汽车电动助力制动系统摩擦建模与补偿控制
制动系统的优化设计与仿真分析
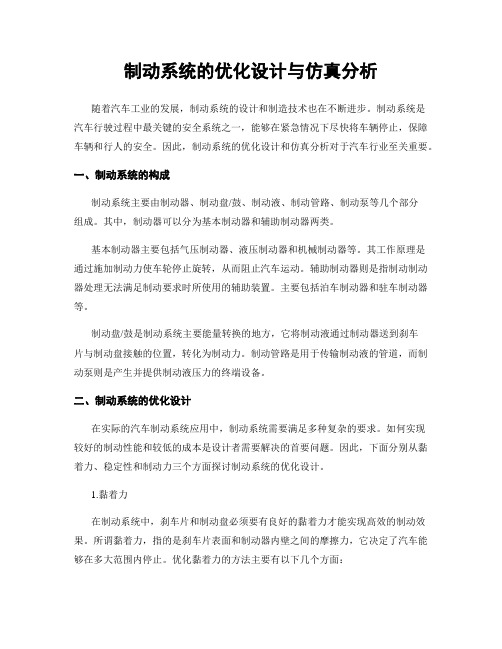
制动系统的优化设计与仿真分析随着汽车工业的发展,制动系统的设计和制造技术也在不断进步。
制动系统是汽车行驶过程中最关键的安全系统之一,能够在紧急情况下尽快将车辆停止,保障车辆和行人的安全。
因此,制动系统的优化设计和仿真分析对于汽车行业至关重要。
一、制动系统的构成制动系统主要由制动器、制动盘/鼓、制动液、制动管路、制动泵等几个部分组成。
其中,制动器可以分为基本制动器和辅助制动器两类。
基本制动器主要包括气压制动器、液压制动器和机械制动器等。
其工作原理是通过施加制动力使车轮停止旋转,从而阻止汽车运动。
辅助制动器则是指制动制动器处理无法满足制动要求时所使用的辅助装置。
主要包括泊车制动器和驻车制动器等。
制动盘/鼓是制动系统主要能量转换的地方,它将制动液通过制动器送到刹车片与制动盘接触的位置,转化为制动力。
制动管路是用于传输制动液的管道,而制动泵则是产生并提供制动液压力的终端设备。
二、制动系统的优化设计在实际的汽车制动系统应用中,制动系统需要满足多种复杂的要求。
如何实现较好的制动性能和较低的成本是设计者需要解决的首要问题。
因此,下面分别从黏着力、稳定性和制动力三个方面探讨制动系统的优化设计。
1.黏着力在制动系统中,刹车片和制动盘必须要有良好的黏着力才能实现高效的制动效果。
所谓黏着力,指的是刹车片表面和制动器内壁之间的摩擦力,它决定了汽车能够在多大范围内停止。
优化黏着力的方法主要有以下几个方面:(1)选择合适的材料。
选择合适的刹车片材料可以改善制动器与制动盘之间的黏着力,从而提高制动性能。
目前主流的刹车片材料有金属、有机和陶瓷等,不同材料的优缺点也不同。
(2)改善制动盘表面。
制动盘表面会因为使用而损耗,会影响刹车片与制动盘之间的黏着力。
对制动盘进行适当的处理或涂层处理可以改善黏着性能。
(3)优化刹车片结构。
刹车片的厚度和面积也会影响制动性能。
适当增加刹车片的面积或者采用具有弹性可调的刹车片结构可以增强黏着性能。
乘用车电动助力转向系统的补偿控制

Co p ns to Co r lS r e y f e t i m e a i n nt o t at g orEl c r c Powe e rng S t m fPa s n r Ve i l r St e i yse o s e ge h c e
图 1 电动 助 力 转 向系 统 模 型
1 电动助力转 向系统数学建模及原理
图1 为轴 助力式 电动助力转 向系统 的模 型 . 该
系统 由机械 转 向 系统 、 向盘转 矩 传感 器 、 转 车速 传 感器 、 电流传 感器 、 制器 、 力 电动 机及减 速机 构 控 助
电动助 力转 向 系统 的补 偿 控 制 策略 进 行仿 真 研 究 。仿 真 结 果表 明 , 真模 型的 动 态 转 向效 果和 回正 能 力得 到 了 仿 改善 . 决 了转 向轻 便 性 和 路感 的 问题 。 解 关 键词 : 电动 助 力 转 向 ; 偿 控 制 ; 态 空 间 ; 补 状 车辆
W a g Re r i n n u ,Ru n Mi i g, h o Yo q n a qn Z a u u
( aj gU i ri f e nui n so at s N ni 10 6 hn ) N ni nv s y r at sadA t n ui , aj g2 0 1 ,C ia n e to A o c r c n
Ke ywor s:ee ti we te ng;c d lcrcpo rse r i omp ns to o to ;sa e pa e;v hil e a in c nr l tt-s c e ce
电动汽车声品质的评价分析及建模

电动汽车声品质的评价分析及建模随着人们对环境保护意识的提高以及新能源技术的不断进步,电动汽车已经成为了人们日常生活中越来越常见的一种出行方式。
然而,与传统燃油车相比,电动汽车的声品质一直是广大消费者关注的焦点。
因此,本文将从声品质的角度对电动汽车进行评价分析,并建立一种声品质评价的数学模型。
电动汽车的声品质主要包括以下几个方面:1. 噪音:电动汽车在行驶过程中产生的运动噪音和驱动系统噪音相对较小,但电动机咆哮、轮胎与路面的摩擦噪音、车内舱噪音等在低速行驶时仍然较为明显,影响驾驶者的驾驶体验。
2. 振动:电动汽车的振动相对于传统燃油车会更小,但同时也会受到驱动系统和制动系统的影响,如轮胎与路面间的摩擦力等。
3. 声音:电动汽车的声音比传统燃油车要小,但具有独特的声音特征,如电动机的高频噪音、电子设备的电磁干扰噪音等。
对于电动汽车的声品质评价,首先需要确定评价指标。
本文选取了以下五个指标来评估电动汽车的声品质:1. 噪音级别:使用噪音仪器测得电动汽车在不同速度下的噪音大小。
2. 振动级别:使用振动仪器测得电动汽车在不同路况下的振动大小。
3. 安静度:使用环境噪音仪器测得车内环境下的噪音大小。
4. 低频音质:使用360度环境声场仪器测得电动汽车在不同速度下低频音的情况。
5. 高频音质:使用频谱分析仪器测得电动汽车在不同速度下高频音的情况。
在确定了评价指标后,我们需要对电动汽车的声品质进行建模,以定量化地评价汽车的声音质量。
1. 噪音级别模型:噪音级别模型使用如下公式计算:Lp = 10 log10 (p2/p1) + K其中,Lp表示声级,p2表示被测物体产生的声压级,p1表示参考级别(一般取10^-12 Pa),K为常数。
通过该公式可以计算出电动汽车在不同速度下的噪音级别。
2. 振动级别模型:振动级别模型使用如下公式计算:V = (1/N) ∑ (v^2)其中,V表示振动级别,N为采样点数,v表示每个采样点的振动大小。
电动汽车的动力学建模与控制

电动汽车的动力学建模与控制随着环境保护意识的增强和新能源技术的不断改进,电动汽车作为一种绿色交通工具,受到了越来越多人的关注和选择。
然而,要想提高电动汽车的性能和效能,建立合理的动力学模型并进行有效的控制是至关重要的。
电动汽车的动力学建模是通过研究其运动学和力学特性,将其转化为数学模型。
这对于车辆性能分析、控制策略制定和系统仿真至关重要。
一种常用的建模方法是使用电动汽车的整体动态方程。
这个方程包括了汽车的质量、阻力、增速器和动力系统的参数。
通过对这些参数进行动态建模以及考虑其他因素如电池特性、驱动系统效率等,我们可以得到一个准确且可信的模型。
为了更好地控制电动汽车的性能,我们需要设计合适的控制算法。
控制算法可以分为开环和闭环两种。
开环控制是基于预定义的参考信号来实现汽车的期望行为。
它不考虑外部干扰和系统误差。
闭环控制则通过测量系统输出以及与期望输出的偏差来调整控制信号,以实现更加精确的控制。
闭环控制通常包括反馈控制和前馈控制。
反馈控制中最常用的方法是PID控制器。
PID控制器通过比较实际输出与期望输出的偏差,根据比例、积分和微分三个项计算出控制信号。
PID控制器的参数需要根据实际情况进行调整,以达到最佳控制效果。
前馈控制则是通过预测汽车的未来行为,提前计算出所需的控制信号,并进行补偿。
前馈控制可以大大减小系统在跟踪参考信号时出现的误差。
除了PID控制器和前馈控制之外,还有一些先进的控制算法如模型预测控制(MPC)、自适应控制和人工智能控制等。
这些算法能够更好地处理非线性系统和模型不确定性,并提供更快速、更精确的控制。
在进行动力学建模和控制之前,我们还需要进行系统辨识。
系统辨识是为了确定电动汽车的物理特性和参数,从而为建模和控制提供准确的数据。
常用的系统辨识方法包括频域分析、时域分析和信号处理等。
在动力学建模和控制方面,还有一些特殊的问题需要考虑。
例如,电动汽车的能量管理问题,即如何合理分配和利用电池的能量以及优化整个系统的能量利用效率。
汽车转向系统摩擦分析与优化

汽车转向系统摩擦分析与优化摘要:汽车转向系统对汽车的行驶安全至关重要,其功能就是按照驾驶员的意愿控制汽车的行驶方向。
转向系统摩擦是转向系统中一个重要的参数,它影响着转向盘力矩对驾驶员的操纵感觉,同时对车辆回正起到一定的影响。
本文分析了汽车转向系统摩擦力对转向力和回正力的影响,与此同时,对某一实车进行了转向系统摩擦优化。
关键词:转向系统;摩擦;转向力;回正力前言随着时代的进步,汽车已成为现代生活必不可少的出行工具。
汽车行业逐步发展的同时,人们对驾驶感觉要求越来越高。
转向系统作为影响驾驶感觉的重要部分,得到了越来越多的重视。
本文主要是对转向系统中影响驾驶感觉的参数-转向系统摩擦进行分析和优化。
1转向系统介绍1.1转向系统的类型转向系统分为机械转向系统和动力转向系统。
其中,完全靠驾驶员手力操纵的转向系统称为机械转向系统;借助动力来操纵的转向系统称为动力转向系统。
动力转向系统可分为液压动力转向系统和电动助力转向系统。
1.2机械转向系统简介机械转向系统是由驾驶员的力量驱动的,所有这些都是机械的。
机械转向系统由转向操纵机构、转向器和转向传动机构组成。
1.2.1转向操纵机构转向操纵机构由方向盘、转向轴、转向管柱等组成。
该功能是将驾驶员的力量由方向盘传向转向器。
1.2.2转向器转向器是将旋转运动转到直线(或近似直线)运动,同时也是转向系统中的减速装置。
目前,常见的有齿轮齿条式、圆球曲柄销式、蜗杆曲柄销式、圆球齿条式、蜗轮式等。
1.2.3转向传动机构转向传动机构的功能是转向器输出的力和运动传到转向桥两边转向节,使两边转向轮偏转,两个转向轮偏转角按一定关系改变,以确保车轮在汽车方向盘和地面的相对滑动尽可能小。
1.3动力转向系统简介当转向轴载荷较小时,汽车转向系统使用机械转向装置可以实现顺利转向,当转向轴载荷较大时,仅仅依靠驾驶员的身体力量作为动力就难以转向。
动力转向系统是在机械转向系统的基础上形成的,即在机械转向系统上增加了助力装置。
基于ANSYS的汽车制动盘模态仿真与优化

w2M jwCK x(w) Fw
(6)
系统阻尼可以取方程(7)所示的比例形式:
C M K
(7)
上式中, 和 为比例常数。由于结构自由度较大,
方程解耦较为困难,利用模态坐标,将耦合方程变为 N 个相
互独立的方程式,可得:
x(w) ΦQ
(8)
式中: = 1,2 N 为各阶模态向量组成的矩阵,
式中:M—质量矩阵;K—刚度矩阵;C—阻尼矩阵;F
—统所受外载荷。
方程(1)为有阻尼的 n 自由度系统的强迫振动微分方
程,阻尼对结构的振型和固有频率影响不大,可以忽略阻尼
的影响,无外力作用时即外载荷 F=0,,故方程(1)可以简
化为:
M x K x 0
(2)
方程的(2)解的一般形式为:
x X e jw t
构进行修改和优化,但其分析精度受建模精度的影响较大,
且具有内部阻尼信息描述不准确等缺点。而试验模态分析具
有分析精度较高,实际被测对象的动态特性描述准确等优点,
但具有试验周期长、资金消耗较大,结构的修改困难等缺点。
鉴于上述两种方法各有优缺点,为提高精度。本文采用
试验模态分析和有限元模态分析相结合的方法,利用试验模 态分析结果修正和检验有限元模型精度[3]。通过修改模态相
称为模态矩阵;Q 为模态坐标值,将方程 (8)代入方程(6)
可得:
w2M jwC K ΦQ F w
(9)
考虑到模态振型的正交性,在式(9)中左右两边同时乘
T ,则可得:
ΦTS CΦr
cs
0,r s ms ks r
s
(10)
式中, cr 称为模态参数于是方程(9)变为:
分析电子驻车制动系统仿真与试验

分析电子驻车制动系统仿真与试验摘要:电子驻车制动系统(ElectronicStarterBar,ESS)是在汽车制动系统中广泛应用的一种制动技术,其应用将大大提高汽车的安全性和舒适性。
由于ESS系统是一种全新的制动技术,因此其研究具有较高的实际意义。
本文主要介绍了基于ESS系统的汽车制动控制策略,利用MATLAB/Simulink软件建立了ESS系统的仿真模型,并对不同的ESS系统控制策略进行了仿真分析。
最后通过试验验证了基于ESS系统的汽车制动控制策略的正确性和可行性。
关键词:电子驻车制动;控制;摩擦;建模;仿真随着汽车技术的快速发展,人们对汽车的安全性和舒适性提出了更高的要求。
传统的机械驻车制动系统(BAS)虽然具有较高的稳定性和可靠性,但其在紧急情况下无法实现电子驻车制动(ESS),只能依靠驾驶员对汽车的操纵实现驻车制动,这样就增加了驾驶员在紧急情况下对汽车制动系统操作的难度,降低了汽车行驶过程中的稳定性。
因此,为了提高汽车行驶过程中的稳定性和安全性,需要在传统BAS系统的基础上增加电子驻车制动系统(ESS)。
电子驻车制动系统(ESS)是在传统BAS系统基础上增加了电子控制单元(ECU)和信号传感器。
ECU是控制单元,负责整个系统的控制和维护。
信号传感器用于检测路面状态、环境温度和速度等,信号将被输入ECU。
ECU对来自传感器信号进行处理并根据路面情况和环境温度等信息来控制制动器施加适当的制动力矩。
制动器通过ECU控制其液压执行机构来实现制动。
1.系统组成及工作原理ESS系统的主要功能包括:1.电子驻车制动控制单元(EWMC)通过采集驾驶员施加制动力矩和路面状况等信息,与预先设定的车辆横摆角速度、车轮减速度等参数相比较,计算出最合适的制动力矩。
2.将计算出的制动力矩进行分配给各个车轮。
3.对制动踏板力进行精确控制,使驾驶员能够最大限度地使用制动力矩,减少紧急制动时的点头现象,从而提高了制动效能和安全性。
基于stribeck摩擦模型的新型制动系统的振动研究

基于stribeck摩擦模型的新型制动系统的振动研究【摘要】本文主要研究基于Striebeck摩擦模型的新型制动系统的振动特性。
在首先介绍了研究背景,即制动系统在汽车工程中的重要性和存在的挑战,然后阐明了研究的目的是为了改善制动系统的振动问题。
在详细介绍了Striebeck摩擦模型的原理和新型制动系统的设计方案,然后分析了制动系统的振动特性,并提出了数值模拟方法和实验验证。
结论部分总结了振动研究的成果,并展望了未来研究方向。
通过本文的研究,有望为制动系统的设计和优化提供重要的理论支持,同时为解决制动系统振动问题提供新的思路和方法。
【关键词】关键词:stribeck摩擦模型、制动系统、振动研究、数值模拟、实验验证、振动特性、研究背景、研究目的、成果总结、未来展望1. 引言1.1 研究背景随着现代汽车工业的快速发展,制动系统作为汽车安全性能的重要组成部分,其稳定性和可靠性需求也日益提高。
传统的制动系统在高速运行时往往会出现振动现象,影响到制动效果和驾驶舒适性。
如何有效地降低制动系统的振动成为当前研究中的一个重要课题。
本文旨在基于stribeck摩擦模型,研究新型制动系统的振动特性,通过数值模拟和实验验证的方法,探讨如何优化制动系统的设计,降低振动产生,提高制动性能和驾驶舒适性。
通过这项研究,期望能为制动系统的改进和优化提供参考,推动汽车安全性能的不断提升。
1.2 研究目的研究目的是为了探究基于Stribeck摩擦模型的新型制动系统在振动特性方面的表现,从而更好地了解其工作原理和性能特点。
通过深入分析新型制动系统的设计和振动特性,可以为制动系统的优化设计和性能改进提供理论支持和实践指导。
通过数值模拟和实验验证,可以验证理论分析的准确性和可靠性,为今后制动系统的研究和开发奠定基础。
通过本次研究,我们希望能够深入了解新型制动系统的振动机理,为其在实际工程应用中的性能提升和优化提供可靠的依据。
通过本次研究成果的总结和展望,可以为未来相关领域的研究工作提供参考和启示,促进制动系统技术的进一步发展和完善。
基于Modelica的电动汽车制动系统建模仿真与参数优化

基于Modelica的电动汽车制动系统建模仿真与参数优化随着社会的发展,电动汽车已经成为一个必然趋势,并且成为了解决环境问题的重要手段。
然而,电动汽车的制动系统与传统汽车的制动系统有很大的不同,需要重新对制动系统进行建模和优化。
基于Modelica语言,我们可以建立一个电动汽车的制动系统模型,并对其进行仿真和优化。
在这个模型中,我们把制动系统分成了三个部分,即制动器、电机和控制器。
制动器部分使用Modelica.Mechanics.Rotational子库中的元件进行建模。
我们把制动器建模成了一个摩擦片和转子的组合体。
当制动器处于制动状态时,摩擦片会和转子发生摩擦,从而减速汽车。
电机部分主要建模电机的动力学特性,使用Modelica.Electrical.Machines库进行建模。
我们采用了一个直流电机,并根据电机参数建立动力学模型,包括转矩-转速曲线等。
在制动时,电机接通再反向运转,产生负功率,从而带动轮胎减速。
控制器部分主要控制制动系统的动作,采用了Modelica.Blocks中的元件进行建模。
控制器部分的主要功能是根据汽车速度和制动踏板的行程,计算制动器的力矩,从而控制汽车制动。
在建立完毕制动系统的模型之后,我们可以使用仿真软件对制动系统进行仿真测试。
通过仿真测试,我们可以观测到制动系统是否能够正常运作,并且可以得到控制参数的优化方案。
我们可以通过调整控制器部分的参数来达到最佳制动效果。
例如,通过改变制动器的力矩大小,我们可以调整制动系统的制动能力。
如果力矩太小,制动效果不佳;如果力矩太大,会导致轮胎打滑。
因此,我们需要进行参数优化,以达到最佳制动效果。
在最终的仿真测试结果中,我们得到了一个能够良好运作的电动汽车制动系统模型,该模型的制动系统具有良好的稳定性和可靠性,并能够通过控制器的参数优化实现最佳制动效果。
基于Modelica的电动汽车制动系统建模仿真与参数优化可以帮助我们更好地了解电动汽车的特性,并且优化它们的制动性能。
基于stribeck摩擦模型的新型制动系统的振动研究

基于stribeck摩擦模型的新型制动系统的振动研究1. 引言1.1 背景介绍制动系统是汽车、列车、飞机等交通工具中至关重要的部件之一,其性能直接关系到车辆的行驶安全和稳定性。
随着科技的不断发展,对制动系统的要求也在不断提高。
而制动系统的振动问题一直是制约其性能的重要因素之一。
为了提高制动系统的稳定性和安全性,研究制动系统的振动特性显得尤为重要。
传统的制动系统振动研究缺乏对摩擦副内部摩擦特性的深入理解,往往只停留在表面现象的探究上。
针对这一问题,本文基于Striebeck 摩擦模型,通过对摩擦副内部摩擦特性的研究,设计了一种新型的制动系统,旨在降低制动系统的振动水平,提高其稳定性和安全性。
本文将首先介绍摩擦副的基本工作原理和Striebeck摩擦模型的理论基础,然后详细阐述基于Striebeck摩擦模型的制动系统设计方法。
接着,将介绍振动分析方法和实验设计,分析实验结果并进行参数优化。
将探讨制动系统振动研究的意义,总结研究结果的启示,并展望未来研究方向。
通过本文的研究,有望为制动系统的振动问题提供新的解决方案,推动制动系统的性能进一步提升。
1.2 研究目的本研究的目的是探索基于Striebeck摩擦模型的新型制动系统的振动特性,从而提高制动系统的性能和稳定性。
具体目标包括:1.研究不同摩擦副对制动系统振动特性的影响,找到最优摩擦副组合;2.验证Striebeck摩擦模型在制动系统设计中的可行性,探讨其对振动的影响;3.建立基于振动分析的制动系统设计方法,提高设计效率和准确性;4.通过实验设计与结果分析,探讨参数优化对振动的影响,为制动系统的性能优化提供理论支持。
通过本研究的实施,旨在为提高制动系统的稳定性和效率提供基础理论支持,为制动系统的设计和优化提供新的思路和方法。
1.3 文献综述在制动系统振动研究领域,已有大量相关文献进行了深入探讨。
在过去的研究中,学者们主要关注于分析制动系统的振动特性对整车性能和驾驶舒适性的影响。
汽车制动系统的设计及仿真

汽车制动系统的设计及仿真任务书1.设计的主要任务及目标汽车制动器是制动系中最重要的一个部件,是制动系统中用以产生阻碍汽车运动或运动趋势的力的部件。
凡是利用固定元件与旋转元件工作表面的摩擦而产生制动力矩的制动器都成为摩擦制动器。
摩擦制动器可分为鼓式和盘式两大类。
前者的摩擦副中的旋转元件为制动鼓,其工作表面为圆柱面;后者的旋转元件则为圆盘状的制动盘,以端面为工作表面。
2.设计的基本要求和内容(1)了解汽车制动系统的工作过程。
(2)熟悉汽车制动系统的设计过程和设计参数。
(3)结合汽车制动性能要求设计汽车制动器。
(4)结合三维建模软件,并实现制动器的运动仿真。
3.主要参考文献[1] 王望予.汽车设计[M].北京:机械工业出版社,2004[2] 余志生.汽车理论[M].北京:机械工业出版社,2003[3] 陈家瑞.汽车构造[M].北京:机械工业出版社,2003[4] 林秉华.最新汽车设计实用手册[M],黑龙江:黑龙江出版社,2005[5] 张尉林.汽车制动系统的分析与设计[M].北京:机械工业出社,20024.进度安排注:一式4份,系部、指导教师各1份、学生2份:[毕业设计]及答辩评分表各一份汽车制动系统的设计及仿真摘要:汽车的制动系是汽车行车安全的保证,许多制动法规对制动系提出了许多详细而具体的要求,这是我们设计的出发点。
从制动器的功用及设计的要求出发,依据给定的设计参数,进行了方案论证。
对各种形式的制动器的优缺点进行了比较后,选择了浮动钳盘的形式。
这样,制动系有较高的制动效能和较高的效能因素稳定性。
随后,对盘式制动器的具体结构的设计过程进行了详尽的阐述。
选择了简单液压驱动机构和双管路系统,选用了间隙自动调节装置。
在设计计算部分,选择了几个结构参数,计算了制动系的主要参数,盘式制动器相关零件的设计计算。
关键词: 制动器,同步附着系数,制动盘,制动钳Automobile brake system design and simulationAbstracts:The braking system in a vehicle guaranteed the safety of driving .Many rules and regulations have been made for the braking system in detail, which is the starting of our design.Firstly, I demonstrate the project on the base of the function of the brake, And analysis their strong point and shortcomings .I choose the form of front-disked. In this way, the braking system have higher braking efficiency and high stability of the performance factors. Subsequently, the specific structure of the disc brake design was elaborated in detail.I designed the hydraulic drive system and two-pipe system and selected clearance automatic adjusting device.In the calculate part .I chosen several structural parameters, calculated the main parameters of the braking system drive mechanism.Key words:disc brakes,synchronous attachment coefficient,brake disc,brake caliper目录1 绪论 (1)1.1 课题研究的目的及意义 (1)1.2制动系统研究现状 (1)1.3课题设计思路 (3)2制动系统概述 (4)2.1制动系的类型 (4)2.2汽车制动系统组成 (4)2.3 制动器的组成 (5)2.4 制动器的要求 (5)2.5 制动器的种类 (7)3 汽车参数计算 (14)3.1汽车的基本参数 (14)3.2 制动系的主要参数及其选择 (15)3.3 盘式制动器的结构参数与摩擦系数的确定 (16)3.4 制动衬块的设计计算 (18)3.5 摩擦衬块磨损特性的计算 (19)4 制动器主要零件的结构设计 (21)4.2 制动钳 (21)4.4 摩擦材料 (21)4.5 盘式制动器间隙的调整方法及相应机构 (22)4.6 制动驱动机构的结构型式选择与设计计算 (22)结论 (25)参考文献 (26)致谢 (27)附录 (28)1 绪论1.1 课题研究的目的及意义汽车的设计与生产涉及到许多领域,其独有的安全性、经济性、舒适性等众多指标,也对设计提出了更高的要求。
汽车电动助力转向控制系统控制器设计
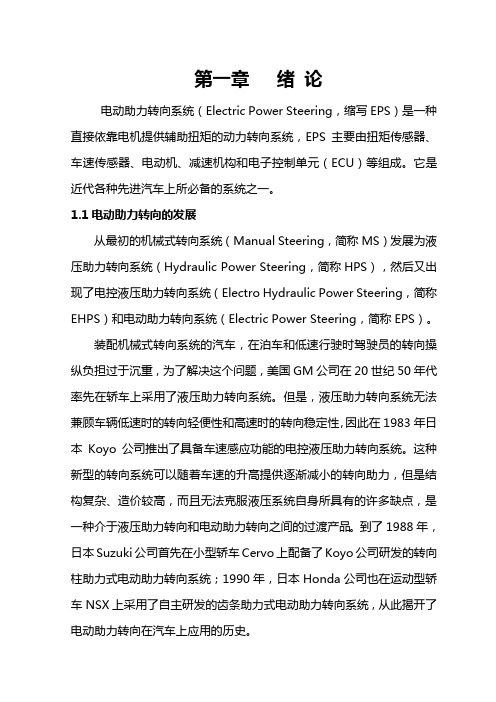
第一章绪论电动助力转向系统(Electric Power Steering,缩写EPS)是一种直接依靠电机提供辅助扭矩的动力转向系统,EPS主要由扭矩传感器、车速传感器、电动机、减速机构和电子控制单元(ECU)等组成。
它是近代各种先进汽车上所必备的系统之一。
1.1电动助力转向的发展从最初的机械式转向系统(Manual Steering,简称MS)发展为液压助力转向系统(Hydraulic Power Steering,简称HPS),然后又出现了电控液压助力转向系统(Electro Hydraulic Power Steering,简称EHPS)和电动助力转向系统(Electric Power Steering,简称EPS)。
装配机械式转向系统的汽车,在泊车和低速行驶时驾驶员的转向操纵负担过于沉重,为了解决这个问题,美国GM公司在20世纪50年代率先在轿车上采用了液压助力转向系统。
但是,液压助力转向系统无法兼顾车辆低速时的转向轻便性和高速时的转向稳定性,因此在1983年日本Koyo公司推出了具备车速感应功能的电控液压助力转向系统。
这种新型的转向系统可以随着车速的升高提供逐渐减小的转向助力,但是结构复杂、造价较高,而且无法克服液压系统自身所具有的许多缺点,是一种介于液压助力转向和电动助力转向之间的过渡产品。
到了1988年,日本Suzuki公司首先在小型轿车Cervo上配备了Koyo公司研发的转向柱助力式电动助力转向系统;1990年,日本Honda公司也在运动型轿车NSX上采用了自主研发的齿条助力式电动助力转向系统,从此揭开了电动助力转向在汽车上应用的历史。
1.2 电动助力转向的分类:机械液压助力机械液压助力是我们最常见的一种助力方式,它诞生于1902年,由英国人Frederick W. Lanchester发明,而最早的商品化应用则推迟到了半个世纪之后,1951年克莱斯勒把成熟的液压转向助力系统应用在了Imperial车系上。
基于stribeck摩擦模型的新型制动系统的振动研究

基于stribeck摩擦模型的新型制动系统的振动研究【摘要】本文针对基于Stribeck摩擦模型的新型制动系统的振动特性展开研究。
在探讨了该研究的背景和意义。
在首先介绍了Stribeck摩擦模型的基本原理,然后描述了新型制动系统的设计方案。
接着分析了系统的振动特性,并进行了实验验证和数值模拟。
结论部分总结了研究结果,提出了进一步研究的展望。
通过本文的研究,可以为新型制动系统的设计和优化提供理论支持,并对振动特性进行深入探讨,为制动系统的性能提升提供参考。
【关键词】关键词:Striebeck摩擦模型、新型制动系统、振动研究、振动特性、实验验证、数值模拟、研究背景、研究意义、结论总结、研究展望。
1. 引言1.1 研究背景研究背景:随着汽车行业的不断发展和制动系统性能要求的不断提高,传统的摩擦制动系统已经很难满足其在提高制动效率、降低磨损和减少振动方面的需求。
为了解决这一问题,越来越多的研究者开始关注基于Striebeck摩擦模型的新型制动系统。
Striebeck摩擦模型是一种描述摩擦现象的数学模型,能够更准确地描述不同工况下的摩擦特性,有助于提高制动系统的性能和稳定性。
目前,新型制动系统的研究已成为制动系统领域的热点之一。
通过结合Striebeck摩擦模型和先进的制动技术,研究者们试图设计出更为高效、可靠和稳定的制动系统。
振动问题作为制动系统中的一个重要挑战,也成为研究的焦点之一。
制动系统的振动不仅会影响到驾驶舒适性和安全性,还会对整车的稳定性产生负面影响。
研究新型制动系统的振动特性具有重要的意义和价值。
1.2 研究意义基于stribeck摩擦模型的新型制动系统的振动研究旨在探究制动系统的振动特性并提出改进方案,以减少振动对系统性能的影响。
制动系统作为车辆的重要部件,在车辆行驶过程中承担着关键的安全功能。
由于制动时的摩擦作用和不稳定性,制动系统在工作过程中往往会产生振动现象,影响其性能和稳定性。
研究制动系统的振动特性对于提高制动系统的工作效率和安全性具有重要意义。
含摩擦环节伺服系统的分析及控制补偿研究

含摩擦环节伺服系统的分析及控制补偿研究含摩擦环节伺服系统的分析及控制补偿研究摘要:本文旨在分析含摩擦环节的伺服系统,并探讨相应的控制补偿方法。
首先,介绍了伺服系统的基本原理和组成结构。
随后,以含摩擦环节的伺服系统为研究对象,分析摩擦环节对系统的影响。
并针对摩擦带来的不稳定性问题,提出相应的控制补偿方法。
最后通过仿真实验验证了控制方法的可行性和有效性。
关键词:伺服系统;摩擦环节;控制补偿;稳定性;摩擦模型1. 引言伺服系统作为一种重要的控制系统,广泛应用于机械、电子和自动化等领域。
伺服系统的目标是根据输入信号精确控制输出信号,使得输出信号能够准确追踪输入信号的变化。
然而,在实际应用中,伺服系统往往会受到各种干扰因素的影响,其中包括摩擦力。
摩擦是阻碍物体相对运动的力,存在于伺服系统的传动环节中,如轴承、滑动副等。
摩擦力的存在会对伺服系统的性能产生显著的影响,例如导致系统的不稳定、迟滞和非线性等问题。
因此,对于含摩擦环节的伺服系统,深入分析其影响因素,并采取相应的控制补偿措施,对于提高伺服系统的性能和稳定性至关重要。
2. 伺服系统的基本原理和组成结构伺服系统由输入端、控制器、执行机构和反馈元件组成。
输入端接收输入信号,经控制器的处理后,通过执行机构产生相应的输出信号。
反馈元件将输出信号与输入信号进行比较,并将比较结果反馈给控制器,用于调整控制器的输出。
3. 含摩擦环节的伺服系统的分析含摩擦环节的伺服系统具有一定的非线性特性,主要表现为摩擦力随速度和方向的变化而变化。
根据摩擦力的特点,一般将其分为静摩擦力和动摩擦力。
静摩擦力是指物体在静止状态下受到的摩擦力,其大小与施加在物体上的压力成正比。
动摩擦力是指物体在运动状态下受到的摩擦力,其大小和方向与物体的速度和运动方向相关。
由于摩擦力的存在,伺服系统会产生迟滞现象和不稳定性,严重影响系统的动态响应和精度。
4. 摩擦力的建模与分析为了更好地理解和控制含摩擦环节的伺服系统,需要准确建立摩擦力的数学模型。
电动助力转向电机补偿控制方法

电动助力转向电机补偿控制方法李绍松;牛加飞;盛任;于志新;涂永发【摘要】搭建电动助力转向(Electric Power Steering,EPS)硬件在环试验平台,基于最小二乘法辨识电机电参数.传统基于转速符号函数或饱和函数的摩擦补偿控制方法,只有在相对转动时补偿系统的动摩擦转矩,为此提出一种动静摩擦共同补偿控制方法.此外,基于电机角加速度进行惯量补偿控制,改善EPS系统惯量对手力的影响;基于电机角速度进行阻尼补偿控制,改善汽车回正性能.【期刊名称】《制造业自动化》【年(卷),期】2016(038)003【总页数】4页(P82-85)【关键词】电动助力转向;硬件在环试验平台;电机参数辨识;电机补偿控制【作者】李绍松;牛加飞;盛任;于志新;涂永发【作者单位】长春工业大学机电工程学院,长春130012;长春工业大学汽车工程研究院,长春130012;长春工业大学机电工程学院,长春130012;长春工业大学机电工程学院,长春130012;长春工业大学机电工程学院,长春130012;长春工业大学机电工程学院,长春130012【正文语种】中文【中图分类】U467.3作为电子技术与转向系统相结合的产物,EPS系统紧扣汽车工业发展大主题[1],在提供助力、减轻驾驶员操纵负担的同时,也能够提高汽车转向性能,以其优越的性能和特点有逐步替代液压助力转向趋势,具有广阔的应用前景[2]。
EPS根据车速信号和转向盘转矩信号确定电机目标控制电流,通过PID控制方法消除电机实际电流与目标电流的偏差,控制电机产生助力[3]。
EPS电机惯量、阻尼补偿控制分别基于电机角加速度、角速度信号确定补偿控制电流,对EPS基本助力控制电流进行修正,降低EPS电机及减速机构的惯量、阻尼对转向性能的影响[4,5]。
EPS电机摩擦补偿控制主要基于转速的符号函数或饱和函数来实现[6],施加的摩擦补偿转矩只有在电机转动时才能融入系统控制中,补偿系统的动摩擦转矩,不能补偿系统的静摩擦力矩。
汽车电动助力制动系统摩擦建模与补偿控制

汽车电动助力制动系统摩擦建模与补偿控制何睿;吴坚;高吉【摘要】The power assisted braking system ( PABS) of vehicle is a typical electromechanical servo sys-tem, and friction, as a non-linear effect commonly existing in electromechanical system, is one of the main factors influencing the control quality of PABS. In this paper, a LuGre friction model is built for representing the friction characteristics of the system,and genetic algorithm is used to conduct the parameter identification of LuGre model, which is then verified by bench test. Finally, the LuGre model is applied to the compensation control of PABS, and the results of real vehicle test verify the control effectiveness of PABS.%汽车电动助力制动系统是典型的机电伺服系统,摩擦作为机电系统中普遍存在的非线性效应,是影响电动助力制动系统控制质量的主要因素.本文中建立了LuGre摩擦模型来表征系统的摩擦特性,并采用遗传算法进行摩擦模型的参数辨识,并通过台架试验进行了验证.最后,将摩擦模型应用到电动助力制动系统的补偿控制中,实车试验结果验证了电动助力制动系统控制的有效性.【期刊名称】《汽车工程》【年(卷),期】2017(039)006【总页数】6页(P683-688)【关键词】电动助力制动系统;LuGre摩擦模型;参数辨识;PID控制【作者】何睿;吴坚;高吉【作者单位】吉林大学,汽车仿真与控制国家重点实验室,长春 130025;吉林大学,汽车仿真与控制国家重点实验室,长春 130025;吉林大学,汽车仿真与控制国家重点实验室,长春 130025【正文语种】中文近年来,采用电机驱动主缸活塞从而产生制动力的制动系统成为汽车领域新的研究热点。
基于制动意图的线控制动系统滑模变结构控制

基于制动意图的线控制动系统滑模变结构控制尘帅;王吉忠;郑龙月;吕林;张西龙【摘要】针对线控制动系统的不确定性和非线性问题,提出将制动强度与制动意图联系起来作为对线控制动系统整体控制的基础,建立了1/2车辆动力学模型及线控制动系统模型;将路面、制动踏板开度及其变化率作为识别器输入,建立了基于神经模糊系统的制动意图识别器;离线求解出不同路面上制动强度与最优滑移率的关系,应用改进滑模变结构控制方法,结合路面识别方法对线控制动系统在Simulink与Carsim中进行联合仿真.仿真结果表明,在不同的路面上,考虑驾驶员制动意图和制动强度的滑模变结构控制方法可以快速稳定地追踪目标滑移率,且具有很强的适应性.【期刊名称】《济南大学学报(自然科学版)》【年(卷),期】2019(033)005【总页数】7页(P425-430,438)【关键词】制动意图;制动强度;路面识别;线控制动系统;滑模控制【作者】尘帅;王吉忠;郑龙月;吕林;张西龙【作者单位】青岛理工大学机械与汽车工程学院,山东青岛 266033;青岛理工大学机械与汽车工程学院,山东青岛 266033;青岛理工大学机械与汽车工程学院,山东青岛 266033;青岛理工大学机械与汽车工程学院,山东青岛 266033;青岛理工大学机械与汽车工程学院,山东青岛 266033【正文语种】中文【中图分类】U463.5汽车安全技术的研究与开发是当今世界汽车技术发展的重要方向之一,对汽车制动系统的不断改进和完善是汽车技术永恒的课题[1]。
由于制动意图和制动强度影响着线控制动系统(brake-by-wire,BBW)的制动效果,因此基于制动意图和制动强度的控制系统方法成为当下研究的热点。
王庆年等[2]应用制动踏板开度及其变化率为输入构建制动意图识别器的模糊控制策略。
许世维等[3]采用制动踏板位移及其变化率为输入设计模糊推理规则,应用神经模糊系统建立制动意图识别模型。
唐先智等[4]运用模糊C均值聚类算法构建了制动意图实时识别模型。
- 1、下载文档前请自行甄别文档内容的完整性,平台不提供额外的编辑、内容补充、找答案等附加服务。
- 2、"仅部分预览"的文档,不可在线预览部分如存在完整性等问题,可反馈申请退款(可完整预览的文档不适用该条件!)。
- 3、如文档侵犯您的权益,请联系客服反馈,我们会尽快为您处理(人工客服工作时间:9:00-18:30)。
2017年(第39卷)第6期汽车工程Automotive Engineering2017(V〇1.39)N〇.6doi:10.1956^^j.chinasae.qcgc.2017.06.012汽车电动助力制动系统摩擦建模与补偿控制+何睿,吴坚,高吉(吉林大学,汽车仿真与控制国家重点实验室,长春130025)[摘要]汽车电动助力制动系统是典型的机电伺服系统,摩擦作为机电系统中普遍存在的非线性效应,是影响电动助力制动系统控制质量的主要因素。
本文中建立了 LuGre摩擦模型来表征系统的摩擦特性,并采用遗传算 法进行摩擦模型的参数辨识,并通过台架试验进行了验证。
最后,将摩擦模型应用到电动助力制动系统的补偿控制 中,实车试验结果验证了电动助力制动系统控制的有效性。
关键词:电动助力制动系统;L u G re摩擦模型;参数辨识;P ID控制Modeling and Compensation Control for Friction inVehicle Power Assisted Braking SystemHe R ui,Wu Jian &Gao JiJilin University,State Key Lab of ASCL,Changchun130025[Abstract]The power assisted braking system (PABS)of vehicle is a typical electromechanical servo system,and friction,as a non-linear effect commonly existing in electromechanical system,is one of the main factors influencing the control quality of PABS.In this paper,a LuGre friction model is built for representing the friction characteristics of the system,and genetic algorithm is used to conduct the parameter identification of LuGre model,which is then verified by bench test.Finally,the LuGre model is applied to the compensation control of PABS,and the results of real vehicle test verify the control effectiveness of PABS.Keywords:power assisted braking system;LuGre friction model;parameter identification;PID control刖言近年来,采用电机驱动主缸活塞从而产生制动 力的制动系统成为汽车领域新的研究热点。
目前,国外大的汽车零部件公司都进行了相关的产品研 发,如博世iBooster、日产e-ACT和LSP公司的IBS 等[1-2]。
国内各大高校也展开相关的理论研究和功 能样机的研发[3-4]。
电动助力制动系统一般由电机作为动力源,通 过减速增矩机构和运动转换机构将电机力转化为主 缸推杆的推力从而和驾驶员一起促动主缸产生制动压力。
电动助力系统是一个复杂的机电伺服控制 系统,在这种系统中,摩擦对系统性能的影响不容忽 视。
摩擦对电动助力制动系统的影响,主要集中在 两个方面:一是机构运动过程中产生的摩擦力会和 正常的力叠加在一起影响反馈控制;二是摩擦会使 机构控制过程中出现抖动现象[5]。
为了消除摩擦对电动助力制动系统控制的影 响,建立准确的摩擦模型进行补偿是亟需解决的关 键问题。
基于摩擦模型进行控制补偿是较广泛采用 的一种方法[6-7],本文中通过对电动助力制动系统 的传动机构进行摩擦特性分析,建立了 LuGre摩擦 模型来表征系统的摩擦特性,并通过遗传算法对摩*国家自然科学基金(51605185)和国家自然基金联合基金(U1564211)资助。
原稿收到日期为2016年8月26日,修改稿收到日期为2016年12月13日。
通信作者:吴坚,副教授,博士,E-mail:wujian@ 。
• 684 •汽车工程2017年(第39卷)第6期擦模型的参数进行辨识,结合台架试验对模型进行 了验证,最后进行了电动助力制动系统摩擦补偿控 制策略的研究。
1系统结构与工作原理本文中针对小型电动车,进行了电动助力制动 系统的开发,结构原理如图1所示。
电动助力制动 系统包括制动踏板、踏板转角传感器、电机、蜗轮蜗 杆、齿轮齿条、制动主缸和制动轮缸等几大部分。
其 工作原理:电子控制器(图中未画出)根据踏板转角 传感器采集的驾驶员输人信号来判断驾驶员的意 图,然后通过控制电机产生助力转矩,并经过蜗轮蜗 杆和齿轮齿条传动机构传递到主缸推杆上,从而和 驾驶员踩踏板的力一同作用促使主缸产生制动力,实现制动助力功能。
2摩擦模型与参数辨识2.1 L u G re摩擦模型电动助力制动系统的控制核心和难点是系统的 摩擦补偿,因此须分析系统的摩擦特性即速度与力 的对应关系。
如果系统摩擦是黏性摩擦,基本上就 是比例关系;但由于机械机构本身特性及加工安装 误差,系统还存在其他非线性因素,例如库伦摩擦、迟滞损失等。
这些非线性因素使速度和力的关系呈 现较强的非线性,可能使踏板感觉不连续,助力很难 补偿。
因此,建立准确的摩擦模型,表征电动助力系 统机构的摩擦特性,并对摩擦带来的非线性进行补 偿,对系统的控制非常重要。
电动助力制动系统工作过程中的摩擦具有动态 特性,具体表现为低速时的爬行、去程与回程时的摩 擦滞后和不同位置的可变最大静摩擦力。
其中,低 速爬行是由于蜗轮蜗杆和齿轮齿条机构在速度较低时动摩擦和静摩擦切换时的黏滑运动导致的;摩擦 滞后是由于电动助力机构在解除助力时,踏板需要 回位,这时电动助力机构的运动方向发生改变,由于 回程时的摩擦力不同于去程时的摩擦力,因此会产 生一个摩擦滞环;可变最大静摩擦力是指最大静摩 擦力与齿轮齿条的位置和运动速率有关,并不是一 个定值。
因此,本文中采用了 LuGre摩擦模型来表 征系统的非线性摩擦特性[8]。
LuGre摩擦模型可用作控制中的摩擦补偿模型,因为它包含大部分的静态和动态摩擦特性,包括 Stribeck效应、摩擦滞后和可变最大静摩擦力等[9]。
LuGre模型的原理:两个表面之间的摩擦界面 被认为是鬃毛之间的联系,鬃毛下表面的刚度大于 上表面。
当有切向力作用时,鬃毛会像弹簧一样偏 转,表征出摩擦力。
如果切向力足够大,则鬃毛偏转 到一定程度就会变为相对滑动。
设鬃毛的平均变形为^则摩擦力F和鬃毛的变 形状态z可表示为dzF= ^〇2+^| +^2 ^dtdz I v Ig(v)= [。
+ (^〇-〇2]l^0式中:%为刚性系数,N/mm;^为黏性阻尼系数, N •s/mm;^2为黏性摩擦系数,N •s/mm;Fs为静摩 擦力,N;vs为Stribeck速度,m/s;F(,为库伦摩擦力,N;v为鬃毛上下表面间的相对速度,m/s。
2.2基于遗传算法的摩擦模型参数辨识在LuGre摩擦模型中,z是不可测量的内部变 量,同时,模型中使用的参数的测量也十分困难,因此,可通过基于试验数据的离线参数辨识方法获得。
本文中通过遗传算法进行LuGre摩擦模型的参数辨 识[1〇-11],首先对LuGre摩擦模型进行离散化:'g(k)= Fc+ (Fs-Fc)e-(Mk)/t〇1^〇z(^-1) I v(^-1) Iz(k)= AT v(k-1)- +z(k-1) ^L g(k-1) 」z(k)-z(k-1)Ff(k)= a〇z(k)+^1----AT----+^2v(k)(2)式中:A T为采样间隔时间;k为当前的采样时刻。
遗传算法辨识原理如图2所示。
图中:w(k)为系统的输人;y(k)为系统输出实2017(V 〇1.39)N 〇.6何睿,等:汽车电动助力制动系统摩擦建模与补偿控制• 685 •推杆位移1 2 3 4 5 6 7时间/s图5输人和输出的力差和踏板推杆位移的时间历程采用遗传算法辨识出最优摩擦模型参数为X = [0.8 50 100 50 5 2.2]。
2.4摩擦模型试验验证确定LuGre 摩擦模型的参数后,通过试验验证 模型的有效性,试验同样采用如图4所示的试验平 台,分别进行如下3种工况的摩擦力估计和测试。
(1)断续推进工况,即驾驶员分段踩下踏板,使 齿条前进一段位移。
重复此过程,以表征齿条在不 同位置时的可变最大静摩擦力。
图4电动助力制动系统摩擦特性测试原理图5为测量的系统的输人与输出的力差和踏板 推杆位移的时间历程。
然后利用测量的数据,采用上节所述的遗传算法进行LuGre 模型的参数辨识。
与蜗轮蜗杆和齿轮齿条传动机构(简称一体化机 构)之间、一体化机构与主缸活塞推杆之间均安装有 力传感器,同时通过拉线式位移传感器测量踏板推 杆位移,通过压力传感器测量主缸和轮缸压力。
一 体化机构两端的两个力传感器记录机构的输人和输 出的力。
两个力传感器的差值减去系统的惯性力即 表征系统的摩擦力。
图2遗传算法辨识原理际观测值;)为估计模型计算值;e a )为估计误 差,e (A ) = y (A ) -y e( A )。
为获得满意的过渡过程动 态特性,对该特性进行优化,要求最小化的目标函数 是估计误差平方的积分:J 2( k )dt(3)J 0令X =[\ F (. Fs ^。
…。
]作为个体,采 用随机取样保留最优个体的方法,设种群大小为M ,/(')为个体适应度函数,则有下式成立:{c …1=max{J(')l “=1,2,",M!/(')=c m -j(')遗传算法的计算过程如图3所示。
(4)图3遗传算法流程图2.3摩擦特性测试试验为了进行LuGre 摩擦模型的参数辨识,本文中 进行了电动助力制动系统的摩擦特性测试,通过搭 建试验台测量电动助力制动机构中的踏板行程和摩擦力的关系。
具体测试方案如图4所示,踏板推杆oo o o 104 32 1 0-O IO I O I32 100^• 686 •汽车工程2017年(第39卷)第6期(2) 准静态推进工况,即驾驶员缓慢踩制动踏 板,并踩到底,然后松开制动踏板,以表征系统的库伦摩擦力。
(3)快速踩踏板工况,即驾驶员快速踩制动踏 板并松开,以表征系统的黏性摩擦和惯性力总和。