Interoperability with IFC in the automated rebar fabrication
吉利发布的第一条标准

吉利发布的第一条标准英文回答:The first standard released by Geely requires a comprehensive understanding and application of two languages, English and Chinese. This standard aims to promote bilingual communication and ensure effective communication within the company. As a Geely employee, I fully embrace this requirement and believe that it will greatly benefit both personal and professional development.Being able to communicate in multiple languages is a valuable skill in today's globalized world. English is widely recognized as the international language of business and is essential for effective collaboration with colleagues and partners from different countries. It allows us to expand our network, exchange ideas, and learn from diverse perspectives. Moreover, English proficiency enables us to access a wealth of information and resourcesavailable in this language, which can greatly enhance ourknowledge and expertise.On the other hand, Chinese is the native language of Geely's headquarters and most of our colleagues. It is crucial to have a good command of Chinese to effectively communicate with our Chinese colleagues, understand their culture, and build strong relationships. Chineseproficiency also allows us to fully grasp and contribute to discussions and meetings held in Chinese, ensuring that we are actively engaged in decision-making processes.To illustrate the importance of bilingual communication, let me share a personal experience. I was once involved ina project that required collaboration between Geely's Chinese and international teams. The meetings were conducted in both English and Chinese, and it was essential for all participants to understand and contributeeffectively in both languages. Those who were proficient in both languages were able to bridge the communication gap, ensuring that ideas were accurately conveyed and understood by all team members. This not only improved the efficiencyof the project but also fostered a sense of unity andcamaraderie among team members.中文回答:吉利发布的第一条标准要求我们全面掌握并应用英文和中文两种语言。
请做好车辆保障措施英语

请做好车辆保障措施英语IntroductionWith the increase of automobiles on the roads, vehicle safety has become a major concern for drivers, passengers, and pedestrians alike. Therefore, it is essential to follow proper vehicle safety measures to ensure the safety of all road users. In this article, we will discuss the importance of vehicle safety and measures that can be taken to ensure road safety in English.Importance of Vehicle SafetyVehicle safety should be a top priority for all drivers. It not only protects the occupants of the vehicle but also those around it. There are many factors that can cause a car accident such as distracted driving, speeding, and poor road conditions. However, practicing proper vehicle safety measures can significantly reduce the risk of accident.Vehicle Safety MeasuresHere are some vehicle safety measures that can be taken to ensure safer road travel:1. Regular MaintenanceRegular maintenance of your vehicle is crucial to ensure its proper working and safety. This includes checking the tires, brakes, engine, lights, and other essential parts of the car. It is recommended that you schedule an annual inspection to ensure that your vehicle is in good condition.2. Following Traffic RulesFollowing traffic rules is the simplest and most effective way to ensure road safety. Obeying traffic rules like crossing at designated crosswalks, wearing seat belts, and not exceeding the speed limit can prevent accidents.3. Avoiding DistractionsDistracted driving is one of the leading causes of car accidents. Avoiding distractions like using cellphones, eating, drinking, grooming, or any other activity that takes your attention away from the road is crucial for vehicle safety.4. Stay Alert and AttentiveBeing alert and attentive while driving is important for avoiding accidents. Always stay focused on the road ahead, keep a safe distance from other vehicles, and be aware of your surroundings.5. Planning AheadPlanning ahead is essential for avoiding accidents. This includes checking the weather and road conditions before traveling, avoiding rush hours, and planning routes in advance.ConclusionPracticing proper vehicle safety measures is vital for ensuring road safety. Regular maintenance, following traffic rules, avoiding distractions, staying alert and attentive, and planning ahead are some of the measures that can be taken to reduce the risk of car accidents. Remember that the safety of every road user is a shared responsibility, and it is up to us to take the necessary precautions to ensure safety on the roads.。
KUKA 协作机器人 LBR iiwa说明书

Issued: 23.05.2016 Version: Spez LBR iiwa V7LBR iiwa© Copyright 2016KUKA Laboratories GmbHZugspitzstraße 140D-86165 AugsburgGermanyThis documentation or excerpts therefrom may not be reproduced or disclosed to third parties withoutthe express permission of the KUKA Laboratories GmbH.Other functions not described in this documentation may be operable in the controller. The user hasno claims to these functions, however, in the case of a replacement or service work.We have checked the content of this documentation for conformity with the hardware and softwaredescribed. Nevertheless, discrepancies cannot be precluded, for which reason we are not able toguarantee total conformity. The information in this documentation is checked on a regular basis, how-ever, and necessary corrections will be incorporated in the subsequent edition.Subject to technical alterations without an effect on the function.Translation of the original documentationKIM-PS5-DOCPublication:Pub Spez LBR iiwa enBook structure:Spez LBR iiwa V4.1Version:Spez LBR iiwa V72 / 81Issued: 23.05.2016 Version: Spez LBR iiwa V7Contents Contents1Introduction (5)1.1Industrial robot documentation (5)1.2Representation of warnings and notes (5)1.3Terms used (5)2Purpose (7)2.1Target group (7)2.2Intended use (7)3Product description (9)3.1Overview of the robot system (9)3.2Description of the LBR iiwa (9)4Technical data (11)4.1Technical data, overview (11)4.2Technical data, LBR iiwa 7 R800 (11)4.2.1Basic data, LBR iiwa 7 R800 (11)4.2.2Axis data, LBR iiwa 7 R800 (12)4.2.3Payloads, LBR iiwa 7 R800 (13)4.2.4Foundation data, LBR iiwa 7 R800 (15)4.3Technical data, LBR iiwa 14 R820 (17)4.3.1Basic data, LBR iiwa 14 R820 (17)4.3.2Axis data, LBR iiwa 14 R820 (17)4.3.3Payloads, LBR iiwa 14 R820 (19)4.3.4Foundation data, LBR iiwa 14 R820 (21)4.4Plates and labels (22)4.5Stopping distances and times (23)4.5.1General information (23)4.5.2Terms used (24)4.5.3Stopping distances and stopping times for LBR iiwa 7 R800 (26)4.5.3.1Stopping distances and stopping times for STOP 0, axis 1 to axis 4 (26)4.5.3.2Stopping distances and stopping times for STOP 1, axis 1 (27)4.5.3.3Stopping distances and stopping times for STOP 1, axis 2 (29)4.5.3.4Stopping distances and stopping times for STOP 1, axis 3 (31)4.5.3.5Stopping distances and stopping times for STOP 1, axis 4 (33)4.5.4Stopping distances and stopping times for LBR iiwa 14 R820 (34)4.5.4.1Stopping distances and stopping times for STOP 0, axis 1 to axis 4 (35)4.5.4.2Stopping distances and stopping times for STOP 1, axis 1 (36)4.5.4.3Stopping distances and stopping times for STOP 1, axis 2 (38)4.5.4.4Stopping distances and stopping times for STOP 1, axis 3 (40)4.5.4.5Stopping distances and stopping times for STOP 1, axis 4 (42)5Safety (45)5.1Legal framework (45)5.1.1Liability (45)5.1.2Intended use of the industrial robot (45)5.1.3EC declaration of conformity and declaration of incorporation (46)5.2Safety functions (46)Issued: 23.05.2016 Version: Spez LBR iiwa V73 / 81LBR iiwa5.2.1Terms used (47)5.2.2Personnel (48)5.2.3Workspace, safety zone and danger zone (49)5.2.4Safety-oriented functions (50)5.2.4.1EMERGENCY STOP device (51)5.2.4.2Enabling device (51)5.2.4.3“Operator safety” signal (52)5.2.4.4External EMERGENCY STOP device (52)5.2.4.5External safety stop 1 (path-maintaining) (52)5.2.4.6External enabling device (53)5.2.4.7External safe operational stop (53)5.2.5Triggers for safety-oriented stop reactions (53)5.2.6Non-safety-oriented functions (54)5.2.6.1Mode selection (54)5.2.6.2Software limit switches (55)5.3Additional protective equipment (56)5.3.1Jog mode (56)5.3.2Labeling on the industrial robot (56)5.3.3External safeguards (56)5.4Safety measures (57)5.4.1General safety measures (57)5.4.2Transportation (58)5.4.3Start-up and recommissioning (58)5.4.4Manual mode (60)5.4.5Automatic mode (61)5.4.6Maintenance and repair (61)5.4.7Decommissioning, storage and disposal (62)5.4.8Safety measures for “single point of control” (62)5.5Applied norms and directives (63)6Planning (65)6.1Mounting variant (65)6.1.1Machine frame mounting with centering (65)6.2Connecting cables and interfaces (66)7Transportation (69)7.1Transportation (69)7.1.1Transportation with transport packaging (69)7.1.2Transportation with transport box (optional) (70)8KUKA Service (71)8.1Requesting support (71)8.2KUKA Customer Support (71)Index (79)4 / 81Issued: 23.05.2016 Version: Spez LBR iiwa V75 / 81Issued: 23.05.2016 Version: Spez LBR iiwa V7 1 Introduction1Introduction1.1Industrial robot documentationThe industrial robot documentation consists of the following parts:⏹Documentation for the manipulator ⏹Documentation for the robot controller⏹Operating and programming instructions for the System Software ⏹Instructions for options and accessories ⏹Parts catalog on storage mediumEach of these sets of instructions is a separate document.1.2Representation of warnings and notesSafetyThese warnings are relevant to safety and must be observed.This warning draws attention to procedures which serve to prevent or remedy emergencies or malfunctions:NoticesThese notices serve to make your work easier or contain references to further information.1.3Terms usedThese warnings mean that it is certain or highly probablethat death or severe injuries will occur, if no precautionsare taken.These warnings mean that death or severe injuries mayoccur, if no precautions are taken.These warnings mean that minor injuriesmay occur, if no precautions are taken.These warnings mean that damage to propertymay oc-cur, if no precautions are taken.These warnings contain references to safety-relevant information or general safety measures.These warnings do not refer to individual hazards or individual pre-cautionary measures.Procedures marked with this warning must be followedexactly.Tip to make your work easier or reference to further information.Term DescriptionLBR iiwaLightweight robot i ntelligent i ndustrial w ork a ssistantLBR iiwaManipulator The robot arm and the associated electricalinstallationsKCP smartPAD The KCP (KUKA Control Panel) teach pendant has all the operator control and display functions required for operating and programming the industrial robot.The KCP variant for the KUKA Sunrise Cabinet is called KUKA smartPAD. The general term “KCP”, however, is generally used in this docu-mentation.Term Description6 / 81Issued: 23.05.2016 Version: Spez LBR iiwa V77 / 81Issued: 23.05.2016 Version: Spez LBR iiwa V7 2 Purpose2Purpose2.1Target groupThis documentation is aimed at users with the following knowledge and skills:⏹Advanced knowledge of mechanical engineering ⏹Advanced knowledge of electrical and electronic systems ⏹Knowledge of the robot controller system2.2Intended useUseThe industrial robot is intended for handling tools and fixtures, or for process-ing or transferring components or products. Use is only permitted under the specified environmental conditions.MisuseAny use or application deviating from the intended use is deemed to be imper-missible misuse; examples of such misuse include:⏹Transportation of persons and animals ⏹Use as a climbing aid⏹Operation outside the permissible operating parameters ⏹Use in potentially explosive environments ⏹Outdoor operation ⏹Leaning on the robot arm ⏹Underground operationFor optimal use of our products, we recommend that our customers take part in a course of training at KUKA College. Information about the training program can be found at or can be ob-tained directly from our subsidiaries.Changing the structure of the manipulator, e.g. by drilling holes, etc., can result in damage to the components. Thisis considered improper use and leads to loss of guarantee and liability enti-tlements.LBR iiwa8 / 81Issued: 23.05.2016 Version: Spez LBR iiwa V79 / 81Issued: 23.05.2016 Version: Spez LBR iiwa V7 3 Product description3Product description3.1Overview of the robot systemA robot system (>>> Fig. 3-1 ) comprises all the assemblies of an industrial robot, including the manipulator (mechanical system and electrical installa-tions), controller, connecting cables, end effector (tool) and other equipment.The industrial robot consists of the following components:⏹Manipulator⏹KUKA Sunrise Cabinet robot controller ⏹KUKA smartPAD control panel ⏹Connecting cables ⏹Software⏹Options, accessories3.2Description of the LBR iiwaOverviewThe LBR iiwa is classified as a lightweight robot and is a jointed-arm robot with 7 axes. All drive units and current-carrying cables are installed inside the ro-bot.Every axis contains multiple sensors that provide signals for robot control (e.g. position control and impedance control) and that are also used as a protective function for the robot. Every axis is monitored by sensors: axis range sensors ensure that the permissible axis range is adhered to, torque sensors ensure that the permissible axis loads are not exceeded, and temperature sensorsFig. 3-1: Overview of robot system 1Connecting cable to the smartPAD 2KUKA smartPAD control panel 3Manipulator4Connecting cable to KUKA Sunrise Cabinet robot controller 5KUKA Sunrise Cabinet robot controllerLBR iiwamonitor the thermal limit values of the electronics. In the case of an unfavor-able combination of permanently high demand on robot power and externaltemperature influences, the LBR is protected by this temperature monitoringwhich switches it off if the thermal limit values are exceeded. Following a cool-ing time, the LBR can be restarted with no need for additional measures. Tech-nical Support is available to answer any questions.The kinematic system of both robot variants is of redundant design due to its7 axes and consists of the following principal components:In-line wrist The robot is fitted with a 2-axis in-line wrist. The motors are located in axes A6 and A7.Joint module The joint modules consist of an aluminum structure. The drive units are situat-ed inside these modules. In this way, the drive units are linked to one anothervia the aluminum structures.Base frame The base frame is the base of the robot. Interface A1 is located at the rear of the base frame. It constitutes the interface for the connecting cables betweenthe robot, the controller and the energy supply system.Electrical installa-tions The electrical installations include all the supply and control cables for the mo-tors of axes A1 (J1) to A7 (J7). All the connections on the motors are plug-and-socket connections. The entire cabling is routed internally in the robot.The connecting cable is connected to the robot controller. The energy supply system cables are connected to the periphery.Fig. 3-2: Main assemblies and robot axes1In-line wrist2Joint module3Base frame10 / 81Issued: 23.05.2016 Version: Spez LBR iiwa V74Technical data4.1Technical data, overviewThe technical data for the individual robot types can be found in the following sections:4.2Technical data, LBR iiwa 7 R8004.2.1Basic data, LBR iiwa 7 R800Basic dataRobotTechnical dataLBR iiwa 7 R800⏹Basic data(>>> 4.2.1 "Basic data, LBR iiwa 7 R800" Page 11)⏹Axis data(>>> 4.2.2 "Axis data, LBR iiwa 7 R800" Page 12)⏹Payloads(>>> 4.2.3 "Payloads, LBR iiwa 7 R800" Page 13)⏹Mounting base data(>>> 4.2.4 "Foundation data, LBR iiwa 7 R800" Page 15)⏹Plates and labels(>>> 4.4 "Plates and labels" Page 22)⏹Stopping distances and times(>>> 4.5.3 "Stopping distances and stopping times for LBR iiwa 7 R800" Page 26)LBR iiwa 14 R820⏹Basic data(>>> 4.3.1 "Basic data, LBR iiwa 14 R820" Page 17)⏹Axis data(>>> 4.3.2 "Axis data, LBR iiwa 14 R820" Page 17)⏹Payloads(>>> 4.3.3 "Payloads, LBR iiwa 14 R820" Page 19)⏹Mounting base data(>>> 4.3.4 "Foundation data, LBR iiwa 14 R820" Page 21)⏹Plates and labels(>>> 4.4 "Plates and labels" Page 22)⏹Stopping distances and times(>>> 4.5.4 "Stopping distances and stopping times for LBR iiwa 14 R820" Page 34)LBR iiwa 7 R800Number of axes7Number of controlled axes 7Volume of working envelope 1.7 m³Pose repeatability (ISO 9283)± 0.1 mm Weight approx. 23.9 kg Rated payload 7 kg Maximum reach 800 mm Protection ratingIP54Protection rating, in-line wristIP54Ambient condi-tions4.2.2Axis data, LBR iiwa 7 R800 Axis dataWorking envelope The diagram (>>> Fig. 4-1 ) shows the shape and size of the working enve-lope for the robot:Sound level< 75 dB (A)Mounting position Floor;Ceiling;WallFootprint-Permissible angle of inclination-Default color Base frame: white aluminum (RAL9006);Moving parts: white aluminum (RAL9006);Cover: KUKA orange 2567 Controller KUKA Sunrise Cabinet Transformation name-LBR iiwa 7 R800Ambient temperature during opera-tion5 °C to 45 °C (278 K to 318 K)Ambient temperature during stor-age/transportation0 °C to 45 °C (273 K to 318 K)Air humidity20 % to 80 %In the case of overheating, the robot switches off automatically and isthus protected against thermal destruction.Range of motionA1±170 °A2±120 °A3±170 °A4±120 °A5±170 °A6±120 °A7±175 °Speed with rated payloadA198 °/sA298 °/sA3100 °/sA4130 °/sA5140 °/sA6180 °/sA7180 °/s4.2.3Payloads, LBR iiwa 7 R800PayloadsFig. 4-1: LBR iiwa 7 R800 working envelope, side viewFig. 4-2: LBR iiwa 7 R800 working envelope, top viewThe height of the LBR iiwa depends on the media flange mounted onit. The dimensions of the media flange can be found in the Media Flange documentation.Rated payload7 kg Rated mass moment of inertia0.3 kgm²Load center of gravity For all payloads, the load center of gravity refers to the distance from the face of the mounting flange on axis A7.Permissible mass inertia at the design point (L x, L y, L z) is 0.3 kgm².Rated total load7 kgRated supplementary load, baseframe0 kgMaximum supplementary load,base frame-Rated supplementary load, rotatingcolumn0 kgMaximum supplementary load,rotating column-Rated supplementary load, link arm0 kgMaximum supplementary load, linkarm-Rated supplementary load, arm0 kgMaximum supplementary load, arm-Nominal distance to load center of gravityLxy35 mmLz60 mmFig. 4-3: Load center of gravityPayload diagramSupplementaryloadThe robot cannot carry a supplementary load.4.2.4Foundation data, LBR iiwa 7 R800Mounting base loads The specified forces and moments already include the payload and the inertia force (weight) of the robot.Fig. 4-4: LBR iiwa 7 R800 payload diagramThe payloads depend on the type of media flange used.Further information about the payloads dependent on the mediaflange can be found in the Media Flangedocumentation.This loading curve corresponds to the maximum load ca-pacity. Both values (payload and mass moment of iner-tia) must be checked in all cases. Exceeding this capacity will reduce the service life of the robot and overload the motors and the gears; in any such case KUKA Customer Support must be consulted beforehand.The values determined here are necessary for planning the robot application. For commissioning the robot, additional input data are required in accor-dance with the operating and programming instructions of the control soft-ware.Fig. 4-5: Loads acting on the foundation, floor mountingFig. 4-6: Loads acting on the foundation, ceiling mounting Vertical force F(v)F(v normal)-F(v max)524 NHorizontal force F(h)F(h normal)-F(h max)240 NTilting moment M(k)M(k normal)-M(k max)310 Nm4.3Technical data, LBR iiwa 14 R8204.3.1Basic data, LBR iiwa 14 R820Basic dataAmbient condi-tions4.3.2Axis data, LBR iiwa 14 R820Axis dataTorque about axis 1 M(r)M(r normal)-M(r max)156 NmThe foundation loads specified in the table are the maxi-mum loads that may occur. They must be referred towhen dimensioning the foundations and must be adhered to for safety rea-sons. Failure to do so may result in material damage.LBR iiwa 14 R820Number of axes7Number of controlled axes 7Volume of working envelope 1.8 m³Pose repeatability (ISO 9283)± 0.15 mm Weight approx. 29.9 kg Rated payload 14 kg Maximum reach 820 mm Protection ratingIP54Protection rating, in-line wrist IP54Sound level< 75 dB (A)Mounting positionFloor;Ceiling;Wall Footprint-Permissible angle of inclination -Default colorBase frame: white aluminum (RAL 9006);Moving parts: white aluminum (RAL 9006);Cover: KUKA orange 2567ControllerKUKA Sunrise Cabinet Transformation name-Ambient temperature during opera-tion5 °C to 45 °C (278 K to 318 K)Ambient temperature during stor-age/transportation 0 °C to 45 °C (273 K to 318 K)Air humidity20 % to 80 %In the case of overheating, the robot switches off automatically and is thus protected against thermal destruction.Range of motion A1±170 °Working envelope The diagram (>>> Fig. 4-7 ) shows the shape and size of the working enve-lope for the robot:A2±120 °A3±170 °A4±120 °A5±170 °A6±120 °A7±175 °Speed with rated payloadA185 °/sA285 °/sA3100 °/sA475 °/sA5130 °/sA6135 °/sA7135 °/sFig. 4-7: LBR iiwa 14 R820 working envelope, side view4.3.3Payloads, LBR iiwa 14 R820 PayloadsLoad center of gravity For all payloads, the load center of gravity refers to the distance from the face of the mounting flange on axis A7.Fig. 4-8: LBR iiwa 14 R820 working envelope, top viewThe height of the LBR iiwa depends on the media flange mounted onit. The dimensions of the media flange can be found in the MediaFlange documentation.Rated payload14 kgRated mass moment of inertia0.3 kgm²Rated total load14 kgRated supplementary load, baseframe0 kgMaximum supplementary load,base frame-Rated supplementary load, rotatingcolumn0 kgMaximum supplementary load,rotating column-Rated supplementary load, link arm0 kgMaximum supplementary load, linkarm-Rated supplementary load, arm0 kgMaximum supplementary load, arm-Nominal distance to load center of gravityLxy40 mmLz44 mmPermissible mass inertia at the design point (L x , L y , L z ) is 0.3 kgm².Payload diagramFig. 4-9: Load center of gravityFig. 4-10: LBR iiwa 14 R820 payload diagramThe payloads depend on the type of media flange used.Further information about the payloads dependent on the media flange can be found in the Media Flange documentation.SupplementaryloadThe robot cannot carry a supplementary load.4.3.4Foundation data, LBR iiwa 14 R820Mounting base loads The specified forces and moments already include the payload and the inertia force (weight) of the robot.This loading curve corresponds to the maximum load ca-pacity. Both values (payload and mass moment of iner-tia) must be checked in all cases. Exceeding this capacity will reduce the service life of the robot and overload the motors and the gears; in any such case KUKA Customer Support must be consulted beforehand.The values determined here are necessary for planning the robot application. For commissioning the robot, additional input data are required in accor-dance with the operating and programming instructions of the control soft-ware.Fig. 4-11: Loads acting on the foundation, floor mounting4.4Plates and labelsIdentification plate The following plates and labels are attached to the robot. They must not be re-moved or rendered illegible. Illegible plates and labels must be replaced. Fig. 4-12: Loads acting on the foundation, ceiling mountingVertical force F(v)F(v normal)-F(v max)541.2 NHorizontal force F(h)F(h normal)-F(h max)228.4 NTilting moment M(k)M(k normal)-M(k max)281.6 NmTorque about axis 1 M(r)M(r normal)-M(r max)172.6 NmThe foundation loads specified in the table are the maxi-mum loads that may occur. They must be referred to when dimensioning the foundations and must be adhered to for safety rea-sons. Failure to do so may result in material damage.4.5Stopping distances and times4.5.1General informationInformation concerning the position control data:The stopping distance is the axis angle traveled by the robot from the mo-ment the stop signal is triggered until the robot comes to a complete stand-still.Fig. 4-13: Plates and labels⏹The stopping time is the time that elapses from the moment the stop signal is triggered until the robot comes to a complete standstill.⏹The data are given for axes A1, A2, A3 and A4. These axes are the axes with the greatest deflection.⏹The data apply to single-axis motions. Superposed axis motions can result in longer stopping distances.⏹As reference, PTP motions with position control have been used without further parameterization (e.g. robot.move(ptp(Zielpose)) ).⏹Stopping distances and stopping times in accordance with DIN EN ISO 10218-1, Annex B.⏹Stop categories:⏹Stop category 0 » STOP 0⏹Stop category 1 » STOP 1 (path-maintaining)according to IEC 60204-1⏹The values specified are guide values determined by means of tests and simulation. They are average values which conform to the requirements of DIN EN ISO 10218-1. The actual stopping distances and stopping times may differ due to internal and external influences on the braking torque. It is therefore advisable to determine the exact stopping distances and stop-ping times under the real conditions of the actual robot application.⏹Measuring techniqueThe stopping distances were measured using the robot-internal measur-ing technique with rated payloads.⏹The wear on the brakes varies depending on the operating mode, robot application and the number of STOP 0 stops triggered. It is therefore ad-visable to check the stopping distance at least once a year.The stopping distances and stopping times can be determined, for example, by using safety monitoring to trigger axis-specific or Cartesian workspace monitoring of the safety stop that is to be checked and evaluating the corre-sponding measured data from the trace (by means of DataRecorder).4.5.2Terms usedExtension The following figures illustrate the 0%, 33%, 66% and 100% extensions of axes A1-A4:Extension 0%The robot is in 0% extension when the axes are in the following positions:Term Descriptionm Mass of the rated load and the supplementary load on the arm.PhiAngle of rotation (°) about the corresponding axis. This value can be entered in the controller via the KCP and is displayed on the KCP .POVProgram override (%) = velocity of the robot motion. This value can be entered in the controller via the KCP and is displayed on the KCP .Extension Distance (l in %) between axis 1 and the intersection of axes 6 and 7.KCPThe KCP teach pendant has all the operator control and display functions required for operating and pro-gramming the robot system.Extension 33%Axis A1 (J1)A2 (J2)A3 (J4)A4 (J5)A5 (J6)A6 (J7)A7 (J8)10°0º0º0º0º0º0°20°0°90°0°0°0°0°30°90°0°90°0°0°0°40°90°0°90°90°0°0°Fig. 4-14: Extension 0%, axis 1 - axis 4Fig. 4-15: Extension 33%, axis 1 - axis 4Extension 66%Extension 100%4.5.3Stopping distances and stopping times for LBR iiwa 7 R800The stopping distances and stopping times indicated apply to the following media flange:⏹Basic flange4.5.3.1Stopping distances and stopping times for STOP 0, axis 1 to axis 4The table shows the stopping distances and stopping times after a STOP 0 (category 0 stop) is triggered. The values refer to the following configuration:⏹Extension l = 100%⏹Program override POV = 100%⏹Mass m = maximum load (rated load + supplementary load on arm)Fig. 4-16: 66% extension, axis 1 - axis 4Fig. 4-17: Extension 100%, axis 1 - axis 4The stopping distances and times of other media flanges are speci-fied in the media flange assembly and operating instructions.Stopping distance (°)Stopping time (s)Axis 1 5.1930.182Axis 2 5.0920.212Axis 38.0910.166Axis 47.5380.1144.5.3.2Stopping distances and stopping times for STOP 1, axis 1Fig. 4-18: Stopping distances for STOP 1, axis 1Fig. 4-19: Stopping times for STOP 1, axis 14.5.3.3Stopping distances and stopping times for STOP 1, axis 2Fig. 4-20: Stopping distances for STOP 1, axis 2Fig. 4-21: Stopping times for STOP 1, axis 24.5.3.4Stopping distances and stopping times for STOP 1, axis 3Fig. 4-22: Stopping distances for STOP 1, axis 3Fig. 4-23: Stopping times for STOP 1, axis 34.5.3.5Stopping distances and stopping times for STOP 1, axis 4Fig. 4-24: Stopping distances for STOP 1, axis 44.5.4Stopping distances and stopping times for LBR iiwa 14 R820The stopping distances and stopping times indicated apply to the following media flange:Fig. 4-25: Stopping times for STOP 1, axis 4⏹Basic flange4.5.4.1Stopping distances and stopping times for STOP 0, axis 1 to axis 4The table shows the stopping distances and stopping times after a STOP 0 (category 0 stop) is triggered. The values refer to the following configuration:⏹Extension l = 100%⏹Program override POV = 100%⏹Mass m = maximum load (rated load + supplementary load on arm)The stopping distances and times of other media flanges are speci-fied in the media flange assembly and operating instructions.Stopping distance (°)Stopping time (s)Axis 15.7420.188Axis 25.9980.200Axis 39.3230.198Axis 4 3.1620.0924.5.4.2Stopping distances and stopping times for STOP 1, axis 1Fig. 4-26: Stopping distances for STOP 1, axis 1Fig. 4-27: Stopping times for STOP 1, axis 14.5.4.3Stopping distances and stopping times for STOP 1, axis 2Fig. 4-28: Stopping distances for STOP 1, axis 2Fig. 4-29: Stopping times for STOP 1, axis 24.5.4.4Stopping distances and stopping times for STOP 1, axis 3Fig. 4-30: Stopping distances for STOP 1, axis 34 Technical dataFig. 4-31: Stopping times for STOP 1, axis 3。
译文GMW3172

General Specification Electrical/Electronic GMW3172General Specification for Electrical/Electronic Component Analytical/Development/Validation (A/D/V) Procedures forConformance to Vehicle Environmental, Reliability, Durability, and Performance Requirements Version 电子零件通用标准汽车环境,靠得住性,耐久性和大体性能要求分析/开发/验证程序 1 Summary of Critical Information 概述The information provided in section one is a summary of the critical requirements for Validation. Detailed explanation of each test or analysis is provided starting in section two. 第一部份是验证要求的概述。
第二部份详细的说明了每一个实验或分析的条件。
1.1 How To Use This Document 如何去用那个文件Figure 1 How To UseThisDocumentQuoting Requirements in Documentation.报价要求Example CTS Reliability Paragraph:”The analytical, developmental and validation mandatory tasks identified in GWM3172 must be performed to ensure adequate product maturity by the end of the product development lifecycle. The component shall pass the Design Validation and Product Validation environmentaland durability requirements of GMW3172. These requirements shall be clearly identifiedthrough use of the GMW3172 Coding System resulting from the location of the product in thevehicle. The code for this product is _____________. A product reliability of at least 97%, witha statistical confidence of 50%, shall be demonstrated on test as described within GMW3172 for product subjected to a combination of vibration and thermally induced fatigue. Thedemonstration of 97% Reliability on-Test corresponds to a field reliability of % under theassumption of a Customer Variability Ratio of three. The Test Flows identified in GMW3172must be followed with any exception receiving prior approval before establishing the ADV supplier must attain world-class reliability for this product. The test requirements contained in this document are necessary but may not be sufficient to meet this world-class field reliability requirement. The supplier is responsible for assuring that other actions are taken such that world class field reliability requirements are met.”在GMW3172中分析、开发、验证被强制要求执行是为了确保最终产品的成熟。
ECE 21

E/ECE/324 )Rev.1/Add.20/Rev.2/Amend.2E/ECE/TRANS/505 )March 25, 2003STATUS OF UNITED NATIONS REGULATIONECE 21UNIFORM PROVISIONS CONCERNING THE APPROVAL OF:VEHICLES WITH REGARD TO THEIR INTERIOR FITTINGSIncorporating:Supplement 2 to the 01 series of amendments Date of Entry into Force: 18.01.98 Corr. 1 to the 01 series of amendments Date of Entry into Force: 08.03.00 Supplement 3 to the 01 series of amendments Date of Entry into Force: 31.01.03E/ECE/324 )Rev.1/Add.20/Rev.2/Amend.2E/ECE/TRANS/505 )March 25, 2003UNITED NATIONSAGREEMENTCONCERNING THE ADOPTION OF UNIFORM TECHNICAL PRESCRIPTIONS FOR WHEELED VEHICLES, EQUIPMENT AND PARTS WHICH CAN BE FITTED AND/OR BE USED ON WHEELED VEHICLES AND THE CONDITIONS FOR RECIPROCAL RECOGNITION OFAPPROVALS GRANTED ON THE BASIS OF THESE PRESCRIPTIONS (*)(Revision 2, including the amendments which entered into force on October 16, 1995)Addendum 20: Regulation No. 21Revision 2 — Amendment 2Supplement 3 to the 01 series of amendments - Date of entry into force: January 31, 2003UNIFORM PROVISIONS CONCERNING THE APPROVAL OF VEHICLES WITH REGARDTO THEIR INTERIOR FITTINGS(*)Former title of the Agreement:Agreement Concerning the Adoption of Uniform Conditions of Approval and Reciprocal Recognition of Approval for Motor Vehicle Equipment and Parts, done at Geneva on March 20, 1958.REGULATION No. 21UNIFORM PROVISIONS CONCERNING THE APPROVAL OF VEHICLES WITH REGARDTO THEIR INTERIOR FITTINGSCONTENTSREGULATION1. Scope2. Definitions3. Application for approval4. Approval5. Requirements6. Modifications and extension of approval of the vehicle type7. Conformity of production8. Penalties for non-conformity of production9. Production definitely discontinued10. Names and addresses of technical services responsible for conducting approval tests, and ofadministrative departmentsANNEXESAnnex 1 Determination of the Head-impact ZoneAnnex 2 Communication concerning the approval or extension or refusal or withdrawal of approval or production definitely discontinued of a vehicle type with regard to its interior fittings,pursuant to Regulation No. 21Annex 3 Arrangements of the approval marksAnnex 4 Procedure for testing energy-dissipating materialsAnnex 5 Procedure for determining the "H" point and the actual torso angle for seating positions in motor vehiclesAnnex 6 Method of measuring projectionsAnnex 7 Apparatus and procedure for application of Paragraph 5.2.1. of this regulationAnnex 8 Determination of a dynamically determined head impact zoneAnnex 9 Typical position of cylindrical test rod in the opening roof and window openingsAnnex 10 Explanatory notesREGULATION No. 21UNIFORM PROVISIONS CONCERNING THE APPROVAL OF VEHICLES WITH REGARDTO THEIR INTERIOR FITTINGS1. SCOPEThis Regulation applies to the interior fittings of vehicles of Category M1 with regard to:1.1the interior parts of the passenger compartment other than the rear-view mirror or mirrors; 1.2the arrangement of the controls;or opening roof, androof1.3 the1.4the seat-back and the rear parts of seats.1.5.power-operation of windows, roof panels and partition systems.2. DEFINITIONSFor the purpose of this Regulation,2.1"approval of a vehicle" means the approval of a vehicle type with regard to its interiorfittings;2.2."vehicle type" with regard to the interior fittings of the passenger compartment meansvehicles of Category M1 which do not differ in such essential respects as:2.2.1.the lines and constituent materials of the bodywork of the passenger compartment;2.2.2.the arrangement of the controls;2.2.3.the performance of the protective system, if the reference zone within the head impact zonedetermined according to Annex 8 (dynamic evaluation) is chosen by the applicant.2.2.3.1. Vehicles that differ only in the performance of the protective system(s) belong to the samevehicle type if they offer an equal or better protection for the occupants compared with thesystem or vehicle submitted to the technical service responsible for conducting the approvaltests.2.3."reference zone"is the head-impact zone as defined in Annex 1 to this Regulation, or atthe choice of the manufacturer, according to Annex 8, excluding the following areas: (seeAnnex 10, explanatory notes, Paragraphs 2.3. and 2.3.1.)2.3.1.the area bounded by the forward horizontal projection of a circle circumscribing the outerlimits of the steering control, increased by a peripheral band 127 mm in width; this area isbounded below by the horizontal plane tangential to the lower edge of the steering controlwhen the latter is in the position for driving straight ahead; (see Annex 10, explanatorynotes, Paragraphs 2.3. and 2.3.1.)2.3.2.the part of the surface of the instrument panel comprised between the edge of the areaspecified in Paragraph 2.3.1. above and the nearest inner side-wall of the vehicle; this partof the surface is bounded below by the horizontal plane tangential to the lower edge of thesteering control and; (see Annex 10, explanatory notes, Paragraphs 2.3. and 2.3.1.)2.3.3.the windscreen side pillars; (see Annex 10, explanatory notes, Paragraphs 2.3. and 2.3.1.) 2.4."level of the instrument panel" means the line defined by the points of contact of verticaltangents to the instrument panel; (see Annex 10, explanatory notes, Paragraph 2.4.)2.5."roof" means the upper part of the vehicle extending from the upper edge of thewindscreen to the upper edge of the rear window and bounded at the sides by the upperframework of the side-walls; (see Annex 10, explanatory notes, Paragraph 2.5.)2.6."belt line" means the line constituted by the transparent lower contour of the side windowsof the vehicle;2.7."convertible car" means a vehicle where, in certain configurations, there is no rigid part ofthe vehicle body above the belt line with the exception of the front roof supports and/or theroll-over bars and/or the seat belt anchorage points; (see Annex 10, explanatory notes,Paragraphs 2.5. and 2.7.)2.8."vehicle with opening roof" means a vehicle of which only the roof or part of it can befolded back or be opened, or may slide, leaving the existing structural elements of thevehicle above the belt line; (see Annex 10, explanatory notes, Paragraph 2.5.)2.9."folding (tip-up) seat" means an auxiliary seat intended for occasional use and which isnormally folded out of the way.system" means interior fittings and devices intended to restrain the occupants.2.10. "protective2.11. "type of a protective system" means a category of protective devices which do not differin such essential respects as:technology;2.11.1. their2.11.2. theirgeometry;2.11.3.their constituent materials.2.12. "power-operatedwindows" means windows which are closed by power supply of the vehicle.systems" means movable panels in the vehicle roof whichroof-panel2.13. "power-operatedare closed by power supply of the vehicle by either a sliding and/or tilting motion, and whichdo not include convertible top systems.systems" means systems which divide a passenger carpartition2.14. "power-operatedcompartment into at least two sections and which are closed using the power supply of thevehicle.2.15. "opening" is the maximum unobstructed aperture between the upper edge or leading edge,depending on the closing direction, of a power-operated window or partition or roof paneland the vehicle structure which forms the boundary of the window, partition or roof panel,when viewed from the interior of the vehicle or, in the case of partition system, from the rearpart of the passenger compartment.To measure an opening, a cylindrical test rod shall (without exerting force) be placedthrough it normally perpendicular to the edge of the window, roof panel or partition andperpendicular to the closing direction as shown in Figure 1 of Annex 9, from the interiorthrough to the exterior of the vehicle or, as applicable, from the rear part of the passengercompartment.2.16. "key"2.16.1."ignition key" means the device that operates the electric power supply necessary tooperate the engine or motor of the vehicle. This definition does not preclude a nonmechanical device.2.16.2."power key" means the device which allows power to be supplied to the power systems ofthe vehicle. This key may also be the ignition key. This definition does not preclude a nonmechanical device.2.17. "airbag" means a device installed to supplement safety belts and restraint systems inpower driven vehicles, i.e. systems which in the event of a severe impact affecting thevehicle automatically deploy a flexible structure intended to limit, by compression of the gascontained within it, the severity of the contacts of one or more parts of an occupant of thevehicle with the interior of the passenger compartment.2.18. A "sharp edge" is an edge of a rigid material having a radius of curvature of less than2.5 mm except in the case of projections of less than3.2 mm, measured from the panelaccording to the procedure described in Paragraph 1 of Annex 6. In this case, the minimumradius of curvature shall not apply provided the height of the projection is not more than halfits width and its edges are blunted (see Annex 10, explanatory notes, Paragraph 2.18.)3. APPLICATION FOR APPROVAL3.1.The application for approval of a vehicle type with regard to its interior fittings shall besubmitted by the vehicle manufacturer or by his duly accredited representative.3.2.It shall be accompanied by the undermentioned documents in triplicate and the followingparticulars:a detailed description of the vehicle type with regard to the items mentioned inParagraph 2.2. above, accompanied by a photograph or an exploded view of the passengercompartment. The numbers and/or symbols identifying the vehicle type shall be specified. 3.3.The following shall be submitted to the technical service responsible for conducting theapproval tests:3.3.1.at the manufacturer's discretion, either a vehicle representative of the vehicle type to beapproved or the part or parts of the vehicle regarded as essential for the checks and testsprescribed by this Regulation;3.3.2.at the request of the aforesaid technical service, certain components and certain samples ofthe materials used.4. APPROVAL4.1.If the vehicle type submitted for approval pursuant to this Regulation meets therequirements of Paragraph 5. below, approval of that vehicle type shall be granted.4.2.An approval number shall be assigned to each type approved. Its first two digits (at present01 corresponding to the 01 series of amendments which entered into force onApril 26, 1986) shall indicate the series of amendment incorporating the most recent majortechnical amendments made to the Regulation at the time of issue of the approval. Thesame Contracting Party may not assign the same number to another vehicle type.4.3.Notice of approval or of extension or refusal or of withdrawal of approval or productiondefinitely discontinued of a vehicle type pursuant to this Regulation shall be communicatedto the Parties to the Agreement which apply this Regulation by means of a form conformingto the model in Annex 2 to this Regulation.4.4.There shall be affixed, conspicuously and in a readily accessible place specified on theapproval form, to every vehicle conforming to a vehicle type approved under this Regulation,an international approval mark consisting of:4.4.1. a circle surrounding the Letter "E" followed by the distinguishing number of the countrywhich has granted approval; (1)4.4.2.the number of this Regulation, followed by the Letter "R", a dash and the approval numberto the right of the circle prescribed in Paragraph 4.4.1. above.4.5.If the vehicle conforms to a vehicle type approved, under one or more other Regulationsannexed to the Agreement, in the country which has granted approval under thisRegulation, the symbol prescribed in Paragraph 4.4.1. need not be repeated; in such acase, the regulation and approval numbers and the additional symbols of all the Regulationsunder which approval has been granted in the country which has granted approval underthis Regulation shall be placed in vertical columns to the right of the symbol prescribed inParagraph 4.4.1. above.4.6.The approval mark shall be clearly legible and be indelible.4.7.The approval mark shall be placed close to or on the vehicle data plate affixed by themanufacturer.4.8.Annex 3 to this Regulation gives examples of arrangement of the approval marks.5. REQUIREMENTS5.1.Forward interior parts of the passenger compartment above the level of the instrument panelin front of the front seat "H" points, excluding the side doors.5.1.1.The reference zone defined in Paragraph 2.3. above shall not contain any dangerousroughness or sharp edges likely to increase the risk of serious injury to the occupants. If thehead impact area is determined according to Annex 1, the parts referred to in Paragraphs5.1.2. to 5.1.6. below shall be deemed satisfactory if they comply with the requirements ofthose paragraphs. If the head impact area is determined according to Annex 8, therequirements of Paragraph 5.1.7. shall apply (see Annex 10, explanatory notes,Paragraph 5.1.1.)(1)1 for Germany,2 for France,3 for Italy,4 for the Netherlands,5 for Sweden,6 for Belgium,7 for Hungary,8 for the CzechRepublic, 9 for Spain, 10 for Yugoslavia, 11 for the United Kingdom, 12 for Austria, 13 for Luxembourg, 14 for Switzerland,15 (vacant), 16 for Norway, 17 for Finland, 18 for Denmark, 19 for Romania, 20 for Poland, 21 for Portugal, 22 for theRussian Federation, 23 for Greece, 24 for Ireland, 25 for Croatia, 26 for Slovenia, 27 for Slovakia, 28 for Belarus, 29 for Estonia, 30 (vacant), 31 for Bosnia and Herzegovina, 32 for Latvia, 33 (vacant), 34 for Bulgaria, 35-36 (vacant), and 37 for Turkey, 38-39 (vacant), 40 for The former Yugoslav Republic of Macedonia, 41 (vacant), 42 for the European Community (Approvals are granted by its Member States using their respective ECE symbol), 43 for Japan, 44 (vacant), 45 for Australia and 46 for Ukraine. Subsequent numbers shall be assigned to other countries in the chronological order in which they ratify or accede to the Agreement concerning the Adoption of Uniform Technical Prescriptions for Wheeled Vehicles, Equipment and Parts which can be Fitted and/or be Used on Wheeled Vehicles and the Conditions for Reciprocal Recognition of Approvals Granted on the Basis of these Prescriptions, and the numbers thus assigned shall be communicated by the Secretary-General of the United Nations to the Contracting Parties to the Agreement5.1.2.Vehicle parts within the reference zone with the exception of those which are not part of theinstrument panel and which are placed at less than 10 cm from glazed surfaces shall beenergy-dissipating, as prescribed in Annex 4 to this Regulation. Those parts within thereference zone which satisfy both of the following conditions shall also be excluded fromconsideration if: (see Annex 10, explanatory notes, Paragraph 5.1.2.)5.1.2.1. during a test in accordance with the requirements of Annex 4 of this Regulation, thependulum makes contact with parts outside the reference zone; and5.1.2.2. parts to be tested are placed less than 10 cm away from the parts contacted outside thereference zone, this distance being measured on the surface of the reference zone;any metal support fittings shall have no protruding edges.5.1.3.The lower edge of the instrument panel shall, unless it meets the requirements ofParagraph 5.1.2. above, be rounded to a radius of curvature of not less than 19 mm. (seeAnnex 10, explanatory notes, Paragraph 5.1.3.)5.1.4.Switches, pull-knobs and the like, made of rigid material which, measured in accordancewith the method prescribed in Annex 6, project from 3.2 mm to 9.5 mm from the panel shallhave a cross sectional area of not less than 2 cm2, measured 2.5 mm from the pointprojecting furthest and shall have rounded edges with a radius of curvature of not less than2.5 mm. (see Annex 10, explanatory notes, Paragraph 5.1.4.)5.1.5.If these components project more than 9.5 mm from the surface of the instrument panel,they shall be so designed and constructed as to be able, under the effect of a longitudinalhorizontal force of 37.8 daN delivered by a flat-ended ram of not more than 50 mmdiameter, either to retract into the surface of the panel until they do not project by more than9.5 mm or to become detached; in the latter case, no dangerous projections of more than9.5 mm shall remain; a cross-section of not more than 6.5 mm from the point of maximumprojection shall be not less than 6.5 cm2 in area. (see Annex 10, explanatory notes,Paragraph 5.1.5.)5.1.6.In the case of a projection comprising a component made of non-rigid material of less than50 shore A hardness mounted on a rigid support, the requirements of Paragraphs 5.1.4. and5.1.5. shall apply only to the rigid support or it shall be demonstrated by sufficient testsaccording to the procedure described in Annex 4 that the soft material of less than 50 shoreA hardness will not be cut so as to contact the support during the specified impact test. Inthat case the radius requirements shall not apply (see Annex 10, explanatory notes,Paragraph 5.1.6.).5.1.7.The following Paragraphs shall apply:5.1.7.1. If the protective system of the vehicle type cannot prevent head contacts of the occupantsdefined in Paragraph 1.2.1. of Annex 8 with the instrument panel, and a dynamic referencezone according to Annex 8 is determined, the requirements of Paragraphs 5.1.2. to 5.1.6.are applicable only to the parts located in that zone.Parts in other areas of the dashboard above the level of the instrument panel, if contactableby a 165 mm diameter sphere, shall be at least blunted.5.1.7.2. If the protective system of the vehicle type is able to prevent head contacts of the occupantsdefined in Paragraph 1.2.1. of Annex 8 with the instrument panel and therefore no referencezone can be determined, the requirements of Paragraphs 5.1.2. to 5.1.6. are not applicableto this vehicle type.Parts of the dashboard above the level of the instrument panel, if contactable by a 165 mmdiameter sphere, shall be at least blunted.5.2.Forward interior parts of the passenger compartment below the level of the instrument paneland in front of the front seat "H" points, excluding the side doors and the pedals5.2.1.Except for the pedals and their fixtures and those components that cannot be contacted bythe device described in Annex 7 to this Regulation and used in accordance with theprocedure described therein, components covered by Paragraph 5.2., such as switches, theignition key, etc. shall comply with the requirements of Paragraphs 5.1.4. to 5.1.6.5.2.2.The handbrake control, if mounted on or under the instrument panel, shall be so placed thatwhen it is in the position of rest there is no possibility of the occupants of the vehicle strikingagainst it in the event of a frontal impact. If this condition is not met, the surface of thecontrol shall satisfy the requirements of Paragraph 5.3.2.3. below. (see Annex 10,explanatory notes, Paragraph 5.2.2.)5.2.3.Shelves and other similar items shall be so designed and constructed that the supports inno case have protruding edges, and they shall meet one or other of the following conditions:(see Annex 10, explanatory notes, Paragraph 5.2.3.)5.2.3.1. The part facing into the vehicle shall present a surface not less than 25 mm high with edgesrounded to a radius of curvature of not less than 3.2 mm. This surface shall consist of or becovered with an energy-dissipating material, as defined in Annex 4 of this Regulation, andshall be tested in accordance therewith, the impact being applied in a horizontal longitudinaldirection. (see Annex 10, explanatory notes, Paragraph 5.2.3.1.)5.2.3.2. Shelves and other similar items shall, under the effect of a forward-acting horizontallongitudinal force of 37.8 daN exerted by a cylinder of 110 mm diameter with its axis vertical,become detached, break up, be substantially distorted or retract without producingdangerous features on the rim of the shelf. The force must be directed at the strongest partof the shelves or other similar items. (see Annex 10, explanatory notes, Paragraph 5.2.3.2.) 5.2.4.If the items in question contain a part made of material less than 50 shore A hardness whenfitted to a rigid support, the above requirements, except for the requirements covered byAnnex 4 relating to energy-absorption, shall apply only to the rigid support or it can bedemonstrated by sufficient tests according to the procedure described in Annex 4 that thesoft material of less than 50 shore A hardness will not be cut so as to contact the supportduring the specified impact test. In that case the radius requirements shall not apply.5.3.Other interior fittings in the passenger compartment in front of the transverse plane passingthrough the torso reference line of the manikin placed on the rearmost seats (see Annex 10,explanatory notes, Paragraph 5.3.)5.3.1. ScopeThe requirements of Paragraph 5.3.2. below apply to control handles, levers and knobs andto any other protruding objects not referred to in Paragraphs 5.1. and 5.2. above. (See alsoParagraph 5. 3. 2. 2.)5.3.2. RequirementsIf the items referred to in Paragraph 5.3.1. above are so placed that occupants of the vehiclecan contact them, they shall meet the requirements of Paragraphs 5.3.2.1. to 5.3.4. If theycan be contacted by a 165 mm diameter sphere and are above the lowest "H" point (seeAnnex 5 of this Regulation) of the front seats and forward of the transverse plane of thetorso reference line of the manikin on the rearmost seat, and outside the zones defined inParagraphs 2.3.1. and 2.3.2., these requirements shall be considered to have beenfulfilled if: (see Annex 10, explanatory notes, Paragraph 5.3.2.)terminates in rounded edges, the radii of curvature being not less than 3.2 mm;5.3.2.1. theirsurface(see Annex 10, explanatory notes, Paragraph 5.3.2.1.)5.3.2.2. control levers and knobs shall be so designed and constructed that, under the effect of aforward acting longitudinal horizontal force of 37.8 daN either the projection in its mostunfavourable position is reduced to not more than 25 mm from the surface of the panel orthe said fittings become detached or bent; in the two latter cases no dangerous projectionsshall remain. Window winders may, however, project 35 mm from the surface of the panel;(see Annex 10, explanatory notes, Paragraph 5.3.2.2.)5.3.2.3. the handbrake control, when in the released position, and the gear lever, when in anyforward gear position, have, except when placed in the zones defined in Paragraphs 2.3.1.and 2.3.2. and in the zones below the horizontal plane passing through the "H" point of thefront seats, a surface area of not less than 6.5 cm2 measured at a cross-section normal tothe longitudinal horizontal direction up to a distance of 6.5 mm from the part projectingfurthest, the radius of curvature being not less than 3.2 mm. (see Annex 10, explanatorynotes, Paragraph 5.3.2.3.)5.3.3The requirements in Paragraph 5.3.2.3. shall not apply to a floor-mounted handbrakecontrol; for such controls, if the height of any part in the released position is above ahorizontal plane passing through the lowest "H" point of the front seats (see Annex 5 of thisRegulation) the control shall have a cross sectional area of at least 6.5 cm2 measured in ahorizontal plane not more than 6.5 mm from the furthest projecting part (measured in thevertical direction). The radius of curvature shall not be less than 3.2 mm.5.3.4.The other elements of the vehicle's equipment not covered by the above paragraph, such asseat slide rails, devices for regulating the horizontal or vertical part of the seat, devices forrolling up safety belts, etc. are not subject to any regulation if they are situated below ahorizontal line passing through the "H" point of each seat even though the occupant is likelyto come into contact with such elements. (see Annex 10, explanatory notes,Paragraph 5.3.4.)5.3.4.1. Components mounted on the roof, but which are not part of the roof structure, such as grabhandles, lamps and sun visors, etc. shall have a radius of curvature not less than3.2 mm. In addition, the width of the projecting parts shall not be less than the amount oftheir downward projection; alternatively, these projecting parts shall pass theenergy-dissipating test in accordance with the requirements of Annex 4. (see Annex 10,explanatory notes, Paragraph 5.3.4.1.)5.3.5.If the parts considered above comprise a component made of material of less than50 shore A hardness, mounted on a rigid support, the above requirements shall apply onlyto the rigid support or it can be demonstrated by sufficient tests according to the proceduredescribed in Annex 4 that the soft material of less than 50 shore A hardness will not be cutso as to contact the support during the specified impact test. In that case the radiusrequirements shall not apply.5.3.6.In addition, power operated windows and partition systems and their controls shall meet therequirements of Paragraph 5.8. below.5.4. Roof (see Annex 10, explanatory notes, Paragraph 5.4.)5.4.1. Scope5.4.1.1. The requirements of Paragraph 5.4.2. below apply to the inner face of the roof.5.4.1.2. However, they do not apply to such parts of the roof as cannot be touched by a sphere165 mm in diameter.5.4.2. Requirements5.4.2.1. That part of the inner face of the roof which is situated above or forward of the occupantsshall exhibit no dangerous roughness at sharp edges, directed rearwards ordownwards. The width of the projecting parts shall not be less than the amount of theirdownward projection and the edges shall have a radius of curvature of not less than5 mm. In particular, the rigid roof sticks or ribs, with the exception of the header rail of theglazed surfaces and door frames, shall not project downwards more than 19 mm. (seeAnnex 10, explanatory notes, Paragraph 5.4.2.1.)5.4.2.2. If the roof sticks or ribs do not meet the requirements of Paragraph 5.4.2.1. they shall passthe energy-dissipating test in accordance with the requirement of Annex 4 to thisRegulation.5.4.2.3. The metal wires which stretch the lining of the roof and the frames of the sun visors shallhave a maximum diameter of 5 mm or be able to absorb the energy, as prescribed inAnnex 4 to this Regulation. Non-rigid attachment elements of the frames of the sun visorsshall meet the requirements of Paragraph 5.3.4.1. above.。
英汉对照的1236-1238说明书

AC INDUCTION MOTOR CONTROLLERS交流感应电动机控制器M O D E L 1 2 3 6 / 1 2 3 8 D E S C R I P T I O N1 2 3 6 / 1 2 3 8实用范围Curtis Models 1236 and 1238 provide advanced control of AC induction motors performing on-vehicle traction drive or hydraulic pump duties. They offer vehicle developers a highly cost-effective combination of power, performance and functionality.柯蒂斯模型1236和1238提供了先进控制的交流感应电机车牵引传动或液压泵履行职责。
他们提供开发者一个极具成本效益的结合力强,性能和功能。
A P P L I C A T I O NDesigned primarily for use on medium to large material handling vehicles such as counterbalance or warehouse trucks.The Model 1236 is equally suitable for Light-On-Road passenger vehicles utility vehicles. .The larger Model 1238 is also intended for use and on all heavy-duty applications such as Tow Tractors and Airport Ground Support Equipment (GSE).主要用于大中型材料处理车辆如平衡或货仓车。
2024版年度UCP600

Disclaimer and Exceptions
2024/2/2
01
UCP 600 rules apply only to the relationship between banks and not to the underlying transaction.
02
Banks are not responsible for the accuracy or authenticity of the documents they handle.
03
Providing necessary documents and information.
04
Paying the required fees and charges.
2024/2/2
8
Beneficiary process
01
Receiving and reviewing the letransactions.
16
The impact of UCP600 on international trade
2024/2/2
Increased efficiency
UCP600 streamlines the process of handling documentary credits, which helps to increase efficiency and reduce the time and cost associated with international trade transactions.
risk associated with extending credit to importers and exporters. This, in turn, helps to promote
ICCUCP600跟单信用证统一惯例中英文对照

ICC UCP600跟单信用证统一惯例(中英文对照) 第一条UCP的适用范围第二条定义第三条解释第四条信用证与合同第五条单据与货物、服务或履约行为第六条兑用方式、截止日和交单地点第七条开证行责任第八条保兑行责任第九条信用证及其修改的通知第十条修改第十一条电讯传输的和预先通知的信用证和修改第十二条指定第十三条银行之间的偿付安排第十四条单据审核标准第十五条相符交单第十六条不符单据、放弃及通知第十七条正本单据及副本第十八条商业发票第十九条涵盖至少两种不同运输方式的运输单据第二十条提单第二十一条不可转让的海运单第二十二条租船合同提单第二十三条空运单据第二十四条公路、铁路或内陆水运单据第二十五条快递收据、邮政收据或投邮证明第二十六条“货装舱面”、“托运人装载和计数”、“内容据托运人报称”及运费之外的费用第二十七条清洁运输单据第二十八条保险单据及保险范围第二十九条截止日或最迟交单日的顺延第三十条信用证金额、数量与单价的伸缩度第三十一条部分支款或部分发运第三十二条分期支款或分期发运第三十三条交单时间第三十四条关于单据有效性的免责第三十五条关于信息传递和翻译的免责第三十六条不可抗力第三十七条关于被指示方行为的免责第三十八条可转让信用证第三十九条款项让渡The Uniform Customs and Practice for Documentary Credits, 2007 Revision, ICC Publication no. 600 (“UCP”) are rules that apply to any documentary credit (“credit”) (including, to the extent to which they may be applicable, any standby letter of credit) when the text of the credit expressly indicates that it is subject to these rules. They are binding on allparties thereto unless expressly modified or excluded by the credit.跟单信用证统一惯例,2007年修订本,国际商会第600号出版物,适用于所有在正文中标明按本惯例办理的跟单信用证(包括本惯例适用范围内的备用信用证)。
全面版车辆使用协议英文版

全面版车辆使用协议英文版Comprehensive Vehicle Utilization AgreementThis document serves as a comprehensive agreement outlining the terms and conditions for the use of vehicles within our organization. It is essential for all employees to familiarize themselves with the guidelines specified herein to ensure safe and efficient utilization of company vehicles.1. Vehicle UsageEmployees are permitted to use company vehicles for official business purposes only. Personal use of company vehicles is strictly prohibited unless authorized by management.2. Maintenance and CareIt is the responsibility of the driver to ensure that the vehicle iswell-maintained and in good working condition. Regular maintenance checks should be conducted, and any issues should be reported promptly.3. Reporting AccidentsIn the event of an accident, employees must report the incident immediately to their supervisor and complete an accident report form. Failure to do so may result in disciplinary action.4. Fuel and ExpensesEmployees are required to keep track of fuel consumption and any other expenses related to vehicle usage. Proper documentation should be maintained and submitted to the appropriate department for reimbursement.5. Vehicle ReturnUpon completion of the assigned task, the vehicle must be returned to the designated parking area. It is the responsibility of the driver to ensure that the vehicle is parked securely and all belongings are removed.6. Compliance with RegulationsAll employees must adhere to traffic laws and regulations while operating company vehicles. Any violations may result in legal consequences and disciplinary action.7. ConfidentialityEmployees are prohibited from disclosing any confidential information obtained during the course of their vehicle usage. Any breach of confidentiality will result in severe consequences.8. Termination of AgreementThis agreement may be terminated at any time by the organization if there is a breach of any of the terms and conditions outlined herein.Employees must return the vehicle immediately upon termination of the agreement.By signing below, the employee acknowledges that they have read and understood the terms of this agreement and agree to abide by them.Employee Signature: ___________________________Date: ___________________________。
UCP600中英文版

《跟单信用证统一惯例(UCP600)》Article 1 Application of UCP第一条 UCP的适用范围The Uniform Customs and Practice for Documentary Credits, 2007 Revision, ICC Publication no. 600 (“UCP”) are rules that apply to any documentary credit (“credit”including, to the extent to which they may be applicable, any standby letterof credit) when the text of the credit expressly indicates that it is subject to these rules. They are binding on all parties thereto unless expressly modified or excluded by the credit.跟单信用证统一惯例,2007年修订本,国际商会第600号出版物,适用于任何在正文中标明按本惯例办理的跟单信用证(包括本惯例适用范围内的备用信用证)。
除非信用证明确修改或排除,本惯例对一切有关当事人均具有约束力。
Article 2 Definitions第二条定义For the purpose of these rules:就本惯例而言:Advising bank means the bank that advises the credit at the request of the issuing bank.通知行意指应开证行要求通知信用证的银行。
Applicant means the party on whose request the credit is issued.申请人意指发出开立信用证申请的一方。
Cars with the Best Infotainment Systems

Cars with the Best Infotainment Systems When it comes to cars, having a top-notch infotainment system can make a significant difference in the overall driving experience. From entertainment to navigation and connectivity, a good infotainment system can greatly enhance the convenience and enjoyment of being on the road. In this article, we'll explore some of the cars with the best infotainment systems, taking into account factors such as user interface, features, connectivity, and overall user experience. One car that often receives praise for its infotainment system is the Tesla Model S. With its large touchscreen display, the Tesla Model S offers a user-friendly interface that seamlessly integrates entertainment, navigation, and vehicle controls. The system is highly responsive and supports over-the-air updates, ensuring that drivers always have access to the latest features and improvements. Additionally, the Tesla Model S comes with a host of connectivity options, including Bluetooth, Wi-Fi, and smartphone integration, allowing drivers to stay connected while on the go. Another car known for its exceptional infotainment system is the Audi A8. The Audi MMI infotainment system found in the A8 features a dual touchscreen display with haptic feedback, providing a futuristic andintuitive user interface. The system supports natural language voice recognition and integrates seamlessly with smartphone devices, allowing for easy access to apps, contacts, and music. The Audi A8 also offers advanced navigation features, including real-time traffic updates and predictive destination suggestions, making it a standout in the luxury car segment. Moving on to the realm of luxury SUVs, the Range Rover Velar stands out for its advanced infotainment system. The Touch Pro Duo infotainment system in the Velar features two high-definition touchscreens that control everything from entertainment and climate settings to off-roaddriving modes. The system is highly customizable, allowing drivers to personalize their user interface and access their favorite features with ease. With supportfor both Apple CarPlay and Android Auto, the Range Rover Velar ensures seamless smartphone integration for a connected driving experience. For those in the market for a more budget-friendly option, the Mazda CX-5 offers a compelling infotainment system that rivals those found in more expensive vehicles. The Mazda Connect system in the CX-5 features a user-friendly interface with a centrallypositioned touchscreen display. The system is known for its responsiveness andease of use, with intuitive menu navigation and quick access to essential features. With standard features such as Bluetooth connectivity and smartphone integration, the Mazda CX-5 provides a well-rounded infotainment experience at an affordable price point. In the realm of electric vehicles, the Chevrolet Bolt EV stands out for its comprehensive infotainment system. The Bolt EV features a large touchscreen display with an intuitive user interface that seamlessly integrates entertainment, navigation, and vehicle settings. The system supports features such as energy usage monitoring and charging station location services, catering to the unique needs of electric vehicle drivers. With built-in 4G LTE Wi-Fi and supportfor smartphone integration, the Chevrolet Bolt EV offers a connected driving experience for tech-savvy drivers. Last but not least, the Volvo XC90 deserves a mention for its advanced Sensus infotainment system. The XC90 features avertically oriented touchscreen display that serves as the central hub for entertainment, navigation, and vehicle controls. The system is known for its crisp graphics and responsive touch controls, providing a modern and luxurious user experience. With support for features such as Apple CarPlay, Android Auto, and in-car Wi-Fi, the Volvo XC90 ensures that drivers and passengers stay connected and entertained throughout their journeys. In conclusion, a good infotainment system can greatly enhance the driving experience, providing convenience, entertainment, and connectivity on the road. Whether it's the futuristic interface of the Tesla Model S, the dual touchscreen setup of the Audi A8, or the budget-friendly Mazda Connect system in the CX-5, there are plenty of cars with standout infotainment systems to choose from. As technology continues to advance, we can expect to see even more innovative infotainment systems in future car models, further enhancing the driving experience for consumers.。
SINAMICS S120 单轴和多轴驱动系统说明书

SIMOCRANE meets SINAMICSThe SINAMICS S120 offers the optimum system for each and every drive application – and all of the drives can be engineered, parameterized, commissioned and operated in a standard way.This system represents an entry-level solution for AC/AC single-axis drives and coordinated AC/DC drives for multi-axis applications, making it the perfect basis for simple and more sophisticated crane applications in all industrial sectors.Modular SolutionSINAMICS S120 includes single-axis (AC/AC drive system) as well as multi-axis (DC/AC drive system) configurations. Both systems have a modular design.The AC/AC drive system comprises a Control Unit (CU 310-2) and Power Module (PM) for the power range from 0.55 kW to 250 kW. The DC/AC drive system includes a Line Module, a Control Unit (CU320-2) and Motor Module for the power range from 1 kw to 800 kW. Active Line Modules return regenerative energy to the supply system. SIMOCRANE functions can be applied modularly on de-mand. SIMOCRANE Drive-Based Technology can be used with optional SIMOCRANE Drive-Based Sway Control. Integrated SafetyAs in SINAMICS, the crane smart features are supplemented by integrated safety functions. These support the simple implementation of innovative safety concepts which conform to standards. Safety functions are fully integrated in the control system preventing damage to crane, load and surrounding objects or people. All basic functions are license-free. The Safety Integrated Extended Functions require the optional license for each drive.Smart functionsLoad sag prevention, smart slow-down, fine manual positioning, adaptive speed to operate at peak performance are smart features of SIMOCRANE Drive-Based Technology. Sensorless sway control is an add-on highlight of SIMOCRANE Drive-Based Sway Control. All intelligence are embedded in SINAMICS drives.Simple startupVia Basic Operator Panel (BOP20) or even Web Browser, commissioning can be started by using the ‘Ready-to-Run’ solution without any engineering effort.In case of ‘Ready-to-Apply’, the crane functions are config-ured automatically by simply selecting the axis and the set value.The crane functions are integrated in the drive parameter-ization. The parameterization is individually adaptableusing the STARTER software or BOP20 or web browser. Cranes | SIMOCRANE in SINAMICS********************Applicationsupport:***********************************SIMOCRANE Drive-Based Crane Technology (DBT)SIMOCRANE in SINAMICS:Simple, flexible and fast commissioning/cranesSimple – low engineering effortThe drive-based functionality for crane applications is implemented in two software solutions: SIMOCRANE Drive-Based Technology and SIMOCRANE Drive-Based Sway Control.Both technologies are integrated in the SINAMICS drive system and provide the function blocks needed to control the motions of crane drives. By using pre-configured standard applications for hoist, trolley or gantry, the function blocks are easily integrated into the drive control, resulting in shorter engineering time and fewer commissioning costs.Using standard applications (“ready-to-run”) and simple adaptation (“ready-to-apply”) to start up a crane drive, only basic knowledge of the SINAMICS drive system is required. The software commissioning tool STARTER used by SINAMICS can be used unchanged.Fast – increase productivityLoad-dependent field weakening for hoist applications is a functionality integrated in SIMOCRANE Drive-Based Technology. Compared to operating at full load, this solution automatically increases the maximal speed for lifting and lowering as a function of the current load. With this functionality, a lift cycle with partial-load and no-load is even faster, increasing the cranes’ productivity.With SIMOCRANE Drive-Based Sway Control, the load sway is damped during trolley or gantry traveling. Without the load sway, a faster and easier traveling and positioning of the load is possible. The sway damping is integrated in the movement. No additional waiting time or additionaloperation for damping the load sway is necessary.SIMOCRANE in SINAMICS | CranesFor both single-axis and multi-axes solutionSIMOCRANE Drive-Based Technology V1.0 SP2 HF1Ordering number: 6GA7270-1AA20-0AA0SIMOCRANE Drive-Based Sway Control Manual mode Ordering number: 6GA7280-1AA10-0AB0Single-axis solutionMulti-axis solutionSIMOCRANE Drive-Based Sway ControlManual mode and Positioning Ordering number: 6GA7280-1AA20-0AB0SIMOCRANE Drive-Based Sway Control Manual mode Ordering number: 6SL3077-6AA00-2AB0SIMOCRANE Drive-Based Sway ControlManual mode and Positioning Ordering number: 6SL3077-6AA00-3AB0For hoist applications, an encoder is requested for safety reasons and for providing pendulum length to cross travel (trolley) and long travel (gantry).For sensorless sway control, no encoder is required in manual operation. Only for positioningoperation encoders are required fortrolley and gantry.For more information, refer to catalog D21.4 (Chapter 7).• Performance Manual Mode: n = 2740 RPM, ramp-up time = 2 s Pendelum length = 2.27 mResidual sway = 1 mm at standstill speed 20 RPM Residual sway = 0 mm at standstill speed 0 RPM • Crane ConfigurationConfiguration with 3 single-axis drives, controlled via onboard I/O of SINAMICS Control Unit (CU310-2)• Hoist, Trolley or GantryPre-configured application for hoist or trolley or gantry. Easy installation: the commissioning can start with low engineering effort• Power RangeThe SINAMICS AC/AC single-axis drives cover the power range from 0.55 kW to 250 kW• Drive-Based TechnologyProvides crane-specific functions: prevents load sag and uses adaptive speeds. Smart slow-down on all axis• Drive-Based Sway ControlCan damp sway in manual operation for trolley and gantryApplication: fast and easy control solution for single-axis control requirementsThe Ready-to-Apply solution is a standard application example with a mask for users to select the configu-ration of each required axis.After selection, the required files are generated automatically.PROFINET communication combines the field bus and Ethernet advan-tages. Configuration easily adaptable to be fine-tuned for enhancedproductivity.Application: comprehensive control solution for multi-axis control requirements• Crane Controlby PLC via PROFINET communication• Performance Positioning Mode v = 20 m/min, ramp up time = 3 Pendelum length = 7.9 mDistance = 7 m, time = 32.18 s, precision = 1mm Residual sway = 0.47mm• Crane ConfigurationSINAMICS S120 topology with multi-axis drives with regenerative Line Module, Motor Modules and Control Unit (CU320-2)• Power RangeSINAMICS DC/AC multi-axis cover the power range: 1.6 kW to 800 kW• CommunicationThe ProfiSafe telegram enables the SINAMICS integrated safety function by PROFINET communication• Drive-Based TechnologyCrane-specific motion control functions for hoist, short travel and long travel• Drive-Based Sway Controlis added to short travel and long travel for sway damping in manual and positioning modeFor more information, refer to catalogue D21.4.。
jstd035声学扫描
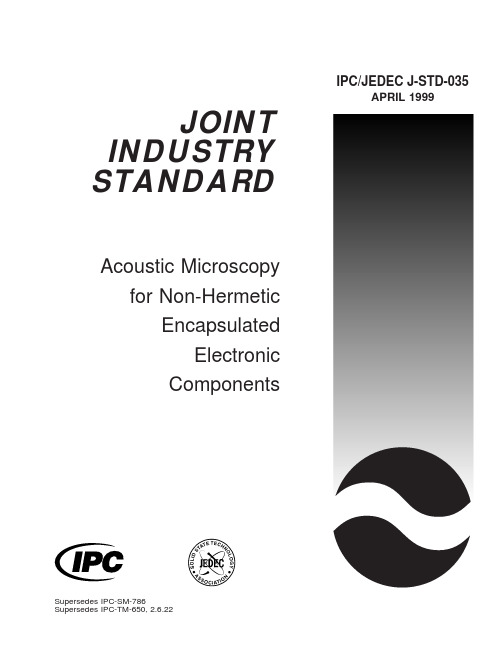
JOINT INDUSTRY STANDARDAcoustic Microscopy for Non-HermeticEncapsulatedElectronicComponents IPC/JEDEC J-STD-035APRIL1999Supersedes IPC-SM-786 Supersedes IPC-TM-650,2.6.22Notice EIA/JEDEC and IPC Standards and Publications are designed to serve thepublic interest through eliminating misunderstandings between manufacturersand purchasers,facilitating interchangeability and improvement of products,and assisting the purchaser in selecting and obtaining with minimum delaythe proper product for his particular need.Existence of such Standards andPublications shall not in any respect preclude any member or nonmember ofEIA/JEDEC or IPC from manufacturing or selling products not conformingto such Standards and Publications,nor shall the existence of such Standardsand Publications preclude their voluntary use by those other than EIA/JEDECand IPC members,whether the standard is to be used either domestically orinternationally.Recommended Standards and Publications are adopted by EIA/JEDEC andIPC without regard to whether their adoption may involve patents on articles,materials,or processes.By such action,EIA/JEDEC and IPC do not assumeany liability to any patent owner,nor do they assume any obligation whateverto parties adopting the Recommended Standard or ers are alsowholly responsible for protecting themselves against all claims of liabilities forpatent infringement.The material in this joint standard was developed by the EIA/JEDEC JC-14.1Committee on Reliability Test Methods for Packaged Devices and the IPCPlastic Chip Carrier Cracking Task Group(B-10a)The J-STD-035supersedes IPC-TM-650,Test Method2.6.22.For Technical Information Contact:Electronic Industries Alliance/ JEDEC(Joint Electron Device Engineering Council)2500Wilson Boulevard Arlington,V A22201Phone(703)907-7560Fax(703)907-7501IPC2215Sanders Road Northbrook,IL60062-6135 Phone(847)509-9700Fax(847)509-9798Please use the Standard Improvement Form shown at the end of thisdocument.©Copyright1999.The Electronic Industries Alliance,Arlington,Virginia,and IPC,Northbrook,Illinois.All rights reserved under both international and Pan-American copyright conventions.Any copying,scanning or other reproduction of these materials without the prior written consent of the copyright holder is strictly prohibited and constitutes infringement under the Copyright Law of the United States.IPC/JEDEC J-STD-035Acoustic Microscopyfor Non-Hermetic EncapsulatedElectronicComponentsA joint standard developed by the EIA/JEDEC JC-14.1Committee on Reliability Test Methods for Packaged Devices and the B-10a Plastic Chip Carrier Cracking Task Group of IPCUsers of this standard are encouraged to participate in the development of future revisions.Contact:EIA/JEDEC Engineering Department 2500Wilson Boulevard Arlington,V A22201 Phone(703)907-7500 Fax(703)907-7501IPC2215Sanders Road Northbrook,IL60062-6135 Phone(847)509-9700Fax(847)509-9798ASSOCIATION CONNECTINGELECTRONICS INDUSTRIESAcknowledgmentMembers of the Joint IPC-EIA/JEDEC Moisture Classification Task Group have worked to develop this document.We would like to thank them for their dedication to this effort.Any Standard involving a complex technology draws material from a vast number of sources.While the principal members of the Joint Moisture Classification Working Group are shown below,it is not possible to include all of those who assisted in the evolution of this Standard.To each of them,the mem-bers of the EIA/JEDEC and IPC extend their gratitude.IPC Packaged Electronic Components Committee ChairmanMartin FreedmanAMP,Inc.IPC Plastic Chip Carrier Cracking Task Group,B-10a ChairmanSteven MartellSonoscan,Inc.EIA/JEDEC JC14.1CommitteeChairmanJack McCullenIntel Corp.EIA/JEDEC JC14ChairmanNick LycoudesMotorolaJoint Working Group MembersCharlie Baker,TIChristopher Brigham,Hi/FnRalph Carbone,Hewlett Packard Co. Don Denton,TIMatt Dotty,AmkorMichele J.DiFranza,The Mitre Corp. Leo Feinstein,Allegro Microsystems Inc.Barry Fernelius,Hewlett Packard Co. Chris Fortunko,National Institute of StandardsRobert J.Gregory,CAE Electronics, Inc.Curtis Grosskopf,IBM Corp.Bill Guthrie,IBM Corp.Phil Johnson,Philips Semiconductors Nick Lycoudes,MotorolaSteven R.Martell,Sonoscan Inc. Jack McCullen,Intel Corp.Tom Moore,TIDavid Nicol,Lucent Technologies Inc.Pramod Patel,Advanced Micro Devices Inc.Ramon R.Reglos,XilinxCorazon Reglos,AdaptecGerald Servais,Delphi Delco Electronics SystemsRichard Shook,Lucent Technologies Inc.E.Lon Smith,Lucent Technologies Inc.Randy Walberg,NationalSemiconductor Corp.Charlie Wu,AdaptecEdward Masami Aoki,HewlettPackard LaboratoriesFonda B.Wu,Raytheon Systems Co.Richard W.Boerdner,EJE ResearchVictor J.Brzozowski,NorthropGrumman ES&SDMacushla Chen,Wus Printed CircuitCo.Ltd.Jeffrey C.Colish,Northrop GrummanCorp.Samuel J.Croce,Litton AeroProducts DivisionDerek D-Andrade,Surface MountTechnology CentreRao B.Dayaneni,Hewlett PackardLaboratoriesRodney Dehne,OEM WorldwideJames F.Maguire,Boeing Defense&Space GroupKim Finch,Boeing Defense&SpaceGroupAlelie Funcell,Xilinx Inc.Constantino J.Gonzalez,ACMEMunir Haq,Advanced Micro DevicesInc.Larry A.Hargreaves,DC.ScientificInc.John T.Hoback,Amoco ChemicalCo.Terence Kern,Axiom Electronics Inc.Connie M.Korth,K-Byte/HibbingManufacturingGabriele Marcantonio,NORTELCharles Martin,Hewlett PackardLaboratoriesRichard W.Max,Alcatel NetworkSystems Inc.Patrick McCluskey,University ofMarylandJames H.Moffitt,Moffitt ConsultingServicesRobert Mulligan,Motorola Inc.James E.Mumby,CibaJohn Northrup,Lockheed MartinCorp.Dominique K.Numakura,LitchfieldPrecision ComponentsNitin B.Parekh,Unisys Corp.Bella Poborets,Lucent TechnologiesInc.D.Elaine Pope,Intel Corp.Ray Prasad,Ray Prasad ConsultancyGroupAlbert Puah,Adaptec Inc.William Sepp,Technic Inc.Ralph W.Taylor,Lockheed MartinCorp.Ed R.Tidwell,DSC CommunicationsCorp.Nick Virmani,Naval Research LabKen Warren,Corlund ElectronicsCorp.Yulia B.Zaks,Lucent TechnologiesInc.IPC/JEDEC J-STD-035April1999 iiTable of Contents1SCOPE (1)2DEFINITIONS (1)2.1A-mode (1)2.2B-mode (1)2.3Back-Side Substrate View Area (1)2.4C-mode (1)2.5Through Transmission Mode (2)2.6Die Attach View Area (2)2.7Die Surface View Area (2)2.8Focal Length(FL) (2)2.9Focus Plane (2)2.10Leadframe(L/F)View Area (2)2.11Reflective Acoustic Microscope (2)2.12Through Transmission Acoustic Microscope (2)2.13Time-of-Flight(TOF) (3)2.14Top-Side Die Attach Substrate View Area (3)3APPARATUS (3)3.1Reflective Acoustic Microscope System (3)3.2Through Transmission AcousticMicroscope System (4)4PROCEDURE (4)4.1Equipment Setup (4)4.2Perform Acoustic Scans..........................................4Appendix A Acoustic Microscopy Defect CheckSheet (6)Appendix B Potential Image Pitfalls (9)Appendix C Some Limitations of AcousticMicroscopy (10)Appendix D Reference Procedure for PresentingApplicable Scanned Data (11)FiguresFigure1Example of A-mode Display (1)Figure2Example of B-mode Display (1)Figure3Example of C-mode Display (2)Figure4Example of Through Transmission Display (2)Figure5Diagram of a Reflective Acoustic MicroscopeSystem (3)Figure6Diagram of a Through Transmission AcousticMicroscope System (3)April1999IPC/JEDEC J-STD-035iiiIPC/JEDEC J-STD-035April1999This Page Intentionally Left BlankivApril1999IPC/JEDEC J-STD-035 Acoustic Microscopy for Non-Hermetic EncapsulatedElectronic Components1SCOPEThis test method defines the procedures for performing acoustic microscopy on non-hermetic encapsulated electronic com-ponents.This method provides users with an acoustic microscopy processflow for detecting defects non-destructively in plastic packages while achieving reproducibility.2DEFINITIONS2.1A-mode Acoustic data collected at the smallest X-Y-Z region defined by the limitations of the given acoustic micro-scope.An A-mode display contains amplitude and phase/polarity information as a function of time offlight at a single point in the X-Y plane.See Figure1-Example of A-mode Display.IPC-035-1 Figure1Example of A-mode Display2.2B-mode Acoustic data collected along an X-Z or Y-Z plane versus depth using a reflective acoustic microscope.A B-mode scan contains amplitude and phase/polarity information as a function of time offlight at each point along the scan line.A B-mode scan furnishes a two-dimensional(cross-sectional)description along a scan line(X or Y).See Figure2-Example of B-mode Display.IPC-035-2 Figure2Example of B-mode Display(bottom half of picture on left)2.3Back-Side Substrate View Area(Refer to Appendix A,Type IV)The interface between the encapsulant and the back of the substrate within the outer edges of the substrate surface.2.4C-mode Acoustic data collected in an X-Y plane at depth(Z)using a reflective acoustic microscope.A C-mode scan contains amplitude and phase/polarity information at each point in the scan plane.A C-mode scan furnishes a two-dimensional(area)image of echoes arising from reflections at a particular depth(Z).See Figure3-Example of C-mode Display.1IPC/JEDEC J-STD-035April1999IPC-035-3 Figure3Example of C-mode Display2.5Through Transmission Mode Acoustic data collected in an X-Y plane throughout the depth(Z)using a through trans-mission acoustic microscope.A Through Transmission mode scan contains only amplitude information at each point in the scan plane.A Through Transmission scan furnishes a two-dimensional(area)image of transmitted ultrasound through the complete thickness/depth(Z)of the sample/component.See Figure4-Example of Through Transmission Display.IPC-035-4 Figure4Example of Through Transmission Display2.6Die Attach View Area(Refer to Appendix A,Type II)The interface between the die and the die attach adhesive and/or the die attach adhesive and the die attach substrate.2.7Die Surface View Area(Refer to Appendix A,Type I)The interface between the encapsulant and the active side of the die.2.8Focal Length(FL)The distance in water at which a transducer’s spot size is at a minimum.2.9Focus Plane The X-Y plane at a depth(Z),which the amplitude of the acoustic signal is maximized.2.10Leadframe(L/F)View Area(Refer to Appendix A,Type V)The imaged area which extends from the outer L/F edges of the package to the L/F‘‘tips’’(wedge bond/stitch bond region of the innermost portion of the L/F.)2.11Reflective Acoustic Microscope An acoustic microscope that uses one transducer as both the pulser and receiver. (This is also known as a pulse/echo system.)See Figure5-Diagram of a Reflective Acoustic Microscope System.2.12Through Transmission Acoustic Microscope An acoustic microscope that transmits ultrasound completely through the sample from a sending transducer to a receiver on the opposite side.See Figure6-Diagram of a Through Transmis-sion Acoustic Microscope System.2April1999IPC/JEDEC J-STD-0353IPC/JEDEC J-STD-035April1999 3.1.6A broad band acoustic transducer with a center frequency in the range of10to200MHz for subsurface imaging.3.2Through Transmission Acoustic Microscope System(see Figure6)comprised of:3.2.1Items3.1.1to3.1.6above3.2.2Ultrasonic pulser(can be a pulser/receiver as in3.1.1)3.2.3Separate receiving transducer or ultrasonic detection system3.3Reference packages or standards,including packages with delamination and packages without delamination,for use during equipment setup.3.4Sample holder for pre-positioning samples.The holder should keep the samples from moving during the scan and maintain planarity.4PROCEDUREThis procedure is generic to all acoustic microscopes.For operational details related to this procedure that apply to a spe-cific model of acoustic microscope,consult the manufacturer’s operational manual.4.1Equipment Setup4.1.1Select the transducer with the highest useable ultrasonic frequency,subject to the limitations imposed by the media thickness and acoustic characteristics,package configuration,and transducer availability,to analyze the interfaces of inter-est.The transducer selected should have a low enough frequency to provide a clear signal from the interface of interest.The transducer should have a high enough frequency to delineate the interface of interest.Note:Through transmission mode may require a lower frequency and/or longer focal length than reflective mode.Through transmission is effective for the initial inspection of components to determine if defects are present.4.1.2Verify setup with the reference packages or standards(see3.3above)and settings that are appropriate for the trans-ducer chosen in4.1.1to ensure that the critical parameters at the interface of interest correlate to the reference standard uti-lized.4.1.3Place units in the sample holder in the coupling medium such that the upper surface of each unit is parallel with the scanning plane of the acoustic transducer.Sweep air bubbles away from the unit surface and from the bottom of the trans-ducer head.4.1.4At afixed distance(Z),align the transducer and/or stage for the maximum reflected amplitude from the top surface of the sample.The transducer must be perpendicular to the sample surface.4.1.5Focus by maximizing the amplitude,in the A-mode display,of the reflection from the interface designated for imag-ing.This is done by adjusting the Z-axis distance between the transducer and the sample.4.2Perform Acoustic Scans4.2.1Inspect the acoustic image(s)for any anomalies,verify that the anomaly is a package defect or an artifact of the imaging process,and record the results.(See Appendix A for an example of a check sheet that may be used.)To determine if an anomaly is a package defect or an artifact of the imaging process it is recommended to analyze the A-mode display at the location of the anomaly.4.2.2Consider potential pitfalls in image interpretation listed in,but not limited to,Appendix B and some of the limita-tions of acoustic microscopy listed in,but not limited to,Appendix C.If necessary,make adjustments to the equipment setup to optimize the results and rescan.4April1999IPC/JEDEC J-STD-035 4.2.3Evaluate the acoustic images using the failure criteria specified in other appropriate documents,such as J-STD-020.4.2.4Record the images and thefinal instrument setup parameters for documentation purposes.An example checklist is shown in Appendix D.5IPC/JEDEC J-STD-035April19996April1999IPC/JEDEC J-STD-035Appendix AAcoustic Microscopy Defect Check Sheet(continued)CIRCUIT SIDE SCANImage File Name/PathDelamination(Type I)Die Circuit Surface/Encapsulant Number Affected:Average%Location:Corner Edge Center (Type II)Die/Die Attach Number Affected:Average%Location:Corner Edge Center (Type III)Encapsulant/Substrate Number Affected:Average%Location:Corner Edge Center (Type V)Interconnect tip Number Affected:Average%Interconnect Number Affected:Max.%Length(Type VI)Intra-Laminate Number Affected:Average%Location:Corner Edge Center Comments:CracksAre cracks present:Yes NoIf yes:Do any cracks intersect:bond wire ball bond wedge bond tab bump tab leadDoes crack extend from leadfinger to any other internal feature:Yes NoDoes crack extend more than two-thirds the distance from any internal feature to the external surfaceof the package:Yes NoAdditional verification required:Yes NoComments:Mold Compound VoidsAre voids present:Yes NoIf yes:Approx.size Location(if multiple voids,use comment section)Do any voids intersect:bond wire ball bond wedge bond tab bump tab lead Additional verification required:Yes NoComments:7IPC/JEDEC J-STD-035April1999Appendix AAcoustic Microscopy Defect Check Sheet(continued)NON-CIRCUIT SIDE SCANImage File Name/PathDelamination(Type IV)Encapsulant/Substrate Number Affected:Average%Location:Corner Edge Center (Type II)Substrate/Die Attach Number Affected:Average%Location:Corner Edge Center (Type V)Interconnect Number Affected:Max.%LengthLocation:Corner Edge Center (Type VI)Intra-Laminate Number Affected:Average%Location:Corner Edge Center (Type VII)Heat Spreader Number Affected:Average%Location:Corner Edge Center Additional verification required:Yes NoComments:CracksAre cracks present:Yes NoIf yes:Does crack extend more than two-thirds the distance from any internal feature to the external surfaceof the package:Yes NoAdditional verification required:Yes NoComments:Mold Compound VoidsAre voids present:Yes NoIf yes:Approx.size Location(if multiple voids,use comment section)Additional verification required:Yes NoComments:8Appendix BPotential Image PitfallsOBSERV ATIONS CAUSES/COMMENTSUnexplained loss of front surface signal Gain setting too lowSymbolization on package surfaceEjector pin knockoutsPin1and other mold marksDust,air bubbles,fingerprints,residueScratches,scribe marks,pencil marksCambered package edgeUnexplained loss of subsurface signal Gain setting too lowTransducer frequency too highAcoustically absorbent(rubbery)fillerLarge mold compound voidsPorosity/high concentration of small voidsAngled cracks in package‘‘Dark line boundary’’(phase cancellation)Burned molding compound(ESD/EOS damage)False or spotty indication of delamination Low acoustic impedance coating(polyimide,gel)Focus errorIncorrect delamination gate setupMultilayer interference effectsFalse indication of adhesion Gain set too high(saturation)Incorrect delamination gate setupFocus errorOverlap of front surface and subsurface echoes(transducerfrequency too low)Fluidfilling delamination areasApparent voiding around die edge Reflection from wire loopsIncorrect setting of void gateGraded intensity Die tilt or lead frame deformation Sample tiltApril1999IPC/JEDEC J-STD-0359Appendix CSome Limitations of Acoustic MicroscopyAcoustic microscopy is an analytical technique that provides a non-destructive method for examining plastic encapsulated components for the existence of delaminations,cracks,and voids.This technique has limitations that include the following: LIMITATION REASONAcoustic microscopy has difficulty infinding small defects if the package is too thick.The ultrasonic signal becomes more attenuated as a function of two factors:the depth into the package and the transducer fre-quency.The greater the depth,the greater the attenuation.Simi-larly,the higher the transducer frequency,the greater the attenu-ation as a function of depth.There are limitations on the Z-axis(axial)resolu-tion.This is a function of the transducer frequency.The higher the transducer frequency,the better the resolution.However,the higher frequency signal becomes attenuated more quickly as a function of depth.There are limitations on the X-Y(lateral)resolu-tion.The X-Y(lateral)resolution is a function of a number of differ-ent variables including:•Transducer characteristics,including frequency,element diam-eter,and focal length•Absorption and scattering of acoustic waves as a function of the sample material•Electromechanical properties of the X-Y stageIrregularly shaped packages are difficult to analyze.The technique requires some kind offlat reference surface.Typically,the upper surface of the package or the die surfacecan be used as references.In some packages,cambered packageedges can cause difficulty in analyzing defects near the edgesand below their surfaces.Edge Effect The edges cause difficulty in analyzing defects near the edge ofany internal features.IPC/JEDEC J-STD-035April1999 10April1999IPC/JEDEC J-STD-035Appendix DReference Procedure for Presenting Applicable Scanned DataMost of the settings described may be captured as a default for the particular supplier/product with specific changes recorded on a sample or lot basis.Setup Configuration(Digital Setup File Name and Contents)Calibration Procedure and Calibration/Reference Standards usedTransducerManufacturerModelCenter frequencySerial numberElement diameterFocal length in waterScan SetupScan area(X-Y dimensions)Scan step sizeHorizontalVerticalDisplayed resolutionHorizontalVerticalScan speedPulser/Receiver SettingsGainBandwidthPulseEnergyRepetition rateReceiver attenuationDampingFilterEcho amplitudePulse Analyzer SettingsFront surface gate delay relative to trigger pulseSubsurface gate(if used)High passfilterDetection threshold for positive oscillation,negative oscillationA/D settingsSampling rateOffset settingPer Sample SettingsSample orientation(top or bottom(flipped)view and location of pin1or some other distinguishing characteristic) Focus(point,depth,interface)Reference planeNon-default parametersSample identification information to uniquely distinguish it from others in the same group11IPC/JEDEC J-STD-035April1999Appendix DReference Procedure for Presenting Applicable Scanned Data(continued) Reference Procedure for Presenting Scanned DataImagefile types and namesGray scale and color image legend definitionsSignificance of colorsIndications or definition of delaminationImage dimensionsDepth scale of TOFDeviation from true aspect ratioImage type:A-mode,B-mode,C-mode,TOF,Through TransmissionA-mode waveforms should be provided for points of interest,such as delaminated areas.In addition,an A-mode image should be provided for a bonded area as a control.12Standard Improvement FormIPC/JEDEC J-STD-035The purpose of this form is to provide the Technical Committee of IPC with input from the industry regarding usage of the subject standard.Individuals or companies are invited to submit comments to IPC.All comments will be collected and dispersed to the appropriate committee(s).If you can provide input,please complete this form and return to:IPC2215Sanders RoadNorthbrook,IL 60062-6135Fax 847509.97981.I recommend changes to the following:Requirement,paragraph number Test Method number,paragraph numberThe referenced paragraph number has proven to be:Unclear Too RigidInErrorOther2.Recommendations forcorrection:3.Other suggestions for document improvement:Submitted by:Name Telephone Company E-mailAddress City/State/ZipDate ASSOCIATION CONNECTING ELECTRONICS INDUSTRIESASSOCIATION CONNECTINGELECTRONICS INDUSTRIESISBN#1-580982-28-X2215 Sanders Road, Northbrook, IL 60062-6135Tel. 847.509.9700 Fax 847.509.9798。
Realize Your Product Promise in Automotive

Realize Your Product Promise tmin AutomotiveDriven to InnovateMore than a century after the first car debuted, the global automotive industry is undergoing a period of dramatic transformation. As consumers and regulators demand more energy-efficient ve -hicles that minimize environmental impact, few technologies are exempt from scrutiny.Automotive and transportation pioneers are looking to replace traditional internal combustion engines with fuel cells, batteries, opposed-piston technologies and electric traction motors — in an incredibly short time frame, and often from scratch. Novel composite materials impart strength while shaving weight, making it possible to reduce fuel consumption. Optimizing complex aerodynamics improves fuel economy even further. Smart electronics are adding new levels of automation, control, safety and comfort. Despite these technological leaps, consumers are demanding rock-bottom prices.From cars and motorcycles to commercial trucks and construction equipment to rail vehicles, the worldwide transportation industry views innova-tion as a critical competency. Engineering simu-lation — in which R&D teams design and validate products in a virtual environment — provides pacesetters with a powerful platform for creating innovations that are truly category-changing.As the demand for fuel-efficient, environmentally responsible vehicles intensifies, the global auto industry is transforming itself. Is yourbusiness ready to deliver category-changing innovations?ANSYS: Accelerating New Products and ProcessesAdvanced engineering simulation software from ANSYS supports development of revolutionary new products and processes at the heart of this transformation — and we stand ready to help your business emerge as an innovation leader.By driving time and costs out of the development cycle, our solutions help you bring innovations to market quickly, so you can gain a significant “ANSYS software is vital to our business. It enables Red BullRacing to reduce lead times rapidly, getting solutions to thecircuit quicker and making us more competitive race by race.We try to get as much performance out of every small part ofour car as possible, and ANSYS is essential in achieving that.”Steve NeveyBusiness DevelopmentRed Bull Racingedge on the competition. And because you applyANSYS tools in a low-risk, virtual designenvironment where anything is possible — evenwithin targeted time frames — your engineeringteams are more likely to push boundaries andcreate outside-the-box innovations. At the sametime, your business can benefit from a highdegree of confidence that products will performas predicted in the physical world, enabling youto realize your product promise to customersand other stakeholders.Electronic throttlecontrols offer benefits inautomotive applicationssuch as stability control,automatic braking, cruiseand traction control, andpre-crash systems. KSRInternational designsinductance sensors thatare part of such systems.The company initiallyused trial-and-errormethods to developcustom inductancesensors, a process thattook approximately threemonths. Using ANSYStools to evaluate soft-ware prototypes — ratherthan building and testinghardware — has allowedthe engineering team toreduce development timeto only two weeks.Steering Your Business toward SuccessBeing first to market is synonymous with success. Automotive companies that lead in anticipating and meeting market needs will emerge as winners, while others struggle to catch up. But you cannot afford to sacrifice product confidence for speed. In an industry characterized by well-known product recalls, your engineering team must combine speed with a strong commitment to deliver on your product promise.Whether your organization is in an emerging or a mature market, an OEM or a supplier, ANSYS software provides the proven capabilities to help meet the challenges at hand. Our tools have already supported the rapid launch of countless innovative automotive products and processes.ANSYS: Kick-Starting Innovation in Diverse ApplicationsConsumer, regulatory and market pressures exist in diverse segments ranging from passenger cars to Formula 1® race cars, construction vehicles, commercial trucks, tractors, motorcycles and locomotives.Auto developers use ANSYS solutions to develop engines that burn fuels more efficiently, rely on alternative energy sources or incorporate next-generation emissions control devices. By delivering multiphysics capabilities in a single platform, we make it easier for your engineeringIn a range of applications, ANSYS helps automotive companiesspeed ahead of competitors with rapid product and process design.team to examine the complex issues surrounding engine performance and outputs. Our tools have been central in advancing industry “lightweighting” initiatives that focus on the use of novel composite materials to optimize a variety of components and reduce overall fuel consumption.Innovators apply ANSYS to highly specialized problems such as brake squeal in passenger cars and noise, vibration and harshness. By illumi-nating the causal factors behind complex physical Bühler Motor used ANSYS tools to develop mecha-tronic DC drives and gear motors, systematically analyzing and optimizing different components to reach the highest possible optimization level while also meeting safety standards.General Motors, ANSYS and the University of South Carolina are working together to develop CAE design tools that accurately represent multiphysics phenomena across a wide range of scales for cells and packs, funded by an award from the U.S. Department of Energy’s National Renewable Energy Laboratory. The project will contribute to making HEV/EV batteries more affordable, better performing and longer lasting.“The ease of using ANSYS simulation tools has helped to transform our organization from a test-centric culture to an analysis-centric culture” Bob Tickel Director of Structural and Dynamic Analysis Cummins, Inc.“When you design innovation, you can’t design in just one area — you have to couple everything at the early stage of the project. And we found that ANSYS enables us to do that.”Pierre Solomalala Power Electronics R&D EngineerAlstom Transport phenomena, our solutions help engineering teams increase product reliability and minimize costly manufacturer recalls. Whatever the pressing competitive issue — from body to transmission to interior — ANSYS delivers broad simulation capabilities and deep automotive expertise to help your business emerge as the next industrysuccess story.Road-tested, Industry-Leading technologiesAn early adopter of simulation technology, the automotive industry continues to look for ways to bring simulation as close to reality as possible. The engineering tool you choose should be reliable and accurate to reduce dependence on physical prototyping. The ANSYS suite goes far beyond, facilitating communication across vari -ous engineering disciplines. For the automotive industry, this is a key initiative for expediting the design cycle and reducing product recalls.Only ANSYS offers a single, integrated technology platform built for this level of global collabora-tion. The ANSYS Workbench™ platform delivers unprecedented ease of use while integrating industry-leading structural, thermal, electromag -netics and fluids physics needed to solve compli -cated problems at both component and systems levels. To address the collaboration needs of all global supply chain participants, we offer engineering knowledge management capabilities that can be used across the enterprise.ANSYS supports HPC environments required to manage large-scale simulations created by automotive engineers every day. Parallel processing capabilities combined with HPC tools, such as graphics processing units, enable you to speed and streamline even the most complex and numerically large simulations.Proven solutions from ANSYS deliver the multiphysics and system-level perspective needed to drive innovation across the entire vehicle design cycle.To better understand fuel injection technology, Delphi Automotive Systems ran simulations using a number of ANSYS fluid dynamics models, including discrete phase, drag, breakup, collision and coalescence, wall-impingement,and evaporation. C o u r t e s y C u m m i n s , I n c .ANSYS: Addressing Challenges from Bumper to BumperFrom aerodynamics and thermal management to engine design, durability and NVH, our products and application knowledge can help you understand product performance long before a prototype is ever built.We have worked aggressively to assemble our technology suite so that you can address the wide range of complexities and transform your organization into an innovator. Our CFD products include advanced turbulence models to help optimize aerodynamic performance of vehicles. Our structural solutions incorporate nonlinear, fatigue and rigid-body dynamics tools to support development of composites and other Almost half the value of next-generation automobiles will come from onboard electronics and electromechanical components. These devices must survive in harsh operating conditions, such as significant swings in humidity levels. Product developers can apply our tools to incorporate effects such as Joule heating phenomena in package or board substrates. “By adopting a comprehensive approach for implementing FEA across the worldwide organization, Delphi has incorporated an extremely powerful technology into the product development process. The initiative to focus on upfront analysis in particular has resulted in outstanding value.”Fereydoon Dadkhah Senior Engineer Delphi Electronics & Safety SystemsThe Engine NVH Analysis Section at Ford Motor Company used ANSYS software to conduct design-of-experiments studies, gaining insight into modal and vibra-tional response, radiated noise, and crank/block dynamic interactions.The automotive global supply chain is crowded with OEMs and multi-tier suppliers. ANSYS provides tools to address their varied design issues — and to manage the huge amount of data that simulation generates. The result: fewer surprises when components and systems are assembled into a finished vehicle.new materials. You can tightly couple a number of products to assess traditional engine tech-nologies as well as fuel cells, hybrid–electric engines and other emerging technologies. Passenger cars are on the verge of becoming more electric than mechanical in nature. We have the clear leadership in electromagnetics simula-tion to support revolutionary developments — as well as the multiphysics capabilities to optimize component interaction with other systems.Automotive engineers consider complex real-world physics interactions and make value-added design trade-offs. Every day, and in every automotive segment, they use industry-leading multiphysics tools from ANSYS to position theircompanies for innovation leadership. Courtesy Timoney Technology.。
全面版车辆挂靠协定英文版

全面版车辆挂靠协定英文版Comprehensive Vehicle Attachment AgreementThis document serves as a comprehensive agreement between the parties involved in the vehicle attachment arrangement. The purpose of this agreement is to outline the terms and conditions under which the vehicle will be attached to the designated entity.Parties InvolvedThe parties involved in this agreement are referred to as the "Owner" and the "Entity". The Owner is the individual or entity that owns the vehicle, while the Entity is the organization to which the vehicle will be attached.Vehicle AttachmentThe Owner agrees to attach the vehicle to the Entity for a specified period of time. During this period, the vehicle will be used for the designated purposes outlined in this agreement.Responsibilities of the Owner1. The Owner is responsible for maintaining the vehicle in good working condition throughout the attachment period.2. The Owner must provide all necessary documents and permissions for the attachment of the vehicle to the Entity.3. The Owner must comply with all laws and regulations related to the operation of the vehicle.Responsibilities of the Entity1. The Entity is responsible for using the vehicle for the designated purposes outlined in this agreement.2. The Entity must ensure the proper care and maintenance of the vehicle during the attachment period.3. The Entity must comply with all laws and regulations related to the use of the vehicle.Duration of AttachmentThe vehicle attachment will begin on [start date] and end on [end date]. Any changes to the duration of attachment must be agreed upon by both parties in writing.Termination of AgreementEither party may terminate this agreement by providing written notice to the other party. The agreement will be considered terminated upon receipt of the written notice.Governing LawThis agreement shall be governed by the laws of [jurisdiction]. Any disputes arising out of this agreement shall be resolved through arbitration in accordance with the laws of [jurisdiction].SignaturesBoth parties agree to the terms and conditions outlined in this agreement by signing below:Owner's Signature: ______________________Entity's Signature: ______________________This agreement is effective as of the date first written above.。
IEC60335-2-34

Further information on IEC publications
The technical content of IEC publications is kept under constant review by the IEC, thus ensuring that the content reflects current technology. Information relating to this publication, including its validity, is available in the IEC Catalogue of publications (see below) in addition to new editions, amendments and corrigenda. Information on the subjects under consideration and work in progress undertaken by the technical committee which has prepared this publication, as well as the list of publications issued, is also available from the following: • • IEC Web Site (www.iec.ch) Catalogue of IEC publications The on-line catalogue on the IEC web site (http://www.iec.ch/searchpub/cur_fut.htm) enables you to search by a variety of criteria including text searches, technical committees and date of publication. On-line information is also available on recently issued publications, withdrawn and replaced publications, as well as corrigenda. • IEC Just Published This summary of recently issued publications (http://www.iec.ch/online_news/ justpub/jp_entry.htm) is also available by email. Please contact the Customer Service Centre (see below) for further information. • Customer Service Centre If you have any questions regarding this publication or need further assistance, please contact the Customer Service Centre: Email: custserv@iec.ch Tel: +41 22 919 02 11 Fax: +41 22 919 03 00
美国电气制造商协会(NEMA)电机应用指导

© Copyright 2001 by the National Electrical Manufacturers Association. All rights including translation into other languages, reserved under the Universal Copyright Convention, the Berne Convention for the Protection of Literary and Artistic Works, and the International and Pan American Copyright Conventions.
NOTICE AND DISCLAIMER
The information in this publication was considered technically sound by the consensus of persons engaged in the development and approval of the document at the time it was developed. Consensus does not necessarily mean that there is unanimous agreement among every person participating in the development of this document.
NEMA standards and guideline publications, of which the document contained herein is one, are developed through a voluntary consensus standards development process. This process brings together volunteers and/or seeks out the views of persons who have an interest in the topic covered by this publication. While NEMA administers the process and establishes rules to promote fairness in the development of consensus, it does not write the document and it does not independently test, evaluate, or verify the accuracy or completeness of any information or the soundness of any judgments contained in its standards and guideline publications. NEMA disclaims liability for any personal injury, property, or other damages of any nature whatsoever, whether special, indirect, consequential, or compensatory, directly or indirectly resulting from the publication, use of, application, or reliance on this document. NEMA disclaims and makes no guaranty or warranty, express or implied, as to the accuracy or completeness of any information published herein, and disclaims and makes no warranty that the information in this document will fulfill any of your particular purposes or needs. NEMA does not undertake to guarantee the performance of any individual manufacturer or seller’s products or services by virtue of this standard or guide. In publishing and making this document available, NEMA is not undertaking to render professional or other services for or on behalf of any person or entity, nor is NEMA undertaking to perform any duty owed by any person or entity to someone else. Anyone using this document should rely on his or her own independent judgment or, as appropriate, seek the advice of a competent professional in determining the exercise of reasonable care in any given circumstances. Information and other standards on the topic covered by this publication may be available from other sources, which the user may wish to consult for additional views or information not covered by this publication. NEMA has no power, nor does it undertake to police or enforce compliance with the contents of this document. NEMA does not certify, test, or inspect products, designs, or installations for safety or health purposes. Any certification or other statement of compliance with any health or safety–related information in this document shall not be attributable to NEMA and is solely the responsibility of the certifier or maker of NTS
ABB SACE Emax 2 空气电路断路器产品说明说明书

ABB’s Low Voltage Products Division is proud to present SACE Emax 2,its next generation of air circuit-breakers. Over 70 years of cutting edge research and experience inthe electromechanical industry has allowed ABB SACE to create this new benchmark of air circuit-breakers. Not only does Emax 2 meet or exceed the standard performances and functions that the market demands from an air circuit-breaker, but it has evolved into a true power manager. Emax 2 and its Ekip brand of trip units and accessories contain the perfect blend of control, connectivity, performance, ease of use and safety to efficiently satisfy any application or need.− A patented, Power Controller moni-tors and controls power usage toreduce management costs.−Extensive, direct communication abilities simplify network integrationand eliminate the need for costly and difficult conversion components.−Optimal frame organization and ac-curate design provide the ability forhigh performance switchboards andswitchgear with a reduction of bothmaterials and space required.−Busbar friendly, modifiable terminals eliminate the need to bend and ex-tend bus bar and provide quick, easy installation.−Large, color touchscreen interfaces allow for clear navigation, creating asimple and quick way to find informa-tion or make adjustments.− A wide variety of accessories have been designed to simplify use orinstallation and to increase safety.−The Emax 2 contains several features that are either new to the market orsuperior to existing solutions, mak-ing it the best choice for low voltage network needs.ControlThe Power Controller function of Emax 2uses a patented algorithm to determinethe average absorbed power over aperiod of time and then controls a loadlist to maintain the maximum power limitspecified by the user. The elimination ofinstantaneous based measurements andability to synchronize with utility mea-surement devices creates an efficientenvironment that saves on electricitybills without the need for additionalmonitoring systems.The Ekip Link system and Ekip ControlPanel enable local monitoring of circuit-breakers and switchgear functions in anindividual switchboard. They require noprogramming and are available for eventhe most basic Emax 2 trip unit, provi-ding an economic way for a small plantto increase monitoring capabilities or alarge plant to simplify local supervisionand maintenance.A Network Analyzer feature is able onEmax 2 to analyze the quality of powerin real time, with extreme precision inaccordance with EN 50160 and IEC6100-4 30. As a result, it is possibleto identify the causes of an increase ofpower lost or a reduction of the workinglife of cables and capacitors without ha-ving to install costly, external instrumen-tation. With Emax 2’s Network Analyzer,malfunctions can be prevented andinstallation efficiency and the workinglife of appliances can be increased.The Ekip Synchrocheck module enablesthe control of the synchronism conditionfor placing two lines in parallel beforeenabling circuit breaker closing.The ability of the Emax 2 to provide thisfeature as a module eliminates the needfor the purchase and installation of inde-pendent monitoring systems.Emax 2 offers Generator versions of itsEkip Touch and Ekip Hi-touch trip units.These trip units include all the functionsof true generator protection switchgearwithout the need for external relays ordevices, wiring or inspections. The Gversion offers a safe control solutionthat is immediately ready for use.ConnectivityEvery Emax 2 can be equipped with multiple cartridge-type communication modules at any time. The modules allow the circuit breakers to be directly integrated into automation and ener-gy management systems through the seven most popular global protocols; including IEC 61850 for the creation of Smart Grid Networks. All functions can be accessed via the internet, in comple-te safety, using the Ekip Link switchgear monitoring system.Not only can the rear terminals of Emax 2 be field rotated from horizontal to vertical, but they have been specifically designed to fit the most common bus configurations. Each terminal has been created to the standard width of bus bar for that amperage and is equipped with one, two or three terminal stabs for easy connection of one to four bus runs. The terminal technology provides the oppor-tunity for easy connection and installati-on with less bus bar stock required.The Ekip Supply Module can be con-nected to any voltage in AC or DC to internally supply auxiliary power for the trip units and terminal box modules consecutively. The need for any external power supply converter elsewhere in the cabinet is eliminated, saving both space and cost.The neutral position on Emax 2 can be modified from left to right to provide ultimate flexibility. In addition, the E6.2 is available with neutral conductor sizes of 50% or 100% to allow for the correct sizing of bus bar and an opportunity to reduce construction costs. PerformanceEmax 2 uses four frame sizes, each only as wide as the amperage need requires, so that designers can optimize their space and material. The breaker design and quality materials allow for a small size while maintaining the high perfor-mances required by the most deman-ding conditions.The family of Emax 2 contains:−E1.2, 1600A with a 440V Icu of 66kA and Icw 1s of 50kA in a 210mmwidth.−E2.2, 2500A with a 440V Icu of100kA and Icw 1s of 85kA in a276mm width.−E4.2, 4000A with a 440V Icu of150kA and Icw 1s of 100kA in a384mm width.−E6.2, 6300A with a 440V Icu of200kA and Icw 1s of 120kA in a762mm width.Emax 2 contains new generationRogowski sensors that allow the mostprecise measurement on the market.The tolerance to 1% of the actual valueof current, 0.5% of voltage and 2% ofpower and energies guarantee precisionand enable the circuit-breaker to act asa measurement device in switchgear.Measurements can be read directly onthe wide trip unit display so additionaldevices can be eliminated.The Ekip Fan Module continuouslymonitors the internal temperature at thefixed part and activates cooling fans ifrequired. This allows for the ability ofincreased current-carrying capacity inswitchgear.Ease of use and safetyEmax 2 is the first circuit-breaker tooffer large, color touch screen displays.They provide clear, easy navigation forquick access to information and adjust-ment capability that is invaluable in theevent of a fault or emergency.The trip units are capable of ten langu-ages, reducing the need for extensivetraining. In addition, they can be readand used directly, without the need forexpensive HMI units.If desired, they can also be program-med and consulted from a tablet, smartphone or PC via the Ekip Connectapplication.Removal of the main Emax 2 cover al-lows access to the accessory mountingarea only, not the operating mechanismor other components.This protects both maintenance person-nel and the breaker itself from unwanteddamage. In addition, the key lock ac-cessory is mounted inside the acces-sory area and allows for the breakerto remain locked, avoiding unwantedoperation during maintenance.Dedicated guide rails simplify movementand allow correct, locked and clearlyidentifiable positioning. The rails extendoutside the fixed part so that the mobilepart can be easily inserted. In addition,shutters on the fixed part can be lockedfrom the front, without access throughthe inside of the fixed part. These fea-tures allow for easy and safe installationand maintenance.Implementation of breaker settings issimplified with the aid of ABB’s DOCsoftware and Ekip Connect interface.Curves and settings can be determi-ned and saved using the DOC softwareand the Ekip Connect program canopen and read the DOC file, eliminatingthe need to retype the settings intothe breaker or software program andallowing for easy, error free implemen-tation.Emax 2 contains push in terminal boxtechnology, making wiring easy andtooling-free. This feature ensures imme-diate, safe wiring. In addition, Emax 2terminal boxes and wiring set ups arecommon across the line and its tripunits are field interchangeable, creatingflexibility and the potential for easy,rapid upgrades without the added costof a service technician.ABB SACEA division of ABB S.p.A.L.V. BreakersVia Baioni, 3524123 Bergamo - ItalyPhone: +39 035 395.111Fax: +39 035 395.306-433The data and illustrations are not binding.We reserve the right to make changes in the courseof technical development of the product.Copyright 2012 ABB. All rights reserved.1SDC225R21。
- 1、下载文档前请自行甄别文档内容的完整性,平台不提供额外的编辑、内容补充、找答案等附加服务。
- 2、"仅部分预览"的文档,不可在线预览部分如存在完整性等问题,可反馈申请退款(可完整预览的文档不适用该条件!)。
- 3、如文档侵犯您的权益,请联系客服反馈,我们会尽快为您处理(人工客服工作时间:9:00-18:30)。
33rd International Symposium on Automation and Robotics in Construction (ISARC 2016)Interoperability with IFC in the automated rebar fabricationMaciel, Alex R. a and Corrêa, Fabiano R.bEscola Politécnica, University of Sao Paulo, Brazil E-mail: a alex_roda@usp.br , b fabiano.correa@usp.br Abstract – Some problems of efficiency in the cut and bent rebar supply chain is related to stakeholder’s interaction and the flow of information between designers, constructors and rebar fabricator. In the actual process, distinctive standards are used for exchange of information between design and fabrication. The BVBS format represents a standard widely used for automated cut and bent rebar production while the Industry Foundation Classes (IFC) aims to become the standard for exchange in the AEC industry with the use of Building Information Modeling (BIM). This study aims to explore the use of IFC schema to enable an effective integration of the rebar fabrication process with the BIM workflow, improving data exchange and reducing the need for manual intervention. Initially, the requirements for exchanging reinforcement data laid down in BVBS standard are reviewed. Key requirements to a digital interface are parsed across IFC schema specification in order to ascertain how this information are mapped on IFC. The current way for geometric representation of reinforcing bars, used by some structural BIM tools to export IFC files, is reviewed, in addition with new entities release in IFC4. Some recommendations are provided for improving the interoperability efficiency. Keywords – BIM; IFC; Reinforcement bar; Automated bending machine; In the Brazilian cut & bent rebar supply chain, both the design and rebar's detailing activities are performed by the engineering firm and delivered to the constructor or General Contractor (GC) [2]. This configuration features a high dependence among stakeholder's, particularly for the fabricator [1] that carries out the reckoning, produces and deliver the rebar goods to construction site based on the drawings and order form handed in by GC. It is crucial that they received accurate information [2]. The main source of problems in the Brazilian case [4] is related to failures on information flow and communication between the agents involved, especially due to: a) imprecise order and b) poor quality of structural design. The use of Building Information Modeling (BIM) contributes to improving the quality and integrity of the process. The production of detailing drawings [5] directly from 3D coordinated reinforcement models (with bidirectional associativity) can reduce errors and considerably enhance its consistency. To that end, it is necessary to establish how the information could be exchanged from BIM design environment and the standard accepted by the automated process of cut and bend rebar. Currently, the main among the available formats used in cut and bent rebar for Cast-in-place (CIP) is the BVBS standard, allowing a digital data exchange with CAM controlled bending machine or Production Planning and Scheduling (PPS) software. However, it is limited to geometry and some references between detailing and placing rebar drawings, and do not allow the addition of information under the contractor's responsibility relating to the order and delivery date. Another point to be considered is the feasibility of this interface, which demands synergy between the engineering firm and fabricator. Due to the supply chain configuration, such as Brazilian case, these agents does not collaborate directly. This link is effected through the general contractor and he acts as an intermediate. The importance of improvement of existing interfaces or development of new standards is highlighted by [5] in order to reduce the need for manual intervention by the1IntroductionSeveral authors [1][2][3][4] have studied the interaction between agents involved in the supply chain of reinforcement bars. Although some activities, such as raw material supply, design of required reinforcement and on-site assembly, have a clear actor designated to that role, other activities such as detailing, reckoning and fabrication can be performed by different actors depending of particular supply chain configuration [1].Building Information Modeling (BIM)fabricator. However, it must also consider interfaces that allow the reuse of information created along the design, detailing, planning and procurement phases and enables the collaboration between all stakeholders. Nowadays, the improvement of existing standards maintaining compatibility with existing cut and bent reinforcement industrial plants can be considered a suitable choice to be held alongside the development of new standards. For being a consolidated and non-proprietary format for information exchange in the AEC industry, the use of the Industry Foundation Classes (IFC) appears as a good option alongside rebar supply chain. In this study we analyzed the requirements for exchanging reinforcement data laid down in BVBS standard in order to ascertain how this information are mapped on IFC schema. There is a particular interest in the geometric representation of reinforcing bars, and we provide a comparison of forms present in some structural BIM tools to export IFC files, in addition with the reviewed new entities released in IFC4.proprietary while others are created jointly by the cutting and bending rebar supply chain stakeholders. Amid the available formats the BVBS standard represent the main used on automation of cut and bent rebar manufacture for Cast-in-Place industry. ProgressXML and Unitechnik standards are widely used in precast industry, generally for production of precast wall panels and floor slab. Some BIM authoring tools have native support for these standards, while others require a third-party plugin to accomplish the design-production digital interface.3BVBS interface2Design-production digital interfaceAlthough the CAD-CAM integration have been in use for several years, the majority of standards and file formats have been developed considering a CAD context focused on bending patterns based on 2D drawings Error! Reference source not found.. This solution is effective especially when both detailing and production are under fabricator's control as in the United States. Otherwise, it requires a smooth communication among the players. Table 1. List of some standard files formats used for digital interface Name BVBS ProgressXML Unitechnik 7.0 Unitechnik 6.1 Rebar Data Exchange Developer BundesVereinigung der BauSoftwarehäuser E.V. Progress Maschinen & Automation AG. Unitechnik Systems GmbH Unitechnik Systems GmbH Applied Systems Associates, Inc. (aSa) File format .abs .pxml .uxml .cam .rdxThe BundesVereinigung der BauSoftwarehäuser standard (BVBS) [6] was developed in consensus by bending machine factories, construction software companies, reinforcement bending works, steel producers and academic institutions to assist the exchange of information between rebar detailing software and CNC controlled bending machines or PPS software without manual intervention. The BVBS specification features a data structure from the designer's perspective regardless of the fabrication machine which will be used and may also be understandable without authoring CAD/BIM tool. The reinforcement data are exchanged through a ASCII encoded text file and, as other CAD-CAM formats, BVBS is focused on 2D drawings. These files are composed by a data string divided into blocks, and preceded by a recognition code used to set the shape type group, which can be: two-dimensional rebar (BF2D), three-dimensional rebar (BF3D), spiral links (BFWE), mesh (BFMA) or lattice girders (BFGT). The recognition code also enables the machine to check if it will be able to produce the specified shape. The blocks in the file are arranged in the following order: 1. 2. 3. 4. 5. 6. Header block (H): provides data about identification and characteristics of the bar; Geometry block (G): describes the rebar’s shape bending geometry; Chair mesh block (A): defines the positions of the chair mesh in relation to bars. Bar block (X/Y): used only to mesh for define a diameter, bar origins and length; Private block: used for project or other internal data; Checksum block (C): for a checksum value.There is a variety of standards and files formats on the market, which allows the transcription of the information contained in the reinforcement detailing design in a digital format, as shown in Table 1. Some formats areBesides being a standard widely used in rebar's Castin-Place industry, the BVBS choice was held because it provides the data required by CNC controlled bending machine and can be used either directly at machine via USB or via barcode as a mass production workflow, via PPS software.33rd International Symposium on Automation and Robotics in Construction (ISARC 2016)Although this standard encompasses a wide variety of reinforcements types like spiral links, standardized meshes or engineered meshes, this article focused only on 2D and 3D reinforcement bars, and in the following sections the header and geometric blocks will be explored in more details.3.2Geometric block requirements3.1Header block requirementsThe requirement of the BVBS header block can be split essentially into three groups of information containing: Identification and document reference: project number (j), drawing number (r) and revision number index (i); Material and rebar properties: steel grade (g), bar diameter (d) and bending diameter (s); Quantity Sets: bar length (l), item quantity (n), weight per bar item (e);The coordinate system adopted by BVBS to describe the reinforcement bar geometry is set according to the shape group. While the BF2D (2D rebar) uses polar coordinate, the BF3D (3D rebar) is described in Cartesian coordinates. The measuring of shape dimensions is based on external length, similarly to the way predicted by some detailing standards as American ACI 315 [7], British BS 8666 [8] or European ISO 3766 [9]. BF2D geometry is described by the leg length (l) and subsequently by angle of the following bend (w). Each bend is determined by the bending diameter indicated in the header block and remains unique for all transitions. In case where distinctive bending diameters are needed, the radius of the bent element (r) must be set on the geometric block. For defining the BF3D geometry the coordinates of the bar's vertex (X,Y,Z) shall be provided. Figure 1 illustrates the BVBS specification for a twodimensional reinforcement bar.Figure 1. Example of a two-dimensional reinforcement bar (BF2D) according to BVBS specification [6]4Interoperability with IFCSince 2013, the Industry Foundation Classes (IFC) is a ISO standard (ISO 16739:2013) proposed by buildingSMART, and currently is in its IFC4 Add. 1 [10] version. It is a data schema that encodes information related to the entire lifecycle of a building. In its data architecture, there is a layer of data with many different discipline domains including the Structural Elements Domain, where most of the entities necessary to the workflow described here are modelled. From the 17 entities included in structural elements domain, 8 are new entities in IFC4, and other 6 were changed following the difference in conceptual modelling proposed by this new version of IFC. Itappears to be advocating the use of object types for attribute specifications instead of using the very instance of the object entity, which is a positive change. The reinforcement of a concrete structural element can be defined in multiple ways when relied upon the production and assembly hierarchy [11] [12]: a) individual bars; b) a set of identical bars distributed on a row pattern (e.g. stirrup) or a group of rebar with same function; or c) a rebar cage. The way how the reinforcement will be represented in the IFC schema also depend on the way they were defined. Information related to rebar's geometry and properties are defined at object-type level by means of IfcReinforcingBarType entity. Through the mapped representation associated with a single or multipleBuilding Information Modeling (BIM)IfcMappedItem, individual rebars or sets of same rebars can be represented in the object-level occurrence as shown in Figure 2 . The IfcReinforcingBar (attributes changed in IFC4) and IfcReinforcingBarType (new in IFC4) entities are the central objects for the discussion in the following sections that presents how the information regarding the header and geometry blocks of BVBS could be represented inside the IFC specification.drawings be referenced in the IFC through the IfcRelAssociatesDocuments objectified relationship. This set of documents, issued in printed or digital formats, are extremely important to allow the tracking and reinforcement assembly on site. Though not stored explicitly in the model, external documents can be described on the IFC by means of IfcDocumentInformation or have their location, identification, name and description designated by an IfcDocumentReference entity. An IfcDocumentInformation captures external document metadata, providing a set of identification and source information, and control information like status revision and data. The rebar mark identifier (item number) would be provided by the IfcElement.Tag attribute that is inherited by the IfcReinforcingBar entity.4.2Material and rebar propertiesFigure 2. Example of a set of the same rebars (stirrup) represented by multiple mapped entities.4.1Identification and document referenceThroughout the structural design, several documents are produced. But despite being BIM-based generated, it has some graphic information that presently remains on the authoring BIM tool. Currently, the design documentation is focused fundamentally in a paper-based format [13]. However, it is possible to produce detailed and placing drawings directly from the 3D coordinated reinforcement models, often using a 2D orthographic projections. Annotation, schedules, 2D details, notes and symbols used on drawing sheets are not explicitly represented in the IFC model. In order to fulfill the current reference document requirements of BVBS header block it's recommended that reference information of detailing and placingBefore the release of IFC4, in the 2x3 version that is still in use throughout the market, the reinforcement bar proprieties such as steel grade and diameter were described in IfcReinforcingElement and IfcReinforcingBar entities, respectively. In IFC4, these values were deprecated and currently the diameter is given by IfcReinforcingBarType's nominal diameter attribute and the steel grade turned to be provide by IfcMaterial entity. Besides the steel grade attribute, defined in IfcMaterial, an applicable standard can be appointed as an external reference by IfcExternalReferenceRelationship entity. If required, the mechanical properties shall be provided by the set of properties specified in the Pset_MaterialSteel. Reinforcing bars have standardized sizes and characteristics determined in accordance with national standard (e.g. NBR 7880 in Brazil, ASTM A615 in the US). Besides defining the bar's properties these standards also define the types steel mill rebars produced by a particular country. The rebar steel mechanical characteristics are defined based on the steel grade (yield strength level) and all bar properties are set based upon the nominal diameter (or bar designator number) given by the standard adopted. Currently this information is handled asunder by the IFC schema where inherent to bar properties are defined in the context of instance or element type. The ability to link the bar properties via external reference relationship with an applicable standard (by means of IfcClassificationReference) together with an IfcReinforcementBarProperties entity are possible but nowadays this entity is used for a specify section rebar proprieties on an early design phase defining a required as-design reinforcement.33rd International Symposium on Automation and Robotics in Construction (ISARC 2016)This would require disjoin the section's particular properties, as such TotalCrossSectionArea, EffectiveDepth and BarCount attributes, of the standardized rebar's properties. An option could be the creation of a new entity (e.g. IfcSectionReinforcementBarProperties) and the subsequent use of IfcReinforcementBarProperties entity only to the specific rebar properties.4.4Geometric representation4.3Quantity SetsThe quantities associated with the rebar elements are represented by an IfcElementyQuantity entity. An objectified relationship between the IfcReinforcingBar and the IfcElementQuantity is represented by the IfcRelDefinedByProperties entity. It is possible to represent one or a row of rebars with the IfcReinforcingBar, and the quantities must be calculated accordingly. Currently, there is a reinforcement quantity definition template in IFC, Qto_ReinforcingElementBaseQuantities that predicts the following base quantity measures: count, length and weight. The IfcElementQuantity that contains this data is also related to three specific IfcPhysicalQuantity (which is an abstract supertype): IfcQuantityCount, IfcQuantityLength, and IfcQuantityWeight. These quantities are derived from the physical properties of the elements and related with the global identifier of each instance.Although it is recommended [5] [10] the use of a swept disk solid as the rebar section, swept along a three dimensional curve (directrix) to define the rebar geometry, the method of how the segments of this directrix will be made is not standardized by the buildingSMART in IFC. This swept disk solid can be defined by IfcSweptDiskSolid entity or its subtype IfcSweptDiskSolidPolygonal. While the directrix attribute is defined in IfcSweptDiskSolid by an IfcCurve type, IfcSweptDiskSolidPolygonal require the use of a IfcPolyline. An IfcCurve is an abstract entity used to represent curves in 2D or 3D space. This entity is the supertype of many subtypes like lines, polylines, circles and others primitives used to represent bounded and unbounded curves. The reinforcement bar shape is a curve with finite length composed by straight and arc segments. Although it is possible to use any subtype of IfcCurve, some options demand a combination of other IFC entities to describe this composite curve. This fact can affect the size of the models files, compromising the performance and usability of the model. The subtype IfcSweptDiskSolidPolygonal, included in IFC4, allowed an additional fillet radius attribute applied to all transitions of polyline segments requiring only the definition of straight segments of the directrix for a rebar geometric representation which can be a smart choice, especially in case of rebar shapes with standard bending radius.Figure 3. IfcIndexedPolyCurve entity included in IFC 4 Addendum 1 [10] Also, the current IFC release provided a simplified and more compact way for the geometric representation of composite curves using a list of indexed segments with the employment of the IfcIndexedPolyCurve entity, a subtype of IfcBoundedCurve (Figure 3). The use of swept disk solid directrix definition to drive a geometric shape on fabrication can be considered as a common point for geometric data exchanging. In deciding the best approach to model or represent reinforcing bars, one must consider that most of the its shapes are produced with the minimum bent diameter determined in accordance to national structural designBuilding Information Modeling (BIM)standard (e.g. NBR 6118, ACI 318, Eurocode 2) along with reinforcement detailing standards such as ACI 315, BS 8666 or EN ISO 3766. It is generally considered a multiplier of rebar nominal diameter, relative to a structural purpose, to specify the bending machine mandrel diameter. Due to this, the use of IfcSweptDiskSolidPolygonal with fillet radius attribute defined according these standards should be considered, serving almost all cases. This option also favor the bending diameter attribute track down required on BVBS header block.4.5Geometric representation authoring toolsinBIMTo better illustrate the discussion about geometric representation of structural elements in IFC, a test with three of the most representative authoring BIM tools was conducted: Autodesk Revit 2017, Tekla Structure 2016 and Allplan Engineering 2016. In order to evaluate the method for geometric representation used by some of the main structural detailing BIM tools, a model was created based on the example of a single reinforcement stirrup present in the IFC4 Add. 1 documentation [14]. In its constant evolution, the new release of the IFC schema included others forms of geometric representation. Nevertheless, these new entities are not supported by the reviewed BIM tools. The current method used to export reinforcing bars in IFC files, specifically the directrix attribute that establishes the swept disk solid shape, were comparedwith a new entities released in IFC4 and IFC4 Add.1 with the purpose of verifying their influence in the size of the models files. Distinctive methods are adopted by the structural detailing BIM tools for define the directrix. In Table 2 are present the method employed by reviewed BIM tools for a reinforcement bars geometric representation. Included in the Annex E of IFC4 Add. 1 documentation, the sample E.14.5 uses the new entity IfcIndexedPolyCurve to define the swept disk solid directrix. This option allows a simplified and more compact way for describe this stirrup shape, requiring only two lines of an IFC file to describe a composite curve. The first line is used for indexing of the segments (straight and curved) and the second line to define the coordinates of the points, grouped with the use of IfcCartesianPointList3D. The directrix is defined in Autodesk Revit 2017 by IfcCompositeCurve, straight segments are defined with IfcPolyline and curve segments by IfcTrimmedCurve with IfcCircle basis curve. The method adopted by Tekla Structure 2016 also uses an IfcCompositeCurve to define the swept disk solid directrix. Both segments which compose the parent curve are defined by IfcTrimmedCurve entity by means of IfcLine for straight segments and IfcCircle for arc segments. In Allplan Engineering 2016, the directrix is defined only by IfcPolyline curve. The segments in curve are discretized in several straight segments with intermediate points of the arc.Table 2.Geometric representation of reinforcement bars by reviewed BIM tools Model Rebar IFC4 Add. 1 E.14.5 IfcReinforcingBar IfcReinforcingBartype IfcSweptDiskSolid Directrix Line segment Arc segment IFC release IfcIndexedPolycurve IfcLineIndex IfcArcIndex IFC 4 Add.1 Autodesk Revit 2017 IfcReinforcingBar IfcSweptDiskSolid IfcCompositeCurve IfcCompositeCurveSegment + IfcPolyline IfcCompositeCurveSegment + IfcTrimmedCurve IFC 2x3 CV Tekla Structures 2016 IfcReinforcingBar IfcSweptDiskSolid IfcCompositeCurve Allplan Engineering 2016 IfcReinforcingBar IfcSweptDiskSolid IfcPolylineIfcCompositeCurveSegment IfcCatersianPoint + IfcLine IfcCompositeCurveSegment + IfcTrimmedCurve IFC 2x3 CV IFC 2x3 CV33rd International Symposium on Automation and Robotics in Construction (ISARC 2016)5ConclusionsIt is necessary to improve the existing interface of information exchange required by the fabricator and to promote the development of a way that allow a collaboration between rebar supply chain players based on IFC model instead of the current flow based 2D drawings. In order to summarize the results, Figure 4 represents the proposal discussed in this article to map the required information content of the BVBS standard into the IFC data schema, in its 4th version. The overview of how the information required by BVBS header block are currently mapped on the IFC schema are shown in Table 3. In this article, a BVBS-IFC digital interface for the workflow of the rebar cut and bend supply chain was proposed. The principal characteristics of the BVBS standard were shown and a possible mapping inside IFCschema was elaborated and discussed. Particular attention was given to the geometric representation of reinforcement bars in IFC and inside some BIM authoring tools. The review of some structural detailing BIM tools has shown that distinctive methods of geometric representation are currently used for exporting reinforcement bars in IFC. IFC4 version incorporated many changes in the structural elements domain, when compared to the previous IFC2x3 version, and these changes helped to solve part of the problems existent in the structural design workflow. The use of IFC object-type on reinforcement domain (included in the IFC4) simplify the representation of structural elements and its assemblies, allowing the reuse of common characteristics shared by similar rebar occurrence. But some issues still exist, which must be addressed in the future development of IFC schema.Figure 4. BVBS requirements map in IFC 4 Addendum 1Building Information Modeling (BIM)Table 3. BVBS Header block information in IFC 4 Add.1 Field Identification H j r i p l n e d g s Header-Block description Project number (optional) Drawing number of the respective drawing Index of the respective drawing re-bar/mesh item number bar/mesh length [mm] item quantity weight per mesh/bar item [kg] bar diameter [mm] steel grade bending diameter [mm] IFC entity IfcProject IfcDocumentInformation IfcDocumentInformation IfcReinforcingBar IfcReinforcingBarType IfcQuantityCount ▬ IfcReinforcingBarType IfcMaterial ▬ Attribute #3 Name #1 Identification #8 Revision #8 Tag # 13 BarLength #4 CountValue ▬ ▬ # 11 NominalDiameter #1 Name ▬ ▬References[1] Polat G., Ballard G., Construction supply chains: Turkish supply chain configurations for cut and bent rebar, in: 11th Annual Conference of the International Group for Lean Construction, Virginia, USA, 2003. [2] Marder T.S., Formoso C.T., Oportunidades de melhorias na cadeia de suprimentos do aço cortado e dobrado para a construção civil, in: I Conferência Latino-Americana Construção Sustentável X Encontro Nacional de Tecnologia do Ambiente Construído, São Paulo, Brasil, 2004: p. 14. [3] Azambuja M.M.B., Isatto E.L., Marder T.S., Formoso C.T., The importance of commitments management to the integration of make-to-order supply chains in construction industry, in: 14th Annual Conference of the International Group for Lean Construction, Santiago, Chile, 2006: pp. 609– 623. [4] Isatto E.L., Azambuja M., Formoso C.T., The Role of Commitments in the Management of Construction Make-to-Order Supply Chains, J. Manag. Eng. 31 (2015) 04014053. doi:10.1061/(ASCE)ME.1943-5479.0000253. [5] Aram S., Eastman C., Sacks R., Requirements for BIM platforms in the concrete reinforcement supply chain, Autom. Constr. 35 (2013) 1–17. doi:10.1016/j.autcon.2013.01.013. [6] BundesVereinigung der BauSoftwarehäuser, BVBS - Guidelines: Exchanging Reinforcement Data interface description release 2.0, 2.0 ed., BundesVereinigung der BauSoftwarehäuser E.V., Bonn, Germany, 2000.[7] American Concrete Institute (ACI), ACI 315-99 Details and Detailing of Concrete Reinforcement, ACI Committee 315, Farmington Hills, MI, USA, 1999. [8] BSi, BS 8666 - Scheduling, dimensioning, bending and cutting of steel reinforcement for concrete Specification, Britsh, 2005. [9] ISO, BS EN ISO 3766 - Construction drawings Simplified representation of concrete reinforcement, EN ISO 3766:2003/AC:2004, UK, 2003. [10] buildingSMART, Industry Foundation Classes Version 4 - Addendum 1, (2015). On-line: /ifc/IFC4/Add1/html/, Accessed: 15/06/216. [11] Venugopal M., Eastman C.M., Sacks R., Teizer J., Semantics of model views for information exchanges using the industry foundation class schema, Adv. Eng. Informatics. 26 (2012) 411–428. doi:10.1016/j.aei.2012.01.005. [12] Venugopal M., Eastman C., Sacks R., Panushev I., Aram V., Engineering semantics of model views for building information model exchanges usinf IFC, in: Proc. CIB W78 2010 27th Int. Conf., Cairo, Egypt, 2010 [13] Eastman C., Teicholz P., Sacks R., Liston K., BIM handbook : a guide to building information modeling for owners, managers, designers, engineers, and contractors, 2nd ed., John Wiley & Sons, Hoboken, New Jersey, 2011. [14] buildingSMART, IFC4 Add1 Example E.14.5 Reinforcing stirrup, (2015). On-line: /ifc/IFC4/Add1/html/annex/annexe/reinforcing-stirrup.htm, Accessed: 15/06/216.。