高碳高铬轧辊用钢激光相变强化研究
攀钢协力公司激光表面强化技术通过鉴定
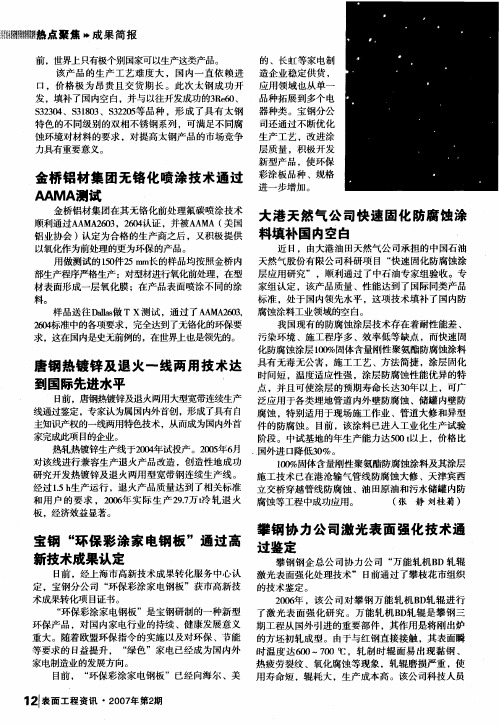
金桥铝材集 团在其无铬化前处理氟碳喷涂技术 大港 天 然气公 司快 速 固化 防腐 蚀 涂 顺利 通过 A M 20 ,20认证 ,并被 A MA( 国 A A 63 64 A 美 铝业协会 ) 认定为合格 的生产商之后 ,又积极提供 料填补国内空白 以氧化作为前处理的更为环保的产品。 近 日,由大港 油 田天然 气公 司承 担 的中 国石油 用做 测试 的 1o ̄2 m 的样 品均按 照金桥 内 天然气股份有限公司科研项 目 “ 5 f 5i a r长 快速 固化防腐蚀涂 部生产程序严格生产 : 对型材进行氧化前处理 ,在型 层应用研究” ,顺利通过 了中石油专家组验收。专 材表 面形 成一 层氧 化膜 ;在 产 品表 面喷涂 不 同的涂 家组认定 , 该产品质量 、性能达到 了国际同类产品 标准,处于国内领先水平 ,这项技术填补了国内防 料。 样 品送往 D1 . ̄做 Tx测 试 ,通 过 了 A MA 63 1 A 20, 腐蚀涂料工业领域的空白。 准中的各项要求 ,完全达到了无铬化的环保要 我国现有的防腐蚀涂层技术存在着耐性能差 、 污染环境 、 施工程序多 、效率低等缺点 ,而快速 固 求, 这在国内是史无前例的,在世界 匕 也是领先的。 化防腐蚀涂层 10 0%固体含量刚性聚氨酯防腐蚀涂料 唐 钢热镀 锌及 退火 一线两 用技 术达 具有无毒无公害 ,施工工艺 、方法简捷 ,涂层固化 时间短,温度适应性强 ,涂层防腐蚀性能优异的特 到国际先进水平 点, 并且可使涂层 的预期寿命长达3年以上 ,可广 0 日 , 前 唐钢热镀锌及退火两用大型宽带连续生产 泛应用 于各类埋地管道内外壁防腐蚀 、储罐内壁防 线通过鉴定 ,专家认为 属国内外 首创 ,形 成了具有 自 腐蚀 ,特别适用于现场施工作业 、管道大修 和异型 主知识产权 的一线两用 特色技 术 ,从 而成为国内外 首 件 的 防腐蚀 。 目前 ,该涂 料 已进 人工 业化 生产 试验 家完成此项 目的企业 。 阶段 。 中试 基地 的年生 产能 力达 50t 0 以上 ,价 格 比 热轧热镀锌生产线于20 年试投产。20年6 国外 进 口降低 3 %。 04 05 月 0 对该线进行兼容生产退火产品改造 ,创造性地成功 10 0%固体含量刚性聚氨酯防腐蚀涂料及其涂层 研究 开发 热镀 锌及 退火 两用 型宽 带钢 连续 生产 线 。 施工技术已在港沧输气管线防腐蚀大修 、天津宾西
冷轧辊各种毛化工艺简介与激光毛化的比较

1 前言2 表面粗糙度的研究表面粗糙度的分类对表面粗糙度的控制3 各种毛化工艺的比较喷丸毛化技术电火花毛化技术激光毛化技术4 激光毛化工艺的应用激光毛化工艺可显着提高轧辊使用寿命·表面改性与细晶强化作用·毛化形貌的耐磨作用·表面应力松驰的韧化作用对冷轧生产的作用•避免轧制时“粘钢”•提高轧制速度和压下率•减轻轧制“横纹”•消除退火产生的“粘连”•改善轧件表面质量•在普通冷带轧机上实现异步轧制提高产品使用性能•改善深冲性能•提高涂装性能和鲜映度•改善抗摩擦性能•新板型的开发1 前言具有特殊表面形貌的冷轧薄钢板在制造业中有着广泛的应用,特别是在汽车和家电产业中。
在冷轧薄钢板的生产和应用研究中,人们发现冷轧板的一系列表面形貌参数对钢板的冲压性、涂层后光亮度等工艺性能有重要影响,而冷轧板的表面形貌在很大程度上又取决于冷轧生产过程中工作辊及平整辊的表面形貌。
实质上,轧制钢板的表面形貌是轧辊表面形貌的衰减性“拷贝”。
因此,研究、控制冷轧轧辊及冷轧钢板表面形貌的轧辊毛化技术应运而生。
轧辊毛化技术包括毛化钢板表面形貌与其工艺性能之间关系的研究、轧辊毛化工艺过程的研究及毛化设备的研制。
80年代以来,先进工业国家对轧辊毛化技术进行了许多研究并付诸工业应用,随着汽车、家电等产业的发展,对冷轧薄板提出了更高的品质要求。
冷轧钢板的表面形貌和工艺性能研究发现,为了改善冷轧钢板的冲压性能和涂层光亮度等工艺性能,描述冷轧板的表面形貌,要引入包括传统的表面粗糙度在内的一系列参数作为判据。
表面粗糙度Ra:毛化轧辊的Ra一般在l~10μm 之间。
Ra较大,有利于改善短材的冲压性能和涂层牢固度,而Ra较小时,有利于提高板材涂层后的光亮度。
峰值密度PPI:定义为每英寸长度内高度大于m 的表面峰值数。
PPI值越大,涂层粘着力越好。
波度wca:钢板表面的凹凸不平呈不同波长的周期。
以上几个参数中,既独立描述冷轧板的表面形貌,又彼此相互影响。
拉拔方式对高碳钢丝组织性能的影响
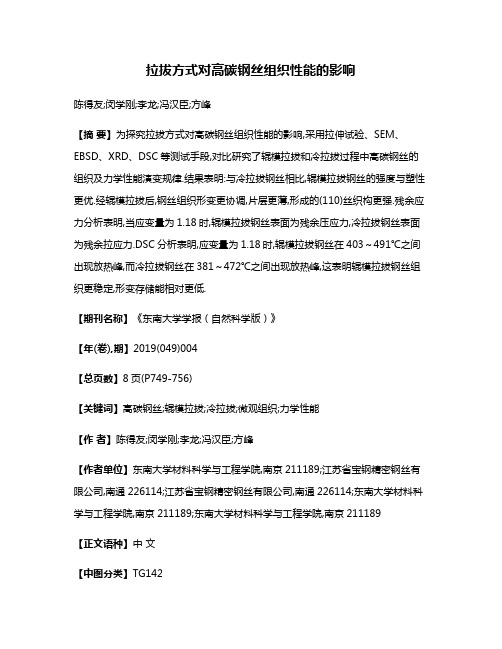
拉拔方式对高碳钢丝组织性能的影响陈得友;闵学刚;李龙;冯汉臣;方峰【摘要】为探究拉拔方式对高碳钢丝组织性能的影响,采用拉伸试验、SEM、EBSD、XRD、DSC等测试手段,对比研究了辊模拉拔和冷拉拔过程中高碳钢丝的组织及力学性能演变规律.结果表明:与冷拉拔钢丝相比,辊模拉拔钢丝的强度与塑性更优.经辊模拉拔后,钢丝组织形变更协调,片层更薄,形成的(110)丝织构更强.残余应力分析表明,当应变量为1.18时,辊模拉拔钢丝表面为残余压应力,冷拉拔钢丝表面为残余拉应力.DSC分析表明,应变量为1.18时,辊模拉拔钢丝在403~491℃之间出现放热峰,而冷拉拔钢丝在381~472℃之间出现放热峰,这表明辊模拉拔钢丝组织更稳定,形变存储能相对更低.【期刊名称】《东南大学学报(自然科学版)》【年(卷),期】2019(049)004【总页数】8页(P749-756)【关键词】高碳钢丝;辊模拉拔;冷拉拔;微观组织;力学性能【作者】陈得友;闵学刚;李龙;冯汉臣;方峰【作者单位】东南大学材料科学与工程学院,南京211189;江苏省宝钢精密钢丝有限公司,南通226114;江苏省宝钢精密钢丝有限公司,南通226114;东南大学材料科学与工程学院,南京211189;东南大学材料科学与工程学院,南京211189【正文语种】中文【中图分类】TG142大应变珠光体钢丝通常是高碳钢盘条经冷拉拔形变制得,因其兼具高强度和良好的韧性而被广泛应用于汽车轮胎钢帘线、大跨度桥梁斜拉索以及高层建筑等重要领域[1-3].冷拉拔是制备高强度钢丝的主要技术,但其存在表面摩擦阻力及剪切变形较大等不足,这些因素不仅会造成模具磨损,影响表面质量,甚至还会影响钢丝使用性能.辊模拉拔因其具有低摩擦、高速减径以及低能耗等优势,在低碳钢中已得到广泛应用[4-7],随着辊模材料及模具制备技术的突破,该技术有可能成为高强度钢丝制备技术的有益补充.与传统冷拉拔相比,辊模拉拔所需拉拔力较小,能耗更低,组织变形更均匀,在避免出现中心裂纹的情况下,具有较大的道次压缩率[5].形变后,低碳钢丝的强塑性均提升,表面性能得到改善[6-7];高碳钢丝的表面残余拉应力减小,横截面应变分布更均匀,钢丝表面温升低,表面质量更高[8-9].目前针对多道次辊模拉拔高碳钢丝的力学性能以及组织变形机理缺乏系统的研究.因此,本文通过拉伸试验、SEM、EBSD、XRD、DSC等测试手段,对比研究了多道次辊模拉拔和冷拉拔过程中高碳钢丝的力学性能及组织变形特征,进一步探讨了辊模拉拔技术在制备高强度钢丝方面的可行性,以期为辊模拉拔技术在高强度钢丝制备中的应用奠定基础.1 实验材料与方法实验材料为宝钢提供的SWRS72A高碳钢盘条(直径Φ=5.5 mm),其化学成分如表1所示.图1为辊模拉拔和冷拉拔工艺示意图.将盘条酸洗硼化后,再分别进行辊模拉拔(设备型号CL30 C1 33)和冷拉拔(设备型号LW1/600H76/600)处理,经多道次拉拔至3.05 mm,总应变量ε为1.18.表1 盘条的化学成分 %w(C)w(Mn)w(Si)w(Cr)w(Ni)w(S)w(P)w(Fe)0.7040.5010.1970.0140.012 90.004 60.005 9Bal.(a) 辊模拉拔 (b) 冷拉拔图1 2种拉拔工艺示意图采用CMT5105微机控制电子万能试验机测试钢丝样品的抗拉强度(拉伸温度25 ℃,拉伸速率2 mm/min).在Sirion-400场发射扫描电子显微镜(SEM)下观察钢丝纵截面的显微组织,并使用Nano Measurer统计片层间距.通过电子背散射衍射技术(EBSD)采集钢丝纵截面中心区域的晶体学取向信息,测试设定参数为:步长1.5 μm,区域宽度500 μm×400 μm,放大倍数500倍,经OIM analysis 处理分析织构演变规律.采用线切割在离钢丝(ε=1.18)表面0.2 mm处沿纵向切取厚1 mm、长8 mm的样品,经机械抛光及二氧化硅抛光液抛光后,使用智能X 射线衍射仪(Smartlab 3)测试其残余应力.测试设定参数:衍射源为CuKα,电压40 kV,电流30 mA,扫描范围80°~84°,扫描速度0.001 2°/s.选取试样表面法线与(211)晶面法线的夹角Ψ为0°、15°、30°、45°,测试不同Ψ下的(211)晶面衍射峰.由布拉格方程2dsinθ=nλ(其中,d为晶面间距;θ为布拉格角;n为衍射指数;λ为入射线波长)可知[10],当入射线波长一定时,应力在引起晶面间距变化时,衍射角也会随之改变,根据XRD的sin2Ψ法则[10-11],利用Jade 6计算残余应力.对钢丝样品(ε=1.18)进行差热扫描分析(STA449 F3),测试温度范围为25~550 ℃,升温速率为20 ℃/min,保护气体为氩气.采用透射电子显微镜(JEM2000EX)分析不同拉拔方式下钢丝纵向组织形貌演变.2 试验结果与分析2.1 宏观力学性能图2(a)为辊模拉拔和冷拉拔钢丝的抗拉强度随应变量变化曲线.可以看到,不同拉拔方式下钢丝的抗拉强度均随应变量的增加而增加,同一应变量下,辊模拉拔钢丝的抗拉强度均高于冷拉拔;当应变量为1.18时,辊模拉拔钢丝的强度为1 583 MPa,冷拉拔钢丝的强度为1 493 MPa,辊模拉拔钢丝的强度较冷拉拔提升约6%.图2(b)为辊模拉拔和冷拉拔钢丝的断面收缩率与应变量关系曲线.可以看到,冷拉拔钢丝的断面收缩率随应变量的增加而下降,而辊模拉拔钢丝的断面收缩率变化不大.综合可知,经辊模拉拔形变后,钢丝的强度与塑性均优于冷拉拔钢丝.2.2 珠光体组织形貌图3为不同应变量下的组织形貌照片.可以看到,未经形变的盘条组织呈等轴状,层片平直排列,方向随机分布.经辊模拉拔后,当应变量为0.23时,层片呈2种典型的形态:与拉拔轴向夹角较小的层片被均匀拉长、减薄,而与拉拔轴向夹角较大的层片发生剪切、弯折变形[12],如图3(b)中A、B区域所示.当应变量增加到0.74时,珠光体层片逐步平行于拉拔轴向排列,且进一步减薄.应变量为1.18时,层片变得更加细长,珠光体组织整体保持较好的层片结构.经冷拉拔后,当应变量为0.23时,图3(e)中A区域层片发生剪切变形,且剪切方向与拉拔方向夹角较大,B区域与拉拔轴向夹角较大的层片发生弯折变形,弯折方向朝向拉拔轴向.当应变量增加到0.74时,因较大剪切应力的存在,渗碳体片在剪切位置产生应力集中而发生断裂[13-14],如图3(f)中C区域所示.应变量为1.18时,珠光体层片基本平行于拉拔方向,局部观察到断裂、碎化的渗碳体颗粒,如图3(g)中D区域所示.(a) 抗拉强度(b) 断面收缩率图2 不同拉拔方式下钢丝力学性能比较(a) 原始盘条(ε=0)(b) 辊模拉拔(ε=0.23)(c) 辊模拉拔(ε=0.74)(d) 辊模拉拔(ε=1.18)(e) 冷拉拔(ε=0.23)(f) 冷拉拔(ε=0.74)(g) 冷拉拔(ε=1.18)图3 不同应变量下钢丝组织形貌图(纵截面)由不同拉拔方式下的组织形貌可知,两者在直观上无明显差异,为进一步分析组织形变特征,采用Nano Measurer统计了不同拉拔方式下钢丝组织中的珠光体片层间距(相邻铁素体片层中心的距离).图4为钢丝心部与边缘处片层间距随应变量变化曲线.可以看到,各应变量下,辊模拉拔钢丝心部与边缘的片层间距相近,而冷拉拔钢丝心部与边缘的片层间距则相差较大,表明其组织变形不均匀.图5为平均片层间距与应变量关系曲线.可以看到,辊模拉拔和冷拉拔钢丝的平均片层间距均随应变量的增加而不断减小,经辊模拉拔后,同一应变量下,钢丝的平均片层间距小于冷拉拔状态.此外,观察误差棒可知,冷拉拔钢丝的平均片层间距波动较大,辊模拉拔钢丝的平均片层间距波动较小.这表明,辊模拉拔方式更有利于钢丝片层组织的协调变形.(a) 辊模拉拔(b) 冷拉拔图4 钢丝心部与边缘处片层间距随应变量变化曲线图5 平均片层间距随应变量变化曲线综合比较2种拉拔变形过程可知,随着应变量的增加,钢丝的片层组织均沿拉拔方向逐渐减薄,区别在于,辊模拉拔钢丝片层组织形变更协调,促进了片层的减薄.2.3 EBSD织构演变图6为不同拉拔方式下钢丝纵截面取向成像图.可以看到,原始盘条组织呈等轴状,不同颜色的晶粒代表不同的取向,未形变盘条晶粒取向随机分布,呈各向异性;形变后,组织沿拉拔方向拉长,晶粒尺寸得到细化,产生择优取向.经OIM analysis 处理后,得到不同拉拔方式下不同应变量钢丝沿拉拔方向的反极图,如图7所示.可以看到,原始盘条中存在较弱的〈110〉丝织构,在2种拉拔变形方式下,随着应变量的增加,〈110〉丝织构均在逐渐增强.根据图7作出不同拉拔方式下〈110〉丝织构强度与应变量关系曲线,如图8所示.可以看到,形变后,〈110〉丝织构强度均随应变量的增加而增加;两者相比,同一应变量下,辊模拉拔钢丝产生的〈110〉丝织构强度高于冷拉拔状态,且织构强度差值随应变量的增加呈增大趋势.(a) 原始盘条(ε=0)(b) 辊模拉拔(ε=1.18)(c) 冷拉拔(ε=1.18)图6 不同拉拔方式下钢丝取向成像图(纵截面)(a) 原始盘条(ε=0)(b) 辊模拉拔(ε=0.49)(c) 辊模拉拔(ε=0.74)(d) 辊模拉拔(ε=1.18)(e) 冷拉拔(ε=0.49)(f) 冷拉拔(ε=0.74)(g) 冷拉拔(ε=1.18)图7 不同应变量下的织构反极图(纵截面)图8 〈110〉丝织构强度随应变量变化曲线2.4 残余应力分析采用XRD测试了不同拉拔形变钢丝(ε=1.18)在不同Ψ角下铁素体(211)晶面对应衍射峰的变化,如图9所示.可以看到,随Ψ角的增大,辊模拉拔钢丝中铁素体(211)晶面的衍射峰逐渐向右偏移,对应的衍射角逐渐增大,如图9(a)所示.冷拉拔钢丝中铁素体(211)晶面的衍射峰逐渐向左偏移,对应的衍射角逐渐减小,如图9(b)所示.(a) 辊模拉拔(b) 冷拉拔图9 应变量为1.18时铁素体(211)晶面不同Ψ角的XRD图根据半高宽法确定不同拉拔方式下不同Ψ角的铁素体(211)晶面衍射角,计算对应的晶面间距,作出(211)晶面间距d与sin2Ψ的关系曲线,如图10所示.可以看到,辊模拉拔钢丝中铁素体(211)晶面间距与sin2Ψ成负线性关系,而冷拉拔钢丝中铁素体(211)晶面间距与sin2Ψ成正线性关系.残余应力计算公式如下:(1)σ=KM(2)(4)(4)式中,εΨ为与表面成任意Ψ角的(211)晶面的应变;dΨ为不同Ψ角上的(211)晶面间距;d0为试样表面法线与(211)晶面法线平行时的晶面间距;K为常数;M为因变量;E为弹性模量;υ为泊松比.图10 铁素体(211)晶面间距与sin2Ψ关系曲线结合图10结果,由式(1)~(4)可知[10-11,15]:残余应力σ正比于M,当M<0时,表现为残余压应力;当M>0时,表现为残余拉应力.因此,经辊模拉拔后,M<0,钢丝表面为残余压应力;而对于冷拉拔钢丝,M>0,钢丝表面为残余拉应力.利用Jade软件计算表面残余应力大小.结果表明:经辊模拉拔后,钢丝表面残余压应力约为(146±20) MPa;而经冷拉拔后,钢丝表面残余拉应力约为(154±18) MPa.2.5 DSC分析图11给出了辊模拉拔和冷拉拔钢丝(ε=1.18)的DSC曲线.可以看到,辊模拉拔钢丝在403~491 ℃之间出现放热峰,峰值温度为446 ℃;冷拉拔钢丝在381~472 ℃之间出现放热峰,峰值温度为408 ℃.在放热温度区间内,放热峰的产生主要与渗碳体发生球化现象[16-18]有关.辊模拉拔钢丝中渗碳体发生球化的温度更高,这表明辊模拉拔方式下渗碳体片具有更好的热稳定性,形变存储能相对更低.比较峰值温度后半段曲线可知,冷拉拔钢丝DSC曲线的斜率高于辊模拉拔,表明冷拉拔钢丝组织放热效应更明显.图11 不同拉拔方式下应变量为1.18时钢丝的DSC曲线3 讨论不同拉拔方式下,应力的不同是导致钢丝显微组织变化的主要因素.在一个道次的辊模拉拔变形过程中,钢丝横截面形状变化以及受力分析如图12所示.图中,T为拉应力,C为压应力.可以看到,与冷拉拔相比,一个道次的辊模拉拔过程可分为2个阶段:首先钢丝横截面由初始的圆形变化为椭三角形,然后又变化为圆形.钢丝在一个道次经历的2次变形中,表面各部分受力状态不同,前后两个阶段相同位置处的钢丝表面受力状态相反,这充分促进了钢丝组织的塑性流动.此外,在拉拔过程中,钢丝轴向拉应力较小,径向压应力较大,这种倾向于轧制的应力状态,显著改善了难变形金属制品高碳钢丝的塑性.研究表明[13-14,19],当初始片层方向平行于拉拔轴向时,拉拔阻力最小,片层组织沿拉拔方向拉长、减薄;当初始片层方向与拉拔方向夹角小于30°时,珠光体片层将发生转动,并沿拉拔轴向减薄;当初始片层方向与拉拔轴向夹角大于30°时,拉拔阻力最大,片层组织以剪切变形方式发生断裂、破碎.结合2.2节的组织形貌及2.5节的DSC曲线特征可知,辊模拉拔产生的较软应力状态,使得钢丝片层间距较小,这表明,辊模拉拔形变方式下,更多渗碳体片的排列位向处于有利取向,片层形变阻力小,主要表现为拉长、减薄特征.冷拉拔钢丝片层间距较大,这表明,冷拉拔形变方式下,较多渗碳体片的排列位向处于不利取向,片层形变阻力大,主要表现为扭折、剪切至断裂.DSC结果显示,冷拉拔钢丝片层组织形变存储能更高,这表明,冷拉拔钢丝产生的变形程度较大,致使较多的渗碳体片发生破碎.因此,相较于冷拉拔,辊模拉拔钢丝组织形变更协调.(a) 钢丝横截面形状变化(b) 受力示意图图12 辊模拉拔一个道次形变过程在拉拔形变过程中,通常形成铁素体〈110〉丝织构有2种途径:一种是铁素体位错滑移,另一种是片层的转动使铁素体〈110〉取向接近拉拔轴向.辊模拉拔钢丝片层间距更小,更多渗碳体片的排列位向平行或者接近平行拉拔轴向,从而使得更多铁素体〈110〉取向转到拉拔方向,形成较强的〈110〉丝织构.冷拉拔钢丝片层间距较大,渗碳体片的排列位向不利,主要以剪切方式变形,因应力集中而导致断裂、破碎,破碎的渗碳体易造成位错堆积、缠结,使得铁素体位错滑移受阻,片层组织后续形变变得困难,从而难以形成〈110〉丝织构.因此,辊模拉拔方式更有利于〈110〉丝织构的形成,减小了沿拉拔方向上的形变阻力,有助于提高钢丝的轴向力学性能[20].不同拉拔方式下钢丝在应变量0.23、1.18时的透射照片如图13所示.可以看到,形变后,当应变量为0.23时,在辊模拉拔过程中,渗碳体片主要以缓慢弯曲方式协调变形;在冷拉拔过程中,渗碳体片主要发生剪切变形,剪切位置易产生大量缠结的位错,因应力集中而造成渗碳体片发生断裂、破碎.当应变量增加到1.18时,位错密度进一步增加,位错运动以多系滑移为主,〈110〉丝织构的形成促使片层方向转向拉拔轴向,钢丝组织形变阻力减小,片层得到进一步细化.统计应变量为1.18时的片层间距分布比例,如表2所示.可以看到,辊模拉拔钢丝的片层间距集中分布在80~100 nm,平均片层间距约为94 nm.冷拉拔钢丝的片层间距集中分布在100~130 nm,平均片层间距约为125 nm.辊模拉拔方式产生的较强〈110〉丝织构,使得钢丝形变阻力更小,从而促进了片层间距的减小.(a) 辊模拉拔(ε=0.23)(b) 冷拉拔(ε=0.23)(c) 辊模拉拔(ε=1.18)(d) 冷拉拔(ε=1.18)图13 不同拉拔方式下钢丝组织的透射照片(纵截面)表2 应变量为1.18时片层间距分布比例 %片层间距/nm[60,80)[80,100)[100,130)[130,150)[150,∞)辊模拉拔21.646.428.73.3冷拉拔7.524.526.021.720.3图14为不同拉拔方式下平均片层间距与应变量关系曲线,钢丝片层间距S与应变量ε的关系一般满足S=S0exp(-ε/2)[21](式中,S0为未变形盘条的片层间距).可以看到,冷拉拔状态的片层间距变化和理论值基本一致,辊模拉拔状态的片层间距变化则位于理论曲线下方.通常,较小的片层间距会增加位错滑移的障碍,使得钢丝变形抗力增大,进而提高钢丝强度.因此,辊模拉拔方式下,片层产生的强化作用高于冷拉拔状态.此外,相界面的增多能有效阻止裂纹的扩展,从而提升了钢丝塑性.另一方面,不同拉拔方式形变后,应变量为1.18时,冷拉拔钢丝表面为残余拉应力,辊模拉拔钢丝表面为残余压应力.研究表明[22-24],表面残余压应力的存在可提高钢丝在拉拔过程中的形变速率,改善钢丝表面质量,降低钢丝环境促进断裂及疲劳失效的倾向,延长钢丝在复杂环境条件下的使用寿命.图14 不同拉拔方式下平均片层间距随应变量变化曲线综上可知,经辊模拉拔后,钢丝形变更协调,形成的〈110〉丝织构更强,片层更薄,力学性能得以提升;然而,与冷拉拔技术相比,辊模拉拔尺寸精度较低,更高强度钢丝的生产难以实现;并且经多道次减径后,钢丝易产生侧向宽展[8-9],不利于织构的形成,会对钢丝性能造成影响.已有研究指出[25-26],为减小细丝在辊模拉拔过程中的变形不均匀性,单道次减径大小应控制在4%~8%,此方法将大大降低生产效率,增加成本.若结合2种技术的优点,在起始时采用辊模进行拉拔,得到组织性能较好的高强度钢丝,最终再通过冷拉拔进行精整加工,将可以获得综合性能良好、尺寸精度较高的产品.因此,辊模拉拔与冷拉拔的联合使用有望在弹簧钢丝、冷镦钢丝等领域得到广泛应用.4 结论1) 不同拉拔方式下高碳钢丝的抗拉强度均随应变量的增加而增加,同一应变量下,辊模拉拔钢丝的强度与塑性均优于冷拉拔钢丝.2) 与冷拉拔钢丝相比,辊模拉拔钢丝组织形变更协调,片层更薄,产生的〈110〉丝织构更强.3) 残余应力分析表明,当应变量为1.18时,辊模拉拔钢丝表面为残余压应力,冷拉拔钢丝表面为残余拉应力.4) DSC结果表明,应变量为1.18时,辊模拉拔钢丝在403~491 ℃之间出现放热峰,峰值温度为446 ℃;冷拉拔钢丝在381~472 ℃之间出现放热峰,峰值温度为408 ℃.经辊模拉拔形变后,高碳钢丝片层组织具有更好的热稳定性.参考文献【相关文献】[1] Borchers C, Kirchheim R. Cold-drawn pearlitic steel wires [J]. Progress in Materials Science, 2016, 82: 405-444.DOI: 10.1016/j.pmatsci.2016.06.001.[2] Zhang X D, Godfrey A, Huang X X, et al. Microstructure and strengthening mechanisms in cold-drawn pearlitic steel wire [J]. Acta Materialia, 2011, 59(9): 3422-3430.DOI:10.1016/j.actamat.2011.02.017.[3] Li Y J, Choi P, Goto S, et al. Evolution of strength and microstructure during annealing of heavily cold-drawn 6.3 GPa hypereutectoid pearlitic steel wire [J]. Acta Materialia, 2012, 60(9): 4005-4016.DOI: 10.1016/j.actamat.2012.03.006.[4] Gokyu I, Saito Y. Studies on the roller-die [J]. Tetsu-to-Hagane Overseas, 1964, 4: 44-52.[5] Bitkov V. Expediency of roller dies application in wire drawing—part 2 [J]. Wire Cable Technology International, 2008, 36(3): 112-113.[6] El Amine K, Larsson J, Pejryd L. Experimental comparison of roller die and conventional wire drawing [J]. Journal of Materials Processing Technology, 2018, 257: 7-14.DOI:10.1016/j.jmatprotec.2018.02.012.[7] Lee J W, Baek H M, Hwang S K, et al. The effect of the multi-pass non-circular drawing sequence on mechanical properties and microstructure evolution of low-carbon steel [J]. Materials & Design, 2014, 55: 898-904.DOI: 10.1016/j.matdes.2013.10.068.[8] Pilarczyk J W, van Houtte P, Aernoudt E. Effect of hydrodynamic and roller die drawing on the texture of high carbon steel wires [J]. Materials Science and Engineering: A, 1995, 197(1): 97-101.DOI: 10.1016/0921-5093(94)09756-9.[9] Pilarczyk J W, Dyja H, Golis B, et al. Effect of roller die drawing on structure, texture and other properties of high carbon steel wires [J]. Metals and Materials, 1998, 4(4): 727-731.DOI: 10.1007/bf03026388.[10] Yang F, Jiang J Q, Wang Y, et al. Residual stress in pearlitic steel rods during progressively cold drawing measured by X-ray diffraction [J]. Materials Letters, 2008,62(15): 2219-2221.DOI: 10.1016/j.matlet.2007.11.054.[11] Yang F, Wang Y, Jiang J Q, et al. Stress evolution of cold-drawn pearlitic steel wire subjected to uniaxial tension [J]. Materials Science and Engineering: A, 2008, 487(1/2): 468-472.DOI: 10.1016/j.msea.2007.10.061.[12] 张晓丹, Godfrey A, 刘伟,等. 珠光体钢丝冷拉拔过程中微观组织及铁素体微区取向与织构演变[J]. 金属学报, 2010, 46(2): 141-146.DOI: 10.3724/sp.j.1037.2009.00247.Zhang X D, Godfrey A, Liu W, et al. Evolutions of microstructure and ferritic micro-orientation and texture in a pearlitic steel wire during cold drawing [J]. Acta Metallurgica Sinica, 2010, 46(2): 141-146.DOI: 10.3724/sp.j.1037.2009.00247. (in Chinese)[13] 周立初, 胡显军, 马驰,等. 珠光体层片取向对冷拔珠光体钢丝形变的影响 [J]. 金属学报, 2015, 51(8): 897-903.Zhou L C, Hu X J, Ma C, et al. Effect of pearlitic lamella orientation on deformation of pearlite steel wire during cold drawing [J]. Acta Metallurgica Sinica, 2015, 51(8): 897-903. (in Chinese)[14] Zhao T Z, Zhang G L, Zhang S H, et al. Influence of lamellar direction in pearlitic steel wire on mechanical properties and microstructure evolution [J]. Journal of Iron and Steel Research International, 2016, 23(12): 1290-1296.DOI:10.1016/S1006-706X(16)30190-X. [15] 周玉, 武高辉. 材料分析测试技术 [M]. 哈尔滨:哈尔滨工业大学出版社, 2007: 97-100. Zhou Y, Wu G H. Analysis methods in materials science [M]. Harbin:Harbin Institute of Technology Press, 2007: 97-100. (in Chinese)[16] Fang F, Hu X J, Chen S H, et al. Revealing microstructural and mechanical characteristics of cold-drawn pearlitic steel wires undergoing simulated galvanization treatment [J]. Materials Science and Engineering: A, 2012, 547: 51-54.DOI:10.1016/j.msea.2012.03.075.[17] Fang F, Zhou L C, Hu X J, et al. Microstructure and mechanical properties of cold-drawn pearlitic wires affect by inherited texture [J]. Materials & Design, 2015, 79: 60-67.DOI: 10.1016/j.matdes.2015.04.036.[18] 熊毅, 陈正阁, 厉勇,等. 温压缩变形过程中渗碳体的球化行为 [J]. 材料热处理学报, 2008,29(1): 42-46.Xiong Y, Chen Z G, Li Y, et al. Spheroidization behavior of cementite during warm compression deformation [J]. Transactions of Materials and Heat Treatment, 2008, 29(1): 42-46. (in Chinese)[19] Zhang X D, Godfrey A, Hansen N, et al. Evolution of cementite morphology in pearlitic steel wire during wet wire drawing [J]. Materials Characterization, 2010, 61(1): 65-72.DOI: 10.1016/j.matchar.2009.10.007.[20] 赵天章, 宋鸿武, 张光亮,等. 拉拔过程中珠光体钢丝心部的织构演化规律及其对力学性能的影响 [J]. 金属学报, 2014, 50(6): 667-673.DOI: 10.3724/sp.j.1037.2013.00799.Zhao T Z, Song H W, Zhang G L, et al. The texture evolution at the center of pearlitic steelwire during drawing and its influence on the mechanical properties [J]. Acta Metallurgica Sinica, 2014, 50(6): 667-673.DOI: 10.3724/sp.j.1037.2013.00799. (in Chinese)[21] Embury J D, Fisher R M. The structure and properties of drawn pearlite [J]. Acta Metallurgica, 1966, 14(2): 147-159.DOI: 10.1016/0001-6160(66)90296-3.[22] Elices M. Influence of residual stresses in the performance of cold-drawn pearlitic wires [J]. Journal of Materials Science, 2004, 39(12): 3889-3899.DOI:10.1023/B:JMSC.0000031470.31354.b5.[23] Elices M, Ruiz J, Atienza J M. Influence of residual stresses on hydrogen embrittlement of cold drawn wires [J]. Materials and Structures, 2004, 37(5): 305-310.DOI: 10.1007/BF02481676.[24] Atienza J M, Elices M. Influence of residual stresses in the stress relaxation of cold drawn wires [J]. Materials and Structures, 2004, 37(5): 301-304.DOI: 10.1007/BF02481675.[25] Lambiase F, di Ilio A. Deformation inhomogeneity in roll drawing process [J]. Journal of Manufacturing Processes, 2012, 14(3): 208-215.DOI: 10.1016/j.jmapro.2011.12.005. [26] Asakawa M, Shigeta H, Shimizu A, et al. Experiments on and finite element analyses of the tilting of fine steel wire in roller die drawing [J]. ISIJ International, 2013, 53(10): 1850-1857.DOI: 10.2355/isijinternational.53.1850.。
辊式矫直技术与设备发展概况
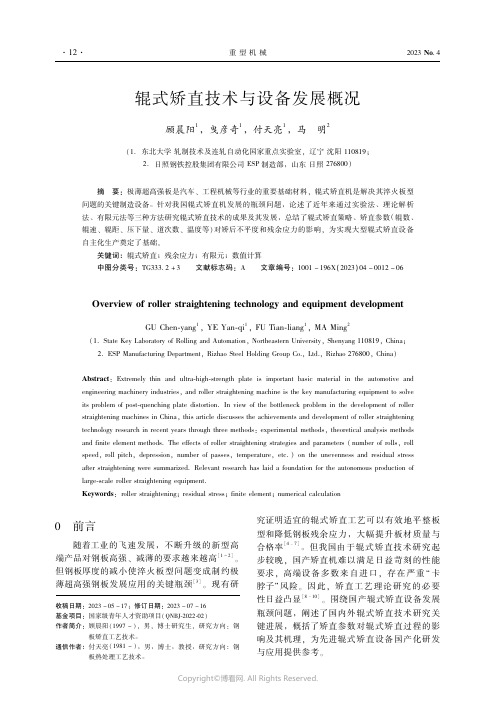
!"(=R8R?I?KH8[9U8R9UK9VN9SS7@A8@C 1DR9X8R79@" 59UR>?8TR?U@ E@7P?UT7RK" =>?@K8@A""*,"+" M>7@8# #(L=WF8@DV8QRDU7@Aa?\8URX?@R" N7J>89=R??S;9SC7@A/U9D\ M9(" HRC(" N7J>89#)',**" M>7@8$
Copyright©博看网. All Rights Reserved.
#*#$ 8&0%!!!!!!!!!!!!!!! !!!重 型 机 械
+"$+
"!辊式矫直机简介与国内矫直机
发展现状
!!辊式矫直 机 的 矫 直 原 理 是 金 属 经 多 次 反 复 弯曲" 使曲率从大变小而最终平直& 辊式矫直 机的出现" 避免了压 力 矫 直 机 间 歇 工 作 的 问 题" 大幅提升了矫直的质量和效率& 国外对于 辊式矫直技术的研究要远早于国内" 因此早期
Copyright©博看网. All Rights Reserved.
+"%+
重 型 机 械!! !!!!!!!!!!!!!!!!#*#$ 8&0%
表 "!矫直实验数据")
倾斜矫直方案
平行矫直方案
最大弯曲
曲率 ')
轧辊的失效及其修复技术

轧辊的失效及其修复技术摘要:轧辊生产率与生产成本都取决于轧制的生产质量,当轧辊不足供应,价格高时,整个轧辊都会磨损失效,这会导致大量的材料报废。
轧辊的修复是轧辊行业的主要问题。
过早磨损最常见轧辊失效的原因,轧辊的工作表面的硬度取决于耐磨性,正确的热处理符合辊的硬度要求。
轧机是轧辊变形的主要工具。
通过自己的材料和恶劣的工作条件,延长寿命需要修复技术,失效甚至报废。
概述了轧辊的工作条件、材料和失效,介绍了几种常见的修复技术。
关键词:冷轧辊热轧辊;失效修复;表面改性技术引言激光处理技术在钢铁工业中的应用越来越多。
随着钢铁工业的复苏和世界钢需求量的增加,我国的钢铁产量目前地位领先。
轧辊消费量大幅增加,进一步提高了产量和质量。
与此同时,各种新角色正在应用于钢铁行业。
因此,轧辊的修复和化是钢铁工作者和激光设备的一个重要问题。
减少组件消耗会对企业的生产成本和经济性产生积极影响,并提供显着的成本节约机会。
目前,激光用于加固和修复辊面,引起了业界的关注。
1轧辊的损坏形式1.1正常磨损轧辊金属微粒在轧制和磨削过程中辊身分离,工作层变薄,直径较小,吨位随磨辊次数的增加而减小。
如果直径太小,以致于表面硬度降低到某个特定值,则即使没有其他缺陷(自然磨损或正常磨损),辊也无法继续工作。
这种磨损是可预见的,也是有风险的,最危险的损害通常是非正常磨损。
1.2非正常损坏如果辊的直径和表面硬度仍处于连续运转状态,则由于另一个缺陷甚至断裂,无法使用,这称为“非正常”和“特殊损坏”,具体由:(1)表面裂纹。
冷轧辊的裂纹分别为60%和20%,且裂纹的区域通常位于辊的中心。
裂缝有所不同的概率大致相同。
轧辊的制造质量对裂缝的形成和扩大至关重要。
因此,减少裂纹是提高轧辊的制造质量的关键。
例如,碎裂是轧槽经轧制过程中的冷热影响以及钢坯的磨损较低,导致轧槽表面上出现网格裂纹,从而导致断裂。
冷却水压力不足可能导致裂内部的汽化扩张力大,有助于增加裂缝。
激光淬火技术
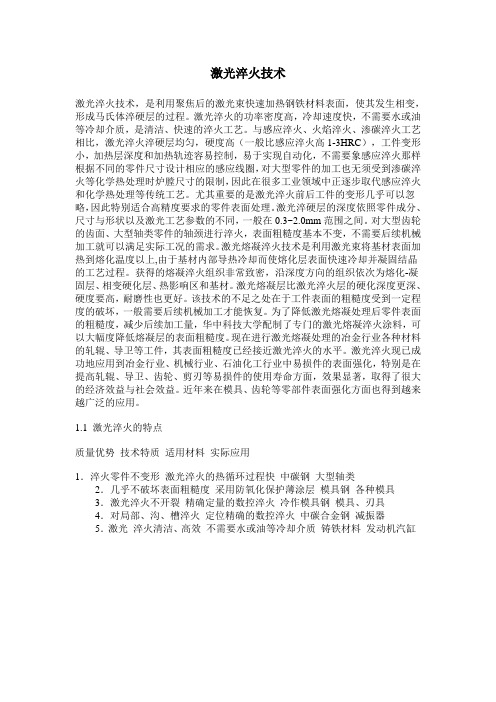
激光淬火技术激光淬火技术,是利用聚焦后的激光束快速加热钢铁材料表面,使其发生相变,形成马氏体淬硬层的过程。
激光淬火的功率密度高,冷却速度快,不需要水或油等冷却介质,是清洁、快速的淬火工艺。
与感应淬火、火焰淬火、渗碳淬火工艺相比,激光淬火淬硬层均匀,硬度高(一般比感应淬火高1-3HRC),工件变形小,加热层深度和加热轨迹容易控制,易于实现自动化,不需要象感应淬火那样根据不同的零件尺寸设计相应的感应线圈,对大型零件的加工也无须受到渗碳淬火等化学热处理时炉膛尺寸的限制,因此在很多工业领域中正逐步取代感应淬火和化学热处理等传统工艺。
尤其重要的是激光淬火前后工件的变形几乎可以忽略,因此特别适合高精度要求的零件表面处理。
激光淬硬层的深度依照零件成分、尺寸与形状以及激光工艺参数的不同,一般在0.3~2.0mm范围之间。
对大型齿轮的齿面、大型轴类零件的轴颈进行淬火,表面粗糙度基本不变,不需要后续机械加工就可以满足实际工况的需求。
激光熔凝淬火技术是利用激光束将基材表面加热到熔化温度以上,由于基材内部导热冷却而使熔化层表面快速冷却并凝固结晶的工艺过程。
获得的熔凝淬火组织非常致密,沿深度方向的组织依次为熔化-凝固层、相变硬化层、热影响区和基材。
激光熔凝层比激光淬火层的硬化深度更深、硬度要高,耐磨性也更好。
该技术的不足之处在于工件表面的粗糙度受到一定程度的破坏,一般需要后续机械加工才能恢复。
为了降低激光熔凝处理后零件表面的粗糙度,减少后续加工量,华中科技大学配制了专门的激光熔凝淬火涂料,可以大幅度降低熔凝层的表面粗糙度。
现在进行激光熔凝处理的冶金行业各种材料的轧辊、导卫等工件,其表面粗糙度已经接近激光淬火的水平。
激光淬火现已成功地应用到冶金行业、机械行业、石油化工行业中易损件的表面强化,特别是在提高轧辊、导卫、齿轮、剪刃等易损件的使用寿命方面,效果显著,取得了很大的经济效益与社会效益。
近年来在模具、齿轮等零部件表面强化方面也得到越来越广泛的应用。
一种高硬度高碳合金锻钢轧辊复合制造工艺
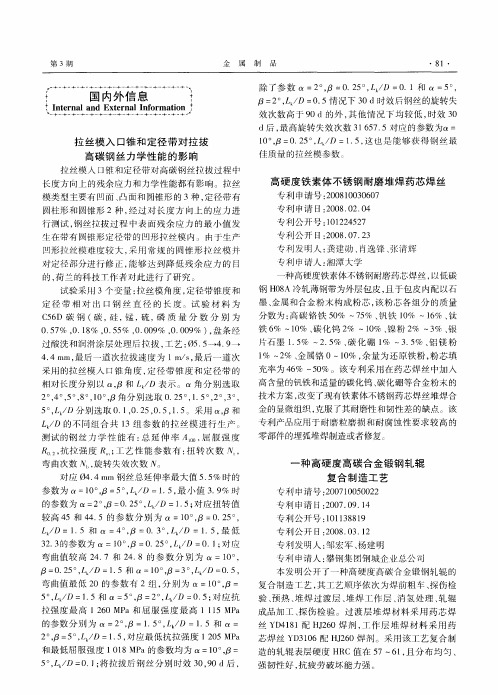
0 2 ,J D =1 5和 =1 。 =3 ,J D =0 5, . 5。 , / k . 0, 。 ,/ k .
弯 曲值 最 低 2 0的参 数 有 2组 , 别 为 O =1 。 = 分 . 1 0,
1 ~ %、 % 2 金属铬 0~1% , 量 为还原 铁 粉 , 芯填 Nhomakorabea 0 余 粉
充率为 4 % ~ 0 。该 专 利采 用 在药 焊 丝 中加 入 6 5% 高含量 的钒铁 和适量 的碳 化钨 、 化硼 等合金粉 末 的 碳
技 术方案 , 变了现有铁 素体不锈 钢药芯 焊丝堆 焊合 改
,
专 利产 品应 用 于耐磨 粒 磨损 和 耐腐 蚀性 要求 较 高 的
零 部 件的埋 弧堆焊制造 或者修 复。
抗 拉 强 度 R 工 艺性 能 参 数 有 : 转 次数 Ⅳ , ; 扭
一
弯 曲次数 , v 旋 转 失效 次数 Ⅳ。
种 高 硬 度 高 碳 合 金 锻 钢 轧辊 复 合 制 造 工 艺
专利 公 开号 :0 2 4 2 11257 专利 公 开 日:0 8 0 . 3 2 0 .7 2
行 测试 , 钢丝 拉拔 过 程 中表 面残 余 应 力 的最 小值 发
生 在带 有 网锥形定 径 带 的凹形 托丝模 内。 由于生 产 凹形托 丝模 难度 较 大 , 用 常规 的 网锥 形 拉 丝模 并 采
=
t I tr a n tr a n 0 ma in n e n l d Ex e n l fr t a I o
+ + +
2 , D= . 。L/ 0 5情况 下 3 效后 钢丝 的旋转 失 0d时
激光合金化技术提高轧辊寿命的研究
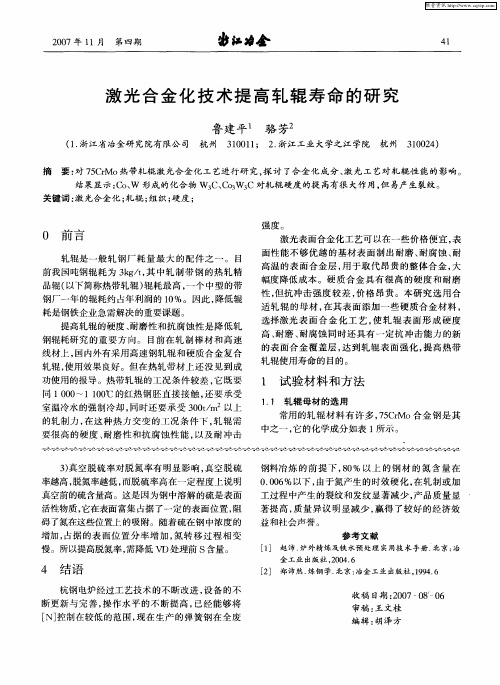
激 光表 面合 金 化工 艺可 以在一 些 价 格便 宜 , 表 面性 能不 够 优 越 的基 材 表 面 制 出 耐磨 、 腐 蚀 、 耐 耐
钢厂 一年 的辊 耗约 占年利 润 的 1 %。因此 , 0 降低 辊 耗 是 钢铁企 业 急需 解决 的重 要课 题 。
高温 的表面合金层 , 于取代 昂贵 的整体合金, 用 大 幅度降低成本 。硬 质合金具有很高的硬度和耐磨 性 , 冲击 强度较差 , 但抗 价格 昂贵 。本研 究选用合 适轧辊 的母材 , 在其表面添加一些硬质合金材料 , 选择 激光 表 面 合 金 化 工 艺 , 轧 辊 表 面 形 成 硬 度 使 高、 耐磨 、 耐腐蚀同时还具有 一定抗 冲击能力 的新 的表 面 合 金 覆 盖 层 , 到 轧 辊 表 面 强 化 , 高 热 带 达 提
1 3 激光 强化 使用 的合 金材料 .
0. - 0 2 7- . 0~ 0. 0 7 ~ 0.5~ 0. 0 7 2 ~
0. 8 0. 0 6 0 9 .0 10 .0
≤
≤
0. 5 4 0. 3 0 0 0 05 .3
该 材料 具有 良好 的抗拉 强 度 和 冲击 性 能 , 表 在
慢。所以提高脱氮率 , 需降低 V D处理前 S 含量 。
4 结 语
杭 钢 电炉经 过工 艺技 术 的 不 断改 进 , 备 的 不 设 断更新 与完 善 , 操作 水 平 的不 断提 高 , 经 能够 将 已
[ ] 郑 沛然 . 2 炼钢 学. 北京 : 冶金 工业 出版社 ,9 4 6 1 9 .
轧 辊使 用 寿命 的 目的。
提高轧辊的硬度 、 耐磨性和抗腐蚀性是降低轧
钢 辊耗 研 究 的 重 要 方 向。 目前 在 轧 制棒 材 和 高 速
高铬钢复合轧辊铸造中大型夹杂物的分析及控制办法
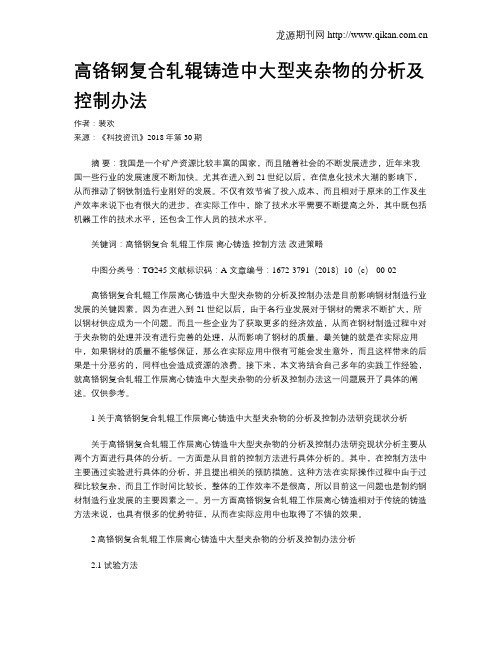
高铬钢复合轧辊铸造中大型夹杂物的分析及控制办法作者:裴欢来源:《科技资讯》2018年第30期摘要:我国是一个矿产资源比较丰富的国家,而且随着社会的不断发展进步,近年来我国一些行业的发展速度不断加快。
尤其在进入到21世纪以后,在信息化技术大潮的影响下,从而推动了钢铁制造行业刚好的发展。
不仅有效节省了投入成本,而且相对于原来的工作及生产效率来说下也有很大的进步。
在实际工作中,除了技术水平需要不断提高之外,其中既包括机器工作的技术水平,还包含工作人员的技术水平。
关键词:高铬钢复合轧辊工作层离心铸造控制方法改进策略中图分类号:TG245 文献标识码:A 文章编号:1672-3791(2018)10(c)-00-02高铬钢复合轧辊工作层离心铸造中大型夹杂物的分析及控制办法是目前影响钢材制造行业发展的关键因素。
因为在进入到21世纪以后,由于各行业发展对于钢材的需求不断扩大,所以钢材供应成为一个问题。
而且一些企业为了获取更多的经济效益,从而在钢材制造过程中对于夹杂物的处理并没有进行完善的处理,从而影响了钢材的质量。
最关键的就是在实际应用中,如果钢材的质量不能够保证,那么在实际应用中很有可能会发生意外,而且这样带来的后果是十分恶劣的,同样也会造成资源的浪费。
接下来,本文将结合自己多年的实践工作经验,就高铬钢复合轧辊工作层离心铸造中大型夹杂物的分析及控制办法这一问题展开了具体的阐述。
仅供参考。
1 关于高铬钢复合轧辊工作层离心铸造中大型夹杂物的分析及控制办法研究现状分析关于高铬钢复合轧辊工作层离心铸造中大型夹杂物的分析及控制办法研究现状分析主要从两个方面进行具体的分析。
一方面是从目前的控制方法进行具体分析的。
其中,在控制方法中主要通过实验进行具体的分析,并且提出相关的预防措施。
这种方法在实际操作过程中由于过程比较复杂,而且工作时间比较长,整体的工作效率不是很高,所以目前这一问题也是制约钢材制造行业发展的主要因素之一。
超高强冷轧316l不锈钢 马氏体相变强化 研究现状

超高强冷轧316l不锈钢马氏体相变强化研究现状随着科技的不断进步和工业发展的需求,超高强度冷轧316L不锈钢因其优异的力学性能和耐腐蚀性而备受关注。
在提高其强度的同时,保持良好的塑韧性至关重要。
马氏体相变强化作为一种有效的强韧化手段,在超高强度冷轧316L不锈钢中得到了广泛应用。
一、引言超高强度冷轧316L不锈钢是一种具有高强度、良好耐腐蚀性和焊接性能的钢材,广泛应用于航空航天、汽车、核工业等领域。
为满足这些领域对材料强度的需求,研究者对超高强度冷轧316L不锈钢进行了大量研究。
马氏体相变强化作为一种有效的强韧化手段,在提高超高强度冷轧316L不锈钢的强度和塑韧性方面具有重要意义。
二、研究现状1.国内外超高强度冷轧316L不锈钢的研究进展随着研究的深入,国内外学者在超高强度冷轧316L不锈钢方面取得了一系列研究成果。
我国研究者已成功研发出强度达到1000MPa级的超高强度冷轧316L不锈钢,并已应用于实际生产。
2.马氏体相变强化技术在超高强度冷轧316L不锈钢中的研究热点马氏体相变强化技术是目前超高强度冷轧316L不锈钢研究的热点之一。
研究者主要关注冷轧工艺、热处理工艺和合金元素对马氏体相变的影响,以期提高材料的强度和塑韧性。
三、超高强度冷轧316L不锈钢的马氏体相变强化技术1.冷轧工艺对超高强度冷轧316L不锈钢马氏体相变的影响冷轧工艺参数如轧制速度、轧制压力和冷却速度等对超高强度冷轧316L 不锈钢的马氏体相变具有显著影响。
合理调整冷轧工艺参数,可有效提高马氏体相变的体积分数,从而提高材料的强度。
2.热处理工艺对超高强度冷轧316L不锈钢马氏体相变的影响热处理工艺如退火、正火和调质等对超高强度冷轧316L不锈钢的马氏体相变具有显著影响。
适当调整热处理工艺参数,可优化马氏体相变的分布和形态,提高材料的强韧性能。
3.合金元素对超高强度冷轧316L不锈钢马氏体相变的影响合金元素如氮、钛、钒等对超高强度冷轧316L不锈钢的马氏体相变具有显著影响。
衡量一个国家综合国力 [新材料开发与产业化 衡量综合国力的重要标志]
![衡量一个国家综合国力 [新材料开发与产业化 衡量综合国力的重要标志]](https://img.taocdn.com/s3/m/755a56e0de80d4d8d15a4fe8.png)
衡量一个国家综合国力[新材料开发与产业化衡量综合国力的重要标志]当你坐在新型环保的办公室,享受着地下水屋内循环对流而造成最佳温度带来的舒适,捧起手中的纳米杯,喝一口热腾腾的茶,然后用电脑开始办公的时候,你有没有想过,你所接触的一切都与新材料息息相关。
人类历史的发展,是以新材料的突破为时代标志,从石器的打制、铁器的制造,到机械的应用、晶体的出现,使人类不但脱离野蛮时代,进入工业时代,而且迎来信息时代。
当今,新材料研发与信息技术、生物技术构成了21世纪最重要、最具发展潜力的三大领域。
新材料作为高新技术的基础和先导,应用范围极其广泛,几乎涉及国民经济的每个部门,渗入大众生活的各个方面,备受科技界的推崇和世界各国的高度重视。
目前,新材料的研发与产业化发展水平,已成为衡量一个国家综合实力的重要标志。
“谁掌握了新材料,谁就掌握了未来”,世界各国均把大力研究和开发新材料作为21世纪的重大战略决策。
专家预测,信息功能陶瓷材料及其制品的全球销售收入,到2010年将达800亿美元;全球钕铁硼稀土永磁材料产值,到2010年将达83亿美元;世界超导材料销售额,到2010年将达600-900亿美元。
美国科学基金会预测,未来10年,全球纳米技术市场规模将达到1万亿美元左右。
发达国家清楚地看到了新材料产业所蕴藏的巨大商机和具有的重要战略地位,纷纷制定出相关战略计划并投入巨资进行开发。
我国政府对新材料的研究开发也给予了高度重视,近年出台了一系列相关鼓励政策,指定了一批新材料研发中心和重点实验室,规划了一批新材料成果转化与产业建设基地,特别是在国家先后出台的一些重大科技开发和产业化计划中,均把新材料列为重点支持的领域之一。
国家的重大科技计划中,“863”计划、“973”计划、火炬计划、科技攻关计划、中小企业创新基金等项目,全部都对新材料的长期开发与研究投入了大量的人力物力,对其的关注已经占到了整体科学研究中非常大的一个比例。
国家自然科学基金,是国家为支持自然科学基础性研究而设立的专项基金,它大力支持具有重要应用前景,特别是具有新思想、新方法以及可能产生新成果的材料方面的基础性研究。
国际轧制技术发展
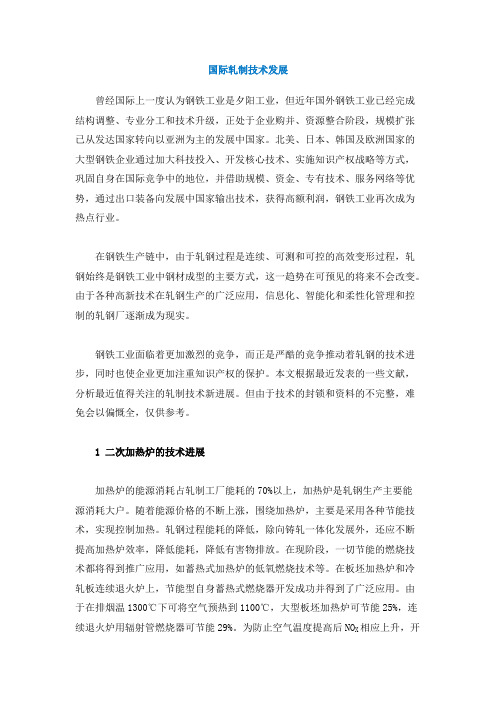
国际轧制技术发展曾经国际上一度认为钢铁工业是夕阳工业,但近年国外钢铁工业已经完成结构调整、专业分工和技术升级,正处于企业购并、资源整合阶段,规模扩张已从发达国家转向以亚洲为主的发展中国家。
北美、日本、韩国及欧洲国家的大型钢铁企业通过加大科技投入、开发核心技术、实施知识产权战略等方式,巩固自身在国际竞争中的地位,并借助规模、资金、专有技术、服务网络等优势,通过出口装备向发展中国家输出技术,获得高额利润,钢铁工业再次成为热点行业。
在钢铁生产链中,由于轧钢过程是连续、可测和可控的高效变形过程,轧钢始终是钢铁工业中钢材成型的主要方式,这一趋势在可预见的将来不会改变。
由于各种高新技术在轧钢生产的广泛应用,信息化、智能化和柔性化管理和控制的轧钢厂逐渐成为现实。
钢铁工业面临着更加激烈的竞争,而正是严酷的竞争推动着轧钢的技术进步,同时也使企业更加注重知识产权的保护。
本文根据最近发表的一些文献,分析最近值得关注的轧制技术新进展。
但由于技术的封锁和资料的不完整,难免会以偏慨全,仅供参考。
1 二次加热炉的技术进展加热炉的能源消耗占轧制工厂能耗的70%以上,加热炉是轧钢生产主要能源消耗大户。
随着能源价格的不断上涨,围绕加热炉,主要是采用各种节能技术,实现控制加热。
轧钢过程能耗的降低,除向铸轧一体化发展外,还应不断提高加热炉效率,降低能耗,降低有害物排放。
在现阶段,一切节能的燃烧技术都将得到推广应用,如蓄热式加热炉的低氧燃烧技术等。
在板坯加热炉和冷轧板连续退火炉上,节能型自身蓄热式燃烧器开发成功并得到了广泛应用。
由于在排烟温1300℃下可将空气预热到1100℃,大型板坯加热炉可节能25%,连续退火炉用辐射管燃烧器可节能29%。
为防止空气温度提高后NO X相应上升,开发成功低氧燃烧技术,即在空气预热温1150℃下,将氧浓度由15%降到2%后仍可稳定燃烧,NO X由750ppm降到40ppm。
在线数学模型在其中起到关键作用。
高镍铬铸铁轧辊材料激光相变组织与耐磨性研究
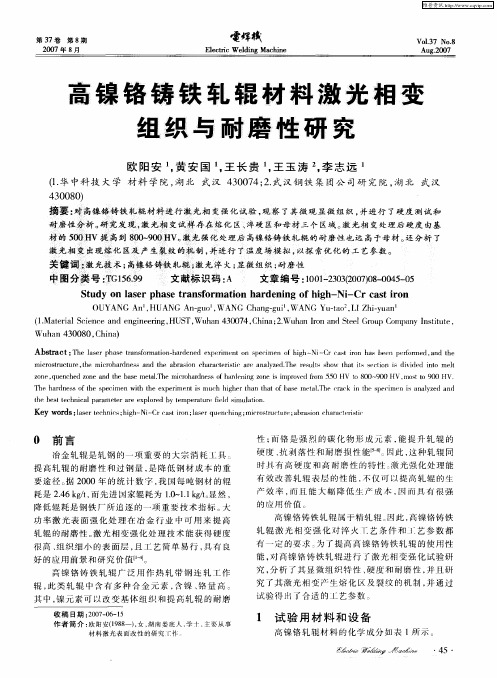
(. tr l ce c n n i er g HU T, h n4 0 7 C ia 2Wu a rna dSe l ru o a yI si t 1Maei in ea d e gn ei , S Wu a 3 0 4, hn ; . h nI n te G o pC mp n nt ue, aS n o t
Wu a 3 0 0 C ia h n4 0 8 ,hn)
Ab ta t T e lsr h s a s r t nh r e e x ei n n s e i n o i — i C . ti n h sh e efr e ,n h sr c : h e p a et n f ma o — ad n d ep r a r o i me t p c o me f g N — r( s r a e n p r m d a d te h h a o o
耐 磨性 分析 。 究发 现 , 研 激光相 变试样存 在 熔化 区、 淬硬 区和母 材三 个 区域 。 激光相 变处理 后硬度 由基
材 的 5 0HV提 高3 0 ~ 0 Vo 0 1 , 0 9 0H 激光 强化 处理后 高镍铬铸 铁 轧辊 的耐磨性 也远 高于母 材。 8 还分 析 了
激 光相 变出现 熔化 区及 产 生裂纹 的机 制 , 并进 行 了温度场模 拟 , 以探 索优 化 的工 艺参数 。
维普资讯
第3 7卷 第 8期 20 0 7年 8月
嚏珲梭
E e ti ed n c i e lc r W li g Ma h n c
钢的强化方法及机理

强化3Cr2W8V钢属过共析钢, 原材料晶粒粗大, 碳化物偏析严重往往呈块、网、带状分布。
通过改锻(三次循环调质处理), 击碎块状碳化物, 七碎粗晶粒, 并使其形成的纤维组织沿着模具轮廓呈无定向分布, 增加钢的塑性、韧性与强度。
经三次高温固溶淬火, 使未锻透的内层组织中的残留块状、网状、带状碳化物和难溶的碳化物质点和合金元素充分溶解于奥氏体中, 大大增加了固溶体中的合金化程度, 大大降低了碳化物偏析对基体的切割作用。
升至淬火温度保温后出炉水冷2一3秒淬人硝盐等温, 获得强韧性高的板条弥散组织,再经二次高温回火后碳化物呈高度弥散析出, C一N硬化层有硬度较高的过渡层支承, 基体具有良好的强韧性, 使凹模具有外硬型面和内韧基体特性, 获得一顶十的高寿命。
3Cr2W8V钢可采用淬火、回火处理,渗碳、渗氮、渗硼及碳氮共渗、渗铝、渗铬及铬一铝一硅三元共渗等化学热处理,镀金属等表面强化处理来提高其高温强度、冷热疲劳抗力、耐磨性、抗腐蚀性及防粘模等性能,从而达到提高3Cr2W8V钢制模具的使用寿命的目的。
渗金属渗铬处理可显著提高模具高温耐磨性、热疲劳抗力。
真空热处理。
采用真空热处理,模具表面光洁,硬度均匀,变形小,尤其适应对精度要求和表面粗糙度要求高的模具。
3Cr2W8V钢超塑形变处理与常规热处理比较,其强度和韧性同时得到提高电火花表面强化是利用火花放电时释放的能量,将一种导电材料熔渗到工件表面,构成合金化的表面强化层,从而改善工件表面的物理及化学性能喷丸强化是借助于硬丸粒,高速、连续锤击金属表面,使其产生强烈的冷作硬化。
通过喷丸可以明显改变金属表层的应力状态、显微硬度、表层的微观形貌,从而提高模具的疲劳强度、抗冲击磨损及抗应力腐蚀离子注入是将被注入元素的原子利用离子注入机电离成带一个正电荷的离子,经高压电场作用后,强行注入材料的表面,使其产生物理、化学性能的优化的工艺方法。
可将任何元素注入任何材料中,浓度可严格控制,且不受材料固溶度的限制,强化层也不会剥落,处理温度低,易于控制,工件的基体材料不可能因温升而弱化,也不会产生变形和翘曲。
轧辊表面激光强化的试用
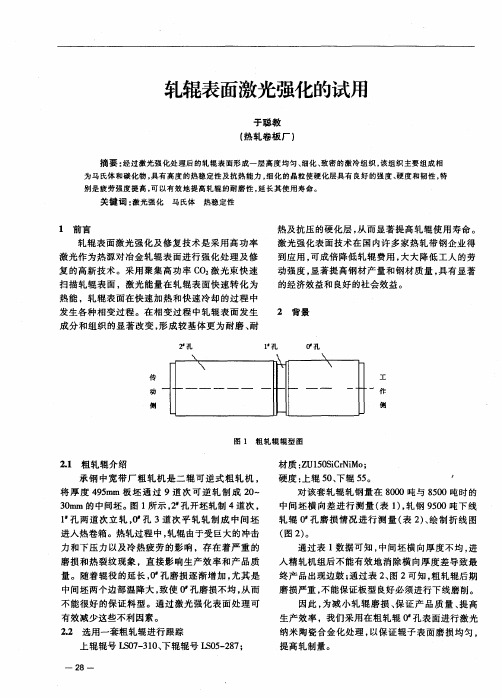
.
.
.
.
.
/
‘
.
’ ’ ’ V
. .
一
一 卜
l ●l一一1 。
\
^
l ’、 -b, 1
\
I 、_ .
r
-, I I I
-
-
1
2
3
4
5
6
7
8
9
1 0
l 1 1 2
1 1 3 4
图 4 强 化 粗 轧 辊 孔 磨 损 折 线 图
发 生各 种相 变过 程 。在 相 变过 程 中轧辊 表 面 发生 成 分 和组 织 的显 著改 变 , 成较 基 体更 为 耐磨 、 形 耐
2 孔 I l 孔 ‘ 孔
、
传
动 侧
-一 _- —
\
一
工
一 作 侧
图 1 粗 轧 辊 辊 型 图
21 粗 轧辊 介绍 .
不能 很 好 的保证 料 型 。通 过 激光 强化 表 面处 理 可
通 过表 1数据 可知 , 间坯横 向厚 度不 均 , 中 进 入 精 轧机 组后 不能 有效 地 消 除横 向厚度 差 导致 最 终 产 品 出现 边鼓 ; 通过 表 2 图 2可知 , 轧辊后 期 、 粗 磨 损严 重 , 能保证 板 型 良好 必须进 行下 线磨 削。 不 因此 , 为减 小 轧 辊 磨 损 、 证 产 品 质 量 、 高 保 提 生产 效率 ,我们 采用 在 粗轧 辊 孔 表 面进行 激 光
承 钢 中宽 带 厂 粗 轧机 是二 辊 可逆 式 粗 轧 机 , 将 厚 度 4 5 m 板 坯 通 过 9道 次 可 逆 轧 制 成 2 - 9m 0 3 mm的 中间坯 。图 1所示 , 孔 开坯轧 制 4道次 , 0 l 孔 两 道 次 立 轧 , 孔 3道 次平 轧轧 制 成 中 间 坯 进 入热 卷箱 。热轧过 程 中 , 轧辊 由于 受 巨大的 冲击
表面强化技术课件

• 基本过程:将工件放在有足够功率输出 的感应线圈中,在高频交流磁场的作用 下,产生很大的感应电流,并由于集肤 效应而集中分布于工件表面,使表面迅 速加热到钢相变点Ac3或Accm之上,然 后在冷却介质中快速冷却,使工件表面 获得M。
• 2.特点:
• a、加热速度快(感应加热速度可达 103℃ /s,激光加热则可达到105--109℃/s ) 且加热温度要高于整体淬火的温度;
• b、冷却速度快;
• c、表面硬度高(其硬度比普通淬火高 HRC2~4 );
• d、需预备热处理;
• e、适合中高碳钢。
二、感应加热表面淬火
• 1.原理: • 利用感应电流
塑料喷丸退漆是近年来发展起来的新工艺。其原 理为:颗粒状塑料在压缩空气的作用下.通过喷 管高速喷射到工件表面在塑料丸较锋利的棱角切 割和冲撞击打双重作用下使漆层表面发生割裂和 剥离,从而达到高效退漆的目的。
6.喷丸新技术-空气火焰超音速表面喷 砂、喷丸
空气火焰超音速表面喷砂、喷丸:空气火焰超音 速表面预处理技术,是利用气体燃料或液体燃料 与高压电气或高压空气.在超音速喷枪燃烧室内 混合燃烧膨胀产生高温高速焰流.从而带动砂粒 或丸粒以超音速喷向零件处理表面。燃烧焰流速 度达1500m/s以上,粒子速度为300—600m/s,从 而可获得高效优质的表面预处理效果。
• 2.机理: 加工硬化机理。即随变形量的 增加,金属强度硬度升高,塑性韧性下 降。
• 原因:a、位错密度随变形量增加而增加, 从而变形抗力增加;b、随变形量增加, 亚结构细化,亚晶界对位错运动有阻碍; c、随变形量增加,空位密度增加;d、 几何硬化。
二、喷丸强化
▪ 1.原理:喷丸强化又称为受控喷丸强化,
轧辊激光表面处理工艺对轧辊表面质量的影响研究

轧辊激光表面处理工艺对轧辊表面质量的影响研究随着工业技术的不断发展,轧辊激光表面处理工艺被广泛应用于金属材料的加工和表面改性。
在金属制造业中,轧辊作为关键的制造工具,其表面质量对产品的质量和生产效率具有重要影响。
因此,了解轧辊激光表面处理工艺对轧辊表面质量的影响是非常重要的。
轧辊激光表面处理工艺是一种使用激光作为能量源对轧辊表面进行加工和改性的技术。
该工艺具有以下几个优点:高能量密度、无接触加工、热影响区(HEZ)较小、加工速度快、可控性好等。
这些优点使得轧辊激光表面处理工艺成为一种受欢迎的表面处理工艺。
首先,轧辊激光表面处理工艺对轧辊表面质量的影响主要体现在以下几个方面。
第一,激光熔覆。
激光熔覆是一种将粉末材料通过高能量密度的激光束熔化并喷涂到轧辊表面的工艺。
激光熔覆可以大幅度改善轧辊的表面硬度、磨损性能和耐蚀性能。
此外,激光熔覆还可以修复轧辊表面的损伤,提高其使用寿命。
第二,激光熔化。
激光熔化是一种通过激光束直接加热轧辊表面,使其瞬间熔化并迅速冷却的工艺。
激光熔化可以使轧辊表面形成高度致密的结构,提高轧辊的表面硬度和耐磨性。
此外,激光熔化还可以消除轧辊表面的气孔和裂纹,提高轧辊的使用寿命和性能。
第三,激光合金化。
激光合金化是一种将合金粉末喷涂到轧辊表面后进行激光加热处理的工艺。
激光合金化可以使轧辊表面形成均匀的合金层,提高轧辊的硬度、抗磨性和耐蚀性。
此外,激光合金化还可以调整轧辊表面的化学成分,进一步提高轧辊的性能。
除了以上几种表面处理工艺,还有其他一些激光表面处理工艺,如激光抛光、激光熔化等,它们都可以对轧辊表面质量产生重要影响。
然而,轧辊激光表面处理工艺也面临一些挑战。
首先,轧辊材料的选择对加工过程和表面质量具有重要影响。
不同材料的熔点、热导率和热膨胀系数等物理特性会影响工艺参数的选择和表面质量的控制。
其次,激光能量的选择和控制对轧辊表面质量的影响也很大。
激光能量过高或过低都可能导致表面质量不理想。
- 1、下载文档前请自行甄别文档内容的完整性,平台不提供额外的编辑、内容补充、找答案等附加服务。
- 2、"仅部分预览"的文档,不可在线预览部分如存在完整性等问题,可反馈申请退款(可完整预览的文档不适用该条件!)。
- 3、如文档侵犯您的权益,请联系客服反馈,我们会尽快为您处理(人工客服工作时间:9:00-18:30)。
, ,
图
〔 〕 王 长贵 李 志远 黄安 国
钢铁 组织 及 性 能 分析 〔 〕
, ,
侧 阮
铸 钢 轧辊 激 光 熔 凝 强 化 的
一
又
,
醉
〔 〕 姜 幼 卿 黄安 国 周 龙早等 冶金 用 铸 钢 轧辊激光 熔凝 强 化 的 研 究 和 应 用 〔〕 钢铁
,
,
,
,
。
以兀
,
一
,
〔 〕 王 贵 王 建 国 周 新初 等 轧辊钢 激 光熔凝 处 理 组 织 及 性能研 究
金属 热 处 理 〔〕
, ,
,
,
一
的硬度 曲 的硬度 曲线基本 位 于 激 光功 率 为 仪 。 线 上 方 都不 产 生 软 化带 在 图 中 激光 扫描 速 率 同 为
为
,
。
,
〔 〕 代 毅 黄 文 荣 汤 光平 激 光 技术
变诱 导 马 氏 体相 变 和 微 细 碳 化物 析 出
,
。
一 定 量 的残 余 奥 氏
。
体具有 提高 抗裂纹 扩 展 的能 力 能有 效避 免粘 着 破 坏
图
次表
淬硬 区 微 观组 织 夕 】
,
激 光 相 变 强 化硬 度 分 布 根 据 不 同 的工 艺参 数处 理 的 扫 描 道 进 行沿 深度方 向 的 一 型 显 微 硬度 计 显 微 硬度 测 试 实验所 用 仪 器 为
。
,
面 的残余 奥 氏体 可 以 避 免 与摩擦 副直 接接触 而遭 到 粘 着 破
坏
。
同 时 残 余 奥 氏 体 在转 变 为 马 氏 体 的 过 程 中 有 利 于 提
。
,
,
高轧 辊 的使用 寿命
轧辊 的使用 性 能
。
因此 一 定量 的 残 余奥 氏 体 并不 会 影 响
,
硬 度试 验加 载力 么刃梦 保 压时间
激 光杂 志 》 《
所 以 不熔解 但 在奥 氏 体 化 后 在 激光 淬 火 的条 件 下 会 发 生 马 氏体相 变 形 成隐 晶马 氏体 残 余 奥 氏 体 细小 的
,
辊 用 钢激 光相 变 强 化研究
巧
双刃
℃
,
,
高铬 钢激光相变 硬 化 处 理 后 会 由 于 白亮 区 的 熔 化 产 生 一 个
,
提 高到
。
峰值 可达
驯刃
。
当扫描 速度 为
口扩
,
激光 功 率 为 刀田
,
光斑直径为
一
时 可得到
肠 石一 似 钊侧
一 一
,
深 的淬硬层 且 不 出现 软化带
,
关 键 词 激 光 技术 高碳高铬轧辊 激 光 淬火 显微组 织 软化带
中 圈分类 号
七
肠 卯
文 献 标识 码
别犯
曰
一
,
文 章编 号 伏巧
红习 璐伪
, ,
时 没有软 化 区 生 成
。
刀
刃
一
实 验 结果 分 析
由高铬钢 硬 度 曲线 图 发 现 当激 光 功 率 大 于
,
〔 〕 刘 江龙 邹 至 荣 激 光 相 变 硬 化 后 的 残 余 奥 氏 体 分 析
机械 〕
时
,
工 程材料
,
,
一
近室温 结果 只 有少 量 转 变 为 马 氏 体 大部分则 以 残余 奥 氏
,
。
体 的形式 存 在
用
。
。
,
射线衍射 仪测 高 铬钢 的残 余 奥 氏体 含 量 扫描速度
口
可 以 看到 晶界 部分碳 化 物部分熔 解 晶 内为屈 氏体
,
。
同为
含量为
,
时 当激 光 功 率 为
,
尸 尸
二
仪 班
。
,
冷 却后 残余
,
抽记即
驯叉
,
由面 司
几叱 伴司
肠 旧妞
。
呷
日“ 屺
曰加
印
曲 司 吨 而
旧 山
移
田记
双币即
翔
价 『。 ,
加
,
甲
功
如
甲
二坛
一
一
动
叱
,
翔
花
,
动
川
。
热 轧 辊作 为冶金 轧 钢 厂 轧制 生 产 的 关 键部 件 要 求 整 体 有较好 的强 韧 性 配 合 尤 其 工 作表 面 必 须 具有较 高 的 耐 磨 性 ‘ 泪 和 抗 热 疲劳性 〔 为此 常用 高频 淬火 堆 焊等 阁 方法 进行
,
相应 地得到 提高
二
,
挤
,
功 率密度
,
二
宇 时 可产生
图
深度 的 淬 硬 深度 不 产 生 软 化
参 考 文 献
高碳 高铬 轧辊 用 钢激 光 相 变 强 化 硬 度 分布 曲线 图
。
, ,
带 以适应 生 产 要 求
, ,
。
从 图 中可 高 钢 激光淬 火 后 的显 微 硬 度 在 深度 方 向上 自 白亮 区 向 母 材 递 幻 时 白亮 区 接 近 表层 的 地 方 显 微 硬度 减 当功 率 高 于 一 较低 逐 渐 增 大 到 一 峰 值 后 开 始 向基材递 减 以 可 看 出 扫描速 率 同为 加“ 的情况 下 激 光 功 率 从图
欧 么刃 《 激光 杂 志 》
繁辊
用钢激光 相变强 化研究
州
么刀
高碳 高 铬 轧 辊 用 钢 激 光 相 变 强 化 研 究
‘ ’ ’ ’ 欧阳安 黄安国 王 玉 涛 王 长贵 吴国胜 李志远
, ,
, , ,
华 中科技 大 学材 料成 形 与 模 具 技 术 国 家重 点 实验 室 武 汉
,
武 汉钢 铁 集 团 公 司研 究 院 武 汉
软化带 软化带深 度 范 围为距 边 缘 大致
辊 表 面 的温 度 可 以 达 到
℃以 上
,
,
,
以内
。
℃以 上 在 晶界 上 熔 解 的碳 碳化 物 淬 硬 区 部 分温 度在 化 物会 发 生 碳 向晶内扩散 使 原来 的 碳 化 物 白区 变 宽 快 速 冷却后 在原 来 碳 化 物 区 域 内产 生 残 余 奥 氏 体 和 碳 化 物 共 晶 但 尺 寸较原来 变小 从 而达 到 晶粒 细 化 的效果 图 所 示 的是 淬 硬 区 的微观结构 其 中 图 映 了从 白亮 区 到基 材 的碳化 物发 生 的变化 在 白亮 区 碳 化 物几 乎 全 部 熔解 淬硬 区 内碳 化 物部分 熔 解 碳 化 物扩 散 导致 白 区 变宽 基 材 中碳 化物 不 发 生 熔 解 图 为淬 硬 区 内部 分碳 化物熔 解 图 为激 光 相 变 强 化 后 基 体 组织 照 片 从 图 中
处理 的难点 主要表 现 为易 于 出 现熔 化 区 由于 熔化 区 碳 含量
,
高 容易 出现微裂纹 并 且 大 量 的残 余 奥 氏 体导致 该 区 的 硬 度 降低 不 能 起 到激光相变硬化 的效 果 本文 采 用 高功 率 激 光器进 行 了 高碳 高铬 轧辊 激 光 相 变强 化试验研 究 并 进行 了 组 织 变化 和 硬 度特征分析
明显 的 白亮 区 奥 氏 体 枝状 晶 胞 状 晶及 奥 氏 体 一 碳 化 物 共
、
,
晶
、
淬硬 区 隐 晶 马 氏 体
。
残余 奥 氏 体
,
细 小 的碳 化 物 和
母材 三 个 区 域 提高 到 当
,
在激光相 变 硬 化 处 理 中 相 变 硬 度 由 基材 的
一
。
,
峰值可 以 达 到
,
以幻
,
硬 度 和 耐磨 性 都
,
。
结论
本 文 采用
,
连 续横 流 仇 激 光 器对 高碳 高 铬轧辊进
, ,
行 了 激光相 变 强 化 试 验 并 进 行 了 显 微 组 织 分 析 和 硬 度 测 试 分析 了软化带 出现 的 原 因 得 出 以 下 结 论
高碳 高铬 轧 辊进 行 激 光 相 变 强 化 后 显 微 组 织 存 在
,
奥 氏 体 含量 已 达
当激 光 功 率 为
。
残 余 奥 氏体
,
同时未熔 碳 化 物 总 含量 也很 少
。
这说明 激 光
功 率越 高 残 余奥 氏 体量越大 导 致软化带产 生 的根 本原 因
而 大 量 残 余 奥 氏 体 的存 在 是
,
残余 奥 氏 体 在受 到较 大 的 应 力 作 用 下 可 以 发 生 应
,
,
,
】 不 锈 钢 激光 表 面强 化技 术 研 究 〔 〕
、时
拼田
,
在 距 离 表 层 岌刃脚 的 深 度 处 激 光 处 理 功 率 为 时 出 现 了一 定 深 度 的 软 化 区 而 激 光 功 率 为
,
,
,
狡
,
刀一
,
【 〕 黄 开 金 谢 长生 许 德胜 脉 冲激光熔凝 和 相 变 硬 化 的 研 究现 状 〔〕 激 光技 术 浏刃
,
化组 织 并 可 得到相变 强 化 硬度 的分布 曲线
。
,
、
表 面 处理 但 这些方法 会 使 轧辊在 凝 固 过程 中易沿 晶界 产 生 热裂纹 影 响其强 度 激光相 变 强 化 处 理 技 术能 获得 硬 度很