机制技术(02)零件表面及形成
机械制造专业课程设计指导书

机械制造专业方向课程设计指导书仅供参考一、设计目的“机械制造专业课程设计”是在本专业方向学生已学习了专业技术基础课程之后进行的一次技能综合训练;这次专业课程设计是整个教学计划中的一个重要环节,目的是培养和提高学生综合运用所学专业知识进行机构设计的能力和工艺设计的能力,为后续的毕业设计作一次基本训练;二、设计要求1.能正确应用专业技术基础知识,分析零件的工艺可行性,制定零件的工艺路线;2.能正确应用机械制造技术基础及夹具设计原理中的基本理论,根据被加工零件的加工要求,拟定夹具方案,设计夹具结构;3.能够按照机械制图规范绘制夹具装配图和零件图;4.熟悉和运用有关机制工艺、夹具等手册和资料,培养工程技术人员的基本工作方法;三、设计内容和步骤本设计题目为:”指定零件的加工工艺规程及其工艺装备设计”;(一)每位学生明确自己的工艺设计对象由指导教师指定二研究分析零件1.了解该零件在机械装备中的地位与作用;2.对零件的图纸表达及结构特点分析;3.对零件主要加工面的尺寸、形位精度、表面粗糙度及设计基准等进行分析; 4.对零件的材料、热处理及工艺性进行分析;5.确定毛坯尺寸及其制造方法三确定生产类型及批量所有零件按照批量设计;生产条件假定为本校已有设备;四确定毛坯制造方法毛坯选择应按生产批量大小,非加工面的技术要求,以及零件的复杂程度,技术要求的高低等几方面综合考虑,它对整个工艺过程经济合理影响甚大;分析毛坯时,注意余量的分配,浇冒口、分型面的位置等,毛坯的结构形式,对以后安排工艺和采取必要工艺措施有关;用红笔在所发零件图上画出毛坯外形,如孔等未加工前的部位要全部涂红,最后,要在这张毛坯图上注全毛坯尺寸;五制定零件的机械加工工艺路线1.制定工艺路线;在对零件分析基础上,至少拟出二个工艺方案,然后进行分析比较,选择其中较为合理的一个;2.选择定位基准,进行工序尺寸计算根据粗精基准选择原则,合理选定各工序的定位基准,当工序中所用的定位基准与设计基准不重合时,则需要工序尺寸计算;3.选择机床及工、夹、量、刀具机床设备的选用,应是既要保证加工要求,又要经济合理,在成批生产条件下,一般是采用通用机床和专用工艺装备;4.加工余量及工序间尺寸与公差的确定根据工艺路线的安排,首先确定一个加工表面的工序加工余量,其工序间尺寸公差按经济精度确定;一个表面的总余量,则为该表面各工序间余量的总和;因时间有限,每个学生只计算其中一个主要表面的各工序间余量及公差;其余表面可直接查阅相关手册中的“工序间的加工余量”部分;5.切削用量和时间定额的确定在机床、刀具、加工余量等确定的基础上,可按有关公式进行计算;因时间有限,本次设计内容仅限于指定工序;6.设计工艺文档将上述各项内容填入“机械加工工艺过程卡片”;至于各工序的加工简图定位夹紧示意图,可选择主要工序,画在说明书上,内容包括:1工件外形及加工部位用红线,并注上工序要求的尺寸,尺寸公差,形位公差和表面粗糙度;2按规定符号,表示出工件的定位,夹压部位和约束的自由度;3在加工开始位置,画上刀具及标上切削运动,进给运动等方向以箭头表示;4每一工序图上,应示清与工艺过程卡中相同的“工序号”、“工序名称”、“机床型号”、“夹具名称”;六夹具结构设计每一学生必须按照指导教师的指定工序设计专用夹具;1.确定设计方案要求至少提出二个进行比较后正式确定;2.选择定位元件,计算定位误差;3.计算所需的夹紧力,设计夹紧机构;4.绘制夹具装配图装配图比例:1:1,工件用双点划线,加工面用加粗实线,其它要求见相关教材;七撰写设计说明书希望每个学生在设计的过程中,及时整理和书写自己的设计说明书;要求:字迹工整、语言简练、文字通顺、插图正确;说明书统一用十六开纸书写,四周留出边框,最后用学校统一印发的封面将报告正文和图纸一起装订成册;设计说明书主要包括以下内容:1.零件分析;2.生产类型及批量的确定;3.毛坯的确定;4.工艺方案分析和有关计算工序尺寸等计算;5.夹具方案分析和有关计算定位误差,夹紧力计算等;6.小结 7. 参考文献等;八课程设计资料的提交设计说明书装订的大致顺序如下:1.封面课程设计专用,黄颜色封面,学校教材科领取2.目录3.设计说明书的正文见七4.小结5. 附录:1指导教师指定零件的零件图2毛坯图3指定零件的机械加工工艺过程卡4机械加工工序卡4夹具总装配图5“夹具体”或“底座”零件图四、成绩考核本课程设计应在规定的时间内结束,由学生本人亲自交指导老师验收,否则不与接收;指导老师最后抽查部分同学质疑,形式可以是个别进行或以小组形式集体进行;课程设计的成绩评定,应根据平时的设计态度和独立工作能力,工艺分析和夹具设计的水平及图画和说明书的质量,进行综合衡量;五、参考资料1.柯建宏等主编;机械制造技术基础课程设计;武汉:华中科技大学出版社,20082.于骏一主编;机械制造技术基础;北京:机械工业出版社,20093.邹青主编;机械制造技术基础课程设计指导教程;北京:机械工业出版社,20044.尹成湖, 李保章, 杜金萍主编;;北京:高等教育出版社,20095.王小华;机床夹具图册;北京:机械工业出版社,19926.李名望主编;;北京:化学工业出版社,20097.胡凤兰主编;互换性与测量技术基础;北京:高等教育出版社,20088.陈宏钧主编;;北京:机械工业出版社,20039.王绍俊主编;机械制造工艺设计手册;哈尔滨:哈尔滨工业大学出版社;10.冯辛安,黄玉美等编着;机械制造装备设计;北京:机械工业出版社;1998;11.刘文剑等编;;哈尔滨:黑龙江科学技术出版社,198712.东北重型机械学院等编;机床夹具设计手册第二版;上海:上海科技出版社;13.张进生;机械制造工艺与夹具设计指导;北京:机械工业出版社,199714.赵家齐;机械制造工艺学课程设计指导书;北京:机械工业出版社,199715.李旦等编着;机床专用夹具图册;黑龙江:哈尔滨工业大学出版社16.刘文剑等编;夹具工程师手册;黑龙江:黑龙江科学技术出版社;六、设计安排本课程设计共两周合计十天,具体分配参照如下:1.布置任务、分析工艺、画毛坯图由指导教师指定 2天2.制定工艺路线、计算工序尺寸1天3.夹具方案装配草图设计通过指导教师审核并确认1天4.定位误差、夹紧力计算 1天5.夹具结构的详细设计总装图,夹具体或底座的工程图通过指导教师审核并确认 3天6.整理设计说明书 1天7.提交文档并考核 1天。
《CA6140普通车床结构剖析[精选]》
![《CA6140普通车床结构剖析[精选]》](https://img.taocdn.com/s3/m/7b467225ba0d4a7303763a7e.png)
《CA6140普通车床结构剖析[精选]》第一篇:ca6140普通车床结构剖析[精选]实验课教案实验名称:cA6140普通车床结构剖析实验学时:2实验班级:机制09-1机制09-1(专)实验时间:11-12-1学期第周节一、实验目的及要求:1、了解机床的用途,总体布局以及机床的主要技术性能;2、对照机床传动系统图,分析机床的传动路线;3、了解和分析机床主要零件的构造和工作原理。
二、设备及器材:cA6140普通车床三、环节安排及组织实施:讲解、示范、指导、总结布置作业。
四、预作报告:五、课后札记:六、讲稿及指导计划实验二cA6140普通车床结构剖析一、实验目的和要求1、了解机床的用途,总体布局以及机床的主要技术性能;2、对照机床传动系统图,分析机床的传动路线;3、了解和分析机床主要零件的构造和工作原理.二、车床简介1、车床的用途车床类机床。
能加工各种零件的回转表面。
内外圆柱面、圆锥面、成形回转表面和旋转体的端面,有的车床还能加工螺纹面及孔加工。
车床上使用工具。
主要是车刀、有些车床可用孔加工刀具,如钻头、扩孔钻及铰刀等,和螺纹刀具如丝锥、板牙等。
对车螺纹。
主轴的旋转和刀架的移动是两个分运动。
(主运动)对车圆柱面。
主轴的旋转和刀架移动是两个独立运动。
(主运动和进给运动)。
车床除了能实现表面成形运动外,还有一些不可缺少的辅助运动,如切入运动、退刀运动、有的车床还有刀架的横纵向的机动快移,重型车床还有尾架的机动快移。
2、车床的分类,在车床类机床中,按其用途和结构不同可分为:①卧式车床和落地车床②立式车床③转塔车床④单轴和多轴、自动和半自动车床⑤仿形车床和多刀车床⑥数控车床和车削中心3、卧式车床,能加工轴类、套类的用途和布局①用途、盘类和环类零件上的回转表面(内外圆柱面、圆锥面、环槽及成形回转面)能加工端面、螺纹面;能加工孔(钻孔、扩孔、铰孔)和滚花.见下图②机床的布局。
机床的总体布局是指机床所有主要部件的位置的配置及相互关系。
数控机床复习题
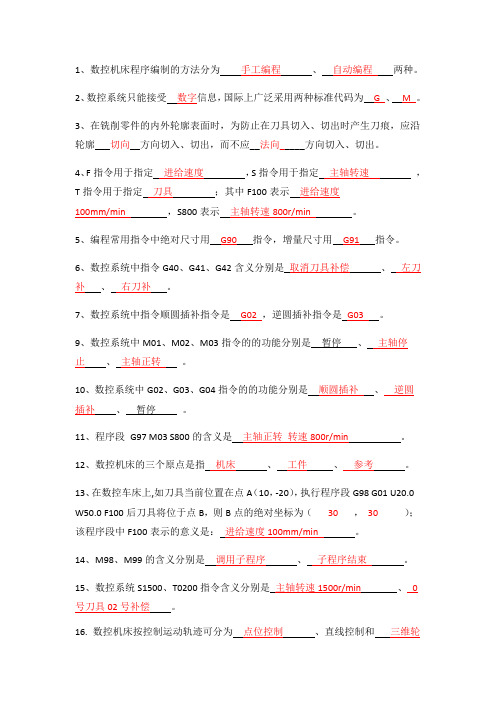
1、数控机床程序编制的方法分为手工编程、自动编程两种。
2、数控系统只能接受数字信息,国际上广泛采用两种标准代码为G 、M 。
3、在铣削零件的内外轮廓表面时,为防止在刀具切入、切出时产生刀痕,应沿轮廓___切向__方向切入、切出,而不应__法向_____方向切入、切出。
4、F指令用于指定进给速度,S指令用于指定主轴转速,T指令用于指定刀具;其中F100表示进给速度100mm/min ,S800表示主轴转速800r/min 。
5、编程常用指令中绝对尺寸用G90指令,增量尺寸用G91指令。
6、数控系统中指令G40、G41、G42含义分别是取消刀具补偿、左刀补、右刀补。
7、数控系统中指令顺圆插补指令是G02 ,逆圆插补指令是G03 。
9、数控系统中M01、M02、M03指令的的功能分别是暂停、主轴停止、主轴正转。
10、数控系统中G02、G03、G04指令的的功能分别是顺圆插补、逆圆插补、暂停。
11、程序段G97 M03 S800的含义是主轴正转转速800r/min。
12、数控机床的三个原点是指机床、工件、参考。
13、在数控车床上,如刀具当前位置在点A(10,-20),执行程序段G98 G01 U20.0 W50.0 F100后刀具将位于点B,则B点的绝对坐标为(30,30);该程序段中F100表示的意义是:进给速度100mm/min 。
14、M98、M99的含义分别是调用子程序、子程序结束。
15、数控系统S1500、T0200指令含义分别是主轴转速1500r/min、0号刀具02号补偿。
16. 数控机床按控制运动轨迹可分为点位控制、直线控制和三维轮廓控制几种。
17. 在轮廓控制中,为了保证一定的精度和编程方便,通常需要有刀具长度和半径补偿功能。
18. 数控机床实现插补运算较为成熟并为大多机床所具有的是直线插补和圆弧插补功能。
19. 与机床主轴重合或平行的刀具运动坐标轴为z 轴,远离工件的刀具运动方向为正方向。
机械制造技术基础重点知识总结

机械制造技术基础重点总结生产过程:从原材料进场一直到把成品制造出来的各有关劳动过程的总和工艺过程:在生产过程中凡属直接改变生产对象的尺寸形状物理化学性能以及相对位置关系的过程工艺规程:一个同样要求的零件,可以采用不同的工艺过程加工,但其中有一种是在给定的条件下最合理的,并把该过程的有关内容用文件的形式固定下来指导生产零件的生产类型分单件,成批,大量工艺过程的组成:工序,一个工人或一组工人在一个工作地对对同一工件或同时对几个工件所连续完成的工艺过程;安装,工件经一次装夹后完成的工艺过程;工位,工件在一次装夹中工件相对机床每占据一个确切位置所完成的工艺过程;工步,在加工表面切削刀具和切削用量都不变的情况下所完成的工艺过程;走刀,每切削一次,称为一次走刀基准:用来确定生产对象几何要素几何关系所依据的那些点线面,分为设计基准(设计图样上标注设计尺寸所依据的基准)和工艺基准(工艺过程中所使用的基准)工艺基准:工序基准,在工序图上用来确定本工序加工表面尺寸形状和位置所依据的基准;定位基准:用来定位;测量基准:工件加工或加工后测量尺寸或行为误差所依据的基准;装配基准:装配时用来确定零件或部件在产品中相对位置的基准工件的装夹过程是定位和夹紧,夹紧的任务是是保持工件的定位位置不变,定位误差和夹紧误差之和为装夹误差工件装夹有找正装夹和夹具装夹两种,找正装夹风直接找正和划线找正六点定位原理:欲使工件在空间处于完全定位,就必须选用与加工件相适应的六个支撑点来限制工件在空间的六个自由度切削运动:主进给合成,切削用量:切削速度,进给量,背吃刀量;切削层参数:公称宽度,厚度,横截面积基面 :通过主切削刃上某一指定点并与该点切削速度方向垂直的面,切削平面:通过主切削刃上某一指定点并与主切削刃相切并垂直该点基面的平面,正交平面:通过主切削刃上某一指定点同时垂直该点基面和切削平面的面前角:前刀面和基面夹角,后角:主后刀面和切削平面夹角,主偏角:基面内测量的主切削刃在基面上的投影与进给运动方向夹角,副偏角 :在基面内测量的副切削刃在基面上的投影与进给运动反方向间的夹角,刃倾角:在切削平面测量的主切削刃与基面间夹角刀具材料性能要求:较高硬度各耐磨性,足够强度和韧性,较高耐热性,良好导热性和耐冲击性,良好工艺性常用刀具:高速钢,硬质合金,工具钢,陶瓷,立方氮化硼,金刚石。
最新机械工艺——车削02教学教案

课堂教学设计【板书设计及时间安排】:一、外圆柱面车削1、外圆车刀2、车刀装夹3、切削用量选择二、平面与阶台车削1、车端面2、车阶台三、沟槽车削与切断1、车槽2、切断四、孔的车削五、圆锥面车削1、斜置上滑板法2、偏移尾座法3、靠模法六、成形面车削1、联合进刀法2、用成形车刀法3、仿形法七、螺纹车削1、车刀的刀尖角2、车刀的装夹3、螺距或导程的调整4、螺纹的车削八、车削实例1、零件工艺分析2、加工步骤【教学内容】:一、外圆柱面车削1、外圆车刀主偏角45°弯头车刀,可以车外圆,车平面和倒角,但切削时背向力较大,车细长件时,容易被顶玩而引起振动,常用于车削刚性好的工件。
主偏角60°—75°刀尖强度较高,散热条件好,主偏角增大,背向力减小,可车刚性稍差的工件,适用于粗、精车外圆。
主偏角90°可以车外圆、端面、阶台。
背向切削力较小,2、车刀的装夹⑴车刀刀杆伸出刀架长度应不超过刀杆高度的1.5倍⑵车刀刀杆中心线应与进给方向垂直⑶车刀刀尖一般应与工件轴线等高,但在粗车外圆时刀尖应略高于工件轴线,精车细长轴外圆时刀尖应略低于工件轴线。
3、切削用量选择粗车主要是切除加工表面的大部分加工余量,在允许范围内应尽量选择大的切削深度和进给量。
而切削速度则相应选低点。
半精加工阶段主要是使零件达到一定的准确度,为重要表面的精加工作好准备,并完成一些次要表面的加工。
精加工主要是达到零件的全部尺寸和技术要求,半精车和精车应尽量选取较小的切削深度和进给量,而切削速度则可以取高点。
切削用量是先确定切削深度,再进给量,最后确定切削速度。
二、平面与阶台车削1、车端面用75°劈刀或45°弯头刀,装刀时刀尖高度必须严格保证与工件轴线等高2、车阶台先用75°偏刀粗车,切除大部分余量,再用90°—95°偏刀精车三、沟槽车削与切断1、车槽车刀刀头宽度等于槽宽,刀头长度稍大于槽深2、切断车刀刀头的长度应稍大于实心工件的半径或空心工件、管料的壁厚,刀头宽度应适当;切实心件时,刀尖应与工件轴线等高,切空心件应稍低于工件轴线。
离子氮化硬度和深度

离子氮化硬度和深度离子渗氮作为强化金属表面的一种利用辉光放电现象,将含氮气体电离后产生的氮离子轰击零件表面加热并进行氮化,获得表面渗氮层的离子化学热处理工艺,广泛适用于铸铁、碳钢、合金钢、不锈钢及钛合金等。
零件经离子渗氮处理后,可显著提高材料表面的硬度,使其具有高的耐磨性、疲劳强度,抗蚀能力及抗烧伤性等。
如果氧化是在氮化结束后停炉过程中产生的,则仅影响外观质量,对渗层硬度、深度无影响。
1.离子氮化工艺技术的内涵及原理离子氮化是为了提高工件表面耐磨性、耐疲劳性、耐蚀性及耐高温等性能,利用等离子辉光放电在离子氮化设备内制备氮化层的一种工艺方法。
离子氮化分三个阶段,第一阶段活性氮原子产生,第二阶段活性氮原子从介质中迁移到工件表面,第三阶段氮原子从工件表面转移到芯部。
其中第一阶段电离和第三阶段扩散机制比较清楚,第二阶段活性氮原子如何从介质中迁移到工件表面的机理尚存争议,普遍认可的是“溅射-沉积”理论。
具体原理为:高能离子轰击工件表面,铁原子脱离基体飞溅出来和空间中的活性氮原子反应形成渗氮铁,渗氮铁分子凝聚后再沉积到工件表面。
渗氮铁在一定的渗氮温度下分解成含氮量更低的氮铁化合物,释放出氮原子,渗氮铁不断形成为一定厚度的渗氮层。
2.离子氮化工艺技术的发展历史(1)1932年德国人B.Berghaus发明。
3.离子氮化工艺技术的优点(1)工件涂层可根据预期性能要求通过调节氮、氢及其他(如碳、氧、硫等)气氛的比例调整实现相组成调节。
(2)制备涂层时间是普通渗氮的三分之一到五分之一,效率高。
(3)制备过程十分清洁而无需防止公害,无需额外加热和检测设备,能够获得均匀的温度分布,能源消耗是气体渗氮的40~70%,节能环保;耗气量极少(仅为气体渗氮的百分之几),可大大减少离子氮化的常见缺陷;适用的材质和温度范围广泛。
(4)工件制备完涂层后可获得无氧化的加工表面,表面光洁度高,变形量小。
4.离子氮化工艺技术的难点(1)空心阴极效应限制了在带小孔、间隙和沟槽零件中的应用(2)边角效应导致导致工件边角部位硬度和其余部位不一致(3)不同结构工件混装时温度的控制和测量存在困难(4)零件表面产生弧光放电(打弧)造成等离子不稳定或高洁净工件表面损伤5.离子氮化工艺技术应用常见问题(1)硬度低。
机械加工过程与工艺规程(02)

机械加工过程与工艺规程(02)第四节毛坯的选择选择毛坯,主要是确定毛坯的种类、制造方法及其制造精度。
毛坯的形状、尺寸越接近成品,切削加工余量就越少,从而可以提高材料的利用率和生产效率,然而这样往往会使毛坯制造困难,需要采用昂贵的毛坯制造设备,从而增加毛坯的制造成本。
所以选择毛坯时应从机械加工和毛坯制造两方面出发,综合考虑以求最佳效果。
一、毛坯的种类毛坯的种类很多,同一种毛坯又有多种制造方法。
1.铸件铸件适用于形状复杂的零件毛坯。
根据铸造方法的不同,铸件又分为:⑴砂型铸造的铸件这是应用最为广泛的一种铸件。
它又有木模手工造型和金属模机器造型之分。
木模手工造型铸件精度低,加工表面需留较大的加工余量;木模手工造型生产效率低,适用于单件小批生产或大型零件的铸造。
金属模机器造型生产效率高,铸件精度也高,但设备费用高,铸件的重量也受限制,适用于大批量生产的中小型铸件。
⑵金属型铸造铸件将熔融的金属浇注到金属模具中,依靠金属自重充满金属铸型腔而获得的铸件。
这种铸件比砂型铸造铸件精度高、表面质量和力学性能好,生产效率也较高,但需专用的金属型腔模,适用于大批量生产中的尺寸不大的有色金属铸件。
⑶离心铸造铸件将熔融金属注入高速旋转的铸型内,在离心力的作用下,金属液充满型腔而形成的铸件。
这种铸件晶粒细,金属组织致密,零件的力学性能好,外圆精度及表面质量高,但内孔精度差,且需要专门的离心浇注机,适用于批量较大的黑色金属和有色金属的旋转体铸件。
⑷压力铸造铸件将熔融的金属在一定的压力作用下,以较高的速度注入金属型腔内而获得的铸件。
这种铸件精度高,可达IT11~IT13;表面粗糙度值小,可达R a3.2~0.4μm;铸件力学性能好。
可铸造各种结构较复杂的零件,铸件上各种孔眼、螺纹、文字及花纹图案均可铸出。
但需要一套昂贵的设备和型腔模。
适用于批量较大的形状复杂、尺寸较小的有色金属铸件。
⑸精密铸造铸件将石蜡通过型腔模压制成与工件一样的腊制件,再在腊制工件周围粘上特殊型砂,凝固后将其烘干焙烧,腊被蒸化而放出,留下工件形状的模壳,用来浇铸。
十种常用的材料表面处理工艺
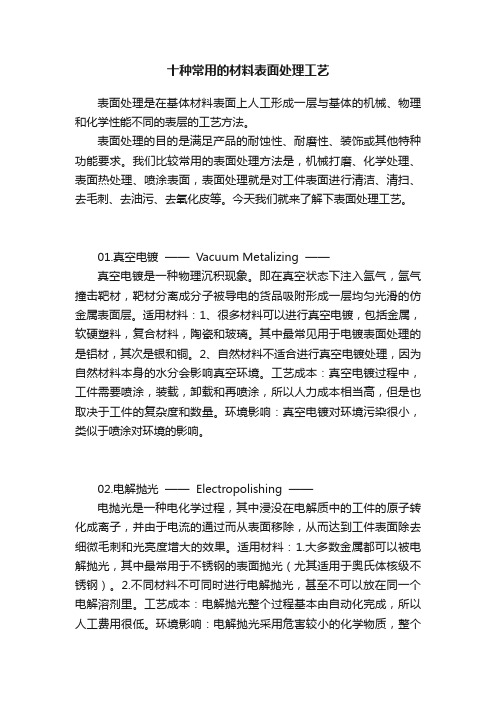
十种常用的材料表面处理工艺表面处理是在基体材料表面上人工形成一层与基体的机械、物理和化学性能不同的表层的工艺方法。
表面处理的目的是满足产品的耐蚀性、耐磨性、装饰或其他特种功能要求。
我们比较常用的表面处理方法是,机械打磨、化学处理、表面热处理、喷涂表面,表面处理就是对工件表面进行清洁、清扫、去毛刺、去油污、去氧化皮等。
今天我们就来了解下表面处理工艺。
01.真空电镀—— Vacuum Metalizing ——真空电镀是一种物理沉积现象。
即在真空状态下注入氩气,氩气撞击靶材,靶材分离成分子被导电的货品吸附形成一层均匀光滑的仿金属表面层。
适用材料:1、很多材料可以进行真空电镀,包括金属,软硬塑料,复合材料,陶瓷和玻璃。
其中最常见用于电镀表面处理的是铝材,其次是银和铜。
2、自然材料不适合进行真空电镀处理,因为自然材料本身的水分会影响真空环境。
工艺成本:真空电镀过程中,工件需要喷涂,装载,卸载和再喷涂,所以人力成本相当高,但是也取决于工件的复杂度和数量。
环境影响:真空电镀对环境污染很小,类似于喷涂对环境的影响。
02.电解抛光—— Electropolishing ——电抛光是一种电化学过程,其中浸没在电解质中的工件的原子转化成离子,并由于电流的通过而从表面移除,从而达到工件表面除去细微毛刺和光亮度增大的效果。
适用材料:1.大多数金属都可以被电解抛光,其中最常用于不锈钢的表面抛光(尤其适用于奥氏体核级不锈钢)。
2.不同材料不可同时进行电解抛光,甚至不可以放在同一个电解溶剂里。
工艺成本:电解抛光整个过程基本由自动化完成,所以人工费用很低。
环境影响:电解抛光采用危害较小的化学物质,整个过程需要少量的水且操作简单,另外可以延长不锈钢的属性,起到让不锈钢延缓腐蚀的作用。
03.移印工艺—— Pad Printing ——能够在不规则异形对象表面上印刷文字、图形和图象,现在正成为一种重要的特种印刷。
适用材料:几乎所有的材料都可以使用移印工艺,除了比硅胶垫还软的材质,例如PTFE等。
(仅供参考)机械零件工程制图规范

5)、零件的最大变形应控制在 孔壁严禁拉伤;
7)、未注圆角 R0.2 以下;
8)、未注表面粗糙度 12.5μmRmax;
9)、孔的测量方法:
A、测量孔的公差下限值时,自重小于 3gf 的塞规应能从孔内自由下落,
B、测量孔的公差上限值时,自重大于 10gf 的塞规应不能从孔内自由下落,
图5
华阳多媒体电子有限公司
机械零件工程制图规范
编 号:WI.RD.016 第 5 页,共 10 页 第 A 版第0次 受控号:
5.6.4 尺寸与公差精度 尺寸与公差精度根据需要确定。
5.6.5 尺寸布局 尺寸之间间隔均匀、适当,尺寸文字一般置于尺寸线的中央。
5.6.6 尺寸编号 尺寸按从左到右,从上到下的顺序依次编号,按①、②、③……顺序递增,针对某个视图可按照
头宽 W:箭头长 L=1:2:4,具体设置见图 2。
图2 5.6 尺寸、公差 5.6.1 尺寸标注标准及尺寸延伸线设置
尺寸标注标准规定为 ISO。打开 Solidworks 工具下的选项命令,在文件属性标签下的出详图分支 中,设定尺寸标注标准为 ISO,设置尺寸延伸线与零件轮廓线间隙及超出尺寸线为 0.6mm,见图 3。
华阳多媒体电子有限公司
机械零件工程制图规范
编 号:WI.RD.016 第 10 页,共 10 页 第 A 版第0次 受控号:
5.10.5.2 齿轮件技术要求。
1)、浇口、模号、顶针位置须与设计者商定;
2)、顶针及浇口痕迹低于零件表面 0.2 以内;
3)、未注平行度、直角度应控制在公差范围内;
4)、未注拔模斜度应控制在公差范围内;
5.10.4.2 弹簧件技术要求。
1)、毛刺高度控制在 0.05 以下;
机械制造技术ppt课件(完整版)

机械制造技术课件
汇报人:
目录
01 02 03 04 05 06
机械制造概述 传统机械制造技术 现代机械制造技术 机械制造工艺流程 机械制造质量控制 机械制造的未来发展
01
机械制造概述
机械制造的定义
机械制造是将原材料转化为成品的生产过程。 机械制造包括产品设计、工艺设计、加工制造、检测和质量控制等环节。 机械制造广泛应用于各个领域,如航空、汽车、机床等。 机械制造的核心目标是提高生产效率、降低成本、保证产品质量。
05
机械制造质量控制
质量控制的方法
统计过程控制 测量系统分析 过程能力分析 质量改进方法
质量检测的步骤
检测计划制定 检测工具准备 样品选择与制备 检测数据记录与分析
质量问题的解决
确定问题:明确机械制造过程中出现的质量问题
分析原因:分析问题产生的原因,如材料、工艺、设备等
制定措施:根据分析,制定相应的解决措施,如改进工艺、更换材料、 调整设备等 实施方案:按照制定的措施实施方案,并对实施过程进行监控和调 整
精密加工技术
定义:使用精密机床和精细加工刀具进行加工 分类:超精加工、镜面加工、纳米加工等 应用:航空航天、医疗器械、光学仪器等领域 发展趋势:高精度、高效率、智能化
04
机械制造工艺流程
零件的定位与装夹
定位原理:六点 定位原理,限制 工件的自由度
装夹方法:如三 爪卡盘、四爪卡 盘等,固定工件
定位元件:如V 形块、定位销等, 限制工件的自由 度
焊接工艺及 设备
焊接种类及 特点
焊接应用及 发展
切削加工技术
定义:利用切削 工具从工件上切 除多余材料的加 工方法
分类:车削、铣 削、钻孔、刨削、 磨削等
机械零件表面精整与光饰
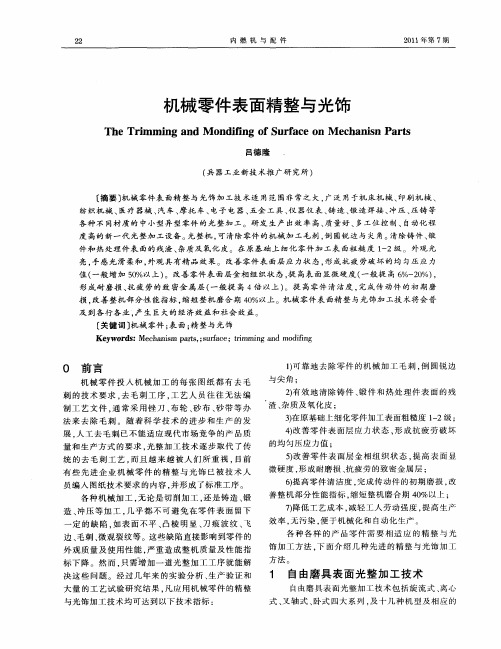
机 械 零 件 投 入 机 械 加 工 的每 张 图纸 都 有 去 毛 刺 的技 术要 求 . 毛 刺 工 序 , 艺 人 员往 往无 法 编 去 工 制 工 艺 文件 . 常采 用 锉 刀 、 通 布轮 、 布 、 带 等 办 砂 砂
法 来 去 除 毛 刺 。随 着 科 学 技 术 的进 步 和 生 产 的发
离 状 态 的磨 块 始 终 以一 定 的压 力 对 零 件 表 面 进 行 碰 撞 、 压 及 微量 磨 削 , 而 细化 表 面粗 糙 度 , 除 滚 从 去 加 工 毛刺 和 表 面 微 观 缺 陷 .改 善 表 面 物 理 机 械 性 能 .达 到 提 高 零 件 表 面 质 量 和 改 善 使 用 性 能 的 目 的 。当设 备 选定 后 , 还必 须确 定合 适 的磨块 种类 、 装 入 量 、 合 比 、 工 时 间 等 参 数 才 能 获 得 理 想 的光 混 加
2有 效 地 清 除铸 件 、 件 和 热处 理 件 表 面 的 残 1 锻
渣 、 质及 氧化 皮 ; 杂 3在原 基础上 细化零件 加工表 面粗糙度 1 2 ; ) — 级
展 . 工 去 毛刺 已不能 适 应现 代 市 场竞 争 的产 品质 人 量 和 生产 方 式 的要 求 , 整加 工 技 术逐 步取 代 了传 光 统 的去 毛 刺 工 艺 , 而且 越 来 越 被 人 们 所 重 视 , 目前 有 些 先 进 企 业 机 械 零 件 的精 整 与 光 饰 已被 技 术 人 员 编人 图纸技术 要 求 的内容 , 并形 成 了标准 工序 。
铁 和铁 中 的杂质 浸 泡在 有 H 、 H1F[ O] [ 一[HC 3等 O t ] 一
多 种 离 子 的 溶 液 中一 样 , 形成 了腐 蚀 电 池 , 是 阳 铁
零件图上的技术要求

表面粗糙度:在零件加工表面存在的一种由较小间距和微小峰谷 形成的微观几何形状误差。
1)宏观几何形状 几何形 状误差 2)表面波度 λ>10mm 1mm< λ<10mm
(在工件表面所形成的间距比粗糙度大得多的 表面不平度)
3)表面粗糙度
λ<1mm
一、表面结构
2.表面粗糙度对互换性的影响 表面粗糙度直接影响产品的质量,对零件表面许多功能都有 影响。其主要表现 : 1. 配合性质 2. 耐磨性 3. 耐腐蚀性
1.公差与配合的标注
2) 配合代号在装配图上的标注形式 如图所示。标注时可根据实际情况,选择其中之一的形式 标注,其中下图(b)所示的形式的标注应用最广泛。
例题(查表)
求 和 的极限偏差,并判断其配合性质? 解: 1)查标准公差表得: 2)由题意得 是基孔制, 基轴制。
3)查基本偏差表1和表2得 ES=+0.03
1、形位公差项目及符号
为控制机器零件的形位误差,提高机器的精度和延长
使用寿命,保证互换性生产,标准相应规定了14项形位公
差项目
2.形位公差带的标注
形位公差的标注
公差框格
形位公差的框格有两格或多格组成。 第一格填写公差项目的符号; 第二格填写公差值及有关符号;
指引线 形位公差 符号 公差带的形状 基准字母 形位公差数值
一、表面结构
国家标准GB/T131-1993对表面粗糙度的符号、代号及
其标注做了规定。
1.表面粗糙度符号
一、表面结构
2.表面粗糙度代号及其标注
当需要表示的加工表面对表面特征的其他规定有要求时,应在
表面粗糙度符号的相应位置,注上若干必要项目的表面特征规定。
机械基础机械零件的精度

表面粗糙度还会影响零件的耐 腐蚀性。表面粗糙度越小,耐 腐蚀性越好。
05
典型机械零件的精度要求
轴类零件的精度要求
直径公差
轴的直径尺寸精度要求,包括轴径和配合轴 径的精度。
圆度公差
轴的形状精度要求,限制轴截面内圆的实际 轮廓与理想轮廓的差异。
圆柱度公差
限制实际轴线与理想轴线的差异,使其在全 长上呈无波动的直线。
机械基础-机械零件的精度
汇报人: 日期:
目 录
• 机械零件精度概述 • 零件尺寸精度 • 零件形状与位置精度 • 零件表面粗糙度 • 典型机械零件的精度要求 • 机械零件精度的检测与质量控制
01
机械零件精度概述
零件精度的概念
零件精度是指零件在加工过程中所达 到的几何参数和性能指标符合技术要 求的程度。
形位公差的确定方法
根据加工经济精度确定
根据经济精度确定形位公差,以保证零件的 制造和使用经济性。
根据使用要求确定
根据零件的使用性能要求,确定形状和位置 公差。
根据经验确定
根据相似零件的实际制造和使用情况,确定 形位公差。
04
零件表面粗糙度
表面粗糙度的概念
01
表面粗糙度是指零件表面由于 加工或自然因素所形成的微观 不平度。
VS
零件精度包括形状精度、尺寸精度、 位置精度和表面粗糙度等多个方面。
零件精度的分类
根据精度要求的不同,可以将零件精度分为高、中、低三个等级。
高精度要求零件的各项参数和性能指标符合很高的技术要求,如精密机床的主轴轴承、高精度齿轮等;中精度要求零件的各 项参数和性能指标符合比较高的技术要求,如一般机床的主轴轴承、中精度齿轮等;低精度要求零件的各项参数和性能指标 符合基本的技术要求,如普通机床的导轨、轴承座等。
机械制造技术基础(第2版)第四章课后习题答案

《机械制造技术基础》部分习题参考解答第四章机械加工质量及其控制4-1什么是主轴回转精度?为什么外圆磨床头夹中的顶尖不随工件一起回转,而车床主轴箱中的顶尖则是随工件一起回转的?解:主轴回转精度——主轴实际回转轴线与理想回转轴线的差值表示主轴回转精度,它分为主轴径向圆跳动、轴向圆跳动和角度摆动。
车床主轴顶尖随工件回转是因为车床加工精度比磨床要求低,随工件回转可减小摩擦力;外圆磨床头夹中的顶尖不随工件一起回转是因为磨床加工精度要求高,顶尖不转可消除主轴回转产生的误差。
4-2 在镗床上镗孔时(刀具作旋转主运动,工件作进给运动),试分析加工表面产生椭圆形误差的原因。
答:在镗床上镗孔时,由于切削力F的作用方向随主轴的回转而回转,在F作用下,主轴总是以支承轴颈某一部位与轴承内表面接触,轴承内表面圆度误差将反映为主轴径向圆跳动,轴承内表面若为椭圆则镗削的工件表面就会产生椭圆误差。
4-3为什么卧式车床床身导轨在水平面内的直线度要求高于垂直面内的直线度要求?答:导轨在水平面方向是误差敏感方向,导轨垂直面是误差不敏感方向,故水平面内的直线度要求高于垂直面内的直线度要求。
4-4某车床导轨在水平面内的直线度误差为0.015/1000mm,在垂直面内的直线度误差为0.025/1000mm,欲在此车床上车削直径为φ60mm、长度为150mm的工件,试计算被加工工件由导轨几何误差引起的圆柱度误差。
解:根据p152关于机床导轨误差的分析,可知在机床导轨水平面是误差敏感方向,导轨垂直面是误差不敏感方向。
水平面内:0.0151500.002251000R y∆=∆=⨯=mm;垂直面内:227()0.025150/60 2.341021000zRR-∆⎛⎫∆==⨯=⨯⎪⎝⎭mm,非常小可忽略不计。
所以,该工件由导轨几何误差引起的圆柱度误差0.00225R∆=mm。
4-5 在车床上精车一批直径为φ60mm 、长为1200mm 的长轴外圆。
机电设备装调技能(第2版)项目一
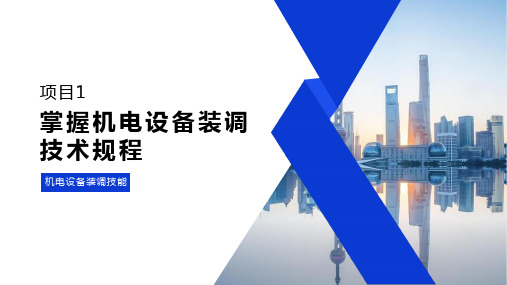
掌握机电设备装调 技术规程
机电设备装调技能
01 02 03
熟悉电设备装 调技术一般规程
掌握机电设备装 调的一般步骤
掌握机电设备装调 工作的安全常识
熟悉机电设备装调 技术一般规程
项目1 掌握机电设备装调技术规程
01
1.1 装配工艺规程的作用 装配工艺规程 1.是生产实践和科学实验的总结 2.是提高劳动生产效率和产品质量的必要措施 3.是组织生产的重要依据 4.能保证装配工作的顺利进行,降低生产成本, 增加经济效益 5.随生产力的发展而不断改进
2 掌握机电设备装调的一般步骤
1.清洗
:
(1) 校正:产品中相关零件间相互位置的找正、 找平及相应调整工作 (2) 调整:是指相关零、 部件相互位置的具体调节工作 (3) 配作: 通常指的是配钻、 配铰、 配刮及配磨等,装配中附加的一 些钳工和机械加工工作
:
(1)验收试验:机械产品装配完后,应根据有关 技术标准和规定,对产品进行较全面的检验和试 验工 作,合格后方准出厂。 (2) 举例:普通车床在总装后,需要进行静态检 查、 空运转试验、 负荷试验等
1)成批生产:在一定的时间内,成批地制造出相同的产品 2)成批生产装配工作:通常分为部件装配和总装配
1.4 制定装配工艺规程 1.研究产品的装配图及检验技术条件
(1) 审核产品图样的完整性、 正确性 (2) 分析产品的结构工艺性 (3) 审核产品装配的技术要求和验收标准 (4) 分析和计算产品装配尺寸链
2 掌握机电设备装调工作的安全常识
1.机械拆装实习室 安全制度
:
(1) 实习前按规定穿戴好工作服,依次有序进入实习场地。 (2) 实习前做好充分准备,了解实习的目的、 要求、 方法与步骤及实习 应注意的事项。 (3) 进入实习室必须按规定就位,听从实习指导老师的要求进行实习。 (4) 保持实习室的安静、 整洁,不得吵闹、 喧哗,不得随地吐痰及乱扔 脏物,与实习 无关的物品不得带入实习室。 (5) 实习前首先核对实习用品是否齐全, 若有不符, 应立即向实习指导 老师提出补领 或调换。
机械加工
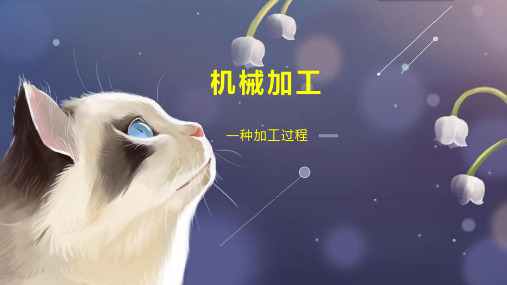
基准介绍
概念
分类
机械零件是由若干个表面组成的,研究零件表面的相对关系,必须确定一个基准,基准是零件上用来确定其 它点、线、面的位置所依据的点、线、面。根据基准的不同功能,基准可分为设计基准和工艺基准两类。
设计基准:在零件图上用以确定其它点、线、面位置的基准,称为设计基准。
工艺基准:零件在加工和装配过程中所使用的基准,称为工艺基准。工艺基准按用途不同又分为装配基准、 测量基准及定位基准。
(1)装配基准:装配时用以确定零件在部件或产品中的位置的基准,称为装配基准。
(2)测量基准:用以检验已加工表面的尺寸及位置的基准,称为测量基准。
(3)定位基准:加工时工件定位所用的基准,称为定位基准。作为定位基准的表面(或线、点),在第一道 工序中只能选择未加工的毛坯表面,这种定位表面称粗基准.在以后的各个工序中就可采用已加工表面作为定位基 准,这种定位表面称精基准。
加工余量
由毛坯变成成品的过程中,在某加工表面上切除的金属层的总厚度称为该表面的加工总余量。每一道工序所 切除的金属层厚度称为工序间加工余量。对于外圆和孔等旋转表面而言,加工余量是从直径上考虑的,故称为对 称余量(即双边余量),即实际所切除的金属层厚度是直径上的加工余量之半。平面的加工余量则是单边余量, 它等于实际所切除的金属层厚度。在工件上留加工余量的目的是为了切除上一道工序所留下来的加工误差和表面 缺陷,如铸件表面冷硬层、气孔、夹砂层,锻件表面的氧化皮、脱碳层、表面裂纹,切削加工后的内应力层和表 面粗糙度等。从而提高工件的精度和表面粗糙度。加工余量的大小对加工质量和生产效率均有较大影响。加工余 量过大,不仅增加了机械加工的劳动量,降低了生产率,而且增加了材料、工具和电力消耗,提高了加工成本。 若加工余量过小,则既不能消除上道工序的各种缺陷和误差,又不能补偿本工序加工时的装夹误差,造成废品。 其选取原则是在保证质量的前提下,使余量尽可能小。一般说来,越是精加工,工序余量越小。
- 1、下载文档前请自行甄别文档内容的完整性,平台不提供额外的编辑、内容补充、找答案等附加服务。
- 2、"仅部分预览"的文档,不可在线预览部分如存在完整性等问题,可反馈申请退款(可完整预览的文档不适用该条件!)。
- 3、如文档侵犯您的权益,请联系客服反馈,我们会尽快为您处理(人工客服工作时间:9:00-18:30)。
κ r
f
asp
工作平面Pfe 界限平面PC
界限平面PB
切削面积AD
hD
零件表面
背吃刀量asp:在通过切削刃选定点并垂直于 工作平面Pfe的方向上测量的吃刀量。
切削要素
asp=(dw-dm)/2
机床型号
二、切削运动与切削要素
2、辅助运动
⑴、切入运动 ⑵、分度运动 ⑶、调位运动 ⑷、其它空行程运动
零件表面
切削要素
机床型号
3
3
1
3
滑鞍转塔车床
滑枕转塔车床
1/10
1/10
卡盘直径
卡盘直径
三、机床型号及编制
常用机床组系代号及主参数 △ △ (△)○(○) △△△(×△)(○)/(○)-(○)
类 组 系 5 5 6 6 1 2 0 1 2 4 1 5 9 机床名称 单柱立式车床 双柱立式车床 落地车床 卧式车床 马鞍车床 卡盘车床 仿形车床 多刀车床 铲齿车床 主参数折算系数 1/100 1/100 1/100 1/10 1/10 1/10 1/10 1/10 1/10 主参数 最大车削直径 最大车削直径 最大工件回转直径 床身上最大回转直径 床身上最大回转直径 床身上最大回转直径 刀架上最大车削直径 刀架上最大车削直径 最大工件直径
零件表面
切削要素 相切法铣削成形面
机床型号
一、零件表面及形成方法
零件表面
右图所示为 插齿加工齿面: 刀具和工件的定 轴转动(展成运动) 形成渐开线母线, 而刀具的向下切 削运动为导线。
切削要素
机床型号
一、零件表面及形成方法
表面成形运动:直接参与切削过程、 在工件上形成一定几何形状表面的刀具和 工件间的相对运动。
一、零件表面及形成方法
下图圆柱面,可以由一条直线沿一圆运 动而获得,也可以由圆沿直线运动而获得。
零件表面
切削要素
左图中,直线称为母线,圆称为导线; 右图中,圆称为母线,直线称为导线。
机床型号
一、零件表面及形成方法
这种母线和导线可以互换的表面称为可 逆表面。对可逆表面而言,可供选择的加工 方法较多,加工更方便。 并不是所有的零件表面都是可逆表面。 如果母线和导线不能互换,则称其为不可逆 表面。不可逆表面的获得方法较少,可供选 择的加工方法也较少。
B1
零件表面
切削要素
A21
A22
机床型号
一、零件表面及形成方法
用成形法形成下图所示手柄的成形面, 只有一个成形运动:工件的定轴转动(导 线)B,而刀具的运动与工件形状无关,不 属于成形运动。
B
零件表面
切削要素
机床型号
一、零件表面及形成方法
A
零件表面
用成形法 形成右图所示 曲面,只有一 个成形运动: 刀具的直线运 动(导线)A。
发生线可以是由刀具切削刃的形状或切削刃 相对工件的运动得到,故发生线可以用不同的方 法来形成。 下图所示的发生线可以由多钟方法来实现:
零件表面
切削要素
机床型号
一、零件表面及形成方法
1、轨迹法:切削刃上切削点按一定的 规律作轨迹运动,从而获得所需发生线曲线, 如图示。
零件表面
切削要素
切削点为获得图示发生线,必须有相应 的运动。该形成所需形状的运动就是成形运 动。
机床型号
一、零件表面及形成方法
2、成形法:切削刃的形状与发生线的 形状相一致,即:切削刃的形状直接形成发 生线。 由于刀具的运动与发生线的形成无关, 故该运动不属于成形运动。
零件表面
切削要素
机床型号
一、零件表面及形成方法
3、向切法:切削刃上切削点作定轴转 动(如圆周铣刀),而刀具回转中心按一定的 规律作轨迹运动,由切削刃(图中圆)包络出 所需发生线曲线,如图示。
磨床 2M 3M 2磨 3磨
齿轮加工机床
螺纹加工机床 铣床 刨插床 拉床
Y
S X B L
牙
丝 铣 刨 拉
零件表面
切削要素
锯床
其它机床
G
Q
割
其
机床型号
三、机床型号及编制
通用特性 高精度 精密
代号 读音 G M 高 密
通用特性代号 自动 Z 自 △ △ (△)○(○) △△△(×△)(○)/(○)-(○) 半自动 B 半
如果一个独立的成形运动,是由单独 的旋转运动或直线运动构成,则称此成形 运动为简单的成形运动,亦即简单运动;
如果一个独立的成形运动,是由两个 或两个以上保持严格速比关系的旋转和/ 或直线运动构成,则称此成形运动为复合 的成形运动,亦即复合运动。
零件表面
切削要素
机床型号
一、零件表面及形成方法
成形表面的形成必然需要运动,这种 运动是由金属切削机床提供的。 在分析成形运动时,通常以A表示直 线运动,以B表示旋转运动,其下标的数 字表示成形运动的序号。如果一个成形运 动是由多个运动构成(即复合运动),则下 标的第一位数字表示成形运动的序号,第 二位数字表示构成该成形运动不同运动的 序号。
零件表面
切削要素
机床型号
二、切削运动与切削要素
以车削外圆为例:
过渡表面 主运动
待加工表面
已加工表面
零件表面
进给运动
刀具前面
切削要素
机床型号
二、切削运动与切削要素
以车削外圆为例:
主运动速度vc
Vc=πdwn/1000
零件表面
进给速度vf 工作平面Pfe
切削要素
机床型号
Vf=n f (= n z fz )
零件表面
切削要素
机床型号
一、零件表面及形成方法
例如,用轨迹法形成下图所示手柄的成形面, 需要两个运动:刀尖的运动A2(母线)和工件的定 轴转动B1(导线)。其中,A2为复合运动,由A21和 A22构成;B1为简单运动。显然,A21和A22间必须 保证严格的速比关系,否则,不能获得图示要求 的母线形状;而B1的快慢仅影响加工效率和粗糙 度,不影响其形状。
切削要素
机床型号
二、切削运动与切削要素
零件表面
切削要素
机床型号
二、切削运动与切削要素
零件表面
切削要素
机床型号
二、切削运动与切削要素
零件表面
切削要素
机床型号
二、切削运动与切削要素
零件表面
切削要素
机床型号
二、切削运动与切削要素
零件表面
切削要素
机床型号
二、切削运动与切削要素
1、成形运动
⑴、主运动:由机床或人力提供的 主要运动,它促使刀具和工件之间产生 相对运动,从而使刀具前面接近工件。 ⑵、进给运动:由机床或人力提供 的运动,它使刀具与工件之间产生附加 的相对运动,加上主运动,即可不断地 或连续地切除切屑,并得出具有所需几 何特性的已加工表面。
零件表面
切削要素
机床型号
成形法车削成形面
一、零件表面及形成方法
用成形法形 成右图所示曲面, 只有一个成形运 动:刀具运动 (导线,箭头方 向所示),而母 线由刀刃形状获 得。
成形法刨削成形面
零件表面
切削要素
机床型号
一、零件表面及形成方法
用相切法形成下图所示的成形面,其 成形运动为:刀具中心的运动轨迹和刀具 的定轴转动。
△为阿拉伯数字;
△ ○为大写汉语拼音字母,或阿拉伯数字, 或两者兼而有之.
切削要素
机床型号
三、机床型号及编制
通用机床的型号规定为:
△ △ (△)○(○) △△△(×△)(○)/(○)-(○)
主参数或设计序号
系代号
组代号 通用特性或结构特性代号
零件表面
类代号
分类代号
切削要素
机床型号
三、机床型号及编制
二、切削运动与切削要素
以车削外圆为例:
过渡表面 主运动 待加工表面 已加工表面
工作平面Pfe
刀具前面 进给运动
零件表面
切削要素
机床型号
二、切削运动与切削要素
以车削外圆为例:
f 工作平面Pfe 界限平面PC 界限平面PB
零件表面
切削面积AD
asp
hD
刀具前面
切削要素
机床型号
二、切削运动与切削要素
切削要素
机床型号
一、零件表面及形成方法
用相切法形成下图所示的成形面,其 成形运动为:刀具中心的运动A2和刀具的 定轴转动B1,工件成形面的深度由刀具的 长度来完成。
零件表面
B1
A22
A21
切削要素
机床型号
一、零件表面及形成方法
B12
零件表面
右图所示为插 B11 齿加工齿面:刀具 和工件的定轴转动 B11和B12(展成运动) 形成渐开线母线, 而刀具的向下切削 运动A2为导线。
机床型号
一、零件表面及形成方法
综上所述,用轨迹法形成下图所示手 柄的成形面,需要两个运动:刀尖的运动 (母线)和工件的定轴转动(导线) 。
零件表面
切削要素
轨迹法车削成形面
机床型号
一、零件表面及形成方法
用成形法形成下图所示手柄的成形面, 只有一个成形运动:工件的定轴转动(导 线),而母线由刀刃形状获得。此时,刀 具的运动与工件形状无关,不属于成形运 动。
机械制造技术
零件表面及形成
零件表面
切削要素
机床型号
一、零件表面及形成方法
机械零件通常由平 面、圆柱面、圆锥面及 其它成形面组成。
右图所示零件为一 凸轮,其表面组成为: 零件表面 内、外圆柱面、两端平 面、健槽平面、凸轮槽 切削要素 成形面等。
机床型号
一、零件表面及形成方法
下图所示零件为一支座,其表面组 成为:内圆柱面、平面及过渡圆弧等。