前处理液槽管理规范
前处理槽液浓度检测与添加方法简介

前处理槽液浓度检测与添加方法简介
皮膜槽内总酸度:取槽液10毫升于锥型瓶中,加3~4滴酚酞指示剂,用0.1N NAOH标准滴定,颜色由无色变为粉红色为滴定终点.此时消耗的NAOH数即为总酸的点数。
一般为18-25点,每提升1点每吨槽液加2KG 皮膜剂。
(每桶升1.2点)
1.皮膜槽内游离酸:取槽液10毫升,加蒸馏水稀释至100毫升,再加入溴
酚篮3~4滴,用0.1N NAOH标准液滴定,溶液由亮黄色变为浅蓝色为滴定终点.所消耗NAOH数即为游离酸的点数。
一般为1~2点,降低1点游离酸,每吨槽液加0.5KG中和剂。
2.皮膜槽内促进剂:取槽液装入雀形弯管内八分满(注意上端不允许有气
泡),加入B试剂1-3G,用拇指按住管口,翻转5秒后静置,此时顶部产生气体即为AC点数。
一般为2~4点为正常,每吨槽液升1点加0.5KG 促进剂。
3.除油槽总碱度:取槽液10毫升于锥型瓶中,加蒸馏水稀释至100毫升,
再加3~4滴溴酚蓝指示剂,用0.1N盐酸或硫酸标准液滴定,颜色由紫色变为亮黄色,所肖耗的盐酸或硫酸标准液毫升数即为总碱度的点数。
一般为30-50点,每提升1点每吨槽加2KG脱脂剂。
4.表调槽PH值测试法,取一条精密试纸,放入槽液半秒钟取出,对照广泛
测试之数据便为PH值,一般8~9为正常。
5.水洗槽一律用PH值测试,一般用循环清水洗。
涂装化学前处理安全要求

涂装化学前处理安全要求
1采用敞开式全浸型化学前处理的作业场所,应布置于单独建筑物内,或布置在建筑物的靠外墙一侧。
该作业场所墙面和地面应使用防腐蚀材料,照明和其他电气设施应采用防潮型。
2敞开式全浸型化学前处理应配置专用的输送设备,不应手工搬运工件。
使用有驾驶室的起重机,其驾驶室应设在化学槽的另一侧。
3大型全浸型化学槽的槽口应至少高出操作平台0.8m。
当槽体埋入地面时,应按标准要求设置防护栏杆和安全标志。
4全浸型有挥发性化学液和加热要求的化学槽,应设置局部排风系统。
5化学槽配制槽液时应先注入水,后注入化学液,对挥发性较强的化学槽配制后应施加覆盖层。
6化学品原液和添加剂的容器应加盖严封,并应张贴标识。
7使用强酸作业场所,应设置具有明显标志的事故喷淋装置和洗眼用具。
8采用全喷淋型的各化学前处理设备应为全封闭或半封闭式,工件出入口应设置防喷淋液飞溅的屏幕室,该室用门洞或挡帘隔开,并设置独立的排风系统。
9喷淋用泵应与排风装置联锁,待风机运行正常后泵再启动;喷淋过程结束,排风装置应延迟5min关闭;当排风装置发生故障,喷淋操作应立即停止。
10所有与腐蚀性化学液接触的前处理槽体、加热系统、循环搅拌系统、喷淋系统、加料系统、排风系统及驱动设备等均应具有耐腐蚀性。
11高压喷射清洗装置应配置压力控制和联锁装置。
12高压喷枪应配置自锁安全机构,喷射间歇应将喷枪自锁。
13高压水泵使用后,应立即清洗保养,使用前应检查高压水系统耐压性和密封性。
14化学前处理作业场所应有防止处理液外溢流出作业区的措施。
15大型工件采用通道式化学槽室,通道进出口应使用柔性材料遮挡封隔。
前处理安全操作规程

预处理安全操作规程为确保生产安全,吐绝一切安全隐患,稳定产品质量,针对预处理操作人员和进入车间的人员,制定以下安全操作规程:一、材料储存1.预处理药液和空桶应放在专用仓库集中存放和装载,并由专人保管,车间根据生产需要按需领用。
2.物料在装装卸、搬运过程中应小心轻放,防止包装破裂;若桶破裂,溢出的液体必须收集在专用桶中。
操作过程中须做好防护措施,避免药液接触眼睛、皮肤,若身体不慎触药液,立即用清水冲洗,并及时就医。
二、药用补充剂1.添加药水前必须采取安全防护措施:穿戴耐酸胶手套,戴安全防护面罩及胶围裙。
2.在添加工作药水时,应每一放、二避的操作进行,确保每次操作人员的生产安全三、处理操作流程1.操作员每天上班前必须穿戴个人防护装备,检查各液槽的水位及液池周边情况,判断是否有泄漏现象,并用PH值试纸检测各槽液酸碱度,确保各项指标合格后方可进行生产操作。
2.合理控制吊机运行情况,吊笼入池、出池过程要慢速、匀速起降,防止工作液飞溅和罐笼与罐壁碰撞,损坏储液罐。
3.吊笼升起后在移至下一槽位之前应稍停留2~3几分钟后,工件上的药液干燥后,可以将其移动到下一个槽中。
4.在操作过程中,每两小时测试一次工作液的浓度和加工产品的质量,及时添加药液原料。
四、污水(泥)收集、处理和回收要点:生产过程中产生的所有液体的预处理(包括地板上的积水)、固体污泥沉淀渣一律不允对外排放,对全部污水(泥)进行集中安全处理。
1.来自净水池的溢流污水和地板上收集的污水被泵送至中和池进行处理和回收(见流程图).2.污水处理池和工作液池中的固体沉淀物收集后暂存于渣储槽中,至一定数量后交由有资质的回收公司(柳州金太阳工业废物处理有限公司)定点回收处理。
五、安全应急方案1.非预处理车间工作人员尽量不要靠近工作液池,任何人不得在池中洗手,洗衣服等做与工作无关的事情,车间人员有向不知者作提醒的义务。
2.如果在生产操作或充液过程中不怕液体飞溅和接触身体部位,应用大量清水清洗身体污染处,并尽快到医院就医。
汽车涂装前处理槽液的工艺管理
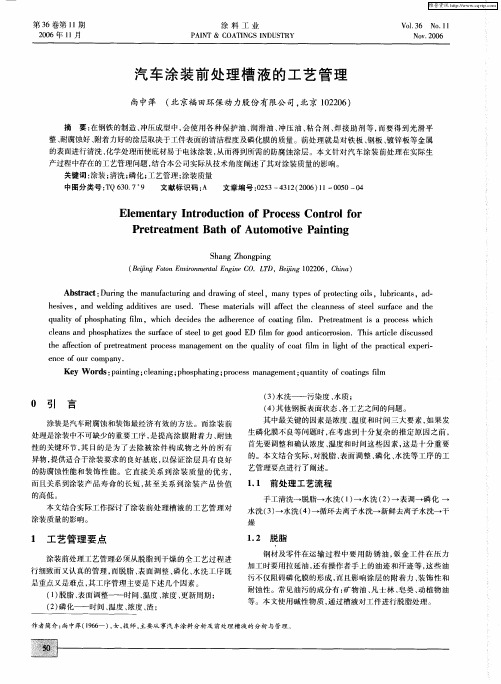
摘 要: 在钢铁 的制造 、 冲压成 型中 , 会使用 各种 保护 油 、 润滑 油 、 冲压 油 、 粘合 剂 、 焊接助 剂等 , 要得 到光滑平 而
整、 耐腐蚀好 、 附着 力好 的涂层取决 于工件 表面的清洁程度及磷化膜 的质量 。前处 理就是 对铁 板 、 钢板 、 锌板等金 属 镀 的表面进行清洗 、 化学处理而使底材易 于电泳 涂装 , 从而得到所需 的防腐蚀涂层 。本文针对 汽 车涂装前 处理在实 际生 产过程中存在 的工艺管理问题 , 结合本公 司实 际从技术 角度 阐述了其对涂装质量 的影 响。
维普资讯
第3 6卷第 1 期 1
20 0 6年 1 月 1
涂 料 工 业
P N & COA I AI T T NGS I DUS RY N T
V 1 . 0 V 2 06
汽 车 涂 装 前 处 理 槽 液 的 工 艺 管 理
性 的关键环节 , 目的是为 了去 除被涂 件构成 物 之外 的所有 其 异物 , 提供适合于涂装要求的 良好基底 , 以保 证涂层 具有 良好 的防腐蚀性能和 装饰 性能 。它 直接关 系到 涂 装质 量的优 劣 , 而且关 系到涂装产 品寿命 的长 短 , 甚至 关系 到涂装 产品 价值
S a g Zh n p n h n o g ig
( ei o nE v o m na E gn O T B rn 0 26, hn ) B rn F t ni n etl n ieC .L D, eig1 20 C i g o r a
Ab t a t: in h n f cu i g a r wi fse l sr c Dur g t e ma u a t rn nd d a ng o te ,ma y tp s o r tc ig ol ,lbrc n s d n y e fp oe t is u i a t ,a — n h sv s n l i g a d tv s a e u e . Th s mae i l l af c h l a e s o te u f c a d t e e ie ,a d we d n d iie r s d ee tras wil fe tt e c e nn s fse ls ra e n h q lt fp o ph tn i ,whih d c d s te d e e c fc ai g fl uai o h s ai g f m y l c e i e h a h r n e o o tn m. Pr te t n s a p o e s whih i e r ame ti r c s c c e n n h s h tz st e s ra e o te o g tg o l a sa d p o p a ie h u f c fse lt e o d ED l f rg o n io r so i f m o o d a tc ro in.Th sa tce dic s d i ril s use t e afc in o r te t n r c s na e n n t e q lt fc a l i ih ft e p a t a x r— h fe to fp e r ame tp o e s ma g me to h uai o o tf m n l to h r c i le pe y i g c i
汽车涂装前处理槽液的工艺管理

喷淋前处理及槽体制作规范
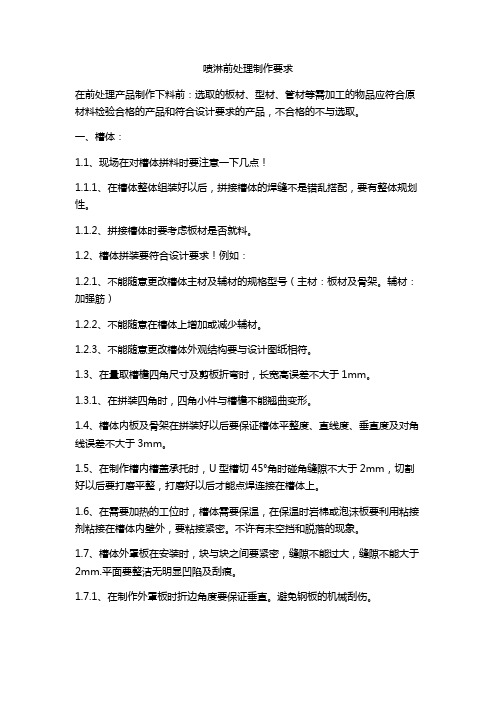
喷淋前处理制作要求在前处理产品制作下料前:选取的板材、型材、管材等需加工的物品应符合原材料检验合格的产品和符合设计要求的产品,不合格的不与选取。
一、槽体:1.1、现场在对槽体拼料时要注意一下几点!1.1.1、在槽体整体组装好以后,拼接槽体的焊缝不是错乱搭配,要有整体规划性。
1.1.2、拼接槽体时要考虑板材是否就料。
1.2、槽体拼装要符合设计要求!例如:1.2.1、不能随意更改槽体主材及辅材的规格型号(主材:板材及骨架。
辅材:加强筋)1.2.2、不能随意在槽体上增加或减少辅材。
1.2.3、不能随意更改槽体外观结构要与设计图纸相符。
1.3、在量取槽檐四角尺寸及剪板折弯时,长宽高误差不大于1mm。
1.3.1、在拼装四角时,四角小件与槽檐不能翘曲变形。
1.4、槽体内板及骨架在拼装好以后要保证槽体平整度、直线度、垂直度及对角线误差不大于3mm。
1.5、在制作槽内槽盖承托时,U型槽切45°角时碰角缝隙不大于2mm,切割好以后要打磨平整,打磨好以后才能点焊连接在槽体上。
1.6、在需要加热的工位时,槽体需要保温,在保温时岩棉或泡沫板要利用粘接剂粘接在槽体内壁外,要粘接紧密。
不许有未空挡和脱落的现象。
1.7、槽体外罩板在安装时,块与块之间要紧密,缝隙不能过大,缝隙不能大于2mm.平面要整洁无明显凹陷及刮痕。
1.7.1、在制作外罩板时折边角度要保证垂直。
避免钢板的机械刮伤。
1.8、在槽体内壁板及外罩板开洞时,绝对不允许用电焊开洞。
特别要注意在外罩板上开洞。
一定要保证外观质量,需要从侧边往里开洞时,处理缝隙不得大于1mm。
有必要时利用两个半圆加以修饰。
1.9、槽体的焊接要求:1.9.1、槽体内壁焊接时一定要先点焊在全焊,不锈钢槽必须要求用氩弧焊加不锈钢焊丝焊接,加强筋焊接时不用满焊只需段焊,在段焊时每段长35mm间距150mm,两边对称焊接,焊好过后酸洗.槽檐需要打磨抛光。
1.9.2、如需在外罩板上点焊时,点好后打磨,打钠抛光。
前处理液槽管理规范

文件编号:
文件名称
前处理液槽管理规范
版号:A/0
分发日期:
1/3码:页
分发编号:
一、予脱脂:浓度:30-35,时间10-15分钟
浓度测定、管理方法:1、取工作液10ml,以酚酞作指示剂,用0.1NH2S4溶液滴定,使溶液从粉红色变至无色时消耗之毫升数为溶液的游碱度。
2、浓度尽量保持在基准范围内,如果低于基准点,加脱脂剂提高其浓度。
三、除锈:浓度120-150,时间:10-15分钟。
测定、管理方法:
1、用比重器放入液槽中,所余之数为基数。
2、定期检测,正常情况3-5个月更换新液。
四、水洗:时间:1-2分钟
1、清水保持溢流。
2、定期每周更换清水。
编写
审核
批准
环城制品厂程序文件
文件编号:
文件名称
前处理液槽管理规范
版号:A/0
分发日期:
划痕至基体形成九个方块。方格边长为1毫米,用手指轻轻触摸,
方格脱落不超过2个以内为合格。或用粘贴法进行胶带试验。
编写:
审核:
批准:
环城制品厂程序文件
文件编号:
文件名称
喷涂车间制程检验作业指导
版号:A/0
分发日期:
页码:1/2
分发编号:
1、目的
喷涂工序作为工件表面处理的一个特殊过程,对工件最终是否合格,起到关键的作用。因此对每一质量控制点及过程参数必须进行控制和监督,以确保满足规定要求。
要求:1、喷涂完成的工件经过十分钟时间流平。
2、温度与速度(时间)保持控制在标准的范围内。
九:检验:
要求:1、色差与样板一致,表面必须平整,光滑、无砂粒,无疙瘩,
前处理槽液工艺及检测标准

散热器前处理槽液检测标准、方法及工艺一、试剂的配比1、0.100mol/l Na2S2O3 标准溶液(硫代硫酸钠):称取Na2S2O3·5H2O(5水和硫代硫酸钠)固体25g溶于水500ml 中,转移至1000ml棕色容量瓶中加水稀释至刻度,放置一个星期后标定。
2、0.500mol/l NaOH标准溶液(氢氧化钠):称取氢氧化钠固体40.5g于500ml烧杯中,加纯水300ml,加入0.5-1.0g BaCl2,待冷却后,移于2000ml容量瓶中,加水稀释至刻度,放置数小时后取清澈液后,浑浊液静置过滤。
3、0.100mol/l NaOH标准溶液:称取4.05克NaOH于500ml烧杯中,加纯水300ml,加入0.5-1.0g BaCl2待冷却后,移于1000ml容量瓶中,加水稀释至1000ml摇匀,放置数小时,取清澈液后,浑浊液静置过滤。
4、50% H2SO4溶液(硫酸):取500ml水于1000mL烧杯中,把烧杯放在冷水,沿着玻璃棒慢慢加入浓硫酸并不断搅拌下加入500ml浓硫酸混匀,再稀释至1000ml。
5、25% H2SO4溶液(硫酸):取500ml水于1000mL烧杯中,把烧杯放在冷水,沿着玻璃棒慢慢加入浓硫酸并不断搅拌下加入250ml浓硫酸混匀,再稀释至1000ml。
6、酚酞指示剂(1%):称取1.0g酚酞指示剂,用95%无水乙醇稀释至100mL,让其完全溶解备用。
7、淀粉指示剂(1%):取100ml纯水加热煮沸倒入已用少许水湿润过的1.0g淀粉杯中,放在电炉加热煮沸1-2min(分钟)8、溴酚蓝指示剂:①、0.1克溴酚蓝溶于20ml酒精中,再加80ml水,倒入容器中备用。
②、0.1克溴酚蓝溶于100ml无水乙醇(酒精)中,转移入滴瓶中,贴标签备用。
9、Pa酸指示剂(N-苯基邻氨基苯甲酸)0.2 克N-苯基邻氨基苯甲酸和0.2克硫酸钠用水溶解后定容到100毫升的容量瓶中,混匀过滤使用。
前处理作业指导书

3.5.1用10ml吸管取10ml加工液置于三角烧杯中。
3.5.2滴加3~5滴BPB指示剂,摇匀。
3.5.3以0.1N NaOH进行滴定,边滴定边晃动烧杯。
3.5.4溶液由黄色变为淡蓝色为终止点,滴定过程中所消耗至0.1NNaOH毫升即为浓度,1ml=1piont。
降到规定温度
皮膜槽促进剂过高
调节降低
酸比过高
调节降低酸比
3.皮膜不均匀,甚至不上膜
脱脂不彻底
检测浓度后添加脱脂剂
表调液浓度偏低或老化
调整或更新
酸洗槽浓度太低
检测浓度后补充浓H2SO4
皮膜槽全酸度偏低或促进剂浓度偏高
检测浓度后进行调整
4.皮膜有水痕
烘干温度不足
升温
工件内水未流干净
改变挂具
5.皮膜发黑
酸洗槽浓度过高或浸泡时间过久
版本
制定日期
2012年8月6日
3.4槽液全酸度(TA)的测试方法:
3.4.1用10ml吸管取10ml加工液置于三角烧杯中。
3.4.2滴加3~5滴PP指示剂,摇匀。
3.4.3以0.1N NaOH进行滴定,边滴定边晃动烧杯。
3.4.4溶液由无色变为粉红色为终止点,滴定过程中所消耗至0.1NNaOH毫升即为浓度,1ml=1piont。
3.4.4溶液由黃色变为藍色为终止点,滴定过程中所消耗之0.1NNaOH毫升数即为浓度,1ml=1piont
3.4.5检验完毕。清洗所使用的测试工具,并放入指定位置。
3.4.6记录所测试浓度
★注意:1.轻拿轻放,小心打碎玻璃仪器(如三角烧杯、试管等)。
2.小心药水溅到眼睛(如溅到立即用水冲洗)。
3.切记清洗试管、烧杯,防止试药被污染。
汽车涂装前处理槽液的工艺管理.doc

汽车涂装前处理槽液的工艺管理作者:尚中萍来源:万方数据时间:2009-3-11 9:53:09在钢铁的制造、冲压成型中,会使用各种保护油、润滑油、冲压油、粘合剂、焊接助剂等,而要得到光滑平整、耐腐蚀好、附着力好的涂层取决于工件表面的清洁程度及磷化膜的质量。
刖处理就是对铁板、钢板、镀锌板等金属的表面进行清洗、化学处理而使底材易于电泳涂装,从而得到所需的防腐蚀涂层。
本文针对汽车涂装前处理在实际生产过程中存在的工艺管理问题,结合结口本公司实际从技术角度阐述了其对涂装质量的影响。
在钢铁的制造、冲压成型中,会使用各种保护油、润滑油、冲压油、粘合剂、焊接助剂等,而要得到光滑平整、耐腐蚀好、附着力好的涂层取决于工件表面的清洁程度及磷化膜的质量。
前处理就是对铁板、钢板、镀锌板等金属的表面进行清洗、化学处理而使底材易于电泳涂装,从而得到所需的防腐蚀涂层。
本文针对汽车涂装前处理在实际生产过程中存在的工艺管理问题,结合本公司实际从技术角度阐述了其对涂装质量的影响。
0引言涂装是汽车耐腐蚀和装饰最经济有效的方法。
而涂装前处理是涂装中不可缺少的重要工序,是提高涂膜附着力、耐蚀性的关键环节,其目的是为了去除被涂件构成物之外的所有异物,提供适合于涂装要求的良好基底,以保证涂层具有良好的防腐蚀性能和装饰性能。
它直接关系到涂装质量的优劣,而且关系到涂装产品寿命的长短,甚至关系到涂装产品价值的高低。
本文结合实际工作探讨了涂装前处理槽液的工艺管理对涂装质量的影响。
1 工艺管理要点涂装前处理工艺管理必须从脱脂到干燥的全工艺过程进行细致而又认真的管理,而脱脂、表面调整、磷化、水洗工序既是重点又是难点,其工序管理主要是下述几个因素。
(1)脱脂、表面调整-时间、温度、浓度、更新周期;(2)磷化-时间、温度、浓度、渣;(3)水洗-污染度、水质;(4 )其他钢板表面状态、各工艺之间的问题。
其中最关键的因素是浓度、温度和时间三大要素,如果发生磷化膜不良等问题时,在考虑到十分复杂的推定原因之前,首先要调整和确认浓度、温度和时间这些因素,这是十分重要的。
槽液配制调整安全操作规程
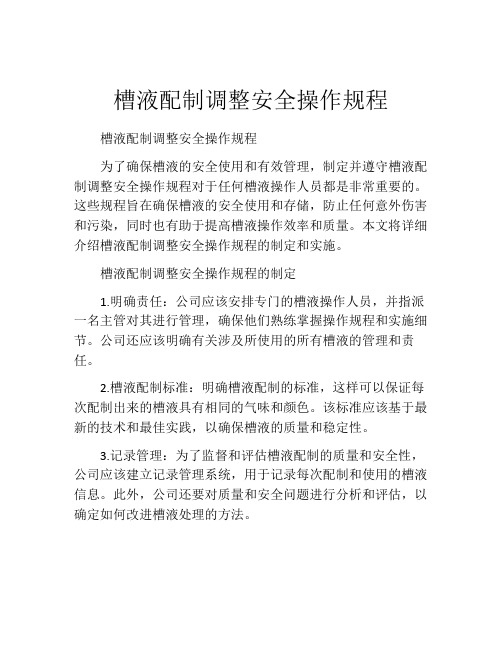
槽液配制调整安全操作规程槽液配制调整安全操作规程为了确保槽液的安全使用和有效管理,制定并遵守槽液配制调整安全操作规程对于任何槽液操作人员都是非常重要的。
这些规程旨在确保槽液的安全使用和存储,防止任何意外伤害和污染,同时也有助于提高槽液操作效率和质量。
本文将详细介绍槽液配制调整安全操作规程的制定和实施。
槽液配制调整安全操作规程的制定1.明确责任:公司应该安排专门的槽液操作人员,并指派一名主管对其进行管理,确保他们熟练掌握操作规程和实施细节。
公司还应该明确有关涉及所使用的所有槽液的管理和责任。
2.槽液配制标准:明确槽液配制的标准,这样可以保证每次配制出来的槽液具有相同的气味和颜色。
该标准应该基于最新的技术和最佳实践,以确保槽液的质量和稳定性。
3.记录管理:为了监督和评估槽液配制的质量和安全性,公司应该建立记录管理系统,用于记录每次配制和使用的槽液信息。
此外,公司还要对质量和安全问题进行分析和评估,以确定如何改进槽液处理的方法。
4.员工培训:公司应该为每个涉及槽液配制和操作的员工提供必要的培训,以确保他们能够理解操作规程和实施细节。
该培训应包括槽液安全知识、操作规程和设备的使用方法。
5.设备维护:公司应该定期维护和检查所有涉及槽液操作的设备,以确保其正常运转并符合安全标准。
如果发现任何设备故障或不合格情况,应立即对其进行修复和更换。
槽液配制调整安全操作规程的实施1.操作前准备:在操作槽液之前,请确保您已经读取并理解了槽液操作规程。
另外,请清理操作区域,确保没有任何障碍物和垃圾。
2.选择权威配件:选择适当的配件确保槽液的质量。
建议使用原厂设备或受权代理商提供的配件。
3.精确量化:使用准确的量器和量杯确保槽液的配制准确和稳定。
每次操作时请仔细记录所使用的配件数量和配制过程。
4.注意安全:在槽液配制和操作过程中,请始终关注安全问题。
这包括穿戴防护装备,避免混合不同类型的槽液,避免使用已过期或受损的配件等。
5.妥善存储:存储槽液时,请关注存储环境和安全问题。
前处理除油槽工艺要求

前处理除油槽工艺要求
1.配槽方法
将槽加水七分满,按吊篮高度,评估槽液多少吨,一般每吨槽加脱脂粉20KG,脱脂剂30KG,用空压气搅拌均匀便可使用。
2.处理时间
常温5-10分钟,(必要时根据工件油污而定处理时间,如再有必要时,还可加热处理)。
3.浓度控制和操作
生产中由于浓度会被消耗,需添加脱脂粉和脱脂剂增加它的碱度,每吨槽液加入2-5 原液可提升碱度1点。
(原液比例为脱脂粉0.5KG,脱脂剂1.5KG),一般采用PH值测试法:取一条试纸放入槽液中半秒钟取出,对照试纸上之PH值,PH值为10-14之间均可生产。
4.脱脂不彻底会有什么影响:
除油不净,易造成工件表面漆层脱落,结合力不牢,早期生锈,针孔气泡、麻面等不良。
5.安全措施:
操作中戴好相关劳保用品,严禁不相关之人员动用化学物品,如有不慎药水进入眼睛,立即用清水冲洗眼睛15分钟,误食者,用水漱口,
给予饮牛奶或蛋清,必要时送院治疗,避免工件掉落在槽内,如有必须捞出,以免压坏,经常打捞槽面油污和杂物。
前处理工艺槽液的日常管理

前处理工艺槽液的日常管理一、脱脂槽:1.开新槽,按每吨水添加脱脂粉50㎏,脱脂剂1﹪即达到游离碱度40点。
为了增加除油效果,减少除油时间,采用加温方法来提高脱脂速度。
槽液温度控制在60-70°C之间。
2.检测与添加,首先用试管吸入10ml槽夜放入锥形瓶中加入酚酞指示剂3-4滴,再用试管吸入0.1N HCL标准液滴定由红色变为无色时为终点,所消耗0.1N HCL标准液(ml)即为游离碱度。
添加方法:每吨槽液添加脱脂粉1.8㎏,游离碱会提高3度。
二、除锈槽:开新槽:按每吨水加31﹪的浓盐酸180㎏,即得18﹪的槽液浓度。
添加方法一般按坯件除锈效果作适量添加。
三、表调槽:新开槽按每吨水加入表调剂(胶肽)2㎏即达到PH值8。
日常管理:生产时防止酸性、碱性污染表调槽,影响表调效果。
PH值应保持在8-9,正常生产一段时间后应更换槽液。
四、磷化槽:新开槽按每吨水加入磷化剂60㎏,促进剂2㎏充分搅拌均匀,即符合规定的槽液。
日常管理,每天总酸度控制在25-35度之间,促进剂点数在1.5-3.0之间检测与添加。
总酸度:用试管吸入槽液10ml放入锥形瓶中加入酚酞指示剂3-4滴再用试管吸入0.1N NaOH标准液加入由无色变为红色时为止,所消耗NaOH溶液ml数即为总酸度。
促进剂:用发酵管装满磷化剂再加入1g左右发酵粉上下振动静止后发酵管所显示的即为促进剂点数。
当槽液总酸度低于规定值时,每吨槽液添加磷化液1.5升总酸度提高1度。
促进剂:低于规定值时按每吨槽液添加促进剂2.5㎏,度数上升1度。
日常每天1-2次磷化渣打捞。
五、水洗槽:生产时每道水洗槽保持溢流水,平时有计划的轮流清洗洗水槽。
脱脂后水洗槽PH值控制在7-8之间。
酸洗后的水洗槽PH值控制在6-7之间。
磷化后的水洗槽PH值控制在7。
六、按GB/T601-2002《化学试剂标准滴定溶液的制备》规定:量取9ml盐酸,注入1000ML水中,所得为0.1mol/l,因盐酸的当量浓度与摩尔浓度相同,也就是0.1N的盐酸了。
电泳槽液的管理

电泳槽液的管理无论是阳极电泳还是阴极电泳,电泳程序包括四个基本部分:前处理、电沉积、后冲洗和烘烤。
阴极电泳根据用途,可分为两类:一是以提高耐蚀性为目的的阴极电泳底层涂装。
它用于汽车、冰箱、洗衣机等壳体和相关零件。
二是以装饰为目的的阴极电泳涂装。
电泳工艺操作一般要注意如下内容:①系统准备(投槽);②前处理;③加料—树脂/颜料;④涂料循环;⑤冷却;⑥过滤;⑦超滤(UF);⑧后冲洗;⑨阳极液系统;⑩配电;11、烘烤;12、槽液转移及槽的清洗。
一、初次投槽初次投槽包括:涂装线及相关设施的检查与清洗、电泳槽的配槽、槽液的熟化及产品试涂装。
不同的阴极电泳涂料品种配槽程序虽有所不同,但其基本程序是:设备功能试验、设备清洗、配槽液、试涂装、正式投产。
设备功能试验又称冷调试。
当设备安装完后先从电气调试(输入软件)开始,检查泵、风机的电动机的转向,清扫环境和设备,分区加水打压试验,检查有无渗漏部位,并检查管路、过滤器等管路系统有无异物,如有问题立刻消除。
㈠涂装线相关设施的检查与清洗①清洗对象:电泳槽及槽内外的配管;置换槽及槽内外的配管;水洗槽、水洗室及有关设备;UF装置及有关设备;补给装置及有关设备;调温设备的循环设备;纯水供给设备及有关的设备和其他;运输设备和烘烤室也要擦洗净。
尤其是在能引起涂膜弊病的场合。
清除所有异物,如金属屑、油污、润滑油、纸等,并尽可能的做得彻底。
用高压自来水清洗杂质、泥砂等,碱性污物用涂料中和剂(如乳酸、醋酸)与水的质量比为1:100的溶液循环冲洗。
酸性污物用水与氨水的质量比为100:0.5的水溶液循环冲洗。
②操的管路系统、循环系统中的所有过滤器都必须清洗。
超滤管会滤芯应拆除,清洗循环仅在超滤单元回路中进行,清洗超滤单元用“空管”代替滤芯进行。
③用自来水或去离子水充满整个系统,其中每100kg水加7kg的弱碱(如氨水),清洗过程始终保证7%的浓度。
④在系统管路中,管(包括喷嘴)循环上述溶液至少16h,所有泵也用上述清洗液清洗,在清洗过程中应多次开关所有阀和设备。
前处理投槽操作指导

如果低于 40℃时喷淋,表面活性剂会产生泡沫。
检测方法:
将 10ml 槽液样品放入锥型瓶,加纯水至 50 ml;加入 3-5 滴酚酞指
示剂;使用 0.05 M H2SO4 滴定由红色变成无色,每消耗 1 ml 0.05 M H2SO4
相当于 1.0 游离碱点。
槽液的补充
每消耗 1 游离碱点加入 2 g/L Gardoclean 10037/2,加入 0.5g/L
Gardoclean H7354/1
南京凯密特尔表面技术有限公司
NANJING CHEMETALL SURFACE TECH. CO., LTD.
槽液更换: 2-4 个月(根据生产量及槽液含油量而定) 设备要求
· 配备槽液搅拌泵,使槽液循环达到 2-4 次/小时 · 油水分离装置 · 热水介质热交换装置 · 主脱脂槽→预脱脂槽能溢流 · 推荐采用专用过滤系统,脱脂槽底部有锥面,便于清除脏物。
1.预脱脂阶段:
作用:
脱脂,阶段 1(D1)
成分:
Gardolean 10037/2 +Gardoclean H7354/1
浓度
Gardoclean 10037/2
20g/L
+Gardoclean H7354/1
5g/L
温度:
45-55℃
总碱点:
10-20 点
喷淋压力:
0.1-0.2MPa
处理时间:
0.5min
配制过程(新槽液)
把容器排空,清洗后,加入自来水
加入 Gardoclean 10037/2 加热槽液,,等待温度达到 50℃,然后
打开喷淋
再加入表面活性剂 Gardoclean H7354/1
涂装前处理槽液检测作业规范

4.3.1.检测仪器及药品
10毫升刻度吸管、吸耳球、150毫升三角烧杯、滴瓶胶头、指示剂滴瓶、10毫升雀形弯管、酚酞指示剂、溴酚兰指示剂、0.1N NaOH标准溶液、氨基磺酸试剂
4.3.2.检测方法
4.3.2.1.总酸度测定方法:用刻度吸管取槽液10毫升于三角烧杯中,加酚酞指示剂3—4滴于槽液样品中并晃动均匀,用0.1N NaOH溶液滴定到混合溶液中,且均匀摇动使溶液由无色变为浅红色为止,所消耗液标准溶液的毫升数即为总酸度点数。滴定过程中,三角烧杯底部应匀速作画圆运动,使槽液与滴定液充分溶合。
4.3.2.2.游离酸测定方法:用刻度吸管取槽液10毫升于三角烧杯中,再加纯净水(自来水)40毫升至总液体50毫升,加入溴粉兰指示剂3—4滴于槽液样品中并晃动均匀,用0.1N NaOH溶液滴定至混合溶液从亮黄色变至浅紫色为止,所消耗标准溶液的毫升数即为游离酸点数。滴定过程中,三角烧杯底部应匀速作画圆运动,使槽液与滴定液充分溶合。
涂装前处理槽液检测作业规范(试行版)
1.目的
为了进一步规范公司涂装前处理检测人员正确检测前处理槽液,稳定前处理指标从而保证喷涂产品的质量,结合本公司实际情况制订本作业规范。
2.适用范围
本作业规范适用于公司涂装前处理各槽液的检测。
3.定义
(无)
4.前处理各槽液检测作业规范
.1主脱脂槽液的检测
4.1.1.检测仪器及药品
4.1.2.2.碱性PH值检测方法:取一张1—14广泛试纸一条浸入可测溶液中,半秒后取出与之标准色卡比较,所对应颜色的点色即为溶液的PH值;
.2表调槽液的检测
4.2.1.检测仪器及药品
1-14广泛试纸
4.2.2.检测方法
碱性PH值检测方法:取一张1—14广泛试纸一条浸入可测溶液中,半秒后取出与之标准色卡比较,所对应颜色的点色即为溶液的PH值。
前处理化验操作规程

1.目的:规范前处理化验操作及槽液日常维护,确保槽液在正常工艺范围内生产,保证产品质量。
2.适用范围:适用于喷涂前处理槽液化验和维护。
3.使用物品:仪器:锥形瓶、移液管、洗耳球、酸式滴定管、碱式滴定管、滴定架、发酵管药品:0.1N H2SO4、 0.1N NaOH 、氨基磺酸指示剂:溴酚兰、酚酞检测仪器:PH剂4.操作步骤:4.1 取液:用移液管分别取10ML脱脂液、酸洗液、磷化液分置于各锥形瓶中。
注:在取液前必须将各容器清洗干净,并把容器在相应的溶液中再清洗一次,避免在取液时容器中有残留水份稀释而检测不准。
4.2 滴加指示剂:在被检测总碱度或总酸度的脱脂液、酸洗液、磷化液中分别滴入3-4滴酚酞;在检测游离酸度的磷化液中滴加3-4滴溴酚兰;并轻摇均匀。
4. 3 化验操作要求a.在取操作液或标准液时,移液管和容器必须清洗干净b.操作时标准液需慢慢滴入并轻摇均匀,认真观察容器内操作液颜色变化c.在最终滴定读数时,眼睛应与滴定管内标准液下降所至的刻度保持水平状态,准确读出刻度数:如下图示标准液慢慢滴入并轻摇均匀水平目视下降刻度4.4. 滴定规范:a游离碱(脱脂槽):取10ML操作液,滴人3-4滴酚酞指示剂,用0.1N H2SO4标准液滴定,边滴边轻摇容器,接近终点时慢慢滴加,注意观察直到溶液由粉红色变为无色,30S不变色为滴定终值,所消耗的H2SO4标准液的毫升数为游离碱度。
如下图:由粉红色变为无色b总酸度(除锈槽):取1ML操作液,滴入3-4滴酚酞指示剂,用0.1N NaOH标准液滴定,边滴边轻摇容器,接近终点时慢慢滴加,注意观察直到溶液由无色变为橙色,30S不变色为滴定终值,所消耗的NaOH标准液的毫升数为总酸度。
如下图:由无色变为橙色c游离酸(磷化槽):取10ML操作液,滴入3-4滴溴酚蓝指示剂,用0.1N NaOH标准液滴定,边滴边轻摇容器,接近终点时慢慢滴加,注意观察直到溶液由浅蓝色变为蓝紫色,30S不变色为滴定终值,所消耗的NaOH标准液的毫升数为游离酸度。
前处理除油槽工艺要求
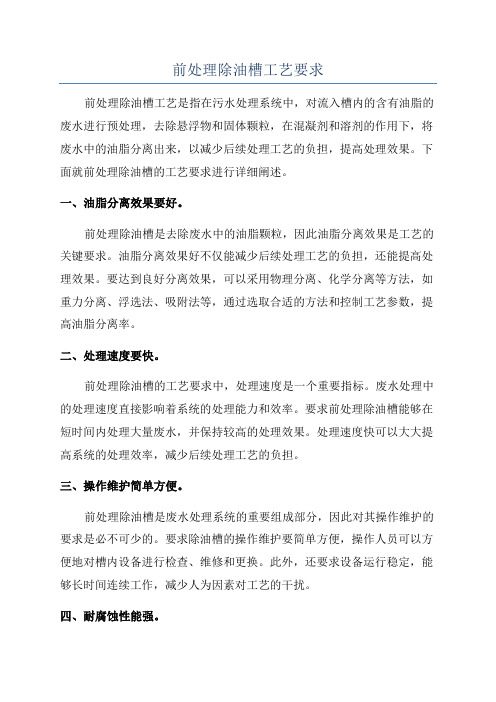
前处理除油槽工艺要求前处理除油槽工艺是指在污水处理系统中,对流入槽内的含有油脂的废水进行预处理,去除悬浮物和固体颗粒,在混凝剂和溶剂的作用下,将废水中的油脂分离出来,以减少后续处理工艺的负担,提高处理效果。
下面就前处理除油槽的工艺要求进行详细阐述。
一、油脂分离效果要好。
前处理除油槽是去除废水中的油脂颗粒,因此油脂分离效果是工艺的关键要求。
油脂分离效果好不仅能减少后续处理工艺的负担,还能提高处理效果。
要达到良好分离效果,可以采用物理分离、化学分离等方法,如重力分离、浮选法、吸附法等,通过选取合适的方法和控制工艺参数,提高油脂分离率。
二、处理速度要快。
前处理除油槽的工艺要求中,处理速度是一个重要指标。
废水处理中的处理速度直接影响着系统的处理能力和效率。
要求前处理除油槽能够在短时间内处理大量废水,并保持较高的处理效果。
处理速度快可以大大提高系统的处理效率,减少后续处理工艺的负担。
三、操作维护简单方便。
前处理除油槽是废水处理系统的重要组成部分,因此对其操作维护的要求是必不可少的。
要求除油槽的操作维护要简单方便,操作人员可以方便地对槽内设备进行检查、维修和更换。
此外,还要求设备运行稳定,能够长时间连续工作,减少人为因素对工艺的干扰。
四、耐腐蚀性能强。
废水中往往含有一定的酸碱等化学物质,因此对除油槽的材质要求具有较强的耐腐蚀性能。
选用耐腐蚀性能强的材质可以延长设备的使用寿命,减少维护和更换的频率,降低运行成本。
五、设备体积要小。
六、设备运行稳定可靠。
以上是前处理除油槽工艺的一些要求,包括油脂分离效果好、处理速度快、操作维护简单方便、耐腐蚀性能强、设备体积小、设备运行稳定可靠等。
只有在满足这些要求的前提下,才能保证前处理除油槽的正常运行和废水处理系统的高效运行。
- 1、下载文档前请自行甄别文档内容的完整性,平台不提供额外的编辑、内容补充、找答案等附加服务。
- 2、"仅部分预览"的文档,不可在线预览部分如存在完整性等问题,可反馈申请退款(可完整预览的文档不适用该条件!)。
- 3、如文档侵犯您的权益,请联系客服反馈,我们会尽快为您处理(人工客服工作时间:9:00-18:30)。
编写:
审核:
批准:
环城制品厂程序文件
文件编号:
文件名称
刮腻子(油灰)工作业要求及岗位职责
版号:A/0
分发日期:
页码:1/1
分发编号:
1、接到上级安排的生产指令,确认来料型号,数目是否符合要求,并
抽查质量,发现异常,向上级报告。确保信息及时反馈相关部采取
改善纠正措施。
2、根据待喷面的刮痕程度,调油灰(腻子)按原子灰和催硬剂比例100
引起刮伤,划痕的野蛮作业方法。
4、打磨至刮油灰边缘处形成毛絮状为适宜。
5、工件槽孔位及边缘处不允许有油灰渣应清除干净。
6、每批作业结束,记录完成工件数目,并作标识。
7、作业结束,下班前,清洁作业现场保持整齐干净。关闭电、气源。
编写:
审核:
批准:
环城制品厂程序文件
文件编号:
文件名称
手工研磨和保护作业要求及岗位职责
前检:要求:表面平整、光滑、无砂化。
编写
审核
批准
环城制品厂程序文件
文件编号:
文件名称
喷涂生产工艺操作规范
版号:A/0
分发日期:
页码:2/2
分发编号:
七:喷涂面漆:
要求:1、用压缩空气将表面灰尘杂物吹扫干净。
2、用手持喷枪将工作弯角内及研磨露底部补好。
3、油漆粘度按规度:18-23(涂4#杯)
4、漆膜厚度:20+2um
未磨平等现象,并仍有蔓延趋势,及时通知操作工及领班,采取防护措
施。
3.4.9对于喷粉件,在保护区域出现多余粉末时,应检查是否擦拭干净。
3.4.10发生异常情况时(如喷枪坏、风机燃烧炉坏,更换油漆)停线时间不
能超过3分钟,超过时则及时通知操作工开线,避免炉内喷好面漆工
件出现色差。
3.4.11交班时,烤炉内仍有大量喷好面漆工件,通知领导提前10分钟降温,
环城制品厂程序文件
文件编号:
文件名称
前处理液槽管理规范
版号:A/0
分发日期:
页码:1/3
分发编号:
一、予脱脂:浓度:30-35,时间10-15分钟
浓度测定、管理方法:
1、取工作液10ml,以酚酞作指示剂,用0.1NH2S4溶液滴定,使溶液从粉红色变至无色时消耗之毫升数为溶液的游碱度。
2、浓度尽量保持在基准范围内,如果低于基准点,加脱脂剂提高其浓度。
文件名称
喷涂生产工艺操作规范
版号:A/0
分发日期:
页码:1/2
分发编号:
一、磷化合格的工件上线:
要求:1、工件必须完全干燥。
3、磷化膜均匀致密,灰白色,无锈迹。
二、喷涂底漆:
要求:
A、先用压缩空气将表面灰尘杂物清理干净
B、油漆粘度18-23(涂4#杯)。
C、漆膜存度:15+2um
D、不露底,不流淌、无疙瘩。
分发日期:
页码:3/3
分发编号:
C、正常情况下磷化槽药液定期每1-2个月更换新液。
九、水洗:时间1-2分钟
A、清水保持每天溢流。
B、定期每周更换新清水。
一十、水洗:时间1-2分钟
A、清水保持每天溢流。
B、定期每3天更换清水。
一十一、烘烤
A、一般钢铁件:100℃-120℃,时间10-15分钟
B、铝材类:80℃-100℃,时间10-15分钟
三、除锈:浓度120-150,时间:10-15分钟。
测定、管理方法:
1、用比重器放入液槽中,所余之数为基数。
2、定期检测,正常情况3-5个月更换新液。
四、水洗:时间:1-2分钟
1、清水保持溢流。
2、定期每周更换清水。
编写
审核
批准
环城制品厂程序文件
文件编号:
文件名称
前处理液槽管理规范
版号:A/0
分发日期:
分发日期:
页码:1/1
3.2.2检查各水洗池是否干净,是否保持每天溢流,督促操作工定期更换清水。
3.2.3检查各溶液池的处理能力是否下降,督促车间添加药剂。
3.2.4检查磷化好的工件膜层颜色为浅灰色至深灰色,磷化膜必须连续、均匀、
致密、无疏松膜、无严重挂灰、手印、锈斑等。
3.2.5磷化后到喷涂时间间隔为24小时,超过24小时须重新磷化。
3、促进剂、将工作液装满发酵管内,再以指示剂(粉状)氨基磺酸2-5g添加摇动成气体,视其产生之气体量为基准值。
4、日常维持方法:
A、日常维持方法:
B、促进剂除生产性消耗剂,在液槽中有自耗特性。正常每天上班前由技术员检测、添加。
编写:
审核:
批准:
环城制品厂程序文件
文件编号:
文件名称
前处理液槽管理规范
版号:A/0
浓度检测、管理方法:
1、总酸度:取工作液10ml放入烧杯中加指示剂(PP)酚酞2-5滴并摇动,然后用0.1NNAOH氢氧化钠溶液滴定至粉红色,所消耗之数即为基准值勤。
2、游离酸:取工作液10ml放入烧杯中加指示剂B.P.B药3-5滴,摇动成黄色,然后用0.1NNAOH氢氧化钠溶液滴定至浅兰色,所滴定之消耗数即为基准值。
比2,搅拌均匀。
3、有生锈,油污的工件,退回上工序作返工处理。
4、填压刮痕,压痕等凹痕时,刮压方向应保持一致性。不允许多次交
叉刮拉作业。
5、刮压时,刮灰刀随着作业方向由大至小逐渐倾斜压进。
6、刮灰完毕工件,摆放在指定位置自然干燥十分钟以上,干燥后才可
整剂放置于料箱里或木架上。
7、工件要轻拿轻放,以免磕碰,刮伤或划伤表面,同时要去除槽孔上
3.2.6磷化后待喷工件须保持清洁、干燥、严禁赤手接触。
3.3刮灰、打磨
3.3.1检查刮灰前是否彻底清除此之外需补灰的金属表面锈迹、油渍、水份,
否则涂后在此部位容易起泡。
3.3.2原子灰主剂和硬化剂按重量比100:2比例混合搅匀,在10分钟内用完。
3.3.3检查刮灰处是否刮平、压紧,不允许留有气泡疏松灰。
2、固化:定期检测,采用纯酒精按规定的次数、力度擦磨表面,不
露底漆为合格。
4、附着力:刀片切片法:用小单面刀片在漆膜上横竖垂直切线四条
划痕至基体形成九个方块。方格边长为1毫米,用手指轻轻触摸,
方格脱落不超过2个以内为合格。或用粘贴法进行胶带试验。
编写:
审核:
批准:
环城制品厂程序文件
文件编号:文件名称来自编写:审核:批准:
环城制品厂程序文件
文件编号:
文件名称
喷涂车间制程检验作业指导
版号:A/0
分发日期:
页码:2/2
分发编号:
3.3.4刮灰工件必须待其彻底固化后才开始妍磨(20摄氏度约1小时固化)。
先用粗砂纸(260#)磨平,后用细砂纸(400#)磨光滑。
3.3.5通手手感、目测检查工件刮灰处平滑。沙粒浅划痕,流挂全部磨平好方
可转入喷涂。
3.4喷涂制程
3.4.1对照图纸了解上线待喷工件质量要求,表面处理代码,喷漆还是喷粉,
什么颜色,纹路是否洒点。
3.4.2检查待喷工件,应无油、无水、无尘、无锈,磷化膜均匀致密,表面光
滑平整。
3.4.3检查压缩空气净化情况应无油、无水、气压≥5kg/cm.
3.4.4监督检查油漆粘度高至规定粘度19-23秒;水帘无水花飞溅。
另外磷化后打钉还必须注意打钉后是否重新生锈和沾有油污等现象。
3.1.5焊接件检查是否有假焊、漏焊、焊穿、未焊透、未焊牢、焊缝未磨平、
残留焊渣、打磨太深、破坏折变圆弧等现象。
3.1.6对图纸要求不喷涂区域或表面,检验有无严重划碰伤或电解层氧化膜被
破坏现象。
3.2前处理
3.2.1监督和检查操作工是否按工艺流程进行前处理操作(附表)。
编写:
审核:
批准:
环城制品厂程序文件
文件编号:
文件名称
电动打磨工作业要求及岗位职责
版号:A/0
分发日期:
页码:1/1
分发编号:
1、根据生产安排,抽查待磨工件腻子的干燥程度及待喷表面未刮油灰
的缺陷。
2、针对工件刮油灰的厚薄,选择与之相适应的砂纸号数,合理使用砂
低。
3、作业过程中,所有工件应轻放,应避免乱扔、乱丢、导致相互磕碰,
接班时在低于规定温度5摄氏度内开始开线,防止色差。
3.4.12上线挂料时,温度速度相同或接近的工件应挂在一起,便于调整。
3.4.13终检时,对于出现在非正面的流挂、喷落、沙粒线划痕等通过修补可
以达到质量要求的,应作出标识,并隔离。
3.4.14对合格件须进行包装防护措施,并监督实施,防止在转运和交付时发
5、不允许局部堆积、流挂、气泡、麻点。
6、喷枪使用参照喷枪安全使用管理标准。
八:烘干:温度:150℃,时间9-12分钟。
要求:1、喷涂完成的工件经过十分钟时间流平。
2、温度与速度(时间)保持控制在标准的范围内。
九:检验:
要求:1、色差与样板一致,表面必须平整,光滑、无砂粒,无疙瘩,
无流淌、露底现象。
使角落和U型槽溶液排泄。
3、生产作业时,认真执行生产工艺要求。
4、每日定期测试药液配比浓度。并补添消耗成份;根据实际水质状况
定期更换清水。保证水质清澈。
5、前处理完成品,作标识并记录数目及完成时间,放置于待喷区。
6、坚持机器设备,前处理溶液槽、烤炉、工件筐的是常维护和保养工
作。
7、下班前作业结束时,坚持作业现场清洁工作并关好水电气开关。
3.1.1检查每一批来料是否有路线卡、工艺卡和零件图,三者缺一不可。
3.1.2对照路线卡和工艺卡检查是否属于正常转序,每道工序有无检验员签
字,发现有漏项未加工或无检验员签字,要及时反馈。