注塑成型工艺过程和特性之结晶性塑料
塑料注塑性能工艺概括
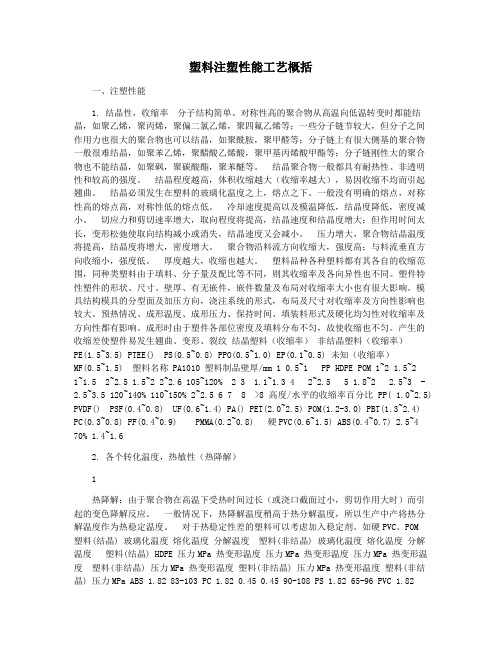
塑料注塑性能工艺概括一、注塑性能1. 结晶性,收缩率分子结构简单、对称性高的聚合物从高温向低温转变时都能结晶,如聚乙烯,聚丙烯,聚偏二氯乙烯,聚四氟乙烯等;一些分子链节较大,但分子之间作用力也很大的聚合物也可以结晶,如聚酰胺,聚甲醛等;分子链上有很大侧基的聚合物一般很难结晶,如聚苯乙烯,聚醋酸乙烯酸,聚甲基丙烯酸甲酯等;分子链刚性大的聚合物也不能结晶,如聚砜,聚碳酸酯,聚苯醚等。
结晶聚合物一般都具有耐热性、非透明性和较高的强度。
结晶程度越高,体积收缩越大(收缩率越大),易因收缩不均而引起翘曲。
结晶必须发生在塑料的玻璃化温度之上,熔点之下。
一般没有明确的熔点,对称性高的熔点高,对称性低的熔点低。
冷却速度提高以及模温降低,结晶度降低,密度减小。
切应力和剪切速率增大,取向程度将提高,结晶速度和结晶度增大;但作用时间太长,变形松弛使取向结构减小或消失,结晶速度又会减小。
压力增大,聚合物结晶温度将提高,结晶度将增大,密度增大。
聚合物沿料流方向收缩大,强度高;与料流垂直方向收缩小,强度低。
厚度越大,收缩也越大。
塑料品种各种塑料都有其各自的收缩范围,同种类塑料由于填料、分子量及配比等不同,则其收缩率及各向异性也不同。
塑件特性塑件的形状、尺寸、壁厚、有无嵌件,嵌件数量及布局对收缩率大小也有很大影响。
模具结构模具的分型面及加压方向,浇注系统的形式,布局及尺寸对收缩率及方向性影响也较大。
预热情况、成形温度、成形压力、保持时间、填装料形式及硬化均匀性对收缩率及方向性都有影响。
成形时由于塑件各部位密度及填料分布不匀,故使收缩也不匀。
产生的收缩差使塑件易发生翘曲、变形、裂纹结晶塑料(收缩率)非结晶塑料(收缩率)PE(1.5~3.5) PTEE() PS(0.5~0.8) PPO(0.5~1.0) EP(0.1~0.5) 未知(收缩率)MF(0.5~1.5) 塑料名称 PA1010 塑料制品壁厚/mm 1 0.5~1 PP HDPE POM 1~2 1.5~21~1.5 2~2.5 1.5~2 2~2.6 105~120% 2 3 1.1~1.3 4 2~2.5 5 1.8~2 2.5~3 - 2.5~3.5 120~140% 110~150% 2~2.5 6 7 8 >8 高度/水平的收缩率百分比 PP( 1.0~2.5) PVDF() PSF(0.4~0.8) UF(0.6~1.4) PA() PET(2.0~2.5) POM(1.2-3.0) PBT(1.3~2.4) PC(0.3~0.8) PF(0.4~0.9) PMMA(0.2~0.8) 硬PVC(0.6~1.5) ABS(0.4~0.7) 2.5~4 70% 1.4~1.62. 各个转化温度,热敏性(热降解)1热降解:由于聚合物在高温下受热时间过长(或浇口截面过小,剪切作用大时)而引起的变色降解反应。
尼龙注塑成型工艺
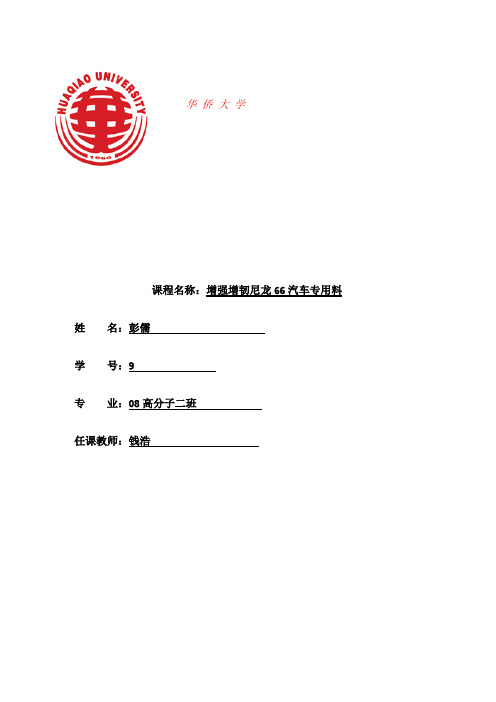
华侨大学课程名称:增强增韧尼龙66汽车专用料姓名:彭儒学号:9专业:08高分子二班任课教师:钱浩前言:尼龙是结晶型塑料,品种颇多,已达到130多种,应用于注塑加工的有尼龙6、尼龙66、尼龙610、尼龙1010以及共聚性尼龙、超韧性尼龙、玻璃纤维增强尼龙、矿物增强尼龙等等。
世界市场中,应用量最大的是尼龙66。
尼龙最早在1889年首先由Gabriel和Maass 两人合成制得,但系统的研究并最终实现工业化实在1929年,由美国杜邦公司的Carothers着手进行的。
1931年Carothers申请了第一篇尼龙专利,1935年首先制得尼龙66,1939年实现工业化。
尼龙66的应用领域一般在汽车、电子电器、化工设备、机械设备等方面。
从最终用途看,汽车行业消耗的尼龙66占第一位,电子电器占第二位。
大约有88%的尼龙66通过注射成型加工成各种制件,约12%的尼龙66则通过挤出、吹塑等成型加工成相应的制品。
由于尼龙66优良的耐热性、耐化学药品性、强度和加工方便等,因而在汽车工业得到了大量应用,目前几乎已能用于汽车的所有部位,如发动机部位,电器部位和车体部位。
发动机部位包括进气系统和燃油系统,如发动机气缸盖罩、节气门、空气滤清器机器外壳,车用空气喇叭、车用空调软管、冷却风扇及其外壳、进水管、刹车油罐及灌盖,等等。
车体部位零部件有:汽车挡泥板、后视镜架、保险杠、仪表盘、行李架、车门手柄、雨刷支架、安全带扣搭、车内各种装饰件等等。
车内电器方面如电控门窗、连接器、保鲜盒、电缆扎线等。
工艺特点:⑴吸水性尼龙66较易吸湿,如果长时间暴露在空气下,会吸收大气中的水分。
吸水后会发生体积膨胀,影响制品的尺寸精度,如在注塑前吸收过量的水分时,其制作的外国外观和力学性质都会受损。
⑵结晶性尼龙66为结晶性高聚物,一般在20%~30%之间。
结晶度的高低与性能有关,结晶度高,拉伸强度、耐磨性、硬度、润滑性等性能有所提高,热膨胀系数和吸水性趋于下降。
PET塑料注塑工艺解析
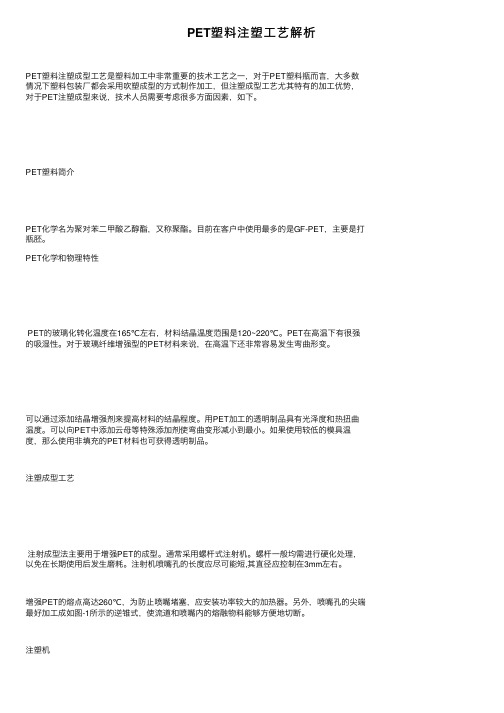
PET塑料注塑⼯艺解析PET塑料注塑成型⼯艺是塑料加⼯中⾮常重要的技术⼯艺之⼀,对于PET塑料瓶⽽⾔,⼤多数情况下塑料包装⼚都会采⽤吹塑成型的⽅式制作加⼯,但注塑成型⼯艺尤其特有的加⼯优势,对于PET注塑成型来说,技术⼈员需要考虑很多⽅⾯因素,如下。
PET塑料简介PET化学名为聚对苯⼆甲酸⼄醇酯,⼜称聚酯。
⽬前在客户中使⽤最多的是GF-PET,主要是打瓶胚。
PET化学和物理特性PET的玻璃化转化温度在165℃左右,材料结晶温度范围是120~220℃。
PET在⾼温下有很强的吸湿性。
对于玻璃纤维增强型的PET材料来说,在⾼温下还⾮常容易发⽣弯曲形变。
可以通过添加结晶增强剂来提⾼材料的结晶程度。
⽤PET加⼯的透明制品具有光泽度和热扭曲温度。
可以向PET中添加云母等特殊添加剂使弯曲变形减⼩到最⼩。
如果使⽤较低的模具温度,那么使⽤⾮填充的PET材料也可获得透明制品。
注塑成型⼯艺注射成型法主要⽤于增强PET的成型。
通常采⽤螺杆式注射机。
螺杆⼀般均需进⾏硬化处理,以免在长期使⽤后发⽣磨耗。
注射机喷嘴孔的长度应尽可能短,其直径应控制在3mm左右。
增强PET的熔点⾼达260℃,为防⽌喷嘴堵塞,应安装功率较⼤的加热器。
另外,喷嘴孔的尖端最好加⼯成如图-1所⽰的逆锥式,使流道和喷嘴内的熔融物料能够⽅便地切断。
注塑机注塑成型主要⽤于增强PET的成型。
PET⼀般情况下只能选⽤螺杆式注塑机成型。
最好选⽤顶部带有⽌逆环的突变型螺杆,其表⾯硬度⼤⽽且耐磨损,长径⽐未L/D=(15~20):1压缩⽐约为3:1。
L/D太⼤物料在料筒内停留时间过长,过度受热容易引起降解,影响制品性能。
压缩⽐太⼩剪切⽣热少,易塑化不良,制品性能差。
反之会使玻璃纤维较多的断裂,⼒学性能下降。
加⼯玻璃纤维增强PET时,料筒内壁磨损较厉害,料筒使⽤耐磨材料制造或者衬有耐磨材料。
喷咀以短为好,内壁要求磨光,孔径要求尽可能⼤些。
以液压制动阀门式喷咀为好。
喷咀要有保温和控制温度的措施来保证喷咀不会冻结堵塞。
塑料注塑工艺标准

塑料注塑工艺标准1、PP塑料制品:1.1概述:聚丙烯,英文简称PP,为一种白色蜡状材料,密度0.90g/cm3。
PP具有良好的电性能和化学稳定性,其机械性能、耐热性均高于PE,经过增强的PP可用做工程材料。
PP成纤性好,耐疲劳性好,用其制成的铰链几十万次不断;PP低温冲击性不好,成型收缩率大,产品精度不高。
1.2加工:1.2.1成型特性:1.2.1.1结晶性料,吸湿性小,可能发生熔融破裂,长期与热金属接触易发生分解。
1.2.1.2流动性极好,溢边值0.03mm左右。
1.2.1.3冷动速度快,浇注系统及冷却系统应散热缓慢。
1.2.1.4成型收缩范围大,收缩率大,易发生缩孔、凹痕、变形、方向性强。
1.2.1.5注意控制成型温度,料温低方向性明显,尤其是低温高压时更明显,模温低于50℃以下塑件不光泽,易发生熔接不良、流痕;90℃以上时易发生翘曲、变形。
1.2.1.6塑件应壁厚均匀,避免缺口、尖角,以避免应力集中。
1.2.1.7注塑模及注塑制品:A、最小脱模斜度30’---1°。
B、最小壁厚0.85mm。
C、流程与壁厚的关系: ,其中t为壁厚(mm),l为流程(mm)。
D、塑件转接处均应有不小于0.5---1mm的圆角。
E、塑件壁厚应尽可能均匀一致,以防制品结构缩水和翘曲、变形。
1. 3注塑工艺条件:1.2.3.1干燥温度和时间:封袋PP无须干燥即可注塑,预热温度和时间:80---100℃/1---2h。
1.2.3.2料筒温度:200---230℃。
1.2.3.3射嘴温度:180---190℃。
1.2.3.4模温:20---60℃。
1.2.3.5注射压力:≤69---98Mpa1.2.3.6注射时间(包括保压时间):≤20---60S。
1.2.3.7冷却时间:≤20---90S。
1.2.3.8螺杆转速:≤80rpm。
2、PE塑料制品:2.1概述:聚乙烯,英文简称PE,有低密度聚乙烯(LDPE)、高密度聚乙烯(HDPE)及线性低密度聚乙烯(LLDPE)三种。
常用塑料的注塑工艺分析
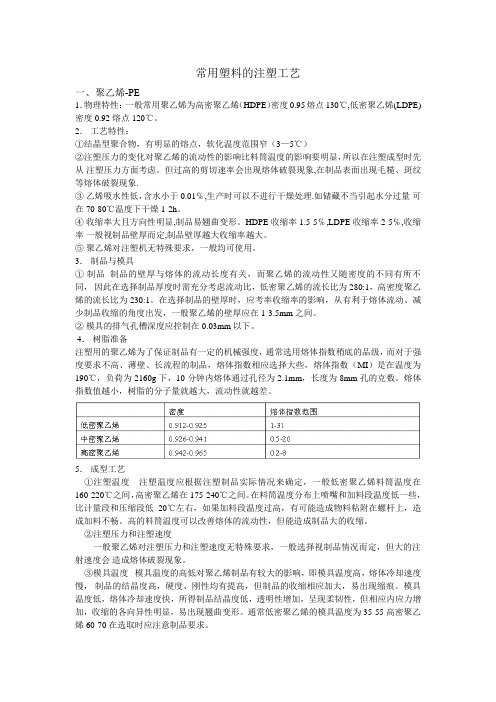
常用塑料的注塑工艺一、聚乙烯-PE1.物理特性:一般常用聚乙烯为高密聚乙烯(HDPE)密度0.95熔点130℃,低密聚乙烯(LDPE)密度0.92熔点120℃。
2.工艺特性:①结晶型聚合物,有明显的熔点,软化温度范围窄(3—5℃)②注塑压力的变化对聚乙烯的流动性的影响比料筒温度的影响要明显,所以在注塑成型时先从注塑压力方面考虑。
但过高的剪切速率会出现熔体破裂现象,在制品表面出现毛糙、斑纹等熔体破裂现象.③乙烯吸水性低,含水小于0.01℅,生产时可以不进行干燥处理.如储藏不当引起水分过量可在70-80℃温度下干燥1-2h。
④收缩率大且方向性明显,制品易翘曲变形。
HDPE收缩率1.5-5℅,LDPE收缩率2-5℅,收缩率一般视制品壁厚而定,制品壁厚越大收缩率越大。
⑤聚乙烯对注塑机无特殊要求,一般均可使用。
3.制品与模具①制品制品的壁厚与熔体的流动长度有关,而聚乙烯的流动性又随密度的不同有所不同,因此在选择制品厚度时需充分考虑流动比,低密聚乙烯的流长比为280:1,高密度聚乙烯的流长比为230:1。
在选择制品的壁厚时,应考率收缩率的影响,从有利于熔体流动、减少制品收缩的角度出发,一般聚乙烯的壁厚应在1-3.5mm之间。
②模具的排气孔槽深度应控制在0.03mm以下。
4.树脂准备注塑用的聚乙烯为了保证制品有一定的机械强度,通常选用熔体指数稍底的品级,而对于强度要求不高、薄壁、长流程的制品,熔体指数相应选择大些,熔体指数(MI)是在温度为190℃,负荷为2160g下,10分钟内熔体通过孔径为2.1mm,长度为8mm孔的克数。
熔体指数值越小,树脂的分子量就越大,流动性就越差。
5.成型工艺①注塑温度注塑温度应根据注塑制品实际情况来确定,一般低密聚乙烯料筒温度在160-220℃之间,高密聚乙烯在175-240℃之间。
在料筒温度分布上喷嘴和加料段温度低一些,比计量段和压缩段低20℃左右,如果加料段温度过高,有可能造成物料粘附在螺杆上,造成加料不畅。
常用塑料注塑工艺参数

6、RPVC注塑中的注意问题: 选用螺杆式注塑机,不能选用柱塞注塑机; 要做好设备的防腐工作; 所有与PVC塑料接触的部分,不充许对塑化熔体产生任何粘附或 滞留; 设备的温度控制系统应指标准确,反应灵敏; 螺杆长径比可小些,螺杆头部呈尖头;螺杆的压缩比为2~2.5, 螺杆的三段长度可分别设置为40%、40%和20%; 选用孔径的通用喷嘴,并配有加热控温装置; 掌握好清洗料筒的技术; 注意温升程序,并在料筒升温过程中,应密切注意温升情况。 料筒内的物料是否过热,可通过主流道料的表面是否有棕色条纹 来判断。如果主流道的料有棕色条纹,则说明料筒内的塑料已过 热,应立即采取措施,对料筒进行清洗,切不可继续操作; 停机时,应先将料筒内的料全部排完,并用PS或PE等塑料及时清 洗料筒,或加入专用的PVC停车料将料筒原来的RPVC基本过清方 可停机。 停机后立即在模具的型腔与流道表面等处涂油防锈。
1、PS为无定型塑料,熔融温度范围较宽,热稳定性较好; 2、热变形温度为70~100℃,粘流温度为150~204℃, 300℃以上出现分解; 3、PS熔体的粘度对温度的敏感性和对剪切速率的敏感性都适 中,流动性好,易成型; 4、PS树脂的吸水率很低,一般为0.01~0.03%,成型前可 不干燥 ,[必要时,可在70~80℃的循环热风中干燥2~ 3h]。 5、注塑时的料筒温度控制在180~215℃范围内,喷嘴温度比 料筒最高温度低10~20℃。 6、注射压力一般控制在60~150MPa。大浇口、形状简单及厚 壁制品,注射压力可选低些,约60~80MPa。 7、易形成内应力并引起开裂,残余应力问题较为突出。为减 小内应力,加工时往往需要较高的料温、模温,以使熔体 缓慢冷却,取向的分子得到松弛。也可选择流动性高的品 级,或添加流动性助剂;
各种塑料的成型参数

ABS 丙烯腈-丁二烯-苯乙烯共聚物典型应用范围:汽车(仪表板,工具舱门,车轮盖,反光镜盒等),电冰箱,大强度工具(头发烘干机,搅拌器,食品加工机,割草机等),电话机壳体,打字机键盘,娱乐用车辆如高尔夫球手推车以及喷气式雪撬车等。
注塑模工艺条件:干燥处理:ABS材料具有吸湿性,要求在加工之前进行干燥处理。
建议干燥条件为80~90C下最少干燥2小时。
材料温度应保证小于0.1%。
熔化温度:210~280C;建议温度:245C。
模具温度:25…70C。
(模具温度将影响塑件光洁度,温度较低则导致光洁度较低)。
注射压力:500~1000bar。
注射速度:中高速度。
化学和物理特性:ABS是由丙烯腈、丁二烯和苯乙烯三种化学单体合成。
每种单体都具有不同特性:丙烯腈有高强度、热稳定性及化学稳定性;丁二烯具有坚韧性、抗冲击特性;苯乙烯具有易加工、高光洁度及高强度。
从形态上看,ABS是非结晶性材料。
三中单体的聚合产生了具有两相的三元共聚物,一个是苯乙烯-丙烯腈的连续相,另一个是聚丁二烯橡胶分散相。
ABS的特性主要取决于三种单体的比率以及两相中的分子结构。
这就可以在产品设计上具有很大的灵活性,并且由此产生了市场上百种不同品质的ABS材料。
这些不同品质的材料提供了不同的特性,例如从中等到高等的抗冲击性,从低到高的光洁度和高温扭曲特性等。
ABS材料具有超强的易加工性,外观特性,低蠕变性和优异的尺寸稳定性以及很高的抗冲击强度。
PC 聚碳酸酯典型应用范围:电气和商业设备(计算机元件、连接器等),器具(食品加工机、电冰箱抽屉等),交通运输行业(车辆的前后灯、仪表板等)。
注塑模工艺条件:干燥处理:PC材料具有吸湿性,加工前的干燥很重要。
建议干燥条件为100C到200C,3~4小时。
加工前的湿度必须小于0.02%。
熔化温度:260~340C。
模具温度:70~120C。
注射压力:尽可能地使用高注射压力。
注射速度:对于较小的浇口使用低速注射,对其它类型的浇口使用高速注射。
塑料在成型过程中的变化1(精)
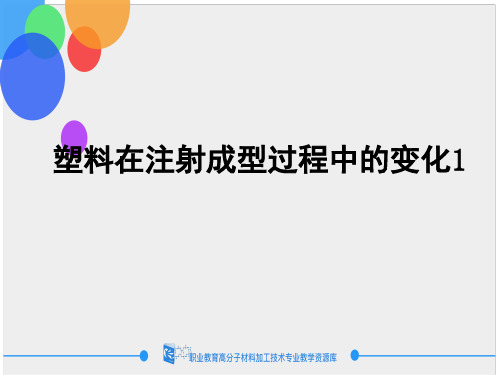
如:聚乙烯、聚偏氯乙烯、聚异丁烯、 聚四氟乙烯、反式聚丁二烯、全同聚丙烯、 全同聚苯乙烯等易结晶。无规聚丙烯、聚苯 乙烯、聚甲基丙烯酸甲酯、顺式聚丁二烯、 乙烯丙烯无规共聚物等不结晶。聚氯乙烯为 低结晶度。天然橡胶在高温下结晶。
3 高聚物的结晶能力与结晶过程
温度对结晶速度影响最大,高于(熔点)或 低于(玻璃化转变温度)都不能结晶。结晶开 始的温度比低10~30℃,这一个区域称为过冷 区。结晶速率最大值出现在与之间,可以从和/ 或值来估计,公式如下(温度取K计算):
如前所述,熔融温度高和熔融时间长,则 结晶速率慢,结晶尺寸大;相反,熔融温度 低,时间短,则结晶速率快,晶体尺寸小而 均匀,有利于提高制品的力学性能和热变形 温度。
8 应力对结晶的结构和形态的影响
在剪切应力和拉伸应力作用下,熔体中往 往生成一长串纤维晶体。
9 结晶对性能的影响
由于完全结晶与完全无定形的试样很难制得, 所以结晶对聚合物性能的影响只能根据结晶度的不 同进行相对比较。结晶过程中分子链敛集作用使聚 合物的体积收缩,密度增大。密度增大意味着分子 间引力增加,分子集中而有序,这就使得晶态聚合 物的某些物理力学性能如弹性模量、硬度、屈服强 度等随着结晶度的增加而提高;而聚合物的抗冲击 强度和断裂伸长率则随结晶度的提高而降低。结晶 度增大,还会使材料变脆。
球晶的形成过程包括成核、生长和截顶终 止。成核分均相成核和异相成核两种,前者 来源于分子的热运动产生的局部有序排列, 因而不是同时出现的;后者来源于杂质或熔 融的残存结构,称“预定核”。
4 聚合物的结晶度 结晶性高聚物与结晶高聚物是两个不同 的概念,结晶度定义为:不完全结晶的聚合 物中晶相所占的质量分数(或体积分数)。 应当指出:由于结晶聚合物中同时存在着不 同程度的有序状态,晶区与非晶区的界限不 明确,再加以各种测试方法对晶区与非晶区 的理解不同,所以测得的结晶度差别很大。 因此在提出聚合物的结晶度时,必须说明测 试的方法。
15种塑料特性和加工条件
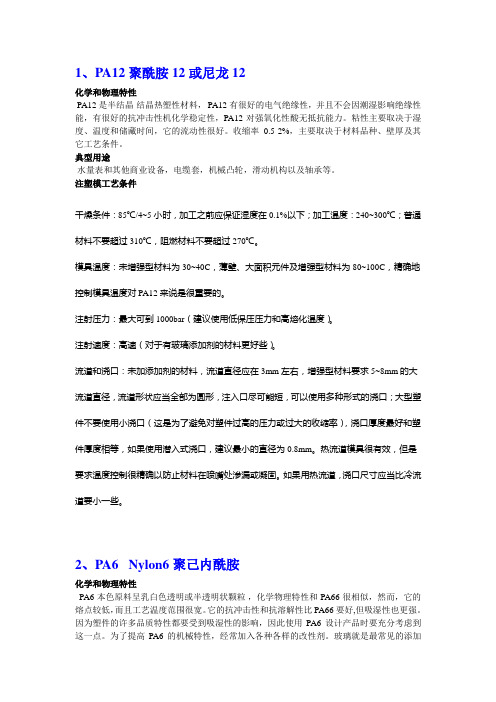
1、PA12 聚酰胺12或尼龙12化学和物理特性PA12是半结晶-结晶热塑性材料, PA12有很好的电气绝缘性,并且不会因潮湿影响绝缘性能,有很好的抗冲击性机化学稳定性,PA12对强氧化性酸无抵抗能力。
粘性主要取决于湿度、温度和储藏时间,它的流动性很好。
收缩率0.5-2%,主要取决于材料品种、壁厚及其它工艺条件。
典型用途水量表和其他商业设备,电缆套,机械凸轮,滑动机构以及轴承等。
注塑模工艺条件干燥条件:85℃/4~5小时,加工之前应保证湿度在0.1%以下;加工温度:240~300℃;普通材料不要超过310℃,阻燃材料不要超过270℃。
模具温度:未增强型材料为30~40C,薄壁、大面积元件及增强型材料为80~100C,精确地控制模具温度对PA12来说是很重要的。
注射压力:最大可到1000bar(建议使用低保压压力和高熔化温度)。
注射速度:高速(对于有玻璃添加剂的材料更好些)。
流道和浇口:未加添加剂的材料,流道直径应在3mm左右,增强型材料要求5~8mm的大流道直径,流道形状应当全部为圆形,注入口尽可能短,可以使用多种形式的浇口;大型塑件不要使用小浇口(这是为了避免对塑件过高的压力或过大的收缩率),浇口厚度最好和塑件厚度相等,如果使用潜入式浇口,建议最小的直径为0.8mm。
热流道模具很有效,但是要求温度控制很精确以防止材料在喷嘴处渗漏或凝固。
如果用热流道,浇口尺寸应当比冷流道要小一些。
2、PA6 Nylon6聚己内酰胺化学和物理特性PA6本色原料呈乳白色透明或半透明状颗粒,化学物理特性和PA66很相似,然而,它的熔点较低,而且工艺温度范围很宽。
它的抗冲击性和抗溶解性比PA66要好,但吸湿性也更强。
因为塑件的许多品质特性都要受到吸湿性的影响,因此使用PA6设计产品时要充分考虑到这一点。
为了提高PA6的机械特性,经常加入各种各样的改性剂。
玻璃就是最常见的添加剂,有时为了提高抗冲击性还加入合成橡胶,如EPDM和SBR等。
注塑生产工艺及问题解析

注塑生产工艺及问题解析一、注塑成型工艺过程1、注塑过程完整的注塑过程包括加料、塑化、注射入模、保压冷却和脱模等几个步骤,但究其实质可看做只是塑化和流动/冷却两个过程.(1)塑化这是塑料在料筒内经加热及螺杆旋转剪切达到流动状态并具备良好可塑性的全过程。
螺杆旋转不断地将料斗中落下的料粒拽入料筒的同时螺杆后退让料筒中的料在外电热及剪切摩擦热下进行熔化,最后将已熔融的胶料定量贮存到螺杆端部等待注射.(2)流动与冷却这一过程是指螺杆在油缸作用下前进,将具有流动性和温度均匀的熔胶注入模具开始,而后经过型腔注满,熔体在受控制条件下(如施以保压)冷固定型,直至塑件在模中脱出.a)充满阶段:这一阶段以螺杆开始向前移动起,直玫模腔被熔胶充满.b)压实阶段:这是指熔胶充满模腔时起至螺杆撤回(倒索)为至的阶段.C)倒流阶段:这一阶段是从螺杆后退时开始的,这时模腔内的压力比流道内高,因此就会发生未凝结的熔胶倒流,使模腔内的压力下降.d)冻结后的冻却阶段:这一阶段是指浇口的塑料完全冻结时起到塑件在模内顶出为止.2、成型工艺条件注塑工艺最重要的条件即是影响塑化流动和冷却的温度、压力及相应的各个作用时间。
可以说:要保证塑件质量合格及稳定,必须的条件是准确而稳定的工艺参数。
在调整工艺参数时,原则上按压力--------------- 时间----- 温度的顺序来调机,不应该同时变动两个或以上参数,防止工艺条件紊乱造成塑件质量不稳定.以下是对各工艺参数的说明:(D温度参数注塑成型过程中需控制的温度有料筒温度,喷嘴温度和模具温度,料筒温度及喷嘴温度主要影响塑料的流动和冷却. a)料筒温度:一般自后至前逐步升•高,以使均匀塑化.b)喷嘴温度:通常略低于料筒最高温度,防止喷嘴发生“流涎”现象,但亦不可太低防早凝堵塞.C)模具温度:对塑件内在性能和表现质量影响很大,对于表面要求比较高的胶件模温要求较高.(2)压力参数注塑成型过程中的压力包括塑化压力(背压)和注射压力.a)塑化压力(背压)・保证螺杆在旋转覆位时增加塑化压力使熔胶的温度均匀及把挥发性气体包括空气排出射料缸外.・把附加剂(如:色粉.色种.扩散剂等)与熔胶均匀地混合起来・提供均匀稳定的塑化熔胶以便保证塑件重量稳定.・在保证塑件质量的情况下尽可能低以免徙耗损材料・背压的大小调节视胶料不同而异,一般不超过20KG∕CM2(具体各胶料背压值可参见本工艺资料第一部分有关内容)b)注射压力•克服塑料熔体从料筒流向型腔的滞阻力,给予充模压力及对充入的熔料进行压质.•对于流动性差的塑料,注射压力要取大,对于型腔阻力大的薄壁胶料,注射压力也要取大.⑶时间参数(成型周期)I --- 充模时间—注射时间—I' -- 保压时间----- 1I总冷却时间成型周期 --------- 闭模冷却时间------------------ 1---- 其它时间(如:开模.脱模.喷脱剂等)・注射时间和冷却时间是基本组成部分,其多少对啤塑件的质量有决定性的影响.・充模时间一般不超过IOSo・保压时间较长,与胶件臂厚有关(厚壁取长时间),以保证最小收缩.•冷却时间取决于塑料结晶性,制品料厚,模具温度等因素视具体情形调整.⑷注射速度・注射速度通过调节单位时间内向注射油缸供油多少来实现.•一般说来(在不引负作用的前提下)尽量使用高射速充模,以保证塑件熔接强度及表现质量,而相对低的压力也使塑件内应力减小提高了强度.・用高压低速进料的情况可使流速平稳,剪切速度小,塑件尺寸稳定,避免缩水缺陷.二、塑料模的基本认识塑料模具是注射成型生产中赋予塑料形状所用部件的组合体,塑料模的结构视塑料性质、制件形状、结构以及注射机的不同等因素而可能形式大小差异很大,然而其基本结构大致相同,即主要由浇注系统、成型零件、结构零件三大部分组成.其中浇注系统与成型零件是塑料直接接触的部分,并随塑料制品而变化,它是模具中最重要、最复杂、变化最大、要求表面精度及光洁度最高的部分.**浇注系统&成型零件浇注系统指塑料从喷嘴进入型腔的流道部分,包括:主流道、冷料穴、分流道和浇口等.成型零件指构成成品形状的各零件,包括:动、静模型腔/型芯、排气槽、(成型)顶针等.**典型的模具结构典型的模具结构包括以下几个主要部分:1.主流道:是模具连接注射机喷嘴通至型腔或分流道的一段,主流道进口顶部呈凹形,以便与喷嘴连接.主流道进口直径应略大于喷嘴直径(0.8mm)以免溢料并防止两者连接不准而发生堵截.进口直径根据制品大小而定,一般为Φ4-8πιπι主流道直径应向内扩大,呈3-5角度,以便流道顺利出模.2.分流道:在多型腔模中连接主流道和各个型腔的通道.为使熔料能等速度地充满各型腔,分流道在模里的排列应尽可能等距对称,而分流道的截面积形状/尺寸对熔料的流动有很大影响,且对脱模/造模的难易都有影响.常用的分流道截面形状是梯形或半圆形而且是开在带有脱模杆的半模上.流道的表面必须抛光以减小流动阻力而提供较快速度充模,流道的尺寸决定于塑料品种,制品尺寸及壁厚(具体参见有关数据数据)在满足成型要求的前提下应尽量减少截面积,以免增加水□料的比例及使冷却时间增加,降低了生产效率.3.冷料位:设在主流道末端的空穴,用来容纳喷嘴两次注射之间所产生的冷料,从而防止分流道或水口堵塞.如果冷料进入型腔则会导致制件内应力加大或机械强度不足,冷料位尺寸一般为Ψ3-10mm,深度6mm左右,为便于脱模(拉出水口),其底部通常都是拉料杆位(脱模杆),拉料杆的头部通常都设计成下凹陷或带有沟槽形成,便于拉出主流道连整个流道系统.4.浇口(入水口)是熔料通过直/分流道后进入型腔的通道,浇口的截面积通常是整个流道系统中截面积最小的部分.内浇口的尺寸形状对制件的质量影响很大,其主要的作用可列述以下几点:1)控制料流速度;2)成型中水口位早凝结可防其倒流;3)使料通过时产生较高的剪切力使料温提升,从而降低其表面粘度,提高其流动性;4)便于制件与流道分离;浇口的形状尺寸和位置设计都须根据塑料品种,制件结构和形状等具体情况做出选择,一般来说,浇口的位置都是开在制件厚壁位(以利补缩)及不影响外观的位置.浇口尺寸设计应考虑熔体的性质.5.型腔是制件在模具中成型的部分,用来构成型腔的零件称为成型零件,一般包含以下:1)凹模 ----- 构成制件外形的成型零件;2)凸模/型芯 ----- 构成制件内部形状,如:沟、孔、槽等;由于熔体进入型腔后产生很高的压力,故对成型零件的材料强度、刚度要求较高,且材料应具耐腐蚀性.成型零件一般都经过热处理提高硬度.注:常用于塑料模的钢材有:718、S-136;而合金模具是用热作钢8407.6.排气位1)开设在模具内的槽形排气位,防止熔料进入型腔时卷入气体.当熔料进入型腔时,原存入型腔的空气及熔料带入的气体必须在料流的尽头通过排气槽向外排出,如排出不完全,则可能会造成件带气孔、熔接痕、充模料不齐,甚至困入高温压缩空气而烧伤胶件的情况出现.2)一般情况下,排气孔既可开设在型腔内熔料流动的尽端,也可开设在模具的分模面上.(在凹模上开一般0.03-0.06mm深,L5-6.Omm宽的槽)3)注射件排气孔是不会有很多熔料渗(迫)出的,因为熔料会在该处冷却固化而自动将通道堵死。
常用塑料注塑工艺参数知识详解

七、RPVC注塑工艺特性与工艺参数的设定
1、RPVC是典型的热敏性塑料。经过稳定化的RPVC即使在不太高的温度 下如180℃,如果时间很长(如40min以上)仍会导致RPVC严重分解。 所以要严格控制成型温度和物料在料筒中的停留时间。RPVC的成型温度 范围在160~200℃之间。通常为160~190℃,最高不超过200℃;料筒 温度分布通常采用阶梯式设置;喷嘴温度应比料筒末端温度低10~20℃。 2、对要求不高的制品,成型前原料可不干燥; 但原料中水分含量较高时也要进行干燥。干 燥方法通常是在热风循环烘箱中,在 90~100℃的温度下干燥1~2.5h。 3、RPVC的流动性通常较差, 注塑时通常采用较 高的注射压力和较低的注射速率。注射压力在 90MPa以上,保压压力大多在60~80MPa;注射 速率太高还会产生较多的摩擦热而使塑料烧焦、 产生变色等问题。因此,成型RPVC时,可采用 中等或较低的注射速率。 4、模具温度一般在40℃以下,最高不超过60℃; 5、螺杆转速一般为20~50r/min;螺杆转速过快会导致温升过大,导致物 料分解。
1、PS为无定型塑料,熔融温度范围较宽,热稳定性较好; 2、热变形温度为70~100℃,粘流温度为150~204℃, 300℃以上出现分解; 3、PS熔体的粘度对温度的敏感性和对剪切速率的敏感性都适 中,流动性好,易成型; 4、PS树脂的吸水率很低,一般为0.01~0.03%,成型前可 不干燥 ,[必要时,可在70~80℃的循环热风中干燥2~ 3h]。 5、注塑时的料筒温度控制在180~215℃范围内,喷嘴温度比 料筒最高温度低10~20℃。 6、注射压力一般控制在60~150MPa。大浇口、形状简单及厚 壁制品,注射压力可选低些,约60~80MPa。 7、易形成内应力并引起开裂,残余应力问题较为突出。为减 小内应力,加工时往往需要较高的料温、模温,以使熔体 缓慢冷却,取向的分子得到松弛。也可选择流动性高的品 级,或添加流动性助剂;
注塑成型工艺过程和特性之结晶性塑料
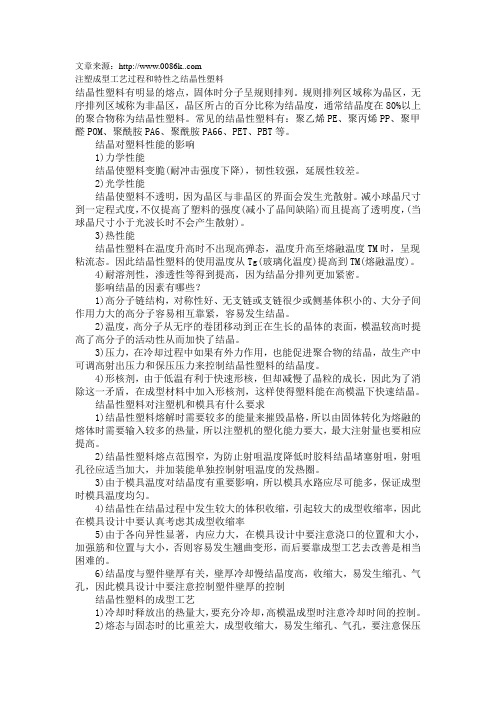
文章来源:注塑成型工艺过程和特性之结晶性塑料结晶性塑料有明显的熔点,固体时分子呈规则排列。
规则排列区域称为晶区,无序排列区域称为非晶区,晶区所占的百分比称为结晶度,通常结晶度在80%以上的聚合物称为结晶性塑料。
常见的结晶性塑料有:聚乙烯PE、聚丙烯PP、聚甲醛POM、聚酰胺PA6、聚酰胺PA66、PET、PBT等。
结晶对塑料性能的影响1)力学性能结晶使塑料变脆(耐冲击强度下降),韧性较强,延展性较差。
2)光学性能结晶使塑料不透明,因为晶区与非晶区的界面会发生光散射。
减小球晶尺寸到一定程式度,不仅提高了塑料的强度(减小了晶间缺陷)而且提高了透明度,(当球晶尺寸小于光波长时不会产生散射)。
3)热性能结晶性塑料在温度升高时不出现高弹态,温度升高至熔融温度TM时,呈现粘流态。
因此结晶性塑料的使用温度从Tg(玻璃化温度)提高到TM(熔融温度)。
4)耐溶剂性,渗透性等得到提高,因为结晶分排列更加紧密。
影响结晶的因素有哪些?1)高分子链结构,对称性好、无支链或支链很少或侧基体积小的、大分子间作用力大的高分子容易相互靠紧,容易发生结晶。
2)温度,高分子从无序的卷团移动到正在生长的晶体的表面,模温较高时提高了高分子的活动性从而加快了结晶。
3)压力,在冷却过程中如果有外力作用,也能促进聚合物的结晶,故生产中可调高射出压力和保压压力来控制结晶性塑料的结晶度。
4)形核剂,由于低温有利于快速形核,但却减慢了晶粒的成长,因此为了消除这一矛盾,在成型材料中加入形核剂,这样使得塑料能在高模温下快速结晶。
结晶性塑料对注塑机和模具有什么要求1)结晶性塑料熔解时需要较多的能量来摧毁晶格,所以由固体转化为熔融的熔体时需要输入较多的热量,所以注塑机的塑化能力要大,最大注射量也要相应提高。
2)结晶性塑料熔点范围窄,为防止射咀温度降低时胶料结晶堵塞射咀,射咀孔径应适当加大,并加装能单独控制射咀温度的发热圈。
3)由于模具温度对结晶度有重要影响,所以模具水路应尽可能多,保证成型时模具温度均匀。
PC塑料的主要性质及成型工艺要求

PC塑料的主要性质及成型工艺要求PC(聚碳酸酯)俗称“防弹玻璃胶”,属结晶性塑料,下面对其主要性质及成型工艺简述如下:一.聚碳酸酯(PC)的主要性质1.外观透明,刚硬带韧性.燃烧慢,离火后慢熄.2.PC料耐冲击性是塑料中最好的.3.成型收缩率小(0.5-0.7%),成品精度高,尺寸稳定性高.4.化学稳定性较好,但不耐碱,酮,芳香烧等有机溶剂.5.耐疲劳强度差,对缺口敏感,耐应力开裂性显著.二.聚碳酸酯(PC)的主要成型工艺要求:1.PC在高温下即使对微量水份亦很敏感,故成型前应充分干燥,使含水率降到OOI5-0.02%以下.干燥条件:温度110T20°C,时间8-12小时.2.流动性差,须用高压注塑,但注塑压力过高会使产品残留内应力而易开裂.3.PC料粘度对温度很敏感,提高温度时,粘度有明显下降.啤塑温度参数:前料管240-260o C,中260-280o C,后220-230°C.料管温度勿超过310℃,PC料成型提高后料管温度对塑化有利,而一般塑料加工,料管温度控制都是前高后低的原则.4.模具的设计要求较高:模具的设计尽可能使流道粗而短,弯曲部位少,用圆形截面分流道;仔细研磨抛光流道等,总之是减小流动阻力以适合其高粘度塑料的填充.另外熔料硬易损伤模具,型腔和型芯应经热处理淬火或经镀硬铭.5.注射速度太快,易出现熔体破裂现象,在浇口周围会有糊斑,产品表面毛糙等缺陷或因排气不良(困气)而使产品烧焦.6.模温以控制在80-100℃为宜,控制模温目的是减小模温及料温的差异,降低内应力.7.成型后为减小内应力,可采用退火处理,退火温度:125T35°C,退火时间2小时,自然冷却到室温.以上有关PC塑料的主要性质及成型工艺要求需在实践中掌握和熟练运用。
PBT塑料性能及注塑工艺

PBT塑料性能及注塑工艺聚对苯二甲酸丁二醇酯(PBT)是通用的工程塑料。
PBT的聚合工艺成熟、成本较低,成型加工容易。
未改性PBT 性能不佳,实际应用要对PBT进行改性,其中,玻璃纤维增强改性牌号占PBT的70%以上。
1 PBT的工艺特性PBT 具有明显的熔点,熔点为225~235℃,是结晶型材料,结晶度可达40%。
PBT熔体的粘度受温度的影响不如剪切应力那么大,因此,在注塑中,注射压力对PBT熔体流动性影响是明显。
PBT在熔融状态下流动性好,粘度低,仅次于尼龙,在成型易发生“流延”现象。
PBT成型制品各向异性。
PBT在高温下遇水易降解。
2注塑机选用螺杆式注塑机时。
应考虑如下几点。
①制品的用料量应控制在注塑机额定最大注射量的30%~80%。
不宜用大注塑机生产小制品。
②应选用渐变型三段螺杆,长径比为15~20,压缩比为2.5~3.0。
③应选用自锁式喷嘴,并带有加热控温装置。
④在成型阻燃级PBT时,注塑机的有关部件应经防腐处理。
3制品与模具设计①制品的厚度不宜太厚,PBT对缺口很敏感,因此,制品的直角等过渡处应采用圆弧连接。
②PBT的成型收缩率较大,在1.7%~2.3%,模具要有一定的脱模斜度。
③模具需要设排气孔或排气槽。
④浇口的口径要大。
⑤模具需设置控温装置。
模具最高温度不能超过100℃。
⑥阻燃级PBT成型,模具表面要镀铬,以防腐。
4原料准备注塑前要进行干燥、要将水分含量控制在0.02%以下。
采用热风循环干燥时,当温度为105℃、120℃或140℃时,所对应的时间不超过8h、5h、3h。
料层厚度低于30mm。
5注塑工艺参数①注射温度PBT的分解温度为280℃,所以实际生产中一般控制在245~260℃之间。
②注射压力注射压力一般为50~100MPa。
③注射速率PBT冷却速度快,因此要采用较快的注射速率。
④螺杆转速和背压成型PBT的螺杆转速不宜超过80r/min,一般在25~60r/min之间。
背压一般为注射压力的10%~15%。
热塑性塑料(注塑成型)的工艺性能、 热固性塑塑料工艺性能-课件
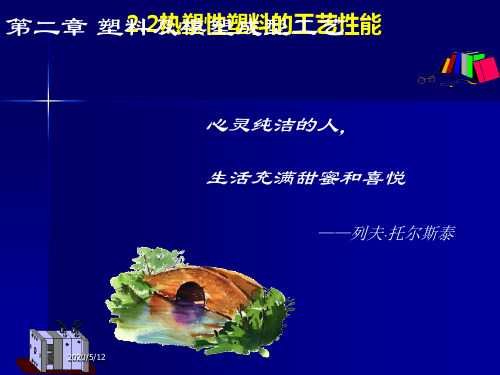
拉伸取向—由拉应力引起,取向方向与拉伸方向一致; 由拉应力引起,取向方向与拉伸方向一致; 流动取向—在切应力作用下沿着熔体流动方向形成的. 在切应力作用下沿着熔体流动方向形成的.
按流动性质不同,取向结构可分为: 按流动性质不同,取向结构可分为:
单轴取向—结构单元均沿着一个流动方向有序排列(取向); 单轴取向—结构单元均沿着一个流动方向有序排列(取向); 多轴取向—结构单元可沿两个或两个以上流动方向有序排列; 多轴取向—结构单元可沿两个或两个以上流动方向有序排列; 按结晶与非结晶聚合物分为: 按结晶与非结晶聚合物分为: 结晶取向 / 非结晶取向
a—中心层定向 最小 ; 中心层定向 b—内层定向较大; 内层定向较大; 内层定向较大 c—外层定向最大; 外层定向最大; 外层定向最大 d—表层未定向。 表层未定向。 表层未定向
20122012-2-23
定向原因: 定向原因:
2.2热塑性塑料的工艺性能 2.2热塑性塑料的工艺性能
d—未取向区 c—高度取向区 b—中等取向区 a—轻度取向区
2.2热塑性塑料的工艺性能 2.2热塑性塑料的工艺性能
定向:
在成型加工中聚合物在 某方向的压力作用下, 某方向的压力作用下,由于 剪应力造成的速度梯度的诱 导,聚合物分子在很大程度 上会顺着流动的方向整齐地 作平行的排列, 作平行的排列,这就是分子 取向的一种情况。 取向的一种情况。
d—未取向区 c—高度取向区 b—中等取向区 a—轻度取向区
2.2热塑性塑料的工艺性能 2.2热塑性塑料的工艺性能 第二章 塑料及模塑成型工艺
心灵纯洁的人, 生活充满甜蜜和喜悦
——列夫·托尔斯泰
20122012-2-23
2.2热塑性塑料的工艺性能 2.2热塑性塑料的工艺性能 2.2热塑性塑料的工艺性能
2.1 塑料成型工艺(注射、压缩)
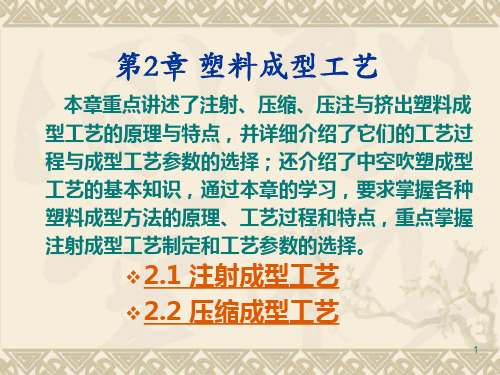
C、分流梭 设置在塑化室的中央,与加热料筒的内壁形成均匀 分布的薄浅流道。料筒的部分热量通过数根翅翼 ( 亦 称肋 ) 使分流梭受热。当塑料进入加热室时,就形成 了一个较薄的塑料层,同时受到加热料筒和分流梭两 方面的受热,从而提高了塑化能力,改善了塑化质量。
分流梭
28
②螺杆式塑化部件 结构:由螺杆、料筒、喷嘴等组成。 功能: 塑料在转动螺杆的连续推进过程中,实现 物理状态的变化,最后呈熔融状态而被注入模腔,完 成均匀塑化、定量注射。
32
C、喷嘴 主要功能: 预塑时,建立背压,排除气体,防止熔料流涎,提 高塑化质量。 注射时,使喷嘴与模具主流道良好接触,保证熔料 在高压下不外溢;建立熔体压力,提高剪切应力,并 将压力能转换为动能,提高注射速率和升温,加强混 炼效果和均化作用。 保压时,便于向模腔补料。 冷却定型时,增加回流阻力,防止模腔中的熔料回 流。 调温、保温和断料功能。
熔体经过喷嘴及模具浇注系统充满型腔为止。
36
保压阶段:塑料熔体充满型腔后,熔体开始冷 却收缩,但柱塞或螺杆继续保持施压状态,料筒内
的熔料会向模具型腔内继续流入进行补缩,以形成
形状完整而致密的塑件。 倒流阶段:是柱塞或螺杆开始后退保压结束时 开始的,这时型腔内的压力比流道内的压力高,因 此会发生塑料熔体的倒流,从而使型腔内的压力迅
15
(3)料筒的清洗
在注塑生产中,经常需要更换原料、调换颜色,或 由于温度的升高会造成原料分解,所有这些情况发生 时,都需要对注塑机的料筒进行清洗。清理方法有如 下几种: ①柱塞式注塑机料筒的清洗,要把组装件拆卸后再 进行清洗。 ②螺杆式注塑机料筒的清洗,通常采用直接换料清 洗。为了便于料筒清洗,一般颜色浅的、熔融温度 低的、热稳定性差的注射制品先加工。
第41节:结晶性塑料注塑工艺要点

第四十一问:结晶性塑料注塑工艺要点一、结晶性塑料的定义:分子链部分形成有序排列、冷却后组成规整结晶结构的塑料称为结晶性塑料。
通常把结晶度在50%以上的聚合物称为结晶性塑料,一般而言,结晶性塑料的结晶度在50%~80%间。
塑料按结晶性来分有结晶性塑料和非结晶性塑料,结晶塑料的分子链是有规则排列,非结晶形塑料分子链是无定型排列。
常见结晶性塑料有:聚乙烯PE、聚丙烯PP、聚甲醛POM、聚酰胺PA(包括PA6、PA66、PA46、PA9T、PA6T、PA1010、PA610、PARA、PA MXD6等)、聚亚胺PAI、聚四氟乙烯PTFE、氯化聚醚CPT、聚苯硫醚PPS、液晶树脂LCP、聚对苯二甲酸乙二醇酯PET、聚对苯二甲酸丁二醇酯PBT、四氟乙烯—全氟烷氧基乙烯基醚共聚物PFA、乙烯-四氟乙烯共聚物ETFE、脂肪族聚酮POK、聚醚醚酮PEEK、聚4-甲基戊烯TPX、间规聚苯乙烯SPS等等。
结晶性塑料在注塑生产方面有比较明显的特性,以下简单介绍:二、结晶性塑料的特性:1.力学性能:结晶性塑料分子排列规则,通常呈许多线状、细长的高分子集合态,分子间的引力相互作用力强,故有韧性强的特性;结晶度越大,材料脆性高,产品的屈服强度、弹性模量、刚硬度随之提高,但同时延展性较差,抗冲击性能降低。
2.光学性能:由于结晶塑料的分子结晶面与非结晶面之间会产生光散射,所以其透明性能不高,常会不透明状态;一般说来,结晶性塑料是不透明的,但有以下几种情况特别:◎尼龙经非结晶共聚改性后,有透明尼龙,此时巳转化为非结晶性塑料;◎PP、PE、PET等材料的吹塑等级是透明或半透明的,因为产品较薄的原因。
◎结晶性塑料聚4-甲基戊烯TPX却为透明材料。
3.热学性能:结晶性塑料有明显的熔点,在温度上升过程不出现高弹态,当温度上升到熔融温度TM时,呈粘流态;塑料的结晶温度是在熔点以下、玻璃化温度以上,不同的塑料种类有不同的最快结晶温度点。
如PP料的最快结晶温度128℃。
结晶与非结晶材料的区别
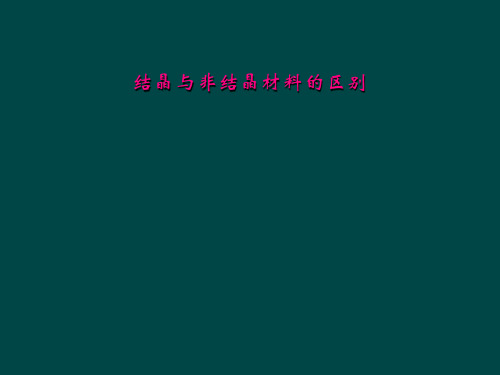
谢谢大家!
4)形核剂,由于低温有利于快速形核,但却 减慢了晶粒的成长,因此为了消除这一矛盾,在 成型材料中加入形核剂,这样使得塑料能在高模 温下快速结晶。
4
四、结晶性塑料对注塑机和模具有什么要求 1)结晶性塑料熔解时需要较多的能量来摧毁晶格 ,所以注塑机的塑化能力要大,最大注射量也要 相应提高。 2)结晶性塑料熔点范围窄,为了防止射咀温度降 低时胶料结晶堵塞射咀,射咀孔径应适当加大, 并且装能单独控制射咀温度的发热圈。 3)由于模具温度对结晶度有重要影响,所以模 具水路应尽量多,保证成型时模具温度均匀。 4)结晶性在结晶过程中发生较大的体积收缩,引 起较大的成型收缩率,因此在模具设计中要认真 考虑其成型收缩率。
3
三、影响结晶的因素的哪些?
1)高分子链结构,对称性好、无支链或支链 很少或侧基体积小的、大分子间作用力大的高分 子容易相互靠紧,容易发生结晶。
2)温度,高分子从无序的卷团移动到正在生 长的晶体的表面,模温较高时提高了高分子的活 动性从而加快了结晶。
3)压力,在冷却过程中如果有外力作用,也 能促进聚合物的结晶。故生产时可调高射出压力ห้องสมุดไป่ตู้和保压来控制结晶性塑料的结晶度。
5
5)由于各向异性显著,内应力大,在模具设计中 要注意浇口的位置和大小,加强筯和位置与大小 ,否则容易发生翘曲变形,而后要靠成型工艺去 改善是相当困难的。 6)结晶度与塑件壁厚有关,壁厚冷却慢结晶度高 ,收缩大,易发生缩孔,气孔,因此模具设计中 要注意控制塑件的壁厚。
6
五:结晶性塑料的成型工艺
1)冷却时释放出的热量大,要充分冷却,高模 温成型时注意冷却时间的控制。
7
为什么分为二类呢? 1)结晶塑料表面是滑性,不能涂刷,不能镀
- 1、下载文档前请自行甄别文档内容的完整性,平台不提供额外的编辑、内容补充、找答案等附加服务。
- 2、"仅部分预览"的文档,不可在线预览部分如存在完整性等问题,可反馈申请退款(可完整预览的文档不适用该条件!)。
- 3、如文档侵犯您的权益,请联系客服反馈,我们会尽快为您处理(人工客服工作时间:9:00-18:30)。
结晶性塑料有明显的熔点,固体时分子呈规则排列。
规则排列区域称为晶区,无序排列区域称为非晶区,晶区所占的百分比称为结晶度,通常结晶度在80%以上的聚合物称为结晶性塑料。
常见的结晶性塑料有:聚乙烯PE、聚丙烯PP、聚甲醛POM、聚酰胺PA6、聚酰胺PA66、PET、PBT等。
结晶对塑料性能的影响
1)力学性能
结晶使塑料变脆(耐冲击强度下降),韧性较强,延展性较差。
2)光学性能
结晶使塑料不透明,因为晶区与非晶区的界面会发生光散射。
减小球晶尺寸到一定程式度,不仅提高了塑料的强度(减小了晶间缺陷)而且提高了透明度,(当球晶尺寸小于光波长时不会产生散射)。
3)热性能
结晶性塑料在温度升高时不出现高弹态,温度升高至熔融温度TM时,呈现粘流态。
因此结晶性塑料的使用温度从Tg(玻璃化温度)提高到TM(熔融温度)。
4)耐溶剂性,渗透性等得到提高,因为结晶分排列更加紧密。
影响结晶的因素有哪些?
1)高分子链结构,对称性好、无支链或支链很少或侧基体积小的、大分子间作用力大的高分子容易相互靠紧,容易发生结晶。
2)温度,高分子从无序的卷团移动到正在生长的晶体的表面,模温较高时提高了高分子的活动性从而加快了结晶。
3)压力,在冷却过程中如果有外力作用,也能促进聚合物的结晶,故生产中可调高射出压力和保压压力来控制结晶性塑料的结晶度。
4)形核剂,由于低温有利于快速形核,但却减慢了晶粒的成长,因此为了消除这一矛盾,在成型材料中加入形核剂,这样使得塑料能在高模温下快速结晶。
结晶性塑料对注塑机和模具有什么要求
1)结晶性塑料熔解时需要较多的能量来摧毁晶格,所以由固体转化为熔融的熔体时需要输入较多的热量,所以注塑机的塑化能力要大,最大注射量也要相应提高。
2)结晶性塑料熔点范围窄,为防止射咀温度降低时胶料结晶堵塞射咀,射咀孔径应适当加大,并加装能单独控制射咀温度的发热圈。
3)由于模具温度对结晶度有重要影响,所以模具水路应尽可能多,保证成型时模具温度均匀。
4)结晶性在结晶过程中发生较大的体积收缩,引起较大的成型收缩率,因此在模具设计中要认真考虑其成型收缩率
5)由于各向异性显着,内应力大,在模具设计中要注意浇口的位置和大小,加强筋和位置与大小,否则容易发生翘曲变形,而后要靠成型工艺去改善是相当困难的。
6)结晶度与塑件壁厚有关,壁厚冷却慢结晶度高,收缩大,易发生缩孔、气孔,因此模具设计中要注意控制塑件壁厚的控制
结晶性塑料的成型工艺
1)冷却时释放出的热量大,要充分冷却,高模温成型时注意冷却时间的控制。
2)熔态与固态时的比重差大,成型收缩大,易发生缩孔、气孔,要注意保压压力的设定
3)模温低时,冷却快,结晶度低,收缩小,透明度高。
结晶度与塑件壁厚有关,塑件壁厚大时冷却慢结晶度高,收缩大,物性好,所以结晶性塑料应按要求必须控制模温。
4)各向异性显着,内应力大,脱模后未结晶折分子有继续结晶化的倾向,处于能量不平衡状态,易发生变形、翘曲,应适当提高料温和模具温度,中等的注射压力和注射速度。
注射工艺的影响因素
液态金属充型技术
机床加工线切屑集中处理方案
合适的检测方法是液位测量成功的关键
全面解析注塑机伺服系统及未来市场趋势
利用信息技术提高塑料粉碎机产品曝光率
中走丝线切割机床选型时常遇到的七大陷阱注塑行业多元发展微注塑工艺技术分析
新科技带来塑料机械行业发展新空间
数控机床操作中需注意的问题
壳牌液压油通过新技术提升液压系统效率
食品软包装材料检测的发展趋势
螺杆泵运行时注意事项
超声波金属塑料焊接术未来iPhone更轻更坚
塑料,橡塑 编辑:mszcm。