金刚石刀具PCD加工方法
PCD刀具重要的制造技术
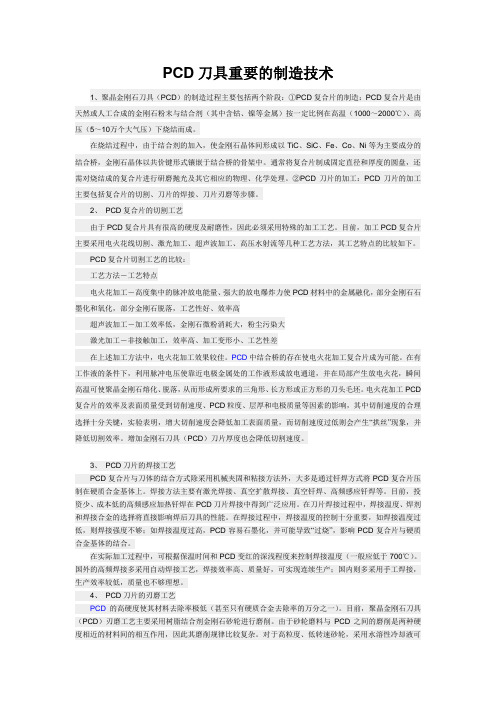
PCD刀具重要的制造技术1、聚晶金刚石刀具(PCD)的制造过程主要包括两个阶段:①PCD复合片的制造:PCD复合片是由天然或人工合成的金刚石粉末与结合剂(其中含钴、镍等金属)按一定比例在高温(1000~2000℃)、高压(5~10万个大气压)下烧结而成。
在烧结过程中,由于结合剂的加入,使金刚石晶体间形成以TiC、SiC、Fe、Co、Ni等为主要成分的结合桥,金刚石晶体以共价键形式镶嵌于结合桥的骨架中。
通常将复合片制成固定直径和厚度的圆盘,还需对烧结成的复合片进行研磨抛光及其它相应的物理、化学处理。
②PCD刀片的加工:PCD刀片的加工主要包括复合片的切割、刀片的焊接、刀片刃磨等步骤。
2、PCD复合片的切割工艺由于PCD复合片具有很高的硬度及耐磨性,因此必须采用特殊的加工工艺。
目前,加工PCD复合片主要采用电火花线切割、激光加工、超声波加工、高压水射流等几种工艺方法,其工艺特点的比较如下。
PCD复合片切割工艺的比较:工艺方法-工艺特点电火花加工-高度集中的脉冲放电能量、强大的放电爆炸力使PCD材料中的金属融化,部分金刚石石墨化和氧化,部分金刚石脱落,工艺性好、效率高超声波加工-加工效率低,金刚石微粉消耗大,粉尘污染大激光加工-非接触加工,效率高、加工变形小、工艺性差在上述加工方法中,电火花加工效果较佳。
PCD中结合桥的存在使电火花加工复合片成为可能。
在有工作液的条件下,利用脉冲电压使靠近电极金属处的工作液形成放电通道,并在局部产生放电火花,瞬间高温可使聚晶金刚石熔化、脱落,从而形成所要求的三角形、长方形或正方形的刀头毛坯。
电火花加工PCD 复合片的效率及表面质量受到切削速度、PCD粒度、层厚和电极质量等因素的影响,其中切削速度的合理选择十分关键,实验表明,增大切削速度会降低加工表面质量,而切削速度过低则会产生“拱丝”现象,并降低切割效率。
增加金刚石刀具(PCD)刀片厚度也会降低切割速度。
3、PCD刀片的焊接工艺PCD复合片与刀体的结合方式除采用机械夹固和粘接方法外,大多是通过钎焊方式将PCD复合片压制在硬质合金基体上。
PCD和PCBN刀具制造及应用
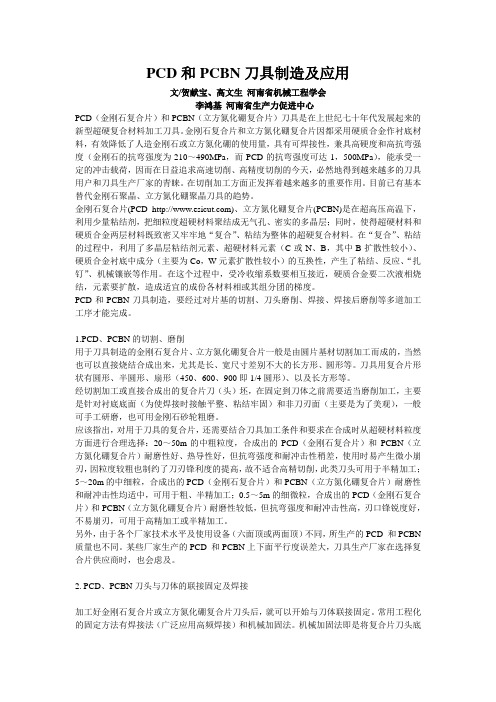
PCD和PCBN刀具制造及应用文/贺献宝、高文生河南省机械工程学会李鸿基河南省生产力促进中心PCD(金刚石复合片)和PCBN(立方氮化硼复合片)刀具是在上世纪七十年代发展起来的新型超硬复合材料加工刀具。
金刚石复合片和立方氮化硼复合片因都采用硬质合金作衬底材料,有效降低了人造金刚石或立方氮化硼的使用量,具有可焊接性,兼具高硬度和高抗弯强度(金刚石的抗弯强度为210~490MPa,而PCD的抗弯强度可达1,500MPa),能承受一定的冲击载荷,因而在日益追求高速切削、高精度切削的今天,必然地得到越来越多的刀具用户和刀具生产厂家的青睐。
在切削加工方面正发挥着越来越多的重要作用。
目前已有基本替代金刚石聚晶、立方氮化硼聚晶刀具的趋势。
金刚石复合片(PCD )、立方氮化硼复合片(PCBN)是在超高压高温下,利用少量粘结剂,把细粒度超硬材料聚结成无气孔、密实的多晶层;同时,使得超硬材料和硬质合金两层材料既致密又牢牢地“复合”、粘结为整体的超硬复合材料。
在“复合”、粘结的过程中,利用了多晶层粘结剂元素、超硬材料元素(C或N、B,其中B扩散性较小)、硬质合金衬底中成分(主要为Co,W元素扩散性较小)的互换性,产生了粘结、反应、“扎钉”、机械镶嵌等作用。
在这个过程中,受冷收缩系数要相互接近,硬质合金要二次液相烧结,元素要扩散,造成适宜的成份各材料相或其组分团的梯度。
PCD和PCBN刀具制造,要经过对片基的切割、刀头磨削、焊接、焊接后磨削等多道加工工序才能完成。
1.PCD、PCBN的切割、磨削用于刀具制造的金刚石复合片、立方氮化硼复合片一般是由圆片基材切割加工而成的,当然也可以直接烧结合成出来,尤其是长、宽尺寸差别不大的长方形、圆形等。
刀具用复合片形状有圆形、半圆形、扇形(450、600、900即1/4圆形)、以及长方形等。
经切割加工或直接合成出的复合片刀(头)坯,在固定到刀体之前需要适当磨削加工,主要是针对衬底底面(为使焊接时接触平整、粘结牢固)和非刀刃面(主要是为了美观),一般可手工研磨,也可用金刚石砂轮粗磨。
PCD球头刀的制作工艺
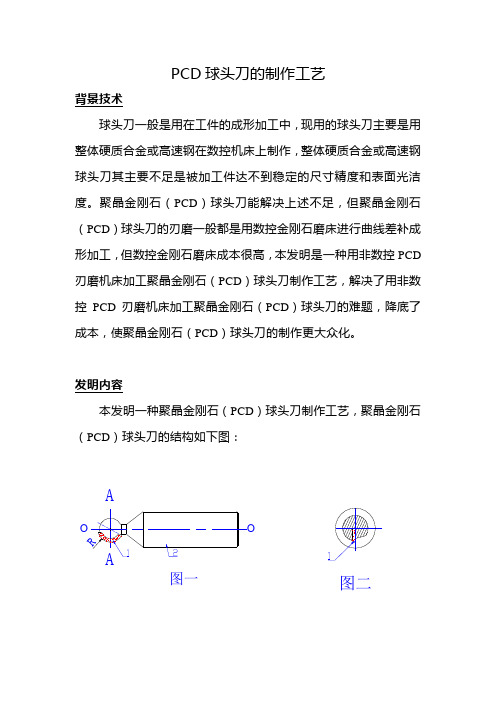
PCD 球头刀的制作工艺 背景技术球头刀一般是用在工件的成形加工中,现用的球头刀主要是用整体硬质合金或高速钢在数控机床上制作,整体硬质合金或高速钢球头刀其主要不足是被加工件达不到稳定的尺寸精度和表面光洁度。
聚晶金刚石(PCD )球头刀能解决上述不足,但聚晶金刚石(PCD )球头刀的刃磨一般都是用数控金刚石磨床进行曲线差补成形加工,但数控金刚石磨床成本很高,本发明是一种用非数控PCD 刃磨机床加工聚晶金刚石(PCD )球头刀制作工艺,解决了用非数控PCD 刃磨机床加工聚晶金刚石(PCD )球头刀的难题,降底了成本,使聚晶金刚石(PCD )球头刀的制作更大众化。
发明内容本发明一种聚晶金刚石(PCD )球头刀制作工艺,聚晶金刚石(PCD )球头刀的结构如下图:oA图一图二图一球头刀的正视图,图二是以A-A为剖面的侧面剖视图,它由带有圆弧R的PCD刀片1和金属刀杆2组成,PCD刀片1焊接或粘接在刀杆2球头上的刀槽内,前角0°,后角20°左右。
加工工件时,刀具绕刀杆2的回转中心O—O回转,在被加工件上形成一个半径为R的球形凹槽,最终产品的尺寸检测是用一半径为R标准球在涂有红丹的工件的凹槽内滚动,以接触面的百分比来判定合格否。
生产加工工艺方案聚晶金刚石(PCD)球头刀的刃磨一般都是用数控金刚石磨床进行曲线差补成形加工,在没有能刃磨球头PCD数控机床时,通过下工艺我们可以在非数控PCD刃磨机床上进行加工。
其工艺路线如下:10、切割PCD刀片120、磨PCD刀片1圆弧R控制尺寸精度和形状精度30、检验PCD刀片1尺寸R 下接第130工序40、刀杆2下料50、车刀杆2外形60、刀杆2淬火、回火70、电火花打刀杆2中心孔80、研磨刀杆2中心孔90、磨刀杆2外圆100、磨刀杆2球头110、线切割切刀杆2球头上刀槽120、磨刀杆2球头排屑倒角130、将PCD刀片1焊在刀杆2球头上刀槽内140、检验PCD刀片1中心偏量和轴向倾角150、检验PCD刀片1刃口在所有工序中,工序20、110、130、150对刀具精度的影响最大;其中,工序20磨PCD刀片1圆弧R控制尺寸精度是核心工艺技术,是关键工序。
金刚石(PCD)铰刀的产品介绍及应用

量,是对金刚石铰刀寿命有很大的影响。 ⑥ 前导向部:前导部是考虑与加工前的孔,其中最小间隙为10--20米欧。
同时还需要注意冷却槽的设计 金刚石铰刀铰孔时,若热量和切屑来不及排出,刀体将发热膨胀,孔的加工质量会明显降低,严重时还会发生“咬死”刀现象。
内镀法
金刚石铰刀内镀的方法: 采用稳定材料制造一个与铰刀外形相反的
高精度内孔胎模,将金刚石磨粒电镀在胎模内表 面,加厚形成电镀层,再将镀层与刀杆粘结在一 起。
金刚石颗粒的顶端整齐,规则地排列在模具 的内表面上,等高性和均匀性较好;
无需修磨,微刃锋利;
所加工孔的尺寸精度和几何精度较高,表面 粗糙度较小,使用寿命较长。
2 PCD铰刀
PCD铰刀的定义及优势
PCD铰刀,一般根据直径大小,采用合金基体或者钢制基体。刃数为2刃或2刃以上。此类刀具主要用于加工公 差要求比较严格,光洁度要求比较高的孔,通孔盲孔均可加工。此类刀具加工的孔,光洁度最高可达Ra0.1以内。
PCD铰刀的优势
具有超高硬度和耐磨性; 具有超长刀具使用寿命; 切削性能稳定,加工效率高; 提高尺寸精度和工艺可靠性。
备注:一般直径15mm左右的可以做成可调式金刚石铰刀,但由于国内市场,可调式金刚石铰刀精度没有固定时金刚 石铰刀好,如果要求精度较高的情况下, 建议选择固定式金刚石铰刀
金刚石铰刀的组成结构及优势
金刚石铰刀的优势
镀层结合力,金刚石粘结牢度,金刚石颗粒分布均匀,外观质量高; 金刚石铰刀前后导向外圆度达到0.005mm,圆柱度为0.005mm/100mm,前导向外圆粗糙度Ra0.63微米, 后导向外圆粗糙度Ra0.16um,刀柄与前后导向部分的同轴度达到0.015mm; 被铰孔工件圆柱度小于0.003,粗糙度可达Ra0.4-0.2,精度高,效率高,使用寿命长; “量体裁衣”式服务,规范化流程,为客服创造的价值超越契约。
pcd工艺技术

pcd工艺技术PCD工艺技术(Polycrystalline Diamond)是一种综合利用钻石结晶技术制造的新材料。
它具有钻石硬度高、耐磨性好和热稳定性好等特点,被广泛应用于机械加工、矿山工具、石油勘探等领域。
PCD工艺技术的制造过程主要包括镀膜、压制和烧结三个步骤。
首先,在刀具表面镀上一层金属膜,以增加PCD与基体的结合力。
然后,将金属粉末与聚结剂混合均匀,填充在模具中,经过高温高压的条件下,金属粉末固化成坚硬的基体。
最后,将钻石晶粒均匀分布在基体中,再次进行高温高压的处理,使钻石晶粒与基体结合紧密,形成具有钻石硬度的PCD。
PCD工艺技术的优点主要体现在以下几个方面。
首先,PCD材料的硬度可达到钻石的六倍,因此具有极高的耐磨性。
在机械加工领域,使用PCD材料制造的刀具能够在高速切削和重负荷的工况下保持长时间的使用寿命。
其次,PCD材料具有极高的热稳定性,能够在高温和高速的加工环境下保持稳定的性能。
在石油勘探领域,使用PCD材料制造的特殊钻头能够快速、高效地穿透各种复杂的地层。
此外,PCD材料的导电性好,因此可以应用于电子器件的制造。
最后,PCD材料的结构稳定,不会轻易损坏,因此能够在恶劣的工作环境中长期使用。
然而,PCD工艺技术也存在一些挑战和局限性。
首先,PCD材料的制造工艺复杂,需要采用高温高压的处理,因此生产成本较高。
其次,由于钻石是一种贵重的材料,PCD材料的价格也相对较高,限制了其在一些领域的广泛应用。
此外,由于PCD材料的硬度高,加工和修复过程相对困难,也增加了维护和使用成本。
总之,PCD工艺技术是一种重要的先进材料制备技术。
它适用于各种领域,如机械加工、矿山工具和石油勘探等。
尽管制造工艺复杂,成本较高,但其优异的性能使其在特定领域有着广阔的应用前景。
未来,随着科技的不断发展,PCD工艺技术有望进一步完善,降低生产成本,提高材料性能,推动其在更多领域的应用。
PCD刀具刃磨

PCD刀具刃磨PCD复合片的硬度一般在HV4500HV8000之间,仅次于金刚石的硬度(HV9000),同时其硬度因生产厂或牌号的不同而不同。
因此,如何解决PCD刀具的刃磨题目是加工、使用PCD刀具的关键。
目前有两种PCD刀具常用刃磨方法:金刚石砂轮刃磨法采用金刚石砂轮来刃磨PCD刀具,对所用机床要求较高:机床系统刚性好,进给机构精度高,有微进给机构,重复精度高,磨头往复摆动平稳无冲击,同时还需选用合适的金刚石砂轮。
瑞士EWAG公司生产的RS系列机床尤其是RS15机床具有精度高、附件多并带有刃磨PCD刀具(带HSK刀柄)的附件等特点,是PCD刀具刃磨机床的代表。
采用RS15机床刃磨PCD刀具,刀具尺寸精度可达0.001mm,表面粗糙度可达Ra0.08左右。
电蚀刃磨法电蚀刃磨是将工件(PCD刀具)和电蚀轮(或钼丝)形成正负电极,通过正负电极间放电,达到往除PCD的效果。
电蚀刃磨法的PCD往除效果取决于电蚀轮(或钼丝)与PCD刀具刃口间的间隙、走刀进给速度以及电压高低、电流大小等。
电蚀刃磨机床的特点是生产效率高,尺寸精度一般在.0.01mm 左右,表面粗糙度在Ra0.25左右。
德国VOLLMER公司的QM和QW系列机床是采用电蚀法刃磨PCD刀具的代表,其中的新产品Q和QWD760都是五轴联动数控机床。
Q是轮电蚀刃磨机床,用于直线形刃口的PCD 刀具电蚀刃磨。
QWD760是线电蚀刃磨机床,用于各种曲线形刃口的PCD刀具电蚀刃磨。
根据不同机床刃磨PCD刀具的适应范围,一般说来,对尺寸精度和表面粗糙度要求高的PCD铰刀、镗刀等,在RS15等机床上用金刚石砂轮刃磨;对PCD铣刀、锯片和PCD木工刀具等,用Q或QWD760机床进行电蚀刃磨,而用于强化地板开榫的PCD刀具和各种曲线外形的PCD刀具,则采用QWD760机床电蚀刃磨。
PCD刀具的刃磨加工

R i e s从 2 0世 纪 8 0年 代 初 刀具 的 寿命 。R i e s表示 , 在E D M 出 了将 传 统 磨 削 加 工 与 E DM 加
就开 始采 用 E DM 工 艺加 工 P CD 加 工 后 是 否还 要 进 行 精 磨 加 工 , 工集成 在一起 的 P C D 刀 具 复 合
对磨 削加 工 构成 了挑 战 。 实际上, 器, 而 电容 器 有 其 固 有 的充 电和 P C D 刀具 寿 命 是 磨 制 P C D 刀 具
用 已知硬 度 最 高 的金 刚 石磨 轮去 放 电时 间 。我 们 尝 试采 用 其他 电 寿 命 的 8 5 %。“ 基 于 从 那 时 以来
磨 削 与其 硬 度 相 当 的 P C D 刀 尖 气元件来 改变充放 电性能 ,或控 电火花 发生器性能 的不 断改善 , 会 耗 费 大量 时 间 和磨 轮 。 V o l l me r 制 充 放 电的速 度 。 ” 美国公司 P C D 部 门经 理 S c o t t 我 估 计 现 在 的 刀 具 寿 命 能 达 到 R i e s 指出, 放 电脉 冲 的 可 控 9 0 % 一9 5 % 。我 需 要 考 虑 , 如 果
我们 没 有采 取 每 天三 班 倒 的生 产 用传 统 的磨 削 功 能加 工 硬质 合 金 具 光洁 度 ,并 采 用 线切 割 机床 来 方式 , 而 是 由工人 值 白班 , 其 他 两 刀杆上 的刀槽 ,最后再对 刀具端 加 工 用 E D G 无 法 实现 的 特 定 刀
火花 a n T 的 电导 体 。 用 电火花 磨 加 工 实 际上 能够 达 到 的表 面 光洁 然而 , 有 些采 用 P C D切 削 刃
削或线切 割工艺 加工 P CD 刀 具 度 已与 磨 削 加 工 不 相 上 下 。 ” 目 的 刀具 也 需 要 对其 硬质 合 金 刀柄 刃 形 的 主 要 好 处 是 可 以 降 低 加 前 , E D M 加 工 已 有 可 能 达 到 进 行磨 削加 工 。 此外 , 有些 刀具会 工成 本 。R i e s指 出 , “ 采 用 非接 触 R 。0 . 2 u m 的表 面粗 糙度。
PCD刀具磨削机理及刃磨工艺研究论文
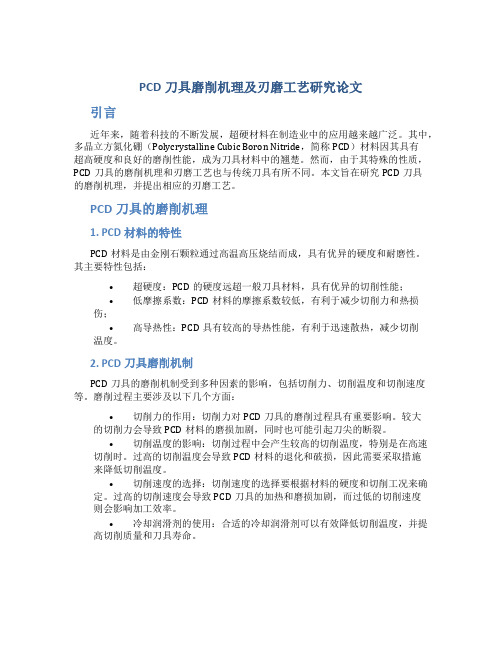
PCD刀具磨削机理及刃磨工艺研究论文引言近年来,随着科技的不断发展,超硬材料在制造业中的应用越来越广泛。
其中,多晶立方氮化硼(Polycrystalline Cubic Boron Nitride,简称PCD)材料因其具有超高硬度和良好的磨削性能,成为刀具材料中的翘楚。
然而,由于其特殊的性质,PCD刀具的磨削机理和刃磨工艺也与传统刀具有所不同。
本文旨在研究PCD刀具的磨削机理,并提出相应的刃磨工艺。
PCD刀具的磨削机理1. PCD材料的特性PCD材料是由金刚石颗粒通过高温高压烧结而成,具有优异的硬度和耐磨性。
其主要特性包括:•超硬度:PCD的硬度远超一般刀具材料,具有优异的切削性能;•低摩擦系数:PCD材料的摩擦系数较低,有利于减少切削力和热损伤;•高导热性:PCD具有较高的导热性能,有利于迅速散热,减少切削温度。
2. PCD刀具磨削机制PCD刀具的磨削机制受到多种因素的影响,包括切削力、切削温度和切削速度等。
磨削过程主要涉及以下几个方面:•切削力的作用:切削力对PCD刀具的磨削过程具有重要影响。
较大的切削力会导致PCD材料的磨损加剧,同时也可能引起刀尖的断裂。
•切削温度的影响:切削过程中会产生较高的切削温度,特别是在高速切削时。
过高的切削温度会导致PCD材料的退化和破损,因此需要采取措施来降低切削温度。
•切削速度的选择:切削速度的选择要根据材料的硬度和切削工况来确定。
过高的切削速度会导致PCD刀具的加热和磨损加剧,而过低的切削速度则会影响加工效率。
•冷却润滑剂的使用:合适的冷却润滑剂可以有效降低切削温度,并提高切削质量和刀具寿命。
PCD刀具的刃磨工艺研究1. PCD刀具的刃磨方法刃磨是PCD刀具加工过程中的重要环节。
常见的PCD刃磨方法包括:•电火花刃磨:利用电火花放电原理将切削刃磨成所需形状。
•摩擦刃磨:通过材料之间的摩擦磨去刃口,得到所需的切削刃。
•光束刃磨:利用高能光束将刃口融化并形成所需形状。
PCD刀具的刃口加工方法及技术

小, 可 降低加 工 表面粗 糙 度 。但 由 于聚 晶金 刚 石 与铁 族元 素有 很强 的亲和 力 , 因此不 适合 加工 黑 色金属 及
其合金。 P C D刀具在有色金属及其合金、 非 金 属 材 料 及 复合 材料 的切 削 中体 现 出优 良的切 削性 能 , 可用 于制 作 车刀 、 镗刀 、 铣 刀 和钻头 、 铰刀、 锪刀、 锯刀 、 镂刀、 剃
Ab s t r a c t : Th e P CD c u t t i n g t o o l i s a n e w t y p e o f t o o l d e v e l o p i n g s i n c e t h e 7 0 S ,i t s g o o d p e r f o r ma n c e s h a s p l a y e d a n i mp o r t a n t r o l e i n mo d e r n p r o c e s s i n g i n d u s t r y . Th i s p a p e r d e s c r i b e s t h e PC D c u t t i n g t o o l c o m mo n l y u s e d p a r t s p r o c e s s i n g me t h o d,i . e ..e l e c t r i c a l d i s c h a r g e ma c h i n i n g -d i a mo n d g r i n d i n g wh e e l p r o c e s s i n g a n d d i a mo n d g r i n d i n g p r o c e s s i n g - a n a l y z e s t h e p r o c e s s i n g p r i n c i p l e ,i n f l u e n c e f a c t o r s t p r o c e s s i n g c o n d i t i o n a n d a p p l i c a t i o n s i t u a t i o n e t c . . By c h o o s i n g t h e r e a s o n a b l e PC D c u t t i n g t o o l e d g e p r o c e s s i n g me t h o d t o
PCD聚晶金刚石刀具特性及其适合加工的材料简介

PCD 聚晶金刚石刀具特性及其适合加工的材料简介图1努氏硬度图2断裂韧性图3导热性制备工艺PCD是由大量随机定向的金刚石颗粒在极困难的条件下进行人工合成得到的。
它通过在高压高温下烧结精选的金刚石颗粒进行制备。
烧结过程在金刚石稳定区内被严格地控制,于是生产出一种极硬且耐磨的结构。
特性PCD是由大量随机定向的金刚石颗粒在极困难的条件下进行人工合成得到的。
它通过在高压高温下烧结精选的金刚石颗粒进行制备。
烧结过程在金刚石稳定区内被严格地控制,于是生产出一种极硬且耐磨的结构。
特性以聚晶形态组成的金刚石提供了一种强大的切削刀具,它提供极好的硬度及由此得到的耐磨性,并与聚晶结构所带来的极佳韧性相结合。
此外,金刚石拥有所有刀具材料中最高的导热性,使得热量迅速从切削刃传递出来。
除PCD与铁的高亲合力以外,PCD不会与工件材料粘结,在正确的切削参数下,积屑瘤是最小化的。
所有的SecomaxPCD刀具都拥有镜面抛光的前刀面,提供最低的摩擦系数和光滑的切削刃。
适合加工的工件材料铝合金铝合金已成为交通工业需求的致力于减轻重量的理想材料。
尽管铝合金的生产在能量消耗上具有更大的初始需求,但在长期运作中证明有更多的益处,这些合金的性能将超过其它与其竞争的材料。
纯铝的硬度低、耐腐蚀。
举例讲,添加铜或镁等合金元素将使该材料具有更高的强度。
巿场上有很多种铝合金,最著名的莫过于分别用于汽车与航空航天行业的2000及6000系列。
锻造和铸造铝合金之间有明显的分界线,各有几种不同的材质等级,而且有各式各样的硬化处理性能。
对于硅(Si)含量低到中等的硅合金来说,PCD在铣削应用与粗加工中提供了最好的耐磨性,见下表。
所遭遇到的最常见的问题应该是积屑瘤。
即使是很高的切削速度,加工低硅铝合金时也会发生这种情况。
切削刃的几何角度和质量必须要被小心地应用。
采用这样的参数,当与工件的接触时间越久,产生的热量上升,其直接的影响就是刀具寿命的缩短。
对于加工高硅铝合金,PCD的耐磨性被完全地利用。
pcd数控刀具切削参数
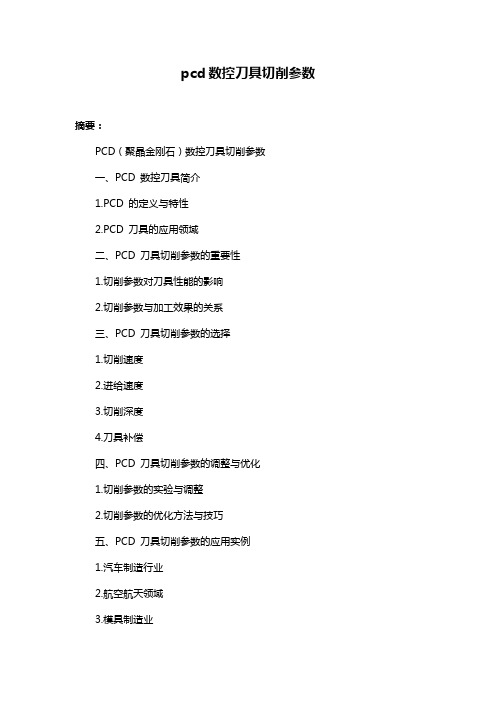
pcd数控刀具切削参数摘要:PCD(聚晶金刚石)数控刀具切削参数一、PCD 数控刀具简介1.PCD 的定义与特性2.PCD 刀具的应用领域二、PCD 刀具切削参数的重要性1.切削参数对刀具性能的影响2.切削参数与加工效果的关系三、PCD 刀具切削参数的选择1.切削速度2.进给速度3.切削深度4.刀具补偿四、PCD 刀具切削参数的调整与优化1.切削参数的实验与调整2.切削参数的优化方法与技巧五、PCD 刀具切削参数的应用实例1.汽车制造行业2.航空航天领域3.模具制造业六、总结1.PCD 刀具切削参数的发展趋势2.对我国制造业的意义与启示正文:PCD(聚晶金刚石)数控刀具切削参数PCD(聚晶金刚石)是一种具有高硬度、高热导率和高抗磨损性能的材料。
由于这些特性,PCD 刀具在数控加工领域得到了广泛应用。
本文将介绍PCD 数控刀具的切削参数及其在制造业中的应用。
一、PCD 数控刀具简介PCD 是由金刚石微粉和金属结合剂经过高温高压制成的一种复合材料。
它具有极高的硬度和热导率,以及良好的抗磨损性能。
因此,PCD 刀具在难加工材料、高硬材料和高温材料加工方面具有显著优势。
PCD 刀具广泛应用于汽车制造、航空航天、模具制造等行业。
二、PCD 刀具切削参数的重要性切削参数是影响PCD 刀具性能和加工效果的重要因素。
合适的切削参数可以提高刀具的耐用度、加工效率和加工质量。
切削参数与刀具性能和加工效果之间的关系主要表现在以下几个方面:1.切削速度:影响刀具的磨损、加工热量和加工表面的质量。
2.进给速度:影响刀具的磨损、加工热量和加工表面的质量。
3.切削深度:影响刀具的磨损和加工效率。
4.刀具补偿:影响刀具的加工精度和加工质量。
三、PCD 刀具切削参数的选择选择合适的切削参数是提高PCD 刀具加工效果的关键。
以下是一些建议:1.切削速度:根据加工材料和刀具材质选择合适的切削速度,以降低刀具磨损和加工热量。
2.进给速度:根据加工材料和刀具材质选择合适的进给速度,以降低刀具磨损和加工热量。
PCD刀具的金刚石砂轮机械刃磨工艺

PCD刀具的金刚石砂轮机械刃磨工艺1PCD 刀具的特点聚晶金刚石(PCD)是将粒度为微米级的金刚石微粉与少量金属粉末(如Co) 混合后在高温(1400℃)、高压(6000M Pa)下烧结而成的聚晶体。
与其它刀具材料相比,PCD具有极高的硬度和耐磨性、高导热性、低热膨胀系数、摩擦系数小、切削散热快、切削温度低、热变形小、可降低加工表面粗糙度等性能特点。
但由于PCD与铁族元素有很强亲和力,因此不适合加工黑色金属及其合金。
已实现商品化供货的PCD复合片是将0.5 ~0.7mm 厚的PCD层烧结在硬质合金基体上制备而成,因此兼具了PCD的高硬度、高耐磨性和硬质合金的良好强度与韧性。
PCD刀具在有色金属及其合金、非金属材料的高速切削中体现出优良的切削性能,已广泛应用于汽车、航空、航天、建材等工业领域。
但是,PCD 的高硬度、高耐磨性使刀具刃磨相当困难,主要体现在材料磨除率小、砂轮损耗大、刃磨效率低、刃口呈锯齿状等。
PCD刀具的刃磨工艺性已成为其推广应用的障碍之一,为了突破这一工艺瓶颈,国内外学者进行了大量研究开发工作。
2PCD刀具的金刚石砂轮刃磨工艺常用的PCD刀具刃磨工艺有金刚石砂轮机械刃磨、放电刃磨、电解刃磨等,其中以金刚石砂轮机械刃磨在技术上最为成熟,在目前使用也最为广泛。
该方法虽然刃磨效率较低、加工成本较高,但可获得良好的刀具刃口质量和完整、光洁的前后刀面。
2.1刃磨加工机理金刚石砂轮机械刃磨PCD刀具的材料去除机理比较复杂,国内外学者对此进行了大量研究,目前主要存在以下几种观点:(1)德国学者M .Kenter认为,金刚石砂轮磨削PCD刀具的过程中发生了刻划作用和滑动作用,材料的去除方式主要为粘结、刻划、摩擦化学反应和表面断裂。
他认为,在绝大多数情况下,PCD 材料的去除是以摩擦化学反应和表面断裂为主。
由于PCD材料脆性大,在金刚石磨粒的挤压下容易诱发裂纹,裂纹在机械和热应力作用下扩展,最终导致小片PCD材料剥落,同时,摩擦热会使PCD 发生石墨化和其它摩擦化学反应。
金刚石刀具加工方法
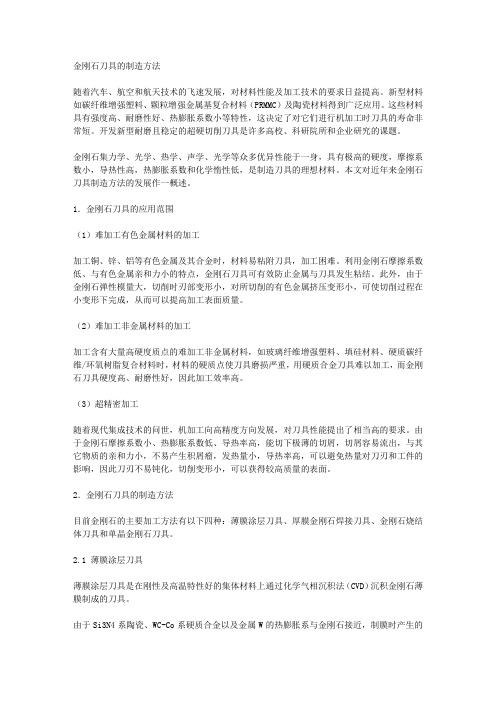
金刚石刀具的制造方法随着汽车、航空和航天技术的飞速发展,对材料性能及加工技术的要求日益提高。
新型材料如碳纤维增强塑料、颗粒增强金属基复合材料(PRMMC)及陶瓷材料得到广泛应用。
这些材料具有强度高、耐磨性好、热膨胀系数小等特性,这决定了对它们进行机加工时刀具的寿命非常短。
开发新型耐磨且稳定的超硬切削刀具是许多高校、科研院所和企业研究的课题。
金刚石集力学、光学、热学、声学、光学等众多优异性能于一身,具有极高的硬度,摩擦系数小,导热性高,热膨胀系数和化学惰性低,是制造刀具的理想材料。
本文对近年来金刚石刀具制造方法的发展作一概述。
1.金刚石刀具的应用范围(1)难加工有色金属材料的加工加工铜、锌、铝等有色金属及其合金时,材料易粘附刀具,加工困难。
利用金刚石摩擦系数低、与有色金属亲和力小的特点,金刚石刀具可有效防止金属与刀具发生粘结。
此外,由于金刚石弹性模量大,切削时刃部变形小,对所切削的有色金属挤压变形小,可使切削过程在小变形下完成,从而可以提高加工表面质量。
(2)难加工非金属材料的加工加工含有大量高硬度质点的难加工非金属材料,如玻璃纤维增强塑料、填硅材料、硬质碳纤维/环氧树脂复合材料时,材料的硬质点使刀具磨损严重,用硬质合金刀具难以加工,而金刚石刀具硬度高、耐磨性好,因此加工效率高。
(3)超精密加工随着现代集成技术的问世,机加工向高精度方向发展,对刀具性能提出了相当高的要求。
由于金刚石摩擦系数小、热膨胀系数低、导热率高,能切下极薄的切屑,切屑容易流出,与其它物质的亲和力小,不易产生积屑瘤,发热量小,导热率高,可以避免热量对刀刃和工件的影响,因此刀刃不易钝化,切削变形小,可以获得较高质量的表面。
2.金刚石刀具的制造方法目前金刚石的主要加工方法有以下四种:薄膜涂层刀具、厚膜金刚石焊接刀具、金刚石烧结体刀具和单晶金刚石刀具。
2.1 薄膜涂层刀具薄膜涂层刀具是在刚性及高温特性好的集体材料上通过化学气相沉积法(CVD)沉积金刚石薄膜制成的刀具。
金刚石刀具切削加工
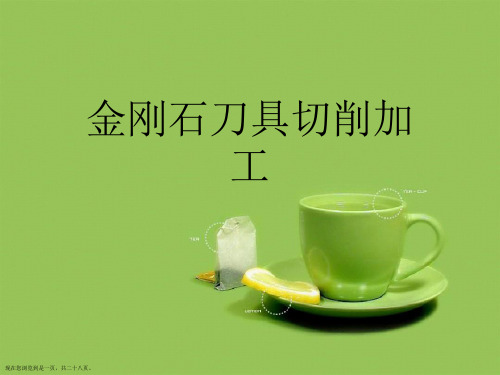
κr
• (2)金刚石车刀切削部分 • 前角γ0=0º; • 后角α0=5º~8º; • 主偏角Kr=45º。
现在您浏览到是九页,共二十八页。
刀具磨损破损和耐用度
金刚石刀具的磨损、破损 刀具的磨损形式: 机械磨损、粘结磨损、相变磨损、扩散磨损、破损和碳化磨损。 金刚石刀具的磨损形式:机械磨损、破损和碳化磨损。最常见的磨损形式为 机械磨损、破损,碳化磨损较少见。 (1)机械磨损 由于机械摩擦所造成的磨损。 后刀面一般情况是形成阶梯形磨损。 前刀面是由于切屑流过而引起的,产生凹槽形的磨损带。 金刚石刀具的机械磨损一般很小,磨损后的表面非常平滑,对加工一般不会 显著地影响加工表面质量。 这种机械磨损主要产生在金刚石刀具加工铝、铜尼龙等物质材料。但是在加 工过程中切削过程稳定、没有冲击振动。
金刚石刀具的研磨,采用普通的顶尖式研磨机很难达到理 想的要求,一般用空气轴承的研磨机。研磨盘多采用低压烧结工艺而
制成的镶嵌的铸铁研磨盘。 由于振动小,可达到很低的粗糙度和极小的刃口半径,
(3)特殊刀头的形状
小型刀头和全R刀头是属于特殊形状的刀头。另外,还有直线 拟合曲线形状的特殊用途的刀头,要求复杂形状时,可采用几个 刀片组合而成。
1000kg/mm2之间。
制作刀具时,尽可能与(111)面平行研磨并形成前刀面。
但与(111)面成平行的研磨会使加工成本过高,通常是以3º左右的 倾角进行研磨以形成前刀面和锋利的切削刃。
现在您浏览到是四页,共二十八页。
(3) 热传导率大
金刚石是由碳原子的共价结合而成的,其热传导率在矿物中 是最大的。
如果金刚石晶面方向选择不当,切削力容易引起金刚石的解理,使刀具寿命急 剧下降,尤其是在有冲击振动、切削不稳定的条件下,更容易产生解理。
pcd数控刀具切削参数

pcd数控刀具切削参数
摘要:
1.PCD 数控刀具切削参数的重要性
2.影响切削参数的因素
3.建议的切削参数
4.切削参数的调整方法
5.结论
正文:
PCD(聚晶金刚石)数控刀具切削参数在加工过程中起到关键作用,这些参数直接影响到加工效率和工件质量。
在选择切削参数时,需要综合考虑刀具材料、刀具形状、工件材料和加工环境等多种因素。
首先,切削速度是影响刀具磨损和工件表面质量的重要因素。
对于PCD 刀具,推荐采用较高的切削速度,一般在100-300m/min 之间。
进给速度也是影响加工效率的关键因素,合理的进给速度可以降低刀具磨损。
一般推荐采用较高的进给速度,如50-100mm/min。
其次,刀具的摆动角对于提高切削效率和刀具寿命也具有重要意义。
合理的摆动角有利于提高切削效率和刀具寿命。
推荐采用10-30°的摆动角,具体数值需根据刀具形状和工件材料调整。
此外,刀具的磨损补偿是保持切削性能的关键。
在加工过程中,刀具磨损是不可避免的。
磨损补偿是指在刀具磨损后,通过调整切削参数来保持切削性能。
推荐采用定期检测刀具磨损,并根据检测结果调整切削参数的方法。
最后,冷却液的选择和使用对于降低刀具磨损、提高加工效率和工件表面质量具有重要意义。
推荐采用含有机磨剂的冷却液,并根据实际加工情况调整冷却液的浓度和喷射压力。
总之,选择合适的PCD 数控刀具切削参数是提高加工效率和工件质量的关键。
pcd铰刀切削参数

pcd铰刀切削参数摘要:1.PCD 铰刀的概念与特点2.PCD 铰刀切削参数的种类3.PCD 铰刀切削参数的选择方法4.PCD 铰刀切削参数对切削性能的影响5.总结正文:一、PCD 铰刀的概念与特点PCD 铰刀,全称为聚晶金刚石铰刀,是一种采用聚晶金刚石作为刀片材料的高性能切削工具。
PCD 铰刀具有高硬度、高耐磨性和高热导率等优点,因此在切削过程中具有较高的切削速度和较长的使用寿命。
由于其优异的性能,PCD 铰刀在航空、航天、汽车等领域的高精度、高效率切削加工中得到了广泛应用。
二、PCD 铰刀切削参数的种类PCD 铰刀切削参数主要包括切削速度、进给速度和刀具摆动角等。
这些参数对于提高切削效率、保证切削质量和降低刀具磨损具有重要意义。
1.切削速度:切削速度是PCD 铰刀在切削过程中沿刀具进刀方向的相对速度。
切削速度的选择应根据工件材料、刀具材料和机床性能等因素综合考虑。
2.进给速度:进给速度是PCD 铰刀在切削过程中沿刀具摆动方向的相对速度。
进给速度的选择应根据切削深度、刀具摆动角和切削速度等因素综合考虑。
3.刀具摆动角:刀具摆动角是PCD 铰刀在切削过程中刀尖线与切削速度方向的夹角。
刀具摆动角的选择应根据切削深度、切削速度和进给速度等因素综合考虑。
三、PCD 铰刀切削参数的选择方法在选择PCD 铰刀切削参数时,应根据以下原则进行:1.切削速度:先根据工件材料选择合适的切削速度,再根据刀具材料和机床性能进行调整。
在保证切削质量的前提下,尽量选择较高的切削速度以提高生产效率。
2.进给速度:根据切削深度、刀具摆动角和切削速度等因素选择合适的进给速度。
在保证切削质量的前提下,尽量选择较高的进给速度以提高生产效率。
3.刀具摆动角:根据切削深度、切削速度和进给速度等因素选择合适的刀具摆动角。
在保证切削质量的前提下,尽量选择较大的刀具摆动角以提高切削效率。
四、PCD 铰刀切削参数对切削性能的影响PCD 铰刀切削参数对切削性能的影响主要表现在以下几个方面:1.切削速度:切削速度的合理选择能够保证切削质量和提高生产效率。
pcd刀片切削参数

pcd刀片切削参数PCD刀片是一种高效的切削工具,广泛应用于机械制造、汽车制造、航空航天等领域。
在进行切削加工时,合理的刀具切削参数对于提高加工效率和保证加工质量至关重要。
本文将从刀具材料、切削速度、进给速度、切削深度等方面介绍PCD刀片的切削参数。
刀具材料是影响切削参数选择的重要因素之一。
PCD刀片是由多个单晶体金刚石颗粒通过高温高压工艺制成的,具有优异的硬度和耐磨性。
在选择切削参数时,要考虑PCD刀片的刀具材料特性,避免过高的切削速度和进给速度,以免引起刀具过热、磨损过快的问题。
切削速度是切削参数中最基本的参数之一。
切削速度过高会导致刀具过热、磨损加剧,甚至断刀的情况发生;切削速度过低则会降低加工效率。
在选择切削速度时,要根据被加工材料的硬度、刀具材料的特性以及加工表面质量要求进行综合考虑。
一般来说,对于硬度较高的材料,切削速度应适当降低,以保证刀具的寿命和加工质量。
进给速度是切削参数中另一个重要的参数。
进给速度过高会导致切削力过大,容易引起振动和表面质量不佳;进给速度过低则会降低加工效率。
在选择进给速度时,要根据刀具材料的特性、被加工材料的硬度以及加工表面质量要求进行综合考虑。
一般来说,对于刚性好的材料,可以适当提高进给速度,以提高加工效率。
切削深度是切削参数中影响加工效率和加工质量的重要参数。
切削深度过大会导致切削力过大,容易引起振动和表面质量不佳;切削深度过小则会降低加工效率。
在选择切削深度时,要根据刀具材料的特性、被加工材料的硬度以及加工表面质量要求进行综合考虑。
一般来说,对于硬度较高的材料,切削深度应适当降低,以保证加工质量和刀具寿命。
除了以上几个基本的切削参数外,还有一些辅助切削参数也需要注意。
例如切削液的选择和使用,可以降低切削温度、减少刀具磨损;切削方式的选择,可以根据被加工材料的特性和加工表面质量要求选择合适的切削方式;刀片的安装和调整,要保证刀具的刃部与工件的接触良好,避免刀具的偏摆和过度磨损。
- 1、下载文档前请自行甄别文档内容的完整性,平台不提供额外的编辑、内容补充、找答案等附加服务。
- 2、"仅部分预览"的文档,不可在线预览部分如存在完整性等问题,可反馈申请退款(可完整预览的文档不适用该条件!)。
- 3、如文档侵犯您的权益,请联系客服反馈,我们会尽快为您处理(人工客服工作时间:9:00-18:30)。
通讯件滤波器腔体盖板面和凸台面接刀问题解决方案
1.目的:
对于现场通讯件滤波器腔体出现问题进行先期策划,以引导资源识别隐患,避免过多机加浪费,造成后工序不良费用增加(电镀),及客户端调试不良带来不良影响。
2、范围:
适用于本公司通讯件滤波器腔体类结构,机械加工工艺流程的编制,机械产品的CNC现场加工等策划与实施。
3、职责与权限
1.项目工程部工艺主管工程师,工艺设计人员负责图纸的审核,编制,管理和结
构的设计的沟通,更改。
组织召开评审会议及相关培训,项目完成时负责整
理相关资料归档。
2.机械技术部CNC程序工程师负责程序的编制,管理,图纸设计优化改进及数控
机床,刀具的选用。
3.机械品质部门负责腔体盖板面和凸台面接刀问题的验证和加工现场相关内容
调整的监管。
4.机械生产调机部门完成程序的首件调试完成,交接及首件加工中的问题反馈。
生产部门对该腔体接刀的维护,控制,调整和管理。
4、CNC腔体盖板面和凸台面接刀管理
4-1 刀具的选用。
1. CNC工程师在编制腔体盖板面和谐振杆凸台面时应优先选用大直径刀
具.
2. CNC工程师在编制压铸件盖板面和谐振杆凸台面时应优先选用金刚石
铣刀(PCD)和多刃铣刀.
3. CNC工程师在编制腔体盖板面和谐振杆凸台面时尽可能选用同一把铣
刀,避免出现对刀误差。
4-2 工艺尺寸精度的控制。
1.工艺主管工程师,工艺工程师在图纸下发后对腔体关键部位进行审核,
对盖板面和凸台面深度的尺寸公差应作进一步的优化和控制,提高工艺尺寸的精度。
4-3 预留余量的设置。
C工程师在编制腔体盖板面和谐振杆凸台面刀路遵循先开粗后精加工
的顺序采用共用2把铣刀加工的原则。
C工程师在编制腔体盖板面刀路时开粗预留0.1MM,谐振杆凸台面刀
路开粗预留0.10MM-0.3MM的余量.
4-4 CNC数控机床的影响。
1.机械生产计划部在安排机床加工腔体时优先选用精度高的主轴。
判断标
准以同一把铣刀加工表面时其接刀控制在0.01MM以内。
2.机械生产部定期检查机床切削液管道的通畅,润滑情况,满足加工部位
的充分冷却。
3.机械生产部定期检查机床移动工作台的清理,保养,选用移动精度高
的工作台。
4-5 转角处清角时Z轴台阶接刀的影响。
1.在不影响调试性能的情况下,项目工程师应及时和客户端结构工程师沟
通,更改工程图纸加大转角处得R角,避免清角。
2.生产调机人员及时调整刀长补正。
控制Z轴方向接刀光顺平滑。
4-6 多种刀具结合的运用。
C工程师在编制腔体刀路同时选用多把刀具加工盖板面和凸台面时,
尽量控制刀具数量最少化,避免对刀误差形成接刀和尺寸超差。
以不超过3把为宜。
4-7 走刀轨迹的选择。
C工程师在编制腔体盖板面和凸台面程序时做相应的非锐角辅助线,
选用顺着筋加工的走刀轨迹。
减少提刀,保证刀具路径光顺不能有残
留。
4-8 点孔及轮廓倒角的影响。
1.腔内螺纹孔孔口,盖板面轮廓及谐振杆凸台轮廓倒角应小于C0.1,电
气非功能区倒角大于C0.1.
C工程师在编制腔体盖板面和凸台面程序时将电气功能区和非功能区
倒角刀补给不同数值。
4-9 夹具稳定性的影响。
1.工艺工程师在设计厚度较薄的压制腔体时,增加浮动支撑,增加接触面
积增加工件的稳定性。
2. CNC工程师在编制厚度较薄的腔体时,应增加开粗留余量再精加工的方
式。
4-10 机床加工速度F和转速S的选择。
1.视工件材质,大小,厚度及刀具的运用CNC工程师在编程时选用合理
的参数值,原则上在非高速机精加工速度F不大于1800mm/min.
4-11 所加工材质的影响。
1.在加工压铸件材质ALSi12和ADC12这两种材料时,从现场加工的情况
分析,同样的刀具及加工状态, ALSi12材质加工特性要次于ADC12
材质。
编制:陈海伟日期:2017-07-14。