毛坯图纸技术要求
图纸上的技术要求汇总
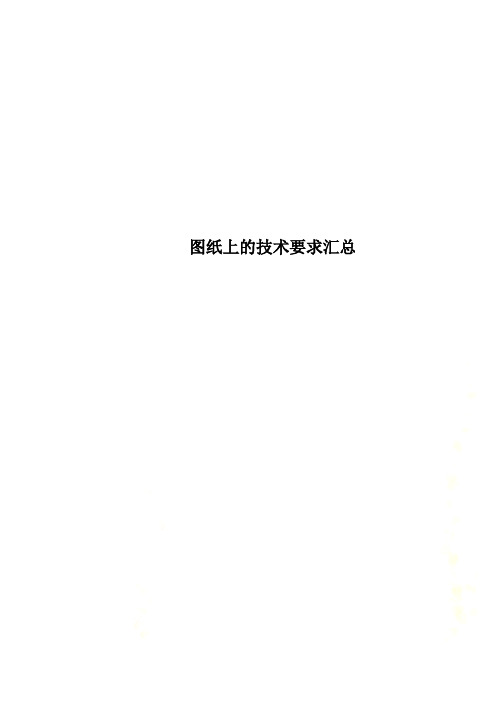
图纸上的技术要求汇总图纸技术要求一、一般技术要求制件去除表面氧化皮;制件不得有划痕、擦伤等损伤零件表面的缺陷;去除毛刺飞边;锐角倒钝;未注倒角均为0.5×45%%d;未注越程槽均为1.2×0.3;表面平整无毛刺;二、未注公差技术要求(金属件)未注公差尺寸的极限偏差按GB/T 1804-m;未注形位公差按GB/T 1184-K;未注长度尺寸允许偏差±0.5;三、表面处理技术要求表面镀白(黑)锌处理;表面喷漆(喷塑)处理;表面发黑处理;表面电泳处理;表面镀铬处理;表面抛光处理;表面滚花,直纹(网纹)m=0.4 GB/T 6403.3;四、热处理技术要求制件氮化450-480HV;制件毛坯须调质处理220-260HB;制件调质处理30-35HRC;制件高频淬火45~50HRC;制件渗碳处理,深度>0.1;制件进行高温回火处理;制件整体淬火40-45HRC;五、铸件技术要求1、压铸件技术要求未注公差尺寸的极限偏差按GB/T 1804-m;未注形位公差按GB/T 1184-K;未注倒角均为0.5×45%%d;未注壁厚2.5;未注筋板1.5~2;未注过渡圆角R0.5-R2;未注脱模斜度≤1%%d;制件饱满光洁、无气孔、缩松、裂纹、夹渣、缺料等缺陷;各脱模顶料推杆压痕均应低于该制件表面0.2;制件要求符合GB/T 15114《铝合金压铸件》标准规定;表面喷漆(喷塑)处理,不得污染到已加工表面;加工表面在表面处理后加工,加工后涂油保护;未注尺寸参照三维造型;制件表面处理及其它要求按客户定;2、砂型铸造技术要求未注铸造圆角R5-10;铸件应彻底清砂,浇冒口应清除平整;铸件需人工时效;铸件不得有砂眼、气孔、缩松、裂纹等缺陷;粗加工后应再次进行人工时效;不加工表面涂底漆;六、冲压件技术要求制件未注公差尺寸的极限偏差按GB/T 15055-m;制件未注形位公差按GB/T 13916-2级;制件不得有裂纹或缺损;制件表面平整,不得有沟痕、碰伤等损坏表面,降低强度及寿命的缺陷;去除边角毛刺;表面处理:七、塑料件技术要求未注公差尺寸的极限偏差按GB/T 14486-MT6级;制件应饱满光整、色泽均匀;无缩痕、裂纹、银丝等缺陷;浇口、溢边修剪后飞边≤0.3,且不得伤及本体;未注壁厚3;未注筋板1.5~2;表面打光(喷砂)处理;未注过渡圆角取R0.3~R1,脱模斜度≤0.3%%d;各脱模顶料推杆压痕均应低于该制件表面0.2;与对应装配结合面外形配合错位≤0.5;制件应进行时效处理;制件机械强度须符合GB 3883.1标准规定;制件内腔表面打上材料标记和回收标志;未注尺寸参照三维造型;制件表面处理及其它要求由客户定;八、焊接件技术要求未注公差线性及角度尺寸的极限偏差均按GB/T 19804-B级;未注形位公差按GB/T 19804-F级;焊缝应均匀平整,焊渣清理干净;焊缝应焊透,不得烧穿及产生裂纹等影响机械性能的缺陷;九、各类零、部件技术要求1、齿轮(齿轴)技术要求未注公差尺寸的极限偏差按GB/T 1804-m;未注形位公差按GB/T 1184-K;制件毛坯须调质220~260HB;制件材料的化学成分和力学性能应符合GB/T 3077的规定;齿面接触斑点:按齿高不小于40%,按齿长不小于50%;齿面高频淬火回火至49-52HRC;制件表面不应有锈迹、裂纹、灼伤等影响使用寿命的伤痕及缺陷;最终工序热处理表面不得有氧化皮;2、一般轴芯(无铣齿)技术要求未注公差尺寸的极限偏差按GB/T 1804-m;未注形位公差按GB/T 1184-K;未注倒角均为0.5×45%%d;未注越程槽均为1.2×0.3;制件毛坯须调质220~260HB;尺寸%%c 档车正反两条螺旋槽,螺距10,深0.4;螺纹表面不允许有磕碰、乱扣、毛刺等缺陷;热处理:表面处理:3、包轴毛坯(一次成型)技术要求未注公差尺寸的极限偏差按GB/T 1804-m;未注形位公差按GB/T 1184-K;绝缘层应饱满光洁,无裂纹、气孔、缺料、杂质等缺陷;包轴毛坯:绝缘层%%c 档(注:指冲片配合档)与轴芯间应能承受50Hz,实际正弦波电压2500V历时1min不击穿,其余绝缘层档3750V历时1min不击穿;一次成型:铁芯与轴芯间应能承受50Hz,实际正弦波电压2500V历时1min不击穿,其余绝缘层档3750V历时1min不击穿;4、包轴(加工)技术要求未注公差尺寸的极限偏差按GB/T 1804-m;未注形位公差按GB/T 1184-K;塑层应饱满光洁,无裂纹、气孔、缺料、杂质等缺陷;塑层%%c 档(注:指冲片配合档)与轴芯间应能承受50Hz,实际正弦波电压2500V历时1min不击穿,其余塑层档3750V历时1min不击穿;制件磨加工后应烘干除水处理;5、转子技术要求未注公差尺寸的极限偏差按GB/T 1804-m;未注形位公差按GB/T 1184-K;绕组接线按转子绕线原理图;绕组绝缘漆应均匀充满绕组并充分固化,漆膜应均匀无气泡或裂痕;云母槽开深0.8~1,槽宽0.6,槽内不得残留云母片;绕组冷态绝缘电阻不低于50MΩ;装风叶后校动平衡,其精度应不低于G6.3级;去重不允许有冲片铣穿、残缺现象;铁芯外圆不加工,绝缘漆不得高出铁芯外圆,并不得有明显积瘤;铁芯与轴芯间应能承受50Hz,实际正弦波电压2500V,1min不击穿;绕组与铁芯间应能承受50Hz,实际正弦波电压1250V,1min不击穿;匝间绝缘应能承受1000Hz,峰值为2100V,历时3s不击穿;换向器与轴芯间应能承受50Hz,实际正弦波电压3750V,1min不击穿;应去除铁屑、铜粉、油污等杂质;铁芯外圆应涂透明淡金水防锈处理;6、定子技术要求绕组绕制整齐无松散;引线接头应牢固可靠且充分绝缘;绕组与铁芯间应能承受50Hz,实际正弦波电压1250V历时1min不击穿;匝间绝缘应能承受1000Hz,峰值为2100V,历时3s不击穿;绕组绝缘漆应均匀充满绕组并充分固化,漆膜应均匀无气泡或积瘤;铁芯表面不得有明显绝缘漆;7、定、转子铁芯技术要求未注公差尺寸的极限偏差按GB/T 1804-m;未注形位公差按GB/T 1184-K;冲片叠装应紧密可靠,片间无夹杂,表面及槽内无污物和油渍;冲片按同一冲制方向压装;冲片齿槽口整齐与转轴平行,误差不大于0.5;铁芯两端弹开度不大于0.5;8、定、转子冲片技术要求制件未注公差尺寸的极限偏差按GB/T 15055-m;制件未注形位公差按GB/T 13916-2级;制件应表面平整,完整无缺料;尖角处允许用R0.3过渡;制件毛刺不大于0.05(注:高速冲时不大于0.02);制件应不含油脂,剪切油不能用机油;9、绝缘纸技术要求表面不得有划痕、折痕;裁边不起毛;10、换向器技术要求未注公差尺寸的极限偏差按GB/T 1804-m;未注形位公差按GB/T 1184-K;外观完整,表面光滑,应无裂纹、毛刺、锈蚀、气孔、夹杂等缺陷;绝缘电阻:室温下内孔与换向片之间大于50MΩ;云母片厚度取0.5;换向片对换向器轴线偏斜度不大于云母片厚度的1/3;介电强度:片间承受频率50Hz,泄露电流为0.1mA,实际正弦波电压600V历时1s不击穿;换向片与内孔轴芯间承受频率50Hz,泄露电流为0.25mA,实际正弦波电压3750V历时1min不击穿;试验与检验应符合JB/T 10107《电动工具换向器》标准要求;11、电缆线技术要求电缆线长度尺寸指工具电缆出口至插头的导线部分,不包括插头和插脚;软电缆应符合GB/T 5013《额定电压450V/750V及以下橡皮绝缘电缆》标准要求;聚氯乙烯电缆应符合GB/T 5023《额定电压450V/750V及以下聚氯乙烯绝缘电缆》标准要求;插脚与可触及插头表面的绝缘应能承受50Hz,实际正弦波电压3750V历时1min不击穿;制件还应符合GB 1002《家用和类似用途单相插头插座型式、基本参数和尺寸》和GB 2099《家用和类似用途插头插座》标准要求;12、开关技术要求未注公差尺寸的极限偏差按SJ/T 10628-7级;除本图要求的外形尺寸、功能、图形、文字外,试验和检验均应符合GB/T 22692《电动工具开关》标准要求;开关的使用性能应保证5万次无故障正常使用;13、电缆护套技术要求未注公差尺寸的极限偏差按GB/T 3672.1-2级;未注形位公差按GB/T 3672.2-M级;制件不得有缺料、破裂等缺陷。
铸件毛坯的质量要求

铸件毛坯的质量要求
目的:明确外协厂商铸造配件的来料质量要求,以保证产品加工过程中的正常加工。
范围:使用于所有本公司铸件加工产品的来料,使外协厂商确保铸件产品完好地供应到仓库。
要求
1.精度尺寸与材质请参照技术图纸的要求。
2.铸件毛坯不得有砂眼、气孔、缩松、夹砂、结疤、粘砂、裂纹
等铸造缺陷。
3.铸件毛坯要进行退火处理,以消除内应力,要经过530-560度
的炉冷处理。
4.提高铸件的外观质量和尺寸精度减少加工余量。
诚锋机械制造有限公司
质检部
2010-11-06。
图纸技术要求问题点

序号1 2 3 4 5 6 7 8 9 10 11 12 13 14 15 16 17 18 19
技术要求
未指示普通公差参照:SASG:K22-01A,压铸毛坯的普通公差参照SASG:K22-02A-CT5
未指示毛刺高度为0.15mm以下
以往的问题经验(压铸保证方法、过程控制方法、检测手段、清洗控制方法、包装方式等)
未指示脱模斜度为2°以下
本产品的材料需满足SAS:K50-03A(特定物使用限制),另外,材料成分表需要提交
允许的表面缺陷与外观限度要求(例如加工面上的气孔大小、数量,非加工的缺陷大小)
图纸需要提供DWG格式的图纸,PDF图纸看不清楚,例如图区H5 是螺纹底孔还是倒角孔尺寸不能确定,3D孔尺寸是φ3.0,倒角是φ3.6.
15.PPAP LEVEL 3 来应对
需要清理搬运时防止生锈产生
清洁度检查需满足表面张力38mN/m ,做清洁度测试区域图纸需要标识
异物检查为130um以下目标,异物区域图纸是否可以注明(散热片区域不能100%探测到)
技术要求内容
未指示R角为R0.5以下
测量基准测量方法管理尺寸需要对方设计协商
机加工面参照APSI:GC-18A的区分(不同于压铸件表面缺陷)
螺纹孔参照JIS B0205(ISO 261)螺纹公差为JIS B0209(ISO 965等级6H
材料:ADC12
气密性实验 68KPA以上
.顶杆痕迹满足凹MAX0.5mm以下到平坦
表面处理:喷砂,未指示粗糙度RZ25以下,机加公面粗糙为Rz12.5以下。
压铸毛坯图纸技术要求
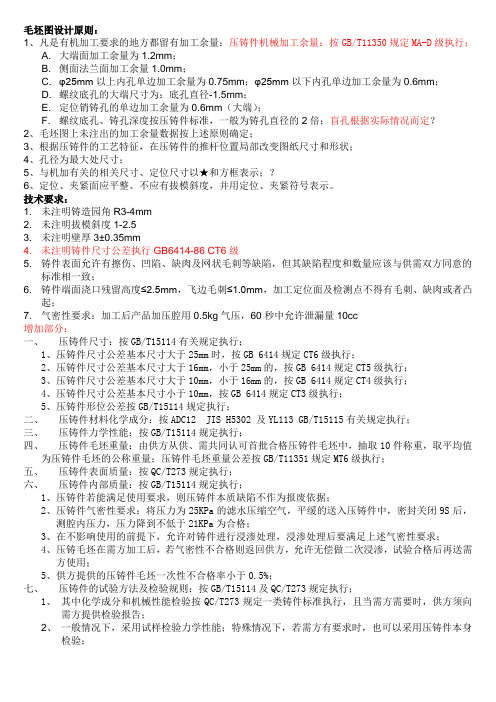
毛坯图设计原则:1、凡是有机加工要求的地方都留有加工余量:压铸件机械加工余量:按GB/T11350规定MA-D级执行;A. 大端面加工余量为1.2mm;B. 侧面法兰面加工余量1.0mm;C. φ25mm以上内孔单边加工余量为0.75mm;φ25mm以下内孔单边加工余量为0.6mm;D. 螺纹底孔的大端尺寸为:底孔直径-1.5mm;E. 定位销铸孔的单边加工余量为0.6mm(大端);F. 螺纹底孔、铸孔深度按压铸件标准,一般为铸孔直径的2倍;盲孔根据实际情况而定?2、毛坯图上未注出的加工余量数据按上述原则确定;3、根据压铸件的工艺特征,在压铸件的推杆位置局部改变图纸尺寸和形状;4、孔径为最大处尺寸;5、与机加有关的相关尺寸、定位尺寸以★和方框表示;?6、定位、夹紧面应平整、不应有拔模斜度,并用定位、夹紧符号表示。
技术要求:1. 未注明铸造园角R3-4mm2. 未注明拔模斜度1-2.5°3. 未注明壁厚3±0.35mm4. 未注明铸件尺寸公差执行GB6414-86 CT6级5. 铸件表面允许有擦伤、凹陷、缺肉及网状毛刺等缺陷,但其缺陷程度和数量应该与供需双方同意的标准相一致;6. 铸件端面浇口残留高度≤2.5mm,飞边毛刺≤1.0mm,加工定位面及检测点不得有毛刺、缺肉或者凸起;7. 气密性要求:加工后产品加压腔用0.5kg气压,60秒中允许泄漏量10cc增加部分:一、压铸件尺寸:按GB/T15114有关规定执行;1、压铸件尺寸公差基本尺寸大于25mm时,按GB 6414规定CT6级执行;2、压铸件尺寸公差基本尺寸大于16mm,小于25mm的,按GB 6414规定CT5级执行;3、压铸件尺寸公差基本尺寸大于10mm,小于16mm的,按GB 6414规定CT4级执行;4、压铸件尺寸公差基本尺寸小于10mm,按GB 6414规定CT3级执行;5、压铸件形位公差按GB/T15114规定执行;二、压铸件材料化学成分:按ADC12 JIS H5302 及YL113 GB/T15115有关规定执行;三、压铸件力学性能:按GB/T15114规定执行;四、压铸件毛坯重量:由供方从供、需共同认可首批合格压铸件毛坯中,抽取10件称重,取平均值为压铸件毛坯的公称重量;压铸件毛坯重量公差按GB/T11351规定MT6级执行;五、压铸件表面质量:按QC/T273规定执行;六、压铸件内部质量:按GB/T15114规定执行;1、压铸件若能满足使用要求,则压铸件本质缺陷不作为报废依据;2、压铸件气密性要求:将压力为25KPa的滤水压缩空气,平缓的送入压铸件中,密封关闭9S后,测腔内压力,压力降到不低于21KPa为合格;3、在不影响使用的前提下,允许对铸件进行浸渗处理,浸渗处理后要满足上述气密性要求;4、压铸毛坯在需方加工后,若气密性不合格则返回供方,允许无偿做二次浸渗,试验合格后再送需方使用;5、供方提供的压铸件毛坯一次性不合格率小于0.5%;七、压铸件的试验方法及检验规则:按GB/T15114及QC/T273规定执行;1、其中化学成分和机械性能检验按QC/T273规定一类铸件标准执行,且当需方需要时,供方须向需方提供检验报告;2、一般情况下,采用试样检验力学性能;特殊情况下,若需方有要求时,也可以采用压铸件本身检验;。
工程图常见技术要求

一般技术要求1、零件去除氧化皮。
2、零件加工表面上,不应有划痕、擦伤等损伤零件表面的缺陷。
3、去除毛刺飞边。
热处理要求1、经调质处理,HRC50~55。
2、零件进行高频淬火,350~370℃回火,HRC40~45。
3、渗碳深度0、3mm。
4、进行高温时效处理。
公差要求1.未注形状公差应符合GB1184-80的要求,有等级要求H K L,要求依次降低。
2.未注线性与角度尺寸公差应符合GB/T 1804-m(表示中等)f m c v ,要求依次降低。
2、未注长度尺寸允许偏差±0、5mm。
3、铸件公差带对称于毛坯铸件基本尺寸配置。
如图示例,标在标题栏附近或技术要求中。
零件棱角1、未注圆角半径R5。
2、未注倒角均为2×45°。
3、锐角/尖角/锐边倒钝。
装配要求1、各密封件装配前必须浸透油。
2、装配滚动轴承允许采用机油加热进行热装,油的温度不得超过100℃。
3、齿轮装配后,齿面的接触斑点与侧隙应符合GB10095与GB11365的规定。
4、装配液压系统时允许使用密封填料或密封胶,但应防止进入系统中。
5、进入装配的零件及部件(包括外购件、外协件),均必须具有检验部门的合格证方能进行装配。
6、零件在装配前必须清理与清洗干净,不得有毛刺、飞边、氧化皮、锈蚀、切屑、油污、着色剂与灰尘等。
7、装配前应对零、部件的主要配合尺寸,特别就是过盈配合尺寸及相关精度进行复查。
8、装配过程中零件不允许磕、碰、划伤与锈蚀。
9、螺钉、螺栓与螺母紧固时,严禁打击或使用不合适的旋具与扳手。
紧固后螺钉槽、螺母与螺钉、螺栓头部不得损坏。
10、规定拧紧力矩要求的紧固件,必须采用力矩扳手,并按规定的拧紧力矩紧固。
11、同一零件用多件螺钉(螺栓)紧固时,各螺钉(螺栓)需交叉、对称、逐步、均匀拧紧。
12、圆锥销装配时应与孔应进行涂色检查,其接触率不应小于配合长度的60%,并应均匀分布。
13、平键与轴上键槽两侧面应均匀接触,其配合面不得有间隙。
图纸上的技术要求汇总

图纸技术要求一、一般技术要求制件去除外表氧化皮;制件不得有划痕、擦伤等损伤零件外表的缺陷;去除毛刺飞边;锐角倒钝;×45%%d;×0.3;外表平整无毛刺;二、未注公差技术要求〔金属件〕未注公差尺寸的极限偏差按GB/T 1804-m;未注形位公差按GB/T 1184-K;未注长度尺寸允许偏差±0.5;三、外表处理技术要求外表镀白〔黑〕锌处理;外表喷漆〔喷塑〕处理;外表发黑处理;外表电泳处理;外表镀铬处理;外表抛光处理;外表滚花,直纹〔网纹〕m=0.4 GB/T 6403.3;四、热处理技术要求制件氮化450-480HV;制件毛坯须调质处理220-260HB;制件调质处理30-35HRC;制件高频淬火45~50HRC;制件渗碳处理,深度>0.1;制件进行高温回火处理;制件整体淬火40-45HRC;五、铸件技术要求1、压铸件技术要求未注公差尺寸的极限偏差按GB/T 1804-m;未注形位公差按GB/T 1184-K;×45%%d;~2;未注过渡圆角R0.5-R2;未注脱模斜度≤1%%d;制件饱满光洁、无气孔、缩松、裂纹、夹渣、缺料等缺陷;各脱模顶料推杆压痕均应低于该制件外表0.2;制件要求符合GB/T 15114《铝合金压铸件》标准规定;外表喷漆〔喷塑〕处理,不得污染到已加工外表;加工外表在外表处理后加工,加工后涂油保护;未注尺寸参照三维造型;制件外表处理及其它要求按客户定;2、砂型铸造技术要求未注铸造圆角R5-10;铸件应彻底清砂,浇冒口应清除平整;铸件需人工时效;铸件不得有砂眼、气孔、缩松、裂纹等缺陷;粗加工后应再次进行人工时效;不加工外表涂底漆;六、冲压件技术要求制件未注公差尺寸的极限偏差按GB/T 15055-m;制件未注形位公差按GB/T 13916-2级;制件不得有裂纹或缺损;制件外表平整,不得有沟痕、碰伤等损坏外表,降低强度及寿命的缺陷;去除边角毛刺;外表处理:七、塑料件技术要求未注公差尺寸的极限偏差按GB/T 14486-MT6级;制件应饱满光整、色泽均匀;无缩痕、裂纹、银丝等缺陷;浇口、溢边修剪后飞边≤0.3,且不得伤及本体;~2;外表打光〔喷砂〕处理;未注过渡圆角取R0.3~R1,脱模斜度≤0.3%%d;各脱模顶料推杆压痕均应低于该制件外表0.2;与对应装配结合面外形配合错位≤0.5;制件应进行时效处理;制件机械强度须符合GB 3883.1标准规定;制件内腔外表打上材料标记和回收标志;未注尺寸参照三维造型;制件外表处理及其它要求由客户定;八、焊接件技术要求未注公差线性及角度尺寸的极限偏差均按GB/T 19804-B级;未注形位公差按GB/T 19804-F级;焊缝应均匀平整,焊渣清理干净;焊缝应焊透,不得烧穿及产生裂纹等影响机械性能的缺陷;九、各类零、部件技术要求1、齿轮〔齿轴〕技术要求未注公差尺寸的极限偏差按GB/T 1804-m;未注形位公差按GB/T 1184-K;制件毛坯须调质220~260HB;制件材料的化学成分和力学性能应符合GB/T 3077的规定;齿面接触斑点:按齿高不小于40%,按齿长不小于50%;齿面高频淬火回火至49-52HRC;制件外表不应有锈迹、裂纹、灼伤等影响使用寿命的伤痕及缺陷;最终工序热处理外表不得有氧化皮;2、一般轴芯〔无铣齿〕技术要求未注公差尺寸的极限偏差按GB/T 1804-m;未注形位公差按GB/T 1184-K;×45%%d;×0.3;制件毛坯须调质220~260HB;尺寸%%c 档车正反两条螺旋槽,螺距10,深0.4;螺纹外表不允许有磕碰、乱扣、毛刺等缺陷;热处理:外表处理:3、包轴毛坯〔一次成型〕技术要求未注公差尺寸的极限偏差按GB/T 1804-m;未注形位公差按GB/T 1184-K;绝缘层应饱满光洁,无裂纹、气孔、缺料、杂质等缺陷;包轴毛坯:绝缘层%%c 档〔注:指冲片配合档〕与轴芯间应能承受50Hz,实际正弦波电压2500V历时1min不击穿,其余绝缘层档3750V历时1min不击穿;一次成型:铁芯与轴芯间应能承受50Hz,实际正弦波电压2500V历时1min不击穿,其余绝缘层档3750V历时1min不击穿;4、包轴〔加工〕技术要求未注公差尺寸的极限偏差按GB/T 1804-m;未注形位公差按GB/T 1184-K;塑层应饱满光洁,无裂纹、气孔、缺料、杂质等缺陷;塑层%%c 档〔注:指冲片配合档〕与轴芯间应能承受50Hz,实际正弦波电压2500V历时1min不击穿,其余塑层档3750V历时1min不击穿;制件磨加工后应烘干除水处理;5、转子技术要求未注公差尺寸的极限偏差按GB/T 1804-m;未注形位公差按GB/T 1184-K;绕组接线按转子绕线原理图;绕组绝缘漆应均匀充满绕组并充分固化,漆膜应均匀无气泡或裂痕;云母槽开深0.8~1,槽宽0.6,槽内不得残留云母片;绕组冷态绝缘电阻不低于50MΩ;装风叶后校动平衡,其精度应不低于G6.3级;去重不允许有冲片铣穿、残缺现象;铁芯外圆不加工,绝缘漆不得高出铁芯外圆,并不得有明显积瘤;铁芯与轴芯间应能承受50Hz,实际正弦波电压2500V,1min不击穿;绕组与铁芯间应能承受50Hz,实际正弦波电压1250V,1min不击穿;匝间绝缘应能承受1000Hz,峰值为2100V,历时3s不击穿;换向器与轴芯间应能承受50Hz,实际正弦波电压3750V,1min不击穿;应去除铁屑、铜粉、油污等杂质;铁芯外圆应涂透明淡金水防锈处理;6、定子技术要求绕组绕制整齐无松散;引线接头应牢固可靠且充分绝缘;绕组与铁芯间应能承受50Hz,实际正弦波电压1250V历时1min不击穿;匝间绝缘应能承受1000Hz,峰值为2100V,历时3s不击穿;绕组绝缘漆应均匀充满绕组并充分固化,漆膜应均匀无气泡或积瘤;铁芯外表不得有明显绝缘漆;7、定、转子铁芯技术要求未注公差尺寸的极限偏差按GB/T 1804-m;未注形位公差按GB/T 1184-K;冲片叠装应紧密可靠,片间无夹杂,外表及槽内无污物和油渍;冲片按同一冲制方向压装;冲片齿槽口整齐与转轴平行,误差不大于0.5;铁芯两端弹开度不大于0.5;8、定、转子冲片技术要求制件未注公差尺寸的极限偏差按GB/T 15055-m;制件未注形位公差按GB/T 13916-2级;制件应外表平整,完整无缺料;尖角处允许用R0.3过渡;制件毛刺不大于0.05〔注:高速冲时不大于0.02〕;制件应不含油脂,剪切油不能用机油;9、绝缘纸技术要求外表不得有划痕、折痕;裁边不起毛;10、换向器技术要求未注公差尺寸的极限偏差按GB/T 1804-m;未注形位公差按GB/T 1184-K;外观完整,外表光滑,应无裂纹、毛刺、锈蚀、气孔、夹杂等缺陷;绝缘电阻:室温下内孔与换向片之间大于50MΩ;云母片厚度取0.5;换向片对换向器轴线偏斜度不大于云母片厚度的1/3;介电强度:片间承受频率50Hz,泄露电流为0.1mA,实际正弦波电压600V历时1s不击穿;换向片与内孔轴芯间承受频率50Hz,泄露电流为0.25mA,实际正弦波电压3750V历时1min不击穿;试验与检验应符合JB/T 10107《电开工具换向器》标准要求;11、电缆线技术要求电缆线长度尺寸指工具电缆出口至插头的导线部分,不包括插头和插脚;软电缆应符合GB/T 5013《额定电压450V/750V及以下橡皮绝缘电缆》标准要求;聚氯乙烯电缆应符合GB/T 5023《额定电压450V/750V及以下聚氯乙烯绝缘电缆》标准要求;插脚与可触及插头外表的绝缘应能承受50Hz,实际正弦波电压3750V历时1min不击穿;制件还应符合GB 1002《家用和类似用途单相插头插座型式、基本参数和尺寸》和GB 2099《家用和类似用途插头插座》标准要求;12、开关技术要求未注公差尺寸的极限偏差按SJ/T 10628-7级;除本图要求的外形尺寸、功能、图形、文字外,试验和检验均应符合GB/T22692《电开工具开关》标准要求;开关的使用性能应保证5万次无故障正常使用;13、电缆护套技术要求未注公差尺寸的极限偏差按GB/T 3672.1-2级;未注形位公差按GB/T 3672.2-M级;制件不得有缺料、破裂等缺陷。
毛坯图纸技术要求

毛坯图设计原则:1、凡是有机加工要求的地方都留有加工余量:压铸件机械加工余量:按GB/T11350规定MA-D级执行;A. 大端面加工余量为1.2mm;B. 侧面法蓝面加工余量1.0mm;C. φ25mm以上内孔单边加工余量为0.75mm;φ25mm以下内孔单边加工余量为0.6mm;D. 螺纹底孔的大端尺寸为:底孔直径-1.5mm;E. 定位销铸孔的单边加工余量为0.6mm(大端);F. 螺纹底孔、铸孔深度按压铸件标准,一般为铸孔直径的2倍;盲孔根据实际情况而定?2、毛坯图上未注出的加工余量数据按上述原则确定;3、根据压铸件的工艺特征,在压铸件的推杆位置局部改变图纸尺寸和形状;4、孔径为最大处尺寸;5、与机加有关的相关尺寸、定位尺寸以★和方框表示;?6、定位、夹紧面应平整、不应有拔模斜度,并用定位、夹紧符号表示。
技术要求:1. 未注明铸造园角R3-4mm2. 未注明拔模斜度1-2.5°3. 未注明壁厚3±0.35mm4. 未注明铸件尺寸公差执行GB6414-86 CT6级5. 铸件表面允许有擦伤、凹陷、缺肉及网状毛刺等缺陷,但其缺陷程度和数量应该与供需双方同意的标准相一致;6. 铸件端面浇口残留高度≤2.5mm,飞边毛刺≤1.0mm,加工定位面及检测点不得有毛刺、缺肉或者凸起;7. 气密性要求:加工后产品加压腔用0.5kg气压,60秒中允许泄漏量10cc附加部分:一、压铸件尺寸:按GB/T15114有关规定执行;1、压铸件尺寸公差基本尺寸大于25mm时,按GB 6414规定CT6级执行;2、压铸件尺寸公差基本尺寸大于16mm,小于25mm的,按GB 6414规定CT5级执行;3、压铸件尺寸公差基本尺寸大于10mm,小于16mm的,按GB 6414规定CT4级执行;4、压铸件尺寸公差基本尺寸小于10mm,按GB 6414规定CT3级执行;5、压铸件形位公差按GB/T15114规定执行;二、压铸件材料化学成分:按ADC12 JIS H5302 及YL113 GB/T15115有关规定执行;三、压铸件力学性能:按GB/T15114规定执行;四、压铸件毛坯重量:由供方从供、需共同认可首批合格压铸件毛坯中,抽取10件称重,取平均值为压铸件毛坯的公称重量;压铸件毛坯重量公差按GB/T11351规定MT6级执行;五、压铸件表面质量:按QC/T273规定执行;六、压铸件内部质量:按GB/T15114规定执行;1、压铸件若能满足使用要求,则压铸件本质缺陷不作为报废依据;2、压铸件气密性要求:将压力为25KPa的滤水压缩空气,平缓的送入压铸件中,密封关闭9S后,测腔内压力,压力降到不低于21KPa为合格;3、在不影响使用的前提下,允许对铸件进行浸渗处理,浸渗处理后要满足上述气密性要求;4、压铸毛坯在需方加工后,若气密性不合格则返回供方,允许无偿做二次浸渗,试验合格后再送需方使用;5、供方提供的压铸件毛坯一次性不合格率小于0.5%;七、压铸件的试验方法及检验规则:按GB/T15114及QC/T273规定执行;1、其中化学成分和机械性能检验按QC/T273规定一类铸件标准执行,且当需方需要时,供方须向需方提供检验报告;2、一般情况下,采用试样检验力学性能;特殊情况下,若需方有要求时,也可以采用压铸件本身检验;。
挤压、粉末冶金、不锈钢精铸类毛坯件技术规范

挤压、粉末冶金、不锈钢精铸类零件及毛坯技术规范批准前言本规范的附录A是规范性附录。
挤压、粉末冶金、不锈钢精铸类零件及毛坯技术规范1范围本规范规定了挤压、粉末冶金、不锈钢精铸类零件及毛坯件(以下简称零件及毛坯件)技术要求。
本规范适用于零件及毛坯件的验收规范。
2规范性引用文件下列文件中的条款通过本规范的引用而成为本规范的条款。
凡是注日期的引用文件,其随后的所有修改单(不包括勘误的内容)或修订版均不适用于本规范,然而,鼓励根据本规范达成协议的各方研究是否可使用这些文件的最新版本。
凡不注日期的引用文件,其最新版本适用于本规范。
Q QG-0029/ZK-11/2007 成件供方质量管理要求21E/105.021.050 关于ROHS要求的成品及物料检验规定Q/21EJ1.165 金属壳体件倒圆、倒角及典型键槽设计、加工、检测通用规范Q/21EJ1.1 金属壳体零件表面质量控制的有关规定Q/21EJ1.162 滚花设计、加工、检测规范3术语3.1内表面指零件的包容面,在其之内没有本零件的材料,是指与孔、空腔特征直接相关的表面,如孔壁、盲孔孔底、孔内台阶面、孔内环槽面、空腔壁、空腔腔底面、空腔内的台阶特征面、空腔内的槽特征面等。
典型示意零件见图1。
3.2外表面指零件的被包容面,是零件的最外层轮廓面,在其之外没有本零件的材料,典型示意零件见图1。
3.3毛坯面由模具直接成型,后续不采用切削加工的面。
图1 外表面和内表面示意图4技术要求和检验4.1合格鉴定按本规范提交的零件应是经过相关试验验证或试生产合格的零件。
4.2材料4.2.1进行零件及毛坯件加工的生产单位,应优先使用由我公司提供的合格材料进行生产。
4.2.2零件及毛坯件生产单位可以采用自购料方式,但应遵守QG-0029/ZK-11/2007的规定进行采购和生产。
零件生产单位需提供所加工每批零件的材料检验编号或材质检测报告,材料检验编号必须由我公司出具,材质检验报告必须由我公司或我公司认可的具备材质检测资质的第三方机构出具。
图纸上的技术要求汇总

图纸技术要求一、一般技术要求制件去除表面氧化皮;制件不得有划痕、擦伤等损伤零件表面的缺陷;去除毛刺飞边;锐角倒钝;未注倒角均为0.5×45%%d;未注越程槽均为1.2×0.3;表面平整无毛刺;二、未注公差技术要求(金属件)未注公差尺寸的极限偏差按GB/T 1804-m;未注形位公差按GB/T 1184-K;未注长度尺寸允许偏差±0.5;三、表面处理技术要求表面镀白(黑)锌处理;表面喷漆(喷塑)处理;表面发黑处理;表面电泳处理;表面镀铬处理;表面抛光处理;表面滚花,直纹(网纹)m=0.4 GB/T 6403.3;四、热处理技术要求制件氮化450-480HV;制件毛坯须调质处理220-260HB;制件调质处理30-35HRC;制件高频淬火45~50HRC;制件渗碳处理,深度>0.1;制件进行高温回火处理;制件整体淬火40-45HRC;五、铸件技术要求1、压铸件技术要求未注公差尺寸的极限偏差按GB/T 1804-m;未注形位公差按GB/T 1184-K;未注倒角均为0.5×45%%d;未注壁厚2.5;未注筋板1.5~2;未注过渡圆角R0.5-R2;未注脱模斜度≤1%%d;制件饱满光洁、无气孔、缩松、裂纹、夹渣、缺料等缺陷;各脱模顶料推杆压痕均应低于该制件表面0.2;制件要求符合GB/T 15114《铝合金压铸件》标准规定;表面喷漆(喷塑)处理,不得污染到已加工表面;加工表面在表面处理后加工,加工后涂油保护;未注尺寸参照三维造型;制件表面处理及其它要求按客户定;2、砂型铸造技术要求未注铸造圆角R5-10;铸件应彻底清砂,浇冒口应清除平整;铸件需人工时效;铸件不得有砂眼、气孔、缩松、裂纹等缺陷;粗加工后应再次进行人工时效;不加工表面涂底漆;六、冲压件技术要求制件未注公差尺寸的极限偏差按GB/T 15055-m;制件未注形位公差按GB/T 13916-2级;制件不得有裂纹或缺损;制件表面平整,不得有沟痕、碰伤等损坏表面,降低强度及寿命的缺陷;去除边角毛刺;表面处理:七、塑料件技术要求未注公差尺寸的极限偏差按GB/T 14486-MT6级;制件应饱满光整、色泽均匀;无缩痕、裂纹、银丝等缺陷;浇口、溢边修剪后飞边≤0.3,且不得伤及本体;未注壁厚3;未注筋板1.5~2;表面打光(喷砂)处理;未注过渡圆角取R0.3~R1,脱模斜度≤0.3%%d;各脱模顶料推杆压痕均应低于该制件表面0.2;与对应装配结合面外形配合错位≤0.5;制件应进行时效处理;制件机械强度须符合GB 3883.1标准规定;制件内腔表面打上材料标记和回收标志;未注尺寸参照三维造型;制件表面处理及其它要求由客户定;八、焊接件技术要求未注公差线性及角度尺寸的极限偏差均按GB/T 19804-B级;未注形位公差按GB/T 19804-F级;焊缝应均匀平整,焊渣清理干净;焊缝应焊透,不得烧穿及产生裂纹等影响机械性能的缺陷;九、各类零、部件技术要求1、齿轮(齿轴)技术要求未注公差尺寸的极限偏差按GB/T 1804-m;未注形位公差按GB/T 1184-K;制件毛坯须调质220~260HB;制件材料的化学成分和力学性能应符合GB/T 3077的规定;齿面接触斑点:按齿高不小于40%,按齿长不小于50%;齿面高频淬火回火至49-52HRC;制件表面不应有锈迹、裂纹、灼伤等影响使用寿命的伤痕及缺陷;最终工序热处理表面不得有氧化皮;2、一般轴芯(无铣齿)技术要求未注公差尺寸的极限偏差按GB/T 1804-m;未注形位公差按GB/T 1184-K;未注倒角均为0.5×45%%d;未注越程槽均为1.2×0.3;制件毛坯须调质220~260HB;尺寸%%c 档车正反两条螺旋槽,螺距10,深0.4;螺纹表面不允许有磕碰、乱扣、毛刺等缺陷;热处理:表面处理:3、包轴毛坯(一次成型)技术要求未注公差尺寸的极限偏差按GB/T 1804-m;未注形位公差按GB/T 1184-K;绝缘层应饱满光洁,无裂纹、气孔、缺料、杂质等缺陷;包轴毛坯:绝缘层%%c 档(注:指冲片配合档)与轴芯间应能承受50Hz,实际正弦波电压2500V历时1min不击穿,其余绝缘层档3750V历时1min不击穿;一次成型:铁芯与轴芯间应能承受50Hz,实际正弦波电压2500V历时1min不击穿,其余绝缘层档3750V历时1min不击穿;4、包轴(加工)技术要求未注公差尺寸的极限偏差按GB/T 1804-m;未注形位公差按GB/T 1184-K;塑层应饱满光洁,无裂纹、气孔、缺料、杂质等缺陷;塑层%%c 档(注:指冲片配合档)与轴芯间应能承受50Hz,实际正弦波电压2500V历时1min不击穿,其余塑层档3750V历时1min不击穿;制件磨加工后应烘干除水处理;5、转子技术要求未注公差尺寸的极限偏差按GB/T 1804-m;未注形位公差按GB/T 1184-K;绕组接线按转子绕线原理图;绕组绝缘漆应均匀充满绕组并充分固化,漆膜应均匀无气泡或裂痕;云母槽开深0.8~1,槽宽0.6,槽内不得残留云母片;绕组冷态绝缘电阻不低于50MΩ;装风叶后校动平衡,其精度应不低于G6.3级;去重不允许有冲片铣穿、残缺现象;铁芯外圆不加工,绝缘漆不得高出铁芯外圆,并不得有明显积瘤;铁芯与轴芯间应能承受50Hz,实际正弦波电压2500V,1min不击穿;绕组与铁芯间应能承受50Hz,实际正弦波电压1250V,1min不击穿;匝间绝缘应能承受1000Hz,峰值为2100V,历时3s不击穿;换向器与轴芯间应能承受50Hz,实际正弦波电压3750V,1min不击穿;应去除铁屑、铜粉、油污等杂质;铁芯外圆应涂透明淡金水防锈处理;6、定子技术要求绕组绕制整齐无松散;引线接头应牢固可靠且充分绝缘;绕组与铁芯间应能承受50Hz,实际正弦波电压1250V历时1min不击穿;匝间绝缘应能承受1000Hz,峰值为2100V,历时3s不击穿;绕组绝缘漆应均匀充满绕组并充分固化,漆膜应均匀无气泡或积瘤;铁芯表面不得有明显绝缘漆;7、定、转子铁芯技术要求未注公差尺寸的极限偏差按GB/T 1804-m;未注形位公差按GB/T 1184-K;冲片叠装应紧密可靠,片间无夹杂,表面及槽内无污物和油渍;冲片按同一冲制方向压装;冲片齿槽口整齐与转轴平行,误差不大于0.5;铁芯两端弹开度不大于0.5;8、定、转子冲片技术要求制件未注公差尺寸的极限偏差按GB/T 15055-m;制件未注形位公差按GB/T 13916-2级;制件应表面平整,完整无缺料;尖角处允许用R0.3过渡;制件毛刺不大于0.05(注:高速冲时不大于0.02);制件应不含油脂,剪切油不能用机油;9、绝缘纸技术要求表面不得有划痕、折痕;裁边不起毛;10、换向器技术要求未注公差尺寸的极限偏差按GB/T 1804-m;未注形位公差按GB/T 1184-K;外观完整,表面光滑,应无裂纹、毛刺、锈蚀、气孔、夹杂等缺陷;绝缘电阻:室温下内孔与换向片之间大于50MΩ;云母片厚度取0.5;换向片对换向器轴线偏斜度不大于云母片厚度的1/3;介电强度:片间承受频率50Hz,泄露电流为0.1mA,实际正弦波电压600V历时1s不击穿;换向片与内孔轴芯间承受频率50Hz,泄露电流为0.25mA,实际正弦波电压3750V历时1min不击穿;试验与检验应符合JB/T 10107《电动工具换向器》标准要求;11、电缆线技术要求电缆线长度尺寸指工具电缆出口至插头的导线部分,不包括插头和插脚;软电缆应符合GB/T 5013《额定电压450V/750V及以下橡皮绝缘电缆》标准要求;聚氯乙烯电缆应符合GB/T 5023《额定电压450V/750V及以下聚氯乙烯绝缘电缆》标准要求;插脚与可触及插头表面的绝缘应能承受50Hz,实际正弦波电压3750V历时1min不击穿;制件还应符合GB 1002《家用和类似用途单相插头插座型式、基本参数和尺寸》和GB 2099《家用和类似用途插头插座》标准要求;12、开关技术要求未注公差尺寸的极限偏差按SJ/T 10628-7级;除本图要求的外形尺寸、功能、图形、文字外,试验和检验均应符合GB/T22692《电动工具开关》标准要求;开关的使用性能应保证5万次无故障正常使用;13、电缆护套技术要求未注公差尺寸的极限偏差按GB/T 3672.1-2级;未注形位公差按GB/T 3672.2-M级;制件不得有缺料、破裂等缺陷。
图纸上的技术要求汇总
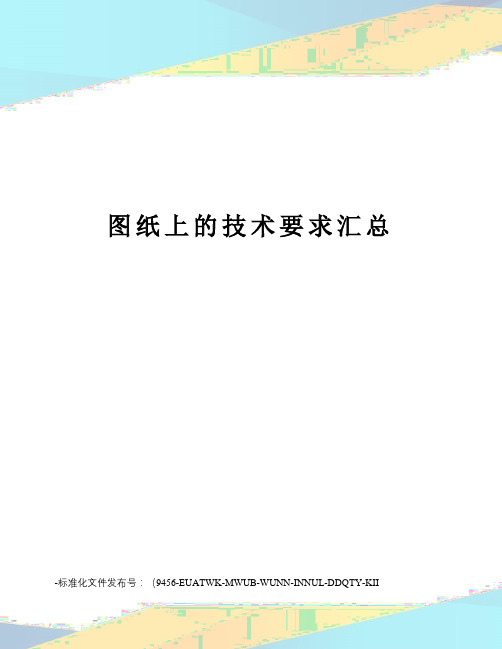
图纸上的技术要求汇总-标准化文件发布号:(9456-EUATWK-MWUB-WUNN-INNUL-DDQTY-KII图纸技术要求一、一般技术要求制件去除表面氧化皮;制件不得有划痕、擦伤等损伤零件表面的缺陷;去除毛刺飞边;锐角倒钝;未注倒角均为0.5×45%%d;未注越程槽均为1.2×0.3;表面平整无毛刺;二、未注公差技术要求(金属件)未注公差尺寸的极限偏差按GB/T 1804-m;未注形位公差按GB/T 1184-K;未注长度尺寸允许偏差±0.5;三、表面处理技术要求表面镀白(黑)锌处理;表面喷漆(喷塑)处理;表面发黑处理;表面电泳处理;表面镀铬处理;表面抛光处理;表面滚花,直纹(网纹)m=0.4 GB/T 6403.3;四、热处理技术要求制件氮化450-480HV;制件毛坯须调质处理220-260HB;制件调质处理30-35HRC;制件高频淬火45~50HRC;制件渗碳处理,深度>0.1;制件进行高温回火处理;制件整体淬火40-45HRC;五、铸件技术要求1、压铸件技术要求未注公差尺寸的极限偏差按GB/T 1804-m;未注形位公差按GB/T 1184-K;未注倒角均为0.5×45%%d;未注壁厚2.5;未注筋板1.5~2;未注过渡圆角R0.5-R2;未注脱模斜度≤1%%d;制件饱满光洁、无气孔、缩松、裂纹、夹渣、缺料等缺陷;各脱模顶料推杆压痕均应低于该制件表面0.2;制件要求符合GB/T 15114《铝合金压铸件》标准规定;表面喷漆(喷塑)处理,不得污染到已加工表面;加工表面在表面处理后加工,加工后涂油保护;未注尺寸参照三维造型;制件表面处理及其它要求按客户定;2、砂型铸造技术要求未注铸造圆角R5-10;铸件应彻底清砂,浇冒口应清除平整;铸件需人工时效;铸件不得有砂眼、气孔、缩松、裂纹等缺陷;粗加工后应再次进行人工时效;不加工表面涂底漆;六、冲压件技术要求制件未注公差尺寸的极限偏差按GB/T 15055-m;制件未注形位公差按GB/T 13916-2级;制件不得有裂纹或缺损;制件表面平整,不得有沟痕、碰伤等损坏表面,降低强度及寿命的缺陷;去除边角毛刺;表面处理:七、塑料件技术要求未注公差尺寸的极限偏差按GB/T 14486-MT6级;制件应饱满光整、色泽均匀;无缩痕、裂纹、银丝等缺陷;浇口、溢边修剪后飞边≤0.3,且不得伤及本体;未注壁厚3;未注筋板1.5~2;表面打光(喷砂)处理;未注过渡圆角取R0.3~R1,脱模斜度≤0.3%%d;各脱模顶料推杆压痕均应低于该制件表面0.2;与对应装配结合面外形配合错位≤0.5;制件应进行时效处理;制件机械强度须符合GB 3883.1标准规定;制件内腔表面打上材料标记和回收标志;未注尺寸参照三维造型;制件表面处理及其它要求由客户定;八、焊接件技术要求未注公差线性及角度尺寸的极限偏差均按GB/T 19804-B级;未注形位公差按GB/T 19804-F级;焊缝应均匀平整,焊渣清理干净;焊缝应焊透,不得烧穿及产生裂纹等影响机械性能的缺陷;九、各类零、部件技术要求1、齿轮(齿轴)技术要求未注公差尺寸的极限偏差按GB/T 1804-m;未注形位公差按GB/T 1184-K;制件毛坯须调质220~260HB;制件材料的化学成分和力学性能应符合GB/T 3077的规定;齿面接触斑点:按齿高不小于40%,按齿长不小于50%;齿面高频淬火回火至49-52HRC;制件表面不应有锈迹、裂纹、灼伤等影响使用寿命的伤痕及缺陷;最终工序热处理表面不得有氧化皮;2、一般轴芯(无铣齿)技术要求未注公差尺寸的极限偏差按GB/T 1804-m;未注形位公差按GB/T 1184-K;未注倒角均为0.5×45%%d;未注越程槽均为1.2×0.3;制件毛坯须调质220~260HB;尺寸%%c 档车正反两条螺旋槽,螺距10,深0.4;螺纹表面不允许有磕碰、乱扣、毛刺等缺陷;热处理:表面处理:3、包轴毛坯(一次成型)技术要求未注公差尺寸的极限偏差按GB/T 1804-m;未注形位公差按GB/T 1184-K;绝缘层应饱满光洁,无裂纹、气孔、缺料、杂质等缺陷;包轴毛坯:绝缘层%%c 档(注:指冲片配合档)与轴芯间应能承受50Hz,实际正弦波电压2500V历时1min不击穿,其余绝缘层档3750V历时1min不击穿;一次成型:铁芯与轴芯间应能承受50Hz,实际正弦波电压2500V历时1min不击穿,其余绝缘层档3750V历时1min不击穿;4、包轴(加工)技术要求未注公差尺寸的极限偏差按GB/T 1804-m;未注形位公差按GB/T 1184-K;塑层应饱满光洁,无裂纹、气孔、缺料、杂质等缺陷;塑层%%c 档(注:指冲片配合档)与轴芯间应能承受50Hz,实际正弦波电压2500V历时1min不击穿,其余塑层档3750V历时1min不击穿;制件磨加工后应烘干除水处理;5、转子技术要求未注公差尺寸的极限偏差按GB/T 1804-m;未注形位公差按GB/T 1184-K;绕组接线按转子绕线原理图;绕组绝缘漆应均匀充满绕组并充分固化,漆膜应均匀无气泡或裂痕;云母槽开深0.8~1,槽宽0.6,槽内不得残留云母片;绕组冷态绝缘电阻不低于50MΩ;装风叶后校动平衡,其精度应不低于G6.3级;去重不允许有冲片铣穿、残缺现象;铁芯外圆不加工,绝缘漆不得高出铁芯外圆,并不得有明显积瘤;铁芯与轴芯间应能承受50Hz,实际正弦波电压2500V,1min不击穿;绕组与铁芯间应能承受50Hz,实际正弦波电压1250V,1min不击穿;匝间绝缘应能承受1000Hz,峰值为2100V,历时3s不击穿;换向器与轴芯间应能承受50Hz,实际正弦波电压3750V,1min不击穿;应去除铁屑、铜粉、油污等杂质;铁芯外圆应涂透明淡金水防锈处理;6、定子技术要求绕组绕制整齐无松散;引线接头应牢固可靠且充分绝缘;绕组与铁芯间应能承受50Hz,实际正弦波电压1250V历时1min不击穿;匝间绝缘应能承受1000Hz,峰值为2100V,历时3s不击穿;绕组绝缘漆应均匀充满绕组并充分固化,漆膜应均匀无气泡或积瘤;铁芯表面不得有明显绝缘漆;7、定、转子铁芯技术要求未注公差尺寸的极限偏差按GB/T 1804-m;未注形位公差按GB/T 1184-K;冲片叠装应紧密可靠,片间无夹杂,表面及槽内无污物和油渍;冲片按同一冲制方向压装;冲片齿槽口整齐与转轴平行,误差不大于0.5;铁芯两端弹开度不大于0.5;8、定、转子冲片技术要求制件未注公差尺寸的极限偏差按GB/T 15055-m;制件未注形位公差按GB/T 13916-2级;制件应表面平整,完整无缺料;尖角处允许用R0.3过渡;制件毛刺不大于0.05(注:高速冲时不大于0.02);制件应不含油脂,剪切油不能用机油;9、绝缘纸技术要求表面不得有划痕、折痕;裁边不起毛;10、换向器技术要求未注公差尺寸的极限偏差按GB/T 1804-m;未注形位公差按GB/T 1184-K;外观完整,表面光滑,应无裂纹、毛刺、锈蚀、气孔、夹杂等缺陷;绝缘电阻:室温下内孔与换向片之间大于50MΩ;云母片厚度取0.5;换向片对换向器轴线偏斜度不大于云母片厚度的1/3;介电强度:片间承受频率50Hz,泄露电流为0.1mA,实际正弦波电压600V历时1s不击穿;换向片与内孔轴芯间承受频率50Hz,泄露电流为0.25mA,实际正弦波电压3750V历时1min不击穿;试验与检验应符合JB/T 10107《电动工具换向器》标准要求;11、电缆线技术要求电缆线长度尺寸指工具电缆出口至插头的导线部分,不包括插头和插脚;软电缆应符合GB/T 5013《额定电压450V/750V及以下橡皮绝缘电缆》标准要求;聚氯乙烯电缆应符合GB/T 5023《额定电压450V/750V及以下聚氯乙烯绝缘电缆》标准要求;插脚与可触及插头表面的绝缘应能承受50Hz,实际正弦波电压3750V历时1min不击穿;制件还应符合GB 1002《家用和类似用途单相插头插座型式、基本参数和尺寸》和GB 2099《家用和类似用途插头插座》标准要求;12、开关技术要求未注公差尺寸的极限偏差按SJ/T 10628-7级;除本图要求的外形尺寸、功能、图形、文字外,试验和检验均应符合GB/T 22692《电动工具开关》标准要求;开关的使用性能应保证5万次无故障正常使用;13、电缆护套技术要求未注公差尺寸的极限偏差按GB/T 3672.1-2级;未注形位公差按GB/T 3672.2-M级;制件不得有缺料、破裂等缺陷。
图纸技术要求
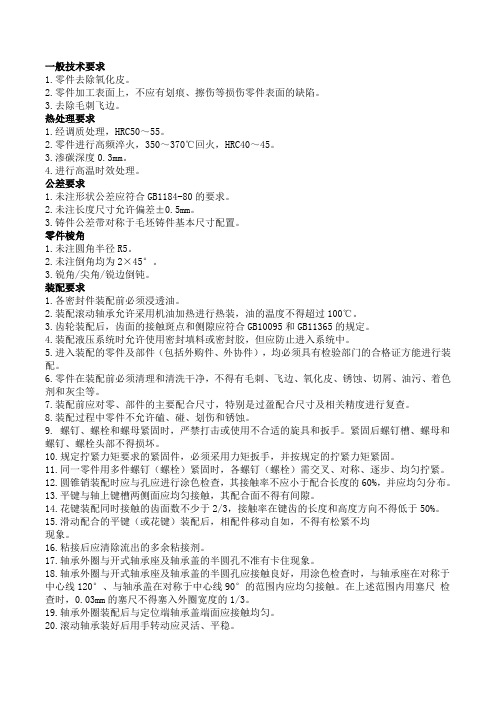
一般技术要求1.零件去除氧化皮。
2.零件加工表面上,不应有划痕、擦伤等损伤零件表面的缺陷。
3.去除毛刺飞边。
热处理要求1.经调质处理,HRC50~55。
2.零件进行高频淬火,350~370℃回火,HRC40~45。
3.渗碳深度0.3mm。
4.进行高温时效处理。
公差要求1.未注形状公差应符合GB1184-80的要求。
2.未注长度尺寸允许偏差±0.5mm。
3.铸件公差带对称于毛坯铸件基本尺寸配置。
零件棱角1.未注圆角半径R5。
2.未注倒角均为2×45°。
3.锐角/尖角/锐边倒钝。
装配要求1.各密封件装配前必须浸透油。
2.装配滚动轴承允许采用机油加热进行热装,油的温度不得超过100℃。
3.齿轮装配后,齿面的接触斑点和侧隙应符合GB10095和GB11365的规定。
4.装配液压系统时允许使用密封填料或密封胶,但应防止进入系统中。
5.进入装配的零件及部件(包括外购件、外协件),均必须具有检验部门的合格证方能进行装配。
6.零件在装配前必须清理和清洗干净,不得有毛刺、飞边、氧化皮、锈蚀、切屑、油污、着色剂和灰尘等。
7.装配前应对零、部件的主要配合尺寸,特别是过盈配合尺寸及相关精度进行复查。
8.装配过程中零件不允许磕、碰、划伤和锈蚀。
9. 螺钉、螺栓和螺母紧固时,严禁打击或使用不合适的旋具和扳手。
紧固后螺钉槽、螺母和螺钉、螺栓头部不得损坏。
10.规定拧紧力矩要求的紧固件,必须采用力矩扳手,并按规定的拧紧力矩紧固。
11.同一零件用多件螺钉(螺栓)紧固时,各螺钉(螺栓)需交叉、对称、逐步、均匀拧紧。
12.圆锥销装配时应与孔应进行涂色检查,其接触率不应小于配合长度的60%,并应均匀分布。
13.平键与轴上键槽两侧面应均匀接触,其配合面不得有间隙。
14.花键装配同时接触的齿面数不少于2/3,接触率在键齿的长度和高度方向不得低于50%。
15.滑动配合的平键(或花键)装配后,相配件移动自如,不得有松紧不均现象。
一般的图纸技术要求填写
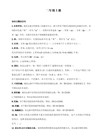
铸钢件表面堆焊接时,焊道间的重叠量不得小于焊道宽度的1/3。
10.锻件要求:
每个钢锭的水口、冒口应有足够的切除量,一以保证锻件无缩孔和严重的偏折。
锻件应在有足够能力的锻压机上锻造成形,以保证锻件内部充分锻透。
锻件不允许有肉眼可见的裂纹、折叠和其他影响使用的外观缺陷。局部缺陷可以清除,但清理深度不得超过加工余量的75%,锻件非加工表面上的缺陷应清理干净并圆滑过渡。
滑动配合的平键(或花键)装配后,相配件移动自如,不得有松紧不均现象。
粘接后应清除流出的多余粘接剂。
轴承外圈与开式轴承座及轴承盖的半圆孔不准有卡住现象。
轴承外圈与开式轴承座及轴承盖的半圆孔应接触良好,用涂色检查时,与轴承座在对称于中心线120°、与轴承盖在对称于中心线90°的范围内应均匀接触。在上述范围内用塞尺检查时,0.03mm的塞尺不得塞入外圈宽度的1/3。
渗碳深度0.3mm。
进行高温时效处理。
3.公差要求:
未注形状公差应符合GB1184-80的要求。
未注长度尺寸允许偏差±0.5mm。
铸件公差带对称于毛坯铸件基本尺寸配置。
4.零件棱角:
未注圆角半径R5。
未注倒角均为2×45°。
锐角倒钝。
5.装配要求:
各密封件装配前必须浸透油。
装配滚动轴承允许采用机油加热进行热装,油的温度不得超过100℃。
规定拧紧力矩要求的紧固件,必须采用力矩扳手,并按规定的拧紧力矩紧固。
同一零件用多件螺钉(螺栓)紧固时,各螺钉(螺栓)需交叉、对称配合长度的60%,并应均匀分布。
平键与轴上键槽两侧面应均匀接触,其配合面不得有间隙。
机械加工之图纸技术要求大全

机械加工之图纸技术要求大全一样技术要求1.零件去氧化皮;2.零件加工表面上,不该有划痕、擦伤等损伤零件表面的缺点;3.去除毛刺飞边。
热处置要求1.经调质处置,HRC50-552.零件进行高频淬火,350-370℃回火,HRC40-50;3.渗碳深度;4.进行高温时效处置。
公差要求1.未注形状公差应符合GB1184-80的要求;2.未注长度尺寸许诺误差±;3.铸件公差带对称毛坯铸件大体尺寸配置。
零件棱角1.未注圆角半径R5;2.未注倒角均为2*45°;3.锐角/尖角/钝边倒钝。
装配要求1.各密封件装配前必需渗透油;2.装配转动轴承许诺采纳机油加热进行热装,油的温度不得超过100℃;3.齿轮装配后,齿面的接触斑点和侧隙应符合GB10095和GB11365的规定;4.装配液压系统时许诺利用密封填料或密封胶,但应避免进入系统中;5.进入装配的零件及部件,均必需具有合格证才能进行装配;6.零件在装配前必需清理和清洗干净,不得有毛刺、飞边、氧化皮、锈蚀、切削、油污、着色剂和尘埃等;7.装配前应付零部件的要紧配合尺寸,专门是过盈配合尺寸及相应精度进行复查。
8.装配进程中零件不许诺磕碰。
划伤和锈蚀;9.螺钉、螺栓和螺母紧固时,严禁冲击或利用不适合的旋具和扳手。
紧固后螺钉槽、螺母和螺钉、螺栓头部不得损伤;10.规定拧紧力矩要求的紧固件,必需采使劲矩扳手,并按规定的拧紧力矩紧固;11.同一零件用多件螺钉紧固时,各螺钉(螺栓)需交叉、对称、慢慢、均匀拧紧;12.圆锥销装配时应与孔应进行涂色检查,其接触率不该小于配合长度的60%,并应均匀散布;13.平键与轴上键槽双侧面应均匀接触,其配合面不得有间隙;14.花键装配同时接触的齿面数很多于2/3,接触率在键齿的长度和高度方向不得低于50%;15.滑动配合的平键(花键)装配后,相配件移动自如,不得有松紧不均现象;16.粘接后应清除流出的多余粘结剂;17.轴承外圈与开式轴承座机轴承盖的半圆孔不准有卡住现象;18.轴承外圈与开式轴承座机轴承盖的半圆孔应接触良好,用涂色检查时,与轴承座在对称于中心线120°、与轴承盖在对称于中心线90°的范围内应均匀接触。
汽车发动机缸体毛坯-2023标准
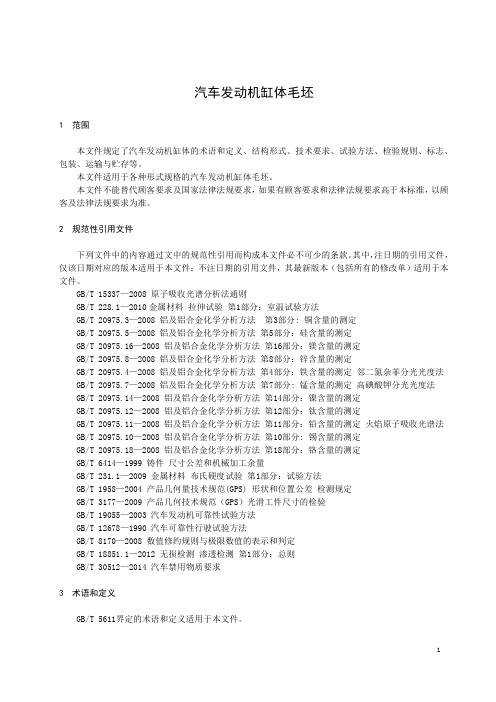
汽车发动机缸体毛坯1范围本文件规定了汽车发动机缸体的术语和定义、结构形式、技术要求、试验方法、检验规则、标志、包装、运输与贮存等。
本文件适用于各种形式规格的汽车发动机缸体毛坯。
本文件不能替代顾客要求及国家法律法规要求,如果有顾客要求和法律法规要求高于本标准,以顾客及法律法规要求为准。
2规范性引用文件下列文件中的内容通过文中的规范性引用而构成本文件必不可少的条款。
其中,注日期的引用文件,仅该日期对应的版本适用于本文件;不注日期的引用文件,其最新版本(包括所有的修改单)适用于本文件。
GB/T15337—2008原子吸收光谱分析法通则GB/T228.1—2010金属材料拉伸试验第1部分:室温试验方法GB/T20975.3—2008铝及铝合金化学分析方法第3部分:铜含量的测定GB/T20975.5—2008铝及铝合金化学分析方法第5部分:硅含量的测定GB/T20975.16—2008铝及铝合金化学分析方法第16部分:镁含量的测定GB/T20975.8—2008铝及铝合金化学分析方法第8部分:锌含量的测定GB/T20975.4—2008铝及铝合金化学分析方法第4部分:铁含量的测定邻二氮杂菲分光光度法GB/T20975.7—2008铝及铝合金化学分析方法第7部分:锰含量的测定高碘酸钾分光光度法GB/T20975.14—2008铝及铝合金化学分析方法第14部分:镍含量的测定GB/T20975.12—2008铝及铝合金化学分析方法第12部分:钛含量的测定GB/T20975.11—2008铝及铝合金化学分析方法第11部分:铅含量的测定火焰原子吸收光谱法GB/T20975.10—2008铝及铝合金化学分析方法第10部分:锡含量的测定GB/T20975.18—2008铝及铝合金化学分析方法第18部分:铬含量的测定GB/T6414—1999铸件尺寸公差和机械加工余量GB/T231.1—2009金属材料布氏硬度试验第1部分:试验方法GB/T1958—2004产品几何量技术规范(GPS)形状和位置公差检测规定GB/T3177—2009产品几何技术规范(GPS)光滑工件尺寸的检验GB/T19055—2003汽车发动机可靠性试验方法GB/T12678—1990汽车可靠性行驶试验方法GB/T8170—2008数值修约规则与极限数值的表示和判定GB/T18851.1—2012无损检测渗透检测第1部分:总则GB/T30512—2014汽车禁用物质要求3术语和定义GB/T5611界定的术语和定义适用于本文件。
铸件毛坯图的要求[管理资料]
![铸件毛坯图的要求[管理资料]](https://img.taocdn.com/s3/m/50c0a4015e0e7cd184254b35eefdc8d376ee14b9.png)
铸件毛坯图的画法(一)毛坯图一般包括以下内容i.毛坯的形状、尺寸公差、加工余量、工艺余量、拔模斜度、铸造圆角、分型面、浇冒口、残根位置、工艺基准、合金牌号、铸件重量、零件标识、铸造方法及其它有关技术要求。
ii.在毛坯图上一般只标注特殊要求的公差,拔模斜度、铸造圆角一般不标注在图上而写在技术条件中。
(二)毛坯图的技术要求i.合金牌号;ii.铸造方法;iii.铸造精度,公差等级;iv.未注明拔模斜度,圆角半径;v.铸件综合技术条件;及检验规则的文件号,vi.铸件的交货状态:a)浇冒口残根的大小。
精铸件及压铸件残根一般为0.3-0.5mm,砂型铸件及硬模铸件一般为0.5-2mm;b)铸件的表面状态(抛丸、涂漆、防锈等);c)铸件是否要进行气压或液压试验,压力要求;d)铸件热处理方法,硬度要求。
(三)毛坯图会签i.会签内容:a)工艺性、加工余量、几何尺寸、公差要求、分模位置、材料硬度、表面处理等b)拔模角、残留毛刺、表面缺陷等c)定位、加紧位置d)工艺凸台ii.会签过程:a)草签机加单位对毛坯制造单位提出的毛坯图进行仔细分析研究,将工艺要求的定位点、加紧点标注在毛坯图上,然后交给毛坯制造单位,毛坯制造单位如果有无法满足要求的项目由双方协同设计单位共同协商解决,可以对产品、机加工艺提出更改,取得一致意见后草签。
b)毛坯图确认毛坯制造单位根据草签的毛坯图进行生产准备,调试毛坯,经检查合格后认为可以满足机加要求,将毛坯件与机加鉴定单一起送交机加单位进行试加。
机加单位进行机械加工及性能试验,确认铸件尺寸精度、缺陷状态满足加工要求及性能要求,没有问题,可以进行毛坯图确认,并最终会签。
(四)毛坯图更改i.毛坯制造单位或机加单位需要对毛坯图进行更改时,需要填写《毛坯更改申请通知单》,经气研、毛坯制造单位、机加单位、总成单位同意并签字后方可更改并换发毛坯图。
ii.毛坯图更改必须注明更改标记、更改数目、更改内容、更改日期、更改根据、更改人员姓名。
工程图常见技术要求

1. 零件去除氧化皮。
2. 零件加工表面上,不应有划痕、擦伤等损伤零件表面的缺陷。
3. 去除毛刺飞边。
热处理要求1. 经调质处理,HRC50~55。
2. 零件进行高频淬火,350~370℃回火,HRC40~45。
3. 渗碳深度。
4. 进行高温时效处理。
公差要求1.未注形状公差应符合GB1184-80的要求,有等级要求H K L,要求依次降低。
2.未注线性和角度尺寸公差应符合GB/T 1804-m(表示中等)f m c v ,要求依次降低。
2. 未注长度尺寸允许偏差±。
3. 铸件公差带对称于毛坯铸件基本尺寸配置。
如图示例,标在标题栏附近或技术要求中。
零件棱角1. 未注圆角半径R5。
2. 未注倒角均为2×45°。
3. 锐角/尖角/锐边倒钝。
装配要求1. 各密封件装配前必须浸透油。
2. 装配滚动轴承允许采用机油加热进行热装,油的温度不得超过100℃。
3. 齿轮装配后,齿面的接触斑点和侧隙应符合GB10095和GB11365的规定。
4. 装配液压系统时允许使用密封填料或密封胶,但应防止进入系统中。
5. 进入装配的零件及部件(包括外购件、外协件),均必须具有检验部门的合格证方能进行装配。
6. 零件在装配前必须清理和清洗干净,不得有毛刺、飞边、氧化皮、锈蚀、切屑、油污、着色剂和灰尘等。
7. 装配前应对零、部件的主要配合尺寸,特别是过盈配合尺寸及相关精度进行复查。
8. 装配过程中零件不允许磕、碰、划伤和锈蚀。
9. 螺钉、螺栓和螺母紧固时,严禁打击或使用不合适的旋具和扳手。
紧固后螺钉槽、螺母和螺钉、螺栓头部不得损坏。
10. 规定拧紧力矩要求的紧固件,必须采用力矩扳手,并按规定的拧紧力矩紧固。
11. 同一零件用多件螺钉(螺栓)紧固时,各螺钉(螺栓)需交叉、对称、逐步、均匀拧紧。
12. 圆锥销装配时应与孔应进行涂色检查,其接触率不应小于配合长度的60%,并应均匀分布。
13. 平键与轴上键槽两侧面应均匀接触,其配合面不得有间隙。
- 1、下载文档前请自行甄别文档内容的完整性,平台不提供额外的编辑、内容补充、找答案等附加服务。
- 2、"仅部分预览"的文档,不可在线预览部分如存在完整性等问题,可反馈申请退款(可完整预览的文档不适用该条件!)。
- 3、如文档侵犯您的权益,请联系客服反馈,我们会尽快为您处理(人工客服工作时间:9:00-18:30)。
毛坯图纸技术要求
毛坯图设计原则:
1、凡是有机加工要求的地方都留有加工余量:压铸件机械加工余量:按GB/T11350规定MA-D级执行;
A. 大端面加工余量为1.2mm;
B. 侧面法蓝面加工余量1.0mm;
C. φ25mm以上内孔单边加工余量为0.75mm;φ25mm以下内孔单边加工余量为0.6mm;
D. 螺纹底孔的大端尺寸为:底孔直径-1.5mm;
E. 定位销铸孔的单边加工余量为0.6mm(大端);
F. 螺纹底孔、铸孔深度按压铸件标准,一般为铸孔直径的2倍;盲孔根据实际情况而定?
2、毛坯图上未注出的加工余量数据按上述原则确定;
3、根据压铸件的工艺特征,在压铸件的推杆位置局部改变图纸尺寸和形状;
4、孔径为最大处尺寸;
5、与机加有关的相关尺寸、定位尺寸以★和方框表示;?
6、定位、夹紧面应平整、不应有拔模斜度,并用定位、夹紧符号表示。
技术要求:
1. 未注明铸造园角R3-4mm
2. 未注明拔模斜度1-2.5°
3. 未注明壁厚3±0.35mm
4. 未注明铸件尺寸公差执行GB6414-86 CT6级
5. 铸件表面允许有擦伤、凹陷、缺肉及网状毛刺等缺陷,但其缺陷程度和数量应该与供需双方同意的
标准相一致;
6. 铸件端面浇口残留高度≤2.5mm,飞边毛刺≤1.0mm,加工定位面及检测点不得有毛刺、缺肉或者凸
起;
7. 气密性要求:加工后产品加压腔用0.5kg气压,60秒中允许泄漏量10cc
附加部分:
一、压铸件尺寸:按GB/T15114有关规定执行;
1、压铸件尺寸公差基本尺寸大于25mm时,按GB 6414规定CT6级执行;
2、压铸件尺寸公差基本尺寸大于16mm,小于25mm的,按GB 6414规定CT5级执行;
3、压铸件尺寸公差基本尺寸大于10mm,小于16mm的,按GB 6414规定CT4级执行;
4、压铸件尺寸公差基本尺寸小于10mm,按GB 6414规定CT3级执行;
5、压铸件形位公差按GB/T15114规定执行;
二、压铸件材料化学成分:按ADC12 JIS H5302 及YL113 GB/T15115有关规定执行;
三、压铸件力学性能:按GB/T15114规定执行;
四、压铸件毛坯重量:由供方从供、需共同认可首批合格压铸件毛坯中,抽取10件称重,取平均值
为压铸件毛坯的公称重量;压铸件毛坯重量公差按GB/T11351规定MT6级执行;
五、压铸件表面质量:按QC/T273规定执行;
六、压铸件内部质量:按GB/T15114规定执行;
1、压铸件若能满足使用要求,则压铸件本质缺陷不作为报废依据;
2、压铸件气密性要求:将压力为25KPa的滤水压缩空气,平缓的送入压铸件中,密封关闭9S后,
测腔内压力,压力降到不低于21KPa为合格;
3、在不影响使用的前提下,允许对铸件进行浸渗处理,浸渗处理后要满足上述气密性要求;
4、压铸毛坯在需方加工后,若气密性不合格则返回供方,允许无
偿做二次浸渗,试验合格后再送需
方使用;
5、供方提供的压铸件毛坯一次性不合格率小于0.5%;
七、压铸件的试验方法及检验规则:按GB/T15114及QC/T273规定执行;
1、其中化学成分和机械性能检验按QC/T273规定一类铸件标准执行,且当需方需要时,供方须向
需方提供检验报告;
2、一般情况下,采用试样检验力学性能;特殊情况下,若需方有要求时,也可以采用压铸件本身
检验;。