PFPE lubrication performance
全氟聚醚润滑脂

PFPE Lubricating GreaseDr. Martin Schweigkofler, Dr. Stefan Grundei, Dr. Wallace Zhang, Jocelyn ZhaoDr. Thomas Kilthau, Dr. Martin Schmidt-Amelunxen, Dr. Stefan Seemeyer,Klüber Lubrication München SE & Co. KGKlüber Lubrication Industries (Shanghai) Co.,Ltd.AbstractThe paper discloses lubricating greases which contain perfluoropolyether. Composition1.PFPE oilLubrication greases use base oils like mineral oils, native oils, and synthetic hydrocarbon oils, such as PAO, alkylated naphthalines, alkylated phenylethers, silicone oils, ester oils, polyglycols and so on. All these base oils contain hydrogen bonded to Carbon, i.e. CH, CH2 and CH3 groups. These base oils cannot be used at very high temperatures and can react with different chemicals like oxidizing materials. Some of them are not sufficiently stable against hydrolysis or nucleophilic substances, e.g. amines. These hydrocarbon oils can also have a strong undesired impact on seal materials or components made out of plastics such as POM, Polyamides and PEEK.These weakness can be minimized or avoided by using Perfluoropolyether (PFPE) of the general formulaX´O(CF2O)m(CF2CF2O)n[CF2CF(CF3)O]s [CF(CF3)O]u(CF2CF2CF2O)v X (I)As base oil or part of the base oil.In drawing (I) the perfluoroalkyloxy units can be distributed randomly throughout the chain. The subscripts m, n, s, u, and v can independently be 0 to maximal 200. The molecular weight of the material for example determined by the ratio of the terminal groups compared to the internal groups via NMR analysis can be up to 20000 u.The kinematic viscosity of the perfluoropolyether can be between 5 and 2000 mm²/sec at 40°C, more preferable between 15 and 1300 mm²/sec.The pour point of the perfluoropolyether can be as low as – 80°C.The end groups X and X´ can be can be short chain perfluoroalkyl groups like CF3, C2F5, C3F7,fluorine groups is substituted by a hydrocarbon group, hydrogen, hydroxyl groups, amine groups, amid groups, carbonyl groups, or other functional groups.2.PFPE based greaseTypical PFPE lubricating grease is composed by base oil and thickener. In some PFPE grease, one or more additives are added as well.The NLGI class of the greases can be between 000 and 5, preferred between 0 and 3, even more preferred between 1 and 3.a)Base oili.Pure PFPE base oilThe perfluoropolyether can be used alone or in mixtures of two or more of the possibletypes as indicated by formula I.ii.Hybrid base oilThe base oil can be also composed by one or more type perfluoropolyether, mixed with one or more from the following type oil: mineral oils, synthetic oils or native oils. Typical ratio of PFPE to the other oils is in the range of 1:10 to 10:1.The synthetic oils are selected from an ester of an aliphatic or aromatic di-, tri- ortetracarboxylic acid with one or a mixture of C7 to C22 alcohols, a polyphenyl ether oralkylated diphenyl ether, an ester of trimethylolpropane, pentaerythritol or dipentaerythritol with aliphatic C7 to C22 carboxylic acids, C18 dimer acid esters with C7 to C22 alcohols, complex esters, individual components or in any mixtures. In addition, the synthetic oil may beselected from poly-α-olefins, metallocene catalyzed PAO, alkylated naphthalenes, alkylated benzenes, polyglycols, silicone oils, or alkylated diphenylether.The mineral oils may be selected from paraffin-basic, naphthene-basic, aromatichydrocracking oils; gas to liquid (GTL) liquids, GTL refers to a gas to liquid method anddescribes a method for production of fuel from natural gas. Natural gas is converted bysteam reforming to synthesis gas, which is then converted by Fischer-Tropsch synthesis to fuels by using catalysts. The catalysts and the process conditions control the type of fuel, i.e., whether gasoline, kerosene, diesel or oils are produced. Coal may also be used as a rawmaterial in the same way by the coal to liquid method (CTL) and biomass may be used as a raw material in the biomass to liquid (BTL) method.Triglycerides from animal/vegetable sources that have been upgraded by known methods such as hydrogenation may be used as native oils. The especially preferred triglyceride oils are genetically modified triglyceride oils with high oleic acid content. Typical vegetable oils used therein and genetically modified or cultured having a high oil content include safflower oil, corn oil, canola oil, sunflower oil, soybean oil, linseed oil, peanut oil, lesquerella oil,meadowfoam oil and palm oil. The native oils might further be processed e.g. polymerization processes.b)thickenerThe thickener material used can be fluorinated polymers like polytetrafluoroethylene (PTFE), oxides like silica, organic carbonic acid salts, boron nitride, carbides like silicon carbide, poly- or diurea compounds, polyimides or polyamidimides, melamine cyanurates, graphite, carbon black, carbon nanotubes, molybdates, phosphates.The PTFE used can be produced by polymerization of tetrafluorethylene in suspension or dispersion. To adjust the particle size and the polymer chain length processes like grinding, thermal treatment or irradiation processes can be used. PTFE powders treated as indicated above are e.g. known as micronized PTFE, but also dispersion processes leading to lowmolecular weight PTFE are known. These PTFE products can be used without the processes indicated above.Typical molecular weights are between 10000 g/mol and 10exp8 g/mol, preferred between 100000 g/mol and 10exp7 g/mol.Also recycling of PTFE by processes as indicated above can produce PTFE powders that can be used for thickeners of lubricants.The organic acids can be saturated or unsaturated, branched or unbranched, mono or di or tri or polyacids containing 6 to 25 carbon acids and their mixtures like stearic acid,hydroxystearic acid, benzoic acid, oleic acid, acelaic acid, sebacic acids, behenic acid, amid groups containing acids. Amid group containing acids can for example be prepared byreacting primary or secondary aliphatic amines with di-acids or di-esters of aliphatic oraromatic carbonic acids.The cations of the organic acid salts can be lithium, sodium, potassium, magnesium, calcium, aluminum, barium or zinc.The urea compounds are reaction products of aliphatic or aromatic mono or diisocyanatemixtures. Examples for suitable urea compounds are reaction products of diisocyanates, preferably 2,4-diisocyanatotoluene, 2,6-diisocyanatotoluene,4,4′-diisocyanatodiphenylmethane, 2,4′-diisocyanatodiphenylmethane,4,4′-diisocyanatodiphenyl, 4,4′-diisocyanato-3,3′-dimethyldiphenyl,4,4′-diisocyanato-3,3′-dimethylphenylmethane which may be used individually or incombination, with an amine of the general formula R′2N—R or a diamine of the generalformula R′2N—R—N—R′2 where R is an aryl, alkyl or alkylene radical with 2 to 22 carbon atoms and R′ is identical to or different from a hydrogen, an alkyl, alkylene or aryl radical, or with mixtures of amines and diamines.These thickener materials can be used alone or in combination.The particle size of the thickener is usually below 100µ, preferred below 20 µm.The amount of thickener material is below 50 %, preferred below 40 %c)AdditivesAdditionally additives can be used to improve the EP, anti-corrosion properties, frictionproperties, wear properties, oxidation resistance properties. The additives can be materials soluble in PFPE oils or insoluble materials.PFPE soluble materials comprise one or more functional groups based on phosphates,phosphazenes, triazines, aromatic nitro compounds, acid amides, carbonic acid derivatives, ammonium salts and linking groups or end groups consisting of PFPE moieties like groups (II) and (III),CbF(2b+1)O(CF2O)m(CF2CF2O)n[CF2CF(CF3)O]s [CF(CF3)O]u(CF2CF2CF2O)v- (II)-O(CF2O)m(CF2CF2O)n[CF2CF(CF3)O]s [CF(CF3)O]u(CF2CF2CF2O)v- (III).PFPE insoluble additives can be metal molybdates, metal phosphates, salt of organic acids, nitrite salts, metal sulfides like molybdenum disulfide or zinc sulfide, oxides like silicates, hexagonal boron nitride, metal oxides or hydroxides or hydrogen carbonates and theirmixtures.The cations in the mentioned oxides, hydroxides, hydrogen carbonates and carbonates can be derived from alkaline or earth alkaline metals like sodium, lithium, magnesium, potassium, calcium.Further additives which are not soluble in PFPE can be arylamine derivatives, phenolderivatives, metal salts of organic carbonic or sulfonic acids or phosphoric acids ofThe additives can for example be chosen from the group comprising butyl hydroxy toluene, dialkyl diphenylamines, styrolized diphenylamines, alkylated phenyl-alpha-naphthylamines, polymeric trimethyl dihydroquinoline, sulfurized fatty acid esters, diphenyl cresyl phosphate, amine-neutralized phosphates, alkylated and non-alkylated triaryl phosphates, alkylated and non-alkylated triaryl thiophosphates, zinc-dialkyl dithiophosphates, carbamates, thiocarbamates, zinc-dithiocarbamates, dimercaptothiadiazole, succinic acid semi-ester, calcium sulfonates, benzotriazole derivatives, K-pentaborates, Na-thiosulfates, andNa-pyrophosphates.The amount of additives in the grease can be up to 15 % by weight, more preferable less than 10 % by weight.ApplicationThe lubricant formulations can be used in technical components like bearings, gears, chains, screws, valves, spindles, actuators, armatures, electrical contacts, ropes, combustion and electrical motors, seals, pneumatic or hydraulic devices, compressors, brakes.Bearing industry, automotive industry, automotive supplier industry, foil producing industry, wood panel industry, food processing industry, cement industry, mining industry, marine industry, convey or …..Typical formulation:Sample I1.PFPE 83% (kin.vis. @ 40°C 100 mm2/s)2.PTFE 17% D50 < 20 µmSample II1.PFPE80% (kin.vis. @ 40°C 100 mm2/s)2.PTFE 20% D50 < 20 µmSample III1.PFPE 75% (kin.vis. @ 40°C 200 mm2/s)2.PTFE 20% D50 < 20 µm3.BN 5%Sample IV1.PFPE 73% (kin.vis. @ 40°C 400 mm2/s)2.PTFE 25% D50 < 20 µm3.ZnS 2%Sample V1.PFPE 76% (kin.vis. @ 40°C 1000 mm2/s)2.PTFE 22% D50 < 20 µm3.ZnS 2%Sample VI1.PFPE 42% (kin.vis. @ 40°C 400 mm2/s)2.Trimellitate ester, 45% (kin.vis. @ 40°C 70 mm2/s)3.Urea thickener, 8%4.Alkyl phenyl amine, 2%5.Alkyl phenol, 2%6.ZnDDP, 1%Sample VII1.PFPE 37% (kin.vis. @ 40°C 400 mm2/s)2.PAO, 45% (kin.vis. @ 40°C 400 mm2/s)3.Lithium 12OH-stearate, 8%4.Lithium sebacate, 2%5.Alkyl phenyl amine, 2%6.Alkyl phenol, 2%8.Calcium sulphonate 2%Reference1.PAO, 75% (kin.vis. @ 40°C 400 mm2/s)2.Urea thickener, 8%3.Alkyl phenyl amine, 2%4.Alkyl phenol, 2%5.ZnDDP, 1%6.Calcium sulphonate 2%Table 1. Test result of PFPE greasePage | 8全氟聚醚润滑脂Dr. Martin Schweigkofler, Dr. Stefan Grundei, Dr. Wallace Zhang, Jocelyn ZhaoDr. Thomas Kilthau, Dr. Martin Schmidt-Amelunxen, Dr. Stefan Seemeyer,Klüber Lubrication München SE & Co. KG克鲁勃润滑产品(上海)有限公司摘要本文章公开了含有全氟聚醚的润滑脂。
派克精密流体微型泵说明书
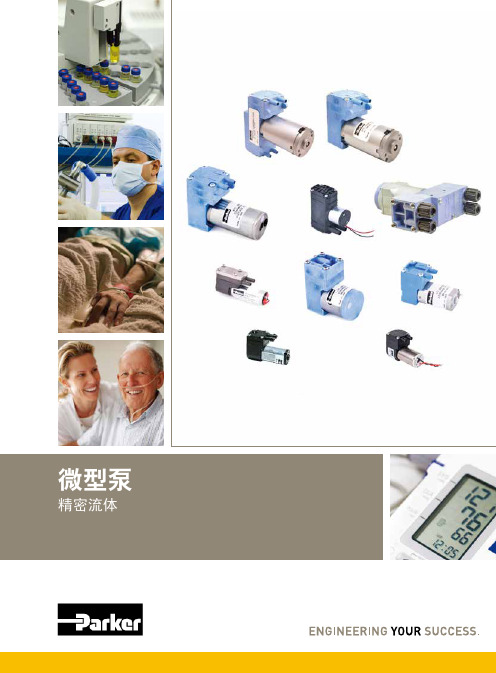
您与运动和控制技术领域的先行者合作,就是希望促进您的业务发展和全球的发展。
从微型电磁阀到高集成型自动化系统,我们的产品对于用于药物研发和病原体检测的救生医疗设备和科学仪器至关重要。
并且对于缩短上市时间和降低总体拥有成本也十分关键。
因此,请与派克合作,准备改变这一切吧!/precisionfluidics 1 603 595-1500目录页T2-05Helix124高效和紧凑型 13.5mm 宽泵 – 高达 800 mLPM高压泵 – 超过5.5 LPM 和高达100 PSI 的压力T2-0320高性能与尺寸比率泵 – 高达2.5 LPMLTC 系列76液体系列传送泵 – 高达 650 mLPMEZ 底座92振动隔离安装系统小型活塞泵(空气)微型泵(空气/气体)微型泵(液体)T2-0494超紧凑型、高效泵 – 高达 7.5LPMBTC-IIS 系列62应用广泛的多功能双头泵系列产品 – 高达 11 LPMBTC 系列52应用广泛的多功能泵系列产品 – 高达6 LPMLTC-IIS 系列84液体系列双头传送泵 – 高达1.5 LPMCTS 系列BTX-Connect 2836高性能紧凑型 20 mm 宽泵 – 高达 2.5 LPM多功能双头和单头泵系列,适合多种应用-高达10 LPMTTC 系列74紧凑、高效、低压泵 – 高达 6 LPMTTC-IIS 系列84紧凑、高效、低压双头泵 - 高达 11 LPM附件4Helix 微型高压泵高达100 PSI (6.9 bar)压力Parker Helix 是一款紧凑型高压泵,旨在实现小型即时临床护理仪器。
Helix 可在挑战性的高海拔环境和无法使用外部压缩空气的应用中实现高压操作。
Helix 泵可提供5.5 LPM 以上的流量和高达100 PSI (6.9 bar)的压力,为性能至关重要且空间有限的台式诊断设备提供了出色的解决方案。
• 集成了用于卸荷的X 阀,可实现高压重启• 内部飞轮可在高压下低速运行• 无油活塞• 简单的安装特性• 带有推入式接头的快速流体连接• 符合RoHS 指令和REACH 标准产品特性• 液上空气• 气动驱动•微流控芯片• 即时临床护理检验• 分子诊断• 核酸纯化•基因组学典型应用典型市场产品规格物理特性电子5微型隔Helix 微型高压泵典型流量曲线• 曲线展示了0.080"偏移泵的流量性能• 使用5.0 Vdc 控制输入时,泵将以大约4400 RPM 的转速和高达8.5 LPM的流量的状态运行,但不建议连续工作。
六氟丙烯齐聚物的制备[发明专利]
![六氟丙烯齐聚物的制备[发明专利]](https://img.taocdn.com/s3/m/c9b2b42e9ec3d5bbfc0a749a.png)
专利名称:六氟丙烯齐聚物的制备专利类型:发明专利
发明人:R·A·普罗科普
申请号:CN93121609.5
申请日:19931228
公开号:CN1095367A
公开日:
19941123
专利内容由知识产权出版社提供
摘要:一种六氟丙烯的齐聚反应方法,包括在极性的质 子惰性溶剂如乙腈存在下,将六氟丙烯与选自碱金 属,季铵和季鏻的氰化物,氰酸盐和硫化氰酸盐中的 一种催化剂或催化剂混合物相接触。
本发明方法特 别可通过适当地选择溶剂和催化剂选择性地获得高 产率的六氟丙烯二聚体,例如全氟-2-甲基-2-戊烯 和全氟-2-甲基-3-戊烯。
申请人:美国3M公司
地址:美国明尼苏达州
国籍:US
代理机构:上海专利事务所
代理人:林蕴和
更多信息请下载全文后查看。
红外光谱技术在润滑油分析中的应用
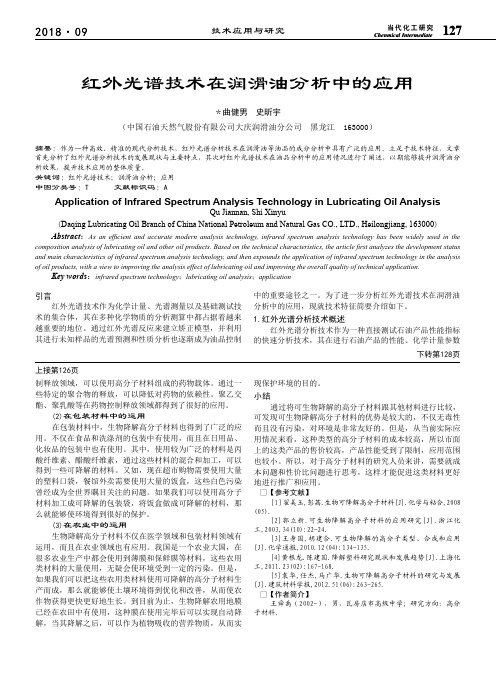
环境工程2018·09127Chenmical Intermediate当代化工研究技术应用与研究红外光谱技术在润滑油分析中的应用*曲健男 史昕宇(中国石油天然气股份有限公司大庆润滑油分公司 黑龙江 163000)摘要:作为一种高效、精准的现代分析技术,红外光谱分析技术在润滑油等油品的成分分析中具有广泛的应用。
立足于技术特征,文章首先分析了红外光谱分析技术的发展现状与主要特点,其次对红外光谱技术在油品分析中的应用情况进行了阐述,以期能够提升润滑油分析效果,提升技术应用的整体质量。
关键词:红外光谱技术;润滑油分析;应用中图分类号:T 文献标识码:AApplication of Infrared Spectrum Analysis Technology in Lubricating Oil AnalysisQu Jiannan, Shi Xinyu(Daqing Lubricating Oil Branch of China National Petroleum and Natural Gas CO., LTD., Heilongjiang, 163000)Abstract :As an efficient and accurate modern analysis technology, infrared spectrum analysis technology has been widely used in thecomposition analysis of lubricating oil and other oil products. Based on the technical characteristics, the article first analyzes the development status and main characteristics of infrared spectrum analysis technology, and then expounds the application of infrared spectrum technology in the analysis of oil products, with a view to improving the analysis effect of lubricating oil and improving the overall quality of technical application.Key words :infrared spectrum technology ;lubricating oil analysis ;application引言红外光谱技术作为化学计量、光谱测量以及基础测试技术的集合体,其在多种化学物质的分析测算中都占据着越来越重要的地位。
lubrication
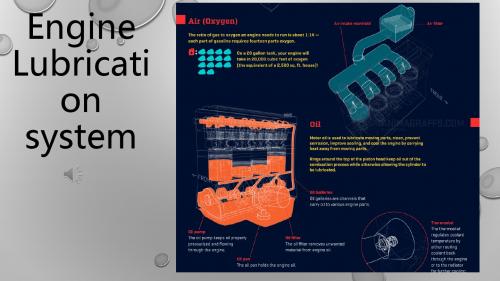
Pump In most cars, the oil pump is in the crankcase above the sump. It draws oil through a tub that extends downwards into the sump. This tube has a filter screen over its bottom end.
rub 摩擦 wear power loss功率损失 film膜
Lubrication system 润滑系统
friction 摩擦
The lubrication system must supply a continuous flow of oil to all the engine bearings and lubricated surfaces to maintain the oil film of each components and minimize wear. 润滑系统必须向所有发动机轴承和润滑表面提供连续的油流,以保持每个部 件的油膜并尽量减少磨损。 The correct oil viscosity is also essential to reduce friction 润滑油正确的粘度也是减少摩擦的必要条件 Bearing 轴承 viscosity 粘度 Component 部件 minimize [ˈmɪnɪmaɪz] 把…减至最低数量[程度]
Besides the gauze screen that prevents pieces of metal entering the pump there is an external filter which can be renewed periodically.
磷扩散均匀性的修复方法[发明专利]
![磷扩散均匀性的修复方法[发明专利]](https://img.taocdn.com/s3/m/663319726bec0975f565e25c.png)
专利名称:磷扩散均匀性的修复方法专利类型:发明专利
发明人:乐雄英,李静
申请号:CN201711263983.8
申请日:20171205
公开号:CN107993930A
公开日:
20180504
专利内容由知识产权出版社提供
摘要:本发明公开一种磷扩散均匀性的修复方法,包括氧化、第一次沉积、第二次沉积、第三次沉积、推结五个步骤,且五个步骤于不相同的温度条件下完成。
通过将传统的单步磷扩散过程变为多步扩散过程,同时将传统的恒温磷扩散过程变成了变温磷扩散过程,克服了传统的磷扩散方法在界面区域容易扩散不均匀的弊端,增加多步变温磷扩散处理,可以使磷扩散沉积的界面的均匀性得到比较好的修复,提高磷扩散的均匀性的同时,提升晶硅电池的转换效率。
申请人:苏州润阳光伏科技有限公司
地址:215300 江苏省苏州市昆山开发区前进东路科技广场8楼
国籍:CN
更多信息请下载全文后查看。
往复式内燃机 声压法声功率级的测定 第4部分:现场测量简易法-最新国标
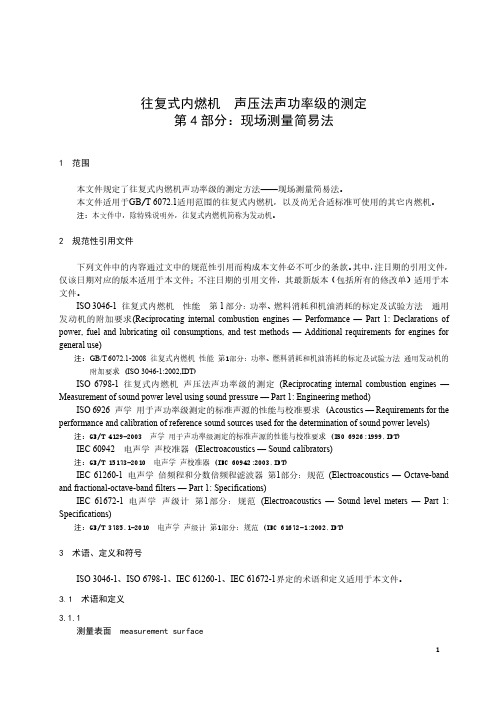
往复式内燃机声压法声功率级的测定第4部分:现场测量简易法1 范围本文件规定了往复式内燃机声功率级的测定方法——现场测量简易法。
本文件适用于GB/T 6072.1适用范围的往复式内燃机,以及尚无合适标准可使用的其它内燃机。
注:本文件中,除特殊说明外,往复式内燃机简称为发动机。
2 规范性引用文件下列文件中的内容通过文中的规范性引用而构成本文件必不可少的条款。
其中,注日期的引用文件,仅该日期对应的版本适用于本文件;不注日期的引用文件,其最新版本(包括所有的修改单)适用于本文件。
ISO 3046-1 往复式内燃机性能第1部分:功率、燃料消耗和机油消耗的标定及试验方法通用发动机的附加要求(Reciprocating internal combustion engines —Performance —Part 1: Declarations of power, fuel and lubricating oil consumptions, and test methods —Additional requirements for engines for general use)注:G B/T 6072.1-2008往复式内燃机性能第1部分:功率、燃料消耗和机油消耗的标定及试验方法通用发动机的附加要求 (ISO 3046-1:2002,IDT)ISO 6798-1 往复式内燃机声压法声功率级的测定(Reciprocating internal combustion engines —Measurement of sound power level using sound pressure — Part 1: Engineering method) ISO 6926 声学用于声功率级测定的标准声源的性能与校准要求 (Acoustics — Requirements for the performance and calibration of reference sound sources used for the determination of sound power levels) 注:G B/T 4129-2003 声学用于声功率级测定的标准声源的性能与校准要求 (ISO 6926:1999,IDT)IEC 60942 电声学声校准器 (Electroacoustics — Sound calibrators)注:G B/T 15173-2010 电声学声校准器 (IEC 60942:2003,IDT)IEC 61260-1 电声学倍频程和分数倍频程滤波器第1部分:规范(Electroacoustics — Octave-band and fractional-octave-band filters — Part 1: Specifications)IEC 61672-1 电声学声级计第1部分:规范(Electroacoustics —Sound level meters —Part 1: Specifications)注:G B/T 3785.1-2010 电声学声级计第1部分:规范 (IEC 61672-1:2002,IDT)3 术语、定义和符号ISO 3046-1、ISO 6798-1、IEC 61260-1、IEC 61672-1界定的术语和定义适用于本文件。
德国克鲁伯的一款高温油脂

BARRIERTA L 55 series, Art-No. 090014, 090013, 090035, 090042, en Edition 21.12.2011 [replaces edition 21.12.2011]Benefits for your application–Higher machine availability and less need for maintenance –at very high operating temperatures up to 260 °C –under the influence of aggressive media and vapours–where other lubricants might affect sensitive plastic components–Tried and tested over many years in numerous industries and component types–thanks to BARRIERTA base oils, which are made specifically to enable long-term stability –backed by a large number of approvals and references for various applications –four consistency classes to suit different applicationsDescriptionBARRIERTA is Europe's oldest high-quality brand of high-temperature lubricants based on perfluorinated polyether oil (PFPE). Today the name of BARRIERTA is widely regarded as synonymous with long-term stability and thermal resistance.Specifically made raw materials and continued development have made BARRIERTA products the first choice of lubrication experts in many sectors worldwide.BARRIERTA L 55/0-3 series long-term greases offer excellent resistance to high temperature and aggressive media and at the same time compatibility with plastics and elastomers.BARRIERTA L 55/0-3 are NSF H1 registered and therefore comply with FDA 21 CFR § 178.3570. The lubricants were developed for incidental contact with products and packaging materials in the food-processing, cosmetics, pharmaceutical or animal feed industries. The use of BARRIERTA L 55/0-3 cancontribute to increase reliability of your production processes. We nevertheless recommend conducting an additional risk analysis,e.g. HACCP.ApplicationRolling and plain bearings subject to high temperatures One of the well-known strengths of the BARRIERTA L 55 series is the products' suitability for the lubrication of bearings and guides operating under extreme temperatures. A low evaporation rate enables longest grease lives and hence longest relubrication intervals.Typical applications include:–conveyors (load and turn rollers)–kiln cart wheel bearings –calender bearings –fan bearings–chain bearings in film stretching stentersBARRIERTA L 55/2 is most frequently used for initial and long-term lubrication.For relubrication softer grades of NLGI class 1 or lower are recommended.Friction points under the influence of mediaBARRIERTA L 55 greases offer exceptionally long service lifetimes even when exposed to any of a large number of aggressive media such as concentrated acids, lyes, organic solvents or gases.In addition to their resistance to media, BARRIERTA L 55/2 and BARRIERTA L 55/3 offer also good adhesion and a sealing effect,which makes them suitable for application in –valves, fittings and installations e.g. in the chemical industry –pneumatic components–level gauges, e.g. for fuels or chemicals –seals (static, dynamic)–extraction systems Food-processing and pharmaceutical industriesAll BARRIERTA L 55 greases are registered as NSF-H1 and are therefore in compliance with FDA 21 CFR § 178.3570. The additional certification according to ISO 21469 supports the compliance with the hygienic requirements in your productionBARRIERTA L 55 seriesHigh-temperature long-term greasesProduct informationplant. You will find further information on ISO Standard 21469 on our website .White-coloured BARRIERTA L 55 special lubricants can therefore also be used on friction points where occasional contact with food products cannot be ruled out for technical reasons, e.g. in rolling and plain bearings and guides operating under high thermal loads in –automatic baking ovens –cooking or frying lines –conveyor systemsPlastic-plastic friction pointsBARRIERTA L 55 greases – irrespective of NLGI grade - are neutral towards the majority of plastic materials. Results of pertinent tests with fluoroelastomers can be found overleaf. We recommend testing lubricant compatibility with the materials in question prior to series application.Application notesFor optimum results we recommend cleaning all friction points with white spirit 180/210 and then with Kl beralfa XZ 3-1 prior to initial lubrication. Subsequently, the friction points should be dried with clean dry compressed air or hot air to remove all solvent residues.The friction point must be free from oil, grease, perspiration and contamination particles before initial lubrication.Please contact our technical sales staff for details of best practice with BARRIERTA L 55 lubricants to ensure longest lifetimes and highest performance outcomes are achieved.Minimum shelf lifeThe minimum shelf life is approx. 60 months if the product isstored in its unopened original container in a dry, frost-free place.Material safety data sheetsMaterial safety data sheets can be downloaded or requested via our website . You may also obtain them through your contact person at Kl ber Lubrication.BARRIERTA L 55 seriesHigh-temperature long-term greasesProduct informationBARRIERTA L 55 series, Art-No. 090014, 090013, 090035, 090042, en Edition 21.12.2011 [replaces edition 21.12.2011]Product data BARRIERTA L55/0BARRIERTA L55/1BARRIERTA L55/2BARRIERTA L55/3Article number090035 090042 090013 090014NSF-H1 registration129 523 129 561 129 400 129 562 Chemical composition, type of oil PFPE PFPE PFPE PFPE Chemical composition, solid lubricant PTFE PTFE PTFE PTFELower service temperature-40 °C / -40 °F-40 °C / -40 °F-40 °C / -40 °F-30 °C / -22 °F Upper service temperature260 °C / 500 °F260 °C / 500 °F260 °C / 500 °F260 °C / 500 °F Colour space white white white whiteDensity at 20 °C approx. 1.95g/cm³approx. 1.95g/cm³approx. 1.96g/cm³approx. 1.96g/cm³Shear viscosity at 25 °C, shear rate 300 s-1; equipment:rotational viscometer approx. 4 500mPasapprox. 10 000mPasapprox. 14 000mPasShear viscosity at 25°C, shear rate 300 s-1,equipment:rotational viscometer, upper limit value5 500 mPas8 000 mPasShear viscosity at 25 °C, shear rate 300 s-1,equipment: rotational viscometer, lower limit value3 500 mPas4 000 mPasKinematic viscosity of the base oil, DIN 51562 pt. 01/ASTM D-445/ASTM D 7042, 40 °C approx. 420mm²/sapprox. 420mm²/sapprox. 420mm²/sapprox. 420mm²/sKinematic viscosity, DIN 51562 pt. 01/ASTM D-445/ASTM D 7042, 100 °C approx. 40mm²/sapprox. 40mm²/sapprox. 40mm²/sapprox. 40mm²/sFlow pressure of lubricating greases, DIN 51805, testtemperature: -30 °C<= 1 400 mbarFlow pressure of lubricating greases, DIN 51805, testtemperature: -40 °C<= 1 400 mbar<= 1 600 mbarFour-ball tester, welding load, DIN 51350 pt. 04>= 6 000 >= 7 000 >= 8 000 >= 8 000Speed factor (n x dm) approx. 300 000mm/min approx. 300 000mm/minapprox. 300 000mm/minapprox. 300 000mm/minCorrosion inhibiting properties of lubricating greases, DIN 51802, (SKF-EMCOR), test duration: 1 week, distilled water <= 1 corrosiondegree<= 1 corrosiondegree<= 1 corrosiondegreeAdditional data: resistance to fluoroelastomersChange75 FKM 58580 FKM 61060 FVMQ 565 Exposure life [h] / exposure temp. [°C]168 / 160168 / 160168 / 150 Volume [%]+ 0.5+0.5- 0.3 Hardness (Shore A)+ 0.5- 1- 2Tensile strength [%]+ 15+ 15- 16 Elongation at tear [%]- 11- 11- 10Klüber Lubrication – your global specialist Innovative tribological solutions are our passion. Throughpersonal contact and consultation, we help our customers to be successful worldwide, in all industries and markets. With our ambitious technical concepts and experienced, competent staff we have been fulfilling increasingly demanding requirements by manufacturing efficient high-performance lubricants for more than 80 years.Klüber Lubrication München KG /Geisenhausenerstraße 7 / 81379 München / Germany /phone +49 89 7876-0 / fax +49 89 7876-333.The data in this document is based on our general experience and knowledge at the time of publication and is intended to give information of possible applications to a reader with technical experience. It constitutes neither an assurance of product properties nor does it release the user from the obligation of performing preliminary field tests with the product selected for a specific application. All data are guide values which depend on the lubricant's composition, the intended use and the application method. The technical values of lubricants change depending on the mechanical, dynamical, chemical and thermal loads, time and pressure. These changes may affect the function of a component. We recommend contacting us to discuss your specific application. If possible we will be pleased to provide a sample for testing on request. Kl ber products are continually improved. Therefore, Kl ber Lubrication reserves the right to change all the technical data in this document at any time without notice.Publisher and Copyright: Kl ber Lubrication M nchen KG. Reprints, total or in part, are permitted only prior consultation with Kl ber Lubrication M nchen KG and if source is indicated and voucher copy is forwarded.a company of the Freudenberg GroupProduct information。
- 1、下载文档前请自行甄别文档内容的完整性,平台不提供额外的编辑、内容补充、找答案等附加服务。
- 2、"仅部分预览"的文档,不可在线预览部分如存在完整性等问题,可反馈申请退款(可完整预览的文档不适用该条件!)。
- 3、如文档侵犯您的权益,请联系客服反馈,我们会尽快为您处理(人工客服工作时间:9:00-18:30)。
E. Devine Swales and Associates Beltsville, Maryland
R.E. Predmore Goddard Space Flight Greenbelt, Maryland Center
Prepared for the 207th National Meeting sponsored by the American Chemical San Diego, California, March 13-18,
NASA
Technical
Memorandum
106937IFra bibliotek/_Enhancement Lubrication
I. Preliminary
of Pertluoropolyether Performance
Results
Boundary
W.R. Jones, Jr. Lewis Research Center Cleveland, Ohio O.O. Ajayi, A.J. Goodell, Wedeven Associates, Inc. Edgmont, Pennsylvania and L.D. Wedeven
(refs. 1 and 2). In addition, these fluids are candidates for high temperature aeronautical applications (ref. 3). Several commercial fluids are available, such as Krytox (ref. 4), Fomblin Z and Y (refs. 5 and 6), and Demnurn (ref. 7). Of these fluids, only Krytox and Fomblin Z have been used extensively as liquid lubricants and greases for space applications (ref. 8). Conventional lubricants are always supplied with an additive package that enhances their performance. These additives include: antiwear, EP, anti-oxidant, anti-degradation, anticorrosion, etc. In contrast, PFPE's are usually supplied as unformulated (nonadditive) basestocks. This is because conventional additives developed for mineral oils, esters, hydrocarbons, etc. are not soluble in PFPE fluids. A few PFPE soluble additives have been developed. The first synthesized additives were to function as degradation inhibitors at high temperatures. These included phosphines (ref. 9 to 1 I) and phosphatriazines (refs. 12 to 14). The perfluoroaryl phosphines have been reported to extend the upper temperature limits of Krytox fluids to 343 °C and Fomblin Z fluids to 288 °C (ref. 15). However, other data (ref. 16) have shown the loss of additive function at 343 °C. There is also limited activity for both additive types at 316 °C (ref. 12) and limited time of activity (75 to 100 hr) at 288 °C (ref. 13). X-Ray photoelectron spectroscopy (XPS) studies (ref. 17) of the passivation film formed on M-50 steel surfaces during oxidation-corrosion testing with a PFPE fluid containing a perfluoroaryl phosphine concluded that protective action was afforded by high surface concentrations of some type of phosphorus compound.
apparatus. These additives yielded antiwear activity with the PFPE acid being the most effective. Sharma et al (ref. 20) reported antiwear activity for an additive (structure not disclosed) in Fomblin Z. Later, this was reported (ref. 21) to be an alcohol terminated PFPE. Reference 21 also reported wear reduction for a PFPE ketone. Recently, four-ball wear results (ref. 22) have been reported for two other PFPE derivatives: a polar amine salt and a phosphorus containing end group. These additives yielded promising results in Fomblin Z and Fomblin Y base fluids to 200 °C. A different class of additives (halogenated aryl esters) has been successfully developed for the lubrication of gold coated slip rings (ref. 23). A unique bearing simulator (ref. 24) has been developed for the evaluation of lubricant formulations and surface treatments. This device, known as the WAM 3 apparatus, can alsogenerate a complete performance map showing the transitions from boundary to mixed and finally to EHL lubrication. Therefore, the objective of this work was to use this apparatus to develop a test protocol in order to determine the enhancement of the boundary lubricating ability of a PFPE (Krytox 143AB) by the use of (1) soluble boundary additives, (2) bearing surface modifications, (3) run-in surface films, and (4) ceramic bearing components In addition, results are compared with two non-perfluorinated liquid lubricant formulations.
Society 1994
(NASA-TM-106937) PERFLU(]RGPCLYETHER LUb_tlCATIQN National Space Aeronautics Administration and PRELIMINARY Research
ENHANCEMENT BOUNDARY PERFORMANCE: RESULTS Center) 12 (NASA. p I.
Introduction
Perfluoropolyethers a variety of spacecraft (PFPE) have been used as lubricants for applications for more than two decades
Basset Hermant (ref. 18) reported antiwear activity for and a series of fluorinated carboxylic acids and their amine salts. However, only a hydrocarbon basestock was studied. It was concluded that the acids formed a soap that was subsequently converted into surface fluoride. Masuko et al (ref. 19) studied a series of PFPE derivatives (acids, alcohols, and phosphate esters) in a Demnum basestock using a vacuum four-ball