注射模设计步骤
注塑模具设计步骤(经典)

设计者:农文生
步骤2
【1】设计区域(之 后修补零件再分型)
【2】创建曲面补片 【3】编辑分型线段 【4】创建分型面 【5】创建型芯、型 腔 【6】型腔布局
步骤3
设计者:农文生
创建定位圈、 浇口套、流道 等
步骤4
说明:由于本塑造成品存在倒扣 现象故应设计滑块和斜顶机构
【滑块与顶料装置】
1创建滑块 2创建斜顶
设计者:农文生
பைடு நூலகம்
步骤5
【标准件管理】【顶杆】
1创建顶出系统
【冷却】
2创建冷却系统
(水嘴、冷却道、喉塞等)
设计者:农文生
整体效果 及 学习心得
细心+耐心+独 立思考+合作
设计者:农文生
谢
呼~呼、、完成任务、爬上去、嘻嘻!
谢 欣 赏
设计者:农文生
注射模具设计流程介绍
1总体设计思路分享 2基本设计步骤介绍 3整体效果及学习心得
设计者:农文生
总体设计思路分享
首先分析零件结构、分型、创建型芯型 腔,接着调用LKM-SG模架,然后创建定位 圈、浇口套、滑块、斜顶机构、顶出系统、 冷却系统等
设计者:农文生
基本设计步骤1
• 项目初始化、工件 • 在【注射模向导】工具条 中单击【项目初始化】按 钮,打开部件文件设置参 数及选项;调整WCS坐标 系,设计模具坐标 • 在【注射模向导】工具条 中单击【工件】在弹出的 【工件尺寸】对话框中设 置工件的参数及选项
注射模设计步骤及实例

注射模设计步骤及实例注射模是用于制作注射器、针筒等医疗设备的模具。
模具的制作是一个复杂而精细的过程,需要经历多个步骤。
下面将详细介绍注射模的设计步骤及实例。
1.确定需求:在开始设计之前,首先需要与客户充分沟通,了解客户的需求和要求,包括产品的形状、尺寸、材料等。
同时还需要了解注射模的使用环境和功能要求,以确保设计出符合实际需要的模具。
2.绘制初步草图:在了解客户需求的基础上,设计师将根据实际情况绘制初步草图。
这个过程需要考虑到模具的整体结构、零件的尺寸和形状等。
设计师可以使用CAD等软件进行绘图,以便对模具的设计进行更好的规划和控制。
3.模具分析:在绘制初步草图之后,设计师需要进行模具分析。
这个过程包括识别和解决可能出现的问题,比如材料选择、产品的易变形部位等。
同时,还需要对模具进行结构分析,确保模具的稳定性和可靠性。
4.详细设计:在完成模具分析之后,设计师将开始进行详细设计。
这个过程需要考虑到模具的每个零件的制造和组装过程。
设计师需要了解材料的特性,选择合适的工艺和加工方法,并进行每个零件的细节设计。
5.制造模具:在完成详细设计之后,设计师需要将设计图纸交给模具制造厂家进行加工和制造。
制造过程需要使用各种加工设备,比如车床、铣床等,对模具的零件进行加工。
在制造过程中,需要进行严格的质量控制,确保每个零件的精度和质量。
6.装配和调试:在完成模具的制造之后,需要对模具进行装配和调试,以保证模具的正常运行。
这个过程包括将各个零件按照设计要求进行组装,并对模具进行调整和测试。
在调试过程中,需要确保模具的各个部分和功能都正常运作。
7.试模和样品确认:在完成装配和调试之后,需要进行试模和样品确认。
试模是指将模具放入注射机进行注射,获得产品样品,并对产品进行检验。
样品确认是指客户对样品进行验收,并根据需要提出修改要求。
8.修改和改进:根据客户的反馈和需求,设计师需要对模具进行修改和改进。
这个过程包括根据样品确认的结果,对模具的设计进行修改,以提高模具的性能和使用效果。
注射塑制件模具设计

注射塑制件模具设计摘要东南沿海江浙中小民营企业制造实际注射塑制件产品,叙述其注射塑制件模具设计流程。
生产流程中应用ug nx8.0具体完成全部流程设计工作,设计工程附加应用pro/e-plastic advisor 模流分析对塑料制件。
关键词注射塑制件模具设计;ug nx8.0;塑制件;cad/cae/cam 中图分类号tq320.5 文献标识码a 文章编号1674-6708(2012)65-0165-02模具制造对塑件进行模具设计之前的初步构思,主要,是模仁的部分设计满足塑件要求的设计。
主要是成型的浇口、分型面,侧抽芯的设计。
dfm顺序:1)浇口设计:应用pro/e-plastic advisor对塑件进行浇口位置及填充性分析,找出进胶位置。
浇口设置于塑件外表面,需减少浇注痕迹,又需考虑模具自行拉断流道废料,采用点进胶;2)分型面的选择:塑件开模方向垂直向上,脱模斜度设置为1°,分型面选择在塑件底面,利于脱模且不影响塑件外观质量,还可利用间隙与型芯、顶针、入子等间隙排气。
为方便加工提高精度,在塑件侧面钩槽使用入子成型,可使分型面为一平面;3)抽芯机构设计:采用斜导柱滑块侧向分型抽芯机构,槽位用滑块成型便于开模;4)模仁部分的设计:(1)分型前准备设计过程第一步加载产品和对设计项目初始化。
初始化过程中,自动产生模具装配结构,装配结构由构成模具的标准元素组成。
将塑件加载进去,设置工作坐标系,选择材料及相应的收缩率;(2)型腔布局根据经验值数据计算模仁的尺寸数据。
从塑件的工艺分析得出塑件形状复杂、尺寸小、精度高。
为提高生产效率、降低成本、模具简单、降低加工难度,所以应用双腔同模设计方案;(3)补孔分模过程就是做出一个面,然后用此面将模仁分割为型芯和型腔两部分,但这样的面要让ug这个软件识别出来,首先要把面上开放的孔和槽覆盖起来,那些需要覆盖的孔和槽就是需要修补的地方,因此修补零件是分模以前需要完成的工作。
典型注塑模设计-项目1-模块三

1.排气系统
大多数情况下可利用模具分型面或模具零件间的配合间隙自然地排气 ,其间隙值通常为0.01~0.03mm,以不产生溢料为限。
排气与引气系统的设计
相关理论知识
2.引气系统的设计 大型深壳形制品包紧型芯形成真空,难以脱模,需要引气装置。 镶拼式侧隙引气 气阀式引气 相关理论知识
能合理地设计浇注系统
能合理地进行成型零件设计
能正确地绘制模具装配图和零件工作图
1.能设计合理的冷却系统 2.能设计合理的排气系统 3.能绘制合理的冷却水道布置图
学习目标
工作任务
根据图示的塑件零件图以及已确定的总体结构方案,设计本模具的冷却系统和排气系统,并绘制冷却水道布置图。
冷却系统设计
低粘度-低模温
单击此处添加正文,文字是您思想的提炼,为了演示发布的良好效果,请言简意赅地阐述您的观点。您的内容已经简明扼要,字字珠玑,但信息却千丝万缕、错综复杂,需要用更多的文字来表述;但请您尽可能提炼思想的精髓,否则容易造成观者的阅读压力,适得其反。正如我们都希望改变世界,希望给别人带去光明,但更多时候我们只需要播下一颗种子,自然有微风吹拂,雨露滋养。恰如其分地表达观点,往往事半功倍。当您的内容到达这个限度时,或许已经不纯粹作用于演示,极大可能运用于阅读领域;无论是传播观点、知识分享还是汇报工作,内容的详尽固然重要,但请一定注意信息框架的清晰,这样才能使内容层次分明,页面简洁易读。如果您的内容确实非常重要又难以精简,也请使用分段处理,对内容进行简单的梳理和提炼,这样会使逻辑框架相对清晰。
根据图示的塑件零件图以及已确定的总体结构方案,设计本模具的冷却系统和排气系统并绘制冷却水道布置图。
练习
高粘度-高模温
注塑模具设计流程
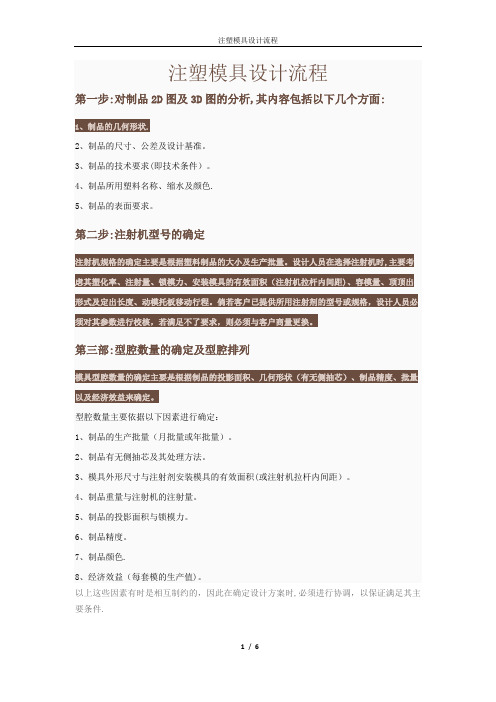
注塑模具设计流程第一步:对制品2D图及3D图的分析,其内容包括以下几个方面:1、制品的几何形状.2、制品的尺寸、公差及设计基准。
3、制品的技术要求(即技术条件)。
4、制品所用塑料名称、缩水及颜色.5、制品的表面要求。
第二步:注射机型号的确定注射机规格的确定主要是根据塑料制品的大小及生产批量。
设计人员在选择注射机时,主要考虑其塑化率、注射量、锁模力、安装模具的有效面积(注射机拉杆内间距)、容模量、顶顶出形式及定出长度、动模托板移动行程。
倘若客户已提供所用注射剂的型号或规格,设计人员必须对其参数进行校核,若满足不了要求,则必须与客户商量更换。
第三部:型腔数量的确定及型腔排列模具型腔数量的确定主要是根据制品的投影面积、几何形状(有无侧抽芯)、制品精度、批量以及经济效益来确定。
型腔数量主要依据以下因素进行确定:1、制品的生产批量(月批量或年批量)。
2、制品有无侧抽芯及其处理方法。
3、模具外形尺寸与注射剂安装模具的有效面积(或注射机拉杆内间距)。
4、制品重量与注射机的注射量。
5、制品的投影面积与锁模力。
6、制品精度。
7、制品颜色.8、经济效益(每套模的生产值)。
以上这些因素有时是相互制约的,因此在确定设计方案时,必须进行协调,以保证满足其主要条件.型腔数量确定之后,便进行型腔的排列,以及型腔位置的布局。
型腔的排列涉及模具尺寸、浇注系统的设计、浇注系统的平衡、抽芯(滑块)机构的设计、镶件型芯的设计以及热流道系统的设计。
以上这些问题由于分型面及浇口位置的选择有关,所以在具体设计过程中,要进行必要的调整,以达到最完美的设计。
第四步:分型面的确定分型面,在一些国外的制品图中已作具体规定,但在很多的模具设计中要由模具人员来确定,一般来讲,在平面上的分型面比较容易处理,有时碰到立体形式的分型面就应当特别注意.其分型面的选择应遵照以下原则:1、不影响制品的外观,尤其是对外观有明确要求的制品,更应注意分型面对外观的影响.2、利于保证制品的精度。
塑料注射模具课程设计

塑料注射模具课程设计一、课程目标知识目标:1. 学生能理解并掌握塑料注射模具的基本结构及其工作原理;2. 学生能了解并描述塑料注射模具的设计流程和关键参数;3. 学生能掌握相关模具材料的选择和应用。
技能目标:1. 学生能运用CAD软件进行塑料注射模具的设计;2. 学生能运用CAE软件对塑料注射模具进行模拟分析;3. 学生能运用CAM软件进行模具的制造编程。
情感态度价值观目标:1. 学生培养对工程技术专业的热爱和兴趣;2. 学生树立正确的工程观念,注重产品质量,遵循工匠精神;3. 学生培养团队协作意识,提高沟通与表达能力。
分析课程性质、学生特点和教学要求,本课程旨在让学生掌握塑料注射模具设计的基本知识和技能,培养他们解决实际工程问题的能力。
课程目标具体明确,分解为以下具体学习成果:1. 学生完成模具结构设计,并能清晰地展示设计思路和步骤;2. 学生完成模具模拟分析,对分析结果进行合理解释;3. 学生完成模具制造编程,并能对制造过程进行优化;4. 学生在课程实践中,展现出良好的团队协作和沟通能力,以及对工程技术专业的热情。
二、教学内容1. 塑料注射模具基础知识- 模具分类及工作原理- 塑料材料性能与选择- 模具结构及其组成2. 塑料注射模具设计流程- 设计前期准备- 模具结构设计- 模具关键参数确定- 设计验证与优化3. 塑料注射模具CAD/CAE/CAM软件应用- CAD软件进行模具设计- CAE软件进行模拟分析- CAM软件进行制造编程4. 塑料注射模具实践操作- 模具设计与分析案例- 模具制造与调试- 故障分析与解决方案教学内容按照以下进度安排:第一周:塑料注射模具基础知识学习;第二周:塑料注射模具设计流程学习;第三周:CAD/CAE/CAM软件操作学习;第四周:实践操作与案例分析。
教学内容与教材关联紧密,涵盖以下章节:1. 教材第1章:塑料注射成型概述2. 教材第2章:塑料注射模具设计基础3. 教材第3章:塑料注射模具CAD/CAE/CAM技术4. 教材第4章:塑料注射模具实践操作与案例分析教学内容科学系统,确保学生能够循序渐进地掌握塑料注射模具相关知识,为后续课程打下坚实基础。
注射模具成型零件的设计.pptx
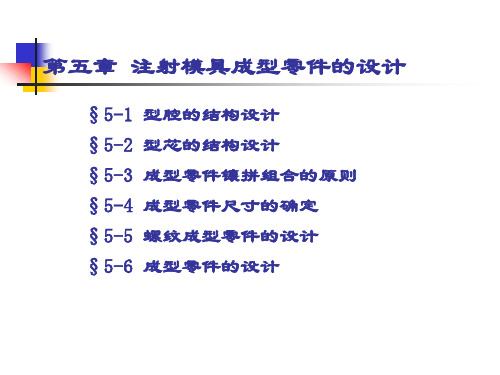
第四节 成型零件尺寸的确定
一、影响塑件尺寸的因素 成型收缩率的选择和成型收缩的波动引起的尺寸误差 成型零件的制造误差、组装误差及相对移动引起的误差; 成型零件脱模斜度引起的误差 成型零件磨损及化学腐蚀引起的误差 二、确定成型零件尺寸的原则
1.综合考虑以下因素,确定合适的塑料收缩率 塑件壁厚、形状及嵌件:壁厚较大、形状较复杂或有时嵌件取偏小值 熔料流向:与进料方向平行的尺寸取偏小值 浇口截面积:浇口截面积小的比大的收缩率大,应取偏大值 与浇口的距离:近的部位比远的部位收缩率小,应选较小值 型腔尺寸取小于平均收缩率的值,型芯尺寸取大于平均收缩率的值 2.据成型零件的性质决定各部分成型尺寸:图5-17 3.脱模斜度的取向:型腔尺寸以大端为准,脱模斜度向缩小方向取得;型
第二节 型芯的结构设计
型芯又叫凸模,是构成塑件内部几何形状的零件。包括主体型芯、小型芯、侧 抽芯和成型杆及螺纹型芯等
一、型芯的结构形式 完全整体式图5-11 主体型芯与动模板做成一体。结构简单,强度、刚度较
好;费工费材,不易修复和更换,只用于形状简单的单型腔或强度、刚度要 求很高的注射模 整体嵌入式图5-12 将主体型芯镶嵌在模板上并固定 局部组合式图5-13、图5-14 塑件局部有不同形状的孔或沟槽不易加工时, 在主体型芯上局部镶嵌与之对应的形状,以简化加工工艺,便于制造和维修 完全组合式图5-15由多块分解的小型芯镶拼组合而成,用于形状规则又难于 整体加工的塑件 二、小型芯的固定形式 图5-16
Δ
2.型芯尺寸
d——型芯径向最大基本寸 d0—塑件径向最小基本尺寸
h —— 型芯高度最大尺寸 h0—塑件内形深度最小尺寸
3.中心距尺寸
保证同心度和尺寸精度,且便于热处理 局部组合式图5-3 型腔由整块材料制成,局部镶有成型嵌件。用于型腔较深、
《注射模设计》
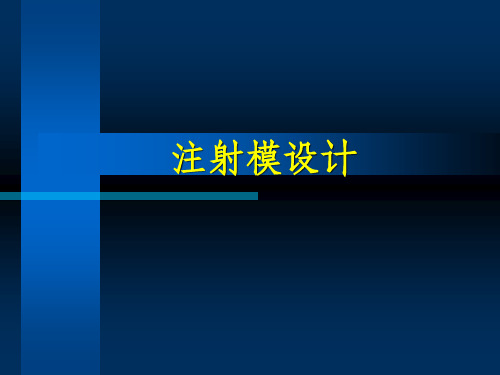
.
39
(二)型腔的布置
1.平衡式浇注系统
分流道到浇口及型腔,其形状、长宽尺寸、圆角、模 壁的冷却条件都完全相同,熔体能以相同的成型压 力和温度同时充满所用型腔。
缺点:流道 总长度要长 些,热量压 力损失大, 模板尺寸大。
.
40
(二)型腔的布置
2.非平衡式浇注系统 由于主流道到各型腔的分流道长度各不相同或 者各型腔形状尺寸不同而使得浇注系统不平衡。
.
16
一、分型面设计 (一)分型面的形式
分型面:是模具上开模时用于取出塑件和(或)浇 注系统冷凝料的可分离的接触表面。
分型面的分类:
1.按其位置与注射机开模运动方向的关系来分类:
垂直于注射机开模运动方向,平行于开模方向,倾 斜于开模方向
2.按分型面的形状来分类 :平面分型面,曲面分型面, 阶梯分型面和斜面分型面
定范围,也不意味浇口浇口越小越好。
.
46
(一)浇注系统流变学
(2)合理的选择剪切速率
在较低的剪切速率范围内,由于剪切速率的微 小变化会引起粘度的巨大变化。这将使注射成型难 以控制,使塑件出现表面不良、充模不匀、密度不 均、内应力高、翘曲以及收缩不均等毛病。所以,
要在ηa ~γ́ 曲线上选取这么一段剪切速率,使它
.
20
(二)选择分型面的原则
使塑件开模时留在动模侧:
.
21
(二)选择分型面的原则
简化模具制造:
.
22
(二)选择分型面的原则
有利于抽芯(活动型芯置于动模):
.
23
(二)选择分型面的原则
有利于抽芯(缩短抽芯距离):
.
24
(二)选择分型面的原则
一模四腔透盖注射模具课程设计说明书
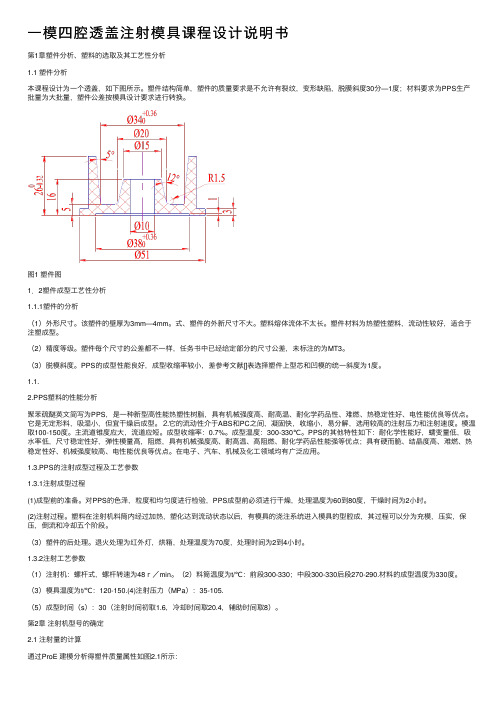
⼀模四腔透盖注射模具课程设计说明书第1章塑件分析、塑料的选取及其⼯艺性分析1.1 塑件分析本课程设计为⼀个透盖,如下图所⽰。
塑件结构简单,塑件的质量要求是不允许有裂纹,变形缺陷,脱膜斜度30分—1度;材料要求为PPS⽣产批量为⼤批量,塑件公差按模具设计要求进⾏转换。
图1 塑件图1.2塑件成型⼯艺性分析1.1.1塑件的分析(1)外形尺⼨。
该塑件的壁厚为3mm—4mm。
式、塑件的外新尺⼨不⼤。
塑料熔体流体不太长。
塑件材料为热塑性塑料,流动性较好,适合于注塑成型。
(2)精度等级。
塑件每个尺⼨的公差都不⼀样,任务书中已经给定部分的尺⼨公差,未标注的为MT3。
(3)脱模斜度。
PPS的成型性能良好,成型收缩率较⼩,差参考⽂献[]表选择塑件上型芯和凹模的统⼀斜度为1度。
1.1.2.PPS塑料的性能分析聚苯硫醚英⽂简写为PPS,是⼀种新型⾼性能热塑性树脂,具有机械强度⾼、耐⾼温、耐化学药品性、难燃、热稳定性好、电性能优良等优点。
它是⽆定形料,吸湿⼩,但宜⼲燥后成型。
⒉它的流动性介于ABS和PC之间,凝固快,收缩⼩,易分解,选⽤较⾼的注射压⼒和注射速度。
模温取100-150度。
主流道锥度应⼤,流道应短。
成型收缩率:0.7%。
成型温度:300-330℃。
PPS的其他特性如下:耐化学性能好,蠕变量低,吸⽔率低,尺⼨稳定性好,弹性模量⾼,阻燃,具有机械强度⾼、耐⾼温、⾼阻燃、耐化学药品性能强等优点;具有硬⽽脆、结晶度⾼、难燃、热稳定性好、机械强度较⾼、电性能优良等优点。
在电⼦、汽车、机械及化⼯领域均有⼴泛应⽤。
1.3.PPS的注射成型过程及⼯艺参数1.3.1注射成型过程(1)成型前的准备。
对PPS的⾊泽,粒度和均匀度进⾏检验,PPS成型前必须进⾏⼲燥,处理温度为60到80度,⼲燥时间为2⼩时。
(2)注射过程。
塑料在注射机料筒内经过加热,塑化达到流动状态以后,有模具的浇注系统进⼊模具的型腔成,其过程可以分为充模,压实,保压,倒流和冷却五个阶段。
- 1、下载文档前请自行甄别文档内容的完整性,平台不提供额外的编辑、内容补充、找答案等附加服务。
- 2、"仅部分预览"的文档,不可在线预览部分如存在完整性等问题,可反馈申请退款(可完整预览的文档不适用该条件!)。
- 3、如文档侵犯您的权益,请联系客服反馈,我们会尽快为您处理(人工客服工作时间:9:00-18:30)。
注射模设计步骤:
1、工艺性分析
从塑件尺寸、精度等级、塑件要求、方便加工和热处理等方面对塑件型腔数目、浇口型式、型芯与型腔结构形式作出分析。
2、确定型腔数目
根据塑件的生产批量及尺寸精度要求确定型腔数目。
按照任务书塑件图(图附在计算说明书上),计算塑件体积(小沟、槽等部位简化),单位为3
cm。
塑件体积:≈
V
s
根据查表4-1得知的塑料ABS密度,计算单件塑件重量,单位为g。
m
单件塑件重量:=
s
3、型腔、型芯工作部位尺寸的确定
ABS塑料的收缩率是%
3.0,计算平均收缩率k。
%
8.0
~
平均收缩率:=
k
分别计算型腔径向尺寸L、型腔深度尺寸H、型芯径向尺寸l、型芯高度尺寸h(按照教材P74~75计算公式计算)。
型腔径向尺寸:L=
型腔深度尺寸:H=
型芯径向尺寸:l=
型芯高度尺寸:h=
加收缩率后各工作部位尺寸计算结果附图表示。
通常,塑件中1mm和小于1mm并带有大于0.05mm公差的部位以及2mm和小于2mm并带有大于0.1mm公差的部位不需要进行收缩率计算。
4、浇注系统设计
(1)确定分型面位置
根据塑件结构,确定分型面形式。
必须加粗标出分型面位置。
(2)确定浇口型式及位置
浇口直径可以根据经验公式计算:
42)20.0~14.0(A d δ=
式中 d —浇口直径(mm );
δ—塑件在浇口处的壁厚(mm );
A —型腔表面积(2mm )
分型面及浇口位置附图表示。
(3)确定型腔位置的排布
布置形式附图表示。
(4)初步设计主流道及分流道形状和尺寸
由教材P 77~80确定主流道及分流道形状和尺寸,并附图表示。
根据流道设计参数校核流动比
∑=Φi i t L /
式中 Φ —流动距离比;
i L —模具中各段料流通道及各段模腔的长度(mm );
i t —模具中各段料流通道及各段模腔的截面厚度(mm )。
影响流动比的因素主要是塑料的流动性,ABS 塑料与聚甲醛的流动性均为中等,查表4-3参考聚甲醛的允许流动比[Φ]=210~110,判断是否满足Φ<[Φ]。
5、选用模架
(1)计算型腔强度和刚度
由于型腔壁厚计算比较麻烦,型腔壁厚可参考经验推荐数据,查表4-4、4-5获得。
(2)初选注射机
1)计算注射量
粗略计算浇注系统重量:
ρ⨯=j j V m
式中 j V —浇注系统体积,3cm ;
ρ—材料密度,3/cm g 。
总体积: V =塑件体积+浇注系统体积
总重量: ρ⨯=V M
校核是否满足注射量 80.0/V V ≥机
式中 机V —额定注射量(g )。
2)注射压力
成型注p p ≥
查表4-2,ABS 塑料成型时的注射压力成型p =
3)锁模力
pF P ≥锁模力
式中 p —塑料成型时型腔压力,ABS 塑料的型腔压力a MP p 30=; F —浇注系统和塑件在分型面上的投影面积和(2mm )。
根据以上分析、计算,查表4-6,初选注射机型号为:
列出所选注射机有关技术参数:
最大开合模行程: mm
模具最大厚度: mm
模具最小厚度: mm
喷嘴圆弧半径: mm
喷嘴孔直径: mm
动、定模板尺寸: mm mm ⨯
拉杆空间: mm
(3)选标准模架
根据以上分析、计算以及型腔尺寸及位置尺寸,可确定模架的结构形式和规格。
查表4-8选用:
型号:
定模板厚度: mm
动模板厚度: mm
垫块厚度: mm
模具厚度: mm
模具外形尺寸: mm mm mm ⨯⨯
6、校核注射机
(1)注射量、锁模力、注射压力、模具厚度的校核
由于在初选注射机和选用标准模架时是根据以上四个技术参数及计算壁厚等因素选用的,所以注射量、锁模力、注射压力、模具厚度不必进行校核,已符合所选注射机要求。
(2)开模行程的校核
注射机最大开模行程 )(浇件10~52++≥h h S
式中 件h —塑件高度(mm );
浇h —浇注系统高度(mm )。
(3)模具在注射机上的安装
标准模架外形尺寸<注射机拉杆空间。
7、推出机构的设计
(1)推件力的计算
推件力 1)sin cos (qA Ap F t +-=ααμ
式中 A —塑件包络型芯的面积(2mm );
p —塑件对型芯单位面积上的包紧力,取a P 77102.1~108.0⨯⨯; μ—塑件对钢的摩擦系数,约为0.1~0.3;
α—脱模斜度;
q —大气压力a MP 09.0;
1A —塑件垂直于脱模方向的投影面积(2mm )
(2)确定推出方式及推杆位置
按需要确定推杆和拉料杆形状和尺寸,查表4-9定出型号。
安装位置附图表示。
8、冷却系统设计
冷却水路布置附图表示。
9、排气系统设计
说明采用何种方式排气。
一般为间隙排气。
10、按要求绘制模架装配图
附图表示。