FMEA
FMEA

FMEA是一组系统化的活动,其目的是:发现、评价产品/过程中潜在的失效及其后果找到能够避免或减少这些潜在失效发生的措施PFEMA是过程的失效模式分析,必须:FMEA分为:1、SFMEA为系统FMEA2、DFMEA为设计FMEA3、PFMEA为过程FMEA'4、kFMEA为德国DFMEA的书写5、FMEAs为设计FMEA和系统FMEA的合称在过程可行性分析阶段或之前开始在生产工装到位之前而且要考虑以单个零件到总成的所有制造工序DFEMA是设计的失效模式分析在一个设计概念最终形成之时或之前开始在产品开发各阶段中,当设计有变化或得到其它信息时,应持续及时地予以更新在产品图样完成之前全部结束SFMEA为系统潜在失效模式和后果分析DFMEA和PFMEA分别是设计阶段和生产过程阶段的,它们具有一定的局限性和适用性,而SFMEA是以整个系统来分析的,它考虑的更全面,主要是分析系统所有组成的失效模式和后果情况。
具有综合性、全面性2)FMEA(Failure Mode and Effect Analysis,失效模式和效果分析)是一种用来确定潜在失效模式及其原因的分析方法。
具体来说,通过实行FMEA,可在产品设计或生产工艺真正实现之前发现产品的弱点,可在原形样机阶段或在大批量生产之前确定产品缺陷。
FMEA最早是由美国国家宇航局(NASA)形成的一套分析模式,FMEA是一种实用的解决问题的方法,可适用于许多工程领域,目前世界许多汽车生产商和电子制造服务商(EMS)都已经采用这种模式进行设计和生产过程的管理和监控。
FMEA简介FMEA有三种类型,分别是系统FMEA、设计FMEA和工艺FMEA,本文中主要讨论工艺FMEA。
1)确定产品需要涉及的技术、能够出现的问题,包括下述各个方面:需要设计的新系统、产品和工艺;对现有设计和工艺的改进;在新的应用中或新的环境下,对以前的设计和工艺的保留使用;形成FMEA团队。
理想的FMEA团队应包括设计、生产、组装、质量控制、可靠性、服务、采购、测试以及供货方等所有有关方面的代表。
FMEA
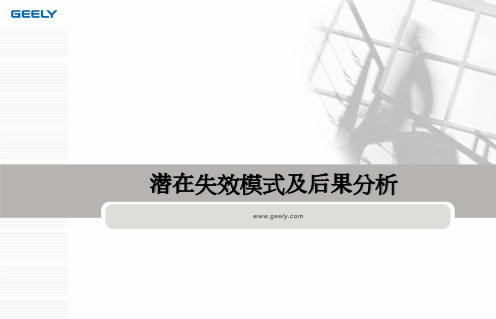
现行设计控制
失效模式如同疾病 设计控制则象医生采取的诊断方法 (医生喜欢采取预防措施)
如果可能,最好的途径是采用预防控制。假如预防性控制被融
入设计意图并成为其一部分,它可能会影响最初的频度定级。 探测度的最初定级将以探测失效起因/机理或探测失效模式的 设计控制为基础。
现行设计控制方法检测出失效模式的能力
1.5FMEA成功的条件
适时性:在“时间之窗”关闭之前
+
小组的努力:集体的智慧
1.5.1适时性
成功实施FMEA项目的 最重要因素之一
FMEA是预防性的 不是反应性的
应当尽量避免失效 而不是等着顾客提出申诉
概念提出 和批准
项目批准
样件
试生产
投产
1、策划
DFMEA PFMEA 2、产品设计和开发 3、过程策划和开发 4、产品和过程确认 5、生产
计划和确 定项目
产品设计和 开发验证
过程设计和 开发验证
产品和过 程确认
反馈评定和 纠正措施
1.5.2小组努力
尽管有的人视野很宽,但不可能面面俱到。 只有依靠集体的视野才能综观全局。
设 计
生 产
扩大视野 综观 全局
实 验
财 务
生产规划
销 售
质 保
FMEA专家
优先选择经验丰富、 有创新思维的人员
团队协作
引起的相互作用以及从市场上所获得的历史信息。它可包 括法规要求的变更。
在新的环境、场所、应用或使用形式下(包括工作 循环、法规要求等),使用现有的设计和过程。
FMEA范围应当着重于新的环境、场所、应用或使用形式
对现有设计和过程的影响。
1.4FMEA 的种类
系统-FMEA 研究的是系统、子系统、环境与顾客之间 的接口关系和相互作用,为避免产生系统上的设 计缺陷。 设计-FMEA 研究的是原件、部件的设计,涉及:设 计、原材料选择、(加工和装配)。
FMEA简述

缺陷产品;不需要分拣;需要向供应商提供反馈
触感令人略微感觉不舒服。
1
非常低 没有可觉察到的影响
没有可觉察到的影响或没有影响
没有可觉察到的影响。
注:绿色为公司重点采用的相关评判标准,灰色为不常用标准。
十、第五版FMEA内容——失效原因
· 由小组结合特定的知识和经验来确定 · 失效原因能够直接确定或者通过理解失效的原理来确定
八、第四版FMEA
过程步骤/功能
要求
潜在失效模式
潜在失效影 响
SEV 严重度
分类
潜在失效原因
OCC发生 度
现行过程控制 预防
Plasma清洗
芯片背面 无污染
D/B 焊胶层 芯片背面污染 脱落,电参
失效
8
Plasma能量&时间参 数不恰当 Plasma工艺气压值偏 小或偏大
气体流量偏小
1.限制参数编辑权限,仅工程部负责人有
· 描述失效模式对客户的影响:
- 内部客户(下一个操作/后续操作/操作目标) - 外部客户(下一级/OEM/经销商)政府法律法规
- 产品或产品最终用户/操作者 - 立法机构
要求 四个螺钉
失效模式
影响
最终顾客:座垫松动,有噪音。
少于四个螺钉 制造和装配:由于受影响的部分,因而停止发
运,并进行额外挑选和返工。
1.要求作业员每班检查气罐接口是否漏气 2.气体流量超出范围时,设备自动报警
DET RP 探测度 N
4 64
4 64 2 32
推荐措施 NONE NONE NONE
Action Results/实施结果
职责和目标完 成日期
采取的措施 和有效日期
SE V 严重 度
最全的FMEA教程和讲解

目
CONTENCT
录
• FMEA概述与基本原理 • FMEA实施流程与步骤 • FMEA关键技术与方法论 • FMEA在各行业应用案例分析 • FMEA与其他质量管理工具结合应
用探讨 • 总结回顾与未来发展趋势预测
01
FMEA概述与基本原理
FMEA定义及发展历程
FMEA定义
通过对汽车设计、制造过程中可能出现的故障 模式进行识别,以便在产品投放市场前采取预 防措施。
制定改进措施
针对识别出的故障模式和影响,制定相应的设 计、制造、检验等改进措施,提高产品质量和 安全性。
航空航天:确保飞行安全可靠性
分析系统复杂性
航空航天器系统复杂,涉及多个子系统和部件,FMEA可 帮助识别各部件之间的潜在故障和相互作用。
评估风险等级
分析故障模式对能源设备运行和人员安全的影响程度, 评估风险等级。
制定预防措施
针对识别出的安全隐患和风险等级,制定相应的预防 措施和应急预案,确保能源领域生产安全。
05
FMEA与其他质量管理工具结合应用探讨
FMEA与六西格玛管理法相结合
01 02
流程优化
六西格玛管理法强调流程优化与变异减少,而FMEA可以在流程设计初 期识别潜在失效模式,为六西格玛的DMAIC(定义、测量、分析、改 进、控制)循环提供输入。
FMEA(Failure Mode and Effects Analysis,失效模式与影响分析) 是一种预防性的质量工具,用于识别、评估和优先处理潜在的问题 或故障模式,以减少产品或过程在设计和开发阶段的风险。
发展历程
FMEA起源于20世纪40年代的军事领域,后来逐渐应用于航空、汽 车、电子等各个行业。随着质量管理理念的不断发展和完善,FMEA 已经成为一种广泛应用于产品设计和过程控制的重要工具。
FMEA的定义

FMEAFMEA是一种可靠性设计的重要方法。
它实际上是FMA(故障模式分析)和FEA(故障影响分析)的组合。
它对各种可能的风险进行评价、分析,以便在现有技术的基础上消除这些风险或将这些风险减小到可接受的水平。
目录50年代初,美国第一次将FMEA思想用于一种战斗机操作系统的设计分析;60年代中期,FMEA技术正式用于航天工业(Apollo计划);1976年,美国国防部颁布了FMEA的军用标准,但仅限于设计方面。
70年代末,FMEA技术开始进入汽车工业和医疗设备工业。
80年代初,进入微电子工业。
80年代中期,汽车工业开始应用过程FMEA确认其制造过程。
1988年,美国联邦航空局发布咨询通报要求所有航空系统的设计及分析都必须使用FMEA。
1991年,ISO-9000推荐使用FMEA提高产品和过程的设计。
1994年,FMEA又成为QS-9000的认证要求。
编辑本段产品分类概要由于产品故障可能与设计、制造过程、使用、承包商/供应商以及服务有关,因此FMEA又细分为:DFMEA:设计FMEAPFMEA:过程FMEAEFMEA:设备FMEASFMEA:体系FMEA其中设计FMEA和过程FMEA最为常用。
DFMEA:设计FMEA设计FMEA(也记为d-FMEA)应在一个设计概念形成之时或之前开始,并且在产品开发各阶段中,当设计有变化或得到其他信息时及时不断地修改,并在图样加工完成之前结束。
其评价与分析的对象是最终的产品以及每个与之相关的系统、子系统和零部件。
需要注意的是,d-FMEA在体现设计意图的同时还应保证制造或装配能够实现设计意图。
因此,虽然d-FMEA 不是靠过程控制来克服设计中的缺陷,但其可以考虑制造/装配过程中技术的/客观的限制,从而为过程控制提供了良好的基础。
进行d-FMEA有助于:· 设计要求与设计方案的相互权衡;· 制造与装配要求的最初设计;· 提高在设计/开发过程中考虑潜在故障模式及其对系统和产品影响的可能性;· 为制定全面、有效的设计试验计划和开发项目提供更多的信息;· 建立一套改进设计和开发试验的优先控制系统;· 为将来分析研究现场情况、评价设计的更改以及开发更先进的设计提供参考。
什么是FMEA(FMECA)
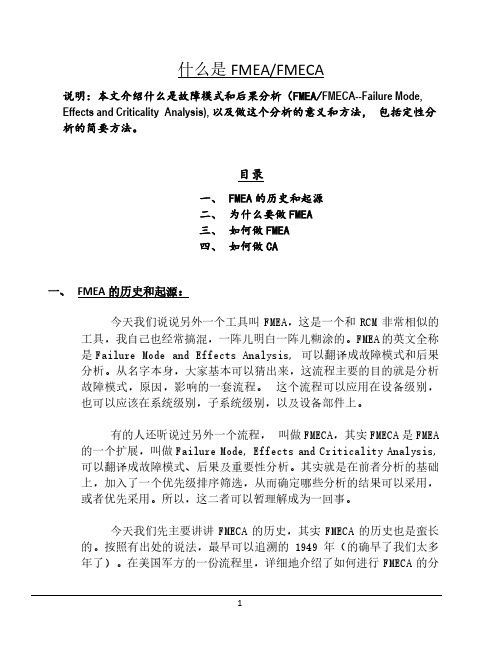
什么是FMEA/FMECA说明:本文介绍什么是故障模式和后果分析(FMEA/FMECA--Failure Mode, Effects and Criticality Analysis), 以及做这个分析的意义和方法,包括定性分析的简要方法。
目录一、FMEA的历史和起源二、为什么要做FMEA三、如何做FMEA四、如何做CA一、FMEA的历史和起源:今天我们说说另外一个工具叫FMEA,这是一个和RCM非常相似的工具,我自己也经常搞混,一阵儿明白一阵儿糊涂的。
FMEA的英文全称是Failure Mode and Effects Analysis, 可以翻译成故障模式和后果分析。
从名字本身,大家基本可以猜出来,这流程主要的目的就是分析故障模式,原因,影响的一套流程。
这个流程可以应用在设备级别,也可以应该在系统级别,子系统级别,以及设备部件上。
有的人还听说过另外一个流程,叫做FMECA,其实FMECA是FMEA 的一个扩展,叫做Failure Mode, Effects and Criticality Analysis,可以翻译成故障模式、后果及重要性分析。
其实就是在前者分析的基础上,加入了一个优先级排序筛选,从而确定哪些分析的结果可以采用,或者优先采用。
所以,这二者可以暂理解成为一回事。
今天我们先主要讲讲FMECA的历史,其实FMECA的历史也是蛮长的。
按照有出处的说法,最早可以追溯的1949年(的确早了我们太多年了)。
在美国军方的一份流程里,详细地介绍了如何进行FMECA的分析,流程编号是MIL-P-1629 (当然,这份流程后来在80年代又进行了修改,编号也变成了MIL-STD-1629A)。
在上世纪60年代初期,美国航空航天局(NASA)曾经大量使用了FMECA流程进行分析。
其中著名的阿波罗计划,维京计划,旅行者计划,麦哲伦计划,伽利略计划以及美国第一个空间站计划,都进行了FMECA分析。
我曾经拜读过1966年NASA编写的阿波罗计划FMECA实施流程,全文共37页,具体的实施方法和现如今没有太大改变。
认识质量管理工具FMEA

医疗器械行业对产品的质量和安 全性要求极高,因此FMEA在医疗 器械行业中也有广泛应用。
通过FMEA分析,可以识别出医疗 器械的潜在故障模式和风险,例 如设备失灵、误操作等,从而采 取相应的措施进行改进和优化, 确保产品的安全性和有效性。
以上案例表明,FMEA作为一种有 效的质量管理工具,可以帮助企 业识别产品的潜在故障模式和风 险,采取相应的措施进行改进和 优化,提高产品的质量和可靠性。 在不同行业中,可以根据具体的 产品特性和要求,灵活应用FMEA 进行分析和改进。
认识质量管理工具FMEA
目录
• FMEA简介 • FMEA的基本原理 • FMEA的实施步骤 • FMEA的应用场景 • FMEA的案例分析 • FMEA的未来发展与挑战
01 FMEA简介
FMEA的定义
FMEA(Failure Modes and Effects Analysis,失效模式与影响分析)是一种预防 性的质量工具,用于评估产品设计或过程中潜在的失效模式及其对系统性能的影响。
风险优先数
风险优先数(RPN)是一种评估潜在失效模式及其相关原因的 严重性、发生频率和可检测性的综合数值,用于确定改进措施 的优先级。
RPN的计算公式为:严重性×发生频率×可检测性。通过比较 RPN值,可以确定哪些失效模式需要优先采取措施进行改进和 预防。
03 FMEA的实施步骤
确定分析范围和边界
3
FMEA还可以与PFMEA(过程FMEA)结合使用, 对生产过程进行风险评估和优化,降低生产成本 和不良品率。
服务阶段
在服务阶段,FMEA可以用于分析服务流程中 的潜在问题,识别关键服务环节和可能影响客 户满意度的因素。
通过FMEA分析,可以发现潜在的服务缺陷、 沟通障碍和客户需求不匹配的情况,并采取相 应的改进措施,提高客户满意度和忠诚度。
FMEA

FMEAFMEA是一种可靠性设计的重要方法。
它实际上是FMA(故障模式分析)和FEA(故障影响分析)的组合。
它对各种可能的风险进行评价、分析,以便在现有技术的基础上消除这些风险或将这些风险减小到可接受的水平。
FMEA(失效模式与影响分析)F ailure M ode and E ffects A nalysis 潜在失效模式与后果分析产品分类由于产品故障可能与设计、制造过程、使用、承包商/供应商以及服务有关,因此FMEA又细分为:DFMEA:设计FMEA PFMEA:过程FMEA EFMEA:设备FMEA SFMEA:体系FMEA 其中设计FMEA和过程FMEA最为常用。
FMEA—8D流程的介绍QS9000、ISO/TS16949、ISO9001、TL9000、ISO14001、OHSAS18001等管理体系中都有涉及到“预防措施”;依据“ISO9001:2000质量管理体系—基础和术语”的定义,“预防措施”是指“为消除潜在不合格或其他潜在不期望情况的原因所采取的措施”,或者简单地定义为:采取预防措施是为了防止发生。
在企业实际的管理体系运作中,虽然都会去编制一份有关“预防措施”的形成文件的程序,但真正可以达到预见性地发现较全面的潜在问题通常存在较大难度,也即:这样作业的可操作性不强;取而代之的主要是“纠正措施”;但“纠正措施”与“预防措施”的确是两个不同的概念,“纠正措施”是为了防止同样的问题再次出现所采取的措施。
为能有效地实施“预防措施”,使可能存在的潜在问题无法出现,需要一个从识别问题到控制潜在影响的管理系统,对于这一点,各企业都可能制定各自不同的方法以对应,这些方法也许都是适用的;但这里所要介绍的是一种行之有效且便于操作的制定和实施“预防措施”的方法,即:美国三大车厂(戴姆勒克莱斯特、福特、通用)制定的“潜在失效模式及后果分析”,或简称为FMEA。
FMEA于2002年推出第三版本,该第三版本较第二版本更具备简便的可操作性。
fmea是什么意思_fmea的中文意思

fmea是什么意思_fmea的中文意思【fmea】abbr. 故障模式与理象分析(Failure Mode and Effects Analysis) 【网络释义】失效模式与影响分析失效模式与影响分析(FMEA)是一种确定和预防产品及工艺过程问题的系统方法。
FMEA以预防缺陷、强化安全性以及提高客户满意度为重点。
失效模式与效应分析失效模式与效应分析(FMEA)作为一种风险分析方法在设计、制造中用以预防、避免差错的应用早已为人们所熟悉。
近.失效模式与效果分析(Failure Mode And Effect Analysis)预先危险分析(PHA Preliminary Hazard Analysis失效模式分析(Failure Model Effectiveness Analysis)参与新机型的导入和延伸机型的设计,针对产品客诉问题进行产品结构方面的改善;FMEA(失效模式分析)的制作等。
【词组短语】功能FMEA Functional FMEAProcess FMEA 程失效模式及后果分析; 过程; 工艺FMEA 工艺FMEA Process FMEA-PFMEA ; process FMEAFMEA ACI 美国混凝土学会标准structured FMEA 结构; 结构FMEAFMEA设计Design FMEA(Fail Mode and Effect Analysis)FMEA introduction 文件名称D FMEA 第三十八章FMEA方法FMEA method【例句】Is the process FMEA prepared and have improvement measures been established?准备和改善措施是建立在这个故障模式影响分析过程中吗?MetsoAutomation has implemented a Failure Mode and Effect Analysis (FMEA) programmeto extend the lifecyles and lower the cost of ownership of its products.Metso自动化已经实现了一个FailureModeandEffectAnalysis (故障模式和影响分析FMEA)程序,以便扩展其产品的生命周期并降低拥有权成本。
fmea评级标准及示例
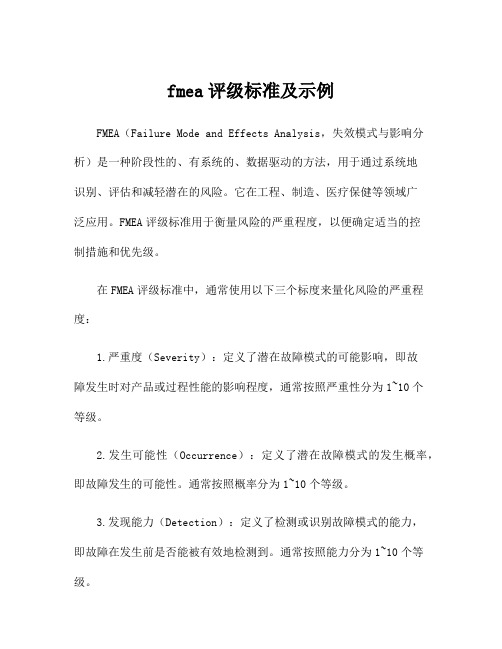
fmea评级标准及示例FMEA(Failure Mode and Effects Analysis,失效模式与影响分析)是一种阶段性的、有系统的、数据驱动的方法,用于通过系统地识别、评估和减轻潜在的风险。
它在工程、制造、医疗保健等领域广泛应用。
FMEA评级标准用于衡量风险的严重程度,以便确定适当的控制措施和优先级。
在FMEA评级标准中,通常使用以下三个标度来量化风险的严重程度:1.严重度(Severity):定义了潜在故障模式的可能影响,即故障发生时对产品或过程性能的影响程度,通常按照严重性分为1~10个等级。
2.发生可能性(Occurrence):定义了潜在故障模式的发生概率,即故障发生的可能性。
通常按照概率分为1~10个等级。
3.发现能力(Detection):定义了检测或识别故障模式的能力,即故障在发生前是否能被有效地检测到。
通常按照能力分为1~10个等级。
以上三个标度的乘积(Severity × Occurrence × Detection)被称为风险优先级数(Risk Priority Number,简称RPN)。
使用RPN可以对潜在故障模式进行优先级排序,从而确定需要采取的控制措施。
以下是一个关于汽车制造业的FMEA评级标准和示例:1.制动系统故障严重度:8发生可能性:5发现能力:7RPN:2802.气囊系统故障严重度:6发生可能性:4发现能力:8RPN:1923.发动机故障严重度:9发生可能性:6发现能力:6RPN:3244.转向系统故障严重度:7发生可能性:5发现能力:8RPN:280根据以上示例,可以看出不同故障模式的风险优先级,从而决定需要采取的控制措施。
比如,发动机故障的风险优先级最高,需要采取更严格的检测和控制措施。
而制动系统故障和转向系统故障的风险优先级较高,也需要采取相应的控制措施来降低风险。
FMEA评级标准可以根据不同行业和应用进行调整,以更好地适应特定的需求。
质量管理五大核心工具之FMEA

质量管理五大核心工具之FMEA一、什么是FMEA:潜在的失效模式与后果分析(Potential Failure Mode and Effects Analysis),简称为FMEA,是一种定性的具有工程实用价值的可靠性分析方法。
使用这种方法,可以发现和评价产品/过程中一切潜在的失效模式,及早地指出根据经验判断出的弱点和可能发生的缺陷,并分析导致的失效后果和风险,最后在决策过程中找到能够避免或减少这些潜在失效发生的措施,并将这样一组系统化活动的整个过程文件化。
所有FMEA的重点在于设计,无论是用在设计产品或过程。
1、FMEA的由来:FMEA最早由美国航天工业于上世纪60年代所发展出来的一套信赖度分析工具。
北美福特公司于1972年发展信赖度训练计划时将FMEA包括与内。
发展至今,已被汽车工业界广为采用,并对提高汽车工业产品的可靠性卓有成效。
现在,无论在ISO/TS16949:2002体系标准中,还是在汽车行业顾客对供应商的质量能力评审中,都已明确规定必须采用FMEA。
2、FMEA的优点:由于FMEA是一种定性的分析方法,因此与定量的分析方法相比,FMEA就显得简便易懂,且较直观,易于被人们掌握并运用。
尤其是在一些不能用定量的可靠性数字说明问题的工程关键阶段,FMEA就更为适用。
3、FMEA的实施l 减少减少潜在的隐忧——使用FMEA作为专门的技术应用、以识别并减少潜在的隐患;——全面实施FMEA能够避免许多车辆抱怨事件的发生。
l 适时性是成功实施FMEA的最重要因素之一——是”事发前”的行为,要求FMEA必须在设计或过程失效模式被无意纳入产品或过程之前进行;——事先花时间完成FMEA分析,能更容易并低成本地对产品/过程进行修改,从而减轻事后修改的危机;.—— FMEA能够减少或消除因进行预防/纠正而带来更大损失的机会。
l FMEA适用场合——新设计、新技术或新过程。
该FMEA的领域是完成设计、技术或过程。
FMEA
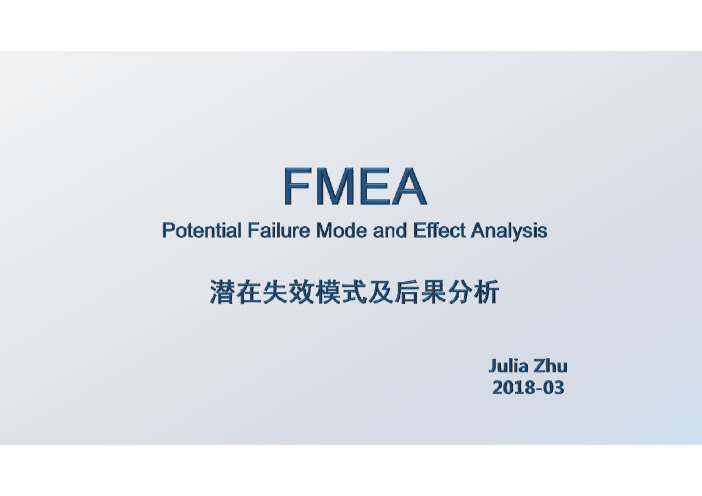
DFMEA分析的前提
DFMEA不依靠过程控制来克服设计中潜在的缺陷,但必须要考虑到制造/装配过 程中的技术、物质等限制。如: 必要的拔模(斜度) 表面处理能力的限制 装配空间/工具可接近 要求的钢材强度 公差/过程能力/性能等
DFMEA还可能要考虑到一旦产品投入使用,产品的维护(服务)及回收利用在技术/ 物质等方面的限制。如: 便利的维修工具可获得性 诊断能力水平 材料的分类符号(回收利用) 用于制造过程中的材料/化学等物质等
典型的后果举例:
噪声、不良外观、工作不稳定、间歇性工作、粗糙、失去功能、异味、性能衰
退、等等。
DFMEA的填写说明
项目 功能
要求
潜在 失效模式
失效 潜在后果
严 重 度
等 级
潜在失效 起因/机理
频 度
现行的 设计控制
预防 探测
探R 测 P 建议措施 度N
责任与 目标 完成日期
措施执行结果
采行措施
Ⅱ类失效: 是产生了有害的非期望功能
噪声、振动、电磁干扰、有害排放、等等。
DFMEA的填写说明
项目 功能
要求
潜在 失效模式
失效 潜在后果
严 重 度
等 级
潜在失效 起因/机理
频 度
现行的 设计控制
预防 探测
探R 测 P 建议措施 度N
责任与 目标 完成日期
措施执行结果
采行措施
ቤተ መጻሕፍቲ ባይዱ
严 重 度
频 度
探 测 度
严 重 度
频 度
探 测 度
R P N
失效潜在后果范例
34
DFMEA的填写说明
项目 功能
要求
潜在 失效模式
FMEA简介

2.1 FMEA的定义
FMEA Failure Mode and Effect Analysis 失效模式与效应分析
哪些原因可能造 分析 预计现行的过程可能 分析 对顾客或下工
成这个失效模式
产生的失效模式
序的影响
行动
采取可行 之对策
2.2 FMEA的起源
FMEA起始于60年代航空航天工业项目。
1974年美海军用于舰艇装备的标准,首先将它用于军事项 目合约。
完成FMEA要靠集体协作,必须综合每个人的智慧,需要设 计、制造、工艺、设备、售后服务、质量及可靠性等各方面 人员密切配合及通力合作;
产品/工艺责任者为FMEA责任者,对高风险项目进行FMEA 并根据情况召集FMEA team对产品/工艺FMEA进行及时修订;
2.6 FMEA的三种效应
失效应考虑的三种效应
2.1 FMEA的定义
FMEA Failure Mode and Effect Analysis 失效模式与效应分析
失效----产品丧失了规定的功能。 失效模式 ----失效的表现形式。 效应----失效模式在客户处(包括下工序)所造成的结果。
在产品设计和过程设计阶段,对构成产品的系统、子系 统或零部件、工序中可能存在、可能产生的弱点和缺陷, 以及这些弱点和缺陷可能产生的后果与风险进行分析, 并采取必要的措施加以消除的系统的、文件化的、持续 的、预防性的活动。
5.量化 6.优化
风险
措施
使用流程图 以展示目前或 计划的制程; 剖析系统/产 品生产过程的 单元组成;
针对每一个 过程列出所有 功能。
对各过程每 一个功能可能 出现的失效进 行评估:失效 模式、失效后 果、失效原因 、现行控制
根据给定的 评分标准对风 险进行量化评 估:S、O、D 、RPN
何为FMEA

用现行设计控制方法对潜在失效起因/机理
及后续的失效模式探测能力的评价
为了减小 D 值 需不断改进设计控制方法
何为FMEA
不易探测度数(D)推荐的评价准则
(设计小组对评定准则和分级规则应意见一致,即使因为个别产品 分析作了修改也应一致)
何为FMEA
表格说明
18 风险顺序数(RPN)
RPN是对设计风险性的度量
何为FMEA
13 级别(重要程度)
表格说明
用于对零件、子系统或系统的产品特性分级 (例如:关键、主要、重要和重点)
用适当的字母或符号在DFMEA中注明并在 建议措施中记录,是特殊过程控制的依据。
何为FMEA
表格说明
14 潜在失效的起因/机理
指明失效模式发生的原因或作用机理
是产品设计所固有的
与产品的使用有关
≥
≤
何为FMEA
16 现行设计控制
表格说明
能够确保设计充分性的任何技术
失效模式如同疾病 设计控制则象医生采取的诊断方法
(医生喜欢采取预防措施)
(1)消除失效产生的原因 设计控制有三种类型:(2)查明失效的原因
(3)检测失效模式
何为FMEA
17 不易探测度数(D
表格说明
)
指在零部件、子系统或系统投产之前
列出每个失效模式的所有可以想象到的 失效起因和机理
许多失效模式是多种原因造成的
失效通常是由一连串的原因造成的,从 直接原因到根本原因(原因链)
何为FMEA
表格说明
14 潜在失效的起因/机理
简明扼要、完整地将起因/机理列出来
典型的失效起因如:
典型的失效机理如:
规定的材料不对 设计寿命估计不当 应力过大 润滑不足 维修保养说明不当 环境保护不够 计算错误等
FMEA百度百科
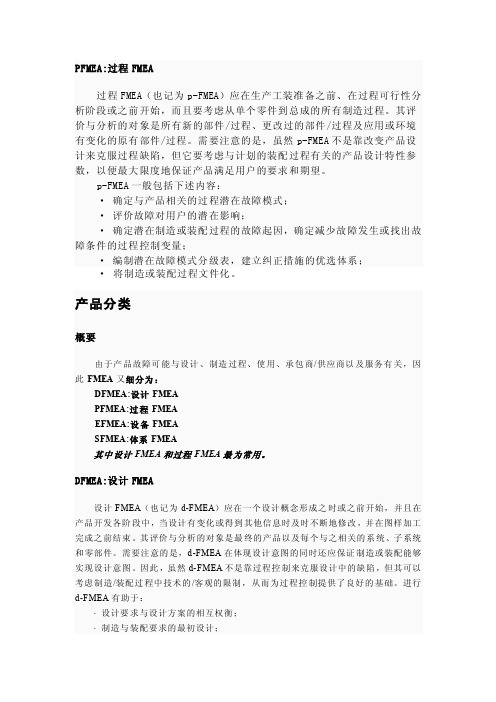
PFMEA:过程FMEA过程FMEA(也记为p-FMEA)应在生产工装准备之前、在过程可行性分析阶段或之前开始,而且要考虑从单个零件到总成的所有制造过程。
其评价与分析的对象是所有新的部件/过程、更改过的部件/过程及应用或环境有变化的原有部件/过程。
需要注意的是,虽然p-FMEA不是靠改变产品设计来克服过程缺陷,但它要考虑与计划的装配过程有关的产品设计特性参数,以便最大限度地保证产品满足用户的要求和期望。
p-FMEA一般包括下述内容:· 确定与产品相关的过程潜在故障模式;· 评价故障对用户的潜在影响;· 确定潜在制造或装配过程的故障起因,确定减少故障发生或找出故障条件的过程控制变量;· 编制潜在故障模式分级表,建立纠正措施的优选体系;· 将制造或装配过程文件化。
产品分类概要由于产品故障可能与设计、制造过程、使用、承包商/供应商以及服务有关,因此FMEA又细分为:DFMEA:设计FMEAPFMEA:过程FMEAEFMEA:设备FMEASFMEA:体系FMEA其中设计FMEA和过程FMEA最为常用。
DFMEA:设计FMEA设计FMEA(也记为d-FMEA)应在一个设计概念形成之时或之前开始,并且在产品开发各阶段中,当设计有变化或得到其他信息时及时不断地修改,并在图样加工完成之前结束。
其评价与分析的对象是最终的产品以及每个与之相关的系统、子系统和零部件。
需要注意的是,d-FMEA在体现设计意图的同时还应保证制造或装配能够实现设计意图。
因此,虽然d-FMEA不是靠过程控制来克服设计中的缺陷,但其可以考虑制造/装配过程中技术的/客观的限制,从而为过程控制提供了良好的基础。
进行d-FMEA有助于:·设计要求与设计方案的相互权衡;·制造与装配要求的最初设计;·提高在设计/开发过程中考虑潜在故障模式及其对系统和产品影响的可能性;·为制定全面、有效的设计试验计划和开发项目提供更多的信息;·建立一套改进设计和开发试验的优先控制系统;·为将来分析研究现场情况、评价设计的更改以及开发更先进的设计提供参考。
FMEA知识点

潜在失效模式及后果分析POTENTIAL FAILURE MODE AND EFFECTS ANALYSIS(FMEA)什么是FMEAFMEA可以描述为一组系统化的活动,其目的是:(a)认可并评价产品/过程中的潜在失效以及该失效的后果;(b)确定能够消除或减少潜在失效发生机会的措施;(c)将全部过程形成文件。
FMEA是对确定设计或过程必须做哪些事情才能使顾客满意这一过程的补充。
所有的FMEA都关注设计,无论是产品设计或者是过程设计。
FMEA的实施FMEA是一门专门的技术,其应用是识别并帮助最大程度地减少潜在的隐患。
实施的时间性成功实施FMEA项目的最重要因素之一是时间性。
其含义是指“事件发生前”的措施,而不是“事实出现后”的演练。
为实现最大价值,FMEA必须在产品或过程失效模式被纳入到产品或过程之前进行。
事先花时间很好地完成FMEA分析,能够最容易、低成本地对产品或过程进行更改,从而最大程度地降低后期更改的危机。
FMEA能够减少或消除实施可能会带来更大隐患的预防/纠正性更改的机会。
应在所有FMEA小组间提倡交流和协作。
实施的顺序进行FMEA分析有一定的顺序,并不是简单地填写一下表格,而是要理解FMEA的过程,以便消除风险并策划适宜的控制方法以确保顾客满意。
潜在失效模式及后果分析顺序实施FMEA的时机1、新设计、新技术或新过程。
FMEA的范围是全部设计、技术或过程。
2、对现有设计或过程的修改(假设对现有设计或过程已有FMEA)。
FMEA的范围应集中于对设计或过程的修改、由于修改可能产生手工艺相互影响以及现场的历史情况。
3、将现有的设计或过程用于新的环境、场所或应用(假设对现有设计或过程已有FMEA)。
FMEA的范围是新环境或场所对现有设计或过程的影响。
实施FMEA的人员FMEA是一个小组活动的成果,在最初的设计FMEA过程中,设计工程师应能够直接地、主动地联系所有有关部门的代表。
这些代表包括(但不限于)装配、制造、设计、分析/试验、可靠性、材料、质量、服务和供方以及负责更高或更低一层次的总成或系统、子系统或部件的设计领域。
- 1、下载文档前请自行甄别文档内容的完整性,平台不提供额外的编辑、内容补充、找答案等附加服务。
- 2、"仅部分预览"的文档,不可在线预览部分如存在完整性等问题,可反馈申请退款(可完整预览的文档不适用该条件!)。
- 3、如文档侵犯您的权益,请联系客服反馈,我们会尽快为您处理(人工客服工作时间:9:00-18:30)。
R.R. Mohr February 2002 8th Edition
Background
PREMISE – You own/operate/require/design/or are responsible for equipment essential to a system/process/activity which may be small or large, simple or complex. It may be a future plan, or be presently in operation. NEED – Reassurance that causes, effects, and risks of system failures have been reviewed systematically.
1.
6
8671
The Process
Define the system to be analyzed, and obtain necessary drawings, charts, descriptions, diagrams, component lists. Know exactly what you’re analyzing; is it an area, activity, equipment? – all of it, or part of it? What targets are to be considered? What mission phases are included? 2. Break the system down into convenient and logical elements. System breakdown can be either Functional (according to what the System elements “do”), or Geographic/Architectural (i.e., according to where the system elements “are”), or both (i.e., Functional within the Geographic, or vice versa). 3. Establish a coding system to identify system elements. 4. Analyze (FMEA) the elements.
Element
Switch Valve Spring Cable Relay Operator
Failure Mode Examples
open, partially open, closed, partially closed, chatter open, partially open, closed, partially closed, wobble stretch, compress/collapse, fracture stretch, break, kink, fray contacts closed, contracts open, coil burnout, coil short wrong operation to proper item, wrong operation to wrong item, proper operation to wrong item, perform too early, perform too late, fail to perform
4
8671
Definitions
FAILURE EFFECT: – The consequence(s) of a failure mode on an operation, function, status of a system/process/activity/environment. The undesirable outcome of a fault of a system element in a particular mode. The effect may range from relatively harmless impairment of performance to multiple fatalities, a major equipment loss, and environmental damage, for example. • All failures are faults; not all faults are failures. Faults can be caused by actions that are not strictly failures. • A system that has been shut down by safety features responding properly has NOT faulted (e.g., an overtemperature cutoff.) • A protective device which functions as intended (e.g., a blown fuse) has NOT failed. FAILED/FAULTED SAFE: – Proper function is compromised, but no further threat of harm exists (e.g., a smoke detector alarms in the absence of smoke). FAILED/FAULTED DANGEROUS: – Proper function is impaired or lost in a way which poses threat of harm (e.g., a smoke detector does not alarm in the presence of smoke).
1.
7
8671
The Process: Three Questions to Ask/Answer
1. Will a failure of the system result in intolerable/undesirable loss? If NO, document and end the analysis. If YES, see (1.a.). 1.a.Divide the system into its subsystems*. Ask this questions for each subsystem: Will a failure of this subsystem result in These intolerable/undesirable loss? If NO, document and end the “filtering” analysis. If YES, see (1.b). questions shorten the 1.b. Divide each subsystem into its assemblies. Ask this question for analysis each assembly: Will a failure of this assembly result in and intolerable/undesirable loss? If NO, document and end the conserve analysis. If YES, continues this questioning through the manhours. subassembly level, and onward – into the piece-part level if necessary. These two 2. For each analyzed element, what are the Failure Modes? questions, alone, guide 3. For each failure mode, what are the Failure Effects? “classical” FMEA – General FMEA. FMECA – Severity and Probability assessments
3
8671
Definitions
“Failure Modes…” is a FAULT: misnomer– some sources – Inability to function in a desired manner, or operation now call FMEA by in an undesired manner, regardless of cause. another name – “Fault FAILURE: Hazard Analysis.” – A fault owing to breakage, wear out, compromised structural integrity, etc. – FMEA does not limit itself strictly to failures, but includes faults. FAILURE MODE: – The manner in which a fault occurs, i.e., the way in which the element faults.
sual use, “FMEA” also means “FMECA”– the distinction between the two has become blurred.
APPROACH: – Perform an FMEA or FMECA. • FMEA + C = FMECA • C = Critically = Risk = Severity/Probability Assessment • Analogy: PHL / PHA = FMEA / FMECA CLASSICAL FMEA QUESTION (for each system element): 1. How ( i.e., in what ways) can this element fail (failure modes)? 2. What will happen to the system and its environment if this element does fail in each of the ways available to it (failure effects)? FMEA ORIGIN: – FMEA is a tool originated by SAE reliability engineers. It continues to be associated by many with reliability engineering. It analyzes potential effects caused by system elements ceasing to behave as intended.