冷轧酸洗线工艺
《冷轧酸洗线工艺》课件

02
冷轧酸洗线工艺流程
酸洗前的准备
设备检查
确保酸洗线设备处于良好状态,无故障隐 患。
清洗和Байду номын сангаас处理
去除待酸洗钢板表面的杂质和氧化物,确 保酸洗效果。
《冷轧酸洗线工艺》PPT课件
CONTENTS
• 冷轧酸洗线工艺简介 • 冷轧酸洗线工艺流程 • 冷轧酸洗线工艺设备 • 冷轧酸洗线工艺操作要点 • 冷轧酸洗线工艺的优化与改进
01
冷轧酸洗线工艺简介
冷轧酸洗线工艺的定义
冷轧酸洗线工艺是一种金属加工技术,主要用于生产高质量 的冷轧钢板。它通过酸洗去除金属表面的氧化物和杂质,以 提高钢板的表面质量和性能。
致酸洗液分解和设备腐蚀。
01
酸洗浓度
02 适当提高酸洗液的浓度可以提高
酸洗效果,但浓度过高会增加生
产成本和环境污染。
酸洗时间
延长酸洗时间可以提高酸洗效果
,但时间过长会导致金属过度腐
03
蚀和设备损坏。
酸洗液流速
04 合理控制酸洗液流速可以提高酸
洗效果,同时还能减少金属杂质
在设备中的沉积。
谢谢您的聆听
。
04
冷轧酸洗线工艺操作要点
酸洗液的配制与调整
总结词
酸洗液的配制与调整是冷轧酸洗线工艺 中的重要环节,直接影响到酸洗效果和 产品质量。
VS
详细描述
在配制酸洗液时,需要选择合适的酸种类 和浓度,并根据实际情况调整酸洗液的成 分比例。同时,需要定期检测酸洗液的浓 度和酸度,确保其处于最佳状态。
冷轧酸洗工艺流程
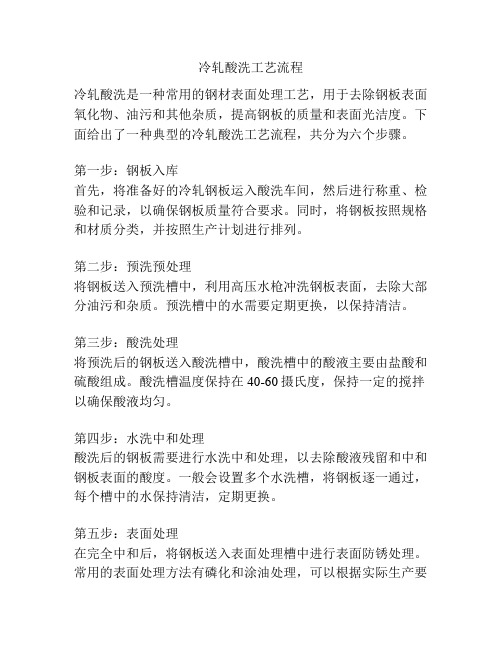
冷轧酸洗工艺流程
冷轧酸洗是一种常用的钢材表面处理工艺,用于去除钢板表面氧化物、油污和其他杂质,提高钢板的质量和表面光洁度。
下面给出了一种典型的冷轧酸洗工艺流程,共分为六个步骤。
第一步:钢板入库
首先,将准备好的冷轧钢板运入酸洗车间,然后进行称重、检验和记录,以确保钢板质量符合要求。
同时,将钢板按照规格和材质分类,并按照生产计划进行排列。
第二步:预洗预处理
将钢板送入预洗槽中,利用高压水枪冲洗钢板表面,去除大部分油污和杂质。
预洗槽中的水需要定期更换,以保持清洁。
第三步:酸洗处理
将预洗后的钢板送入酸洗槽中,酸洗槽中的酸液主要由盐酸和硫酸组成。
酸洗槽温度保持在40-60摄氏度,保持一定的搅拌以确保酸液均匀。
第四步:水洗中和处理
酸洗后的钢板需要进行水洗中和处理,以去除酸液残留和中和钢板表面的酸度。
一般会设置多个水洗槽,将钢板逐一通过,每个槽中的水保持清洁,定期更换。
第五步:表面处理
在完全中和后,将钢板送入表面处理槽中进行表面防锈处理。
常用的表面处理方法有磷化和涂油处理,可以根据实际生产要
求进行选择。
第六步:烘干和质检
表面处理完毕后,将钢板送入烘干炉中进行烘干处理,以去除钢板表面的水分。
烘干完毕后,对钢板进行质量检查,检查项包括表面光洁度、镀锌涂层质量等。
同时进行记录和统计,为下一道工序做准备。
以上就是一种典型的冷轧酸洗工艺流程。
需要注意的是,在整个工艺流程中,需要严格控制各个参数,如温度、浓度、时间等。
同时,还要加强安全防护和环保措施,确保工艺的稳定性和钢板的质量。
冷轧不锈钢的退火及酸洗工艺

冷轧不锈钢的退火及酸洗工艺不锈钢热轧带钢经热带退火酸洗后,为了达到一定的性能及厚度要求,需进行常温轧制处理,即冷轧。
不锈钢冷轧时发生加工硬化,冷轧量越大,加工硬化的程度也越大,若将加工硬化的材料加热到200—400℃就能够排除变形应力,进一步提升温度则发生再结晶,使材料软化。
冷轧后的退火按退火方式分为连续卧式退火和立式光亮退火;按退火工序分为中间退火和最终退火。
顾名思义,中间退火是指中间轧制后的退火,而最终退火是指最终轧制后的退火,两者在工艺操纵和退火目的上无全然区别,因此下文统称为冷轧退火或者退火。
连续卧式退火(连退炉)连退炉是目前广为使用的退火设备,广泛用于带钢的热处理,其特点是带钢在炉内呈水平状态,边加热边前进。
炉子的结构一样要紧由预热段、加热段和冷却段组成。
卧式退火炉通常与开卷机、焊机、酸洗线等组成一条连续退火酸洗机组。
冷轧退火对不锈钢成品材料的机械性能有专门大阻碍,如晶粒度、抗拉强度、硬度、延伸率和粗糙度等。
其中退火温度和退火时刻对冷轧材料再结晶后的晶粒度具有最直截了当的阻碍。
10 晶粒度(ASTM)5 0 2 46 8 退火时刻(分)图1.SUS304带钢1100℃时退火时刻与晶粒度关系示意图如前所述,连退炉一样由预热、加热、冷却三大部分组成。
预热段没有烧嘴燃烧,而是利用后面加热段的辐射热来加热带钢,如此能够有效的利用热能,节约能源成本。
加热段利用燃料燃烧直截了当对带钢进行加热,该段一样分为若干各区,每个区都有高温计来操纵和显示温度。
燃烧后高达700多度的废气被废气风机抽出加热室后进入换热器,在换热器内将冷的燃烧空气进行加热(可加热到400多度),加热后的燃烧空气直截了当被送到各个烧嘴。
换热器的目的在于有效回收废气热量。
炉内燃烧条件的治理。
燃料(液化石油气或天然气)在炉内的燃烧状况对质量、成本、热效率等都有专门大阻碍。
空燃比是燃烧治理的一个重要指标。
空燃比越高,燃烧越充分,然而排废量也相应增加,炉内氧含量提升,增加了带钢的氧化程度。
冷轧酸洗线工艺介绍

本文摘自再生资源回收-变宝网()
冷轧酸洗线工艺介绍
变宝网11月14日讯
冷轧酸洗是用化学方法出去金属表面氧化铁皮的过程,通常采用盐酸,因此也叫化学洗酸。
此项工艺对金属行业来说尤为重要。
下面简单介绍一下冷轧酸洗线工艺。
目的:去除热轧带钢表面的氧化铁皮(铁锈)
轧制时会将氧化铁皮压入带钢基体,影响冷轧板表面质量及加工性能。
氧化铁皮破碎后进入冷却润滑的乳化液系统,损坏设备并虽短乳化液使用寿命。
损坏轧辊。
酸洗概述—除磷(氧化铁皮)方法
机械除磷:砂轮研磨、弯曲破磷、喷丸破磷
化学除磷:有酸除磷、无酸除磷、碱洗除磷、电解除磷
机械—化学联合除磷
弯曲—酸洗、喷丸破磷—酸洗、拉矫—酸洗
酸洗种类:盐酸酸洗、硫酸酸洗、硝酸酸洗、磷酸酸洗、氢氟酸酸洗、混合酸酸洗
酸洗机组
按带钢酸洗的过程分类可分为连续卧式酸洗机组、连续塔式酸洗机组和半连续酸洗机组。
连续酸洗机组的工艺特点是钢卷逐卷展开后,钢卷与钢卷之间头尾焊接起来连续地通过酸洗槽。
推拉式酸洗机组酸洗,每根带钢经夹送辊一次咬入,不用焊接,推送向前,直至卷取,逐卷带钢间断地通过酸洗机组。
更多冷轧酸洗资讯关注变宝网查阅。
本文摘自变宝网-废金属_废塑料_废纸_废品回收_再生资源B2B交易平台网站;
变宝网官网网址:/newsDetail373225.html
网上找客户,就上变宝网!免费会员注册,免费发布需求,让属于你的客户主动找你!。
冷轧生产线酸洗工艺
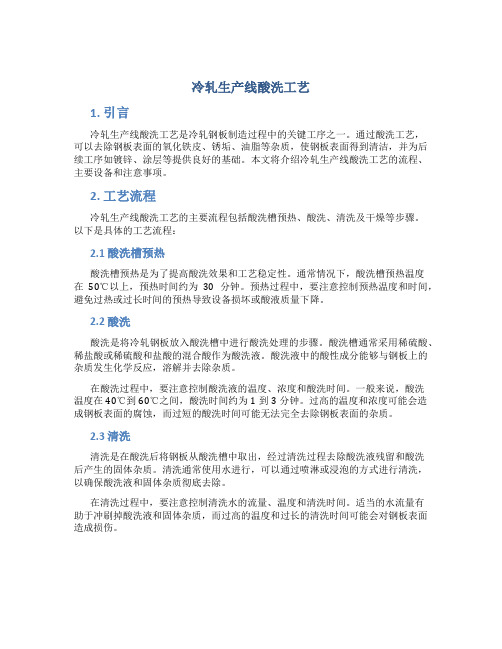
冷轧生产线酸洗工艺1. 引言冷轧生产线酸洗工艺是冷轧钢板制造过程中的关键工序之一。
通过酸洗工艺,可以去除钢板表面的氧化铁皮、锈垢、油脂等杂质,使钢板表面得到清洁,并为后续工序如镀锌、涂层等提供良好的基础。
本文将介绍冷轧生产线酸洗工艺的流程、主要设备和注意事项。
2. 工艺流程冷轧生产线酸洗工艺的主要流程包括酸洗槽预热、酸洗、清洗及干燥等步骤。
以下是具体的工艺流程:2.1 酸洗槽预热酸洗槽预热是为了提高酸洗效果和工艺稳定性。
通常情况下,酸洗槽预热温度在50℃以上,预热时间约为30分钟。
预热过程中,要注意控制预热温度和时间,避免过热或过长时间的预热导致设备损坏或酸液质量下降。
2.2 酸洗酸洗是将冷轧钢板放入酸洗槽中进行酸洗处理的步骤。
酸洗槽通常采用稀硫酸、稀盐酸或稀硫酸和盐酸的混合酸作为酸洗液。
酸洗液中的酸性成分能够与钢板上的杂质发生化学反应,溶解并去除杂质。
在酸洗过程中,要注意控制酸洗液的温度、浓度和酸洗时间。
一般来说,酸洗温度在40℃到60℃之间,酸洗时间约为1到3分钟。
过高的温度和浓度可能会造成钢板表面的腐蚀,而过短的酸洗时间可能无法完全去除钢板表面的杂质。
2.3 清洗清洗是在酸洗后将钢板从酸洗槽中取出,经过清洗过程去除酸洗液残留和酸洗后产生的固体杂质。
清洗通常使用水进行,可以通过喷淋或浸泡的方式进行清洗,以确保酸洗液和固体杂质彻底去除。
在清洗过程中,要注意控制清洗水的流量、温度和清洗时间。
适当的水流量有助于冲刷掉酸洗液和固体杂质,而过高的温度和过长的清洗时间可能会对钢板表面造成损伤。
2.4 干燥干燥是将清洗后的钢板进行烘干的步骤,以防止钢板表面的水分引起锈蚀。
通常采用热风或热轧过程中的余热进行干燥。
干燥温度和时间要根据钢板厚度和材质的不同进行调整,以确保钢板表面干燥均匀。
3. 主要设备冷轧生产线酸洗工艺中的主要设备包括酸洗槽、清洗设备和干燥设备。
以下是这些设备的主要功能:3.1 酸洗槽酸洗槽可以用于储存和加热酸洗液,起到预热和酸洗钢板的作用。
酸洗和冷轧工艺

酸洗线教程1 酸洗车间的作用我厂一期的建设共分四条线:酸洗。
冷轧、镀锌和彩涂。
热轧板卷(0.8-4.0,580-1680mm)140万吨60万吨65万吨15万吨酸洗商品卷30冷轧商品卷镀锌商品卷连续彩涂线彩涂商品卷从上图可以看出冷轧厂所有的商品板卷首先都要进行酸洗处理,酸洗生产线即是酸洗商品卷的最后一道工序,又是其他生产线的第一道工序。
2 酸洗机组的技术进步和常见的酸洗形式2.1 酸洗机组的技术进步2.1.1湍流式酸洗60年代以前冷轧原料的除鳞主要是用硫酸酸洗。
这种方法废酸不能完全回收,钢的损耗也较大。
1959年奥地利鲁特纳发明了盐酸酸洗废液再生方法,盐酸可以完全回收,产生的铁粉也可做高档的磁性材料,这样盐酸酸洗法成为成本低、酸洗带钢表面质量好的工艺而得到普遍发展。
这时酸洗槽由深槽逐步发展为浅槽。
1983年原西德MDS公司开发出湍流式酸洗新技术。
其特点是将酸洗液送入很窄的酸洗室槽缝中,使酸洗液在带钢表面上形成湍流状态。
这种工艺已不存在深槽的概念,带钢在一条很窄的沟槽中运行并处于张力状态,酸的流动方向与带钢的运行方向相反。
这种酸洗技术提高了酸洗效率,改善了酸洗质量。
同样的酸液温度及带钢条件,湍流式机组的功能与传统的深槽、浅槽机组3种传统酸洗方式的比较见表1-14。
自从80年代推出湍流酸洗以来,浅槽湍流酸洗机组因其造价低、酸洗事故处理时间短而很快发展起来。
原西德波鸿、澳大利亚BHP、日本住友金属、日本和歌山、日本神钢加古川冷轧厂、比利时西格马公司等于1986-1990年先后建成并投产了湍流酸洗机组。
这种机组的年产量从60万t发展到最大达250万t。
2.1.2机械除鳞法工序的边疆化导致复合除鳞技术的发展。
在传统的化学酸洗的基础上增加了机械方式除鳞。
机械除鳞法有:反复弯曲法、轧制法、喷丸法、NID法及APO法等。
NID法(用高压水喷铁砂浆的除鳞法)是1973年日本石川岛播磨公司开发的,其原理是将铁砂送入高压水流,通过扁缝式喷嘴,形成铁砂流布满钢带的横向表面。
酸洗原理及工艺

?
?
?
ARP
到此告一段落!
由于准备得较仓促,讲 得比较粗浅,敬请原谅。
谢谢大家的关注,并请批
评指正。
酸槽是钢板衬橡胶并内砌耐酸砖的结构。对于耐酸砖衬,在与
酸液直接接触的部分,是两层耐酸砖 (2×65mm) 配合灰浆(共厚 150mm) 砌成。其余部分是一层耐酸砖 (70mm) 砌成。
两层耐酸砖结构的优点在于提高了酸洗线安全运行的系数,也
就是说缩短了事故停机的时间,减少了相应的产量损失。
槽盖为分段式,每个酸槽有 4个槽盖,液压动力开闭。分段式
的要求。而超浅槽紊流酸洗的优势就是体现在这些参数
需要变更的时候。
紊流度
板带运行速度
不需任何额外的介质
由于超浅槽紊流酸洗工艺高效的控制能力, SMS
Demag 的酸洗工艺不需添加任何额外的介质,如增强 剂、抑制剂等。
有些酸洗工艺需要这些添加剂,无疑是增加了酸
洗的成本。
紊流度
板带运行速度
超浅槽酸洗其他优势
因此,板带的高速通过,再加上喷排和侧喷口
的作用,就更容易引起酸液产生较强的紊流效果。
而对喷酸压力和流量的调整,就会很容易地控制紊 流的强弱。 SMS Demag 的酸洗工艺中喷酸的压力可
达 2.5~3bar ,约是其竞争对手压力的 10倍。高的喷酸 压力保证了紊流度的最大值和较大的调整范围。
酸洗中紊流的必要性
先选取一个静态的酸
洗环境,大家就会看到如 右图的一个反应分层。
当板带运动起来时,
如果没有大的紊流效果, 由于分子间作用力的影响, 反应层和临界层只是变薄, 而不能消除。
要提高酸洗效率,就 要将这个反应的分层破坏
掉,使新酸尽可能多地接
冷轧酸洗工艺流程 (1)
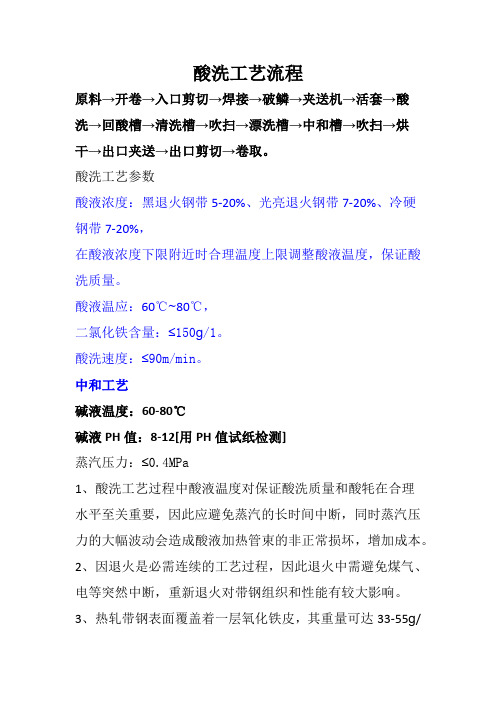
酸洗工艺流程原料→开卷→入口剪切→焊接→破鳞→夹送机→活套→酸洗→回酸槽→清洗槽→吹扫→漂洗槽→中和槽→吹扫→烘干→出口夹送→出口剪切→卷取。
酸洗工艺参数酸液浓度:黑退火钢带5-20%、光亮退火钢带7-20%、冷硬钢带7-20%,在酸液浓度下限附近时合理温度上限调整酸液温度,保证酸洗质量。
酸液温应:60℃~80℃,二氯化铁含量:≤150ɡ/1。
酸洗速度:≤90m/min。
中和工艺碱液温度:60-80℃碱液PH值:8-12[用PH值试纸检测]蒸汽压力:≤0.4MPa1、酸洗工艺过程中酸液温度对保证酸洗质量和酸牦在合理水平至关重要,因此应避免蒸汽的长时间中断,同时蒸汽压力的大幅波动会造成酸液加热管束的非正常损坏,增加成本。
2、因退火是必需连续的工艺过程,因此退火中需避免煤气、电等突然中断,重新退火对带钢组织和性能有较大影响。
3、热轧带钢表面覆盖着一层氧化铁皮,其重量可达33-55ɡ/㎡,厚度为7.5~15um,甚至可达20um,现代化热连轧机生产的带钢,其表面氧化铁皮厚度也约为10um。
4、为孓保证成口带钢的表面质量,降低力能消牦,减少轧辊磨损和有利带钢深加工,因此钢带冷轧前必须将氧化铁皮处除掉。
5、我们利用氧化铁皮与酸发生化学反应的基本原理,将钢带浸泡在一定浓度和温度的酸液中,并使钢带与酸液相对运动,加速化学反应速度,从而达到清除氧化铁皮的目的。
酸再生工艺流程:废酸收集→废酸过滤→废酸预浓缩→培烧再生→再生酸收集酸再生是将废酸液定量的送往酸再生装置再生成游离酸返回酸洗机组,同时得到氧化铁粉的一个体系。
酸再生过程是一个化学过程,浓缩废酸通过啧抢以雾状喷入焙烧炉内,焙烧炉通过两个喷嘴进行操作,操作期间煤气和空气流量自动控制,流量由孔板和差压传感器测量并在显示屏上显示。
煤气流量:200~300m /h,煤气压力:0.01mpa轧制工艺流程酸洗卷上卷→开卷→矫头→切头→焊接→活套入口夹送→充套→活套出口夹送→连轧(三机架或五机架)→测厚→卷取→分卷剪切→打包→卸卷→吊运技术参数工作辊直径:168mm~175mm(175-550-1388mm)中间辊直径:185mm~190mm(190-520-1244mm)外部支承辊直径:550mm(550-520-1576mm)轧辊辊面宽度:520mm轧制压力:550t~700t设计速度每秒:6米轧制:带钢不经加热而在室温下进行的轧制变形,我们称之为冷轧。
冷轧酸洗工艺流程-(1)资料
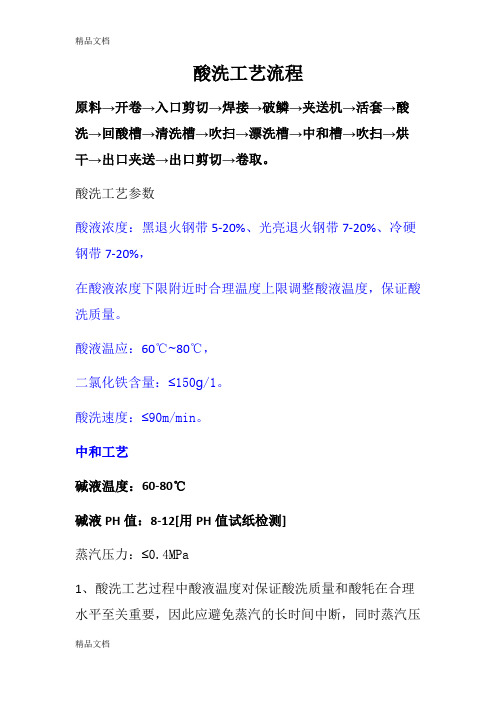
酸洗工艺流程原料→开卷→入口剪切→焊接→破鳞→夹送机→活套→酸洗→回酸槽→清洗槽→吹扫→漂洗槽→中和槽→吹扫→烘干→出口夹送→出口剪切→卷取。
酸洗工艺参数酸液浓度:黑退火钢带5-20%、光亮退火钢带7-20%、冷硬钢带7-20%,在酸液浓度下限附近时合理温度上限调整酸液温度,保证酸洗质量。
酸液温应:60℃~80℃,二氯化铁含量:≤150ɡ/1。
酸洗速度:≤90m/min。
中和工艺碱液温度:60-80℃碱液PH值:8-12[用PH值试纸检测]蒸汽压力:≤0.4MPa1、酸洗工艺过程中酸液温度对保证酸洗质量和酸牦在合理水平至关重要,因此应避免蒸汽的长时间中断,同时蒸汽压力的大幅波动会造成酸液加热管束的非正常损坏,增加成本。
2、因退火是必需连续的工艺过程,因此退火中需避免煤气、电等突然中断,重新退火对带钢组织和性能有较大影响。
3、热轧带钢表面覆盖着一层氧化铁皮,其重量可达33-55ɡ/㎡,厚度为7.5~15um,甚至可达20um,现代化热连轧机生产的带钢,其表面氧化铁皮厚度也约为10um。
4、为孓保证成口带钢的表面质量,降低力能消牦,减少轧辊磨损和有利带钢深加工,因此钢带冷轧前必须将氧化铁皮处除掉。
5、我们利用氧化铁皮与酸发生化学反应的基本原理,将钢带浸泡在一定浓度和温度的酸液中,并使钢带与酸液相对运动,加速化学反应速度,从而达到清除氧化铁皮的目的。
酸再生工艺流程:废酸收集→废酸过滤→废酸预浓缩→培烧再生→再生酸收集酸再生是将废酸液定量的送往酸再生装置再生成游离酸返回酸洗机组,同时得到氧化铁粉的一个体系。
酸再生过程是一个化学过程,浓缩废酸通过啧抢以雾状喷入焙烧炉内,焙烧炉通过两个喷嘴进行操作,操作期间煤气和空气流量自动控制,流量由孔板和差压传感器测量并在显示屏上显示。
煤气流量:200~300m /h,煤气压力:0.01mpa轧制工艺流程酸洗卷上卷→开卷→矫头→切头→焊接→活套入口夹送→充套→活套出口夹送→连轧(三机架或五机架)→测厚→卷取→分卷剪切→打包→卸卷→吊运技术参数工作辊直径:168mm~175mm(175-550-1388mm)中间辊直径:185mm~190mm(190-520-1244mm)外部支承辊直径:550mm(550-520-1576mm)轧辊辊面宽度:520mm轧制压力:550t~700t设计速度每秒:6米轧制:带钢不经加热而在室温下进行的轧制变形,我们称之为冷轧。
冷轧线酸洗工艺

冷轧线酸洗工艺1. 引言冷轧线酸洗工艺是冷轧钢板生产中的一个重要工艺环节。
通过酸洗工艺可以去除钢板表面的铁氧化物、锈蚀、尺寸偏差等缺陷,提高钢板的表面质量和尺寸精度。
本文将介绍冷轧线酸洗工艺的原理、流程以及常见的酸洗剂和设备。
2. 酸洗工艺原理在冷轧线酸洗工艺中,酸洗液主要起到去除表面缺陷和清洁钢板的作用。
酸洗液通常由一种或几种酸性溶液组成,如硫酸、盐酸、硝酸等。
这些酸洗剂可以与钢板表面的氧化物和锈蚀发生化学反应,使其溶解或转化为易于清洁的物质。
酸洗液还可以降低钢板表面的粗糙度,提高表面质量。
3. 酸洗工艺流程冷轧线酸洗工艺一般包括以下几个步骤:3.1 准备工作在进行酸洗之前,需要对待处理的钢板进行准备工作。
首先,需要检查钢板表面是否有明显的氧化物和锈蚀,如果发现有,则需要进行预处理,如机械除锈或喷砂处理。
其次,需要对酸洗设备进行检查和维护,确保其正常运行。
3.2 油脂去除将待处理的钢板放入去油槽中,使用油脂去除剂进行清洗。
油脂去除剂可以将钢板表面的油污和涂层去除,以减少酸洗液的消耗和污染。
3.3 酸洗将经过油脂去除处理的钢板放入酸洗槽中,浸泡一定时间,使酸洗液与钢板表面的铁氧化物和锈蚀发生反应。
酸洗时间一般根据钢板的厚度和表面质量要求进行调整。
3.4 清洗酸洗后的钢板需经过清洗工艺,以去除表面的酸洗液残留。
常用的清洗方法包括水清洗和碱洗。
水清洗可以将酸洗液冲洗掉,碱洗可以中和酸洗液的酸性残留。
3.5 防锈处理为防止酸洗后的钢板再次氧化和锈蚀,需要对其进行防锈处理。
常见的方法包括喷涂防锈液和烘干。
4. 常见的酸洗剂和设备4.1 酸洗剂•硫酸:具有强酸性和去除氧化物的能力,适用于处理高碳钢和不锈钢。
•盐酸:对于低碳钢和冷轧钢板,盐酸是一种常用的酸洗剂。
•硝酸:对于高碳钢和合金钢的酸洗具有较好的效果。
4.2 设备•酸洗槽:由耐酸材料制成的槽体,用于盛放酸洗液和钢板。
•喷淋装置:用于将酸洗液均匀地喷洒到钢板表面,以加速化学反应的进行。
冷轧酸洗工艺流程-完整

酸洗工艺流程原料→开卷→入口剪切→焊接→破鳞→夹送机→活套→酸洗→回酸槽→清洗槽→吹扫→漂洗槽→中和槽→吹扫→烘干→出口夹送→出口剪切→卷取。
酸洗工艺参数酸液浓度:黑退火钢带5-20%、光亮退火钢带7-20%、冷硬钢带7-20%,在酸液浓度下限附近时合理温度上限调整酸液温度,保证酸洗质量。
酸液温应:60℃~80℃,二氯化铁含量:≤150ɡ/1。
酸洗速度:≤90m/min。
中和工艺碱液温度:60-80℃碱液PH值:8-12[用PH值试纸检测]蒸汽压力:≤0.4MPa1、酸洗工艺过程中酸液温度对保证酸洗质量和酸牦在合理水平至关重要,因此应避免蒸汽的长时间中断,同时蒸汽压力的大幅波动会造成酸液加热管束的非正常损坏,增加成本。
2、因退火是必需连续的工艺过程,因此退火中需避免煤气、电等突然中断,重新退火对带钢组织和性能有较大影响。
3、热轧带钢表面覆盖着一层氧化铁皮,其重量可达33-55ɡ/㎡,厚度为7.5~15um,甚至可达20um,现代化热连轧机生产的带钢,其表面氧化铁皮厚度也约为10um。
4、为孓保证成口带钢的表面质量,降低力能消牦,减少轧辊磨损和有利带钢深加工,因此钢带冷轧前必须将氧化铁皮处除掉。
5、我们利用氧化铁皮与酸发生化学反应的基本原理,将钢带浸泡在一定浓度和温度的酸液中,并使钢带与酸液相对运动,加速化学反应速度,从而达到清除氧化铁皮的目的。
酸再生工艺流程:废酸收集→废酸过滤→废酸预浓缩→培烧再生→再生酸收集酸再生是将废酸液定量的送往酸再生装置再生成游离酸返回酸洗机组,同时得到氧化铁粉的一个体系。
酸再生过程是一个化学过程,浓缩废酸通过啧抢以雾状喷入焙烧炉内,焙烧炉通过两个喷嘴进行操作,操作期间煤气和空气流量自动控制,流量由孔板和差压传感器测量并在显示屏上显示。
煤气流量:200~300m/h,煤气压力:0.01mpa轧制工艺流程酸洗卷上卷→开卷→矫头→切头→焊接→活套入口夹送→充套→活套出口夹送→连轧(三机架或五机架)→测厚→卷取→分卷剪切→打包→卸卷→吊运技术参数工作辊直径:168mm~175mm(175-550-1388mm)中间辊直径:185mm~190mm(190-520-1244mm)外部支承辊直径:550mm(550-520-1576mm)轧辊辊面宽度:520mm轧制压力:550t~700t设计速度每秒:6米轧制:带钢不经加热而在室温下进行的轧制变形,我们称之为冷轧。
冷轧生产线酸洗工艺
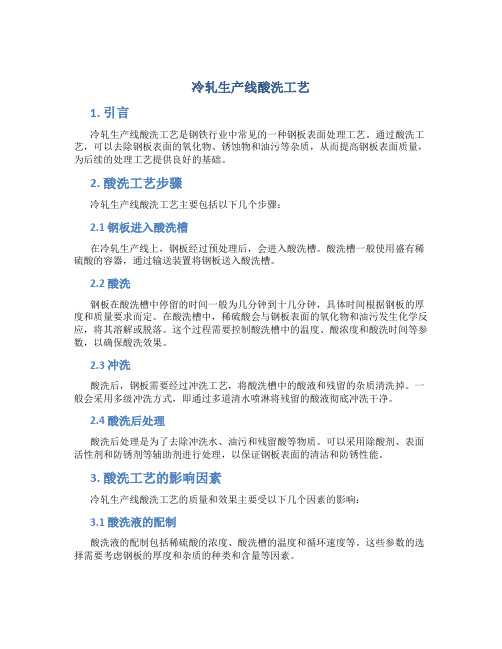
冷轧生产线酸洗工艺1. 引言冷轧生产线酸洗工艺是钢铁行业中常见的一种钢板表面处理工艺。
通过酸洗工艺,可以去除钢板表面的氧化物、锈蚀物和油污等杂质,从而提高钢板表面质量,为后续的处理工艺提供良好的基础。
2. 酸洗工艺步骤冷轧生产线酸洗工艺主要包括以下几个步骤:2.1 钢板进入酸洗槽在冷轧生产线上,钢板经过预处理后,会进入酸洗槽。
酸洗槽一般使用盛有稀硫酸的容器,通过输送装置将钢板送入酸洗槽。
2.2 酸洗钢板在酸洗槽中停留的时间一般为几分钟到十几分钟,具体时间根据钢板的厚度和质量要求而定。
在酸洗槽中,稀硫酸会与钢板表面的氧化物和油污发生化学反应,将其溶解或脱落。
这个过程需要控制酸洗槽中的温度、酸浓度和酸洗时间等参数,以确保酸洗效果。
2.3 冲洗酸洗后,钢板需要经过冲洗工艺,将酸洗槽中的酸液和残留的杂质清洗掉。
一般会采用多级冲洗方式,即通过多道清水喷淋将残留的酸液彻底冲洗干净。
2.4 酸洗后处理酸洗后处理是为了去除冲洗水、油污和残留酸等物质。
可以采用除酸剂、表面活性剂和防锈剂等辅助剂进行处理,以保证钢板表面的清洁和防锈性能。
3. 酸洗工艺的影响因素冷轧生产线酸洗工艺的质量和效果主要受以下几个因素的影响:3.1 酸洗液的配制酸洗液的配制包括稀硫酸的浓度、酸洗槽的温度和循环速度等。
这些参数的选择需要考虑钢板的厚度和杂质的种类和含量等因素。
3.2 酸洗时间酸洗时间是指钢板在酸洗槽中停留的时间。
时间过短会导致酸洗效果不好,时间过长则浪费资源。
因此,酸洗时间的控制非常关键。
3.3 温度控制酸洗槽中的温度对酸洗效果有重要影响。
一般情况下,较高的温度可以加快化学反应速率,但过高的温度可能会导致钢板表面脱碳,影响钢板的性能。
3.4 冲洗水质量冲洗水的质量对去除酸液和杂质有很大影响。
如果冲洗水质量不好,可能会带来新的污染问题。
因此,冲洗水的净化和循环利用非常重要。
4. 酸洗工艺的优缺点冷轧生产线酸洗工艺具有如下优点:•能够有效去除钢板表面的氧化物、锈蚀物和油污等杂质;•提高钢板表面质量,使其更适合后续加工工艺;•可以改善钢板的防锈性能。
冷轧机 退火酸洗工艺流程

冷轧机退火酸洗工艺流程英文回答:Cold rolling is a process used to reduce the thickness and improve the surface finish of steel or other metal sheets. After the cold rolling process, the material may undergo an annealing and pickling process to furtherimprove its properties. This process is known as annealing and pickling, or acid pickling.The annealing process involves heating the material toa specific temperature and then slowly cooling it down.This helps to relieve the internal stresses and improve the material's ductility. Annealing can be done in various ways, such as batch annealing or continuous annealing. In batch annealing, the material is placed in a furnace and heatedto the desired temperature. It is then allowed to cool down slowly in the furnace. Continuous annealing, on the other hand, involves passing the material through a series of heated chambers, where it is heated and cooled down in acontrolled manner.After annealing, the material is pickled to remove any scale or impurities on the surface. Pickling is typically done by immersing the material in an acid bath, such as hydrochloric acid or sulfuric acid. The acid reacts withthe scale and impurities, dissolving them and leavingbehind a clean surface. The pickling process also helps to improve the material's corrosion resistance.Once the material has been pickled, it is rinsed with water to remove any remaining acid. It is then dried andcan be further processed or used as is.中文回答:冷轧是一种用于减小钢材或其他金属板材厚度并改善表面光洁度的工艺。
山钢日照冷轧推拉式酸洗线工艺及设备特点简述
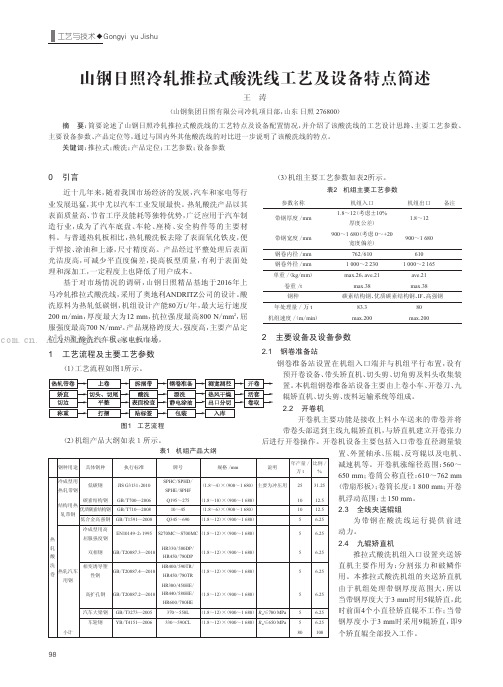
5
6.25
减速机等。 开卷机涨缩径范围:560~ 650 mm;卷筒公称直径:610~762 mm (带扇形板);卷筒长度:1 800 mm;开卷 机浮动范围:±150 mm。 2.3 全线夹送辊组
为带钢在酸洗线运行提供前进
冷成型用高
EN10149-2:1995 S270MC~S700MC (1.8~12)×(900~1 680)
牌号
规格 /mm
说明
年产量 / 比例 /
万t
%
SPHC/SPHD/ (1.8~4)×(900~1 680) 主要为冲压用 25
SPHE/SPHF
31.25
Q195~275 (1.8~10)×(900~1 680)
10
12.5
10~45
(1.8~6)×(900~1 680)
10
12.5
Q345~690 (1.8~12)×(900~1 680)
热
屈服强度钢
轧
HR330/580DP/
双相钢 GB/T20887.3—2010
(1.8~12)×(900~1 680)
酸
HR450/780DP
5
6.25
动力。
2.4 九辊矫直机
5
6.25
推拉式酸洗机组入口设置夹送矫
洗
相变诱导塑
卷 热轧汽车
性钢Байду номын сангаас
GB/T20887.4—2010
用钢
高扩孔钢 GB/T20887.2—2010
HR400/590TR/ (1.8~12)×(900~1 680)
HR450/780TR HR300/450HE/ HR440/580HE/ (1.8~12)×(900~1 680) HR600/780HE
冷轧生产线酸洗工艺

紊流酸洗
引言
• 热轧带钢的表面铁鳞与酸液的化学反应速度受多方面因 素的影响,如酸液的浓度和温度、钢板表面温度等,不 可能无限制的提高。但另一方面,在实用的范围内,通 过提高酸洗速度,达到促进扩散,使钢板表面温度迅速 达到酸液的温度,这样就必须加快钢板表面的物质传递, 即酸和化学反应物的扩散,改善传导率。其方法就是使 酸液在带钢表面形成高速紊流,促进物质传递,达到使 钢板表面急速升温的目的,从而大大缩短酸洗时间。
浅槽酸洗
70年代中期。酸液深400~1000mm。
浅槽紊流酸洗
70年代末期,1983年德国MDS公司开发了紊流酸洗。酸液深小于 400mm 。
酸洗概述—三种酸洗技术的比较
参数比较 酸洗时间*,% 酸雾量*,% 电耗量*,% 热传递*,% 槽内带钢提升器 槽内带钢位置控制
深槽
浅槽
紊流
100
80
65
100
影响酸洗的因素
其它
• 最后应当指出的是,一些含碳量较高强度较大的中、 高碳钢,为了便于轧制,在酸洗之前都要进行退火 处理(初退火)。这些经过初退火的带钢,长时间 (大约24小时)在高温(约780℃)下加热,使得钢板
表面的氧化膜加厚,加之钢中的硅、铬等元素的原子在高 温下较多地从钢板内部向外扩散并与钢板表面的氧原子结 成难溶的氧化物,从而增加了酸洗的困难。为了除去这些 初退火后带钢表面生成的氧化铁皮,就必须增加酸的浓度、 延长酸洗时间或采用混合酸酸洗(如硫酸、酸洗时加入食 盐,形成硫酸和盐酸的混合酸)。
影响酸洗的因素
机械拉矫影响
• 带钢经拉伸矫直机反复弯曲变形后,由于氧化 铁皮与基铁的塑性不同,氧化铁皮将会不同程 度地从带钢表面上剥落下来或产生裂缝,因此, 破鳞将能明显地增加酸洗速度。实验指出,用 硫酸酸洗时,采用破鳞机可减少10%~50%的 酸洗时间。
- 1、下载文档前请自行甄别文档内容的完整性,平台不提供额外的编辑、内容补充、找答案等附加服务。
- 2、"仅部分预览"的文档,不可在线预览部分如存在完整性等问题,可反馈申请退款(可完整预览的文档不适用该条件!)。
- 3、如文档侵犯您的权益,请联系客服反馈,我们会尽快为您处理(人工客服工作时间:9:00-18:30)。
目录
1、酸洗理论基础
(1)酸洗概述 (2)酸洗原理 (3)影响酸洗的因素 (4)紊流酸洗 (5)酸洗后序处理—漂洗工艺 (6)酸洗引起的带钢缺陷
2、首钢1850mm酸洗工艺设计
(1)1850mm工艺流程 (2)1850mm化学工艺段设计描述 (3)1850mm酸洗模型
酸洗概述—酸洗定义
酸洗原理—带钢氧化铁皮组织结构
酸洗原理—带钢氧化铁皮组织结构 氧化铁Fe2O3 磁性体Fe3O4 富氏体FeO 带钢基体
红色氧化皮表面,生成温度570~1100℃
酸洗原理—带钢氧化铁皮组织结构 氧化铁Fe2O3
磁性体Fe3O4
带钢基体
红色氧化皮表面,生成温度570~1100℃, 但从570℃开始缓冷
酸洗后带钢表面残留物 **,mg/m2带钢
300~200
150
பைடு நூலகம்
≤50
酸洗概述—酸洗机组
• 按带钢酸洗的过程分类可分为连续卧式酸 洗机组、连续塔式酸洗机组和半连续式酸 洗机组(它也称推拉式或推式)。
酸洗概述—酸洗机组的比较:连续酸洗机组
• 连续式酸洗机组的工艺特点是钢卷逐卷展开后, 钢卷与钢卷之间头尾焊接起来连续地通过酸洗槽。
酸洗原理—氧化铁皮的形成
结论:带钢表面的氧化铁皮是热轧带钢在 终轧后、卷曲时及冷却时产生的。
酸洗原理—氧化铁皮的形成
在从精轧末机架出来的带钢表面上,铁原 子首先与空气中的氧原子结合形成第一层 氧化物,这层氧化物可能是致密的Fe3O4, 或者是疏松的FeO。在第一种情况下,氧化 铁皮的进一步增长过程可能只靠氧和铁的 离子扩散来进行的;在第二种情况下,空 气中的氧可自由地通过多孔、疏松的氧化 铁皮,而使氧化铁皮加厚和致密化。无论 上述哪种情况,最终结果就是形成了我们 通常所看到的带钢表面的氧化铁皮。
酸洗是用化学方法除去金属表面氧化铁皮的 过程,通常采用盐酸(HCl),因此也叫化 学酸洗。
酸洗概述—酸洗目的
目的:去除热轧带钢表面的氧化铁皮(铁锈)
• 轧制时会将氧化铁皮压入带钢基体,影响 冷轧板表面质量及加工性能。 • 氧化铁皮破碎后进入冷却润滑的乳化液系 统,损坏设备并缩短乳化液使用寿命。 • 损坏轧辊。
@ @
@ @ @ @ @
穿带速度高
运行速度高
@
@
酸洗原理—氧化铁皮的形成
氧化铁皮是金属在加热、热处理或在热状态 进行加工时形成的一层附着在金属表面上的 金属氧化物。
酸洗原理—氧化铁皮的形成
轧件经粗轧后沿辊道向热连轧轧机运行时,温度 为1000℃左右,这时在轧件表面上已生成了一层 薄的氧化铁皮,而轧前高压水除鳞机可将它们清 除掉。当轧件在连轧机上轧制时,板坯在各机架 轧机间暴露的时间极短,而且大的压下阻碍了带 钢表面上形成厚的氧化铁皮,而所形成的氧化薄 膜立即被破坏并受到水的冲洗,因此,可以说刚 刚从精轧末机架出来的带钢,虽然温度有780~ 850℃的较高温度,但带钢表面的氧化铁皮是极 薄的。带钢从精轧末机架出来后,进入喷水装置, 而后卷成带钢卷并缓慢冷却,就是在这段时间里, 带钢表面被氧化而生成氧化铁皮。
酸洗概述—除磷(氧化铁皮)方法
机械除鳞
化学除鳞
机械—化学联合除鳞
砂轮研磨
有酸除鳞
无酸除鳞
弯曲—酸洗
喷丸破鳞 酸洗
—
弯曲破鳞
喷丸破鳞
碱洗除鳞
电解除鳞
拉矫—酸洗
酸洗概述—酸洗种类
盐酸酸洗
混合酸酸洗
硫酸酸洗
酸洗种类
氢氟酸酸洗 硝酸酸洗
磷酸酸洗
酸洗概述—酸洗技术发展
早期。酸液深1000~1200mm。
酸洗概述—酸洗机组的比较:推拉式酸洗机组
• 推拉式酸洗机组酸洗,每根带钢经夹送辊依次 咬入,不用焊接,推送向前,直至卷取,逐卷 带钢间断地通过酸洗机组。
酸洗概述—酸洗机组的优缺点比较
比较项目 连续 推拉
设备简单 设备重量轻
厂房高度较低 投资省 组织生产灵活性 酸洗时间短,加热启动快,调节酸液成分快 重新启动时无需引带 动力剪外还可使用拉剪 改善带钢平直度能力较好 @ @ @
FeO Fe3O4 Fe2O3 体积总分子量
FeO
Fe3O4
温度(摄氏度)700 900
Fe2O3
1100
氧化温度对氧化铁皮的影响图
酸洗原理—带钢氧化铁皮组织结构
由于热轧带钢的化学成分、轧制温度、轧 制后的冷却速度及卷取温度的不同,所以 带钢表面上所生成的氧化铁皮的结构、厚 度性质亦有所不同。
深槽酸洗
70年代中期。酸液深400~1000mm。
浅槽酸洗
浅槽紊流酸洗
70年代末期,1983年德国MDS公司开发了紊流酸洗。酸液深 小于400mm 。
酸洗概述—三种酸洗技术的比较
参数比较 酸洗时间*,% 酸雾量*,% 电耗量*,% 热传递*,% 槽内带钢提升器 槽内带钢位置控制 槽内断带事故处理 深槽 100 100 100 100 有必要 不可能准确检测 困难,费时 浅槽 80 60 70 200 没必要 可以准确检测 容易 紊流 65 60 70 700 没必要 可以准确检 测 容易
酸洗原理—有利于酸洗的氧化铁皮
影响带钢表面氧化铁皮的因素 终轧温度及速度 冷却速度 卷曲温度 轧辊粗糙度
酸洗原理—有利于酸洗的氧化铁皮
• 终轧温度和轧制速度
氧化铁皮厚度
氧化时间
氧化速度
轧制速度
准确 控制 轧制 速度
温度(摄氏度)400
600 800
1200
卷曲温度
FeO
Fe3O4
酸洗原理—有利于酸洗的氧化铁皮
酸洗原理—氧化铁皮的形成
Fe
FeO Fe3O4 Fe2O3
O
酸洗原理—氧化铁皮的形成
温度
1200
Fe3O4
γFe+FeO
Fe2O3
FeO+Fe3O4 FeO
1000
Fe3O4 + Fe2O3
800
αFe+FeO
600
αFe+Fe3O4
400
含氧量
22
24
26
铁氧状态图
28
30
32
酸洗原理—氧化铁皮的形成
酸洗原理—带钢氧化铁皮组织结构
磁性体Fe3O4
富氏体FeO 带钢基体
蓝灰色氧化铁皮表面,生成温度大于1100℃
酸洗原理—带钢氧化铁皮组织结构
结论: 经过一般的热轧和退火后,氧化铁皮由FeO 相组成,Fe3O4层仅为氧化铁皮层的4~18%, 在许多情况下没有Fe2O3。且氧化铁皮层不 分层的,在铁被氧化的同时,体积增大使 氧化铁皮层出现裂缝和起皮,从而使生成 的氧化铁相互渗透而且是不规则的。