树脂基复合材料原位固化制造技术概述
树脂基复合材料

透光性、抛光性能、及保持表面光滑的性能极佳,且耐磨 耗性能较好。
为了提高填料添加量,事先在工厂中通过机械强力混 合向树脂基质中加入较多的超微填料,后用机械方式 粉碎成预聚合填料。
将预聚合填料与超微填料添加到树脂基质,制出含有 预聚合填料的复合树脂。
用于牙齿缺损、缺失的直接或间接修复。
第一节 组成及固化反应
一、组成
(一)树脂基质
树脂基质是复合树脂的主体成分,主要作用是 将复合树脂的各组成粘附结合在一起,赋予可 塑性、固化特性和强度。
树脂基质由含两个或两个以上的甲基丙烯酸酯 官能团的单体构成。
树脂基质----双酚A双甲基丙烯酸缩水甘油酯(BIS-GMA)
结合来实施聚合。
第二节 复合树脂
一、分类
(一)按无机填料大小分类
1、 超微填料复合树脂 2、 混合填料复合树脂 3、 纳米填料复合树脂
1、 超微填料复合树脂
超微填料(microfiller)的初级粒子平均直径为0.04μm ,但相互黏附、聚集使粒径为0.4-0.7μm。
超微粒子表面积大,增稠作用大,填料的添加量一般不超 过38%,
1.流动性(flowable)复合树脂 较大的流动性,注射到牙齿的微小窝洞内。 无机填料含量少,弹性模量低。 固化深度可达4mm 大体积充填复合树脂。 2. 可压实复合树脂 无机填料含量高(70%~80%),充填时材料不易
从周围挤出,易压实,特别是容易形成良好的后牙邻 面接触点。该材料主要用于后牙较大缺损的修复。
(三)按应用部位分类
1.前牙(anterior)复合树脂 具有优良的色泽、半透明性和抛光性能。 超微填料复合树脂就是一种前牙复合树脂。
树脂基复合材料成型工艺的发展
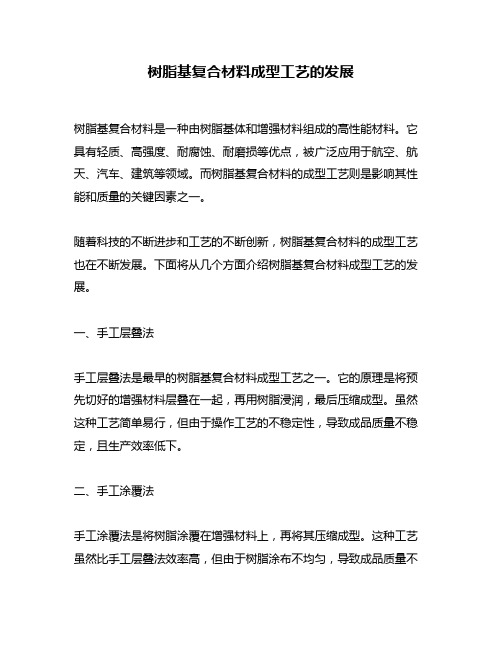
树脂基复合材料成型工艺的发展树脂基复合材料是一种由树脂基体和增强材料组成的高性能材料。
它具有轻质、高强度、耐腐蚀、耐磨损等优点,被广泛应用于航空、航天、汽车、建筑等领域。
而树脂基复合材料的成型工艺则是影响其性能和质量的关键因素之一。
随着科技的不断进步和工艺的不断创新,树脂基复合材料的成型工艺也在不断发展。
下面将从几个方面介绍树脂基复合材料成型工艺的发展。
一、手工层叠法手工层叠法是最早的树脂基复合材料成型工艺之一。
它的原理是将预先切好的增强材料层叠在一起,再用树脂浸润,最后压缩成型。
虽然这种工艺简单易行,但由于操作工艺的不稳定性,导致成品质量不稳定,且生产效率低下。
二、手工涂覆法手工涂覆法是将树脂涂覆在增强材料上,再将其压缩成型。
这种工艺虽然比手工层叠法效率高,但由于树脂涂布不均匀,导致成品质量不稳定。
三、自动化层叠法自动化层叠法是将预先切好的增强材料通过机器自动层叠,再用树脂浸润,最后压缩成型。
这种工艺具有生产效率高、成品质量稳定等优点,但由于机器设备的成本较高,导致生产成本较高。
四、自动化涂覆法自动化涂覆法是将树脂通过机器自动涂覆在增强材料上,再将其压缩成型。
这种工艺具有生产效率高、成品质量稳定等优点,但由于机器设备的成本较高,导致生产成本较高。
五、注塑成型法注塑成型法是将树脂和增强材料混合后,通过注塑机器将其注入模具中,最后压缩成型。
这种工艺具有生产效率高、成品质量稳定等优点,但由于模具成本较高,导致生产成本较高。
综上所述,树脂基复合材料成型工艺的发展经历了从手工到自动化的演变过程。
随着科技的不断进步和工艺的不断创新,树脂基复合材料的成型工艺将会更加智能化、高效化和环保化。
史上最全树脂基复合材料成型工艺,详解

史上最全树脂基复合材料成型⼯艺,详解复合材料成型⼯艺是复合材料⼯业的发展基础和条件。
随着复合材料应⽤领域的拓宽,复合材料⼯业得到迅速发展,⼀些成型⼯艺⽇臻完善,新的成型⽅法不断涌现,⽬前聚合物基复合材料的成型⽅法已有20多种,并成功地⽤于⼯业⽣产,如:⼀、接触低压成型⼯艺接触低压成型⼯艺的特点是以⼿⼯铺放增强材料,浸清树脂,或⽤简单的⼯具辅助铺放增强材料和树脂。
接触低压成型⼯艺的另⼀特点,是成型过程中不需要施加成型压⼒(接触成型),或者只施加较低成型压⼒(接触成型后施加0.01~0.7MPa压⼒,最⼤压⼒不超过2.0MPa)。
接触低压成型⼯艺过程,是先将材料在阴模、阳模或对模上制成设计形状,再通过加热或常温固化,脱模后再经过辅助加⼯⽽获得制品。
属于这类成型⼯艺的有⼿糊成型、喷射成型、袋压成型、树脂传递模塑成型、热压罐成型和热膨胀模塑成型(低压成型)等。
其中前两种为接触成型。
接触低压成型⼯艺中,⼿糊成型⼯艺是聚合物基复合材料⽣产中最先发明的,适⽤范围最⼴,其它⽅法都是⼿糊成型⼯艺的发展和改进。
接触成型⼯艺的最⼤优点是设备简单,适应性⼴,投资少,见效快。
根据近年来的统计,接触低压成型⼯艺在世界各国复合材料⼯业⽣产中,仍占有很⼤⽐例,如美国占35%,西欧占25%,⽇本占42%,中国占75%。
这说明了接触低压成型⼯艺在复合材料⼯业⽣产中的重要性和不可替代性,它是⼀种永不衰落的⼯艺⽅法。
但其最⼤缺点是⽣产效率低、劳动强度⼤、产品重复性差等。
1、原材料接触低压成型的原材料有增强材料、树脂和辅助材料等。
(1)增强材料接触成型对增强材料的要求:①增强材料易于被树脂浸透;②有⾜够的形变性,能满⾜制品复杂形状的成型要求;③⽓泡容易扣除;④能够满⾜制品使⽤条件的物理和化学性能要求;⑤价格合理(尽可能便宜),来源丰富。
⽤于接触成型的增强材料有玻璃纤维及其织物,碳纤维及其织物,芳纶纤维及其织物等。
(2)基体材料接触低压成型⼯艺对基体材料的要求:①在⼿糊条件下易浸透纤维增强材料,易排除⽓泡,与纤维粘接⼒强;②在室温条件下能凝胶,固化,⽽且要求收缩⼩,挥发物少;③粘度适宜:⼀般为0.2~0.5Pa·s,不能产⽣流胶现象;④⽆毒或低毒;⑤价格合理,来源有保证。
树脂基复合材料成型工艺介绍

树脂基复合材料成型工艺介绍树脂基复合材料成型工艺介绍(1):模压成型工艺模压成型工艺是复合材料生产中最古老而又富有无限活力的一种成型方法。
它是将一定量的预混料或预浸料加入金属对模内,经加热、加压固化成型的方法。
模压成型工艺的主要优点:①生产效率高,便于实现专业化和自动化生产;②产品尺寸精度高,重复性好;③表面光洁,无需二次修饰;④能一次成型结构复杂的制品;⑤因为批量生产,价格相对低廉。
模压成型的不足之处在于模具制造复杂,投资较大,加上受压机限制,最适合于批量生产中小型复合材料制品。
随着金属加工技术、压机制造水平及合成树脂工艺性能的不断改进和发展,压机吨位和台面尺寸不断增大,模压料的成型温度和压力也相对降低,使得模压成型制品的尺寸逐步向大型化发展,目前已能生产大型汽车部件、浴盆、整体卫生间组件等。
模压成型工艺按增强材料物态和模压料品种可分为如下几种:①纤维料模压法是将经预混或预浸的纤维状模压料,投入到金属模具内,在一定的温度和压力下成型复合材料制品的方法。
该方法简便易行,用途广泛。
根据具体操作上的不同,有预混料模压和预浸料模压法。
②碎布料模压法将浸过树脂胶液的玻璃纤维布或其它织物,如麻布、有机纤维布、石棉布或棉布等的边角料切成碎块,然后在金属模具中加温加压成型复合材料制品。
③织物模压法将预先织成所需形状的两维或三维织物浸渍树脂胶液,然后放入金属模具中加热加压成型为复合材料制品。
④层压模压法将预浸过树脂胶液的玻璃纤维布或其它织物,裁剪成所需的形状,然后在金属模具中经加温或加压成型复合材料制品。
⑤缠绕模压法将预浸过树脂胶液的连续纤维或布(带),通过专用缠绕机提供一定的张力和温度,缠在芯模上,再放入模具中进行加温加压成型复合材料制品。
⑥片状塑料(SMC)模压法将SMC片材按制品尺寸、形状、厚度等要求裁剪下料,然后将多层片材叠合后放入金属模具中加热加压成型制品。
⑦预成型坯料模压法先将短切纤维制成品形状和尺寸相似的预成型坯料,将其放入金属模具中,然后向模具中注入配制好的粘结剂(树脂混合物),在一定的温度和压力下成型。
树脂复合材料的制备

树脂复合材料的制备树脂复合材料是一种将树脂和增强材料(如玻璃纤维、碳纤维等)组合起来制成的新型材料。
因为其轻便、高强度、高耐腐蚀性等特点,已被广泛应用于航空、汽车、建筑等领域。
本文将介绍树脂复合材料的制备方法。
一、预处理1. 增强材料的选择和预处理增强材料的选择会影响到复合材料的性能。
根据不同的应用领域,可以选择不同类型的增强材料。
例如,玻璃纤维适用于一般用途,碳纤维则适用于高强度、高刚度的要求。
在使用增强材料前,需要将其涂覆上一层“大小粒子”填充物,以提高增强材料表面的粗糙度和附着力。
2. 树脂的选择和预处理树脂的选择和预处理也会对复合材料的性能产生影响。
常用的树脂有环氧树脂、酚醛树脂、聚酯树脂等。
在选择树脂的时候需要考虑到其生产工艺、成本和使用需求。
为了提高树脂的附着力和表面粗糙度,也需要对树脂进行预处理。
二、混合制备将增强材料和树脂按照一定比例混合起来,制备成树脂基复合材料。
在混合制备的过程中需要注意混合比例、混合时间以及混合温度等因素。
如果混合比例不正确,会使得复合材料的性能受到影响;如果混合时间过短,会使得树脂和增强材料不充分混合;如果混合温度过高,会导致树脂的分解或黏度增大。
三、成型完成混合制备之后,需要将其成型。
常用的成型方式有手工层压法、自动层压法、挤出成型法等。
其中,手工层压法适用于小型复合材料的制备,自动层压法适用于中小型复合材料的制备,挤出成型法适用于大型复合材料的制备。
四、固化完成成型之后,还需要对复合材料进行固化。
固化是指在一定温度和时间下,使得树脂分子间发生交联反应,形成强度高、密度大的复合材料。
常用的固化方式有热固化和光固化。
其中,热固化适用于大型复合材料的固化,光固化适用于小型复合材料的固化。
五、后处理完成固化之后,复合材料还需要进行后处理。
后处理包括切割、修整、打磨、测量等步骤。
通过切割、修整和打磨可以得到满足要求的形状和尺寸,通过测量可以检查复合材料的尺寸和性能。
树脂基复合材料

树脂基复合材料树脂基复合材料》是一种具有广泛应用潜力的新型材料。
它是由树脂基质和增强材料组成的复合材料,兼具树脂的优良性能和增强材料的高强度特性。
树脂基复合材料在现代工程和科技领域中得到了广泛应用。
它的出现主要是为了解决传统材料的局限性,例如金属材料的重量和腐蚀问题,以及陶瓷材料的脆性。
树脂基复合材料具有优异的物理性能和化学稳定性,能够满足多种应用需求。
树脂基复合材料的基本结构包括树脂基质和增强材料。
树脂基质通常是一种聚合物,如环氧树脂、聚酯树脂或聚丙烯等。
增强材料可以是纤维(如碳纤维、玻璃纤维)或颗粒(如陶瓷颗粒、金属颗粒)等。
通过将树脂基质与增强材料结合起来,形成了具有优异性能的树脂基复合材料。
树脂基复合材料具有许多优点。
首先,它们具有较低的密度和高强度,使其成为替代传统材料的理想选择。
其次,树脂基复合材料具有良好的耐腐蚀性和耐热性,在恶劣环境下仍能保持稳定性。
此外,它们还具有良好的可加工性,可以通过各种加工方法制备成不同形状和尺寸的产品。
总之,《树脂基复合材料》是一种具有广泛应用潜力的新型材料,通过将树脂基质与增强材料结合,能够满足多种工程和科技领域的需求。
树脂基复合材料主要由树脂和增强物构成。
树脂是树脂基复合材料的主要基质,在其中起到粘结和固化增强物的作用。
树脂可以是不同类型的聚合物,如环氧树脂、酚醛树脂、聚酰亚胺树脂等。
这些树脂具有良好的粘结性和成型性,能够满足不同应用需求。
增强物是树脂基复合材料中的另一个关键组成部分,用于增强材料的机械性能和耐久性。
常见的增强物包括纤维材料、颗粒材料和填料等。
纤维材料常用的有玻璃纤维、碳纤维和芳纶纤维等,它们具有较高的强度和刚度,可在复合材料中增强和增加承载能力。
颗粒材料可用于提高复合材料的硬度和耐磨性。
填料可以改善复合材料的流动性和加工性能。
树脂和增强物的选择根据应用需求和性能要求而定,通过合理的配方可以获得具有优异性能的树脂基复合材料。
这种复合材料在航空航天、汽车、建筑和电子等领域具有广泛的应用前景。
树脂基复合材料和应用
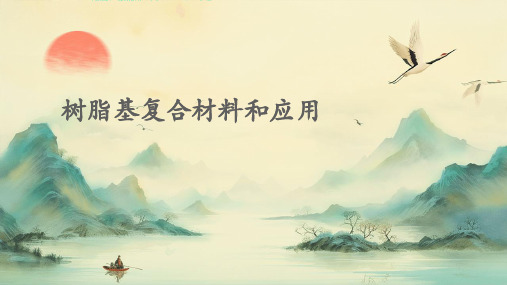
缩短产品研发周期。
连续纤维增强技术
02
优化连续纤维增强复合材料的制造工艺,提高纤维的排布密度
和增强效率,以获得更好的力学性能。
绿色制造技术
03
采用环保型的制造工艺和原材料,降低复合材料生产过程中的
环境污染和资源消耗。应用来自域的拓展新能源汽车领域
利用树脂基复合材料的轻质、高强度特点,开发新能源汽车车身、 底盘等关键部件,提高车辆能效和安全性。
纤维增强工艺是将纤维增强材料 与树脂基体进行复合的过程,是 树脂基复合材料制造的关键环节
之一。
常见的纤维增强工艺包括手糊成 型、喷射成型、模压成型和层压 成型等,不同的工艺适用于不同
类型和规模的复合材料制品。
纤维增强工艺对复合材料的性能 和外观质量有重要影响,因此需 要选择合适的工艺参数和技术条
件。
树脂基复合材料和应用
• 树脂基复合材料简介 • 树脂基复合材料的制造工艺 • 树脂基复合材料的应用领域 • 树脂基复合材料的优势与局限性 • 未来发展方向与前景
01
树脂基复合材料简介
定义与特性
定义
树脂基复合材料是由有机高分子 化合物(树脂)作为基体,与纤 维、填料、添加剂等经过复合工 艺结合而成的材料。
电子产品
电路板
树脂基复合材料可以作为电子产品的电路板,具有优良的绝缘性能和耐热性。
手机外壳
手机外壳通常采用树脂基复合材料制造,具有轻量化和美观等特点。
04
树脂基复合材料的优势与局限性
材料优势
高强度与轻量化
树脂基复合材料具有高强度和轻量化的特点,能 够满足现代工业对高性能材料的需求。
可设计性强
树脂基复合材料的组成和结构可以根据需要进行 调整,具有很强的可设计性。
热塑性树脂基复合材料激光原位固化研究进展

生产[12‑16]。
图2
Fig. 2
图1
Fig. 1
激光原位固化铺放头
Laying head of laser in‑situ curing equipment
激光原位固化过程是:热塑性预浸带通过输送装
置传送到压辊下方,预浸带受到激光辐射加热,碳纤维
材料名称
弯曲强度/MPa
弯曲模量/GPa
拉伸强度/MPa
拉伸模量/GPa
压缩强度/GPa
热变形温度/℃
PEEK
142
4. 0
97
2. 8
130
230
聚四氟乙烯(PTFE)
13
0. 7
20
0. 4
12
55
聚苯醚(PPO)
110
2. 0
66
2. 7
100
190
聚酰亚胺(TPI)
176
3. 3
116
3. 0
国外经过 30 多年的发展,该技术已从实验研究迈
入工程应用阶段。热塑性树脂基复合材料目前已成功
地应用于空客 A340‑600 机翼前缘等次承载结构、电磁
炮轨道、汽车、导弹壳体及 V22 鱼鹰直升机机身壁板等
复杂结构形式的零件制造中(图 3、4)。美国 Automat‑
ed Dynamics 公司以及法国 Coriolis 公司均采用机器人
Key words:laser in‑situ curing;thermoplastic;composite;crystallization kinetics;temperature field;the laser absorption
先进树脂基复合材料制造技术探析

先进树脂基复合材料制造技术探析引言早在1990年末,关于复合材料飞机有关的概念就已被人们提出,但至今,这一构想仍然没有实现,究其主要原因是,构成复合材料的成本要比铝合金构件的成本高很多,因而较高的成本使得航空航天等相关领域难以运用此技术。
所以,基于此,当前在复合材料界一致认为在原先已有的主要材料基础上,再进行新复合材料的开发很有必要。
1 树脂基复合材料制造技术综述及应用1.1低温固化技术在复合材料中低温固化技术一般是指固化时的温度不超过100摄氏度,能够在自由的形态下对复合材料进行高温处理的一种制造技术。
对低温固化技术进行研究,能够有效降低复合材料在生产中使用的昂贵模具、耗能较多的设备以及性能较高的工艺辅料时需要的费用。
除此以外,低温固化复合材料构件具有较高精度的尺寸,且固化残余的应力不够高,因此很适合用在制备大型的且形态比较复杂的复合材料构件,还能够对复合材料结构进行修补以及复合材料工装材料上。
低成本制造技术中最为重要的一个组成部分即是复合材料低温固化技术,由于低温固化复合材料,尤其是由于真空压力而形成的复合材料,成型时受到的压力较低,温度也不够高,因此,复合材料的孔隙率会比较高,对于复合材料的力学性能以及湿热性能有着十分严重的影响。
所以,在复合材料的低温固化技术的具体应用中,最需要关注的问题就是如何降低材料孔隙率。
1.2 树脂传递模塑技术所谓的树脂传递模塑技术又称之为RTM技术,其是一种比较适用于品种较多,批量中等,质量较高的复合材料构件的一种成本较低的成型技术,该技术的基本原理是将预成型的增强体放置在模具中,待模具闭合后,在模具内注入所需的树树脂,当材料被树脂充分浸润后,再进行固化加热,而后脱模,从而获得新产品。
树脂传递模塑技术最为突出的一个特点就是能够将树脂浸润的过程,固化成型的过程、增强纤维结构设计和制造等环节分开进行,这样一来便能够确保设计者创造出的材料设计剪裁足够独特,以达到技术上精确且复杂的要求。
先进树脂基复合材料制造技术进展

先进树脂基复合材料制造技术进展摘要:先进的树脂基复合材料是一种新型材料,以有机聚合物材料为基体,以高性能连续纤维为增强材料,由复合技术制备,性能明显优于原组分。
目前,在航空航天领域广泛应用的先进树脂基复合材料主要包括环氧、双马来酰亚胺和高性能连续纤维增强聚酰胺基复合材料。
先进的树脂基复合材料具有较高的强度和比模量、疲劳强度、耐腐蚀性、高的可设计性和便于在大面积内进行整体成型。
它们已成为铝合金、钛合金和钢材后最重要的航空结构材料之一,并已广泛应用于航空航天等领域。
关键词:树脂基复合材料;制造技术;模拟与优化技术;自动化制造;国家先进的树脂基复合材料制造技术经过30多年的发展,初步形成了一个先进的树脂基复合材料制造系统,其表现形式是热熔预浸料的制造、自成型和树脂转移技术(RTM),以及制备的先进树脂基复合材料在中得到广泛应用。
一、热压罐成型技术与数字化、自动化技术相结合热压罐成型技术的主要过程包括预浸料制备、切割、摊铺和固化。
热压罐成型技术的优点是:(1)纤维体积含量高;(2)质量稳定性好;(3)成型模具简单。
但热压罐成型工艺存在能耗高、设备投资成本高、零件尺寸受热压罐尺寸限制等问题。
20世纪60年代以来,我国热压罐成型技术有了很大发展,主要体现在热熔预浸料制备技术、预浸料铺切技术和数字化集成的建立,以及高韧性复合材料技术和复合材料结构集成技术的快速发展和广泛应用。
早期国产复合预浸料采用溶液法制造,由于有机溶剂的大量使用和生产的不连续,导致预浸料质量一致性差,生产效率低,污染严重。
20世纪90年代初以来,预浸料热熔制备技术得到发展,建立了热熔预浸料设备设计制造技术和预浸料热熔制备技术,实现了热熔预浸料的连续批量制造。
通过多层次增韧技术的发展,建立了高性能复合材料的增韧技术体系,开发出满足航空应用要求的高韧性环氧和高韧性双马来酰亚胺树脂基复合材料体系。
热压罐成型技术从最初以手工为主的铺切发展到与预浸料自动下料、激光辅助定位铺放等数字化技术相结合,提高了热压罐成型的技术水平,明显提高了预浸料的铺切精度,进一步提高了复合材料的制造效率和构件质量。
原位固化技术
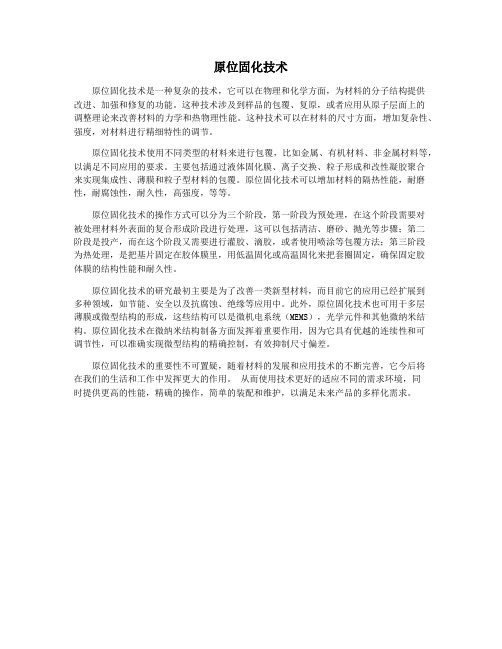
原位固化技术原位固化技术是一种复杂的技术,它可以在物理和化学方面,为材料的分子结构提供改进、加强和修复的功能。
这种技术涉及到样品的包覆、复原,或者应用从原子层面上的调整理论来改善材料的力学和热物理性能。
这种技术可以在材料的尺寸方面,增加复杂性、强度,对材料进行精细特性的调节。
原位固化技术使用不同类型的材料来进行包覆,比如金属、有机材料、非金属材料等,以满足不同应用的要求。
主要包括通过液体固化膜、离子交换、粒子形成和改性凝胶聚合来实现集成性、薄膜和粒子型材料的包覆。
原位固化技术可以增加材料的隔热性能,耐磨性,耐腐蚀性,耐久性,高强度,等等。
原位固化技术的操作方式可以分为三个阶段,第一阶段为预处理,在这个阶段需要对被处理材料外表面的复合形成阶段进行处理,这可以包括清洁、磨砂、抛光等步骤;第二阶段是投产,而在这个阶段又需要进行灌胶、滴胶,或者使用喷涂等包覆方法;第三阶段为热处理,是把基片固定在胶体膜里,用低温固化或高温固化来把套圈固定,确保固定胶体膜的结构性能和耐久性。
原位固化技术的研究最初主要是为了改善一类新型材料,而目前它的应用已经扩展到多种领域,如节能、安全以及抗腐蚀、绝缘等应用中。
此外,原位固化技术也可用于多层薄膜或微型结构的形成,这些结构可以是微机电系统(MEMS),光学元件和其他微纳米结构。
原位固化技术在微纳米结构制备方面发挥着重要作用,因为它具有优越的连续性和可调节性,可以准确实现微型结构的精确控制,有效抑制尺寸偏差。
原位固化技术的重要性不可置疑,随着材料的发展和应用技术的不断完善,它今后将在我们的生活和工作中发挥更大的作用。
从而使用技术更好的适应不同的需求环境,同时提供更高的性能,精确的操作,简单的装配和维护,以满足未来产品的多样化需求。
复合材料基体固化成型工艺综述

浙江科技学院学报,第20卷第4期,2008年12月Jo ur na l of Zhejiang U niv ersity of Science and T echnolog yVo l.20No.4,Dec.2008复合材料基体固化成型工艺综述诸爱士1,郑传祥2,成忠1(1.浙江科技学院生物与化学工程学院,杭州310023;2.浙江大学材料与化学工程学院,杭州310027)摘要:树脂基复合材料具有比强度高、比模量高、抗疲劳性能优良、工艺性能良好及具有可设计性等特点,一直受到工业界的重视,各种复合材料产品被应用到各行各业,尤其是在航空航天领域。
复合材料从原材料到形成制品的过程,都需经过固化与成型,方法已经有几十种。
文中介绍了国内外复合材料主要的基体固化方法、成型工艺和相关研究;固化方法主要有热固化、辐射固化与微波固化等,成型工艺主要有模压成型、渗透成型、缠绕成型与拉挤成型等;同时,对工艺研究与应用也进行了展望。
关键词:复合材料;基体固化;成型工艺中图分类号:T Q322.4;T B332文献标识码:A文章编号:1671-8798(2008)04-0269-05Review of matrix solidification and forming processes ofcomposite materialsZH U A-i shi1,ZH ENG Chuan-x iang2,CH ENG Zhong1(1.Schoo l of Biolog ical and Chemical Eng ineer ing,Zhejiang U niversity of Science and Technology,Hangzhou310023,China; 2.Co llege of M aterials Science and Chem ical Engineering,Z hejiang U niv ersity,H ang zho u310027,China)Abstract:Resin matrix com posite materials have characteristics such as high streng th ratio and modulus ratio,good ant-i fatigue pro perties and techno logy perform ance,able to desig n and so on.In the industr ial it has alw ays been attached im por tance.Various co mpo site m aterials products have been applied to all w alks o f life,especially the aerospace field.T he process from raw m aterial to create products o f com po site mater ials need all to cure and fo rm.The w ays of curing and form-ing hav e been do zens.We introduce m ajo r matr ix so lidification methods and fo rming pr ocesses of com po site materials domestic and foreign,and related researches.So lidification methods m ainly in-clude heat-curing,radiation-curing and micro w av e-curing.For ming processes mainly include die pressing form ing,penetration for ming,w inding forming,draw and w ring fo rming.T he pr ospect of processes resear ch and application are described.Key words:composite m aterials;matrix so lidification;form ing technique收稿日期:2008-08-19基金项目:浙江省科技计划重点项目(2007C21063)作者简介:诸爱士(1966)),男,浙江湖州人,副教授,主要从事单元操作与应用化学研究。
树脂基复合材料
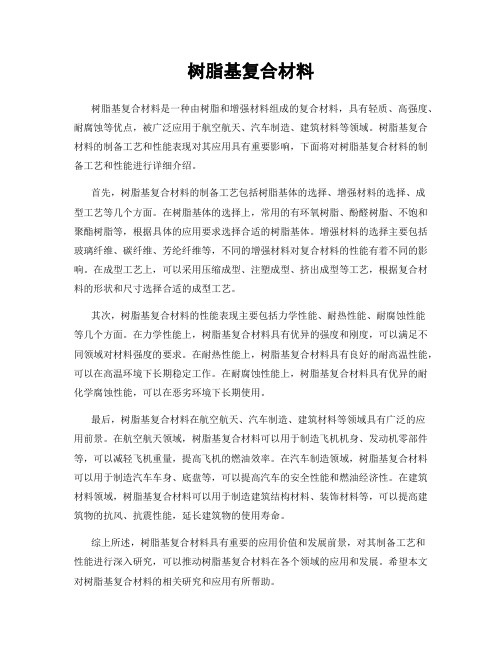
树脂基复合材料树脂基复合材料是一种由树脂和增强材料组成的复合材料,具有轻质、高强度、耐腐蚀等优点,被广泛应用于航空航天、汽车制造、建筑材料等领域。
树脂基复合材料的制备工艺和性能表现对其应用具有重要影响,下面将对树脂基复合材料的制备工艺和性能进行详细介绍。
首先,树脂基复合材料的制备工艺包括树脂基体的选择、增强材料的选择、成型工艺等几个方面。
在树脂基体的选择上,常用的有环氧树脂、酚醛树脂、不饱和聚酯树脂等,根据具体的应用要求选择合适的树脂基体。
增强材料的选择主要包括玻璃纤维、碳纤维、芳纶纤维等,不同的增强材料对复合材料的性能有着不同的影响。
在成型工艺上,可以采用压缩成型、注塑成型、挤出成型等工艺,根据复合材料的形状和尺寸选择合适的成型工艺。
其次,树脂基复合材料的性能表现主要包括力学性能、耐热性能、耐腐蚀性能等几个方面。
在力学性能上,树脂基复合材料具有优异的强度和刚度,可以满足不同领域对材料强度的要求。
在耐热性能上,树脂基复合材料具有良好的耐高温性能,可以在高温环境下长期稳定工作。
在耐腐蚀性能上,树脂基复合材料具有优异的耐化学腐蚀性能,可以在恶劣环境下长期使用。
最后,树脂基复合材料在航空航天、汽车制造、建筑材料等领域具有广泛的应用前景。
在航空航天领域,树脂基复合材料可以用于制造飞机机身、发动机零部件等,可以减轻飞机重量,提高飞机的燃油效率。
在汽车制造领域,树脂基复合材料可以用于制造汽车车身、底盘等,可以提高汽车的安全性能和燃油经济性。
在建筑材料领域,树脂基复合材料可以用于制造建筑结构材料、装饰材料等,可以提高建筑物的抗风、抗震性能,延长建筑物的使用寿命。
综上所述,树脂基复合材料具有重要的应用价值和发展前景,对其制备工艺和性能进行深入研究,可以推动树脂基复合材料在各个领域的应用和发展。
希望本文对树脂基复合材料的相关研究和应用有所帮助。
树脂基复合材料
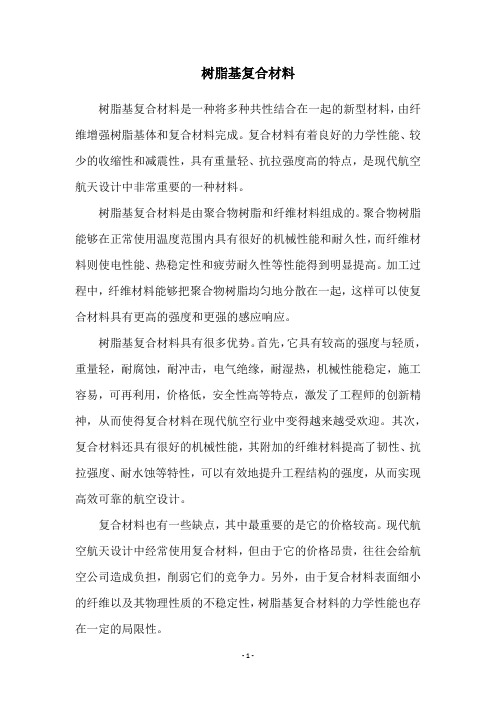
树脂基复合材料树脂基复合材料是一种将多种共性结合在一起的新型材料,由纤维增强树脂基体和复合材料完成。
复合材料有着良好的力学性能、较少的收缩性和减震性,具有重量轻、抗拉强度高的特点,是现代航空航天设计中非常重要的一种材料。
树脂基复合材料是由聚合物树脂和纤维材料组成的。
聚合物树脂能够在正常使用温度范围内具有很好的机械性能和耐久性,而纤维材料则使电性能、热稳定性和疲劳耐久性等性能得到明显提高。
加工过程中,纤维材料能够把聚合物树脂均匀地分散在一起,这样可以使复合材料具有更高的强度和更强的感应响应。
树脂基复合材料具有很多优势。
首先,它具有较高的强度与轻质,重量轻,耐腐蚀,耐冲击,电气绝缘,耐湿热,机械性能稳定,施工容易,可再利用,价格低,安全性高等特点,激发了工程师的创新精神,从而使得复合材料在现代航空行业中变得越来越受欢迎。
其次,复合材料还具有很好的机械性能,其附加的纤维材料提高了韧性、抗拉强度、耐水蚀等特性,可以有效地提升工程结构的强度,从而实现高效可靠的航空设计。
复合材料也有一些缺点,其中最重要的是它的价格较高。
现代航空航天设计中经常使用复合材料,但由于它的价格昂贵,往往会给航空公司造成负担,削弱它们的竞争力。
另外,由于复合材料表面细小的纤维以及其物理性质的不稳定性,树脂基复合材料的力学性能也存在一定的局限性。
尽管复合材料存在一些缺点,但其积极的作用和优点已经被广泛地认识到。
复合材料表现出良好的机械性能和耐久性,并且具有体积小、质量轻、力学性能高、价格低等特点,运用在航空航天设计中得到广泛应用,其应用将使航空航天工程的范围更加广泛。
综上所述,树脂基复合材料是一种具有很多优势的新型材料,具有良好的力学性能、较少的收缩性和减震性,并且还具有重量轻、抗拉强度高等优点,在现代航空航天设计中得到广泛应用,它的应用将为航空航天研究和设计带来更多可能性。
树脂基复合材料简介
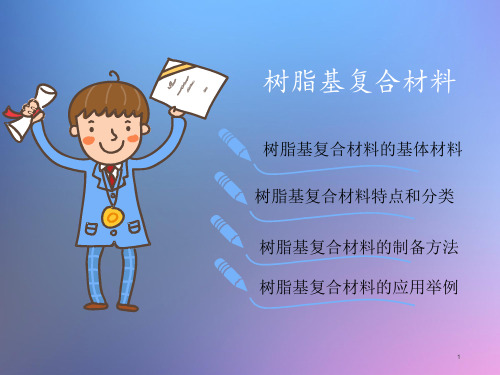
Tg:玻璃化转变温度, Tf:流动温度 Tm:粘流温度(熔点)
6
热塑性基体的最重要优点: 其高断裂韧性(高断裂应变和高冲击强度),这使得FRP具 有更高的损伤容限。 还具有预浸料不需冷藏且贮存期无限、成型周期短、可再 成型、易于修补、废品及边角料可再生利用等优点。
热塑性基体的缺点: 是热塑性基体的熔体或溶液粘度很高,纤维浸渍困难,预 浸料制备及制品成型需要在高温高压下进行, 聚碳酸酯或尼龙这样一些工程塑料,因耐热性、抗蠕变性 或耐药品性等方面问题而使应用受到限制。
9
三·树脂基复合材料的制备成型工艺方法
纤维、树脂、添加剂等原料 A
固化 C 一步法:工艺简单, 但复合材料中会存 在孔洞,均匀性差
整修 E
预浸料 预混料
二步法:降低孔隙 率,提高均匀性 B 预成型
D 脱模
10
成型工艺主要方法
手糊成型
喷射成型
袋压成型
缠绕成型
拉挤成型
树脂传递模成型
11
四·树脂基复合材料的应用举例
缺点:预浸料需低温冷藏且贮存期有限,成型周期长和
材料韧性差。
5
热塑性树脂:
1)具有线形或支链结构的有机高分子化合物。特点是预 热软化或熔融而处于可塑性状态,冷却后又变坚硬。
2)成型利用树脂的熔化、流动,冷却、固化的物理过程 变化来实现的,过程具有可逆性,能够再次加工。
3)聚集状态为晶态和非晶态的混合,结晶度在(20%85%)。
2
一·树脂基复合材料的基体材料
热固性
A
树脂
热塑性
B
树脂
环氧 、 酚 醛 、 不 饱 和 聚酯、双马来酰亚胺、 聚酰亚胺
聚醚砜 、 聚 苯 硫 醚 、 聚醚酰亚胺、聚醚醚 酮、聚醚酰亚胺
复合材料树脂基制备

复合材料树脂基制备
复合材料是一种由两种或两种以上的材料组成的结构材料,具有
优异的机械性能和适用性。
其中,树脂作为基体材料起到了至关重要
的作用。
树脂基的复合材料制备方法可大致分为两种:手工层压和自
动化生产工艺。
本文将主要介绍树脂基复合材料的手工层压制备方法。
手工层压制备方法是根据设计要求,先将纤维材料按适当方向堆
叠称为预制板,再将预制板与树脂制成的粘合剂压合固化形成复合材料。
具体步骤如下:
1. 制作纤维预制板
将纤维材料按照设计要求堆叠成预制板,可采用单向、双向甚至多向
组合方式,亦可将不同类型的纤维材料混合使用。
2. 制备树脂粘合剂
选用不同性能和用途的树脂作为基材,在其中加入一定量的固化剂和
助剂,制成粘合剂。
通常采用环氧树脂、酚醛树脂、不饱和聚酯树脂等。
3. 板材涂胶
将预制板放在平整的工作面上,采用专业的胶刷或滚筒均匀地将粘合
剂涂刷或滚涂在预制板上。
4. 层压
将涂有粘合剂的预制板按规定的层数堆叠,压实固化。
此步骤需要配
备专业的压制设备,压力均匀,度量准确。
5. 固化
在确定的时间和温度条件下,使树脂粘合剂固化,使得树脂和纤维之
间紧密粘合,形成高强度的纤维复合材料。
在以上步骤中,关键的一步是树脂粘合剂的制备和使用。
树脂的
选择应根据工作环境和设计要求确定,固化剂和助剂的使用应符合制
备规范。
在实际操作中,还应注意操作规程的掌握,确保复合材料制
备质量的稳定和一致性。
- 1、下载文档前请自行甄别文档内容的完整性,平台不提供额外的编辑、内容补充、找答案等附加服务。
- 2、"仅部分预览"的文档,不可在线预览部分如存在完整性等问题,可反馈申请退款(可完整预览的文档不适用该条件!)。
- 3、如文档侵犯您的权益,请联系客服反馈,我们会尽快为您处理(人工客服工作时间:9:00-18:30)。
mal n t co a e rdain[ ] C mp s e—atA: l a d wi mirw v ait y h o J . o oi s r t P
脂 基 复 合 材 料 原 位 固 化 制 造 技 术 的 研 究 作 了 综 述 ; 比分 析 了 用 射 线 、 射 线 、 、 波 、 外 光 和 电子 束 等 固 化 方 式 对 x 热 微 紫
进 行 原 位 固 化 制 造 中 各 自优 缺 点 及 存 在 的 问 题 , 对 其 发展 方 向 进行 了 展 望 。 并 关 键 词 : 位 固化 ; 原 树脂 基 复 合 材 料 ; 进 制 造 ; 成 本 ; 效 率 先 低 高
工 艺作 为树脂 基 复合材 料构 件最 终成 型必 要 的工序 之
一
,
对树 脂基 复合 材料 最 终 性 能 和其 制 造 成 本 起 着 至
5 , 计划 中的 空 客 A3 O飞 机更 是 将 复 合 材 料 的 O 而 5
用量 提 高 到 5 。复 合 材 料 的 应 用 可使 飞 机 结 构 减 2
中 图分 类 号 : 6 . 7 T 3 2 V2 1 9 ; B 3 文献 标 识 码 :A 文 章 编 号 :1 0 -3 1 2 1 ) 00 8 — 7 0 14 8 ( O 1 1 0 40
Absr c :W ih t nl r me fa plc to r a a nc e sn e o e i a rx c m p st s,de ta t t he e a ge nto p ia i n a e nd i r a i g us f r s n m t i o o ie — v l pi g a oma e nd l e o n ut t d a ow o t ma f c u i t o s be o e a r s a c o u n t d a e c s nu a t rng me h ds ha c m e e r h f c s i he a v nc d ma nuf c urn il a t i g fed.I hi pe n t spa r,t e c c pt m e g n ea a i fr sn m a rx c m p ie n h on e ,e r e c nd me n ng o e i t i o ost si - st u i nu a t n e hn o a e n i r iu c rng ma f c ur g t c ol gy h s b e ntodu e n d t i. i c d i e al Re e r he b t v ro wst s a c s a ou a i us i iu c rng ma f c urn e ho o e i a rx c m p ie t ho e a b oa r a n y r viwe u i nu a t i g m t ds f r r s n m t i o ost s a m nd a r d a e m i l e e d, a d m an a a t ge n ia v nt ge f7 r y, r y, a , c o v u t a i l ta l c r n be m n i dv n a s a d d s d a a s o 一 a X— a he t mir wa e, lr v o e nd ee t o a c rng me h s f n s t u i nu a t rng a e c u i t od ori -iu c rng ma f c u i r omp r tv l na y e a a i e y a l z d. Ke r s i - iu c i y wo d : n st urng; e i a rx c m p ie; dv nc d ma f c urn l w os ; gh e fce c rsnm ti o ost a a e nu a t i g;o c t hi fii n y
罐 或热 压模 等 的热 固化 方 式随着 复合 材料 构件 的大型
化 表现 出了一些 难 以克服 的缺 点 , 如能耗 高 、 成型 时间
长、 固化过 程难 以控 制 ; 型 零 件 因 热效 应 , 成 残余 变 形
体 水平 的重 要指 标 。此外 , 脂基 复合 材料在 船舶 、 树 汽 车 、 力发 电等行 业 的应 用也 越来越 多 的得 到重 视 , 风 使
关 重要 的作 用 。现 阶段 树脂 基 复合材 料构 件 比较成 熟
和主流 的 固化方 式是 热 固化 , 这 种传 统 的基 于 热 压 但
重 1 ~4 , 不 仅 提 高 了飞 机 燃 油 效 率 , 低 了 O 0/ 这 9 6 降 成 本 , 且 污染物 排 放 量也 明显 降低 u ] 所 以飞 机 结 而 6 , 构 复合 材料 的用 量 和结构 重量 占比 已成 为衡 量 飞机整
用量 在逐 年提 高 。 随着 树脂 基复 合 材 料 的应 用 逐 渐 发 展 到 机 身 、 机
或残余 应力 大 ; 尤其 是尺 寸大 和厚 、 形状 复杂 的树 脂基
复合 材料 构件 , 固化 不 可 避免 的热 梯 度 会 引起 固化 热
不均 匀 和不完 全 ; 了解 决 高温梯 度 带来 的不 利影 响 , 为
8 4
材 料 工 程 /2 1 年 l 01 O期
树 脂 基 复合 材 料 原 位 固化 制造 技 术 概 述
Ov r iw nst e v e ofI - iu Curng M a f c u i g Te h l gy f r i nu a t rn c no o o Re i a rx Com p ie sn M ti ost s
Xia io o g U nv riy, ’ n 7 0 5 , ia ’ n Ja t n ie st Xia 1 0 4 Ch n ) 摘 要 : 着 树 脂 基 复 合 材 料 应 用 领 域 的 扩 大 和使 用量 的增 加 , 展 树 脂 基 复 合 材 料 自动 化 、 成 本 制 造 技 术 成 为 先 进 制 随 发 低 造 技 术 领 域 的研 究 热 点 。本 文 详 细 介 绍 了 树 脂 基 复 合 材 料 原 位 固 化 制 造 技 术 的 概 念 、 生 与 意 义 , 目前 国 内外 各 种 树 产 对
迪力 穆拉 提 ・ 卜 阿 力孜 , 段玉 岗 , 涤尘 , 中良 李 鲁
( 西安 交通 大学 机 械制造 系统 工程 国家重点 实验 室 , 安 7 0 5 ) 西 1 0 4
ABULI lmul t , ZIDii a iDUAN — a Yu g ng, — he LU LIDic n, Zho —i n ng la g ( a e Ke b r t r o a f c urn s e s Eng ne rng, St t y La o a o y f r M nu a t i g Sy t m i ei
e ea c n lg nc ndTe h oo y,1 9 9 9,3 9 0( ):1 5 — 1 1 0 5 07 .
[2 S 2 ] ONME Z F O,AKB UT M .P oeso t zt n o a e UL rcs pi ai ftp mi o
pae n rtemo lsi cmp s e[] o o i sP r A l metf h r pat o oi sJ .C mp s e at - c o c t t
预 成型 件模具 必 须具 有 很低 的热 膨 胀 系 数 , 因此 要 采
翼、 船体 和车 身等 大 型的结 构件 , 其高 制造 成本 成 为约
用 比较 昂 贵 的 I NVAR 合 金 制 造口 此 外 , 脂 基 复 ; 树
9 0
Pa t A- p i d S in e n c no o r Ap l c e c a d Te h l gy,2 0 e 0 材料具 有 高 比模 量 、 比强度 、 高 可
设计 性强 、 疲劳 性能 和耐 腐蚀 性能 好等 特点 , 抗 因而 在 航 空航 天 、 舶 、 车 和 能 源 等 领 域 的 应 用 越 来 越 广 船 汽 泛 _ 。例 如在 航 空 航 天 领 域 , 2 】 ] 从 0世 纪 7 0年 代 开 始应 用 到飞机 结构 , 经过 几 个 阶 段 的发 展 树 脂 基 复 合 材料 在 飞机 结构上 的应 用 已经 实 现 了从 非 承 力 、 承 次
sr n t r p riso a b n f r/ p x o o i s u e h r te g h p o et f r o i e e o yc mp s e rd t e— e c b t c
[3 P 2 ] ARL VL E ,B RS E H E N,B E ITPP E E EUKE S A.R s u l R ei a d
束 树脂 基复合 材料 进一 步发 展 和应用 的关 键 因素 。因
此, 国内外在 纤维 缠绕 成型 、 拉挤 成型 等基 础上 相继 发
展 了纤 维 自动铺 放技 术 ( 括 自动铺 带 技 术 和 自动 铺 包
丝 技术 ) 液 体 模 塑 成 型 技 术 ( 括 RT , , 包 M VART , M
7 9 9 .
材 料 工 程 /2 1 0 1年 l 期 O
E T,CH0U W T [ 7 TH 0STENS0N 3] .M ir wa ep o e sn c o v r c s i g:f n u —
d metl a da piain[ ] o oi sP r A Ap l dSi a nas n p 1 t sJ .C mp s e at - pi c c o t e —