数控钻--PCB冲裁
PCB数控钻孔机及锣机CNC刀具指令大全
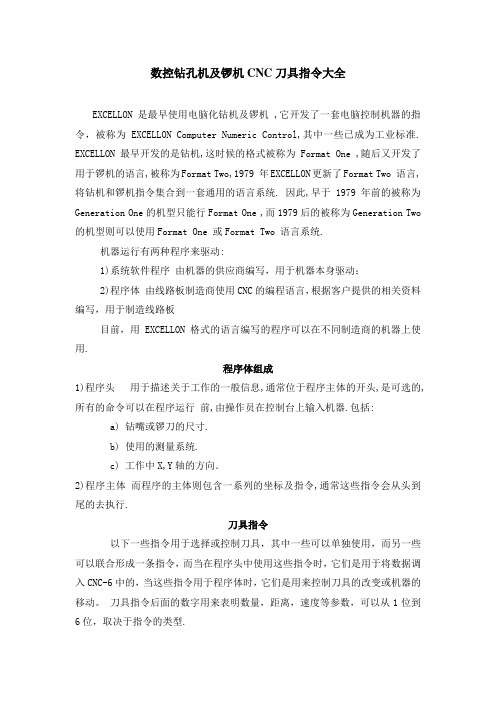
数控钻孔机及锣机CNC刀具指令大全EXCELLON是最早使用电脑化钻机及锣机 ,它开发了一套电脑控制机器的指令,被称为EXCELLON Computer Numeric Control,其中一些已成为工业标准. EXCELLON 最早开发的是钻机,这时候的格式被称为 Format One ,随后又开发了用于锣机的语言,被称为Format Two,1979 年EXCELLON更新了Format Two 语言,将钻机和锣机指令集合到一套通用的语言系统. 因此,早于1979年前的被称为Generation One的机型只能行Format One ,而1979后的被称为Generation Two 的机型则可以使用Format One 或Format Two 语言系统.机器运行有两种程序来驱动:1)系统软件程序由机器的供应商编写,用于机器本身驱动;2)程序体由线路板制造商使用CNC的编程语言,根据客户提供的相关资料编写,用于制造线路板目前,用EXCELLON格式的语言编写的程序可以在不同制造商的机器上使用.程序体组成1)程序头用于描述关于工作的一般信息,通常位于程序主体的开头,是可选的,所有的命令可以在程序运行前,由操作员在控制台上输入机器.包括:a) 钻嘴或锣刀的尺寸.b) 使用的测量系统.c) 工作中X,Y轴的方向.2)程序主体而程序的主体则包含一系列的坐标及指令,通常这些指令会从头到尾的去执行.刀具指令以下一些指令用于选择或控制刀具,其中一些可以单独使用,而另一些可以联合形成一条指令,而当在程序头中使用这些指令时,它们是用于将数据调入CNC-6中的,当这些指令用于程序体时,它们是用来控制刀具的改变或机器的移动。
刀具指令后面的数字用来表明数量,距离,速度等参数,可以从1位到6位,取决于指令的类型.T#(#)F#S#C#H#Z+/-#T#刀具选择这个指令可以在手动或自动设置状态下使用,它可以用于程序头或程序主体。
PCB电路板PCB数控钻孔机及锣机CNC刀具指令大全

PCB电路板PCB数控钻孔机及锣机CNC刀具指令大全数控钻孔机及锣机C刀具指令大全EXCELLON是最早使用电脑化钻机及锣机,它开发了一套电脑控制机器的指令,被称为EXCELLONputerNumericControl,其中一些已成为工业标准.EXCELLON最早开发的是钻机,这时候的格式被称为FormatOne,随后又开发了用于锣机的语言,被称为FormatTwo,1979年EXCELLON更新了FormatTwo语言,将钻机和锣机指令集合到一套通用的语言系统.因此,早于1979年前的被称为GenerationOne的机型只能行FormatOne,而1979后的被称为GenerationTwo的机型则可以使用FormatOne或FormatTwo语言系统.机器运行有两种程序来驱动:1)系统软件程序由机器的供应商编写,用于机器本身驱动;2)程序体由线路板制造商使用C的编程语言,根据客户提供的相关资料编写,用于制造线路板目前,用EXCELLON格式的语言编写的程序可以在不同制造商的机器上使用.程序体组成1)程序头用于描述关于工作的一般信息,通常位于程序主体的开头,是可选的,所有的命令可以在程序运行前,由操作员在控制台上输入机器.包括:a)钻嘴或锣刀的尺寸.b)使用的测量系统.c)工作中X,Y轴的方向.2)程序主体而程序的主体则包含一系列的坐标及指令,通常这些指令会从头到尾的去执行.刀具指令以下一些指令用于选择或控制刀具,其中一些可以单独使用,而另一些可以联合形成一条指令,而当在程序头中使用这些指令时,它们是用于将数据调入C-6中的,当这些指令用于程序体时,它们是用来控制刀具的改变或机器的移动。
刀具指令后面的数字用来表明数量,距离,速度等参数,可以从1位到6位,取决于指令的类型.T#T#(#)F#S#C#H#Z+/-#T#刀具选择这个指令可以在手动或自动设置状态下使用,它可以用于程序头或程序主体。
在自动换刀具设置状态下:主轴夹头将自动将正在使用的刀具放进T座,而抓取#所对应的刀具,并自动移动到程序主体下一个坐标。
pcb钻孔工艺常见问题及处理

(6) 钻孔前用 20 倍镜检查刀面,将不良钻咀刃磨或者报废处理。 (7) 多次核对、测量。 (8) 在更换钻咀时可以测量所换下钻咀,已更换钻咀测量所钻第一个 孔。 (9) 排列钻咀时要数清楚刀库位置。 (10) 更换钻咀时看清楚序号。 (11) 在备刀时要逐一核对孔径图的实际孔径。 (12) 清洗夹咀,造成压刀后要仔细测量及检查刀面情况。 (13) 在输入刀具序号时要反复检查。 5、漏钻孔 产生原因有:断钻咀(标识不清);中途暂停;程序上错误;人为无意 删除程序;钻机读取资料时漏读取。 解决方法: (1) 对断钻板单独处理,分开逐一检查。
解决方法: (1) A、检查主轴是否偏转; B、减少叠板数量,通常双面板叠层数量为钻头直径的 6 倍而多层板 叠层数量为钻头直径的 2~3 倍; C、增加钻咀转速或降低进刀速率; D、检查钻咀是否符合工艺要求,否则重新刃磨; E、检查钻咀顶尖与钻咀柄是否具备良好同中心度; F、检查钻头与弹簧夹头之间的固定状态是否紧固; G、检测和校正钻孔工作台板的稳定和稳定性。 (2) 选择高密度 0.50mm 的石灰盖板或者更换复合盖板材料(上下两 层是厚度 0.06mm 的铝合金箔,中间是纤维芯,总厚度为 0.35mm)。 (3) 根据板材的特性,钻孔前或钻孔后进行烤板处理(一般是 145℃± 5℃,烘烤 4 小时为准)。 (4) 检查或检测工具孔尺寸精度及上定位销的位置是否有偏移。 (5) 检查重新设置压脚高度,正常压脚高度距板面 0.80mm 为钻孔最 佳压脚高度。 (6) 选择合适的钻头转速。 (7) 清洗或更换好的弹簧夹头。 (8) 面板未装入销钉,管制板的销钉太低或松动,需要重新定位更换 销钉。 (9) 选择合适的进刀速率或选抗折强度更好的钻头。 (10) 更换表面平整无折痕的盖板铝片。
PCB板钻孔制程介绍
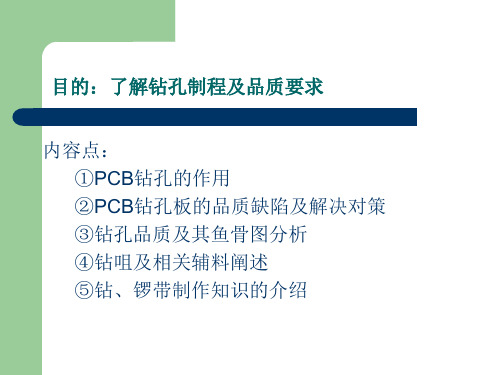
五、钻锣带制作知识的介绍
c.单位制
公制(METRIC) mm 英制(ENGLISH) inch or mil
d.单位换算
1 inch=1000 mil=2.54 cm=25.4 mm 1 mm=0.03937inch=39.37 mil
五、钻锣带制作知识的介绍
2、钻(锣)带文件头介绍(以常用的EXEL格式为例)
3、垫板 要求垫板本身树脂成分不能过高,否则钻孔时将会形成熔融的脂 球黏附在孔壁。常用的有: a.普通纸质垫板 b.高密度纸质垫板 c.酚醛垫板
五、钻锣带制作知识的介绍
1、钻孔档(Drill File)介绍 a.常见格式:
Exel系
S&m系
b.坐标格式
LEADING ZERO 省前0补后0 例:12.3→12300
原因分析
解决对策
钻咀磨损过度
更换钻咀
板材问题
更换板材
切割速度过快
降低转速或下钻速
钻头断或钻咀长度不够 更换钻咀重新补孔
台面不平
调整台面平整度
下钻深度设置错误
更改合理设置
操作失误Biblioteka 补孔或报废钻带出错或格式用错 用正确格式的钻带生产
三、钻孔品质及其鱼骨图分析
1、钻孔的品质要求 孔径:+0/-1mil 孔位:≤2mil
原因分析
解决对策
内层焊盘不硬
检查内层
板材厚板不均匀
更换更好的板材
压力脚不平或压力不足 更换压脚或调整气压
烤板时间或温度不够 重新烤板
钻床不稳定
检查钻床固定座
主轴偏摆过大
清洗夹嘴或维修主轴
钻咀类型不附或有缺口 更换钻咀
盖板不好
更换盖板
PCB数控钻孔机精度检测及补偿研究
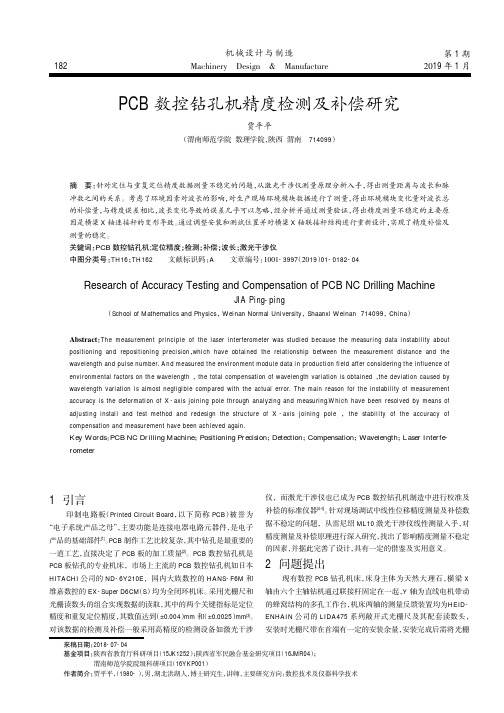
仪,而激光干涉仪也已成为 PCB 数控钻孔机制造中进行校准及 补偿的标准仪器[4-6]。针对现场调试中线性位移精度测量及补偿数 据不稳定的问题,从雷尼绍 ML10 激光干涉仪线性测量入手,对 精度测量及补偿原理进行深入研究,找出了影响精度测量不稳定 的因素,并据此完善了设计,具有一定的借鉴及实用意义。
来稿日期:2018-07-04 基金项目:陕西省教育厅科研项目(15JK1252);陕西省军民融合基金研究项目(16JMR04);
渭南师范学院院级科研项目(16YKP001) 作者简介:贾平平,(1980- ),男,湖北洪湖人,博士研究生,讲师,主要研究方向:数控技术及仪器科学技术
第1期
贾平平:PCB 数控钻孔机精度检测及补偿研究
1 引言
印制电路板(Printed Circuit Board,以下简称 PCB)被誉为 “电子系统产品之母”,主要功能是连接电器电路元器件,是电子 产品的基础部件[1]。PCB 制作工艺比较复杂,其中钻孔是最重要的 一道工艺,直接决定了 PCB 板的加工质量[2]。PCB 数控钻孔机是 PCB 板钻孔的专业机床,市场上主流的 PCB 数控钻孔机如日本 HITACHI 公司的 ND-6Y210E,国内大族数控的 HANS-F6M 和 维嘉数控的 EX-Super D6CM(S)均为全闭环机床。采用光栅尺和 光栅读数头的组合实现数据的读取,其中的两个关键指标是定位 精度和重复定位精度,其数值达到(依0.004)mm 和(依0.0025)mm[3]。 对该数据的检测及补偿一般采用高精度的检测设备如激光干涉
粤遭泽贼则葬糟贼:The measurement principle of the laser interferometer was studied because the measuring data instability about positioning and repositioning precision,which have obtained the relationship between the measurement distance and the wavelength and pulse number. A nd measured the environment module data in production field after considering the influence of environmental factors on the wavelength ,the total compensation of wavelength variation is obtained ,the deviation caused by wavelength variation is almost negligible compared with the actual error. The main reason for the instability of measurement accuracy is the deformation of X-axis joining pole through analyzing and measuring.W hich have been resolved by means of adjusting install and test method and redesign the structure of X -axis joining pole ,the stability of the accuracy of compensation and measurement have been achieved again. Key Words:PCB NC Drilling Machine;Positioning Precision;Detection;Compensation;Wavelength;Laser Interferometer
PCB数控背钻机械钻孔机钻孔深度异常原因分析
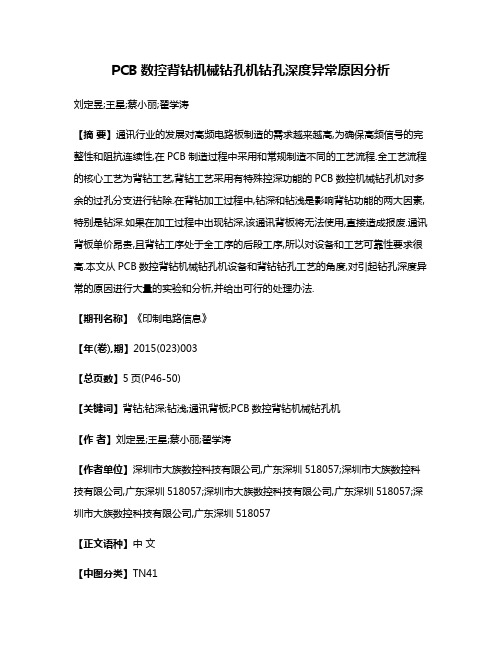
PCB数控背钻机械钻孔机钻孔深度异常原因分析刘定昱;王星;蔡小丽;翟学涛【摘要】通讯行业的发展对高频电路板制造的需求越来越高,为确保高频信号的完整性和阻抗连续性,在PCB制造过程中采用和常规制造不同的工艺流程.全工艺流程的核心工艺为背钻工艺,背钻工艺采用有特殊控深功能的PCB数控机械钻孔机对多余的过孔分支进行钻除.在背钻加工过程中,钻深和钻浅是影响背钻功能的两大因素,特别是钻深.如果在加工过程中出现钻深,该通讯背板将无法使用,直接造成报废.通讯背板单价昂贵,且背钻工序处于全工序的后段工序,所以对设备和工艺可靠性要求很高.本文从PCB数控背钻机械钻孔机设备和背钻钻孔工艺的角度,对引起钻孔深度异常的原因进行大量的实验和分析,并给出可行的处理办法.【期刊名称】《印制电路信息》【年(卷),期】2015(023)003【总页数】5页(P46-50)【关键词】背钻;钻深;钻浅;通讯背板;PCB数控背钻机械钻孔机【作者】刘定昱;王星;蔡小丽;翟学涛【作者单位】深圳市大族数控科技有限公司,广东深圳518057;深圳市大族数控科技有限公司,广东深圳518057;深圳市大族数控科技有限公司,广东深圳518057;深圳市大族数控科技有限公司,广东深圳518057【正文语种】中文【中图分类】TN41随着全球通讯行业的迅速发展,高阶多层通讯板需求急剧增加,4G或更高频数字信号传输对高频电路板制造提出更高的要求。
普通多层线路板在信号经过时在过孔处有不连续信号通路,容易引起阻抗不连续,并带来衰减、反射、延迟等信号完整性问题。
为了解决过孔带来的信号完整性问题,PCB厂商多采用背钻工艺加工特殊的多层线路板来确保信号的完整性,行业内也称这种板为通讯背板。
通讯背板采用和常规制造不同的工艺流程,全工艺流程中核心工艺为背钻工艺,如图1所示。
背钻工艺一般在图电后,所以需要二次定位,这样对钻孔机的精度要求高。
背钻是用比钻孔工序更大直径的钻头,从过孔的背面将沉铜电镀孔内多余的过孔分支金属钻掉,如图2所示。
PCB钻孔的流程、分类和技巧
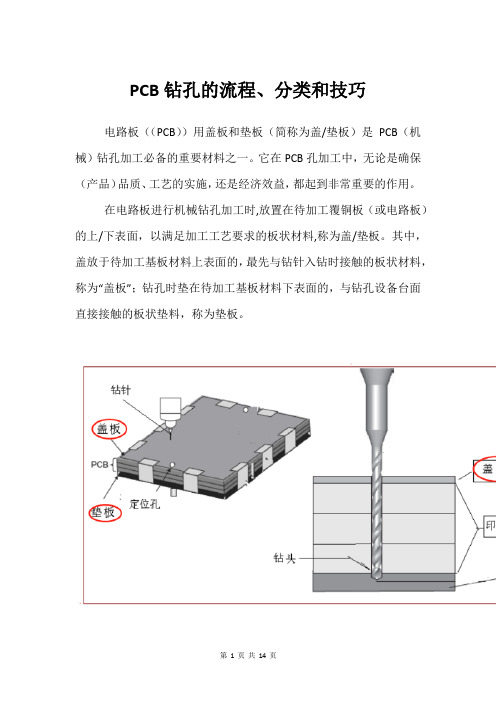
PCB钻孔的流程、分类和技巧电路板((PCB))用盖板和垫板(简称为盖/垫板)是PCB(机械)钻孔加工必备的重要材料之一。
它在PCB孔加工中,无论是确保(产品)品质、工艺的实施,还是经济效益,都起到非常重要的作用。
在电路板进行机械钻孔加工时,放置在待加工覆铜板(或电路板)的上/下表面,以满足加工工艺要求的板状材料,称为盖/垫板。
其中,盖放于待加工基板材料上表面的,最先与钻针入钻时接触的板状材料,称为“盖板”;钻孔时垫在待加工基板材料下表面的,与钻孔设备台面直接接触的板状垫料,称为垫板。
钻孔是PCB制造中最昂贵和最耗时的过程。
PCB钻孔过程必须小心实施,因为即使是很小的错误也会导致很大的损失。
钻孔工艺是PCB制造过程中最关键的工艺。
钻孔工艺是通孔和不同层之间连接的基础,因此钻孔技巧十分重要。
PCB钻孔一、PCB钻孔技术主要有2 种PCB 钻孔技术:机械钻孔和激光钻孔。
PCB钻孔技术1、机械钻孔机械钻头的精度较低,但易于执行。
这种钻孔技术实现了钻头。
这些钻头可以钻出的最小孔径约为6密耳(0.006 英寸)。
机械钻孔的局限性当用于FR4 等较软的材料时,机械钻可用于800 次冲击。
对于密度比较大的材料,寿命会减少到200 计数。
如果PCB 制造商忽视这一点,则会导致出现错误的孔,从而导致电路板报废。
2、激光钻孔另一方面,激光钻可以钻出更小的孔。
激光钻孔是一种非接触式工艺,工件和工具不会相互接触。
激光束用于去除电路板材料并创建精确的孔,可以毫不费力地控制钻孔深度。
激光技术用于轻松钻出受控深度的过孔,可以精确钻出最小直径为2 密耳(0.002”)的孔。
激光钻孔限制电路板由铜、玻璃纤维和树脂制成,这些PCB 材料具有不同的(光学)特性,这使得激光束很难有效地烧穿电路板。
在激光钻孔的情况下,该过程的成本也相对较高。
二、PCB钻孔流程对于PCB(工程师)来说,如果设计电路板,也必须要了解PCB 的制造。
这样才能保证(PCB设计)是可制造,也是可靠的,反过来如果在设计时就注意到制造上的工艺,可以降低成本,并且可以在规定的时间内交付产品。
pcb生产机械加工及激光钻孔工艺基础
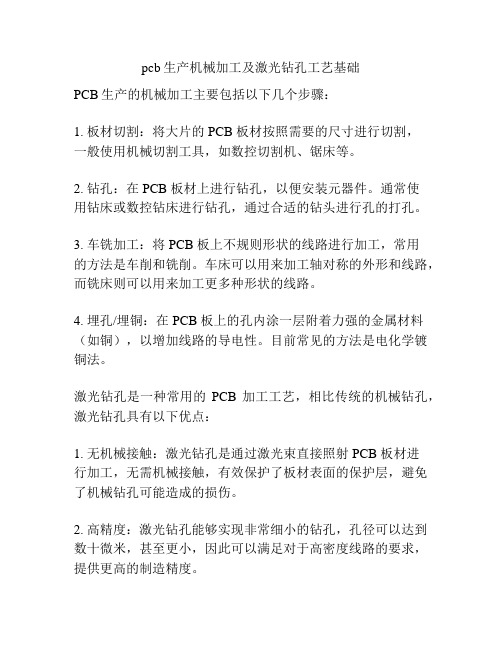
pcb生产机械加工及激光钻孔工艺基础
PCB生产的机械加工主要包括以下几个步骤:
1. 板材切割:将大片的 PCB 板材按照需要的尺寸进行切割,
一般使用机械切割工具,如数控切割机、锯床等。
2. 钻孔:在 PCB 板材上进行钻孔,以便安装元器件。
通常使
用钻床或数控钻床进行钻孔,通过合适的钻头进行孔的打孔。
3. 车铣加工:将 PCB 板上不规则形状的线路进行加工,常用
的方法是车削和铣削。
车床可以用来加工轴对称的外形和线路,而铣床则可以用来加工更多种形状的线路。
4. 埋孔/埋铜:在 PCB 板上的孔内涂一层附着力强的金属材料(如铜),以增加线路的导电性。
目前常见的方法是电化学镀铜法。
激光钻孔是一种常用的PCB 加工工艺,相比传统的机械钻孔,激光钻孔具有以下优点:
1. 无机械接触:激光钻孔是通过激光束直接照射 PCB 板材进
行加工,无需机械接触,有效保护了板材表面的保护层,避免了机械钻孔可能造成的损伤。
2. 高精度:激光钻孔能够实现非常细小的钻孔,孔径可以达到数十微米,甚至更小,因此可以满足对于高密度线路的要求,提供更高的制造精度。
3. 布线灵活:激光钻孔可以实现任意位置的钻孔,布线更加灵活,可以为设计者提供更多的设计自由度。
4. 加工速度快:相比传统的机械钻孔,激光钻孔的速度通常更快,可以提高 PCB 加工的效率。
总体来说,机械加工和激光钻孔是 PCB 生产中常用的工艺基础,根据具体的需求和要求,可以选择不同的加工方法来进行PCB 的制造。
PCB数控钻床的关键技术研究应用
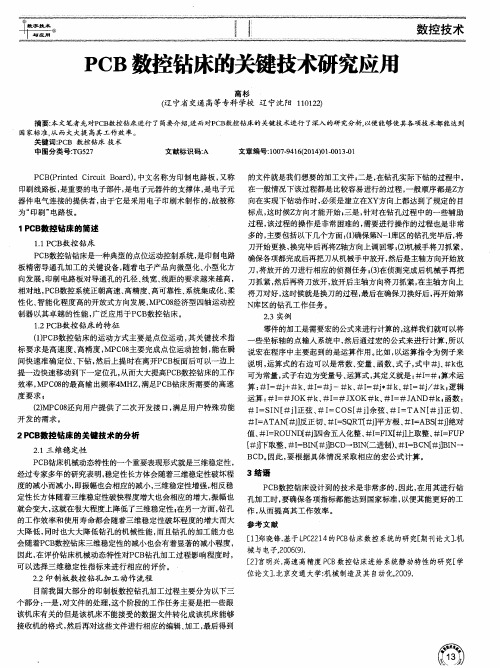
2 P C B 数控钻床的关键技术的分析
2 . 1三 维 稳 定 性
值、 #I = RO UND [ #j 】 四合五人化整、 #I = F I x[ #j ] 上取整、 #I = F U P
P C B 钻床机械动态特性 的一个重要表现形式就是三维稳定性 , 经过专家多年的研究表 明, 稳定性长方体会随着三维稳定性破坏程 3结 语 度的减小而减小 , 即振幅也会相应 的减小 , 三维 稳定性增强 , 相反 稳
P C B ( P r i n t e d C i r c u i t B o a r d ) , 中文名称 为 印制 电路板 , 又称 的文件就 是我们想要的加工文件 ; 二 是, 在钻孔实际下钻 的过程 中, 印刷线路板 , 是重要的电子部件 , 是电子元器件的支撑体 , 是 电子元 在一般情况下该过程都是 比较容 易进行 的过程 , 一般 顺序 都是z 方
黪
黪 。 l 与 应用
数控技术
P C B数控钻床的关键技术研究应用
高杉
( 辽宁省交通高等专科 学校 辽 宁沈阳 1 1 0 1 2 2 )
摘 要: 本文 笔者先 对P C B 数控 钻床 进行 了简要 介绍 , 进而 对P C B 数控钻 床 的关键技 术进行 了深入的研 究分 析, 以便 能够使 其各项技 术都 能达 到 国家标 准, 从 而 大 大提 高其 工作 效 率 。 关键 词 : P C B 数控 钻床 技 术 中 图分 类号: T G 5 2 7 文献 标识码 : A 文章 编号 : 1 0 0 7 - 9 4 1 6 ( 2 0 1 4 ) 0 1 - 0 0 1 3 - 0 1
pcb钻孔机的操作技术及流程详解
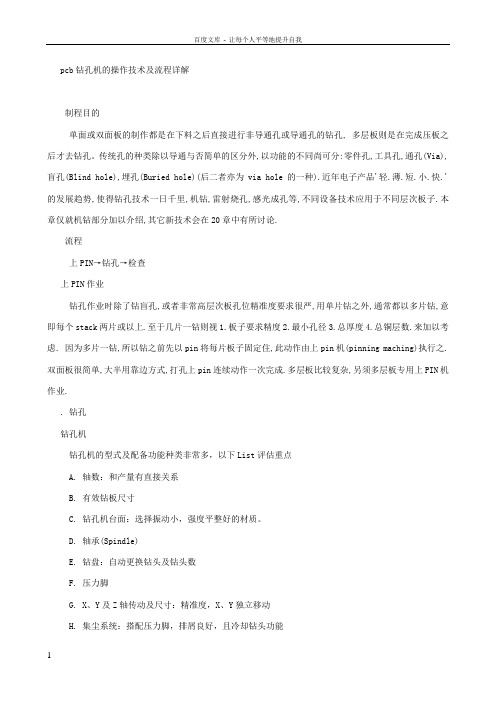
pcb钻孔机的操作技术及流程详解制程目的单面或双面板的制作都是在下料之后直接进行非导通孔或导通孔的钻孔, 多层板则是在完成压板之后才去钻孔。
传统孔的种类除以导通与否简单的区分外,以功能的不同尚可分:零件孔,工具孔,通孔(Via),盲孔(Blind hole),埋孔(Buried hole)(后二者亦为via hole的一种).近年电子产品'轻.薄.短.小.快.'的发展趋势,使得钻孔技术一日千里,机钻,雷射烧孔,感光成孔等,不同设备技术应用于不同层次板子.本章仅就机钻部分加以介绍,其它新技术会在20章中有所讨论.流程上PIN→钻孔→检查上PIN作业钻孔作业时除了钻盲孔,或者非常高层次板孔位精准度要求很严,用单片钻之外,通常都以多片钻,意即每个stack两片或以上.至于几片一钻则视1.板子要求精度2.最小孔径3.总厚度4.总铜层数.来加以考虑. 因为多片一钻,所以钻之前先以pin将每片板子固定住,此动作由上pin机(pinning maching)执行之. 双面板很简单,大半用靠边方式,打孔上pin连续动作一次完成.多层板比较复杂,另须多层板专用上PIN机作业.. 钻孔钻孔机钻孔机的型式及配备功能种类非常多,以下List评估重点A. 轴数:和产量有直接关系B. 有效钻板尺寸C. 钻孔机台面:选择振动小,强度平整好的材质。
D. 轴承(Spindle)E. 钻盘:自动更换钻头及钻头数F. 压力脚G. X、Y及Z轴传动及尺寸:精准度,X、Y独立移动H. 集尘系统:搭配压力脚,排屑良好,且冷却钻头功能I. Step Drill的能力J. 断针侦测K. RUN OUT钻孔房环境设计A. 温湿度控制B. 干净的环境C. 地板承受之重量D. 绝缘接地的考虑E. 外界振动干扰物料介绍钻孔作业中会使用的物料有钻针(Drill Bit),垫板(Back-up board),盖板(Entry board)等.以下逐一介绍:图为钻孔作业中几种物料的示意图.钻针(Drill Bit), 或称钻头,其质量对钻孔的良窳有直接立即的影响, 以下将就其材料,外型构、及管理简述之。
pcb数控钻孔机基本知识
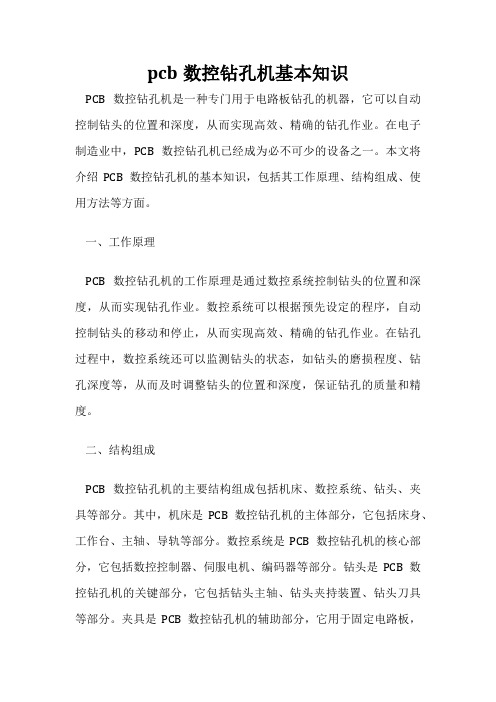
pcb数控钻孔机基本知识PCB数控钻孔机是一种专门用于电路板钻孔的机器,它可以自动控制钻头的位置和深度,从而实现高效、精确的钻孔作业。
在电子制造业中,PCB数控钻孔机已经成为必不可少的设备之一。
本文将介绍PCB数控钻孔机的基本知识,包括其工作原理、结构组成、使用方法等方面。
一、工作原理PCB数控钻孔机的工作原理是通过数控系统控制钻头的位置和深度,从而实现钻孔作业。
数控系统可以根据预先设定的程序,自动控制钻头的移动和停止,从而实现高效、精确的钻孔作业。
在钻孔过程中,数控系统还可以监测钻头的状态,如钻头的磨损程度、钻孔深度等,从而及时调整钻头的位置和深度,保证钻孔的质量和精度。
二、结构组成PCB数控钻孔机的主要结构组成包括机床、数控系统、钻头、夹具等部分。
其中,机床是PCB数控钻孔机的主体部分,它包括床身、工作台、主轴、导轨等部分。
数控系统是PCB数控钻孔机的核心部分,它包括数控控制器、伺服电机、编码器等部分。
钻头是PCB数控钻孔机的关键部分,它包括钻头主轴、钻头夹持装置、钻头刀具等部分。
夹具是PCB数控钻孔机的辅助部分,它用于固定电路板,保证钻孔的稳定性和精度。
三、使用方法PCB数控钻孔机的使用方法主要包括以下几个步骤:1.准备工作:将电路板放置在夹具上,并调整夹具的位置和角度,使其与钻头的位置和角度相匹配。
2.设置参数:根据电路板的要求,设置钻头的直径、深度、转速等参数。
3.启动机器:按下启动按钮,机器开始工作,钻头开始自动控制移动和停止,完成钻孔作业。
4.检查质量:完成钻孔作业后,需要对钻孔的质量进行检查,如钻孔直径、深度、位置等,以确保钻孔的精度和质量。
四、注意事项在使用PCB数控钻孔机时,需要注意以下几个事项:1.安全操作:在操作机器时,需要注意安全,如佩戴防护眼镜、手套等,避免发生意外事故。
2.维护保养:定期对机器进行维护保养,如清洁机器、更换钻头等,以保证机器的正常运行和使用寿命。
3.合理使用:在使用机器时,需要合理使用,如避免过度使用、避免超负荷使用等,以保证机器的稳定性和寿命。
即学即用PCB模数控钻

—i ■ 群
促 成新 手快速 上路 ,实现 即学 即用 。
■“ ! l・
} 一 曩
二 、D I钻 孔 予处 理 RL
现 有 一 用V N 0 0 出 的 钻 孔 代 码 文 件 拷 贝在 I2 0 输 G盘 ,文件 名为 3 31( (L 文 件 )o 3 A1(( 点 3 . _T 径 -r > ¥ 3 3 。>r -_打 文件 ) 内有 N ( 一 步 )L 为20 MM定 位 7 2 , , 1第 T径 .3 L只 N 第 二步 )L 为 08 2( T径 .MM孔 1 只 ,N ( 三步 ) 6 3第 孔径
变换 、G一 项 、H一 单 、 I显 码 、J 显 辅 、K 查 杂 清 一 一 一
询 、 L 存 码 、 M一 图 、 N 加 工 、 O一 描 、 P 参 一 存 一 扫 一 数 ,一 级左 主 菜 单 包括 F 一 画 、 F 一 屏 、 F 一 1重 2满 3 渐
放、F一 4 渐缩 、 F 一 5 显点 、 F 一 6 断跳 、 F 一 7 回退 、 F 一 8 重作 、F 一 9 浏览 、F 孔 径 、F 窗 口。 A一 D一
而 Biblioteka 2 6 0月 5 8 ・ 0 年 9 第期・ 0 t
维普资讯
技 术 交 流
TEe 0 EXC HA G
键 或C r 或 鼠标 右键 即可 ;输 / 个 或 2 以上 的 t +C l X2 个 数据 时 ,数据 之 间用逗 号 隔 开 。 一 级右 主 菜单 包 括 A 打开 、 B 铣 边 、C 优 化 、 D 模 拟 、 E 删 除、F 一 一 一 一 一 一
鼠标单 击左键 ,或 用键盘 输入 菜单 中最 左边 的英 文字
母 ;要选择 用尖括 号括 起来 的命令 提 示默认值 ,只要 按一 下键盘 的任 意键 即可 ,或者 按一 下 鼠标 左键 ;想
PCB数控钻孔机及锣机CNC刀具指令大全

数控钻孔机及锣机CNC刀具指令大全EXCELLON是最早使用电脑化钻机及锣机,它开发了一套电脑控制机器的指令,被称为EXCELLON Computer Numeric Control,其中一些已成为工业标准. EXCELLON 最早开发的是钻机,这时候的格式被称为Format One ,随后又开发了用于锣机的语言,被称为Format Two,1979 年EXCELLON更新了Format Two 语言,将钻机和锣机指令集合到一套通用的语言系统. 因此,早于1979年前的被称为Generation One的机型只能行Format One ,而1979后的被称为Generation Two 的机型则可以使用Format One 或Format Two 语言系统.机器运行有两种程序来驱动:1)系统软件程序由机器的供应商编写,用于机器本身驱动;2)程序体由线路板制造商使用CNC的编程语言,根据客户提供的相关资料编写,用于制造线路板目前,用EXCELLON格式的语言编写的程序可以在不同制造商的机器上使用.程序体组成1)程序头用于描述关于工作的一般信息,通常位于程序主体的开头,是可选的,所有的命令可以在程序运行前,由操作员在控制台上输入机器.包括:a) 钻嘴或锣刀的尺寸.b) 使用的测量系统.c) 工作中X,Y轴的方向.2)程序主体而程序的主体则包含一系列的坐标及指令,通常这些指令会从头到尾的去执行.刀具指令以下一些指令用于选择或控制刀具,其中一些可以单独使用,而另一些可以联合形成一条指令,而当在程序头中使用这些指令时,它们是用于将数据调入CNC-6中的,当这些指令用于程序体时,它们是用来控制刀具的改变或机器的移动。
刀具指令后面的数字用来表明数量,距离,速度等参数,可以从1位到6位,取决于指令的类型.T#T#(#)F#S#C#H#Z+/-#T#刀具选择这个指令可以在手动或自动设置状态下使用,它可以用于程序头或程序主体。
pcb数控钻孔机基本知识
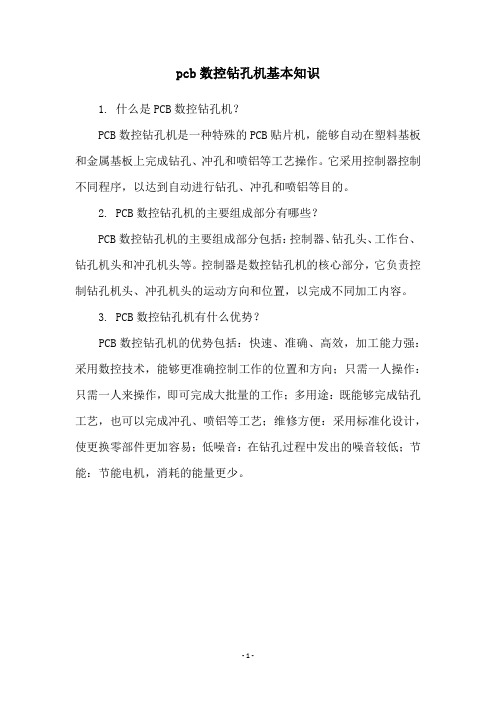
pcb数控钻孔机基本知识
1. 什么是PCB数控钻孔机?
PCB数控钻孔机是一种特殊的PCB贴片机,能够自动在塑料基板和金属基板上完成钻孔、冲孔和喷铝等工艺操作。
它采用控制器控制不同程序,以达到自动进行钻孔、冲孔和喷铝等目的。
2. PCB数控钻孔机的主要组成部分有哪些?
PCB数控钻孔机的主要组成部分包括:控制器、钻孔头、工作台、钻孔机头和冲孔机头等。
控制器是数控钻孔机的核心部分,它负责控制钻孔机头、冲孔机头的运动方向和位置,以完成不同加工内容。
3. PCB数控钻孔机有什么优势?
PCB数控钻孔机的优势包括:快速、准确、高效,加工能力强:采用数控技术,能够更准确控制工作的位置和方向;只需一人操作:只需一人来操作,即可完成大批量的工作;多用途:既能够完成钻孔工艺,也可以完成冲孔、喷铝等工艺;维修方便:采用标准化设计,使更换零部件更加容易;低噪音:在钻孔过程中发出的噪音较低;节能:节能电机,消耗的能量更少。
- 1 -。
- 1、下载文档前请自行甄别文档内容的完整性,平台不提供额外的编辑、内容补充、找答案等附加服务。
- 2、"仅部分预览"的文档,不可在线预览部分如存在完整性等问题,可反馈申请退款(可完整预览的文档不适用该条件!)。
- 3、如文档侵犯您的权益,请联系客服反馈,我们会尽快为您处理(人工客服工作时间:9:00-18:30)。
数控钻--PCB冲裁印制板下料,孔和外形加工都可采用模具冲裁的方法。
冲孔;生产批量大,孔的种类和数量多而形状复杂的单面纸基板和双面非金属化孔的环氧玻璃布基板,通常采用一付或几付模具冲孔。
外形加工:印制板生产批量大的单面板和双面板的外形,通常采用模具冲。
根据印制板的尺寸大小,可分为上落料模和下落料模。
复合加工:印制板的孔与孔,孔与外形之间要求精度高,同时为了缩短制造周期,提高生产率,采用复合模同时加工单面板的孔和外形。
用模具加工印制板,关键是模具的设计、加工,需要专业技术知识,除此之外,模具的安装与调试也十分重要。
1.根据模具设计计算的冲裁力,模具的大小,闭合高度等选择冲床(包括类型,吨位)。
2.开动冲床,全面检查包括离合器、刹车,滑块等各部分是否正常,操作机构是否可靠,决无连冲现象。
3.冲模下的垫铁,一般是2块,必须在磨床上同时磨出,确保模具安装平行、垂直。
垫铁放置的闰置即不防碍落料同时又要尽可能靠近模具中心。
4.要准备几套压板及T形头压板螺钉,以便与模具对应使用。
压板前端不能碰到下模直壁。
各接触面之间应垫砂布,螺钉必须拧紧。
5.模具安装时要十分注意下模上的螺钉、螺母不要碰到上模(上模下降,闭合)。
6.调整模具时尽可能用手动,而不要机动。
7.为改善基材的冲裁性能,纸基板要予热。
其温度以70~90℃为好。
模具冲裁印制板的孔与外形,其质量缺陷有下述几种:1.冲孔时:孔的四周凸起或者铜箔起翘或者分层;孔与孔间有裂纹;孔位置偏或者孔本身不垂直;2.毛刺大;3.断面粗糙4.冲制的印制板成锅底形翘曲;5.废料上跳;6.废料堵塞。
其原因如下:1.冲床的冲裁力、刚性是否足够;2.模具设计是否合理,刚性是否足够;3.凸、凹模的及导柱、导套的加工精度是否达到,安装是否同心、垂直。
配合间隙是否均匀。
4.凸、凹的间隙过小或过大都会产生质量缺陷,是模具设计、加工、调试、使用中最重要的问题。
5.凸、凹模刃口不允许圆角,倒角。
凸模不允许有锥度,特别是冲孔时不论是正锥与倒锥都不允许。
生产中要随时注意凸、凹模刃口是否磨损。
6.排料口是否合理、阻力小。
推料板,打料杆是否合理,力足够。
7.被冲板材厚度,基板的结合力、含胶量,与铜箔的结合力,予热湿度与时间等也是冲裁质量缺陷分析时要考虑的因素。
数控钻--铣工艺铣的技术包括选择,走刀方向、下刀点和定位方法。
是保证铣加工精度的重要方面。
走刀方向图铣刀的切入1,进给的正向 2,进给的反向 3,进给的中性点如图所示,当铣刀切入板材时,有一个被切削面总是迎着铣刀的切削刃,而另一面总是逆着铣刀的切削刃。
前者,被加工面光洁,尺寸精度高。
主轴总是顺时针方向转动。
所以不论是主轴固定工作台运动或是工作台固定主轴运动的数控铣床,在铣印制板的外部轮廓时,要采用逆时针方向走刀。
这就是通常所说的逆铣。
定位方法和下刀点定位方法可分为两种;一是内定位,二是外定位。
定位问题,属于机械工程的范畴。
除上述的铣垫板、销钉之外,定位方法也是很重要的,应使操作者认识。
内定位是通用的方法。
所谓内定位是选择印制板内的安装孔,插拨孔或其它非金属化孔作为定位孔。
孔的相对位置力求在对角线上并尽可能挑选大直径的孔。
实际证明:不能使用金属化孔。
因为孔内镀层厚度的差异会改变一个孔到另一个孔配合的一致性和质量。
还有,在保证印制板定位的条件下,销钉数量愈少愈好。
下刀点和加工顺序选择的好,能使框架保持最大的强度。
选择的不好,框架变形而使印制板报废。
铣的工艺参数用硬质合金铣刀铣印制板外形,铣刀的切削速度为180~270m/min。
计算公式如下:S=pdn/1000(m/min)式中:p:PI(3.1415927)d:铣刀直径,mmn;铣刀转速,r/min与切削速度相匹配的是进给。
若进给太低,由于磨擦热使印制板材料软化甚至溶化或烧焦,堵塞铣刀的排屑槽,切削无法进行。
如果进给太快,铣刀磨损快,承受的径向负荷大,让刀量大,工作质量差,尺寸不一致。
如何判断进给的快慢呢?要考虑下述诸项:印制板材料,厚度,每叠块数,铁刀直径、排屑槽。
只有低于额定负载,主轴马达的转速才能保持。
负载增大,转速下降,直至铣刀折断。
有两种情况造成此结果:一是主轴马达功率不足,二是每叠板数太多,切削负荷太大。
通常叠板块数不大于表推荐值。
数控钻--数控铣定位所谓数控铣的定位,就是用定位销将待加工的印制板定位到铣床的工作台上,从而方便、准确地加工印制板外形。
要求定位简单可靠,能快速装、卸板同时能排除切屑。
定位方法有多种,如有的数铣床设计了往复式工作台,当一个工作台在加工时,另一个工作台装、卸板。
还有用两套铣定位垫板的方法,当一个铣定位垫板在数控铣工作台上加工时,另一个铣定位垫板在平台上装、卸板。
两者交换只需几秒钟。
数控铣工作台本身就是一块定位板,它是一块以销钉定位,螺钉固定的铝合金板。
在每个数控铣的主轴之下工作台面上有一孔一槽式定位系统。
铣垫板实际上是中间定位夹具,有时称为“软定位”。
要求其既能可靠的定位又能快速卸板,减少辅助时间,提高生产效率。
在铣外形之前,在铣垫板上预先铣出和印制板外形尺寸一样的沟槽。
一般,槽宽的尺寸是实际加工用铣刀直径加0。
5mm。
槽深是2。
5mm。
在加工过程中,它是铣刀运动轨迹的一条通路。
由于吸尘器吸尘,在沟槽里产生一股气流,排除切屑,使被加工更光洁,防止切屑堵塞铣刀排屑槽,降低锋。
加工时,要使铣刀伸进沟槽1。
5~2mm。
这样可防止由于铣刀连续切入板材使末端磨损,直径减小以及由于铣刀制造允许的末端直径减小等造成印制板加工尺寸的偏差。
在每个批量生产之前,在数控铣工作台上装好铣垫板,拧上新的尼龙螺纹塞。
在螺纹塞上钻孔,装上定位销即可使用。
铣垫板上的排屑槽,铣的更深更宽一些,会更利于气流畅通,排屑,使被加工表面更光洁。
但是,却减弱了支撑面,特别是排屑槽靠近定位销时,将使定位不牢固。
大多数铣垫板采用非金属层压板。
材料相对是软的。
当销钉反复的装、卸,定位孔磨损、扩大。
如半专用性、消耗性铣垫板就是在这样的条件下工作的。
通常,销钉在铣垫板上压配,过盈量0.005~0.01mm。
如果是专用性铣垫板或采用高密纤维板作铣垫板,则采用更紧的配合为好。
但半专用性铣垫板或消耗性铣垫板,过盈量大于0.007mm,在压配销钉时,有可能使销孔内的部分基材切下,形成深的槽或空隙。
销子反复的装、卸,层压板的销孔也产生分层或碎裂。
在铣印制板时,切销力大部分由定位销承受,这种侧向压力挤压销孔再加上孔内缺陷,使销钉一个一个的松动偏斜。
它直接影响印制板的外形尺寸,不能保证严格的公差。
定位销直径愈小,相对的偏斜量也愈大。
所以,应尽可能采用大直径的孔作为定位孔。
定位销直径和偏斜量也直接影响生产率。
例如,原定一叠四块,一次可铣完。
由于销钉直径小,偏斜量大,那么只好铣三块,使效率降低25%。
在加工过程中,定位销应紧密配合,使加工板可靠定位。
而不应靠胶粘带或胶粘剂的帮助,因为这要花时间去粘接、固化。
紧密配合也意味着严格的公差,铣多层板或高质量双面板也能保证精度。
通常,钻头直径是下偏差,一般是0~0.005mm,有的是0~0.01mm。
大多数非金属层压板,钻孔后有一定的收缩量,一般为0.005~0.007mm。
这样的下偏差为0.005~0.01mm的孔配上标准销钉,可产生0.005mm的过盈量。
因而不必考虑特别的加工技术,也不必去逐个测量钻头直径,挑选小直径钻头,就可以达到压配合的要求,节省了时间。
例如,某种1.6mm厚的印制板,外形公差±0.013mm,每次铣四块一叠。
钻孔位置公差+/-0.025mm,钻孔直径差±0.025mm,使用标准销钉。
那么装、卸板困难,费时间。
因为有可能使销钉锁紧在被铣板材里。
本例指出销钉与被板配合,要采用较松的滑配合。
当然,如果间隙太大,要影响加工精度和边缘光洁。
数控钻--钻孔质量印制板钻孔的质量缺陷,分为钻孔缺陷和孔内缺陷。
钻孔缺陷有偏孔、多孔、漏孔和孔径错。
以及断钻头、堵孔、未钻透。
孔内缺陷:可分铜箔缺陷和基材缺陷铜箔的缺陷1.分层:与基板分离。
2.钉头:内层毛刺。
3.腻污:热和机械的粘附层。
4.毛刺:钻孔后留在表面的突出物。
5.碎屑:机械性的粘附物。
6.粗糙:机械性的粘附物。
基板缺陷1.分层:基板层间分离。
2.空洞:增强纤维被撕开而留下的空腔。
3.碎屑堆:堆积在空腔里碎屑。
4.腻污:热和机械的粘附层。
5.松散纤维:未粘结牢的纤维。
6.沟糟:树脂上的条纹。
7.来福线:螺旋形凹槽线。
数控钻--垫板印制板钻孔,使用上、下垫板有利于提高印制板的质量、提高成品率。
虽然,由于使用这种辅助材料有一定花费,但由于上述原因,事实上是降低了成本。
对钻孔用上垫板的要求是:有一定表面硬度防止钻孔上表面毛刺。
但又不能太硬而磨损钻头。
要求上垫板本身成份不合树脂,否则钻孔时将腻污孔。
要求导热系数大,能迅速将钻孔时产生的热量带走,降低钻孔温度。
要有一定的刚性防止提钻时板材颤动,又要有一定弹性当钻头下钻接触的瞬间立即变形,使钻头精确地对准被钻孔的位置,保证钻孔位置精度。
如果上垫板表面又硬又滑,钻头可能打滑偏离原来的孔位。
目前国内使用的上垫板主要时0.3~0.5mm厚的酚醛纸胶板环氧玻璃布板和铝箔如厚度0.3mm的LF2Y2(2号防锈铝,半冷作硬化状态)或LF21Y(21号防锈铝,冷作硬化状态)作为普通双面板钻孔的上垫板,效果较好,达到:∙硬度适宜,可以防止钻孔上表面毛刺;∙铝导热性好,对钻头有一定散热作用,能降低钻孔温度;∙与酚醛板、环氧板相比较,不会因为所含树脂而腻污孔。
国外有一种复合上垫板,其上、下两层是0。
06mm的铝合金箔,中间层是纯纤维质的芯,总厚度是0。
35mm。
不难看出,这种结构和材质能满足印制板钻孔上垫板的要求,用于高质量多层板的上垫板,其优点是:∙提高了钻孔质量;∙保证了孔位精度;延长了钻头寿命。
为适宜钻小孔和钻SMT或FPT板的孔,相应的将复合上垫板的厚度减到0.16mm,成为薄复合上垫板。
数控钻--钻头钻头参数要注意下述6点1.钻头的种类与几何形状2.材质3.拿刀与放刀4.精度5.表面粗糙度6.重磨次数钻头的种类与结构印制板钻孔用钻头有直柄麻花钻头、定柄麻花钻头和铲形钻头。
直柄麻花钻头大都用于单头钻床,钻较简单的印制板或单面板,钻孔深度可达钻头直径的10倍。
在基板叠层不高的情况下,使用钻套可避免钻偏。
在“Y“范围内,裂纹、缺口、气孔和其它表面缺陷深度不大于0.0127mm,宽度不大于0.0254mm。
在“X“=1。
5直径范围内,不允许有裂纹,缺口和气孔。
定柄钻头的特点是能实现自动更换钻头。
定位精度高,不需要使用钻套。
大螺旋角,排屑速度快,适于高速切削。
在排屑槽全长范围内,钻头直径是一个倒锥,钻削时与孔壁的磨擦小,钻孔质量较高。