高硫煤燃烧技术交流
锅炉高硫煤掺烧技术措施

锅炉高硫煤掺烧技术措施随着能源需求的不断增加和煤炭资源的逐渐匮乏,燃用高硫煤已成为我国一种常见的现象。
然而,高硫煤的燃烧会释放出大量的有害物质,对环境产生巨大的负面影响。
为了减少高硫煤燃烧对环境的影响,锅炉高硫煤掺烧技术日益得到重视。
本文将就锅炉高硫煤掺烧技术和相关措施进行探讨。
锅炉高硫煤掺烧技术锅炉高硫煤掺烧技术是指将高硫煤掺入普通煤中进行燃烧的技术。
通过这种方法,不仅可以减少燃烧产生的二氧化硫等有害气体的排放,同时还能够利用高硫煤的热值,减少能源浪费。
锅炉高硫煤掺烧需要解决的技术难题主要有以下几个方面:1. 热力学特性不同高硫煤和普通煤的热力学特性不同,导致了它们在燃烧过程中产生的热效率、氧化反应速率、燃烧温度等存在差异,因而需要对锅炉的控制和设计进行调整和改进。
为了解决热力学差异所带来的问题,需要采用先进的锅炉控制技术,以充分发挥高硫煤的热值。
2. 燃料适应性差高硫煤的燃烧温度和普通煤不同,其挥发性和灰分存在很大差异。
因此,在锅炉中同时燃烧高硫煤和普通煤时,需要对该锅炉进行相应的调整和改造,以保证燃料的适应性。
3. 对污染物的控制高硫煤燃烧后,会产生大量的二氧化硫等污染物。
面对这一问题,需要采用先进的废气处理设备,如脱硫技术、脱硝技术和颗粒物捕集技术等,以达到国家和地方政策标准,减少环境污染。
锅炉高硫煤掺烧技术措施为了实现高硫煤掺入普通煤中实现控制减排的目的,需要采取以下措施:1. 采用先进控制技术采用先进的锅炉控制技术,以充分发挥高硫煤的热值。
在控制模式方面,可以采用模糊控制、PID控制、决策树控制等。
2. 选用适合的高硫煤为了实现高硫煤掺入普通煤中,还需要选择适合的高硫煤,以保证其与普通煤的适应性和焚烧性能。
同时,需要对高硫煤进行粉煤预处理,以减少硫和灰分含量。
3. 应用生产过程控制技术应用生产过程控制技术,对煤粉的颗粒大小进行控制。
采用细磨、湿法细磨、加氢堆积等技术,优化煤粉颗粒的结构分布和细度,从而提高其灰除能力和减少SO2的排放。
高硫煤燃前脱硫技术

1 物理法
物理法是主要利用煤炭颗粒与含硫化合物的物 理特性 ,如密度 、磁性 、导电性 、表面性质等 ,将硫铁矿 和煤及煤矸石分开 ,除去煤中无机硫的方法 ,它是应 用最多 、方法最简单 、成本最低的脱硫方法 ,但无法除 去有机硫 。物理法主要有重选法 、浮选法 、磁选法 、电 选法 、干选法 、絮凝法 、微波处理法和辐射脱硫法等 。 1. 1 重选法
常压气体湿法主要有以下两种 。 2. 2. 1 KVB 法
KVB法是在常压下利用 NO2 选择性氧化煤中含硫 组分 ,并以水洗或热碱液处理后再水洗除去煤中的硫。 2. 2. 2 氯解法
氯解法也称 JPL法 ,在氯化作用下 ,硫铁矿可被氧 化为氯化铁和硫酸 ,有机硫可被氧化为磺酸或硫酸。 2. 3 溶剂法
热压浸出法主要有以下 3种 。 2. 1. 1 热碱液浸出法
热碱液浸出法又称水热法 ,是用 Na2 CO3 4% ~ 10%和 Ca (OH ) 2 2%的混和水溶液为浸出剂 ,可将煤 中硫铁矿转化为可溶性硫化物 、硫代硫酸盐 、有机硫
田正山 高硫煤燃前脱硫技术 20091Vo l123 , No. 7 化工时刊
浮选法脱硫是依据煤和黄铁矿表面物理化学性 质的不同 ,利用浮选机或浮选柱作分选设备 ,通过加 入适当的抑制剂来达到脱硫目的 ,脱硫率达 53%左 右 。浮选法脱硫是在技术和经济上最为可行的脱硫 方法之一 ,尤其是浮选柱特别适合脱除煤中的黄铁 矿 ,它比机械搅拌式浮选机具有更好的颗粒与气泡接 触的效能 ,而且动力消耗少 。电化学调控高硫煤浮选 脱硫新技术采用一种新的黄铁矿抑制方法 ,为高硫煤 浮选脱硫提供了一条新途径 [ 4 ] 。 1. 3 磁选法
试论高硫煤炼焦过程的脱硫技术

试论高硫煤炼焦过程的脱硫技术【摘要】以有机硫为主的高硫煤,洗选后精煤硫份比原煤更高。
焦煤中的硫份只有30%-50%经裂解进入煤气中,大部分硫残留在焦炭中,根据硫份在焦炭中的位置,可将脱硫技术分为入炉前脱硫,焦化过程脱硫和煤气脱硫三个阶段过程,本文主要探讨了高硫煤入焦炉前物理、化学法脱硫,焦化过程高温加氢(焦炉煤气)脱硫工艺和煤气中硫元素回收利用进行最终脱硫。
【关键词】焦煤入炉前脱硫;碳化过程加氢脱硫;回收煤气脱硫1.焦煤入焦炉前脱硫1.1无机硫的脱除无机硫脱除一般以物理法为主,它主要以硫铁矿和硫酸盐的形态存在于煤的夹层中,以地质结合为主,由于国内原煤洗选工艺一般以脱灰为主,原煤中无机硫的脱除率一般在40%左右,如将原煤洗选粒度降至一定程度,硫铁矿的脱除率可大幅提高,因此只要将部分洗煤设备和工艺加以改进,即可有效的提高无机硫的脱除效率,目前,国内外已有成熟的设备,通过优化洗选工艺,脱除原煤中的硫铁矿。
它工艺可靠,脱除效率高、投资省、运行成本低,已得到洗煤行业的高度重视,一些专业的洗煤厂商已将脱除无机硫做为设计重点,主要采用重力法、浮选法、磁选法等几种工艺。
重力法是按煤和硫铁矿比重差异进行脱硫,这是目前焦煤脱硫的主要手段,使用重介质旋流器可以实现低密度,高精度的分选,分选粒度下限可以达到0.1-0.2mm,能有效地排除未充分解离的中间密度的硫铁矿与煤的连生体,而获得较高回收率的低灰低硫精煤,高密度的硫铁矿使用重介工艺可使煤与硫铁矿进行有效的分离,且脱除率较高。
浮选法主要处理重介质分选粒度下限微未级的细微粒煤,上限可以达到0.3mm 以上,弥补了重介质分选的粒度范围,在该粒度状况下,煤与硫铁矿连生体已基本被分离,只要选用合适的浮选制,利用颗粒表面润湿差异和空气微泡有条件吸附而形成的表面张力就能有效的分离出硫铁矿和灰分,微泡浮选柱具有明显的去硫除灰能力,而且对微末级的极细粒煤效果非常好。
磁选法主要利用硫铁矿自身的磁性对其进行脱硫,它是根据煤效组份与硫铁矿的磁性差异进行脱硫。
锅炉高硫煤掺烧技术措施
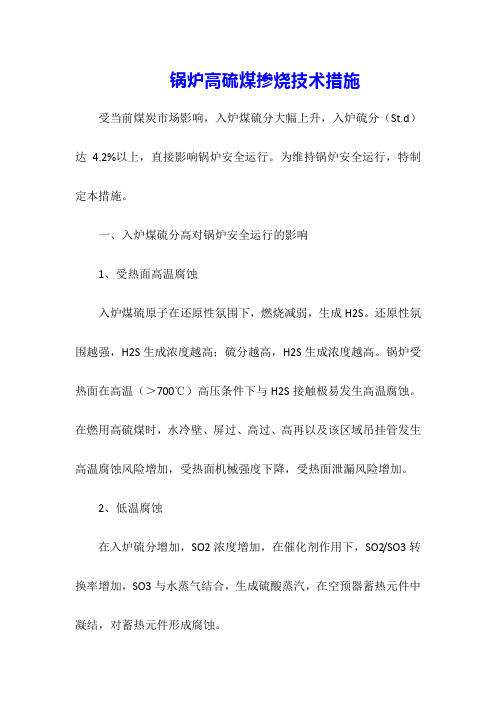
锅炉高硫煤掺烧技术措施受当前煤炭市场影响,入炉煤硫分大幅上升,入炉硫分(St.d)达 4.2%以上,直接影响锅炉安全运行。
为维持锅炉安全运行,特制定本措施。
一、入炉煤硫分高对锅炉安全运行的影响1、受热面高温腐蚀入炉煤硫原子在还原性氛围下,燃烧减弱,生成H2S。
还原性氛围越强,H2S生成浓度越高;硫分越高,H2S生成浓度越高。
锅炉受热面在高温(>700℃)高压条件下与H2S接触极易发生高温腐蚀。
在燃用高硫煤时,水冷壁、屏过、高过、高再以及该区域吊挂管发生高温腐蚀风险增加,受热面机械强度下降,受热面泄漏风险增加。
2、低温腐蚀在入炉硫分增加,SO2浓度增加,在催化剂作用下,SO2/SO3转换率增加,SO3与水蒸气结合,生成硫酸蒸汽,在空预器蓄热元件中凝结,对蓄热元件形成腐蚀。
3、空预器堵塞SO3浓度增加,与NH3反应生成硫酸氢铵的起凝温度上升,使硫酸氢铵沉积高度上移,发生跨层沉积,蒸汽吹灰难以清除。
同时受起凝温度上升,单侧升温清除硫酸氢铵措施,难以清除沉积的硫酸氢铵,空预器堵塞风险增加。
4、锅炉结焦增强经试验,当前燃用高硫煤灰熔点软化温度仅1160℃,结焦倾向为严重结焦(ST<1250℃)。
锅炉结焦后排烟温度增加,发生集中垮焦时,发生锅炉灭火及砸伤水冷壁风险增加。
二、运行措施1、每班接班后,及时向输煤运行了解配煤方式,根据配煤方式,在保证燃烧安全的前提下,通过调整给煤机(同一台磨,给煤机偏差上限20t/h)、磨煤机出力偏差,使入炉硫分保持在3.8%~4.2%,热值3800kCal/kg~3900kCal/kg。
热值低于3800kCal/kg优先调整热值;热值大于3800kCal/kg,优先调整硫分。
2、因高硫煤灰熔点低,原则上高硫煤避免上C/D磨原煤仓,优先上A/F磨原煤仓,避免翼墙区域结焦。
3、严格执行《防止锅炉严重结焦的措施》,并对照措施进行配风及切换磨机,防止锅炉结大焦。
4、任一省煤器出口氧量测点不低于2.8%,综合氧量不低于标杆0.3%,防止局部缺氧,烟气呈还原性氛围。
关于燃用高挥发份煤的安全技术措施

关于燃用高挥发份煤的安全技术措施背景介绍高挥发份煤是指挥发份在20%以上的煤炭,通常指烟煤、焦炭等。
燃用高挥发份煤时,由于其挥发份高易燃、易爆炸等特点,存在一定的安全隐患。
因此,必须采取一系列的安全技术措施来确保炉内燃烧的安全稳定。
安全技术措施煤气点火系统煤气点火系统要求高挥发份煤炭必须用煤气作为点火介质,点火前煤气的流量要进行严格的控制,并通过可靠的手段来保证煤气点火的安全性和准确性。
在点火后的初始阶段,应对炉内煤气进行监控,确保点火安全、燃烧稳定。
烟气净化系统在高挥发份燃料燃烧后产生的烟气中,含有大量的化学物质和粒子物质,将严重污染大气环境。
因此,必须对烟气进行净化处理,包括除尘、脱酸、脱硫等步骤。
在实际工程应用中,还可采用高效除尘器、脱硝催化剂、烟气再生系统等现代化技术设备来减少对环境的影响。
炉内温度控制高挥发份煤炭的燃烧会产生大量的高温和火焰。
在炉内温度过高或火焰不稳定的情况下,很容易引发燃烧事故。
因此,在燃用高挥发份煤的工程中,应严格控制炉内温度,并对燃烧过程进行实时监控和控制。
安全监控系统安全监控系统是整个高挥发份煤储燃系统的核心部分,其目的是对煤气和烟气进行连续监测,确保炉内燃烧的安全运行。
安全监控系统需要具备自动化程度高、实时性强、安全可靠的特点,并与其他工程设备实现联动控制。
废弃物处理系统高挥发份煤产生的废气和灰渣是一种重要的环境污染来源,必须采取有效的处理措施。
在废弃物处理系统中,常用的技术手段包括干法除尘、湿法脱硫、废气处理、危废处理等。
这些技术手段能够有效地降低废弃物对环境的影响,提高整个储燃系统的环保指标。
结语在工业生产中,高挥发份煤炭的燃烧是一种普遍存在的现象。
针对其易燃、易爆炸等不安全因素,必须采取一系列的安全技术措施来确保安全。
煤气点火系统、烟气净化系统、炉内温度控制等技术手段可以使整个储燃系统在燃烧中保持稳定、安全和环保。
同时,安全监控系统和废弃物处理系统同样是储燃系统的重要组成部分,对于提高整个燃烧过程的安全性和环保性具有重要意义。
燃用高挥发分、高发热量煤种的安全技术措施
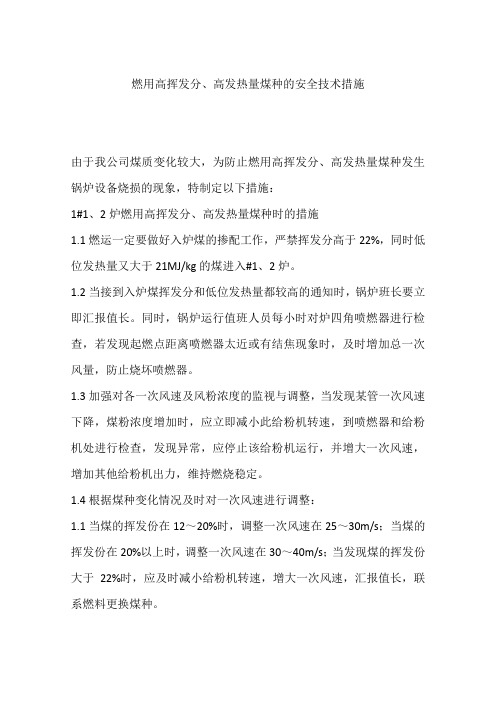
燃用高挥发分、高发热量煤种的安全技术措施由于我公司煤质变化较大,为防止燃用高挥发分、高发热量煤种发生锅炉设备烧损的现象,特制定以下措施:1#1、2炉燃用高挥发分、高发热量煤种时的措施1.1燃运一定要做好入炉煤的掺配工作,严禁挥发分高于22%,同时低位发热量又大于21MJ/kg的煤进入#1、2炉。
1.2当接到入炉煤挥发分和低位发热量都较高的通知时,锅炉班长要立即汇报值长。
同时,锅炉运行值班人员每小时对炉四角喷燃器进行检查,若发现起燃点距离喷燃器太近或有结焦现象时,及时增加总一次风量,防止烧坏喷燃器。
1.3加强对各一次风速及风粉浓度的监视与调整,当发现某管一次风速下降,煤粉浓度增加时,应立即减小此给粉机转速,到喷燃器和给粉机处进行检查,发现异常,应停止该给粉机运行,并增大一次风速,增加其他给粉机出力,维持燃烧稳定。
1.4根据煤种变化情况及时对一次风速进行调整:1.1当煤的挥发份在12~20%时,调整一次风速在25~30m/s;当煤的挥发份在20%以上时,调整一次风速在30~40m/s;当发现煤的挥发份大于22%时,应及时减小给粉机转速,增大一次风速,汇报值长,联系燃料更换煤种。
1.2当煤的挥发份在22%以上时,应适当开启磨煤机入口冷风门,降低磨煤机出口温度,#1、2炉磨煤机出口温度不大于90℃,防止制粉系统爆炸。
1.3当煤的挥发份在22%以上时,应适当降低煤粉仓粉位,保证粉仓各点温度不大于110℃,防止粉仓自燃。
1.4当煤的挥发份在22%以上时,应保持氧量在3~5%,炉膛压力在-50~-100Pa,严禁正压运行。
1.5当发现喷燃器有发红或火焰向外喷时,应立即停止相应的给粉机运行,继续通一次风,将煤粉管道内余粉吹扫干净,同时减小其他给粉机出力,并及时汇报值长,并根据事态发展,决定是否紧急停炉。
1.6当#3、4炉燃用气肥煤时,煤粉炉值班人员要充分做好事故预想。
1.7在投用喷燃器前和停用喷燃器后,应对煤粉管道进行吹扫,防止煤粉管道内有积粉。
配高硫煤炼焦的研究

配高硫煤炼焦的研究高硫煤是一种含硫量较高的煤种,广泛应用于国内外炼钢、炼熔、冶金和燃料等行业。
由于其硫含量较高,炼焦过程中可能出现一系列问题,如低生产率,沉淀物结垢或无机物质堆积,工艺难度加大,对环境造成污染等。
为此,实施有效的配高硫煤炼焦技术是提高燃煤炼焦质量和降低燃煤炼焦污染的关键。
为提高燃煤炼焦质量及降低污染,配高硫煤炼焦必须综合考虑技术、经济性和环境友好性的要求,因此,目前已经采取了三种主要的技术措施,即焦化、脱硫和脱硫脱硝。
首先,焦化技术是降低燃煤炼焦温度,以最大限度的提高焦炭抽出率和热效率的有效措施。
通过采用半水洗机或磷脂洗机等设备实现焦化技术,可以在保持煤质和产量情况下,降低焦炭抽出温度,改善焦炭特性。
其次,脱硫技术是采用吸收剂将高硫煤中的硫从烟气中吸附,从而提高炼焦过程的热效率和炼焦质量。
其目前已经形成了两大体系,一是半干式吸收,采用高温、中温和低温三种技术,主要应用于煤粉炉焦炉;另一种是湿式吸收,主要应用于瓦斯炉焦炉,通过催化和非催化等技术实现。
最后,脱硫脱硝技术是将烟气中的硫和氮气进行有效去除,从而实现高硫煤脱硝脱硫的目的,该技术可以显著降低焦化过程中的污染,提高炼焦质量。
脱硫脱硝有吸收和催化两种技术方式,按照烟气中的硫和氮含量,可将其分为高中低排放类,并发展出相应的处理技术方案。
总之,通过以上三种技术措施,可以有效改善高硫煤焦化过程中的热效率、炼焦质量以及烟气排放污染,从而保持燃煤炼焦质量的提高和环境保护的要求。
可以看出,改善配高硫煤炼焦技术,对于提高炼焦质量和降低污染有着重要的意义。
针对配高硫煤炼焦的技术问题,中国在研究和开发上努力不懈,在焦化、脱硫和脱硫脱硝技术方面取得了一定成就。
为此,我国应加强对配高硫煤炼焦技术的研究和改进,进一步提高燃煤炼焦技术水平,为国民经济提供良好的燃料基础和环境服务。
综上所述,配高硫煤炼焦是提高燃煤炼焦质量和降低烟气污染的重要技术,其成功实施需要综合考虑技术、经济性和环境友好性等多方面因素,并加以不断改进,以提高炼焦水平,减少污染。
燃用高硫煤脱硫的分析与对策
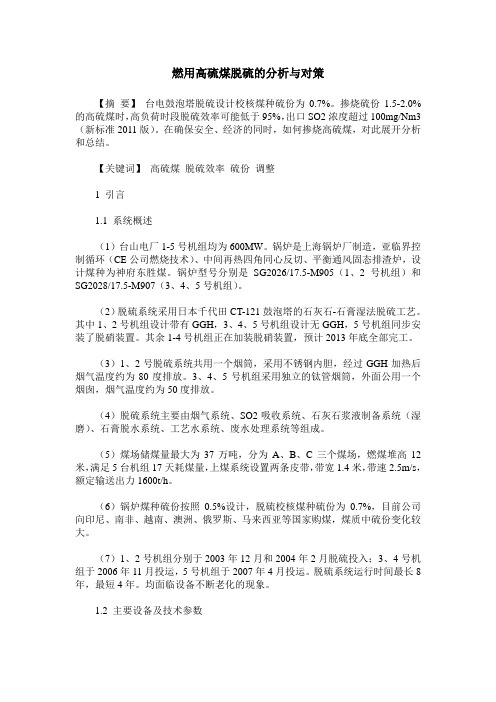
燃用高硫煤脱硫的分析与对策【摘要】台电鼓泡塔脱硫设计校核煤种硫份为0.7%。
掺烧硫份1.5-2.0%的高硫煤时,高负荷时段脱硫效率可能低于95%,出口SO2浓度超过100mg/Nm3(新标准2011版)。
在确保安全、经济的同时,如何掺烧高硫煤,对此展开分析和总结。
【关键词】高硫煤脱硫效率硫份调整1 引言1.1 系统概述(1)台山电厂1-5号机组均为600MW。
锅炉是上海锅炉厂制造,亚临界控制循环(CE公司燃烧技术)、中间再热四角同心反切、平衡通风固态排渣炉,设计煤种为神府东胜煤。
锅炉型号分别是SG2026/17.5-M905(1、2号机组)和SG2028/17.5-M907(3、4、5号机组)。
(2)脱硫系统采用日本千代田CT-121鼓泡塔的石灰石-石膏湿法脱硫工艺。
其中1、2号机组设计带有GGH,3、4、5号机组设计无GGH,5号机组同步安装了脱硝装置。
其余1-4号机组正在加装脱硝装置,预计2013年底全部完工。
(3)1、2号脱硫系统共用一个烟筒,采用不锈钢内胆,经过GGH加热后烟气温度约为80度排放。
3、4、5号机组采用独立的钛管烟筒,外面公用一个烟囱,烟气温度约为50度排放。
(4)脱硫系统主要由烟气系统、SO2吸收系统、石灰石浆液制备系统(湿磨)、石膏脱水系统、工艺水系统、废水处理系统等组成。
(5)煤场储煤量最大为37万吨,分为A、B、C三个煤场,燃煤堆高12米,满足5台机组17天耗煤量,上煤系统设置两条皮带,带宽1.4米,带速2.5m/s,额定输送出力1600t/h。
(6)锅炉煤种硫份按照0.5%设计,脱硫校核煤种硫份为0.7%,目前公司向印尼、南非、越南、澳洲、俄罗斯、马来西亚等国家购煤,煤质中硫份变化较大。
(7)1、2号机组分别于2003年12月和2004年2月脱硫投入;3、4号机组于2006年11月投运,5号机组于2007年4月投运。
脱硫系统运行时间最长8年,最短4年。
均面临设备不断老化的现象。
高硫煤煅烧

高硫煤的煅烧某1000t/d预分解窑厂从2008年7月开始,窑内频繁出球,长长厚窑皮,烟室也结了皮,窑尾漏料严重,粉尘满天飞,工作环境恶劣。
从生料、熟料化学成分看没有多大变化,采用的煅烧操作方法和窑热工控制参数亦无多大变化。
那到底是什么原因造成这种现象呢?通过认真分析,在2008年7月以前,水泥中石膏配比都在6%~7%之间波动,但从7月开始,水泥中石膏配比减到4%~5%之间(石膏成分比较稳定、水泥中SO3控制目标一致),于是就怀疑是熟料中SO3过高所致,通过检测,熟料中SO3明显偏高,达到 2.0%左右,由此推断是因为煤中的硫含量过高导致了熟料中SO3偏高。
通过采用艾士卡法检测煤中全硫达4%左右。
由于使用了高硫煤作燃料,硫的矿化作用致使熟料液相提前出现,液相量过大,促使了窑内长长厚窑皮,频繁结球,以致窑尾漏料使生产环境恶化。
1 高硫煤对熟料煅烧的影响 1.1高硫煤促使熟料液相量过大,由于煤中的高硫带入,在烧结过程中,因为SO3的矿化作用,液相提前出现,而且液相量大大增加,在该情况下,如果生料中Fe2O3、Al2O3含量配臵不当,势必导致液相量过大、通风不良,产生强大还原气氛(结球料中有白色的极度还原熟料),煤粉燃烧不完全,结球在所难免,熟料质量降低是必然结果。
1.2 高硫煤促使熟料C3S含量降低液相出现提前,C3S形成过快,部分C2S尚未来得及吸收CaO形成C3S便被包裹在C3S晶体中,导致熟料中C3S含量偏低,同时较高的SO3存在,它势必争夺部分CaO而形成CaSO4使熟料的实际饱和比降低,若配料时再按常规计算,则保证C3S生成的CaO量就显得相对不足,致使熟料中C3S含量进一步偏低,导致熟料强度的降低。
2 使用高硫煤煅烧水泥熟料的实践 2.1确定适宜的熟料饱和比和降低熟料液相量在用高硫煤煅烧水泥熟料时,为保证有足够的C3S生成量,在配料时就必须比常规配料的CaO量要高得多,即熟料的KH应达到0.95左右,同时,要降低Al2O3的含量,但是该厂采用灰石、砂岩、铁矿三组份配料,为保证适宜的熟料饱和比和硅酸率,Al2O3的降低始终有一个限度,于是同时通过逐渐稳妥地降低出窑熟料中Fe2O3含量来降低液相量,改善物料的烧结范围,即在配料中逐步提高硅酸率(SM 2.9)和铝氧率(IM1.8)的控制指标,降低熟料中的液相量,提高熟料硅酸盐矿物的总体含量,特别是C3S的含量,使熟料中的Fe2O3降低至2.5%左右或更低(根据窑内煅烧状况)。
高硫煤炉内燃烧脱硫的试验研究

摘 要 : 用正 交 实验 的方 法 对济 源 高硫 煤 炉 内燃烧 脱硫 进 行 了实验研 究 , 定 了影 响 固 采 确
硫 率 的主要 因素 , 制 出 了适 于济 源 高硫 煤 炉 内燃烧 脱硫 的 固硫 剂 , 研 并进 行 了工业 性试
验 。 果表 明 , 过 添加 固硫 剂 可 有效 地减 少燃煤过 程 中 S 。 结 通 O 的排 放 , 于 以有机 硫 为主 对 的济 源 高硫 煤 , 内燃 烧 脱硫 是 一 种行 之 有 效的 脱硫 方 法 。 炉
维普资讯
第 1 卷 第 3期 6 11 , . ,0 2 0 .6 № 3 2 0
跷 / 痢 婉 珑 豌 的 炉
张传 祥 郑继东 谌伦建 张如 意 尹 国勋
( 焦作 工 学 院 , 河南 焦作 4 4 0 ) 5 00
关 键词 : 高硫 煤 ; 烧 脱硫 ; 燃 固硫 剂
中图分 类 号 : 7 13 X 0 、
文 献标 识 码 : A
文章 编 号 :06 8 5 (0 2 0 — 0 1 0 10 — 7 9 20 ) 3 0 2 — 5
AN ' E= E
匝NTAL Ⅱ Jl ON UL S DY S FUR 即 NnON
OF RAW COA C L OM US I T ON
Z A G C un x n H N j— og C E u —i Z A G R 一r I u — u H N h a — i g Z E dn H NL n j n a i a H N u ) N G o xn i Y
(/ zoIstt o e n l y, i zo H ’,l4 4 0 ) J ou ntu Tc o g J ou , e t / 5 0 0 a i ef h o a /  ̄
天溪煤制油分公司三废锅炉运行实践及成果交流

天溪煤制油分公司三废锅炉运行实践及成果交流山西晋城无烟煤矿业集团有限责任公司天溪煤制油分公司首次采用循环返烧式三废综合混燃炉燃烧技术,由阜阳市节能化工工程有限公司研制,该文着重介绍此锅炉主要设计特点及运行状况,可供同类型锅炉设计参考。
晋煤集团天溪煤制油分公司是以当地高硫煤为原料生产汽油的化工企业,在造气及其它生产过程中,每天产生造气炉渣、二旋飞灰、烘干细粉、合成弛放气、MTG弛放气,由于排放的废灰、废气、炉渣当中的含碳量及可燃成分高,造成能源的浪费和环境二次污染,没有从根本上实现完全燃烧和节能减排的理想效果,同时为企业粉煤灰的处理和现场管理带来了难题,为了达到节能减排、提高经济效益的目的,针对企业目前的现状和近期的发展规划,选用75t/h循环返烧式三废综合混燃炉一台,回收燃用合成弛放气、MTG弛放气,并掺烧造气炉的炉渣和烘干细粉、二旋细粉等可燃废弃物。
锅炉概述本锅炉为75t/h中温、中压循环流化床锅炉,采用近年发展起来的循环流化床燃烧技术,并根据无锡华光锅炉股份有限公司与国内著名院校多年合作开发循环流化床锅炉的经验,以及同类型循环流化床锅炉运行的成功经验基础上,完善了本锅炉,本锅炉结构简单、紧凑,主要由混合燃烧室、除尘器、锅炉、静电除尘器及布袋除尘器、烟囱、风机及给煤设备等组成。
1 锅炉设计燃料本锅炉设计燃料为:造气炉渣、烘干细粉、二旋飞灰、合成弛放气、MTG 弛放气,具体参数如下所示。
(1)烘干细粉,固定碳65.88%,灰分35.83%,挥发分7.36%,水分0.93%,含硫量1.98%;二旋飞灰,固定碳73.71%,灰分22.58%,挥发分1.05%,水分2.66%,含硫量0.6%;造气炉渣,固定碳30%-40%。
(2)合成弛放气:低位发热值3046.28大卡/Nm3,MTG弛放气:低位发热值10186.98大卡/Nm3(按甲烷计)。
2 锅炉主要技术参数(1)锅炉型号:UG-75/4.0-MQ。
高硫煤的燃烧调整与净烟SO2浓度控制

一、入厂高硫煤储存方式和入炉煤控制方法将入厂的高硫煤定点放置在卸煤沟B3/B4,将煤质发热量、水分、硫份通报发电部;每天根据高硫煤消耗数量控制入厂高硫煤数量;为保证运行安全,必须确保#1筒仓为低硫煤,将高硫煤储存到#2筒仓,#3筒仓储存高热值煤。
#1/2炉A、C仓上高硫煤,B、D仓上低硫煤。
锅炉人员接到脱硫人员通知烟气入口SO2浓度增大,环保参数超标时,立即降低A、C给煤机煤量(减10t/ h左右),加大B、D给煤机煤量(不超过40t/h),如果烟气入口SO2浓度仍然增大,值长应降负荷,继续降低A、C给煤机煤量,确保合格排放。
经过掺配的入炉煤保证发热量在4200kcal/kg以上,硫份尽量小于1.5%。
二、烧高硫煤对锅炉主要影响及控制措施1.尾部烟道对流受热面易玷污、积灰。
措施:加强对尾部烟道受热面的吹灰。
2.低温腐蚀,含硫高,烟气中二氧化硫和三氧化硫高,遇到有冷凝水形成酸,进而腐蚀设备。
空预器冷端、尾部烟道、布袋除尘器腐蚀,且水分大会加剧低温腐蚀。
另外,空预器冷端元器件硫酸氢氨生成几率提高,易造成空预器堵塞、布袋除尘器布袋腐蚀和尾部烟道腐蚀。
措施:提高排烟温度,增大总风量;提高空预器入口风温。
3.灰熔点降低,水冷壁结渣、燃烧器喷口易结焦,严重时会导致炉膛吸热减少、出口烟温升高,飞灰含碳量增加,过热器、再热器减温水量增加,排烟温度升高,机组效率降低;结焦严重时甚至可能爆管。
措施:加强对燃烧器喷口的检查,开大A、C层一次粉管周界风,提高一次风刚性,维持一次风压力,避免火焰冲刷水冷壁;降低火焰中心位置。
4.硫酸氢铵容易使空预器、催化剂堵塞,催化剂活性降低,影响NOX排放,威胁设备安全。
措施:严格执行SCR区、空预器蒸汽吹灰制度,加强对SCR区催化剂层压差、空预器进出口压差的监视,发现增大,加强吹灰。
空预器吹灰改为每四小时一次。
热解炉出口温度不低于340℃,控制氨空气混合气母管温度不低于315℃。
5.高温腐蚀。
配高硫煤炼焦的研究

配高硫煤炼焦的研究
配高硫煤是一种含有较高硫含量的煤种,因其特殊的化学成分,采用传统焦炉炼焦则会产生污染,一些技术问题也会产生。
目前,采用一定的技术路线来炼制高硫煤炼出的焦炭裂解能力与质量已经有
了极大的改善,因而高硫煤炼制焦炭的研究迎来红火的发展期。
一方面,高硫煤焦化工艺需要把硫含量控制在一定的范围内。
在高硫焦的热加工过程中,主要的技术措施是满足安全要求的热处理方案,即在热处理过程中,充分利用热量,加强焦炭的淬火,控制焦炭中硫含量,提高炼焦焦炭的质量和性能。
另一方面,采用热技术处理过程可有效降低烟气中污染物的排放,特别是SO2和粉尘排放,也可以提高炼焦焦炭的质量和性能。
还包括改善焦炉焦皮的技术改进。
焦皮是一种紧贴炉壁,导热,导电的中间层层,它可以决定炉床炼焦水平。
焦皮主要由耐火材料组成,而耐火材料又分为耐高温材料与耐抗火,即外层是防止熔融气体渗透的特殊耐高温耐火材料,内层是防止热量散失的有机物绝热材料。
通过对焦炉焦皮采用以上材料,可以使炉床温度更有效地传递到焦炉内,提高炼焦炉床的效果,同时利用热力学的原理,将热量在炉子内最大化的利用,减少炼焦焦炭的热量损失,从而提高炼焦效率。
此外,高硫焦炉的环境保护措施也不可忽视。
高硫焦有高温、高压、腐蚀性强等特点,因此在生产过程中,对环境的污染非常严重。
因此采用环境保护技术,比如建立解放阀、脱硫装置等设施,在炼焦排放、废气处理等方面,进行排放标准和污染防治工程,以保护环境。
总之,高硫煤的炼焦技术发展目前已经到了火热的地步,但要想使之持续发展,还需要开展更多的研究,提高技术水平,提高焦炭的质量和性能,并落实有效的环境保护措施,以确保高硫焦的可持续发展。
配高硫煤炼焦的研究

配高硫煤炼焦的研究随着工业开发不断推进,煤炭资源的日渐匮乏,高硫煤更是近年来受到了越来越多的关注。
高硫煤是指含硫量高的煤,也叫烯烃煤,具有自然气味,黑色发亮的碳质状,摩擦使其有明亮的火花,分类较混乱,堆放时容易自燃及火绒的消失等特点。
它的含硫量可以达到5%以上,它可以当作矿石有用的材料,因为它含有较多的类焦化煤、沥青质煤等。
由于高硫煤具有较多的特点,研究如何对其进行炼焦,能够起到经济及社会效益的双重作用,提高炼焦质量,以及提高炼焦产量。
因此,配高硫煤炼焦的研究就显得尤为重要。
高硫煤炼焦的主要技术有焦炼法和气化法。
在焦炼法中,矿石本身的含硫量会影响其炼焦效果,气化法中,由于矿石没有经过炼焦,因此,排放的焦炉烟就不会含有较高的锰元素。
同时,有关配高硫煤炼焦的研究,还受到了高温烧成技术、热点过滤、焦炉热解等技术的影响。
在高温烧成技术中,高温可以使高硫煤中的挥发性物质化合物完全分解,从而提高炼焦的产品率和质量;而在热点过滤技术中,其可以防止焦炉烟因高硫煤的烧结而污染空气;在焦炉热解技术中,其可以使煤中的有害物质完全热解掉,并将其转化为可以利用的炼焦热量。
配高硫煤炼焦的研究,还应该考虑到煤的性能,煤的级别等因素。
煤的性能主要指煤的热值、灰熔点、H2O等,而煤的级别主要指煤在供应过程中的混合比率,以及在炼焦过程中的物理结构改变。
这些因素都会直接影响到配高硫煤炼焦的结果,因此需要研究这些因素,以便确定最佳的配高硫煤炼焦方案。
最后,配高硫煤炼焦的研究,还受到烟气脱硫技术的影响。
烟气脱硫技术主要指对焦炉烟的排放,进行烟气脱硫的处理,以满足环保要求。
烟气脱硫技术可以有效减少作业中所产生的污染物,从而达到节能减排的目的。
总之,高硫煤炼焦是一项复杂而重要的工作,其研究需要综合考虑煤炭性质、焦炉烟、高温烧成技术等因素,并结合当地的环境条件来研究最佳的炼焦方案,以达到经济效益和社会效益的统一。
配高硫煤炼焦的研究,既能够有效利用高硫煤的资源,又能有效的减少环境的污染,为我们的社会发展增加了新的动力,是值得我们去探索和研究的一个领域。
掺烧高挥发分或高硫份煤种时需注意问题

1、在掺烧高挥发分煤种时,需重点防治制粉系统及周边着火,按专工要求严格控制磨煤机出口温度,发现该制粉系统有漏点必须及时处理并清理积粉,防治积粉着火。
2、掌握掺烧煤种的灰熔点特性,发现有结焦迹象时应采取调整措施。
如果燃料上煤时不同煤种进行掺混,由于混煤的灰熔点不具备加和性,最终上仓煤灰熔点可能会比两种单煤都低,可能形成低灰熔点的共熔体,造成受热面结焦。
(控制周界风开度)3、掺烧高硫煤时水冷壁高温腐蚀的影响(疑问:H2S为可燃气体,燃点260摄氏度,H2S+O2=SO2+H2O[O2充足],H2S+O2=S+H2O[O2不足],为什么炉内还会存在较高浓度H2S气体?)掺烧高硫煤时,水冷壁区域容易出现高温腐蚀。
燃用高硫煤时炉内存在较高浓度的H2S气体,与炉管发生反应形成腐蚀,如在壁面存在较高CO浓度,当炉管温度较高时,腐蚀速率加快。
特别是在高参数超临界锅炉上,能在较短时间造成水冷壁破坏,有的电厂已出现类似问题,被迫更换部分受热面,运行中应尽量调整配风方式降低该层燃烧器附近CO浓度。
4、由于高挥发份煤种在燃烧器处结焦概率偏大,继而引起粉管堵管。
运行中发现磨煤机风量下降,粉管压力上升或管壁温度下降迹象时,应全面检查磨煤机各参数,不应首先怀疑测点。
如果运行中磨煤机某一粉管堵管未及时发现,还可能会造成火焰中心偏斜,引起局部结渣。
运行中严格按专工要求开大高挥发份磨煤机周界风,防止着火点提前燃烧器结焦。
5、当掺烧高硫份煤时,烟气的酸露点温度降低(待验证:水蒸气分压力降低,对应的饱和温度下降,水的结露温度降低),当空预器冷端进口壁面温度低于酸露点温度时,空预器波纹板上产生结露,结露以后会对波纹板形成腐蚀,同时粘附飞灰,造成流道堵塞。
在冬季温度较低且掺烧高硫煤时空预器腐蚀及堵塞尤为严重,严重时引起引风机喘振以致影响锅炉稳燃。
燃煤硫份高,环境温度低时可开大热风再循环减少低温腐蚀,运行中应加强监视空预器差压,必要时采取增加空预器吹灰次数,尽量用后屏汽源。
掺烧高硫煤方案及措施

掺烧高硫煤方案及措施掺烧高硫煤方案及措施编制:初审:审核:批准:2015年10月22日掺烧高硫煤方案及措施根据公司经营形势需要及煤炭市场变化,在确保锅炉各种工况稳定燃烧的前提下,最大限度掺烧高硫煤种,燃煤掺烧是一项长期工作,也是精细化管理的内容之一,现就公司掺烧高硫煤种工作制订如下方案以及相关措施。
1.高硫煤特点我公司进厂高硫煤为贫瘦煤,该煤种具有低水分、低挥发份、高灰分、高硫份(含硫量1.2~2.4%)、热值接近设计煤质热值的特点。
因此掺烧该煤种后,锅炉着火稳燃性差、燃烬率偏低、烟气硫份高,对电除尘、输灰、排渣系统运行压力增较大。
2.掺烧方案2.1掺配比例控制2.1.1 4×300MW机组各炉A原煤仓不掺烧高硫煤,B、C、D、E 仓掺烧比例为从20%开始参烧。
2.1.2 2×660MW机组各炉A、B原煤仓不掺烧高硫煤,C、D、E 仓掺烧比例为从25%开始参烧。
2.1.3 掺烧工作按阶段进行,每个阶段掺烧按照4~5天进行观察试验,掺烧无问题后,掺烧比例提高5%进入下一个掺烧阶段;2.1.4 4×300MW机组各炉控制掺烧最高比例不超过30%,660MW机组控制掺烧最高比例不超过40%;3、掺烧管控与信息沟通3.1 掺烧比例由调度室具体管控,燃料运检部按照值长调度命令严格按照要求控制各阶段掺烧比例。
3.2 运行分部在掺烧高硫煤期间,应按照《掺烧高硫煤期间的技术措施》要求加强检查与调整工作,出现问题时及时将信息汇报值长,必要时降低掺烧比例或停止掺烧,按照《日配煤掺烧指标统计表》要求,各班组将当班期间将各机组的运行参数反馈到集控一单元班长处,由白班进行汇总,并将运行信息反馈生技部、调度室、运行分部。
3.3 生技部每个掺烧阶段组织召开高硫煤配煤掺烧会议,对配煤掺烧工作进行总结,针对存在的不足提出整改意见。
4.掺烧高硫煤期间的技术措施4.1锅炉运行的工作重点4.1.1接班后第一时间询问值长入炉煤煤质情况及配煤情况,并将本机组存在的缺陷以及影响稳定燃烧的隐患向值长汇报,同时向灰控、脱硫专业通报锅炉燃烧情况及煤质情况。
煤中硫的测定高温燃烧-酸碱滴定法实验讨论
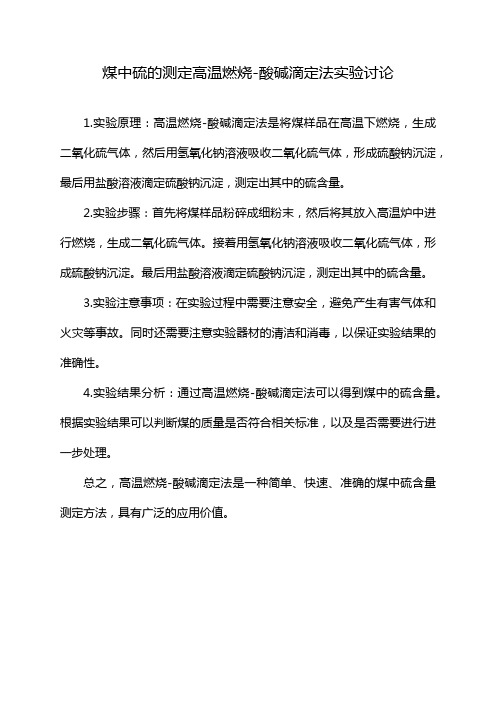
煤中硫的测定高温燃烧-酸碱滴定法实验讨论
1.实验原理:高温燃烧-酸碱滴定法是将煤样品在高温下燃烧,生成二氧化硫气体,然后用氢氧化钠溶液吸收二氧化硫气体,形成硫酸钠沉淀,最后用盐酸溶液滴定硫酸钠沉淀,测定出其中的硫含量。
2.实验步骤:首先将煤样品粉碎成细粉末,然后将其放入高温炉中进行燃烧,生成二氧化硫气体。
接着用氢氧化钠溶液吸收二氧化硫气体,形成硫酸钠沉淀。
最后用盐酸溶液滴定硫酸钠沉淀,测定出其中的硫含量。
3.实验注意事项:在实验过程中需要注意安全,避免产生有害气体和火灾等事故。
同时还需要注意实验器材的清洁和消毒,以保证实验结果的准确性。
4.实验结果分析:通过高温燃烧-酸碱滴定法可以得到煤中的硫含量。
根据实验结果可以判断煤的质量是否符合相关标准,以及是否需要进行进一步处理。
总之,高温燃烧-酸碱滴定法是一种简单、快速、准确的煤中硫含量测定方法,具有广泛的应用价值。
高硫煤煅烧
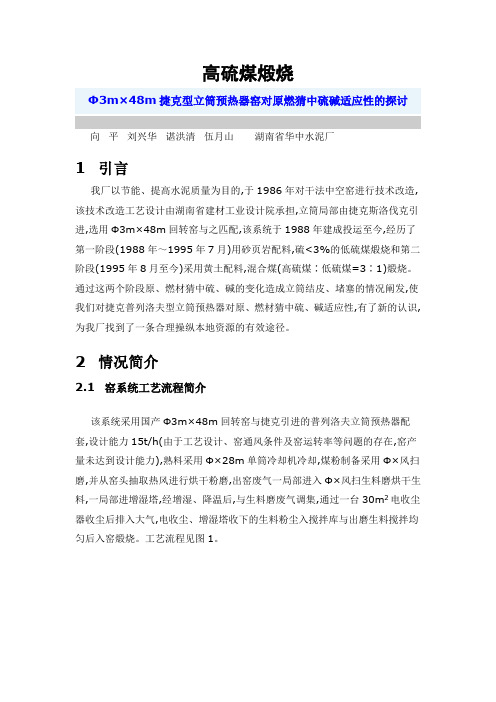
高硫煤煅烧Φ3m×48m捷克型立筒预热器窑对原燃猜中硫碱适应性的探讨向平刘兴华谌洪清伍月山湖南省华中水泥厂1 引言我厂以节能、提高水泥质量为目的,于1986年对干法中空窑进行技术改造,该技术改造工艺设计由湖南省建材工业设计院承担,立筒局部由捷克斯洛伐克引进,选用Φ3m×48m回转窑与之匹配,该系统于1988年建成投运至今,经历了第一阶段(1988年~1995年7月)用砂页岩配料,硫<3%的低硫煤煅烧和第二阶段(1995年8月至今)采用黄土配料,混合煤(高硫煤∶低硫煤=3∶1)煅烧。
通过这两个阶段原、燃材猜中硫、碱的变化造成立筒结皮、堵塞的情况阐发,使我们对捷克普列洛夫型立筒预热器对原、燃材猜中硫、碱适应性,有了新的认识,为我厂找到了一条合理操纵本地资源的有效途径。
2 情况简介2.1 窑系统工艺流程简介该系统采用国产Φ3m×48m回转窑与捷克引进的普列洛夫立筒预热器配套,设计能力15t/h(由于工艺设计、窑通风条件及窑运转率等问题的存在,窑产量未达到设计能力),熟料采用Φ×28m单筒冷却机冷却,煤粉制备采用Φ×风扫磨,并从窑头抽取热风进行烘干粉磨,出窑废气一局部进入Φ×风扫生料磨烘干生料,一局部进增湿塔,经增湿、降温后,与生料磨废气调集,通过一台30m2电收尘器收尘后排入大气,电收尘、增湿塔收下的生料粉尘入搅拌库与出磨生料搅拌均匀后入窑煅烧。
工艺流程见图1。
图1 窑系统工艺流程2.2 立筒的外型及热工参数普列洛夫型立筒预热器,由1个圆柱形直筒、一级旋风预热筒(2个)、一级旋风收尘筒(8个)组成,出窑废气经上升烟道(截面尺寸:1400mm×1400mm)切线进入立筒,进入立筒的气流呈螺旋上升,经中心风管进入旋风预热筒,出旋风预热筒废气,经旋风收尘筒收尘后,进入高温风机。
生料通过气力提升泵送入中心风管,经旋风预热筒预热后,与旋风收尘筒收下的生料一道进入立筒,经撒料器分散后,在气流离心力和自身重力的作用下,呈螺旋状自上而下运动,进行热交换,充实预热好的生料进入立筒锥部,经下料管进入窑内。
- 1、下载文档前请自行甄别文档内容的完整性,平台不提供额外的编辑、内容补充、找答案等附加服务。
- 2、"仅部分预览"的文档,不可在线预览部分如存在完整性等问题,可反馈申请退款(可完整预览的文档不适用该条件!)。
- 3、如文档侵犯您的权益,请联系客服反馈,我们会尽快为您处理(人工客服工作时间:9:00-18:30)。
④ 在靠近炉膛处实测各煤粉管风速风压,并进行调整,保证四角平
衡
燃用高硫煤的技术交流
五、低温腐蚀的原理
低温腐蚀的形成:燃料中的硫燃烧生成二氧化硫(S+O2=SO 2),二氧化硫在催化剂的作用下进一步氧化生成三氧化硫(2SO2+ O2=2SO3),SO3与烟气中的水蒸汽生成硫酸蒸汽(SO3+ H2O=H2SO4)。由于空预器中空气的温度较低,预热器区段的烟气温 度不高,壁温常低于烟气露点,这样硫酸蒸汽就会凝结在空预器受热 面上,造成硫酸腐蚀。
g) 火焰偏斜
燃用高硫煤的技术交流
四、针对高温腐蚀的原因采取以下措施
a) 燃烧假想切圆过大,造成飞边 ① 将#1、#3角一次风喷口与前后墙夹角由原来的45度改为48, 将#2、#4角一次风喷口与前后墙夹角由原来的37度改为40加 大对冲效果。 ② 开大周界风增强一次风刚度 ③ 减少一次风量来,降低着火热,有利于煤粉完全燃烧。 ④ 磨入口风压最大维持8.2kpa,必要时减小给煤量,一次风速 尽量维持在33m/s以下,通提高二次风箱压力,加快二次风 速 ⑤ 下摆燃烧器火嘴,减弱水平切圆动能
燃用高硫煤的技术交流
四、针对高温腐蚀的原因采取以下措施
b 煤的灰熔点低
① 加强配煤,掺混其它高灰熔点的煤
② 在燃煤中掺入石灰石或白云石,减少SO3的生成
燃用高硫煤的技术交流
四、针对高温腐蚀的原因采取以下措施
c)燃烧不完全,生成还原性气体CO多,使灰熔点降低 ① BC、CD两层二次风开大 ② 减少炉膛底部漏风,冷灰斗水封要严密,捞渣机水温要不高 于65度,减少水汽蒸发对底层磨燃烧的影响 ③ 提高二次风速及风量,改善水冷壁附近的补气条件,使煤粉 能完全燃烧,减少CO的生成 ④ 高负荷期间适当开大上部FF、OFA1、OFA2
华光电厂燃用高硫煤的技术交流
刘治中
燃用高硫煤的技术交流
一、燃用高硫煤的危害
高温腐蚀 管壁变薄,大面积爆管
高硫煤
省煤器、空预、电除、GGH低温腐蚀
金属Hale Waihona Puke 面腐烂燃用高硫煤的技术交流
二、高温腐蚀原理
高温积灰所生成的内灰层含有较多的碱金属,它与飞灰中的铁铝 等成分以及烟气中通过松散外灰层扩散进来的氧化硫的较长时间的化 学作用便生成碱金属的硫酸盐等复合物。熔化或半熔化状态的碱金属 硫酸盐复合会与再热器和过热器的合金钢会发生强烈的氧化反应,使 壁厚减薄应力增大以致引起管子产生里蠕变管壁更薄最后导致应损坏 而爆管。
e)炉膛断面热负荷过大,炉温过高使煤粉在靠近水冷壁未能凝固,造成
水冷壁结焦
① 发现水冷壁有对结焦时,应将单台磨出力降到55t/h以下 ② 加强对水冷壁的吹灰,可适当提高吹灰压力至2.5MPa,提高吹 灰效果,对吹灰缺陷及时处理,防止局部长时间结灰结焦造成 腐蚀 ③ 适当增大各层二次风量,能够除低水冷壁附近温度便于冷却灰 渣,但过大会影响到燃烧工况。
燃用高硫煤的技术交流
四、针对高温腐蚀的原因采取以下措施
d)炉温过高,在炉膛出口处灰未能凝固,粘在过热器上造成结焦结灰 ① 根据煤种内水,挥发份、发热量适当降低磨出口温度 ② 开大上部二次风 ③ 磨煤机细度控制在10—12% ④ 根据结焦情况适当接带负荷
燃用高硫煤的技术交流
四、针对高温腐蚀的原因采取以下措施
腐蚀
① 减少燃煤全水,加强配煤工作
② 运行中维持氧量在3—4%
③ 在燃煤中掺入石灰石或白云石,减少SO3的生成
燃用高硫煤的技术交流
七、针对低温腐蚀的原因采取以下措施
b)排烟温度低于烟气的露点 ① 空预冷端入口一、二次风温不低于15度,及时投入一二次暖风器 ② 空预吹灰由蒸汽吹改为冲击波吹灰器 ③ 如排烟温度低于105度,在没必要的情况下不吹空预 ④ 锅炉吹灰要完全疏水,防止带水 ⑤ 电除尘要利用停炉机会进行清灰,定期检查 ⑥ GGH要定期检查,吹扫时要对杂用空气罐放水,保证吹扫效果, 防止结灰造成腐蚀
燃用高硫煤的技术交流
四、针对高温腐蚀的原因采取以下措施
f) 空气量过剩,造成SO3的生成增多
① 运行中维持氧量在3—4%
② 燃煤发热量降低后,磨运行台数增加,相应的一次风量也增加, 此时应适当减少二次风量,以维持总风量不变,磨运行台数减少
后应适当增加二次风量
③ 在保证磨煤机的干燥出力和输粉的同时,尽量降低一次风量,增 加二次风量。
低温腐蚀常发生在空预器、电除尘极板以及GGH上。
燃用高硫煤的技术交流
六、低温腐蚀原因分析
a) 燃烧生成的SO3增多,与水蒸汽反应生成的H2SO4增 多,造成对金属的腐蚀 b) 排烟温度低于烟气的露点
燃用高硫煤的技术交流
七、针对低温腐蚀的原因采取以下措施
a) 燃烧生成的SO3增多,与水蒸汽反应生成的H2SO4增多,造成对金属的
燃用高硫煤的技术交流
八、总结
在这里只是抽象地分析了燃用高硫煤的若干问题,希望大家 给予补充和指正,在实际燃用此煤种时发现其它问题,我们会根 据实际状况进行一定的调整,确保机组稳定运行安全发电。
燃用高硫煤的技术交流
四、针对高温腐蚀的原因采取以下措施
g) 火焰偏斜
① 从停炉后观察水冷壁结焦情况上看,主要集中要#4角的前、侧墙
附近,在短吹221和230最能掉大焦,不难发现火焰偏向#4角,所 以提意将各台磨的#1、#2、#3角月牙挡板关小
② 从DCS画面显示A侧的二次风箱压力要比B侧的小,导致#3、#4角
燃用高硫煤的技术交流
三、高温腐蚀原因分析
高温腐蚀通常伴有结焦或结灰的发生,所以我们从结焦入手 分析其原因如下:
a) 燃烧假想切圆过大,造成飞边
b) 煤的灰熔点低 c) 燃烧不完全,生成的还原性气体CO过多,导致灰熔点降低 d) 炉温过高,在炉膛出口处灰未能凝固,粘在过热器上造成结焦结灰 e) 炉膛断面热负荷过大,炉温过高使煤粉在靠近水冷壁未能凝固,造 成水冷壁结焦 f) 空气量过剩,造成SO3的生成增多