IBL 汽相回流焊优越性
回流焊原理以及工艺

回流焊原理以及工艺1.什么是回流焊回流焊是英文Reflow是通过重新熔化预先分配到印制板焊盘上的膏装软钎焊料,实现表面组装元器件焊端或引脚与印制板焊盘之间机械与电气连接的软钎焊。
回流焊是将元器件焊接到PCB板材上,回流焊是对表面帖装器件的。
回流焊是靠热气流对焊点的作用,胶状的焊剂在一定的高温气流下进行物理反应达到SMD的焊接;之所以叫'回流焊'是因为气体在焊机内循环流动产生高温达到焊接目的。
回流焊原理分为几个描述:(回流焊温度曲线图)A.当PCB进入升温区时,焊膏中的溶剂、气体蒸发掉,同时,焊膏中的助焊剂润湿焊盘、元器件端头和引脚,焊膏软化、塌落、覆盖了焊盘,将焊盘、元器件引脚与氧气隔离。
B.PCB进入保温区时,使PCB和元器件得到充分的预热,以防PCB突然进入焊接高温区而损坏PCB和元器件。
C.当PCB进入焊接区时,温度迅速上升使焊膏达到熔化状态,液态焊锡对PCB的焊盘、元器件端头和引脚润湿、扩散、漫流或回流混合形成焊锡接点。
D.PCB进入冷却区,使焊点凝固此;时完成了回流焊。
双轨回流焊的工作原理双轨回流焊炉通过同时平行处理两个电路板,可使单个双轨炉的产能提高两倍。
目前, 电路板制造商仅限于在每个轨道中处理相同或重量相似的电路板。
而现在, 拥有独立轨道速度的双轨双速回流焊炉使同时处理两块差异更大的电路板成为现实。
首先,我们要了解影响热能从回流炉加热器向电路板传递的主要因素。
在通常情况下,如图所示,回流焊炉的风扇推动气体(空气或氮气)经过加热线圈,气体被加热后,通过孔板内的一系列孔口传递到产品上。
可用如下方程来描述热能从气流传递到电路板的过程,q = 传递到电路板上的热能; a = 电路板和组件的对流热传递系数; t = 电路板的加热时间; A = 传热表面积; ΔT = 对流气体和电路板之间的温度差我们将电路板相关参数移到公式的一侧,并将回流焊炉参数移到另一侧,可得到如下公式: q = a | t | A | | T双轨回流焊PCB已经相当普及,并在逐渐变得复那时起来,它得以如此普及,主要原因是它给设计者提供了极为良好的弹性空间,从而设计出更为小巧,紧凑的低成本的产品。
气相回流焊如何避免空洞缺陷

气相回流焊如何避免空洞缺陷1.焊点中空洞(气泡)形成的机理从本质上来说,任何SMT焊点中出现空洞都是因为在焊接回流的融化过程中,焊球中的气体没有及时排放出去造成的。
影响焊点中空洞形成的原因是多方面的,如锡膏、PCB焊盘表面处理方式、回流曲线设置、回流气氛、焊盘设计、微孔、盘中孔等在这里我们重点讨论,回流气氛对空洞形成的影响。
回流环境中的氧气会加速PCB焊盘表面金属的氧化,导致焊盘的可焊性降低。
当在铜或镍金属上焊接时,这种现象更为明显。
由于可焊性差、润湿不良的位置更容易吸收过量的助焊剂,因此更容易生成空洞缺陷。
2.消除焊点中空洞(气泡)的措施消除或降低焊点中空洞比例采取的措施可以归纳如下:(1)均热时间足够,焊接媒介热传递性能卓越,保证焊点中的气体在焊点固化之前能够得到充分的释放;(2)在无氧环境中回流(焊接);(3)焊膏在回流(焊接)之前在空气中的暴露时间不易过长,印刷、贴片、回流焊接尽快完成,不易停留过长时间;(4)在选择PCB表面处理方式时考虑对空洞的影响;(5)保证焊点和PCB焊盘有良好的可焊性;(6)焊料粉的颗粒尺寸不易过小,除非有特殊需要;(7)对于有盘中孔、微孔的焊盘改善其可焊性、在贴片之前预填充工艺,设定合适的回流曲线使盘中孔、微孔中的溶剂、助焊剂挥发掉;(8)保证PCB镀孔工艺的质量,避免镀层表面出现多孔性缺陷。
3. 气相回流焊是如何消除或减少焊点中的空洞缺陷的?气相回流焊利用加热气相液的方式形成无氧、热传递性能良好的蒸汽回流(焊接)区,使焊点中的气体,在回流过程中充分的挥发掉。
目前行业中的气相回流焊主要分为垂直槽式和喷射法(即真空气相回流焊)。
主要区别在于:垂直槽式气相回流焊,在一个槽里中,把气相液加热到沸点,在气相液上方形成稳定饱和的惰性气体回流(焊接)区。
喷射法(真空气相回流焊),先用传送带把PCB送到回流(焊接)腔中,然后密封起来,抽真空。
首先加热回流腔底部和侧面的加热部件,然后把一定数量的气相液喷入回流腔中,当气相液接触到回流腔的底部和侧面后,就会沸腾并形成蒸汽回流(焊接)区。
回流焊无铅焊接的特点和对策

回流焊无铅焊接的特点和对策一、无铅焊接技术的现状无铅焊料合金成分的标准化目前还没有明确的规定。
IPC等大多数商业协会的意见:铅含量<0.1-0.2WT%(倾向<0.1%,并且不含任何其它有毒元素的合金称为无铅焊料合金。
1、无铅焊料合金无铅化的核心和首要任务是无铅焊料。
据统计全球范围内共研制出焊膏、焊丝、波峰焊棒材100多种无铅焊料,但真正公认能用的只有几种。
(1)目前最有可能替代Sn/Pb焊料的合金材料最有可能替代Sn/Pb焊料的无毒合金是Sn基合金。
以Sn为主,添加Ag、Cu、Zn、Bi、In、Sb等金属元素,构成二元、三元或多元合金,通过添加金属元素来改善合金性能,提高可焊性、可靠性。
主要有:Sn-Bi系焊料合金,Sn-Ag共晶合金,Sn-Ag-Cu三元合金,Sn-Cu系焊料合金,Sn-Zn系焊料合金(仅日本开发应用),Sn-Bi系焊料合金,Sn-In和Sn-Pb 系合金。
(2)目前应用最多的无铅焊料合金三元共晶形式的Sn95.8\Ag3.5\Cu0.7(美国)和三元近共晶形式的Sn96.5\Ag3.0\Cu0.5(日本)是目前应用最多的用于再流焊的无铅焊料。
其熔点为216-220℃左右。
由于Sn95.8\Ag3.5\Cu0.7无铅焊料美国已经有了专利权,另外由于Ag含量为3.0WT%的焊料没有专利权,价格较便宜,焊点质量较好,因此IPC推荐采用Ag含量为3.0WT%(重量百分比)的Sn-Ag-Cu焊料。
Sn-0.7Cu-Ni焊料合金用于波峰焊。
其熔点为227℃。
虽然Sn基无铅合金已经被较广泛应用,与Sn63\Pb37共晶焊料相比无铅合金焊料较仍然有以下问题:(A)熔点高34℃左右。
(B)表面张力大、润湿性差。
(C)价格高2、PCB焊盘表面镀层材料无铅焊接要求PCB焊盘表面镀层材料也要无铅化,PCB焊盘表面镀层的无铅化相对于元器件焊端表面的无铅化容易一些。
目前主要有用非铅金属或无铅焊料合金取代Pb-Sn热风整平(HASL)、化学镀Ni和浸镀金(ENIC)、Cu表面涂覆OSP、浸银(I-Ag)和浸锡(I-Sn)。
回流焊技术
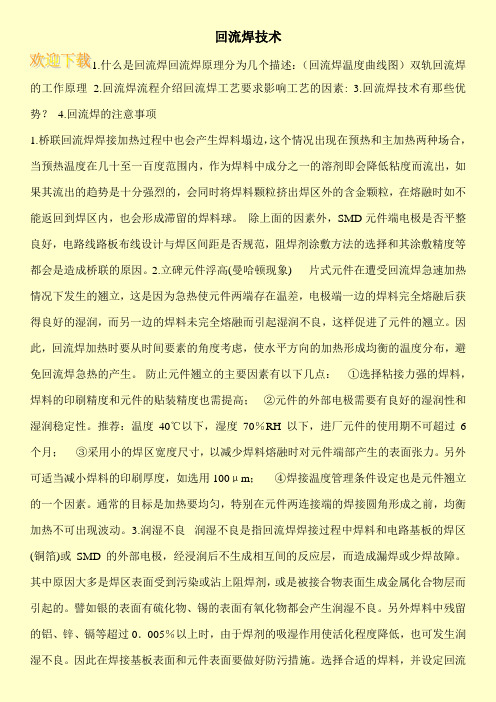
回流焊技术1.什么是回流焊回流焊原理分为几个描述:(回流焊温度曲线图)双轨回流焊的工作原理2.回流焊流程介绍回流焊工艺要求影响工艺的因素:3.回流焊技术有那些优势?4.回流焊的注意事项1.桥联回流焊焊接加热过程中也会产生焊料塌边,这个情况出现在预热和主加热两种场合,当预热温度在几十至一百度范围内,作为焊料中成分之一的溶剂即会降低粘度而流出,如果其流出的趋势是十分强烈的,会同时将焊料颗粒挤出焊区外的含金颗粒,在熔融时如不能返回到焊区内,也会形成滞留的焊料球。
除上面的因素外,SMD元件端电极是否平整良好,电路线路板布线设计与焊区间距是否规范,阻焊剂涂敷方法的选择和其涂敷精度等都会是造成桥联的原因。
2.立碑元件浮高(曼哈顿现象) 片式元件在遭受回流焊急速加热情况下发生的翘立,这是因为急热使元件两端存在温差,电极端一边的焊料完全熔融后获得良好的湿润,而另一边的焊料未完全熔融而引起湿润不良,这样促进了元件的翘立。
因此,回流焊加热时要从时间要素的角度考虑,使水平方向的加热形成均衡的温度分布,避免回流焊急热的产生。
防止元件翘立的主要因素有以下几点:①选择粘接力强的焊料,焊料的印刷精度和元件的贴装精度也需提高;②元件的外部电极需要有良好的湿润性和湿润稳定性。
推荐:温度40℃以下,湿度70%RH以下,进厂元件的使用期不可超过6个月;③采用小的焊区宽度尺寸,以减少焊料熔融时对元件端部产生的表面张力。
另外可适当减小焊料的印刷厚度,如选用100μm;④焊接温度管理条件设定也是元件翘立的一个因素。
通常的目标是加热要均匀,特别在元件两连接端的焊接圆角形成之前,均衡加热不可出现波动。
3.润湿不良润湿不良是指回流焊焊接过程中焊料和电路基板的焊区(铜箔)或SMD的外部电极,经浸润后不生成相互间的反应层,而造成漏焊或少焊故障。
其中原因大多是焊区表面受到污染或沾上阻焊剂,或是被接合物表面生成金属化合物层而引起的。
譬如银的表面有硫化物、锡的表面有氧化物都会产生润湿不良。
回流焊的发展现状

回流焊的发展现状及趋势姓名:学号:微电子制造工程(桂林电子科技大学机电工程学院广西桂林 541004)摘要:最近几年来,随着众多电子产品往小型,轻型,高密度方向发展,特别是手持设备的大量使用,在元器件材料工艺方面都对原有SMT技术提出了重大的挑战,也因此使SM 得致到了飞速发展的机会。
IC发展到0.5mm,0.4mm.0.3mm脚距;BGA已被广泛采用,CSP 也崭露头角,并呈现也快速上涨趋势。
一个总的趋势就是要求回流焊采用更先进的热传递方式,达到节约能源,均匀温度,适合双面板PCB和新型器件封装方式的焊接要求,并逐步实现对波峰焊的全面代替。
关键词:SMT;回流焊;焊接;发展;趋势Reflow of the status quo and development trend(College of mechanical and electrical engineering Guilin University of Electronic Technology Guilin 541004 ) Abstract: In recent years, along with many electronic products to small, light weight, high density development, especially the use of handheld devices, components in the process of the material aspects of the original SMT technology presents a great challenge, so that SM induced by rapid development opportunities. Development of IC to 0.5mm, 0.4mm.0.3mm pitch; BGA has been widely used, CSP also cut a striking figure, and is also the trend of rapid rise. A general trend is to ask the reflow adopts more advanced heat transfer way, achieve energy saving, uniform temperature, suitable for double-sided plate PCB and a novel device encapsulation welding requirements, and gradually realize the soldering fully replace.Key words: SMT; Reflow soldering; welding; development trend;1 引言经过近20多年的飞速发展,国外SMT设备单机结构性框架已基本趋于成熟,并进一步向模块化、灵活、柔性组线方向发展,以发挥设备的最大使用效率,满足快速增长的生产需要。
回流焊技术
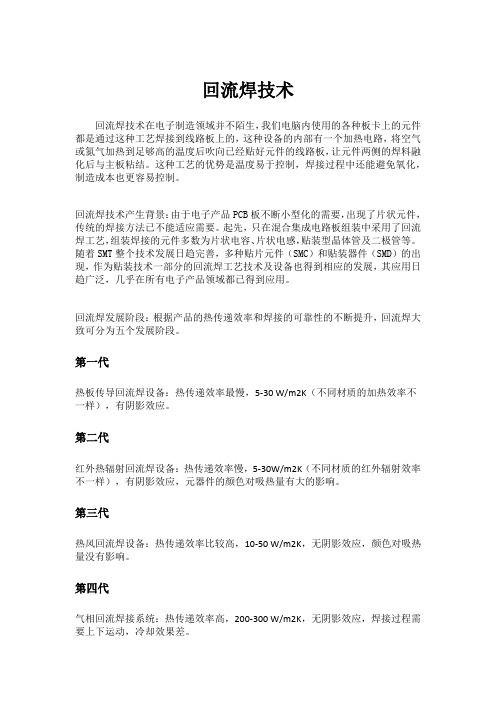
回流焊技术回流焊技术在电子制造领域并不陌生,我们电脑内使用的各种板卡上的元件都是通过这种工艺焊接到线路板上的,这种设备的内部有一个加热电路,将空气或氮气加热到足够高的温度后吹向已经贴好元件的线路板,让元件两侧的焊料融化后与主板粘结。
这种工艺的优势是温度易于控制,焊接过程中还能避免氧化,制造成本也更容易控制。
回流焊技术产生背景:由于电子产品PCB板不断小型化的需要,出现了片状元件,传统的焊接方法已不能适应需要。
起先,只在混合集成电路板组装中采用了回流焊工艺,组装焊接的元件多数为片状电容、片状电感,贴装型晶体管及二极管等。
随着SMT整个技术发展日趋完善,多种贴片元件(SMC)和贴装器件(SMD)的出现,作为贴装技术一部分的回流焊工艺技术及设备也得到相应的发展,其应用日趋广泛,几乎在所有电子产品领域都已得到应用。
回流焊发展阶段:根据产品的热传递效率和焊接的可靠性的不断提升,回流焊大致可分为五个发展阶段。
第一代热板传导回流焊设备:热传递效率最慢,5-30 W/m2K(不同材质的加热效率不一样),有阴影效应。
第二代红外热辐射回流焊设备:热传递效率慢,5-30W/m2K(不同材质的红外辐射效率不一样),有阴影效应,元器件的颜色对吸热量有大的影响。
第三代热风回流焊设备:热传递效率比较高,10-50 W/m2K,无阴影效应,颜色对吸热量没有影响。
第四代气相回流焊接系统:热传递效率高,200-300 W/m2K,无阴影效应,焊接过程需要上下运动,冷却效果差。
第五代真空蒸汽冷凝焊接(真空汽相焊)系统:密闭空间的无空洞焊接,热传递效率最高,300 W-500W/m2K。
焊接过程保持静止无震动。
冷却效果优秀,颜色对吸热量没有影响。
回流焊根据技术分类:热板传导回流焊:这类回流焊炉依靠传送带或推板下的热源加热,通过热传导的方式加热基板上的元件,用于采用陶瓷(Al2O3)基板厚膜电路的单面组装,陶瓷基板上只有贴放在传送带上才能得到足够的热量,其结构简单,价格便宜。
回流焊和波峰焊
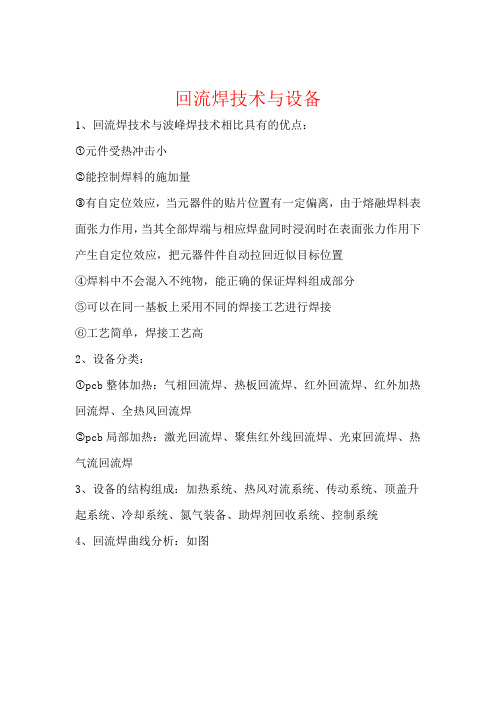
回流焊技术与设备1、回流焊技术与波峰焊技术相比具有的优点:①元件受热冲击小②能控制焊料的施加量③有自定位效应,当元器件的贴片位置有一定偏离,由于熔融焊料表面张力作用,当其全部焊端与相应焊盘同时浸润时在表面张力作用下产生自定位效应,把元器件件自动拉回近似目标位置④焊料中不会混入不纯物,能正确的保证焊料组成部分⑤可以在同一基板上采用不同的焊接工艺进行焊接⑥工艺简单,焊接工艺高2、设备分类:①pcb整体加热:气相回流焊、热板回流焊、红外回流焊、红外加热回流焊、全热风回流焊②pcb局部加热:激光回流焊、聚焦红外线回流焊、光束回流焊、热气流回流焊3、设备的结构组成:加热系统、热风对流系统、传动系统、顶盖升起系统、冷却系统、氮气装备、助焊剂回收系统、控制系统4、回流焊曲线分析:如图回流焊目的:使表贴电子元件(smc)与pcb之间正确而可靠的焊接在一起。
工艺原理:当焊料元件与pcb的温度达到焊料熔点温度以上的焊料融化填充原件与pcb之间的间隙,然后随着冷却焊料凝固形成焊接接头。
回流焊曲线的分析重要不同的资料对回流焊温度曲线的温度划分为:预热区、保温区/活性区、回流区、冷却区四个温区。
下面是某种焊料温度曲线划分在不同温区的分析:第一升温区:是将焊锡膏pcb及元器件的温度从室温提升到预定预热温度,预热温度是一低于焊料熔点的温度,升温段的重要参数是:升温速率一般情况下其值应在1—2℃/s;由于pcb及元器件吸热速度不同,从而导致pcb板面上的温度分布出现梯度,因此此段所有点温度均在焊料熔点以下,所以温度梯度的存在无大碍,在第一升温区结束时温度约为100—110℃,时间约为30—90s,以60s左右为宜。
②保温区(干燥渗透区):保温的目的是让焊锡膏中的助焊剂有充足的时间来清理焊点去除焊点上的氧化膜,同时使pcb板及元器件有充足的时间达到温度均衡,消除温度梯度。
此阶段时间应设定在60—120s,保温结束时温度为140—150℃.③第二升温区:温度从150℃左右升到183℃,这一温区是活化剂的活化期,pcb板温度均匀一致的区间,一半时间为30—45s时间不异长,影响焊接效果④焊接区:在焊接区焊料融化并达到pcb与元件脚良好钎合的目的,在焊接区温度开始迅速上升,元器件仍会以不同的速率吸热,再一次产生温差,素以要控制好温度消除这一温差,一般来讲此段最高温度应高于焊料熔点30—40℃以上,时间在30—60s左右但在225℃以上的时间应控制在10s以内,在215℃以上的温度应控制在20s以内,如果此段温度过高则会损坏元器件,温度过低则会造成部分焊点湿润及焊接不良,为避免及克服上述缺陷目前选用强制热风回流焊接效果好。
回流焊的特点与回流曲线的关系

由于回流曲线的实现是在回流炉中完成的,不同的回流焊炉因加热区的数目和长短不同,气流的大小不同,炉温的容量不同,对回流曲线都会造成影响。
回流焊机、铅回流焊机对回流曲线的影响可归纳为下面几点:1.回流焊炉加热区数目的因素加热区多的回流焊,每个炉区都能单设定炉温,因此调整回流温度曲线比较容易。
对要求较复杂的回流曲线同样可以做到。
加热区少的回流焊,因为可调温区少,很难得到复杂的温度曲线,对于没有特别要求并且贴片元件少的SMT焊接,温区短炉子也能满足要求,而且价钱便宜。
长炉子的优点是传送带的带速可以比短炉子提高的多,这样长炉的产量相应的要比相对短的炉子要大的多并且相对长的回流焊因温区多可以使线路板上的锡膏和元件在炉内充分的融接从而能使产品达到更高的焊接品质。
当大批量生产线追求产能并且线路板上的元件比较密时,这点是关重要的。
2.回流焊热风气流的因素目前大多数回流焊以风扇强制驱动热风循环为主,风扇的转速决定了风量的大小。
在相同的带速和相同的温度设定下,风扇的转速越高,回流曲线的温度越高。
当风扇马达出现故障停转时,即使炉温显示正常,炉温的曲线测量也会比正常曲线低很多,若故障马达在回流区,则PCB板易产生冷焊,若故障马达在冷却区,则PCB板的冷却效果就会下降。
因此对马达转速是可编程调节的回流焊接炉,风扇的转速也是需要经常检查的参数。
3.回流焊炉温容量的因素在回流焊接中,有时会出现这样的现象,当焊接块小尺寸的PCB板时,焊接效果非常好,而焊接块大尺寸的PCB板时,某些温区炉温会出现稍微下降的现象。
这是由于大板子吸热较多,炉子的热容量不足引起的。
炉温的容量主要是由炉体结构,加热器功率等设计因素决定的,这是炉子设备厂设计时已经固定了的,用户在选择回流焊时必须考虑这个因素。
热容量越大越好,保温效果做的越充分越好这样炉子相对消耗的功率要小的多,通俗的来说也就是更省电些。
回流焊profle讲解

焊接(Soldering)By Phil Zarrow回流焊接表面贴装元件现在有二十年之久了。
虽然基本理论没有改变,但在元件包装和材料方面已经有进步,再加上新一代的、“对流为主(convection-dominant)”的、极大改善热传导效率的回流炉。
大规模的回流焊接,特别是在对流为主的(强制对流forced convection),以及激光和凝结惰性的(condensation-inert)(即汽相Vapor phase)焊接中,在可见的未来将仍然是大多数表面贴装连接工艺的首选方法。
尽管如此,新的装配工艺和那些要求整个基板均匀加热、温度变化很小、高的温度传导效率的新应用技术,在促进对流为主的回流焊接的进化。
无数的因素,包括增加的装配复杂性、更新的互连材料和环境考虑,结合在一起对工艺和设备提出了额外的要求。
更快更经济地制造产品,这个持之以恒不断增长的要求驱动这一切的前进。
回流焊接温度曲线作温度曲线(profiling)是确定在回流整个周期内印刷电路板(PCB)装配必须经受的时间/温度关系的过程。
它决定于锡膏的特性,如合金、锡球尺寸、金属含量和锡膏的化学成分。
装配的量、表面几何形状的复杂性和基板导热性、以及炉给出足够热能的能力,所有都影响发热器的设定和炉传送带的速度。
炉的热传播效率,和操作员的经验一起,也影响反复试验所得到的温度曲线。
锡膏制造商提供基本的时间/温度关系资料。
它应用于特定的配方,通常可在产品的数据表中找到。
可是,元件和材料将决定装配所能忍受的最高温度。
涉及的第一个温度是完全液化温度(full liquidus temperature)或最低回流温度(T1)。
这是一个理想的温度水平,在这点,熔化的焊锡可流过将要熔湿来形成焊接点的金属表面。
它决定于锡膏内特定的合金成分,但也可能受锡球尺寸和其它配方因素的影响,可能在数据表中指出一个范围。
对Sn63/Pb37,该范围平均为200 ~ 225°C。
回流焊炉的实验总结

回流焊炉的实验总结
回流焊炉是一种常用的电子组装工艺设备,用于将电子元件焊接到电
路板上。
在进行回流焊炉实验过程中,我对其性能和效果进行了评估和总结。
首先,回流焊炉能够提供稳定的温度控制。
在实验中,我设置了合适
的焊接温度,并观察了焊接过程中的温度变化情况。
通过使用回流焊炉,
我发现它能够准确地控制温度,并且温度的变化范围较小,有利于焊接质
量的保证。
其次,回流焊炉的加热速度较快。
在实验中,我对不同规格的电子组
件进行了焊接试验,结果显示,在回流焊炉的加热下,焊接速度明显提高。
这对于大规模生产来说,能够节省大量的时间和人力成本。
另外,回流焊炉还具有良好的焊接质量。
通过实验证明,在回流焊炉
的控制下,电子组件与电路板的焊接质量非常稳定,焊点牢固可靠,丝毫
不影响电子器件的性能。
此外,回流焊炉在焊接过程中还起到了防氧化的作用。
在实验中,我
观察到焊接后的电子组件表面无明显氧化现象,焊点和电路板表面光洁平整。
这对于电子元件长期稳定运行非常重要。
然而,回流焊炉也存在一些不足之处。
首先,回流焊炉的设备成本较高,对于小型工作室或个人使用来说可能不太实用。
其次,回流焊炉的使
用需要一定的技术和经验,操作不当可能会导致焊接质量下降。
综上所述,回流焊炉在电子组装工艺中具有重要的作用,并且具备稳
定的温度控制、快速的加热速度、良好的焊接质量和防氧化作用等优点。
然而,我们还需要考虑其设备成本和使用技术要求。
在未来的实验中,我将进一步研究和应用回流焊炉技术,以提高焊接效果和质量。
元器件测试回流焊的不同描述方式

元器件测试回流焊的不同描述方式元器件测试回流焊是现代电子制造过程中至关重要的一环。
它涉及到对于电子产品所使用的元器件进行测试和焊接,以确保其质量和可靠性。
在这篇文章中,我将以不同的方式描述元器件测试回流焊,并探讨它们的优缺点。
通过深入了解这些描述方式,我们能够更好地理解元器件测试回流焊的重要性和作用。
1. 描述方式一:技术层面的描述在技术层面上,元器件测试回流焊是一种将电子元器件固定在电路板上的过程。
它涉及到在高温条件下,使用热气流或者热波等方式来加热元器件和焊点,使其熔化并与电路板连接。
这样可以确保元器件与电路板之间良好的电气连接和机械固定。
优点:技术层面的描述让我们更加了解元器件测试回流焊的基本原理和操作过程。
它帮助我们理解为什么要使用高温和热气流,以及它们是如何确保焊点质量和可靠性的。
这种描述方式非常直观,容易理解。
缺点:技术层面的描述可能过于抽象和专业化,对于非专业人士来说可能有些难以理解。
它忽略了元器件测试回流焊在整个电子制造过程中的重要性和作用。
2. 描述方式二:质量保证的描述从质量保证的角度来描述,元器件测试回流焊是一种关键的环节,它能够确保电子产品制造的质量和可靠性。
通过对元器件进行测试和正确的焊接,可以避免因焊点质量低下而引起的故障和损耗。
优点:质量保证的描述让我们明白了元器件测试回流焊在电子产品制造中的重要性。
它帮助我们认识到只有通过良好的焊点连接,才能确保电子产品的质量和可靠性。
这种描述方式突出了元器件测试回流焊对于产品质量的贡献,对于制造商和消费者来说都非常重要。
缺点:质量保证的描述可能过于注重整体效果,而忽略了元器件测试回流焊的具体操作和技术细节。
它没有提供足够的相关信息,使得读者可能无法理解元器件测试回流焊的具体实施方式和细节。
3. 描述方式三:环保意识的描述从环保意识的角度来描述,元器件测试回流焊是一种需要注意的过程,因为它涉及到高温和热气流的使用,这可能对环境造成负面影响。
回流焊凸点材料

回流焊凸点材料
摘要:
一、回流焊凸点材料概述
1.回流焊凸点材料定义
2.回流焊凸点材料的作用
二、回流焊凸点材料的种类
1.锡铅凸点材料
2.无铅凸点材料
三、回流焊凸点材料的选择与应用
1.选择原则
2.应用领域
四、回流焊凸点材料的发展趋势
1.环保要求
2.技术进步带来的变化
正文:
回流焊凸点材料是一种应用于电子制造行业的关键材料,它对焊接过程有着重要的影响。
本文将对回流焊凸点材料进行详细介绍,包括其定义、种类、选择与应用以及发展趋势。
一、回流焊凸点材料概述
回流焊凸点材料,顾名思义,是在回流焊过程中,用于形成焊点的材料。
它起到了连接电子元件与电路板的作用,对于保证焊接质量和提高产品性能至
关重要。
二、回流焊凸点材料的种类
回流焊凸点材料主要有锡铅凸点材料和无铅凸点材料两大类。
锡铅凸点材料具有良好的焊接性能和成本优势,广泛应用于消费类电子产品等领域。
而无铅凸点材料则因环保要求日益严格而逐渐成为市场主流。
三、回流焊凸点材料的选择与应用
在选择回流焊凸点材料时,需要考虑诸多因素,如焊接过程的要求、产品性能指标、环保要求等。
在应用方面,回流焊凸点材料广泛应用于各类电子产品,如手机、电脑、电视等。
四、回流焊凸点材料的发展趋势
随着环保要求的不断提高,无铅凸点材料的应用将越来越广泛。
同时,随着技术进步,新型回流焊凸点材料也将不断涌现,以满足电子制造行业日益严苛的要求。
总之,回流焊凸点材料在电子制造行业中具有举足轻重的地位。
灯带回流焊的原理

灯带回流焊的原理
灯带回流焊的原理是利用高温热风流在PCB板上,将电子元器件与PCB板焊接在一起的过程。
首先,将电子元器件放置在PCB板上,并在元器件的引脚上涂上焊膏。
然后,将PCB板放入回流焊炉中,启动加热系统,使炉内的温度升高,从而使PCB板和元器件上的焊膏熔化。
同时,热风流会将焊膏推向PCB板和元器件的焊点,使它们焊接在一起。
最后,将焊接好的PCB板从回流焊炉中取出,进行冷却和检查,以确保焊点的质量。
这种焊接方式具有速度快、效率高、焊接质量好等优点,广泛应用于电子制造业中。
- 1 -。
回流焊无铅焊接的特点和对策

钎焊机理钎焊分为硬钎焊和软钎焊。
主要是根据钎料(以下称焊料)的熔化温度来区分的,一般把熔点在450℃以下的焊料叫作软焊料,使用软焊料进行的焊接就叫软钎焊;把熔点在450℃以上的焊料叫作硬焊料,使用硬焊料进行的焊接就叫硬钎焊。
在美国MIL SPEC军用标准中,是以800℉(429℃)的金属焊料的熔点作为区分硬钎焊和软钎焊的标准。
电子装联用锡焊是一种软钎焊,其焊料主要使用锡Sn、铅Pb、银Ag、铟In、铋Bi等金属,目前使用最广的是Sn-Pb和Sn-Pb-Ag 系列共晶焊料,熔点一般在185℃左右。
钎焊意味着固体金属表面被某种熔化合金浸润。
这种现象可用一定的物理定律来表示。
如果从热力学角度来考虑浸润过程,也有各种解释的观点。
有一种观点是用自由能来解释的。
⊿F=⊿U-T⊿S 在这里,F是自由能,U是内能,S是熵。
⊿F 与两种因素有关,即与内能和熵的改变有关。
一般S常常趋向于最大值,因此促使-T⊿S也变得更小。
实际上,当固体与液体接触时,如果自由能F减少,即⊿F是负值,则整个系统将发生反应或趋向于稳定状态。
由此可知,熵是浸润的促进因素,因为熵使⊿F的值变得更小。
⊿F的符号最终决定于⊿U的大小和符号,它控制着浸润是否能够发生。
为了产生浸润,焊料的原子必须与固体的原子接触,这就引起位能的变化,如果固体原子吸引焊料,热量被释放出来,⊿U是负值。
如果不考虑⊿U的大小和量值,那么,熵值的改变与表面能的改变有同样的意义,浸润同样是有保证的。
在基体金属和焊料之间产生反应,这就表明有良好的浸润性和粘附性。
如果固体金属不吸引焊料,⊿U是正值,这种情况下,取决于⊿U在特殊温度下的大小值,才能决定能否发生浸润。
这时,增加T⊿S值的外部热能,能对浸润起诱发作用。
这种现象可以解释弱浸润。
在焊接加温时,表面可能被浸润,在冷却时,焊料趋于凝固。
在开始凝固的区域,⊿U是正值,其值比T⊿S大得多,当⊿F最终变为正值时,浸润现象就发生了。
iBoo回流焊炉温测试仪之回流焊原理

iBoo回流焊炉温测试仪之回流焊基本原理由于电子产品PCB板不断小型化的需要,出现了片状元件,传统的焊接方法已不能适应需要。
首先在混合集成电路板组装中采用了回流焊工艺,组装焊接的元件多数为片状电容、片状电感,贴装型晶体管及二极管等。
随着SMT整个技术发展日趋完善,多种贴片元件(SMC)和贴装器件(SMD)的出现,作为贴装技术一部分的回流焊工艺技术及设备也得到相应的发展,其应用日趋广泛,几乎在所有电子产品领域都已得到应用,而回流焊技术,围绕着设备的改进也经历以下发展阶段。
这类回流焊炉依靠传送带或推板下的热源加热,通过热传导的方式加热基板上的元件,用于采用陶瓷(Al2O3)基板厚膜电路的单面组装,陶瓷基板上只有贴放在传送带上才能得到足够的热量,其结构简单,价格便宜。
我国的一些厚膜电路厂在80年代初曾引进过此类设备。
回流焊外观编辑本段红外线辐射回流焊:此类回流焊炉也多为传送带式,但传送带仅起支托、传送基板的作用,其加热方式主要依红外线热源以辐射方式加热,炉膛内的温度比前一种方式均匀,网孔较大,适于对双面组装的基板进行回流焊接加热。
这类回流焊炉可以说是回流焊炉的基本型。
在我国使用的很多,价格也比较便宜。
编辑本段红外加热风(Hot air)回流焊:这类回流焊炉是在IR炉的基础上加上热风使炉内温度更均匀,单纯使用红外辐射加热时,人们发现在同样的加热环境内,不同材料及颜色吸收热量是不同的,即(1)式中Q值是不同的,因而引起的温升ΔT也不同,例如IC等SMD的封装是黑色的酚醛或环氧,而引线是白色的金属,单纯加热时,引线的温度低于其黑色的SMD本体。
加上热风后可使温度更均匀,而克服吸热差异及阴影不良情况,IR + Hot air的回流焊炉在国际上曾使用得很普遍。
编辑本段充氮(N2)回流焊:随着组装密度的提高,精细间距(Fine pitch)组装技术的出现,产生了充氮回流焊工艺和设备,改善了回流焊的质量和成品率,已成为回流焊的发展方向。
回流焊.doc

热风回流焊接的原理回流焊接的过程回流焊的基本原理比较简单,它首先对PCB板的表面贴装元件LTCL-3088(SMD)焊盘印刷锡膏,然后通过自动贴片机把SMD贴放到预先印制好锡膏的焊盘上。
最后,通过回流焊接炉,在回流焊炉中逐渐加热,把锡膏融化,称为回流MCR (Reflow),接着,把PCB板冷却,焊锡凝固,把元件和焊盘牢固地焊接到一起。
在回流焊中,焊盘和元件管脚回流焊都不融化。
这是回流焊(Reflow Soldering)与金属融焊(Welding)的不同。
深入的了解回流焊就必须从焊锡膏的作用原理和焊接过程中发生的物理化学变化入手。
锡膏的成分主要锡铅合金的粉末和助焊剂混合而成。
在受热的条件下,融化的焊锡材料中的锡原子和焊盘或焊接元件(主要成分是铜原子)的接触界面原子相互扩散,形成金属间化合物(IMC),首先形成的Cu6Sn5,称n-phase,它是形成焊接力的关键连接层,只有形成了 n-phase,才表示有真正的可靠焊接。
随着时间的推移,在n-phase和铜层之间中威力泰会继续生成Cu3Sn,称为∈-phase,它将减弱焊接力量和减低长期可靠性。
在焊点剖面的金相图中,可以清楚地看到这个结构。
电子扫描显微镜(SEM)显示的Cu-Sn IMC金属间化合物是焊点强度的关键因素,因此许多人员专门研究金属间化合物的变化对焊点的长期可靠性带来的影响[4][10]。
为了保护焊盘或元件管脚的可焊性,一般它们表面都镀有锡铅合金层或有机保护层。
对非铜的金属材料的管脚一般在管脚镀层和金属之间加有镀镍层作为阻断层防止金属扩散。
这个回流焊机价格镍镀层还用来阻挡与焊锡不可焊或不相容的金属与焊锡层的接触 [5]。
另一个有关镀层的问题是关于镀金层的问题,有文章[5]指出如果焊点中金的成分达到3~4%以上,焊点有潜在的脆性增大的危险。
回流焊温度曲线要得到好的回流焊接效果必须有一个好的回流温度曲线(Profile)。
那么什么是一个好的回流曲线呢?一个好的回流曲线应该是对所要焊接的PCB板上的各种表面贴装元件都能够达到良好的焊接,且焊点不仅具有良好的外观品质而且有良威力泰商城好的内在品质的温度曲线。
回流焊的工作原理
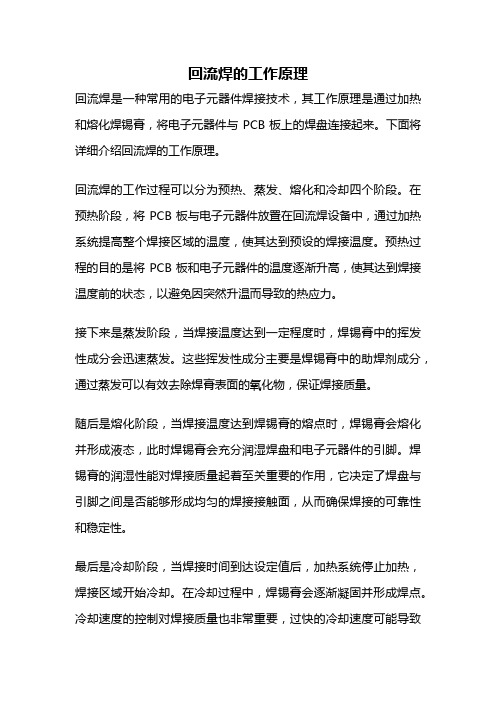
回流焊的工作原理回流焊是一种常用的电子元器件焊接技术,其工作原理是通过加热和熔化焊锡膏,将电子元器件与PCB板上的焊盘连接起来。
下面将详细介绍回流焊的工作原理。
回流焊的工作过程可以分为预热、蒸发、熔化和冷却四个阶段。
在预热阶段,将PCB板与电子元器件放置在回流焊设备中,通过加热系统提高整个焊接区域的温度,使其达到预设的焊接温度。
预热过程的目的是将PCB板和电子元器件的温度逐渐升高,使其达到焊接温度前的状态,以避免因突然升温而导致的热应力。
接下来是蒸发阶段,当焊接温度达到一定程度时,焊锡膏中的挥发性成分会迅速蒸发。
这些挥发性成分主要是焊锡膏中的助焊剂成分,通过蒸发可以有效去除焊膏表面的氧化物,保证焊接质量。
随后是熔化阶段,当焊接温度达到焊锡膏的熔点时,焊锡膏会熔化并形成液态,此时焊锡膏会充分润湿焊盘和电子元器件的引脚。
焊锡膏的润湿性能对焊接质量起着至关重要的作用,它决定了焊盘与引脚之间是否能够形成均匀的焊接接触面,从而确保焊接的可靠性和稳定性。
最后是冷却阶段,当焊接时间到达设定值后,加热系统停止加热,焊接区域开始冷却。
在冷却过程中,焊锡膏会逐渐凝固并形成焊点。
冷却速度的控制对焊接质量也非常重要,过快的冷却速度可能导致焊点的冷焊或冷裂,从而影响焊接质量。
需要注意的是,回流焊的工作原理中还涉及到焊接温度、焊接时间和焊锡膏的选择等因素。
焊接温度应根据元器件和PCB板的要求进行调整,一般情况下,焊接温度在200-260摄氏度之间。
焊接时间的长短取决于焊接质量的要求,一般在30-120秒之间。
焊锡膏的选择应考虑到焊接工艺、焊接温度和焊接要求等因素,常用的焊锡膏有无铅焊锡膏和铅锡焊锡膏。
回流焊是一种通过加热和熔化焊锡膏,将电子元器件与PCB板焊接在一起的技术。
通过预热、蒸发、熔化和冷却等阶段,实现了焊接过程的控制和管理。
回流焊技术具有焊接速度快、焊接质量高、可自动化等优点,广泛应用于电子制造行业。
气相回流焊缩写
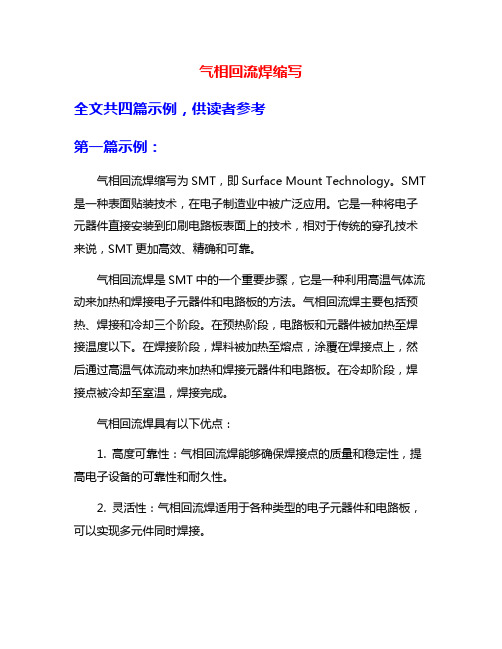
气相回流焊缩写全文共四篇示例,供读者参考第一篇示例:气相回流焊缩写为SMT,即Surface Mount Technology。
SMT 是一种表面贴装技术,在电子制造业中被广泛应用。
它是一种将电子元器件直接安装到印刷电路板表面上的技术,相对于传统的穿孔技术来说,SMT更加高效、精确和可靠。
气相回流焊是SMT中的一个重要步骤,它是一种利用高温气体流动来加热和焊接电子元器件和电路板的方法。
气相回流焊主要包括预热、焊接和冷却三个阶段。
在预热阶段,电路板和元器件被加热至焊接温度以下。
在焊接阶段,焊料被加热至熔点,涂覆在焊接点上,然后通过高温气体流动来加热和焊接元器件和电路板。
在冷却阶段,焊接点被冷却至室温,焊接完成。
气相回流焊具有以下优点:1. 高度可靠性:气相回流焊能够确保焊接点的质量和稳定性,提高电子设备的可靠性和耐久性。
2. 灵活性:气相回流焊适用于各种类型的电子元器件和电路板,可以实现多元件同时焊接。
3. 高效性:气相回流焊具有快速、高效的特点,能够大幅提高生产效率和节约成本。
4. 环保性:气相回流焊采用无铅焊料,符合环保要求,对环境没有污染。
气相回流焊也存在一些缺点:1. 高成本:气相回流焊设备和工艺复杂,投入成本较高。
2. 工艺要求高:气相回流焊需要严格控制焊接温度和时间,操作要求较高。
3. 人为因素:操作人员的技术水平对焊接质量有很大影响,需要经过专门的培训。
气相回流焊作为SMT技术的一个重要环节,在电子制造业中扮演着至关重要的角色。
随着电子产品的不断更新换代和技术的不断发展,气相回流焊也在不断演进和完善,以适应市场的需求。
希望未来气相回流焊能够更加智能化、高效化,为电子行业的发展做出更大的贡献。
第二篇示例:气相回流焊(PGR)是一种常见的表面贴装技术,也是一种重要的半导体封装技术。
PGR是通过将PCB板与组件预热到一定温度,然后将气相回流焊炉中的热空气加热到一定温度,通过气流将焊料熔化后送到焊点上,实现焊接的一种方法。
- 1、下载文档前请自行甄别文档内容的完整性,平台不提供额外的编辑、内容补充、找答案等附加服务。
- 2、"仅部分预览"的文档,不可在线预览部分如存在完整性等问题,可反馈申请退款(可完整预览的文档不适用该条件!)。
- 3、如文档侵犯您的权益,请联系客服反馈,我们会尽快为您处理(人工客服工作时间:9:00-18:30)。
IBL 汽相回流焊优越性
1、机电一体化设计,结构紧凑、占用场地少、自动化程度高、人机界面合理、
操作简单易行。
2、系列化产品,有台式、单机式、在线式、共有4种系列16种标准型,还有
17种功能模块选件,可满足用户不同批量、不同配置、不同性能的需求,以及千差万别的各种特殊要求。
3、采用汽相传热原理,使整个PCB板温度十分均匀一致,3种精确的回流焊温
度:2000C、2150C、2300C,其中2000C适用于SnPb合金,2300C适用于无铅焊(SnAg3.5)。
4、彻底杜绝过热现象发生,确保元器件安全。
5、提供100%惰性汽相环境,氧气含量0 ppm,无焊点氧化现象。
6、可实现长时间焊接,确保PLCC、QFP、BGA、CSP等复杂器件焊点的可靠
性。
7、可实现任何复杂加工件的同时焊接,而与PCB板形状、层数、元器件密度
及形状等都无关,使加工件上应力降低到极低,比其它回流焊方法更容易获得高质量、高可靠性焊点。
8、其它回流焊方法容易使多层PCB板产生爆米化现象(popcorn cracking)及
分层现象,而汽相回流焊消除了这一现象。
9、系统启动时间短,开机预热15~20分钟后即可进行焊接。
10、使用内置预热系统SVP模式可实现用户要求的各种形状的温度曲线,对PCB
板的加温速率可在1~60C/秒内调节。
11、使用SVP模式不会产生“墓碑现象”(Tombestone effect)。
12、系统的重复性极佳,只要装订的焊接条件不变,保证任何时间的工作条件都
是一致的,这样就能保证长期、安全、可靠地运行。
13、系统装有特殊的快速冷却系统RCS,最高冷却速度高达50C/秒,大大缩短了
焊点凝固时间,提高了焊点质量。
14、系统设置有冷却水不足、加热面过热、工作液不足等停机保护措施,保证了
设备和人员安全。
15、内置工作液回收系统,保证了最少的工作液损耗,降低了生产成本。
16、回流焊接中,排入大气的助焊剂蒸汽比其它回流焊少,是环保型焊接工艺。
17、系统能耗成本、工艺监控成本、惰性气体中的加工成本都低于其它回流焊方
法,是成本回报率最高的回流焊设备。
18、系统能对工件进行回流焊返修,甚至对QFP320及各种BGA或CGA都能毫
无损害地进行解焊,取下来的器件还可再用。
19、系统装有透明观察窗口及照明设备,可观察整个焊接过程。
20、几种回流焊方法中,唯有汽相回流焊能100%满足ISO-9000要求。