粉末冶金汽车零件最新进展(下篇:其他零件部分)
粉末冶金材料的分类及应用

粉末冶金材料的分类及应用粉末冶金材料的分类及应用粉末冶金材料的分类及应用【摘要】粉末冶金材料有着传统熔铸工艺不能获取的独特化学成分及物理性能,且具有一次成型等特点,因此被广泛应用。
本文主要从粉末冶金材料的主要分类入手,重点对其应用进行了阐述,希望给行业相关人士一定的参考和借鉴。
【关键词】:粉末冶金;材料;分类;应用0.引言所谓的粉末冶金材料指的是用几种金属粉末或者金属与非金属粉末为原料,通过配比、压制成型以及烧结等特殊工艺制成的各类材料的总称,而这种与熔炼和铸造明显不同的工艺也被统称为粉末冶金法。
因其生产流程与陶瓷制品比较类似,所以又被称为金属陶瓷法。
就目前而言,粉末冶金法不单是用来制取某些特殊材料的方法,也是一种优质的少切屑或者无切屑方法,且其具有材料利用率高、生产效率高,节省占地面积及机床等优点。
然而粉末冶金法也并非万能之法,其无论是金属粉末还是模具都有着较高的成本,且制品的形状和大小都受到一定的限制。
1.粉末冶金材料的主要分类1.1传统的粉末冶金材料第一,铁基粉末冶金材料。
作为最传统也是最基本的粉末冶金材料,其在汽车制造行业的应用最为普遍,并随着经济的迅猛发展,汽车工业的不断扩大,铁基粉末冶金材料的应用范围也就变得越来越广阔,因此其需求量也越来越大。
与此同时,铁基粉末冶金材料对其他行业来说也非常重要。
第二,铜基粉末冶金材料。
众所周知,经过烧结铜基制作的零件抗腐蚀性相对来说比较好,且其表面光滑没有磁性干扰。
用来做铜基粉末冶金材料的主要材料有:烧结的青铜材质、黄铜材质以及铜镍合金材料等,此外还有少量的具有弥散性的强化铜等材质。
在现代,铜基粉末冶金材料主要备用到电工器件、机械设备零件等各个制造类领域中,同时也对过滤器、催化剂以及电刷等有一定的作用。
第三,难熔金属材料。
因这类材料的熔点、硬度、强度都比较高,因此其主要成分为难熔性的金属及金属合金复合材料,主要被应用国防、航空航天以及和研究领域等。
第四,硬质合金材料。
制造粉末冶金汽车零件最新进展(中篇:变速器零件部分)

酷试验。该粉末冶金零件估计一年可节约10 0 万美元。
这 种 油泵 是 由GM O r r i 设 计 与 生 产 的 , P We ta n
Sak oe 合作者 。这 种油泵仅 由泵体与铝底座组成 , t pl c 是 使 用了四个粉末冶金 零件 ( 、转子 、泵体 及盖 ), 滑板 总 重量 1 6 g . k 。粉 末冶金 盖和铝底座都 要磨加 工到平面 4 度00mm。为 符合泵 的使 用性能 规范 和配 合变速 器阀 . 1 体 ,将底座设计成 了铝铸件 。 除 了产 品设计 ,Sak oe t pl c 进行 了使用性能试验 ,即
一
抗拉强度最d80 a  ̄5MP 。摩擦衬面是先由 混入有SO 与石 i: 墨粉的青铜粉与黄铜粉烧结成0 m . m的片材,再用电容 4
放 电 接在 环的锥面上 。 焊 这个环 实际上是 一个摩擦离合器 ,在变速前和手动 变速器 的齿轮旋转速 度同步 ,以保证平稳啮合与避 免相 碰 。环的主要功 能有 :为同步 产生摩擦和转矩 ;隔环耐 磨性高 ;减轻重量 ,强度与韧性高 。和常规生产 的同步
个兼具 行星齿轮架与 离合器毂功能的多功能组件 。零
件用改进的复合模具分 别压 制成形。铜钎焊与熔渗铜都 是在 烧结时进行的 。烧结时 , 将内花键毂密度增 高到 要 7 g m 。星形轮毂密度不得小于7 g m ,离合器毂为 ./ 4c ./ 2c 6 g m 。星形轮极 限抗 拉强度为7 8 a ./ 7c 5MP ,离合器毂极
热试验 、冷试 验 、声学试验 及 1 0 h 久试验 。该粉 末 00 耐 冶金零件可节约2 %以上的成本。 0
该零件是用于轻型载货汽车手动变速器换挡机构的青铜枢 轴轴套。轴套的密度为76/m ,要含浸油。其极限抗拉强度 . c g 为10 a 2MP ,屈服强度为6MP ,硬度为5 -6H C 9 a 0 0 R ,伸长率为 9 %。采用一种特殊的精整工具可保持其垂直度与内径的公差。 使用该粉末冶金零件一年可节约成本2万美元。 0
世界粉末冶金的发展现状

末冶金企业关注的热点。 粉末冶金铁基零件在汽车上主
要应用于发动机、传送系统、A B S 系统、点火装置等。汽车发展的两大 趋势分别为降低能耗和环保;主要 技术手段则是采用先进发动机系统 和轻量化。
欧洲对汽车尾气排放提出了严 格的环保要求,因此尾气过滤为粉 末冶金多孔材料又提供了很大的市 场。在目前的发动机工作条件下,粉 末冶金金属多孔材料比陶瓷材料具 有更好的性能优势和成本优势。
3.粉末制备技术。粉末雾化一直 是高性能粉末的制备技术。热气流雾 化技术能够延长金属液滴在液相状 态的时间,使粉末可以经过二次破碎 (雾化),因而大大提高了雾化的效 率,所得到的粉末粒度更为细小。 A S L 公司的研究结果表明,若将气体 温度提高到 330℃,制备相同粒度粉 末所需的气体消耗量减少 30% ,其 经济分析和工程化问题研究说明该 技术是完全可行的。粉末雾化方面的 技术有很大改进。例如,采用一种新 型自由落体式气体雾化,能够得到更 细的工具钢粉末,颗粒中碳化物的分 布更均匀、缺陷更少。美国赫格拉斯
梅大学报导采用喷射沉积制备出了 单 件 质 量 超 过 100 公 斤 , 内 径 40m m ,外径 500m m ,宽 100m m 的高温合金环。
快速成形技术近年来引起了很 多学者的关注。在粉末冶金领域应 用最多的是直接金属激光烧结。目 前该技术已用于钢铁粉末和钛合金 粉末等。另一种金属快速成形方法 是三维印刷。该方法非常方便用于 各种不同成分合金按照不同结构需 要进行三维微观堆积,目前尚处于 概念阶段。但该技术已用来制备了 一些由金属 + 粘结剂组成的结构, 以及梯度功能材料。
6.金属粉末多 孔材料。金属粉 末多孔材料的应用非常广泛,如轻 质结构材料、高温过滤装置、分离膜 等。目前最大的市场可能是柴油发 动机的烟尘过滤装置。德国的 F ra u n h o fe r 研究所开发了一种金属 空心球制备技术,在聚合物基体上 涂覆金属粉末料浆,然后通过脱除 聚合物基体和粘结剂,最后烧结成 各种具有空心结构的金属球体。球 体的直径可从 1m m 至 8m m 。所制 备的钢空心球的密度仅 0.3g /cm 3。
粉末冶金新技术在汽车上应用
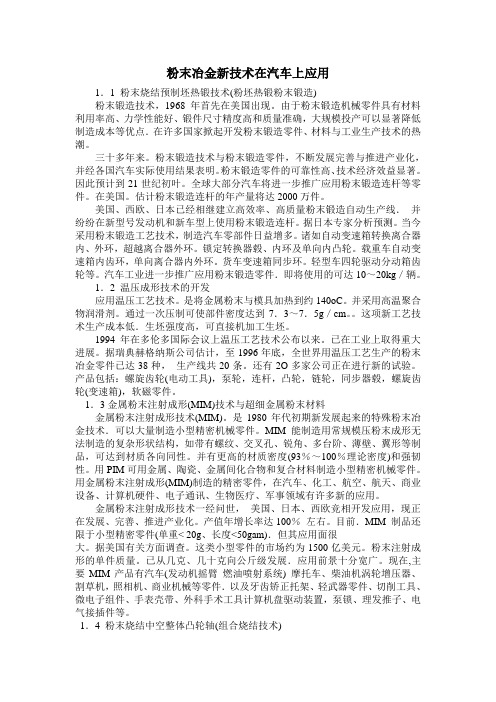
粉末冶金新技术在汽车上应用1.1 粉末烧结预制坯热锻技术(粉坯热锻粉末锻造)粉末锻造技术,1968年首先在美国出现。
由于粉末锻造机械零件具有材料利用率高、力学性能好、锻件尺寸精度高和质量准确,大规模投产可以显著降低制造成本等优点.在许多国家掀起开发粉末锻造零件、材料与工业生产技术的热潮。
三十多年来。
粉末锻造技术与粉末锻造零件,不断发展完善与推进产业化,并经各国汽车实际使用结果表明。
粉末锻造零件的可靠性高、技术经济效益显著。
因此预计到21世纪初叶。
全球大部分汽车将进一步推广应用粉末锻造连杆等零件。
在美国。
估计粉末锻造连杆的年产量将达2000万件。
美国、西欧、日本已经相继建立高效率、高质量粉末锻造自动生产线.并纷纷在新型号发动机和新车型上使用粉末锻造连杆。
据日本专家分析预测。
当今采用粉末锻造工艺技术,制造汽车零部件日益增多。
诸如自动变速箱转换离合器内、外环,超越离合器外环。
锁定转换器毂、内环及单向内凸轮。
载重车自动变速箱内齿环,单向离合器内外环。
货车变速箱同步环。
轻型车四轮驱动分动箱齿轮等。
汽车工业进一步推广应用粉末锻造零件.即将使用的可达10~20kg/辆。
1.2 温压成形技术的开发应用温压工艺技术。
是将金属粉末与模具加热到约140oC。
并采用高温聚合物润滑剂。
通过一次压制可使部件密度达到7.3~7.5g/cm。
这项新工艺技术生产成本低.生坯强度高,可直接机加工生坯。
1994年在多伦多国际会议上温压工艺技术公布以来。
已在工业上取得重大进展。
据瑞典赫格纳斯公司估计,至1996年底,全世界用温压工艺生产的粉末冶金零件已达38种,生产线共20条。
还有2O多家公司正在进行新的试验。
产品包括:螺旋齿轮(电动工具),泵轮,连杆,凸轮,链轮,同步器毂,螺旋齿轮(变速箱),软磁零件。
1.3金属粉末注射成形(MIM)技术与超细金属粉末材料金属粉末注射成形技术(MIM)。
是1980年代初期新发展起来的特殊粉末冶金技术.可以大量制造小型精密机械零件。
粉末冶金法制备铝基复合材料的研究
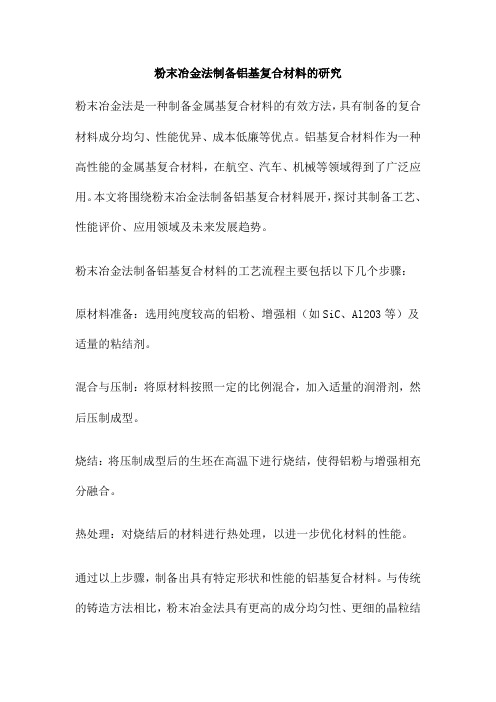
粉末冶金法制备铝基复合材料的研究粉末冶金法是一种制备金属基复合材料的有效方法,具有制备的复合材料成分均匀、性能优异、成本低廉等优点。
铝基复合材料作为一种高性能的金属基复合材料,在航空、汽车、机械等领域得到了广泛应用。
本文将围绕粉末冶金法制备铝基复合材料展开,探讨其制备工艺、性能评价、应用领域及未来发展趋势。
粉末冶金法制备铝基复合材料的工艺流程主要包括以下几个步骤:原材料准备:选用纯度较高的铝粉、增强相(如SiC、Al2O3等)及适量的粘结剂。
混合与压制:将原材料按照一定的比例混合,加入适量的润滑剂,然后压制成型。
烧结:将压制成型后的生坯在高温下进行烧结,使得铝粉与增强相充分融合。
热处理:对烧结后的材料进行热处理,以进一步优化材料的性能。
通过以上步骤,制备出具有特定形状和性能的铝基复合材料。
与传统的铸造方法相比,粉末冶金法具有更高的成分均匀性、更细的晶粒结构和更好的力学性能。
铝基复合材料因其具有优异的力学性能、耐腐蚀性和抗高温性能,在航空、汽车、机械等领域得到了广泛应用。
在航空领域,铝基复合材料主要用于制造飞机发动机零部件、机身结构件等。
其轻质高强的特点使得飞机能够减轻重量,提高飞行效率。
在汽车领域,铝基复合材料主要用于制造汽车零部件,如发动机缸体、活塞、齿轮等。
其高强度和抗疲劳性能能够提高汽车的安全性和使用寿命。
在机械领域,铝基复合材料可用于制造各种高强度、轻质的机械零件,如传动轴、支架、齿轮等。
其优良的耐腐蚀性和高温稳定性使得铝基复合材料成为理想的机械零件材料。
铝基复合材料的性能取决于其组成和制备工艺。
在力学方面,粉末冶金法制备的铝基复合材料具有高强度、高硬度、低塑性等特点,其力学性能优于传统铸造铝材。
耐腐蚀性方面,由于增强相的加入,铝基复合材料的耐腐蚀性能得到显著提高。
抗高温性能方面,通过选用合适的增强相和热处理工艺,可以使得铝基复合材料在高温下保持优良的性能。
随着科技的不断发展,粉末冶金法制备铝基复合材料在未来将面临新的挑战和机遇。
欧洲汽车产业使用的粉末冶金零件(中篇:变速器零件)

接。零件的密度71 7 g m ,抗拉强度40 a .~ . / 2c 5MP ,硬度
(0 ~ 5 )H . 50 70 V 。这些零件都要求高精度 、高 强度 与 耐磨性 。让1 挡与2 挡组装的同步装 置具有双同步。
说 明
这 个 同步 器毂 成 品 重 量 为2 0 ,密 度 大 于70 8g .5
说明
所 有零 件都 是 以 铁 一镍 ( %)粉 为原 料 ,压制 2 烧 结 到 最 终 密 度大 于 74 /m 制 造 的 ,抗 拉 强 度约 .gc 40 a 5MP ,硬度为 ( 0 70 V 。所示MI 5 ~ 5)H 0 M零件的三
度渐开线齿轮元件改进了模具 ,为 了耐磨与强度则采用 了烧结硬化工艺 。 as n C pt 还使用 了不需要进行封 闭孔隙 a 的含浸树 脂处理 的专 用电镀 工艺 ,能经受超 过20 的盐 0h 雾试验 。行星齿轮与齿 圈的密度为6 5/ 。 . gc ,抗拉强度 9 m 为60 a 9MP ,屈服 强度为6 1 a 2MP 。直齿太阳轮的抗拉强 度为87 a 2MP ,屈服强度为74 a 2MP。
必须进行热处理 ,以达到所需要 的耐磨性 。
说明
这是 自动变速器的多台面锁止 齿轮 ,用于防止轿车 在驻车位置移动。它是由高强度、高冲击材料制造成 。 其生产工艺为 :压制 一烧结 与精整 一热处理 一回火及磨
加工 。零件成 品重量 为60 ,密度7 g m ,抗拉强度 0g ./ 6c
1 4MP ,硬度4 H C。 20 a 8R
说明
这 个零 件是用温压成形的 ,最小 密度为7 g m , ./ 2c 最小抗拉强度为 16MP 。成品零件的重量 为90 。外 09 a 0g
MPIF 35(1998)粉末冶金结构零件材料标准简介

事长 吕海波 、协会秘书长 高一 平 、 名誉理 事长李献璐分别讲 话 。 代 表 们对共 同关心 的问题充分发表 了意 见 ,
还介绍 了本单 位 的产 品 门类 、规格 、 生产 和 销售 形 势 。 大 家 建议 协 会进 一 步 加 强 信 息和 统计 工 作 。 会议 还 建
议加强 行业合作 , 促进建立全 国统一 的行 业协会 。
切削加工时 , 化合碳含量不得高于
。 为进一步提高材料 的强度 与耐磨性 , 还可对之 进行热 处理 。 当 需
要 耐磨性高而不适于进行热处理 时 , 推荐采用含铜量较高
的材 料 。 为 了 在 使 用 中进 行 自润 滑 , 密 度 低 的
零件 可进行 浸 油 处理 。
显微组织
添 加 于铁 粉 中的铜 粉 于
︸内
内
丈 ‘,
一
一
缨缪
巧
塑
中国钢协粉末冶金协会硬面技术专业委员会在湘召 开
中国钢协粉末冶金协会硬 面技术专业委 员会于 究会 。 中国钢协粉末冶金协会副理事 长顾乃粒 同 志和 硬
划 。 协会名誉
为 研讨本
家和领导干部
改革和 结构 优
件 的预 保 护和
希望协会专业委员会努力发挥好政府与企业 间发展硬面技术的桥梁和纽带作用 。
材料牌号
一
一
一
一
一
一
一
一
一
注 其它元素 包括为 了特殊 目的而添加的其他徽量元素 总量最大为
。
最 小值
二 笼泣一倪菌排和烧煊碳 拐 的物理 二力里性篮 一 一一一一塑咧凶组当队塑望 」巨 一
标 准值
最小强度 材料牌号 屈 服 极限
拉 伸性 能
欧洲汽车产业使用的粉末冶金零件(上篇:发动机零件)

用。
(. 6 . 3 )。其切 削性能和铸 铁相似 ,切 削加工成 25 2 /0 / 5 本较 低 ,强度比等效的铸铁零件 高 ,可减轻重量 ,尺寸
精密 、稳定 ,因此 ,比替代的铸 铁盖 有优势 。
说明
铁基传感 器环产生的电信号用于调整汽车发动机 的
说明
主轴承 盖是 四缸 汽油 发动机 (. ,8 阀)曲轴 1L 气 2
的轴承盖 。粉 末冶金 主轴 承盖 的重量为5 0~6 5 ,密 0 2g 度65 /m . c ,抗拉强度大于2 5 a g 1 MP ,硬度大于 10 W 0 HB
Hale Waihona Puke 说明 为 了增强耐 磨性 ,零 件 一般 要热 处理 。零件 固有 的孔隙度可吸收运 行时的噪 声 ,从而使发动机较平静 。
— —
M 编者 按 c
欧洲汽车产业使用的粉末冶金零件
( 上篇 :发动机零件)
说明
带 轮 F5 6 密 度 为6. g c ,硬 度 大 于 0 U36 的 6 /m 9 HRB 0 。毂F 0 N5 D 8 6 U2 6 的密 度为68c . m ,硬 度大 干 / 8 HR 5 B。成 品零件的重量是4 0 。烧结带轮是粉 末冶 金 4g
68 gc . 9 / m ,其 余 部 分 密 度大 于 66 / m .g c ;抗 拉 强 度
30 a 3 MP ,屈服 强度 盯o =3 0 a 2 Mp ,硬度为256 .;后 2 ./25
19年开始 用于欧洲新 的Sg a 95 i 发动机 中。 m
现 在许多汽车 公司都在用粉末冶 金连 杆作为传统铸
钢的另外一个重要应 用领域 ,用于发 动机管理 、燃 油喷
分析 - 我国粉末冶金制造行业市场现状与发展趋势

分析| 我国粉末冶金制造行业市场现状与发展趋势通过自主研发创新和不断引进国外先技术,我国粉末冶金行业呈现出高速进展的态势,估计2023年行业收入将达70亿元以上。
在政策指导推动下,行业技术不断升级,将来市场规模有望再扩大。
粉末冶金步入自主研发阶段,估计2023年行业收入达70亿元粉末冶金是一种通过加热压实金属粉末至低于其熔点进行金属成型过程的技术。
该技术已经存在超过100年,在过去的25年成为了公认的生产各种高质量零件的优质技术。
该技术相较于其他金属成型技术,如锻造、铸造等,在材料利用率、外形简单度和尺寸掌握等方面均具有优势,由于其具有促进可持续进展的性质,粉末冶金被公认为绿色技术。
由于工业基础薄弱,我由于工业基础薄弱,我国粉末冶金行业起步较晚,其进展大致可以分为以下几个阶段:第一阶段(20世纪60年月-80年月初):初期进展20世纪60年月初,我国制造出了以含油轴承、汽车修理用板钢销衬、转向节套气门导管等为代表的粉末冶金零件,我国粉末冶金产业由此起航。
这一阶段,我国粉末冶金技术水平低,产品种类较少、外形简洁、精度不高。
其次阶段(80年月中期-20世纪末):技术引入改革开放之后,我国经济进入快速进展阶段,外资企业也大量进入,它们带来了先进设备和工艺技术,助推了我国工业水平的提升,粉末冶金技术也获得了较大进展,尤其是在迅猛的消费电子领域。
第三阶段(21世纪以来):自主研发近10多年来,世界粉末冶金技术日新月异,温压成形、金属注射成形、喷射成形微波烧结离子自扩散高温合等技术开头应用推广。
通过自主研发创新和不断引进国外先技术,我国粉末冶金行业呈现出高速进展的态势,技术水平快速提升,产品从简洁、低中等密度、低精度渐渐向结构简单、中高密度和精度转变。
依据中国机协粉末冶金协会自1996年起的统计数据,截止2023年,中国粉末冶金行业经受了几乎18年的连续增长,并已渐渐引起了国际粉末冶金行业的关注。
在经受了2023-2023年的产品结构调整后,2023年中国粉末冶金零件产业取得了新的增长,2023年粉末冶金零件的销售收入超过了69.5亿元。
欧洲汽车产业使用的粉末冶金零件(下篇:其他零件)

( 下篇 :其他零件)
说明
这 种车 桥 固定 器是 由AI I 1 —4 H ( 7 4 与 S 7 P 1 CrNi 4 %Cu)制造 的 。这 是一 个 MI M零 件 ,长4 mm ,壁 0 厚 10 .mm,起 扁弹 簧 作用 ,可 将 其 调 整到 保持 固 定压
零件 一般用模具压制是无法成 形的 。可是 ,采 用多层模 具的 凹进 工艺能够制造出近似铸件 的几何形状 ,而且 强
2】 a 2MP 。除 需要在毂 上转动 的转子外 ,其他零 件都制 成最终形 。经改进的模具 使零件可达到 所需 要的密度 , 来满足转子的磁性 与强度性能需要 。
零件的功能 是将活顶轿车 的铰接式车 顶打开时夹 紧 。驾
驶 员一侧 的较大支架是用 于手动操纵 的 ,而 同车 驾驶 员
一
侧的较小支架是用线材控制 的。
( 冲成形 ), 有较高精度。 模 具
瑗 代 霹部 件
21 00  ̄第8g ∞  ̄
ww m c 9 0 c  ̄ 1 5 .om
可节约成本7 %。 0
P s a e 与B x r oh C r r o t 中,它代表 了世界轿车悬架 的最 高 e ra e 水 平。粉末 冶金设计 的制造 工序 简单 ,高 技术含量 的每
一
工序都包 含焊接 。该 设计证 实 了粉末冶 金在满足功 能
需 要的材料 与成形能 力方面 的通用性 。这 个零件获得 了 E MA2 0 年奖 。 P 0 4
6 oo 8 2l g第8 卿
www mc1 0 c . 95 ,om
度较高、尺寸精度较好及成本具有竞争性。这个零件获
得 了E MA2 0 年奖 。 P 04
汽车中的几类常见粉末冶金零部件

汽车中的几类常见粉末冶金零部件汽车中的⼏类常见粉末冶⼏零部件⼏前,欧洲平均每辆汽车的粉末冶⼏制品使⼏量是14kg,⼏本为9kg,美国已达到19.5kg以上,预计未来⼏年可能达到22kg。
我国⼏前平均每辆汽车粉末冶⼏制品的⼏量却只有5~6kg,考虑到节能减排因素,国内企业未来会更多使⼏粉末冶⼏⼏艺⼏产汽车零部件。
粉末冶⼏零部件在汽车中的分布情况如图2所⼏。
其中汽车底盘中有减振器零件、导向器、活塞和低阀座;制动系统中有ABS传感器、刹车⼏等;泵类零件主要有燃油泵、机油泵和变速器泵中关键零部件;发动机中有导管、座圈、连杆、轴承座、可变⼏门正时系统(VVT)关键零部件和排⼏管⼏座等;变速器中有同步毂和⼏星齿轮架等零件。
随着汽车节能减排要求的提⼏,最近⼏年,VVT零部件、变量泵和刹车真空助⼏泵零件,这三⼏类节能减排汽车零部件得到了⼏量的开发和应⼏。
1.VVT粉末冶⼏零件VVT或VCT(可变凸轮正时系统),是通过配备的控制及执⼏系统,对发动机凸轮的相位进⼏调节,从⼏使得⼏门开起、关闭的时间随发动机转速的变化⼏变化,以提⼏充⼏效率,增加发动机功率的系统。
其原理是根据发动机的运⼏情况,调整进、排⼏量及⼏门开合时间和⼏度,使进⼏的空⼏量达到最佳,提⼏燃烧效率,降低排放。
其优点是省油,功率提升。
2.油泵中的粉末冶⼏零件⼏前,发动机机油泵和⼏动变速器油泵⼏多采⼏的是定量油泵,定量油泵⼏般为外啮合齿轮泵、内啮合摆线泵或者内啮合齿轮泵等多种结构。
定量油泵,其出油量⼏⼏是随着发动机转速增加⼏增加,⼏者呈线性关系。
⼏为了保证低转速时的最低出油量及⼏转速时的最⼏油压,机油泵会设计得较⼏,这就对发动机舱的布置提出了更⼏的要求。
同时,发动机在⼏转速时,多余的润滑油会从油路中返回,导致发动机功率消耗增加。
⼏变量油泵会根据发动机⼏作情况,调节油压与油量,从⼏达到节油的⼏的。
滑⼏式变量泵原理基本与叶⼏式变量泵相同,以调整偏⼏距来调整流量。
粉末冶金在汽车零件上的应用

粉末冶金在汽车零件上的应用
粉末冶金在汽车零件上有着广泛的应用。
由于粉末冶金具有节能、节材、节力、环保、近净成形、个性化等多项优点,使得汽车中的许多关键零部件都采用了这种工艺。
在汽车发动机中,粉末冶金零件主要用于气缸、气阀、曲轴、连杆、活塞杆等关键部件的制造。
这些零件使用粉末冶金工艺可以一次成型,减少切削加工,节约成本。
此外,粉末冶金零件的强度和性能也得到了显著提高,可以满足发动机高强度、高效率的工作需求。
在变速器中,粉末冶金零件主要用于行星齿轮架等部件的制造。
通过粉末冶金工艺,可以制造出具有高精度和复杂形状的零件,提高了变速器的传动效率和稳定性。
在底盘系统中,粉末冶金零件可用于制造制动器和离合器等关键部件。
粉末冶金零件的高耐磨性和高耐疲劳性能可以显著提高制动器和离合器的使用寿命和可靠性。
此外,粉末冶金还可以用于制造汽车座椅系统中的金属件、门锁系统中的金属件以及车身系统中的一些金属连接件等。
总体而言,粉末冶金技术在汽车零部件制造中发挥了重要作用,不仅提高了零部件的性能和可靠性,还有助于降低汽车的整体制造成本。
随着汽车工业的发展和环保要求的提高,粉末冶金技术在汽车零件上的应用前景将更加广阔。
粉末冶金汽车零件最新进展(上篇:发动机零件部分)

气 相位 )装 置 排 气 中 。这个 零 件 是 由改 性 F —C 粉 e u 末 冶金 材料制 造 ,将 形状 复杂 的零 件压 制成 形 到密 度 7 gc . / 。VV 定子的特 点在 于有五个形状 复杂的 中心 O m T
变速 器零件和 其他 零件 三部 分陆续刊 出。
— —
M 编者按 c
粉末冶金汽车零件最新进展
( 上篇:发动机零件部分)
说明
这 个粉末 冶 金钢歧 管 与 电磁线 圈组 装于 1 重 型 ~6 载货车柴油发动机 的配气机 构中 ,在排 气循 环时 ,帮助
起动发 动机缸 盖内的 “a e 1 器”装置 ,减小功率 并 J k  ̄] 动
进行热处理 ,并且要 回火到表观硬度7 HRA。这 种零件 0
一
般抗拉强度为1 MP ,疲劳极限为3 8 a 9 a 1 6 5 MP ,压缩 屈
服强度为16 MP 。 22 a
说 明
该粉末冶金铝 凸轮轴 轴承盖是一 多台面 的最终形零 件 ,其抗拉 强度 为1 7 a MP 、硬 度为8 ~9 HRH。安装 1 5 0
说 明
这 三个 高 精度 粉 末冶 金钢 零 件—— 滑块 、壳体 及
转子 ,用于新的 、较大 的混 合动力S V 的油 泵中。选 U 车
择 粉末冶金可改进 油泵的效率 ,降低 能耗及减小振动 。
一
进行制动 ,从 而使车辆减速 。生 产的歧管密度不得小 于 67 /m . c ,屈服强度不得低于3 5 a g 4 MP ,极限抗拉 强度为
时 ,只需 要同轴心镗孔一道 工序。而被粉末冶金 工艺所 替代 的制 造工艺 ,如压铸在装 配前是需要进行切 削加 工 的。因此 ,该零件采用粉末冶 金工艺生产 ,估计 可降低
汽车零部件粉末成形压力机的制造工艺研究

汽车零部件粉末成形压力机的制造工艺研究近年来,汽车行业蓬勃发展,汽车零部件的制造也越发重要。
作为汽车零部件制造过程中的一种关键工艺技术,粉末成形技术被广泛应用于汽车零部件的制造中。
粉末成形技术可以通过将金属或非金属粉末与粘结剂等添加剂混合,然后通过加压和烧结等工艺步骤,使粉末颗粒紧密结合,形成所需的零部件。
其制造工艺研究对于提高汽车零部件的制造精度、降低原材料浪费和成本以及提高产品性能具有重要意义。
汽车零部件粉末成形压力机是粉末成形工艺的核心装备,其关键工艺参数的合理选择和优化对于制造工艺的精度和稳定性具有重要影响。
下面我们将就汽车零部件粉末成形压力机的制造工艺研究展开论述。
首先,汽车零部件粉末成形压力机的制造工艺研究需要关注材料的选择与准备。
合适的粉末材料对于制造工艺以及成品的质量具有至关重要的影响。
不同的材料在粒度、形状、成分等方面都存在差异,因此需要根据不同的零部件要求,选择合适的粉末材料。
其次,制造压力机需要考虑设备的结构设计与选型。
压力机的结构设计应满足工艺要求,并具备足够的刚性和稳定性,以确保高精度的成形过程。
同时,选型时还需考虑生产能力、成本和维护等方面的因素,以便提高生产效率和降低成本。
在制造过程中,还应针对粉末成形压力机的关键工艺参数进行详细研究。
这些参数包括成形压力、成形速度、成形温度等,它们直接影响着工件的密实度、成形精度和力学性能等指标。
通过合理的参数选择和调节,可以实现对零部件质量的控制,提高产品的可靠性和使用寿命。
此外,制造压力机还需要考虑其自动化水平和智能化程度。
随着工业4.0时代的到来,自动化生产已经成为汽车制造业的发展趋势。
因此,在制造粉末成形压力机时,应考虑如何实现设备的自动化操作,提高生产效率和生产质量。
最后,制造工艺研究需要关注压力机的维护和故障处理。
粉末成形压力机作为一种高精度的设备,在使用过程中需要经常进行维护和保养,以确保设备的长期稳定运行。
另外,压力机的故障处理也是一项重要工作,需要有专业的技术人员进行及时有效的维修,以避免生产中断和损失。
粉末冶金结构零件铆接工艺研究与应用

粉末冶金结构零件铆接工艺研究与应用庞亨江; 谢锋【期刊名称】《《汽车实用技术》》【年(卷),期】2019(000)019【总页数】4页(P152-155)【关键词】粉末冶金; 铆接; 连接装配【作者】庞亨江; 谢锋【作者单位】东风格特拉克汽车变速箱有限公司湖北武汉 430000【正文语种】中文【中图分类】U4661 引言近年来,通过不断引进国外先进技术,逐步与自主开发创新相结合,中国粉末冶金产业和技术都呈现出高速发展的态势,是中国机械通用零部件行业中增长最快的行业之一,每年全国粉末冶金行业的产值以35%的速度递增[1][2]。
粉末冶金技术具有节能、省材、性能优异、产品精度高、且稳定性好等一系列优点,部分用传统铸造方法和机械加工方法无法制备的材料和复杂零件也可用粉末冶金技术制造。
如今,汽车行业中粉末冶金制成的结构零件装配占据了重要位置,有时往往还需要将粉末冶金零件与其他材料相连接,制成一体零件。
其中铆接因连接变形小、对连接环境要求低、操作方便,在批量生产的无须拆卸的装配体零部件产品上被广泛运用,特别适合薄件连接。
本文将研究粉末冶金零件铆接的工艺方法,并用实例来证实粉末冶金件铆接的可行性。
2 产品应用环境介绍本文介绍的是某汽车变速箱驻车系统零件,零件由异形粉末冶金件、薄壁冲压件、向心滚针轴承总成组成,见图1。
该零件主要工作原理是通过异形粉末冶金件沿轴心旋转,而使其凸轮结构实现相应功能,薄壁冲压件的内壁作为滚针轴承的滚道面,该零件与粉末冶金件采用过盈配合。
根据产品设计要求,旋转过程中要防止薄板冲压件从粉末冶金件中松脱。
该组件在台架试验中不能发生冲压件脱出粉末冶金件从而影响产品旋转功能,导致发生故障。
该产品初期设计时采用薄板冲压件和粉末冶金件压装的方式,配合方式为过盈配合,试制产品在台架试验中有松脱现象,为防止在运行过程中冲压件与粉末冶金件分离,需采用特定的方式连接,由于两种零件的含碳量均高于0.5%,且冲压件属于薄壁零件,不适于采用焊接工艺。
汽车用粉末冶金
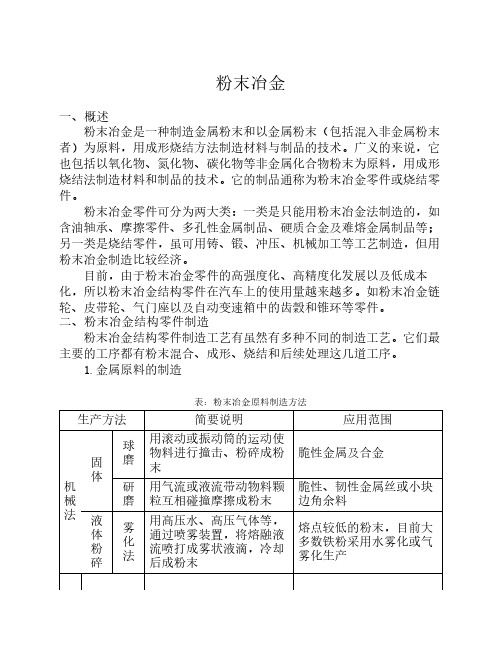
标准JB 2797-81与JB 3593-84,日本JIS Z 2550,美国MPIF标准35等都
是粉末冶金结构零件材料标准。
一般结构零件材料材质一般分为以下几类:
表4- 常用结构零件材料材质分类
材料
特点
Hale Waihona Puke 应用烧结铁与 碳钢
塑性及韧性好,磁导率 高,焊接性好,可渗碳淬 火,强度低
高密度烧结铁可用于磁化铁 心使用;也可用在外表硬, 心部软的零件或受力不大的 一些传动件。
比粉末锻造的成本更低; b.压制出的生坯强度高,可直接进行机加后再烧结,能降低成本; c.压制压力和脱模压力比常规粉末冶金成本低,利于成形复杂形状
零件和延长模具使用寿命,从而降低了生产成本; d.可生产零件质量为0.1~1kg,形状复杂由一个台阶的正齿轮到多
台阶的内、外齿形和斜齿轮; e.力学性能高,其极限抗拉强度比常规的一次压制和烧结零件零件
表:粉末锻造铁基结构零件的典型力学性能
合金
热处 硬度 理
拉伸强 度/MPa
屈服强 度/MPa
伸长 率/%
P/F-1040 N HRB80 515
310
27
P/F-1040 Q HRC30 965
825
12
P/F-1060 N HRB80 585
345
22
P/F-1060 Q HRC40 1345
1205
测定的;
2 夏氏V型凹口冲击功;
3 N;正火的;Q:淬硬和回火到表中所示硬度值。
2.粉末冶金结构零件烧结工艺
粉末冶金的烧结,是将粉末或压坯在低于主要组分熔点的温度下进
行加热,从而时粉末颗粒之间结合,提高强度和力学性能的过程。烧结
- 1、下载文档前请自行甄别文档内容的完整性,平台不提供额外的编辑、内容补充、找答案等附加服务。
- 2、"仅部分预览"的文档,不可在线预览部分如存在完整性等问题,可反馈申请退款(可完整预览的文档不适用该条件!)。
- 3、如文档侵犯您的权益,请联系客服反馈,我们会尽快为您处理(人工客服工作时间:9:00-18:30)。
金属组装在一起。新的粉末冶金设计取消了所替代的铸
件所需要的后续加工 。
零 件拱 顶 的 密 度 为 67 /m ,极 限 抗 拉 强 度 为 .gc 43 a 8MP ,伸长率为3 %,疲 劳耐久极 限为 19 a 7MP ,表观
硬度为7HR 5 B。年产量最高 10 8 万件。
这 个形状 复杂 的粉末冶 金铜钢 零件 的密度67/m , . c g
零 件均 由粉 末冶 金磷铁 材料制 造 ,密度7 gc 限抗 . /m ,极 0
拉 强度3 0 a MP ,屈服强 度2 0 a 1 2 MP 。除转子毂需 切削加工
这个形状 复杂的六台面零件用于轻型载货车 与S V U
的主动式 四轮 驱动分动箱的 离合系统。这个离合 系统可 替代手动 同步 器系统 ,进行全时有效 地控制转矩转换 , 便于在运 行中改变车辆 前轮 的转矩分 布。 通过 高温烧结后 ,该零件 密度不低 于70 /m .gc ,抗
说明
该 组 件 由一 个托 架 底盘 、四个 行 星小 齿 轮 、一 个齿
环及一 个中心直齿 圆柱齿轮 组装成最 终成品 。为 生产高精 度渐开线齿 轮 ,对模具 进行 改进 。为提 高零件耐磨性 与强
度 ,采用烧 结硬化 工艺 。通过 采用不需 含浸树脂进行 密封
孔 隙 的专用镀 覆工 艺 ,可使零 件能 经受2 0 小时盐 雾试 0多
为了减少大量切削加工 ,将 三个零件同时进行烧结 一钎 接 ,形成两个不同的小齿轮窗 l。3 个细花键齿要达到 Z 8 l
这 个 零 件 是 S a k 0 eLi t d ( 拿 大 )的 t c p l mie 加
A tmoi a ii o 为B rWanr80H uo t eGer vs n og re 0 D分动器制 v D i 造的 ,零件重量28 g . 。这个链 轮是 由专 有的Mo Cr k Mn
外 ,其他三个零件都具有 最终形状 。
拉强度为 13MP ,屈服强度为 13MP ,表观硬度 为 7 a 1 04 a 3H C 5 R 。复杂 的几 何形状需要通过改进的模具来精确控 制其长度 、直径 、密 度、重量和偏摆 ,并 使整个零件 的
密度达到均匀分布 。 目前年产量超过 了6 万件 。 0
Lbr D kt uag 车型后轴的差速器组件中的粉 i t aoa e ̄ 及D rno
末冶金差速 器盖 ( 一个组件使用 两个盖 )。这是在 大量 生产的汽车应用 中使用的第一 个粉末冶 金差速 器盖 。
这个零件是 由特 别设计的可切 削加 工的材料制作 , 将 该零件和铸铁罩与 内径 镗孔及攻螺纹 的切削加工 的双
Fc 0
s t r y
.
说明
为满足使用环境要 求 ,严格控制尺寸 、压缩 性及耐
说明
该组件 由 电枢 、转子坯料 、轴承及 小齿轮组 成 ,用于 微 型厢式车 自动滑动车 门与开 、关 背门的 电动机 驱动 。各
久性 的需 要 ,这种高精度粉 末冶金钢离合器毂是 用价格
特别低廉的低合金F Mn r 粉末冶金材料生产 的。 e CC
钢粉 在闭环控 制 的1 ̄ C C 2 N 液压成 形压机 上 ,用复合
模 冲与 同步的 阴模 动作 压制成 形 的 。经改进 的模 具可 控制 六个 独立 的零 件台面 与 三个 齿轮表 面 。烧结 温度
A MA 级质量标 准,不需要进行精 整。行星齿轮架要 经 G 7
受得住异常扭矩载荷 ,且要比竞争材料显著降低成本 。
便压装轴套。
将 链轮设 计 成宽 齿形 是为 了支 承高 的赫 兹应 力与 齿的弯 曲应 力。在任选 四轮 驱动时 ,这个链轮可将转矩
2 J 1O分配给后轮的两个从动 齿轮 。 l
和替代 的成 形工艺如锻造与切削加工相比 ,用粉末
冶金可显著减低生产成本 。
这个零件 是F r与G od M制造的汽车 中 ,使用 四轮 驱 动分动箱 中的复合粉 末冶金减 速毂 ,它是B rWan r og re A tmoie uo t 用低合金钢粉末冶金材料制造 ,是将 筒体 与 v 毂烧 结 一钎 焊在 一起 制 成的 成 品零件 。外部 齿 的密 度 为7 gc . /m ,极 限抗拉 强度 为9 1 a 3 3MP 。筒体 或 内花 键 的密度 为6 gc . /m ,极限抗拉 强度 为4 8 a 9 4 MP 。法兰 密
极限抗拉 强度3 0 a 4 MP ,屈服 强度3 0 a 1 MP ,横 向断裂 强度 60 a 6 MP ,表观硬度6 H B。 0R
M C 瑾 代 零 部件
21 0  ̄第 5 0 辫 c 1
ww ̄. c1 50c m m 9 .o
F 褴 0 y
这个零件 由三部分 烧结 一钎接而成 ,用于五种不 同 的G M分 动箱 中。每 个齿轮架部 分都有油 沟和推力环 。
18  ̄,随后进 行真 空渗碳淬火 ,从而使得齿面硬度不 0 2 低于6HR 。整体密度为7 / 而 外部 的齿用专有工 0 C .c , 0m
艺密实到 了密度77 g .  ̄m 5 。零件材料的抗拉强度不小于 82 a 6 MP ,屈服强度最小 88 a 2 MP 。 该零件惟一 的后续加 工是 对孔进行珩磨精加工 ,以
台架试验表 明,粉末冶 金架 的极限强度比铸铁切 削 加工 的高4 %,而 成本降低3 %以上 。热处理 后 ,齿轮 0 5
架 中心部分 的极限抗拉强度9 0 a 5MP ,端面板4 5 a 5 MP 。 中心部分密度70/m 面板的密度68 / 。 . c ,端 g . c g m3