锻造技术的发展_从前8届国际塑性加工会议看锻造技术的发展
锻造行业发展现状及未来发展趋势

锻造行业发展现状及未来发展趋势一、行业发展现状锻造行业是制造业的重要组成部分,它在工业生产中起着至关重要的作用。
锻造是通过对金属材料施加力量,使其产生塑性变形,从而得到所需形状和性能的一种加工方法。
以下是锻造行业的发展现状:1. 锻造行业的规模不断扩大:随着工业化进程的加快,全球锻造行业的规模不断扩大。
根据统计数据,全球锻造行业的产值已经超过1000亿美元,并且还在稳步增长。
2. 技术水平不断提高:随着科技的进步,锻造技术也在不断创新和改进。
传统的手工锻造逐渐被自动化和智能化的锻造设备所取代,提高了生产效率和产品质量。
3. 锻造行业应用广泛:锻造行业广泛应用于汽车、航空航天、能源、冶金等领域。
特别是汽车行业的快速发展,对锻造行业提出了更高的要求。
4. 锻造行业的竞争激烈:由于市场需求的增加和技术进步的推动,锻造行业的竞争越来越激烈。
企业需要不断提高产品质量、降低成本,以保持竞争优势。
二、未来发展趋势1. 智能化生产将成为主流:随着人工智能和大数据技术的发展,智能化生产将成为锻造行业的未来发展趋势。
通过引入智能设备和自动化系统,可以提高生产效率和产品质量。
2. 绿色制造将受到重视:环保和可持续发展已经成为全球关注的焦点,锻造行业也不例外。
未来,锻造企业将更加注重减少能源消耗、降低废物排放,采用环保材料和工艺,实现绿色制造。
3. 个性化定制将成为新趋势:随着消费者需求的多样化,个性化定制将成为锻造行业的新趋势。
企业需要根据客户的需求,提供定制化的产品和服务,以满足不同消费者的需求。
4. 3D打印技术的应用:3D打印技术在制造业中的应用越来越广泛,锻造行业也不例外。
通过3D打印技术,可以实现复杂形状和结构的锻件制造,提高生产效率和产品质量。
5. 国际合作将加强:随着全球化的推进,锻造行业的国际合作将更加紧密。
企业之间将加强技术交流和合作,共同应对市场竞争和挑战。
总结:锻造行业作为制造业的重要组成部分,其发展前景广阔。
锻造行业发展现状及未来发展趋势

锻造行业发展现状及未来发展趋势概述:锻造行业是创造业中的重要组成部份,其作用不仅体现在工业领域,还广泛应用于汽车、航空航天、能源等领域。
本文将对锻造行业的现状进行分析,并探讨未来的发展趋势。
一、锻造行业的现状1. 锻造行业的基本概况锻造是一种通过对金属材料进行塑性变形来改变其形状和性能的加工方法。
锻造行业主要包括冷锻、热锻和温锻等多种工艺。
目前,锻造行业在全球范围内得到广泛应用,其市场规模不断扩大。
2. 锻造行业的发展历程锻造行业起源于古代,经历了手工锻造、水力锻造、蒸汽锻造等多个阶段的发展。
随着科技的进步和机械化程度的提高,锻造行业的生产效率和质量得到了显著提升。
3. 锻造行业的市场规模目前,全球锻造行业的市场规模呈现稳步增长的趋势。
据统计,2022年全球锻造行业的市场规模达到了X亿美元,估计到2025年将达到X亿美元。
4. 锻造行业的应用领域锻造行业广泛应用于汽车、航空航天、能源、石油化工等领域。
在汽车行业中,锻造件被广泛应用于发动机、底盘、传动系统等关键部件。
在航空航天领域,锻造件在发动机、机身结构等方面发挥着重要作用。
二、锻造行业的未来发展趋势1. 技术创新推动行业发展随着科技的不断进步,锻造行业也在不断进行技术创新。
例如,3D打印技术的应用使得锻造件的创造更加灵便和高效。
此外,智能创造技术的发展也将进一步提升锻造行业的生产效率和质量。
2. 环保意识促使行业转型升级在全球环保意识的提升下,锻造行业将面临转型升级的压力。
传统的锻造工艺产生大量废气、废水和废渣,对环境造成为了一定的污染。
因此,锻造行业需要加强环保技术的研发和应用,减少对环境的影响。
3. 自动化生产成为发展趋势随着自动化技术的发展,自动化生产将成为锻造行业的发展趋势。
自动化生产可以提高生产效率、降低人工成本,并且能够保证产品的一致性和质量稳定性。
因此,锻造企业需要加大对自动化设备的投入,提高生产线的智能化水平。
4. 智能创造助力行业升级智能创造是未来锻造行业升级的重要方向。
锻造行业发展现状及未来发展趋势

锻造行业发展现状及未来发展趋势一、引言锻造行业作为金属加工行业的重要组成部分,具有广泛的应用领域和巨大的市场潜力。
本文将详细介绍锻造行业的发展现状,并展望未来的发展趋势。
二、锻造行业发展现状1. 锻造行业的定义和范围锻造是指通过对金属材料进行加热、塑性变形和冷却等工艺,使其形成所需形状和性能的工艺过程。
锻造行业涵盖了锻造设备制造、锻造工艺研究、锻造模具制造和锻造产品制造等多个领域。
2. 锻造行业的市场规模目前,全球锻造行业市场规模约为5000亿美元,年均增长率约为3%。
中国是全球最大的锻造产品生产国家,占据了全球市场的30%以上份额。
3. 锻造行业的发展状况(1)技术水平不断提升:随着科技的进步和创新,锻造工艺和设备得到了迅速发展。
液压锻造、电磁锻造、高能锻造等新技术的应用,使得锻造工艺更加精确、高效和环保。
(2)产品结构优化升级:锻造产品在汽车、航空航天、能源等领域得到广泛应用。
高强度、轻量化、高温耐受等特性成为市场需求的主要方向。
(3)市场竞争加剧:随着锻造行业市场规模的扩大,国内外企业纷纷进入市场,竞争日益激烈。
企业需要加强技术创新、提高产品质量和降低成本,以保持竞争力。
三、锻造行业未来发展趋势1. 智能化生产随着人工智能、大数据和物联网技术的快速发展,智能化生产将成为锻造行业的主要趋势。
通过智能化设备和系统,实现生产过程的自动化、信息化和智能化,提高生产效率和产品质量。
2. 绿色制造环保和可持续发展已成为全球关注的重要议题。
锻造行业需要采用清洁能源、节能减排的技术和工艺,减少对环境的影响。
同时,回收利用废弃物料和能源也是未来发展的重要方向。
3. 个性化定制随着市场需求的多样化和个性化,锻造行业需要提供更加灵活、定制化的产品和服务。
通过数字化技术和柔性生产方式,实现产品的快速设计和生产,满足客户个性化需求。
4. 国际合作与市场拓展随着全球经济一体化的深入发展,锻造行业需要加强国际合作,开拓国际市场。
锻造实训题库及答案解析

锻造实训题库及答案解析一、单项选择题1. 锻造过程中,金属材料的塑性变形主要发生在()。
A. 初始阶段B. 中间阶段C. 终了阶段D. 全过程答案:B2. 锻造工艺中,为了提高金属的塑性,通常采用()。
A. 降低温度B. 提高温度C. 保持室温D. 交替温度答案:B3. 在锻造过程中,金属材料的变形抗力随着温度的升高而()。
A. 增加B. 减少C. 不变D. 先增加后减少答案:B4. 下列哪项不是锻造的基本工序之一?A. 镦粗B. 拔长C. 切割D. 冲孔答案:C5. 锻造过程中,金属材料的变形量通常用()来表示。
A. 长度B. 宽度C. 厚度D. 真应变答案:D二、多项选择题6. 锻造工艺中,常用的加热设备包括()。
A. 电炉B. 燃气炉C. 感应炉D. 空气炉答案:A, B, C7. 锻造中,金属材料的塑性变形可以通过()来实现。
A. 压力B. 温度C. 速度D. 化学成分答案:A, B8. 锻造过程中,金属材料的变形抗力受哪些因素影响?A. 材料的化学成分B. 材料的初始温度C. 变形速度D. 变形程度答案:A, B, C, D三、判断题9. 锻造过程中,金属材料的塑性变形总是伴随着硬度的增加。
()答案:正确10. 锻造过程中,金属材料的塑性变形可以通过增加变形速度来实现。
()答案:错误四、简答题11. 简述锻造工艺中常见的几种锻造方法及其特点。
答案:锻造工艺中常见的锻造方法包括自由锻造、模锻、锤锻和压力机锻造。
自由锻造适用于形状简单的零件,操作灵活;模锻适用于形状复杂、精度要求高的零件,生产效率高;锤锻适用于中小批量生产,设备简单;压力机锻造适用于大批量生产,精度高,生产效率高。
五、计算题12. 若某金属材料在锻造过程中的真应变为2,求其变形量。
答案:真应变定义为ε = ln(Lf/Li),其中Lf为最终长度,Li为初始长度。
当ε=2时,Lf = Li * e^2。
变形量为Lf - Li,即Li* (e^2 - 1)。
锻造工艺学(完整版)

家的工业水平。
Seite 20
二、锻件生产的分类及其工艺流程
根据所用工具和生产工艺的不同可分为自由锻造、模锻和特 种锻造。
1.自由锻造 把加热好的坯料放在自由锻造设备的平砧之间 或简单的工具中进行锻造的方法称为自由锻。
一般由锻工控制金属的变形方向和形状尺寸。
手工锻造
Seite 23
自由锻还可以借助简单的模具进行锻造,称 胎模锻。
胎模锻造是把加热好的坯料用自由锻方法预 锻成近似锻件的形状,然后在自由锻设备上用胎 模终锻成形(形状简单的锻件可直接把坯料放入 胎模内成形),这种锻造方法称为胎模锻造。
Seite 24
2.模锻 把加热好的坯料放在固定于模锻设备上的 模具内进行锻造的方法称为模锻。
这些缺陷的形成与冶炼、浇注和结晶过 程紧密相关,并且不可避免。
Seite 48
⑴偏析 包括枝晶偏析(指钢锭在晶体范围内化学 成分的不均匀性)和区域偏析(钢锭在宏观范围 内的不均匀性)
造成力学性能不均匀和裂纹缺陷。枝晶偏析现
象可以通过锻造、再结晶、高温扩散和锻后热处
理得到消除。区域偏析只有通过反复镦—拔变形工
Seite 38
4) 提高锻件的内在质量。 5) 提高机械化、自动化水平。 6) 发展以煤气、油、电等为热源的先进加热 技术,改善劳动条件。
Seite 39
(三)目前,我国锻造业面临的问题可以归纳 为如下
装备水平低,其主要表现是设备老化、精确度低 管理体制亟待理顺,生产厂点过多,力量分散 厂家封闭式经营 研究和生产不平衡
2) 高产 指机械化生产,生产率高
二、三百件/小时,现在更高了,一百多件/分, 1.2万件/小时。据统计,每模锻100万吨钢,由于提高 了生产率,可比切削加工减少2~3万工人,少用15000 台机床。在现今技术水平条件下,几乎任何一种金属 材料都可用锻造方法制成半成品零件,只是难易程度 不同而已。
锻压技术的发展趋势

锻压技术的发展趋势Development trends of forging technol摘要:工业生产的发展和科学技术的进步,为锻压技术的发展提供了广阔的空间。
随着许多新技术、新工艺的迅猛发展和计算机的广泛使用,锻压技术必定有长足发展。
本文将在锻压配置自动化,高速化复合化相和配置控制体系几个方面综述锻压技术的发展趋势Abstract: the development of industrial production and the progress of science and technology, for forging technology has provided a broad space for development. As with many new technology, new technology rapid development and the widespread use of computers, there must be a great development of forging technology. This article will in forging configuration of mechanized, large-scale press and die technology growth aspects of forging technology development trend关键词:自动化、高速化、控制、环保Key words: automatic, high-speed, control, environmental protection毫无疑问,现代锻压生产的发展趋势:提高锻件的性能和质量,实现少、无切屑加工和污染,做到清洁生产。
利用IT技术,发展高柔性和高效率的自动化锻压设备,提高零件的生产效率,降低生产成本提高生产率是永恒的追求目标,现代的大型锻造车间的锻造液压机、操作机、锻造吊车实现率联动控制,全部机械化,并配有短件尺寸自动测量装置,锻造液压机与操作机数控联动,锻造机加热炉自动控制。
铸造的发展与摘要(汉语+英语)

The Development and Summary of Casting铸造的发展与摘要Casting is one of the oldest of all industries, both ancient and medieval history offering examples of the manufacture and use of casting. From simple axeheads poured from copper in open moulds some 5000 years age, casting in the pre-Christian world developed to a point at which elaborate bronze statuary could be produced in two-piece and cored moulds. By the end of the medieval period, decorated bronze and pewter casting had begun to be used in European church and domestic life.金属铸造是最古老的产业之一,远古时期和中世纪就有人使用和制造铸件了。
5000年前人们只能用铜在开式模具中浇注简单的斧头,二公元前已经能够用分体式模具和型芯制造复杂的青铜雕塑了。
中世纪末期,欧洲的交通那个和家庭开始使用青铜和锡铅合金铸件制造器皿进行装饰。
The widespread adoption of cast iron as engineering material awaited the success of Abraham Darby in 1790 in smelting in the coke blast furnace; this paved the way for the massive use of cast iron in construction during the years following the industrial revolution.工程材料广泛只用铸铁得益于1709年希伯来用鼓风炼焦炉融化金属,这为工业革命时期在建设中大量使用铸铁铺平了带路。
制造技术的发展历程

制造技术的发展历程制造技术的发展历程可以追溯到人类最早的文明时期。
在这个过程中,制造技术得到了持续改进和创新,随着时间的推移越来越成熟。
这一发展历程可以概括为以下几个阶段:1. 手工制造阶段:在人类的早期,所有产品都是通过手工劳动制作的。
这个时期的制造技术主要依赖于人力和简单的工具,生产规模有限,效率较低。
2. 工艺制造阶段:随着社会的进步和文明的发展,人们开始探索并发展了一些基本的工艺制造技术。
这个时期的制造过程已经引入了一些机械设备和工艺流程,如铁器制作、纺织工艺等。
这使得制造效率有所提升,并且产品质量也有了一定的保证。
3. 机械制造阶段:随着机械和工业革命的到来,制造技术迎来了一次巨大的变革。
使用蒸汽机、水力机器和机械化生产线等机械设备,大大提高了生产力和制造效率。
例如,蒸汽机的出现使得纺织行业从手工制造转变为机械化的大规模制造。
这个阶段的制造技术也为现代工业的发展奠定了基础。
4. 自动化制造阶段:随着电力、电子技术和计算机技术的发展,制造技术进一步实现了自动化和智能化。
各种自动化设备和控制系统被广泛应用于生产过程中,实现了生产线的自动化、产品质量的提高和生产效率的大幅度提升。
例如,计算机数控机床、机器人等的出现,使得制造过程更加高效、精确,并且可以实现更加灵活的生产。
5. 数字化制造阶段:随着信息技术的迅速发展,制造技术进入了数字化时代。
数字化制造采用了大数据、云计算、物联网和人工智能等先进技术,实现了生产过程的全面数字化和智能化。
生产数据的实时监测和分析,使得制造过程更加可控、高效,并且可以实现精细化生产。
总结起来,制造技术的发展经历了从手工制造到工艺制造、机械制造、自动化制造和数字化制造等阶段。
每个阶段的技术进步都为制造业的发展做出了重要贡献,推动了生产效率和产品质量的不断提升。
随着科技的不断创新,制造技术也将继续发展,为我们的生活和经济发展带来更多的机遇和挑战。
锻造行业发展现状及未来发展趋势

锻造行业发展现状及未来发展趋势一、引言锻造行业是创造业中的重要环节,其发展对于国家经济和工业的发展具有重要意义。
本文将对锻造行业的发展现状进行分析,并展望未来的发展趋势。
二、锻造行业发展现状1. 锻造行业的定义和范围锻造行业是指通过对金属材料进行加热、塑性变形和冷却等工艺,将其加工成所需形状和尺寸的工艺过程。
锻造行业包括冷锻和热锻两种方式。
2. 锻造行业的发展历程锻造行业起源于古代,经过几千年的发展,逐渐形成为了现代锻造技术体系。
在过去的几十年中,随着科技的进步和工业化的发展,锻造行业得到了快速发展。
3. 锻造行业的发展现状目前,全球锻造行业已经成为创造业中的重要组成部份。
中国是全球最大的锻造生产国家之一,锻造行业在国内经济中占领重要地位。
锻造企业数量众多,技术水平也在不断提高。
4. 锻造行业的市场需求随着工业化进程的加快,对于锻造产品的需求也在不断增长。
锻造产品广泛应用于汽车、航空航天、军工等领域,市场需求潜力巨大。
5. 锻造行业的技术发展随着科技的不断进步,锻造行业也在不断引入新的技术和设备。
数控锻造、自动化生产线等先进技术的应用,提高了锻造产品的质量和生产效率。
三、锻造行业未来发展趋势1. 智能化生产随着人工智能技术的发展,智能化生产将成为锻造行业的重要趋势。
通过引入机器人和自动化设备,可以提高生产效率和产品质量。
2. 绿色环保在全球环境保护意识的提高下,锻造行业也将朝着绿色环保方向发展。
减少能源消耗、降低废气废水排放,将成为锻造企业的重要任务。
3. 高端产品创造随着科技的进步和市场需求的变化,锻造行业将更加注重高端产品的创造。
高强度、耐磨、耐高温等特殊材料的锻造将成为发展的重点。
4. 国际合作与竞争随着全球化进程的不断推进,锻造行业将面临更加激烈的国际竞争。
加强国际合作,提高自身竞争力,将是锻造企业未来发展的关键。
5. 人材培养与技术创新锻造行业需要大量的技术人材,人材培养和技术创新将成为行业发展的重要支撑。
铝合金锻造生产技术的发展
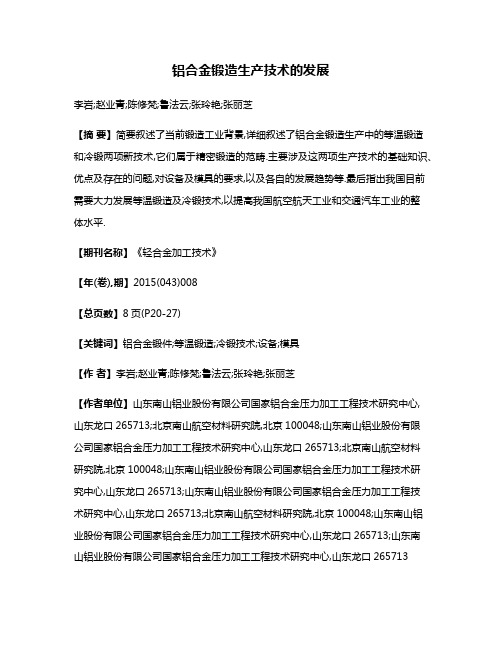
铝合金锻造生产技术的发展李岩;赵业青;陈修梵;鲁法云;张玲艳;张丽芝【摘要】简要叙述了当前锻造工业背景,详细叙述了铝合金锻造生产中的等温锻造和冷锻两项新技术,它们属于精密锻造的范畴.主要涉及这两项生产技术的基础知识、优点及存在的问题,对设备及模具的要求,以及各自的发展趋势等.最后指出我国目前需要大力发展等温锻造及冷锻技术,以提高我国航空航天工业和交通汽车工业的整体水平.【期刊名称】《轻合金加工技术》【年(卷),期】2015(043)008【总页数】8页(P20-27)【关键词】铝合金锻件;等温锻造;冷锻技术;设备;模具【作者】李岩;赵业青;陈修梵;鲁法云;张玲艳;张丽芝【作者单位】山东南山铝业股份有限公司国家铝合金压力加工工程技术研究中心,山东龙口265713;北京南山航空材料研究院,北京100048;山东南山铝业股份有限公司国家铝合金压力加工工程技术研究中心,山东龙口265713;北京南山航空材料研究院,北京100048;山东南山铝业股份有限公司国家铝合金压力加工工程技术研究中心,山东龙口265713;山东南山铝业股份有限公司国家铝合金压力加工工程技术研究中心,山东龙口265713;北京南山航空材料研究院,北京100048;山东南山铝业股份有限公司国家铝合金压力加工工程技术研究中心,山东龙口265713;山东南山铝业股份有限公司国家铝合金压力加工工程技术研究中心,山东龙口265713【正文语种】中文【中图分类】TG319锻造生产不但能获得精密的机械零件,而且能改善其内部组织并提高力学性能,是向各个工业行业提供机械零件的主要途径之一。
对于力学性能要求高、承受力大的重要机械零件,多数采用锻造方法来制造。
在飞机上锻压件的重量占80%,坦克上锻压件重量占70%,汽车上锻压件重量占60%,电力工业中的水轮机主轴、透平叶轮、转子、护环等也都通过锻压而成,锻造生产在工业制造业中占有极重要的地位[1]。
本文重点介绍两种铝合金锻造生产新技术,多用于航空航天产品锻造生产的等温锻造技术与常用于交通汽车工业用产品的冷锻技术及冷锻-温锻联合成形技术。
锻造技术的发展现状及趋势
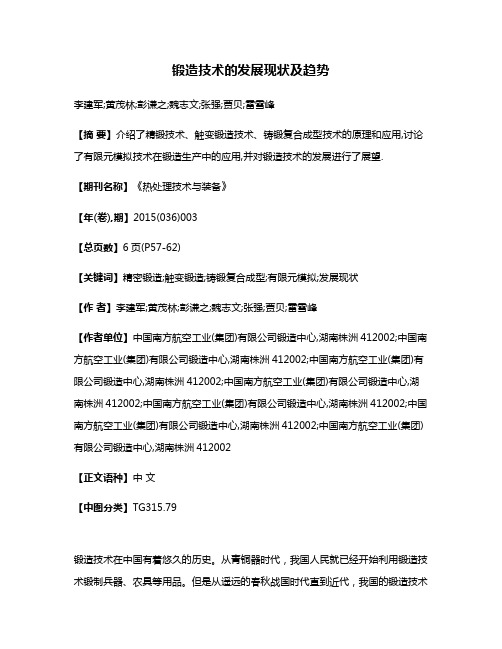
锻造技术的发展现状及趋势李建军;黄茂林;彭谦之;魏志文;张强;贾贝;雷雪峰【摘要】介绍了精锻技术、触变锻造技术、铸锻复合成型技术的原理和应用,讨论了有限元模拟技术在锻造生产中的应用,并对锻造技术的发展进行了展望.【期刊名称】《热处理技术与装备》【年(卷),期】2015(036)003【总页数】6页(P57-62)【关键词】精密锻造;触变锻造;铸锻复合成型;有限元模拟;发展现状【作者】李建军;黄茂林;彭谦之;魏志文;张强;贾贝;雷雪峰【作者单位】中国南方航空工业(集团)有限公司锻造中心,湖南株洲412002;中国南方航空工业(集团)有限公司锻造中心,湖南株洲412002;中国南方航空工业(集团)有限公司锻造中心,湖南株洲412002;中国南方航空工业(集团)有限公司锻造中心,湖南株洲412002;中国南方航空工业(集团)有限公司锻造中心,湖南株洲412002;中国南方航空工业(集团)有限公司锻造中心,湖南株洲412002;中国南方航空工业(集团)有限公司锻造中心,湖南株洲412002【正文语种】中文【中图分类】TG315.79锻造技术在中国有着悠久的历史。
从青铜器时代,我国人民就已经开始利用锻造技术锻制兵器、农具等用品。
但是从遥远的春秋战国时代直到近代,我国的锻造技术一直处于手工作坊生产的状态,锻造工艺也以手工自由锻为主。
直到二战结束和新中国成立之后,才利用从日军手里缴获的锻造设备和苏联援建的一些锻造设备建立起我国的现代锻造工业。
目前科技发展日新月异,锻造技术也取得了长足的进步。
本文综述了锻造工艺的发展现状,分别讨论精锻技术、触变锻造技术、铸锻复合成形技术的特点及其应用,分析了有限元法在锻造生产中应用,并对今后锻造技术的发展方向进行了展望,希望能给读者以有益的启示。
1 锻造工艺的发展现状1.1 精密锻造技术1.1.1 传统精锻技术精密锻造是指零件锻造成形后,只需少量加工或不再加工即符合零件尺寸精度要求的成形技术。
锻造操作机设计

目 录
摘要:.....................................................................1 关键词.....................................................................1 Abstract................................................................... 1
4.1 升降机构............................................................. 6 4.2 转轴滑块机构.......................................................... 6 4.3 平衡装置.............................................................. 7 4.4 5 缓冲装置............................................................. 7 夹紧机械手设计......................................................... 8
铝合金等温锻造技术的发展

3 .国外铝合金等温锻造的进展
16 ,美 国国际商务机器公 司开始 用等温锻造成 94年
小 ,可等温模 压出形状 复杂 的且 满足尺寸精度 要求的纵 向摇臂 ,避免 了锻件 的外表 面和 内部 的冶金缺陷 ,质量
当时达到或超过法 国锻件的技术要求。
形零件 ,在 2 世纪 7 0 0年代就使用 特种等温锻 造设备和
锻件 的微观组织和综合性能具有 良好的均匀性 和一致性。
( ) 显著提高金属材料 的塑性 ,毛坯
() 由于减少或消除了模 具激冷 和材 料应变硬化 的 3
影响 ,不仅锻造载荷 小,设 备吨位 大大降低 ,而且还有 助于简 化成形过程 ,因此 可以锻造出形状 复杂 的大型结
形方法。在较 高温度条 件下 ,锻件 以较 低的应 变速率变 形 ,因此变形 材料能够充 分再结 晶,从 而可 以大 部分或
全 部 克 服 加工 硬 化 的影 响 。
所示为某型号直升飞机的铝合金 简式绝缘套 。每辆空 中
客车上使用了 10 厚铝板 ,大多数巡航导 弹的壳体是用 8t
优质铝合金铸锻 件制造的。 目前 ,铝材 在 民用 飞机 结构
合金 发 生 过 烧 ,在 3 0~40 、应 变 速 率 0 05~ 9 5% .0 00 s 范围内变形较为合适。低应变速率变形 时 , . 5 发生
高温合金 及飞机用大型结构锻件的精密设备和先进技 术。
8 0年代初期 ,前苏联 系列生产 了等 温锻造专用 液压 机, 如 20 、60 、10 t 4 0 t 5 t 3 t 60 和 0 0 液压机 。这些设 备均 安装 在现俄罗斯有关厂所 院校 ,进行 铝合金叶 片、飞机 结构 件和粉末高温合金 涡轮盘等零件的等温锻造研究 和应用 。 9 O年代 ,美 国相继开发了 50 t 1 0 t 00 和 00 0 的液压机 ( 当 时世界上最大的等温锻造液压机 ,如图 2所示) 。
金属锻造技术的创新与发展

金属锻造技术的创新与发展金属锻造技术是一种历史悠久的技术,也是现代制造业的重要组成部分。
在未来,随着科技的不断进步和人们对高性能和低成本制造业的需求的增加,金属锻造技术将继续得到发展和创新。
一、金属锻造技术的概述金属锻造技术是将金属加工成所需形状和尺寸的一种加工工艺。
它可以在热态或冷态下进行,适用于各种金属和合金。
在金属锻造过程中,所使用的金属材料会被加热到过于硬化但又没有熔化的温度,然后被锤或压成所需形状和尺寸。
锻造工艺可以用于生产各种各样的金属零部件,例如发动机曲轴、连接杆、轴承、齿轮和各种结构零件。
由于它可以通过改变锤头的速度和力来调整金属材料的性质,所以在金属锻造过程中还可以通过处理来改变金属材料的强度、韧性和可塑性等性质。
二、金属锻造技术的发展历程金属锻造技术可以追溯到古代的青铜时代,当时人们就使用锤炼的方法来加工铜、锡和黄铜等金属材料。
随着炼铁技术的进步,和铁制品需要获得更高的强度和韧性的需求,人们开始使用锻造技术生产铁制品。
在18世纪初期,金属锻造技术得到了革命性的发展,当时发明了蒸汽动力锤和压力锻机,这些设备使得金属锻造工艺变得更加高效和精确。
到19世纪和20世纪初期,汽车、铁路和军事工业带动了金属锻造技术的快速发展和创新,如推出了电力锻压机和挤压机。
随着计算机控制技术的发展,金属锻造技术又迎来了新一轮的革命。
现代计算机辅助设计、计算机数控机床和快速成型等技术手段对金属锻造工艺进行了深入的探究和应用,并在锻造工艺中涌现出了新技术、新材料、新设备。
三、金属锻造技术的新技术和发展趋势随着通讯、航天、能源等领域的持续发展和庞大的市场需求,金属锻造技术更需要在质量、效率、创新和可持续性方面实现变革和革新。
当前,金属锻造技术的新技术和发展趋势主要包括以下几个方面:1. 精密锻造技术传统的锻造技术难以满足人们对精度、一致性和重量的高要求。
高精度锻造技术是国内外金属锻造技术的热门研究方向。
现代精密锻造技术具有以下特点:高成形精度;较小的误差范围;小型、高速、高效和节能等。
机械锻造技术的发展与核心要义解析
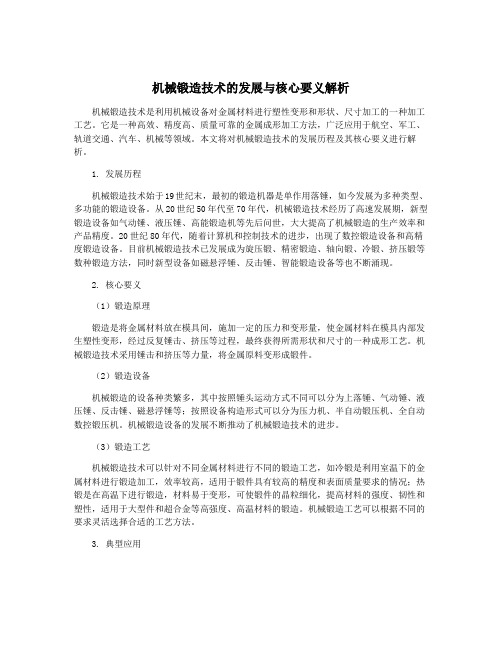
机械锻造技术的发展与核心要义解析机械锻造技术是利用机械设备对金属材料进行塑性变形和形状、尺寸加工的一种加工工艺。
它是一种高效、精度高、质量可靠的金属成形加工方法,广泛应用于航空、军工、轨道交通、汽车、机械等领域。
本文将对机械锻造技术的发展历程及其核心要义进行解析。
1. 发展历程机械锻造技术始于19世纪末,最初的锻造机器是单作用落锤,如今发展为多种类型、多功能的锻造设备。
从20世纪50年代至70年代,机械锻造技术经历了高速发展期,新型锻造设备如气动锤、液压锤、高能锻造机等先后问世,大大提高了机械锻造的生产效率和产品精度。
20世纪80年代,随着计算机和控制技术的进步,出现了数控锻造设备和高精度锻造设备。
目前机械锻造技术已发展成为旋压锻、精密锻造、轴向锻、冷锻、挤压锻等数种锻造方法,同时新型设备如磁悬浮锤、反击锤、智能锻造设备等也不断涌现。
2. 核心要义(1)锻造原理锻造是将金属材料放在模具间,施加一定的压力和变形量,使金属材料在模具内部发生塑性变形,经过反复锤击、挤压等过程,最终获得所需形状和尺寸的一种成形工艺。
机械锻造技术采用锤击和挤压等力量,将金属原料变形成锻件。
(2)锻造设备机械锻造的设备种类繁多,其中按照锤头运动方式不同可以分为上落锤、气动锤、液压锤、反击锤、磁悬浮锤等;按照设备构造形式可以分为压力机、半自动锻压机、全自动数控锻压机。
机械锻造设备的发展不断推动了机械锻造技术的进步。
(3)锻造工艺机械锻造技术可以针对不同金属材料进行不同的锻造工艺,如冷锻是利用室温下的金属材料进行锻造加工,效率较高,适用于锻件具有较高的精度和表面质量要求的情况;热锻是在高温下进行锻造,材料易于变形,可使锻件的晶粒细化,提高材料的强度、韧性和塑性,适用于大型件和超合金等高强度、高温材料的锻造。
机械锻造工艺可以根据不同的要求灵活选择合适的工艺方法。
3. 典型应用。
热锻工艺工艺的发展历程

热锻工艺工艺的发展历程热锻工艺是一种常用的金属成形工艺,通过利用金属在高温条件下的可塑性,使其在模具中受到压力作用,从而得到所需的形状和尺寸。
热锻工艺的发展经历了多个阶段,不断得到改进和创新。
热锻工艺最早可以追溯到公元前3000年左右的古代埃及。
当时,人们已经发明了冶炼和锻造铜制品的技术,通过高温加热和人工敲打,锤炼出所需的形状。
这种简单的热锻工艺为后来的发展奠定了基础。
随着冶金技术和设备的不断改进,热锻工艺开始进一步发展。
在公元前14世纪的古代希腊和罗马时期,人们开始使用燃烧木炭的炉子进行高温加热,使金属在较高温度下变得更加可塑,从而实现更复杂的锻造工艺。
到了18世纪,随着工业革命的到来,热锻工艺得到了进一步改进。
人们发明了蒸汽锤,利用蒸汽的压力和能量来驱动锻造锤头的运动。
这种新型的锤具不仅减轻了工人的劳动强度,也提高了生产效率和锻造质量。
20世纪初,热锻工艺开始应用于更多领域。
特别是在第一次世界大战和第二次世界大战期间,热锻工艺在军事工业中得到了广泛应用,其中包括航空航天、汽车、武器装备等领域。
为适应不同材料的高温塑性和机械性能要求,人们开始研究并发展多种热锻方法和工艺参数。
在20世纪中叶,随着科学技术的发展和计算机控制技术的应用,热锻工艺迎来了新的提升。
自动化、智能化的锻造设备开始使用,实现了更高的锻造速度和精度。
数值模拟技术的引入,使热锻工艺的优化和仿真变得更加容易。
随着21世纪的到来,热锻工艺进一步发展。
新型材料的出现和应用,为热锻工艺提出了新的挑战和机遇。
高强度和高温材料的锻造要求更高的工艺控制和设备性能。
非常规形状的零部件和微小零件的锻造也成为研究热点。
目前,人们在热锻工艺方面的研究主要集中在以下几个方面:1. 材料研究:通过改变材料的成分和热处理工艺,改善材料的塑性和强度,以适应不同的热锻工艺需求。
2. 设备研发:研制更高效、更精密的热锻设备,提高锻造速度和质量。
包括锻造机床、模具和加热装置等。
中国铸造简史及发展简介

B.战国时期的曾侯乙编钟
编钟的出土震惊了中国,震惊了世界,举世瞩目, 被誉为 “世界奇观中独一 无二的珍宝”,“古代世界的第八奇迹”, 是“精神世界的圣山”, 曾侯乙 编钟是我国目前出土数量最多、重量最重、音律最全、气势最宏伟的一套 编钟,堪称『编钟王』。凡有机会耳闻目睹过的人,无不为此千古绝响, 惊 叹叫绝,赞誉它不愧是中华民族文化艺术之瑰宝,世界音乐史之奇迹。是 中国古老优秀文明的象征,是我国文物考古、音乐史和冶铸史上的空前重 大发现。
一、中国古代铸造的发展简史
• 我国的铸造技术已有6000年的悠久历史,是世界上最早掌握 铸造工艺的文明古国之一。
• 我国商朝(公元前1600年——公元前1046年)起就己创造了 灿烂的青铜文化,所谓“钟鸣鼎食”,成了当时贵 族权势和地 位的标志。
• 在河北省兴隆县的古燕国铸冶作坊遗址的发掘中,发现距今 2200~ 2350年的战国时期的铁范 (铁质铸型)等87件,说明早在 战国时期,铸铁件在我国已广泛应用了。
出自战国时期的秦国。由3462个铸件组成,总重量达1241公斤
在汉代,铸造技术进一步提高。从唐宋时期起, 我国在用泥范铸造大型和特大型铸件方面,取得了令 人瞩目的成就。如沧州的五代铁狮,当阳的北宋铁塔, 北京大钟寺明代的大钟等,它们的重量都有几十吨, 即使在现代条件下铸造,也不是容易的事情。
我国古代在泥范铸造方面还有一项重大的发明枣 叠铸法。所谓叠铸,是把许多个范块或成对范片叠合 装配,由一个共同的浇道进行浇注,一次得到几十甚 至上百个铸件。这种铸造方法效率高,铸件质量好, 节约造型材料和金属液,适合于小型铸件的成批大量 生产。
商代时期的青铜冶铸场景
锻造工艺的历史

锻造工艺的历史锻造是一种古老而重要的金属加工工艺,其历史可以追溯到古代文明。
以下是锻造工艺的历史概述:1.早期锻造:早期的锻造工艺可以追溯到公元前近3000年的铜器时代。
在这个时期,人们开始使用石器工具和木制模具,通过锤打将金属(主要是铜)锻造成各种形状,制作出刀剑、饰品等物品。
2.青铜时代:随着对金属工艺的进一步掌握,青铜时代的到来带动了金属的广泛应用。
铜合金的制备和锻造技术的提高使人们能够制作更为复杂和坚固的器物,如青铜器、武器和工具。
3.铁器时代:铁器时代的到来标志着金属工艺的一个重大进步。
铁的开采和冶炼技术的发展使得铁成为一种广泛应用的金属。
锻造铁器的技术进一步提高,制作了更坚固、更锋利的武器和工具,如铁剑、铁犁等。
4.古代文明:在古代文明中,如希腊、罗马、埃及和中国等,锻造技术得到了不断的发展。
这些文明的工匠通过改良工具、引入新的锻造技术,创造出许多具有艺术性和实用性的金属制品。
5.中世纪和文艺复兴:中世纪时期,锻造技术在欧洲继续发展。
锻造成为制造武器和护甲的重要工艺,同时在建筑、艺术和工业领域也得到广泛应用。
文艺复兴时期,对古代文化的研究和技术的创新促进了锻造工艺的进一步发展。
6.工业革命:18世纪的工业革命带来了机械化和工业化的浪潮,影响了锻造工艺。
新的机械设备和先进的冶炼技术使得大规模的金属生产成为可能,推动了现代锻造工业的形成。
7.现代锻造:在现代,锻造工艺得到了极大的发展,涉及到多种金属,包括钢、铝、铜等。
电力锻造和数控锻造等先进技术的引入使得锻造过程更加精密和高效。
总体而言,锻造工艺经历了漫长的历史发展过程,从最早的手工操作到现代的自动化和机械化生产,为人类提供了丰富多彩、实用耐用的金属制品。
锻造 技艺

锻造技艺锻造技艺是一项古老而重要的手工艺术,它可以将金属材料加工成各种形状和用途的器具。
从古代到现代,锻造技艺一直在不断发展和创新,成为了现代工业生产中不可或缺的一部分。
本文将从锻造技艺的历史、分类、工具、材料、流程和应用等方面进行详细介绍。
一、历史锻造技艺可以追溯到早期人类使用石头制作工具的时代。
随着冶金技术的发展,人们开始使用铜和铁等金属材料进行锻造。
在古代中国,锻造技艺已经非常发达,汉朝时期就出现了著名的“四铁”(刀剑、车马、器皿、钱币)制作技艺。
在欧洲中世纪时期,锻造成为了一个非常重要的行业,并且在文艺复兴时期得到了进一步发展。
二、分类根据加热方式不同,锻造可以分为冷锻和热锻两种类型。
冷锻是指在常温下对金属进行加工,通常用于制作小型零件或精密零件。
热锻是指在高温下对金属进行加工,通常用于制作大型零件或高强度零件。
三、工具锻造需要使用各种不同的工具,其中最重要的是锤子和铁砧。
锤子可以用于敲打金属材料,而铁砧则可以提供一个坚硬的表面来支撑金属材料。
除此之外,还需要使用钳子、切割器、钻孔机等各种辅助工具。
四、材料在锻造过程中,最常用的材料是金属。
不同种类的金属有着不同的性质和特点,在选择时需要根据具体情况进行考虑。
一些常见的金属包括钢、铜、铝、镍等。
五、流程锻造过程可以分为以下几个步骤:1. 切割:首先需要将原始金属材料切割成适当大小和形状。
2. 加热:将金属材料加热到适当温度,以便进行加工。
3. 锻造:使用锤子和铁砧对金属进行敲打和形变,直到达到所需形状和尺寸。
4. 冷却:将金属材料冷却至室温,以便进行后续处理。
5. 后续处理:根据具体情况,可以进行打磨、抛光、涂漆等后续处理工作。
六、应用锻造技艺广泛应用于各种领域,包括航空航天、汽车制造、建筑工程等。
在航空航天领域,锻造技艺可以用于制造高强度零件和结构件;在汽车制造领域,锻造技艺可以用于制造发动机零件和车轮等部件;在建筑工程领域,锻造技艺可以用于制造门窗、栏杆、楼梯等装饰性零件。
钼的锻造技术

钼的锻造技术
张振兴
【期刊名称】《中国钨业》
【年(卷),期】1989(000)011
【摘要】目前,钼及钼合金已能成功地锻造成各种零件,从小型零部件(叶片和配件)到大型的(重达1000磅以上)的锥形物和圆盘。
虽然钼及钼合金可用大多数常规手段进行闭模或开模锻造,但是最有效的钼锻造技术是高能锻造。
高能锻造是利用高压气体,使锻锤加速向锻件冲锻。
高能锻锤的质量小于常规的动力锤,但其锻造速度却高达70英尺/秒,而普通动力锤的最高锻速只有30英尺/秒。
用高能
【总页数】2页(P1-2)
【作者】张振兴
【作者单位】
【正文语种】中文
【中图分类】TF841.1
【相关文献】
1.从低品位钼精矿或钼中间产品生产工业氧化钼、二钼酸铵和纯三氧化钼 [J], 张文钲
2.加强技术交流提升铁路车辆锻造技术水平——“铁道车辆锻造技术研讨会”在南宁召开 [J], 刘继峰;邓彬
3.《中国钼业》“钼及钼合金材料关键制备技术与应用”专刊征稿启事 [J], 《中国钼业》编辑部
4.锻造技术的发展——从前8届国际塑性加工会议看锻造技术的发展 [J], 何祝斌;初冠南;张吉;王仲仁
5.金堆城钼业股份有限公司主持制定的国家标准《钼及钼合金金相检验方法》通过审定 [J],
因版权原因,仅展示原文概要,查看原文内容请购买。
- 1、下载文档前请自行甄别文档内容的完整性,平台不提供额外的编辑、内容补充、找答案等附加服务。
- 2、"仅部分预览"的文档,不可在线预览部分如存在完整性等问题,可反馈申请退款(可完整预览的文档不适用该条件!)。
- 3、如文档侵犯您的权益,请联系客服反馈,我们会尽快为您处理(人工客服工作时间:9:00-18:30)。
模具的弹性变形; 成形条件稳定性。其中模具的弹 性变形对零件的精度有重要影响。因此如何控制模
图 1 冷锻的发展 F ig 1 Dev elo pment of cold fo rg ing technolo gy
具的弹性变形对冷锻件精度的影响成为冷锻成形研 究的热点。 模具尺寸 主要靠提高加 工精度来保 证。近年 , 随着数控加工的出现 , 模具加工精度得到不断提高 , 对于比较规则的模具型腔, 现在的加工精度可达到 1um, 但对于一些复杂几何形状的模具型腔加工 精度仍不够理想, 然而, 模具精度已不是影响锻件 质量的决定性因素。 金属在室温下的变形抗力一般都较大, 因此锻 造过程中模具存在较大的弹性变形 , 并大大降低锻
初冠南
张
吉
王仲仁
要 : 该文对前 8 届国际塑性加工会议 ( Int ernational Co nfer ence on T echnolog y of P lasticit y) 论文集中锻造方面
的文献进行了综述 , 分析了 24 年来锻造工艺的发展历程 。总结了热锻、温 锻和冷锻 的技术优缺 点和近年 来的技术 突破。从中可以较充分地了解该技术的一些新的发展动向。 关键词 : 国际塑性加工会议 ; 热锻 ; 温锻 ; 冷锻 中图分类号 : T G302 文献标识码 : A 文章编号 : 1007 -2012 ( 2008) 04 - 0013 - 06
Development of forging technology
HE Zhu - bin CH U Guan - nan ZH A NG Ji Z R W ang China) ( School of M ater ials Science & Engineering , H ar bin Institute of T echnolog y, H ar bin 150001
2
2 1
温锻
温锻成形的提出
温锻是介 于冷锻和热锻之间的一种锻造工艺 , 成形温度区间一般在 650 ~ 900 。 相比于冷锻成形, 温锻成形可应用于变形抗力 相对较高的中碳钢及部分合金钢的成形。此外 , 某 些室温下延伸率很低的金属难以采用冷锻成形 , 温 锻可以很好地克服这一缺点。因此 , 可认为温锻是 冷锻应用的一个拓展。此外 , 冷锻成形时存在严重 的加工硬化现象, 工件内部残余应力大, 后续加工 中常需要进行去应力退火以消除加工硬化, 而温锻 成形可省略此类热处理工序。因此 , 温锻在精确成 形中碳钢和合金钢方面有较大的优势, 近年来得到 了较快的发展 。 2 2 温锻成形的优点 温锻工艺的优点是 , 尺寸精度高; 材料利用率 高 ; 零件表面质量高 ; 后续加工较少。 2 3 温锻的应用 温 锻工艺 可成形 部分截 面形 状较复 杂的零 件
形力相对较低。目前 , 冷锻主要用来成形两大类零 件, 即齿轮和 CVJ 连接件, 如图 2 所示。
图 2 典型冷锻件 Fig 2 T y pical cold fo rg ing component s
件尺寸精度。且由于不同部位的受力情况不同 , 各 区的弹性变形量存在较大差异 , 因此很难通过简单 的误差补偿改善这一缺点。实际生产中降低模具弹 性变形的方法主要有两种: 一是采用高强度的模具 钢和相应的热处理; 二是通过优化工艺过程降低成 形力。模具钢受材料发展限制 , 因此大部分研究主 要集中在通过降低成形力来降低模具的弹性变形以 提高锻件精度。日本的 Ko ndo, K Osakada, 英国 的 T A Dean 等在这方面都做了大量研究 , 并有很 多成果发表。 1 3 1 分流法[ 3- 5] 分流法提出的依据是通过降低变形抗力的方式 间接降低模具的弹性变形, 从而提高锻件的尺寸精 度。分流法的原理如图 4 所示 , 通过改变成形过程 中的金属流动模式和金属填充顺序降低变形抗力。
。 由于金属在室温时变形抗力大 , 因此冷锻技术
主要用来成形轴对称零件 , 这类零件形状简单 , 成
14
塑性工程学报
第 15 卷
形锻件精度高、材料 利用率高、后 续机加工序少 , 所以在成本节约上具有非常显著的优势[ 2] 。这也是 冷成形件受到越来越广泛应用的一个重要原因。 1 3 冷锻成形的关键技术 影响冷锻件精度的主要因素为 : 模具尺寸误差 ;
图5 Fig 5
积极摩擦原理
应当指出, 在温锻成形中分流法和积极摩擦法 同样被广泛采用。一些学者研究了采用分流法和积 极摩擦法进行复杂零件的成形。如文献 [ 15] 采用 积极摩擦成形了直齿齿轮 , 为降低模具的弹性变形 , 采用了先温锻、后冷锻的成形工艺。 此外, 在温锻成形的热力学、摩擦方面也有研 究 , 得到的结论如下 [ 16] :
目前冷锻件的公差可控制在 0 01 m ~ 0 05 m 以内 , 德国已经实现了汽车传动用十字轴的内外弧 齿齿轮的净形锻造。图 3 为弧齿齿轮挤压的模具装 置图。该装置有 3 个的特点, 即凸模球面自位支撑, 可以避免侧向力; 下模有调节装置 , 可保证上下模 同心 ; 下模有液压夹紧装置, 能保持对中夹持。
图3
弧齿齿轮挤压的模具装置图
F ig 3 Schematic of the die used for curv ed - g ear fo rg ing
1 2
冷锻件优点及应用
图 4 分 流法原理图
1 -Punch; 2 -Blank; 3 - Cont ain er
冷锻的显著优点在于成形件的尺寸精度高, 材 料利用率高。因此冷锻成形也被称为净成形或近净 成形。此外, 冷锻件还有零件表面质量高、后续加 工少及环保的特点。 锻造技术的成本构造中原材料费用约占总成本 的 40% , 辅助加工费用约占总成本的 25% 。而冷成
1
1 1
冷锻
冷锻的发展 20 世纪 60 年代以前, 冷锻成形技术在 实际生
产中的应用非常有限 , 主要用于弹壳制造。二次世 界大战之后 , 随着汽车业的蓬勃发展, 对零件使用 性能要求日益提高。由于能源危机 受到日益重视 , 对当时汽车的燃油利用率提出了更高的要求, 因此 冷锻技术就进入了人们的视野。研究者发现, 热锻 件的缺点主要在于成形件尺寸精度低, 需要后续加 工 , 破坏了金属内 部的纤维组织和 流线的连续性 , 使零件使用性能降低 , 且带来材料浪费。而采用冷 锻 / 温锻成形出的零件尺寸精度高, 不需或只需很少 的后续加工 , 内部金属纤维组织的连续性得到保留 , 零件有很好的使用性能 , 材料利用率高, 因此得到
何祝斌
E - mail: hithe@ hit edu cn
了高速的发展。图 1 为 20 世纪中后期冷锻技术的发 展情况 , 由图 1 中可见, 冷锻成形件的增长非常迅 速
[ 1]
作者简介 : 何祝 斌 , 男 , 1977 年 生 , 江苏 淮 阴人 , 哈尔 滨工业大学 , 讲师 , 博士 , 研究方向为塑性加工理论、管 材液力成形及型材成形新工艺 收稿日期 : 2008 - 05 - 28; 修订日期 : 2008 - 06 - 03
引 言
锻造是人类发明的最古老的生产技术之一。人 类发明和使用金属几千年的历史 , 都伴随锻造技术 的发展。从最初锻造农具和制造盔甲 , 到现在生活 中随处可见的千千万万的锻造产品 , 都证明这一技 术对人类的宝贵价值。目前, 人类生产的金属材料 中的很大部分, 都是经过锻造方法加工成成品零件 的。随着人们对材料利用率和成形件使用性能要求 的提高和成本的降低 , 冷锻和温锻近年来得到了很 大的发展。本文对 1984 年以来 8 届国际塑性加工会 议论文集中锻造方面的文献进行了分析 , 从中可以 了解到热锻、温锻、冷锻的发展进程和趋势。
F ig 4
Schematic of div ided flow metho d
在分流法发展之前 , 研究者发现, 相同截面积 的圆环镦粗所需要的镦粗力小于相同截面积的圆柱
第4期
何祝斌 等 : 锻造技术的发展
15
镦粗时的变形力。通过分析发现 , 圆环镦粗时金属 是分流的, 一部分向环的内侧流动 , 一部分向环的 外侧流动, 这种流动方式可大大降低成形力。分流 法在 1987 年的第二届 ICT P 会议上由 K Ko ndo 正 式提出, 在成形力只有原来 1/ 4 的情况下成功成形 了直齿齿轮件, 在后来的几届会议上 Kondo 课题组 利用该方法成形了带高凸台和复杂油槽的直齿、斜 齿齿轮件 。 此外 , Dohmann[ 8] 提出通过 杯形件镦 粗成 形齿 轮件可大大降低成形力, 且锻件有很好的成形精度。 成形过程主要分为 4 步: 厚 板拉伸得到杯形件 整 形 预成型 终成形。该方法是在杯形件镦粗过程 中完成齿形件的成形。因成形过程中金属可沿径向 向内向外同时流动, 因此成形阻力低 , 模具的弹性变 形小 , 成形件精度高, 模具寿命也因此得到提高。从 该方法降低成形力的本质看, 其核心思想与分流法一 致, 都是通过金属分流达到降低变形抗力的目的。 1 3 2 积极摩擦法 直齿齿轮件锻造成形时 , 端部直角区域 ( 见图 5 中区域 A) 非常难以填充 , 即使 锻造力提高很大 也难以实现直角部 分的成形。在成形这类零 件时, 虽然可以通过施加足够的成形力或者提高变形温度 以获得好的填充效果, 但提高成形力的同时, 模具 弹性变形增大, 成形件精度降低, 模具寿命也缩短; 而提高温度则带来氧化和低的表面质量 , 对于精确 成形均不宜采用。针对这一困难 , 有学者提出利用 模具与坯料间的摩擦在不增大成形力的前提下, 可 很好地克服这一困难。积极摩擦的原理如图 5 所示。 成形中模具与冲头一起运动, 利用模具与坯料间的 摩擦带动棒料填充底部尖角区域。
第 15 卷 第 4 期 2008 年 8 月
塑性工程学报
JOURNAL OF PL AST ICIT Y ENGINEERING
Vol 15 Aug
No 4 2008