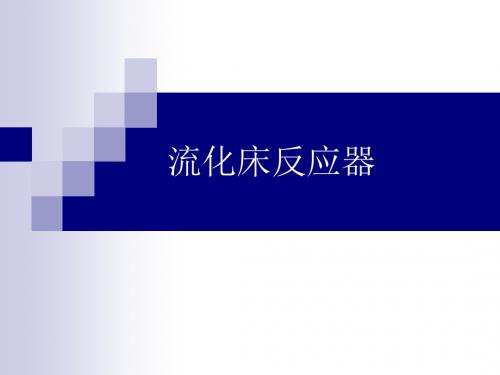
流化床基本结构
结构分为: 浓相段、稀相段、扩大
段、锥底。
内部构件: 气体分布板、换热装置、
气固分离装置、挡板档 网、气体预分布器等。
流化床反应器的特点
1.床层温度均匀,避免局部过热。 2.颗粒处于运动状态,表面更新,强化传质。 3.颗粒小,催化剂有效系数高。 4.流化状态,便于操作。 5.传热系数大,换热面积小。 6.生产强度大。 7.返混严重,一次转化率低。 8.颗粒磨损,要求催化剂强度大。 9.对设备磨损严重。
流化数
u k 操
u 临
流化床的压力降
颗粒悬浮静止时受力 向下:重力 向上:浮力、流体阻力
平衡时 重力=浮力+流体阻力
公式推导:式(3-6) 说明:床层压力降与流速无关
超过带出速度时,空隙率增大、压力降减 小。
膨胀比和空隙率
膨胀比
VL
R f f
பைடு நூலகம்
VL
0
mf
空隙率
Δtm——平均传热温度差,K
(三)流化床内换热器的结构型式
列管式换热器:单管式和套管式 管束式换热器:直列和横列 鼠笼式换热器 蛇管式换热器
列管式换热器:单管式
列管式换热器:套管式
立式管束式
横排管束式换热器
鼠笼式换热器
蛇管式换热器
三、流化床反应器的计算
(一)流化床直径的计算 (二)流化床高度的确定
确定方法 :半经验公式
带出速度U带
操作速度大于带出速度时,催化剂颗粒将 被带出流化床反应器
确定方法 注意 原则上:临界流化速度<操作速度<带出速度 实际上:往往偏离这个范围。有些工业反应
实验十三 流化床演示实验

实验十三 流化床演示实验一、实验目的流化床反应器,由于其结构上的特点,具有床内温度分布均匀,传热、传质效率较好,因此广泛地应用在石油、化工、煤炭、医药等部门,流态化技术日益受到重视。
通过本演示实验,要求了解气固相的运动特征,固定床、流化床的压降,如何表示临界流化速度及最大流化速度。
二、实验原理气体通过固定床时,压力降随着流速不断增大。
当压力降达到最高值时,床层开始松动,即开始流化。
此时的流速称为临界流化速度u mf ,当流速继续增大,以致使床层的固体颗粒带出,不再停留床内,此地的流速称为最大流化速度,u mf 因此测量压力降可直接反映流化速度。
流速与压力降的关系可用图13-1表示。
当流体通过床层固体颗粒时,由于流体与床层固体颗粒间的摩擦及流体的紊流作用产生压降。
压力降随空塔流速增大而增大。
如AB 线所示,AB 为未流化的固定床。
达到接近临界流化速度B 点时,固体颗粒层开始膨胀而不流化,由于空隙率增大,压力降较前降低。
在B 点后,颗粒可以在小范围内重新排列,空隙率略有增大。
在C 点后,全部床层流态化,若再增大流速,当流体的向上流速大于颗粒的沉降速度时,则固体颗粒被流体带出,此时的压力降将减少。
通过压力降的测量可以清楚表示它们的关系。
关于临界流休速度及最大流化速度,文献介绍的计算公式很多,但误差也很大,一般都采用实验方法实测求得。
流量用孔板流量计测量:ρρρ)(2-=R gR oAo C Vs式中:Vs ——流体的体积流量,m 3/s ;R ——U 型管压差计读数,m ;ρR ——压差计中指示液密度,kg/m 3; C o ——孔流系数。
图13-1 流速与压强的关系示意图Vs Aw V sw =∝∝压降:22f p l u h h f fg d gR p g λρρ∆==∙∝∆∆=△p=ΔR(ρ指-ρ)g其中:ρ指——压差计中指示液密度,kg/m 3。
ΔR ——U 型管中位差,m 。
g ——重力加速度,g=9.81m/s 2。
流化床电化学反应器研究:(Ⅱ)导电机理及电位波动特性的实验研究
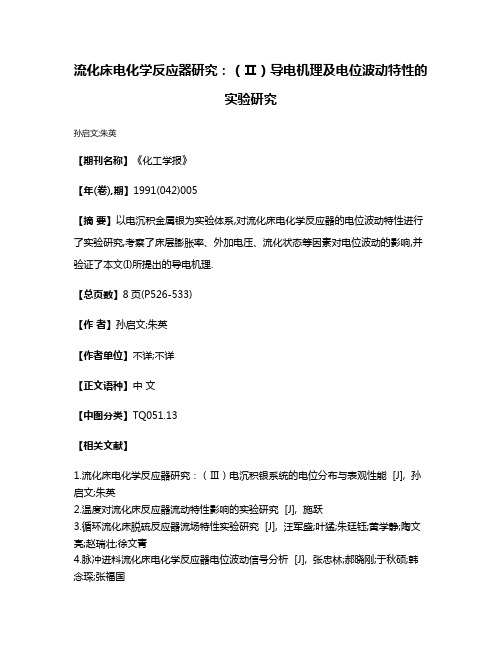
流化床电化学反应器研究:(Ⅱ)导电机理及电位波动特性的
实验研究
孙启文;朱英
【期刊名称】《化工学报》
【年(卷),期】1991(042)005
【摘要】以电沉积金属银为实验体系,对流化床电化学反应器的电位波动特性进行了实验研究,考察了床层膨胀率、外加电压、流化状态等因素对电位波动的影响,并验证了本文(I)所提出的导电机理.
【总页数】8页(P526-533)
【作者】孙启文;朱英
【作者单位】不详;不详
【正文语种】中文
【中图分类】TQ051.13
【相关文献】
1.流化床电化学反应器研究:(Ⅲ)电沉积银系统的电位分布与表观性能 [J], 孙启文;朱英
2.温度对流化床反应器流动特性影响的实验研究 [J], 施跃
3.循环流化床脱硫反应器流场特性实验研究 [J], 汪军盛;叶猛;朱廷钰;黄学静;陶文亮;赵瑞壮;徐文青
4.脉冲进料流化床电化学反应器电位波动信号分析 [J], 张忠林;郝晓刚;于秋硕;韩念琛;张福国
5.流化床横向波动特性实验研究 [J], 胡南;刘世杰;徐梦;张缦;杨海瑞;赵冰;巩太义;王家林
因版权原因,仅展示原文概要,查看原文内容请购买。
- 1、下载文档前请自行甄别文档内容的完整性,平台不提供额外的编辑、内容补充、找答案等附加服务。
- 2、"仅部分预览"的文档,不可在线预览部分如存在完整性等问题,可反馈申请退款(可完整预览的文档不适用该条件!)。
- 3、如文档侵犯您的权益,请联系客服反馈,我们会尽快为您处理(人工客服工作时间:9:00-18:30)。
实验一流化床反应器的特性测定一、实验目的流化床反应器的重要特征是细颗粒催化剂在上升气流作用下作悬浮运动,固体颗粒剧烈地上下翻动。
这种运动形式使床层内流体与颗粒充分搅动混和,避免了固定床反应器中的“热点”现象,床层温度分布均匀。
然而,床层流化状态与气泡现象对反应影响很大,尽管有气泡模型与两相模型的建立,但设计中仍以经验方法为主。
本实验旨在观察和分析流化床的操作状态,目的如下:1、观察流化床反应器中的流态化过程。
2、掌握流化床压降的测定并绘制压降与气速的关系图。
3、计算临界流化速度及最大流化速度,并与实验结果作比较。
二、实验原理与固定床反应器相比,流化床反应器的优点是:①可以实现固体物料的连续输入和输出;②流体和颗粒的运动使床层具有良好的传热性能,床层内部温度均匀,而且易于控制,特别适用于强放热反应;③便于进行催化剂的连续再生和循环操作,适于催化剂失活速率高的过程的进行,石油馏分催化流化床裂化的迅速发展就是这一方面的典型例子。
流化床存在的局限性:①由于固体颗粒和气泡在连续流动过程中的剧烈循环和搅动,无论气相或固相都存在着相当广的停留时间分布,导致不适当的产品分布,阵低了目的产物的收率;②反应物以气泡形式通过床层,减少了气-固相之间的接触机会,降低了反应转化率;③由于固体催化剂在流动过程中的剧烈撞击和摩擦,使催化剂加速粉化,加上床层顶部气泡的爆裂和高速运动、大量细粒催化剂的带出,造成明显的催化剂流失。
(1)流态化现象气体通过颗粒床层的压降与气速的关系如图4-1所示。
当流体流速很小时,固体颗粒在床层中固定不动。
在双对数坐标纸上床层压降与流速成正比,如图AB段所示。
此时为固定床阶段。
当气速略大于B点之后,因为颗粒变为疏松状态排列而使压降略有下降。
图1-1 气体流化床的实际ΔP -u关系图该点以后流体速度继续增加,床层压降保持不变,床层高度逐渐增加,固体颗粒悬浮在流体中,并随气体运动而上下翻滚,此为流化床阶段,称为流态化现象。
开始流化的最小气速称为临界流化速度u mf 。
当流体速率更高时,如超过图中的E点时。
整个床层将被流体所带走,颗粒在流体中形成悬浮状态的稀相,并与流体一起从床层吹出,床层处于气流输送阶段。
E点之后正常的流化状态被破坏,压降迅速降低,与E点相应的流速称为最大流化速度u t 。
(2)临界流化速度临界流化速度可以通过ΔP与u关系进行测定,也可以用公式计算。
常用的经验计算式有:在条件满足的情况下,常通过实验直接测定颗粒的临界流化速度。
(3)最大流化速度最大流化速度u t亦称颗粒带出速度,理论上应等于颗粒的沉降速度。
按不同情况可用下式计算:Minnan Normal University Wu Wen-bing其中:临界流化速度,—;最大流化速度,—;流体粘度,—;颗粒密度,—;流体密度,—颗粒当量直径,—smusmusmkgmkgmkgmdudmftSgpgtpp/ ///Re133⊕⊕=μρρμρ三、实验装置及流程流化床特性测试实验实物图和示意流程见图1-2和1-3。
图1-3 流化床反应器特性测试流程图实验用的固体物料是不同粒度的石英砂,气体用空气。
由空气压缩机来的空气经稳压阀稳压后,由转子流量计调节计量,随后可通入装有石英砂固体颗粒的流化床反应器。
气体经分布板吹入床层,从反应器上部引出后放空。
由于出口与大气相通,床层压力降可通过进口压力表测得。
流化床反应器的主要技术指标:气体流量:0~4L/min(空气);最高操作压力:0~0.16MPa;催化剂填装量:10~30ml;反应段:Φ25×2.5mm,长450mm;扩大段:φ76×3 mm,长180mm;总长630mm;四、实验步骤及方法1、打开空压机,稳压后调节空气流量,测定空管时压力降与流速关系以作比较。
2、关闭气源,小心卸下玻璃流化床反应器,装入己筛分的一定粒度石英砂,检漏。
3、通入气体,在不同气速下观察玻璃流化床反应器中流化现象,测定不同气速下床层高度与压降值。
874TCITCI-控温热电偶;TI-测温热电偶;PI-压力计;K-调节阀;V-三通阀;W-球阀;L-六通阀1、1'-气体钢瓶;2、2'-钢瓶减压阀;3-稳压阀;4-转子流量计;5、5'-干燥器;6-取样器;7-预热炉;8-预热器;9 -反应炉;10-流化床反应器;11 -冷凝器;12-气液分离器;13-湿式流量计; 14-加料罐;15-液体泵;16-缓冲罐;17-玻璃流化床PI51213151 1'2 2'4511TCITIPI10TCITCI9K KVV161417WLMinnan Normal University Wu Wen-bing4、改变石英砂粒度重复实验。
5、实验结束关闭气源。
五、实验数据处理1、记录不同条件下的压降ΔP与气体流量的变化值,在双对数坐标纸上进行标绘;2、确定相应的临界流化速度与最大流化速度;3、按实验条件计算临界流化速度与最大流化速度;注意:最大流化速度u t不能直接算出,需假定Re p范围后试算,再校核Re p是否适用。
六、结果与讨论1、分析讨论流态化过程所观察的现象,与理论分析作比较;2、分析影响临界流化速度与最大流化速度的因素有哪些,归纳实验得到的结论;3、比较理论计算值与实验值,并作误差分析;七、思考题(任选两题)1、气体通过颗粒床层有哪几种操作状态?如何划分?2、流化床中有哪些不正常流化现象?各与什么因素有关?3、流化床反应器对固体颗粒有什么要求?为什么?实验二甲醇脱水制备清洁能源——二甲醚一、实验目的1、掌握内循环无梯度反应器、气相色谱仪的工作原理、工艺结构与操作过程;2、了解甲醇气相脱水法制二甲醚的基本原理和基本工艺。
3、了解反应产物定性、定量的分析的方法,学会实验数据处理的方法。
二、实验原理二甲醚(DME),又称木醚,甲醚,分子量46.069,是一种无毒、无味、环境友好的化合物。
DME的性质和液化石油气(LPG)十分相近,在贮存、运输、使用上比LPG安全,燃烧性能好,无残液,不析炭,是一种洁净的民用燃料;二甲醚还可用作汽车燃Minnan Normal University Wu Wen-bing料,其辛烷值比柴油高,尾气不需要催化转化处理,能满足汽车超低排放尾气标准的要求。
因此近几年提出把DME作为环境友好的燃料,得到了极大的关注。
二甲醚的生产方法包括两步法和一步法,其中甲醇脱水制二甲醚属两步法,该法是从传统的浓硫酸甲醇脱水法的基础上发展起来的。
其基本原理是在催化反应器中将甲醇蒸汽通过固体酸性催化剂(氧化铝、分子筛、结晶硅酸铝等),发生非均相反应,脱水生成二甲醚,脱水后混合物还需进行分离提纯。
工艺流程如图1-1:图1-1 气相甲醇脱水法工艺流程美国Mobil公司1965年用气相脱水法生产二甲醚,就获得了80%的转化率和98%的选择性。
日本三井东亚化学公司获得了74.2%的转化率和99%的选择性[28]。
该法以精甲醇为原料,脱水反应副产物少,三废少,操作容易,易获得高纯度的二甲醚产品(可达99.9%)。
甲醇脱水制二甲醚反应机理主要取决于其活性中心位,基于此,国内外许多研究学者提出了不同的观点,主要有双活性中心、弱酸中心和强酸中心三种。
三、实验材料与装置1、主要原料与试剂甲醇(≥99.5%);催化剂(NKC-2,硅铝比15);色谱用高纯氢(≥99.999%)催化剂置于1M的H3PO4溶液中,在50℃下浸渍120min,在80℃下浸渍180min,在120℃下干燥10h,然后在马弗炉中于550℃焙烧24h。
2、实验装置与流程本实验采用常压内循环无梯度反应器,实物图和示意流程见图1-2和1-3。
甲醇换热反应分离提纯二甲醚Minnan Normal University Wu Wen-bing图1-2 内循环无梯度反应器实物图916TITCI7810TCI-控温;TI-测温;PI-压力计;V-截止阀;K-调节阀;J-三通阀;1-氮气;2-稳压阀;3-干燥器;4-过滤器;5-质量流量计;6-缓冲器;7-预热器;8-预热炉;9-反应器;10-反应炉;11-马达;12-六通阀;13-冷阱;14-保温瓶;15-湿式流量计;16-加料泵111VTCI245K3151314色谱系统12VV图1-3甲醇内循环无梯度脱水反应流程图3、色谱分析方法SP-1000气相色谱仪(北京北分瑞利分析仪器公司),GDX-401色谱填充柱(φ3mm×3m,最高使用温度250℃),以氢气为载气。
色谱条件:柱温100℃,进样器120℃,热导池检测器,检测器温度120℃,热丝温度140℃,载气流速20mL/min。
Minnan Normal University Wu Wen-bing四、实验步骤及方法(1)称取约4g催化剂(称准至1 mg),装入反应器中,系统试漏。
打开搅拌系统冷却水(实验过程中,务必保证冷却水通畅,若停水,应立即停止搅拌,停止实验),启动反应装置总电源,开各温度电源和搅拌系统电源。
开启反应装置软件。
(2)设定反应装置温度,包括:设定反应控温为235~310℃(对应的反应测温约为160~220 ℃,具体可参考测温与控温关系表)(这里的反应测温即为催化剂中心的反应温度,由控温来调节。
由于控温为加热温度,传给反应物料的过程中存在热损失,导致测温值偏离控温值较大。
实验过程中,通过测温与控温的关系表给定控温初设值,观察反应温升情况,给予调整。
目的是保证反应测温值在预定的反应温度上,偏差尽量控制在±2℃)。
设定预热温度为120℃,保温系统温度为140℃,阀箱温度为120℃。
搅拌速度设定为1500r/min。
温度设定建议在反应装置软件上完成。
测温与控温的关系表(仅供参考,实验中会有偏差)控温℃ 235 245 285 288 300测温℃ 160 170 200 210 215(3)微量泵的运行准备工作:将微量泵进料管浸于原料液中(实验过程中泵进料管的白色吸附头要保证完全浸没于液面以下),旋松中间吸液口,用针筒将原料液吸出排气,旋紧中间吸液口。
打开泵电源,设定值调为0.5mL/min,三通阀旋向“排空”位置,将原料瓶移至排空口,按“Run/Stop”,启动泵抽液,直到排空口出现连续均匀液滴时。
先按“Run/Stop”,停泵,再将三通阀旋向“反应器”位置,此时泵的运行准备工作完毕。
(4)气相色谱操作:通载气、开总电源、温度达设定值、开检测器、色谱基线。
通色谱载气,启动气相色谱仪,设定柱箱、汽化室和检测器温度为100℃、120℃、120℃,色谱温度稳定后,设定热丝温度为140℃。
打开色谱工作站和反应装置软件,色谱基线平稳后方可对产物进行检测。