斜齿轮的成形磨削逼近法研究
成形磨齿机的切削参数分析与优化
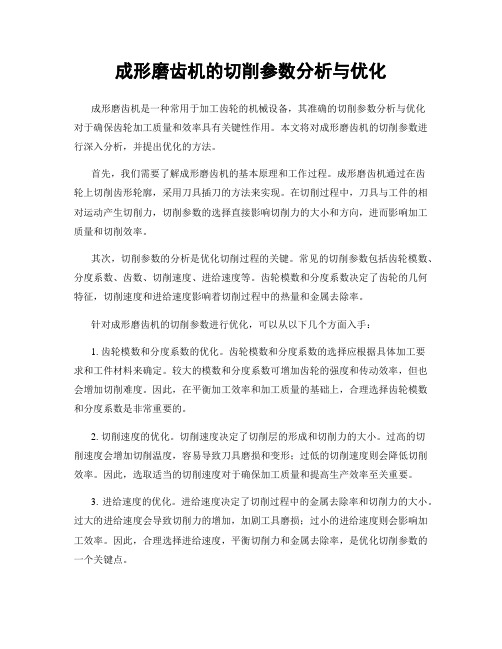
成形磨齿机的切削参数分析与优化成形磨齿机是一种常用于加工齿轮的机械设备,其准确的切削参数分析与优化对于确保齿轮加工质量和效率具有关键性作用。
本文将对成形磨齿机的切削参数进行深入分析,并提出优化的方法。
首先,我们需要了解成形磨齿机的基本原理和工作过程。
成形磨齿机通过在齿轮上切削齿形轮廓,采用刀具插刀的方法来实现。
在切削过程中,刀具与工件的相对运动产生切削力,切削参数的选择直接影响切削力的大小和方向,进而影响加工质量和切削效率。
其次,切削参数的分析是优化切削过程的关键。
常见的切削参数包括齿轮模数、分度系数、齿数、切削速度、进给速度等。
齿轮模数和分度系数决定了齿轮的几何特征,切削速度和进给速度影响着切削过程中的热量和金属去除率。
针对成形磨齿机的切削参数进行优化,可以从以下几个方面入手:1. 齿轮模数和分度系数的优化。
齿轮模数和分度系数的选择应根据具体加工要求和工件材料来确定。
较大的模数和分度系数可增加齿轮的强度和传动效率,但也会增加切削难度。
因此,在平衡加工效率和加工质量的基础上,合理选择齿轮模数和分度系数是非常重要的。
2. 切削速度的优化。
切削速度决定了切削层的形成和切削力的大小。
过高的切削速度会增加切削温度,容易导致刀具磨损和变形;过低的切削速度则会降低切削效率。
因此,选取适当的切削速度对于确保加工质量和提高生产效率至关重要。
3. 进给速度的优化。
进给速度决定了切削过程中的金属去除率和切削力的大小。
过大的进给速度会导致切削力的增加,加剧工具磨损;过小的进给速度则会影响加工效率。
因此,合理选择进给速度,平衡切削力和金属去除率,是优化切削参数的一个关键点。
除了以上三个方面,还需要考虑切削润滑条件、刀具的选择和工件夹紧等因素。
合适的切削润滑条件可以减小切削力,提高刀具寿命;正确选择刀具材料、几何形状和涂层可以增加切削效率和加工质量;有效的工件夹紧方式可以减少变形和振动,提高切削稳定性。
为了进一步优化成形磨齿机的切削参数,可以借助模拟和仿真技术进行虚拟实验。
基于斜齿圆柱齿轮数控成形磨削方式下的砂轮修形轨迹计算
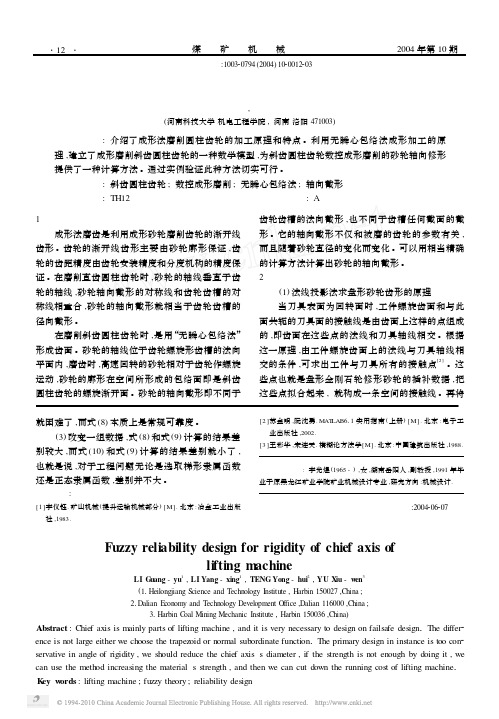
Fuzzy reliability design for rigidity of chief axis of
lifting machine
L I Guang - yu1 , L I Yang - xing1 , TENG Yong - hui2 , Y U Xiu - wen3 (11Heilongjiang Science and Technology Institute , Harbin 150027 ,China ;
c
=
acosαy sinαy
rb
(2)
这样给出角度
α y
值
,按式 (1) 和式 (2)
计算出参
数
b
和
c
,
它们与
α y
一起确定砂轮的位置 。如图
2
的 P - P 截面 ,可得
tg v
=
KM BK
=
(
bcosαy - c) tgλb cosαt bcosαt - c
(3)
式中
cosαt
=
1 tgλb tgβ
· 12 · 煤 矿 机 械 2004 年第 10 期
文章编号 :100320794 (2004) 1020012203
基于斜齿圆柱齿轮数控成形磨削方式下的砂轮修形轨迹计算
贺红霞 , 张洛平 (河南科技大学 机电工程学院 , 河南 洛阳 471003)
摘 要 : 比较普通蜗杆传动与 TOP 型蜗杆传动的特点 , 分析平面二次包络蜗轮的形成原理 ,
叙述关于损坏的非标准 TOP 型蜗轮的测绘内容 ,蜗轮结构及材料的选择 。重点论述 TOP 蜗轮 6 项
主要几何尺寸的计算方法和步骤以及蜗轮加工的技术要求 。
齿轮磨削工艺技术
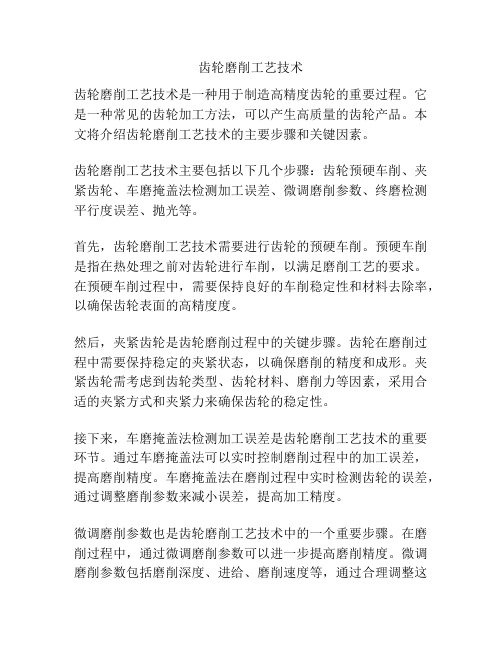
齿轮磨削工艺技术齿轮磨削工艺技术是一种用于制造高精度齿轮的重要过程。
它是一种常见的齿轮加工方法,可以产生高质量的齿轮产品。
本文将介绍齿轮磨削工艺技术的主要步骤和关键因素。
齿轮磨削工艺技术主要包括以下几个步骤:齿轮预硬车削、夹紧齿轮、车磨掩盖法检测加工误差、微调磨削参数、终磨检测平行度误差、抛光等。
首先,齿轮磨削工艺技术需要进行齿轮的预硬车削。
预硬车削是指在热处理之前对齿轮进行车削,以满足磨削工艺的要求。
在预硬车削过程中,需要保持良好的车削稳定性和材料去除率,以确保齿轮表面的高精度度。
然后,夹紧齿轮是齿轮磨削过程中的关键步骤。
齿轮在磨削过程中需要保持稳定的夹紧状态,以确保磨削的精度和成形。
夹紧齿轮需考虑到齿轮类型、齿轮材料、磨削力等因素,采用合适的夹紧方式和夹紧力来确保齿轮的稳定性。
接下来,车磨掩盖法检测加工误差是齿轮磨削工艺技术的重要环节。
通过车磨掩盖法可以实时控制磨削过程中的加工误差,提高磨削精度。
车磨掩盖法在磨削过程中实时检测齿轮的误差,通过调整磨削参数来减小误差,提高加工精度。
微调磨削参数也是齿轮磨削工艺技术中的一个重要步骤。
在磨削过程中,通过微调磨削参数可以进一步提高磨削精度。
微调磨削参数包括磨削深度、进给、磨削速度等,通过合理调整这些参数可以减小磨削误差,提高加工精度。
终磨检测平行度误差也是齿轮磨削工艺技术中的一个关键环节。
通过终磨检测可以准确测量齿轮的平行度误差,进一步改善加工精度。
终磨检测平行度误差需要使用高精度的测量仪器和设备,以确保测量结果的准确性。
最后,齿轮磨削工艺技术还需要进行抛光等后续处理。
抛光可以进一步提高精度和光洁度,使得齿轮的表面更加光滑和平整。
总的来说,齿轮磨削工艺技术是一种制造高精度齿轮的重要方法。
通过预硬车削、夹紧齿轮、车磨掩盖法检测加工误差、微调磨削参数、终磨检测平行度误差和抛光等步骤,可以获得高质量的齿轮产品。
这些步骤中的关键因素包括材料选用、磨削参数调整、夹紧方式等,需要进行合理的选择和调整,以实现高精度度的齿轮磨削。
斜齿轮加工原理
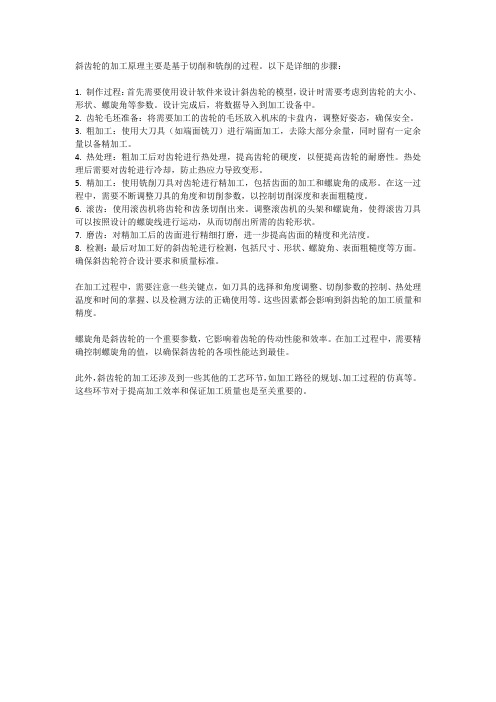
斜齿轮的加工原理主要是基于切削和铣削的过程。
以下是详细的步骤:1. 制作过程:首先需要使用设计软件来设计斜齿轮的模型,设计时需要考虑到齿轮的大小、形状、螺旋角等参数。
设计完成后,将数据导入到加工设备中。
2. 齿轮毛坯准备:将需要加工的齿轮的毛坯放入机床的卡盘内,调整好姿态,确保安全。
3. 粗加工:使用大刀具(如端面铣刀)进行端面加工,去除大部分余量,同时留有一定余量以备精加工。
4. 热处理:粗加工后对齿轮进行热处理,提高齿轮的硬度,以便提高齿轮的耐磨性。
热处理后需要对齿轮进行冷却,防止热应力导致变形。
5. 精加工:使用铣削刀具对齿轮进行精加工,包括齿面的加工和螺旋角的成形。
在这一过程中,需要不断调整刀具的角度和切削参数,以控制切削深度和表面粗糙度。
6. 滚齿:使用滚齿机将齿轮和齿条切削出来。
调整滚齿机的头架和螺旋角,使得滚齿刀具可以按照设计的螺旋线进行运动,从而切削出所需的齿轮形状。
7. 磨齿:对精加工后的齿面进行精细打磨,进一步提高齿面的精度和光洁度。
8. 检测:最后对加工好的斜齿轮进行检测,包括尺寸、形状、螺旋角、表面粗糙度等方面。
确保斜齿轮符合设计要求和质量标准。
在加工过程中,需要注意一些关键点,如刀具的选择和角度调整、切削参数的控制、热处理温度和时间的掌握、以及检测方法的正确使用等。
这些因素都会影响到斜齿轮的加工质量和精度。
螺旋角是斜齿轮的一个重要参数,它影响着齿轮的传动性能和效率。
在加工过程中,需要精确控制螺旋角的值,以确保斜齿轮的各项性能达到最佳。
此外,斜齿轮的加工还涉及到一些其他的工艺环节,如加工路径的规划、加工过程的仿真等。
这些环节对于提高加工效率和保证加工质量也是至关重要的。
变速器齿轮磨削工艺研究
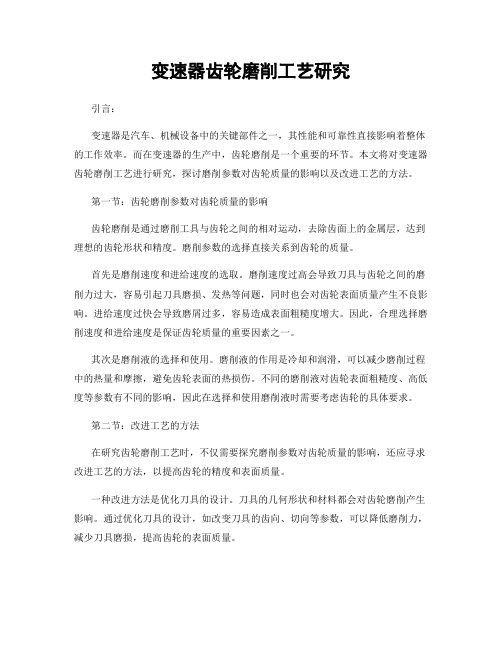
变速器齿轮磨削工艺研究引言:变速器是汽车、机械设备中的关键部件之一,其性能和可靠性直接影响着整体的工作效率。
而在变速器的生产中,齿轮磨削是一个重要的环节。
本文将对变速器齿轮磨削工艺进行研究,探讨磨削参数对齿轮质量的影响以及改进工艺的方法。
第一节:齿轮磨削参数对齿轮质量的影响齿轮磨削是通过磨削工具与齿轮之间的相对运动,去除齿面上的金属层,达到理想的齿轮形状和精度。
磨削参数的选择直接关系到齿轮的质量。
首先是磨削速度和进给速度的选取。
磨削速度过高会导致刀具与齿轮之间的磨削力过大,容易引起刀具磨损、发热等问题,同时也会对齿轮表面质量产生不良影响。
进给速度过快会导致磨屑过多,容易造成表面粗糙度增大。
因此,合理选择磨削速度和进给速度是保证齿轮质量的重要因素之一。
其次是磨削液的选择和使用。
磨削液的作用是冷却和润滑,可以减少磨削过程中的热量和摩擦,避免齿轮表面的热损伤。
不同的磨削液对齿轮表面粗糙度、高低度等参数有不同的影响,因此在选择和使用磨削液时需要考虑齿轮的具体要求。
第二节:改进工艺的方法在研究齿轮磨削工艺时,不仅需要探究磨削参数对齿轮质量的影响,还应寻求改进工艺的方法,以提高齿轮的精度和表面质量。
一种改进方法是优化刀具的设计。
刀具的几何形状和材料都会对齿轮磨削产生影响。
通过优化刀具的设计,如改变刀具的齿向、切向等参数,可以降低磨削力,减少刀具磨损,提高齿轮的表面质量。
另一种改进方法是引入超声波辅助磨削技术。
超声波振动可以改变切削区域的状况,进一步提高齿轮磨削的精度和效率。
超声波辅助磨削技术可以减小刀具与齿轮之间的接触力,降低刀具磨损,同时还可以改善材料的断裂行为,提高齿轮的表面质量。
结论:在变速器齿轮磨削工艺研究中,磨削参数的选取和改进工艺的方法都是关键因素。
合理选择磨削速度和进给速度,使用适当的磨削液,可以提高齿轮的质量。
优化刀具的设计和引入超声波辅助磨削技术,可以进一步提高齿轮的精度和表面质量。
通过不断的研究和改进,变速器齿轮磨削工艺将会更加完善,为汽车和机械设备的工作效率提供更好的保障。
齿轮加工方法分析与研究

齿轮加工方法分析与研究齿轮是一种常见的机械传动元件,广泛应用于各种机械设备中。
齿轮的加工质量直接影响到机械设备的性能和使用寿命,因此齿轮加工方法的优化和研究对于机械设备的性能提升具有重要意义。
本文将从齿轮加工方法的分析和研究角度出发,探讨齿轮加工的相关技术和方法,为齿轮加工工艺提供一定的指导和参考。
一、齿轮加工的传统方法在齿轮加工的传统方法中,常见的有铣削、滚齿、切削、锻造等多种方法。
铣削是齿轮加工中最常用的方法之一。
铣削加工齿轮的优点是工艺简单、成本低、适用范围广,但由于铣削是一种切屑加工方式,因此存在切削热量大、切削力大、切屑难以处理等缺点,尤其对于硬质、高精度的齿轮加工来说,铣削加工存在一定的局限性。
滚齿是另一种常见的齿轮加工方法,它利用专用的滚刀进行滚刀齿加工,具有加工效率高、加工成本低、加工质量好的优点,适用于大批量、高精度的齿轮生产。
但是滚齿加工需要配备专用的滚刀和设备,对生产成本和设备投入要求较高。
切削和锻造是另外两种齿轮加工的传统方法,它们分别利用切削和锻造的方式进行齿轮加工。
切削加工适用于生产大型、重载、高精度的齿轮,而锻造加工适用于生产大中型齿轮。
但是这两种方法在加工周期长、成本高、易产生残余应力等方面存在一定的不足。
随着科技的发展和机械加工技术的进步,现代齿轮加工方法也得到了较大的发展。
目前,现代齿轮加工方法主要包括磨削加工、电火花加工、激光加工等多种新颖的加工技术。
磨削加工是一种常见的现代齿轮加工方法,它利用磨削工具对齿轮进行精密的磨削加工。
磨削加工具有磨削车削和磨削磨齿两种方式,前者适用于大型、重载齿轮的精密磨削,后者适用于齿轮高速磨削。
磨削加工具有磨削精度高、表面粗糙度小、加工效率高等优点,适用于大中型齿轮的高精度加工。
电火花加工是一种利用电火花放电原理进行齿轮加工的新型技术。
它的优点是加工精度高、适用范围广、可加工高硬度材料、难加工材料等,在齿轮修理、小批量齿轮加工方面应用较多。
齿轮加工方法分析与研究

齿轮加工方法分析与研究1. 引言1.1 研究背景齿轮是机械传动中常用的元件,具有传递力矩和转速的功能。
齿轮加工是指对齿轮进行加工和制造的过程,其质量直接影响到机械设备的性能和使用寿命。
随着工业化的发展和机械设备的普及,对齿轮加工技术的要求越来越高。
目前,齿轮加工方法繁多,包括铣削、滚齿、刮齿等多种技术。
在现代制造业中,齿轮的加工技术不断得到改进和优化,以满足高精度、高效率和大批量生产的需求。
对不同的齿轮加工方法进行分析和研究,对提高齿轮加工质量和效率具有重要意义。
随着数字化技术和自动化设备的不断发展,齿轮加工设备也在不断更新换代,为齿轮加工工艺提供了更多可能性。
齿轮加工作为机械制造的重要环节,对提高机械设备的性能和可靠性具有重要作用。
对齿轮加工方法的研究和优化具有重要意义,可以促进我国齿轮加工技术的发展,提高我国制造业的整体竞争力。
1.2 研究目的齿轮是机械传动中非常重要的零部件,其加工质量直接影响到整个机械设备的使用效果和寿命。
本文旨在通过对齿轮加工方法的分析与研究,探讨如何提高齿轮加工的效率、精度和质量,促进我国齿轮加工技术的发展。
本研究的目的主要包括以下几个方面:1. 分析各种齿轮加工方法的特点和适用范围,为工程师和研究人员提供参考,帮助他们选择最适合的加工方法。
2. 比较不同齿轮加工方法的优缺点,找出各种加工方式的优化方向,提高加工效率和质量。
3. 探讨齿轮加工工艺的优化研究,包括切削参数的选择、工艺流程的优化等方面,为齿轮加工提供更合理的工艺流程。
通过对齿轮加工方法的详细研究和比较分析,本研究旨在为齿轮加工领域的工程师和研究人员提供参考,推动我国齿轮加工技术的进步与发展。
1.3 研究意义齿轮加工作为制造业中常见的加工方式,在现代工业生产中扮演着重要角色。
研究齿轮加工方法的意义在于提高生产效率、优化加工工艺、提高齿轮质量以及降低生产成本。
通过深入研究齿轮加工基本原理和方法,可以有效提高生产效率。
成形磨齿机的切削机理与切削力学研究
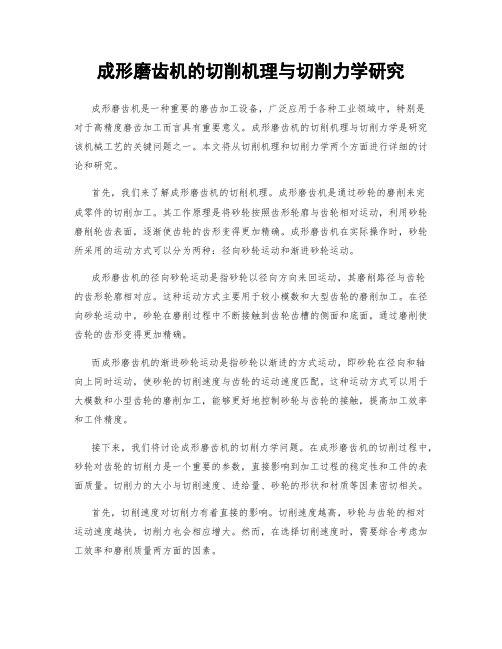
成形磨齿机的切削机理与切削力学研究成形磨齿机是一种重要的磨齿加工设备,广泛应用于各种工业领域中,特别是对于高精度磨齿加工而言具有重要意义。
成形磨齿机的切削机理与切削力学是研究该机械工艺的关键问题之一。
本文将从切削机理和切削力学两个方面进行详细的讨论和研究。
首先,我们来了解成形磨齿机的切削机理。
成形磨齿机是通过砂轮的磨削来完成零件的切削加工。
其工作原理是将砂轮按照齿形轮廓与齿轮相对运动,利用砂轮磨削轮齿表面,逐渐使齿轮的齿形变得更加精确。
成形磨齿机在实际操作时,砂轮所采用的运动方式可以分为两种:径向砂轮运动和渐进砂轮运动。
成形磨齿机的径向砂轮运动是指砂轮以径向方向来回运动,其磨削路径与齿轮的齿形轮廓相对应。
这种运动方式主要用于较小模数和大型齿轮的磨削加工。
在径向砂轮运动中,砂轮在磨削过程中不断接触到齿轮齿槽的侧面和底面,通过磨削使齿轮的齿形变得更加精确。
而成形磨齿机的渐进砂轮运动是指砂轮以渐进的方式运动,即砂轮在径向和轴向上同时运动,使砂轮的切削速度与齿轮的运动速度匹配。
这种运动方式可以用于大模数和小型齿轮的磨削加工,能够更好地控制砂轮与齿轮的接触,提高加工效率和工件精度。
接下来,我们将讨论成形磨齿机的切削力学问题。
在成形磨齿机的切削过程中,砂轮对齿轮的切削力是一个重要的参数,直接影响到加工过程的稳定性和工件的表面质量。
切削力的大小与切削速度、进给量、砂轮的形状和材质等因素密切相关。
首先,切削速度对切削力有着直接的影响。
切削速度越高,砂轮与齿轮的相对运动速度越快,切削力也会相应增大。
然而,在选择切削速度时,需要综合考虑加工效率和磨削质量两方面的因素。
其次,进给量也是影响切削力的重要因素。
进给量越大,切削力也会相应增大。
进给量的选择应根据齿轮的材质、形状和加工要求等因素进行合理配置,以平衡生产效率与磨削质量的要求。
此外,砂轮的形状和材质也对切削力产生影响。
砂轮的尺寸、结构和磨削层厚度等因素都会对切削力的大小和分布产生影响。
修形斜齿轮成形磨削中齿廓精度补偿方法
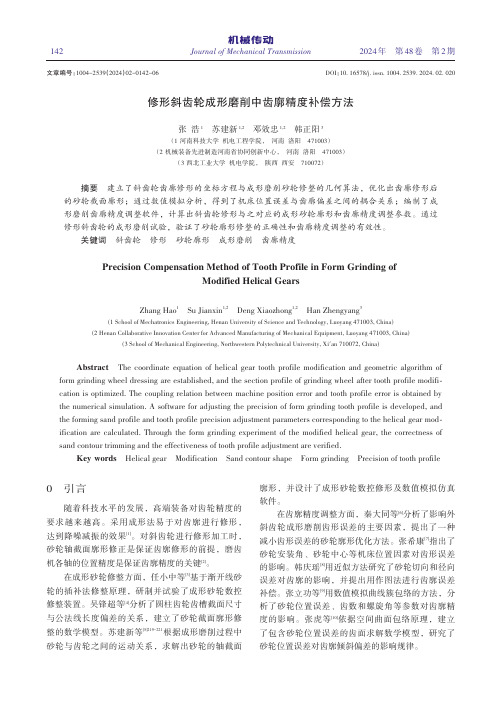
2024年第48卷第2期Journal of Mechanical Transmission修形斜齿轮成形磨削中齿廓精度补偿方法张浩1苏建新1,2邓效忠1,2韩正阳3(1 河南科技大学机电工程学院,河南洛阳471003)(2 机械装备先进制造河南省协同创新中心,河南洛阳471003)(3 西北工业大学机电学院,陕西西安710072)摘要建立了斜齿轮齿廓修形的坐标方程与成形磨削砂轮修整的几何算法,优化出齿廓修形后的砂轮截面廓形;通过数值模拟分析,得到了机床位置误差与齿廓偏差之间的耦合关系;编制了成形磨削齿廓精度调整软件,计算出斜齿轮修形与之对应的成形砂轮廓形和齿廓精度调整参数。
通过修形斜齿轮的成形磨削试验,验证了砂轮廓形修整的正确性和齿廓精度调整的有效性。
关键词斜齿轮修形砂轮廓形成形磨削齿廓精度Precision Compensation Method of Tooth Profile in Form Grinding ofModified Helical GearsZhang Hao1Su Jianxin1,2Deng Xiaozhong1,2Han Zhengyang3(1 School of Mechatronics Engineering, Henan University of Science and Technology, Luoyang 471003, China)(2 Henan Collaborative Innovation Center for Advanced Manufacturing of Mechanical Equipment, Luoyang 471003, China)(3 School of Mechanical Engineering, Northwestern Polytechnical University, Xi'an 710072, China)Abstract The coordinate equation of helical gear tooth profile modification and geometric algorithm of form grinding wheel dressing are established, and the section profile of grinding wheel after tooth profile modifi⁃cation is optimized. The coupling relation between machine position error and tooth profile error is obtained by the numerical simulation. A software for adjusting the precision of form grinding tooth profile is developed, and the forming sand profile and tooth profile precision adjustment parameters corresponding to the helical gear mod⁃ification are calculated. Through the form grinding experiment of the modified helical gear, the correctness of sand contour trimming and the effectiveness of tooth profile adjustment are verified.Key words Helical gear Modification Sand contour shape Form grinding Precision of tooth profile0 引言随着科技水平的发展,高端装备对齿轮精度的要求越来越高。
基于神经网络的修形斜齿轮成形磨削中的接触线优化方法
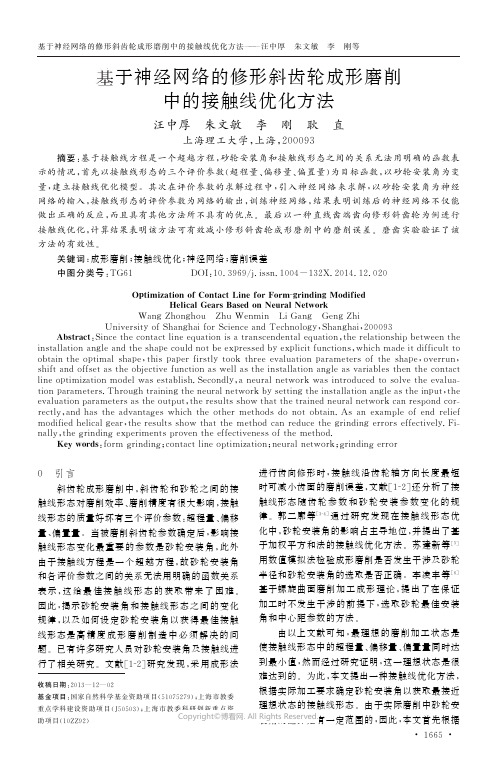
基于神经网络的修形斜齿轮成形磨削中的接触线优化方法汪中厚 朱文敏 李 刚 耿 直上海理工大学,上海,200093摘要:基于接触线方程是一个超越方程,砂轮安装角和接触线形态之间的关系无法用明确的函数表示的情况,首先以接触线形态的三个评价参数(超程量㊁偏移量㊁偏置量)为目标函数,以砂轮安装角为变量,建立接触线优化模型㊂其次在评价参数的求解过程中,引入神经网络来求解,以砂轮安装角为神经网络的输入,接触线形态的评价参数为网络的输出,训练神经网络,结果表明训练后的神经网络不仅能做出正确的反应,而且具有其他方法所不具有的优点㊂最后以一种直线齿端齿向修形斜齿轮为例进行接触线优化,计算结果表明该方法可有效减小修形斜齿轮成形磨削中的磨削误差㊂磨齿实验验证了该方法的有效性㊂关键词:成形磨削;接触线优化;神经网络;磨削误差中图分类号:T G 61 D O I :10.3969/j.i s s n .1004-132X.2014.12.020O p t i m i z a t i o no fC o n t a c t L i n e f o rF o r m ‐g r i n d i n g M o d i f i e d H e l i c a lG e a r sB a s e do nN e u r a lN e t w o r kW a n g Z h o n g h o u Z h u W e n m i n L iG a n g G e n g Zh i U n i v e r s i t y o f S h a n g h a i f o rS c i e n c e a n dT e c h n o l o g y ,S h a n gh a i ,200093A b s t r a c t :S i n c e t h e c o n t a c t l i n e e q u a t i o n i s a t r a n s c e n d e n t a l e q u a t i o n ,t h e r e l a t i o n s h i p be t w e e n t h e i n s t a l l a t i o na n g l e a n d t h e s h a p e c o u l dn o t b e e x p r e s s e db y e x pl i c i t f u n c t i o n s ,w h i c hm a d e i t d i f f i c u l t t o o b t a i n t h eo p t i m a l s h a p e ,t h i s p a p e r f i r s t l y t o o kt h r e ee v a l u a t i o n p a r a m e t e r so f t h es h a pe ,o v e r r u n ,s h if t a n do f f s e t a s t h e o b j e c t i v e f u n c t i o na sw e l l a s t h e i n s t a l l a t i o na n gl e a sv a r i a b l e s t h e n t h e c o n t a c t l i n e o p t i m i z a t i o nm o d e lw a s e s t a b l i s h .S e c o n d l y ,an e u r a l n e t w o r kw a s i n t r o d u c e d t o s o l v e t h e e v a l u a -t i o n p a r a m e t e r s .T h r o u g h t r a i n i n g t h e n e u r a l n e t w o r kb y s e t t i n g t h e i n s t a l l a t i o n a n g l e a s t h e i n pu t ,t h e e v a l u a t i o n p a r a m e t e r s a s t h e o u t p u t ,t h e r e s u l t s s h o wt h a t t h e t r a i n e dn e u r a l n e t w o r k c a n r e s p o n d c o r -r e c t l y ,a n dh a st h ea d v a n t a g e sw h i c ht h eo t h e r m e t h o d sd on o to b t a i n .A sa ne x a m pl eo fe n dr e l i e f m o d i f i e dh e l i c a l g e a r ,t h e r e s u l t s s h o wt h a t t h em e t h o dc a nr e d u c e t h e g r i n d i n g e r r o r s e f f e c t i v e l y .F i -n a l l y ,t h e g r i n d i n g e x pe r i m e n t s p r o v e n t h e ef f e c t i v e n e s s o f t h em e t h o d .K e y wo r d s :f o r m g r i n d i n g ;c o n t a c t l i n e o p t i m i z a t i o n ;n e u r a l n e t w o r k ;g r i n d i n g e r r o r 收稿日期:2013 12 02基金项目:国家自然科学基金资助项目(51075279);上海市教委重点学科建设资助项目(J 50503);上海市教委科研创新重点资助项目(10Z Z 92)0 引言斜齿轮成形磨削中,斜齿轮和砂轮之间的接触线形态对磨削效率㊁磨削精度有很大影响,接触线形态的质量好坏有三个评价参数:超程量㊁偏移量㊁偏置量㊂当被磨削斜齿轮参数确定后,影响接触线形态变化最重要的参数是砂轮安装角,此外由于接触线方程是一个超越方程,故砂轮安装角和各评价参数之间的关系无法用明确的函数关系表示,这给最佳接触线形态的获取带来了困难㊂因此,揭示砂轮安装角和接触线形态之间的变化规律,以及如何设定砂轮安装角以获得最佳接触线形态是高精度成形磨削制造中必须解决的问题㊂已有许多研究人员对砂轮安装角及接触线进行了相关研究㊂文献[1‐2]研究发现,采用成形法进行齿向修形时,接触线沿齿轮轴方向长度最短时可减小齿面的磨削误差,文献[1‐2]还分析了接触线形态随齿轮参数和砂轮安装参数变化的规律㊂郭二廓等[3‐4]通过研究发现在接触线形态优化中,砂轮安装角的影响占主导地位,并提出了基于加权平方和法的接触线优化方法㊂苏建新等[5]用数值模拟法检验成形磨削是否发生干涉及砂轮半径和砂轮安装角的选取是否正确㊂李凌丰等[6]基于螺旋曲面磨削加工成形理论,提出了在保证加工时不发生干涉的前提下,选取砂轮最佳安装角和中心距参数的方法㊂由以上文献可知,最理想的磨削加工状态是使接触线形态中的超程量㊁偏移量㊁偏置量同时达到最小值,然而经过研究证明,这一理想状态是很难达到的㊂为此,本文提出一种接触线优化方法,根据实际加工要求确定砂轮安装角以获取最接近理想状态的接触线形态㊂由于实际磨削中砂轮安装角的选择是有一定范围的,因此,本文首先根据㊃5661㊃基于神经网络的修形斜齿轮成形磨削中的接触线优化方法汪中厚 朱文敏 李 刚等Copyright ©博看网. All Rights Reserved.砂轮截形设计中的造型条件确定砂轮安装角的可选范围,在此基础上建立以砂轮安装角为变量㊁接触线形态的三个评价参数为目标函数的优化模型,并在评价参数的求解中引入神经网络进行处理,然后以一个实例介绍接触线优化的整个流程,最后通过磨齿实验证明该方法的有效性㊂1 砂轮安装角范围1.1 坐标系及砂轮截形的解析法求解为了便于分析研究,建立图1所示坐标系㊂在齿轮上建立坐标系o g x g y g z g ,其中z g 轴与齿轮轴线重合;在砂轮上建立坐标系o w x w y wz w ,其中z w 轴与砂轮轴线重合,a x 为齿向修形时的中心距变化量㊂齿轮轴线和砂轮轴线的最短距离为中心距a ,两轴线的夹角即为砂轮安装角Σ㊂图1 斜齿轮成形磨削坐标系用成形法磨削斜齿轮时,在相对运动的任一瞬间,齿轮螺旋面与砂轮回转面将沿接触线相切接触㊂通过斜齿轮端面形状及砂轮安装参数求出砂轮与齿轮之间的接触线,将接触线绕砂轮轴线旋转投影得到砂轮截形,以此方法可求得中心距一定时,任意砂轮安装角下的砂轮截形㊂给定齿轮螺旋面上任一点M (x g ,y g ,z g ),即可求出砂轮回转面上与齿轮螺旋面M 点对应的磨削接触点P (x w ,y w ,z w ),P 点组成的曲线就是磨削过程中砂轮与齿轮的实际接触线㊂将接触线旋转投影到砂轮截面即可得到成形砂轮截面[7]:R w =x 2w +y 2wZ w =z }w(1)1.2 砂轮安装角范围的确定用成形法磨削斜齿轮时,由于齿根部有过渡曲线连接,砂轮安装角Σ只能在一定范围内选取,这个范围是根据砂轮截形设计中的造型条件确定的[8]㊂为了加工出正确的斜齿轮螺旋面,必须同时满足以下两个造型条件:相切接触条件和互不干涉条件㊂对于相切接触条件,砂轮安装角的选择只需满足关系式:a <|Λ||pc o t Σ|<|Λ{|或a >|Λ||p c o t Σ|>|Λ{|(2)其中Λ是一个与齿轮端面截形曲线上点坐标位置相关的函数,p 为螺旋参数㊂对于互不干涉条件,取齿轮坐标系下齿根过渡螺旋面上任一点S g (x g s ,y g s ,z g s ),将该点转换到砂轮坐标系下得到点S w (x w s ,y w s ,z w s ),则砂轮在该点的切削半径为R 0=x 2w s +y 2w s(3)而斜齿轮在该点的曲率半径为ρ=[1+(d x w s d y w s )]32/(d 2x w s d y 2ws )(4)只要满足Δ=R 0-ρ<0,则在S 点处不会发生干涉现象㊂齿轮参数及中心距确定后,Δ成为只与Σ相关的函数㊂结合两个造型条件即可得到砂轮安装角的取值范围㊂2 接触线优化模型2.1 接触线的性质成形磨削斜齿轮时的接触线是一条空间三维曲线,将接触线投影到齿轮坐标系的o g y g z g 平面上,如图2所示㊂可见接触线形态主要受超程量s a ㊁偏置量s b ㊁偏移量s c 三个评价参数的影响㊂超程量是接触线第一个点和最后一个点在z g 轴方向上的长度㊂偏置量是齿顶圆和渐开线起始圆与同一齿面的交点在z g 轴方向上的长度㊂偏移量是分度圆分别与左右齿面的交点在z g 轴方向上的长度㊂图2 接触线示意图磨削生产中,对于斜齿轮,接触线在齿槽中运动时是一端牵引另一端尾随,因此,砂轮沿齿宽方向的实际工作行程为齿宽加上超程量,在砂轮走刀速度一定的条件下,超程量越小,磨削时间越短,磨削效率越高㊂由于接触线在齿槽中呈倾斜㊃6661㊃中国机械工程第25卷第12期2014年6月下半月Copyright ©博看网. All Rights Reserved.态,齿轮左右两齿面在接触点处受力不平衡,从而产生磨削振颤,为了减小砂轮进出齿轮的受力不平衡,必须减小偏移量㊂另外在进行附加径向运动齿向修形时,偏移量越小,修形精度越高㊂当偏置量趋向最小时,需要考虑该过程会增大偏移量和超程量,因此偏置量最小时仅适合于单侧磨削方式㊂2.2 砂轮安装角与接触线性质分析由上文可知,为了优化接触线以提高磨削效率和磨削精度,必须减小超程量㊁偏移量㊁偏置量的值㊂斜齿轮基本参数见表1㊂表1 斜齿轮基本参数齿数z53模数m n (mm )5压力角α(°)20螺旋角β(°)20变位系数x n0齿顶圆直径d a (mm )292.01齿根圆直径d f (mm )269.51渐开线终止圆直径d n a (mm )290渐开线起始圆直径d f a (mm )273齿轮宽度B (mm )70齿向修形量δ(mm )0.02修形宽度b (mm )10对于表1中的齿轮,当砂轮安装角在69°~73°之间变化时,接触线上的超程量㊁偏移量㊁偏置量随砂轮安装角的变化规律如图3所示㊂随着砂轮安装角的改变,超程量㊁偏移量㊁偏置量也同时发生变化,然而这3个量的最小值不可能在同一砂轮安装角下实现㊂例如在图3中当超程量㊁偏移量㊁偏置量最小时,砂轮安装角分别约为69°㊁69.40°㊁72.38°㊂砂轮安装角由69.40°逐渐增大时,偏移量和超程量增大,偏置量先减小后增大;砂轮安装角由69.40°逐渐减小时,偏移量和偏置量增大,超程量减小㊂图3 接触线评价参数与砂轮安装角的关系2.3 基于约束法的接触线多目标优化模型接触线优化时涉及多个设计指标,即要求超程量㊁偏置量㊁偏移量都为最小值㊂这种同时要求两项或几项设计指标达到最优值的问题就是多目标优化问题㊂该问题的数学模型可表示为目标函数:m i n F =m i n F 1(Σ)m i n F 2(Σ)m i n F 3(Σ{)(5)其中F 1(Σ)㊁F 2(Σ)㊁F 3(Σ)分别为超程量㊁偏移量㊁偏置量关于砂轮安装角Σ的函数㊂约束条件为Σ1<Σ<Σ2(6)(Σ1,Σ2)为砂轮安装角的可选范围㊂由上文可知,本数学模型中的三个设计指标不可能同时达到最优,因此必须根据实际加工需要,选择相对最优的方案㊂约束模型的理论依据如下:若规划问题的某一目标可以给出一个可选择的范围,则该目标就可以作为约束条件而被排除出目标组,进入约束条件组中㊂因此,可以根据加工需要选择需要优化的第一目标,并给其余目标设定可选择的范围㊂例如,当要求提高磨削效率时以超程量最小为第一目标,同时设定偏移量和偏置量不能超出一个范围值,重新构建数学模型,目标函数为m i n F =m i n F 1(Σ)(7)约束条件为Σ1<Σ<Σ2F 2(Σ)<F j2F 3(Σ)<F j üþýïïïï3(8)其中F j2㊁F j 3分别为对偏移量㊁偏置量设置的限制范围㊂至此关于超程量㊁偏移量㊁偏置量的多目标优化转换成为关于超程量的单目标优化㊂3 接触线形态评价参数求解3.1 接触线方程在求解接触线上的超程量㊁偏移量㊁偏置量时,需要求解接触线方程[7]:z g n x +a n y c o t Σ+(a -x g +p c o t Σ)n z =0(9)式中,(n x ,n y ,n z )为斜齿轮螺旋面上点的法向量㊂式(9)是一个超越方程,可结合等误差算法和牛顿迭代法进行求解[9],优化时需要频繁地求解超越方程,这是因为砂轮安装角和超程量㊁偏置量㊁偏移量之间的关系不能用具体的函数表示,具有模糊性㊂为了解决这一问题,可以直接对优化参数和砂轮安装角的函数关系进行拟合㊂由图3可知,可以采用直线拟合方法,这种方法的优点是原理简单,缺点是需要较多的人工干预并且编程较复杂㊂例如,该方法首先要判断在当前齿轮参数和砂轮安装参数下需要对几段直线进行拟合,即必须确定超程量㊁偏置量㊁偏移量分㊃7661㊃基于神经网络的修形斜齿轮成形磨削中的接触线优化方法汪中厚 朱文敏 李 刚等Copyright ©博看网. All Rights Reserved.别为最小值时相应的砂轮安装角,然后以最小砂轮安装角为标准进行分段拟合㊂而神经网络却十分擅长这种输入输出关系不明确的函数逼近,直接调用神经网络的模拟结果而不去求解超越方程可以缩短计算时间和减少人工干预㊂在目前使用的各种神经网络中,B P 神经网络的应用最为广泛,而B P 神经网络的基本功能就是函数逼近㊂3.2 评价参数求解模型设(Σ(k ),F (k )1,F (k )2,F (k )3)(k =1,2, ,n )为输入输出样本数据对,其中,Σ(k )=[Σ1Σ2 Σn ]T为砂轮安装角输入数据,F (k)m=[f (m )1f (m )2 f (m )n ]T (m =1,2,3)为超程量㊁偏置量㊁偏移量输出数据㊂把Σ(k )作为网络的输入,在连接权的作用下,可得到网络的实际输出Y (k)m =[y (m )1y (m )2 y (m )n]T ㊂设神经元i 到j 的连接权为w i j ,则权的调整量Δw i j和模型的均方误差e m 分别为Δw i j =ηδjv i (10)e m =1n ∑nk =1(f (m )k -y (m )k )2(11)式中,η为学习速率;δj 为误差函数对神经元j 输入的偏导数;v i 为第i 个神经元的输出㊂'经过大量的试算发现,函数逼近能力与隐层的数目关系不大,因此本问题采用单隐层的B P 神经网络,这一点与参考文献[10]结论一致,隐层神经元传递函数采用S 形正切函数,输出层神经元传递函数采用S 形对数函数㊂在69.32°~71.53°之间取200个砂轮安装角的值并计算对应的超程量㊁偏置量㊁偏移量,作为训练样本㊂ 按上述方法用表2所示训练参数建立神经网络模型㊂模型的训练结果如图4所示,经过15次迭代,当均方误差收敛于8.32456×10-6时,网络性能达到目标要求,网络自动停止训练㊂表2 训练参数训练次数训练目标学习速率10001×10-50.1图4神经网络建模训练结果图5所示为偏移量真实值和神经网络计算值之间的误差曲线,可见,网络计算值和真实值之间的误差非常小,除了在69.32°~69.4°附近出现了相对比较大的误差外,其余误差都比较小㊂在该处产生较大相对误差的原因可以在图3中反映出来,因为在该处偏移量接近于最小值,而偏移量最小值处为一个值突变点,所以用神经网络进行计算时,会使相对误差较大,但即使最大误差处的偏移量与真实值也仅有0.2mm 的偏差㊂图5 偏移量误差曲线观察图6和图7发现,超程量和偏置量的误差都很小,这是因为在训练样本中的砂轮安装角范围围内超程量和偏置量是单调的,没有值突变点㊂图6 超程量误差曲线图7 偏置量误差曲线4 误差分析模型为验证接触线优化效果,需要进行反向计算,即由最佳砂轮安装角计算出砂轮截形,再根据砂轮截形反算出磨削得到的齿面,以便与设计齿面比较,求解磨削误差㊂对齿轮进行齿向修形时,可选择三种附加运动[11]:中心距变动㊁齿轮转角补偿及砂轮轴向移动㊂齿轮在齿形修形时没有附加运动要求,为方便建立误差分析模型,本文以仅有齿向修形的斜㊃8661㊃中国机械工程第25卷第12期2014年6月下半月Copyright ©博看网. All Rights Reserved.齿轮且砂轮进行中心距变动附加运动为例建立误差分析模型㊂如果由砂轮截形反算到齿面上点为T (x T ,yT ,z T ),而与该点对应的设计齿轮螺旋面上一点为Q (x Q ,yQ ,z Q ),则设计螺旋面和实际加工螺旋面间的磨削误差为[12]e =(x Q -x T )2+(yQ -y T )2+(z Q -z T )2(12)5 计算实例5.1 实例的选取本文为方便计算齿轮磨削误差,选取仅要求齿向修形的斜齿轮(表1)作为实例,此外,因为磨齿实验是采用单侧磨削方式分别对左右齿面进行加工的,所以下述计算实例也以此为前提进行优化㊂5.2 评价参数分析为了满足砂轮和齿轮的互不干涉条件,斜齿轮曲率半径应大于砂轮切削半径,采用第1节中砂轮安装角范围计算方法,可求出砂轮安装角的范围是69.32°~71.53°,如图8所示,经过计算,该范围也满足相切接触条件㊂图8 互不干涉条件下的砂轮安装角范围确定砂轮安装角的范围后,设置砂轮安装角的值并绘制相应的接触线形态曲线,如图9所示㊂当砂轮安装角Σ=70°(与分度圆螺旋角互余)时,偏移量为4.11mm ,超程量为9.98mm ,偏置量为7.12mm ;当砂轮安装角Σ=71.2528°(与基圆螺旋角互余)时,偏移量长度为13.47mm ,超程量1.Σ=70° 2.Σ=69.80° 3.Σ=69.40° 4.Σ=71.2528°图9 不同砂轮安装角接触线对比为16.82mm ,偏置量为3.84mm ;当砂轮安装角Σ=69.40°时,偏移量为0.16mm ,超程量为6.67mm ,偏置量为8.4mm ㊂由上文可见,三个评价参数在相同的砂轮安装角下,有的为较小值,有的为较大值,因此要选择砂轮安装角,必须对超程量㊁偏移量㊁偏置量进行综合考虑㊂在实际磨削加工中,齿向修形时为了减小磨削误差,应减小接触线上的偏移量,同时单侧磨削方式时偏置量和超程量都不宜过大,为此,在接触线的多目标优化设计中,以偏移量最小为第一目标,对偏置量和超程量的值进行约束㊂按第2节和第3节的方法进行优化后得到砂轮安装角Σ=69.80°,偏移量为2.68mm ,超程量为8.80mm ,偏置量为4.22mm ㊂另外,在实际加工中砂轮安装角一般取为与基圆螺旋角互余,即Σ=71.2528°,因此相比砂轮安装角Σ=71.2528°,采用优化后的砂轮安装角时,偏移量减小约80.1%,超程量减小约47.7%,偏置量增大约9.9%,偏移量和超程量都减小,反而偏置量增大,但仅增大0.38mm ,综合考虑,砂轮安装角为69.80°时的接触线形态优于砂轮安装角为71.2528°时的接触线形态㊂5.3 磨削误差分析本节主要对砂轮安装角为71.2528°和69.80°时的齿轮磨削误差进行分析和对比㊂为全面评价齿向修形齿面的误差,先计算出不同轴向位置的理论修形齿面,与第4节中砂轮截形反算得到的齿面进行比较,将齿面在啮合线上展开,齿宽为横轴,齿面展开长度为纵轴,展开长度用展角来表示,得到图10,齿顶在上方,齿根在下方㊂图10a 为砂轮安装角Σ=71.2528°时齿面误差e s 的分布图,图中齿宽中间部分为未修形部分㊂图10b 为砂轮安装角Σ=69.80°时齿面误差的分布图㊂通过图10a 和图10b 的对比可以发现,附加径向运动直线齿端方式齿向修形时,齿面误差关于齿宽对称的两侧齿面误差的分布区域基本对称,而且齿顶部比齿根部齿面误差大㊂对接触线进行优化后,最大齿面误差由8μm 减为5μm ,可见采用最佳砂轮安装角可以明显减小最大齿面误差㊂误差分析结果表明,接触线优化后加工出的齿面比优化前的加工误差分布更均匀,精度等级更高,可满足实际工程应用要求㊂㊃9661㊃基于神经网络的修形斜齿轮成形磨削中的接触线优化方法汪中厚 朱文敏 李 刚等Copyright ©博看网. All Rights Reserved.4.e s =4μm5.e s =5μm6.e s =6μm7.e s =7μm8.e s =8μm (a )Σ=71.2528°时齿面误差3.e s =3μm 4.e s =4μm 5.e s =5μm (b)Σ=69.80°时齿面误差图10 实际磨削齿面相对设计齿面的磨削误差6 磨齿加工实验本文磨齿加工实验采用自主研制的多功能成形磨削机床[13],被加工齿轮及机床如图11所示㊂针对表1所列斜齿轮参数,结合实际加工要求对接触线进行优化,确定砂轮安装角后计算砂轮截形,然后编制数控加工程序完成砂轮的自动修整和齿轮的磨削㊂图11 斜齿轮磨齿实验为了对磨削精度进行对比,排除齿轮毛坯差异可能产生的影响,在加工过程中采用同一齿轮单侧磨削加工方式,左右齿面分别以砂轮安装角Σ=71.2528°和Σ=69.80°进行砂轮截形计算和磨齿加工,两齿面加工时的其他工艺参数保持一致㊂为了对比磨削效率,分别记录左右齿面完成磨齿的时间㊂完成磨齿加工实验后采用哈尔滨中自精合精密仪器有限公司生产的齿轮测量仪进行检测,如图12所示㊂图12 齿轮检测齿形检测报告如图13所示,加工后的齿轮已达到国标3级精度,对比左右两齿面,右齿面的精度明显高于左齿面,可见进行优化后,精度得到很大提高,这主要是因为优化后接触线上的偏移量减小,磨削振颤得到了缓解㊂图13 齿形检测报告齿向检测报告如图14所示,加工后的齿轮达到国标5级精度,右齿面的齿向修形效果很好,达到国标3级,左齿面在加工时由于接触线的偏移量和偏置量过大而产生的 修形扭曲”,故只达到国标5级㊂图14 齿向检测报告加工时左齿面接触线的超程量大于右齿面的超程量,因此左齿面需要的磨削时间更长,在同样㊃0761㊃中国机械工程第25卷第12期2014年6月下半月Copyright ©博看网. All Rights Reserved.的工艺参数条件下,完成左齿面加工耗时约32m i n,右齿面加工耗时约27m i n,可见在大批量生产中,采用优化后的砂轮安装角可有效提高磨削效率㊂7 结论(1)本文对砂轮和斜齿轮的成形磨削运动进行了系统的研究,基于解析法得到了砂轮截形的计算公式,结合砂轮设计中的造型条件确定了不发生干涉时砂轮安装角的可选范围㊂(2)研究了接触线的性质,对影响接触线的三个参数进行分析,建立了基于约束法的接触线优化模型,在评价参数的求解中,引入神经网络来求解接触线条件式㊂(3)建立了附加径向运动直线齿端修形的误差分析模型,通过计算实例和磨齿实验验证了本方法的有效性㊂参考文献:[1] Y o u i c h iK,N o r i t e r u N,Y a s u h i k o O,e ta l.T o o t hT r a c e M o d i f i c a t i o n P r o c e s s i n g o f H e l i x G e a r b yF o r mG r i n d i n g M e t h o d[J].T r a n s a c t i o n so f t h e J a-p a n S o c i e t y o f M e c h a n i c a l E n g i n e e r s,1995,61(590):4088‐4093.[2] N o r i t e r u N,Y o u i c h iK,Y a s u h i k o O,e ta l.T o o t hF l a n k M o d i f i c a t i o nP r o c e s s i n g o fH e l i c a lG e a r sb yF o r mG r i n d i n g M e t h o d[J].T r a n s a c t i o n so f t h e J a-p a n S o c i e t y o f M e c h a n i c a l E n g i n e e r s,1999,65(639):4458‐4463.[3] 郭二廓,黄筱调,袁鸿,等.基于提高成形磨削效率和精度的接触线优化[J].计算机集成制造系统,2013,19(1):67‐74.G u oE r k u o,H u a n g X i a o t i a o,Y u a nH o n g,e t a l.C o n-t a c tL i n eO p t i m i z a t i o n f o r I m p r o v i n g E f f i c i e n c y a n dP r e c i s i o no fF o r m G r i n d i n g[J].C o m p u t e r I n t e g r a t-e d M a n uf a c t u r i ng S y s t e m s,2013,19(1):67‐74.[4] 郭二廓,黄筱调,袁鸿,等.斜齿轮成形磨削接触线优化研究[J].机械科学与技术,2012,31(8):1320‐1324.G u oE r k u o,H u a n g X i a o t i a o,Y u a n H o n g,e t a l.O p-t i m i z a t i o no fC o n t a c tL i n e f o rF o r m G r i n d i n g o f I n-v o l u t e H e l i c a l G e a r s[J].M e c h a n i c a lS c i e n c ea n dT e c h n o l o g y f o r A e r o s p a c e E n g i n e e r i n g,2012,31(8):1320‐1324.[5] 苏建新,邓效忠,任小中,等.基于数值模拟的内斜齿轮成形磨削砂轮修形方法[J].航空动力学报,2011,26(10):2383‐2393.S uJ i a n x i n,D e n g X i a o z h o n g,R e n X i a o z h o n g,e ta l.G r i n d i n g W h e e lD r e s s i n g M e t h o df o r I n n e r H e l i c a lG e a rF o r m G r i n d i n g B a s e d o nN u m e r i c a l S i m u l a t i o n[J].J o u r n a lo f A e r o s p a c e P o w e r,2011,26(10): 2383‐2393.[6] 李凌丰,陈远朋,刘波,等.大导程滚珠螺母磨削砂轮廓型精确设计和干涉消除[J].机械工程学报, 2008,44(1):109‐113.L i L i n g f e n g,C h e n Y u a n p e n g,L i uB o,e ta l.P r e c i s eP r o f i l e o fG r i n d i n g W h e e l a n d I n t e r f e r e n c eE l i m i n a-t i o n f o rH i g h‐l e a dB a l l‐n u t[J].J o u r n a l o fM e c h a n i-c a l E n g i n e e r i n g,2008,44(1):109‐113.[7] 方成刚,葛海燕,洪荣晶.砂轮偏心对单侧成形磨齿齿形误差的影响分析[J].计算机集成制造系统, 2012,18(11):2509‐2514.F a n g C h e n g g a n g,G eH a i y a n,W a n g R o n g j i n.E f f e c to fG r i n d i n g W h e e lE c c e n t r i c i t y o n U n i l a t e r a lG e a rF o r mG r i n d i n g P r o f i l eE r r o r[J].C o m p u t e r I n t e g r a t e d M a n u-f a c t u r i ng S y s t e m s,2012,18(11):2509‐2514.[8] 李儒荀.刀具设计原理与计算[M].南京:江苏科学技术出版社,1985.[9] 苏建新,邓效忠,任小中,等.斜齿轮成形磨削砂轮修形与仿真[J].农业机械学报,2010,41(10):219‐222.S u J i a n X i n,D e n g X i a o z h o n g,R e nX i a o z h o n g,e t a l.F o r mG r i n d i n g W h e e lD r e s s i n g a n dS i m u l a t i o nf o rH e l i c a l‐g e a r[J].T r a n s a c t i o n s o f t h eC h i n e s eS o c i e t yf o rAg r i c u l t u r a lM a chi n e r y,2010,41(10):219‐222.[10] 韦岗,贺前华,欧阳景正.关于多层感知器的函数逼近能力[J].信息与控制,1996,25(6):321‐324.W e iG a n g,H e Q i a n h u a,O u y a n g J i n g z h e n g.F u n c-t i o n A p p r o x i m a t i o n A b i l i t y o f M u l t i l a y e rP e r c e p-t r o n[J].I n f o r m a t i o na n d C o n t r o l,1996,25(6):321‐324.[11] 梁锡昌,邵明,吉野英弘,等.齿轮及其刀具制造的研究[M].重庆:重庆大学出版社,2001. [12] 李国龙,李先广,刘飞,等.拓扑修形齿轮附加径向运动成形磨削中的砂轮廓形优化方法[J].机械工程学报,2008,47(11):155‐162.L i G u o l o n g,L i X i a n g u a n g,L i uF e i,e t a l.M e t h o do fP r o f i l eO p t i m i z a t i o no f aF o r m G r i n d i n g W h e e l f o rG r i n d i n g w i t hA d d i t i o n a l R a d i a lM o t i o n o fT o p o l o-g i c a l l y M o d i f i e d G e a r[J].J o u r n a lo f M e c h a n i c a lE n g i n e e r i n g,2008,47(11):155‐162.[13] 陈敢,汪中厚,王锦华,等.多功能成型磨削机床:中国,C N201210253987.9[P].2012‐10‐17.(编辑 陈 勇)作者简介:汪中厚,男,1963年生㊂上海理工大学机械工程学院教授㊂主要研究方向为齿轮动态力学性能仿真㊁三维复杂曲面测量技术㊁C A E及其应用㊂获部级科技二等奖1项㊂朱文敏,男,1992年生㊂上海理工大学机械工程学院硕士研究生㊂李 刚,男,1986年生㊂上海理工大学机械工程学院博士研究生㊂耿 直,男,1990年生㊂上海理工大学机械工程学院硕士研究生㊂㊃1761㊃基于神经网络的修形斜齿轮成形磨削中的接触线优化方法 汪中厚 朱文敏 李 刚等Copyright©博看网. All Rights Reserved.。
齿轮高效精密磨削加工及表面完整性控制技术研究进展

齿轮高效精密磨削加工及表面完整性控制技术研究进展周春雷(中国航发哈尔滨东安发动机有限公司,黑龙江哈尔滨 150066)【摘要】随着机械工业的不断发展,对齿轮的精度、效率和寿命要求越来越高,因此需要研究和开发高效精密的齿轮磨削加工技术。
在此基础上,对齿轮磨削加工以及当下常用的精密磨削加工技术进行了研究,重点分析了硬齿轮加工技术、强力珩齿技术和齿轮多能场复合制造技术的应用,并进一步探讨了如何在齿轮磨削加工中做好齿轮表面的完整性控制,提出了相关建议和措施,以供参考。
关键词:齿轮精密磨削;加工技术;表面完整性;控制措施中图分类号:TG61 文献标识码:BDOI:10.13596/ki.44-1542/th.2024.02.046Research Progress of High Efficiency Precision Grinding and Surface Integrity Control Technology of GearZhou Chunlei(Air China Development Harbin Dong'an Engine Co., Ltd., Harbin, Heilongjiang 150066, CHN)【Abstract】With the continuous development of machinery industry, the precision, efficiency and life of gear are increasingly demanding, so it is necessary to research and develop efficient and pre⁃cise gear grinding technology. On this basis, the paper studies gear grinding and precision grinding technology commonly used at present, focuses on analyzing the application of hard gear machining technology, strong gear honing technology and gear multi-energy field composite manufacturing technology, and further discusses how to do a good job in the integrity control of gear surface in gear grinding processing, and puts forward relevant suggestions and measures for reference.Key words:gear precision grinding;processing technology;surface integrity;control measure1引言齿轮是一种广泛应用于机械传动领域的核心元件,其性能和质量对整个机械系统的运行有着重要影响。
斜齿轮成形磨削齿向修形齿面模型构造与误差评价
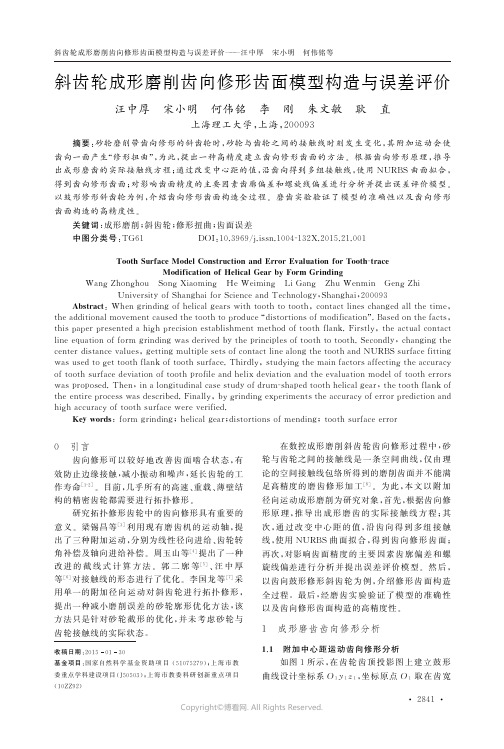
Un
i
ve
r
s
i
t
fShangha
if
o
rSc
i
enc
eandTe
chno
l
ogy,
Shangha
i,
200093
yo
Ab
s
t
r
a
c
t:Wheng
r
i
nd
i
ngo
fhe
l
i
c
a
lge
a
r
swi
t
ht
oo
t
ht
ot
oo
t
h,c
on
t
a
c
tl
i
ne
schangeda
l
lt
het
ime,
“
”
t
headd
对应的磨削接触点P (
xw ,
zw ),
P 点组成的曲
yw ,
ϕ = ϕ(
μ)
由式(
6)得rg = (
MΣMθ ) rw (
μ,
ϕ),最后可得实
际接触线上点的坐标为
xg = -m (
c
o
s
μ)
ϕ +a -ax
线,该 曲 线 在 砂 轮 坐 标
式(
18)是一个关于 μ 、
θ 和ϕ 的超越方程,不易求
得解析解.结合等误差算 法 和 牛 顿 迭 代 法 [11],遍
i
n
θs
i
nΣ -ygc
o
s
θs
i
nΣ +zgc
o
s
Σ +pθcos
斜齿轮的成形磨削逼近法研究
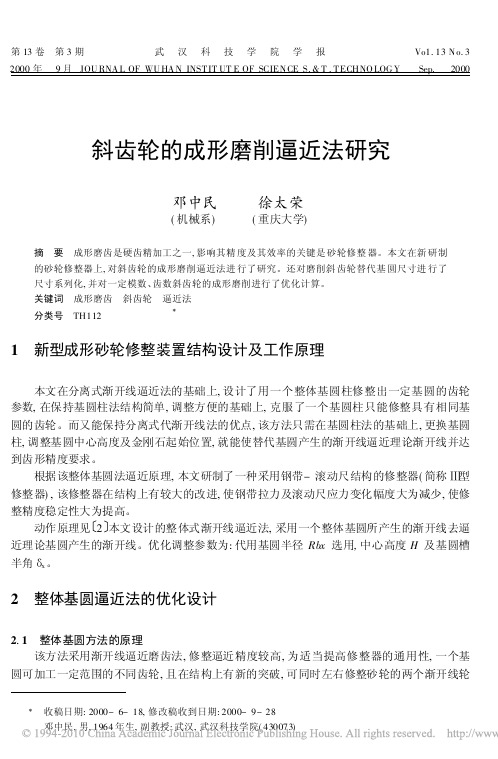
第13卷 第3期武 汉 科 技 学 院 学 报Vo1.13N o.3 2000年 9月 JOU RNA L OF WU HA N INST IT UT E OF SCIEN CE S.&T.T ECHNO LOG Y Sep. 2000斜齿轮的成形磨削逼近法研究邓中民(机械系)徐太荣(重庆大学)摘 要 成形磨齿是硬齿精加工之一,影响其精度及其效率的关键是砂轮修整器。
本文在新研制的砂轮修整器上,对斜齿轮的成形磨削逼近法进行了研究。
还对磨削斜齿轮替代基圆尺寸进行了尺寸系列化,并对一定模数、齿数斜齿轮的成形磨削进行了优化计算。
关键词 成形磨齿 斜齿轮 逼近法分类号 TH1121 新型成形砂轮修整装置结构设计及工作原理本文在分离式渐开线逼近法的基础上,设计了用一个整体基圆柱修整出一定基圆的齿轮参数,在保持基圆柱法结构简单,调整方便的基础上,克服了一个基圆柱只能修整具有相同基圆的齿轮。
而又能保持分离式代渐开线法的优点,该方法只需在基圆柱法的基础上,更换基圆柱,调整基圆中心高度及金刚石起始位置,就能使替代基圆产生的渐开线逼近理论渐开线并达到齿形精度要求。
根据该整体基圆法逼近原理,本文研制了一种采用钢带-滚动尺结构的修整器(简称 型修整器),该修整器在结构上有较大的改进,使钢带拉力及滚动尺应力变化幅度大为减少,使修整精度稳定性大为提高。
动作原理见2!本文设计的整体式渐开线逼近法,采用一个整体基圆所产生的渐开线去逼近理论基圆产生的渐开线。
优化调整参数为:代用基圆半径Rbx选用,中心高度H及基圆槽半角 x。
2 整体基圆逼近法的优化设计2.1 整体基圆方法的原理该方法采用渐开线逼近磨齿法,修整逼近精度较高,为适当提高修整器的通用性,一个基圆可加工一定范围的不同齿轮,且在结构上有新的突破,可同时左右修整砂轮的两个渐开线轮收稿日期:2000-6-18,修改稿收到日期:2000-9-28邓中民,男,1964年生,副教授;武汉,武汉科技学院(430073)图1 新型砂轮修整器结构简图1.转盘;2.基圆;3.滚动尺;4.压轮;5.钢带;6.压轮臂;7.金钢笔;8.8∀弹簧;9.滑轮;10.钢带;11.平衡轮;12.弹簧支架;13.弹簧;14.调节螺杆;13∀,15调节螺杆;16,16∀固定螺钉;18.固定轴销。
成形法磨削斜齿轮的齿形误差分析_张立功

文章编号:1004-2539(2009)01-0073-03成形法磨削斜齿轮的齿形误差分析张立功1 王 军2 邓效忠1(1河南科技大学机电工程学院, 河南洛阳 471003)(2河南科技大学车辆与动力工程学院, 河南洛阳 471003)摘要 在成形法磨削斜齿轮的过程中影响齿轮加工精度的原因很多;根据磨削加工过程,从成形砂轮廓形修形误差和砂轮与齿轮的相对位置误差两方面对其所产生的齿形误差进行了分析,并用数值方法模拟出齿形误差的大小;分析结果和数值模拟结果对设计数控成形磨齿机及编制数控成形磨齿工艺具有重要的参考价值。
关键词 成形磨削 斜齿轮 齿形误差 数值模拟0 引言成形磨齿法即利用成形砂轮来磨削齿轮的齿形,是齿轮精加工的方法之一,由于磨削效率高而越来越受到人们的重视,并得到了飞速的发展。
但是,在成形磨齿过程中,影响齿轮磨削加工精度的原因很多,为了顺利加工出所需精度的齿轮,就需要在磨削前将各加工参数调整到合理的范围内,因此,对磨削加工过程中可能产生齿形误差的各项因素进行深入分析是非常必要的。
本文所研究的成形磨削过程实况如图1所示。
先将工作台右移,由金刚轮修整砂轮,修整完成后再将工作台左移,调整好砂轮和齿轮的相对位置后开始磨削。
针对这种成形磨削过程,本文提出了一种用数值模拟分析齿形误差的新方法,分析的结果对设计数控成形磨齿机及编制数控成形磨齿工艺具有重要的参考价值。
图1 磨削过程实况(俯视图)根据图1所示磨削过程可知,成形法磨削斜齿轮的误差主要由机床设备精度引起的误差和操作者在加工过程中调整不到位引起的误差两部分组成。
由机床设备精度引起的误差往往比较复杂,是加工过程中无法控制的,这里主要讨论操作者在加工过程中调整不到位引起的误差,这部分误差主要有成形砂轮廓形修形误差和砂轮与齿轮的相对位置误差。
1 成形砂轮廓形修形误差引起的齿形误差分析 当刀具表面为回转面时,齿轮螺旋齿面和与此面共轭的刀具面的接触线是由齿面上的法线与刀具轴线相交点组成的,由齿轮螺旋齿面上的法线与刀具轴线相交的条件,可求出齿轮与刀具所有的接触点,把这些点连接起来,就构成一条空间的接触线,再将这条接触线绕刀具轴线回转就可得到刀具的回转面。
齿轮成形磨削工艺流程

齿轮成形磨削工艺流程齿轮成形磨削工艺流程是一种用于生产高精度齿轮的加工方法。
下面将详细介绍齿轮成形磨削的工艺流程。
第一步是选择合适的齿轮材料。
常见的齿轮材料有钢、铸铁和有色金属等。
根据实际应用需求和工作环境选择合适的材料。
第二步是齿轮设计。
根据使用要求,确定齿轮的模数、压力角、齿形等参数,并绘制齿轮图纸。
第三步是齿轮成形。
首先,根据齿轮参数和图纸,制作成形刀具。
然后,将齿轮材料固定在齿轮成形机上,通过成形刀具的运动,将齿轮材料按照图纸上的形状切削成形。
成形过程中需要保证加工速度和切削深度等参数的准确控制,以确保成品的准确度和表面质量。
第四步是齿轮硬化。
成形后的齿轮需要进行热处理,提高其硬度和耐磨性。
常见的硬化方式有渗碳、淬火和电渗碳等。
硬化过程中需要控制温度、时间和冷却速度等参数,以获得理想的硬化效果。
第五步是齿轮磨削。
经过硬化的齿轮表面会形成一层较硬的外表,需要进行磨削以提高其表面质量和准确度。
磨削工艺中需要使用专用的磨削设备和磨削刀具,按照齿轮参数和要求进行磨削操作。
磨削过程中需要注意切削液的选择和冷却,以避免磨削过程中过热对齿轮造成损伤。
第六步是齿轮检测。
完成磨削后的齿轮需要进行检测以确保其质量和准确度。
常见的检测方法有齿弧测量、齿距测量和齿宽测量等。
通过检测可以检查齿轮的形状、尺寸和表面质量等参数,以确保齿轮的功能和使用效果。
最后一步是齿轮组装。
完成所有工艺后,齿轮可以进行组装,用于各种机械设备中。
组装过程中需要注意齿轮的配合间隙和装配精度,以确保齿轮在工作中的可靠性和正常运行。
总之,齿轮成形磨削工艺流程是一套复杂而严谨的加工方法。
通过选择合适的材料、精确的成形、适当的热处理和精细的磨削,可以生产出高精度的齿轮。
在实际应用中,还要根据具体需求对工艺流程进行调整和优化,以满足不同的工程要求和使用环境。
在未来的发展中,齿轮成形磨削工艺流程将不断完善和创新,为齿轮加工提供更高效、更精确的解决方案。
研磨斜齿轮的需求描述

研磨斜齿轮的需求描述斜齿轮是一种常用的传动装置,广泛应用于机械设备中。
然而,由于长时间的运转或使用不当,斜齿轮表面可能会出现磨损或损坏,导致传动效率下降甚至无法正常工作。
为了解决这个问题,需要对斜齿轮进行研磨,恢复其表面的光滑度和精度。
研磨斜齿轮的首要需求是精确的尺寸和几何形状。
因为斜齿轮是一种齿轮,其传动效果取决于齿轮齿面的几何形状和尺寸精度。
研磨斜齿轮时,需要确保齿轮的齿数、模数、压力角等几何参数与设计要求一致,以保证齿轮与其他齿轮的配合和传动效率。
研磨斜齿轮还需要满足表面质量的要求。
斜齿轮的表面质量对传动效果有重要影响。
研磨斜齿轮时,需要确保齿轮表面光滑度高、无明显划痕和磨损,以减小齿轮在运转时的摩擦损失和噪音产生,提高传动效率。
研磨斜齿轮还需要考虑齿面硬度的要求。
齿轮在传动时承受着较大的载荷和摩擦,因此需要具有一定的硬度来保证其使用寿命和传动效果。
研磨斜齿轮时,需要控制好齿面硬度,避免过硬或过软,以确保齿轮在使用过程中不易变形或损坏。
研磨斜齿轮还需要考虑齿轮的材料选择。
不同的材料具有不同的硬度、强度和耐磨性等特性,对研磨工艺和效果都会有影响。
因此,在研磨斜齿轮之前,需要根据实际情况选择合适的材料,以确保研磨后的斜齿轮能够满足使用要求。
研磨斜齿轮还需要考虑研磨工艺和设备的选择。
研磨斜齿轮是一项精密的加工工艺,需要使用专门的研磨设备和工具,以确保研磨效果的准确性和稳定性。
同时,还需要根据齿轮的具体要求选择合适的研磨工艺,如外圆磨削、内圆磨削等,以获得最佳的研磨效果。
研磨斜齿轮的需求描述主要包括精确的尺寸和几何形状、良好的表面质量、适当的齿面硬度、合适的材料选择以及研磨工艺和设备的选择。
只有满足这些需求,才能够有效地研磨斜齿轮,恢复其传动效果,延长其使用寿命。
因此,在进行斜齿轮研磨之前,需要充分了解和理解这些需求,并按照要求进行相应的操作和处理。
- 1、下载文档前请自行甄别文档内容的完整性,平台不提供额外的编辑、内容补充、找答案等附加服务。
- 2、"仅部分预览"的文档,不可在线预览部分如存在完整性等问题,可反馈申请退款(可完整预览的文档不适用该条件!)。
- 3、如文档侵犯您的权益,请联系客服反馈,我们会尽快为您处理(人工客服工作时间:9:00-18:30)。
第13卷 第3期武 汉 科 技 学 院 学 报Vo1.13N o.3 2000年 9月 JOU RNA L OF WU HA N INST IT UT E OF SCIEN CE S.&T.T ECHNO LOG Y Sep. 2000斜齿轮的成形磨削逼近法研究邓中民(机械系)徐太荣(重庆大学)摘 要 成形磨齿是硬齿精加工之一,影响其精度及其效率的关键是砂轮修整器。
本文在新研制的砂轮修整器上,对斜齿轮的成形磨削逼近法进行了研究。
还对磨削斜齿轮替代基圆尺寸进行了尺寸系列化,并对一定模数、齿数斜齿轮的成形磨削进行了优化计算。
关键词 成形磨齿 斜齿轮 逼近法分类号 TH1121 新型成形砂轮修整装置结构设计及工作原理本文在分离式渐开线逼近法的基础上,设计了用一个整体基圆柱修整出一定基圆的齿轮参数,在保持基圆柱法结构简单,调整方便的基础上,克服了一个基圆柱只能修整具有相同基圆的齿轮。
而又能保持分离式代渐开线法的优点,该方法只需在基圆柱法的基础上,更换基圆柱,调整基圆中心高度及金刚石起始位置,就能使替代基圆产生的渐开线逼近理论渐开线并达到齿形精度要求。
根据该整体基圆法逼近原理,本文研制了一种采用钢带-滚动尺结构的修整器(简称 型修整器),该修整器在结构上有较大的改进,使钢带拉力及滚动尺应力变化幅度大为减少,使修整精度稳定性大为提高。
动作原理见2!本文设计的整体式渐开线逼近法,采用一个整体基圆所产生的渐开线去逼近理论基圆产生的渐开线。
优化调整参数为:代用基圆半径Rbx选用,中心高度H及基圆槽半角 x。
2 整体基圆逼近法的优化设计2.1 整体基圆方法的原理该方法采用渐开线逼近磨齿法,修整逼近精度较高,为适当提高修整器的通用性,一个基圆可加工一定范围的不同齿轮,且在结构上有新的突破,可同时左右修整砂轮的两个渐开线轮收稿日期:2000-6-18,修改稿收到日期:2000-9-28邓中民,男,1964年生,副教授;武汉,武汉科技学院(430073)图1 新型砂轮修整器结构简图1.转盘;2.基圆;3.滚动尺;4.压轮;5.钢带;6.压轮臂;7.金钢笔;8.8∀弹簧;9.滑轮;10.钢带;11.平衡轮;12.弹簧支架;13.弹簧;14.调节螺杆;13∀,15调节螺杆;16,16∀固定螺钉;18.固定轴销。
廓,精度稳定性好,使修整效率大大提高。
见图2,令待磨齿轮中心坐标系ox y 渐开线AB 理论基圆半径Rbo 。
修整器所选用的代用基圆半径为R bx ,在坐标系O 1X ∀Y ∀产生的渐开线A ∀B ∀。
变动参数,代用基圆半径R bx ,修整器调节高度h,以及金刚石在O 1X ∀Y ∀坐标系中的基圆槽半角 x ,就可以改变代用渐开线的形状和位置。
由渐开线性质可知,渐开线的形状取决于基圆大小,基圆愈小,则渐开线愈曲,反之则愈平直。
而代用渐开线的位置由调节参数h, x 决定,当参数R bx ,h, x (可用金刚笔伸长量 L = x R b0代替,以简化修整器结构调整)取某最佳值时,可使逼近渐开线AB 的逼近精度满足齿形精度及齿厚精度要求。
为使代用基圆尺寸系列化,在进行调整的最优选择时,先把代用基圆半径尺寸离散化,即按一定规律的尺寸数组制造,供优化设计时由计算机自动选用。
2.2 优化模型的建立用盘状砂轮成形磨削直齿轮,砂轮轴向截形轮廓始终与端面齿形相同,与砂轮直径变化无关。
而磨斜齿轮时,砂轮与齿轮的接触线为一空间曲线,该曲线的形状取决于齿轮参数及砂轮直径。
该空间接触线绕砂轮轴旋转便成为砂轮工作曲面。
因图2 整体逼近数学模型此,砂轮的精确轴向截形并不等于斜齿轮的法向齿形,而应由计算得到。
用盘形砂轮加工螺旋面时,相对坐标系如图3所示:已知右旋渐开线螺旋面上方程,r=r b #cos ( 0+u+ )+r b #u #sin ( 0+u+ )r b #sin ( 0+u+ )+r b #u #cos( 0+u+)(1)经坐标变换,接触点M 在砂轮坐标系方程--sin 2 武 汉 科 技 学 院 2000年砂轮回转曲面的轴向截形方程:R=X 2+Y 2Z=Z(3)变换到修整器坐标系O 1X 1Y 1中坐标:X 1=-Z Y 1=L-R(4)又由接触条件式矢量方程:(k ∃R)#n=0(5)得: -r 2b u p 2-(P #L #tan !+r 2b )#tan !P 2+r b (p #tan !+L)p 2#sin ( 0+u+ )=0(6)令 0+u+=∀ ∀为参变量,则(6)可简化 =cos 2(#b )r 2b (∀- 0)+(p.L.tan !+r 2b )#tan !-r b (p.tan !+L)p 2#sin( 0+u+)(7)由(7)代入(2)(3)(4)式可求出O 1X 1Y 1坐标系中砂轮截面方程根据渐开线齿轮精度测量是沿渐开线方向测量齿形误差和齿厚误差,计算齿形误差如图2,过理论渐开线A ∀B ∀上P ∀点,则误点矢量∃= h +op %&-op%&(8)式中 op %&=XY op ∀%&=X 2Y 2(9) ∃=|∃i |-cos ( 0+%)# i #sin ( 0+%)# j(10)2.3 目标函数的确定考虑到齿轮精度标准中对齿形误差和齿厚误差均有公差要求,为使逼近误差达到最小,可选择同时控制齿形误差,齿厚误差达到最小。
因此,这里是一个多目标函数的最优化问题。
为了使各个分目标函数能均趋向各自的最优值。
这里采用加权组合法的统一目标法。
F =F (R bx ,h, L )=&1# J +&2# S =&1[max {∃i}-min {∃i }]+&2[(∋∃i)/n]式中 &j =&1j ∃&2j (j =1,2)&1j %%%反映第j 项分目标相对重要性的加权因子&2j %%%第j 项目标的校正加权因子,用于调整各分目标间在量级差别方面的影响。
在这里是调整在迭代过程中使 J J %和 S S %大致相等的加权因子取 &1=&11∃&21=u ( J )2;&2=1( S )2u =2E +3~10E +32.4 设计变量及其类型的选取在处理整体基圆代渐开线逼近优化问题时,因目标函数是使齿形、齿厚误差最小,由图3知:逼近渐开线的形状,位置取决于参数R bx ,h, L.由渐开线性质知:渐开线形状取决于基圆的大小,当逼近基圆与理论基圆相同时,h =0, L =0时,两渐开线重合,即逼近误差为零,如果把变量Rbx ,h, L 都取为连续变量,则计算机优化结果必定是R bx =R bo ,h =0, L =0,而设有达到预期的目的,即一个基圆在一定范围内的通用性,为解决这一问题,本程序采用把替代基圆取为离散变量,即预选把一定尺寸范围的基圆尺寸按一定规则的数列排列。
3第3期 邓中民 等: 斜齿轮的成形磨削逼近法研究2.5 优化方法的选取该优化是一个混合变量(即有连续变量又有离散变量)的优化问题,因该优化问题的目标函数比较复杂,很难求导数。
考虑到惩罚函数法与不用求梯度的无约束最优化方法相结合的方法是有效的方法,本文在原优化方法的基础上,对其功能进行了扩充,把全连续就是改进为连续型+离散型的通用混合型惩罚函数法。
2.6 基圆尺寸数组的确定在模数一定时,随着齿数z 增大,基圆半径愈小,渐开线愈平直。
当逼近基圆与理论基圆相差愈大,逼近误差愈大。
优化设计表明:当达到同一逼近精度时,齿轮齿数较小时,逼近基圆与理论基圆的差异允许增大。
优化计算还表明:当齿轮齿数一定时,模数愈大,则逼近误差愈大。
由以上优化计算分析:可把基圆尺寸数的数列取为一变公比等比级数。
R b1,R b2,(R bn (R bn =k.R bn -1)其中,等比系数K 与模数齿数有关。
当逼近精度为6级标准时:K =1.025~1.05小模数;或1.05~1.1大模数由上述优化计算及分析表明:基圆尺寸数组公比系数在大模数小齿数时,取较小值,小模数大齿数时,取较大值。
当K 取值太小时,基圆柱数量增多,K 取值达到结定的逼近精度。
因此K 取值原则,在保证达到给定的逼近精度条件下尽量取大一点,以使基圆柱数目减小。
本程序中K 取 K ={1.05(R j <30)或1.1(R j )30)}得出基圆柱系列尺寸为:18,19,20,21,22,23,24,25,26.6,28,29;30,33,36,40,48,53,58,64,71,78,86,94,104,114,125,138,152,167,183,202,222,244,268,295,325,358,393,433,476,523,576,633,697,766,843,927,10202.7 最优调整参数计算结果的分析表1齿轮调整参数表序齿轮参数选用调整参数精度参数号M Z #基圆半径r b Rbx h L ff (um ) f f /ff T s(um) S /T s 1160528.328.0-0.1340.53100.18158.40.2232240737.87401.2450.98510.50.231365.7-0.2093220919.03191.21030.1317110.23176.650.03643201228.82290.34051.89011.50.23576.650.32154401377.153781.1252.0294130.19876.650.29265201548.6448-3.3120.237160.34787.60.23采用上述混合变量惩罚优化方法计算的最优替代基圆半径,修整器高度调整参数H ,以及金刚石起始位置伸长变动量见表1,不同模数,不同齿数时的优化计算齿形误差比式 ff /ff 见图4。
由图可见:见该方法得出的优化计算齿形误差比均在0.35以下,从以上计算分析,把替代基圆尺寸以一定的等比级数离散化,得出的计算齿形误差比基圆上与模数,齿数无关。
而且保证了替代基圆尺寸的系列化,有利于用此类整体基圆代渐开线方法磨削斜齿轮时,逼近修整法的应用推广。
4 武 汉 科 技 学 院 2000年3 扩展修整器通用性的结构分析采用逼近精度高,精度稳定性好,调整方便,结构简单,制造方便的整体式渐开线逼近法,即采用适当的基圆产生的渐开线去拟合理化基圆产生的渐开线,使用计算机优化调整参数,可以磨合一定基圆范围的齿轮,使基圆柱尺寸系列化。
修整器的合理结构参数随着基圆直径变化而变化,因为当基圆直径改变时,左右滚动尺与水平面的对称平角也改变,必须改变钢带支承轮O 3的位置,压紧轮压在滚动尺上的作用点,也不是滚动尺与基圆切点,而偏离距离 L ,为了使为个偏距 L 不致太大,必须改变压轮臂转轴中心位置,为二个中心位置的改变可通过在转盘1上同一圆一打上均匀分布的安装孔,为些孔之间的角度及孔与中心的半径值通过结构优化计算确定。