锡珠的形成及对策分析共29页文档
浅析SMT组装中锡珠的产生原理及预防措施

浅析SMT组装中锡珠的产生原理及预防措施焊锡珠(SOLDER BALL)现象是表面贴装(SMT)过程中的重要缺陷,主要发生在片式阻容组件(CHIP)的周围,由诸多因素引起。
焊锡珠的存在,不仅影响了电子产品的外观,也对产品的质量埋下了隐患。
本文为大家简单解析一下锡珠的形成原理及应对方法。
一、焊球的分类根据锡珠的发生个数和大小,可以分为4种情况。
单个焊粉的情况下,直径为10~40µm,如果大小有50µm以上,则认为是多个焊粉融合。
二、助焊剂内锡珠形成原理・加热时锡膏坍塌在加热时锡膏出现坍塌,但并不是完全连接两焊盘(见0.1m m位置),而是在绿油桥中形成薄薄的锡珠(见0.2m m位置)。
・助焊剂流出随着溶融时助焊剂流出,较迟溶解的焊粉流出。
三、常见锡珠形成原因①回流焊温度曲线设置不当;②助焊剂未能发挥作用;③模板的开孔过大或变形严重;④贴片时放置压力过大;⑤焊膏中含有水分;⑥印制板清洗不干净,使焊膏残留于印制板表面及通孔中;⑦采用非接触式印刷或印刷压力过大;⑧焊剂失效。
四、常见防止锡珠产生方法PC B线路板上的阻焊层是影响锡珠形成最重要的一个因素。
在大多数情况下,选择适当的阻焊层能避免锡珠的产生。
使用一些特殊设计的助焊剂能帮助避免锡珠的形成。
另外,要保证使用足够多的助焊剂,这样在PC B线路板离开波峰的时候,会有一些助焊剂残留在PC B线路板上,形成一层非常薄的膜,以防止锡珠附着在PC B线路板上。
同时,助焊剂必须和阻焊层相兼容,助焊剂的喷涂必须采用助焊剂喷雾系统严格控制。
1、尽可能地降低焊锡温度;2、使用更多的助焊剂可以减少锡珠,但将导致更多的助焊剂残留;3、尽可能提高预热温度,但要遵循助焊剂预热参数,否则助焊剂的活化期太短;4、更快的传送带速度也能减少锡珠。
锡珠产生的原因分析
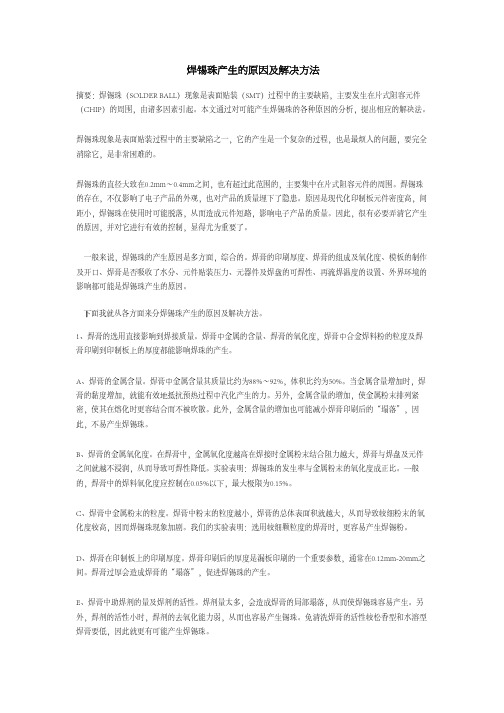
焊锡珠产生的原因及解决方法摘要:焊锡珠(SOLDER BALL)现象是表面贴装(SMT)过程中的主要缺陷,主要发生在片式阻容元件(CHIP)的周围,由诸多因素引起。
本文通过对可能产生焊锡珠的各种原因的分析,提出相应的解决法。
焊锡珠现象是表面贴装过程中的主要缺陷之一,它的产生是一个复杂的过程,也是最烦人的问题,要完全消除它,是非常困难的。
焊锡珠的直径大致在0.2mm~0.4mm之间,也有超过此范围的,主要集中在片式阻容元件的周围。
焊锡珠的存在,不仅影响了电子产品的外观,也对产品的质量埋下了隐患。
原因是现代化印制板元件密度高,间距小,焊锡珠在使用时可能脱落,从而造成元件短路,影响电子产品的质量。
因此,很有必要弄清它产生的原因,并对它进行有效的控制,显得尤为重要了。
一般来说,焊锡珠的产生原因是多方面,综合的。
焊膏的印刷厚度、焊膏的组成及氧化度、模板的制作及开口、焊膏是否吸收了水分、元件贴装压力、元器件及焊盘的可焊性、再流焊温度的设置、外界环境的影响都可能是焊锡珠产生的原因。
㆘面我就从各方面来分焊锡珠产生的原因及解决方法。
1、焊膏的选用直接影响到焊接质量。
焊膏中金属的含量、焊膏的氧化度,焊膏中合金焊料粉的粒度及焊膏印刷到印制板上的厚度都能影响焊珠的产生。
A、焊膏的金属含量。
焊膏中金属含量其质量比约为88%~92%,体积比约为50%。
当金属含量增加时,焊膏的黏度增加,就能有效地抵抗预热过程中汽化产生的力。
另外,金属含量的增加,使金属粉末排列紧密,使其在熔化时更容结合而不被吹散。
此外,金属含量的增加也可能减小焊膏印刷后的“塌落”,因此,不易产生焊锡珠。
B、焊膏的金属氧化度。
在焊膏中,金属氧化度越高在焊接时金属粉末结合阻力越大,焊膏与焊盘及元件之间就越不浸润,从而导致可焊性降低。
实验表明:焊锡珠的发生率与金属粉末的氧化度成正比。
一般的,焊膏中的焊料氧化度应控制在0.05%以下,最大极限为0.15%。
C、焊膏中金属粉末的粒度。
焊锡珠产生的原因及解决方法
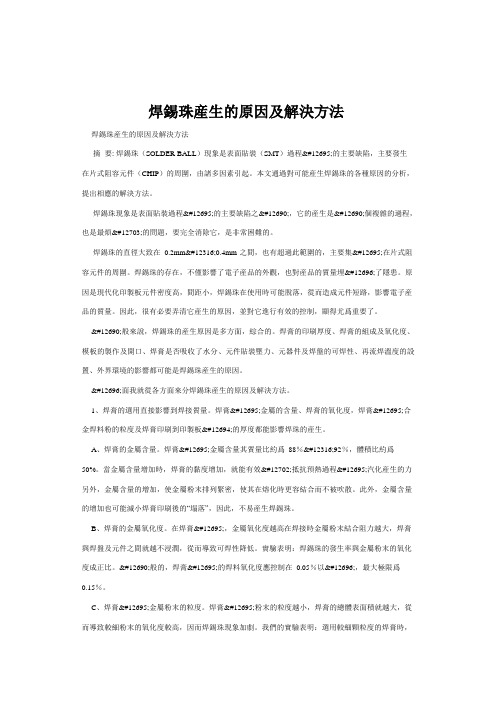
焊錫珠産生的原因及解決方法焊錫珠産生的原因及解決方法摘要: 焊錫珠(SOLDER BALL)現象是表面貼裝(SMT)過程㆗的主要缺陷,主要發生在片式阻容元件(CHIP)的周圍,由諸多因素引起。
本文通過對可能産生焊錫珠的各種原因的分析,提出相應的解決方法。
焊錫珠現象是表面貼裝過程㆗的主要缺陷之㆒,它的産生是㆒個複雜的過程,也是最煩㆟的問題,要完全消除它,是非常困難的。
焊錫珠的直徑大致在0.2mm〜0.4mm 之間,也有超過此範圍的,主要集㆗在片式阻容元件的周圍。
焊錫珠的存在,不僅影響了電子産品的外觀,也對産品的質量埋㆘了隱患。
原因是現代化印製板元件密度高,間距小,焊錫珠在使用時可能脫落,從而造成元件短路,影響電子産品的質量。
因此,很有必要弄清它産生的原因,並對它進行有效的控制,顯得尤爲重要了。
㆒般來說,焊錫珠的産生原因是多方面,綜合的。
焊膏的印刷厚度、焊膏的組成及氧化度、模板的製作及開口、焊膏是否吸收了水分、元件貼裝壓力、元器件及焊盤的可焊性、再流焊溫度的設置、外界環境的影響都可能是焊錫珠産生的原因。
㆘面我就從各方面來分焊錫珠産生的原因及解決方法。
1、焊膏的選用直接影響到焊接質量。
焊膏㆗金屬的含量、焊膏的氧化度,焊膏㆗合金焊料粉的粒度及焊膏印刷到印製板㆖的厚度都能影響焊珠的産生。
A、焊膏的金屬含量。
焊膏㆗金屬含量其質量比約爲88%〜92%,體積比約爲50%。
當金屬含量增加時,焊膏的黏度增加,就能有效㆞抵抗預熱過程㆗汽化産生的力另外,金屬含量的增加,使金屬粉末排列緊密,使其在熔化時更容結合而不被吹散。
表面贴装过程锡珠产生原因和消除方法
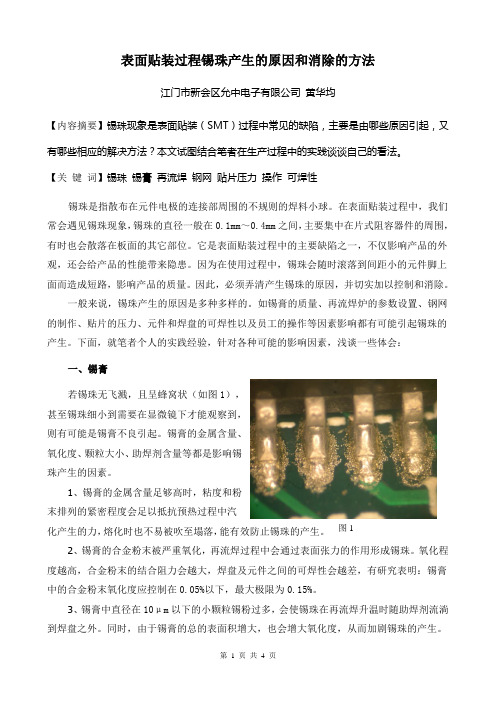
表面贴装过程锡珠产生的原因和消除的方法江门市新会区允中电子有限公司 黄华均【内容摘要】锡珠现象是表面贴装(SMT )过程中常见的缺陷,主要是由哪些原因引起,又有哪些相应的解决方法?本文试图结合笔者在生产过程中的实践谈谈自己的看法。
【关 键 词】锡珠 锡膏 再流焊 钢网 贴片压力 操作 可焊性锡珠是指散布在元件电极的连接部周围的不规则的焊料小球。
在表面贴装过程中,我们常会遇见锡珠现象,锡珠的直径一般在0.1mm ~0.4mm 之间,主要集中在片式阻容器件的周围,有时也会散落在板面的其它部位。
它是表面贴装过程中的主要缺陷之一,不仅影响产品的外观,还会给产品的性能带来隐患。
因为在使用过程中,锡珠会随时滚落到间距小的元件脚上面而造成短路,影响产品的质量。
因此,必须弄清产生锡珠的原因,并切实加以控制和消除。
一般来说,锡珠产生的原因是多种多样的。
如锡膏的质量、再流焊炉的参数设置、钢网的制作、贴片的压力、元件和焊盘的可焊性以及员工的操作等因素影响都有可能引起锡珠的产生。
下面,就笔者个人的实践经验,针对各种可能的影响因素,浅谈一些体会:一、锡膏若锡珠无飞溅,且呈蜂窝状(如图1),甚至锡珠细小到需要在显微镜下才能观察到,则有可能是锡膏不良引起。
锡膏的金属含量、氧化度、颗粒大小、助焊剂含量等都是影响锡珠产生的因素。
1、锡膏的金属含量足够高时,粘度和粉末排列的紧密程度会足以抵抗预热过程中汽化产生的力,熔化时也不易被吹至塌落,能有效防止锡珠的产生。
2、锡膏的合金粉末被严重氧化,再流焊过程中会通过表面张力的作用形成锡珠。
氧化程度越高,合金粉末的结合阻力会越大,焊盘及元件之间的可焊性会越差,有研究表明:锡膏中的合金粉末氧化度应控制在0.05%以下,最大极限为0.15%。
3、锡膏中直径在10μm 以下的小颗粒锡粉过多,会使锡珠在再流焊升温时随助焊剂流淌到焊盘之外。
同时,由于锡膏的总的表面积增大,也会增大氧化度,从而加剧锡珠的产生。
锡珠的产生原因与解决措施

波峰焊接中溅锡珠的形成原因⑴ “小爆炸”理论波峰焊接中在 PCB 的焊接面及元件面上均可能产生锡珠飞溅现象。
普遍认为在 PCB 进入波峰之前有水汽滞留在PCB上的话,一旦与波峰钎料接触,在剧烈升温的过程中,就会在极短的时间内迅速汽化变成蒸汽,发生爆发性的排气过程。
正是这种剧烈的排气可能引发正处在熔融状态中的焊接点内部的小爆炸,从而促使钎料颗粒在脱离波峰时飞溅在PCB上形成锡珠。
在波峰焊接前PCB水汽的来源,杭州东方通信公司对此进行过专题研究和试验,归纳的结论如下:① 制造环境和PCB存放时间制造环境对电子装联的焊接质量有着很大的影响。
制造环境的湿度较重,或PCB包装开封较长时间后再进行贴片和波峰焊生产,或者PCB贴片、插装后放置一段时间后再进行波峰焊,这些因素都很有可能使PCB在波峰焊接过程中产生锡珠。
如果制造环境的湿度太大,在产品制造过程中空气浮动着水汽很容易会在PCB表面凝结,使PCB通孔中凝结有水珠,在过波峰焊时,通孔中的水珠经过预热温区后可能还没有完全挥发完,这些没有挥发完的水珠接触到波峰的焊锡时,经受了高温,就会在短时间内汽化变成蒸汽,而此时正是形成焊点的时候,水汽就会在焊料内产生空隙,或挤出焊料产生锡球。
严重的话就会形成一个爆点,并在它的周围分布有被吹开的细小的锡珠。
假如PCB在包装开封较长时间后再进行贴片和波峰焊,通孔中也会凝结有水珠;PCB完成贴片后或插装完成后放置了一段时间,也会凝结水珠。
同样的原因,这些水珠都有可能在波峰焊过程中导致锡珠产生。
因而,作为从事电子装联的企业,对制造环境的要求和对产品制造过程中的时间安排显得特别地重要。
贴片完成后的PCB应在24小时内完成插装并进行波峰焊,假如天气晴朗干燥,可以在48小时内完成。
② PCB阻焊材料和制作质量在PCB制造过程中所使用的阻焊膜也是波峰焊产生锡球的原因之一。
因为阻焊膜与助焊剂有一定的亲合性,阻焊膜加工不良常常会引起锡珠粘附,产生焊锡球。
SMT锡膏过炉后产生锡珠原因分析

SMT锡膏过炉后产生锡珠原因分析主要有以下几点一,焊料成球焊料成球是最常见的也是最棘手的问题,这指软熔工序中焊料在离主焊料熔池不远的地方凝固成大小不等的球粒;大多数的情况下,这些球粒是由焊膏中的焊料粉组成的,焊料成球使人们耽心会有电路短路、漏电和焊接点上焊料不足等问题发生,随着细微间距技术和不用清理的焊接方法的进展,人们越来越迫切地要求使用无焊料成球现象的SMT工艺。
引起焊料成球的原因包括:1,由于电路印制工艺不当而造成的油渍;2,焊膏过多地暴露在具有氧化作用的环境中;3,焊膏过多地暴露在潮湿环境中;4,不适当的加热方法;5,加热速度太快;6,预热断面太长;7,焊料掩膜和焊膏间的相互作用;8,焊剂活性不够;9,焊粉氧化物或污染过多;10,尘粒太多;11,在特定的软熔处理中,焊剂里混入了不适当的挥发物;12,由于焊膏配方不当而引起的焊料坍落;13、焊膏使用前没有充分恢复至室温就打开包装使用;14、印刷厚度过厚导致“塌落”形成锡球;15、焊膏中金属含量偏低。
二,焊料结珠焊料结珠是在使用焊膏和SMT工艺时焊料成球的一个特殊现象.,简单地说,焊珠是指那些非常大的焊球,其上粘带有(或没有)细小的焊料球.它们形成在具有极低的托脚的元件如芯片电容器的周围。
焊料结珠是由焊剂排气而引起,在预热阶段这种排气作用超过了焊膏的内聚力,排气促进了焊膏在低间隙元件下形成孤立的团粒,在软熔时,熔化了的孤立焊膏再次从元件下冒出来,并聚结起。
焊接结珠的原因包括:1,印刷电路的厚度太高;2,焊点和元件重叠太多;3,在元件下涂了过多的锡膏;4,安置元件的压力太大;5,预热时温度上升速度太快;6,预热温度太高7,在湿气从元件和阻焊料中释放出来;8,焊剂的活性太高;9,所用的粉料太细;10,金属负荷太低;11,焊膏坍落太多;12,焊粉氧化物太多;13,溶剂蒸气压不足。
消除焊料结珠的最简易的方法也许是改变模版孔隙形状,以使在低托脚元件和焊点之间夹有较少的焊膏。
SMT生产工艺中产生锡珠的原因分析及防控措施
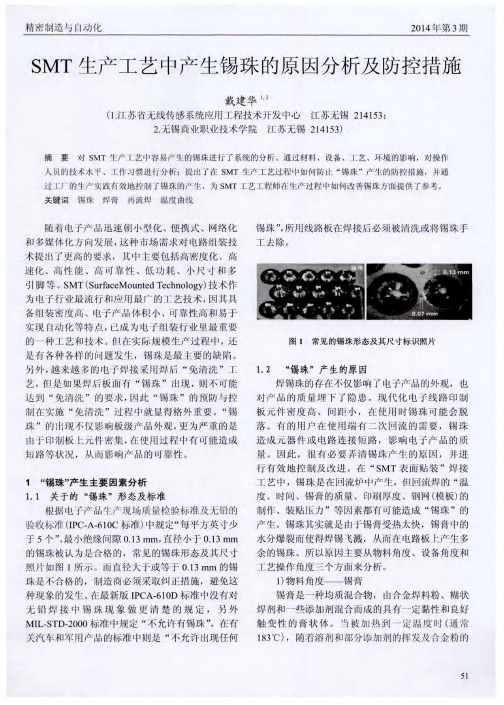
保形 性不 好, 使 印刷 后容 易塌 陷; 如果 模板 内孔 壁粗
糙 不平 , 会造 成锡 膏从模 板 脱落 , 印出 的锡 膏 也容 易 发 生塌 陷 。过 大 的刮 刀压 力会对 锡 膏产 生 比较大 的
图 2 锡膏成分与锡珠率对照 曲线
( 2 ) 锡 膏 中氧 化物 的含 量 。 锡膏 中氧化 物含 量 也
增 高 ,这 就 不利 于焊 料 的完全 “ 润湿 ”从而 导致 细
小 锡珠 产生 。
锡 膏 ,采用激 光 切割模 板 来提 高孔 壁光滑 度 以 降低 刮 刀压 力参数 。有时在 生产 过程 中, 印刷 线 路板 印
错后 需 要将线 路板 上 已经 印制 的锡 膏清洗 干 净 。若 清洗 不 干净 , 印制板表 面和 过孔 内就会有 残 余 的锡
少量 锡粉 飞 出 ,在 焊接 段这 部分 焊粉 熔化 从而 形成
“ 锡珠”。
( 3 ) 回流焊 机 如 果温 区较 少 或 回流 焊 机 的 长度 不够 ,都会 因升温 较快 而产 生锡 珠 。
3 ) 工艺 角度
( 1 ) 印刷 工艺
锡 膏 印刷 时 发 生 的塌 陷使 锡 膏 留在 阻焊 层 上 , 从而 会在 回流 焊 时产生 焊锡 珠 。塌 陷与锡 膏特 性 、 模板 、印刷 参数 设定 有很 大关 系 。 锡 膏 的黏度 较低 、
应 力 的作 用 ,锡 膏 收缩成 焊 点并开 始浸 润爬 升至 焊
( 1 ) 锡 膏 中的金 属含 量 。 锡膏 中金属 含量 的质 量
比约 为 8 9 % ̄9 1 %,体积 比约为 5 0 %左 右 ,如 图 2
所示 。通 常金 属含 量越 多 ,锡膏 中的金 属粉 末排 列
激光焊产生锡珠锡球的原因及解决措施

原因:
(1)焊膏本身质量问题—微粉含量高:粘度过低;触变性不好
(2)元器件焊端和引脚、印制电路基板的焊盘氧化和污染,或印制板受潮
(3)焊膏使用不当
(4)温度曲线设置不当——升温速度过快,金属粉末随溶剂蒸汽飞溅形成焊锡球;预热区温度过低,突然进入焊接区,也容易产生焊锡球
(5)焊膏量过多,贴装时焊膏挤出量多;模板厚度或开口大;或模板与PCB不平行或有间隙
(6)刮刀压力过大、造成焊膏图形粘连;模板底部污染,粘污焊盘以外的地方
(7)贴片的压力大,焊膏挤出量过多,使图形、粘连
对策:
1.控制焊膏质量,小于20um
微粉粒应少于百分之10%
2.严格来料检验,如印制板
受潮或污染,贴装前清洗并烘干
3.按规定要求执行
4.温度曲线和焊膏的升温斜
率峰值温度应保持一致。
160度的升温速度控制在1度/秒~2度/秒
5.①加工合格模板②调整模
板与印制板表面之间距离,是其接触并平行
6.严格控制印刷工艺,保证
印刷的质量
7.提高贴片头Z桌的高度,减小贴片压力。
回流焊接时锡珠的形成及对策详解
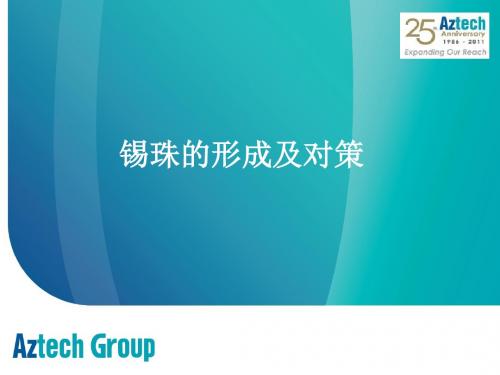
-0 + 20 um
PCB
-0 + 70 um
开口形状
• 凹子型为建议形状
T 字型
锥形
凹字型
V 字型
钢板的孔距
(印刷后)
0.80~0.82mm
0.80~0.82mm
焊锡膏的正确使用方法
大多数锡膏供应商都有他们的使用建议 锡膏的储存一般是在略低于常温而高于0摄氏度的条件下储存
不高于室温可以延长焊剂在使用中的活性寿命,不低于0摄氏度是防止焊剂结晶。储存温 度在2-10摄氏度之间
钢版的厚度
钢板的厚度视零件和焊盘以及引脚间距而综合设计的!
一般选用 0.15mm (6 mil)
( 普通阻容零件,
宽间距
IC脚,
大球BGA 等 )
密间距和小零件选用 0.12 / 0.15(5~6 mil)mm
目前使用最多的是:
单纯锡珠可考虑此厚度
0.12 mm 和 0.15 mm
0.1mm (4 mil) 适合非常密间距的IC或较小零件( <=0402 )
(暂时对策)
调整印刷参数减少减小锡珠
(印刷机的调整)
改良网版设计消除产生锡珠的隐患
(印刷钢板设计的建议)
调整回流温度曲线缓和锡珠的形成
(合适的温度曲线)
形成锡珠的其它原因
(人员素质,生产环境,机版清洁度等)
总结:锡珠的认识-形成的原因-解决方案
(鱼骨图A)
THE END
相关词汇
– – – – – – – – – – • SMT:表面贴装技术(贴片) 锡珠(solder beads):焊料球形成在阻容元件腰部的不良现象 钢版(Stencil):用来印刷(涂布)焊料的模版 回流焊(Reflow):热量以对流形式来加热零部件的炉子 锡膏(Solder Paste):一种金属粉末悬浮于焊接溶剂中的膏状体 温度曲线(Profile):用来监测零部件受热过程的走势图 焊盘(PAD): 电路板线路与零件引脚焊接的金属盘片 PCB :印刷电路版 粘度(Viscosity):锡膏的流变性质,单位是 CP 或 Pa. S(稀,干) 粘性 (Tackiness):粘着零件能力的大小(象胶水), 单位是 gm(克)
推荐-SMT回流焊锡珠产生的原因与防治 精品

锡珠的原因与防治本文介绍,锡珠是一种可能造成短路的缺陷,它可以通过减少沉淀在印刷电路板(PCB)上的锡膏量来大大地减少。
在讨论锡珠(solder beading)的时候,我们首先要准确地定义SMT缺陷。
锡珠是在已经回流焊接的板上发现的,你可以一眼看出它是一个大的锡球,镶嵌在一滩位置紧靠离散组件的助焊剂里面,这些组件具有非常低的离地高度,诸如片状电阻与电容、薄的小外形封装(TSOP)、小外形晶体管(SOT)、D-PAK晶体管、和电阻组合件(图一)。
由于其位置与这些组件的关系,锡珠经常被叫做”卫星”。
由于明显的理由,锡珠有时也叫做”片状中部挤压出的球”,或者类似的东西。
与锡珠比较,锡球(solder balling)的特征是一些微小的球沿着助焊剂残留的外围集结,或者这些球黏在密间距(fine-pitch)焊盘和阻焊的周围。
当要问到防治锡球或锡珠的情况时,第一个问题应该是”它是什么样的,在哪里出现呢?”它为什么是一个问题基本上,锡珠可能形成从一个组件端子到另一个的锡”桥”,因此造成设计上没有的电气连接。
这会引起短路的危险,如果震动造成锡珠松散和移动,短路可能发生在锡珠原来形成的地方,或者在装配上的任何地方。
虽然即使锡珠出现上面的情况,短路也不一定发生,但是锡珠仍然是一个应该尽量减少或消灭的缺陷。
它是怎样发生的在讨论实际的锡珠原因之前,通过图像来展示一下它们一步一步发生的动态是有帮助的:---锡膏印刷在电路板上的焊盘上(图二)。
---在组件贴装期间,一些焊锡被挤到组件下面,并且从焊盘上的焊锡脱离(图三)。
---在回流期间,夹陷在组件下面的焊锡不流回到焊盘。
反过来,它的内聚性能(表面张力)使它形成一个大的锡球(珠)(图四)。
---冷却焊锡的表面张力将组件拉近到焊盘。
再组件被往下拉的时候,锡珠挤出边缘并停留在那里(图五)。
由于过大的刮刀压力或在模板与PCB之间不适当的密封,造成模板底下的锡膏泄漏,这样也可能发生锡珠。
回流焊接锡珠的解决

回流焊接锡珠的解决锡珠是回流焊接中经常出现的缺陷。
锡珠多数分布在无引脚的片式元件两侧, 大小不一且独立存在, 不与其它焊点连接, 见下图。
锡珠的存在, 不仅影响产品的外观, 更重要的是会影响产品的电气性能, 或者给电子设备造成隐患。
锡珠生成的原因是多方面的, 既可能是焊料原因, 也可能是工具或操作等原因造成, 下面将一一讨论。
回流焊锡珠一、锡珠的成因及解决办法原因一: 模版开口不合适。
钢网开口太大,或由于模版开口形状不合适, 导致贴放片式元件时锡膏漫延至焊盘之外, 都会致使回流焊中锡珠生成。
解决方法如下。
①开口尺寸。
一般来说, 片式阻容元件的模版开口尺寸应略小于相应的印制板焊盘, 特别是利用PCB文件制作的模版, 应考虑到线路板一定的蚀刻量, 所以此类焊盘的模版开口一般可开为印制板焊盘的90%-95 %。
②开口形状。
灵活地选择阻容元件的模版开口形状, 可有效地减少或避免锡膏量过多而被挤压出来的情况, 图2 是几种模版开口形状, 制作模版时可以选择其中一种作为阻容元件的开口, 这样既可确保焊接锡膏用量, 又能有效地防止锡珠形成。
SMT钢网元件位开口方式原因二: 对位不准。
模版与印制板对位应准确且印制板及模版应固定完好, 使印锡膏过程模版与印制板保持一致, 因为对位不正也会造成锡膏漫延。
解决方法: 印刷锡膏分为手工、半自动和全自动。
即使是全自动印刷, 其压力、速度、间隙等仍需要人工设定。
所以不管用何种方法, 都必须调整好机器、模版、印制板、刮刀四者的关系,确保印刷质量。
顺便说一下, 印锡膏是整个贴片装配过程的前道工序, 其对整机贴片焊接来说影响很大, 因印刷不良造成的缺陷率远高于其它过程造成的缺陷率,所以印锡膏工艺切不可轻视。
原因三: 锡膏使用不当。
冷藏的锡膏升温时间不足, 搅拌不当, 会使锡膏吸湿, 导致高温回流焊时水汽挥发致锡珠生成。
解决办法: 由于锡膏的有效期较短, 一般使用前都是低温存放的, 使用时, 必须将锡膏恢复至室温后再开盖(通常要求4 小时左右), 并进行均匀搅拌后方可使用, 急于求成必将适得其反。
手工焊接锡珠产生的原因

手工焊接锡珠产生的原因
嘿,你问手工焊接锡珠产生的原因啊?这可有不少情况呢。
一个原因可能是焊接温度太高啦。
就像你做饭火开太大,锅里的东西就容易溅出来。
焊接的时候温度太高,锡就容易变成小珠子到处乱跑。
温度一高,锡就变得特别活跃,不好控制。
还有可能是焊锡丝的质量不太好。
要是焊锡丝里面有杂质啥的,焊接的时候就容易出问题。
就像你买了个质量不好的水果,吃的时候可能会觉得味道怪怪的。
焊锡丝不好,就容易产生锡珠。
操作手法也很重要哦。
如果焊接的时候手不稳,或者速度太快太慢,都可能导致锡珠产生。
就像你写字,如果手不稳,字就写得歪歪扭扭的。
焊接也一样,得稳稳当当的。
另外,电路板不干净也会有影响。
如果电路板上有灰尘、油污啥的,锡就不容易粘在上面,容易形成锡珠。
就像你在脏桌子上画画,颜料就不容易涂均匀。
我给你讲个事儿吧。
我有个朋友自己在家做手工焊接,一开始总是有锡珠。
他不知道咋回事,后来仔细研究了一下。
发现是自己焊接温度调得太高了,而且焊锡丝质量也不太好。
他换了好一点的焊锡丝,调整了温度,焊接的时候也更小心了。
嘿,锡珠就少了很多。
你看,知道锡珠产生的原因很重要呢。
所以啊,手工焊接产生锡珠可能是因为温度太高、焊锡丝质量不好、操作手法不对或者电路板不干净。
在焊接的时候要注意这些问题,才能焊得漂亮。
加油!。
SMT锡膏过炉后产生锡珠原因分析
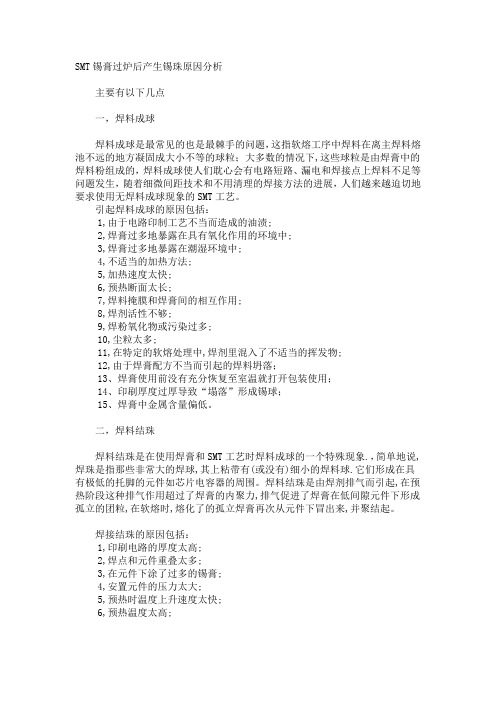
SMT锡膏过炉后产生锡珠原因分析主要有以下几点一,焊料成球焊料成球是最常见的也是最棘手的问题,这指软熔工序中焊料在离主焊料熔池不远的地方凝固成大小不等的球粒;大多数的情况下,这些球粒是由焊膏中的焊料粉组成的,焊料成球使人们耽心会有电路短路、漏电和焊接点上焊料不足等问题发生,随着细微间距技术和不用清理的焊接方法的进展,人们越来越迫切地要求使用无焊料成球现象的SMT工艺。
引起焊料成球的原因包括:1,由于电路印制工艺不当而造成的油渍;2,焊膏过多地暴露在具有氧化作用的环境中;3,焊膏过多地暴露在潮湿环境中;4,不适当的加热方法;5,加热速度太快;6,预热断面太长;7,焊料掩膜和焊膏间的相互作用;8,焊剂活性不够;9,焊粉氧化物或污染过多;10,尘粒太多;11,在特定的软熔处理中,焊剂里混入了不适当的挥发物;12,由于焊膏配方不当而引起的焊料坍落;13、焊膏使用前没有充分恢复至室温就打开包装使用;14、印刷厚度过厚导致“塌落”形成锡球;15、焊膏中金属含量偏低。
二,焊料结珠焊料结珠是在使用焊膏和SMT工艺时焊料成球的一个特殊现象.,简单地说,焊珠是指那些非常大的焊球,其上粘带有(或没有)细小的焊料球.它们形成在具有极低的托脚的元件如芯片电容器的周围。
焊料结珠是由焊剂排气而引起,在预热阶段这种排气作用超过了焊膏的内聚力,排气促进了焊膏在低间隙元件下形成孤立的团粒,在软熔时,熔化了的孤立焊膏再次从元件下冒出来,并聚结起。
焊接结珠的原因包括:1,印刷电路的厚度太高;2,焊点和元件重叠太多;3,在元件下涂了过多的锡膏;4,安置元件的压力太大;5,预热时温度上升速度太快;6,预热温度太高;7,在湿气从元件和阻焊料中释放出来;8,焊剂的活性太高;9,所用的粉料太细;10,金属负荷太低;11,焊膏坍落太多;12,焊粉氧化物太多;13,溶剂蒸气压不足。
消除焊料结珠的最简易的方法也许是改变模版孔隙形状,以使在低托脚元件和焊点之间夹有较少的焊膏。
焊锡珠产生的原因及对策
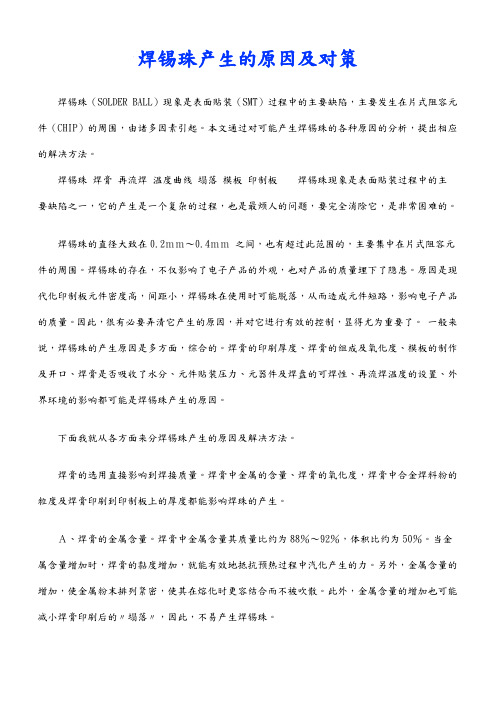
焊锡珠产生的原因及对策焊锡珠(SOLDER BALL)现象是表面贴装(SMT)过程中的主要缺陷,主要发生在片式阻容元件(CHIP)的周围,由诸多因素引起。
本文通过对可能产生焊锡珠的各种原因的分析,提出相应的解决方法。
焊锡珠焊膏再流焊温度曲线塌落模板印制板焊锡珠现象是表面贴装过程中的主要缺陷之一,它的产生是一个复杂的过程,也是最烦人的问题,要完全消除它,是非常困难的。
焊锡珠的直径大致在0.2mm~0.4mm之间,也有超过此范围的,主要集中在片式阻容元件的周围。
焊锡珠的存在,不仅影响了电子产品的外观,也对产品的质量埋下了隐患。
原因是现代化印制板元件密度高,间距小,焊锡珠在使用时可能脱落,从而造成元件短路,影响电子产品的质量。
因此,很有必要弄清它产生的原因,并对它进行有效的控制,显得尤为重要了。
一般来说,焊锡珠的产生原因是多方面,综合的。
焊膏的印刷厚度、焊膏的组成及氧化度、模板的制作及开口、焊膏是否吸收了水分、元件贴装压力、元器件及焊盘的可焊性、再流焊温度的设置、外界环境的影响都可能是焊锡珠产生的原因。
下面我就从各方面来分焊锡珠产生的原因及解决方法。
焊膏的选用直接影响到焊接质量。
焊膏中金属的含量、焊膏的氧化度,焊膏中合金焊料粉的粒度及焊膏印刷到印制板上的厚度都能影响焊珠的产生。
A、焊膏的金属含量。
焊膏中金属含量其质量比约为88%~92%,体积比约为50%。
当金属含量增加时,焊膏的黏度增加,就能有效地抵抗预热过程中汽化产生的力。
另外,金属含量的增加,使金属粉末排列紧密,使其在熔化时更容结合而不被吹散。
此外,金属含量的增加也可能减小焊膏印刷后的″塌落″,因此,不易产生焊锡珠。
B、焊膏的金属氧化度。
在焊膏中,金属氧化度越高在焊接时金属粉末结合阻力越大,焊膏与焊盘及元件之间就越不浸润,从而导致可焊性降低。
实验表明:焊锡珠的发生率与金属粉末的氧化度成正比。
一般的,焊膏中的焊料氧化度应控制在0.05%以下,最大极限为0.15%。
锡珠的产生原因及解决方法
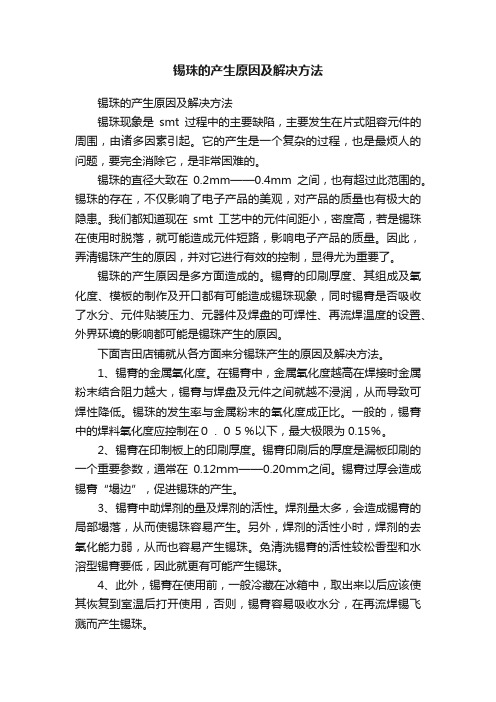
锡珠的产生原因及解决方法锡珠的产生原因及解决方法锡珠现象是smt过程中的主要缺陷,主要发生在片式阻容元件的周围,由诸多因素引起。
它的产生是一个复杂的过程,也是最烦人的问题,要完全消除它,是非常困难的。
锡珠的直径大致在0.2mm——0.4mm之间,也有超过此范围的。
锡珠的存在,不仅影响了电子产品的美观,对产品的质量也有极大的隐患。
我们都知道现在smt工艺中的元件间距小,密度高,若是锡珠在使用时脱落,就可能造成元件短路,影响电子产品的质量。
因此,弄清锡珠产生的原因,并对它进行有效的控制,显得尤为重要了。
锡珠的产生原因是多方面造成的。
锡膏的印刷厚度、其组成及氧化度、模板的制作及开口都有可能造成锡珠现象,同时锡膏是否吸收了水分、元件贴装压力、元器件及焊盘的可焊性、再流焊温度的设置、外界环境的影响都可能是锡珠产生的原因。
下面吉田店铺就从各方面来分锡珠产生的原因及解决方法。
1、锡膏的金属氧化度。
在锡膏中,金属氧化度越高在焊接时金属粉末结合阻力越大,锡膏与焊盘及元件之间就越不浸润,从而导致可焊性降低。
锡珠的发生率与金属粉末的氧化度成正比。
一般的,锡膏中的焊料氧化度应控制在0.05%以下,最大极限为0.15%。
2、锡膏在印制板上的印刷厚度。
锡膏印刷后的厚度是漏板印刷的一个重要参数,通常在0.12mm——0.20mm之间。
锡膏过厚会造成锡膏“塌边”,促进锡珠的产生。
3、锡膏中助焊剂的量及焊剂的活性。
焊剂量太多,会造成锡膏的局部塌落,从而使锡珠容易产生。
另外,焊剂的活性小时,焊剂的去氧化能力弱,从而也容易产生锡珠。
免清洗锡膏的活性较松香型和水溶型锡膏要低,因此就更有可能产生锡珠。
4、此外,锡膏在使用前,一般冷藏在冰箱中,取出来以后应该使其恢复到室温后打开使用,否则,锡膏容易吸收水分,在再流焊锡飞溅而产生锡珠。
58回流焊中锡珠形成的原因及解决方法介绍|南昌回流焊原理2017-03-22 12:44 | #2楼波峰焊第一品牌【精极科技】深圳市精极科技有限公司成立于2002年8月,是一家以设计、生产、销售等工业仓储设备及柔性生产线设备为主的专业生产厂家,同时分销配套的防静电周边产品。
SMT生产工艺中产生锡珠的原因分析及防控措施
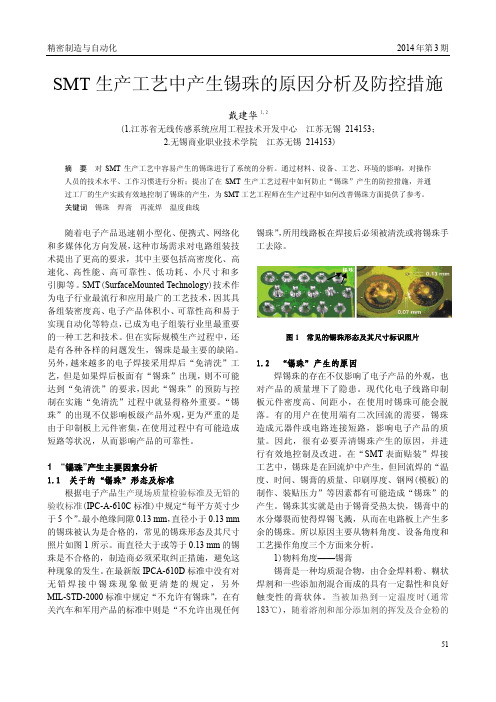
52
戴建华 SMT 生产工艺中产生锡珠的原因分析及防控措施
膏,回流焊时就会形成锡珠,在这一过程中,人员 因素的影响显得尤为突出。因此要加强操作员在 生产过程中的责任心,严格按照工艺要求进行生 产,加强工艺过程的质量控制。
(2)贴片工艺 如果在贴装时压力太大,锡膏就容易被挤压到 元件下面的阻焊层上,在回流焊时焊锡熔化在元件 的周围形成锡珠。可以减小贴装时的压力,调整贴 装压力并设定包含元件本身厚度在内的贴装吸嘴的 下降位置,要注意元器件的物理尺寸,设置正确的 元件高度。
53
精密制造与自动化
2014 年第 3 期
易产生焊锡珠。 (2)锡膏接触空气后,金属颗粒表面可能产生
氧化。金属氧化度越高,在焊接时颗粒越不易结合, 锡膏与焊盘及元件之间就越不浸润,从而导致可焊 性降低。而试验证明锡珠的发生率与锡膏氧化物的 百分率成正比。一般锡膏的氧化物应控制在 0. 03% 左右,最大值不要超过 0. 15%,所以锡膏不宜长时 间暴露的空气中。
(1)印刷机的选用。印刷机本身应选用压力适 中、控制精确的全自动印刷机。特别是与印刷机相 匹配的钢网。钢网的开孔和印刷的压力是印刷工艺 阶段主要控制因素。
(2)贴片机的选用。主要是贴片的压力和位置 精确度,一般选择全自动的贴片机。主流贴片机一 般都能达到使用要求。
产生锡珠的原理

产生锡珠的原理1. 引言锡珠是一种常见的工业原料,广泛应用于电子、建筑、汽车等领域。
本文将探讨产生锡珠的原理,包括锡珠的制备、形成以及其物理性质。
2. 锡珠的制备过程产生锡珠的过程主要包括:原料准备、熔化、冷却、成型四个步骤。
2.1 原料准备制备锡珠的主要原料是锡,以及可能的合金元素。
锡珠通常由纯度高于99.9%的锡制成。
合金元素的添加可根据需要进行调整,以改变锡珠的性能。
2.2 熔化将准备好的锡原料加热到熔点以上,使其完全熔化。
通常使用电炉或气体炉等高温设备进行加热,确保锡珠达到熔化状态。
2.3 冷却在锡珠熔化后,需要将其逐渐冷却。
冷却速度对锡珠的结晶有重要影响,过快或过慢的冷却都可能导致锡珠的结构缺陷。
2.4 成型在冷却过程中,需要通过一定的成型工艺将锡珠塑造成所需的形状。
常见的成型方法包括压制、注射成型等。
3. 锡珠形成的原理锡珠的形成是由于熔化锡在冷却过程中通过相变和凝固产生的。
以下将详细介绍锡珠形成的原理。
3.1 熔化与相变当锡原料加热到熔点时,固体锡开始逐渐熔化成液态锡。
这个过程中,当温度达到锡的熔点时,锡原子开始脱离原子晶格,形成液态结构。
液态锡具有较高的流动性,可以填充在模具中的空隙。
3.2 凝固熔化的锡在冷却过程中,其温度逐渐降低。
当温度低于锡的凝固点时,液态锡开始重新排列,原子逐渐回到晶体晶格中。
这个过程称为凝固,主要包括两个步骤:核化和长大。
3.2.1 核化核化是指在液态锡中形成凝固核的过程。
在锡液中存在一些微小的杂质或基因,它们作为凝固核,引导锡原子重新排列。
核化的发生也依赖于温度和时间等因素。
3.2.2 长大当凝固核形成后,锡液中的锡原子开始围绕凝固核排列,并逐渐增长。
这个过程称为长大。
长大的速度取决于温度梯度以及凝固过程中的固液界面能。
3.3 形成锡珠随着锡液的继续冷却和凝固,凝固核逐渐增大,相邻的凝固核开始连接。
当凝固核连成一片时,锡珠即形成。
锡珠的大小和形状可以通过调整冷却速度、合金成分以及成型工艺等因素进行控制。
产生锡珠的原理
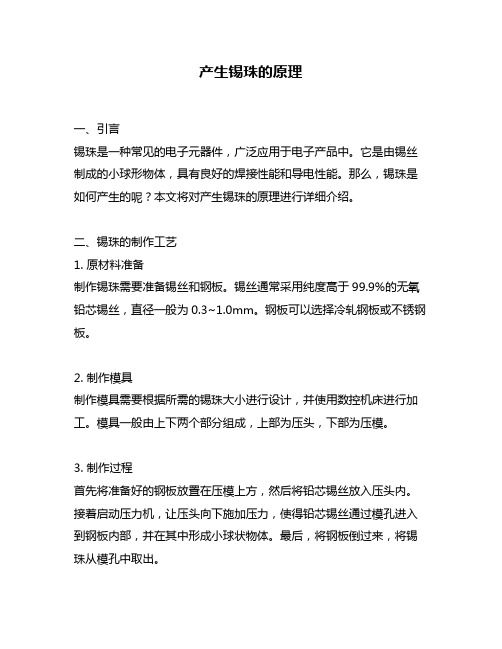
产生锡珠的原理一、引言锡珠是一种常见的电子元器件,广泛应用于电子产品中。
它是由锡丝制成的小球形物体,具有良好的焊接性能和导电性能。
那么,锡珠是如何产生的呢?本文将对产生锡珠的原理进行详细介绍。
二、锡珠的制作工艺1. 原材料准备制作锡珠需要准备锡丝和钢板。
锡丝通常采用纯度高于99.9%的无氧铅芯锡丝,直径一般为0.3~1.0mm。
钢板可以选择冷轧钢板或不锈钢板。
2. 制作模具制作模具需要根据所需的锡珠大小进行设计,并使用数控机床进行加工。
模具一般由上下两个部分组成,上部为压头,下部为压模。
3. 制作过程首先将准备好的钢板放置在压模上方,然后将铅芯锡丝放入压头内。
接着启动压力机,让压头向下施加压力,使得铅芯锡丝通过模孔进入到钢板内部,并在其中形成小球状物体。
最后,将钢板倒过来,将锡珠从模孔中取出。
三、产生锡珠的原理1. 压力作用在制作过程中,压力是产生锡珠的关键因素之一。
通过施加足够的压力,可以使铅芯锡丝进入钢板内部,并在其中形成球状物体。
同时,压力还能够使得球状物体表面变得光滑。
2. 热量作用在制作过程中,热量也是产生锡珠的重要因素之一。
当铅芯锡丝进入钢板内部时,由于摩擦和变形等原因会产生热量。
这些热量会使得铅芯锡丝表面融化,并与钢板表面发生反应,形成球状物体。
3. 表面张力作用表面张力是指液体分子间由于相互吸引而形成的一种力。
在制作过程中,当铅芯锡丝进入钢板内部时,由于表面张力的作用会使得其表面形成球状物体。
四、影响锡珠质量的因素1. 压力大小:如果压力不够大,则无法将铅芯锡丝压入钢板内部,从而无法形成球状物体;如果压力过大,则会使得球状物体表面变得不光滑。
2. 温度大小:温度过低会导致铅芯锡丝无法融化,从而无法与钢板表面发生反应;温度过高则会使得球状物体变形或者表面出现气泡。
3. 模具设计:模具的设计需要根据所需的锡珠大小进行调整。
如果模具设计不合理,则可能会导致锡珠尺寸偏差较大。
4. 原材料质量:原材料的质量直接影响到锡珠的质量。