安钢_300棒材机组控制轧制系统
棒材机组物料跟踪控制系统的研制与开发

2009年10月中国设备工程棒材机组物料跟踪控制系统的研制与开发李永强(安阳钢铁集团公司第一轧钢厂,河南安阳455004)摘要:介绍300棒材机组基本情况,重点阐述机组的物料跟踪控制系统情况、控制流程以及对生产的影响。
关键词:控制;物料跟踪;研制中图分类号:TP2文献标识码:B安阳钢铁集团公司第一轧钢厂φ300mm 棒材机组是一条年产70万t 的半连轧生产线,生产规格为φ20~φ28mm 的圆钢和螺纹钢。
轧件从加热炉的装钢到出炉、轧制、剪切、冷床、头部筛选、打包等各工序,采用自动化物料跟踪控制。
各点控制设备分别是:装钢、出炉安装一套微机和红外线测温仪。
连轧区安装一套1#切头、事故碎断飞剪;在预精轧前安装了一套活套装置;冷床前设有2#倍尺飞剪,通过PLC 模拟运算,实现倍尺分段;精整区安装头部筛选和下卸钢控制PLC 等。
整套物料控制系统是以连轧主PLC 为核心,通过以太网通信方式构建的,信息传递方式见图1。
一、物料跟踪信息传递原理1.加热炉装钢、出炉检测系统系统采用一台微机和红外线检测仪进行控制。
坯料入炉前根据炉号、支数、重量输入微机,出炉时由红外线热金属检测仪对出炉钢的支数进行统计,并与输入的支数校对,检测出的各种参数信息,通过以太网传输到连轧PLC 中进行数据处理。
检测采样原理见图2。
2.1#飞剪控制系统1#飞剪系统采用GE90-30作为控制核心,硬件由热金属检测仪、GE90-30PLC 、电机和各保护信号检测装置组成。
钢料经500轧机和1#飞剪剪前轧机轧制后,被热金属检测仪检测到,信号传送到PLC 输入模块中,进行数据处理,并将数据传送到主PLC 中,以待后期使用。
3.连轧主PLC 控制系统采用GE90-70控制系统,应用实时通信网络,通过以太网采集各监测点的数据信息,内部进行运算,结果送到各站所,进行物料控制。
主PLC 还将各可编程控制器及人机接口计算机联结在一起。
人机接口计算机系统以画面形式向操作人员提供系统工作状态显示,并能输入及修改控制数图1物料跟踪控制系统信息传递网络文章编号:1671-0711(2009)10-0061-03自动化工程61中国设备工程2009年10月据。
Φ300mm棒材机组启停式飞剪改进

曲线等各种功能 , 可非常容易采集到电机 电流 , 将轧机 电机电流 读到 P C中 , L 程序见 图 3 。电机 电流和电机额定 电流 的 3 %进 0 行 比较 , I ≥I , 0 3 6动作 , 当 1 2时 M 8 1 轧机已经含 钢 , 出含 钢信 输
为 21 .m。
安钢第一 轧钢厂 q 0 m b O m棒材 机组是一条 半连 轧生产线 3 ( 1, 图 )生产 q2 ~b 2 b 2 q3mm的圆钢和螺纹钢 筋 , 启停式飞剪 ( 以 下简 称飞剪 ) 安装在 4、 #5 轧机 之间 , 主要 作用是切 头 、 切尾 和 事故 碎断 , 防止劈头 钢对后道轧 机咬入 , 当后道轧 钢 出现故 或 障时切 断轧件 ,防止扩大事故 。飞剪电机型号 Z F - 5 — 2 T S35 4 、
囝 设 篁 与 修 2 1o 苗 理 维 0 1 1N2
— 型 —
』塞 一 —
三 、 决 措施 解
1 入 3、 引 4 主机含钢电流信号 3、 4 主机含钢信号分别与 1、 2 热检信号联 合 ,共同参 与 飞剪剪切控制 ,含钢信 号根据轧机咬钢前后电机 电流值变化进
1 飞剪 P C 分 L, 别 与 l、 检 2 热 感光信号共 同控 制 飞剪 剪 切 , 3
主 机 含 钢 信 号
图 3 采集含钢信号程序
和 1热检 、 4 主机含钢信号和 2 热检均必须两个 同时有信号才 认为信号正常 , 两个 同时无信号才认 为信号丢失 , 中任意一个 其
顶 检查处理 。 采用手 动球 阀, 比旋塞 阀操作方便 、 灵活 , 密封性能
也较好 。 1 . 优点
1-6安钢一轧厂减少300机组轧机工艺事故时间

能顺利咬入轧机。并确认,在此,导板的尺寸设计不能仅按常规经验数据进行,
因此判定导板尺寸小是导致4#不进的主要原因。
确认结果: 要因
确认3:导辊高度低
5月13日小组成员杜永军对4#进口导辊与3#料型尺寸的配合上进行了调 查分析,并依据实际情况绘图分析如下 :
68
3#料型
导辊
制图人:杜永军
时间:2009年5月
(194-2.83×3)÷23.80415=7.79(分钟/万吨钢);
09年1-3月份轧机万吨钢工艺事故时间为:263÷23.80415=11.05(分钟/万吨钢) 那么,万吨钢工艺事故时间将为:11.05-7.79=3.26(分钟/万吨钢) 我们将本次课题目标设定为:万吨钢工艺事故时间达3.26分钟/万吨钢以下。
制表人:杜晓晖
90 80 70
时间/分钟
时间:2009年4月
结论2:进入2009年1月份4# 轧机工艺事故时间突然增多, 初步原因是车间于2009年1月 开发了φ32圆钢、螺纹钢,并
60 50 40 30 20 10 0 1 2 3 4 5 6 7 8 月份 9 10 11 12 1 2 3
投入生产,随着φ32圆钢、螺
2008年《提高棒材产品成材率》获全国优秀质量成果二等奖 2009年《30圆钢设计开发》获冶金行业优秀质量管理成果奖 文化程度 专科 专科 本科 本科 本科 本科 职称、职务 高级技师、组长 助工、副组长 助工、副组长 工程师、组员 高级工程师、组员 助工、组员 组内分工 方案设计 方案实施 数据收集、分析 方案实施 方案实施 数据收集、分析
15 11.05
时间/分钟
10 3.26
现状 目标
5 0
现状
目标
安钢高线机组预精轧机控制系统的优化
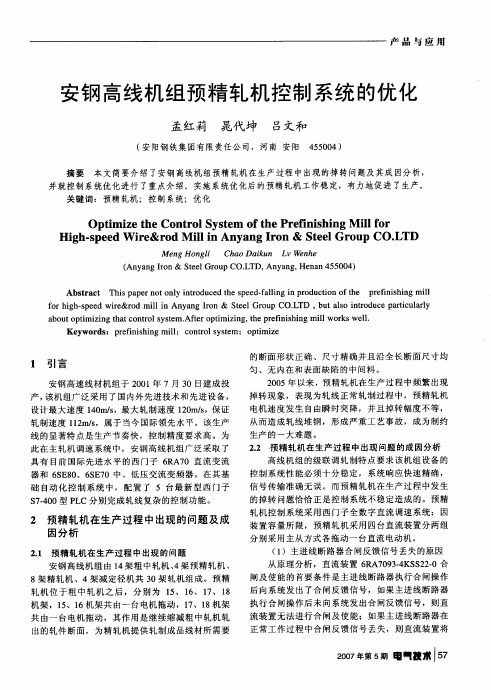
57一 型PLC 分别完成轧线复杂的控制功能。 400
2 预精轧机在生产过程中出现的问题及成
因分析
. 2 1 预精轧机在生产过程中出现的问题 安钢高线机组由 1 架粗中轧机、 架预精轧机、 4 4 8 架精轧机、4 架减定径机共 3 架轧机组成。预精 0 轧机位于粗中轧机之后,分别为 巧、1 、1 、1 6 7 8 机架,巧、1 机架共由一台电机拖动,1 、1 机架 6 7 8 共由一台电机拖动,其作用是继续缩减粗中轧机轧 出的轧件断面,为精轧机提供轧制成品线材所需要
2。 第期 气 京5 。 。 电 玻 }7 7年
产品与应用
会在尽可能短时间内进行分闸及封闭使能信号; 如 果主进线断路器在正常工作过程中合闸反馈信号发 生了瞬时丢失现象,预精轧机调速系统在作出反应 之前合闸反馈信号即已恢复,预精轧机直流调速系 统有可能发生瞬时失速,即发生了预精轧机掉转现 象,最终造成轧线堆钢严重工艺事故。 ( 2) 直流调速系统的原因 如果预精轧机直流调速装置调速参数设定不当 造成预精轧电机的动态性能差,不能完全按照需要 来控制动态过程的电流或转矩的话,同样会造成预 精轧机掉转现象。 如果预精轧机直流调速系统采取主从控制方式的 两套装置间不能保持严格同步,也会造成电机掉转。 ( 3) 预精轧机速度反馈信号系统原因 预精轧机速度反馈检测是由高精度增量型编码 器完成,如果预精轧机速度反馈检测脉冲信号在外 部电磁干扰下发生了信号多发,结果导致系统发生 深度负反馈,也会造成预精轧机掉转现象的发生。
A b s t r 8 Ct
1
引言
安钢高速线材机组于 200 年 7 月 3 日建成投 1 0 产, 该机组广泛采用了国内外先进技术和先进设备, 设计最大速度 1 0耐5, 4 最大轧制速度 12 而5, 0 保证 轧制速度 11 而5,属于当今国际领先水平。该生产 2 线的显著特点是生产节奏快,控制精度要求高。为 此在主轧机调速系统中,安钢高线机组广泛采取了 具有 目前国际先进水平的西门子 6RA70 直流变流 器和 6SE80、6SE70 中、低压交流变频器。在其基 础 自动化控制系统中,配置了 5 台最新型西门子
Φ300mm棒材机组倍尺飞剪自动控制系统
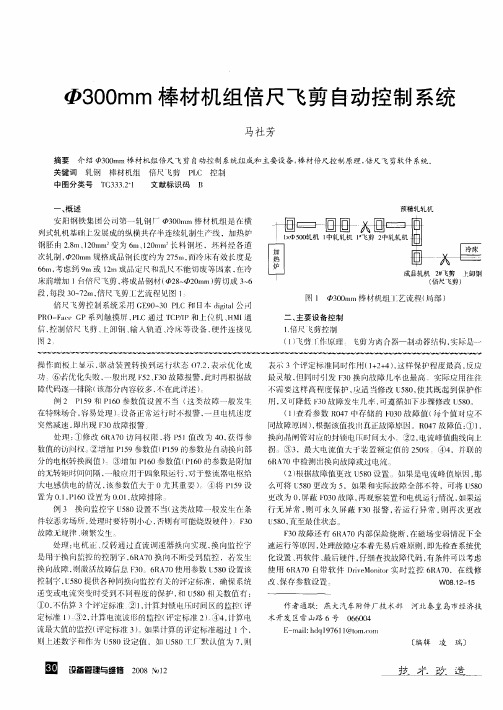
马社 芳
摘要 关键词 介绍 q30 m棒 材机组4 X - 剪 自动控 制系统组成和主要设备,  ̄0 m  ̄ . - E 棒材倍尺控制原理 , 尺飞剪软件系统 倍 轧钢 棒材机组 倍尺 剪 P C 控制 L
B
预精轧 轧机
中 图分 类 号 F 3 3 G 3. l 2
网 l q3 0 50 mm捧 材 机组 j 艺 流 程 ( J : 局部 ) 二 、 要 设备 控 制 主 1 尺 剪控 制 . 倍 () 1飞剪 作 原 理 剪 离 合器 一 制 动器 结 构 , 际是 一 实
P O F c P系 列触 摸 屏 ,I R — aeG P C通 过 T PI 上 f 、 I C/ P和 机 HM 通
在特殊场合 , 容易处理 )设备正 运仃时/报警 , 旦电机速度 : { 一
突然 减 速 . 现 F 0 障 报 警 即 3故
处理 : 修改 6 A 0访 问权 限 . P 1 R7 将 5 值改 为 4 , 0 获得 参 数值的访『仅 。 增加 P 5 口 】 19参数值( l9的参数是 F动换 部 P5 : I 分的电枢转换 值 ) 一@增加 P 6 参数值 ( l0的参数是附加 10 P6
的无 转 矩 时 间 间隔 , 般 廊 片 于 四象 限运 行 . 于整 流 器 电 怄给 一 j 对 大 电感 供 电的 情 况 , 参 数 值 大 于 0 该 尤 重 要 )
置 为 01P 6 ., l0没 置 为 0O , 障 排定值的 20 5 %:④4 ,并联 的
行无异 常 , 町永久屏蔽 F 0报警 , 运行 异常 , 则 3 若 则再 次更改
U 8 , 至 最 佳状 态 。 50 肓
安钢热连轧板型控制系统攻关

安钢热连轧板型控制系统攻关一、攻关的背景和意义热连轧板型控制系统是指通过控制轧机工作过程中的参数,使板材在轧制过程中达到预期的板型要求。
其主要目的在于提高产品品质,减少生产成本,提高生产效率。
而安钢在攻关热连轧板型控制系统的过程中,旨在提高产品的板形精度和一致性,提高生产效率和降低轧制成本,满足市场对高品质钢材的需求。
二、技术的难点和挑战在热连轧板型控制系统的攻关过程中,安钢面临着多方面的技术难点和挑战。
需要解决轧机设备的控制精度不高、板形控制效果不理想的问题。
还需要克服板材温度、厚度、形变等因素对板型控制的影响,提高板材的成型精度和一致性。
还需要提高轧机的自动控制水平,实现轧机工作过程参数的自动调节和优化。
三、攻关的具体措施和方法为了解决热连轧板型控制系统的难点和挑战,安钢采取了一系列具体措施和方法。
对轧机设备进行改造升级,提高设备的控制精度和稳定性。
加强板材成型过程中的温度、厚度、形变等参数监测和控制,利用先进的传感器和控制算法实现板型控制的精确度。
还建立了一套完善的数据分析和预测系统,通过大数据分析和人工智能技术,提前预测板型控制的关键参数,实现轧机工作过程参数的自动优化。
四、攻关取得的成果和效果经过长期的攻关和努力,安钢在热连轧板型控制系统方面取得了一系列的成果和效果。
在产品的板形精度和一致性方面取得了显著的提升,产品的成型质量得到了有效的保障。
生产成本得到了有效的控制和降低,生产效率得到了显著的提高。
产品的市场竞争力得到了有效的增强,市场占有率得到了明显的提高。
五、下一步的工作和展望虽然在热连轧板型控制系统的攻关过程中取得了一定的成果和效果,但是仍然面临着一些问题和挑战。
下一步,安钢将继续加大研发投入,加强轧机设备的改造升级,进一步提高板型控制系统的精度和稳定性。
还将加强数据分析和预测系统的建设,引进更先进的控制算法和人工智能技术,实现热连轧板型控制系统的智能化和自动化。
展望未来,安钢的热连轧板型控制系统将不断迈向更高的水平,为钢铁生产的科学化和智能化发展贡献更大的力量。
棒材生产线自动控制系统优化与应用

后极 限运 行 ,那 坯 料 是不会 准 确运 送 到 出炉辊 道 上 的,所 以必 须 改 变推 钢机 的前极 限,来 使它 满足 步进 梁 为2 8 0 mm步距 ,同时 也能 将 坯料 准确 的送到 出炉 辊道 上 。 通过 查 阅 资料 ,计 算 出推 钢机 的 前极 限 ,把 表达 式 写入程 序 。 步进 梁 的步 距 写入 程序 的 时候 ,将 它 当做 一个 变 量来 写 , 以后 不 论 改什 么 步距 , 只要将 所 要 步距 输入 这个 变 量 ,推钢 机 就会 计算 出一 个与 之 匹配 的前 极 限 ,使 得 坯料 能准 确 的从 出炉辊 道 出去 。 3 . 2 P 1 主操 台增  ̄ I D A S曲线显 示 的改造 在P 1 台安 装 一 台客户 机 ,放置 到P 1 操 作 工所 正对 的粗 轧位 置 。 通过 网线和 网 卡接 入 到三 级 网络拓 扑 结构 中 。该 客户 机装 有 英文 版 的DAS 系统 ( 实时 数 据 采集 系 统 )软 件 ,C H0 . c H7 八个 开 关 量 用 于检 测 粗轧 前及 粗 轧各 架 次 的咬钢 信 号 ,八个 模 拟量 用于 检测 粗 轧 各架 次 的 电流情 况 。正 常过 钢过 程 中P 1 操 作工 通 过方 便 的观 察粗 轧 机组 各架 次 电流 情 况便 可 准确 的判 断 各架 轧机 的运 行 情况 。该系 统 还具 有 历史 记录 功 能 ,每个 班 次接 班后 可 以将 自己 的作业 时 间进 行 保存 ,一旦 有 故障 发生 了意外 堆钢 ,可 以调 出历 史 曲线分 析 故障 原 因 ,为查 明故障 和设 备维 护 提供 了解 决方 向 。 3 . 3 三号 剪的 剪切 程序 优化 改造 ( 1 )原 三 号剪 程 序 只 能设 五 根倍 尺 ,第 五剪 后 倍尺 长度 自动 按第 五 剪设 定 的剪 切长 度剪 切 ,满 足 不 了生产 要 求 ,使得 最后 一 支 倍尺 切成 定 尺后 必将 出现 小 齐尺 。 ( 2 )每 根钢 坯 的长 度 都不 一 样 ,有 误 差 ,细 小 的误 差造 成 最 后 一支 倍尺 出现 小 齐尺 ,尤其 在轧 制 中2 5 以下螺 纹钢 和 圆钢 时 , 由 于 原料 长度 的较 小 波动 ,造 成 最后 倍尺 波 动较 大 ,最 后一 支倍 尺 长 度不 稳 定 ,出现 小齐 尺 的几 率很 大 。 ( 3 )料 型 的变 化 ,随着 料 型 的变 化 ,尤其 生 产 中2 5 以 下螺 纹 钢和 圆钢 ,有时 也会 使得 最 后一 支倍 尺 出现 小齐尺 。 综 上所 述如 果 将倍 尺 设定 根数 由五剪 增加 到 八剪 ,即对 三 号剪 倍尺 优化 可 解决 以上 问题 。
棒材半连轧自动化系统的应用

棒材半连轧自动化系统的应用在安钢第一小型轧钢厂棒材半连轧线电气系统中,用全数字直流调速装置DV-300、PLC、监控机构成数字直流调速系统,最终实现自动化、调速数字化、自动网络化,达到了提高轧制速度、缩短停机检修时间、节电的目的,经济效益显著。
标签:直流调速自动化网络化0 引言安钢第一轧钢厂棒材轧制原来采用模拟系统,用电路板来控制,指针显示,信号不稳定,显示不准确,调节精度不够,造成尺寸波动,现采用数控半连轧,粗轧由单独的直流电机拖动,中、精轧12架轧辊构成连轧,轧制时要求各机架间秒流量相等。
本套半连轧系统采用GE系列,由全数字直流调速装置DV300对电机形成双闭环调速系统,GE series 90-70经PROFIBUS现场总线与各机架数控装置及PLC 相联系,完成轧线的通讯、逻辑控制、故障报警及连锁控制、速度连调的控制。
由cimplicity通过PLC经Ethernet网进行上位机画面监控,完成轧线状态监视及轧线参数的设定,如轧制规格、轧机速度等。
1 用全数字化直流调速装置DV300构成传动系统的原则和步骤1.1 DV300的硬件组成①根据工艺要求,主回路方案选用直流调速装置。
本设备选用GE DV300系列全数字直流调速装置。
②按电机参数选择调速装置的容量。
据本12主传动电机参数选直流调速装置型号参数为:DV3006KDV1800…及6KDV2350…。
③根据电网相数、电机特点、装置位置、检测元件、控制方式设置拨码及输入、输出。
在本调速系统中,DV300使用了三块板子:R-TPD3:完成电枢励磁触发、脉冲使能、数据运算及输出等功能,可根据电网相数(S8)、速度检测方式(S4、S5、S6、S20、S21、S22、S23、S27、S28)、磁场电流(S14)、等设置相应的拨码;TBO:完成模拟数字数据量采集;报警输出;SBI-PDP-32:完成与上下机架及PLC的通讯(如是单机架调速,无通讯,可不选);1.2 DV300调速原理本系统采用双闭环直流调速系统,其一是由DV300内置的电枢电流调节器和电流互感器构成的电流环,其二是由DV300内置速度调节器和安装在直流电机轴上的光电脉冲编码器构成的速度环。
安钢300棒材机组自动打捆系统

安钢 3 0 0棒材机组 自动打捆 系统
目前采用 高性能 的 自动打捆 设备提 高钢铁 产品 的包 装质 量, 既是 钢铁企 业 的迫 切任 务 , 也是 用户 对钢 铁行 业 的要求 。
河 南 安 阳钢 铁 集 团 股 份 有 限 公 司 第 一 轧 钢 厂 3 0 0棒 材 机 组 精整设 备安装 1 、 2 检 验 台架 , 其中 1 检验 台架 处理 部分 9 m
工 作 人 员 非法 操 作 。 莱 钢 铁路 信号 微 机 监 测 系 统 主 要有 以下 创 新 点 :① 应 用 有
4 2 4 D激光测距 仪 、 4 3 7 I I 系列电能质 量分析仪 、 8 0 5振动 烈度 ( 点检 ) 仪 三款新近上市 的新品。
福禄 克公 司亚 太 区总 裁 黄 宜 植 先 生 致词 ,表 达 了福 禄 克 对
主机 之 间采 用 C A N总 线联 接 , 一 台 采集 分 机 可 同时 监 测 多 个 对 象。
[ 武钢重工集 团机制公 司离休 办蔡承万供稿
区 红钢 城 4 3 0 0 8 0 3 0
武汉市青 山
福 禄 克 举 办创 新 产 品发 布 会 推 出 多款 业 内首 创 新 品
本刊讯 记者张卫宁 2 0 1 2年 1 1 月2 2日, 福禄克测试仪 器( 上海 ) 有限公 司在北 京奥莱室 内攀岩馆举 办 2 0 1 2年福禄克 创新产 品发布会 。福禄克结合攀岩这项极 限运动 , 表达 了“ 挑 战 无极 限” 的产品设计研发理念和打造富有创新精神 的企业愿景 ,
区域 占地 面 积 约 1 2万 平 方 公 里 , 并 预 留进 一 步发 展 的条 件 。武 钢 将 按 照 世 界 一 流 标 准精 心设 计 , 采 用世 界 一 流 技 术 , 引人 世 界
安钢_300棒材机组控制轧制系统
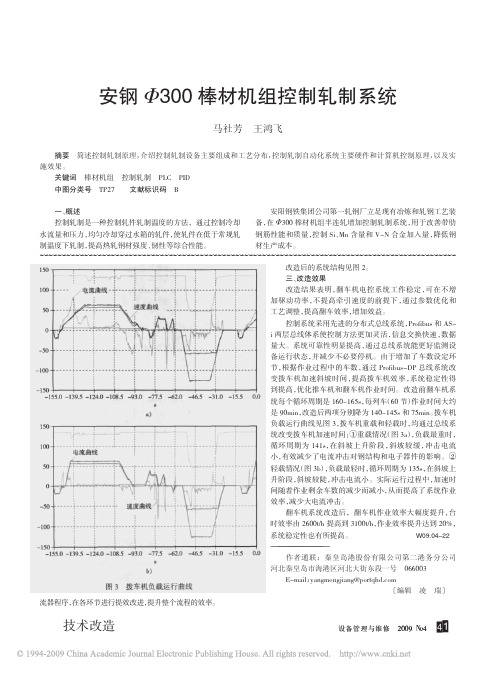
设备管理与维修2009№4流器程序,在各环节进行提效改进,提升整个流程的效率。
改造后的系统结构见图2。
三、改造效果改造结果表明,翻车机电控系统工作稳定,可在不增加驱动功率,不提高牵引速度的前提下,通过参数优化和工艺调整,提高翻车效率,增加效益。
控制系统采用先进的分布式总线系统,Profibus 和AS-i 两层总线体系使控制方法更加灵活,信息交换快速,数据量大。
系统可靠性明显提高,通过总线系统能更好监测设备运行状态,并减少不必要停机。
由于增加了车数设定环节,根据作业过程中的车数,通过Profibus-DP 总线系统改变拨车机加速斜坡时间,提高拨车机效率,系统稳定性得到提高,优化推车机和翻车机作业时间。
改造前翻车机系统每个循环周期是160~165s ,每列车(60节)作业时间大约是90min ,改造后两项分别降为140~145s 和75min 。
拨车机负载运行曲线见图3,拨车机重载和轻载时,均通过总线系统改变拨车机加速时间:①重载情况(图3a ),负载最重时,循环周期为141s ,在斜坡上升阶段,斜坡较缓,冲击电流小,有效减少了电流冲击对钢结构和电子器件的影响。
②轻载情况(图3b ),负载最轻时,循环周期为135s ,在斜坡上升阶段,斜坡较陡,冲击电流小。
实际运行过程中,加速时间随着作业剩余车数的减少而减小,从而提高了系统作业效率,减少大电流冲击。
翻车机系统改造后,翻车机作业效率大幅度提升,台时效率由2600t/h 提高到3100t/h ,作业效率提升达到20%,系统稳定性也有所提高。
W09.04-22———————————————作者通联:秦皇岛港股份有限公司第二港务分公司河北秦皇岛市海港区河北大街东段一号066003E-mail :yangmengjiang@〔编辑凌瑞〕图3拨车机负载运行曲线一、概述控制轧制是一种控制轧件轧制温度的方法,通过控制冷却水流量和压力,均匀冷却穿过水箱的轧件,使轧件在低于常规轧制温度下轧制,提高热轧钢材强度、韧性等综合性能。
棒材机组自控系统特点

( )住 宅设 计 规范 } B 09- 19 (03年版 ) 6 . 3《 G 506 99 20 第 .2 5 条 : 宅供 电系统的设计 , 住 应符合下列基本安 全要求 : 每幢住宅 的总电源进线 断路器 , 应具有漏电保护功能 。 ()高层 民用建筑 设计 防火 规范} B04-9 (05年 4《 G 505 520 版) 9 .条: 第 .1 高层建筑内火灾危险性大、 5 人员密集等场所宜设 置漏电火灾报警系统。 ( )住宅建筑规范 ̄ B06-20 第 8 .条 : 5《 G 538 05 .2 住宅供配电 5
维普资讯
棒材机组 自控 系统m棒材机组生产线 的设备组成 , 控 系统结构 , 0r a 自 以及运行状况。 关键 词 棒材机组 自 控系统 特点
中图分类号 T 2 P7
一
文献标识码
N L1 L L 2 3
( )低压配电设计规范 ̄ B 05-9 第 4 .条: 2《 G 504-5 A1 接地故障 - -
保护的 设置应能防止^ 身间接电击以及电气火灾 、 线路损坏等事 故。接地故障保护电器的选择应根据配电系统的接地型式 , 移动
式、 手握式或固定式电气设备的区别, 及导体截面等因素经技术 以 经济比较确定。 4 . 条: 第 .2 4 1 为减少接地故障引起的电气火灾危险
配置 见 图 1 。
30 m棒材 机组生 产线 l 架 轧机 为半 连续 式小 型轧 钢 0r a 1 机, 分为粗 、 、 中 精轧三个机组 , 粗轧 5o轧机走三个 道次 , 0 原 料由3 m提高到 6 中轧 30 m, 7 高刚度轧机采用连续式布置 , 精 轧高刚度机采用横列布置。 使用三段 连续式加热炉 , 冷料的额定 产量为 1 t 。 5 / 装出料 方式 为端进端 出, 排和双排装料。轧 0h 可单 线上设有 1 台切头和事故碎段剪 , 台倍尺飞剪 , 1 中轧机组机架 问设置水 箱 , 用于降低棒材温度 。采用步进齿条式冷床 , 其有效 面积为 30 : 3m , 在输出侧设有齐头辊道和下卸钢装置 。
安钢一轧厂300机组的PLC系统设计

中图分类号 :P 1 T 35
文献标识码 : A
文章编号 :0 6 4 1 (0 0)2 0 2 — 2 10 — 3 12 1 2 — 19 0
的 中 央 处 理 单 元 ( P , 可 编 程 序 控 制 器 不 仅 可 进 行 逻 辑 控 制 而 C U) 使 0 引 言 可编程序控制器早期主要应用于开关量的逻辑控制 , 故其最初 且还 可 以 对模 拟量 进 行 控 制 。 了使 这 一 新 型 工 业控 制 装 置 的生 产 为 被 称 为 可 编 程 逻 辑 控 制 器 ( rga mal o i o t l r,简 称 和发展标准化 ,美 国电气制造商协 会于 18 Porm be g C nr l ) L c oe 9 0年将它正式命名为可 P C 随着 技 术 的 发 展 , 些 厂 商 采 用 微 处理 器 作 为可 编程 控 制 器 编程 序控 制器 (rga a l L g o t l r , L。 一 Pormm be o i C nr l )简称 P 。 c oe C 可编程序控制器是一种 数字运算操作 的 电子系统 , 为在工业 专 环 境 下 应 用 而 设计 的 , 采 用 了可 编程 序 的 存 储 器 , 来 在 其 内部 它 用 作 者简 介 : 宝 利 ( 9 9 , , 南 安 阳人 , 州 大 学 机 械 工 程 硕 士 , 南 省 张 16 一)女 河 郑 河 安 阳职 业 技 术 学 院 高级 教 师 , 期 从 事机 械 、 长 电气 控 制技 术 等 方 面 存储执行 逻辑运 算、 顺序控 制 、 时、 定 计数和 算术运 算等操 作的指 令 , 通 过 数 字 和 模 拟量 的 输 入 和 输 出 , 制 各种 类 型 机 械 的 生 产 并 控 的教 学 和 研 究 工 作 。
安钢棒材机组钢捆成形器的自动化控制

() 5 自动控制程 序的设计 : 工程技术人员通 过对 工艺要求和机械装置动作原理的了解分析 , 行编 自 制控制程序 , 实现对整 个系统 的控 制 。控制原 理为 : 当 1 收集槽收集 到规定 的根数后 , 号 通过对 1 夹紧 号 器操作, 夹紧器 自动夹紧, 通过限位器停止在夹紧状 态 , 钢捆进行 扎捆后 , 对 自动松开通过 限位器停在松 开 状 态 。钢 捆输 送 辊 道 把 钢捆 送 到 2 成 形槽 位 号 置, 到位后 2 号收集槽 3 个成形器同时动作 , 形成圆 形 钢捆 扎 捆 后 吊 出。 整个 过程 除扎 捆 为人 工操 作 外, 其余实现了自 动控制, 操作简单方便。
钢捆 钢 捆 成 形 器 P C 变频 器 L
变频 器 实现钢捆 成 形 的 自动控 制 70 4 K C 变频器 , R A 4 —5 — H 分三段控制打 捆 输 出辊 道 。每 段辊 道 安装 l 台 3 k 1 . W齿 轮 电动 7 安钢第一轧钢厂 30 m机组生产 2 ~ 0m 0 机, 通过变频器控制辊道速度。 3rm圆 钢 和 螺 纹 钢 , 产 线 为 1× 504× 2 a 生 0/ ( ) 械安 装 : 捆成 形 装置 是 本 次设计 改造 1机 钢 403× 302× 301 30半 连 轧/ 歹 式 0/ 2/ 01 × 0 横 0 的重点工作 , 只对此设备 的结构 、 动作原理及安装 棒材生产线 , 年产钢材 8 万t 0 。精整产品包装方式 是人 工 使 用 Z 一93A型组 合 式气 动 打捆 机 对 棒 进行了分析。钢捆 自动夹紧的核心技术为 自动夹 K 1/2 材进 行 钢带 捆 扎 。气 动打 捆 机提 供 的拉 力 和钢 带 紧成形装置 , 它主要由大臂 、 小臂 、 限位 、 液压缸和 所 能 承 受 的拉 力 均 有 限 , 法对 钢 捆 进 行 拉 紧 成 支撑架等组成。此装置在 2 无 个液压缸的驱动下 , 完 成大臂与小臂动作 , 可夹 紧 西 0 一 ̄50 m棒材 30 0m 型, 打捆 后 的棒 材 钢捆 松散 无 形 , 吊装 和运 输 中 在 极 易 断带 散 捆 , 钢 材 产 品 的储 藏 和 运 输 造成 了 钢捆 ( 图 1。 给 见 ) 根据工艺要求 , 生产 9 2 —1m定尺棒材 , 要安 不便 , 影响了产品在市场的形象 , 降低 了产品的竞 台 分别安装在 l 号检验台 争力 。为此 , 第一钢轧厂在 3 0 m机组 自行设 装 5 自动夹紧成形装置 , 0m 计安装了棒材成形 自动夹紧装置和电气 自动控制 收集辊道西侧 , 号收集辊道东西两侧和中间,号 2 2 系统 , 它是集机械 、 电气 、 液压控制为一体的 自动 检验台收集辊道东侧。 () 2 电气 自动控制 : 电气控制选用了SM TC I A I 化控制系统 , 其动作准确可靠 , 包装质量标 准高。 7 30P C 该 L 结构小巧 , 可靠性 高且运行速 20 年 1 对精 整后 续工 程改 造时 , 08 月 对钢 材成捆 包 s —0 L , P C 度快 , 性能价格 比高 , 编程方便 , 以在线修 改和 可 装 系统进 行 了配套 系统 改造 。 编程 , 可以与其他设备进行通讯 , 并能与多种设备 直接相连等优点。针对现场工艺布置 , 收集辊 如 2 机械 与 电气 的设 计与 安装 液压阀 、 气动挡板等设备 , 依据工艺条件编制 这次改造包括机械和电气改造两部分 , 机械 道 、 控制程序, 完成从收集到成型的 自 动控制。P C L 模 方 面是分 别对 收集 台架 、 装 置 、 收集 对齐 输送辊 道 、 所示 。 活动 对 齐挡 板 、 紧装 置 、 捆输 送 辊道 等设 备 安 块 配置如 表 l 夹 打 () 3 电气传统系统 : 采用三菱F — 70 4 K C R A 4—5 — H 装, 械 安 装 重 点 是 自制 的 钢 捆 自动 夹 紧成 形 装 机 分 组控制 1 3 收集辊道 。该变频器 ~段 置 。电气 方面 是利 用 SMA I 7 30P C实现 自 I TCS— 0 L 变频器 , 3 动 运输 、 自动 夹紧形 成成形 钢捆 , 以及 对齐辊 道 、 对 安装 简 单 、 据 可靠 和 性 能稳 定 , 能 与 SM TC 数 并 I A I 7 oP c 各种信号 、 数据 齐挡板 、 收集装置等电气控制。电气传动系统采用 s —30 L 等外部设备进行通讯 ,
安钢300棒材机组颚板的改进
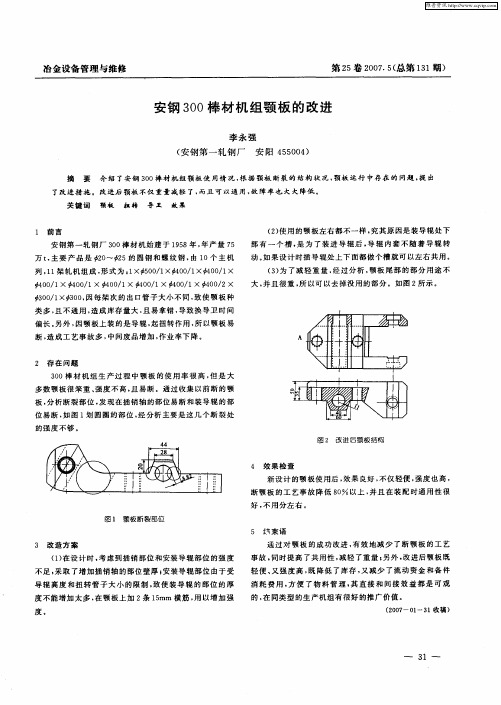
位易 断 , 图 1 圆 圈 的部 位 , 分 析 主 要 是 这 几 个 断 裂 处 如 划 经
的强 度 不 够 。
图 2 改 进 后 颚板 结构
4 效 果检 查
新 设 计 的颚 板 使 用 后 , 果 良好 , 仅 轻 便 , 度 也 高 , 效 不 强 断 颚板 的 工 艺 事 故 降 低 8 以上 , 且 在 装 配 时 通 用 性 很 O 并
维普资讯
冶 金设 备管 理 与维修
第2 5卷 2 0 . ( 第 1 1 ) 0 75总 3期
安钢 3 0棒材 机 组 颚 板 的 改进 0
李 永强
( 安钢第 一 轧钢 厂
安 阳 4 50 ) 5 0 4
摘 要 介 绍 了安 钢 3 0棒 材 机 组 颚 板 使 用情 况 . 据 颚板 断 裂 的 结 构 状 况 , 0 根 颚板 运 行 中存 在 的 问题 , 出 提
 ̄ 0 /  ̄ 0 /  ̄ 0 /1X  ̄ 0 /  ̄ 0 /  ̄ 0 / 4 0 1X 4 0 1X 4 0 4 0 1X 4 0 1X 4 0 2X
 ̄ 0 / X ̄ 0 , 每 架 次 的 出 口管 子 大 小 不 同 . 使 颚 板 种 30 1 30因 致 类 多 , 不 通 用 , 成 库 存量 大 . 易 拿 错 , 致 换 导 卫 时 间 且 造 且 导 偏 长 。 外 , 颚 板 上 装 的 是 导 辊 , 扭 转 作 用 , 以颚 板 易 另 因 起 所 断 , 成 工 艺 事 故 多 , 间 废 品增 加 , 业 率 下 降 。 造 中 作
好 , 用分 左 右 。 不
图 1 颚 板 断裂 部 位
5 结 束语
3 改 造 方 案
通 过 对 颚板 的成 功 改 进 , 效 地 减 少 了断 颚 板 的 工 艺 有 事故 , 同时 提 高 了共 用性 , 轻 了 重 量 ; 外 . 减 另 改进 后 颚 板 既
安钢高速线材电气自动控制系统

安钢第一炼轧厂高速线材连轧机组采用国内外先进技术与装备,原料采用热装热送工艺,加热炉为引进日本中外炉关键燃烧装置的步进梁式加热炉,具有加热质量好,成本低的特点。
全车间共有30架轧机,其中粗、中轧平-立交替14架,45度预精轧4架,精轧机8架,减定径机8架,设计最大速度140m/s,最大轧制速度120m/s,保证轧制速度为112m/s,全线设6个活套,3台飞剪和在线自动测径装置,产品公差±0.10mm;全线采用控制轧制和控制冷却新工艺,有5套控冷水箱,大风量强冷式延迟型散卷保温罩进行低温轧制强制冷却,实现索氏体处理,又可实现缓慢冷却。
设计能力的40万吨/年,主要产品为光面盘条线材:Φ5.5~Φ20mm,螺纹带肋线材:Φ6.0~Φ16mm。
生产钢种有:碳素结构钢、优量碳素结构钢、中高碳钢、合金结构钢等8个钢种。
电气自动控制系统的构成该系统配置5台SIEMENS公司的S7-400系列PLC,设有3个操作站,加热炉区、轧机区、精整区各1个,另外还在主电室设有工程师站。
每个站均配有SIEMENS公司的PIII工控机,操作面板采用SIEMENS公司的PMU,各站操作系统为中文WindowsNT4.0,监控画面采用美国Intellution公司的FIXDMACS软件编制。
现场的润滑、液压系统以及轧线各区域配有59台ET200M,主传动采用SIEMENS公司的6RA70系列产品,交流辅传动采用SIEMENS 公司的6SE70变频器,每套传动装置均配有一块CBP通信模板,用作6RA70和6SE70调速装置与PROFIBUS-DP相连的接口板。
操作站、工程师站、PLC之间的通信采用工业以太网,通信介质采用同轴电缆,PROFIBUS-DP主要完成PLC与6RA70、6SE70、WINCC以及远程ET200M 之间的数据信息通信功能,PROFIBUS-DP的通信介质采用工业屏蔽双绞线。
这条轧线配备了水平较高的电气自动化控制系统,其配置如图1所示。
φ300 mm棒材机组设备扩容后工艺优化

φ300 mm棒材机组设备扩容后工艺优化王晓燕;靳熙;杜永军【摘要】针对φ300 mm棒材机组局部设备设备扩容后,出现的部分设备能力富余,未扩容部分依然存在能力不足,工艺与设备能力匹配度不高的问题,通过对工艺设计的优化,消除生产工艺中的设备薄弱环节,达到增产增效的目的.【期刊名称】《河南冶金》【年(卷),期】2012(020)006【总页数】2页(P45-46)【关键词】设备扩容;工艺优化;增产增效【作者】王晓燕;靳熙;杜永军【作者单位】安阳钢铁股份有限公司;安阳钢铁股份有限公司;安阳钢铁股份有限公司【正文语种】中文0 前言随着钢铁行业棒材连轧技术快速发展,自动化程度越来越高,同时市场竞争日趋激烈,本着节约资源、降低成本和效益最大化的原则,安钢第一轧钢厂为进一步挖掘棒材半连轧机组工艺潜力,加快新技术更新换代应用步伐,对Φ300 mm棒材半连轧机组现有生产工艺进行分析研究,通过均衡优化加热、轧制等工艺参数,解决现场瓶颈问题,机组产能得到进一步提升,减少了金属消耗和能源消耗,取得了良好的效果。
1 工艺概况安钢Φ300 mm棒材机组是一条50年代末期建成并投产的横列式棒材机组。
近年来,多次进行技改革新、深挖潜力,尤其是2003年实施大修改造后,采用半连续式布置,工艺布局为:1×Φ500 mm/7×Φ400 mm/3×Φ320 mm,加热设备为端进端出连续推钢式加热炉,设计加热能力为70 t/h,炉子有效尺寸为22.62 m×6.38 m。
生产规格为:Φ20 mm ~Φ32 mm,改造后年产达到60万。
Φ300 mm机组生产工艺流程如图1所示。
图1 Φ300 mm机组工艺流程近几年通过逐步对主机进行扩容(扩容前后对比见表1),进行提速增产,目前年产达到90余万吨。
2 存在问题2.1 设备能力使用不均衡主机扩容后2#、3#主机功率富裕量大,随着成品速度的提升,转速过高在Ф22 mm规格表现的更加突出,而且由于整体规格的增大,生产Ф25 mm规格时1#飞剪的最大剪切速度已经超过额定速度0.7 m/s;4#孔型在大规格轧制时呈立椭圆,头部变形不好控制,容易带耳子,造成成品缺陷。
300机组500轧机断辊分析及控制措施
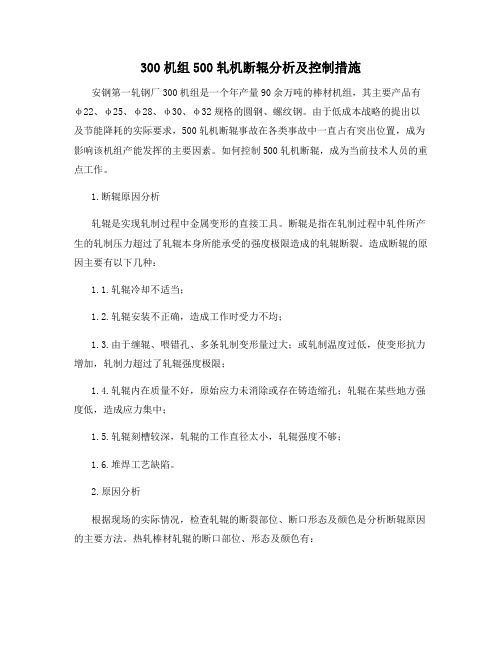
300机组500轧机断辊分析及控制措施安钢第一轧钢厂300机组是一个年产量90余万吨的棒材机组,其主要产品有φ22、φ25、φ28、φ30、φ32规格的圆钢、螺纹钢。
由于低成本战略的提出以及节能降耗的实际要求,500轧机断辊事故在各类事故中一直占有突出位置,成为影响该机组产能发挥的主要因素。
如何控制500轧机断辊,成为当前技术人员的重点工作。
1.断辊原因分析轧辊是实现轧制过程中金属变形的直接工具。
断辊是指在轧制过程中轧件所产生的轧制压力超过了轧辊本身所能承受的强度极限造成的轧辊断裂。
造成断辊的原因主要有以下几种:1.1.轧辊冷却不适当;1.2.轧辊安装不正确,造成工作时受力不均;1.3.由于缠辊、喂错孔、多条轧制变形量过大;或轧制温度过低,使变形抗力增加,轧制力超过了轧辊强度极限;1.4.轧辊内在质量不好,原始应力未消除或存在铸造缩孔;轧辊在某些地方强度低,造成应力集中;1.5.轧辊刻槽较深,轧辊的工作直径太小,轧辊强度不够;1.6.堆焊工艺缺陷。
2.原因分析根据现场的实际情况,检查轧辊的断裂部位、断口形态及颜色是分析断辊原因的主要方法。
热轧棒材轧辊的断口部位、形态及颜色有:2.1.当轧制温度偏低或压下量偏大使变形抗力增大时,轧辊可能在孔型的工作辊径上折断,这时的断裂口是剪应力断口。
剪应力断口为灰白色断口。
2.2.当发生误操作,轧件进入较小规格孔型,轧件进入辊环或缠辊,造成扭转力矩大于轧辊本身强度时,轧辊在辊身与辊径接触处被扭断,这时的断裂口是扭应力断口。
扭应力断口为灰白色断口。
2.3.当轧辊磨损不均匀、受不均匀冷却的交变作用,造成局部缺陷并逐渐扩大时,轧辊发生疲劳断裂。
断裂部位不一定在轧制道次的孔型内,也可能在相邻孔型内,这时的断裂口为疲劳断口。
因疲劳断辊的断口为深褐色断口。
2.4.轧机缺水断辊。
当轧机供水不足或缺水造成轧辊局部温度升高,使轧辊局部晶粒粗大,强度降低,造成断辊。
当轧机缺水,局部温度升高,使轧辊局部材质晶粒粗大,立即给水后急剧冷却,材质经淬火后晶粒变细,产生拉应力,这时断裂部位在轧机应力集中处。
轧钢棒材生产线的PLC控制系统(软件设计)

摘要在自动化控制领域,PLC是一种重要的控制设备。
目前,世界上有200多厂家生产300多品种PLC产品,应用在汽车(23%),粮食加工(16.4%)、化学/制药(14.6%)、金属/矿山(11.5%)、纸浆/造纸(11.3%)等行业。
上世纪80年代至90年代中期,是PLC发展最快的时期,年增长率一直保持为30%—40%。
在这个时期,PLC在处理模拟量能力、数字运算能力、人机接口能力和网络能力得到大幅度提高,PLC逐渐进入过程控制领域,而且在某些应用上取代了在过程控制领域处于统治地位的DCS系统。
现今,PLC已经具有通用性强、使用方便、适应面广、可靠性高、抗干扰能力强,编程简单等特点。
在可预见的将来,PLC在工业自动化控制特别是顺序控制中的主导地位,是其他控制技术无法取代的。
本文介绍了S7-200 PLC控制系统在轧钢棒材生产中系统中的应用,着重描述了系统配置及冷床控制功能。
最后通过,通过测试和实验的成功表明本文研究成果的可行性和可靠性。
关键词:PLC控制系统;轧钢;棒材生产;冷床顺序控制;ABSTRACTIn the area of Automation Control,Programmable Logic Controller is an important control equipment.Currently,there are over 200 manufacturers that produce more than 300 varieties of PLC products,which are now applied in auto industry(23%),grain processing(16.4%),chemical&pharmacy(14.6%),metals&mine(11.5%),paper pulp and paper making(11.3%) and many other industries.The PLC develop fastest during the 1980s and the mid-1990s,the value of gross output of PLC increase at the speed of 30%-40% per year.In this period,the PLC technology has developed rapidly in the field of analogy processing,digital quantity operation,man-machine interface,network service,gradually the PLC entered the field of process control because of these,and in some fields the PLC has token the place of Distributed Control System-the once king in the field of process control.And now,the PLC has been equipped with good commonality,ease of use,wide applicability,high reliability,good anti-interference,easy programmability and some other advantages.In the foreseeable future,the PLC will dominate the industrial automation and control,especially Sequence Control,and it can't be replaced by other control technologies.This article will introduce how s7-200 PLC system works in rolling steel bar production,and it focus on describing System Configuration and cooling bed stly,tests and experiments show that the research results this article describes are practical and reliable.Key words:PLC control system; steel rolling; bar production;sequence control of the cooling bed;目录第一章绪论 01.1 课题研究背景和意义 01.2 国内外发展状况与发展趋势 (2)第二章可编程控制器简介 (9)2.1 可编程控制器的发展历史 (9)2.2 PLC的特点 (10)2.3 PLC的工作原理 (11)2.4 PLC的体系结构 (12)2.5 PLC控制程序设计 (15)第三章轧钢棒材生产线冷床控制系统的硬件设计部分 (17)3.1 硬件组成及控制要求 (17)3.2 PLC输入、输出的安排 (19)第四章系统软件设计部分 (25)4.1 系统流程设计图 (25)4.2 顺序功能图 (25)4.3 PLC程序 (26)第五章结论 (32)致谢 (33)参考文献 (34)第一章绪论钢棒材是经济建设中必不可少的一种材料,钢棒材品种繁多,广泛应用于汽车制造、电气机械、船舶制造工业、大跨度桥梁、高层建筑等社会生活各个方面。
- 1、下载文档前请自行甄别文档内容的完整性,平台不提供额外的编辑、内容补充、找答案等附加服务。
- 2、"仅部分预览"的文档,不可在线预览部分如存在完整性等问题,可反馈申请退款(可完整预览的文档不适用该条件!)。
- 3、如文档侵犯您的权益,请联系客服反馈,我们会尽快为您处理(人工客服工作时间:9:00-18:30)。
设备管理与维修2009№4流器程序,在各环节进行提效改进,提升整个流程的效率。
改造后的系统结构见图2。
三、改造效果改造结果表明,翻车机电控系统工作稳定,可在不增加驱动功率,不提高牵引速度的前提下,通过参数优化和工艺调整,提高翻车效率,增加效益。
控制系统采用先进的分布式总线系统,Profibus 和AS-i 两层总线体系使控制方法更加灵活,信息交换快速,数据量大。
系统可靠性明显提高,通过总线系统能更好监测设备运行状态,并减少不必要停机。
由于增加了车数设定环节,根据作业过程中的车数,通过Profibus-DP 总线系统改变拨车机加速斜坡时间,提高拨车机效率,系统稳定性得到提高,优化推车机和翻车机作业时间。
改造前翻车机系统每个循环周期是160~165s ,每列车(60节)作业时间大约是90min ,改造后两项分别降为140~145s 和75min 。
拨车机负载运行曲线见图3,拨车机重载和轻载时,均通过总线系统改变拨车机加速时间:①重载情况(图3a ),负载最重时,循环周期为141s ,在斜坡上升阶段,斜坡较缓,冲击电流小,有效减少了电流冲击对钢结构和电子器件的影响。
②轻载情况(图3b ),负载最轻时,循环周期为135s ,在斜坡上升阶段,斜坡较陡,冲击电流小。
实际运行过程中,加速时间随着作业剩余车数的减少而减小,从而提高了系统作业效率,减少大电流冲击。
翻车机系统改造后,翻车机作业效率大幅度提升,台时效率由2600t/h 提高到3100t/h ,作业效率提升达到20%,系统稳定性也有所提高。
W09.04-22———————————————作者通联:秦皇岛港股份有限公司第二港务分公司河北秦皇岛市海港区河北大街东段一号066003E-mail :yangmengjiang@〔编辑凌瑞〕图3拨车机负载运行曲线一、概述控制轧制是一种控制轧件轧制温度的方法,通过控制冷却水流量和压力,均匀冷却穿过水箱的轧件,使轧件在低于常规轧制温度下轧制,提高热轧钢材强度、韧性等综合性能。
安阳钢铁集团公司第一轧钢厂立足现有冶炼和轧钢工艺装备,在Φ300棒材机组半连轧增加控制轧制系统,用于改善带肋钢筋性能和质量,控制Si 、Mn 含量和V-N 合金加入量,降低钢材生产成本。
安钢Φ300棒材机组控制轧制系统马社芳王鸿飞摘要简述控制轧制原理,介绍控制轧制设备主要组成和工艺分布,控制轧制自动化系统主要硬件和计算机控制原理,以及实施效果。
关键词棒材机组控制轧制PLCPID 中图分类号TP27文献标识码B!!!!!!!!!!!!!!!!!!!!!!!!!!!!!!!!!!!!!!!!!!!!!!!技术改造賱跁设备管理与维修2009№4二、控制轧制设备1.工艺布置针对Φ300棒材机组连轧设备分布,设计、布置控制轧制设备。
根据轧制规程,生产Φ25mm 、Φ28mm 、Φ32mm 规格螺纹钢,总共轧制11个道次,不用5#、6#轧机,因此为进一步降低大规格棒材轧制温度,在K5与K4轧机间设置控制轧制水箱,在K5与K6轧机间设置2500mm 机架间水箱,这样既保证降温效果,又能充分利用控轧水箱后的长度进行返温,确保后面轧制过程顺利进行。
2.控制轧制设备设备包括:①机架间水箱和控轧水箱,其中冷却器、气吹喷嘴、出口导管均设置在水箱中。
②控制阀门和管路。
③检测仪表。
④自动控制系统。
⑤介质供应系统。
由于切头剪位于水箱前,为避免棒材黑头进入轧机,必须合理配置水冷器和阀门,尽量减少头部避让的长度,其中机架间水箱配2节水冷器,控轧水箱配3节水冷器,每节水冷器各配1个手动截止阀和气动截止阀。
总水管处安装1个电动调节阀,调节水量。
控制轧制设备分布见图1。
三、自动控制系统自动化系统由PLC 系统、检测系统、冷却过程计算机控制系统组成,电气连接见图2。
1.PLC 系统采用GE90-30PLC ,基本配置见表1,PLC 系统接收、执行工艺过程计算机的设定,控制冷却规程,采集、检测、处理仪表信号并上传检测仪表输出信号,全程跟踪控轧过程。
(1)电源模块是PLC 内部电路工作电源,选择型号为IC693PWR321,电源功率300W ,开关稳压电源。
(2)CPU 模块型号为IC693CPU364,和通信卡集成在一起,该CPU 不仅具有AAUI 口,还增加1个10BaseT 口。
(3)Genius 总线控制器模块选择型号为IC693BEM331,作用是操作台和主机架进行网络通信,实现操作台开关、按钮和指示的I/O 控制,具有传输速率高,抗干扰能力强等特点。
(4)I/O 模块选择型号有:①4输入、2输出模拟量混合模块IC693ALG442。
②4输入模拟量输入模块IC693ALG221。
③16点开关量输入模块IC693MDL645。
④16点继电器输出模块IC693MDL940。
(5)编程软件配置。
梯形图编程采用GE Fanuc Series 90PLC 传统编程软件(可与Windows NT 和2000兼容的图形化开发工具)。
2.检测系统检测系统主要有:①钢温检测,T1、T2分别检测轧件进控轧水箱前和出控轧水箱后热钢温度,放置在1#飞剪后和K4轧机进口前。
②冷却水系统检测,压力、水温和流量检测分别采用PTO 、WTO 和F ,均安装在总进水管。
③控冷过程跟踪,使用HMD1、HMD2检测热钢,安装位置同T1、T2。
④控轧水箱内安装湍流管,是单侧下冲水。
3.冷却过程计算机控制系统计算机根据控制轧制过程数学模型,计算、分析控制轧制,在轧件达到控轧装置前给出控制的优化设定值,因此,必须在生产原始数据输入后立即进行控制冷却的设定计算,并将计算值下载至PLC ,并根据PLC 采集的参数进行水冷控制模型(图3)的自学习。
表1PLC 基本配置图3水冷控制模型HMD ———热金属检测器T ———红外辐射温度检测仪S ———气动截止阀F ———电磁流量计C ———电动调节阀WTO ———供水水温传感器PTO ———供水压力传感器K —轧机图1控制轧制设备图2控制轧制自动化系统电气连接Sv —设定值Pv —当前值Mv —控制值PWR321CPU364BEM331GBCALG442ALG221MDL645MDL740PS1234567中央机架(R0)····技术改造賱跂YD31125CNC6大型数控滚齿机陈时权摘要介绍YD31125CNC6大型数控滚齿机所具有的先进技术、结构特点、性能参数。
关键词数控滚齿机研制特点中图分类号TG61+2文献标识码B一、概述重庆机床集团公司研制的用于风力发电行业大模数齿轮加工的YD31125CNC6大型数控滚齿机已完成了大模数齿轮的加工试切,工件参数为模数20mm,齿数25齿,齿宽140mm,外径540mm,一刀切加工精度达到GB10095-2001IT7级,标志着为风力发电行业齿轮加工量身打造的大型全数控滚齿机的研制已取得成功。
近年来,随着风力发电设备、机车、矿山机械、减速机、船舶等重型机械的迅猛发展,这些行业大型齿轮加工机床的需求越来越大,要求也越来越高,特别是大型齿轮加工机床的精度更能受到用户的青睐。
而目前国内市场上多为以美国格里森—普发特、德国利伯海尔等世界一流数控齿轮机床厂家为代表生产的CNC机床,价格非常昂贵。
因为其投入大,收效慢,所以很难满足国内大多数用户的需求。
YD31125CNC6大模数少齿数全数控滚齿机,是重庆机床集团公司2007年启动开发的大型机床新产品。
其开发主要针对我国工程机械、船用减速箱、重型汽车、电梯等行业的齿轮加工的需求。
机床装刀直径、进给行程、刀架刚性等方面达到国外同类机床水平。
在用户的特殊要求下,还可进行硬齿面加工。
机床为六轴控制(一个主轴、五个伺服轴),四轴联动。
以电子链完成切齿时的分齿运动,差动补偿,进给补偿。
机床采用最短的传动链及可靠的传动方式,具有紧凑、高效、可靠的特点。
加工工件的最大模数为24mm,具有很高的动、静刚性。
该机床技术水平处于国内领先地位,价格仅约为同类进口机床的一半,更好地满足了广大齿轮制造用户的需求,同时为以后开发其他数控大型机床,奠定良好的基础和试验条件。
迄今为止,在全国普通机床销售同比增幅回落的大形势下,该系列大型数控滚齿机受风力发电行业利好拉动,累计合同定单已愈亿元,重庆机床集团公司正全力以赴使大型数控机床产业化工程全面实现。
该机床为重庆机床(集团)有限责任公司自主开发,具有完全自主知识产权。
二、机床主要结构特点和先进技术该机床为大模数少齿数、大规格全数控滚齿机,能滚切加工圆柱齿轮、蜗轮、链轮等,实现直齿和斜齿的加工。
该机床采用GB/T8064-1999《数控滚齿机精度》。
1.结构特点(1)机床采用大立柱移动,工作台固定的立式布局方式。
直(1)控制轧制数学模型M V=K p×[S V-P V]+K iT i 乙Edt+K d×dEdt(1)式中K p———比例常数K i———积分常数K d———微分常数T1、T2将温度变换为4~20mA信号输入进PLC,PLC比较该数据和目标值,根据水量、压力等参数,采用PID控制,调整K p、K i、K d,控制调节阀开口度,控制进入水箱的水流量,使轧件在水箱内得到均匀有效的冷却。
控制轧制根据不同钢种控制水冷后的钢温,一般通过水箱后钢温控制在830~900℃。
(2)其他控制。
①水阀控制,轧件到达HMD1,HMD1检测到有钢,PLC得到信号,打开液压阀,通过HMD1后,PLC得到无钢信号,关闭液压阀。
②避头让尾控制。
为保证轧件头部钢温,轧件能够顺利咬入后架轧机,轧件头部不必穿水,即轧件头部出控轧水箱后,再开启水阀门,使轧件头部避开水。
在HMD1发出红钢信号后,延时一段时间开启阀门,无红钢信号后,延时一段时间关闭阀门。
四、实施效果实施控制轧制后,基本解决了钢筋表面起泡问题,铁素体晶粒度得到细化,晶粒度由7级提高到8级,在不改变合金成分的情况下,HRB335和HRB400螺纹钢筋屈服强度分别提高了26MPa和37MPa。
在保证钢材性能基本不发生变化的情况下,可通过降低合金元素含量降低生产成本,HRB335和HRB400螺纹钢的Si、Mn含量均由0.55%和1.45%分别降低0.15%,V-N 合金含量由0.045%降低0.10%,每年可获经济效益1470万元。
W09.04-23———————————————作者通联:安阳钢铁集团公司第一轧钢厂一车间河南安阳市455004E-mail:mashefang@〔编辑凌瑞〕乙乙乙乙乙乙乙乙乙乙乙乙乙乙乙乙乙乙乙乙乙乙乙乙乙乙乙乙乙乙乙乙乙乙乙乙乙乙乙乙乙乙乙乙乙乙乙设备与技术賱跅设备管理与维修2009№4。